AP0166 Testing and Debugging Your Embedded Intelligence
SP6MAWT 6.5英寸封闭70V 25V墙内扬声器系统说明书

SP6MAWT 6.5” Enclosed 70V/25V In-Wall Speaker SystemThank you for your choice of Speco Technologies’ SP6MAWT Speaker. This unit is designed to provide a wall-mount alternative for background music or paging in commercial, public or residential environments. The enclosed, in-wall design offers mounting opportunities not always available to standard in-ceiling speakers.INSTALLATION INSTRUCTIONS:1)Carefully remove the SP6MAWT speaker from its protective packaging.2)The SP6MAWT comes complete with a built-in, easy-select transformer. The transformer dial and voltageselector switch are located behind the grill. Quickly and easily remove the grill by grabbing mounting legs on opposite sides of the speaker, and pushing towards the front. The legs will push the grill off.3)The transformer has settings of 40 Watts, 30W Watts, 15 Watts, 7.5 Watts, 5 Watts, 2.5 Watts, 1 Watts,0.5 Watts & 8 Ohms. The wattage settings are for use with 70V or 25V amplifiers, typically used incommercial environments and selected by a built-in switch. The 8 Ohm setting is for use with constantimpedance 8 Ohm amplifiers, typically in residential environments. Select the setting that best matchesyour amplifier and installation.Warning: Using a transformer selection that does not match the output from your amplifier candamage the amplifier or speaker. Make sure all settings are correct before powering the amplifier.For information on the differences between 70V & 8 Ohm, ask your distributor for the Speco Technologies Commercial Audio Guide.4)This speaker has mounting dimensions of 10.75” H x 7.5” W, with a minimum in-wall depth requirementof 4.13”. There is no in-wall mounting bracket available for this speaker.5)We recommend using 14 or 16 AWG speaker wire for optimal performance. Connect the wire to thecorresponding terminal, located on the bottom rear of the speaker. Red (+) and Black (-) terminals areprovided.6)Insert the speaker into the cutout, and secure the speaker in the wall by tightening each of the 6 built-inmounting legs.7)Replace the grill.SPECIFICATIONS:6.5” Fiberglass Woofer with Rubber Surround1” Titanium Dome TweeterTotal Frequency range: 50Hz ~ 20kHz40 Watt RMS/ 80 Watt MaxSensitivity: 89 +/- 3dBWARRANTY INFORMATION:We warranty this product to be free from any manufacturing or material defects for as long as you own the speaker. (Non-transferrable, LIFETIME WARRANTY)This warranty will not extend to any products which have been subjected to misuse, neglect, accident, or improper installation, used in violation of instructions furnished by us; or to units which have been repaired or altered outside of the factory. This limited warranty does not apply to broken cases, batteries, or other physically damaged parts.Upon request by the customer, Speco Technologies (“The Company”) will, at the customer's expense, repackage merchandise in new cartons, replace missing accessories, and return in resalable condition. Unless requested, the company will replace and return all merchandise in the packaging in which it was received. This warranty is in lieu of all expressed warranties, expressed or implied, and of all obligations or liability on our part, and we neither assume nor authorize any representative or other person to assume for us any obligation or liability. In no event shall we be liable for incidental or consequential damages arising from the use of the product, or for any delay in the use of this product due to causes beyond our control. Some states do not allow limitations of how long an implied warranty lasts and/or do not allow the exclusion or limitation of consequential damages. The above limitations on implied warranty and consequential damages may not apply to you. This warranty gives you specific legal rights. You may have other rights which vary from state to state. See actual warranty statement included with product for limitations and exclusions where applicable. This limited warranty extends to products listed in the company's current price schedule.For more information contact Speco Technologies200 New Highway, Amityville, NY 11701• Toll Free: 1-800-645-5516•Fax: 631-957-9142 or 631-957-3880•Speco Technologies is constantly developing and improving products.We reserve the right to modify product design and specifications without notice and without incurring any obligation. Rev. 8/1/12。
Pyle wireless microphone系统PDWM2560用户手册说明书

interruption. 3. LCD information display. 4. Double noise squelch operation circuit and system will be higher e cient
and much more steady. 5. Use the dynamic type and Unidirectional cartridge, clear to show the sound. 6. High e cient and low consumption design. 7. Use the high extension antennas, the operating distance will reach 175 feet.
PDWM2560
Wireless Microphone System
CATALOG
1. FOREWORD 2 - - - - - - - - - - - - - - - - - - - - - - - - - - - - - - - - - - - - - - - - - - - - - - - - - - - - - - - - - - - - - - - - - - - - - - - - - - - - - - - - - - - - - - - - - - - - 2. SYSTEM FEATURES 2 - - - - - - - - - - - - - - - - - - - - - - - - - - - - - - - - - - - - - - - - - - - - - - - - - - - - - - - - - - - - - - - - - - - - - - - - - - - - - - - - - - - 3. SYSTEM TYPE 2 - - - - - - - - - - - - - - - - - - - - - - - - - - - - - - - - - - - - - - - - - - - - - - - - - - - - - - - - - - - - - - - - - - - - - - - - - - - - - - - - - - - - - - - - - - 4. DUAL CHANNEL RECHARGEABLE RECEIVER FEATURES - - - - - - - - - - - - - - - - - - - - - - - - - - - - - - - 3 5. TRANSMITTER FUNCTION & FEATURES - - - - - - - - - - - - - - - - - - - - - - - - - - - - - - - - - - - - - - - - - - - - - - - - - - - - - - 4 6. SYSTEM CONNECTIONS 5 - - - - - - - - - - - - - - - - - - - - - - - - - - - - - - - - - - - - - - - - - - - - - - - - - - - - - - - - - - - - - - - - - - - - - - - - - - 7. BODYPACK TRANSMITTER CONNECTION - - - - - - - - - - - - - - - - - - - - - - - - - - - - - - - - - - - - - - - - - - - - - - - - - - - 6 8. TRANSMITTER BATTERY INSTALLATION - - - - - - - - - - - - - - - - - - - - - - - - - - - - - - - - - - - - - - - - - - - - - - - - - - - - - 7 9. TROUBLESHOOTING 8 - - - - - - - - - - - - - - - - - - - - - - - - - - - - - - - - - - - - - - - - - - - - - - - - - - - - - - - - - - - - - - - - - - - - - - - - - - - - - - - 10. SYSTEM SPECIFICATIONS 9 - - - - - - - - - - - - - - - - - - - - - - - - - - - - - - - - - - - - - - - - - - - - - - - - - - - - - - - - - - - - - - - - - - - - - - -
ADI电路参考设计CN-0382说明书

电路笔记CN-0382Circuits from the Lab® reference designs are engineered and tested for quick and easy system integration to help solve today’s analog, mixed-signal, and RF design challenges. For more information and/or support, visit /CN0382.连接/参考器件AD7124-4 集成PGA和基准电压源的低功耗24位Σ-Δ型ADCAD5421 16位、环路供电、4 mA至20 mA DAC AD5700 低功耗HART调制解调器SPI隔离器ADuM1441ADP162超低静态电流、150 mA CMOS线性稳压器ADG5433高压防闩锁型三通道SPDT开关Rev. 0Circuits from the Lab® reference designs from Analog Devices have been designed and built by Analog Devices engineers. Standard engineering practices have been employed in the design and construction of each circuit, and their function and performance have been tested and veri ed in a labenvironment at room temperature. However, you are solely responsible for testing the circuit and determining its suitability and applicability for your use and application. Accordingly, in no event shall Analog Devices be liable for direct, indirect, special, incidental, consequential or punitive damages due to any cause whatsoever connected to the use of any Circ uits from the Lab circuits. (Continued on last page) One Technology Way, P.O. Box 9106, Norwood, MA 02062-9106, U.S.A. Tel: 781.329.4700 Fax: 781.461.3113 ©2015 Analog Devices, Inc. All rights reserved.采用低功耗、精密、24位Σ-Δ型ADC的隔离式4 mA至20 mA/HART工业温度和压力变送器评估和设计支持电路评估板DEM O-AD7124-DZ评估板设计和集成文件原理图、布局文件、物料清单、代码示例电路功能与优势图1所示电路是一种隔离式智能工业现场仪表,可与许多类型的模拟传感器,如温度传感器(Pt100、Pt1000、热电偶)或桥式压力传感器等接口。
手机产品质量检验标准

手机产品质量标准
本产品质量标准由以下四个部分组成:
第一部分:产品技术规格书(电性能部分)第二部分:产品外观检验标准
第三部分:产品功能检验标准
第四部分:产品可靠性检验标准
第一部分:产品技术规格书(电性能部分)
4.DCS 1800MHz电性能测试标准(续)
第二部分:产品外观检验标准
注:1。
因装配原因引起的功能/电性能的缺陷,按照功能/电性能检验标准和缺陷定义判断。
2.缝隙的检验方法:使用塞尺在最大缝隙处进行测量(不能用力塞入)为参考。
第三部分:产品功能检验标准
第四部分:产品可靠性检验标准项目常规性能测试项目及标准
项目可靠性实验标准
项目Reliability Test Standard
蓝牙耳机产品测试标准
手机合缝标准版本:0.1
签署:_____________________________ 签署:_____________________________ 姓名:姓名:
职务:职务:
日期:日期:。
WBOX-516X产品手册说明书

产品手册WBOX-516X,无风扇工业计算机版本:V1.01 / 41认可声明AMI 为Award Software International, Inc. 的商标。
Intel 和Atom 为Intel Corporation 的商标。
IBM、PC/AT、PS/2 和VGA 为International Business Machines Corporation的标。
Intel 和Atom 为Intel Corporation 的商标。
Microsoft Windows 为Microsoft Corp. 的注册商标。
RTL 为Realtek Semiconductor Co., Ltd. 的商标。
所有其它产品名称和商标均为其所有者的财产。
本手册适用于WBOX-516x系列.符合性声明这些限制旨在为商业环境下的系统操作提供合理保护,使其免受有害干扰。
本设备会产生、使用和发射无线电频率能量。
如果没有按照手册说明正确安装和使用,可能对无线电通讯造成有害干扰。
但即使按照手册说明进行安装和使用,也并不能保证不会产生干扰。
若本设备会对无线电或电视信号接收产生有害干扰,用户可通过开、关设备进行确认。
当本设备产生有害干扰时,用户可采取下面的措施来解决干扰问题:●1、调整接收天线的方向或位置●2、增大本设备与接收器之间的距离●3、将本设备的电源接头插在与接收器使用不同电路的电源插座●4、若需技术支持,请咨询经销商或经验丰富的无线电/电视技术人员警告!权利可能会被取消。
包装清单在您打开包装时,请确认包装中附有以下各项:●–WBOX-516x 1pcs附件盒,装有以下各项:●- 电源端子1pcs●- 国标电源线1.8米(可选)1pcs●- 电源适配器(可选)1pcs如果其中任何一项缺失或者破损,请立即联系您的销售商或销售代表。
2 / 41选购信息技术支持与服务用户若需技术支持,请与当地分销商、销售代表客服中心联系。
进行技术咨询前,用户须将下面各项产品信息收集完整:–产品名称及序列号–外围附加设备的描述–用户软件的描述(操作系统、版本、应用软件等)–产品所出现问题的完整描述–每条错误信息的完整内容警告! 1. 输入电压为DC 12-24V电源(电源功率90W或以上)2. 包装:需谨慎,请以双手托住设备。
梅索尼兰定位器 SVI-II
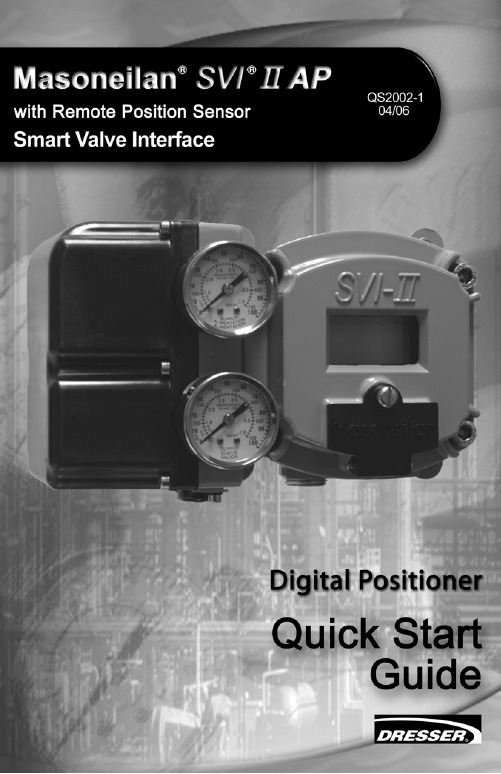
WarrantyItems sold by Dresser® are warranted to be free from defects in materials and workmanship for a period of one year from the date of shipment provided said items are used according to Dresser recommended usages. Dresser, Inc. reserves the right to discontinue manufac-ture of any product or change product materials, design or specifications without notice. This instruction manual applies to the following instruments and approved software: SVI ® II AP Positioner and ValVue® software.The SVI II AP series positioners are warranted for use only with interface software approved by Dresser Inc. Consult Masoneilan Dresser factory locations for approved software listing.About this GuideThis Quick Start Guide applies to the following instruments and approved software: SVI II AP -2 through SVI II AP-3- with Firmware version 3.1.1- with ValVue® version 2.4 or greater- with AMS® ValVue® SNAP-ON® version 2.4 or greater- with Model HH375 HART® Communicator with DD published for SVI II AP- (Masoneilan Device type 202, 0, 00CA)The information in this manual is subject to change without prior notice.The information contained in this manual, in whole or part, shall not be transcribed or copied without Masoneilan’s written permission.In no case does this manual guarantee the merchantability of the positioner or the software or its adaptability to a specific client needs.Please report any errors or questions about the information in this manual to your local supplier or visit .CopyrightAll software is the intellectual property of Dresser, Inc.The complete design and manufacture is the intellectual property of Dresser, Inc. Masoneilan®, FVP®, SVI®, and ValVue®are registered trademarks of Dresser, Inc. All information contained herein is believed to be accurate at the time of publication and is subject to change without notice.Copyright 2006 by Dresser, Inc. All rights reserved.PN 055201-167 REV BThis section provides safety information including safety symbols thatare used on the SVI II AP and the safety symbol definition. Important - Please Read Before Installation!Safety Symbols SVI II AP instructions contain DANGER, WARNING, and CAUTION labels and Notes, where necessary, to alert you to safety related or other important information. Read the instructions carefully before installing and maintaining your instrument. DANGER and WARNING hazards are related to personal injury. CAUTION hazards involve equipment or property damage. Operation of damaged equipment can, under certain operational conditions, result in degraded process system performance that can lead to injury or death. Total compliance with all DANGER, WARNING, and CAUTION notices is required forsafe operation.This is the safety alert symbol. It alerts you to potential personal injury hazards. Obey all safety messages that follow this symbol to avoidpossible injury or death.Indicates a potentially hazardous situation, which if not avoided couldresult in death or serious injury.Indicates a potentially hazardous situation, which if not avoided couldresult in serious injury.Indicates a potentially hazardous situation, which if not avoided could result in minor or moderate injury.Safety InformationMasoneilan Dresser SVI II AP Quick Start Guide When used without the safety alert symbol indicates a potentiallyhazardous situation, which if not avoided could result in property damage.Note:Indicates important facts and conditions.SVI II APProductSafety The SVI II AP positioner is intended for use with industrial compressed air or, natural gas systems only. Ensure that an adequate pressurerelief provision is installed when the application of system supplypressure could cause peripheral equipment to malfunction. Installationmust be in accordance with local and national compressed air andinstrumentation codes.Products certified as explosion proof or flame proof equipment or foruse in intrinsically safe installations MUST BE :Installed, put into service, used and maintained incompliance with national and local regulations andin accordance with the recommendations containedin the relevant standards concerning potentiallyexplosive atmospheres.Used only in situations that comply with the certifi-cation conditions shown in this document and afterverification of their compatibility with the zone ofintended use and the permitted maximum ambienttemperatureInstalled, put into service and maintained by quali-fied and competent professionals who have under-gone suitable training for instrumentation used inareas with potentially explosive atmospheres. Before using these products with fluids other than air or for non-industrial applications, consult Dresser, Inc. This product is notintended for use in life support systems.Under certain operating conditions, the use of damaged instrumentscould cause a degradation of the performance of the system which maylead to personal injury or death.Use only genuine replacement parts which are provided by themanufacturer, to guarantee that the products comply with the essentialsafety requirements of the European Directives mentioned on the frontcover.Changes to specifications, structure, and compo-nents used may not lead to the revision of this man-ual unless such changes affect the function andperformance of the product.ContentsSafety Information. . . . . . . . . . . . . . . . . . . . . . . . . . . . . . . . . . . . . iSafety Symbols . . . . . . . . . . . . . . . . . . . . . . . . . . . . . . . . . . . . . . . . . . . . i SVI II AP Product Safety. . . . . . . . . . . . . . . . . . . . . . . . . . . . . . . . . . . . ii Section 1Installation and Set Up . . . . . . . . . . . . . . . . . . . . . . .1 Introduction. . . . . . . . . . . . . . . . . . . . . . . . . . . . . . . . . . . . . . . . . . . . . . 