VW80101-2003版-德文版
VW801010610-新版 中文版
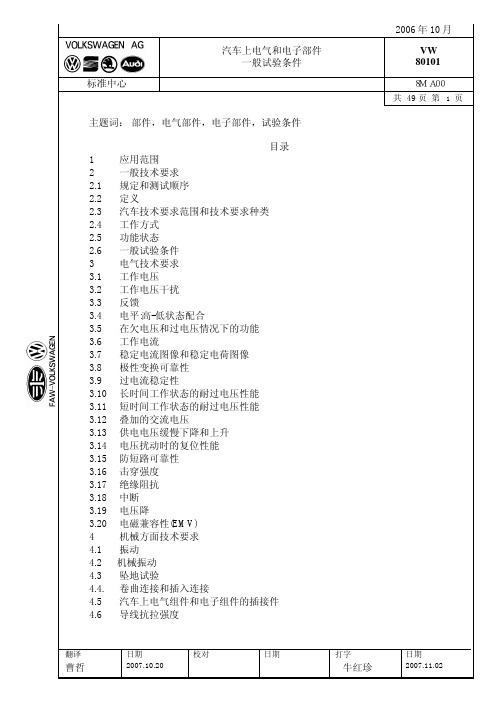
2006年10月汽车上电气和电子部件一般试验条件 VW 80101标准中心 8M A00 共 49 页第1页主题词:部件,电气部件,电子部件,试验条件目录1应用范围2 一般技术要求2.1 规定和测试顺序2.2 定义2.3 汽车技术要求范围和技术要求种类2.4 工作方式2.5 功能状态2.6 一般试验条件3 电气技术要求3.1 工作电压3.2 工作电压干扰3.3 反馈3.4 电平:高-低状态配合3.5 在欠电压和过电压情况下的功能3.6 工作电流3.7 稳定电流图像和稳定电荷图像3.8 极性变换可靠性3.9 过电流稳定性3.10 长时间工作状态的耐过电压性能3.11 短时间工作状态的耐过电压性能3.12 叠加的交流电压3.13 供电电压缓慢下降和上升3.14 电压扰动时的复位性能3.15 防短路可靠性3.16 击穿强度3.17 绝缘阻抗3.18 中断3.19 电压降3.20 电磁兼容性(EMV)4 机械方面技术要求4.1 振动4.2 机械振动4.3 坠地试验4.4. 卷曲连接和插入连接4.5 汽车上电气组件和电子组件的插接件4.6 导线抗拉强度5 气候环境要求5.1 在恒温状态下的试验5.2 在温度交变情况下的试验5.3 分级温度试验5.4 抗大气腐蚀能力5.5 环境稳定性5.6 水是温度突变的原因6 化学方面的技术要求6.1 抗试剂的稳定性7 疲劳试验7.1 电气和电子系统/元件的疲劳试验7.2 电机系统/元件的疲劳试验7.3 零部件的特殊疲劳试验8 表9相关参考资料修订同VW 801 01:2005-06标准比较,作了如下修改:— 2条,一般技术要求作了补充—表5,注释作了补充—取消了材料技术要求条款— 工作方式3作了补充— 3.4条:电压电平。
表7说明输入状态与电压电平的配合情况,在表8中,说明当接线柱5接通时作采纳的电压电平— 在功能状态C、D和E方面,不允许有不明确的功能— 3.5条,在欠电压和过电压情况下的功能,图3电压波形图,都作了校正— 3.8条,极性变换可靠性、用途作了补充,技术要求作了说明— 3.9.2条,电输出,电流负荷作了规定— 3.15条,防短路可靠性,技术要求作了说明,插图有所补充— 3.18条,断路,插头断开有所补充— 4.1条,振动,第1段有修改— 在空调条款中,工作方式3.2,试验时的机械操纵法有补充— 试验尘埃,美国亚利桑那州尘埃A.2,按ISO 12103-1标准处理— 5.2.1条,温度交变与规定的变化速度,工作方式有补充— 5.2.2条,快速温度交变与规定的转变持续时间,补充了印刷体电路(铂)— 5.5.2条,电动机洗涤,以前是在6.2条中— 简化了温度分布曲线图解,工作方式数据作了补充— 疲劳试验,7.1条以及7.1.1条,工作方式和注释都作了补充以前版本1987-06;1988-08;1992-01;1993-04;1994-05;1995-06;1998-01;1999-06;2000-09;2001-04;2003-05;2004-07;2005-061适用范围VW 801 01标准为汽车电气的、机电的和电子的元件/系统规定了一般试验条件在使用该标准时,如果牵涉到零部件特殊的供货技术条件、图纸及货运手册,通常都要使用第8条表27提供的数据(信息),有时还要就一些相关的补充数据与大众康采恩的一些主管专业科室协商行事。
VW 汽车电子电器
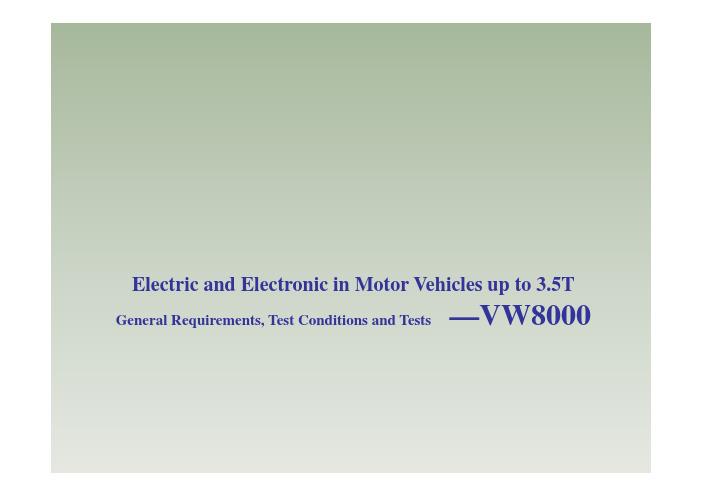
Electric and Electronic in Motor Vehicles up to 3.5TGeneral Requirements, Test Conditions and Tests —VW8000PrefaceThis standard in the present issue is based on template LV 124 Previous issuesVW 80101: 1987-06, 1988-08, 1992-01, 1993-04, 1994-05, 1995-06, 1998-01, 1999-06, 2000-09,2001-04, 2003-05, 2004-07, 2005-06, 2006-10, 2009-03ChangesTransfer of supply specification LV 124 to VW 800004.1 E-01 Long-term overvoltage4.2 E-02 Transient overvoltage4.2 E-02 Transient overvoltage4.3 E-03 Transient undervoltage4.3 E-03 Transient undervoltage4.4 E-04 Jump start4.4 E-04 Jump start4.5 E-05 Load dump4.5 E-05 Load dump4.6 E-06 Superimposed alternating voltage4.6 E-06 Superimposed alternating voltage4.7 E-07 Slow decrease and increase of the supply voltage4.7 E-07 Slow decrease and increase of the supply voltage4.8 E-08 Slow decrease, quick increase of the supply voltage4.8 E-08 Slow decrease, quick increase of the supply voltage4.9 E-09 Reset behavior4.9 E-09 Reset behavior4.10 E-10 Short interruptions4.10 E-10 Short interruptions4.10 E-10 Short interruptions4.10 E-10 Short interruptions4.11 E-11 Start pulses4.11 E-11 Start pulses4.11 E-11 Start pulses4.11 E-11 Start pulses4.11 E-11 Start pulses4.12 E-12 Voltage curve with intelligent generator control4.12 E-12 Voltage curve with intelligent generator control4.13 E-13 Pin interruption4.13 E-13 Pin interruption4.13 E-13 Pin interruption4.14 E-14 Connector interruption4.15 E-15 Reverse polarity4.15 E-15 Reverse polarity4.16 E-16 Ground offset4.17 E-17 Short circuit in signal circuit and load circuits4.17 E-17 Short circuit in signal circuit and load circuits4.18 E-18 Insulation resistance4.19 E-19 Closed-circuit current4.20 E-20 Dielectric strength4.21 E-21 Backfeeds4.22 E-22 Overcurrents5General part5 General part5.1 Referenced standards5.2 Terms and definitions5.3 Operating modes5.4 Maintaining temperature5.5 Parameter test5.6 Continuous parameter monitoring with drift analysis 5.7 Physical analysis57Physical analysis5.1 Referenced standards51Referenced standardsDIN 75220 Aging of Automotive Components in Solar Simulation UnitsDIN EN 60068-2-1 Environmental testing -Part 2-1: Tests -Test A: ColdDIN EN 60068-2-2 Environmental testing -Part 2-2: Tests -Test B: Dry HeatDIN EN 60068-2-11 Environmental Testing -Part 2: Tests -Test Ka: Salt MistDIN EN 60068-2-14 Environmental Testing -Part 2: Tests -Test N: Change of TemperatureDIN EN 60068-2-29 Environmental Testing -Part 2: Tests; Test Eb and Guidance:BumpDIN EN 60068-2-30 Environmental Testing -Part 2-30: Tests -Test Db: Damp Heat, Cyclic (12 h + 12 h)DIN EN 60068238 Environmental Testing Part 2: Tests Test Z/AD: Composite Temperature/Humidity DIN EN60068-2-38Environmental Testing-Part2:Tests-Test Z/AD:Composite Temperature/HumidityCyclic TestDIN EN 60068-2-60 Environmental Testing -Part 2: Tests -Test Ke: Flowing MixedGas Corrosion TestDIN EN 60068-2-64 Environmental Testing -Part 2: Tests; Test Fh: Vibration, Broad-Band Random and DIN EN60068264E i t l T ti P t2T t T t Fh Vib ti B d B d R d d Guidance.DIN EN 60068-2-78 Environmental Testing -Part 2-78: Tests -Test Cab: Damp Heat, Steady