Japan servo motor driven press and market trend
电机行业专业术语
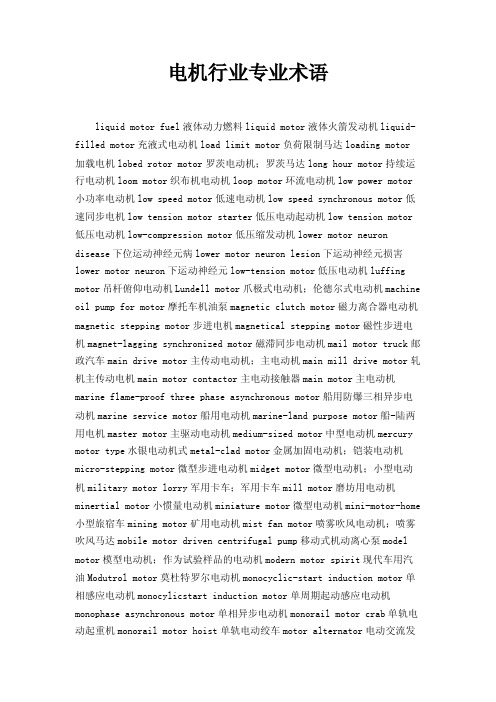
电机行业专业术语liquid motor fuel液体动力燃料liquid motor液体火箭发动机liquid-filled motor充液式电动机load limit motor负荷限制马达loading motor加载电机lobed rotor motor罗茨电动机;罗茨马达long hour motor持续运行电动机loom motor织布机电动机loop motor环流电动机low power motor小功率电动机low speed motor低速电动机low speed synchronous motor低速同步电机low tension motor starter低压电动起动机low tension motor低压电动机low-compression motor低压缩发动机lower motor neuron disease下位运动神经元病lower motor neuron lesion下运动神经元损害lower motor neuron下运动神经元low-tension motor低压电动机luffing motor吊杆俯仰电动机Lundell motor爪极式电动机;伦德尔式电动机machine oil pump for motor摩托车机油泵magnetic clutch motor磁力离合器电动机magnetic stepping motor步进电机magnetical stepping motor磁性步进电机magnet-lagging synchronized motor磁滞同步电动机mail motor truck邮政汽车main drive motor主传动电动机;主电动机main mill drive motor轧机主传动电机main motor contactor主电动接触器main motor主电动机marine flame-proof three phase asynchronous motor船用防爆三相异步电动机marine service motor船用电动机marine-land purpose motor船-陆两用电机master motor主驱动电动机medium-sized motor中型电动机mercury motor type水银电动机式metal-clad motor金属加固电动机;铠装电动机micro-stepping motor微型步进电动机midget motor微型电动机;小型电动机military motor lorry军用卡车;军用卡车mill motor磨坊用电动机minertial motor小惯量电动机miniature motor微型电动机mini-motor-home 小型旅宿车mining motor矿用电动机mist fan motor喷雾吹风电动机;喷雾吹风马达mobile motor driven centrifugal pump移动式机动离心泵model motor模型电动机;作为试验样品的电动机modern motor spirit现代车用汽油Modutrol motor莫杜特罗尔电动机monocyclic-start induction motor单相感应电动机monocylicstart induction motor单周期起动感应电动机monophase asynchronous motor单相异步电动机monorail motor crab单轨电动起重机monorail motor hoist单轨电动绞车motor alternator电动交流发电机motor amplifier电机放大器motor analyser发动机试验机;发动机试验台motor atomizer动力弥雾机motor auger机力螺旋钻motor automatic relay电机自动继电器motor bark remover机动剥树皮机motor base(frame)电动机座motor base(MB)电动机基础motor base pin电动机座销轴motor base电机底座motor battery电动机电池motor bearing电动机轴承motor bearings电机轴承motor bed-plate电动机机座motor board电动机配电盘motor boat摩托艇motor body发动机壳体motor bogie自动转向架motor brake magnet电动机闸磁铁motor branch circuit电动机分支电路;电动机馈电支路motor brass alloy电机黄铜合金motor brass电动机黄铜motor brush电动机刷;电机电刷motor cabinet电机座motor cable电动机电缆motor capacity电动机容量motor car fitter汽车修配工motor car insurance汽车保险motor carbon电动机碳刷;电机碳刷motor carrier传送机motor case电动机壳;发动机壳体motor casing(frame)电动机壳motor casing电机壳;摩托车外胎motor cavity电机座位motor chamber diameter 发动机燃烧室直径motor characteristic电动机特性;电动机特性曲线motor circuit动力电路motor coach长途公共客车motor combination电动机的组合motor commutator电动机整流子motor compressor电动压缩机motor console发动机试验操纵台motor constant电动机常数motor control relay 电动机控制继电器motor control电动机操纵;电动机电子控制;电动机控制motor controller电动机控制器motor cooling jacket发动机冷却套motor cooling电动机冷却motor coordinating center运动协调中枢motor coupling电动机联轴节motor current-transformer电动变流器motor cut-out switch电动机停机开关motor cuts out发动机停车motor cycle insurance摩托车保险motor decussation运动交叉motor disturbance运动障碍motor drill手电钻motor drive asphalt pump电动沥青泵motor drive oil lifter电动油压升降机motor drive shaft电动机驱动轴;马达轴motor drive type电动机传动型motor drive电动机拖动;电动驱动;电机驱动motor driven blower电动鼓风机motor driven distributor电动分配器motor driven hoist电动绞车motor driven layer radiographic X-ray apparatus电动断层X射线机motor driven miniature pump set电动微型水泵机组motor driven psychrometer电动型通风干湿计motor driven pump电动泵motor driven saw电锯motor driven sludge excavator电动挖泥机motor driven slush pump电动泥浆泵motor driven starter电动起动机motor driven switch电机驱动开关motor driven turbine pump电动涡轮泵motor driven welding machine电动焊机;电动机拖动式焊机motor driving time relay电动机式时间继电器motor dynamo unit电动直流发电机组motor dynamo电动发电机;电动直流发电机motor dynamometer电动机功率计motor eccentricity电机偏心率motor effect电动机效应motor efficiency电动机效率motor element电动机元件;运动元件motor enclosure电机壳motor end closure发动机喷口盖motor end plate运动终板motor excitation电动机励磁motor exciting current电动机励磁电流motor fan电扇motor fault 电动机缺陷motor fiber运动纤维motor fire brigade vehicle救火车;救火车motor for boat船用发动机motor for kicker and doffer抖动器和滚筒用电动机motor for wood-working木工电动机motor foundation电动机基础motor frame through bolt电动机长螺栓motor frame电动机架motor fuel additive发动机燃料添加剂motor fuel constituent发动机燃料组成motor function运动功能;运动机能motor fuse电动机熔断器motor gain电动机增益motor gasoline动力汽油motor generator arc welder电动发电机式直流弧焊机motor glider电动滑翔机motor grab电动抓斗motor group电动机组motor head发动机前端motor hoist电动葫芦;电动提升机;电葫芦motor hotel汽车饭店motor hull insurance汽车车身保险motor inclosure电动机壳Motor Industry Research Association(MIRA)汽车工业研究协会motor integrating meter感应式电度表motor interrupter电动断续器motor launch汽艇motor line电动机系列motor load control(MLC)电动机负载控制motor load电动机负载motor lorry(truck)载重汽车motor machine电动机械motor magnet电动电磁铁motor manufacturer电动机制造者motor meter电动机式电度表;电动机型仪表;感应式电表motor method发动机法;发动机开车法motor mount ring发动机安装环motor mower with binder attachment 机动青草割捆机;带打捆装置的动力割草机motor mower with center drive 中央驱动式动力割草机motor mower with side drive侧驱式动力割草机motor mower动力刈草机;机动割草机motor nozzle发动机喷管motor nuclei 运动核motor octane number(MON)马达法辛烷值motor off switch电动机切断开关motor oil电机用油;车用机油;马达油motor on-off switch马达启停开关motor panel电动机配电盘motor performance电动机性能motorpetrol车用汽油motor pinion电动机小齿轮motor pitch电动机节距motor plough自走犁motor plow机动犁motor point运动点motor power(output)电动机功率motor power发动机推力motor press机动压力机motor protection against overheat电动机过热保护;马达过热保护motor protection relay电动机保护继电器motor pulley电动机皮带轮motor pump(MMP)马达泵motor pump works电泵厂motor pump电动泵;机动泵motor rear end plate电动机后端盖motor reducer电动机减速器;电机减速机;马达降速器motor reducing gear电动机减速器;电机减速机motor reduction unit降速电动机motor reel电动机轴motor repair shop汽车修配厂motor repair汽车修理motor road汽车路motor room电机室motor rotor tester电机转子试验装置motor rotor电动机转子motor saw动力锯motor scooter低座小摩托车motor scraper自动铲运机;自行式铲运机motor shaft电机轴motor shell电动机壳motor ship汽船;发动机推进飞行器;内燃机船motor side电动机侧motor siren电笛;电动警笛;马达报警器motor sleigh雪橇motor slide rails电动机导轨motor slip感应电动机转差率motor specification电动机规格motor speech area运动言语中枢motor speed control电动机转速控制motor speed controller发动机转速调节器motor speed电动机转速motor spirit车用汽油motor spring汽车弹簧。
派克伺服电机M系列使用手册
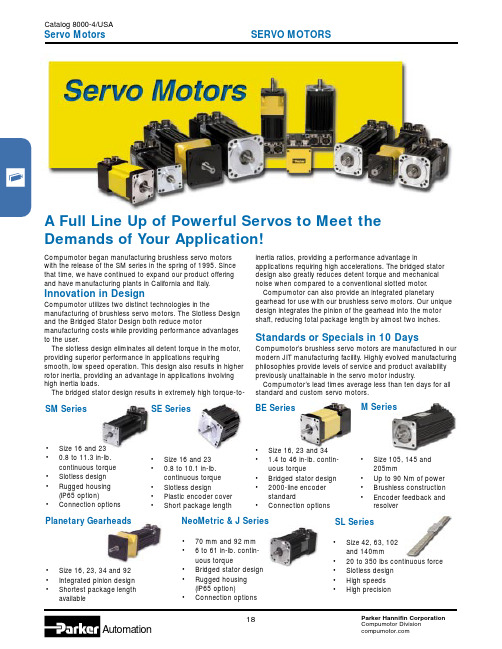