1 Using the Quick Start Guide. . . . . . . . . . . . . . . . . . . . . . . . . . . . . . . . . 2Mounting the SVI II AP . . . . . . . . . . . . . . . . . . . . . . . . . . . . . . . . . . . . . 3 Necessary Precautions . . . . . . . . . . . . . . . . . . . . . . . . . . . . . . . . . . . .4Installing the SVI II AP Remote Position Sensor . . . . . . . . . . . . . . . . 4 Installation Procedure . . . . . . . . . . . . . . . . . . . . . . . . . . . . . . . . . . . . . .5Connecting the Tubing and Air Supply. . . . . . . . . . . . . . . . . . . . . . . . 7 Single Acting Positioner . . . . . . . . . . . . . . . . . . . . . . . . . . . . . . . . . . . . .8 Double Acting Positioner . . . . . . . . . . . . . . . . . . . . . . . . . . . . . . . . . . . .9 Connecting the Air Supply . . . . . . . . . . . . . . . . . . . . . . . . . . . . . . . . . . .9 Wiring the SVI II AP. . . . . . . . . . . . . . . . . . . . . . . . . . . . . . . . . . . . . . . 10 Connecting to the Control Loop . . . . . . . . . . . . . . . . . . . . . . . . . . . . . .10 Wiring Guidelines . . . . . . . . . . . . . . . . . . . . . . . . . . . . . . . . . . . . . . . .10 SVI II AP Setups . . . . . . . . . . . . . . . . . . . . . . . . . . . . . . . . . . . . . . . . . 11 Grounding Practices . . . . . . . . . . . . . . . . . . . . . . . . . . . . . . . . . . . . . .12 Compliance Voltage in Single Drop Current Mode . . . . . . . . . . . . . . .12 Verify Wiring and Connections . . . . . . . . . . . . . . . . . . . . . . . . . . . . . .12Masoneilan Dresser SVI II AP Quick Start GuideSVI II AP Maintenance. . . . . . . . . . . . . . . . . . . . . . . . . . . . . . . . . . . . . 14 Repair . . . . . . . . . . . . . . . . . . . . . . . . . . . . . . . . . . . . . . . . . . . . . . . . .14 Tools Needed for Cover Replacement . . . . . . . . . . . . . . . . . . . . . . . . .14 Display Cover Removal and Installation . . . . . . . . . . . . . . . . . . . . . . .15 Removing the SVI II AP Display Cover . . . . . . . . . . . . . . . . . . . . . . .15 Installing the SVI II AP Display Cover . . . . . . . . . . . . . . . . . . . . . . . .15 Section 2Check Out, Configuration and Calibration . . . . . .17Overview. . . . . . . . . . . . . . . . . . . . . . . . . . . . . . . . . . . . . . . . . . . . . . . . 17Check Out Procedures . . . . . . . . . . . . . . . . . . . . . . . . . . . . . . . . . . . . 17 Physical Inspection . . . . . . . . . . . . . . . . . . . . . . . . . . . . . . . . . . . . . . .17 Actuator, Linkages, or Rotary Adapter . . . . . . . . . . . . . . . . . . . . . . .17 Verify Mounting and Linkage Adjustment . . . . . . . . . . . . . . . . . . . . .18 Checking the Magnet . . . . . . . . . . . . . . . . . . . . . . . . . . . . . . . . . . . .18 Performing a Visual Inspection . . . . . . . . . . . . . . . . . . . . . . . . . .18 Using ValVue 2.4 to Check Magnet Position . . . . . . . . . . . . . . . . . . . .19 Checking the Air Supply . . . . . . . . . . . . . . . . . . . . . . . . . . . . . . . . . . .20 Checking the Electronic Module Connections . . . . . . . . . . . . . . . . . . .20 Making Connections to the Terminal Board . . . . . . . . . . . . . . . . . . . . .22 Operational Checkout. . . . . . . . . . . . . . . . . . . . . . . . . . . . . . . . . . . . . 22 Connecting to the Current Source . . . . . . . . . . . . . . . . . . . . . . . . . . . .22 Pushbutton Locks and Configuration-Lock Jumper . . . . . . . . . . . . . . .23 Hardware Configuration Lock . . . . . . . . . . . . . . . . . . . . . . . . . . . . . .23 Powering Up the SVI II AP . . . . . . . . . . . . . . . . . . . . . . . . . . . . . . . . .23 Configuration. . . . . . . . . . . . . . . . . . . . . . . . . . . . . . . . . . . . . . . . . . . . 24 ValVue 2.4 Software . . . . . . . . . . . . . . . . . . . . . . . . . . . . . . . . . . . . . .24 ValVue 2.4 Lite . . . . . . . . . . . . . . . . . . . . . . . . . . . . . . . . . . . . . . . . .24 System Requirements . . . . . . . . . . . . . . . . . . . . . . . . . . . . . . . . . . .25 ValVue 2.4 Full Trial Version . . . . . . . . . . . . . . . . . . . . . . . . . . . . . . .25 Pushbuttons and Local Display . . . . . . . . . . . . . . . . . . . . . . . . . . . . . .25 Pushbuttons . . . . . . . . . . . . . . . . . . . . . . . . . . . . . . . . . . . . . . . . . . . . .26 Configuration with Pushbuttons . . . . . . . . . . . . . . . . . . . . . . . . . . . . . .27 Viewing Configuration Data . . . . . . . . . . . . . . . . . . . . . . . . . . . . . . .27 Viewing Status Messages . . . . . . . . . . . . . . . . . . . . . . . . . . . . . . . . . .27 VIEW DATA Settings . . . . . . . . . . . . . . . . . . . . . . . . . . . . . . . . . . . . . .28Calibration . . . . . . . . . . . . . . . . . . . . . . . . . . . . . . . . . . . . . . . . . . . . . . 28 Auto Tune . . . . . . . . . . . . . . . . . . . . . . . . . . . . . . . . . . . . . . . . . . . . .29 Check-out with a HART Handheld Communicator. . . . . . . . . . . . . . . .31 Appendix A Specifications and References . . . . . . . . . . .A-1 Physical and Operational Specifications . . . . . . . . . . . . . . . . . . . . A-1 Hazardous Location Installation . . . . . . . . . . . . . . . . . . . . . . . . . . . A-7Installation and Set Up1Introduction The SVI® II AP (Smart Valve Interface) is the next generation ofMasoneilan’s intelligent digital valve positioners. The SVI II AP is acompact, industrial tough, high performance, digital valve positionerthat combines a local display with remote communication anddiagnostic capabilities. The SVI II AP is available with options neededto fulfill virtually all application requirements and communicates usingthe HART® protocol. The SVI II AP offers:Extreme AccuracyExtreme ReliabilityExtreme Digital PrecisionAutomated Valve CommissioningPrecise, Quick, Responsive Control of ValvePositionSophisticated Valve DiagnosticsFigure 1SVI II APSVI II AP Cover SVI II AP AssembledElectronicsModule Pneumatic Train and Cover (I/P Module, Relay)ManifoldRelayI/PMasoneilan Dresser SVI II AP Quick Start GuideFigure 2SVI II AP ComponentsUsing the Quick Start GuideThe SVI II AP Quick Start Guide is intended to help an experiencedField Engineer install, setup, and calibrate an SVI II AP in the mostefficient manner possible. This document provides basic installationand setup instructions and is not intended to replace the in-depthinformation contained in the SVI II AP Instruction Manual EW2002-AP .If you experience problems that are not documented in this guide referto the Masoneilan SVI II AP Instruction Manual EW2002-AP , call yourlocal Masoneilan representative, or go to . Salesoffices are listed on the last page of this documentThe steps necessary to complete the SVI II AP installation and softwaresetup are outlined in Table 1 below. Table 1 SVI II AP Installation Steps Step No.Procedure Reference 1Attach mounting bracket to the actuator.See page 3 for rotary valve and reciprocating valve instructions.2Install the SVI II AP magnetic assembly (rotary valves only).See page 3 for instructions.3Assemble the SVI II AP on thebracket that is mounted to the valveactuator.See page 3 for rotary valve and reciprocating valve instructions.Installation and Set Up Mounting the SVI II AP Failure to adhere to the requirements listed in this manual may causeloss of life and property.Before installing, using, or carrying out any maintenance tasksassociated with this instrument, READ THE INSTRUCTIONSCAREFULLY. (Refer to “Hazardous Location Installation” onpage A-7 of this guide for detailed instructions.)Mounting the SVI II AP This guide provides installation instructions for mounting an SVI II AP on both rotary and reciprocating actuated valves. The mounting process can be broken down into the following:Attach the mounting bracket to the actuator.Install the magnetic assembly.Assemble the SVI II AP on the mounting bracket. Note:The SVI II AP should be mounted with the conduit connections down in order to facilitate drainage of condensate from the con-duit.4Install the Remote Position Sensor, ifnecessary.See page 4 for instructions.5Connect the pneumatic tubing to theSVI II AP.See page 7 for instructions.6Connect the air supply to the SVI IIAP.See page 9 for instructions.7Connect the positioner to the HARTControl Loop segment by installingthe SVI II AP wiring.See page 10 for instructions.8Configure/calibrate using ValVue.2.4See page 24 and page 28 forinstructionsConfigure/calibrate using a HART Hand Held Communicator See page 31 for instructions.Table 1 SVI II AP Installation StepsStep No.Procedure ReferenceMasoneilan Dresser SVI II AP Quick Start Guide Necessary PrecautionsTo avoid injury or the process being affected when installing orreplacing a positioner on a control valve, ensure that:If the valve is located in a hazardous area makesure the area has been certified as “safe” or that allelectrical power to the area has been disconnectedbefore removing any covers or disconnecting anyleads.Shut off air supply to the actuator and to any valvemounted equipment.Ensure the valve is isolated from the process byeither shutting off the process or using bypassvalves for isolation. Tag shutoff or bypass valves toguard against a “turn-on” while work is in progress.Bleed air from actuator and check that valve is in itsunenergized position.It is now safe to disconnect and remove any valve mounted equipmentthat is being replaced.For the procedure to mount rotary and reciprocating valves, refer to theMounting Instructions contained in the valve’s Mounting Box kit.Installing the SVI II AP Remote Position Sensor An option that is available for the SVI II AP is the Remote Position Sensor. The Remote Position Sensor, is a remotely mounted position-sensing device, that is connected electrically to an SVI II AP valve positioner. It is used as position feedback in applications where direct mounting of an SVI II AP to a valve actuator is not practical due, typically but not limited to, extreme vibration, heat or radiation.The Remote Position Sensor is a potentiometer located in an enclosure which can be mounted on a valve or damper to indicate stem position when connected to a suitable receiver. There is a three wire connection provided on a screw terminal block to interconnect to the receiving device.The SVI II AP Remote Position Sensor is suitable for installation outdoors in an industrial environment. Mounting kits are provided topermit mounting on a variety of valves.Do not remove the instrument cover or connect to an electrical circuit ina Hazardous Area unless the power is disconnected.Comply with current national and local regulationsfor electrical installation work.Installation and Set Up Installing the SVI II AP Remote Position SensorComply with national and local explosiveatmosphere regulations.Before carrying out any work on the device, poweroff the instrument or make sure that the localeconditions for potentially explosive atmospherepermit the safe opening of the cover.Installation ProcedureFor the Remote Position Sensor installation procedure refer to themounting instructions provided with the Remote Position Sensor.1.Remove the cover from the Remote Position Sensorassembly by turning the cover in a counter-clockwise (fac-ing the cover) direction.2.Connect the Remote Position Sensor to the mountingbracket by inserting four M6 x 20 mm Socket Head CapScrews through the appropriate screws holes (accordingto the valve) on the Remote Position Sensor bracket andusing a 3⁄16 inch Hex Key with tee handle.3.Route the instrument cable from the SVI II AP to theRemote Position Sensor (see Figure 3 on page 6 forinstallation instructions).4.Thread the cable through the conduit at the bottom of theRemote Position Sensor.ing a blade screwdriver, loosen the screws on theterminal block and connect the black, brown and red wiresto the appropriate labelled connectors.6.Tighten the screws.7.Attach the feedback lever to the Remote Position Sensorshaft. From the cover side, the lever should be pointing tothe left for reciprocating valves and to the right for rotaryvalves.8.Place the Remote Position Sensor on the mountingbracket.9.Attach the Remote Position Sensor and secure theturnbuckle to the lever ensuring that the shaft at the rear ofthe Remote Position Sensor is inserted into the valveactuator. (Refer to Table 2 “Remote Position SensorTurnbuckle Length” below for turnbuckle length.)10.Replace the Remote Position Sensor cover.Table 2 Remote Position Sensor Turnbuckle LengthActuator Size Stroke Turnbuckle Length6 and 100.5 - 0.8 inch 1.25 inch100.5 - 0.8 inch 1.25 inch10>0.8 – 1.5 inch 1.25 inchMasoneilan Dresser SVI II AP Quick Start Guide Figure 3SVI II AP Remote Position Sensor Installation 160.5 - 0.8 inch 2.90 inch 16>0.8 – 1.5 inch 2.90 inch 16>1.5 – 2.5 inch 2.90 inch 230.5 - 0.8 inch 5.25 inch 23>0.8 – 1.5 inch 5.25 inch 23>1.5 – 2.5 inch 5.25 inchStep 1 Connect Drain Wire to Open Terminal Step 2When connecting cable to Remote Position Sensor make sure wire colors match: - Red to Red - Brown to Brown - Black to BlackStep 3Insert Ferrules into “Remote” Terminal Block according to Wire Color SVI II AP Terminal Number Function RedBrownBlack 123 Positive Signal Groundthe chart at the right:Remote Terminal Block123Table 2 Remote Position Sensor Turnbuckle LengthActuator SizeStroke Turnbuckle LengthInstallation and Set Up Connecting the Tubing and Air SupplyConnecting the Tubing and Air Supply The last step in hardware installation for the SVI II AP is to connect the air supply to the positioner. This section describes the process for connecting the tubing and air supply to a single and double actingpositioner.Isolate the valve from the process and disconnect air tubing from the positioner. Disconnect air fully to avoid injury or process damage.1.Install the pneumatic tubing using a regulated, clean,instrument air supply to the air supply port (S←)2.For a single acting actuator - pipe the outbound air fromthe output pressure port (←I) to the valve actuator.3.For a double acting actuator - pipe the air going out ofeach side of valve actuator. Use both output pressure portone (←I) for one side of the actuator and output pressureport two (←II) for the other side of the actuator.4.Connect air supply and actuator outports (1⁄4 inch NPT)Supply pressure for single acting SVI II AP:20 -100 psi (1.4 - 6.9 bar) (138 - 690 kPa)Supply pressure for double acting SVI II AP:20 - 150 psi (1.4 - 10.4 bar) (138 - 1035 kPa)Minimum tubing diameter 1⁄4 inch (6mmx4mm) Note:The SVI II AP Digital Positioner is designed to operate with clean, dry, oil-free, instrument grade air to ANSI-ISA-57.3 1975(R1981) or ISA-S7.3-1975 (R1981) or with a sweet natural gassupply (SVI II AP models SVI II AP-2 through SVI II AP-3).Table 3Dew Point At least 18° F (10° C) below minimum anticipated ambienttemperatureParticulate Matter Filtered to 5 micronsOil Content Less than 1 ppm w/wContaminants Free