State5.1 Referenced standards51Referenced standardsDIN EN ISO 11124 -2 Preparation of Steel Substrates Before Application of Paints and Related Products -Specifications for Metallic Blast-CleaningAbrasives -Part 2: Chilled-Iron GritAbrasives-Part2:Chilled-Iron GritDIN EN ISO 20567-1 Paints and Varnishes -Determination of Stone-Chip Resistance of Coatings -Part 1: Multi-Impact TestingDIN EN ISO 6270-2 Paints and Varnishes –Determination of Resistance to Humidity–Part 2: DIN EN ISO62702Paints and Varnishes Determination of Resistance to Humidity Part2: Procedure for Exposing Test Specimens inCondensation-Water AtmospheresISO 12103-1 Road Vehicles –Test Dust for Filter Evaluation –Part 1:Arizona Test DustISO16750Road Vehicles Environmental Conditions and Testing forElectrical andISO 16750 Road Vehicles —Environmental Conditions and Testing forElectrical and Electronic EquipmentISO 20653 Road Vehicles -Degrees of Protection (IP-Code) -Protection ofElectrical Equipment Against Foreign Objects, Water and AccessE i t A i tF i Obj t W t d A5.2 Terms and definitions5.2 Terms and definitions5.2 Terms and definitions。
机动车扬声器成品检验规范标准

天津中环真美音响科技有限公司J01-002天津中环真美音响科技有限公司J01-002汽车扬声器成品检验规范G版第 4 页天津中环真美音响科技有限公司J01-002 G版第5 页注:检查项目1中规定的内容为所有产品外观检查项目的累计,各产品可按实际项目进行检查。
成品检验外观、纯音抽验方案天津中环真美音响科技有限公司J01-002汽车扬声器成品检验规范G版周期试验(GB/T9397-1996和TL-VW 926)第 6 页天津中环真美音响科技J01-002汽车扬声器成品检验规范G版周期试验(TL-926)第7 页天津中环真美音响科技J01-002汽车扬声器成品检验规范G版周期试验(GB/T 9397-1996)第8 页天津中环真美音响科技J01-002汽车扬声器成品检验规范G版周期试验(Q/12KF)第9页天津中环真美音响科技J01-002汽车扬声器成品检验规范G版周期试验(夏利B系列)第10 页天津中环真美音响科技J01-002汽车扬声器成品检验规范G版周期试验(MES PA 66960)第11 页天津中环真美音响科技J01-002汽车扬声器成品检验规范G版周期试验(产品QC)第12 页天津中环真美音响科技J01-002汽车扬声器成品检验规范G版周期试验(ETD 72-02)第13 页天津中环真美音响科技J01-002汽车扬声器成品检验规范G版周期试验(森力产品1)第14 页天津中环真美音响科技J01-002汽车扬声器成品检验规范G版周期试验(奇瑞Q/SQR.04.041-2007)第15 页天津中环真美音响科技J01-002汽车扬声器成品检验规范G版周期试验(JA7901-A01-2)第16 页天津中环真美音响科技J01-002汽车扬声器成品检验规范G版周期试验(森力产品2)第17 页天津中环真美音响科技J01-002汽车扬声器成品检验规范G版周期试验(MES PA PT001)第18 页3 耐寒性-40±2℃,存放4小时,评估零件的形状和尺寸外观,从恒温室内取出,不接触它放置2小时。
vw80108标准
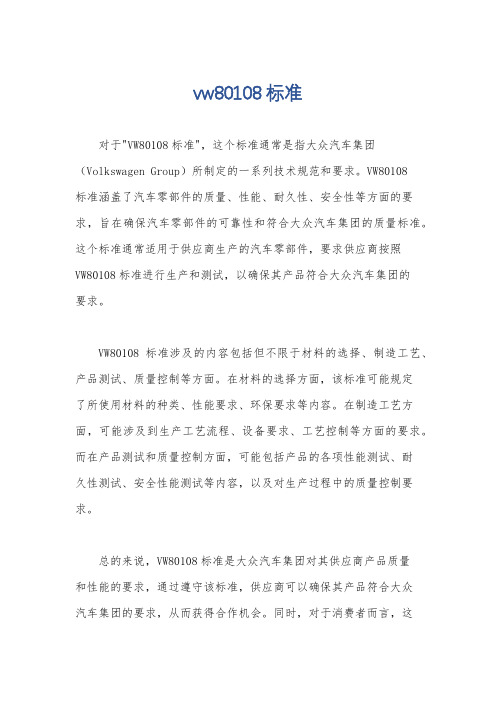
vw80108标准
对于"VW80108标准",这个标准通常是指大众汽车集团(Volkswagen Group)所制定的一系列技术规范和要求。
VW80108
标准涵盖了汽车零部件的质量、性能、耐久性、安全性等方面的要求,旨在确保汽车零部件的可靠性和符合大众汽车集团的质量标准。
这个标准通常适用于供应商生产的汽车零部件,要求供应商按照
VW80108标准进行生产和测试,以确保其产品符合大众汽车集团的
要求。
VW80108标准涉及的内容包括但不限于材料的选择、制造工艺、产品测试、质量控制等方面。
在材料的选择方面,该标准可能规定
了所使用材料的种类、性能要求、环保要求等内容。
在制造工艺方面,可能涉及到生产工艺流程、设备要求、工艺控制等方面的要求。
而在产品测试和质量控制方面,可能包括产品的各项性能测试、耐
久性测试、安全性能测试等内容,以及对生产过程中的质量控制要求。
总的来说,VW80108标准是大众汽车集团对其供应商产品质量
和性能的要求,通过遵守该标准,供应商可以确保其产品符合大众
汽车集团的要求,从而获得合作机会。
同时,对于消费者而言,这
也意味着大众汽车集团的产品在一定程度上符合较高的质量标准,从而提升了产品的可靠性和安全性。
大众实验要求VW80101 中
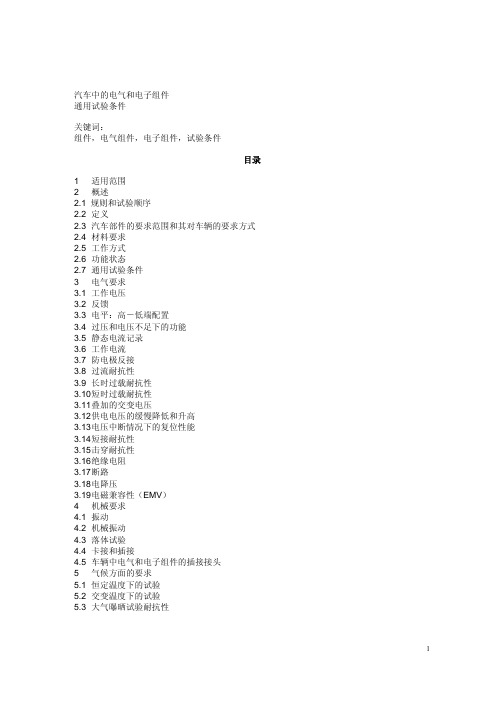
组件
具备逻辑功能的系统的零件,比如执行器,传感器,控制器
试件
待检验系统或者组件
4
2.2.2 缩写
IN
标定电流
TNH
余热温度即为车辆熄火后在要求范围所在的最高环境温度(参见表格2)。
TOL
存放温度上限为试件存放和运输过程中所允许的最高环境温度。它包括例如发动
机舱中油漆干燥和滞留热量。试件不予起动。
TRT TuB,ToB
2.6.1 功能状态A 试件在加载各项试验参数过程中和加载后满足规定中的所有功能。该状态要在具诊断能力的控 制器无任何故障存储记录。
2.6.2 功能状态B 试件在加载各项试验参数过程中和加载后满足规定中的所有功能。但可能有一项或多项功能在 规定的公差范围之外。结束加载试验参数以后试件重新满足所有规定中的所有功能。存储功能 必需保持在功能状态A。
IP 5K 0
s,u m,r,s,t e,f,g,I,j,q,s
a至q
IP 5K 0 IP 5K 0 IP 5K 4K
IP 5K 9K1)
f,g,i,q,s a至q a至q
IP 5K 9K IP 5K 9K1) IP 5K 9K1)
6
对于安全性重要的部件适用: 防尘和防喷溅水密封性要在任务书中进行定义-如果表格 2 中的说明不足的话。 如果试件可以在水下直立,就使用防护方式 IP 68(如门和盖罩,脚踏空间,水箱,被子架, 抽屉内侧)
2.5.2 工作方式2
试件采用蓄电池通电工作、车辆未开动(即为发动机不工作)
所有系统组件(比如传感器、执行器)和缆线全部接通。
工作方式1
系统/组件功能不予激活(比如睡眠模式)。
工作方式2
系统/组件发挥功能和操控规定的工作方式。
汽车电气VW80101_091101_和电子部件一般试验条件_中文版

月 11 年 9002
30�9002�01�6002�60�5002 �70�4002�50�3002�40�1002�90�0002�60�0002�60�9991 �10�8991�60�5991�40�3991�10�2991�80�8891�60�7891�10808 WV 本版前以 件条验试、件部子电、件部气电、件部�词键关 00AM8�号类分
95 共
。2 表和 1 图见 式方求要其及围范求要车汽 。压电验试的接反极电池电蓄下况情动启接外 。压电验试的时作工池电蓄 。压电验试的下况情转运机动发 压电称标 。压电作工许允小最的时作工件试 。压电作工许允大最的时作工续持件试 。作工不 件试。 度温 低最的 许允 所中程 过 输运者 或放存 件试 为意� 限下 的度温 放存 。升温身自虑考予不。作工行进地续持 件试许允时此�度温境环低最或抑高最即�限下或抑限上的度温限极作工 。度温验试为即度温该�明说他其无如。℃�5±32+�温室 。作工不件试。量热留滞和燥干漆油内舱机动发如例括包它 。度温境环高最的许允所中程过输运者或放存件试为意�限上的度温放存
q至a q至a sqjigfe
K9XPI )1 和 K4K5PI K9XPI )1 和 K4K5PI K9XPI )1 和 K4K5PI
热湿 雾盐 热湿 雾盐 热湿 雾盐
041� 041� 09� 031�
04� 04� 04� 04�
021� 04� 舱机动发 2.2.4 4.1.4 2 )3 07� 04� 部外 头车 2 度锐 b1 021� 04� 部内 头车 a1 2 . 2 . 4 4.1.4 )3 。求要体具明说上书务任计设在须必则� �值数�据数的中表定确分充能不要只 。准标 80108 WV 用应须必�式型护防 PI 的境环装安定确确精了为 围范求 要 节照按 击冲械机 节照按 荷负动振 型类求要
电子电气设备外壳防护体系解读IP等级外壳防护解析

一、概述对于户外用的便携式电子电气设备、汽车电子设备、通讯设备等均有外壳防护测试要求,针对某些使用环境条件还可能会有特殊要求,如风沙大,热带潮湿,海岸边多盐雾,多雨淋、喷雾等比较严酷的使用环境条件。
电子电气零部件的外壳必须具备相应的防护能力,主要包括防接触、防水、防爆、防机械碰撞等防护要求,以确保元器件使用的安全性和可靠性。
下面就目前比较流行的外壳防护体系做全面的总结和梳理,介绍各防护体系的标准要求和测试方法,并分析其异同点。
二、IP防护体系IP防护体系来源于国际电工委员会(IEC),也就是国际上和国内普遍采用的IP代码,该代码体系以EN/IEC 60529-2001 Degrees of protection provided by enclosures(IP code)标准为基础,我国标准GB 4208就等同采用了该标准。
IP防护体系中,对外壳提出了防接触和防水的防护要求,一般有两位数字组成,例如IP56,第一位特征数字表示防接触的等级,第二位特征数字则表示防水的等级。