•Size 16 and 23•0.8 to 11.3 in-lb.continuous torque •Slotless design •Rugged housing (IP65 option)•Connection optionsSM Series SE Series•Size 16 and 23•0.8 to 10.1 in-lb.continuous torque •Slotless design•Plastic encoder cover •Short package lengthBE Series•Size 16, 23 and 34• 1.4 to 46 in-lb. contin-uous torque•Bridged stator design •2000-line encoder standard•Connection optionsNeoMetric & J Series•70 mm and 92 mm •6 to 61 in-lb. contin-uous torque•Bridged stator design •Rugged housing (IP65 option)•Connection options•Size 16, 23, 34 and 92•Integrated pinion design •Shortest package length availablePlanetary Gearheads SL SeriesM SeriesA Full Line Up of Powerful Servos to Meet the Demands of Your Application!Compumotor began manufacturing brushless servo motors with the release of the SM series in the spring of 1995. Since that time, we have continued to expand our product offering and have manufacturing plants in California and Italy.Innovation in DesignCompumotor utilizes two distinct technologies in themanufacturing of brushless servo motors. The Slotless Design and the Bridged Stator Design both reduce motormanufacturing costs while providing performance advantages to the user.The slotless design eliminates all detent torque in the motor,providing superior performance in applications requiringsmooth, low speed operation. This design also results in higher rotor inertia, providing an advantage in applications involving high inertia loads.The bridged stator design results in extremely high torque-to-inertia ratios, providing a performance advantage inapplications requiring high accelerations. The bridged stator design also greatly reduces detent torque and mechanical noise when compared to a conventional slotted pumotor can also provide an integrated planetarygearhead for use with our brushless servo motors. Our unique design integrates the pinion of the gearhead into the motor shaft, reducing total package length by almost two inches.Standards or Specials in 10 DaysCompumotor’s brushless servo motors are manufactured in our modern JIT manufacturing facility. Highly evolved manufacturing philosophies provide levels of service and product availability previously unattainable in the servo motor industry.Compumotor’s lead times average less than ten days for all standard and custom servo motors.•Size 105, 145 and 205mm•Up to 90 Nm of power •Brushless construction •Encoder feedback and resolver•Size 42, 63, 102and 140mm•20 to 350 lbs continuous force •Slotless design •High speeds •High precisionFeedback•Higher resolutionencoders•Higher temperatureencodersCommon Special RequestsConnectorization•Right angle connector housing•MS connectors on back cover•Special cable lengths•Hi-flex cables•Customer specified cablesand connectors•Cable exiting throughback coverFlanges•Tapped mounting holes•Customer specified flanges•Face mountBrakes•Internal or externalShafts•Special lengths•Special flats•Special keyways•Special shaft diameters•Metric shaft diameters•Hollow shafts•Rear Shaft Extension•Double flats•Shaft pinning•Pressed on gears•Center tapped•Special shaft materialsGearheads•Non-standard ratios•Customer specifiedflanges•Customer specifiedoutput shaft Compumotor offers a broad range of standard options with allof our brushless servo motor families. Our numerous shaft,feedback and connection options will fulfill the needs of most ofour customers. However, we realize that from time to time theneed arises to have a custom motor designed specially for yourapplication.Whether you need custom connectors, mounting, or acustom winding, Compumotor can build a motor designed toyour exact specifications. Compumotor provides these specialdesigns for our customers with:•Minimal impact on product lead time•Modest impact on pricing•No minimum quantitiesCompumotor’s modern manufacturing system allows us tooffer custom motor solutions without sacrificing product qualityand availability. All of our custom motors are built in ourstandard servo motor work cell, and our computerized customproduct tracking system allows us to provide consistent, high-quality custom products. And, because custom motormanufacturing is integrated into our standard manufacturingprocess, we can often build and ship custom designed motorsand cables in the same time frame as standard products.Compumotor provides this service for one simple reason: tomake it easier for you, our customer, to integrate a Compumo-tor servo motor into your application. We provide more thanjust a component, we provide a custom designed servo motorsolution.Custom Designed Servo Motors for YourSpecific Application!Windings:•Specific bus voltageFeatures•Size 105, 145 and 205mm diameters •53 to 115 lb-in continuous torque •Brushless construction •Thermal protection •IP65 option•Resolver and encoder feedback options •Two-year warranty•CAD (.dxf) drawings available •CE compliant•Electrically released brakes availableLow Cost,High PerformanceThe M Series is Compumotor’s newest series of motors.Completing Compumotor’s line of servos, the M Series moves innovative design into larger-frame motors, yet they remain affordably priced. An eight-pole design allows for highlydynamic motion while minimizing power loss within the motor itself.Part Numbering System1Standard resolver not compatible w/ APEX drives. Please contact Compumotor’s Custom Servo Motor group for motors compatible with the APEX series of drives 2Pipe thread only available in M2053 and M2054 resolver motors 3StandardM SeriesFrame,Magnet Length1053 1453 14551054 1454 20522053 2054WindingJ, K, L, M, N,P , R, SFeedbackJ - 2000 ppr encoderR - Resolver 1ShaftN - Normal K - Keyway 3ConnectionMS - Military style PT - Pipe thread 2OptionsN - None V - IP65B - Brake1 @ 40˚ C ambient, derate phase currents and torques by 7%.2 For higher-speed operation, please call the factory.3 Measured line to line, +/- 10%.4 Value is measured peak of sine wave.5 +/- 30%, line to line, inductance bridge measurement @ 1Khz.6 Initial winding temperature mut be 60˚ C or less before peak current is applied.7 Direct current through a pair of motor phases of a trapezoidally (six state) commutated motor.8 Peak of sinusoidal current in any phase for a sinusoidallycommutated motor.9 Total motor torque per peak of the sinusoidal amps measured in any phase, +/- 10%.10 Maximum time duration with 2 times (or 3 times) rated current applied with initial winding temperature at 60˚ C.M Series Performance Curves10002000300040005000600005010015020025005.6011.216.822.428.010002000300040005000600005010015020025030005.6011.216.822.428.033.650010001500200025003000350040004500100200300400500600700800011.222.433.644.856.067.279.489.6050010001500200025003000350040004500020040060080010001200500100015002000250030000400800120016002000044.889.6134.179.224.M1053KSpeed (RPM)T o r q u e (L b -i n )T orque (Nm)M1054KSpeed (RPM)T o r q u e (L b -i n )T orque (Nm)M1453LSpeed (RPM)T o r q u e (L b -i n )T orque (Nm)M1455PSpeed (RPM)T o r q u e (L b -i n )T orque (Nm)M2052PSpeed (RPM)T o r q u e (L b -i n )T orque (Nm)50010001500200025003000050010001500200025003000056.0112.168.224.280.336.M2054SSpeed (RPM)T o r q u e (L b -i n )T orque (Nm)M2053R Speed (RPM)T o r q u e (L b -i n )T orque (Nm)5001000150020002500300035004000450002004006008001000120022.444.867.289.6112.134.022.444.867.289.6112.134.M1454NSpeed (RPM)T o r q u e (L b -i n )T orque (Nm)CONTINUOUS PEAK(560VDC)I cs (sine) = 109.4 amps, I pk (sine) = 328.2 amps I cs (sine) = 85.0 amps, I pk (sine) = 255.0 amps I cs (sine) = 55.7 amps, I pk (sine) = 167.1 ampsI cs (sine) = 63.6 amps, I pk (sine) = 190.8 ampsI cs (sine) = 60.9 amps, I pk (sine) = 182.7 ampsI cs (sine) = 40.7 amps, I pk (sine) = 122.1 ampsI cs (sine) = 23.7 amps, I pk (sine) = 71.1 amps I cs (sine) = 20.3 amps, I pk (sine) = 60.9 amps05001000150020002500300005001000150020002500300035004000056.0112.168.224.280.336.395.448.M Series Dimensional Drawings Dimensions in inches (mm)105 mm Dimensional Drawing145 mm Dimensional DrawingWiring and Cable Specifications“MS” Connection OptionsThe M Series Motors are available standard with “MS”connectors. These bayonet-style connectors provide quick-disconnect. Mating cables are specified and ordered separately. With the “MS” connection option, the motor phase and brake wires are in one connector, and the hall,encoder, and temperature switch wires are in the other connector. This option works well when using an amplifier with a built-in controller, or when all cables enter into acabinet or enclosure and then are wired into a terminal strip .“PT” Connection OptionsThe M2053 and M2054 motors with resolver feedback are available with the PT connector option due to the high current requirements of these motors. A terminal block is available inside the motor housing to make the required connections.M Series, Feedback SpecificationsCommutation ChartPhase B-A Phase A-CClockwise rotation as viewed from front shaft.PhaseC-BHall #1Hall #2Hall #3。
四冲程摩托车汽油机油

四冲程摩托车汽油机油警告:如果不遵守适当的防范措施,本标准所属产品在生产、贮运和使用等过程中可能存在危险。
本标准无意对与本产品有关的所有安全问题提出建议。
用户在使用本标准之前,有责任建立适当的安全和防范措施,并确定相关规章限制的适用性。
1范围本标准规定了拥有一个共用机油箱的四冲程火花点燃式汽油发动机润滑油(下文称为四冲程摩托车汽油机油)的术语和定义、分类和标记、要求和试验方法、检验规则及标志、包装、运输和贮存。
本标准适用于以精制矿物油、合成油或精制矿物油与合成油的混合油为基础油,加入多种添加剂制成的,在摩托车、轻便摩托车、全地形车(ATV S)的发动机和相关动力传动系统[变速器(箱)、离合器和启动器]以及相关设备中使用的四冲程摩托车汽油机油。
2 规范性引用文件下列文件对于本文件的应用是必不可少的。
凡是注日期的引用文件,仅所注日期的版本适用于本文件。
凡是不注日期的引用文件,其最新版本(包括所有的修改单)适用于本文件。
GB/T 265 石油产品运动粘度测定法和动力粘度计算法GB/T 2433 添加剂和含添加剂润滑油硫酸盐灰分测定法(GB/T 2433-2001,eqv ISO 3987:1994)GB/T 4756 石油液体手工取样法(GB/T 4756-1998, eqv ISO 3170:1988)GB/T 7631.17 润滑剂、工业用油和相关产品(L类)的分类第17部分:E组(内燃机油)(GB/T 7631.17-2014,ISO 6743-15:2007,MOD)GB 11121-2006 汽油机油GB/T 12579 润滑油泡沫特性测定法(GB/T 12579-2002,eqv ISO 6247:1998)GB/T 14906 内燃机油粘度分类NB/SH/T 0059 润滑油蒸发损失的测定诺亚克法NB/SH/T 0824 润滑油中添加剂元素含量的测定电感耦合等离子体原子发射光谱法NB/SH/T 0840 四冲程摩托车汽油机油离合器摩擦特性试验方法SH/T 0103 含聚合物油剪切安定性的测定柴油喷嘴法SH 0164 石油产品包装、贮运及交货验收规则SH/T 0751 高温和高剪切速率下粘度测定法(锥形塞粘度计法)ASTM D4485-2011c 发动机油性能规格标准(Standard Specification for Performance of Engine Oils)ASTM D4683 高温高剪切速率下黏度测定法锥型轴承模拟机法(Standard Test Method for Measuring Viscosity at High Shear Rate and High Temperature by Tapered BearingSimulator)ASTM D7320 用程序IIIG火花点燃发动机,评价汽车发动机油的标准试验方法(Standard Test Method for Evaluation of Automotive Engine Oils in the Sequence IIIG, Spark-Ignition Engine)SAE J300-2009 发动机油黏度分类(Engine Oil Viscosity Classification)3 术语和定义下列术语和定义适用于本文件。
DRIVER FOR MOTOR DRIVEN VEHICLE

专利名称:DRIVER FOR MOTOR DRIVEN VEHICLE发明人:MATSUNAMI KAZUHIKO,松並 和彦申请号:JP特願平6-170040申请日:19940629公开号:JP特開平8-19116A公开日:19960119专利内容由知识产权出版社提供专利附图:摘要:PURPOSE:To improve traveling performance such as a traveling distance,accelerability, gradability, etc., by providing the merits of both a battery having a large output density and a battery having large energy density. CONSTITUTION:A driver 10comprises a lead oxide battery 12 as a battery having a large output density, a sodium-sulfur battery 14 as a battery having large energy density, a motor 18 for rotating drive wheels 16, and an encoder 20 as motor speed detecting means for detecting the number of revolutions N of the motor 18. The driver further comprises a controller 22 for supplying power from the battery 12 to the motor 18 when the number of revolutions N is higher than that detected by the encoder 20 is high and power from the battery 14 to the motor 18 when the number of revolutions N is lower.申请人:SUZUKI MOTOR CORP,スズキ株式会社地址:静岡県浜松市高塚町300番地国籍:JP代理人:高橋 勇更多信息请下载全文后查看。
MOTOR DRIVE CIRCUIT AND AIR-CONDITIONER WITH MOTOR

专利名称:MOTOR DRIVE CIRCUIT AND AIR-CONDITIONER WITH MOTOR DRIVECIRCUIT发明人:SARUHASHI KOICHI,猿橋 浩一,YOSHIDAHIROSHI,吉田 浩申请号:JP特願平7-40748申请日:19950228公开号:JP特開平8-237992A公开日:19960913专利内容由知识产权出版社提供专利附图:摘要:PURPOSE: To drive a motor while decreasing the number of output ports by anarrangement wherein three or more signals are delivered from one output port of an output circuit and converted into a plurality of different signals through a conversion circuit. CONSTITUTION: A signal is delivered from a port U or a bar U in a microcomputer to point P. A comparator 46 functions to produce a waveform at an output port U'. When such waveform is transmitted to the point P, a comparator 47 functions to produce a waveform at an output port bar U'. Similarly, two different signal waveforms are outputted from conversion circuits 40V, 40W. Conventionally, six output ports are required for driving a motor but the number of output ports of microcomputer can be halved in the inventive drive circuit and the output port can be saved.申请人:SANYO ELECTRIC CO LTD,三洋電機株式会社地址:大阪府守口市京阪本通2丁目5番5号国籍:JP代理人:岡田 敬更多信息请下载全文后查看。
MOTOR DRIVE

专利名称:MOTOR DRIVE发明人:SAKUMA, Yoichi OmronCorporation,KAWANO, Atsushi OmronCorporation申请号:EP99973492.4申请日:19991130公开号:EP1160410A1公开日:20011205专利内容由知识产权出版社提供专利附图:摘要:An apparatus for driving a motor that opens and closes the window of vehicle,for example, is so adapted that when the vehicle becomes submersed in the sea, a lake ora river, etc., the window is prevented from being closed owing to malfunctioning of a relay caused when a leakage current flows into an operating switch for opening and closing the window. When submersion is sensed and it is sensed that the motor is being rotated by a malfunction in a direction that closes the window, a relay for rotating the motor in the forward direction is actuated. This prevents the occurrence of a situation in which the motor is caused to rotate (especially in the direction that closes the window) regardless of the fact that the operating switch has not been operated.申请人:Omron Corporation地址:801, Minamifudodo, Horikawahigashiiru, Shiokoji-dori, Shimogyo-ku Kyoto-shi, Kyoto 600-8530 JP国籍:JP代理机构:Kilian, Helmut, Dr.更多信息请下载全文后查看。
Motor drive control apparatus, motor drive control