of all corrosive contaminantsAir Supply RequirementsMasoneilan Dresser SVI II AP Quick Start Guide Single Acting PositionerThe supply and output connections for the SVI II AP, located on bottomof the pneumatic block, are tapped 1⁄4 inch NPT. Output is toward thefront, supply is toward the back. Two pressure gauges, output on top,supply on bottom, are located on the front of the pneumatic block.Maximum allowable air supply pressure to the SVI II AP variesaccording to actuator, valve size, and valve type. See Pressure Droptables in valve specification sheets to determine the correct positionersupply pressure. Minimum supply pressure should be 5 to 10 psi abovemaximum spring pressure but may not exceed the rated actuatorpressure.OutputSupplyFigure 4Air Ports on Single Acting PositionerInstallation and Set Up Connecting the Tubing and Air Supply Double Acting PositionerConnect Output 1, labeled “(←I)” to the inlet port of the actuator andconnect Output 2 labeled “(←II)” to the opposing actuator port (seeFigure 5 below for double acting ports.Output I ConnectorSupply Connector Connector Output IIFigure 5Air Ports on Double Acting PositionerConnecting the Air SupplyAfter the tubing is installed, use the following procedure to connect theair supply.1.Connect a supply of clean, dry compressed air to the filterregulator.2.Turn on the air supply.3.Adjust the filter regulator.4.Supply pressure must be 5 - 10 psi greater than the springrange of the actuator but may not exceed the ratedactuator pressure. Refer to the valve or actuatorinstruction manual.Masoneilan Dresser SVI II AP Quick Start GuideWiring the SVI II AP In order for the SVI II AP to communicate the positioner data the SVI II AP must be physically connected to a HART communication. The procedure below outlines wiring the SVI II AP.Comply with current national and local regulationsfor electrical installation work.Comply with national and local explosiveatmosphere regulations.Before carrying out any work on the device, poweroff the instrument or make sure that the localeconditions for potentially explosive atmospherepermit the safe opening of the cover.Connecting to the Control LoopThe SVI II APpositioner MUST BE grounded according to localregulations. It is important to maintain correct polarity at all times,otherwise the positioner may not operate properly. The SVI II APshould be physically connected to the HART loop using a cablespecified by the HART Communication Foundation. A shielded cableis recommended.To connect the Control Loop to the SVI II AP:1.Connect one end of the cable to the control loop's4 - 20mA output2.Remove the threaded wiring covers on the positioner.3.Connect the other end of the cable to the SVI II AP. Thereare two threaded openings on the positioner. Use theopening with the red plastic insert.4.Maintain polarity + and - respectively.Wiring GuidelinesThis list contains eight guidelines for a successful implementation of DCcurrent signal, DC power, and HART communication to the SVI II AP:pliance voltage at the SVI II AP must be 9 volts at themaximum current of 20 mA.2.Signal to the SVI II AP must be a regulated current in therange 3.2 to 22 mA.3.Controller output circuit must be unaffected by the HARTtones which are in the frequency range between 1200 and2200 Hz.4.Frequency range of the HART tones must have a circuitimpedance of more than 220 Ohms, typically 250 Ohms.5.HART tones may be imposed by the positioner and acommunication device located anywhere on the signalingcircuit.Installation and Set Up Wiring the SVI II AP6.Capacitance of the signaling circuit must not exceed 0.26microfarads or 0.10 microfarads with high seriesresistance.7.Cabling must be shielded to prevent electrical noise thatwould interfere with the HART tones, with the shieldgrounded.8.Signal must be properly grounded in only one place.Note:For details and calculation methods for wiring resistance, andcapacitance and for calculation of cable characteristics pleaserefer to the HART FSK Physical Layer Specification.SVI II AP SetupsTypical system setups are shown in Figure 6 on page 13, GeneralPurpose and Explosion Proof (EEx d) Installation Schematic and Figure7 on page 13, Intrinsically Safe Installation Schematic. The SVI II APpositioner can be located in a general-purpose or hazardous areaprotected by Explosion Proof (EEx d) methods. Wiring diagrams aregeneralized, actual wiring must adhere to Electrical Installation sectionof manual and local electrical codes. The use of a HandheldCommunicator or a HART modem is not permitted in the HazardousArea protected by Explosion Proof (EEx d) methods. In Figure 7 onpage 13 the SVI II AP positioner is located in a hazardous area that isprotected by Intrinsically Safe wiring practices.The SVI II AP requires an electrical input from a 4-20 mA currentsource. The SVI II AP input signal can carry a HART communicationprotocol signal from ValVue 2.4 or greater software and a HARTmodem, or from a HART Hand Held Communicator. Since the processcontrol system, the source of the input signal, is located in a non-hazardous location, setup requires an intrinsic safety barrier be placedbetween the process control system and the SVI II AP. If the SVI II APis located in a hazardous area with Intrinsically Safe protection a barrieris not required for a flameproof installation. Alternatively the systemcan be installed as Explosion Proof ⁄ flameproof. SVI II AP cancommunicate with a remote PC running ValVue software via a modemconnected to the PC's serial or USB port. The PC, which is notintrinsically safe, must be connected to the circuit on the safe area sideof the intrinsic safety barrier if the valve is located in a hazardous area.The SVI II AP can be operated, calibrated, configured, and interrogatedeither by using local pushbutton and display, or by using a PC runningValVue 2.4 software, HART Handheld Communicator, or any registeredHART Host that supports DDs. The HART Handheld Communicator isapproved for Intrinsically Safe use in accordance with FM and ATEXstandards. Read and observe all HHC labelling. The SVI II AP ispolarity sensitive so the positive lead must be connected to the positive(+) terminal and the negative lead to the negative (-) terminal. Reversalof input will not cause damage but the unit will not function.。
Insight Instant Wireless AirBridge模型WBC502安装指南说明书
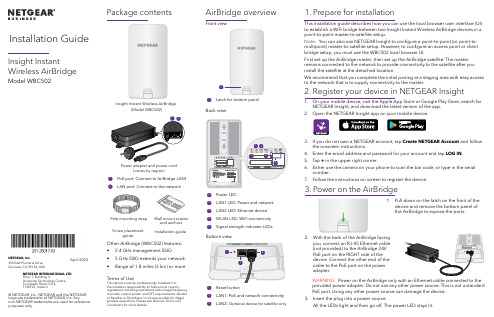
(Model WBC502)Package contents Pole mounting strap Wall mount screws and anchors NETGEAR, Inc.350 East Plumeria Drive San Jose, CA 95134, USA© NETGEAR, Inc., NETGEAR and the NETGEAR Logo are trademarks of NETGEAR, Inc. Anynon‑NETGEAR trademarks are used for reference purposes only.April 2020NETGEAR INTERNATIONAL LTD Floor 1, Building 3,University Technology Centre Curraheen Road, Cork, T12EF21, IrelandInsight Instant Wireless AirBridgeModel WBC502Installation GuideInsight Instant Wireless AirBridgeThis installation guide describes how you can use the local browser user interface (UI) to establish a WiFi bridge between two Insight Instant Wireless AirBridge devices in a point‑to‑point master‑to‑satellite setup.Note: You can also use NETGEAR Insight to configure a point-to-point (or point-to-multipoint) master‑to‑satellite setup . However, to configure an access point or client bridge setup, you must use the WBC502 local browser UI.First set up the AirBridge master, then set up the AirBridge satellite. The master remains connected to the network to provide connectivity to the satellite after you install the satellite at the detached location.We recommend that you complete the initial pairing at a staging area with easy access to the network that is to supply connectivity to the master.AirBridge overview1Power LED2LAN1 LED: Power and network 1. Prepare for installation1Latch for bottom panel1Front viewBack view2. Register your device in NETGEAR Insight1. On your mobile device, visit the Apple App Store or Google Play Store, search forNETGEAR Insight, and download the latest version of the app.2. Open the NETGEAR Insight app on your mobile device.Create NETGEAR Account and followLOG IN .WARNING: provided power adapter. Do not use any other power source. This is not a standard PoE port. Using any other power source can damage the device.2. With the back of the AirBridge facingyou, connect an RJ‑45 Ethernet cable (not provided) to the AirBridge 24V PoE port on the RIGHT side of the device. Connect the other end of the cable to the PoE port on the power adapter.3. Insert the plug into a power source.All the LEDs light and then go off. The power LED stays lit.Other AirBridge (WBC502) features:• 2.4 GHz management SSID• 5 GHz SSID extends your network •Range of 1.8 miles (3 km) or moreThis device must be professionally installed. It is the installer’s responsibility to follow local countryregulations including operations within legal frequency channels, output power and DFS requirements. Vendor or Reseller or Distributor is not responsible for illegal wireless operations. Please see Device’s Terms and Conditions for more details.Terms of Use1PoE port: Connect to AirBridge LAN12LAN port: Connect to the networkInstallation guideScrew placementguide8. Install the master and satelliteSupport and CommunityVisit /support to get your questions answered and access the latest downloads.You can also check out our NETGEAR Community for helpful advice at .For more information about Insight Instant Mesh‑capable products, visit .Regulatory and LegalSi ce produit est vendu au Canada, vous pouvez accéder à ce document en français canadien à https:///support/download/.(If this product is sold in Canada, you can access this document in Canadian French at https:///support/download/.)For regulatory compliance information including the EU Declaration ofConformity, visit https:///about/regulatory/.See the regulatory compliance document before connecting the power supply.For NETGEAR’s Privacy Policy, visit https:///about/privacy-policy .By using this device, you are agreeing to NETGEAR’s Terms and Conditions at https:///about/terms-and-conditions . If you do not agree, return the device to your place of purchase within your return period.Other supported modesOther supported operation modes for the AirBridge include point‑to‑multipoint master‑to satellite, access point, and client bridge. For more information, see the user manual at /support/product/WBC502.Insight Premium and Insight Pro subscribers can use the InsightCloud portal to configure a point‑to‑point master‑to‑satellite setup . For more information, see the NETGEAR Knowledge Base.4. Connect to the network We recommend that you connect the AirBridge to a network with Internet access during setup. If the network includes a DHCP server, such as a router, the AirBridge is automatically assigned a new IP address. (The default IP address is 192.168.0.100.)To prevent a network loop, s et up the AirBridge master first, and then disconnect it from the network before you set up the AirBridge satellite.1. Connect the LAN port on the power adapter to a router or switch on your network.(Do not connect the LAN2 port on the master directly to your network.)2. Connect your mobile device or computer to the same network where youconnected the AirBridge that you are setting up.1. 2. Install the master in such as way that it is in a direct line of site to the locationwhere you want to install the satellite.3. Install the satellite at the detached location, facing the front panel of the master atthe main site.You can place the satellite at a distance of 1.8 miles (3 km) or more from the master.4. Connect power to the devices.After the satellite establishes a WiFi connection with the master, the signal strength indicator (SSI) LEDs light.5. Use the SSI LEDs to adjust the position of the satellite for an optimal WiFi signal.7. Configure the satellite1. Disconnect the AirBridge master from the network, and then connect the AirBridgesatellite to the network.2. Repeat step3. Power on the AirBridge and step 5. Access the Day Zero Easy Setupon the satellite.3. In the AP Login New Password field, enter a new admin local device password.4. From the Operation mode menu, select AirBridge Satellite .5. In the SSID field, enter the same name that you set for the master.6. In the Passphrase field, enter the same passphrase that you set for the master.7. In the Management WPA2 Passphrase field, enter a new passphrase for themanagement SSID, which lets you manage the satellite over a WiFi connection.8. Click the Apply button.Your settings are saved and the satellite reboots to apply your settings.9. Log in as admin with the new local device password, and agree to the Terms of Use. 10. View the LEDs on the back of the satellite device. The green LED on the far rightlights, indicating a strong signal. You can now log out and disconnect the satellite.6. Configure the masterThe first time that you access the local browser UI of an AirBridge, you must set the operation mode, a new admin local device password, a unique name and new passphrase for the 5 GHz SSID, and a new passphrase for the management SSID.Tip: Be sure to write down the SSID name and all your passwords.1. In the AP Login New Password field, enter a new admin local device password.2. From the Operation mode menu, select AirBridge Master .3. In the SSID field, enter a new name for the 5 GHz SSID.4. In the Passphrase field, enter a new passphrase for the 5 GHz SSID.5. In the Management WPA2 Passphrase field, enter a new passphrase for themanagement SSID, which lets you manage the master over a WiFi connection.6. Click the Apply button.Your settings are saved and the master reboots to apply your settings.7. Log in as admin with the new local device password, and agree to the Terms of Use.You can now log out and disconnect the master.1. Enter the IP address of the AirBridge.If you don’t know the IP address of the AirBridge, use the NETGEAR Insight app or another discovery method.Your browser might display a security message. Ignore it or add an exception. 2. For the Management Mode, select the Standalone Mode radio button.The page adjusts to show the Day Zero Easy Setup settings.5. Access the Day Zero Easy SetupGreen LED Right SSI LED solid green . The signal for the WiFi connection is strong. The left and middle SSI LEDs are off.Amber LED Middle SSI LED solid amber . The signal for the WiFi connection is moderately good. The left and right SSI LEDs are off.Red LEDLeft SSI LED solid red . The signal for the WiFi connection is weak. The middle and right SSI LEDs are off.。
INS 036 Security Control Panel User Guide

To TEST the SOUNDERS and STROBE
q Enter your existing code
. The Unset light will flash. Enter
0 0 0 1 . All the zone lights will illuminate. Enter . All the zone lights
Enter Your Code Press Part
Enter Your Code
Enter Your Code Press Full or Part Press Omit Press Zone Number(s) Press Prog
Enter Your Code Press Reset
Enter Your Code Press Chime Press Zone Number(s) Press Prog
q Enter via a designated entry route. The slow entry tone will start.