除了IEC 60529/GB 4208标准之外,标准DIN 40050、ISO 20653等标准也采用了IP防护体系,并针对具体应用补充了三个防水等级,分别是IPX4K、IPX6K和IPX9K,防接触等级则完全一致。
IP防护体系中,各防护等级具体防护含义和相应的测试方法见表1[1]和表2[2].表1 IP防护体系-第一位特征数字参考文献:[1] GB 4208-2008/IEC 60529-2001外壳防护等级(IP代码)[2] ISO 20653-2006 Road vehicles – Degrees of protection (IP-Code) – Protection of electrical equipment against foreign objects. Water and access[3] GB/T 20138-2006/IEC 62262;2002电器设备外壳对外界机械碰撞的防护等级< IK代码>[4] NEMA Standards Publication 250-2003 Enclosures for Electrical Equipment(1000 Volts Maximum)[5] JIS D0203-1994 Method of moisture, rain and spray test for automobile[6] JIS D0207-1977 General rules of dust test for automobile parts。
大众标准清单
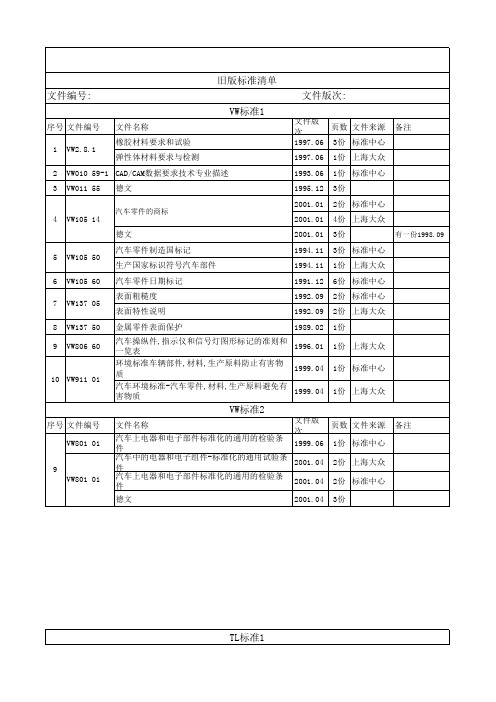
旧版标准清单
文件名称 用于汽车内饰件材料的油漆材料要求 在汽车内部装备材料上涂漆要求 德文 电镀铬塑料件材料要求 成型件的聚苯撑氧材料要求 泡沫胶带,双面粘贴的材料要求 聚丙烯车厢衬里:6个类型 德文
文件版次:
文件版 次
页数 文件来源 备注
1998.11 5份 标准中心
1998.11 1份 上海大众
文件版 次
页数 文件来源
1993.12 6份 标准中心
1993.12 2份 上海大众
1993.12 3份
1993.01 4份 上海大众
1993.01 1份 标准中心
备注
序号 文件编号 文件名称 1 DIN 53 505 橡胶,弹性体和塑料试验
DIN标准1
文件版 次
页数 文件来源 备注
1987.06 2份
1998.11 1份
1993.06 5份 标准中心
1987.11 7份 标准中心
1993.02 1份 标准中心
2002.05 1份
2002.05 1份
序号 文件编号 1 PV1303 2 PV 3900
PV标准1
文件名称 塑料膜,织物层氙弧同步曝光 检验规范-塑料薄膜,平幅织物氙弧灯连续照射 德文
汽车车厢内零部件气味试验
文件版 次
页数 文件来源
1999.06 1份 标准中心
汽车中的电器和电子组件-标准化的通用试验条 件
2001.04
2份 上海大众
汽车上电器和电子部件标准化的通用的检验条 件
2001.04 2份 标准中心
德文
2001.04 3份
备注26
2 TL528 3 TL520 13 4 TL520 18 5 TL523 88
元件检验规范

1范围电子元器件、器件和组件,在本规范中,均统称为电子元器件。
本规范主要针对汽车系统中所使用的电子元器件。
电子元器件的种类繁多。
就安装方式而言,目前可分为传统安装(又称通孔装即DIP)和表面安装两大类(即又称SMT或SMD)。
2目的确定了对设计、生产中所使用的电子元器件进行检验的一般方法和指导。
由于器件的种类繁多,应用目的不同,适用的试验方法上也有区别,具体可查阅相关标准。
3参考文件适合于微电子器件组件的试验检测标准:MIL-STD-883E美国国防部-微电子器件试验方法标准试验、检测方法及标准适用于军用及宇航用的,单片、多片、厚膜薄膜混合微电路、微电路阵列,以及构成微电路和阵列的各类元器件。
对于恶劣环境下的应用,也可以参考本标准对所用器件进行试验和检测。
适合于汽车电子器件的试验标准:VW80101:2005大众-汽车中的电气和电子组件通用试验条件。
GMW3172:2006通用工程标准-汽车电子器件的环境、可靠性、及性能要求符合性分析、开发及验证总规范。
MES PW67600:1995马自达工程标准-汽车器件试验标准。
主要检验标准有:GB/T5729—94《电子设备固定电阻器第一部分:总规范》;GB/T2693-2001《电子设备用固定电容器第1部分:总规范》;GB/T8554—1998《变压器和电感器测量方法及试验程序》;GB/T4023-1997《半导体器件分立器件和集成电路第2部分:整流二级管》;GB/T6571-1995《半导体器件分立器件第3部分:信号(包括开关)和调整二级管》;GB/T4587-94《半导体器件分立器件和集成电路第7部分:双极型晶体管》;GB/T4586-94《半导体器件分立器件第8部分:场效应晶体管》;GB/T15651.2-2003《半导体器件分立器件和集成电路第5-2部分:光电子器件基本额定值和特性》;GB/T15291-94《半导体器件第6部分晶闸管》;GB3442-86《半导体集成电路运算(电压)放大器测试方法的基本原理》;GB/T6798-1996《半导体集成电路电压比较器测试方法的基本原理》;GB/T4377-1996《半导体集成电路电压调整器测试方法的基本原理》;GB3439-82《半导体集成电路TTL电路测试方法的基本原理》;GB3834-83《半导体集成电路CMOS电路测试方法的基本原理》;GB/T14028-92《半导体集成电路模拟开关测试方法的基本原理》;GB3443-82《半导体集成电路MOS随机存储器测试方法的基本原理》;YD/T731-2002《通信用高频开关整流器》;YD/T1019-2001《数字通信用实心聚烯烃绝缘水平对绞电缆》;GJB128A-97《半导体分立器件试验方法》;GJB150-86《军用设备环境试验方法》;GJB360A-96《电子及电气元件试验方法》;GJB548A-96《微电子器件试验方法和程序》等。
德国大众 吨以下汽车电气和电子部件试验标准

共 94 页第1页LV 1243.5吨以下汽车电气和电子部件试验项目、试验条件和试验要求目录页适用范围第一部分:电气要求1 参考标准2 通用部分2.1 概念和定义2.2 扫描率和测量值分辨率2.3 工作电压范围2.4 功能状态2.5 工作方式2.6 参数试验2.7 用漂移分析法不间断监控参数2.8 物理分析2.9 接口说明2.10 实施的限制条件3 试验选择3.1 试验选择表4 电气试验和要求4.1 E-01 长时间过电压4.2 E-02 瞬态过电压4.3 E-03 瞬态欠电压4.4 E-04 Jumpstart(跃变启动)4.5 E-05 Load Dump(甩负荷)4.6 E-06 叠加的交流电压4.7 E-07 供电电压缓慢下降和缓慢提升4.8 E-08 供电电压缓慢下降快速提升4.9 E-09 复位特性4.10 E-10 短时中断4.11 E-11 启动脉冲4.12 E-12 具有智能发电机调整装置的电压波动波形4.13 E-13 插脚中断4.14 E-14 插头中断4.15 E-15 极性变换4.16 E-16 接地偏移4.17 E-17 信号线路和负荷电路短路4.18 E-18 绝缘电阻4.19 E-19 静止电流4.20 E-20 击穿强度4.21 E-21 反馈4.22 E-22 过电流第二部分:环境要求5 通用部分5.1 参考标准5.2 概念和定义5.3 工作方式5.4 渗透温度5.5 参数试验5.6 用漂移分析法不间断监控参数5.7 物理分析6 使用特性曲线6.1 寿命设计6.2 温度集中试验7 试验选择7.1 试验选择表7.2 试验流程图8 机械试验和要求8.1 M-01 自由落体试验8.2 M-02 碎石冲击试验8.3 M-03 防灰尘试验8.4 M-04 振动试验8.5 M-05 机械冲击试验8.6 M-06 机械持续冲击试验9 气候试验和要求9.1 K-01 高温 / 低温存放9.2 K-02 梯度温度试验9.3 K-03 低温工作9.4 K-04 再次油漆温度9.5 K-05 温度冲击试验(部件)9.6 K-06 盐雾喷射试验,在舱外工作情况下9.7 K-07 盐雾喷射试验,在舱内工作情况下9.8 K-08 湿热循环试验9.9 K-09 湿热循环试验(附霜冻)9.10 K-10 防水保护— IPX0至IPX6X9.11 K-11 高压射流清洗 / 蒸汽射流清洗9.12 K-12 有浪涌水的温度冲击试验9.13 K-13 浸入式温度冲击试验9.14 K-14 恒定湿热试验9.15 K-15 与部件组一起的凝露试验9.16 K-16 温度冲击试验(无外壳)9.17 K-17 阳光辐射试验9.18 K-18 有害气体试验10 化学试验和要求11 寿命试验11.1 L-01 机械 / 液压耐久寿命试验11.2 L-02 高温耐久寿命试验11.3 L-03 温度交变耐久寿命试验12 附录12.1 试验流程图12.2 各种安装范围的典型温度集中试验12.3 高温耐久寿命试验计算模型12.4 温度交变耐久寿命试验计算模型12.5 恒定湿热试验计算模型—锐度212.6 凝露试验、试验箱程序设计和曲线12.7 汇总适用范围本标准是对3.5吨以下汽车使用的电气、电子、机械电子部件和系统试验项目、试验条件和试验要求的规定。
一汽-大众VI(01)

12
基础系统
> 2.2 标识组合规范
注: 以上字体,如何使用参见公司应用系统。
11
2.2
标识组合规范
一汽-大众公司标识与名称经过严格组合,形成统一的规范形式,以下的内容提供 了这些组成部分的信息和数字模板的应用模式,规范了如何在应用时确保统一。
2.2
标识组合规范
12 13 15 16 17
2.2-1 标识与中英文简称组合 2.2-2 标识的不可侵犯空间 2.2-3 Das Auto. 标识组合规范 2.2-4 Das Auto. 标识不可侵犯空间
线稿版本
只有当采用平版印刷或数字印刷必将有损图像质量时,才使用线稿版本。 线稿版本适用丝网刺绣、压花、雕刻、蚀刻、轧压、激光作用和喷沙(例如宣传 材料)等用途。
线稿在黑底上的版本(颜色为白色)
线稿在白底上的版本(颜色为黑色)
08
基础系统
> 2.1 标识基本要素规范
2.1-2 标识文字要素规范
一汽 - 大众在信息传播中使用自己公司的字体。这些字体突出品牌标识,强调 一汽-大众汽车品牌的特色。 中文字体采用一汽-大众专用字体,英文字体采用 VW 专用字体。可用于创作专 业印刷品。 颜色以80%K为主。 中文名称字体:汉仪综艺变体字 字体颜色: 80%K C:0 M:0 Y:0 K:80
第四部分:经销商应用系统 通过标注标识及数字辅助方法和设计规则,将明确从广告传播物料、经销商店头 物料到文宣品等各方面的设计规范,明确一汽-大众授权经销商在广告创意及宣传 中,如何正确使用一汽-大众品牌形象元
果断
明确
开放
富
价值
于 创
追求
新
人
Das Auto.
