电器除尘处理沸腾炉炉气汇总
沸腾炉的运行操作

沸腾炉的运行操作一、沸腾炉的工作特点炉排上的煤粒受到来自炉排下方向上吹的风力,当此风力略大于煤粒的重力和摩擦阻力时,煤粒被吹起。
由于煤粒形状是不规则的,因此煤粒的受力也在不断变化。
如果风力调整得合适,可使煤粒在一定的高度内翻腾跳跃;风力过大时,煤粒将被吹走;若风力过小,煤粒在炉排上处于静止状态而不能浮起,因此风力过大或过小,都起不到沸腾的作用。
为了获得沸腾燃烧,须将煤粒直径控制在一定范围内,并根据煤粒大小将风速控制在一定范围内,这就是沸腾炉的工作特点。
二、沸腾炉的点火操作用木柴等引燃物将炉床上的炉料加温,使料层逐步达到正常运行时的温度,以保证连续送入炉膛的煤能够正常燃烧。
现将点火步骤简述如下:1.检查炉膛内部,应无结焦和杂物。
2.在炉排上铺一层炉渣,其粒度与燃煤相似,厚度约为300毫米(mm),然后放置引燃木柴,木柴直径小于100毫米(mm),长为500~700毫米(mm)。
用油棉纱等引火物点燃木柴,使炉内均匀预热。
3.关闭风道门,启动引风机,使炉膛产生负压。
4.启动鼓风机,稍开启送风门,使炭火层稍有跳动,但应注意风量的控制使炭火不要被炉渣掩埋,否则将导致炭火熄灭。
5.从炉门向炭火层均匀撒布烟煤屑,并逐渐增大风量,提高料层的温度。
6.随料层温度的升高,相应增加送风量。
当达到正常运行的“最小风速”时,可暂不增加送风量,用撒人烟煤屑的数量来控制炉温升高的速度。
7.当炉料温度在达到600~700℃(暗红色)之前,应使温度升得较快,同时增加风量使风速较快地超过“最小风速”,以免发生“低温结焦”。
料层温度达到600~700℃后,应尽量使温度平稳地上升,以免造成“高温结焦”。
当料层温度达到800~850℃时,即将炉门关闭,并开动给煤机按正常运行送入给煤量,监视燃烧情况,直至燃烧稳定即告点火成功。
三、沸腾炉的运行调整操作要使沸腾炉能正常运行,其关键在于正确调节沸腾层的送风量,控制风速、风箱静压和沸腾层的温度。
沸腾炉常用参数

ZGCr28
整体耐热不锈钢
Cr28
风帽数据:
孔径mm
5.2
5.5
5.8
6பைடு நூலகம்0
6.2
孔数
6
8
6
8
6
8
6
8
6
8
截面积mm2
125
167
143
190
158
211
169
226
181
242
孔径mm
6.5
6.8
7.0
7.2
7.5
孔数
6
8
6
8
6
8
6
8
6
8
截面积mm2
199
266
217
290
7.燃料理论空气需要量:
(1)理论计算
L0=0.089Cy+0.267Hy+0.033(Sy-Oy)
式中:L0—完全燃烧时理论空气需要量,NM3/kg
Cy、Hy、Sy、Oy—原料中各元素重量百分比
(2)经验计算
L0=1.01Qydw/1000+0.5
Qydw—燃煤分析基低位发热值kcal/kg
L=αL0
(2)经验计算
Vg0=0.89 Qydw/1000+1.65
式中:Vg0—不包括过剩空气的烟气量,Nm3/kg
华中科技大提供的沸腾炉有关参数
风室有关参数
进入风室风速
<10m/s
稳压段高度
>500mm
风室上升风速
<1.5 m/s
风室底部倾角
8~15°
布风板主要参数
布风板厚度
12~20mm
电除尘岗位技术操作规程(5篇范文)

(6)严禁把易燃易爆物品带入操作室,消防设施完好齐全。
(7)检查电场时,必须确定工作负责人,安全监护人。
(8)填写检查(检修)安全工作票。
(9)确认停机指令后,切断电源,锁好控制柜挂牌,开关必须打在接地位置。
(10)工作确认后,保管好控制柜钥匙,用高压接地棒接地后方可开始工作。
7、 进入电场或整流室检查,检修或清扫必须停机组,关闭整流总电源,对电场机组接地放电要有电笔验电,严禁用手触摸是否有电,确认无电并落实互保后,才能进行工作。同时严禁将人孔门关闭,并需在门上悬挂"清理电场,严禁关门"等标牌。
8、 作业人架好进入人孔短梯,带手电筒才能进入电场清扫或排除故障,排除故障必须两人以上才能作业,进电场先要确定走台栏杆是否牢固,防止跌落。
整流变压器外观检查:油位、油色、渗漏油情况,呼吸器的干燥剂、进线电缆、出线套管及信号反馈线与屏蔽接地,工作接地情况等,检查阻尼电阻连接与阻值情况。检查高压开关操作机构运行情况。检查隔离开关、高压开关情况,变压器油温指标及保护情况。
3在电除尘器电场投运前完成加热及振打装置投运。一般程序为:
3.1 在炉子点火前投入灰斗加热或电加热,以防冷灰斗结露或落灰受潮后堵灰。
(16)同时执行矿槽除尘工岗位安全操作规程中的规定。
4.1.4 检查所有电加热器,在开车前24小时预先送电加热高压绝缘部分。
4.1.5 启动所有传动设备,检查运转是否正常。
4.1.6 关闭所有人孔、检查孔。
4.1.7 电场进行试送电,并记录静态和动态载时的电流、电压变化情况,动态空载电压要求>;46kv(动态指阴阳极振打运行条件下)。
锅炉除尘方案

锅炉除尘方案概述:锅炉是工业生产中常见的热能装置,用于将水加热为蒸汽,供应给工艺过程或发电机组。
然而,锅炉燃烧时会产生大量的烟尘颗粒和废气,对环境造成污染,也对工作人员的健康构成威胁。
为了保护环境和人类的健康,采取有效的锅炉除尘方案十分重要。
本文将介绍几种常见的锅炉除尘方案。
一、电除尘器电除尘器通过利用电场力将烟尘颗粒从燃烧废气中去除,是目前应用最广泛的一种除尘设备。
它由收集电极和放电电极组成,通过高压直流电场将电极之间的废气中的烟尘颗粒聚集到电极上,并通过机械方式清除。
电除尘器具有除尘效率高、阻力损失小、可适应高温高湿等优点,因此在锅炉除尘中应用广泛。
二、湿式除尘器湿式除尘器是利用水膜的湿润作用将烟尘颗粒从废气中吸附到水膜上,并通过水的洗涤作用去除烟尘颗粒。
湿式除尘器适用于高温和高粉尘含量的废气处理,能够有效地去除细小的烟尘颗粒和溶解性气体污染物。
然而,湿式除尘器在处理废气时会产生大量的废水,并且需要投资较高的运行成本。
三、布袋除尘器布袋除尘器是利用纤维布袋对烟尘颗粒进行过滤和捕集,将洁净的废气排放到大气中。
它具有除尘效率高、处理能力大、适应性强等优点,能够有效去除不同粒径和形状的烟尘颗粒。
布袋除尘器广泛应用于锅炉烟气中的颗粒物捕集,但对于湿性烟气处理相对有一定的限制。
