热成形技术在车身轻量化设计中的应用
汽车“热成形钢板冲压件”材料手册
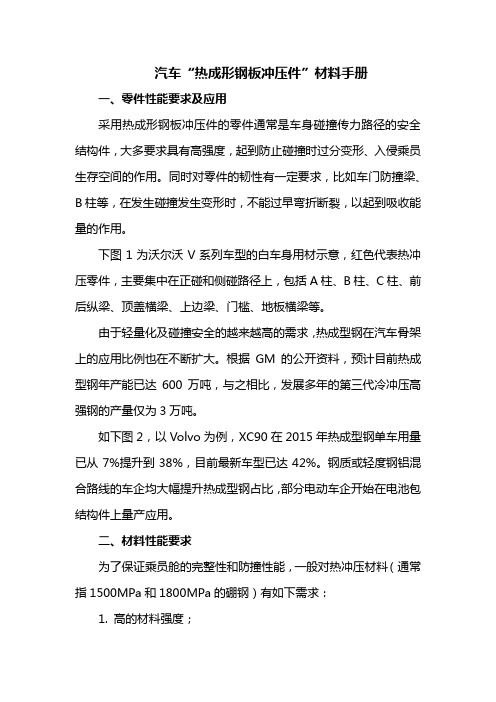
汽车“热成形钢板冲压件”材料手册一、零件性能要求及应用采用热成形钢板冲压件的零件通常是车身碰撞传力路径的安全结构件,大多要求具有高强度,起到防止碰撞时过分变形、入侵乘员生存空间的作用。
同时对零件的韧性有一定要求,比如车门防撞梁、B柱等,在发生碰撞发生变形时,不能过早弯折断裂,以起到吸收能量的作用。
下图1为沃尔沃V系列车型的白车身用材示意,红色代表热冲压零件,主要集中在正碰和侧碰路径上,包括A柱、B柱、C柱、前后纵梁、顶盖横梁、上边梁、门槛、地板横梁等。
由于轻量化及碰撞安全的越来越高的需求,热成型钢在汽车骨架上的应用比例也在不断扩大。
根据GM的公开资料,预计目前热成型钢年产能已达600万吨,与之相比,发展多年的第三代冷冲压高强钢的产量仅为3万吨。
如下图2,以Volvo为例,XC90在2015年热成型钢单车用量已从7%提升到38%,目前最新车型已达42%。
钢质或轻度钢铝混合路线的车企均大幅提升热成型钢占比,部分电动车企开始在电池包结构件上量产应用。
二、材料性能要求为了保证乘员舱的完整性和防撞性能,一般对热冲压材料(通常指1500MPa和1800MPa的硼钢)有如下需求:1. 高的材料强度;2. 良好的弯曲断裂韧性;3.均匀的组织性能;4.合适的成本;5.镀层材料还需求较好的耐蚀性(分为镀AS、镀锌和裸板);6.良好的热处理工艺性能(奥氏体化温度、临界冷却速度);7.良好的点焊、激光焊性能。
当然,现在随着汽车安全件的精细化设计需求,除了需求越来越高强度的硼钢(22MnB5、28MnB5、34MnB5)外,也需要中等强度的高韧性的热冲压材料作为软区材料,例如B柱的下端使用低合金高强钢6Mn6等,此类材料的需求为高弯曲韧性、良好的可焊性、较大的临界冷却速度,室温组织可以为铁素体、珠光体或马氏体组织。
三、行业用材分析1、行业用材现状•从基材来讲:①硬区:目前热冲压钢板主要应用的是1500MPa的22MnB5和1800MPa的34MnB5硼钢,用作硬区部位,即需要超高强度来减小或防止变形的部位;②软区:基于激光拼焊(TWB,Tailored Welded Blanks)技术的成熟,也有500/600MPa级的6Mn6、1000MPa级的8Mn*、1200MPa级的12Mn*等材料用于激光拼焊件的低强度部位,俗称软区。
【技术帖】热成型技术的应用现状和发展趋势

【技术帖】热成型技术的应用现状和发展趋势摘要:阐述了热成型技术在汽车行业的起源和发展过程,简单介绍了热成型的分类与技术原理,探讨了先进热成型技术的发展趋势,分析了国内外的具体应用及现状,总结了热成型技术在国内自主品牌应用中所存在的问题。
关键词:热成型轻量化碰撞1前言随着汽车新材料的不断应用,以及满足市场对轻量化和高安全性能汽车需求的先进设计理念的不断引入,制造工艺也需要不断革新。
采用高强度钢板冲压件制造车身是同时实现车体轻量化和提高碰撞安全性的重要途径。
目前汽车车身安全件普遍采用1 300~1 500 MPa 级的超高强零件,但是高强度钢板强度越高,越难成形,尤其是当钢板强度达到1 500 MPa时,常规的冷冲压成形工艺几乎无法成形。
热成型技术的采用可以很好地解决超高强零件的成型问题。
2热成型技术发展历程19世纪中期,瑞典SSAB公司研发出了第一代热轧与冷轧含硼钢;20 世纪70 年代,热成型工艺首先在瑞典得到开发并取得专利。
瑞典SSAB 汽车公司在1984 年成为第一家采用硬化硼钢板的汽车制造商,生产出第一件热成型汽车零件——客车门内防撞梁。
随后,这一技术相继应用于保险杠横梁、A柱和B柱加强件以及底盘组件等,但是由于加工缓慢,且价格高,应用热成型技术生产的零件种类非常有限,只被原始设备制造商所接受。
80 年代中期之后,热成型技术进入高速发展阶段,当时有3 家公司可提供零件;1991 年,热成型保险杠横梁用于福特汽车;全球生产的热成型零件数量从1987年的3百万件增加到1997年的8百万件。
从2000 年起,更多热成型零件被用在汽车上,而且年产件量在2007 年上升到约1.07 亿件。
2013 年,约80%的白车身骨架类零件均可由热冲压技术加工,产量超过3亿件。
目前,全世界热成型生产线已超过200 条,Benteler 拥有其中近40%,是世界上最主要的热成型零件供应商,GESTAMP 是世界上首个提供热成型件的厂家,其客户主要集中在欧洲车系,COSMA也是主要的热成型供应商之一。
汽车用高强度钢热成型技术
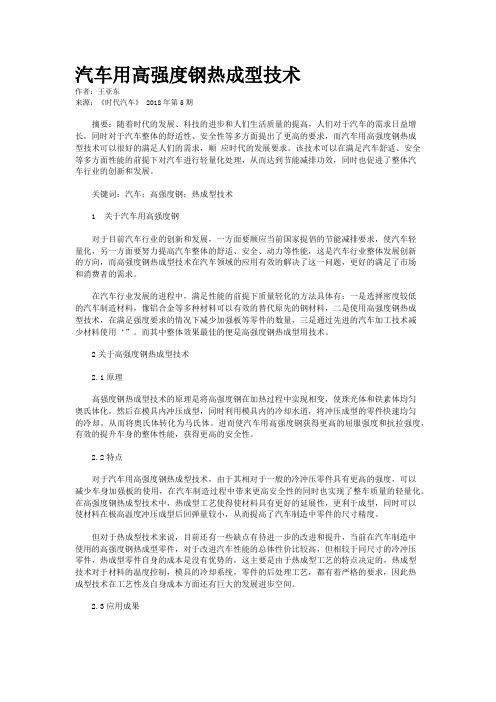
汽车用高强度钢热成型技术作者:王亚东来源:《时代汽车》 2018年第5期摘要:随着时代的发展、科技的进步和人们生活质量的提高,人们对于汽车的需求日益增长,同时对于汽车整体的舒适性、安全性等多方面提出了更高的要求,而汽车用高强度钢热成型技术可以很好的满足人们的需求,顺应时代的发展要求。
该技术可以在满足汽车舒适、安全等多方面性能的前提下对汽车进行轻量化处理,从而达到节能减排功效,同时也促进了整体汽车行业的创新和发展。
关键词:汽车;高强度钢;热成型技术1 关于汽车用高强度钢对于目前汽车行业的创新和发展,一方面要顺应当前国家提倡的节能减排要求,使汽车轻量化,另一方面要努力提高汽车整体的舒适、安全、动力等性能,这是汽车行业整体发展创新的方向,而高强度钢热成型技术在汽车领域的应用有效的解决了这一问题,更好的满足了市场和消费者的需求。