Enter your code
. The system will unset and the entry
tone will stop. The display will flash the zone light of the zone
It is possible to omit (exclude) or include individual zones during
q f p setting. Enter your code
. Press
or
.
O Press . The exit tone and exit timer will stop and the display will
DrayTek VigorAP 1060C 11ax 天花板 AP 快速引导版本 1.0 固件版本

VigorAP 1060C 11ax Ceiling AP Quick Start GuideVersion: 1.0Firmware Version: V1.4.0(For future update, please visit DrayTek web site)Date: March 31, 2021Intellectual Property Rights (IPR) InformationCopyrights © All rights reserved. This publication contains information that is protected by copyright. No part may be reproduced, transmitted, transcribed, stored ina retrieval system, or translated into any language without written permissionfrom the copyright holders.Trademarks The following trademarks are used in this document:●Microsoft is a registered trademark of Microsoft Corp.●Windows, Windows 8, 10 and Explorer are trademarks of Microsoft Corp.●Apple and Mac OS are registered trademarks of Apple Inc.●Other products may be trademarks or registered trademarks of theirrespective manufacturers.Safety Instructions and ApprovalSafety Instructions ●Read the installation guide thoroughly before you set up the device.●The device is a complicated electronic unit that may be repaired only beauthorized and qualified personnel. Do not try to open or repair thedevice yourself.●Do not place the device in a damp or humid place, e.g. a bathroom.●Do not stack the devices.●The device should be used in a sheltered area, within a temperaturerange of 0 to +40 Celsius.●Do not expose the device to direct sunlight or other heat sources. Thehousing and electronic components may be damaged by direct sunlight or heat sources.●Do not deploy the cable for LAN connection outdoor to preventelectronic shock hazards.●Keep the package out of reach of children.●When you want to dispose of the device, please follow local regulationson conservation of the environment.Warranty We warrant to the original end user (purchaser) that the device will be free from any defects in workmanship or materials for a period of two (2) yearsfrom the date of purchase from the dealer. Please keep your purchase receiptin a safe place as it serves as proof of date of purchase. During the warrantyperiod, and upon proof of purchase, should the product have indications offailure due to faulty workmanship and/or materials, we will, at our discretion,repair or replace the defective products or components, without charge foreither parts or labor, to whatever extent we deem necessary tore-store theproduct to proper operating condition. Any replacement will consist of a newor re-manufactured functionally equivalent product of equal value, and willbe offered solely at our discretion. This warranty will not apply if the productis modified, misused, tampered with, damaged by an act of God, or subjectedto abnormal working conditions. The warranty does not cover the bundled orlicensed software of other vendors. Defects which do not significantly affectthe usability of the product will not be covered by the warranty. We reservethe right to revise the manual and online documentation and to make changesfrom time to time in the contents hereof without obligation to notify anyperson of such revision or changes.Declaration of ConformityHereby, DrayTek Corporation declares that the radio equipment type VigorAP 1060C is in compliance with Directive 2014/53/EU.The full text of the EU declaration of conformity is available at the following internet address: https:///ftp/VigorAP 1060C/Document/CE/Manufacturer: DrayTek Corp.Address: No. 26, Fushing Rd, HuKou, Hsinchu Industrial Park, Hsin-Chu County, Taiwan 303 Product: VigorAP 1060CFrequency Information for Europe area:2.4G WLAN 2412MHz - 2472 MHz, max. TX power: 19.86 dBm *15G WLAN 5150MHz - 5250 MHz, max. TX power: 22.85 dBm;5250MHz - 5350 MHz, max. TX power: 22.85 dBm;5470MHz - 5725 MHz, max. TX power: 28.84 dBm *2(*1: for 2.4G WLAN model; *2: for 5G WLAN model)This product is designed for 2.4GHz and 5GHz WLAN network throughout the EC region.Regulatory InformationFederal Communication Commission Interference StatementThis equipment has been tested and found to comply with the limits for a Class B digital device, pursuant to Part 15 of the FCC Rules. These limits are designed to provide reasonable protection against harmful interference in a residential installation. This equipment generates, uses and can radiate radio frequency energy and, if not installed and used in accordance with the instructions, may cause harmful interference to radio communications. However, there is no guarantee that interference will not occur in a particular installation. If this equipment does cause harmful interference to radio or television reception, which can be determined by turning the equipment off and on, the user is encouraged to try to correct the interference by one of the following measures:●Reorient or relocate the receiving antenna.●Increase the separation between the equipment and receiver.●Connect the equipment into an outlet on a circuit different from that to which the receiveris connected.●Consult the dealer or an experienced radio/TV technician for help.This device complies with Part 15 of the FCC Rules. Operation is subject to the following two conditions:(1) This device may not cause harmful interference, and(2) This device may accept any interference received, including interference that may cause undesired operation.Radiation Exposure Statement: This equipment complies with FCC radiation exposure limits set forth for an uncontrolled environment. This equipment should be installed and operated with minimum distance 20cm between the radiator & your body.Company nameABP International Inc.Address 13988 Diplomat Drive Suite 180 Dallas TX 75234 ZIP Code 75234E-mail*******************USA Local Representative Contact PersonMr. Robert MesserTel. 19728311600Caution● Any changes or modifications not expressly approved by the grantee of this device could void theuser's authority to operate the equipment.● Any changes or modifications not expressly approved by the party responsible for compliancecould void the user's authority to operate this equipment.● This equipment complies with CE RF radiation exposure limits set forth for an uncontrolled environment. This equipment should be installed and operated with minimum distance 20cm between the radiator & your body.● Operations in the 5.15-5.35GHz band are restricted to indoor usage only.T a b l e o f C o n t e n t s1. Package Content (1)2. Panel Explanation (2)3. Installation (3)3.1 Ceiling-mount Installation (Wooden Ceiling) (3)3.2 Ceiling-mount Installation (Plasterboard Ceiling) (4)3.3 Suspended Ceiling (Lightweight Steel Frame) Installation (5)3.4 Wall-Mounted Installation (6)4. Connection and Configuration (7)4.1 Connect to a Vigor Router using AP Management (7)4.2 Web Configurations (8)Connected As a Mesh Node (in Mesh Network) (8)Connected As an Access Point (8)5. Customer Service (11)Be a Registered Owner (11)Firmware & Tools Updates (11)1. P a c k a g e C o n t e n tTake a look at the package content. If there is anything missed or damaged, please contact DrayTek or dealer immediately.VigorAP 1060C Main UnitQuick Start Guide15/16" and 9/16" Mount Base(for ceiling mounting)Fixings and Screws (for ceiling mounting)Mount Base (for wall mounting) Screw Set(for wall / ceiling mounting)Cable TieRJ-45 Cable (Ethernet)NotePower Input: 12V 2.5A PoE Input: 54V 0.6ATotal Rated Power Consumption: 21 Watts2.P a n e l E x p l a n a t i o nStatus ExplanationOn (Blue)The system is in boot-loader mode.OffThe system is not ready or fails.1Blinking(Blue)The system is in TFTP mode.Off The system is not ready or fails.2Blinking(Blue) The system is ready and can work normally.ExplanationEthernet Port Connects to LAN or router.Supports PoE power & Gigabit (2.5Gbps).Power Jack(12V 2.5A)Connecter for a power adapter.ExplanationFactory Reset Restores the unit back to factory default settings.To use, insert a small item such as an unbentpaperclip into the hole. You will feel the buttoninside depress gently. Hold it for 5 seconds.The VigorAP will restart with the factory defaultconfiguration and the LED will blink blue.Security Hole A security hole for installing the anti-theft lock.Note For the sake of security, make the accessory kit away fromchildren.FactoryResetPower Jack LEDSecurityHole3.I n s t a l l a t i o nVigorAP can be installed under certain locations: wooden ceiling, plasterboard ceilings, light-weighted steel frame and wall.3.1C e i l i n g-m o u n t I n s t a l l a t i o n(W o o d e n C e i l i n g)Determine where the Access Point to be placed and mark location on the surface for the two mounting holes. Use the appropriate drill bit to drill two holes in the markings and hammer the bolts into the openings.1.Place the mount base under the wooden ceiling and fasten it on the ceilingwith two screws firmly.2.When the mount base is in place, slide the AP into the slot of the mountbase.3.2C e i l i n g-m o u n t I n s t a l l a t i o n(P l a s t e r b o a r d C e i l i n g)1.Place the Mount Base under the plasterboard ceiling and fasten twoturnbuckles firmly.2.Make the screws pass through the Mount Base and insert into the turnbuckles.Fasten them to offer more powerful supporting force.3.When the Mount Base is in place, slide the mount base into the slot of theAP.3.3 S u s p e n d e d C e i l i n g (L i g h t w e i g h t S t e e l F r a m e ) I n s t a l l a t i o nYou cannot screw into ceiling tiles as they are weak and not suitable for bearing loads. Your VigorAP is supplied with mounts (Mount Base) which will be used to attach directly to the ceiling frame of your suspended ceiling.1. Slide the mount base into the slot of the AP.2. Hold the Access Point with one hand to reach the other hand over the T-Railsides of the bracket.3. Rotate and hook the stationary end of the ceiling mount base onto the T-Railceilingframe.Note Warning: The screw set shown below is for wall mounting only.Do not use such set for ceiling mounting due to the danger offalling.3.4W a l l-M o u n t e d I n s t a l l a t i o nFor wall-mounting, the VigorAP has keyhole type mounting slots on the underside.e the appropriate drill bit to drill two 8.1mm diagram and 26mm depthholes in the markings and hammer the bolts into the openings.2.Screw the anchors unto the holes until they are flush with the wall; screwthe included screws into the anchors.3.Place the Access Point against wall with the mounting screw heads.4.C o n n e c t i o n a n d C o n f i g u r a t i o n4.1C o n n e c t t o a V i g o r R o u t e r u s i n g A P M a n a g e m e n tYour VigorAP can be used with Vigor routers which support AP management (such as the Vigor2865 or Vigor2927 series). AP Management enables you to monitor and manage multiple DrayTek APs from a single interface.1.Connect VigorAP to PoE switch (via LAN port) with Ethernet cable. VigorAPwill get the power from the switch directly. Then, connect the VigorSwitchto a Vigor router.2.Access into the web user interface of Vigor router. Here we take Vigor2865as an example. Open Central Management>>AP>>Status.3.Locate VigorAP 1060C. Click the IP address assigned by Vigor router toaccess into web user interface of VigorAP 1060C.4.After entering the username and password (admin/admin), the main screenwill be displayed.4.2W e b C o n f i g u r a t i o n sThis section will guide you to install the AP and make configuration for VigorAP.C o n n e c t e d A s a M e s h N o d e(i n M e s h N e t w o r k)❶Install VigorAP on to the ceiling.❷As a mesh node, settings related to VigorAP 1060C must be configured by a remote Mesh Root (e.g., VigorAP 903) within the mesh network.The user must detect VigorAP 1060C via a Mesh Root to add it as amesh node.C o n n e c t e d A s a n A c c e s s P o i n tAs an access point, VigorAP 1060C must be connected to a router and configured in AP (Access Point) / Range Extender mode.