四、静电除尘器静电除尘器是利用电场力将带静电的烟尘颗粒从废气中去除的设备。
它具有除尘效率高、适应性强、结构简单等特点,适用于处理高温和高含尘量废气。
静电除尘器在锅炉烟气处理中具有广泛的应用。
五、活性炭吸附装置活性炭吸附装置是通过活性炭吸附废气中的污染物,包括烟尘颗粒和有机物质。
它适用于锅炉废气中的有机废气去除。
活性炭吸附装置具有吸附效率高、操作简便等特点,但需要定期更换活性炭,运行成本较高。
结论:在锅炉除尘方案的选择中,应根据锅炉的特点、排放标准和运行成本等因素进行综合考虑。
根据不同的情况,可以通过组合使用多种除尘设备来提高除尘效率。
无机化工工艺学 Word 文档

一、填空或选择✧硫酸的制造方法有:铅室法、塔式法和接触法;其中接触法常用。
✧硫铁矿制酸工艺有沸腾焙烧、电除尘、酸洗净化、电除雾、塔式干吸、两转两吸✧硫铁矿是中国硫酸生产的主要原料,硫铁矿的主要成分是二硫化铁(FeS2)✧接触法制硫酸的三个基本工序:焙烧、转化、吸收✧硫铁矿是处理方法有:硫铁矿的破碎、筛分、配矿、脱水✧硫铁矿焙烧反应是一个气-固相非催化反应✧提高硫铁矿焙烧反应速率的途径有:1、提高反应温度,2、减小矿料粒度,3、提高气体与矿粒的相对运动速度,4、提高入炉气体的氧含量。
✧硫铁矿焙烧炉有:块矿炉、机械炉、沸腾炉,其中现代工业均使用沸腾炉✧焙烧工段的主要作用是制出合格的SO2炉气,并清除炉气中的矿尘✧影响沸腾炉焙烧温度的主要因素有投矿量、矿料的含硫量和水分,以及风量。
✧调节炉底压力可采用调节风量和投矿量两个措施✧炉气的冷却方式有:1、绝热降温(只降温不移热量)2、移热降温✧净化工序由洗涤设备、除雾设备和除热设备组成✧炉气净化流程分湿法和干法两类,目前湿法用得最普遍。
湿法因洗涤液不同分为酸洗和水洗两种,以酸洗为主✧要提高SO2的平衡转化率可降低反应温度、提高系统压力和使用富氧焙烧等措施,还可以移去生成物SO3✧钒催化剂以五氧化钒为主要活性组分,以碱金属(主要是钾)硫酸盐为助催化剂,以硅胶、硅藻土、硅酸铝等作载体✧钒催化剂的毒物有砷、氟、酸雾和水分,还有矿尘✧SO2转化为SO3是从经典的气-固相催化理论走向气-液相催化理论。
✧一般,换热方式有冷激式、间接换热式、冷激与间接换热组合式。
其中冷激式又分原料气冷激和空气冷激两种,冷激与间接换热组合式用得最多✧经两次转化后,SO2的转化率可表示为:X f=X1+(1-X1)X2,其中X1、X2、X f表示第一、第二、最终转化率✧氮肥、磷肥与钾肥是三大营养元素肥料,称为大量元素肥料。
硫肥、钙肥和镁肥称为中量营养元素肥料。
硼、锌、铁、锰、铜、钼等称为微量元素肥料。
转炉干法一次除尘[整理]
![转炉干法一次除尘[整理]](https://img.taocdn.com/s3/m/c2b2b07226d3240c844769eae009581b6bd9bd8e.png)
转炉已一次干法除尘技术1 转炉干法除尘技术背景转炉煤气干法除尘是鲁奇(Lurgi)和蒂森(Thyssen)公司20世纪60年代末合作开发的。
转炉干法除尘的基本原理是对经汽化烟道后的高温煤气进行喷水冷却,将煤气温度由900℃~1000℃降低到200℃左右,采用电除尘器进行处理。
转炉干法除尘系统主要包括:蒸发冷却器、静电除尘器、煤气切换、煤气冷却器、放散烟囱、除灰系统等。
与湿法除尘(OG)法比较,干法除尘有以下优点:.除尘效率高。
净化后烟气含尘量为10mg/Nm3~20mg/Nm3,如有特殊要求可降至5mg/Nm3。
.系统阻力小,耗能低,风机运行费低,寿命长,维修工作少。
.在水、电消耗方面具有明显的优越性。
.不需要泥浆沉淀池及污泥处理设施。
.含铁干粉灰压块后可直接供转炉利用。
2 首钢京唐干法除尘设施的技术特点及实施情况首钢京唐炼钢厂采用2+3的“全三脱”两步法冶炼生产模式。
配置2座300t脱磷转炉和3座300t脱碳转炉。
脱磷转炉平均冶炼周期25min ,脱碳转炉平均冶炼周期28min。
正常情况下,实行2+3转炉全量脱磷、脱碳处理,转炉与板坯连铸机采用3对3的高效快节奏的生产模式。
在欧洲转炉干法除尘技术应用非常普遍,但是欧洲钢厂均没有采用“全三脱”转炉两步法冶炼技术。
在日本“三脱”转炉两步法冶炼技术应用很多,却没有采用转炉干法除尘的实例。
首钢京唐钢铁公司是世界上第一个在“全三脱”两步法冶炼的大型快节奏转炉上采用干法除尘技术的钢厂。
该工艺特点是:“三脱”处理后的铁水,已基本不含Si,C、Mn 含量也有较大的降低。
但是在工业化生产中仍需解决以下两个问题,对“三脱”处理后铁水进行吹炼,开吹后的炉气量和炉气中的CO含量是否会显著增加?如采用干法除尘是否会增加卸爆发生频率?为了实现在“全三脱”冶炼的转炉上应用煤气干法电除尘技术,技术团队对国外进行了考察调研和认真分析研究。
分析结论认为:与常规吹炼相比,“三脱”铁水吹炼前期炉气中CO比率不会增加,这对减少卸爆有利。
电除尘构造及作用
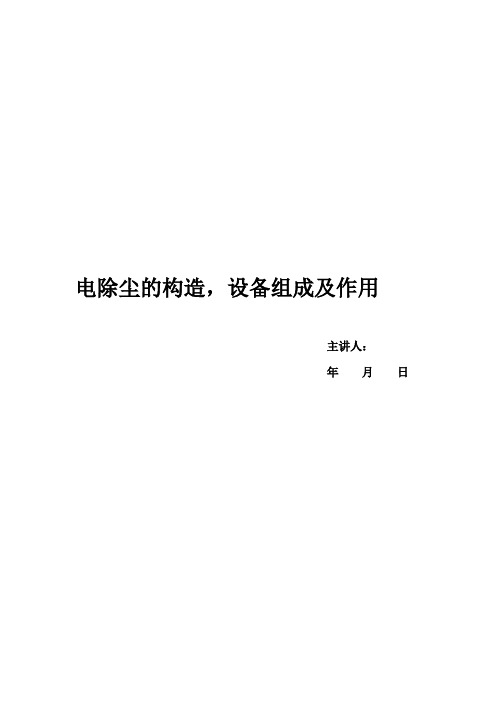
电除尘的构造,设备组成及作用主讲人:年月日绪论一:蒸发冷却器1:供气系统:2:供水系统3:控制系统4:设备的作用二:静电除尘器1:除尘的种类2:内部构造3:原理4:大概故障5;供电装置三:ID风机四:煤气冷却器五:液压站绪论氧气顶吹转炉炼钢时炉内反应激烈,产生大量的炉气。
吹炼过程中碳元素发生激烈的氧化,生产大量的CO和二氧化碳气体,随同少量的其他气体一起构成炉气,氧化反应产生的热量使得熔池温度很高,使得部分铁和杂质蒸发,同时大量的CO气体从熔池浮出时引起熔池沸腾也带出少量微小液滴。
这些蒸发的铁和被带出的微小液滴在随炉气上升过程中被氧气氧化并冷却成极细微的氧化铁尘粒,这就是炉口红棕色的烟雾。
炉气从转炉出来经活动烟罩进入汽化冷却烟道,经汽化冷却烟道冷却后再进入转炉煤气干法净化回收系统中的蒸发冷却器和粗灰尘,最后进入电除尘器进行精除尘转炉煤气干法净化回收系统中的蒸发冷却器的工作原理是将水和气按一定的比例送到特定的双相流喷嘴内,雾化成微细的汽水混合物颗粒后直接喷入蒸发冷却器,并吸收热量迅速蒸发,使高温烟气迅速冷却,将转炉烟气降温,同时烟气中20%到30%的粉尘被凝聚成较大的颗粒沉降到灰斗内一:蒸发冷却器蒸发冷却器的组成设备本体,喷枪,供水系统,供气系统,及控制系统五部分组成1:供气系统:供气系统一般用蒸汽,特殊情况下用氮气代替蒸汽,压力约为0.8Mp为水量的十分之一2:供水系统供水系统主要由水泵,水箱,过滤器,流量调节阀及检测报警装置组成。
