精馏塔的设计计算
精馏塔的设计计算
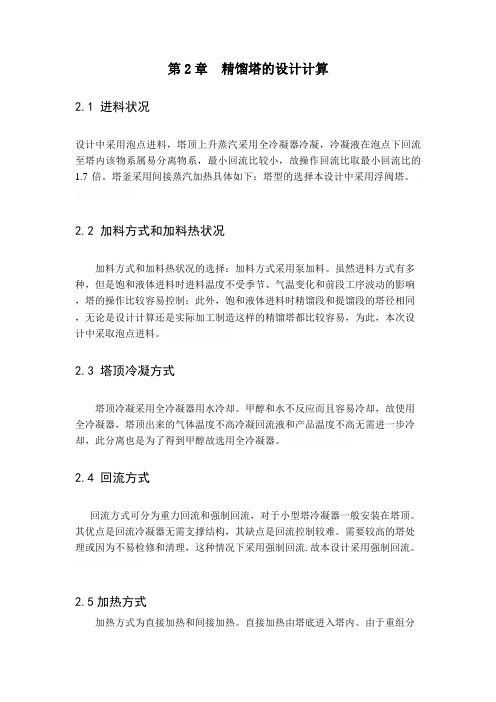
第2章精馏塔的设计计算2.1 进料状况设计中采用泡点进料,塔顶上升蒸汽采用全冷凝器冷凝,冷凝液在泡点下回流至塔内该物系属易分离物系,最小回流比较小,故操作回流比取最小回流比的1.7倍。
塔釜采用间接蒸汽加热具体如下:塔型的选择本设计中采用浮阀塔。
2.2 加料方式和加料热状况加料方式和加料热状况的选择:加料方式采用泵加料。
虽然进料方式有多种,但是饱和液体进料时进料温度不受季节、气温变化和前段工序波动的影响,塔的操作比较容易控制;此外,饱和液体进料时精馏段和提馏段的塔径相同,无论是设计计算还是实际加工制造这样的精馏塔都比较容易,为此,本次设计中采取泡点进料。
2.3 塔顶冷凝方式塔顶冷凝采用全冷凝器用水冷却。
甲醇和水不反应而且容易冷却,故使用全冷凝器,塔顶出来的气体温度不高冷凝回流液和产品温度不高无需进一步冷却,此分离也是为了得到甲醇故选用全冷凝器。
2.4 回流方式回流方式可分为重力回流和强制回流,对于小型塔冷凝器一般安装在塔顶。
其优点是回流冷凝器无需支撑结构,其缺点是回流控制较难。
需要较高的塔处理或因为不易检修和清理,这种情况下采用强制回流.故本设计采用强制回流。
2.5加热方式加热方式为直接加热和间接加热。
直接加热由塔底进入塔内。
由于重组分是水故省略加热装置。
但在一定的回流比条件下,塔底蒸汽对回流有稀释作用,使理论板数增加,费用增加,间接蒸汽加热器是塔釜液部分汽化维持原来浓度,以减少理论板数。
本设计采用间接蒸汽加热。
2.6工艺流程简介连续精馏装置主要包括精馏塔,蒸馏釜(或再沸器),冷凝器,冷却器,原料预热器及贮槽等.原料液经原料预热器加热至规定温度后,由塔中部加入塔内.蒸馏釜(或再沸器)的溶液受热后部分汽化,产生的蒸汽自塔底经过各层塔上升,与板上回流液接触进行传质,从而使上升蒸汽中易挥发组分的含量逐渐提高,至塔顶引出后进入冷凝器中冷凝成液体,冷凝的液体一部分作为塔顶产品,另一部分由塔顶引入塔内作为回流液,蒸馏釜中排出的液体为塔底的产品。
精馏塔的计算

3.解吸:从吸收剂中分离出已被吸收气体的操作。
4.吸收操作传质过程:单向传质过程,吸收质从气相转移到液相的传质过程。
其中包括吸收质由气相主体向气液相界面的传递,及由相界面向液相主体的传递。
5.吸收过程:通常在吸收塔中进行。为了使气液两相充分接触,可采用板式塔或填料塔,少数情况下也选用喷洒塔。
对于易溶气体,H很大,此时,传质阻力集中于气膜中,液膜阻力可以忽略,1/ KG≈1/kG气膜阻力控制着整个吸收过程的速率,吸收总推动力的绝大部分用于克服气膜阻力,这种情况称为“气膜控制”。
对于气膜控制的吸收过程,如要提高其速率,在选择设备型式及确定操作条件时,应特别注意减小气膜阻力。
(2)以C*-C表示总推动力的吸收速率方程式(液相总吸收速率方程式)
解:将液组成换算成摩尔分率。
xF=(40/78)/(40/78+60/92)= 0.44
xD=(97/78)/(97/78+3/92)=0.974
xW=(2/78)/(2/78+98/92)=0.0235
原料平均摩尔质量MF=78×0.44+92×0.56=85.8kg/kmol
由物料衡算:F= D+W =15000/85.8= 175kmol/h
则F = D + W
FxF= DxD+ WxW
