选煤厂创建节约型企业提升洗煤经济运行质量与效益的
落实精益化管理,提升煤炭企业经济效益

落实精益化管理,提升煤炭企业经济效益近年来,随着我国经济发展的快速推进,煤炭产业作为能源行业的核心,一直扮演着重要的角色。
然而,在煤炭产业发展中,存在着生产效率低下、资源浪费、环境污染等问题,这些问题不仅制约了煤炭企业的发展,也给环境造成了巨大的压力。
如何落实精益化管理,提升煤炭企业经济效益,成为煤炭企业需要积极探讨的课题。
一、什么是精益化管理?精益化管理,即精益生产,是日本生产方式的一种。
它是一种综合的生产流程管理模式,强调样本生产、持续改进、精益流程,从而实现生产流程标准化、最小的库存、最快的生产流程和最高的生产效率。
1、提高生产效率煤炭企业通常要面对诸如采煤、运输、加工等各个环节,这些环节影响了煤炭企业的整体生产效率。
通过优化和精益化生产流程,可以降低生产成本,提高生产效率,保证煤炭生产的正常运转。
2、降低资源浪费煤炭企业使用的资源大多是非可再生资源,如煤炭的开采、运输、加工等过程中耗费了大量的能源与水资源。
通过精益化管理的理念,可以避免资源的浪费,提高能源的利用效率,减少环境污染。
3、提高产品质量通过精益化管理的方式,优化生产流程,集中力量不断改进生产流程,能够有效提高产品的质量。
奠定高品质的优势,可以让企业在市场上占据更大的市场份额。
4、增强企业竞争力落实精益化管理可以有效降低企业成本,提升产品质量、生产效率,从而提高企业的竞争力。
可以使企业在市场竞争中稳扎稳打,受益于更大的回报。
1、确立生产流程标准化通过标准化流程,可以让生产过程各环节更加流畅,有效避免因工人操作方式不同而导致的生产效率下降。
标准化的工艺流程,能够为企业奠定一个高效生产的基础。
2、及时分析制定改善方案随着生产流程的标准化实施,公司的运营状况和问题也将逐渐浮现出来,需要通过数据分析来识别问题点,制定针对性的改善方案。
3、建立低库存管理制度传统生产方式中常常存在着库存积压的情况,不仅占用了大量的仓库资源,也会增加企业的资金压力。
降低选煤成本提高洗选效率的措施

降低选煤成本提高洗选效率的措施下载提示:该文档是本店铺精心编制而成的,希望大家下载后,能够帮助大家解决实际问题。
文档下载后可定制修改,请根据实际需要进行调整和使用,谢谢!本店铺为大家提供各种类型的实用资料,如教育随笔、日记赏析、句子摘抄、古诗大全、经典美文、话题作文、工作总结、词语解析、文案摘录、其他资料等等,想了解不同资料格式和写法,敬请关注!Download tips: This document is carefully compiled by this editor. I hope that after you download it, it can help you solve practical problems. The document can be customized and modified after downloading, please adjust and use it according to actual needs, thank you! In addition, this shop provides you with various types of practical materials, such as educational essays, diary appreciation, sentence excerpts, ancient poems, classic articles, topic composition, work summary, word parsing, copy excerpts, other materials and so on, want to know different data formats and writing methods, please pay attention!降低选煤成本提高洗选效率的措施引言随着煤炭产业的不断发展,选煤工艺已成为煤炭生产中至关重要的环节。
加强洗煤厂生产经营管理提高经济效益

高选煤厂 的自主创新能力 。在新形势下 ,提高选 决定着选煤厂产供销流程体 系和选煤厂产业的
煤厂的核心竞争力 ,应高度重视管理在提高选煤 发展方 向,技术创新成为选煤厂赢得市场份额的
厂 自主创新能力 中的作用。只有让技术创新与管 根本途 径 。
理创新协调发展 ,才能真 正提高选煤厂的 自主创 (四)组织创新
限度 回收一平浪煤矿有限 的肥煤资源和提高经 产率。忽高忽低 ,没有实现最大产率的目标。根据
济效益 ,根据况,一平
性情况 ,生产什么等级的精煤才能最大限度回收 浪煤矿选煤厂应确定生产灰分为 1 1.01%一12.50%
有限的肥煤资源和提高我矿 的经济效益 ,是需要 的精煤 ,才能满足不同用户对精煤质量的要求。
认真研讨 的问题。选煤厂是煤矿产品的加工厂 ,
三 、加 强选 煤厂 生产 经营 管理 要有创新 意识
选煤厂生产经营状况直接关系到全矿 的生产经 选煤厂生产经营管理要有创新意识 ,不断提
81
加强洗煤厂生产经营管理提高经济效益
《云南煤炭}2012年第 1期
110 ̄|洗煤厂生产经营管理提高经济效益
一 乎 浪煤矿 王兴 万
摘 要:根据 目前的煤炭市场情况和我矿原 营结果。为此 ,如何搞好洗煤厂生产经营管理 ,在
煤 的 可选 性 情 况 ,结合 工作 实 际 ,就 如 何 搞 好 洗 确保精煤质量满足不同用户要求的前提下 ,努力
关系重要组成部分的选煤厂经 营管理为 自己提 是通过调整优化管理要素人 、财 、物、时间 、信息
供最有效 的发展形式 。无论培养选拔科技人才、 等资源的配置结构 ,提高现有管理要素的效能来
加大科技开发投入 、加强科研设施建设 ,还是培 实现的。选煤厂的组织创新 ,要考虑选煤厂的经
浅谈选煤厂降耗提质增加效益的途径

