车身料架路试要求
投料试车要求

投料试车要求在投料试车前严格检查和确认下列应具备的条件:4.1试车体系4.1.1各级开车指挥系统已成立并有效运转。
4.1.2各项管理制度、程序已制定并实施。
4.1.3生产运行管理人员到位,职责明确,调度人员熟悉试车/开车期向各装置(厂)之间,原料、燃料、产品及动力的联系和衔接,并能在紧急情况时指挥各装置(厂)人员进行应急处理。
4.2 HSE体系4.2.1HSE系统已建立并能够支持试车工作。
4.2.2与HSE相关的制度、程序和规范已制定完并开始执行。
4.2.3与HSE相关的设备、器具和项目已完成并投入正常运作。
4.2.4试车/开车已进行HSE评估,对评估中不满足要求的事项已采取措施或制定应急预案。
4.3 工程完工并已中交4.3.1工程中交根据工程进度可按单元或系统进行,要严格执行《石油[wiki]化工[/wiki]大、中型建设项目试车工作暂行规定》,实现高水平中交。
4.3.2工程质量达到国家标准,初评合格,“三查四定”的问题整改消缺完毕。
4.3.3遗留尾项已处理完善。
影响投料的设计变更项目已施工完。
4.3.4工程已办完中间交接手续,锅炉、压力容器已办理使用证。
4.3.4现场施工用临时设施已全部拆除,现场清洁、无杂物,现场满足HSE规定的试车要求。
设备、管道保温良好。
设备位号和管道介质名称,流向标志齐全。
各类照明投用、道路畅通。
4.4与投料试车相关的作业已按方案全部完成4.4.1各类调试作业如:吹扫、化学清洗、气密、干燥、置换、烘炉、三剂装填、计算机仪表联校、DCS控制、联锁、ESD 系统调校等已完成并经确认合格。
4.4.2设备处于完好备用状态。
4.4.3机电仪等管理制度已落实。
4.4.4装置分析准备工作已就绪,在线分析仪表、仪器经调试具备使用条件,工业空调已投用。
4.4.5岗位工器具已配齐。
4.4.6各装置联动试车已经完成。
4.5人员培训已完成4.5.1国内外同类装置培训、实习已结束。
4.5.2生产操作人员的技术培训(如基本知识和技能,操作规程、DCS、ESD、试车方案等)完毕。
GB18565-2015《道路运输车辆综合性能要求和检验方法》

三、标准变化及要点
安全锤及其放置位置
三、标准变化及要点
▲ 车身外观 --- 车身与驾驶室基本完好。客车车身和货车驾驶室不得有 超过3处的轻微开裂、锈蚀和明显变形,缺陷部位不影响安全性 和密封性。 --- 车身应周正,货车、客车及挂车车轴上方的车身两侧对 称部位的高度差不大于40mm。 --- 车身外部和内部不应有任何可能使人致伤的尖锐凸起物 --- 客车车身和货车驾驶室的表面涂装无明显破损,补漆颜 色与原色基本一致。 --- 货车货箱、车门、栏板和底板应无变形和破损,栏板锁 止机构作用可靠。 --- 驾驶室车窗玻璃不应张贴妨碍驾驶员视野的附加物及镜 面反光遮阳膜。
第二部分 在用道路运输车辆的技术要求
1、唯一性认定 (1)在用道路运输车辆的号牌号码、类型、品牌型号、燃
料类别、车身颜色、发动机号、底盘号或VIN 号、挂车架号、
中重型货车及挂车的外廓尺寸、货车车箱栏板高度应与行驶证 、机动车登记证、道路运输证记载的内容及其它相关资料一致 。其中,外廓尺寸的允许误差为±2%或±100mm,货车车箱栏 板高度的允许误差为±2%或±50mm。汽车列车的外廓尺寸不得
2、燃用柴油或汽油且最大总质量超过3500 kg的货车,其
燃料消耗量应符合JT 719的要求,试验方法执行JT 719的规 定。(参数核查) 3、轻型商用车辆和乘用车的燃料消耗量应符合GB 20997 和GB 19578的要求,试验方法执行该两项标准的有关规定 (工信部)。
三、标准变化及要点
(3) 制动性(工信部)
被检车辆 要求
唯一性认定 电子控制系统 外观及整备 查验
性能检验
二、标准主要内容
第四部分
结果的判定 与处理
车桥零部件台架试验检测项目及依据标准

EQC-193-1999汽车制动气室技术条件
EQCT-159-1999汽车制动气室台架试验方法
驱动桥
检测项目
依据标准
1、驱动桥总成静扭试验
2、驱动桥总成锥齿轮支承刚性试验
3、驱动桥总成齿轮疲劳试验
4、驱动桥总成噪声试验
5、减速器润滑性能试验
6、减速器齿轮接触区试验
7、桥壳刚度及静强度
8、桥壳寿命试验