德国大众3.5吨以下汽车电气和电子部件试验标准
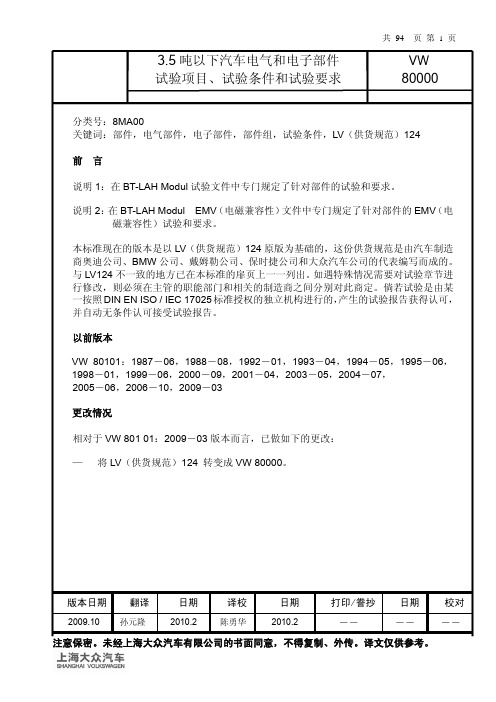
VW 80101:1987-06,1988-08,1992-01,1993-04,1994-05,1995-06, 1998-01,1999-06,2000-09,2001-04,2003-05,2004-07, 2005-06,2006-10,2009-03
更改情况
相对于 VW 801 01:2009-03 版本而言,已做如下的更改:
表 6:标准允差定义
2.1.6 标准值
如果没有另外规定的话,适用表 7 的标准值。
室温 空气湿度 试验温度 标称电压 工作电压(用于试验)
TRT=23℃±5℃ Frel=45%-75%RH T Prüf=TRT UN=12V UB=14V
表 7:标准值定义
2.2 扫描频率和测量值分辨率
测量系统的扫描频率抑或带宽必须与各种试验匹配。必须记录所有带最大值(峰值)的测 量值。
存储器功能必须在任何情况下始终保持在 A 功能状态下。必须随时保证非易失存储器的 完整性(不是及时性)。
必须在部件设计任务书中说明功能状态的时间流程。
必须与委托方协调和规定允许的故障存储器项目。
2.4.1 功能状态 A
试件在加载试验参数期间和之后必须满足预先规定的所有功能。
说明:在与设计功率有偏差时(功能受到高温或者低温限制),试件亦必须达到低于抑或 高于工作电压情况下的功能状态 A,如果工作电压在部件设计任务书中说明是允许的话 (Derating)。
共 94 页 第 4 页
VW80000:2009-10
12 12.1 12.2 12.3 12.4 12.5 12.6 12.7
附录 试验流程图 各种安装范围的典型温度集中试验 高温耐久寿命试验计算模型 温度交变耐久寿命试验计算模型 恒定湿热试验计算模型 — 锐度 2 凝露试验、试验箱程序设计和曲线 汇总
(完整版)汽车扬声器成品检验要求规范2013.8.29G版

天津中环真美音响科技有限公司J01-002汽车扬声器成品检验规范天津中环真美音响科技有限公司J01-002页成品检验外观、纯音抽验方案天津中环真美音响科技有限公司J01-002 汽车扬声器成品检验规范天津中环真美音响科技J01-002 汽车扬声器成品检验规范天津中环真美音响科技J01-002 汽车扬声器成品检验规范天津中环真美音响科技J01-002 汽车扬声器成品检验规范天津中环真美音响科技J01-002 汽车扬声器成品检验规范页汽车扬声器成品检验规范G版周期试验(MES PA 66960)第 11 页天津中环真美音响科技J01-002 汽车扬声器成品检验规范汽车扬声器成品检验规范汽车扬声器成品检验规范天津中环真美音响科技J01-002 汽车扬声器成品检验规范天津中环真美音响科技J01-002 汽车扬声器成品检验规范汽车扬声器成品检验规范天津中环真美音响科技J01-002汽车扬声器成品检验规范G版周期试验(MES PA PT001)第 18 页组别试验项目试验条件判据抽样数试验周期备注尺寸、外观、性能检查按逐批检查要求Ac=0 5 1次/年1 短期耐热性5min内由20℃±5℃升到95℃±2℃,存放5小时后,再在5min内降至到20℃±5℃,在存放2小时,重复2次,试后评估:间隙和平齐:MAX0.5mm;表面波纹:2—3mm;表面皱纹:不允许;灰度污点:无污点;外观:不允许有剥离、偏移、膨胀;颜色:不允许有褪色、光泽变化;表面状态:模糊、表面变粘、软化和硬化。
182 长期耐热性90±2℃保持72小时,然后取出,放置室温2小时。
试后评估:间隙和平齐:MAX0.5mm;表面波纹:2—3mm;表面皱纹:不允许;灰度污点:无污点;外观:不允许有剥离、偏移、膨胀;颜色:不允许有裉色、光泽变化;表面状态:模糊、表面变粘、软化和硬化3 耐寒性-40±2℃,存放4小时,评估零件的形状和尺寸外观,从恒温室内取出,不接触它放置2小时。
VW2.8.1__2003中文版

>200
-
-
-
-
-
-35
-35
-35
-35
-35
-35
-35
VW 2.8.1:2003-11
共 12 页 第 5 页
9
耐臭氧性
3.9
10
光稳定性
3.10
11
气候稳定
3.10
性
12
油漆均匀
3.12
性 VDA
675 219
13
回跳特性
% VDA
675 219
14
绝缘电阻
无裂纹,当图中补充“耐臭氧性”描述时。 相对供货状态无改变,例如:颜色,变脆,分解,裂纹。 除了要求质量 G,仅当图中补充“光稳定性”描述时要求。 相对供货状态无改变,例如:颜色,变脆,分解,裂纹。 当图中补充“气候稳定性”描述时,除了要求质量 G。 无形成光环状,无退色效果,允许有轻微接触变色现象。 仅在当图中补充“油漆均匀性”描述时要求。
-35
-35
-35
-35
-35
无裂纹,当图中补充“耐臭氧性”描述时。 相对供货状态无改变,例如:颜色,变脆,分解,裂纹。 除了要求质量 G,仅当图中补充“光稳定性”描述时要求。 相对供货状态无改变,例如:颜色,变脆,分解,裂纹。 除了要求质量 G,仅当图中补充“耐气候性能”描述时要求。
VW 2.8.1:2003-11
与本标准存在偏差的试验条件必须在图纸和试验报告中说明。
3.1 试验体
按照 VDA 675 205,试验在标准试棒 S3A 上进行,试棒必须取自制成品。在相应的制成 品直径(例如:径向轴密封圈)上也可以用标准试棒 S3。特殊情况下,如果用一台条刀 纵割机器无法从制成品上取出所需要的试棒的话,允许使用试验板(厚度 2 mm)。
大众通用材料标准版本日期明细清单

213
VW_2_8_1_2011-02_EN
214
VW_2_8_1_Englisch_2010-12-01
215
VW_50180(中文版)_辐射性状-2007-12
216
VW_50185(中文版)_露天抗老化性-2000-10
218
大众_TL52231中文版2004年发布
219
大众TL52388内饰PP材料标准-中文版
137
QK002700-2008
138
QK003800_PP、PE带填料的聚丙烯均聚物和共聚物-1997
139
QK004000_Blend from PP and EPDM with fillers-2005
140
QK005100-2007
141
QK006600_PBT-GB聚饱和酯材料性能及要求-2007
142
QK 001260-2007
143
QK 001825-2008
144
QK 002600-2007
145
QK 002900-2007
146
SAE J200-2003(中文版) 橡胶材料分类体系标准
147
SCHULAMID 6 MV5
148
SES A 100_2003_En
149
SES E 150-01_1991_En
190
VW10540-4-07.89(中文)
191
VW10540-5-89.11(中文)
192
VW10540-6-02.91(中英对照)
193
VW10540-7-06.99
194
VW10560_ch_12.1991
195
汽车电气VW80101_091101_和电子部件一般试验条件_中文版

在对应的试验中所要求的功能和试验条件�要始终加以监控并编制成文件�至少要有温度、 供电电压�如果涉及的话�还有开关特性、电压降、负荷电流、静止电流、总线帧�包括 时间和内容�等等�。
如果试验没有说明严苛程度�就必须以标准要求为基础。
VW 80101 标准预先规定了各项试验要求有关温度、抗振动能力和密封性能方面的数 值。如根据安装情况而发生偏差�则应将这种不一致的情况编写在设计任务书上。
汽车电气和电子部件
一般试验条件
共 59 页 第 1 页
VW
80101
分类号�8MA00 关键词�部件、电气部件、电子部件、试验条件
以前版本
VW 80801�1987�06�1988�08�1992�01�1993�04�1995�06�1998�01� 1999�06�2000�06�2000�09�2001�04�2003�05�2004�07� 2005�06�2006�10�2009�03
共 59 页 第 2 页
页 3 3 4 5 6 9 9 10 11 11 11 12 12 15 17 17 18 19 20 20 21 21 22 23 24 25 26 26 27 27 27 37 38
VW 80101�2009-11
4.4 压接和插接 4.5 汽车中电气部件和电子部件的接插连接 4.6 导线抗拉强度 5 气候要求 5.1 恒定温度下的试验 5.2 交变温度下的试验 5.3 梯度温度试验 5.4 大气曝晒耐抗性 5.5 环境耐抗性 5.6 水温突变试验 6 化学要求 6.1 对化学品的耐抗性 7 耐久性试验 7.1 对电气和电子系统/部件的耐久性试验 7.2 对电子机械系统/部件的耐久性试验 7.3 针对零件特殊的耐久性试验 8 共同适用的资料
大众实验要求VW80101 中

汽车中的电气和电子组件通用试验条件关键词:组件,电气组件,电子组件,试验条件目录1 适用范围2 概述2.1 规则和试验顺序2.2 定义2.3 汽车部件的要求范围和其对车辆的要求方式2.4 材料要求2.5 工作方式2.6 功能状态2.7 通用试验条件3 电气要求3.1 工作电压3.2 反馈3.3 电平:高-低端配置3.4 过压和电压不足下的功能3.5 静态电流记录3.6 工作电流3.7 防电极反接3.8 过流耐抗性3.9 长时过载耐抗性3.10 短时过载耐抗性3.11 叠加的交变电压3.12 供电电压的缓慢降低和升高3.13 电压中断情况下的复位性能3.14 短接耐抗性3.15 击穿耐抗性3.16 绝缘电阻3.17 断路3.18 电降压3.19 电磁兼容性(EMV)4 机械要求4.1 振动4.2 机械振动4.3 落体试验4.4 卡接和插接4.5 车辆中电气和电子组件的插接接头5 气候方面的要求5.1 恒定温度下的试验5.2 交变温度下的试验5.3 大气曝晒试验耐抗性5.4 环境耐抗性5.5 温度突变6 化学要求6.1 试剂耐抗性6.2 发动机清洁剂耐抗性7 耐久性试验7.1 零件耐久试验7.2 电气和电子系统/部件耐久性试验7.3 电气机械系统/组件耐久性试验8 表格9 参考资料更改:对VW 801 01:2003-05的版本作了如下更改:-章节2.3,车辆的要求范围和要求方式图1:第8部分增加了“中间隧道”。
-表格2要求范围和其要求方式防尘和防喷溅水密封性的要求中对于前部区域(内/外),发动机舱,发动机附件,水箱,底盘,车顶,前盖外板附件,变速器附件和已脱落进气管的保护方式改为IP 5K9K。
增加了章节:对于安全性重要的部件适用:防尘和防喷溅水密封性要在任务书中进行定义-如果表格2中的说明不足的话。
如果试件可以在水下直立,就使用防护方式IP 68(如门和盖罩,脚踏空间,水箱,被子架,抽屉内侧)。
VW80102_200906_en

Electrical Controls (Switches, Tip Switches)General RequirementsPrevious issuesVW 80102: 1990-10, 1992-09, 1995-05ChangesThe following changes have been made as compared to VW 80102: 1995-05:–Standard completely revised ContentsPageScope .............................................................................................................................2Requirements .................................................................................................................2General requirements ....................................................................................................2Haptic characteristics, appearance, and styling (symbol and illumination) ....................2Haptic appearance and switching noise ........................................................................2Acoustics ........................................................................................................................2Appearance ....................................................................................................................3Symbols .........................................................................................................................3Styling ............................................................................................................................3Illumination .....................................................................................................................4Applicable laws and regulations .....................................................................................4Documentation ...............................................................................................................4Greasing ........................................................................................................................5Definitions ......................................................................................................................5Tip switches ...................................................................................................................5Switches .........................................................................................................................5Actuations ......................................................................................................................5Actuation forces, actuation torques, switching paths, and actuation angles (5)122.12.22.2.12.2.22.2.32.2.42.2.52.2.62.32.42.52.62.6.12.6.22.6.32.7Group StandardVW 80102Issue 2009-06Class. No.:8MC10DDescriptors:switch, tip switch, controlsCheck standard for current issue prior to usage.This electronically generated standard is authentic and valid without signature.The English translation is believed to be accurate. In case of discrepancies the German version shall govern.Numerical notation acc. to ISO practice.Page 1 of 11Technical responsibility Standards Department EEFH Manfred Hintz Tel.: +49-5361-9-31274I/EE-61Uwe GirgsdiesTel.: +49-841-89-90836EKTC/4 Dirk Beinker EKTCTel.: +49-5361-9-32438Manfred TerlindenConfidential. All rights reserved. No part of this document may be transmitted or reproduced without prior permission of a Standards Department of the Volkswagen Group.Parties to a contract can only obtain this standard via the B2B supplier platform .© Volkswagen AktiengesellschaftVWNORM-2008-12hPoint of force application ................................................................................................5Switching safety .............................................................................................................6Materials ........................................................................................................................6Robust design requirements ..........................................................................................6Burning behavior ............................................................................................................7Plug-in connections ........................................................................................................7Self-heating ....................................................................................................................7Switching currents ..........................................................................................................7Voltage drop at the switching contact ............................................................................7Overcurrent strength ......................................................................................................8Switching point ...............................................................................................................8Removal force ................................................................................................................8Contact mats ..................................................................................................................8Electrical signal transmission .........................................................................................8Electrical controls ...........................................................................................................8Emergency light switch ................................................................................................10Test requirements ........................................................................................................10Misuse requirement for tip switches .............................................................................10Continuous current requirement for load isolators .......................................................10Continuous current requirement for fan switches ........................................................10Referenced documents ................................................................................................102.82.92.102.10.12.10.22.112.122.132.142.152.162.172.182.192.19.12.19.22.202.20.12.20.22.20.33ScopeThis standard defines the general requirements for switches and tip switches with a maximum oper‐ating voltage of 30 V and a maximum current of 30 A.Requirements General requirementsApproval of first supply and changes according to Volkswagen standard VW 01155.Switch styling and geometric requirements as well as the tolerances are to be taken from the drawing.The requirements specified in VW 80101 apply.Haptic characteristics, appearance, and styling (symbol and illumination)Haptic appearance and switching noiseHaptics is defined as the active sensing of e.g. size, contour, surface texture, weight, etc. of an object.The sound emission and the actuation sensing must be agreed upon with the responsible design engineer and the responsible engineering departments and must be documented by means of ref‐erence samples.AcousticsThe noise resulting from the actuation of switch elements is to have the same sound as the adjacent switching elements. The acoustics must be agreed upon with the engineering departments.12 2.12.2 2.2.12.2.2Page 2VW 80102: 2009-06DAppearanceThe appearance of vehicle control elements is influenced by material, form, tilt, color, surface, sym‐bols, and illumination. Illumination is not part of this document and is dealt with separately.SymbolsAcc. to VW 80660 and specifications in the drawing.Utilization resistance acc. to Technical Supply SpecificationTL 226.Test of resistance to creams and lotions acc. to PV 3964.StylingThe class-A surfacing is a graphical representation, based on the representative geometry. The class-A surfacing is a form-defining process from the styling point of view, if only some volume-defining plane, vertical, or parallel cross-sections are given.Compliance with the class-A surfacing data defined by the purchaser is mandatory for all surfaces visible in the passenger compartment.Modifications to class-A surfaces are permissible only if they are approved in the class-A surfacing process in consultation with the Styling Department.The trim styling will be defined by the purchaser in the framework of a partial data control model (DKM), in cooperation with Styling.This styling process must be accompanied by the contractor by means of continuous checks whether this is technically realizable.The contractor must be present in respective agreement meetings. Furthermore, the contractor must conduct tests regarding the fulfillment of the legal regulations concerning curvature radii or button heights (ECE-R 21 and 74/6/EWG head impact) accompanying the styling process.Prior to submission of the quotation, the supplier must request the current styling status from the engineering department.Components with external visual function elements must be designed so that operation, even under extreme conditions (e.g. soiling), does not result in functional impairment.The gap contour must comply with the class-A surface specifications and be consistent all around.The different gaps within a device must be harmonious.The following specifications (see Figure 1) are binding during the design of the tool separation and the draft angles for tip switch caps and trims.2.2.32.2.42.2.5Page 3VW 80102: 2009-06DFigure 1Legend 1Tip switch cap2Gap acc. to class-A surfacing specifications3Tool separation of the switch cap on the radius runout 4Trim5Tool separation of the trim on the radius runout 6Draft anglesThe tools are initially designed to the upper tolerance limit of the gap size, afterwards the tools are matched by means of the interior master jig on off-standard production tool parts of the trim.During tip switch actuation, the effective gap is increased. This prevents jamming of the tip switch.IlluminationThe illumination must be agreed upon with the responsible design engineer and the responsible engineering departments and must be documented by means of reference samples. All controls in the vehicle together must form a harmonious illumination.Acc. to specifications by the purchaser, laser technology must be used for illumination of the tip switch lettering and symbols.Applicable laws and regulationsThe respective country-specific laws and regulations must be adhered to.DocumentationSections marked with a documentation bar are subject to mandatory documentation.The documents must be archived for a duration of 15 years.2.2.62.32.4Page 4VW 80102: 2009-06DGreasingElectrical switches must not be greased.If this regulation is derived from, the grease to be used, the application type, and the amount of grease must be agreed upon with the responsible engineering department and the Central Laboratory and must be implemented in a process-reliable manner.DefinitionsThe following applies to tip switches as well as to switches: Changing the physical input variable results in a change of the digital output signal (step function).Representation of electrical switch contacts (switches and tip switches):The switch contact symbol (closing or opening) is represented in unactuated state. The designation of the represented switch contact refers to the function to be triggered.Tip switchesA tip switch is defined as an electrical switching element (closer or opener) which performs an elec‐trical switching operation when an actuation force is applied to the actuation switch, and which returns to its normal position when released (mechanically and electrically).SwitchesA switch is defined as an electrical switching element (closer or opener) that can assume different switch positions.ActuationsTip switches and switches can be actuated directly by the operator or indirectly by physical control variables.Actuation forces, actuation torques, switching paths, and actuation anglesThe main variables acting for switching elements are actuation force and actuation path. These vari‐ables form the load-displacement curve. The load-displacement curve is part of the drawing.All switching points (actuation paths and actuation angles as well as actuation forces and actuation torques) must be indicated in the drawing, including tolerances.Latch switches may latch only in the respective positions. Intermediate positions between the latching positions are not permissible. When switched, no latches may be skipped.Misuse forces must be agreed upon with the responsible engineering department and stipulated in the drawing.The actuation forces are measured in as-received condition as well as after the tests and may not exceed the tolerance limits after the endurance test.Point of force applicationThe point of force application and the actuation direction are defined in the drawing or the Perfor‐mance Specifications. For toggle and rocker switches, the force is applied perpendicular to the ac‐tuation surface. In order to ensure perpendicular force application, an adapter or a test prod must be used for force application in the case of a tilted or uneven actuation surface.2.52.62.6.12.6.22.6.32.72.8Page 5VW 80102: 2009-06DSwitching safetyWhen actuating latch switches, the defined positions must be assumed automatically after overcom‐ing the action point.Intermediate positions are not permissible.If the switch is actuated by an angle or path and if it does not reach the switching point defined in the drawing, it must automatically return to the original latching position.Micro switches or their housings must not be used as a stop of the actuation movement or be damaged when the actuation is finished.During actuation, the switching point must be traveled with sufficient follow-on.It must be ensured that the switch is not used as a limit stop. Lever or spring systems must be used,if necessary.When actuation cams are used, switching safety must be agreed upon with the responsible engi‐neering department.The distance to the switching point must be selected in each switching position such that vibrations or relative movements of the switch do not result in unintended switching.Manufacturing and movement tolerances of the parts must be sufficiently considered in the actuation chain.MaterialsOdors or other evaporations according to VW 50179 und VW 50180.Suitable material combinations with respect to friction behavior, joint strength (two components) and their compatibility must be considered. This also applies to materials that form the installation envi‐ronment of the part.All surfaces visible in their installed condition must be free of sinkmarks, faults, dust inclusions, dirt,scratches, etc. Sink marks, e.g. behind reinforcement ribs or their intersections are only permissible if the part's appropriate functionality and the external appearance are not affected.Voids are not permissible.The materials sliding against each other during actuation must be mirror polished and free of paint in the tool.Tool separations are not permissible, neither in the visible area nor in the functional area.Housing and retainer must not have any sharp edges (risk of injury, shearing or damage to lines during installation and operation). ECE-R-21 must be complied with for edge and radii design.All materials used must be ozone-resistant.Robust design requirementsForeseeable misuse must not result in damage of the part, its material, or the part environment.The minimum misuse force/misuse torque requirements are 250 N and 2 Nm.Specific requirements resulting from the packaging space must be considered.Functional components (tip switch guides, wall thicknesses, etc) must be designed such that - in installed condition (with pre-tension by means of catch springs) over the entire temperature range and over the vehicle service life - no deformations occur that could impair the function.2.92.102.10.1Page 6VW 80102: 2009-06DBurning behaviorThe burning behavior must correspond to the requirements of TL 1010.Plug-in connectionsPlug-in connections on switches or their assemblies must be designed acc. to VW 80106.The plug and pull forces on the housing-mounted connector must be absorbed by the housing. Ap‐plication of force to the PCB is impermissible.Intrusion of water must