在汽车行业发展的进程中,满足性能的前提下质量轻化的方法具体有:一是选择密度较低的汽车制造材料,像铝合金等多种材料可以有效的替代原先的钢材料,二是使用高强度钢热成型技术,在满足强度要求的情况下减少加强板等零件的数量,三是通过先进的汽车加工技术减少材料使用‘”。
而其中整体效果最佳的便是高强度钢热成型用技术。
2关于高强度钢热成型技术2.1原理高强度钢热成型技术的原理是将高强度钢在加热过程中实现相变,使珠光体和铁素体均匀奥氏体化,然后在模具内冲压成型,同时利用模具内的冷却水道,将冲压成型的零件快速均匀的冷却,从而将奥氏体转化为马氏体。
进而使汽车用高强度钢获得更高的屈服强度和抗拉强度,有效的提升车身的整体性能,获得更高的安全性。
2.2特点对于汽车用高强度钢热成型技术,由于其相对于一般的冷冲压零件具有更高的强度,可以减少车身加强板的使用,在汽车制造过程中带来更高安全性的同时也实现了整车质量的轻量化。
在高强度钢热成型技术中,热成型工艺使得使材料具有更好的延展性,更利于成型,同时可以使材料在极高温度冲压成型后回弹量较小,从而提高了汽车制造中零件的尺寸精度。
6. 汽车轻量化的九大关键工艺
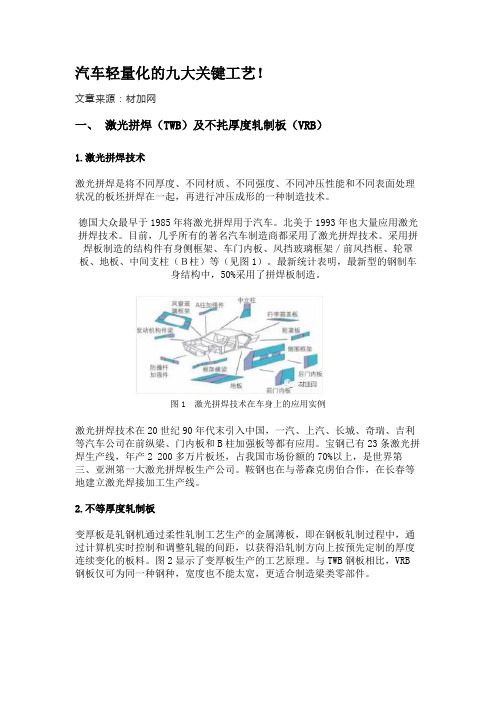
汽车轻量化的九大关键工艺!文章来源:材加网一、激光拼焊(TWB)及不扥厚度轧制板(VRB)1.激光拼焊技术激光拼焊是将不同厚度、不同材质、不同强度、不同冲压性能和不同表面处理状况的板坯拼焊在一起,再进行冲压成形的一种制造技术。
德国大众最早于1985年将激光拼焊用于汽车。
北美于1993年也大量应用激光拼焊技术。
目前,几乎所有的著名汽车制造商都采用了激光拼焊技术。
采用拼焊板制造的结构件有身侧框架、车门内板、风挡玻璃框架/前风挡框、轮罩板、地板、中间支柱(B柱)等(见图1)。
最新统计表明,最新型的钢制车身结构中,50%采用了拼焊板制造。
图1 激光拼焊技术在车身上的应用实例激光拼焊技术在20世纪90年代末引入中国,一汽、上汽、长城、奇瑞、吉利等汽车公司在前纵梁、门内板和B柱加强板等都有应用。
宝钢已有23条激光拼焊生产线,年产2 200多万片板坯,占我国市场份额的70%以上,是世界第三、亚洲第一大激光拼焊板生产公司。
鞍钢也在与蒂森克虏伯合作,在长春等地建立激光焊接加工生产线。
2.不等厚度轧制板变厚板是轧钢机通过柔性轧制工艺生产的金属薄板,即在钢板轧制过程中,通过计算机实时控制和调整轧辊的间距,以获得沿轧制方向上按预先定制的厚度连续变化的板料。
图2显示了变厚板生产的工艺原理。
与TWB钢板相比,VRB 钢板仅可为同一种钢种,宽度也不能太宽,更适合制造梁类零部件。
图2 不等厚度轧制板生产原理德国Mubea公司有两条变厚板生产线,年产7万t。
板厚为0.7~3.5m m,原始板料的最高强度为800MP a级别。
目前,欧洲70余个车型使用变厚板或者变厚管产品。
奔驰C级车中通道加强板、前地板纵梁、后保险杠、后地板横梁等11个零件使用了VRB钢板。
我国宝钢和东北大学均开展了VRB钢板的研发和生产工作,目前具备了小批量供货的能力。
借助于强大的材料开发能力,宝钢形成了VRB零件的设计、材料开发、成形过程模拟、模具设计和产品质量评估的能力,并已试制成功前纵梁、仪表板支架、顶盖横梁等零件,同时也轧制成功了1 500MPa级别的非镀层和铝硅镀层的热冲压成形钢板,成功试制了热冲压成形VRB中通道零件。
汽车轻量化的技术与方法
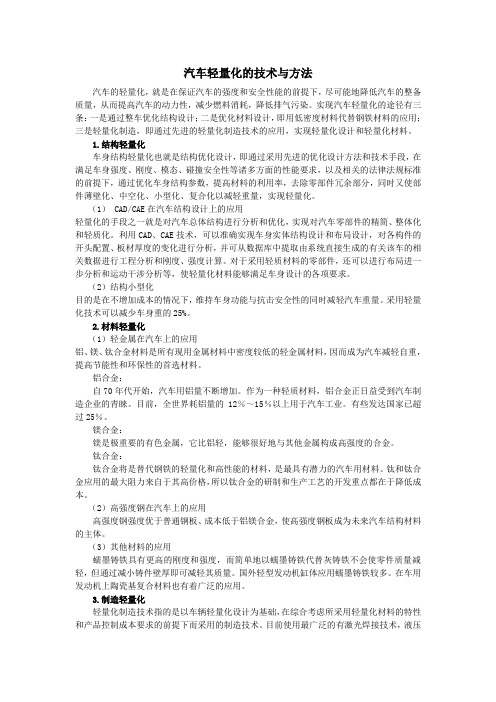
汽车轻量化的技术与方法汽车的轻量化,就是在保证汽车的强度和安全性能的前提下,尽可能地降低汽车的整备质量,从而提高汽车的动力性,减少燃料消耗,降低排气污染。
实现汽车轻量化的途径有三条:一是通过整车优化结构设计;二是优化材料设计,即用低密度材料代替钢铁材料的应用;三是轻量化制造,即通过先进的轻量化制造技术的应用,实现轻量化设计和轻量化材料。
1.结构轻量化车身结构轻量化也就是结构优化设计,即通过采用先进的优化设计方法和技术手段,在满足车身强度、刚度、模态、碰撞安全性等诸多方面的性能要求,以及相关的法律法规标准的前提下,通过优化车身结构参数,提高材料的利用率,去除零部件冗余部分,同时又使部件薄壁化、中空化、小型化、复合化以减轻重量,实现轻量化。
(1) CAD/CAE在汽车结构设计上的应用轻量化的手段之一就是对汽车总体结构进行分析和优化,实现对汽车零部件的精简、整体化和轻质化。
利用CAD、CAE技术,可以准确实现车身实体结构设计和布局设计,对各构件的开头配置、板材厚度的变化进行分析,并可从数据库中提取由系统直接生成的有关该车的相关数据进行工程分析和刚度、强度计算。
对于采用轻质材料的零部件,还可以进行布局进一步分析和运动干涉分析等,使轻量化材料能够满足车身设计的各项要求。
(2)结构小型化目的是在不增加成本的情况下,维持车身功能与抗击安全性的同时减轻汽车重量。
采用轻量化技术可以减少车身重的25%。
2.材料轻量化(1)轻金属在汽车上的应用铝、镁、钛合金材料是所有现用金属材料中密度较低的轻金属材料,因而成为汽车减轻自重,提高节能性和环保性的首选材料。
铝合金:自70年代开始,汽车用铝量不断增加。
作为一种轻质材料,铝合金正日益受到汽车制造企业的青睐。
目前,全世界耗铝量的12%~15%以上用于汽车工业。
有些发达国家已超过25%。
镁合金:镁是极重要的有色金属,它比铝轻,能够很好地与其他金属构成高强度的合金。
钛合金:钛合金将是替代钢铁的轻量化和高性能的材料,是最具有潜力的汽车用材料。
高强度钢板的两种热成形技术
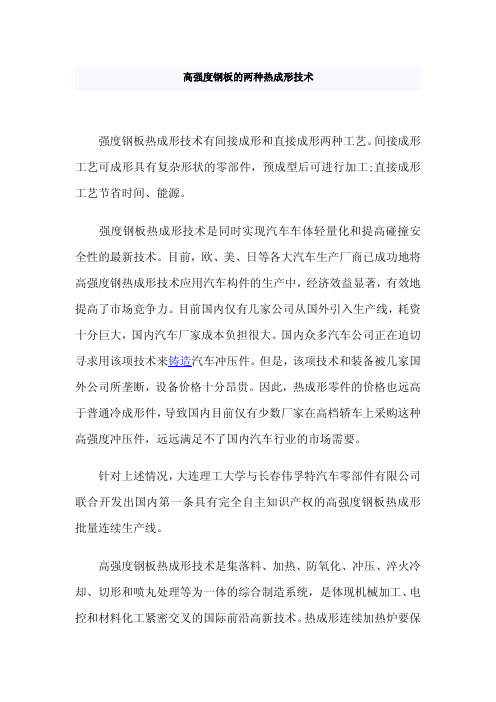
高强度钢板的两种热成形技术强度钢板热成形技术有间接成形和直接成形两种工艺。