5、总成应力测定及强度耐久试验
QC/T316-1999汽车行车制动器疲劳强度台架试验方法
QC/T479-1999货车、客车制动器台架试验方法
QC/T239-1997货车、客车制动器性能要求
制动气室
检测项目
依据标准
1、密封性试验
2、输出力特性试验
3、恢复性试验
4、耐久性试验
5、高温试验
6、低温试验
7、耐压试验
车桥零部件台架试验检测项目及依据标准
前轴
检测项目
依据标准
1、刚度测定
2、疲劳寿命试验
QC/T513-1999汽车前轴台架疲劳寿命试验方法
QC/T483-1999汽车前轴疲劳寿命限制
QC/T494-1999汽车前轴刚度试验方法
汽车制动器
检测项目
依据标准
1、效能ห้องสมุดไป่ตู้验
2、热衰退恢复试验
3、制动器噪声测定
4、制动衬片/衬块磨损试验
QC/T533-1999汽车驱动桥台架试验方法
QC/T534-1999汽车驱动桥台架试验评价指标
半轴
检测项目
依据标准
1、半轴静扭
2、半轴疲劳
QC/T293-1999汽车半轴台架试验方法
QC/T294-1999汽车半轴技术条件
车身密封性设计地的要求的要求规范

车身密封性设计规范前言本标准按照 GB/T 1.1-2009 给出的规则起草。
本规范的主要目的在于提高汽车的乘坐舒适性以及提高车身防腐蚀性要求。
本规范所代替规范的历次版本发布情况为:首次制定。
车身密封性设计规范1 范围本规范规定了乘用车车身密封性的设计要求。
本规范适用于乘用车密封性设计2 规范性引用文件下列文件对于本文件的应用是必不可少的。
凡是注日期的引用文件,仅所注日期的版本适用于本文件。
凡是不注日期的引用文件,其最新版本(包括所有的修改单)适用于本文件。
QC/T 646.1-2000 汽车粉尘密封性试验粉尘洞法QC/T 476-2007 客车防雨密封性限值及试验方法3 概述车身的密封性能是衡量汽车质量的重要指标之一,它直接影响车辆的乘坐舒适性、NVH、防腐性能、空调的效率以及燃油经济性。
此外,车身的密封性还能作为一个检测手段,用来衡量和控制车身的制造质量。
良好的车身密封性能不仅需要合理的车身结构和密封设计,而且还需要良好的工艺保证及生产过程能力控制。
焊装车间对焊接零件间隙的控制、密封胶工艺的正确使用,以及涂装车间PVC胶的涂抹工艺和总装车间的装配工艺都会对整车的密封性能产生巨大的影响。
因此整车的密封性能还是衡量一辆汽车的制造工艺水平、控制产品生产过程质量好坏的一个重要指标,并用来帮助发现生产过程中难以发现的一些隐形问题,以提升质量控制,这对于整车汽车厂具有重大的意义。
4 术语4.1 静态密封车身结构的各连接部分,设计要求对其间隙进行密封,而且在使用过程中这种密封关系是固定不动的,一般采用涂敷密封胶的方法来实现。
4.2 动态密封对车身上的门、窗、孔盖等活动部位之间的配合间隙进行密封。
靠密封条的压缩变形来实现,不仅能防止风、雨和尘埃的侵入,同时还能缓和车门关闭时测冲击和车辆行驶中的振动。
5 主要设计内容5.1 防止(雨)水、尘土、污染气体侵入室内的密封性设计。
5.2 防止振动、噪声、热量侵入室内的密封性设计。
营运车辆技术等级的评定项目和技术要求
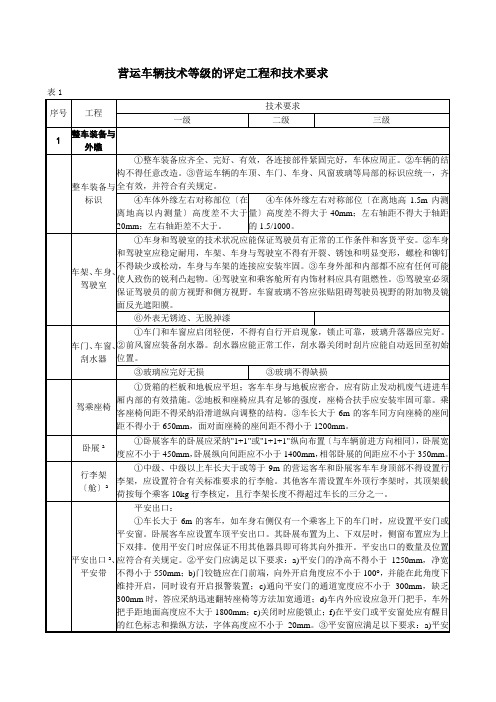
①轮胎螺母和半轴螺母应完整洁全,并应按规定力矩紧固。②中心螺栓和U形螺栓应紧固。
灯光数量、光色、位置
①所有前照灯的近光都不得眩目。②汽车和挂车的外部照明和信号装置的数量、位置、光色、最小几何可见角度等应符合GB4785的有关规定。③全挂车应在挂车前部的左右各装一只红色标志灯,其高度应比全挂车的前栏板高出300mm~400mm,距车箱外侧应小于150mm。④车辆应装置后回复反射器,车长大于10m的车辆应安装侧回复反射器,汽车列车应装有侧回复反射器。回复反射器应能保证夜间在其正面前方150m处用汽车前照灯照耀时,在照耀位置就能确认其反射光。⑤装有前照灯的车辆应有远近光变换装置,同时当远光变为近光时,所有的远光应同时熄灭。同一辆车内的前照灯不答应左、右的远、近灯光交叉开亮。⑥车辆的前位灯、后位灯、示廓灯、挂车标志灯、牌照灯和仪表灯应能同时启闭,当前照灯关闭和发动机熄火时仍能点亮。⑦空载高为3m以上的车辆应安装示廓灯。⑧车辆应安装一只或两只后雾灯,只有当远光灯、近光灯或前雾灯翻开时,后雾灯才能翻开。后雾灯能够独立于任何其他灯而关闭。后雾灯能够连续工作,直至位置灯关闭时为止,之后一直处于关闭状态,直至再次翻开。车辆〔挂车除外〕能够选装前雾灯。⑨车辆应装有危险报警闪光灯,其操纵装置应不受电源总开关的操纵。危险报警闪光灯和转向信号灯的闪光频率为1.5Hz±0.5Hz;起动时刻应不大于1.5s。⑩汽车及挂车均应安装侧转向灯,假设汽车前转向灯在侧面可见时那么视为满足要求。铰接式车辆每一刚性单元必须装有至少一对侧转向灯。