be excluded. In special cases, a sealed plug connection must be used. The part must be equipped with a push-on-connection released within the Volkswagen Group.Device connector receptacles and connectors on the device must be marked in the plastic.Connector housings and contacts must form a unit in order to ensure correct positioning of the plug contact when plugging the mating connector.The contractor must ensure that the connector contacts are not deformed.When the part is carried at the line during handling, e.g. during vehicle assembly, the part and the line connection must not be damaged. The specification regarding the pull-out-strength can be taken from the drawing.Connecting plugs on PCBs must be mechanically attached.Connector pins must be manufactured acc. to the following drawings (see Table 1):Table 1Connector width (mm)Drawing no.0,63N 905 2851,5N 905 8542,8N 905 8564,8N 905 8576,3N 905 8589,5N 905 859Self-heatingIf self-heating occurs due to energy conversion in the switch unit, the maximum surface temperature to be reached must be agreed upon with the responsible engineering department and be documented.Switching currentsSwitching currents up to 60 mA are called control currents. A typical value is 20 mA, ohmic load.Switching currents (rated current) of 60 mA to 30 A are called load currents.Switching currents (rated current) ≥ 30 A must be switched by means of relays. See VW 80932.Voltage drop at the switching contactThe permissible voltage drop must not exceed 100 mV for a rated current of 10 A.2.10.22.112.122.132.14Page 7VW 80102: 2009-06DThe permissible voltage drop must not exceed 60 mV for rated currents larger than 10 A.The permissible voltage drops via the switching contact must not be exceeded over the entire service life. The voltage drop must always be measured between connector input and output. In order to determine the actual switching resistance, additional resistances must be deducted. Several contacts connected in series may cause additional voltage drops. This additionally generated heat must not result in damage of the switch unit and the increased total voltage drop must not result in damage of the overall circuit. These deviations must be agreed upon with the responsible engineering depart‐ment.For switches with cable connection, the voltage drop must be measured for the cable or be calculated on the basis of the specific resistance, the cable diameter and the cable length. The voltage drops via the connecting cable must be deducted from the measured values.For circuit breaking controls, the minimum permissible contact force must be agreed upon with the engineering department and be documented in the drawing.Overcurrent strengthFor design of controls with vehicle fuse connected on line side see VW 80101.Switching pointSwitches that rest in a defined position over a longer time period should be open in this position.The switching point must be defined and documented.The switching point must not change.Removal forceThe removal force of housing parts of control components must be larger than 250 N.Contact matsContact mats must permanently contact in a reliable way.The voltage drops must be documented over the entire endurance test.The permissible changes in haptic characteristics over the service life and when exposed to high temperatures must be agreed upon with the "Haptic Characteristics" team.No mechanical changes (damages or plastic deformation) must occur.In the case of non-vertical actuation, secure contacting must be ensured.Electrical signal transmissionAn integrated device connector or separated cables with coupling are used for electrical connection.Electrical controlsTable 2 shows the number of switching operations and load for which the function and the specified parameters must be guaranteed.There are two types of load: control current and load current. They are differentiated by means of power consuming devices connected on load side.2.152.162.172.182.192.19.1Page 8VW 80102: 2009-06DPage 9VW 80102: 2009-06D Table 2a)Controls that are not mentioned must be agreed upon with the engineering department with regard to actuation frequency and load.b)If lamp loads are used as the type of load, a cooling time of at least 10 s between the switching cycles must be complied with.Alternatively, cooled lamps must be used. Vehicle-specific loads (original loads) must be used.Emergency light switchTable 3 shows the number of switching operations and the load for the emergency light switch for which the function and the specified parameters must be guaranteed.Table 3SwitchesNumber of switching operations (applies to load currents andcontrol currents)Load(only for load isolators;control currents acc. to thedrawing)Emergency light switch25 0006 x 21 WContinuous current requirement for emergency light switchesEmergency light switches must withstand 1 h of permanent flashing at nominal load without functional impairment.Test requirementsMisuse requirement for tip switchesThe tip switch must be capable of resiling from the final position to the initial position without functional impairment and impairment of the specified parameters.Continuous current requirement for load isolatorsLoad isolators must withstand 8 h of continuous current at nominal load according to the drawing without functional impairment.Continuous current requirement for fan switchesFan switches must withstand 1 h of continuous current in the highest stage (load) and the highest operating temperature without functional impairment.Referenced documentsThe following documents cited in this standard are necessary for application.In this Section terminological inconsistencies may occur as the original titles are used.┌2.19.2┐ 2.19.2.1 2.20 2.20.12.20.22.20.33Page 10VW 80102: 2009-06DPage 11VW 80102: 2009-06D Standards with the titles given in German are either only available in German or may be procured in other languages from the institution issuing the standard.PV 3964Surfaces in the Passenger Compartment; Testing of Cream Resistance TL 1010Materials for Vehicle Interiors; Burning Behavior; Material Requirements TL 226Paint Coating on Materials; Used in the Vehicle Interior Trim; Require‐mentsVW 01155Vehicle Supply Parts; Approval of First Supply and ChangesVW 50179Emission Behavior of Components in the Passenger CompartmentVW 50180Components in the Passenger Compartment; Emission BehaviorVW 80101Electrical and Electronic Assemblies in Motor Vehicles; General Test Con‐ditionsVW 80106Plug Connection on and in Electrical and Electronic Components in Vehi‐cles; RequirementsVW 80660Symbols for Operating Devices, Display Units and Indicator LightsVW 80932Relays; Functional Requirements。
- 1、下载文档前请自行甄别文档内容的完整性,平台不提供额外的编辑、内容补充、找答案等附加服务。
- 2、"仅部分预览"的文档,不可在线预览部分如存在完整性等问题,可反馈申请退款(可完整预览的文档不适用该条件!)。
- 3、如文档侵犯您的权益,请联系客服反馈,我们会尽快为您处理(人工客服工作时间:9:00-18:30)。
Q U E L L E : N O L I S5.3Freibewitterungsbeständigkeit (31)5.4Umweltbeständigkeit (31)5.5Schwallwasser / Thermoschock (33)6Chemische Anforderungen (36)6.1Beständigkeit gegen Reagenzien (36)6.2Beständigkeit gegen Motorreinigung (37)7Dauerversuch (37)7.1Teilespezifischer Dauerversuch (37)7.2Dauerversuch für elektrische und elektronische Systeme/Komponenten (37)7.3Dauerversuch für elektromechanische Systeme/Komponenten (40)8Tabelle (42)9Mitgeltende Unterlagen (43)ÄnderungenGegenüber der VW 801 01: 2001-04 wurden folgende Änderungen vorgenommen:─Norm komplett überarbeitetFrühere Ausgaben1987-06; 1988-08; 1992-01; 1993-04; 1994-05; 1995-06; 1998-01; 1999-06; 2000-09; 2001-041 AnwendungsbereichDiese Norm legt allgemeine Prüfbedingungen für elektrische, elektromechanische und elektroni-sche Komponenten/Systemen in Kraftfahrzeugen fest.Bei Verwendung dieser Norm in teilspezifischen Technischen Lieferbedingungen, Zeichnungenund Lastenheften ist Tabelle 23 (Abschnitt 8) zu verwenden und in Absprache mit den zuständigenFachabteilungen um die entsprechenden Angaben zu ergänzen.Anforderungen2 AllgemeineDie Anforderungen gelten für den gesamten Betriebsspannungs- und Betriebstemperaturbereich.Die in der jeweiligen Prüfung geforderten Funktionen und Prüfbedingungen sind permanent zuüberwachen und zu dokumentieren (mindestens Temperatur, Versorgungsspannung und falls zu-treffend Schaltverhalten, Spannungsfälle, Lastströme, Ruhestrom, Busbotschaften inklusiveTiming und Inhalt, usw.)Fehlt die Angabe der Prüfschärfe, sind die normalen Anforderungen zugrunde zu legen.Zeichnungsanforderungen und Angaben in Lastenheften haben gegenüber den teile-spezifischen Technischen Lieferbedingungen Vorrang.Anforderungen in teilespezifischen Technischen Lieferbedingungen haben gegenüberder VW 801 01 Vorrang.Zeichnungsanforderungen, Angaben in Lastenheften und in teilespezifischen Techni-schen Lieferbedingungen beziehen sich grundsätzlich auf konditionierte Komponen-ten/Systeme.2.1 Festlegungen und PrüfreihenfolgeTabelle 1– Prüfung nach VW 801 01Die Prüfreihenfolge ist einzuhalten.Benennung Angabenaus VW 801 01Werkstoffgebrauchstemperatur Grenzwerte siehe LagertemperaturBetriebsspannung siehe Abschnitt 3.1Betriebstemperatur siehe Abschnitt 2.3Lagertemperatur siehe Abschnitt 2.3Durchführung der Prüfungen nach VW 801 01Prüfungsbenennung Angaben beiPrüfungen nachVW 801 01Jedes Teil, jeder Prüfling muss alle Prüfungen in der nachstehenden Reihenfolge erfüllenKonditionierung (Umluftlagerung unbelastet) siehe Abschnitt 5.1.1Werkstoffanforderungensiehe Abschnitt 2.4Crimp- und Steckverbindungen siehe Abschnitt 4.4Steckanschluss an Elektrik- und Elektronik-Komponenten im Kfz siehe Abschnitt 4.5Betrieb bei niedrigen Temperaturen siehe Abschnitt 5.1.2Betrieb bei hoher Temperatur siehe Abschnitt 5.1.3Temperaturwechsel mit festgelegter Änderungs-geschwindigkeit siehe Abschnitt 5.2.1Spannungsfällesiehe Abschnitt 3.18Leitungszugfestigkeitsiehe Abschnitt 4.6Überstromfestigkeitsiehe Abschnitt 3.8Überspannungsfestigkeit Langzeitbetrieb siehe Abschnitt 3.9Überspannungsfestigkeit Kurzzeitbetrieb siehe Abschnitt 3.10Überlagerte Wechselspannung siehe Abschnitt 3.11 Langsames Absenken und Anheben der Versor-gungsspannung siehe Abschnitt 3.12 Kurzschlussfestigkeitsiehe Abschnitt 3.14 Durchschlagfestigkeitsiehe Abschnitt 3.15 Isolationswiderstandsiehe Abschnitt 3.16 Dauerschockprüfung für Systeme/Komponentenin Türen und Klappen siehe Abschnitt 4.2.1 Mechanische Schock-Prüfung für