间接成形工艺可成形具有复杂形状的零部件,预成型后可进行加工;直接成形工艺节省时间、能源。
强度钢板热成形技术是同时实现汽车车体轻量化和提高碰撞安全性的最新技术。
目前,欧、美、日等各大汽车生产厂商已成功地将高强度钢热成形技术应用汽车构件的生产中,经济效益显著,有效地提高了市场竞争力。
目前国内仅有几家公司从国外引入生产线,耗资十分巨大,国内汽车厂家成本负担很大。
国内众多汽车公司正在迫切寻求用该项技术来铸造汽车冲压件。
但是,该项技术和装备被几家国外公司所垄断,设备价格十分昂贵。
因此,热成形零件的价格也远高于普通冷成形件,导致国内目前仅有少数厂家在高档轿车上采购这种高强度冲压件,远远满足不了国内汽车行业的市场需要。
针对上述情况,大连理工大学与长春伟孚特汽车零部件有限公司联合开发出国内第一条具有完全自主知识产权的高强度钢板热成形批量连续生产线。
高强度钢板热成形技术是集落料、加热、防氧化、冲压、淬火冷却、切形和喷丸处理等为一体的综合制造系统,是体现机械加工、电控和材料化工紧密交叉的国际前沿高新技术。
热成形连续加热炉要保证板料加热到设定的温度充分奥氏体化,同时避免没有防氧化涂层板料的高温氧化脱碳,这决定了热成形连续加热炉与其他加热炉相比应具有独特的核心技术。
成形有间接成形和直接成形两种工艺。
热成形间接成形工艺是指板料先经过冷冲压进行预成形,然后加热到奥氏体化温度,保温一段时间后放到具有冷却系统的模具里进行最终成形及淬火。
热成形间接成形工艺的优点如下:(1)可以成形具有复杂形状的车内零部件,几乎可以获得目前所有的冲压承载件。
(2)板料预成形后,后续热成形工艺不需要过多考虑板料高温成形性能,可以确保板料完全淬火得到所需要的马氏体组织。
(3)板料预成形后可以进行修边、翻边、冲孔等工艺加工,避免板料淬火硬化后加工困难问题。
热成形直接成形工艺是指板料加热到奥氏体化温度保温一段时间后直接放到具有冷却系统的模具里进行成形及淬火。
高强度热成型在轻量化钢铝车身中
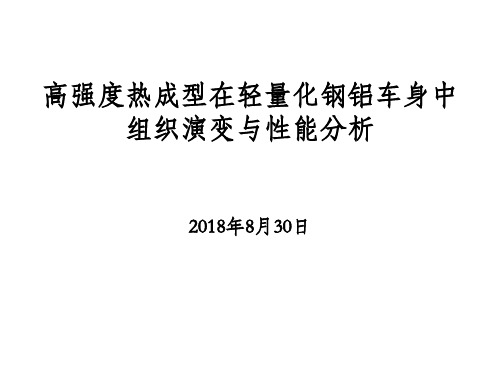
车身用钢的强度演化发展
第二部分:车身用热成型钢组织演变以及以及性能分析
1500Mpa级别热成型钢材22MnB5化学成分表(wgt %)
项目 C
Si Mn Cr Mo P
S
Ti
Al
B
下限 0.20 0.15 1.1
0.02 0.02 0.001
上限 0.25 0.40 1.4 0.35 0.35 0.03 0.01 0.05 0.05 0.005
B
N
V
Nb
下限 0.3 1.1
0.03 0.001
上限
0.38
2
0.4 0.35
0.1
0.05
0.003
0.06
0.004
0.00 6
0.3
0.06
力学性能:
屈服强度:
抗拉强度:
断后伸长率:
2000Mpa级别热成型钢出厂状态组织
CCT曲线图 创新强手化段硬:化机理:
1~5nm
Vanadur®2Gpa热冲压后组织状态
出厂状态力学性能: 屈服强度:350~550Mpa 抗拉强度:500~700Mpa 断后伸长率:>10%
热轧22MnB5钢出厂状态组织
22MnB5材料的CCT曲线图
22MnB5热冲压后组织状态
热冲压后力学性能: 屈服强度: 950~1250 Mpa 抗拉强度:1300~ 1650 Mpa 断后伸长率: >6%
第三部分:车身用铝合金组织演变以及以及性能分析
1.汽车用5xxx系、6xxx系典型铝合金的组织及性能指标 2.汽车用7xxx系热成型铝合金的组织及性能指标 3.热成型铝制零部件生产的关键工艺控制
第四部分:总结与展望
汽车轻量化车身先进连接技术的应用与发展
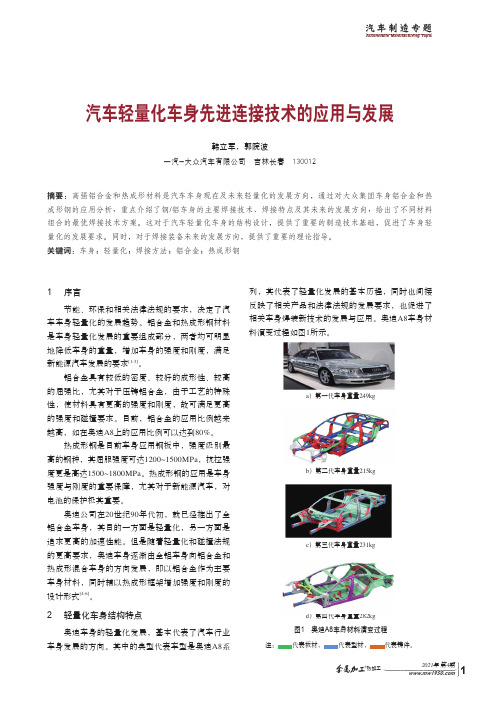
2021年 第4期 热加工1汽车轻量化车身先进连接技术的应用与发展韩立军,郭院波一汽-大众汽车有限公司 吉林长春 130012摘要:高强铝合金和热成形材料是汽车车身现在及未来轻量化的发展方向,通过对大众集团车身铝合金和热成形钢的应用分析,重点介绍了钢/铝车身的主要焊接技术、焊接特点及其未来的发展方向,给出了不同材料组合的最优焊接技术方案。
这对于汽车轻量化车身的结构设计,提供了重要的制造技术基础,促进了车身轻量化的发展要求。
同时,对于焊接装备未来的发展方向,提供了重要的理论指导。
关键词:车身;轻量化;焊接方法;铝合金;热成形钢1 序言节能、环保和相关法律法规的要求,决定了汽车车身轻量化的发展趋势。
铝合金和热成形钢材料是车身轻量化发展的重要组成部分,两者均可明显地降低车身的重量,增加车身的强度和刚度,满足新能源汽车发展的要求[1-3]。
铝合金具有较低的密度、较好的成形性、较高的屈强比,尤其对于压铸铝合金,由于工艺的特殊性,使材料具有更高的强度和刚度,故可满足更高的强度和碰撞要求。
目前,铝合金的应用比例越来越高,如在奥迪A8上的应用比例可以达到80%。
热成形钢是目前车身应用钢板中,强度级别最高的钢种,其屈服强度可达1200~1500MPa ,抗拉强度更是高达1500~1800MPa 。
热成形钢的应用是车身强度与刚度的重要保障,尤其对于新能源汽车,对电池的保护极其重要。
奥迪公司在20世纪90年代初,就已经推出了全铝合金车身,其目的一方面是轻量化,另一方面是追求更高的加速性能。
但是随着轻量化和碰撞法规的更高要求,奥迪车身逐渐由全铝车身向铝合金和热成形混合车身的方向发展,即以铝合金作为主要车身材料,同时辅以热成形框架增加强度和刚度的设计形式[4-6]。
2 轻量化车身结构特点奥迪车身的轻量化发展,基本代表了汽车行业车身发展的方向。
其中的典型代表车型是奥迪A8系列,其代表了轻量化发展的基本历程,同时也间接反映了相关产品和法律法规的发展要求,也促进了相关车身焊装新技术的发展与应用。