175 = D + WD=76.6kmol/h
175×0.44=0.974D+0.0235WW=98.4kmol/ h
例:将含24%(摩尔分率,以下同)易挥发组分的某混合液送入连续操作的精馏塔。要求馏出液中含95%的易挥发组分,残液中含3%易挥发组分。塔顶每小时送入全凝器850kmol蒸汽,而每小时从冷凝器流入精馏塔的回流量为670kmol。试求每小时能抽出多少kmol残液量。回流比为多少?
化工原理课程设计——精馏塔设计

南京工程学院课程设计说明书(论文)题目乙醇—水连续精馏塔的设计课程名称化工原理院(系、部、中心)康尼学院专业环境工程班级K环境091学生姓名朱盟翔学号240094410设计地点文理楼A404指导教师李乾军张东平设计起止时间:2011年12月5日至 2011 年12月16日符号说明英文字母A a——塔板开孔区面积,m2;A f——降液管截面积,m2;A0——筛孔面积;A T——塔截面积;c0——流量系数,无因此;C——计算u max时的负荷系数,m/s;C S——气相负荷因子,m/s;d0——筛孔直径,m;D——塔径,m;D L——液体扩散系数,m2/s;D V——气体扩散系数,m2/s;e V——液沫夹带线量,kg(液)/kg(气);E——液流收缩系数,无因次;E T——总板效率,无因次;F——气相动能因子,kg1/2/(s·m1/2);F0——筛孔气相动能因子,kg1/2/(s·m1/2);g——重力加速度,9.81m/s2;h1——进口堰与降液管间的距离,m;h C——与干板压降相当的液柱高度,m液柱;h d——与液体流过降液管相当的液柱高度,m;h f——塔板上鼓泡层液高度,m;h1——与板上液层阻力相当的高度,m液柱;h L——板上清夜层高度,m;h0——降液管底隙高度,m;h OW——堰上液层高度,m;h W——出口堰高度,m;h'W——进口堰高度,m;Hσ——与克服表面张力的压降相当的液柱高度,m液柱;H——板式塔高度,m;溶解系数,kmol/(m3·kPa);H B——塔底空间高度,m;H d——降液管内清夜层高度,m;H D——塔顶空间高度,m;H F——进料板处塔板间距,m;H P——人孔处塔板间距,m;H T——塔板间距,m;K——稳定系数,无因次;l W——堰长,m;L h——液体体积流量,m3/h;L S——液体体积流量,m3/h;n——筛孔数目;P——操作压力,Pa;△P——压力降,Pa;△P P——气体通过每层筛板的压降,Pa;r——鼓泡区半径,m,t——筛板的中心距,m;u——空塔气速,m/s;u0——气体通过筛孔的速度,m/s;u0,min——漏气点速度,m/s;u'0——液体通过降液管底隙的速度,m/s;V h——气体体积流量,m3/h;V s——气体体积流量,m3/h;W c——边缘无效区宽度,m;W d——弓形降液管宽度,m;W s——破沫区宽度,m;x——液相摩尔分数;X——液相摩尔比;y——气相摩尔分数;Y——气相摩尔比;Z——板式塔的有效高度,m。
化工单元操作:精馏塔计算

(四)单股进料,无侧线出料 塔体上只有一个进料口,除塔顶馏出液和塔底残液,没有其他出料口。
二、全塔物料衡算(质量守恒)
1、物料衡算公式:
F = D + W FzF = DxD + WxW 2、采出率、易挥发组分回收率、难挥发组分回收率的概念和计算
2、提馏段操作线方程
L′ =V ′ + W
L′xm = V ′ym+1 + WxW