蒸发冷却器通常配置独立的工厂供水和补水系统,水泵互为备用,根据烟气量及蒸发冷却器进出口烟气温度的高低,自动调节供水量3:控制系统控制系统主要由EC进出口烟气温度检测装置,供水和供气系统的流量压力检测装置,调节阀组成。
控制系统的功能根据烟气的变化状况,自动调节喷枪的碰水量,以保证EC出口烟气温度维持在所设定的温度范围内,4:设备的作用二:静电除尘器1:除尘设备的种类除尘器可以分成许多类型,不同性能的除尘器用于不同的粉尘和不同的条件按清灰方式不同可分为干式,湿式,雾状粒子,半湿式静电除尘器按气体在除尘器内部的运动方向分立式,卧式按收尘极的形式分为管式,板式按收尘极和电晕极的不同配置分单区和双区按振打方式可分为侧部振打,顶部振打静电除尘器按除尘效率分为高,中,低,除尘器三种,60到95个%特点干式静电除尘器收下的粉尘是干燥状态,,粉尘的电阻率有一定的范围,卧式静电除尘器,可按生产需要适当增加电场数,各电场可分别供电,避免电场间互相干扰,以提高收尘效率板式静电除尘器,清灰比较方便,安装也容易烟尘重返气流后可再次荷电,除尘效率高,主要用于重工业除尘我们用的是干式,板式,单区,高效,卧式静电除尘器2:内部构造除尘器的组成壳体,放电极,收尘极,气流分布装置,振打清灰装置,绝缘子及保温箱等等吧对壳体要求具有足够的刚度,强度,稳定性对收尘极的基本要求,板面场强分布和板面电流分布要尽可能均匀,防止二次扬尘的性能好,振打性能好,机械强度好,耐高温,耐腐蚀,消耗钢材少,加工及安装精度高对放电极的基本要求,放电性能好(起晕电压低,击穿电压高,电晕电流强)机械强度高,耐腐蚀,耐高温,不易断线,清灰性能好,振打时粉尘容易脱落,放电极的形式很多,圆形放电极,星形电极,带形,刀形,锯齿电极芒刺线一二电场采用芒刺线,放电强度高,可以防止产生电晕闭塞,浓度低的电场采用星形线振打方式有,摇臂锤振打,电磁振打,气动振打和振动器振打等用的是仿形锤分布板用的是条珊式的3:原理利用静电力实现粒子与气体分离的一种除尘装置1气体的电离,气体一般是不导电的,当气体分子在外力作用下或得能量时,就可能使气体分子中的电子脱离而成为自由电子,这些电子成为输送电流的媒介,气体就有了导电的能力2粉尘荷电:在放电极和集尘极之间施加直流高压电,使放电极发生电晕放电,气体电离,生产大量的自由电子,和正离子,在放电极附近的所谓电晕区内正离子立即被电晕极吸引过去而失去电荷,自由电子和随即形成的负荷离子则因受电场力的驱使向集尘极移动,并充满到俩极间的绝大部分空间,含尘气流通过电场空间时,自由电子,负离子与粉尘碰撞并附着其上,便实现了粉尘的负电4:大概故障故障机处理方法(1)电源合闸后立即跳闸,或是电流大而电压为接近零原因分析:1电晕线掉落,与阳极板接触2绝缘子被击穿3排灰阀和排灰系统失灵,灰尘接触到电晕极下部4成片铁锈落在阴阳极之间形成短路,高压隔离开关处于接地状态处理方法:1)装好或更换掉落的电晕线2)更换被击穿的绝缘子,并分析检查击穿的原因,出去隐患3)清除积灰,修好排灰阀或排灰系统4)去掉绣片5)拔开开关位置。
完整版电炉配套除尘系统方案详解

5t 电炉烟气除尘初步配置方案及预算5t 电炉烟气除尘系统初步配置方案及预算贵公司电炉车间建有 1 台 5t 电炉,因在作业时产生大量烟气,对周边环境污染严重,现委托我公司进行烟气治理。
方案设计中采用相关国家标准, 重型机械冶金行业标准及企业、除尘系统方案标准,采用主要相关标准有:GB5083-85GB59591-86GB5056-93GB100671-88JB/ZQ4000 3-86GB3085-82TJ36-92GB9078-1996GBJ19-88GBJ114-88GBJ1653-89GBJ4-83GB505155-02生产设备安全卫生设计总则 设备的安全通用部分 设备的电力装置设计规范 设备的基本技术条件 焊接件通用技术条件 大气环境质量标准 工业企业设计卫生准则 钢铁工业废气粉尘排放标准 采暖通风与空气调节设计规范 采暖能风与空气调节制图标准 除尘机组技术性能及测试方法 工业“三废”排放试行标准 采暖通风与空气调节术语标准1.1除尘系统工艺流程如下:为了对电炉在作业过程中产生的烟气进行有效捕集和治理,减少和防止烟气对环境的污染,改善车间工作环境,本设计方案对1台5t 电炉设置独立烟气除尘系统。
1.2系统风量 根据经验及初步计算,5t 电炉系统风量为90000m 3/h ,除尘系统总 风量为 90000m 3/h 。
1.3系统组成除尘系统由烟气捕集器、烟道、除尘器、风机、排灰装置、烟囱及 电气控制组成。
烟气经捕集器进入烟道,在足够长的烟道中温度降低到滤袋允许温 度后进入袋式除尘器,在除尘器中烟气与粉尘分离,净化后的烟气经风 机、烟囱半密闭集烟罩排灰系统压缩空气袋式除尘器排入大气,收集的粉尘由排灰装置排出1.4 主要设备及性能参数1.4.1 烟气捕集器电炉烟气捕集器采用半密闭罩+屋顶罩组成复合捕集型式;1.4.1.1 半密闭罩半密闭罩由固定罩和移动罩组成,形成一个上部密封于炉盖之上,下部进入冷风的半密封罩体。
沸腾焙烧炉的正常作业与故障处理

沸腾焙烧炉的正常作业与故障处理2.5.4正常作业现代炼锌工业的沸腾焙烧炉都设有自控仪表,以指示及记录进入炉内的锌精矿量、空气量、炉内各部分的温度、压力等。
沸腾焙烧的操作,就是根据仪表的指示来维持所规定的技术条件。
所以沸腾焙烧的正常操作是比较简单的。
掌握好沸腾焙烧的操作,关键在于做到“三稳定”:稳定鼓风量,稳定料量,稳定温度。
2.5.4.1鼓风量鼓风量的大小根据炉子的生产能力来决定,在一般的情况下,鼓风量稳定后就不要经常变动。
鼓风分为炉内(大斗)鼓风和前室(小斗)鼓风,而前室鼓风量一般要比炉内鼓风量大5,左右(按单位炉床面积计算),这是因为前室的下料量大,物料的水分也高,需要较大的鼓风量以加速对炉料的翻动。