热冲压成形工艺解析

热冲压成形工艺解析热冲压成形工艺解析随着汽车轻量化的发展,钢板热冲压技术应运而生,其将高强度钢板在温度场内由奥氏体转变为马氏体,提高了板料的强度,降低了板料的重量。
本文对热冲压成形板料和设备应用进行了总结,并预测了热冲压技术的未来发展趋势...安全、节能和环保是消费者最关心的汽车性能指标。
目前,降低汽车燃料消耗、减少CO2和废气排放是社会的主要需求。
车身轻量化对于减轻整车自身重量、降低油耗和促进节能环保至关重要。
为了适应轻量化的发展趋势,热成形工艺和应用技术应运而生。
热成形压力机简称热冲压,是相对于常见的冷冲压成形而言。
为了帮助减轻汽车自身重量并提高汽车的安全性,钢铁业开发出许多种类的高强度钢板。
为了克服高强度钢板冷成形的困难,热冲压需要通过将钢板加热,使其板料上产生一个不断变化的温度场。
在温度场的影响下,板料的基体组织和力学性能发生变化,导致板料的应力场也发生变化,同板料的应力场变化又反作用于温度场。
热成形工艺过程为:首先将常温下强度为500~600MPa的硼合金钢板加热到约940℃,全奥氏体后,将材料从加热炉转移到热成形的压力机中,该过程在空气中进行,必须尽快完成,如果成形前材料温度降到750℃以下,就可能形成铁素体从而恶化零件的机械性能。
送入内部具有冷却系统的模具内,压力机进行冲压、成形。
板料在模具内快速冷却(水冷),将奥氏体转变为马氏体(200℃以下),冷却速度一般为-40~100℃/s以保证零件的淬透性,使冲压件得到硬化,大幅度提高强度(1500MPa)。
所以热成形工艺就是板料内部温度场与应力场共存且相互耦合的变化过程。
热冲压成形的生产流程为拆垛装置、加热炉、上料装置、成形冷却、激光切割和喷丸涂油,如图1所示。
图1 热冲压成形的工艺流程热成形板料选择目前,热成形用钢均选用硼钢,因微量的硼可有效提高钢的淬透性,使零件在模具中以适当的冷却速度获得所需要的马氏体组织,从而保证零件的高强度。
热成形冲压板材主要分为镀层与无镀层板材。
热成型技术的应用现状和发展趋势

摘要:阐述了热成型技术在汽车行业的起源和发展过程,简单介绍了热成型的分类与技术原理,探讨了先进热成型技术的发展趋势,分析了国内外的具体应用及现状,总结了热成型技术在国内自主品牌应用中所存在的问题。
关键词:热成型轻量化碰撞中图分类号:V261.3;TG306文献标识码:BDOI :10.19710/ki.1003-8817.20180167热成型技术的应用现状和发展趋势薛戬(奇瑞汽车股份有限公司,芜湖241006)作者简介:薛戬(1982—),男,助理材料工程师,学士,研究方向为车身底盘金属材料及轻量化。
1前言随着汽车新材料的不断应用,以及满足市场对轻量化和高安全性能汽车需求的先进设计理念的不断引入,制造工艺也需要不断革新。
采用高强度钢板冲压件制造车身是同时实现车体轻量化和提高碰撞安全性的重要途径。
目前汽车车身安全件普遍采用1300~1500MPa 级的超高强零件,但是高强度钢板强度越高,越难成形,尤其是当钢板强度达到1500MPa 时,常规的冷冲压成形工艺几乎无法成形。
热成型技术的采用可以很好地解决超高强零件的成型问题。
2热成型技术发展历程19世纪中期,瑞典SSAB 公司研发出了第一代热轧与冷轧含硼钢;20世纪70年代,热成型工艺首先在瑞典得到开发并取得专利。
瑞典SSAB 汽车公司在1984年成为第一家采用硬化硼钢板的汽车制造商,生产出第一件热成型汽车零件——客车门内防撞梁。
随后,这一技术相继应用于保险杠横梁、A 柱和B 柱加强件以及底盘组件等,但是由于加工缓慢,且价格高,应用热成型技术生产的零件种类非常有限,只被原始设备制造商所接受。
80年代中期之后,热成型技术进入高速发展阶段,当时有3家公司可提供零件;1991年,热成型保险杠横梁用于福特汽车;全球生产的热成型零件数量从1987年的3百万件增加到1997年的8百万件。
从2000年起,更多热成型零件被用在汽车上,而且年产件量在2007年上升到约1.07亿件。
2000 MPa热成形车门防撞梁开发与性能研究

汽车工艺与材料Automobile Technology&Material2000MPa热成形车门防撞梁开发与性能研究段宏强韩志勇王斌(爱驰汽车(上海)有限公司,上海200090)摘要:为了满足纯电动汽车车身的轻量化需求,采用新型2000MPa热成形钢替代传统22MnB5进行车门防撞梁的轻量化设计。
为验证2000MPa热成形车门防撞梁的应用可行性,采用LS-DYNA软件对整车进行侧面碰撞仿真分析,结果显示碰撞侵入量、侵入速度和关键零部件的塑性应变均符合设计要求。
经热冲压仿真分析,2000MPa热成形车门防撞梁符合工艺要求,软模和硬模阶段研究了不同的加热设备和工艺参数对2000MPa热成形车门防撞梁组织和拉伸力学性能的影响,结果显示加热温度930℃,保温时间300s和330s,转移时间约12s,可实现热成形后的抗拉强度≥2000MPa的性能目标。
将前后车门防撞梁分别置于万能试验机上进行零件三点弯曲性能检测,结果显示前车门防撞梁三点弯峰值力大于25kN,后车门防撞梁三点弯峰值力大于29kN,远高于10.01kN的设计目标值。
经过2000MPa热成形车门防撞梁和车门内板的点焊工艺参数优化和连接设计优化,满足了前后车门系统的开闭耐久性能要求。
在保证整车侧碰安全性能的情况下,2000MPa热成形车门防撞梁比采用传统22MnB5质量减轻11.7%,实现显著的轻量化效果。