浅谈选煤厂降耗提质增加效益的途径发布时间:2022-05-13T08:20:07.064Z 来源:《科技新时代》2022年3期作者:韩丹[导读] 提出选煤厂降耗提质增效的各种对策与措施,实现减少浪费、提高质量就是增加效益的目标。
国家能源集团神东煤炭洗选中心布尔台选煤厂内蒙古鄂尔多斯市 017200摘要:分析了选煤中各种损耗产生的主要原因,围绕“节能降耗、降水提质、减少介耗”等3个方面,提出选煤厂降耗提质增效的各种对策与措施,实现减少浪费、提高质量就是增加效益的目标。
关键词:节能降水提质减少介耗1、节能降耗选煤厂属于典型的工业生产企业,目前完全是机械化生产模式,且所有机械设备在其工作状态下的功耗都比较大,突出特点就是负载比较大,机械设备在运行状态下各个部件的磨损比较大。
将选煤厂的机械设备运行条件进行优化,提高其生产效率和质量,提高机械设备的使用寿命,是促进选煤厂企业提质增效运营的有效途径。
1.1选择合理的选煤工艺提高生产企业生产效率和一个重要举措就是降低产品的生产成本。
在生产企业实际运行过程中,一旦某个生产环节出现不合理情况,就会影响到整个生产系统的运行效率和生产质量。
例如,生产各系统设计上的缺陷;设备联动系统中某个设备的选型不正确;或者所选择的溜槽斜度和大小不合理等情况,这些都会对生产效率产生不利影响。
另外,简化工艺流程也是生产企业提质增效的一个重要方法。
例如许多情况下可以减少大功耗设备的使用和改善对机械设备的利用,以及一些短流程的改造,都可以大大降低生产成本。
1.2提高选煤工艺的自动化程度改进选煤工艺的自动调节与控制,优化生产系统中各环节的监控与分析:例如优化介质系统自动分流环节以快速达到使用要求并保持稳定;加大对生产系统中的机械设备进行自动润滑减少人力投入;实现生产全系统的自动在线点检装置的使用,并根据点检数据及时进行分析,已减少设备故障率;配仓的自动化控制及装车的无人化操作等等。
发展趋势表明,当选煤厂自动化程度越高、智能化建设越高,才是实现选煤厂降耗增效的有效手段。
选煤厂降本增效措施

选煤厂降本增效措施洗选厂通过不断的改造创新,确保洗煤连续高效运行,降低洗煤成本,提高精煤回收率,实现洗煤利润最大化。
一是确保浅槽分选效果,确保入洗原煤质量。
(1)对原煤分级振动筛筛孔由70mm改为50mm,是毛煤入洗率提高10%,排矸量在原来的基础上每月可提高3500吨,年可多提矸石4.2万吨,确保浅槽分选机满负荷运转,极大的缓解了重介入洗压力。
(2)针对浅槽分选机入料不足的问题,在满足入洗的情况下,将浅槽大刮板由原来的30块减少至现在的20块,每年可节约材料1.6万元。
(3)将浅槽刮板速度有原来的0.5米/秒降低到现在的0.4米/秒,减少了刮板磨损,年可节约材料及电费5万元以上。
(4)对浅槽入洗皮带降速30%及对浅槽入洗刮板降速10%,既保证了拣选杂物安全,又减少了皮带和刮板磨损,每年可节省材料及电费4万元以上。
二是通过提高原煤入洗量,减少事故影响,降低洗煤费用。
一是对重介操作工加强培训,规范操作,提高事故应变能力,将事故影响降到最低,确保入洗时间。
二是对入洗系统进行改造优化,确保原煤入洗量:(1)对原煤入洗皮带进行更换,将原宽800mm更换为宽1000mm,提高原煤运输量;2)在地下仓安装给煤机,将原下料口直径由400mm增加至600mm,确保供料连续均匀,有利于整个系统平衡稳定,同时给煤机由单位自行设计制年可节约材料费和电费12万元以上;(4)对矸石运输系统进行改造,去掉两条矸石皮带,设计研制一部抛矸机,年可节约材料费和电费30万元以上。
通过以上措施使得原煤入洗能力大幅度提高,洗煤加工费得到了有效控制。
三是加强节能管理。
重介系统投入使用后,洗选厂负荷增加较多,给我厂节能管理工作带来一定难度,为进一步实现节能降耗,一是加强节能宣传,让职工牢固树立节能意识;二是日常做好机电设备维修保养,杜绝大型机电事故影响;三是合理组织生产,尽量做到避峰填谷用电;四是排查用电负荷情况,杜绝大马拉小车现象;五是每天停车四个小时检修,确保检修质量,提高设备完好率,同时加大事故分析力度及事故处罚力度,彻底杜绝资源人力浪费。
最新-选煤厂创建节约型企业提升洗煤经济运行质量与效益的调查报告 精品