汽车整备质量M/kg
双轴驱动车辆的滑行距离/m
单轴驱动车辆的滑行距离/m
M<1000
≥104
≥130
1000≤M≤4000
≥120
新能源汽车台架试验相关标准-概述说明以及解释
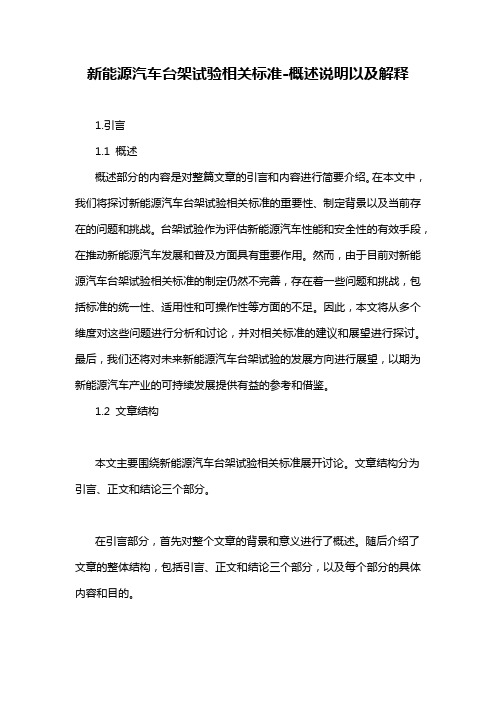
新能源汽车台架试验相关标准-概述说明以及解释1.引言1.1 概述概述部分的内容是对整篇文章的引言和内容进行简要介绍。
在本文中,我们将探讨新能源汽车台架试验相关标准的重要性、制定背景以及当前存在的问题和挑战。
台架试验作为评估新能源汽车性能和安全性的有效手段,在推动新能源汽车发展和普及方面具有重要作用。
然而,由于目前对新能源汽车台架试验相关标准的制定仍然不完善,存在着一些问题和挑战,包括标准的统一性、适用性和可操作性等方面的不足。
因此,本文将从多个维度对这些问题进行分析和讨论,并对相关标准的建议和展望进行探讨。
最后,我们还将对未来新能源汽车台架试验的发展方向进行展望,以期为新能源汽车产业的可持续发展提供有益的参考和借鉴。
1.2 文章结构本文主要围绕新能源汽车台架试验相关标准展开讨论。
文章结构分为引言、正文和结论三个部分。
在引言部分,首先对整个文章的背景和意义进行了概述。
随后介绍了文章的整体结构,包括引言、正文和结论三个部分,以及每个部分的具体内容和目的。
接下来是正文部分,主要包括台架试验的重要性、相关标准的制定背景以及当前存在的问题和挑战三个方面的内容。
在台架试验的重要性方面,我们将探讨为何台架试验对新能源汽车的发展至关重要,以及台架试验在车辆性能、能耗、安全性等方面的作用和意义。
在相关标准的制定背景方面,我们将介绍国内外关于新能源汽车台架试验相关标准的发展历程和现状。
最后,在当前存在的问题和挑战方面,我们将分析当前新能源汽车台架试验所面临的问题,如试验方法的不统一、标准的缺失等,并提出解决方案和对策。
最后是结论部分,我们将对整个文章进行总结,归纳出台架试验的作用和意义,以及对相关标准的建议和展望。
在对相关标准的建议和展望方面,我们将提出如何完善和统一台架试验相关标准的建议,并展望未来可能的发展趋势和方向。
通过以上的结构安排,本文将全面深入地探讨新能源汽车台架试验相关标准的重要性、背景、问题和挑战,并提出相应的建议和展望,为新能源汽车台架试验相关标准的制定和发展提供有益的参考和指导。
整车试验相关标准

整车试验相关标准一、试验准备1.1 试验计划和方案:制定详细的试验计划和方案,包括试验目的、试验项目、试验流程、试验条件、数据处理和分析等内容。
1.2 试验设备和工具:确保试验设备和工具的精度和可靠性,以满足试验要求。
1.3 试验场地:选择符合试验要求的场地,并进行必要的清理和维护,确保试验顺利进行。
1.4 试验人员:安排具备相应资质的试验人员,明确人员职责和操作规范。
二、动力性能2.1 加速性能:通过加速试验测试车辆的加速性能,包括0-100km/h、0-50km/h等不同时速的加速时间。
2.2 爬坡性能:测试车辆的爬坡性能,包括最大爬坡度和爬坡速度等指标。
2.3 最高车速:测试车辆在良好路面条件下的最高车速。
三、经济性能3.1 燃油经济性:通过燃油消耗试验测试车辆在不同行驶条件下的燃油经济性。
3.2 润滑油经济性:测试车辆在长期使用过程中的润滑油消耗情况。
四、制动性能4.1 制动力:测试车辆在不同行驶条件下的制动力,包括制动距离和制动减速度等指标。
4.2 制动稳定性:测试车辆在制动过程中的稳定性和操控性。
五、操作稳定性5.1 行驶稳定性:测试车辆在不同行驶条件下的行驶稳定性,包括侧倾、摆动等。
5.2 操控稳定性:测试车辆在操控过程中的稳定性和反应速度。
六、噪声和排放性能6.1 噪声测试:测试车辆在不同行驶条件下的车内和车外噪声。