y m +1
=
L′ L′ −W
xm
−
WxW L′ −W
或者
y m +1
=
L′ V′
xm
− Wxw V′
它表达了在一定的操作条件下,提馏段内相邻两层塔板的下一层塔板上升蒸汽浓度 ym+1 与上 一层塔板下降液体浓度 xm 的关系。
3)进料线方程 y = q x − xF 进料线的意义:精馏段与提馏段两段操作线的交点轨迹。 q −1 q −1
二、操作线的绘制 步骤:
1、精馏段操作线 2、进料线,并与精馏段操作线有一交点 3、提馏段操作线
精馏塔计算
一、精馏塔塔板层数的确定
1、理论塔板的概念 汽液两相在塔板上充分接触,使离开塔板的两相温度相同,且两相组成互为平衡,则称
D = z F − xW F xD − xW
W = xD − zF =1− D
F xD − xW
F
ηD
=
Dx D Fz F
× 100%
ηW
= W (1 − xW ) ×100% F (1 − z F )
三、精馏操作线方程
1、精馏段操作线方程
精馏塔的工艺计算

2 精馏塔的工艺计算2.1精馏塔的物料衡算2.1.1基础数据 (一)生产能力:10万吨/年,工作日330天,每天按24小时计时。
(二)进料组成:乙苯212.6868Kmol/h ;苯3.5448 Kmol/h ;甲苯10.6343Kmol/h 。
(三)分离要求:馏出液中乙苯量不大于0.01,釜液中甲苯量不大于0.005。
2.1.2物料衡算(清晰分割)以甲苯为轻关键组分,乙苯为重关键组分,苯为非轻关键组分。
01.0=D HK x ,005.0=W LK x ,表2.1 进料和各组分条件由《分离工程》P65式3-23得:,1,,1LKi LK Wi HK D LK Wz xD Fx x =-=--∑ (式2. 1)2434.13005.001.01005.0046875.0015625.08659.226=---+⨯=D Kmol/hW=F-D=226.8659-13.2434=213.6225Kmol/h 0681.1005.06225.21322=⨯==W X W ,ωKmol/h编号 组分 i f /kmol/h i f /% 1 苯 3.5448 1.5625 2 甲苯 10.6343 4.6875 3 乙苯 212.6868 93.7500总计226.86591005662.90681.16343.10222=-=-=ωf d Kmol/h 132434.001.02434.1333=⨯==D X D d ,Kmol/h5544.212132434.06868.212333=-=-=d f ωKmol/h表2-2 物料衡算表2.2精馏塔工艺计算2.2.1操作条件的确定 一、塔顶温度纯物质饱和蒸气压关联式(化工热力学 P199):CC S T T x Dx Cx Bx Ax x P P /1)()1()/ln(635.11-=+++-=-表2-3 物性参数注:压力单位0.1Mpa ,温度单位K编号 组分 i f /kmol/h 馏出液i d 釜液i ω 1 苯 3.5448 3.5448 0 2 甲苯 10.6343 9.5662 1.0681 3 乙苯 212.6868 0.1324 212.5544总计226.865913.2434213.6225组份 相对分子质量临界温度C T 临界压力C P苯 78 562.2 48.9 甲苯 92 591.841.0 