选煤厂创建节约型企业提升洗煤经济运行质量与效益的调查报告找文章到第1更多原创-(1)选煤厂是国家“一五”时期前苏联援建的156项重点工程之一,1956年成立,1960年投产,设计入洗能力97万吨,筛分能力53万吨,整体生产能力150万吨。
原归兴安矿管理,于2019年9月归属****,实行集中专业化管理、经营独立核算。
三年来,厂在集团公司和选煤总厂的正确领导下,牢固树立和落实科学发展观,按照建设节约型企业的总体要求,坚持厉行节约、效益最佳、科技进步、持续发展的工作原则,把推动节能降耗作为企业挖潜增效和转变经济增长方式的重要途径,树立节能意识,落实节能措施,强化节能管理,由2019年以前一直亏损,到如今年盈利2000余万元,企业经济运行质量和效率效益的稳步提高。
主要做法是:一、面对现实找差距,牢固树立节能意识选煤厂2001年以前,采用“跳汰一浮选”联合工艺流程,产品以11级冶炼精煤、其它精煤和洗中块为主。
2001年对主选系统进行技术改造,由目前国内先进的“****”联合工艺流程替代原有工艺,并先后开发了二级气精煤、5-8级冶炼精煤等洗煤品种,有力促进了洗煤生产效率和效益的提高。
尽管洗煤工艺的改进,扩大了入洗加工能力,增加了洗煤品种,优化了洗煤产品结构,解决了制约兴安分厂经济发展的主要矛盾。
但由于各方面原因,影响兴安分厂经济效益稳步提高的因素依然很多,主要表现在两个方面:一是资源利用率不高。
以往实施的技术改造多数侧重于主洗选系统,而煤泥水回收处理系统却依然停留在20世纪50年代落后的水平上,由此带来整体工艺流程不配套、浮选精煤回收率不高、产品水份超标、煤泥水大量外排等实际问题,不仅制约了洗煤生产,浪费了宝贵资源,而且对矿区生态环境造成污染。
二是电耗控制难度大。
建厂初期在用设备105台,装机容量2185千瓦,2019年末在用设备达到420台,装机容量增加到5525千瓦,而且上世纪50-70年代前苏联和国产350台淘。
浅谈选煤厂降本、提质增效的有效途径
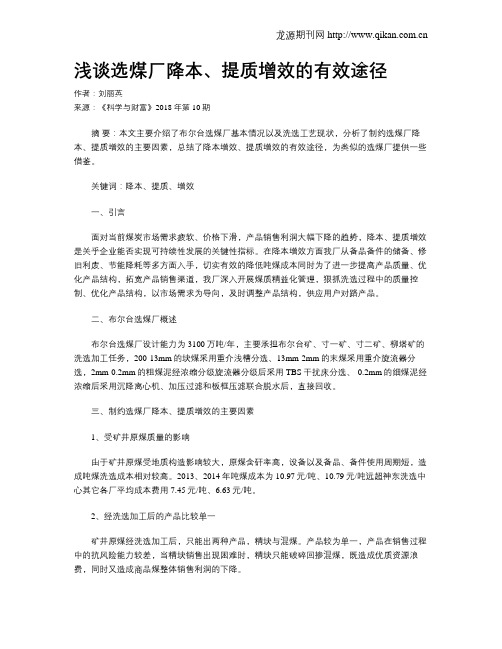
浅谈选煤厂降本、提质增效的有效途径作者:刘丽英来源:《科学与财富》2018年第10期摘要:本文主要介绍了布尔台选煤厂基本情况以及洗选工艺现状,分析了制约选煤厂降本、提质增效的主要因素,总结了降本增效、提质增效的有效途径,为类似的选煤厂提供一些借鉴。
关键词:降本、提质、增效一、引言面对当前煤炭市场需求疲软、价格下滑,产品销售利润大幅下降的趋势,降本、提质增效是关乎企业能否实现可持续性发展的关键性指标。
在降本增效方面我厂从备品备件的储备、修旧利废、节能降耗等多方面入手,切实有效的降低吨煤成本同时为了进一步提高产品质量、优化产品结构,拓宽产品销售渠道,我厂深入开展煤质精益化管理,狠抓洗选过程中的质量控制、优化产品结构,以市场需求为导向,及时调整产品结构,供应用户对路产品。
二、布尔台选煤厂概述布尔台选煤厂设计能力为3100万吨/年,主要承担布尔台矿、寸一矿、寸二矿、柳塔矿的洗选加工任务,200-13mm的块煤采用重介浅槽分选、13mm-2mm的末煤采用重介旋流器分选,2mm-0.2mm的粗煤泥经浓缩分级旋流器分级后采用TBS干扰床分选、-0.2mm的细煤泥经浓缩后采用沉降离心机、加压过滤和板框压滤联合脱水后,直接回收。
三、制约选煤厂降本、提质增效的主要因素1、受矿井原煤质量的影响由于矿井原煤受地质构造影响较大,原煤含矸率高,设备以及备品、备件使用周期短,造成吨煤洗选成本相对较高。
2013、2014年吨煤成本为10.97元/吨、10.79元/吨远超神东洗选中心其它各厂平均成本费用7.45元/吨、6.63元/吨。
2、经洗选加工后的产品比较单一矿井原煤经洗选加工后,只能出两种产品,精块与混煤。
产品较为单一,产品在销售过程中的抗风险能力较差,当精块销售出现困难时,精块只能破碎回掺混煤,既造成优质资源浪费,同时又造成商品煤整体销售利润的下降。
3、由于末煤入洗受煤泥水系统制约,造成商品煤提质作用不明显布尔台选煤厂为群矿型选煤厂,由于各矿井地质构造、断层较多,原煤含矸率高且矸石泥化严重,混煤产品发热量、稳定率相对较低。
落实精益化管理,提升煤炭企业经济效益

落实精益化管理,提升煤炭企业经济效益精益化管理是一个系统性的管理方法,它通过简化流程、减少浪费、提高质量和效率,来实现企业的持续改进和提高经济效益。
在当今竞争激烈的市场环境下,煤炭企业要想保持竞争力和持续盈利,就必须不断地探索和实施精益化管理,以提升经济效益。
煤炭企业在实施精益化管理时,需要着重从以下几个方面入手:一、流程优化:流程是企业运作的核心,影响着整个价值链的顺畅。
煤炭企业需要深入分析生产、销售、供应、物流等各个环节的流程,找出其中的瓶颈和浪费,通过重新设计和优化流程,有效地提高生产效率和降低成本。
通过精益化管理,可以对煤炭生产的整个价值链进行优化,从选煤、洗选、运输到销售等环节,不断地减少浪费、提高资源利用率,从而降低成本,提高生产效率。
二、减少浪费:浪费是精益化管理中的关键概念,它包括了时间、人力、资金、物料等多个方面。
煤炭企业需要通过精益化管理的方法,全面梳理企业内外部的各种资源使用情况,分析各环节的浪费情况,并提出改进方案,减少不必要的浪费,提高资源利用效率。
可以通过引入自动化设备和智能化管理系统,减少人力成本和提高生产效率;通过优化供应链管理,减少物料的过剩采购和库存积压,提高资金的周转效率。
三、质量管理:在精益化管理中,质量是企业生存和发展的基础。
煤炭企业需要注重产品质量,通过全面提升产品质量,提高客户满意度,从而增加市场份额,提高销售量和价格,提升企业的经济效益。
可以通过引入先进的工艺和设备,加强生产流程的管理和控制,提高产品的质量和稳定性;通过建立健全的质量管理体系,加强对产品质量的监控和改进,提高产品合格率,降低废品率。
四、持续改进:精益化管理是一个持续改进的过程,煤炭企业需要不断地寻找和解决存在的问题,进行各种改善活动,实现企业的持续发展和改进。
通过精益化管理,煤炭企业可以建立起一个持续改进的文化氛围和机制,不断地推动企业的改进和提升。
可以通过实施精益生产、精益供应链管理、精益质量管理等精益化管理工具和方法,推动企业不断改进和提升;通过建立起一个全员参与的改善机制,鼓励员工积极参与改进活动,共同推动企业的不断提升。
创建煤矿节约型企业重点目标任务分解方案