6.2 排放测试:测试车辆的排放性能,包括CO、HC、NOx等有害气体排放。
七、碰撞安全性能7.1 碰撞测试:进行不同角度的碰撞测试,评估车辆在碰撞时的安全性能。
7.2 安全防护装置:测试车辆的安全防护装置,如安全带、气囊等的工作性能。
化工生产中投料试车应具备的条件、准备工作及需检查确认的内容

化工生产投料试车前的准备工作一、投料试车应具备的条件化工投料试车前,建设(生产)单位必须组织进行严格细致的试车条件检查。
试车应坚持高标准、严要求,精心组织,严格做到“四不开车”,即:条件不具备不开车,程序不清楚不开车,指挥不在场不开车,出现问题不解决不开车。
未做好前期准备工作,化工投料试车不得进行。
1、所有装置及配套工程,按设计全部施工完毕,经过逐台设备、逐条管线按序号检查核对材质、壁厚、法兰、垫片、螺栓、各种阀门、管件、阀门方向及位置、监测点取样点、操作通道等,工程质量符合要求。
2、施工记录资料齐全准确。
3、全部工艺管道和设备按设计的标准进行试压,完全达到设计试压的要求。
4、设备、管道均已经过气密试验,且保压6 小时无泄漏,确认合格。
5、所的转动设备按规定经过详细检查,单体试车和联动试车满足要求,电机电流、温升正常。
6、原料及分析设施、标准气制备等已备用。
7、各种需要在投料前进行的准备工作,均已完成。
8、自控仪表调试全部完成,报警及联锁的整定值经静态调试已准确好用。
9、所有电气设备的热继电调整和绝缘试验已经完成,具备正常投运条件。
10、公用工程的水、电、汽、仪表空气等已能按设计值保证供应。
11、项目区所有的安全消防设施,包括避雷及静电设施、防毒、事故急救设施、消防设施、可燃气体监测仪、火灾报警系统等都已安装并检验完毕。
12、储运系统经检验已无问题。
13、设备、管线的保温和防腐工作已经完成,并要对设备、管道、阀门、电气、仪表等均用汉字或代号将位号、名称、介质、流向标记完毕。
14、生产指挥系统的通讯,装置内部的通讯设施已能供正常使用。
15、机械、电气、仪表设施都已完工并投入使用,配备了检修队伍。
16、工艺规程、安全规程、分析检验规程、设备维修规程、岗位操作法及试车方案等技术资料已经齐备,并批准颁发。
各项安全操作规程已按要求上墙。
17、试车指挥组织已经建立,操作人员已配备,职责分明,且都已经过技术安全培训并考核合格。
整车厂路试跑道工序质量控制
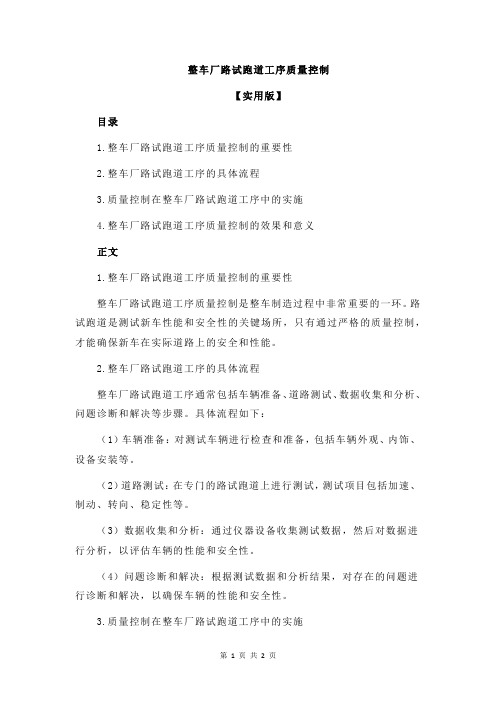
整车厂路试跑道工序质量控制【实用版】目录1.整车厂路试跑道工序质量控制的重要性2.整车厂路试跑道工序的具体流程3.质量控制在整车厂路试跑道工序中的实施4.整车厂路试跑道工序质量控制的效果和意义正文1.整车厂路试跑道工序质量控制的重要性整车厂路试跑道工序质量控制是整车制造过程中非常重要的一环。
路试跑道是测试新车性能和安全性的关键场所,只有通过严格的质量控制,才能确保新车在实际道路上的安全和性能。
2.整车厂路试跑道工序的具体流程整车厂路试跑道工序通常包括车辆准备、道路测试、数据收集和分析、问题诊断和解决等步骤。
具体流程如下:(1)车辆准备:对测试车辆进行检查和准备,包括车辆外观、内饰、设备安装等。
(2)道路测试:在专门的路试跑道上进行测试,测试项目包括加速、制动、转向、稳定性等。
(3)数据收集和分析:通过仪器设备收集测试数据,然后对数据进行分析,以评估车辆的性能和安全性。
(4)问题诊断和解决:根据测试数据和分析结果,对存在的问题进行诊断和解决,以确保车辆的性能和安全性。
3.质量控制在整车厂路试跑道工序中的实施在整车厂路试跑道工序中,质量控制的实施主要通过以下几个方面进行:(1)制定严格的质量标准:根据国家和行业的相关标准,制定整车厂路试跑道工序的质量标准。
(2)设立专门的质量控制部门:负责监督和检查整车厂路试跑道工序的质量,确保质量标准的实施。
(3)培训质量控制人员:对质量控制人员进行专业培训,提高他们的质量意识和能力。
(4)采用先进的质量控制工具和技术:运用现代质量管理方法和技术,提高整车厂路试跑道工序的质量控制水平。
4.整车厂路试跑道工序质量控制的效果和意义整车厂路试跑道工序质量控制对于提高整车性能和安全性具有重要意义。
通过严格的质量控制,可以及时发现和解决测试车辆存在的问题,确保新车在实际道路上的安全和性能。