对42 m2的沸腾炉而言,鼓入18000 m3/h的空气,每天可处理240,250t锌精矿,可产出18500 m3/h的炉气量,炉气含SO2的浓度可达8,,9.5,。
2.5.4.2沸腾层温度与加料量在固定鼓风量的条件下,沸腾层的温度主要由加料的均匀性决定。
若下料不均匀,不仅会引起沸腾层的温度的波动,而且会引起炉气中SO2浓度的变化,对焙砂的质量及硫酸制造过程极为不利。
处于正常状态时,沸腾炉加料均匀稳定,炉内各部分的温度基本上均匀一致。
如加料量过大时,前室温度下降而排料口温度上升;加料量过小时,前室的温度突然上升而排料口的温度下降。
所以加料的均匀程度,是控制炉内的温度的主要环节,要求操作人员密切注视前室及排料口部位的温度变化情况,以便及时调节加料的均匀性。
要做到加料均匀,必须做到勤操作、勤调节。
另外,精矿含硫量及含水量的变化,也会引起沸腾层温度的波动。
如精矿中含硫量增加1,,2,时,温度就可升高20,30?,这时除了调节加料量外,还可以向沸腾层喷入适当的水来调节炉内的温度。
精矿中的水分有变化时,要求前一工序及时进行调整。
2.5.4.3压力降所谓压力降就是压力的变化,它随阻力的增大而加大。
在正常情况下,前室压力降比炉内压力降大l000 Pa左右,这是因为前室料层厚度大于沸腾层料层厚度。
电炉除尘优化改造方案
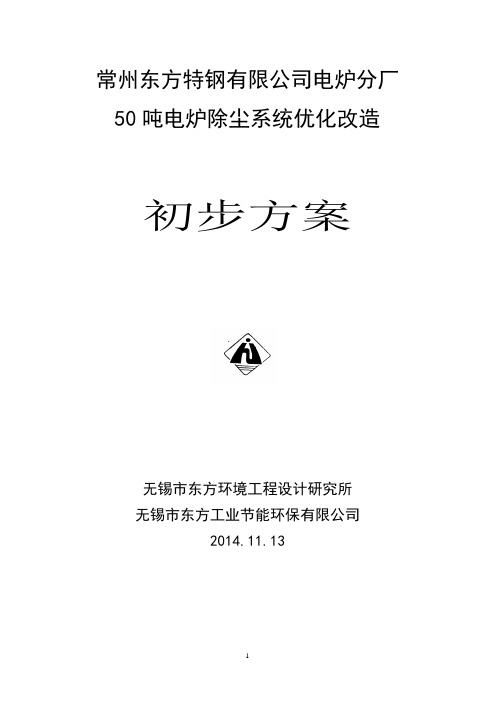
常州东方特钢有限公司电炉分厂50吨电炉除尘系统优化改造初步方案无锡市东方环境工程设计研究所无锡市东方工业节能环保有限公司2014.11.13常州东方特钢有限公司电炉分厂50t电炉除尘系统优化改造方案一、现状概述常州东方特钢有限公司电炉厂50吨电炉在兑铁水加废钢及供氧高峰期有系统能力不足,有黄烟逸出,精炼炉有大量烟尘逸出罩子,环保压力日趋紧张,东方特钢决定对电炉及精炼炉除尘进行改造,同时把现有除尘器卸灰的二次扬尘问题一并解决。
50吨电炉采用铁水热装工艺,铁水吃入量为20-23t左右,炉壳直径为4600mm,兑铁方式为正兑铁,采用炉门氧枪结合炉壁氧枪的供氧方式,最大出钢量为45t。
目前除尘采用内外排混合工艺,内排排烟方式:高温烟气通过水冷烟道进入沉降室,再经高温烟道进入锅炉,在内排风机的作用下与屋顶除尘风管汇合,外排排烟方式:烟气通过屋顶捕集通过风管输送至除尘器净化后排出。
内排风机设计流量12万m3/h(6万Nm3/h左右),外排风机设计流量66万m3/h,配1250KW电机。
二、测试分析总管流量实测为70万m3/h,内排流量实测为5万m3/h。
内排能力因电炉拉渣问题没有开足,制约了内排能力的发挥,同时也降低了蒸汽产出。
外排更换布袋后达到了设计流量,因内排流量的制约外排不能满足生产需要,同时兑铁水加废钢仍有大量烟尘逸出捕集罩。
精炼炉采用半封闭罩,管路接入屋顶除尘总管,风量不能平衡,烟尘逸出严重。
三、设计条件及标准设计条件:1) 大气温度·年平均温度:15.4℃·年平均最高温度:20.3℃·年平均最低温度:11.4℃·最热月平均温度:29.9℃·最冷月平均温度:-2.9℃2) 相对湿度·年平均相对湿度:77%·夏季相对湿度:78%·冬季相对湿度:81%3) 风速、风向·年平均风速:3.4m/s·30年一遇10分钟最大平均风速:25.2m/s ·全年主导风向:东北、东南·夏季主导风向:东南风·冬季主导风向:东北风4) 降雨量·年平均降雨量:1041.7mm·日最大降雨量:198.5mm5) 大气压力·年平均气压:1015.5mb·年最高绝对气压:1046.9mb·年最低绝对气压:989.1mb设计依据:1)东方所在冶金行业烟尘治理方面积累的经验;2)业主对除尘系统改造的意见和要求;3)国家及行业对环境的有关标准及指标;《炼铁工业大气污染物排放标准》(GB28663-2012);《冶金工业环境保护设计规定》(YB9066-95);《冶金工业环境保护设施规划范围规定》(YB9067-95);《工业企业噪声控制设计规范》(GBJ87-85);《工业企业设计卫生标准》(TJ36-79);《采暖通风与空气调节设计规范》(GB50019-2003)。
中频电炉除尘器烟尘收集治理工艺流程
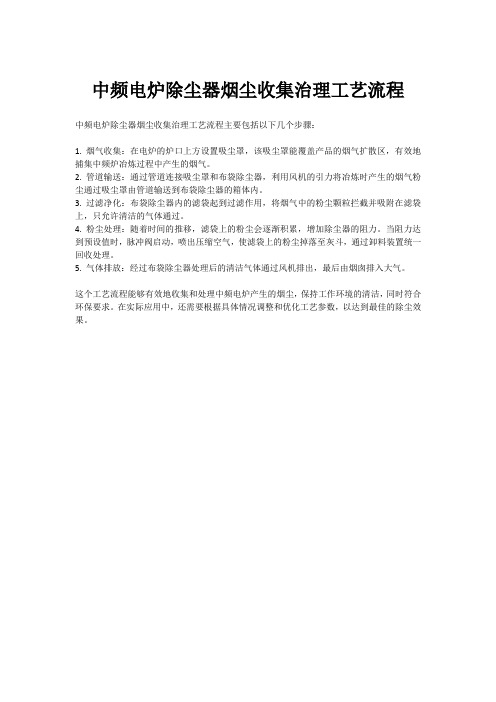
中频电炉除尘器烟尘收集治理工艺流程中频电炉除尘器烟尘收集治理工艺流程主要包括以下几个步骤:
1. 烟气收集:在电炉的炉口上方设置吸尘罩,该吸尘罩能覆盖产品的烟气扩散区,有效地捕集中频炉冶炼过程中产生的烟气。
2. 管道输送:通过管道连接吸尘罩和布袋除尘器,利用风机的引力将冶炼时产生的烟气粉尘通过吸尘罩由管道输送到布袋除尘器的箱体内。
3. 过滤净化:布袋除尘器内的滤袋起到过滤作用,将烟气中的粉尘颗粒拦截并吸附在滤袋上,只允许清洁的气体通过。
4. 粉尘处理:随着时间的推移,滤袋上的粉尘会逐渐积累,增加除尘器的阻力。
当阻力达到预设值时,脉冲阀启动,喷出压缩空气,使滤袋上的粉尘掉落至灰斗,通过卸料装置统一回收处理。
5. 气体排放:经过布袋除尘器处理后的清洁气体通过风机排出,最后由烟囱排入大气。
这个工艺流程能够有效地收集和处理中频电炉产生的烟尘,保持工作环境的清洁,同时符合环保要求。
在实际应用中,还需要根据具体情况调整和优化工艺参数,以达到最佳的除尘效果。
图所示为硫酸生产中的沸腾炉

沸腾炉漏料:由于炉体密封不严或物料流动性差,导致物料泄漏
沸腾炉结垢:由于物料中的杂质或水分过多,导致炉内结垢
故障诊断:通过观察、听、闻、摸等方法,确定故障部位和原因
排除故障:根据诊断结果,采取相应的:沸腾炉通过加热炉料,使炉料中的硫磺和空气在高温下反应,生成二氧化硫气体。
促进化学反应:沸腾炉中的高温环境有利于硫磺和空气中的氧发生化学反应,生成二氧化硫气体。
分离固体产物:沸腾炉中的高温环境可以使炉料中的固体产物与气体产物分离,方便后续处理。
提高生产效率:沸腾炉的高温环境可以加快化学反应速度,提高硫酸生产效率。
通知相关部门进行检修和处理
汇报人:
感谢您的观看
确认工艺流程:确认硫酸生产工艺流程,熟悉操作步骤和注意事项。
严格控制温度和压力:沸腾炉的操作过程中,需要严格控制温度和压力,确保生产安全和产品质量。
保持炉内清洁:定期清理炉内杂物,保持炉内清洁,防止杂物对生产过程产生不良影响。