创建煤矿节约型企业重点目标任务分解方案创建煤矿节约型企业是当前我国煤炭行业发展的重要方向,在我国巨大的煤炭资源优势背景下,节能减排、环境保障和资源利用如何协调发展,成为近年来煤炭企业必须面对的重大问题。
为了实现煤矿节约型企业的目标,需要采取各种措施,优化资源配置,提高资源回收利用率,降低运营成本,并采取更加绿色、环保、可持续发展的经营方式进行煤炭开采。
一、目标任务分析1.提高“三率”水平企业应该减少煤矿生产过程中的能源和资源消耗,增强节能减排意识,执行合理的资源管理,实现减低煤炭业的能源、资源和物资消耗,提高能源和资源利用率,降低运营费用,为实现节约型经济奠定基础。
2.建设节能环保型煤矿企业应该以降低煤炭生产过程中的能耗,水耗,空气污染和固体废弃物排放为目标,开展工艺和技术改进,实现煤炭生产节能减排,使煤矿更加环保和可持续发展。
3.优化生产布局企业应该根据市场需求,调整生产结构,优化生产布局,合理配置资源,降低成本和风险,提高经济效益和社会效益。
二、目标任务分解1.提高“三率”水平(1)加强能耗、物料利用、生产周期等重点指标的统计分析,切实提高企业能耗管控、资源管理水平;(2)科学制定能效、物资利用监管制度,在全员参与下提高工作效率;(3)通过节能减排、投资新技术新装备、规范化制度、改进管理等有计划有步骤推进管理创新;(4)建立、完善能耗考核体系,创建能率化管理工作模式,打造煤炭节能品牌。
2.建设节能环保型煤矿(1)实施清洁生产,确保生产过程绿色环保;(2)加强环境保护设施建设,实现污染物排放标准化管理;(3)推进可持续发展战略,大力发展清洁新能源产业,降低碳排放;(4)整合现有资源,实施能源多元化布局,推行节能环保政策。
3.优化生产布局(1)落实节约型企业目标任务,将资源投放到相应的生产领域中;(2)根据市场需求调整生产结构,对资源进行合理配置;(3)根据资金、人力、技术、土地资源等因素综合考虑,选取最佳的生产布局方案;(4)加大产品推广和市场营销力度,扩大企业影响,实现经济效益和社会效益的协调发展。
洗煤厂降本增效方案

多渠道挖掘潜力,实现洗煤节支降本根据公司降本增效实施意见,洗煤厂在保证选煤系统高效运行的前提下,积极行动,多渠道、全方位挖掘自身潜力,深入开展节支增效工作,实现洗煤效益最大化。
一是加强物资管理,提高资金利用率1、严格按照公司物资全生命周期管理要求,真正实现从物资编制计划开始,到采购、入库、审批、发放、核算、回收、复用、残值处理的全程闭合管控。
同时及时清查库存材料配件,盘活储备资金。
2、对材料费实行严格控制管理,要求上报材料计划的准确性。
尤其对于一次性消耗的物资,如介质粉、浮选药剂等与内部市场化工资收入相结合,节约额按10%的比例兑现奖励,超支额按100%的比例扣罚,力争降低吨煤材料费消耗。
二是大力开展修旧利废、加工制作,提倡节约1、洗煤厂坚持“能修旧的不用新的、能自修的不外委”,不断挖掘自修潜力。
要求在有旧件库存的情况下,不得发放新品;对能够使用(或改造改制)的旧件进行维修后能够复用的予以鼓励使用,改造改制品质量经厂技术部门检验合格的,可对维修单位分别给予原值相应比例的奖励,以嘉奖工资形式直接予以兑现奖励,提高广大职工的积极性和创造性。
2、积极挖掘机修小厂自制自修潜能,例如加工中压DN50-DN300mm法兰盘、收集溜槽、缓冲箱、滚筒壳、浮选机刮泡器等,通过加工自制节约材料成本。
3、积极与其他选煤厂联系,寻找可以使用的设备配件,二月份我们联系到付村洗煤厂振动筛报废,主动去拆解其振动筛上的4台激振器进行使用,节约资金100万元。
三是进一步加强用电管理,杜绝浪费1、充分利用自动控制手段准确掌握设备用电动态,及时调整设备运行负荷,杜绝大马拉小车和设备空运转现象。
2、加强系统流程管理,及时检查发现设备隐患,合理安排生产时间和检修任务,提高设备的运行可靠性和完好率,降低事故台时和系统故障状态下的空车等待时间。
3、各个生产岗位加强协作,八级泵、风机、集中水池及时启停,避免空转状态,入洗运输岗位,及时增减系统处理量,努力提高生产效率。
创建煤矿节约型企业重点目标任务分解方案

创建煤矿节约型企业重点目标任务分解方案随着环保意识的不断提高,煤炭行业也不断进行有益的改革。
为了实现可持续发展,创建煤矿节约型企业已成为目前煤炭行业的重点工作。
因此,本文将围绕这一主题,依次分析煤矿节约型企业的重点目标,制定相应的任务分解方案,从而推动煤矿企业的可持续发展。
一、煤矿节约型企业的重点目标1. 建立节能降耗的基本管理体系节能降耗是煤炭行业实现可持续发展的重要手段。
因此,煤矿企业需要建立节能降耗的基本管理体系,根据不同的生产环节制定节能方案,推广可持续发展理念,加强能源综合利用和节能技术应用。
2. 实现资源回收利用和减排措施煤矿企业需要实现资源回收利用,最大限度地减少资源浪费和排放,提高资源利用率。
同时,煤矿企业需要通过减排措施,改善污染状况,逐步提升环境质量。
3. 建立健全的环境管理体系建立健全的环境管理体系,推进企业环境保护工作。
加强替代能源开发和利用,推动低碳经济发展,提高煤矿企业的可持续发展水平。
二、任务分解方案依据以上的重点目标,可将任务进一步分解,拟定具体的任务分解方案。
1. 实施能源节约降耗项目建立完善的能源管理体系,对所有能源进行统计和综合管理,制定节能方案,采用高效节能技术改造,提高能源利用效率。
2. 推行资源回收利用项目建立完善的资源回收利用体系,建立废弃物处理流程,加强环保宣传教育,推广资源回收利用技术,实现资源最大化价值。
3. 建立健全的环境保护体系建立环境保护机制,制定监测计划,加强环保设施建设和运行,进行大气、水、土壤、噪声等方面的全面监测。
同时开展环保技术研发,实现污染排放的降低和清洁生产。
三、实施方案有计划、有针对性地组织实施节能降耗、资源回收利用和环境保护等项目。
强化监督领导和项目负责人,全面落实各项任务和工程进度。
综上所述,创建煤矿节约型企业是实现可持续发展的重要步骤。
只有建立煤矿节约型企业,才能更好地推进煤炭行业的可持续发展,为实现绿色发展贡献自己的一份力量。
莱新洁净煤公司洗煤厂构架资源节约型和节能型企业