路试作业安全操作规程范文
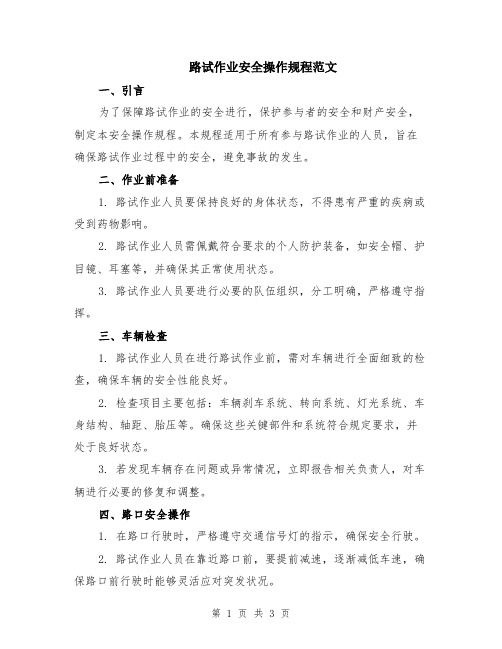
路试作业安全操作规程范文一、引言为了保障路试作业的安全进行,保护参与者的安全和财产安全,制定本安全操作规程。
本规程适用于所有参与路试作业的人员,旨在确保路试作业过程中的安全,避免事故的发生。
二、作业前准备1. 路试作业人员要保持良好的身体状态,不得患有严重的疾病或受到药物影响。
2. 路试作业人员需佩戴符合要求的个人防护装备,如安全帽、护目镜、耳塞等,并确保其正常使用状态。
3. 路试作业人员要进行必要的队伍组织,分工明确,严格遵守指挥。
三、车辆检查1. 路试作业人员在进行路试作业前,需对车辆进行全面细致的检查,确保车辆的安全性能良好。
2. 检查项目主要包括:车辆刹车系统、转向系统、灯光系统、车身结构、轴距、胎压等。
确保这些关键部件和系统符合规定要求,并处于良好状态。
3. 若发现车辆存在问题或异常情况,立即报告相关负责人,对车辆进行必要的修复和调整。
四、路口安全操作1. 在路口行驶时,严格遵守交通信号灯的指示,确保安全行驶。
2. 路试作业人员在靠近路口前,要提前减速,逐渐减低车速,确保路口前行驶时能够灵活应对突发状况。
3. 路试作业人员要观察路口情况,确保车辆通行安全,不得急转弯、变道,以免造成事故。
五、超车安全操作1. 路试作业人员在进行超车操作时,需提前观察并确认超车线路的安全性。
2. 超车前,必须先使用转向灯,并观察车后是否有其他车辆要超越自己。
3. 路试作业人员超车时要保持适当的车速和距离,保证超车过程的安全性。
六、雨天作业注意事项1. 在雨天作业时,路试作业人员要留意路面湿滑,提前减速,确保车辆的稳定性。
2. 雨天能见度较差,路试作业人员要保持更长的安全行车距离,预防追尾事故的发生。
3. 出现大雨天气时,路试作业人员要根据路面情况选择合适的速度,避免发生打滑或控制不住的情况。
七、作业终了及清理1. 路试作业人员在作业结束后,要及时停车并按规定位置进行停放。
2. 路试作业人员要对车辆进行清理,清理驾驶室内的垃圾,并做好车辆的日常维护工作。
汽车下料要注意什么

汽车下料要注意什么汽车下料是汽车制造过程中的一个重要环节,主要是通过将原材料按照特定的尺寸和形状进行切割、打孔、冲压等加工,以便制造出具有特定功能和外观的汽车零部件。
下料质量对汽车的性能、耐用性和外观质量有着重要的影响,因此在汽车下料过程中需要特别注意以下几个方面。
首先,需要注意下料的精度。
下料精度直接关系到零部件的尺寸精度和加工质量。
在下料过程中,要严格控制机床的工作精度,合理选择刀具和下料工艺,以确保下料精度符合设计要求。
此外,还需要加强对设备的维护保养,及时更换磨损严重的刀具,避免因设备磨损而影响下料精度。
其次,需要注意下料的材料选择和处理。
汽车零部件的材料种类繁多,常见的有钢材、铝材、塑料等。
在下料之前,需要根据零部件的性能要求和使用环境,合理选择材料。
不同材料有不同的下料工艺和要求,需要根据实际情况进行加工处理。
例如,对于刚性较强的钢材,可以采用冲压下料的方式;对于柔软的塑料材料,可以采用切割或激光下料的方式。
第三,需要注意下料的安全性。
下料过程中往往涉及到机械设备的操作和刀具的使用,存在一定的安全风险。
因此,在进行下料之前,需要对设备进行全面检查,确保设备的正常运行和操作的安全性。
同时,下料操作人员需要佩戴合适的防护用品,如防护手套、安全帽、防护眼镜等,以防止意外伤害的发生。
第四,需要注意下料的工艺控制。
下料工艺对加工质量有着重要的影响,包括下料顺序、下料速度、下料深度等参数的控制。
在下料过程中,需要根据零部件的形状和材料的性质,采用合适的工艺参数进行操作,以保证下料的质量和效率。
此外,在下料过程中,还需要严格执行工艺规程和操作规程,确保下料工艺的稳定性和可控性。
第五,需要注意下料的环境保护。
下料过程中常常伴随着废料产生,如废铁屑、废塑料等,这些废料对环境造成一定的污染。
因此,在进行下料之前,需要制定合理的废料处理方案,采取有效的措施进行收集、分类和处理。
同时,还需要合理利用资源,降低废料的产生和浪费,以实现环境保护和可持续发展的目标。
车辆底体架预检工艺

车辆底体架预检工艺
1 目的