专利名称:Motor drive control apparatus, motor drivecontrol method and program of the same发明人:Zhiqian Chen,Isao Fujiwara申请号:US11186986申请日:20050722公开号:US20060043919A1公开日:20060302专利内容由知识产权出版社提供专利附图:摘要:A general-purpose comparator can be used as a comparison processing module to reduce the costs of a motor drive control apparatus. The apparatus has an electric machine; a magnetic pole position computation processing module; a pattern generationprocessing module; a switching angle computation processing module which computes a switching angle where switching is done in a next control period based on a pulse pattern;a comparison processing module which compares the magnetic pole position with the computed switching angle to generate a comparison signal; and an on-off output processing module which generates a PWM signal based on the comparison signal indicative of the comparison result. In this case, because the magnetic pole position is compared with the computed switching angle to generate the PWM signal based on the comparison signal, a general-purpose comparator can be used as the comparison processing module.申请人:Zhiqian Chen,Isao Fujiwara地址:Anjo-shi JP,Anjo-shi JP国籍:JP,JP更多信息请下载全文后查看。
CONTROL DEVICE OF FOUR-WHEEL DRIVE VEHICLE

专利名称:CONTROL DEVICE OF FOUR-WHEEL DRIVEVEHICLE发明人:MIKAMI TSUYOSHI,三上 強,KONDO KOICHI,近藤 宏一申请号:JP2004277723申请日:20040924公开号:JP2005059851A公开日:20050310专利内容由知识产权出版社提供专利附图:摘要:PROBLEM TO BE SOLVED: To provide a control device of a four-wheel drive vehiclecapable of proving a target drive force by driving front and rear wheels at an appropriate drive force distribution ratio corresponding to variations even if a vehicle state, a vehicle operating state, or a road state is changed.SOLUTION: This control device is set to a four-wheel drive mode driving the front and rear wheels when, in a second prime mover operation control means 154, the operating state of the vehicle in a vehicle start determination means 138, an acceleration operation determination means 146, a low temperature state determination means 162, and a wheel slip determination means 140 is in either of a start state, an accelerated state, and a low friction coefficient road surface traveling state. When the operating state is not in any of these states, the control device is set to a two-wheel drive mode for driving the front or rear wheels. By this, when they are in either of the start state, accelerated state, and low friction coefficient road surface traveling state, the control device is automatically set to the four-wheel drive mode driving the front and rear wheels. Accordingly, unnecessary four-wheel drive can be avoided according to the operating state to properly prevent a second prime mover operated to set to the four-wheel drive mode from being overheated.COPYRIGHT: (C)2005,JPO&NCIPI申请人:TOYOTA MOTOR CORP,トヨタ自動車株式会社地址:愛知県豊田市トヨタ町1番地国籍:JP代理人:池田 治幸更多信息请下载全文后查看。
N-Series Brushless Servo Motor用户手册说明书

N-SeriesBrushless Servo Motor ManualAllen-BradleyUse of MotorsServo motors are intended to drive machinery. As such, they must be part of a controlled system that includes a transistorized electronic amplifier. They are not intended for direct connection to the power supply or for use with thyristor drives. Instructions in the amplifier and control system manuals must be observed; this document does not replace those instructions.Unless specified otherwise, servo motors are intended for use in a normal industrial environment without exposure to excessive or corrosive moisture or abnormal ambient temperatures. The exact operating conditions may be established by referring to the data for the motor. The mating of motors to machinery is a skilled operation; disassembly or repair must not be attempted. In the event that a motor fails to operate correctly, contact the place of purchase for return instructions.Safety NotesThere are some possible hazards associated with the use of motors. The following precautions should be observed. Specific Warnings and Cautions are listed inside the back cover.Installation and Maintenance: Installation and maintenance or replacement must be carried out by suitably qualified service personnel, paying particular attention to possible electrical and mechanical hazards.Weight: Large motors are generally heavy, and the center of gravity may be offset. When handling, take appropriate precautions and use suitable lifting equipment. Beware of sharp edges; use protec-tive gloves when handling such assemblies.Flying leads: Ensure that flying or loose leads are suitably restrained, to prevent snagging or entan-glement, before carrying motors with such leads.Generation: If the motor is driven mechanically, it may generate hazardous voltages at its power input terminals. The power connector must be suitably guarded to prevent a possible shock hazard. Loose motors: When running an unmounted motor, ensure that the rotating shaft is adequately guarded and the motor is physically restrained to prevent it from moving. Remove the key which otherwise could fly out when the motor is running.Damaged cables: Damage to cables or connectors may cause an electrical hazard. Ensure there is no damage before energizing the system.Supply: Servo motors must not be directly connected to a power supply; they require an electronic drive system. Consult the instructions for the drive system before energizing or using the motor. Brakes: The brakes that are included on motors are holding brakes only and are not to be used as a mechanical restraining device for safety purposes.Safety requirements: The safe incorporation of this product into a machine system is the responsi-bility of the machine designer, who should comply with the local safety requirements at the place where the machine is to be used. In Europe this is likely to be the Machinery Directive. Mechanical connection: Motors must be connected to the machine with a torsionally rigid coupler or a reinforced timing belt. Couplers which are not rigid will cause difficulty in achieving an accept-able response from the control system. Couplings and pulleys must be tight as the high dynamic performance of a servo motor can easily cause couplings to slip, and thereby damage the shaft and cause instability. Care must be taken in aligning couplings and tightening belts so that the motor is not subjected to significant bearing loads, or premature bearing wear will occur. Once connected to a load, tuning will be affected. A system tuned without a load will probably require retuning once a load is applied.Connectors: Motor power connectors are for assembly purposes only. They should not be connected or disconnected while power is applied.