象; 有些设备存在电力浪费现象 ; 口配件费用高, 进 不能及 时到位等 , 制约 着正常 生产 。根据设备 运行 的具体实际, 及时改造 、 优化、 完善系统 , 大胆进行 技 术革新 、 改小革 ,积极 推广应 用新工艺 、 小 新技
术、 新设 备 、 新材料 , 先后 有 4项系统优 化通过集 团 公 司的评议 ,项 科技创新 获省档案成 果三等奖 , 5 全 面提升 企业 节能降耗 的能力和形象 。
பைடு நூலகம்
莱 新洁 净煤公 司 选煤 厂从设 计开 始到生 产运
营, 始终贯穿着 “ 建设环保型企业, 走洁净能源之 路” 的企业发展理念 , 实现了降耗节能、 环境保护 与经济增 长 的和谐 发展 。
l 采取有效得力措施 , 降耗节能
山东莱新洁净煤公司洗煤厂是一家设计年人 洗
经济效益。 四降” “ 是指降低介耗 、 电耗 、 、 油耗 水耗; 控 ” 指控制人洗 量 ;一调 ” 是 “ 是指 调节旋流器人 料压 力 。 通过采 取 以上措施 , 降低 了加 工成本 , 提高 了产 品产率和 产品质量 , 提升 了经济运 行质量 。
上 , 末煤 、 泥 、 对 煤 洗矸 再次 进 行深加 工 , 而使产 从
3 m 以下螺矸 从矸 石 中剥 离并利用 煤泥运 输 n 系统实现了一个 系统输送两 种产品。螺旋分选矸石 进行单独从系统 中剥离存放 , 开发 出新产品 , 每月可
维普资讯
●
第 2 卷第 2 1 期 20 07年 4 月
能 源 环 境 保 护
E e g E v r n n a r t ci n n r y n io me t lP o e to
Vo . 1, 1 2 No. 2 Apr., 00 2 7
节能降耗以创建节约型洗煤厂

节能降耗以创建节约型洗煤厂作者:张锋来源:《中国科技博览》2016年第05期[摘要]选煤是对煤炭的机械化洗选加工过程,是有限资源效益最大化的有效途径,作为煤炭洗选加工行业,在提高煤炭综合利用、保护煤炭资源方面有着极其重要的作用。
[关键词]节能降耗节约型选煤厂中图分类号:TD948.8 文献标识码:A 文章编号:1009-914X(2016)05-0045-01选煤厂的机械设备种类众多,功率较大,机械化、自动化程度高,用水量大,是高耗能的生产单位。
节能降耗是企业的生存之本,树立一种“点点滴滴降成本,分分秒秒增效益”的节能意识,以最好的管理,来实现节能使效益的最大化,是提高竞争力的一条直接而有效的途径。
1 节电降耗选煤厂是机械化的工业企业,装备了许多耗电的机械设备。
其特点是负载变动大,设备部件磨损大等。
改善选煤厂的工作条件,改进生产工艺和提高工作效率,使选煤厂电气设备合理运行,是选煤厂降低电耗的重要保证。
降低单位产品用电量是提高选煤厂生产效率的重要措施。
在实际生产中,如果存在一些薄弱环节,往往会限制许多机械设备的工作。
为提高选煤厂的生产效率,必须消除机械设备联系系统中影响生产能力的薄弱环节,采用先进的工艺或改进现有工艺,以达到工艺系统的合理与优化。
1.1 提高选煤工艺的自动化程度实现选煤工艺的自动调节与控制,对工艺流程中重要的机械设备实行集中控制;实现远距离自动测定容器内液面高度和煤仓中物料的堆积高度,并对工艺系统中的机械设备进行自动润滑;同时在原煤、精煤、中煤和矸石的主要运输路线上设置自动称量装置,并将原来由人工完成的挡板、闸板、阀、栓等的开启与关闭,以及煤仓的清理等均采用机械化自动操作与控制来完成等等。
实践证明,当选煤厂自动调节和控制选煤工艺的各个作业时,也有着巨大的节电潜力。
1.2 合理利用其他能源选煤厂普遍采用的能源是电能,用电动机来传动机械设备,技术经济指标高而且运用方便。
但在有些情况下,可以充分利用其它能源。
落实精益化管理,提升煤炭企业经济效益