避免过度投料:在投料过程中,要避免过度投料,以免对炉内产生过大的压力和温度波动。
沸腾炉与配料系统:配料系统向沸腾炉提供原料,确保生产顺利进行
沸腾炉与余热回收系统:余热回收系统利用沸腾炉的余热,提高能源利用效率
沸腾炉与酸冷系统:酸冷系统对沸腾炉产生的硫酸进行冷却,保证产品质量
沸腾炉与尾气处理系统:尾气处理系统对沸腾炉产生的尾气进行处理,保护环境
沸腾炉的工作原理
沸腾炉的构造:包括炉体、燃烧器、通风装置等部分
沸腾炉的工作原理:燃料在燃烧器中燃烧产生高温气体,使炉内物料呈沸腾状态,实现传热和化学反应
沸腾炉的特点:具有高效传热、高气速、高生产强度等优点
沸腾炉安全操作规程(3篇范文)

沸腾炉安全操作规程(3篇范文)第1篇沸腾炉安全操作规程1、幵车1.1、开车前的准备(1)新砌筑的炉体,需要根据砌筑技术要求,并在专业人员的指导下进行烘炉;(2)准备燃煤,检查燃煤的粒度和水分是否符合要求;(3)准备好司炉工具:钩、耙、锹、推车、锤子等;(4)准备好点火材料:木柴、白煤粉、粗河砂,以及适量引火用油料、废棉纱等;(5)利用视觉方法检查检查风帽是否堵塞,圆盘喂料机是否有异物;出渣系统(二次燃烧室,沉降室等)是否堵塞;(6)检查风管、调节阀、鼓风机及引风机是否正常;(7)检查给料及卸料装置有无异常;(8)对热风系统(含配套设备)及烘干机挡轮、托轮、大小散齿、扬料板、支撑架、减速机件全面检查,确认无误后方能开车。
1.2、开车前的调试(1)在主沸腾床上均匀铺上厚100mm干粗黄砂;(2)开启引风风机;(3)开启鼓风机,并调节鼓风机、引风机开度,至黄砂呈鼓泡状运动;观察沸腾状态,检查有无风帽堵塞;(4)若有堵塞,则停风机将风帽掏通直至整个炉床均匀沸腾为止。
8. 5.1.3.开车程序在主沸腾床上铺干粗黄砂至床料厚度约为200mm,加入床料总量约8%的优质碎烟煤,开启风机使之混合均匀后停机。
零位启动引风机。
在料层上面放置一定量的木材,点火。
待底砂出现发红,零位启动鼓风机,逐渐增加负荷,至河砂呈鼓泡状运行。
同时调节引风机负荷,保障烟气不外溢影响环境,同时又不影响火的燃烧。
观察炉内燃烧情况,逐步添加白煤粉,使炉膛温度达 800°c。
待运行稳定后,启动圆盘喂料机给料,添加白煤粉或焦煤粉,升温到800〜1100°c。
此时可根据运行情况,启动烘干物质给料系统进行烘干操作。
2正常运行操作调节给煤量、给料量、鼓风机开度、引风机开度,保障炉膛温度在800〜1100°c范围内,进行烘干操作;若需要暂时停止烘干操作,则进行压火操作。
压火前,停止给物料,减少燃料给料量,迅速加入料层总量7%左右的煤粒后,待炉温下降到950°c (肉眼观察呈橘黄色)左右。
1号炉电除尘改造总结
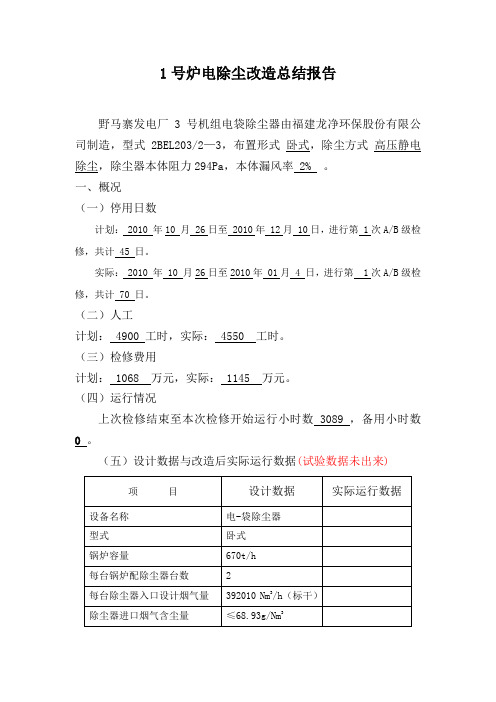
1号炉电除尘改造总结报告野马寨发电厂3号机组电袋除尘器由福建龙净环保股份有限公司制造,型式2BEL203/2—3,布置形式卧式,除尘方式高压静电除尘,除尘器本体阻力294Pa,本体漏风率 2% 。
一、概况(一)停用日数计划: 2010 年10 月 26日至 2010年 12月 10日,进行第 1次A/B级检修,共计 45 日。
实际: 2010 年 10 月26日至2010年 01月 4 日,进行第 1次A/B级检修,共计 70 日。
(二)人工计划: 4900 工时,实际: 4550 工时。
(三)检修费用计划: 1068 万元,实际: 1145 万元。
(四)运行情况上次检修结束至本次检修开始运行小时数 3089 ,备用小时数0 。
(五)设计数据与改造后实际运行数据(试验数据未出来)(六)检修工作评语1号炉电-袋除尘器自2011年1月4日投入运行以来运行正常,未发生原则性施工质量问题和设备故障,运行参数符合设计要求,工程质量优良。
二、简要文字总结(1)施工组织与安全情况。
施工组织:建立以项目经理负责制为主的质量、安全管理体系。
在开工前组织方案的确定,施工中监督施工方案的实施及方案的优化,做好施工前的技术交底,做好施工进度的控制,确保按期、安全、优质完成电除尘改造工作。
安全管理:安全施工是工程顺利进行的基本保障,搞好安全施工是确保工程进度如期完成的前提条件,安全施工方面在电厂工程部门和安监部门的严格管理和大力配合协作下,对安全施工一是抓管理二是抓贯彻执行的检查落实。
具体有:抓好入厂前的安全教育,提高全体施工人员对安全施工的思想和意识;严格执行各项规章制度;严格执行安全措施;严格检查施工过程安全规章制度与措施的执行情况,发现问题立即纠正,做到防患于未然;严格检查施工过程安全隐患,发现后立即组织力量对其进行处理,力争做到万无一失。
做好现场文明施工与环保管理,搞好施工区域文明卫生,并要天天保持现场的环境。
(2)检修文件包及工序卡应用情况。
沸腾炉资料
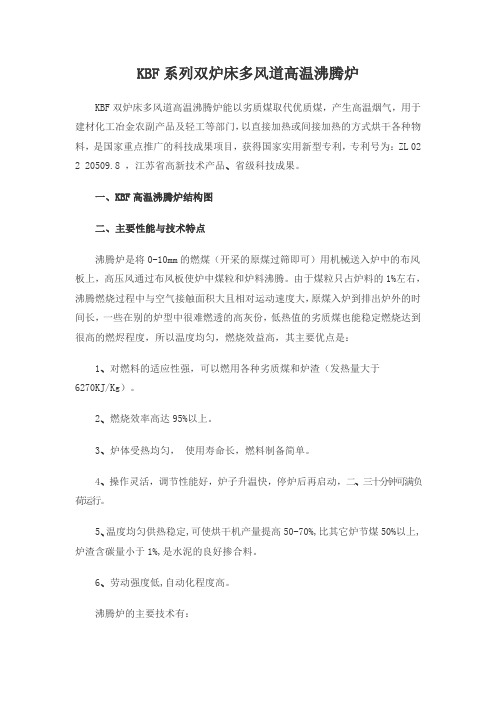
KBF系列双炉床多风道高温沸腾炉KBF双炉床多风道高温沸腾炉能以劣质煤取代优质煤,产生高温烟气,用于建材化工冶金农副产品及轻工等部门,以直接加热或间接加热的方式烘干各种物料,是国家重点推广的科技成果项目,获得国家实用新型专利,专利号为:ZL 02 2 20509.8 ,江苏省高新技术产品、省级科技成果。
一、KBF高温沸腾炉结构图二、主要性能与技术特点沸腾炉是将0-10mm的燃煤(开采的原煤过筛即可)用机械送入炉中的布风板上,高压风通过布风板使炉中煤粒和炉料沸腾。
由于煤粒只占炉料的1%左右,沸腾燃烧过程中与空气接触面积大且相对运动速度大,原煤入炉到排出炉外的时间长,一些在别的炉型中很难燃透的高灰份,低热值的劣质煤也能稳定燃烧达到很高的燃烬程度,所以温度均匀,燃烧效益高,其主要优点是:1、对燃料的适应性强,可以燃用各种劣质煤和炉渣(发热量大于6270KJ/Kg)。
2、燃烧效率高达95%以上。
3、炉体受热均匀,使用寿命长,燃料制备简单。
4、操作灵活,调节性能好,炉子升温快,停炉后再启动,二、三十分钟可满负荷运行。
5、温度均匀供热稳定,可使烘干机产量提高50-70%,比其它炉节煤50%以上,炉渣含碳量小于1%,是水泥的良好掺合料。
6、劳动强度低,自动化程度高。