© 1999 Rockwell International Corporation. All rights reserved.Electro-Craft is a trademark of Rockwell Automation.Printed in the United States of America.Information contained in this manual is subject to change without notice.Motor DataMECHANICAL DATA (1)Rotor Moment of Inertia kg-m20.0000090.000020.000080.000150.000240.00035lb-in-s20.000080.000160.00070.00130.00210.0031Rotor Moment of Inertia Motors W/Brake kg-m20.0000180.0000320.0001220.0002020.0002100.000320 lb-in-s20.000160.000280.001080.001790.001860.00283Motor Weight:NetEst. Shipping kg/lb 1.0/2.2 1.5/3.3 2.6/5.7 3.5/7.7 4.7/10.4 5.9/13.0 kg/lb 1.3/2.9 1.8/4.0 3.0/6.6 4.0/8.8 5.2/11.5 6.7/14.8Brake Motor Weight:NetEst. Shipping kg/lb 1.3/2.9 2.0/4.4 3.4/7.5 4.3/9.5 5.1/11.2 6.9/15.2 kg/lb 1.5/3.3 2.2/4.9 3.9/8.6 4.8/10.6 5.5/12.17.7/17.0Damping Nm/krpm0.0230.0340.130.190.200.19oz-in/krpm0.20.3 1.1 1.7 1.8 1.7 Friction Torque Nm0.120.230.260.340.450.73oz-in 1.0 2.0 2.3 3.0 4.0 6.5 Max. Operating Speed rpm600060006000600060005000 Shaft Material416 Stainless SteelWINDING DATA (1)Poles444444Sine Wave K T Torque Constant (2)Nm/A0.090.220.170.330.400.28 in-lb/A0.8 2.0 1.5 3.0 3.6 2.5Square Wave K T Torque Constant (3)Nm/A0.090.240.180.370.450.3 lb-in/A0.88 2.2 1.6 3.3 4.0 2.7K E Voltage Constant (4)V/krpm112721414934 Winding ResistancePhase to Phase at 25o COhms 3.92 5.89 2.24 2.68 2.790.77Winding InductancePhase to PhasemH 4.28.8 6.18.611.0 2.9 Thermal Resistance o C/Watt 3.0 2.2 1.6 1.2 1.10.83 Dielectric Rating Power Leads (R, S, T) to Ground: 1800 VACrms 50/60 Hz for 1 minute.MECHANICAL DATA (1)Rotor Moment of Inertia kg-m20.00090.00120.0015lb-in-s20.0080.010.013Rotor Moment of Inertia Motors W/Brake kg-m20.0006510.0007780.000893 lb-in-s20.005760.006890.00791Motor Weight:Net kg/lb9.1/20.111/24.313/28.7 Est. Shipping kg/lb9.6/21.211.7/25.813.8/30.4Brake Motor Weight:NetEst. Shipping kg/lb10.9/24.013.2/29.115.9/35.1 kg/lb11.4/25.113.8/30.413.9/37.3Damping Nm/krpm0.350.320.45oz-in/krpm 3.1 2.8 4.0 Friction Torque Nm 1.3 1.6 1.7oz-in111415Max. Operating Speed rpm400040003000Shaft Material416 Stainless SteelWINDING DATA (1) Poles444Sine Wave K T +10% Torque Constant (2)Nm/A0.380.490.63 lb-in/A 3.4 4.4 5.6Square Wave K T Torque Constant (3)Nm/A0.410.540.70 lb-in/A 3.7 4.8 6.2K E Voltage Constant (4)V/krpm476077Winding Resistance Phase to Phase at 25o C Ohms±10%0.89 1.0 1.23Winding InductancePhase to PhasemH 4.3 5.27.0Thermal Resistance o C/Watt0.810.760.70Dielectric Rating Power Leads (R, S, T) to Ground: 1800 VACrms 50/60 Hz for 1 minute.(1) Specifications are at 25o C unless otherwise noted.(3) Peak value of per phase square wave Amperes(2) Peak value of per phase sine wave Amperes (4) Peak value of sinusoidal phase to phase VoltsAmbient Temperature: Operating0 to 40°C (32 - 104°F)Relative Humidity:5% to 95%Storage0 to 50°C (32 - 122°F)non-condensingDimensional DataMotor DimensionsMotor AB AH AJ AK BB BE BF L L Brake S U XD TOLERANCES Model mm/in mm/in mm/in mm/in mm/in mm/in mm/in mm/in mm/in mm/in mm/in mm/in mm inchesN-230270/2.7521/0.81 (1)67/2.6338/1.50 (2)2/.097/0.285/0.21118/4.63161/6.32NA6/.25 (3)NA12345678-0.03-0.01±0.5±0.2-0.035-0.013-0.016-0.046-0.00012-0.0004±0.0196±0.0079-0.0014-0.0051-0.006-0.0181N-2304156/6.13199/7.82N-340663/2.4830/1.19 (1)98/3.8873/2.88 (4)3/.128/0.326/0.22144/5.67193/7.59 3.2 X 3.2 /0.125 X 0.125 (5)13/.5 (3)19/0.75 (6) N-3412169/6.67218/8.59N-421462/2.4535/1.38 (1)126/4.9556/2.19 (7)10/0.397/0.28174/6.85219/8.63 4.8 X 4.8 /0.1875 X 0.1875 (5)16/.63 (3)24/0.94 (6) N-4220199/7.85245/9.63N-563075/2.9650/1.97 (1)149/5.88114/4.50 (8)12/0.470.375 inUNC 199/7.83256/10.0619/.75 (3)38/1.50 (6)N-5637224/8.83281/11.06N-5647250/9.83306/12.06NOTE: Motors are manufactured to inch dimensions. Millimeter dimensions are approximate conversions from inches.Connector N-2302N-2304N-3406N-3412N-4214N-4220N-5630N-5637N-5647 Brake (mm/in)105/4.13143/5.63118/4.66144/5.66145/5.7170/67176/6.94202/7.94227/8.94 Power (mm/in)62/2.43100/3.93173/6.81198/7.81198/7.79223/8.79235/9.25260/10.25286/11.25 Encoder (mm/in)145/5.71183/7.22173/6.81198/7.81198/7.79223/8.79235/9.25260/10.25286/11.25Connector DataEncoder DataEncoders are factory aligned and must not be adjusted outside the factory.Encoder OutputsN-2300N-3400, N-4200 and N-5600Line Count 1000 (1) (2)2000 (1)Supply Voltage 5 VDC5 VDCSupply Current 175 mA max.300 mA max.Line DriverLM33926LS31Line Driver OutputTTLA, B, I signals: Logic 1 =2.5 VDC min @ 20 mA DC source,Logic 0 = 0.5 VDC max @ 20 mA DC sink.HALL signals: Logic 1 = 3.5 VDC min @ 1mA DC source, Logic 0 = 0.5 VDC max @ 5mA DC sink.Index PulseRefer to diagrams below(No key for physical reference)When facing the motor, the key is oriented 90o ±10 clockwise (mechanical) from connectors(1) Standard line count before quadrature.(2) N-2300 encoder does not have Absolute Signal (ABS)I+I-90o I-90N-2300 Encoder OutputN-3400, 4200 and 5600 Encoder OutputEncoder Phase-to-Neutral and Phase-to-PhaseOptions: Connectors and Shaft SealsAn environmentally sealed package may be formed when an N-Series motor is coupled with sealed cable assemblies and shaft seals.Factory manufactured power cables and encoder cables are available in standard cable lengths of 10, 25, 50, 75 and 100 feet (3, 7.6, 15, 23 and 30 meters). Factory cables provide environmental sealing and shield termination.Shaft Seal KitsConnectors and Connector KitsMOTOR SERIESPART NUMBERSIZE(Outside Dia x Inside Dia x Width) mm/inN-23000041-50680.035 x 0.001 x 0.005 / 0.875 x 0.250 x 0.125 N-34000041-50690.044 x 0.019 x 0.010 / 1.125 x 0.500 x 0.250 N-42000041-50700.044 x 0.025 x 0.010 / 1.125 x 0.625 x 0.250 N-56000041-50710.054 x 0.030 x 0.010 / 1.375 x 0.750 x 0.250 NOTE: Shaft seals are manufactured to inch dimensions. Millimeter dimensions are conversions from inches.Shaft seals require a lubricant to reduce wear. Lubricant is provided with kit.Motor Radial Load Force RatingsMotors are capable of carrying an axial load in most applications. The following table provides guidelines for 20,000 hour bearing life with a specified radial load applied to the center of the shaft. Please consult with Reliance Motion Control regarding loads, operating speeds and bearing life in your particular application to ensure the proper selection of motors.Brake Motor Application GuidelinesThe brakes offered as options on these servo motors are holding brakes. They are designed to hold the motor shaft at 0 rpm for up to the rated brake holding torque. The brakes are spring-set type, and release when voltage is applied to the brake coil.The brakes are not designed for stopping rotation of the motor shaft. Servo drive inputs