落实精益化管理,提升煤炭企业经济效益近年来,煤炭行业一直面临着供需矛盾加剧、环境压力增大等问题,煤炭企业经济效益下降的局面越来越突出。
为了提升煤炭企业的经济效益,必须落实精益化管理,提高生产效率、降低生产成本,实现煤炭企业的可持续发展。
精益化管理是一种以高效、低耗为目标的管理理念,旨在通过减少生产过程中的浪费,提高生产资源利用率,提高产品质量和生产效率。
在煤炭企业中,精益化管理可以从以下几个方面进行落实:一是优化生产流程。
煤炭企业生产过程中存在许多不必要的环节和冗余的步骤,这些都会增加生产成本和浪费资源。
通过分析和优化生产流程,可以减少不必要的环节和步骤,提高生产效率。
可以通过引入先进的设备和技术,实现煤炭的自动化生产,提高生产效率和产品质量。
二是优化资源利用。
煤炭企业的资源利用率一直较低,存在着许多不合理的现象。
在煤炭采矿过程中,很多煤炭企业仅利用了矿石中的一部分,剩余的矿石资源被浪费。
通过改变矿石的开采方式和提炼工艺,可以提高资源的利用率,降低生产成本。
还可以通过改变能源的使用方式和提高能源利用效率,减少能源消耗。
三是提高产品质量。
煤炭产品的质量是影响经济效益的重要因素之一。
通过改善生产工艺,提高产品的质量,可以增加产品的附加值,提高产品的市场竞争力。
可以通过改进煤炭的洗选和分级工艺,提高煤炭的品质,降低煤炭的灰分和硫分的含量,提高煤炭的热值和燃烧效率。
四是降低生产成本。
煤炭企业的生产成本一直居高不下,是制约企业经济效益提高的重要因素之一。
通过控制生产过程中的耗能和耗材,降低物料和能源的消耗,可以有效降低生产成本。
可以通过优化生产设备和工艺,减少能源的消耗;选择更加高效的运输方式和仓储管理方式,降低物料和仓储成本。
落实精益化管理,提升煤炭企业的经济效益是当前煤炭行业改革发展的重要任务。
通过优化生产流程,优化资源利用,提高产品质量和降低生产成本,可以实现煤炭企业的可持续发展。
还需要加大科研开发力度,推广和应用新技术、新工艺,提高整个煤炭行业的创新能力和竞争力,为煤炭企业的经济效益提升提供有力保障。
浅谈节能降耗以创建节约型洗煤厂
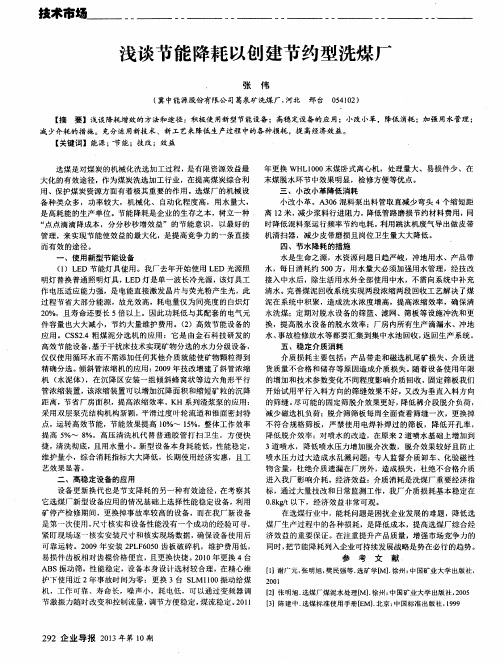
点,运转 高效节能 ,节能效果提高 1 O %~ l 5 %,整体工作效率 提高 5 %~ 8 %。 高 压 清 洗 机 代 替 普 通 胶 管 打 扫 卫 生 ,方 便 快 捷,清洗彻底 , 且用水量小。新型设备本身耗能低,性能稳定, 维 护 量 小 ,综 合 消 耗 指 标大 大 降低 ,长 期 使 用 经 济 实 惠 ,且 工
技术市场
浅谈节能 降耗 以创建节约型洗煤 厂
.
张
伟
邢台 0 5 4 1 0 2 )
( 冀 中能源股份有 限公 司葛泉矿洗煤厂, 河北
【 摘
要 】浅谈降耗增效的方法和途径:积极使用新型节能设备 ;高稳定设备的应用 ;小改 小革 ,降低消耗 ;加强 用水管理 ;
减少介耗 的措施。充分运 用新技术 、新 工艺来降低生产过程 中的各种损耗 ,提 高经济效益。
管理,来 实现 节能使效益的最大化,是提高竞争力的一条直接
而 有 效 的 途径 。
一
使 用 新型 节 能 设 备 ( 1 )L E D节能灯 具使用 。我厂去年开始使用 L E D光源照
、
明灯 替换 普 通 照 明 灯具 , L E D 灯 是 单 一波 长 冷 光源 ,该灯 具 工 作 电压 适 应 能 力 强 ,是 电能 直 接 激 发 晶 片 与 荧 光 粉 产 生 光 ,此 过程节省大部分能源,故光 效高 ,耗 电量仅为 同亮度的 白炽灯 2 O %,且 寿 命 还 要 长 5 倍 以 上 。 因此 功 耗 低 与 其 配 套 的 电 气元 件 容 量 也 大 大 减 小 ,节 约 大 量 维 护 费 用 。 ( 2 )高 效 节 能 设 备 的 应 用 。C S S 2 . 4粗 煤 泥 分 选 机 的应 用 : 它 是 由金 石科 技研 发 的
洗煤厂创新创效工作总结

洗煤厂创新创效工作总结
近年来,随着环保意识的提升和科技的不断发展,洗煤厂在创新创效工作方面
取得了显著的成绩。
通过不断引进先进的洗煤设备、优化工艺流程和提升管理水平,洗煤厂在节能减排、提高产能和产品质量等方面取得了令人瞩目的成绩。
首先,在设备方面,洗煤厂引进了一系列高效节能的洗煤设备,如重介质分离器、脱水筛等,这些设备不仅大大提高了洗煤效率,同时也降低了能耗,实现了节能减排的目标。
此外,洗煤厂还对设备进行了智能化改造,通过数据监测和远程控制,实现了设备的智能化运行,提高了设备的稳定性和可靠性。
其次,在工艺方面,洗煤厂优化了洗煤工艺流程,采用了先进的分选技术和化
学药剂,有效提高了洗煤效率,降低了煤矸石的含量,提高了产品的质量。
同时,洗煤厂还对废水处理工艺进行了改进,实现了废水的零排放,为环境保护作出了积极贡献。
最后,在管理方面,洗煤厂加强了对生产过程的监控和管理,建立了全面的生
产数据分析系统,通过大数据分析,实现了生产过程的精细化管理,提高了生产效率和产品质量。
同时,洗煤厂还加强了员工培训和技能提升,提高了员工的专业素养和责任意识,为企业的可持续发展奠定了坚实的基础。
总的来说,洗煤厂在创新创效工作方面取得了显著的成绩,通过引进先进设备、优化工艺流程和加强管理,实现了节能减排、提高产能和产品质量的目标,为企业的可持续发展做出了积极的贡献。
相信在不久的将来,洗煤厂将会在创新创效工作方面取得更大的突破,为行业的发展注入新的活力。
选煤厂创建节约型企业提升洗煤经济运行质量与效益的调查报告