沸腾炉的主要技术有:1、等压风室,两段燃烧,采用U型燃烧段可分离和收集未燃尽的细小碳粒,又可延长其燃烬时间(当不采用两段燃烧时,入炉煤粒应小于10mm,如限定煤粒为0-5mm)。
2、采用大节距变孔径风帽的布风装置,有良好的流化质量和燃烧工艺,减少边壁效应带来的布风不均匀的影响。
3、采用大过量空气系数,加强炉内空气搅动,强化燃烧,使煤在炉内燃烧充分,温度均匀,控制方便。
4、采用合理的悬浮段结构,烟气流速较低,细灰带走量小,供热烟气最高温度可达1050℃,煤粒燃烬95%以上。
三、沸腾炉的操作(一)烧炉1、沸腾炉砌好后,炉内应仔细清扫,检查,确保炉膛内无铁钉等杂物。
制酸工工作笔记

制酸工工作笔记(1)原料工段在仓库贮存的硫精矿,由装载机送入加料斗,经圆盘给料机、胶带输送机送入笼式破碎机,将成球的尾沙打散,再由胶带输送机送入振动筛筛分,筛上粗颗粒矿经胶带输送机返回仓库,筛下粒度合格的成品矿由胶带输送机送入焙烧工段炉前料斗。
(2)焙烧工段来自原料工段的硫铁矿入炉前料斗贮存,经胶带给料机加入沸腾炉,焙烧产生的浓度为12~13%、温度为900℃的含SO2炉气经余热锅炉移热降温至380℃,以旋风出尘器及电除尘器除尘,使尘含量降至≤0.2g/Nm3后入净化工段文氏管。
焙烧硫铁矿所需空气的由空气鼓风机从炉底送入。
沸腾炉排出的矿渣,余热锅炉及旋风出尘器、电除尘器排出的矿尘进入淋撒式冷却增湿滚筒冷却后喷水增湿。
用胶带输送机送入堆场,以汽车运出。
(3)净化工段自焙烧工段来的350℃炉气进入文氏管,与喷淋的15%左右的稀硫酸接触传质传热降温,除去大部分矿尘及其他杂质,然后进入泡沫塔以2~3%稀硫酸喷淋洗涤,进一步除去矿尘及其他杂质,由间冷器移热降温至40℃左右,经电除雾器除去酸雾,使酸雾降至0.03g/Nm3后进入干吸工段干燥塔。
文氏管排出的15%的稀硫酸经斜管沉降器沉降分离矿尘后,进入循环酸槽,从泡沫塔循环酸泵出口来的2~3%稀硫酸由斜管沉降器出口引出,入稀酸贮槽贮存。
斜管沉降器间断排出的污泥与设备地坪冲洗酸性水一道经酸性水池以泵送至污水处理站。
泡沫塔排出的2~3%稀硫酸入循环酸槽,从间冷器循环酸槽溢流出来的冷凝液调节其浓度,由循环酸泵送入泡沫塔喷淋,增加的稀酸串入文氏管循环酸槽。
间冷器排出的冷凝液入循环槽,以循环泵间断或连续送入间冷器喷淋。
电除雾器除下的酸雾进入间冷器循环槽、净化工段补充的工艺水加入间冷器循环槽。
(4)干吸工段自净化工段来的炉气以空气调节SO2浓度至7.5~8%后进入干燥塔,经喷淋的93~94%硫酸干燥使水份降至0.1g/Nm3,并经塔顶丝网除沫器除去酸沫后进入转化工段。
干燥塔内吸收水份后的硫酸流入循环槽,以一吸塔循环酸系统串入的98%硫酸维持其浓度,以循环酸泵送入干燥塔酸冷却器,冷却降温后入干燥塔喷淋。
烟气量计算
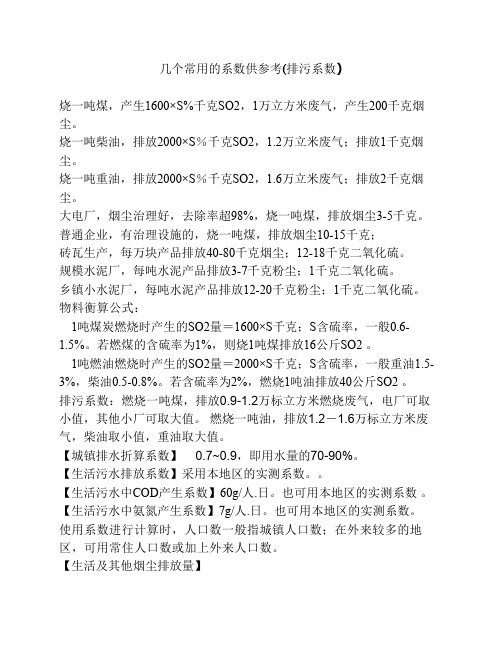
B年——全年燃料耗量(或熟料产量),kg/y;
B时——在正常工况下每小时的燃料耗量(或熟料产
量) ,
kg/h。
2.系数推算法
1)锅炉燃烧废气排放量的计算
①理论空气需要量(V0)的计算
a. 对于固体燃料,当燃料应用基挥发分Vy>15%(烟煤),计算公式
为:
V0=0.251 ×QL/1000+0.278[m3(标)/kg]
几个常用的系数供参考(排污系数)
烧一吨煤,产生1600×S%千克SO2,1万立方米废气,产生200千克烟 尘。 烧一吨柴油,排放2000×S%千克SO2,1.2万立米废气;排放1千克烟 尘。 烧一吨重油,排放2000×S%千克SO2,1.6万立米废气;排放2千克烟 尘。 大电厂,烟尘治理好,去除率超98%,烧一吨煤,排放烟尘3-5千克。 普通企业,有治理设施的,烧一吨煤,排放烟尘10-15千克; 砖瓦生产,每万块产品排放40-80千克烟尘;12-18千克二氧化硫。 规模水泥厂,每吨水泥产品排放3-7千克粉尘;1千克二氧化硫。 乡镇小水泥厂,每吨水泥产品排放12-20千克粉尘;1千克二氧化硫。 物料衡算公式:
按燃用民用型煤和原煤分别采用不同的系数计算: 民用型煤:每吨型煤排放1~2公斤烟尘 原 煤:每吨原煤排放8~10公斤烟尘 一、工业废气排放总量计算
1.实测法 当废气排放量有实测值时,采用下式计算:
Q年= Q时× B年/B时/10000
式中:
Q年——全年废气排放量,万标m3/y;
Q时——废气小时排放量,标m3/h;
1吨煤炭燃烧时产生的SO2量=1600×S千克;S含硫率,一般0.61.5%。若燃煤的含硫率为1%,则烧1吨煤排放16公斤SO2 。
1吨燃油燃烧时产生的SO2量=2000×S千克;S含硫率,一般重油1.53%,柴油0.5-0.8%。若含硫率为2%,燃烧1吨油排放40公斤SO2 。 排污系数:燃烧一吨煤,排放0.9-1.2万标立方米燃烧废气,电厂可取 小值,其他小厂可取大值。 燃烧一吨油,排放1.2-1.6万标立方米废 气,柴油取小值,重油取大值。 【城镇排水折算系数】 0.7~0.9,即用水量的70-90%。 【生活污水排放系数】采用本地区的实测系数。。 【生活污水中COD产生系数】60g/人.日。也可用本地区的实测系数 。 【生活污水中氨氮产生系数】7g/人.日。也可用本地区的实测系数。 使用系数进行计算时,人口数一般指城镇人口数;在外来较多的地 区,可用常住人口数或加上外来人口数。 【生活及其他烟尘排放量】
沸腾炉操作故障和事故处理

沸腾炉操作故障和事故处理(一)常见的操作事故沸腾炉操作上常见的故障,有下料处堆积、高温结疤、生成冷灰(或称沉渣)、不沸腾和突然正压等多种,对这些故障产生的原因、处理方法、预防措施,下面我们分别来进行讨论。
1、进料处堆积这是指沸腾炉内进料部位产生不沸腾堆积现象,有前室的沸腾炉通常在前室发生堆积。
一般现象是进料处炉底温度降到100℃以下,严重时该处中层温度也会降到 100℃以下,在进料口观察或停风检查,已明显可以看到进料部位炉内堆积,矿层发暗,并出现蓝色火苗。
造成这种情况最常见的是原料水分太高,通常原料水分达8%以上就容易出现堆积,水分越高堆积的可能性就越大。
其次是原料粒度增大,可能影响进料和沸腾不好,从而逐步发生堆积。