关键词:2000MPa热成形车门防撞梁轻量化中图分类号:U465.1文献标识码:B DOI:10.19710/ki.1003-8817.20200447Design and Performance Research on2000MPa Hot Forming DoorImpact BeamDuan Hongqiang,Han Zhiyong,Wang Bin(Aiways Automotive(Shanghai)Co.,Ltd.,Shanghai200090)Abstract:In this research,a novel2000MPa hot forming steel is used to replace traditional22MnB5for lightweight design of door impact beam to satisfy the lightweight demands of pure electric vehicle.Side collision simulation analysis is conduct with LS-DYNA to verify the application feasibility of2000MPa hot forming door impact beam,which shows that the intrusion velocity,intrusion displacement,plastic strain of key parts meet the design requirements.The2000MPa hot forming door impact beam is proved to satisfy the process requirements by hot forming simulation analysis.The influence of different heating equipment and process parameters on microstructure and tensile mechanical properties is investigated during soft tooling and hard tooling stage of2000MPa hot forming door impact beam.The result shows that tensile strength target exceeding2000MPa is achieved by heating at930℃for300s and330s with a transferring time of about12s.The front and rear door impact beam are placed on universal testing machine to test the three points bending performance.The result indicates that peak force of front door impact beam exceeds25kN,and that of rear door impact beam exceeds29kN,far beyond the design target of 10.01kN.The opening and closing durability requirements of front and rear door system are satisfied through the spot welding parameter and joining design optimization.Significant lightweight effect of11.7%is eventually achieved by 2000MPa hot forming door impact beam compared with traditional22MnB5under the premise of ensuring side collision performance.Key words:2000MPa,Hot forming,Door impact beam,Lightweight作者简介:段宏强(1991—),男,硕士学位,研究方向为汽车用高强钢、铝合金材料的开发及应用。
奇瑞汽车轻量化技术新进展

发 ( 图6 ,显著 降低 了零部件 的重量 ( 见 ) 见附表 ) 。 同时 奇瑞公司掌握 了S MC ̄IMT I : G 复合材料 的零 部件设
计 、产 品试制和试验验证的综合开发能力 。
()S a MC后 备 门
l
()G 防 护罩 b MT
图 6
材料变化前后零 件重 量对 比表
成形 、热压 成形和滚 压成形等 材料 成形应 用技术将 成为
首选。
汽车轻量化材料应用现状
轻 量 化 材料 是 指 可用 来减 轻 汽车 自重 的材 料 ,它
有两大 类 :一类 是低密度 的轻质材料 ,如铝合 金、镁合 金 、钛 合金 、塑料 和 复合 材 料等 ;另一 类是 高 强 度材 料 ,如 高强度钢 等。 目前 ,已得到实 际工业化应 用的轻 量化材料主要有 高强度钢 、铝合金 、镁 合金和塑料等。
此 外 ,奇 瑞 公司瑞麒 G5 开发 了镁 合金仪表 板 骨架
成本 与普 通 点焊设 计 基本持 平 ,但 能显 著提 高正 碰性
( 见图5 ),已完成各种试验验证 ,实现批量装车。仪
表板 骨架采用镁 合金 整体压铸 ,绿色环保的 同时单 件减
能,在奇瑞A 的前纵梁上已有批量应用 ( 3 见图7 ),并
轻量化 系数的定义为 :
M L =-- -— -- - — - -- C
2铝合金 .