保证货车体底架不发生漏检漏修。
2 范围
各型货车。
3 工装仪器
点检锤,手电筒,钢直尺,钢卷尺,内外卡尺,拉线及线锤,长木平尺,金属测厚仪等。
4作业流程
5 质量要求
5.1 作业准备
开工前应准备好所用工装仪器,确认作用良好、熟悉安全操作规程。
5.2 工作者预检
工作者对入库车辆的底体架进行全面自检、自修,对符合技术要求的复检配件(上心盘、上旁承、前从板座、后从板座、牵引梁磨耗板、冲击座)要画良好“○”标记。
对不符合技术要求的部位及问题,要画上加修标识,按技术要求进行加修。
5.3 检查员复检
检查员对上心盘、上旁承、前从板座、后从板座、牵引梁磨耗板、冲击座进行100%的复检,对复检良好的上述配件必须在“○”标记
上加画一竖,形成一个完整的良好“φ”标记,工作者方可进行下道工序,其他部位要加强中间检查,对不符合技术要求的部位及问题,要画上加修标识,便于工作者按技术要求进行加修。
5.4 质量要求
底体架预检(复检)后应符合《米轨铁路货车检修规程》有关质量要求。
6 质量记录
底体架预检(复检)后,工作者及检查员均应把各自发现的故障填写在《货车检修记录单》(车统—22B)上,相关人员并签章。
整车下线路试规范

新车下线路试规范1.目的为了加强公司路试车辆规范管理,明确车辆路试的流程,确保路试过程中记录准确有效,特制定本规范。
2.范围适用于本公司各种新能源车辆下线路试车辆。
3.术语和定义3.1电动汽车试验质量包括整车整备质量和试验所需附加质量的和。
3.2最高车速电动汽车能够往返各持续行驶1km 以上距离的最高车速的平均值。
3.330分钟最高车速电动汽车能够持续行驶30min以上的最高平均车速。
3.4坡道起步能力电动汽车在坡道上能够起到且在1min 内向上行驶至少10m 的最大坡度。
3.5预热路试车辆应以30分钟最高车速的80% 速度行驶5000m ,使电机及传动系统预热。
4.路试规程4.1路试前车辆检查路试人员按照常规检查记录表(附件一)中检查项目,逐项检查并记录车辆的状态。
4.2路试场地及条件一般应在干燥的路面,路面应坚硬,平整,整洁并有良好的附着系数。
以场区内的试车跑道及周边的区域道路为路试主要区域。
4.3动力电池的初次充电下线路试车辆预热后以30分钟最高车速70%±5%的稳定车速行驶,当车辆速度不能达到30分钟最高车速的65%时停止行驶。
按规定的充电程序为动力电池充电,直至动力电池达到全充满,并记录充电期间来自电网的能量Wh表示。
4.4动力电池放电4.3.1 预热要求行驶后,在场区20%的坡道,测试车辆的坡道起步能力,是否通过并记录。
4.3.2 最高车速测试,选择直线段长度至少1000m的道路,进行最高车速的测试,并记录最高车速。
4.3.3 其余路试按等速法进行a)适用M1,N1类车型按(60±2)km/h 的速度行驶,试验过程中,允许停车两次,每次停车不允许超过2min,当车辆行驶速度低于54 km/h,要求停止路试。
记录路试过程中车辆的行驶距离和所用的时间(道路试验记录表附件二中)。
b) 适用于M1,N1类以外按(40±2)km/h的速度行驶,试验过程中,允许停车两次,每次停车不允许超过2min,当车辆行驶速度低于36 km/h,要求停止路试。
白车身强度台架试验方法及疲劳寿命的研究

1
重庆大学硕士学位论文
1.2 车身强度台架试验方法研究现状
车身强度台架试验方法一般由试验条件(主要是载荷) 、夹具的设计、台架 的安装、试验数据采集和处理、疲劳寿命估算等过程组成。显然要研究试验方法 就必须从这几个方面入手, 找到它们各自的规律和相互的规律才能制定出合理科 学的试验方法。 汽车在实际行驶过程中车身受到的载荷非常复杂, 其主要包括由地面不平度 引起的垂直方向的载荷、汽车转向或侧向风引起的侧向载荷和由汽车加速、制动 引起的纵向方向载荷。 台架强度试验的设计原则是能够模拟整车在实际行驶寿命中所受的外力, 但 由于汽车在实际使用过程中的受力情况千差万别, 国外企业的一般做法是长期跟 踪大量样本车的实际行驶状况和故障状况, 根据统计学理论建立道路谱输入和车 身疲劳之间的数学模型,并利用该模型来设计台架强度试验。这种方式能够较为 准确的考核车身等关键部件的疲劳寿命,但是时间长、耗费大,目前在国内仅有 少数企业或科研单位进行过一些探索,还未进入成熟应用阶段。 