乙苯106617.236.0名称 A B CD表2-3饱和蒸汽压关联式数据以苯为例,434.02.562/15.3181/1=-=-=C T T x1.5)434.033399.3434.062863.2434.033213.1434.098273.6()434.01()(635.11-=⨯-⨯-⨯+⨯-⨯-=-CS P P In01.02974.09.48)1.5ex p(a S P MPa P =⨯=⨯-=同理,可得MPa P b 1.00985.00⨯=露点方程:∑==ni ii p p y 11,试差法求塔顶温度表2-4 试差法结果统计故塔顶温度=105.5℃二、塔顶压力塔顶压力Mpa p 1.0013.1⨯=顶 三、塔底温度苯 -6.98273 1.33213 -2.62863 -3.33399 甲苯 -7.28607 1.38091 -2.83433 -2.79168 乙苯-7.486451.45488-3.37538-2.23048泡点方程:p x pni ii =∑=10试差法求塔底温度故塔底温度=136℃四、塔底压力塔底压力Mpa p 1.0013.1⨯=底 五、进料温度进料压力为Mpa p 1.0013.1⨯=进,泡点方程:p x pni ii =∑=1试差法求进料温度故进料温度=133℃六、相对挥发度的计算据化学化工物性数据手册,用内插法求得各个数据5.105=顶t ℃,961.5=苯α514.2=甲苯α1=乙苯α;136=底t ℃,96.1=甲苯α1=乙苯α; 133=进t ℃,38.4=苯α97.1=甲苯α1=乙苯α综上,各个组份挥发度见下表据清晰分割结果,计算最少平衡级数。
精馏塔工艺工艺设计计算

第三章 精馏塔工艺设计计算塔设备是化工、石油化工、生物化工、制药等生产过程中广泛采用的气液传质设备。
根据塔内气液接触构件的结构形式,可分为板式塔和填料塔两大类。
板式塔内设置一定数量的塔板,气体以鼓泡或喷射形势穿过板上的液层,进行传质与传热,在正常操作下,气象为分散相,液相为连续相,气相组成呈阶梯变化,属逐级接触逆流操作过程。
本次设计的萃取剂回收塔为精馏塔,综合考虑生产能力、分离效率、塔压降、操作弹性、结构造价等因素将该精馏塔设计为筛板塔。
3.1 设计依据[6]3.1.1板式塔的塔体工艺尺寸计算公式 (1) 塔的有效高度T TTH E N Z )1(-= (3-1) 式中 Z –––––板式塔的有效高度,m ; N T –––––塔内所需要的理论板层数; E T –––––总板效率; H T –––––塔板间距,m 。
(2) 塔径的计算uV D Sπ4=(3-2) 式中 D –––––塔径,m ;V S –––––气体体积流量,m 3/s u –––––空塔气速,m/su =(0.6~0.8)u max (3-3) VVL Cu ρρρ-=m a x (3-4) 式中 L ρ–––––液相密度,kg/m 3V ρ–––––气相密度,kg/m 3C –––––负荷因子,m/s2.02020⎪⎭⎫⎝⎛=L C C σ (3-5)式中 C –––––操作物系的负荷因子,m/sL σ–––––操作物系的液体表面张力,mN/m 3.1.2板式塔的塔板工艺尺寸计算公式 (1) 溢流装置设计W O W L h h h += (3-6) 式中 L h –––––板上清液层高度,m ; OW h –––––堰上液层高度,m 。