❶Install VigorAP on to the ceiling.❷Use a twisted-pair cable with RJ-45 plugs at both ends, and plug into Ethernet device (e.g., Vigor router) and Ethernet port of VigorAP.❸ There are two methods to configure VigorAP.Method 1:(a) First, open a web browser on your PC and type https://192.168.1.2. Apop-up window will open to ask for username and password.Note You may either simply set up your computer to get IPdynamically from the router or set up the IP address of thecomputer to be in the same subnet as the IP address ofVigorAP 1060C.● If there is no DHCP server on the network, then VigorAP1060C will have an IP address of 192.168.1.2.● If there is DHCP available on the network, then VigorAP1060C will receive its IP address via the DHCP server.● If you connect to VigorAP by wireless LAN, you could tryto access the web user interface through .(b) After clicking Login, Quick Start Wizard for configuring wirelesssettings will appear as follows.(c)Follow the on-screen steps to finish the network connection. Method 2:(a)Use a mobile phone to scan the QR code named with DrayTek WirelessApp to download DrayTek Wireless APP.(b)After downloading, run the APP.(c)Click Quick Start Wizard. Next, scan the QR code named with ConnectSSID. Later, click Connect to access into the APP user interface ofVigorAP 1060C to set the device in AP or Range Extender mode.5.C u s t o m e r S e r v i c eIf the device cannot work correctly after trying many efforts, please contact your dealer/DrayTek for further help right away. For any questions, please feel freetosende-mailto“*******************”.B e a R e g i s t e r e d O w n e rWeb registration is preferred. You can register your Vigor router viahttps://.F i r m w a r e&T o o l s U p d a t e sDue to the continuous evolution of DrayTek technology, all routers will beregularly upgraded. Please consult the DrayTek web site for more information on newest firmware, tools and documents.https://GPL Notice This DrayTek product uses software partially or completely licensedunder the terms of the GNU GENERAL PUBLIC LICENSE. The author ofthe software does not provide any warranty. A Limited Warranty isoffered on DrayTek products. This Limited Warranty does not coverany software applications or programs.To download source codes please visit:GNU GENERAL PUBLIC LICENSE:https:///licenses/gpl-2.0Version 2, June 1991For any question, please feel free to contact DrayTek technical*************************************************.。
Tripp Lite TLP606USB保护器说明说明书
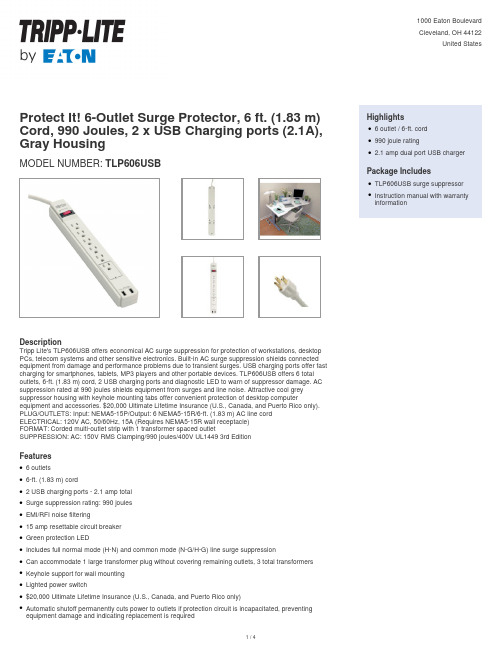
Protect It! 6-Outlet Surge Protector, 6 ft. (1.83 m)Cord, 990 Joules, 2 x USB Charging ports (2.1A),Gray HousingMODEL NUMBER:TLP606USBDescriptionTripp Lite's TLP606USB offers economical AC surge suppression for protection of workstations, desktop PCs, telecom systems and other sensitive electronics. Built-in AC surge suppression shields connected equipment from damage and performance problems due to transient surges. USB charging ports offer fast charging for smartphones, tablets, MP3 players and other portable devices. TLP606USB offers 6 total outlets, 6-ft. (1.83 m) cord, 2 USB charging ports and diagnostic LED to warn of suppressor damage. AC suppression rated at 990 joules shields equipment from surges and line noise. Attractive cool grey suppressor housing with keyhole mounting tabs offer convenient protection of desktop computerequipment and accessories. $20,000 Ultimate Lifetime Insurance (U.S., Canada, and Puerto Rico only).PLUG/OUTLETS: Input: NEMA5-15P/Output: 6 NEMA5-15R/6-ft. (1.83 m) AC line cord ELECTRICAL: 120V AC, 50/60Hz, 15A (Requires NEMA5-15R wall receptacle)FORMAT: Corded multi-outlet strip with 1 transformer spaced outletSUPPRESSION: AC: 150V RMS Clamping/990 joules/400V UL1449 3rd EditionFeatures6 outletsq 6-ft. (1.83 m) cordq 2 USB charging ports - 2.1 amp total q Surge suppression rating: 990 joules q EMI/RFI noise filteringq 15 amp resettable circuit breaker q Green protection LEDq Includes full normal mode (H-N) and common mode (N-G/H-G) line surge suppressionq Can accommodate 1 large transformer plug without covering remaining outlets, 3 total transformers q Keyhole support for wall mounting q Lighted power switchq $20,000 Ultimate Lifetime Insurance (U.S., Canada, and Puerto Rico only)q Automatic shutoff permanently cuts power to outlets if protection circuit is incapacitated, preventing equipment damage and indicating replacement is requiredqHighlights6 outlet / 6-ft. cord q 990 joule ratingq 2.1 amp dual port USB chargerqPackage IncludesTLP606USB surge suppressor q Instruction manual with warranty informationqSpecifications© 2023 Eaton. All Rights Reserved. Eaton is a registered trademark. All other trademarks are the property of their respective owners.。
xPrintServer 使用手册说明书

Print from Your Mobile DevicesThe easy-to-use xPrintServer is the perfect ‘plug-and-print’ solution to enableAirPrint® on your printers in the office, school or home. Once installed, the xPrintServer automatically discovers and provisions your printers without the need for manual set up and without losing your capability to print from Mac OS®. Designed for a wide range of businesses, this small print server provides enterprise features and enables wireless printing from an unlimited number of mobile devices to multiple printers without any licensing fees.Simple and Quick Set-Up NEW!Mobile Print ServeriPrint from your iPadxPrintServer® OfficeThe xPrintServer® Office Mobile Print Server is a ‘plug-and-print’ solution enabling wireless printing for iOS, devices without any proprietary apps.Enables AirPrint on your printers lettingyou print wirelessly from iOS devicesSimple ‘plug-and-print’ installation andintuitive useSupports unlimited number of iOSdevicesNo need to download proprietary appsAdministrative and securityconfigurations via web UIPrint job monitoring and log exportingNetwork (wired/wireless) and USB printersupportSupports over 2000 printer models frommajor manufacturersSupports both DHCP and static IPaddress assignments+ =Features and Specifications© 2020 Lantronix, Inc. All rights reserved. Lantronix and xPrintServer are registered trademarks of Lantronix Inc. Connect Smart. Do more., is a trademark of Lantronix, Inc. Google is a registered trademark, and Google Chrome is a trademark of Google Inc. iPhone, iPad, iPod, Mac OS, AirPrint, AirPrint Logo and Safari are registered trademarks of Apple Inc., registered in the U.S. and other countries. Windows and Internet Explorer are registered trademarks of Microsoft Corporation. Firefox is a registered trademark of Mozilla Foundation. Fire OS is a trademark of , Inc. or its affiliates. All other trademarks and trade names are the property of their respective holders. MPB-00023 Rev C。
N 快速参考指南
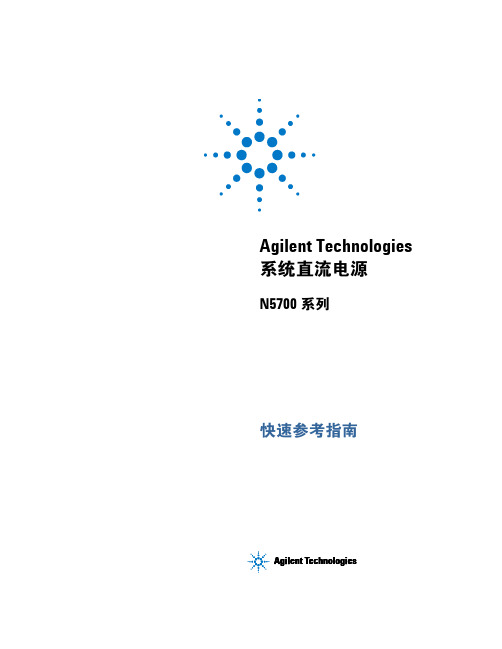
Agilent Technologies系统直流电源N5700 系列快速参考指南A安全注意事项在操作本仪器的所有阶段,必须遵守下列一般性安全预防措施。
不遵守这些预防措施或本手册中的其他特定警告或说明,将违反该仪器的设计、制造和使用的安全标准。
安捷伦科技公司对客户不遵守这些规定而导致的后果不承担任何责任。
一般原则不要以制造商规定之外的方式使用本产品。
如不按照操作手册中规定的方式使用本产品,其保护功能可能会失效。
接通电源前检查是否已采取所有安全预防措施。
在接通电源前,确保进行了设备的所有连接。
请留意在“安全符号”下面介绍的仪器外部标识。
将仪器接地本产品为 1 类安全仪器(提供了保护接地端子)。
要将电击危险降到最低程度,必须将仪器机箱和机盖接地。
必须通过接地电源线将仪器连接到交流电源,接地电线要牢固地连接到电源插座的电气接地(安全接地)端。
中断保护(接地)导线或断开保护接地端子,将产生可导致人身伤害的潜在电击危险。
熔断器为避免火灾,请仅使用指定型号和额定值(正常熔断、延时等)的熔断器来更换电源熔断器。
不要使用维修过的熔断器或短路的熔断器座。
否则可能引起电击或火灾。
不要在易爆环境中操作不要在有易燃性气体或烟雾的场所使用本仪器。
不要卸下仪器机盖只能由合格的、经过维修培训且了解潜在危险的专业人员打开仪器机盖。
在卸下仪器机盖之前,要断开电源线和外部电路。
不要改动仪器不要安装代用零件或对产品擅自改动。
请将仪器返回安捷伦销售和服务部进行维护和维修,以保持其安全特性。
发生损坏时仪器一旦出现损坏或故障迹象,应停止操作并防止无意操作,并等待合格的维修人员进行修理。
小心符号表示存在危险。
它提请用户对某一操作过程、操作方法或类似情况的注意。
如果不能正确执行或遵守规则,则可能对产品造成损坏或丢失重要数据。
在完全理解和满足所指出的小心条件之前,不要继续下一步。
警告符号表示存在危险。
它提请用户对某一操作过程、操作方法或类似情况的注意。
ISO 16016 Soluzione Ready to Go 全面解决方案说明书
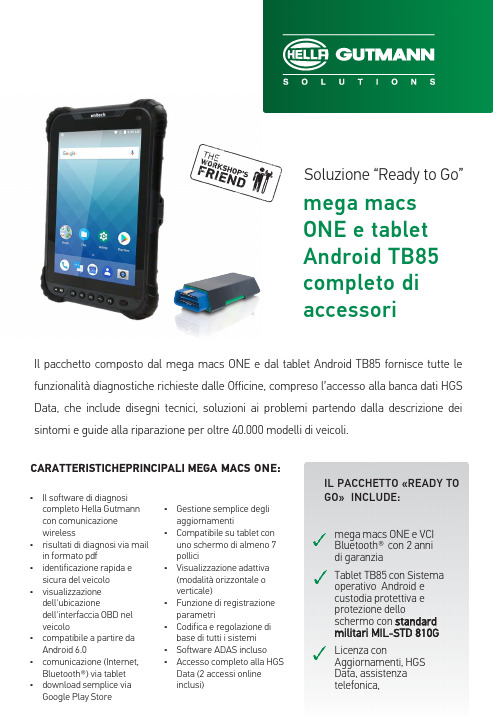
Copyright Protection: Confidential -ISO 16016Soluzione “Ready to Go”mega macs ONE e tablet Android TB85 completo di accessoriIl pacchetto composto dal mega macs ONE e dal tablet Android TB85fornisce tutte le funzionalitàdiagnostiche richieste dalle Officine,compreso l’accesso alla banca dati HGS Data,che include disegni tecnici,soluzioni ai problemi partendo dalla descrizione dei sintomi e guide alla riparazione per oltre 40.000modelli di veicoli.IL PACCHETTO «READY TO GO» INCLUDE:mega macs ONE e VCI Bluetooth®con 2anni di garanziaTablet TB85con Sistema operativo Android e custodia protettiva e protezione delloschermo con standard militari MIL-STD 810G Licenza conAggiornamenti, HGS Data, assistenzatelefonica,CARATTERISTICHEPRINCIPALI MEGA MACS ONE:•Il software di diagnosi completo Hella Gutmann con comunicazione wireless•risultati di diagnosi via mail in formato pdf•identificazione rapida e sicura del veicolo •visualizzazione dell'ubicazionedell'interfaccia OBD nel veicolo•compatibile a partire da Android 6.0•comunicazione (Internet, Bluetooth®) via tablet •download semplice via Google Play Store•Gestione semplice degli aggiornamenti•Compatibile su tablet con uno schermo di almeno 7 pollici•Visualizzazione adattiva (modalità orizzontale o verticale)•Funzione di registrazione parametri•Codifica e regolazione di base di tutti i sistemi •Software ADAS incluso •Accesso completo alla HGS Data (2 accessi onlineinclusi)Copyright Protection: Confidential -ISO 16016T A B L E T E A C C E S S O R I I N C L U S ICARATTERISTICHEAndroid TB85Tablet –Display 8’’ LCD colori –4 GB DDR3 –32 GB eMMC –CPU Qualcomm MSM8953 PRO Octa-Core 2.2 GHz –Risoluzione 1280 x 800 –Sistema Operativo Android 8.0 Certificato GMS –CameraFrontale 5 Megapixel –Fotocamera posteriore 13 Megapixel –Tempo ricarica batteria: meno di 4 oreSupporto mano a strappoPellicole per protezione schermoMEGA MACS ONE –READY TO GODettaglio prodotti e servizi inclusi nel pacchettoCosa comprende la licenza prevista nell’offerta?AGGIORNAMENTI Inclusi per 12 mesiHGS DATA Banca dati esterna Inclusa per 12 mesiCALL FLAT Assistenza tecnica Illimitata per 12 mesiAggiornamenti regolari scaricabili comodamenteda Internet con più veicoli, più funzioni diagnostiche, più componenti elettronici e centraline. Tutto affinché il sistema diagnostico riesca a interagire con quanti più modelli e con il massimo approfondimento di test possibile.HGS Data è una delle banche dati più aggiornate di tutto il mondo che ti fornisce l’accesso diretto ai dati e alle informazioni tecniche di oltre 35.000 modelli di veicoli, schemi elettrici, suggerimentidi riparazione e molto altro ancora.Il nostro call center tecnico fornisce supporto con mega macs nella diagnosi dei veicoli e nella ricerca guasti, ti assiste nell‘interpretazione dei dati dando supporto anche con le informazioni sui ricambi.++Per ulteriori informazioni,contattaci oppure rivolgiti al tuo riferimento HELLA GUTMANN SOLUTIONS di zona*****************-www.hellatechworld.it。
Freescale - MC56F8006DEMO-T-PROMO 数字信号控制器(DSC)评估、演