Syste-me/Komponenten an der Karosserie siehe Abschnitt 4.2.2 Schwingfestigkeitsiehe Abschnitt 4.1 Dauerversuchsiehe Abschnitt 7 Nachfolgende Prüfungen können nach der Konditionierung (Umluftlagerung unbelastet) parallel durchgeführt werden.Nahentstörung nach TL 965 Siehe Abschnitt 3.19.2 Leitungsgebundene Störungen nach TL 820 66 Siehe Abschnitt 3.19.1 Eingestrahlte Störungen nach TL 821 66 Siehe Abschnitt 3.19.3EMV auf Sensorleitungen nach TL 823 66 siehe Abschnitt 3.19.1.3Immunität gegenüber ESD nach TL 824 66 siehe Abschnitt 3.19.4 Unterbrechungensiehe Abschnitt 3.17Funktion bei Unter- und Überspannung siehe Abschnitt 3.4 Verpolsicherheitsiehe Abschnitt 3.7Rückspeisungsiehe Abschnitt 3.2 Spannungspegel: Zuordnung HIGH-/LOW-Zustand siehe Abschnitt 3.3 Betriebsstromsiehe Abschnitt 3.5 Ruhestromaufnahmesiehe Abschnitt 3.6 Resetverhalten bei Spannungseinbruch siehe Abschnitt 3.13Staub- und Spritzwasserdichtheit nachDIN 40 050-9 siehe Abschnitt 5.4.1Feuchte Wärme, zyklisch siehe Abschnitt 5.4.2Salzsprühnebelsiehe Abschnitt 5.4.3Beständigkeit gegen Reagenzien siehe Abschnitt 6.1 Motorreinigungsiehe Abschnitt 6.2 Thermoschocksiehe Abschnitt 5.5 Temperaturschockprüfungsiehe Abschnitt 5.2.2Falltestsiehe Abschnitt 4.3 Freibewitterungsbeständigkeit siehe Abschnitt 5.32.2 Definitionen2.2.1 BegriffeSystem Funktionell verknüpfte Komponenten, z. B. ABS-System, ESP-System. Komponente Teil eines funktionell verknüpften Systems, z. B. Aktor, Sensor, Steuergerät. Prüfling Das zu prüfende System oder die zu prüfende Komponente.Funktionen Beinhalten systemspezifische Funktionen und Diagnosefunktionen.2.2.2 AbkürzungenI N Nennstrom T NHDie Nachheiztemperatur ist die maximale Umgebungstemperatur, die nach demAbstellen des Fahrzeuges im entsprechenden Anforderungsbereich (siehe Tabel-le 2) entsteht.T oLDie obere Lagergrenztemperatur ist die höchste Umgebungstemperatur, die bei Lagerung oder Transport des Prüflings zulässig ist. Sie beinhaltet z. B. Lacktrock-nung und Stauwärme im Motorraum. Der Prüfling wird nicht betriebenT RT Raumtemperatur (23 ± 5) °C. Dies ist die Prüftemperatur, wenn nicht abweichend angegeben.T uB , T oBDie untere bzw. obere Betriebsgrenztemperatur ist die niedrigste bzw. die höchste Umgebungstemperatur, bei der der Prüfling dauerhaft betrieben werden darf. Ei-generwärmung bleibt unberücksichtigt.T uLDie untere Lagergrenztemperatur ist die niedrigste Temperatur, die bei Lagerung oder Transport des Prüflings zulässig ist. Der Prüfling wird nicht betrieben.U Bmax Maximale Betriebsspannung, bei der der Prüfling dauerhaft betrieben werdendarf.U Bmin Minimale Betriebsspannung, bei der der Prüfling betrieben werden darf. U N NennspannungU PAPrüfspannung bei laufendem Motor. U PB Prüfspannung bei Batteriebetrieb. U PC Prüfspannung für verpolten Anschluss einer Batterie beim Fremdstart. 2.3Anforderungsbereiche und deren Anforderungsarten für Fahrzeuge12 FahrwerkBild 1 – AnforderungsbereicheSeite 6VW 801 01: 2003-05 Tabelle 2 – Anforderungsbereiche und deren Anforderungsarten2.4 WerkstoffanforderungenDer Prüfling muss frei von Fehlern sein.Kunststoffteile müssen den jeweils zutreffenden oberen und unteren Lagergrenztemperaturen nach Abschnitt 2.3 standhalten.Alle Werkstoffe, Schmierstoffe und Oberflächenbeschichtungsstoffe müssen der Gefahrstoffver-ordnung (neueste Ausgabe), sowie der Umweltnorm Fahrzeuge nach VW 911 00 und dem Emissi-onsverhalten nach VW 501 80 entsprechen.2.5 BetriebsartenFolgende Betriebsarten werden unterschieden:12.5.1 BetriebsartDer Prüfling wird elektrisch nicht betrieben.─Betriebsart 1.1 Leitungen sind nicht am Prüfling angeschlossen.─Betriebsart 1.2 alle Leitungen sind entsprechend Fahrzeugeinbau angeschlos-sen, aber spannungsfrei.2.5.2 Betriebsart2Der Prüfling wird elektrisch wie im abgestellten Fahrzeug (Motor AUS) mit der Versorgungsspan-nung U PB (Batteriespannung) betrieben.Alle Systemkomponenten (z. B. Sensoren, Aktuatoren) und Leitungen sind angeschlossen.─Betriebsart 2.1 System-/Komponentenfunktionen sind nicht aktiviert (z. B. SleepMode)─Betriebsart 2.2 System-/Komponentenfunktionen mit Funktion und Ansteuerungentsprechend bestimmungsgemäßen Betriebs.32.5.3 BetriebsartDer Prüfling wird mit der Versorgungsspannung U PA (Motor/Generator läuft) betrieben:Alle Systemkomponenten (z. B. Sensoren, Aktuatoren) und Leitungen sind angeschlossen.─Betriebsart 3.1 System-/Komponentenfunktionen sind nicht aktiviert─Betriebsart 3.2 System-/Komponentenfunktionen mit Funktion und Ansteuerungentsprechend bestimmungsgemäßen Betriebs.Laboraufbau2.5.4 BetriebsartWie Betriebsart 3.2, jedoch Prüfspannung und elektrische Belastung entsprechend der jeweiligen Prüfung.2.6 FunktionszuständeDieser Abschnitt beschreibt den Funktionszustand des Prüflings während und nach der Prüfung. Der Funktionszustand des Prüflings ist für jede Prüfung anzugeben. Zusätzliche Anforderungen sind im Lastenheft zu definieren und zu dokumentieren.2.6.1 FunktionszustandADer Prüfling erfüllt während und nach der Beaufschlagung mit den Prüfparametern alle Funktionen wie vorgegeben. Es darf bei diagnosefähigen Steuergeräten kein Fehlerspeichereintrag erfolgen.2.6.2 FunktionszustandBDer Prüfling erfüllt während der Beaufschlagung mit den Prüfparametern alle Funktionen wie vor-gegeben, jedoch können eine oder mehrere Funktionen außerhalb der vorgegebenen Toleranz liegen. Nach Ende der Beaufschlagung mit den Prüfparametern erfüllt der Prüfling wieder alle Funktionen wie vorgegeben. Speicherfunktionen müssen im Funktionszustand A bleiben.2.6.3 FunktionszustandCDer Prüfling erfüllt während der Beaufschlagung mit den Prüfparametern eine oder mehrere Funk-tionen nicht wie vorgegeben, jedoch nach Ende der Beaufschlagung mit den Prüfparametern erfüllt der Prüfling wieder automatisch alle Funktionen wie vorgegeben.2.6.4 FunktionszustandDDer Prüfling erfüllt während der Beaufschlagung mit den Prüfparametern eine oder mehrere Funk-tionen nicht wie vorgegeben, jedoch nach Ende der Beaufschlagung mit den Prüfparametern erfüllt der Prüfling wieder alle Funktionen wie vorgegeben durch einen Reset oder einen einfachen Ein-griff (z. B. Austausch einer defekten Sicherung).2.6.5 FunktionszustandEDer Prüfling erfüllt während der Beaufschlagung mit den Prüfparametern eine oder mehrere Funk-tionen nicht wie vorgegeben und muss nach Ende der Beaufschlagung mit den Prüfparametern repariert oder ausgetauscht werden.2.7 AllgemeinePrüfbedingungenEs sind mindestens 6 Prüflinge zu erproben. Bei erhöhten Anforderungen sind mindestens 10 Prüflinge zu erproben.Alle Prüfungen werden mit bereits konditionierten Prüflingen durchgeführt (Konditionierung siehe Abschnitt 5.1.1).Wenn bei Temperaturen die Toleranzangaben fehlen, gilt eine Toleranz von ± 2 °C. Temperaturmessstellen nach DIN 50 011-11 sowie DIN 50 011-12.Falls nicht anders angegeben, sind alle Prüfungen bei Raumtemperatur T RT und einer relativen Luftfeuchte von 25 % bis 75 % durchzuführen.Die Prüfspannungen müssen Tabelle 3 entsprechen. Andere Prüfspannungen sind nur nach Ab-sprache mit den zuständigen Fachabteilungen der VOLKSWAGEN AG zulässig. Die Prüfspannun-gen müssen in dem Prüfbericht dokumentiert sein.Tabelle 3 - PrüfspannungenPrüfspannung 1) 12 V Systeme(V) 24 V Systeme(V)U PA 14 ± 0,1 28 ± 0,2U PB 12 ± 0,1 24 ± 0,2 1) Prüfspannung am Prüfling anliegend3 Elektrische Anforderungen 3.1 Betriebsspannungen Betriebsspannungen siehe Tabelle 4.Tabelle 4 - Spannungen und AnwendungshinweiseNennspannung U N 1) (V) BetriebsspannungU Bmin U Bmax 1) (V) (V)Anwendungshinweise12 6,0 15für Funktionen, die während des Start-vorganges erhalten bleiben müssen 12 9,0 15für Funktionen, die bei ”Motor AUS” er-halten bleiben müssen12 10,8 15für Funktionen, die bei Motorbetriebvorhanden sein müssen24 obige Werte jeweils verdoppelt.Gruppen wie Nennspannung 12 V1) Begriffe nach DIN 72 251ANMERKUNG Betriebsspannung am Prüfling anliegend.Bei Prüflingen mit Netzwerk muss die Netzwerkfähigkeit entsprechend den Spannungsvorgaben aus den Netzwerk-Lastenheften gegeben sein. 3.2 RückspeisungSpannungsrückspeisungen auf die Klemme 15 sind nur bis zu einem Pegel von maximal 1,0 V zulässig. 3.3Spannungspegel: Zuordnung HIGH-LOW-ZustandFür alle Prüflinge mit nicht definierter Schnittstelle gilt folgende Zuordnung der Spannungspegel zu den Eingangszuständen: HIGH-Erkennung: U ≥ U Bmin – 2 V LOW-Erkennung:U ≤ 2 VDer Zustandswechsel von LOW nach HIGH bzw. HIGH nach LOW darf nur bei Über- bzw. Unter-schreitung der hier definierten Level erfolgen. 3.4Funktion bei Unter- und ÜberspannungWenn Über- oder Unterspannung erkannt wurde, geht der Prüfling in einen sicheren Zustand, d. h. es darf keine Fehlfunktion auftreten. Bei Rückkehr in den Betriebsspannungsbereich erfüllt der Prüfling wieder automatisch alle Funktionen wie vorgegeben.Funktionseinschränkungen sind in der Zeichnung oder im Lastenheft zu definieren.Seite 10VW 801 01: 2003-05Bild 2 - Übersicht Spannungsdefinitionen von vernetzten Systemen mit 12 V Nennspannung Beim Übergang von Unter- bzw. Überspannungsbereich in den Betriebsspannungsbereich ist eine Hysterese von ≤ 0,5 V zulässig.Bei allen für den Motorstart relevanten Steuergeräten, die bis 6 V bzw. 26 V voll funktionsfähig sein müssen, gilt: Keine Fehlerspeichereinträge, wegen anderer Steuergeräte, die im Über- bzw. Unter-spannungsbereich nicht mehr funktionsfähig sein müssen. ANMERKUNGUnterspannungsbereich: Funktionen, die während des Startvorganges erhalten bleiben müssen, sind im Lastenheft zu definieren.