铝 合金在奇瑞 公司的 产品上 已得 到广泛应用 ,铝合
式中:
L —— 轻量化 系数 ;
金零部件 以铸件 为主 ,还有 少量的型材 和板材 ,已 占到 整车备 重的 1%左右 。典 型应用 为变速 器壳体 、发 动机 0 缸 体 、缸盖 、油底 壳 、底盘转 向节 、控制 臂 、隔热板 和 散热器等零 件 ( 见图3 )。另外 ,在 国家 “6 ”项 目的 83 支持下 ,奇瑞完 成了铝合金板 材的应用开发 工作 ,使A 5
电动汽车白车身轻量化设计及性能分析

电动汽车白车身轻量化设计及性能分析摘要:随着全球经济的发展和人们环保意识的不断提高,电动汽车作为新能源汽车的代表,逐渐成为汽车产业的重要发展方向。
与传统燃油汽车相比,电动汽车具有零排放、低噪音、高效节能等优势。
然而,在实际应用中,电动汽车还面临着一系列问题,例如,续航里程不足、使用寿命短、充电速度慢等。
而这些问题都与电动汽车的白车身结构设计和轻量化策略密切相关。
基于此,本文阐述了优化电动汽车白车身轻量化设计的策略,以供参考。
关键词:电动汽车;白车身轻量化设计;优化策略引言汽车白车身轻量化设计是电动汽车的主要组成部分。
对于电动汽车来说,对白车身进行轻量化设计,不仅能够降低对汽车能源的消耗和,还能提高电动汽车的行驶续航力和里程。
因此,对电动汽车白车身进行各种轻量化车型设计,就显得尤为重要。
一、优化电动汽车白车身轻量化设计的意义为发展节能环保的新产业,科技部已经发布了关于新能源电动汽车的重大专项,从长远经济发展、社会效益还是整体经济效益角度进行一个综合衡量考虑,低油耗、低污染排放的电动汽车发展是绿色节约型经济社会汽车发展的大趋势方向,包含纯能源电动汽车在内的多种新能源电动汽车快速发展也将是大势所趋。
与其他传统大型燃油电动汽车产品相比,纯动力电动汽车因为其特殊的传动原理及车身结构,白车身轻量化已经是必然的产业发展战略方向。
电动车白车身轻量化设计是为了提高能源的利用率,从而加强新能源电动车续航能力。
综合考虑人机工程、产品工业工艺技术和设计、成本以及效益等诸多影响因素,确定采用相应的设计生产工艺。
轻量化的技术研究对电动汽车的持续发展来说势在必行,只有真正实现了对于白车身轻量化研究才能大大降低技术开发成本,提高使用性能,从而更加接近国际市场需求。
二、优化电动汽车白车身轻量化设计的策略(一)使用新型的制造材料与传统金属材料相比,新型材料通常更轻、更坚固,因此,在设计和制造电动汽车时,使用新型材料可以将整个车身的重量减轻,从而改善续航里程和节能性。
我们的温热成形技术及产品
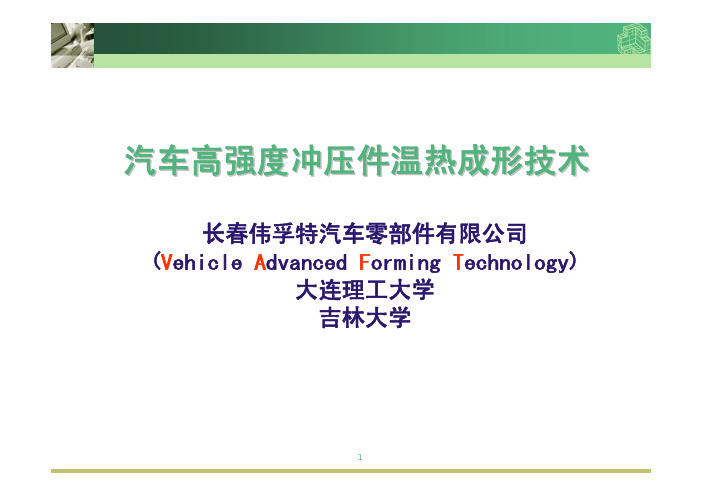
汽车高强度冲压件温热成形技术长春伟孚特汽车零部件有限公司(V ehicle A dvanced F orming T echnology)大连理工大学吉林大学意义1、时下,安全、环保、节能成为汽车制造业发展的主题,采用高强度钢板冲压件制造车身即可以减轻车体重量,又能提高安全性,是同时实现车体轻量化和提高碰撞安全性的最好途径。
2、温热成形技术是用高强度钢板生产高强度冲压件的最新技术,是一项为实现汽车轻量化和提高安全性开发的专门技术。
3、国外汽车业非常重视高强度钢板温热成形技术,欧洲北美等地汽车商要求必须使用温热成形高强度冲压件制造车身,用高强度冲压件制造车身已经成为汽车制造的发展趋势,市场非常广大。
意义(续)4、国内,汽车市场也开始重视该项技术,但是国外技术装备太昂贵(过亿),国内目前仅一两家花费高昂代价采购德国技术生产这种高强度冲压件,为几个车型供应几种冲压件,但远远满足不了市场需要(国内市场需求巨大)。
5、高强度钢板,强度越高,越难成形。
尤其是当强度达到1500MPa时,常规的冷冲压成形工艺几乎无法成形。
因此,如何实现高强度钢板的高精度冲压成形就成为一项迫切需要解决的技术难题。
6、温热成形技术是一项新型的专门用于成形高强度冲压件的先进制造技术。
可用来成形强度高达1500MPa的冲压件。
温热成形工艺原理(2)板料加热系统(1)自动化传送装置(3)模具冷却装置(4)成形模具冷却管道1、2、加热3、成形、淬火下料(1)(2)(3)(4)成形前常温下高强度硼合金钢板强度500-600MPa ;成形后,强度超过1500MPa,提高200%-300%,又称冲压硬化技术。
温热成形技术主要优势1)可成形强度高达1500MPa零件,可组焊成高强度驾乘单元,承受6吨以上的静压不损坏。
2)通过减小壁厚或截面尺寸减轻重量(达18-35%),实现轻量化,并节约材料消耗;3)高温下,材料塑性、成形性好,能一次成形复杂的冲压件;冷冲压中需要多套模具多次成形的冲压件可用温热成形工艺一次成形;可以减少模具数量和成形工序,成形件也可以设计得更复杂;4)高温下成形能消除回弹影响,零件精度高,成形质量好,是温热成形技术最大优点之一。
汽车轻量化技术的研究与进展
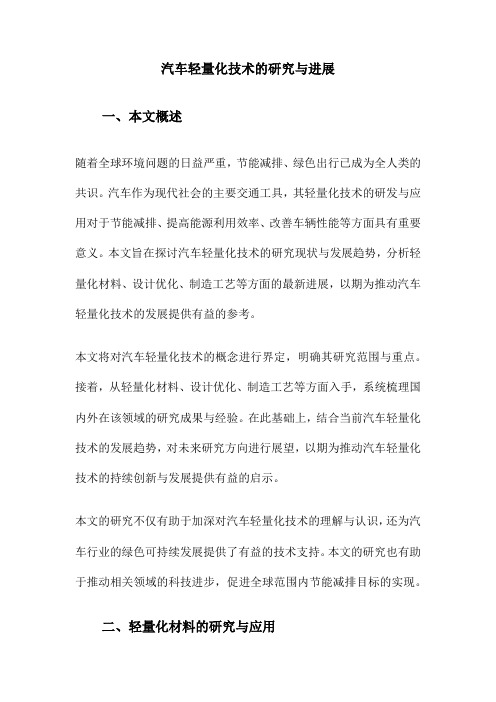
汽车轻量化技术的研究与进展一、本文概述随着全球环境问题的日益严重,节能减排、绿色出行已成为全人类的共识。
汽车作为现代社会的主要交通工具,其轻量化技术的研发与应用对于节能减排、提高能源利用效率、改善车辆性能等方面具有重要意义。
本文旨在探讨汽车轻量化技术的研究现状与发展趋势,分析轻量化材料、设计优化、制造工艺等方面的最新进展,以期为推动汽车轻量化技术的发展提供有益的参考。
本文将对汽车轻量化技术的概念进行界定,明确其研究范围与重点。
接着,从轻量化材料、设计优化、制造工艺等方面入手,系统梳理国内外在该领域的研究成果与经验。
在此基础上,结合当前汽车轻量化技术的发展趋势,对未来研究方向进行展望,以期为推动汽车轻量化技术的持续创新与发展提供有益的启示。