Freescale - MC56F8006DEMO-T-PROMO -MC56F8006DEMO-T-PROMO Demo KitProduct Overview:MC56F8006DEMO-T-PROMO is a cost-effectiveboard targeting quick digital signal controller (DSC)evaluation, demonstration and debugging of theFreescale MC56F8006VLF digital signal controller.The board is equipped to handle USB communicationright out of the box. MC56F8006 demo board has aseries of 6 leds connected to PWM channels in orderto monitor signals and has a Reset and 2 IRQswitches.Kit Contents:The MC56F8006DEMO-TOPROMO contains the hardware essentials you will need to use it. The items in the Development Kit and their use are as follows.∙DVD Getting Started With MC56F8006/2Free CodeWarrior Development Studio for 56F800/E DSC, Special Edition (32KB code size limit)Device and Board Resources7 different MC56F8006 Demo Labs including LED flashing demonstration, USB Serial , Freemaster and FIR Labs.TAP∙ USBCable∙ USB∙MC56F8006DEMO-T Quick Start GuideCard∙ FreescaleWarrantyKey Features:∙Complete pin-out available including a 40 pin header compatible with all 56F80xx boards∙ Supply voltage options from USB connector, direct power supply in J1 and using standard power jack∙ MC56F8006 Demo board with USB connectivity ∙ JTAG control and debug of MC56F8006 ∙ BDM control and debug of MC9S08JM60 ∙ Serial Communications port ready for RS-232 ∙6 LEDs, connected to PWM channelsOrdering Information: Products:Part NumberManufacturerFarnell P/N Newark P/NMC56F8006DEMO-T-PROMO Freescale1758255NAAssociated Products:Part Number Manufacturer DescriptionFarnell P/N Newark P/N MC56F8006VLFFreescaleDigital Signal Controller IC171835811R0875 MC9S08JM60CGT Freescale MCU, 8-BIT, S08, 60KFLASH, QFN48 156286494M8314 USBMLCF FreescaleUSB ColdFire Multilink 1535884 01M6486 MAX3232CDBE4 TI True RS-232 Transceivers 1287435 26M0603 SN74LVC125ADTIQuad buffer driver110297594B6303 MIC2026-1BM MICREL Dual-Channel Power Distribution Switch 446196405C4401 LM1117DT-ADJ/NOPB NS Linear Voltage Regulator IC 1364485 41K3426 MC56F8006VLF Freescale Digital Signal Controller IC 1718358 11R0875 MC9S08JM60CLDFreescale8-Bit Microcontroller IC156286454M7190Similar Products:Part NumberManufacturerDescriptionSupport DeviceFarnell P/NNewark P/NMC56F8006DEMO FreescaleMC56F8006DSC Board MC56F8006 1748988 40P5046MC56F8006DEMO-T FreescaleMC56F8006DSC BoardMC56F8006 1748989 26R6765Document List:Datasheets:Part Number Description SizeMAX3232 3.0V to 5.5V, Low-Power, up to 1Mbps, True RS-232 Transceivers 272KB74LVC125 Quad buffer/line driver with 5 V tolerant input/outputs; 3-state 108KBMIC2026 Dual-Channel Power Distribution Switch 180KBLM1117 LM1117 800mA Low-Dropout Linear Regulator 532KBMC56F8006 MC56F8006 DSC Datasheet 1.82MBMC9S08JM60 MC9S08JM60 Datasheet 10.6MBMC56F8006 MC56F8006 Reference Manual 4MBApplication Notes:File Name SizeImplementing a Modular High Brightness RGB LED Network 1.82MBMC56F8006DEMO User Guide 3.19MBSingle Phase Two-Channel Interleaved PFC Converter Using MC56F8006 344KBHardware & Software:File Name SizeMC56F8006DEMO_FFT_lab 716KBMC56F8006DEMO_FIR_lab 2.17MBMC56F8006DEMO_Freemaster_lab 2.29MBMC56F8006DEMO_hall_motor_lab 796KBMC56F8006DEMO_LED_lab 232KBMC56F8006DEMO_PGA_lab 1MBMC56F8006DEMO_serial_lab 3.46MBMC56F8006DEMOLAB 64KB。
MT3336规格书
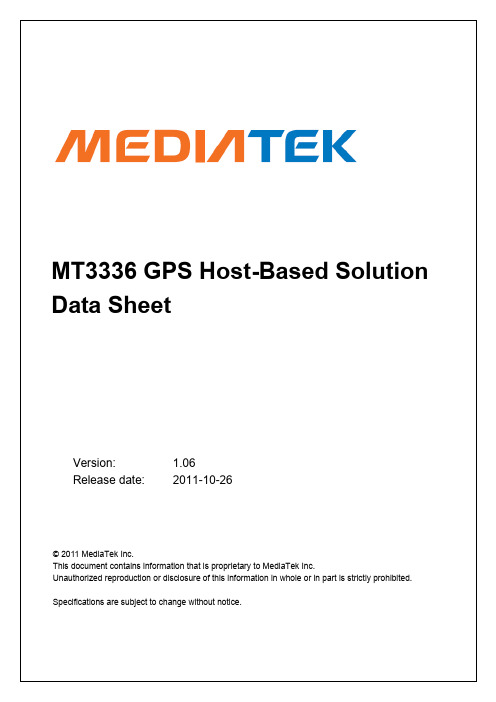
loginid=liub@,time=2013-12-30 19:50:17,ip=113.90.226.174,doctitle=MT3336_data_sheet_external_20111026.doc,company=Leatek_WCX
MT3336 GPS Host-Based Solution Confidential A
M e d
loginid=liub@,time=2013-12-30 19:50:17,ip=113.90.226.174,doctitle=MT3336_data_sheet_external_20111026.doc,company=Leatek_WCX
MT3336 GPS Host-Based Solution Confidential A
0.31
2011/04/01
Loris Li
0.32 0.33
2011/04/07 2011/04/12
Loris Li Loris Li
MediaTek Confidential
This document contains information that is proprietary to MediaTek Inc. Unauthorized reproduction or disclosure of this information in whole or in part is strictly prohibited.
loginid=liub@,time=2013-12-30 19:50:17,ip=113.90.226.174,doctitle=MT3336_data_sheet_external_20111026.doc,company=Leatek_WCX
HP QuickTest Professional手机应用测试要求及Jamo Solutions解决
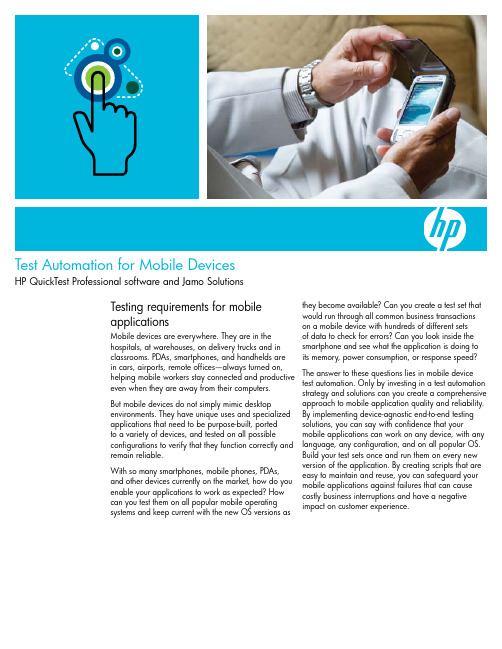
Test Automation for Mobile Devices HP QuickTest Professional software and Jamo SolutionsTesting requirements for mobile applicationsMobile devices are everywhere. They are in the hospitals, at warehouses, on delivery trucks and in classrooms. PDAs, smartphones, and handhelds are in cars, airports, remote offices—always turned on, helping mobile workers stay connected and productive even when they are away from their computers.But mobile devices do not simply mimic desktop environments. They have unique uses and specialized applications that need to be purpose-built, portedto a variety of devices, and tested on all possible configurations to verify that they function correctly and remain reliable.With so many smartphones, mobile phones, PDAs, and other devices currently on the market, how do you enable your applications to work as expected? How can you test them on all popular mobile operating systems and keep current with the new OS versions as they become available? Can you create a test set that would run through all common business transactions on a mobile device with hundreds of different setsof data to check for errors? Can you look inside the smartphone and see what the application is doing to its memory, power consumption, or response speed? The answer to these questions lies in mobile device test automation. Only by investing in a test automation strategy and solutions can you create a comprehensive approach to mobile application quality and reliability. By implementing device-agnostic end-to-end testing solutions, you can say with confidence that your mobile applications can work on any device, with any language, any configuration, and on all popular OS. Build your test sets once and run them on every new version of the application. By creating scripts that are easy to maintain and reuse, you can safeguard your mobile applications against failures that can cause costly business interruptions and have a negative impact on customer experience.Mobile applications test automation solution from HP and JamoHP Software provides one of the most advanced automated functional and regression testing solutions that support all major software applications and environments. Through partnership with cutting-edge, innovative companies such as Jamo Solutions, HP is extending its industry-leading functional testing capabilities to mobile applications. Jamo testing solutions use the HP QuickTest Professional (QTP) software platform and QTP’s best practices and advanced features to bring automation into the world of mobile application testing. The solution allowsfor end-to-end test automation: from the originating mobile device, through the delivery infrastructureto the receiving device. It covers the entire business process from both the IT perspective (monitoring servers, routers, and other infrastructure components) and the mobile devices where messages are being sent and received.Building test scripts for mobile applicationsThe Jamo mobile applications testing solution recognizes objects on a screen just like a user would see them. It captures these GUI objects into a QTP test script, making the scripts easy to navigate, enhance, and maintain. All user interactions with the device—such as sending a multimedia message or pressing the Send button—are captured and can be viewed in QTP in either a keyword or expert view. Using GUI-object recognition makes the script completely independent from the phone’s hardware configurations, processor power, screen resolution, background color, or available buttons. It makes the scripts extremely versatile and reusable, and helps achieve more comprehensive testing of your mobile applications. The ability to regression-test applications without having to recreate the test scripts for every patch or new version creates, perhaps, one of the most notable ROI from automated testing. Manual testing procedures can seldom cover the breadth of data combinations, business process scenarios, and test runs that can be achieved through automation. Replaying the test scriptsAnother tremendous advantage of automation over manual testing is its ability to collect device and connection information during the test run. This data can help you understand the underlying processes behind specific transactions, which can help diagnose and resolve problems faster.With Jamo Solutions, testers can not only checkif an e-mail or an SMS message was successfully transmitted by one phone and received by another but can also go deep into the process information and analyze data such as the number of processes running or the dlls used for each process. Testers can also access configuration details of each device and view screen resolution, battery usage, memory usage, and other related parameters. If the problem lies in the connection, Jamo Solutions allows testers to look into the connectivity details, such as which mobile operator was used for the transmission. All this information helps testers gather additional data during the test replay, analyze application performance, identify problem areas, and find solutions faster.Figure 1: Scripts are based on user actions and are easy to read, maintain, and reuse 2Testers can also recreate scenarios that may cause Array applications to fail. For example, Jamo Solutionssoftware can help testers fill the memory of thedevice to 80 percent or 90 percent to see how theapplications perform under those conditions.Jamo’s ability to access the mobile applicationfunctions on the API level makes it extremely usefulwhen validating application performance. Forinstance, by capturing the outgoing message throughthe internal API, rather than the UI, testers canmeasure the exact time it took for the message to bedelivered from one phone to the other, even if theclocks on both devices are not synchronized.Together, HP and Jamo Solutions enable testers toextend automation best practices from the desktopworld to the new, emerging world of mobileapplications. In addition, through seamless integrationwith HP Quality Center—one of the leading testmanagement software—test engineers can build acentral repository of mobile test scripts. This allowsevery member of the QA team to reuse test scripts,removes duplication of work, and simplifies testmaintenance significantly. You can manage all yourtesting assets from a global, Web-based centrallocation to promote collaboration between workgroups,reuse tests between builds and applications, andperform advanced change and impact analysis.As on-the-go applications continue to become morepopular, more and more companies are expected toinvest in mobile test automation to provide quality,reliability, and performance of their solutions.3About Jamo SolutionsJamo Solutions aims to promote testability in the area of test automation and application monitoring. The company mission is to work together withthe market players to increase the completenessof the management of the end-user experience. Jamo Solutions develops, markets, and sells tools and consultancy that extend the capabilities of best-of-breed testing and monitoring solutions for end-user experience measurement and management.For more information:For an overview of HP Quality Center, visit: /go/qualitycenterFor detailed information on HP QuickTest Professional software, visit: /go/functionaltesting For information on Jamo Solutions, visit:Technology for better business outcomesTo learn more, visit /go/software© Copyright 2009 Hewlett-Packard Development Company, L.P. The information contained herein is subject to change without notice. The only warranties for HP products and services are set forth in the express warranty statements accompanying such products and services. Nothing herein should be construed as constituting an additional warranty. HP shall not be liable for technical or editorial errors or omissions contained herein.4AA2-7048ENW, July 2009。
Sun Electronic Systems, Inc. EC16 环境测试室说明书