还有其它一些原因,包括投料太多、风量不足及长期不清理铁块螺丝杂物以致聚集过多等。
要预防进料处堆积的发生,最主要的是抓好原料管理,一定要设法控制进炉原料水分,不宜超过8%;使用多种原料时最好分开准放;粉碎好的矿料要保存好不要混入杂物;几种品种原料掺烧时,要求尽量掺匀。
一般遇到进料处炉底温度下降时,就要注意检查原料增况,如果检查仪表没有毛病,调节风量与矿量后仍无效,就要及时停炉打开人孔进行处理,否则矿越堆越多,容易影响炉膛内沸腾情况的变化,使事故扩大。
进料处堆积的处理较简便,停炉后只要打开人孔将堆积的料扒出来,检查炉内无疤块杂物,就可将人孔砌好,然后开车,如果原料条件及时改善,很快就会转入正常运行。
2、沸腾炉高温结疤沸腾炉高温结疤通常表现在下列一些方面:1)炉温开始骤升达1000℃以上,约十多分钟后经过处理,大部分温度点可以降下来,但个别点可能仍在1000℃以上,过半小时后它才缓慢下降,但降到200℃~300℃就更慢了,这时其它的温度点也可能陆续下降到100℃以下,说明炉内沸腾情况不正常。
2)炉底压力迅速下降,可降到3.92~4.9KPa并波动较大。
3)炉气出口SO2浓度很快降低,且不易再提高。
- 1、下载文档前请自行甄别文档内容的完整性,平台不提供额外的编辑、内容补充、找答案等附加服务。
- 2、"仅部分预览"的文档,不可在线预览部分如存在完整性等问题,可反馈申请退款(可完整预览的文档不适用该条件!)。
- 3、如文档侵犯您的权益,请联系客服反馈,我们会尽快为您处理(人工客服工作时间:9:00-18:30)。
目录前言 (2)第一章、课程设计的目的与要求 (2)第二章、设计正文 (2)1.总论 (2)2. 工艺流程及工艺原理和基本结构 (3)2.1工艺流程图 (3)2.2沸腾炉焙烧工段工艺流程的简述 (3)2-3.电除尘器的工作原理: (3)2.3.1基本原理示意图: (4)2.3.3影响电除尘性能的主要因素: (5)2.3.4除尘器停运时的工作 (5)2.4电除尘器的基本结构: (6)第三章、设计说明 (7)3-1. 除尘器主要技术参数的确定 (7)3-2.本体结构形式 (7)第四章、电除尘器结构尺寸的计算 (8)第五章、课程设计总结 (10)3. 设计总结 (13)第六章、参考文献 (13)附录 (13)前言我国燃煤锅炉的使用比较普遍 .在锅炉的使用过程中 ,由于煤炭的燃烧和鼓风机的强制送风 ,会产生大量的烟尘 ,特别是沸腾炉 ,由于其工作时是将煤炭磨成粉末状 ,用空气吹进炉膛 ,使其在沸腾状态下 (煤被气流托起 ,上下翻腾 )燃烧 ,因此 ,燃烧时产生的烟尘浓度非常大 。
对环境以及人类的危害非常大,我们大多数采用电器除尘来处理沸腾炉的炉气,炉气废热锅炉出来后经过旋风除尘器出去炉其中大部分灰尘,然后进入电除尘器,在经过50~60千伏的高压直流电场时,气体分子被电离成带正电荷的阳离子和带负电电荷的阴离子,这些离子附着在矿尘上使尘粒也带正或负电荷,各被异性的电极所吸引粘附到正负电极上,于是矿尘便从气体分离出来。
第一章、课程设计的目的与要求为沸腾炉炉气处理设计电除尘器,除尘效率不低于99.5%,试对该电除尘器进行总体设计。
设计参数1)烟气量:h Q /m 480003=;2)炉气含尘量3/20m g第二章、设计正文1.总论1.1设计题目:电除尘器处理沸腾炉炉气设计1.2设计要求:1)烟气量:h Q /m 480003=;2)炉气含尘量3/20m g除尘效率不低于99.5%。
1.3设计资料:见附录“原始资料”。
2.工艺流程及工艺原理和基本结构2.1工艺流程图2.2沸腾炉焙烧工段工艺流程的简述矿石由加料仓1经进料皮带2连续均匀的加入沸腾炉4,沸腾焙烧炉下部由空气鼓风机3鼓入空气,炉气出沸腾炉后进入废热锅炉5,废热锅炉同时起到两重作用;降低炉气温度和利用废热产生蒸汽。
炉气废热锅炉出来后经过旋风除尘器6出去炉其中大部分灰尘,然后进入电除尘器,在经过50~60千伏的高压直流电场时,气体分子被电离成带正电荷的阳离子和带负电电荷的阴离子,这些离子附着在矿尘上使尘粒也带正或负电荷,各被异性的电极所吸引粘附到正负电极上,于是矿尘便从气体分离出来。
2-3.电除尘器的工作原理:电除尘器内部主要有电晕极(阴极)、收尘极(阳极)及振打系统组成 。
当电除尘器通电后,电晕极与收尘极间形成电场,烟气粉尘进入除尘 器后在电场作用下发生电离,荷电后的粉尘逐向收尘极和电晕极。
通过 对这两极的振打,粉尘落入灰斗达到收尘目的。
2.3.1基本原理示意图:当电晕极上施加负性高压电且电压达到一定值时,电晕极的金属线表面出现青蓝色光并发出嘶嘶声,这种现象叫电晕放电。
本厂电除尘器按电极清灰方式分类属干式电除尘器,即在干燥状态下捕集烟气中的粉尘,沉积在除尘板上的粉尘借助机械振打清灰,该种振打式清灰方式易造成粉尘的二次飞扬。
本厂振打方式采用顶部电磁振打。
2.3.2电除尘的几个基本物理过程:(1),气体的电离。
可分为两类:自发电离和非自发电离,非自发电离是在外界能量作用下产生的,如气体受到X 光紫外线或其它辐射线照射时产生的电离。
自发电离能是在高压电场作用下产生的,不需要外加能量。
气体的非自发电离和和自发电离,通过气体的电流并不一定与电位差成正比,当电流增大到一定程度时,即使再增加电压,电流也不会增大,而是形成饱和电流。
(2), 悬浮尘粒的荷电。
在电除尘电场中,尘粒的荷电量与尘粒直径、电场强度和停电时间有关。
尘粒荷电有两种方式:电场荷电和扩散荷电。
所谓电场荷电是电场中离子的依附荷电。
扩散荷电是由于离子扩散现象产生的,对于尘粒直径大于0.5μm 的场合以电场荷电为主;小于0.2μm 的以扩散荷电为主,对于工业电除尘器来讲,电场荷电最为重要。
(3), 荷电尘粒向电极的运动。
一般来讲,荷电尘粒在除尘器中受四种力的作用,其运动服从牛顿定律,这四种作用力分别是:1) 重力 F=mg ,2 )静高压直流电 绝缘子收尘极(管) 电晕极(线)含尘气体净化气体灰斗整流器变压器电源电力 F=Eq ,3 )惯性力F=mdω/dt,4)介质阻力,服从斯托克定律:F=6πaηω,结论,ω=0.11aE2/η即荷电尘粒的速度ω与尘粒直径a成正比,与电场强度E的平方成正比,与介质的粘度η成反比。
(4),荷电粉尘的捕集。