32100084.2⎪⎪⎭⎫⎝⎛=Wh OWl L E h (3-7)式中 h L –––––塔内液体流量,m ; E –––––液流收缩系数,取E=1。
hTf L H A 3600=θ≥3~5 (3-8)006.00-=W h h (3-9) '360000u l L h W h=(3-10)式中 u 0ˊ–––––液体通过底隙时的流速,m/s 。
精馏塔全塔效率计算公式
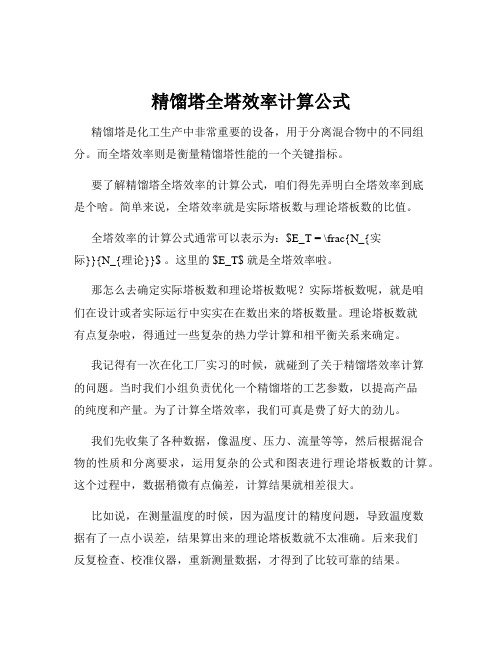
精馏塔全塔效率计算公式精馏塔是化工生产中非常重要的设备,用于分离混合物中的不同组分。
而全塔效率则是衡量精馏塔性能的一个关键指标。
要了解精馏塔全塔效率的计算公式,咱们得先弄明白全塔效率到底是个啥。
简单来说,全塔效率就是实际塔板数与理论塔板数的比值。
全塔效率的计算公式通常可以表示为:$E_T = \frac{N_{实际}}{N_{理论}}$ 。
这里的 $E_T$ 就是全塔效率啦。
那怎么去确定实际塔板数和理论塔板数呢?实际塔板数呢,就是咱们在设计或者实际运行中实实在在数出来的塔板数量。
理论塔板数就有点复杂啦,得通过一些复杂的热力学计算和相平衡关系来确定。
我记得有一次在化工厂实习的时候,就碰到了关于精馏塔效率计算的问题。
当时我们小组负责优化一个精馏塔的工艺参数,以提高产品的纯度和产量。
为了计算全塔效率,我们可真是费了好大的劲儿。
我们先收集了各种数据,像温度、压力、流量等等,然后根据混合物的性质和分离要求,运用复杂的公式和图表进行理论塔板数的计算。
这个过程中,数据稍微有点偏差,计算结果就相差很大。
比如说,在测量温度的时候,因为温度计的精度问题,导致温度数据有了一点小误差,结果算出来的理论塔板数就不太准确。
后来我们反复检查、校准仪器,重新测量数据,才得到了比较可靠的结果。
在确定了实际塔板数和理论塔板数之后,代入全塔效率的计算公式,就能得出全塔效率啦。
通过计算全塔效率,我们可以评估精馏塔的性能,找出可能存在的问题,比如塔板结构不合理、操作条件不合适等等。
总之,精馏塔全塔效率的计算公式虽然看起来简单,但是要准确计算和应用,还需要我们对精馏过程有深入的理解,对数据的收集和处理要非常严谨。
只有这样,才能真正发挥全塔效率这个指标的作用,让精馏塔更好地为化工生产服务。
希望通过我的讲解,能让您对精馏塔全塔效率的计算公式有更清楚的认识。
要是在实际应用中遇到问题,别着急,多思考、多尝试,总会找到解决办法的!。
精馏塔设计
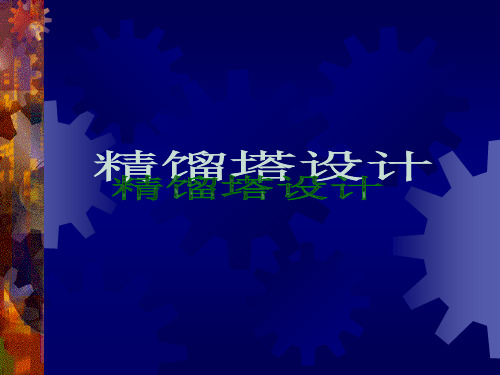
最小回流比Rmin
随着回流比R的减小,则精馏过 程的能耗下降,塔径D也回随之 减小。但因R减小,使操作线交 点向平衡移动,导致过程传质推 动力减小,使得完成相同的分离 要求所需理论板数N随之增加, 使塔增高。 当回流比继续减小,使两操作线 交点落在平衡曲线上,如图中E 点所示。此时完成规定分离要求 所需理论板数为∞。此工况下的 回流比为该设计条件下的最小回 流比Rmin。
当回流比增大时精馏段操作线斜率R/(R+1)增大,则精馏段操作线远离平
衡线。使得精馏塔内各板传质推动力
及
增大,使各板分离能力
提高。 (绿线)
为此,完成相同分离要求,所需理论板数将会减少,由13块减为10块理论 板。然而由于R的增加导致塔内气、液两相流量增加,从而引起再沸器热 流提高。从而使精馏
V=(R+1)D
进料线方程