• 6.16 FT³ WORKING VOLUME•INTEGRAL USER Temperature Probe•LCO 2 , -73ºC TO +315ºC COOLING Optional LN2 , -184ºC to +315ºC•IEEE-488, RS232, RS422Remote Communication•EXPANDED I/O ARCHITECTURE Analog Input Ports Analog Output Ports Auxiliary I/O Drivers Digital Parallel Port High Speed Serial Link•LOCAL TEMPERATURE Controlled RampingThe EC16 is an advanced environmental cham-ber intended for automated test system and laboratory applications requiring fast temperature cycling and a large test volume. Standalone operation is supported by a full function keyboard with a 2 line, 16 character LCD display. The chamber temperature and the user temperature probe readings are normally displayed continuously. User programs are easily entered into the EC16 using a BASIC like command set programming language. In an automated test system, the EC16functions as a remote data acquisition and controlsystem using the capability of its expanded I/O archi-tecture.The electrically isolated user temperature probe allows for direct monitoring of critical temperatures on the device under test or certain areas inside the test chamber. As well as being displayed on the front panel,readings are accessible from the IEEE-488 or RS232/422 interfaces.The EC16 command set, whether entered from the local keyboard or downloaded over the IEEE-488 or RS232/422 interfaces, provides for setting chambertemperature, temperature ramping rate and soak time at temperature, temperature deviation limits and tem-perature upper and lower limits.Probe calibration procedures are built into the EC16 using local menu driven format. Special commu-nication commands allow for communication to the analog I/O ports, the high speed serial port (SPI) and the parallel port. The chamber can be controlled re-motely from the RS232/422 port or the IEEE-488 bus interface. When the IEEE-488 bus interface is used,transparent communication from the IEEE-488 bus to the RS232/422 port is supported. Programs and para-meters are stored in battery-backed memory.The PID coefficients used in the EC16 are user adjustable from the keyboard and remote interfaces. In addition, alarm function and sound level, BAUD rate,interrupt assignments and other communication port options are configurable from the front panel using an easy, menu driven format.The EC16 supports several safety features in-cluding a mechanically adjustable over temperaturethermostat, upper and lower software temperature lim-its, processor watchdog timer and open and short probe detection.The EC16 is designed to be adaptable to your system application. If you have special requirements,call Sun Systems for solutions.LOCAL AND REMOTE CONTROL INTERFACESThe EC16 supports stand-alone operation with a full function keyboard, a 2-line LCD and a powerful programming language. For automated test systems, a complete talker/listener IEEE-488 interface is available with serial and parallel poll capability. For remote operation over long distances, RS232 and RS422 serial interfaces areChart Recorder。
SYS-2016 用户手册说明书
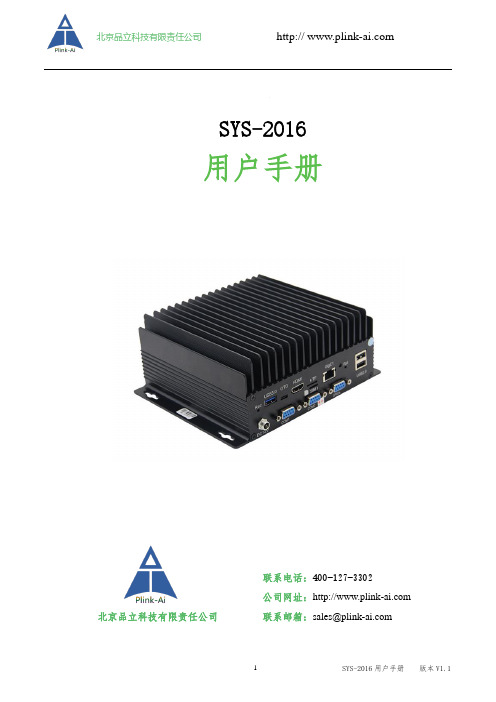
SYS-2016 用户手册北京品立科技有限责任公司联系电话:400-127-3302公司网址: 联系邮箱:******************电子元件和电路对静电放电很敏感,虽然本公司在设计电路板卡产品时会对板卡上的主要接口做防静电保护设计,但很难对所有元件及电路做到防静电安全防护。
因此在处理任何电路板组件时,建议遵守防静电安全保护措施。
防静电安全保护措施包括但不限于以下几点:➢运输、存储过程中应将板卡放在防静电袋中,直至安装部署时再拿出板卡。
➢在身体接触板卡之前应将身体内寄存的静电释放掉:佩戴放电接地腕带。
➢仅在静电放电安全区域内操作电路板卡。
➢避免在铺有地毯的区域搬移电路板。
➢通过板边接触来避免直接接触板卡上的电子元件。
用户手册更新历史文档版本更新日期更新内容适用硬件版本V1.0 2022-12-6 创建文档V1.0V1.1 2023-5-22 添加系统使用Jetpack5.*版本时,系统中GPIOV1.0映射号。
目录用户手册更新历史 (2)1 产品介绍 (4)1.1产品特性 (5)1.2订货信息 (5)1.3可选模组参数信息 (6)2 接口功能描述 (7)3 对外接口功能及位置 (8)4机械尺寸 (8)5使用方法 (10)整机使用方法 (10)R ECOVERY模式 (10)6注意事项及售后维修 (11)注意事项 (11)售后维修 (11)1 产品介绍SYS-2016是一款搭配NVIDIA® Jetson™ Xavier NX / Orin NX系列核心模块的紧凑型AI 工控计算机。
面向工业部署应用,主要接口进行了静电安全保护设计,采用了高可靠性的电源应用方案,输入电源具有过压与反极性保护功能,具有丰富的对外接口,内部接口载板器件均采用宽温型号。
SYS-2016采用大尺寸散热翅片,内部采用紫铜凸台及高性能热管做均热设计,具有良好的热传导及散热性能,使整机可适应更高环境温度场景。
适用于工业自动化、安防、新零售等场景。
ipotest-16i 说明书

ipotest-16i说明书
ipotest-16i遵照B级数字设备的限定而被测试和制造,即依据联邦通讯委员会(FCC)规则的第15部分。
这些限定的制定是为了提出保护的原因,防止对用户的成套设备产生有害干扰。
该设备可产生,使用和能够辐射高频能量,如果没有按照这个规则来安装和使用,则对无线通信可以引起有害干扰。
然而没有保证此干扰不会在个别设备产生。
如果此设备对无线电或电视接收引起有害干扰,该干扰可以被确定是由设备的开关引起的,用户会试着用以下一种或多种方法来纠正这个干扰:
重新调整和确定接收天线方向增大此设备与接收器之间的距离与销售商协商或向有经验的无线电/电视技术人员寻求帮助
该设备所采用的被屏蔽的互联电缆和动力电源电缆必须确保是依照相关的射频(RF)发射限度来进行管理的装置。
用户无权对此设备操作系统生产厂商所没有明确证明的改变或修正。
4xAGP插槽除了上边讲过的82815提供了图形存储器,加速了处理能力,P6ISM主板包括了4XAGP插槽,支持4X的AGP 显卡,提高了原来的带宽,AGP技术在图形和系统处理器之间提供了一个直接的连接,以便图形处理不必和处理器竞争,当需要它时,设计的外围元件互联上另外的设备。
例如,当在处理很大的地图时,要求虚拟变成现实和3D游戏中应用。
aigo A16 Tablet PC User Manual
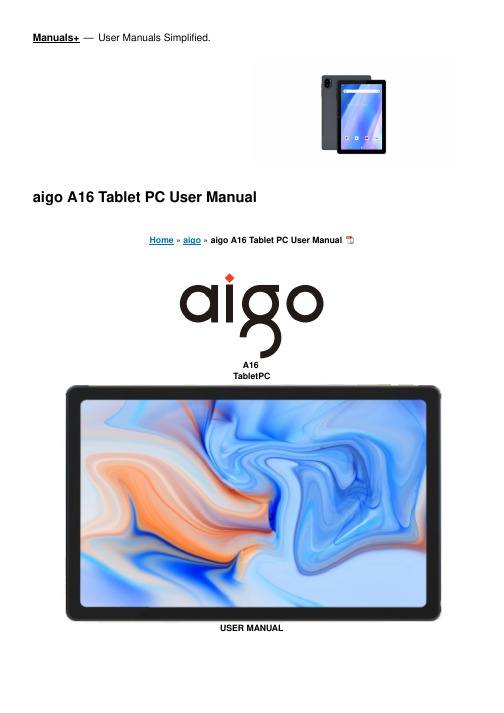
Manuals+— User Manuals Simplified.aigo A16 Tablet PC User ManualHome » aigo » aigo A16 Tablet PC User ManualA16TabletPCUSER MANUALContents1 FEATURES2 UNITATA GLAN3 GETTING STARTED4 ABOUT APPLICATION5 INSTALLING APPLICATIONS6 CONNECTING TO A Wifi NETWORK7 INTERNET NAVIGATING8 CONNECTING TO A BLUETOOTHDEVICE9 OPTIONAL CONNECTIO10 SPECIFICATIONS11 TROUBLESHOOTING12 CONTACT US13 FCC Statement14 Documents / ResourcesFEATURESBrowse the webVisityour favorite websites.Checkyour E-mailKeepin touch with friends and farilies Make watching your favorite videos easier with the YouTube app. Explore brand new content, music, news and more with the official YouTube 2pp.Download your favorite apps on Google PlayDiscover thousands of apps such as music, movies, TV, books, magazines, apps and gamesallon Google Play (Customers need to download these apps on Google Play).Connect to the Internet wirelesslyWith high-speed Wifi 802.11 ac/b/g/n (2.4GHz/5GHz) networking, you can enjoy your media library anytime and anywhere.The 6000mAh battery makes you feel free to listen to popular music, watch videos, and search for photos. Memory card readerIncrease your storage capacity (up to 128G8 supported).Built-in cameraConvenient front-facing camera SMP/rear camera 13MP (support flash).Automatic orientation detectionRead any way you want, the display adjusts automatically!UNITATA GLAN1. Front Camera2. Mmory Cardslot3. Rear Camera4. UsBTypeCPort5. Speaker6. Headphone Jack7. Power Button/Screen Saver8. VoL+poL-GETTING STARTEDTurning on/off the tabletToturn on the tablet;Press and hold the power button till the LCD screen turns on. Wait until the Home screen appears, the tablet s now ready for use.Toturn off the tablet:1. Press and hold the power button tll the Device Options menu appears.2. Tap “Power off” to turn off the tablet.Turning on/off the screen (Sleep mode)Whenthe tablet is on, you can turn off the screento save battery power. Simply press the power button once to turn the screen off. Press the power button again to turn the screen back on.To’save battery power, the screen can be st to turn off automatically when the tabletis notin use (between 15 seconds and 30 minutes).To change the screen timeout, tap Settings — Display — Screen timeout.Changing the languageYou can change the display language to your preferred language at any time.1. Tap Settings — System — Languages & input > Languages — Add a language.2. Select your preferred language from the list by tapping ont.If prompted, select the region for your chosenlanguage.3. Tap and hold your preferred language and drag it to the top of the st Toremove alanguage from the list, tap * –Remove, markthe language you would like to remove, and tap.Home Screen1. Back: Press to check the previous operating display.2. Home Screen: Press to go to the home screen.3. Background: Press to check applications runningin the background. Closing dle apps may help improveperformance.4. Application Panel: Swipe up to check all available applications.Wallpaper1. On yourtablet’s home screen, touch and hold an empty space.2. Tap Wallpapers.3. Pickyourwallpaper.4. Tap Set wallpaper.5. favailable, pick which screen(s) show the wallpaper.Widgets1. On yourtablet’s home screen, touch and hold an empty space.2. Tap “Widgets”.Tip:1. Tomakea folder on the home screen, drag an app or a shortcuton top of another. To rename the folder, tap thefolder, tap “Unnamed Folder”, and then enter the newname.2. Toaccess the quick notification settings, swipe down from the top of your screen.ScreenLockSetascreen lock tosecure your tablet. Goto Settings, tap “Security” – “Screen lock”,and select amode from None, Swipe, Pattern, PIN and Password. You can create a Backup PIN as a safety measure in case: you forgetyour code.Unlocking the ScreenWhen the screen turns off, you will have to unlock the screen when you turn it back on. Tounlock the screen, swipe up the lock icon.Taking a ScreenshotPress and hold the power button and volume down button at the same time to take ascreenshot. The screenshots will be saved in the photos file.ABOUT APPLICATIONTo open an application,tap the application icon on the home screen or swipe up to checkallavailable applications.The screen shown above isfor illustrative purposes only. We reserve the right to modify and improve the final list of applications available on the tabletPre-installed ApplicationsSome applications have beeninstalled on your tablet for your convenience. These applications include:Browse the web.Perform simple mathematical operations.Take picturesorvideoswith the cameracheckyoure-mailPlay musicINSTALLING APPLICATIONSYou can also download and install additional applications from Google Play, the web browser, or other sources. odownload apps from sources other than Google Play, your tablet must be set to allow app installations from unknown sources. Goto Settings, tap “Apps & notifications” — “Advanced” — “Special app access” = “Install unknown apps”. Select the app then tap the Allow from this source switch to turn on or off.Note:1. Usersare responsible for ll charges from specific apps i itis necessary.2. Manufacturers/sellers are not responsible for apps that are incompatible with the device3. In some cases, there may be no icon in the App Panel after an app s installed. Possiblereasons may be thatthis app is not compatible with your OS or the downloaded ile s broken one so you may need to downloada full version. Ifyouinstall and use an OS other than the one provided by the manufacturer,itmay cause your device to malfunction, therefore, your device will o longer be covered by the warranty in this condition.CONNECTING TO A Wifi NETWORKThe Notification bar displays icons thatindicate your tablet’ s ifi statusNotification that an open Wifi networkisin range.Connected to a Wifi network (waves indicate connection strength).[noicon] There are no Wifi networks in range, or the Wifi radio i off1. Turningon Wifia. Swipe up on the screen and tap Settings.b. Tap Network & nternet, and then Wific . Turn on Use Wif.Your device will automatically search for available Wifi networks.Note: Ifa network that you’ve connected to before s available, the tablet connecttoit. Ifthe network you want isn’tlisted, butis nearby, wait or the lst to refresh. Or, tap Add network, enter the network name (SS1D) and security details, andtap Save.2. Connecting to WifiTap the Wifi network you would like to connectto.If the network s open, the tablet will prompt you to confirm the connection to the network. Tap “CONNECT” to confirm. Ifthe network secured (as indicated by a Lock icon), the tablet will promptyou to entera password or other credentials. Enter the network password using the onscreen keyboard, and tap “CONNECT. Youwill see “Connected” below your selected Wifinetwork as well asa Wifiicon i the Status Bar indicating that you are connected.INTERNET NAVIGATINGBefore using your browser, make sure Wifi or mobile data s turned on.Setting BrowserYou can use the pre-installed browser or download others you prefer. Tap more detailed settings.NavigatingTap the browser icon to open your browser. You can access a website quickly by entering the URL using the onscreen keyboard. Websites are optimized for viewing, onyour actual devices.Bookmarks1. Tap on any web page to add a bookmark. You can then tap ” Edit” to save or rename the website.2. Atthetop ight, tap ” § * – “Bookmarks” to see alist of your bookmarks. You can manage your bookmarks. CookiesYou can clear cookies from your device at any time. On a webpage, tap ‘ § “Settings” – “Privacy &security” –“Clear browsing data”.CONNECTING TO A BLUETOOTH DEVICETurning Bluetooth on1. Go to Settings.2. Tap “Connected devices” – “Connection preferences” – “Bluetooth” and tap theslider to turnit on. You will seethe BT icon in the Status Bar.Pairing a Bluetooth Device1. Swipe down from the top of the screen.2. Tapand hold the Bluetoothicon.3. Tap “Pair new device’ Itwill automatically scan and you will see a st of available devices. Ifthe deviceyouwanttopair with sn’tin the list, ensure that the other deviceis in Paring Mode and set to be discoverable.4. Tapthe name of the Bluetooth device you want to pair with.5. Tap “PAIR”. On the other device, accept the pairing if prompted.Device ResetYoumay reset your tablet when necessary. For example, you can choose to reset your tabletif you forgot ts password or PIN. Resetting your tablet willclear allinfo in your tabletand restore it to factory default settings. Warning: If you perform a Hard Reset, al data from your tablet, includingyour account configuration, apps, music, pictures, and files, will be deleted. Pleaseremembertoback up anyimportant data before performing a Hard Reset.OPTIONAL CONNECTIOConnecting to a ComputerConnect the tablet to a computer to transfer files.1. Connect your tablet to the computer. Connect the tablet to your computer’ s USB port after plugging theincluded USB cable into its Type-C port.2. Change the USB computer connection Swipe down the notification panel and tap “Charging this device viaUSB” for more options.SPECIFICATIONSCPU Octa-coreRAM4GBROM128GBDisplay10.61″ IPS Capacitive Touchscreen Wifi Networking WIFI 802.11ac/b/g/n/a(2.4+5G) Audio Output0 3.5mm CTIA headphone jackPC Interface USB Type-C PortAdditional Features Built-in microphone and 2X1W speakers, Front camera 8MP and Rear ca mera 13MPBluetooth BTS.OOperating System AndroidTNPower Rechargeable Li-poly battery with USB Type-C Power Ada pter(5V/2A) Playback Time(hours)15 days of standby time, 1080P playback, 5 hours of video playbackTROUBLESHOOTING1. Device doesn’ t power on.