台架强度试验通常采用等幅循环和道路模拟两种方法。 等幅循环试验方法利 用理论计算,将车身在行驶过程中所受外力简化、分解为各个方向的交变载荷, 即频率恒定、幅值相等的正弦波载荷,然后将车身通过夹具进行约束,在悬架处 施加载荷。该方法的特点是: 将车身所受到的复杂外力简化为等幅交变载荷,在试验条件上容易实现; 对设备要求较低,投入少,无须麻烦的数据处理; 简单易用、对技术人员的要求低; 由于分解了各个方向的受力,宜于了解故障模式与受力方向之间的关系,但 试验时间较长; 难以完全模拟整车所受外力, 且受试验装夹条件的限制, 试验结果不够准确, 难以定量评价与汽车实际使用寿命之间的关系。 道路模拟试验指的是在台架上快速实现车身的道路载荷历程, 并提供车身当 量使用里程作为车身疲劳性能参数, 该方法在欧美汽车工业发达国家已经得到应 用,并且收到非常好的效果,该方法是国内车身强度台架试验的发展方向。 载荷的大小主要考虑的问题是载荷的强化问题, 因为车身疲劳试验往往周期 很长,在可接受的误差范围内,尽可能的减少试验的周期。而目前常用的载荷强 化方式包括:1)增大试验载荷的频率,增大试验的试验频率对试验结果一般不 产生影响,这样可以部分缩短试验时间,但是该方法仅适用于简单的疲劳试验。 2)高频小载荷的折算或忽略,高频小载荷一般占用了大部分试验时间,但它们 却产生小部分的疲劳损伤,在相关疲劳性能数据已知的情况下,可以按当量损伤
吉利料架和台车技术要求

2.7 SPS台车1)数量需求:内饰一60台、内饰二40台;(各线实际数量根据现场需求确定)2)结构要求:四种线体台车底座要求为统一样式,上部根据不同线体零件属性和挂靠方式需要做个性化设计,乙方需提供多套设计方案供甲方选择;SPS台车需结构稳定,能承受较大的载荷并具有较轻的自重;内饰线台车底部有两个万向轮、两个定向轮;SPS台车具体样式在图纸会签时确定。
3)材料要求:底部主梁及框架采用40*40*3mm方钢(四横一纵),喷涂采用喷塑的处理工艺,颜色要求RAL7035,底部横梁喷涂台车编码,编码规则会签时提供;上部采用二代精益管连接成主框架,横向和纵向层间隔板采用硬质PP材料,部分零件防护选用绒布地毯或EVA、EPE等材料;4)焊接要求:图纸上未明示焊接方法时,可用手工电弧焊、二氧化碳电弧焊气体保护焊;图纸中未注的焊缝,均采用连续贴角焊缝,焊缝高度为两连接件中较小厚度的0.8;所有连续焊必须内外侧(管材的内孔无法焊接的除外)连续焊接,接口要平齐;图样中未标明的断续焊接的长度、间距按下表规定;表(单位:毫米)钢板厚度焊缝长度焊缝间距≥1~2 15~20 100~120>2~5 20~30 120~160图样中未规定焊接接头的形式与尺寸,按《碳钢、低合金钢焊缝坡口的基本形式图样中未对焊条做明确规定时,允许按GB/T5117、GB983选用焊条,例如:E4315、F4303。
也允许按GB/T8110、GB4242选用焊条,焊条焊丝应有合格证明;焊前应做好焊接件的前处理工作,喷塑前材料须酸洗磷化处理;焊后应清理焊缝,焊接处表面不允许有溶液、焊瘤、气孔、焊渣、飞溅物等。
焊缝打磨要表面平整圆滑,不要磨平;焊缝不允许有焊瘤、裂纹、焊穿、漏焊等缺陷,其它焊接质量要求和缺陷分级按GB/T12469Ⅲ级质量等级的规定。
2.8流利货架基本要求2.8.1规格:W2000㎜(内)×D1500㎜×H1800㎜,三层流利条,每层配不少于8条流利条,单层承重不小于500㎏,带金属货道分隔。
车辆路试特殊路面试车道

特殊路面特殊试车路面包括扭曲路、鹅卵石路、搓板路、石块路以及普通水泥路面。
一、用途1.1进行车辆的内部噪声和振动状况检查。
1.2进行车辆的车身和车架扭曲状况检查。
1.3进行车辆的转向系统的路感情况检查。
1.4进行车辆悬挂的工作状况检查。
二、设计要求2.1横坡不大于1%,纵坡不大于2‰。
2.2路面:试验路段除特殊路面和特别说明外为水泥混凝土。
2.3试验路段各种路面的长、宽以及地理位置见图1,其他各种路面的参数和具体要求如下:2.3.1扭曲路全长65m,横断面结构及布局见图2。
材料为水泥混凝土。
图2注:扭曲路凸块纵向过渡圆角R为0.5m。
2.3.2鹅卵石路全长65m,横断面结构及布局见图3。
卵石粒径:经线方向300~400mm,纬线方向250~300mm。