本文的研究不仅有助于加深对汽车轻量化技术的理解与认识,还为汽车行业的绿色可持续发展提供了有益的技术支持。
本文的研究也有助于推动相关领域的科技进步,促进全球范围内节能减排目标的实现。
二、轻量化材料的研究与应用随着全球环保意识的增强和能源危机的日益严峻,汽车轻量化已成为汽车工业发展的重要趋势。
轻量化材料的研究与应用是实现这一目标的关键。
轻量化材料主要包括高强度钢、铝合金、镁合金、塑料及复合材料等。
高强度钢以其优良的力学性能和相对较低的成本,在汽车制造中得到了广泛应用。
通过优化钢材成分、改进热处理工艺和微观结构设计,高强度钢不仅具有更高的强度,而且具有更好的塑性和韧性,能够满足汽车结构件对材料性能的要求。
铝合金以其低密度、高比强度、良好的加工性能和耐腐蚀性等特点,在汽车轻量化中发挥着重要作用。
尤其是铝合金铸件和锻件,因其结构紧凑、重量轻,被广泛应用于发动机、底盘和车身等部件的制造中。
镁合金作为一种轻质、高强度的金属材料,在汽车轻量化领域也备受关注。
镁合金具有良好的电磁屏蔽性能、高的阻尼性能和低的热膨胀系数,特别适用于制造汽车仪表板、座椅框架等部件。
然而,镁合金的耐腐蚀性较差,限制了其在汽车领域的应用。
热冲压成形、铝合金热冲压工艺特点-热成型_热冲压_热成形在车身轻量化上的运用

一,热成形工艺特点及原理
一,热成形工艺特点及原理
一,热成形工艺特点及原理
二,热成形零件在轻量化车身上的运用
三,热成形零件生产控制以及检测
四,热成形的新技术
五,铝合金热成型技术
六,钢板热冲压、铝板热冲压基本原理的异同相同点:本质上说,不论钢还是铝,热冲压都利用了以下3个共同的特点:
1.合金元素在高温下的溶解度远大于室温溶解度(钢的过冷奥氏体、铝的过饱和固溶体)
2.高温下面的材料的优良成形性能
3.成形后急速冷却并保压过程,优良的形状冻结能力
不同点:两者的强化机理完全不同,导致工艺过程不一样
1.钢的热冲压,利用的铁本身在不同温度下晶格的变化-同素异构特性,
2.铝的热冲压,则主要靠不同合金元素的溶解分布以及析出强化,铝合金热冲压需要时效处理。
如果你觉得太难于理解的话,可以简单的如下考虑:
钢的热冲压过程类似于做油脂雪糕过程,铝的热冲压过程类似于铺沥青马路的过程
一家之言,欢迎沟通与交流,热冲压李工给你任何你需要的;东西看完了,给大家打个广告吧,需要热冲压零件和模具的联系我天津百事泰汽车科技有限公司,是天津地区一家专业的热冲压零部件生产企业,可生产热冲压裸板、铝硅涂层板的热冲压,
有京津冀地区最好的抛丸涂油生产线
主要服务客户:天津、北京、河北、山东、河南、辽宁、江苏、上海等;
业务联系邮箱:
***************.cn ******************.cn ***************************@ 想讨论热冲压技术的也可以扫二维码加我微信。
汽车车身热成形工艺的发展趋势-概述说明以及解释
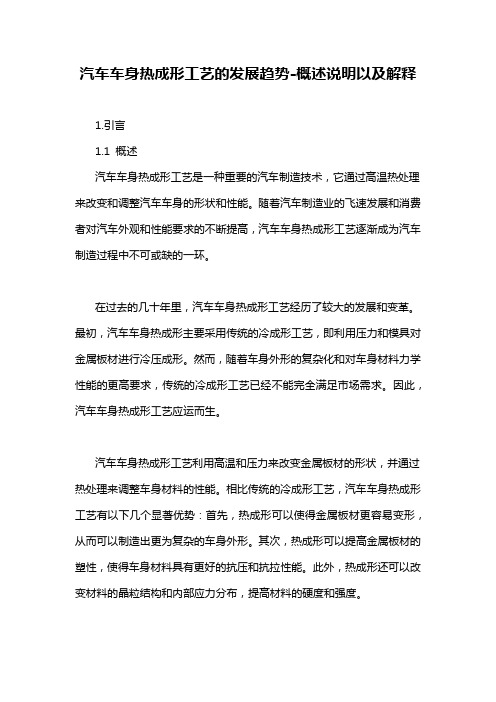
汽车车身热成形工艺的发展趋势-概述说明以及解释1.引言1.1 概述汽车车身热成形工艺是一种重要的汽车制造技术,它通过高温热处理来改变和调整汽车车身的形状和性能。
随着汽车制造业的飞速发展和消费者对汽车外观和性能要求的不断提高,汽车车身热成形工艺逐渐成为汽车制造过程中不可或缺的一环。
在过去的几十年里,汽车车身热成形工艺经历了较大的发展和变革。
最初,汽车车身热成形主要采用传统的冷成形工艺,即利用压力和模具对金属板材进行冷压成形。
然而,随着车身外形的复杂化和对车身材料力学性能的更高要求,传统的冷成形工艺已经不能完全满足市场需求。
因此,汽车车身热成形工艺应运而生。
汽车车身热成形工艺利用高温和压力来改变金属板材的形状,并通过热处理来调整车身材料的性能。
相比传统的冷成形工艺,汽车车身热成形工艺有以下几个显著优势:首先,热成形可以使得金属板材更容易变形,从而可以制造出更为复杂的车身外形。
其次,热成形可以提高金属板材的塑性,使得车身材料具有更好的抗压和抗拉性能。
此外,热成形还可以改变材料的晶粒结构和内部应力分布,提高材料的硬度和强度。
目前,汽车车身热成形工艺已经广泛应用于汽车制造业,特别是高端和豪华汽车的生产过程中。
许多知名汽车制造商已经采用了汽车车身热成形工艺,以提高汽车的外观质感和性能指标。
同时,一些新兴的汽车制造企业也开始关注和运用汽车车身热成形工艺,以求在市场竞争中取得竞争优势。
展望未来,汽车车身热成形工艺有望在汽车制造业中发挥更为重要的作用。
随着材料科学和制造技术的进步,汽车车身热成形工艺将不断创新和完善。
例如,利用先进的金属合金、复合材料和纳米材料,可以进一步提升车身材料的性能和品质。
此外,借助智能制造和自动化技术,汽车车身热成形工艺的生产效率也将得到进一步提高。
综上所述,汽车车身热成形工艺作为一项关键的汽车制造技术,正在不断发展和演变。
其具有的优势和潜力使得它成为汽车制造业中不可或缺的一部分。
随着技术的不断进步和市场的需求变化,汽车车身热成形工艺有望在未来取得更大的突破和发展。
基于Autoform的车身B柱热成形工艺研究

摘要车的发展给人们的生活带来了极大的便利,但同时也带来了严重的能源消耗以及空气污染问题。
为了降低汽车的油耗和环境影响,汽车轻量化已成为汽车行业发展的重要方向。
热成形技术是汽车轻量化、提高汽车抗冲击形以及防撞性能的重要途径。
热成形过程数值模拟的准确性对热成型零件的设计和制造具有重要的指导作用。
本文基于Autoform软件,建立了 B 柱的热成形模型, 采用热力耦合数值分析的方法得到了热成形后零件的厚度,温度分布及破裂起皱的趋势分布等, 通过跟实际调试后的零件的对比,验证了模拟结果的准确性。
关键词:热成型有限元数值模拟 Autoform一、引言十四五时期,我国要努力趋向“碳达峰”和“碳中和”愿景,必须大力推动经济结构、能源结构、产业结构转型升级。