尘粒在电场中的运动轨迹主要取决于气流状态和电场的综合因素,气流的状态和性质是确定尘粒被捕集的基础。
紊流条件下,电场中尘粒的运动途径几乎完全受紊流支配,只有当尘粒偶然进入库仑力能够起作用的层流边界区的地点,尘粒才有可能被捕集。
2.3.3影响电除尘性能的主要因素:1)粉尘特性:主要包括粉尘的粒径分布、真密度和堆积密度、粘附性和比电阻。
2)烟气性能:包括烟气温度、压力、成分、湿度、流速和含尘浓度等。
3)结构因素:包括电晕线的几何尺寸、形状、直径、数量和线间距等,电场数量、电场长度、振打方式、装置及外壳严密程度、灰斗形式和出灰口锁气器等。
4)操作因素:主要有伏安特性、漏风率、气流短路、二次飞扬和电晕线肥大。
2.3.4除尘器停运时的工作1、切断高压电源,将高压隔离开关柜开关开到接地。
2、阴阳极振打系统继续运转8—10小时,待除尘器内部自然冷却后(为防止结露)方可开启入孔门。
若紧急停机抢修可把操作室和就地操作箱中阴、阳极振打系统控制钮开到“手动”状态,连续振动打4小时并使风机保持工作,配合降温及清涮收尘极及电晕极上的积灰,4小时后方可开启入孔门。
3、开启入孔门前必须有“不准合闸”字样的警告牌挂在操作室和高压隔离开关柜上。
4、进入除尘器清除残留积灰。
若为长期停机必须把灰斗及输灰管道清空,防止灰的板结。
并每周开启一次振打系统及卸灰阀,每次4小时,以免锈蚀。
5、检查各振打装置的运行情况,振打锤头与振打砧承击位置是否正确,锤头是否灵活;不装安全销用手转动阴阳极振打轴看是否转动灵活。
不符合要求需修整。
6、检查顶部瓷套管、电瓷转轴和聚四氟乙烯板有无损坏现象,损坏的需更换,并将它们擦拭干净(最好两个月擦拭一次)。
7、检查电场内所有紧固螺栓是否松动,尤其以振打砧为主。
松动螺栓需紧固。
8、检查修整连接不好或变形的极板,极线,剪掉断线。
9、检查极距(阴、阳极间距),同极间距正常为400mm,异极间距正常为200mm。
如发现极距不符,应检查板线是否变形,校正其垂直度,同时观察阳极板间限位板安装是否合理。
限位板位于阳极振打平台,其安装中心线应在阳极板间距中心线上,并且限位板两侧与阳极板底部连接的撞击杆间距应在2mm—3mm左右。
10、检查入孔门的密封材料是否需更换。
入孔门旋转点是否需加润滑油。
11、清洁保温箱及瓷轴箱,使之保持干净。
清洁控制柜、变压器、高压隔离开关柜及其瓷瓶。
更换变压器干燥剂。
12、检查保温箱内的管状加热器、温度继电器工作是否正常,损坏的要更换或修整。
2.1.3除尘器投运前的工作1、开启阴阳极振打,观察振打是否正常。
2、检查除尘器内部,有无返修用过的工具,以及有无异物勾挂在阴、阳极上,灰斗底部卸灰阀内是否有异物。
3、检查各入孔门、检修门的气密性是否良好。
4、把控制室及就地操作箱控制按钮开到自动状态。
5、高压隔离柜接到工作状态并保证准确。
6、除尘器投运前6小时,瓷轴箱及保温箱的加热开始启动,以保证投运时不结露。
2.1.4除尘器投运期间的工作1、在运行中操作人员应监视各高压整流控制柜、集控盘和控制台仪表及指示灯有无异常。
2、操作人员一定要注意电压、电流的变化,特别是二次电压和二次电流,借此来了解除尘器性能改变,是否有设备结构上的故障,以及是否烟气性质有了变化。
从而采取相应的措施。
记录起晕和闪络时的一次电压、电流值及二次电压、电流值和闪络次数。
3、在运行过程中必须保持保温箱内温度在烟气露点温度以上以避免由于烟气中的水蒸气,酸雾粉尘冷凝于瓷套管表面上,造成爬电击穿。
4、对除尘器的巡检过程中要耳听,眼看,手摸。
耳听除尘器有无漏风点;除尘器振打系统工作是否正常。
眼看除尘器各电机转动是否正常,电机转动的同时振打传动轴是否同步转动。
手摸电机及变压器温度是否正常。
检查其油位,不足需适当加注。
注:锅炉燃油时,除尘器禁止投运,燃煤一小时后开始投运。
2.4电除尘器的基本结构:(1)电气系统a)高压供电装置:高压整流变压器,电抗器,高压控制柜b)低压自动控制系统:保温箱的恒温控制,振打程序控制,排灰控制,安全连锁(2)本体系统a)收尘极系统:极板、悬吊及振打b)电晕极系统:电晕线、阴极大、小框架,阴极吊挂,阴极振打c)烟箱:进气烟箱、出气烟箱d)气流均布装置:气流均布板、收尘电场内部阻流板、灰斗阻流板、导流板e)槽形极板:f)壳体:g)支座h)储、排灰系统i)辅助设施第三章、设计说明3-1. 除尘器主要技术参数的确定(1)电场风速:考虑灰的比电阻高,灰分质量轻、粒度小等因数,选取电场风速v = 1.1m/s(2)板间距:考虑到宽极距能有效的减少高比电阻粉尘产生的反电晕,能减少由于安装的误差、运行中的热变形等对除尘器性能的影响,提高运行的稳定性,另外也可以减轻设备质量、降低造价、易于维护保养。
选取板间距2b = 400 mm(3)线间距:考虑采用采用C型板,紧固型悬挂方式,极线采用RS管状芒刺线,选取线间距2c = 500 mm(4)有效驱进速度查阅相关资料及粉尘颗粒直径等因素,选取驱进速度ω = 0.13cm/s3-2.本体结构形式(1)采用卧式电除尘器(2)设计为双室m=2(3)电场数 n=4(4)振打方式:电磁振打(5)进出气烟箱:①进气方式:上进气方式②气流分布:在进气烟箱内设置开孔率为50%气流均布板和导流板③槽形极板:在出气烟箱内设置槽形极板,采用水平出气试(6)灰斗:设置四棱台形灰斗第四章、电除尘器结构尺寸的计算4-1.计算所需的收尘极面积A (取k=1.1) 25.212481.1360008.0%)5.991ln(1050000)1ln(m k Q A =⨯⨯-⨯-=⨯--=ωη 4-2.初定电场断面积2'2.26536001.11050000V Q F m =⨯== 4-3.极板的有效高度m m 1251.1122.2652F h '≈=== 4-4.通道数5523.55124.02.26522b B Z '≈=⨯===bh F 4-5.电厂的有效宽度m b Z B 224.0552'=⨯=⋅=4-6.验算实际断面积2'2642212h m B F =⨯=⋅=验算电场风速s m 11.136002641050000F Q '=⨯==V s m 1.1=V sm 11.1'=V 1.001.0-'〈=V V 错误!未指定书签。