选煤厂创建节约型企业提升洗煤经济运行质量与效益的调查报告调查报告:提升选煤厂洗煤经济运行质量与效益摘要:本调查报告旨在研究并提出措施,以提升选煤厂的经济运行质量与效益。
通过对一家选煤厂的调查以及相关文献研究,本报告得出以下结论:首先,选煤厂需要加大对现有设备的更新改造力度;其次,提高员工技能与经验培训,增强技术创新能力;第三,加强能源利用效率和环境保护意识;最后,加强对选煤厂经济运行质量与效益的监测与评估,以持续改进。
1.介绍选煤厂作为煤矿生产过程中的重要环节,对提高煤炭质量、提高市场竞争力具有重要意义。
然而,目前我国选煤厂存在一些问题,例如,设备老化、技术水平低下、能源浪费严重等,这些问题导致选煤厂的经济运行质量与效益有待提升。
2.调查方法在本调查中,我们选择了一家具有较大规模的选煤厂作为研究对象。
通过观察、访谈员工以及数据收集,我们获得了以下信息:选煤厂设备状况、员工素质、能源利用情况等。
3.调查结果与讨论3.1设备更新改造调查发现,选煤厂存在一定数量的老化设备,其性能下降严重,影响了洗煤效果。
因此,选煤厂应考虑加大设备更新改造力度,购买新的洗煤设备以提高工作效率。
3.2员工技能与经验培训调查发现,选煤厂员工技术水平参差不齐,部分员工缺乏洗煤技术与经验。
因此,选煤厂应加强员工培训,提高其技术水平与实践经验,培养更多的专业人才。
3.3能源利用效率与环境保护调查发现,选煤厂在洗煤过程中存在能源浪费现象,同时对环境保护意识不足。
为了提高经济效益,选煤厂应采取有效措施,增强能源利用效率,减少资源浪费;同时,应加强环保措施,降低环境污染。
3.4监测与评估调查发现,选煤厂缺乏对经济运行质量与效益的监测与评估。
因此,选煤厂应建立相应的监测与评估机制,及时发现问题并采取相应措施改进。
4.结论与建议4.1设备更新改造是提升选煤厂洗煤经济运行质量与效益的关键,选煤厂应加大投资力度,并购买先进的洗煤设备。
4.2加强员工技能与经验培训是提高选煤厂洗煤质量的前提条件,选煤厂应加大人才培养力度,提高员工技术水平。
- 1、下载文档前请自行甄别文档内容的完整性,平台不提供额外的编辑、内容补充、找答案等附加服务。
- 2、"仅部分预览"的文档,不可在线预览部分如存在完整性等问题,可反馈申请退款(可完整预览的文档不适用该条件!)。
- 3、如文档侵犯您的权益,请联系客服反馈,我们会尽快为您处理(人工客服工作时间:9:00-18:30)。
选煤厂是国家“一五”时期前苏联援建的156项重点工程之一,1956年成立,1960年投产,设计入洗能力97万吨,筛分能力53万吨,整体生产能力150万吨。
原归兴安矿管理,于2003年9月归属****,实行集中专业化管理、经营独立核算。
三年来,厂在集团公司和选煤总厂的正确领导下,牢固树立和落实科学发展观,按照建设节约型企业的总体要求,坚持厉行节约、效益最佳、科技进步、持续发展的工作原则,把推动节能降耗作为企业挖潜增效和转变经济增长方式的重要途径,树立节能意识,落实节能措施,强化节能管理,由2002年以前一直亏损,到如今年盈利2000余万元,企业经济运行质量和效率效益的稳步提高。
主要做法是:一、面对现实找差距,牢固树立节能意识选煤厂2001年以前,采用“跳汰一浮选”联合工艺流程,产品以11级冶炼精煤、其它精煤和洗中块为主。
2001年对主选系统进行技术改造,由目前国内先进的“****”联合工艺流程替代原有工艺,并先后开发了二级气精煤、5-8级冶炼精煤等洗煤品种,有力促进了洗煤生产效率和效益的提高。
尽管洗煤工艺的改进,扩大了入洗加工能力,增加了洗煤品种,优化了洗煤产品结构,解决了制约兴安分厂经济发展的主要矛盾。
但由于各方面原因,影响兴安分厂经济效益稳步提高的因素依然很多,主要表现在两个方面:一是资源利用率不高。
以往实施的技术改造多数侧重于主洗选系统,而煤泥水回收处理系统却依然停留在20世纪50年代落后的水平上,由此带来整体工艺流程不配套、浮选精煤回收率不高、产品水份超标、煤泥水大量外排等实际问题,不仅制约了洗煤生产,浪费了宝贵资源,而且对矿区生态环境造成污染。
二是电耗控制难度大。
建厂初期在用设备105台,装机容量2185千瓦,2005年末在用设备达到420台,装机容量增加到5525千瓦,而且上世纪50-70年代前苏联和国产350台淘汰电机仍在使用,占全部设备台数的83%。
这些电气设备功率大、能耗高、效率低、安全可靠性差,2005年全厂电耗达到1594万千瓦时,吨煤电耗13.85千瓦时,占洗煤加工费36.3%,大大超过洗煤行业电耗标准。
面对这些现实和差距,兴安分厂领导班子坚持从提高思想认识入手,利用各种宣传形式,倡导和形成“加强管理、挖潜增效”,“节约光荣、浪费可耻”的舆论氛围。
特别是组织全厂上下深入开展“挖潜堵漏、节能降耗、努力建设节约型企业”大讨论活动。
在讨论中,他们结合上级要求和集团公司创建节约型企业的工作部署,针对影响兴安分厂经济效益稳步提高的两个方面因素,摆事实,讲道理,谈感想,使干部职工充分认识到:挖潜堵漏,节能降耗,努力建设节约型企业,是贯彻落实科学发展观的必然要求,是规范和加强企业管理的根本任务,也是不断提高洗煤生产效率和经济效益的重要途径。
在形成思想共识的基础上,厂领导班子因势利导,集思广益,围绕如何建设节约型企业,动员每个车间和每名职工提合理化建议,确立了科技进步和科学管理“双轮联动”、促进节能降耗的工作思路,并适时提出了保持思想认识、工作方向、措施执行“三个一致性”的工作原则,以此指导和推进节约型企业的深入开展。
二、围绕瓶颈抓改造,全面落实节能措施科学技术是第一生产力,对高耗低效的工艺和设备实施技术改造,是提高洗煤加工效率和效益的治本之策。
为此,他们重点实施了两个方面的技术改造。
一方面,围绕增加资源回收,改造煤泥水回收系统。
2005年,集团公司经过认真的考察论证和专家评审,投资980万元对兴安分厂实施洗水闭路循环系统技术改造。
技改期间,全体施工人员克服工期紧、现场空间狭窄、施工难度大等困难,仅用96天就完成全部改造工程,安装投用加压过滤机、隔膜压滤机和各种运输、辅助设备28台,不仅完善了洗煤工艺、提高了产品质量、改善了矿区环境,而且对节能工作带来非常好的效果。
一是生产效率提高了。
产品综合产率提高1个百分点,精煤产率提高1.5-2个百分点,年可多回收精煤和低灰煤泥1.5万吨。
二是经营成本降低了。
洗水浓度由原来的43.5%降到11.5%,并且做到洗水循环利用,洗煤水耗降到0.15,年节约用水近百万吨,节支90余万元。