石质为花岗岩、玄武岩等硬度石料,抗压强度不小于1200kg/cm²,卵石随机安放于路床上的水泥砂浆中,安放卵石时各卵石露出路床上表面1/3,2/3部分在水泥砂浆中,但不少于40mm且不大于110mm;卵石之间的缝隙为250~300mm。
图32.3.3搓板路全长65m,横断面结构及布局见图4、5。
材料为水泥混凝土。
图4搓板路A-A剖视图搓板路俯视图图52.3.4石块路全长65m,横断面结构及布局见图6。
石料为花岗岩,抗压强度不小于1200kg/cm²。
石块间隙为25±5mm,用水泥砂浆填充。
石块规格为:宽120~130mm,长225~255mm,高160mm。
石块行距150mm,列距240mm。
图6三、辅助设施3.1在每种特殊路面旁设一险速警告牌。
3.2考虑排水系统、隔离防护带等。
资料仅供参考!!!。
化工装置安全试车化工投料试车应具备的条件

化工装置安全试车化工投料试车应具备的条件化工投料试车必须高标准、严要求,按照批准的试车方案和程序进行。
在化工投料试车前应严格检查和确认是否具备以下条件:一、单机试车及工程中间交接完成(一)工程质量初评合格。
(二)“三查四定”的问题整改消缺完毕,遗留尾项已处理。
(三)影响投料的设计变更项目已施工完毕。
(四)单机试车合格。
(五)工程已办理中间交接手续。
(六)化工装置区内施工用临时设施已全部拆除;现场无杂物、无障碍。
(七)设备位号和管道介质名称、流向标志齐全。
(八)系统吹扫、清洗完成,气密试验合格。
二、联动试车已完成(一)干燥、置换、三剂装填、计算机仪表联校等已完成并经确认。
(二)设备处于完好备用状态。
(三)在线分析仪表、仪器经调试具备使用条件、工业空调已投用。
(四)化工装置的检测、控制、联锁、报警系统调校完毕,防雷防静电设施准确可靠。
(五)现场消防、气防等器材及岗位工器具已配齐。
(六)联动试车暴露出的问题已经整改完毕。
三、人员培训已完成(一)国内外同类装置培训、实习已结束。
(二)已进行岗位练兵、模拟练兵、防事故练兵、达到“三懂六会”(三懂:懂原理、懂结构、懂方案规程;六会:会识图、会操作、会维护、会计算、会联系、会排除故障),提高“六种能力”(思维能力,操作、作业能力,协调组织能力,防事故能力,自我保护救护能力,自我约束能力)。
(三)各工种人员和特种作业人员经考试合格,已取得上岗证。
(四)已汇编国内外同类装置事故案例,并组织学习。
对本装置试车以来的事故和事故苗头本着“四不放过”(事故原因未查清不放过,责任人员未处理不放过,整改措施未落实不放过,有关人员未受到教育不放过)的原则已进行分析总结,汲取教训。
四、各项生产管理制度已建立和落实(一)岗位分工明确,班组生产作业制度已建立。
(二)各级试车指挥系统已落实,指挥人员已值班上岗,并建立例会制度。
(三)各级生产调度制度已建立。
(四)岗位责任、巡回检查、交接班等相关制度已建立。
- 1、下载文档前请自行甄别文档内容的完整性,平台不提供额外的编辑、内容补充、找答案等附加服务。
- 2、"仅部分预览"的文档,不可在线预览部分如存在完整性等问题,可反馈申请退款(可完整预览的文档不适用该条件!)。
- 3、如文档侵犯您的权益,请联系客服反馈,我们会尽快为您处理(人工客服工作时间:9:00-18:30)。
车身料架包装测试要求
一、包装测试(装满零件)
1、路况试验:
对普通路面、高速路面进行行驶试验。
2、刹车试验(2次以上):
卡车中前部放置其它容器或空容器,试验包装放在中后部,卡车在大于60 km/h的时速下紧急刹车,检验包装内汽车零部件的状态。
3、颠簸试验(1H以上):
卡车中前部放置其它容器或空容器,试验包装放在中后部。
路面有大于300×300×100(高或深)mm的突起或凹陷,间隔4m,连续1km以上。
卡车以30km/h~60km/h的时速通过,连续颠簸1h,停车容器内汽车零部件的状态。
4、路程试验(2次以上):
根据包装使用时运输距离的长短,选择大于1.5倍实际距运输距离做路程试验,要求在2级及以下公路上。
5、测试标准:
按照试验规范试验后,将零部件从容器内取出检测,不允许零部件有瘪痕、划伤、变形等缺陷,相关性能符合图纸等规格要求,零件精度变化(或变形量)不得超过图纸公差要求,以证明对零部件的保护是有效的。