在进料板上,同时满足精馏段和提馏段的物料衡算,故两操作 线的交点落在进料板上。当q为定值,改变塔操作为回流比时, 两操作线交点轨迹即q线。联立两操作线方程式 和 解得交点q 的坐标为
x 联立以上两式消去 D 得q线方程
xf
当塔顶蒸气全部被冷凝时,则
有:
由于冷凝器全凝,无分离能力, 不计为理论板,则以塔顶计第 一块理论板。因 由工艺所 规定,故 为已知。
成
时结束。此时梯级数N
(含再沸器)为所求的理论塔板数N,
跨过两操作线交点的板为最佳进料
板
。
进料位置的选择 在适宜位置进料,完成规定分离要求所需塔板数会减少。对给定理论板时,
- 1、下载文档前请自行甄别文档内容的完整性,平台不提供额外的编辑、内容补充、找答案等附加服务。
- 2、"仅部分预览"的文档,不可在线预览部分如存在完整性等问题,可反馈申请退款(可完整预览的文档不适用该条件!)。
- 3、如文档侵犯您的权益,请联系客服反馈,我们会尽快为您处理(人工客服工作时间:9:00-18:30)。
•6、热能的利用 • 精馏过程耗能较多,节约和合理地利用精馏过程本身的热能 。 •◇选取适宜的回流比,使过程处于最佳条件下进行,可使能耗 降至最低。 •◇塔顶蒸汽冷凝潜热及釜液产品的余热充分利用。
•
二、工艺计算
•(一)全塔物料衡算
• 1、计算原料液、塔顶、塔底浓度
• 2、平均分子量:(原料液MF、塔顶MD 、塔底MW ) • 3、物料衡算求W、D (或F) kmol/h
•
•5、冷却方式 • ◇冷却器:通常在塔顶设置蒸气全部冷凝的全凝器。其为 辅助设备,需进行选型,多采用列管式,水平或垂直放置。 • ◇冷却剂的选择:由塔顶蒸汽温度决定。如果塔顶蒸汽温 度低,可选用冷冻盐水或深井水作冷却剂。如果能用常温水 作冷却剂,是最经济的。 • ◇水的入口温度:由气温决定,出口温度由设计者确定。 冷却水出口温度取得高些,冷却剂的消耗可以减少,但同时 温度差较小,传热面积将增加。冷却水出口温度的选择由当 地水资源确定,但一般不宜超过50℃,否则溶于水中的无机 盐将析出,生成水垢附着在换热器的表面而影响传热。
•
•3、塔板设计: • ◇设计塔板各主要工艺尺寸 • 溢流装置、塔板布置、筛孔或浮阀的设计及排列(图); • ◇进行流体力学校核计算; • ◇画出塔的负荷性能图。 •4、辅助设备的设计: • ◇换热器的热负荷:求取塔顶冷凝器、冷却器的热负荷和所 需冷却水用量;再沸器的热负荷和所需加热蒸汽用量。
•
• ◇换热器的设计选型 • ◇输液用泵的型号:根据流体的输送量、杨程和流体 物性,选定泵的型号(在各输液泵中任选一个选型); • ◇流程中主要管线的设计:先选定物料在管路中的适 宜流速,经计算、圆整,最后确定管路尺寸和材质。 •5、抄写说明书。 •6、绘制精馏装置工艺流程图和精馏塔装配图。
•
•4、加热方式的选择 • ◇加热方式:蒸馏釜的加热方式通常采用间接蒸汽加热,设 置再沸器。 • 若塔底产物近于纯水,而且在浓度稀薄时溶液的相对挥发度 较大(如酒精与水的混合液),便可采用直接蒸汽加热。 • ◇加热剂:T<180℃,常用饱和水蒸气。 • ◇再沸器结构: • 小塔可在塔底,形式有夹套式、蛇管式、列管式。 • 大塔一般在塔外,形式为列管式,有立式和卧式两种。
• 4、塔板数的计算
• (1)理论板数的计算:
•
第二节 板式精馏塔的工艺计算