Überspannungsbereich: Funktionen, die während des Startvorganges (z. B. Fremdstartsimulation) erhalten bleiben müssen, sind im Lastenheft zu definieren.66,57,58,5911131515,5161726[V]810,310,814)* : Bsp.: Motor, Getriebe, Licht, Wischer, ESP, APS, Blinker,Gateway, Klemmensteuerung (ZAS)183.5 BetriebsstromFür Prüflinge mit einer Leistungsaufnahme ≥ 350 W muss die Stromänderungsgeschwindigkeit ≤ 20 A/s sein. Anderenfalls ist eine Freigabe der zuständigen Fachabteilung der VOLKSWAGEN AG notwendig.Betriebsart 3.23.6 RuhestromaufnahmeGrundsätzlich gilt für alle Prüflinge das Ziel einer Ruhestromaufnahme von 0 mA. Für Prüflinge, die nach Klemme 15 AUS betrieben werden müssen, gilt in der Ruhephase ein Ruhestrom < 0,1 mA (Mittelwert). Die Energieentnahme pro Prüfling darf bei einer Standzeit von 50 Tagen 0,12 Ah nicht überschreiten. Diese Energieentnahme gilt auch für die nach Klemme 15 AUS notwendigen Nach-läufe. Anderenfalls ist eine Freigabe der zuständigen Fachabteilung der VOLKSWAGEN AG not-wendig.Betriebsart 2.13.7 VerpolsicherheitZweckSimuliert wird die Widerstandsfähigkeit des Prüflings gegen den verpolten Anschluss einer Batterie beim Fremdstart. Die Prüfung ist nicht für folgende Teile anwendbar:─Generatoren,─Relais mit festen Dioden, ohne externen Verpolschutz.PrüfungDer Prüfling wird entsprechend der Verschaltung und Absicherung im Fahrzeug angeschlossen. Anlegen der Prüfspannung mit vertauschter Polarität an alle Spannungseingänge, sowie alle Ein-/Ausgänge, die geschaltet an der Versorgungsspannung liegen.Keine Ansteuerung der Ausgänge zulässig.Betriebsart LaboraufbauPrüfdauer (60± 6) sPrüfspannung (siehe Tabelle 5) entsprechend der folgenden Anwendungsfälle:Fall 1:Einsatz bei nicht abgesichertem Generator.Prüfspannung = U PCFall 2:Einsatz bei abgesichertem Generator.Prüfspannung = U PATabelle 5 – Prüfspannungen für VerpolsicherheitNennspannung(V) U PA(V)U PC(V)12 14 ± 0,1 4 ± 0,1AnforderungFunktionszustand D. Der Austausch defekter Sicherungen ist zulässig.3.8 Überstromfestigkeit3.8.1 Mechanische Schalter und KontakteZweckSimuliert wird die Überstromfestigkeit von mechanischen Schaltern und Kontakten.Prüfung (nur für mechanische Schalter und Kontakte)Betriebsart LaboraufbauminBelastungsdauer 10Belastung bei I N≤ 10 A 3 x I NBelastung bei I N > 10 A 2 x I N, jedoch min. 30 A und max. 150 A(unter Last einmal ”AUS” und ”EIN” schalten)Bei Mehrkontaktrelais, -schaltern ist jeder Kontakt einzeln zu prüfen.AnforderungFunktionszustand A.Ausgänge3.8.2 ElektronischeZweckSimuliert wird die Überstromfestigkeit von elektronischen Ausgängen.PrüfungBetriebsart LaboraufbauminBelastungsdauer 30Strombelastung Strom entsprechend LastenheftforderungAnforderungAlle elektronischen Ausgänge müssen entsprechend der Lastenheftforderung überstromfest sein. Funktionszustand C.Langzeitbetrieb3.9 ÜberspannungsfestigkeitZweckSimuliert wird ein defekter Spannungsregler am Generator.PrüfungBetriebsart LaboraufbauTemperatur T = (T oB - 20°C)VPrüfspannung 17-0,2 VPrüfzeit 60 minAnlegen der Prüfspannung an alle Spannungseingänge.AnforderungAlle für den Fahrbetrieb notwendige Funktionen Funktionszustand A.Alle anderen Funktionen mindestens Funktionszustand C.3.10 ÜberspannungsfestigkeitKurzzeitbetriebZweckSimuliert wird der Fremdstart mit erhöhter Spannung (Jump Start).PrüfungBetriebsart LaboraufbauVPrüfspannung 26-0,2 VPrüfzeit 60 sAnlegen der Prüfspannung an alle Spannungseingänge.AnforderungAlle für den Fahrzeugstart notwendige Funktionen Funktionszustand AAlle anderen Funktionen mindestens Funktionszustand C.Wechselspannung3.11 ÜberlagerteZweckSimuliert wird eine überlagerte Wechselspannung auf der Betriebsspannung. PrüfungBetriebsart LaboraufbauVPrüfspannung 13Amplitude der überlagertenWechselspannung (Sinus) U ss = 2 VInnenwiderstand derSpannungsquelle ≤ 100 mΩFrequenzbereich 50 Hz bis 20 kHzlinear Wobbelart Dreieck,min Wobbelperiode 2Prüfdauer 10 minAnforderungFunktionszustand A.3.12 Langsames Absenken und Anheben der Versorgungspannung ZweckSimuliert wird ein langsames Entladen und Laden der Batterie.PrüfungBetriebsart Laboraufbau Anlegen der Prüfspannung an alle Spannungseingänge.Absenken der Versorgungsspannung von U Bmax auf 0 V.Erhöhen der Versorgungsspannung von 0 V auf U Bmax.± 0,1) V pro MinuteSpannungsänderung (0,5AnforderungFunktionszustand A, innerhalb des Betriebsspannungsbereiches.Funktionszustand C, außerhalb des Betriebsspannungsbereiches. 3.13Resetverhalten bei SpannungseinbruchZweckSimuliert wird das Resetverhalten des Prüflings bei verschiedenen Spannungseinbrüchen. Diese Prüfung wird auf Prüflinge mit einer Resetfunktion angewandt (im allgemeinen Prüflinge mit Micro-controller). PrüfungBetriebsart Laboraufbau Versuchsdurchführung für ≥ 10 s U Bmin einstellen Zyklus für 5 s Absenken der Betriebsspannung von U Bmin um 0,5 V,für ≥ 10 s U Bmin einstellen und einen Funktionstest durchführen. In jedem Zyklus wird die Spannung um weitere 0,5 V abgesenkt (siehe Bild 3).Die Prüfung endet, wenn die Spannung einen Wert von ≤ 0,5 V erreicht. Die Spannungsänderung erfolgt innerhalb 100 ms.U BminBild 3 - Spannungsverlauf für U Bmin = 9 VAnforderungFunktionszustand A, innerhalb des Betriebsspannungsbereiches.Funktionszustand C, außerhalb des Betriebsspannungsbereiches.3.14 KurzschlussfestigkeitZweckSimuliert werden Kurzschlüsse an den Ein- und Ausgängen.Die Ein- und Ausgänge (ohne Lastkreis) müssen gegen U PA und Masse kurzschlussfest sein.PrüfungNacheinander alle Ein- und Ausgänge gegen U PA und Masse kurzschließen.Die Prüfung wird mit aktivierten und nicht aktivierten Ausgängen durchgeführt.Betriebsart 3.2Prüfdauer 60 s je KurzschlussANMERKUNG Nur bei angelegter Betriebsspannung.AnforderungFunktionszustand C.3.15 DurchschlagfestigkeitZweckSimuliert wird die Durchschlagsfestigkeit des Prüflings zwischen galvanisch getrennten Bauteilen z. B. Steckerpins, Relais, Wicklungen oder Kabel.Diese Prüfung wird nur für Prüflinge mit induktiven Bauteilen verwendet (z. B. Motoren, Relais, Spulen).PrüfungBetriebsart LaboraufbauPrüftemperatur (35 ± 5) °CLuftfeuchte (50 ± 5) %V eff AC, 50 HzPrüfspannung 500Prüfzeit 60 sAnlegen der Prüfspannung─an Anschlüssen ohne galvanische Verbindung.─zwischen Anschlusspins und elektrisch leitenden Gehäuse ohne galvanische Verbindung.─zwischen Anschlusspins und einer Elektrode, die das Gehäuse umgibt, falls das Gehäuse nicht leitend ist.AnforderungFunktionszustand C. Spannungsdurchschläge und Lichtbogen sind nicht erlaubt.3.16 IsolationswiderstandZweckErmittelt wird der Isolationswiderstand zwischen Bauteilen mit galvanischer Trennung.PrüfungBetriebsart LaboraufbauPrüftemperatur (35 ± 5) °CLuftfeuchte (50 ± 5) %Prüfspannung 100 V DC für Bauteilabstand < 3,8 mm500 V DC für Bauteilabstand > 3,8 mmPrüfzeit 60 sAnlegen der Prüfspannung─an Anschlüssen ohne galvanische Verbindung.─zwischen Anschlusspins und elektrisch leitenden Gehäuse ohne galvanische Verbindung.─zwischen Anschlusspins und einer Elektrode, die das Gehäuse umgibt, falls das Gehäuse nicht leitend ist.AnforderungFunktionszustand C, Isolationswiderstand > 10 MΩ.3.17 UnterbrechungenZweckSimuliert wird eine Leitungsunterbrechung.PrüfungBetriebsart 3.2Pin UnterbrechungAn jedem Stecker Pin für Pin (Pin abziehen und wieder aufstecken)Unterbrechungszeit 10sStecker UnterbrechungStecker für Stecker (Stecker abziehen und wieder aufstecken) unter allen Betriebszuständen (Rei-henfolge beliebig)Unterbrechungszeit 10sAnforderungFunktionszustand C.3.18 SpannungsfälleZweckGeprüft werden die maximal zulässigen Spannungsfälle.Relais in Steuergeräten sind entsprechend Relaiskontakte zu prüfen.PrüfungBetriebsart LaboraufbauRelaiskontakteSpannungsfall ≤ 5 mV/A, jedoch absolut ≤ 100 mVPrüfung bei Nennstrom nach Zeichnung, Lastenheft oder TLBetriebsstrom nach Zeichnung, Lastenheft oder TLSchalterkontakte nach VW 801 02Elektronische Ausgänge nach Zeichnung, Lastenheft oder TLAnforderungenDie zulässigen Spannungsfälle dürfen während der Prüfung und über die Lebensdauer nicht über-schritten werden.3.19 Elektromagnetische Verträglichkeit (EMV)3.19.1 Leitungsgebundene Störungen3.19.1.1 Störaussendung von VersorgungsleitungenAnforderungen nach TL 820 66, Lastenheft oder Zeichnung3.19.1.2 Störfestigkeit von VersorgungsleitungenAnforderungen nach TL 820 66, Lastenheft oder Zeichnung3.19.1.3 Störfestigkeit von SensorleitungenAnforderungen nach TL 823 66, Lastenheft oder Zeichnung3.19.2 NahentstörungAnforderungen nach TL 965 , Lastenheft oder Zeichnung3.19.3 Eingestrahlte StörungenAnforderungen nach TL 821 66, Lastenheft oder Zeichnung3.19.4 Immunität gegenüber elektrostatischen Entladungen (ESD)Anforderungen nach TL 824 66, Lastenheft oder ZeichnungAnforderungen4 Mechanische4.1 SchwingenDie Prüfung ist nicht erforderlich, wenn sie durch den Dauerversuch abgedeckt wird.Die Schwingungsprüfung sichert die Funktion des Prüflings unter praxisnaher Beanspruchung ab. Die Schwingungsprofile und –dauer sollen Ermüdungsfehler aufzeigen. Abnutzungs- und Ver-schleißprüfungen sind diese Schwingungsprüfungen nicht.Es gibt verschiedene Schwingungsprüfungen mit unterschiedlichen Prüfschärfen. Diese hängen von dem Einbauort des Prüflings ab.Die Prüflinge werden mit geeigneten Aufnahmen in Einbaulage auf dem Schwingtisch/Gleittisch montiert. Kabel und Schlauchanschlüsse sowie zugehörige Anbauteile sind entsprechend zu mon-tieren. Kabel und Schläuche sind entsprechend den Einbaubedingungen abzufangen, ohne dass Einfluss auf den Prüfling entsteht.Die angegebenen Werte beziehen sich auf direkt montierte Prüflinge. Der Beschleunigungsmess-punkt ist die Schnittstelle Prüftisch/Prüfling.Bei großen und massiven Prüflingen (z. B. Generator, Starter oder Batterie) kann eine Mittelwert-regelung nach DIN EN 60068-2-64 an den Befestigungspunkten des Prüflings mit den Fachabtei-lungen der VOLKSWAGEN AG vereinbart werden.Prüflingslage und Prüfreihenfolge sind im Prüfbericht zu dokumentieren.Da im Fahrzeug die Schwingungsbeanspruchung unter niedrigen oder hohen Temperaturen auftre-ten kann, wird die Schwingungsprüfung mit einem Temperaturprofil nach Abschnitt 5.2.1 durchge-führt. Elektrischer Betrieb wie in Abschnitt 5.2.1 für Dauerlauf angegeben.Alle folgenden Prüfungen gelten nur für Prüflinge mit Einsatz in Fahrzeugen bis zu einem zulässi-gen Gesamtgewicht von 3,5 t.AnforderungenBei Betriebsart 3.2, Funktionszustand A.Bei allen Betriebsarten sind keine störenden Geräusche zulässig.4.1.1 Prüfung für MotoranbauteileZweckDie Schwingungen an einem Verbrennungsmotor setzen sich aus zwei Teilen zusammen:─Schwingungsanregung sinusförmig, resultierend aus den Bewegungen der Kolben.─Schwingungsanregung Breitbandrauschen, resultierend aus allen anderen Bewegungen.PrüfungBeide Schwingungsprüfungen werden nacheinander durchgeführt.Schwingungsanregung sinusförmigVerfahren und Durchführung nach DIN EN 60068-2-6.Prüfdauer für jede Raumachse 22 hFrequenzdurchlaufzeit 1 Oktave/min, logarithmischKurve 1 ist für Prüflinge, die an Motoren mit 5 oder weniger Zylinder montiert werden.Kurve 2 ist für Prüflinge, die an Motoren mit 6 oder mehr Zylinder montiert werden.Für Komponenten die an Motoren mit 5 oder weniger Zylinder sowie an Motoren mit 6 oder mehr Zylindern verwendet werden können, werden beide Kurven kombiniert (siehe Bild 4).。