should be used to stop motor shaft rotation. The recommended method of stopping motor shaft rotation is to command the servo drive to decelerate the motor to 0 rpm, and engage the brake after the servo drive has decelerated the motor to 0 rpm.If system main power fails, the brakes can withstand use as stopping brakes. However, use of the brakes as stopping brakes creates rotational mechanical backlash that is potentially damaging to the system, increases brake pad wear and reduces brake life. The brakes are not designed nor are they intended to be used as a safety device.A separate power source is required to disengage the brake. This power source may be controlled by the servo motor controls, in addition to manual operator controls.Brake SpecificationsBRAKE DATAMOTOR MAX. BACKLASH HOLDING TORQUE COIL CURRENT SERIES(BRAKE ENGAGED)(lb/in)(Nm)at 24 VDCN-2300 1 degree50.560.28 ADCN-340015 1.690.36 ADCN-420030 3.390.36 ADCN-560050 5.640.71 ADCMotor InstallationObserve the following installation guidelines and those in the Product Notice:1.Do not run motors that are not properly mounted. Attach all power and data cables after the motor is mounted.2.Mount motors with connectors pointing downward and use a drip loop in the cable to keep liq-uids flowing away from the connectors.3.Consider motor case temperature if necessary to safeguard operator and maintenance staff. Maximum case temperature is approximately 100°C (212°F) for a motor used at continuous rat-ing in a 40°C ambient temperature.4.The installer must comply with all local regulations and should use equipment and installation practices that promote electromagnetic compatibility and safety.Preventing Electrical NoiseElectroMagnetic Interference (EMI), commonly called “noise”, may adversely impact motor perfor-mance by inducing stray signals. Effective techniques to counter EMI include filtering the AC power, shielding and separating signal carrying lines, and practicing good grounding techniques. Effective AC power filtering can be achieved through the use of isolated AC power transformers or properly installed AC line filters. Physically separate signal lines from motor cabling and power wiring; do not parallel signal wires with motor or power wires or route signal wires over the vent openings of servo drives. Ground all equipment using a single-point parallel ground system that employs ground bus bars or straps. If necessary, use electrical noise remediation techniques to mitigate EMI in “noisy” environments.Knowledgable cable routing and careful cable construction improves system electromagnetic com-patibility (EMC). General cable build and installation guidelines include:1.Keep wire lengths as short as physically possible.2.Route signal cables (encoder, serial, analog) away from motor and power wiring.3.Separate cables by 1 foot minimum for every 30 feet of parallel run.4.Ground both ends of the encoder cable and twist the signal wire pairs.e shielded motor cables when necessary to prevent electromagnetic interference (EMI) with other equipment.Couplings and PulleysMechanical connections to the motor shaft, such as couplings and pulleys, require a rigid coupling or a reinforced timing belt. The high dynamic performance of servo motors can cause couplings, pulleys or belts to loosen or slip over time. A loose or slipping connection will cause system instability and may damage the motor shaft and keyway. All connections between the system and the servo motor shaft must be rigid to achieve acceptable response from the system. Connections should be periodically inspected to verify the rigidity.When mounting couplings or pulleys to the motor shaft, ensure that the connections are properly aligned and that axial and radial loads are within the specifications of the motor. The section “Load Force Ratings” provides guidelines to achieve 20,000 hours of bearing life. Additional information about load force ratings, including graphical depiction of varied load ratings and bearing life, is available for any motor from the Technical Support groups listed on the back cover. !WARNING: Motors and linkages must be securely mounted for a systemto be operational. Disassembled equipment should be appropriately iden-tified (tagged-out) and access to electrical power restricted (locked-out). Failure to observe these safety procedures could result in personal injuryand damage to equipment.Publication Number 1398-5.9 - May 1999Part Number 0013-1072-001 Rev BCopyright 1999 Allen-Bradley Company, Inc. Printed in USA Product InformationMotor Part Number IdentificationDisposal or Warranty Return of MotorsMotors may contain environmentally regulated materials, such as lead solder and circuit boards. When disposing of a motor, please recycle motors per regulations at your location. You may choose to return a motor for disposal by contacting your supplier.Please contact the source that supplied the motor for warranty, non-warranty, or disposal work. All returned products require a Return Material Authorization (RMA) number for efficient processing and tracking.For more information refer to our web site: /motionFACTORY DESIGNATED SPECIAL OPTIONSAA =STANDARD FLANGEOPTIONS00=STANDARD 04=24 VDC BRAKEENCODER LINE COUNTF =1000 (N-2300 STANDARD)H =2000 (N-3400 thru N-5600 STANDARD)K =5000MOTOR WINDING VOLTAGE DESIGNATOR1=115 VAC2=230 VACCONTINUOUS TORQUE CAPABILITY (LB-IN)FRAME SIZESERIES DESIGNATORN =NEMA FRAME STYLENOTE: OPTIONS NOT AVAILABLE ON ALL SIZES N - 42 14 - 2H 00 - AA。
FESTO EMMB-AS 2 品牌servo电机说明书
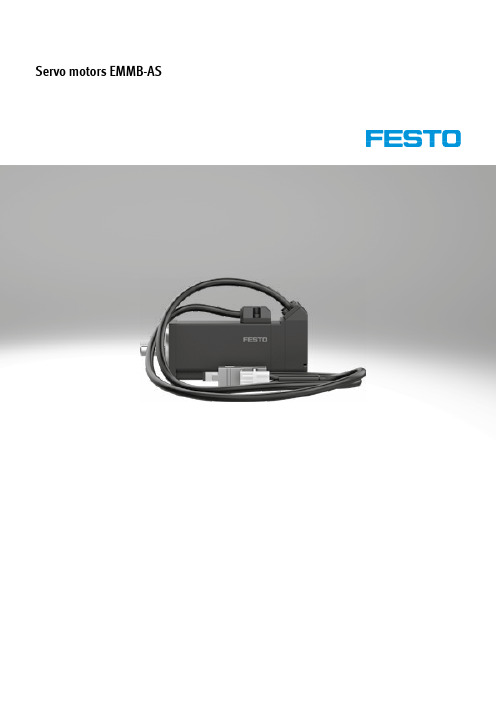
Servo motors EMMB-AS2d Internet: /catalogue/...Subject to change – 2022/11Servo motors EMMB-ASKey featuresEverything from a single source Motors EMMB-ASa Page 4• Brushless, permanently excited synchronous servo motors • Reliable, dynamic, precise• Digital absolute displacement en-coder with single turn, multi-turn optional• Optimised connection technology• Winding variants– For single-phase motor controller– Optimised for rotational speed • Holding brakeGear unit EMGA-EAS/-SASa Page 10• Low-backlash planetary gear • Gear ratio i = 3 and 5, available from stock• Life-time lubrication• Degree of protection: IP54• Other gear unit types, r atios, designs and versions on request Servo drive CMMT-ASa Internet: cmm• Universal servo drive for synchronous s ervo motors • Integrated EMC filters • Integrated brake chopper • Integrated braking resistor • Integrated safety functions• Position controller • Speed controller • Force controller•Range of control functions• Interfaces:– EtherCAT – PROFINETMotor, encoder and connecting cables NEBMa Page 11• Suitable for energy chains• Connection technology on motor side with degree of protection to IP20• Can be used in a wide temperature rangeAxial and parallel kits EAMMa Internet: eamm• Specific kits for all electromechani -cal axes from Festo• Each kit includes the relevant neces-sary coupling housing, couplings and motor flange as well as all screws• Optionally with degree of protection IP65Servo motors EMMB-AS Type codes3 2022/11 – Subject to change d Internet: /catalogue/...4d Internet: /catalogue/...Subject to change – 2022/11Servo motors EMMB-ASData sheetH- -NoteMotors and motor controllers from Festo have been specially designed to be used together. Trouble-free operation cannot be guaranteed in combination with third-party controllers.52022/11 – Subject to changed Internet: /catalogue/...Servo motors EMMB-ASData sheet1)The rotary shaft seal is included in the scope of delivery of the motor.2)For information about the area of use, see the EC declaration of conformity at: /sp d Certificates.If the devices are subject to usage restrictions in residential, commercial or light-industrial environments, further measures for the reduction of the emitted interference may be necessary.6d Internet: /catalogue/...Subject to change – 2022/11Servo motors EMMB-ASData sheetPin allocation – Motor side MotorBrakeEncoder72022/11 – Subject to changed Internet: /catalogue/...Servo motors EMMB-ASData sheetTorque M as a function of rotational speed n Flange size 40Flange size 60Performance class 01Performance class 02Flange size 60Flange size 80Performance class 04Performance class 07Peak torque Nominal torqueH- -NoteTypical motor characteristic curve with nominal voltage and optimal motor controller.Servo motors EMMB-ASData sheet8d Internet: /catalogue/...Subject to change – 2022/1192022/11 – Subject to changed Internet: /catalogue/...Servo motors EMMB-ASData sheetServo motors EMMB-ASData sheet10d Internet: /catalogue/...Subject to change – 2022/11112022/11 – Subject to changed Internet: /catalogue/...Servo motors EMMB-ASAccessories1)The battery is not included in the scope of deliveryServo motors EMMB-ASAccessories12d Internet: /catalogue/...Subject to change – 2022/11。
翻译马自达公司的速度感应四轮转向系统车辆工程外文翻译
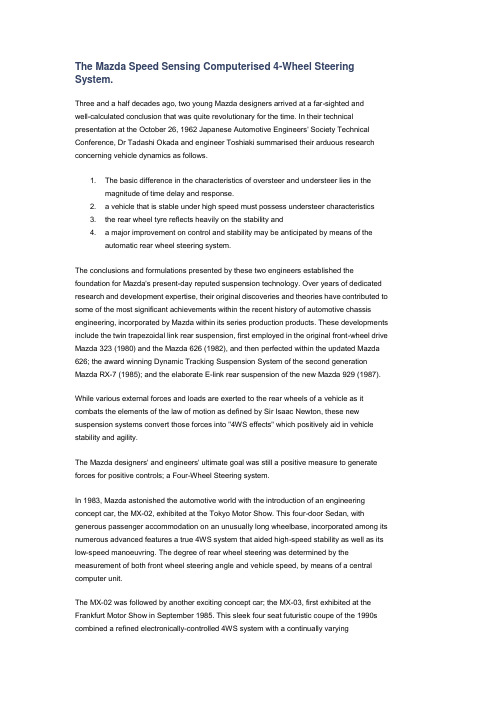
The Mazda Speed Sensing Computerised 4-Wheel Steering System.Three and a half decades ago, two young Mazda designers arrived at a far-sighted andwell-calculated conclusion that was quite revolutionary for the time. In their technical presentation at the October 26, 1962 Japanese Automotive Engineers' Society Technical Conference, Dr Tadashi Okada and engineer Toshiaki summarised their arduous research concerning vehicle dynamics as follows.1. The basic difference in the characteristics of oversteer and understeer lies in themagnitude of time delay and response.2. a vehicle that is stable under high speed must possess understeer characteristics3. the rear wheel tyre reflects heavily on the stability and4. a major improvement on control and stability may be anticipated by means of theautomatic rear wheel steering system.The conclusions and formulations presented by these two engineers established the foundation for Mazda's present-day reputed suspension technology. Over years of dedicated research and development expertise, their original discoveries and theories have contributed to some of the most significant achievements within the recent history of automotive chassis engineering, incorporated by Mazda within its series production products. These developments include the twin trapezoidal link rear suspension, first employed in the original front-wheel drive Mazda 323 (1980) and the Mazda 626 (1982), and then perfected within the updated Mazda 626; the award winning Dynamic Tracking Suspension System of the second generation Mazda RX-7 (1985); and the elaborate E-link rear suspension of the new Mazda 929 (1987).While various external forces and loads are exerted to the rear wheels of a vehicle as it combats the elements of the law of motion as defined by Sir Isaac Newton, these new suspension systems convert those forces into "4WS effects" which positively aid in vehicle stability and agility.The Mazda designers' and engineers' ultimate goal was still a positive measure to generate forces for positive controls; a Four-Wheel Steering system.In 1983, Mazda astonished the automotive world with the introduction of an engineering concept car, the MX-02, exhibited at the Tokyo Motor Show. This four-door Sedan, with generous passenger accommodation on an unusually long wheelbase, incorporated among its numerous advanced features a true 4WS system that aided high-speed stability as well as its low-speed manoeuvring. The degree of rear wheel steering was determined by the measurement of both front wheel steering angle and vehicle speed, by means of a central computer unit.The MX-02 was followed by another exciting concept car; the MX-03, first exhibited at the Frankfurt Motor Show in September 1985. This sleek four seat futuristic coupe of the 1990s combined a refined electronically-controlled 4WS system with a continually varyingtorque-split, four-wheel drive system and a powerful three-rotary engine.Mazda Electronically -Controlled Four-Wheel Steering System:A Beneficial TechnologyMazda's electronically-controlled, vehicle-speed-sensing Four-Wheel Steering System (4WS) steers the rear wheels in a direction and to a degree most suited to a corresponding vehicle speed range. The system is mechanically and hydraulically actuated, producing greatly enhanced stability, and within certain parameters, agility.The driver of a Mazda 4WS-equipped car derives five strategic benefits, over and above the conventional vehicle chassis.1. Superior cornering stability2. Improved steering responsiveness and precision3. High-speed straightline stability4. Notable improvement in rapid lane-changing manoeuvres5. Smaller turning radius and tight-space manoeuvrability at low vehicle speed rangeThe most outstanding advantage of the Mazda 4WS is that it contributes to a notable reduction in driver fatigue over high-speed and extended travelling. This is achieved by optimally:1. reducing the response delay to steering input and action and2. eliminating the vehicle's excessive reaction to steering inputIn essence, by providing the optimum solution to the phenomena researched by the two young Mazda engineers in the early sixties - by the method advocated by them - the 4WS system has emerged as a fully beneficial