•一、设计方案的确定 •1、设计方案确定的原则: • ◇满足工艺和操作的要求:保证产品达到任务规定的要求, 质量要稳定 ,有一定的操作弹性 ,要考虑必需装置的仪表(如 温度计、压强计,流量计等)。 • ◇经济方面:要节省热能和电能的消耗,降低操作费用;减 少设备及基建内容:
• ◇封面(课程设计题目、班级、姓名、指导教师、时间 ); • ◇ 目录; • ◇ 设计任务书; • ◇ 工艺流程及设计方案说明; • ◇ 设计条件及主要物性参数表; • ◇ 工艺设计计算; • ◇ 设计结果汇总表; • ◇ 辅助设备的设计及选型; • ◇ 设计评述及设计者对本设计有关问题的讨论; • ◇参考资料。 •(2) 工艺流程图及主体设备装配图;
•
•2、操作压力的选择:设计压力一般指塔顶压力。 • ◇蒸馏操作通常可在常压、加压和减压下进行。 • ◇确定操作压力时,必须根据所处理物料的性质,兼顾技术 上的可行性和经济上的合理性进行考虑。
• ◇减压操作有利于分离相对挥发度较大组分及热敏性的物料 ,但压力降低将导致塔径增加,同时还需要使用抽真空的设备。 对于沸点低、在常压下为气态的物料,则应在加压下进行蒸馏。 当物性无特殊要求时,一般是在稍高于大气压下操作。
•二、化工原理课程设计的内容
• 1、课程设计的基本内容 • (1)设计方案简介 • 对给定或选定的工艺流程,主要的设备型式进行简要的论述; • (2)主要设备的工艺设计计算 • 包括工艺参数的选定、物料衡算、热量衡算、设备的工艺尺寸 计算及结构设计; • (3)典型辅助设备的选型和计算 • 对典型辅助设备的主要工艺尺寸计算和设备型号规格的选定; • (4)工艺流程简图 • 以单线图的形式绘制流程图,标出主体设备和辅助设备的物料 流向、物流量、能流量和主要化工参数测量点; • (5)主体设备工艺条件图(装配图) • 图面上应包括设备的主要工艺尺寸,技术• 特性表和接管表;
• ◇本次设计,塔顶操作压力为4kPa(表压),每层塔板压降 p≤0.7kPa。
•
•3、进料状况的选择 • 进料状态与塔板数、塔径、回流量及塔的热负荷都有密 切的联系。 • 在实际的生产中进料状态有多种,但一般都将料液预热 到泡点或接近泡点才送入塔中,这主要是由于此时塔的操作比 较容易控制,不致受季节气温的影响。 • 此外,在泡点进料时,精馏段与提馏段的塔径相同,为 设计和制造上提供了方便。
精馏塔的设计计算
2020年7月12日星期日
•第一节 概述
•一、化工原理课程设计的目的和要求
• 通过课程设计,学生应该注重以下几个能力的训练和培养 : • 1. 查阅数据手册,正确选用公式和搜集数据的能力; • 2. 树立既考虑技术上的先进性与可行性,又考虑经济上的 合理性,并注意到操作时的劳动条件和环境保护的正确设计思 想,在这种设计思想的指导下去分析和解决实际问题的能力; • 3. 迅速准确的进行工程计算的能力; • 4. 用简洁的文字,清晰的图表来表达自己• 设计思想的能力
•
•3、注意事项 • 整个设计是由论述、计算和绘图三部分组成。 • ◇论述应该条理清晰,观点明确; • ◇计算要求方法正确,误差小于设计要求,计算公式和所用 数据必须注明出处; • ◇图表应能简要表达计算的结果。
•
•三、化工原理课程设计的步骤
• 本设计按以下几个阶段进行: •1、根据设计任务和工艺要求,确定设计方案。根据给定任务 ,对精馏装置的流程、操作条件、塔板类型等进行论述。 •2、蒸馏塔的工艺计算 • ◇确定理论塔板数(作图法)、实际板数; • ◇确定塔高和塔径。