同时,吨干煤泥油耗降低0.71公斤,絮凝剂每立方米降低0.14克,全部改造工程年可实现增收节支560余万元。
另一方面,围绕控制电力消耗,履行落后的老、旧、杂设备。
重点完成了五项调整改造任务:一是对原布局不合理的6台变压器及设备线路进行全面系统的改造,合理匹配变压器负荷,更换部分电机部件,调整2300米供电线路,有效降低了设备和线路空载损耗,功率因数由原来的0.75增至0.95,用电效率明显提高,全年可节约资金12万元。
二是调整设备电机功率,将130千瓦174#煤泥泵电动机更换为110千瓦,将155千瓦2#池底流泵电动机更换为75千瓦,将215千瓦∮30米底流泵电动机更换为130千瓦,将30千瓦7.5米清水泵电动机更换为22千瓦,将30千瓦老泵室污水泵电动机更换为5.5千瓦,切实解决了“大马拉小车”问题。
三是对174#和172#煤泥泵、∮16m和∮18m浓缩机底流泵、2号池453#煤泥泵,安装了黑龙江瑞普公司生产的“耐普”节电器,实现了电机转速可调、无极变速。
通过计量测试,1-7月5台设备平均节电率29.2%。
四是将原有耗能较大的高压配电柜,全部更换为体积小、价格低、动作可靠的新型节能高压配电柜,运行7个月未发生一起高压影响事故,全年可节约电费支出114万元。
五是将能耗高的普通白炽灯和碘钨灯,更换为功率小、效率高、照明效果好的新型节能灯,累计更换398盏,总功率由62.5千瓦降至25.8千瓦,年可节约电费支出8.2万元。
通过一系列的调整改造,全厂电耗控制取得明显成效,在去年十月后技改设备增容750千瓦情况下,吨煤电耗10.9度时,比去年末下降2.95度时,节支64万元,全年可节支114万元。
三、落实责任严考核,切实强化节能管理作为投产时间比较长的选煤厂,长期的工作实践使他们积累了较为丰富的管理经验,但是与建设节约型企业的新形势、新任务相比,无论是经营理念,还是管理能力都需要不断进行改进和加强。
为此,他们在提高两级管理人员经营素质的基础上,从严落实“一排二责三考核”制度,切实强化节能管理。
“一排”:就是及时排除设备运转故障,提高设备使用效率。
为落实节能降耗工作,他们针对在用设备多,老、旧、杂设备多的实际,以排查各种设备运行状况和能耗指数、及时排除设备运转故障为切入点,组织专业技术人员进行线路巡视和现场勘查,掌握各种设备容量、供电半径、线路状况、设备状态和开机时限,合理安排和落实设备调整改造及故障检修方案,保证各种设备运转正常、安全高效。
在现场勘查过程中,他们发现设备停开车时空耗严重,为此他们要求各车间必须按照调度室确定的检修时间,统一起车,起车前煤仓满煤,并有一定的产品煤储存空间,同时建立检修项目汇报制度,没有在规定时间完成检修任务的按事故进行追查,有效降低了设备空耗,保证了洗煤时间。
“二责”:就是认真落实节能降耗责任,增强全员管理意识。
为把节能降耗工作真正落到实处,他们成立了由厂长任组长、各车间专业技术人员任成员的节能降耗工作领导小组,确定有力有效的降成提效方案,完善材料配件计划和审批、交旧领新、跟踪管理、修旧利废等规定,制定水、电、油等能耗标准,健全单项管理制度和全员、全过程管理责任。
特别是从严落实介耗管理责任,通过对磁铁矿粉进行严格的进货验收,保证介质粒度和磁性物含量;通过加强喷水管理,控制喷水压力,改善脱介筛工作效果;通过强化磁选机运行状态,注重维护保养,保证开机时间,提高了介质回收率。
1-7月份与同期相比,吨煤介耗由1.74公斤降至1.31公斤,按同样入洗量计算,铁介粉消耗节余297吨,节支14.5万元,全年可节支32万元。
“三考核”:就是严格考核经营管理效绩,健全激励约束机制。
为规范和加强节能管理,激励全厂干部职工节能降耗的积极性和主动性,他们依照总厂制定的经营管理办法,结合自身管理实际,健全完善了“用电考核细则”、“节电管理办法”和“节电奖励办法”,并制定出台了介耗、油耗等奖罚制度,将材料、配件、用电、用水等项指标,层层细化分解和落实到各生产车间,按照吨煤消耗标准,实行定期考核与横班竞赛纵横交叉的控制手段,材料费、配件费均按节支额度的20%奖励,超支对等处罚,用规范的制度规定和严肃的绩效考核,控制和提升经营行为,促进了管理工作的不断加强。
自我厂接到集团公司党委、集团公司下发的《关于学习贯彻落实全省煤矿安全生产工作座谈会暨省政府第六次安全生产专项通报会议精神的通知》后,厂党委和总厂各位领导高度重视,立刻组织贯彻落实工作,通过学习教育、宣传发动、查摆隐患、整改提高等项工作,取得了一定的效果,安全生产把握度显著增强,零敲碎打的事故明显下降。
现将我厂具体操作情况汇报如下:一、认真学习文件精神,层层传达贯彻落实。
我们坚持把安全生产摆在一切工作的首位,利用厂两级中心组学习重点组织厂两级班子和生产骨干学习了文件精神。
特别是张左已省长的重要讲话精神,我们更是列为重点内容进行深入学习,深刻领会省长讲话的精神实质,牢固树立了安全发展观,进一步明确了认识到安全工作的重要性。
同时利用车间班前会、安全讲评等时间将省长的讲话精神传达贯彻到全厂每个班组和每名职工,使广大干部职工增强了安全生产和自我保安意识。
二、结合全国“安全生产月”,开展各种安全宣讲活动,加大安全教育力度。
我们在厂显著位置悬挂了活动宣传标语努力营造安全生产月的宣传气氛;举办了安全知识宣传漫画展、安全知识答卷等项活动,普及安全生产知识;与生产一线员工签订安全保证书,规范约束职工安全行为,增强职工自我保安意识。
通过全方位的安全教育活动,在全厂营造出一种“安全第一”、“不安全不生产”的良好的安全氛围,增强职工注重安全生产的自觉性和积极性。
三、深入开展隐患“揭、摆、查”活动,深挖安全隐患。
我们把监督、检查提高到“安全生产最后一道防”的高度来认识,牢固树立“隐患就是事故,事故就必须追查”的观念,严格贯彻执行各项安全措施,加大安全监查力度。
半个月来,由厂安检科牵头、工会、共青团和有关的职能部门相互配合,进行了2次大规模的安全隐患排查活动,重点放在了对人的不安全行为、物的不安全状态和环境的不安全状态的排查上,共查出不安全因素16项,已经全部落实整改,把安全事故消灭在了萌芽中。
四、坚持整改提高,形成安全生产的长效机制。
为确保安全工作常抓不懈,我们进一步强化了安检员、群检员、青岗员之间相互协调、互相配合的群体预防安全事故的安全网络。
要求各个生产班组必须设立群众安全监督员,主体车间安排配备专职安监员,安检科设专人在生产一线跟班进行巡回安全检查,使生产现场时时刻刻有人查安全,做到24小时不失控,形成了排查隐患、保证安全的可靠的长效机制。