technology.Strategic ConstructionThe Mazda 4WS consists of a rack-and-pinion front steering system that is hydraulically assisted by a twin-tandem pump main power source, with an overall steering ratio of 14.2:1. The rear wheel steering mechanism is also hydraulically assisted by the main pump and electronically controlled - according to the front steering angle and vehicle speed. The rear steering shaft extends from the rack bar of the front steering gear assembly to the rear steering-phase control unit.The rear steering system is comprised of the input end of the rear steering shaft, vehicle speed sensors, a steering-phase control unit (determining direction and degree), a power cylinder and an output rod. A centering lock spring is incorporated, which locks the rear system in a neutral (straightforward) position in the event of hydraulic failure. Additionally, a solenoid valve that disengages hydraulic assist (thereby activating the centering lock spring) in case of anelectrical failure is included.The 4WS system varies the phase and ratio of the rear-wheel steering to the front wheels, according to the vehicle speed. It steers the rear wheels toward the opposite phase (direction) of the front wheel during speeds less than 35km/h (22mph) for a tighter turn and "neutralizes" them (to a straightforward direction, as in a conventional two-wheel steering principle) at35km/h (22mph). Above that speed, the system steers toward the same phase-direction as the front wheels, thereby generating an increased cornering force for stability. The maximun steering angle of the rear wheels extends 5 degrees to either left or right, a measurement that Mazda has determined to be optimally effective and natural to human sensitivity.Primary Components1. Vehicle speed sensors Interpret speedometer shelf revolutions and send signal to theelectronic computer unit. two sensors, one within the speedometer and the other atthe transmission output, are used to crosscheck the other for accuracy and failsafemeasures.2. Steering phase control unit* Conveys to the power steering cylinder booster valve thedirection and stroke of rear wheel steering by the combined movement of the control yoke angle and bevel gear revolutions.3. Electric stepper motor Performs altering of the yoke angle and bevel gear phasing4. Rear steering shaft Transmits front wheel steering angle by turning the small bevelgear in the steering phase control unit, which rotates the main bevel gear in theassembly.5. Control valve Feeds hydraulic pressure to the steering actuator, according to thephase and stroke required for appropriate rear wheel steering.6. Hydraulic power cylinder Operates the output rod by hydraulic pressure and steersthe rear wheels. It locks the rear wheels in a "neutral" (straightforward) position withthe centering lock spring, which is activated by a solenoid valve in case of failure toensure a normal 2WS function for the vehicle.7. Hydraulic pump. Provides hydraulic pressure to both the front and rear steeringsystems.Details of Steering Phase Control UnitThe steering phase control unit alters the direction and degree of rear wheel steering. It consists of a stepper motor that controls the rear steering ratio, a control yoke, a swing arm, a main bevel gear engaged to the rear steering shaft via a small bevel gear, and a control rod connected to the control valve. It operates:a. Opposite phase (direction) steering under 35km/h (22mph)1. Control Yoke is at an angle activated by the stepper motor2. Front wheels are steered to the right. The small bevel gear is rotated in direction X bythe rotation of the rear steering shaft. The small bevel gear, in turn, rotates the mainbevel gear.3. Rotation of the main bevel gear causes movement of the control rod toward thecontrol valve.4. Input rod of the control valve is pushed to the right, according to the degree of thecontrol rod's movement (determined by the disposition of the swing arm), which ispositioned to move in an upward direction, to the right. The rear wheels are thussteered to the left, in an opposite direction to the front wheels.5. As the angle of the control yoke is increased in direction A as vehicle speeddecreases, the rear-to-front steering ratio proportionately increases and the vehicle'ssteering lock tightens.b. Same phase (direction) over 35km/h (22mph)The operation of this phase is the reverse of the opposite phase one, because the control yoke is angled toward "positive" in this vehicle speed range, as illustrated. The phasing of the swing arm, yoke rod and bevel gear steers the rear wheels toward the right-the same direction as the front wheels.c. Neutral phase, at 35km/h (22mph) The control yoke's angle is horizontal (neutral). Thus, the input rod is not affected, even if the control rod is moved with the rotation of the bevel gear unit. As a result, the rear wheels are not steered in this mode.Power CylinderThe movement of the input rod of the control valve unit is transmitted to the power cylinder'sspool. The spool's displacement to the sleeve causes a pressure difference between the right and left side chambers in the hydraulic power cylinder. The pressure difference overcomes the output shaft load and initiates sleeve movement. The sleeve-power rod assembly is moved in the direction of the input rod by a proportionate degree. The output rod transmits steering action to the tie rod on either end of the rear wheel steering control-mechanism unit, thereby steering the rear wheels.Fail-Safe MeasuresThe system automatically counteracts possible causes of failure, both electronic and hydraulic. In either case, the centering lock spring housed in the steering system unit returns the output rods in the "neutral" straightforward position, essentially alternating the entire steering system to a conventional 2WS principle.Specifically, if a hydraulic defect should render a reduction in pressure level (by a movement malfunction or a broken driving belt), the rear wheel steering mechanism is automatically locked in a neutral position, activating a low-level warning light.In the event of an electrical failure, such would be detected by a self-diagnostic circuit integrated within the 4WS control unit, which stimulates a solenoid valve and then neutralizes hydraulic pressure and return lines, thereby alternating the system again to that of a 2WS principle. Henceforth, the warning light referencing the 4WS system within the main instrument display is activated, indicating a system failure.翻译马自达公司的速度感应四轮转向系统三十五年前,两个马自达设计师提出了一个远见的、有计算认为是相当革命性的结论。