在“双积分”政策引导下,汽车行业也在大力开展节能减排工作,并以轻量化、新能源作为节能减排的主要手段。
对于传统燃油车,当汽车重量减少10%,燃油效率可以提高约8%;而纯电动汽车因为增加了三电系统导致其重量大幅上升,减轻重量可以减少电池容量或提升续航里程,因此新能源车型轻量化需求比传统燃油车更为迫切。
从汽车性能角度考虑,汽车的轻量化有助于汽车的“行驶、转弯、停车”三大基本性能的提高。
汽车白车身(解决碰撞安全性问题的车身骨架)是抵御碰撞侵入和能量吸收核心单元,约占汽车总重量的30%。
随着日益严格的碰撞安全法规,加强白车身成为必然应对手段,因此全球汽车企业均面临着日益增大的车身加强与轻量化间的矛盾。
其中热成形[1]技术对高强钢板进行成形, 在进行热成形前需将坯料加热到高温,使坯料奥氏体化,然后通过快速冷却,得到完全马氏体组织, 如图1,如采用 22 MnB5高强钢板热成形技术制造汽车保险杠,其强度可达1500MPa以上[ 2 ],该技术已成为世界上众多汽车生产厂商关注的热点。
图1 热成形技术原理通用、福特、大众、沃尔沃等汽车制造公司都在大量使用热成形的高强度汽车零件,某些车型上使用量高达30%。
- 1、下载文档前请自行甄别文档内容的完整性,平台不提供额外的编辑、内容补充、找答案等附加服务。
- 2、"仅部分预览"的文档,不可在线预览部分如存在完整性等问题,可反馈申请退款(可完整预览的文档不适用该条件!)。
- 3、如文档侵犯您的权益,请联系客服反馈,我们会尽快为您处理(人工客服工作时间:9:00-18:30)。
年开发 了不带镀层的热冲压用钢 ( 冷轧B1 5 0 0 HS , 热 ̄ L B R1 5 0 0 H S ),并能批量供货。 ( 3 )热成形模具 热冲压 与冷冲压模具也完全
不 同 ,模具 型面 设 计 时 ,需 要 考 虑钢 板 的 热胀 冷 缩
I . 热成 形技术
( 1 )热成形工艺 钢板热成形技术是一种将特
冷却水回路使工件快速冷却淬火 ,热成形工序如图
1 所示。
兼顾这些 ,很多车企将高强度钢在车身设计中进行
了广 泛 应用 。 图1 热成形工序
目前车 身钣 金 零 件 大 多是 钢 板通 过 模 具 冷 冲 压 成 形 而 得 到 的 ,为 了能够 实现 冲 压 成 形 ,保 证 成 形
纪8 0 年 代提 出 ,其 与 传 统意 义 上 的 热 冲压 技 术 的 本
及布置方式 、冷却孔中心离模具 型面的距离、冷却 水 的流 动方式等) 。模具 内部冷却 回路 是钻孔形成 的 ,模具分块及其精密装配技术都需详细分析 。
质区别在于不是通过空冷 ,而是通过 在模具 中布置
参 磊
疆
Fo r m g
热成形技术在车身轻量化设计中
的应用
华晨 汽车 工程研究 院 ( 辽 宁沈 阳 1 1 0 1 4 1 ) 闰禄 平 李 飞 张丹荣
环境污染和能源消耗 已成为 当今世界亟待解决
的 社 会 问题 ,而 随 着燃 油 价 格 的 不 断上 涨 ,汽 车 油 耗 已经成 为 购 车 者 选车 的一 个 重 要 关注 点 。通 过车 身轻 量 化 设 计 降低 汽 车 自重 是一 种 降低 汽 车 油耗 的 有 效 手 段 。另 一方 面 , 日趋 严格 的碰 撞 法规 又要 求 车 身某 些 区 域具 有 较 高 的 强 度 以保 证 乘 员安 全 。为
殊 高 强 度钢 板 加 热 到 奥 氏体 温 度 后 快 速 冲压 ,通 过 模具 保 压并 实现 淬 火 ,最终 得 到 组 织 为 马 氏体 ,抗
效应 ,并采取有效补偿方案 。其次 ,模具 内部需要
有 冷 却 水 回路 的 设 计 ( 冷 却 孔 径 大 小 、 冷 却 孔 间距
拉强度在1 2 0 0 MP a 以上的超高强度零件的新 型成形 技术。此新技 术最先 由瑞典Ha r d T e c h 公司于2 0 世
质量 ,通常使用的钢板屈服强度并不高。但随着安 全法规的不断提高 ,对车 身某些部位的强度要求也 在不断提高 ,而提高强度 的方法要么增加料厚 ,要
么 使 用 强度 更 高 的 材料 。增 加 料 厚 意 味着 重 量 要 增 加 ,而 使用 强度 更 高 的材 料 冷 冲 压 成 形 工艺 又 难 以
…
4 5
另外 热 成 形 生 产 线 还 配 有 激 光 切 割 及 零 件 表
面处理用的抛丸机殊的高强度钢板 ,有关高强度钢的研究显示 ,仅
使用2 2 Mn B 5 、2 7 Mn C r B 5 、3 7 Mn B 4 钢 级 才能 在 热 冲 压 经 过 水 冷 后得 到完 全 马 氏体 组 织 ,而2 2 Mn B 5 是 最 常 用 于 热 冲 压 的 钢 级 。 在 奥 氏体 化 条 件 下 , 钢 与 空 气接 触 时 很快 就 形 成氧 化 膜 ,为避 免 表 面 氧 化 和 脱 碳 ,大 量 的 金 属 板 会 涂 覆 上 一 层 保 护 层 ,
实现 或质 量 很 不稳 定 。
根据项 目组控制整车 重量 ,降低燃料消耗的开 发思想 ,我们在车 身设计 中分析与借鉴 了其他先进 车 型的设计思想 ,并 与相关部门进行 了成本对比分
析 , 引入 了高 强度 钢 板 热 成 形技 术 ,开 发 出 了热 成 形B 柱 加 强板 ,满 足 了 整车 侧 碰 要 求 并 控 制 了车 身
重量 。
在热冲压 中应用最 为广泛 的是Al — S i 涂 层。 目前 欧
洲Ar c e l o r 能批 量 生 产 带A1 一 s i 涂 层 的热 冲 压 用 钢 板 US I BO R1 5 0 0 ,另 外西 欧 、 日本 及 韩 国 的钢 厂也 能 批量 生 产 热 冲压 用 钢 。 国 内 , 目 前 只有 宝 钢于 2 0 0 6