• Reboot your device after charging it for 30 minutes.• Shortly press your power button to check if it lights up in case your device is in sleep mode.• Press the power button for 20 seconds.• Start a hard reset by pressing the reset button with a pin.2. Device doesn’ t take charge.• Charge your tablet for at least 30 minutes before restarting.• Check that the cable is securely connected to the charger and to your tablet.• Try another outlet or compatible charger.3. Error message appears during operation.• If an error message appears, uninstall the app and then reinstall it. Or update the app to the latest version.• Reset it to factory settings.4. Device can’ t be detected by a PC.• Make sure your device is in “ON” status.• Try with another USB cable.• Connect your device to a different port on your PC.5. Device can’ t be connected with Wifi.• Make sure your turn Wifi to “ON” status.• Unplug the Wifi router, wait for 2 minutes and plug to connect again.• Make sure you input the correct password by selecting “show password” when you input it.• Check and make sure there is no filtering setting or device connection limit in your router setting.• Forget original Wifi connection, reset the Wifi router, and connect again.6. Insufficient storage available.• Delete applications you don’t use often to spare some space.• Clean caches in your device regularly. Tap “Settings” —) “Apps & notifications” to see all apps. Tap on an app, then tap “Storage & cache” to clear cache or data.• Install a third-party system cleaner.• Factory reset your tablet to clear all data.• Insert a memory card to expand its memory.CONTACT USFor any inquiries about aigo products, please feel free to contact us. We will respond within 24 hours. Tel: Email: Web: FCC StatementThis equipment has been tested and found to comply with the limits for a Class B digital device, pursuant to part 15 of the FCC Rules. These limits are designed to provide reasonable protection against harmful interference in a residential installation. This equipment generates, uses and can radiate radio frequency energy and, if not installed and used in accordance with the instructions, may cause harmful interference to radio communications. However, there is no guarantee that interference will not occur in a particular installation. If this equipment does cause harmful interference to radio or television reception, which can be determined by turning the equipment offand on, the user is encouraged to try to correct the interference by one or more of the following measures: Reorient or relocate the receiving antennaIncrease the separation between the equipment and receiver.Connect the equipment into an outlet on a circuit different from that to which the receiver is connected.Consult the dealer or an experienced radio/TV technician for help.Caution:Any changes or modifications to this device not explicitly approved by manufacturer could void your authority to operate this equipment. This device complies with part 15 of the FCC Rules. Operation is subject to the following two conditions: (1) This device may not cause harmful interference, and (2) this device must accept any interference received, including interference that may cause undesired operation. Specific Absorption Rate (SAR) information: This tablet PC meets the government’s requirements for exposure to radio waves. The guidelines are based on standards that were developed by independent scientific organizations through periodic and thorough evaluation of scientific studies. The standards include a substantial safety margin designed to assure the safety of all persons regardless of age or health. FCC RF Exposure Information and Statement the SAR limit of USA (FCC) is 1.6 W/kg averaged over one gram of tissue. Device types: tablet PC has also been tested against this SAR limit. This device was tested for typical body-worn operations with the back of the phone kept 0mm from the body. To maintain compliance with FCC RF exposure requirements, use accessories that maintain an 0mm separation distance between the user’s body and the back of the phone. The use of belt clips, holsters and similar accessories should not contain metallic components in its assembly. The use of accessories that do not satisfy these requirements may not comply with FCC RF exposure requirements, and should be avoided.Documents / Resourcesaigo A16 Tablet PC [pdf] User Manual2BB5W-A16, 2BB5WA16, A16, A16 Tablet PC, Tablet PC, PCManuals+,。
- 1、下载文档前请自行甄别文档内容的完整性,平台不提供额外的编辑、内容补充、找答案等附加服务。
- 2、"仅部分预览"的文档,不可在线预览部分如存在完整性等问题,可反馈申请退款(可完整预览的文档不适用该条件!)。
- 3、如文档侵犯您的权益,请联系客服反馈,我们会尽快为您处理(人工客服工作时间:9:00-18:30)。
Testing and Debugging Your Embedded IntelligenceSummaryApplication NoteAP0166 (v1.0) September 05, 2008This document takes a look at the range of tools available to aide in the debugging ofyour embedded intelligence – the FPGA design itself and any embedded programcode required by processors within that design.Debugging is the act of testing your hardware design and any embedded software (running on 'soft' processors therein), to obtain the desired (correct) performance and functionality. Debugging is an important element of the overall design strategy, and effective debugging can save a lot of time and money when it comes time to deploy your end design in the field.This document takes a look at the various debugging tools available within Altium Designer.Virtual InstrumentationIn Altium Designer, debugging of hardware is provided courtesy of 'virtual' instrument – components which are 'wired' into the actual FPGA design but which, on programming the physical device, offer software-based controls for interrogation and control of nodes within the design. Imagine being able to walk around inside the physical FPGA device, armed with your favorite test instruments, and you'll have some idea of what these instruments can offer as part of a 'live' debugging environment.Virtual instruments are placed from the \Library\Fpga\FPGA Instruments.IntLib library.How do I use instruments in my FPGA design? – this video looks at the use of embedded instruments in an FPGA design. Accessing Virtual Instruments at RuntimeBefore looking at the instruments themselves, it is worth taking the time to see how instruments are accessed from within Altium Designer and the underlying communications scheme that makes this possible.Communications from the Altium Designer software environment to embedded processors and virtual instruments in an FPGA design, is carried out over a JTAG communications link. This is referred to on the Desktop NanoBoard NB2DSK01 as the Soft JTAG (or Nexus) chain. Within Altium Designer, such devices included in the chain are presented in the Devices view (View » Devices View ) as part of the Soft Devices chain (the bottom-most chain in the view), as shown in Figure 1.Figure 1. Example virtual instruments appearing in the Soft Devices chain of the Devices view.Note: The Soft Devices chain only becomes populated with the Nexus-enabled devices for a design, once that design has been programmed into the target device.Testing and Debugging Your Embedded IntelligenceThe interface for a virtual instrument is accessed by double-clicking on the corresponding icon for it. Doing so will give access toits associated instrument panel (Figure 2). Use the panel to interactively debug your design as required.Figure 2. Example of a virtual instrument's associated panel, which provides the necessary controls to actively debug your design.For information on working in the Devices view, refer to the document AP0103 Processing the Captured FPGA Design . How do I build an FPGA design? – this video looks at processing a design from within the Devices view and running it onsome target hardware.Enabling the Soft Devices JTAG ChainThe Soft JTAG chain signals (NEXUS_TMS , NEXUS_TCK , NEXUS_TDI and NEXUS_TDO )are derived in the NB2DSK01's NanoTalk Controller (Xilinx Spartan-3). As part of thecommunications chain, these signals are wired to four pins of the daughter board FPGA.To interface to these pins, you need to place the NEXUS_JTAG_CONNECTOR designinterface component (Figure 3). This can be found in the FPGA NB2DSK01 Port-Plugin integrated library (\Library\Fpga\FPGA NB2DSK01 Port-Plugin.IntLib).This component 'brings' the Soft JTAG chain into the design. In order to wire all relevant Nexus-enableddevices (processors, virtual instruments) into this chain, you need to also place a NEXUS_JTAG_PORTcomponent (Figure 4), and connect this directly to the NEXUS_JTAG_CONNECTOR (Figure 5). Thiscomponent can be found in the FPGA Generic integrated library (\Library\Fpga\FPGAGeneric.IntLib ).Figure 3. Nexus JTAG Connector. The presence of the NEXUS_JTAG_PORT component instructs the software to wire all components thatpossess the parameter NEXUS_JTAG_DEVICE=True into the Soft JTAG chain. Figure 4. NexusJTAG Port.Figure 5. Connecting JTAG devices into the Soft JTAG chain.For information on the JTAG communications, refer to the document AR0130 PC to NanoBoard Communications .How do I hook up the JTAG chains in my target system? – this video looks at how the JTAG communications protocol is used with FPGAs and how you can take advantage of Altium Designer's LiveDesign debugging features in a target systemon your production or third party development board.Testing and Debugging Your Embedded IntelligenceCustom InstrumentThe Custom Instrument component is a fully-customizable 'virtual'instrument with which to monitor and control signals within an FPGAdesign.As part of the instrument's configuration you are able to create your ownGUI – the interface that is seen once the design is programmed into thetarget device and the instrument is accessed. A palette of standardcomponents and instrument controls enable you to quickly construct theinstrument panel, while various properties associated with a control allowyou to make fine-tuning adjustments. Figure 6. Example Custom Instrument.Defined IO signals, wired to the instrument on the schematic, can be hooked up directly to the various controls in your custom GUI, or you can write your own DelphiScript code to process IO as required. Scripts can be fired whenever the instrument polls, and in relation to specified events.One of the key features of this particular virtual instrument is that its configuration can be downloaded with the FPGA design and stored within the target physical device (in Block RAM). This allows for interaction with the design, through use of the Custom Instrument, directly in the field – particularly attractive to Field Service Engineers!Configuration of the instrument is carried out using the Custom Instrument Configurationdialog (Figure 7).Figure 7. Customize the look and feel of your Custom Instrument through the various tabs of its associated configuration dialog. The Signals tab allows you to define base instrument options, including specification of the configuration file and how it is retrieved by Altium Designer. TheDesign tab provides the canvas with which to create the customized GUI used to interact with the instrument at run-time. The Code tab offers an area in which to write any underlying script code used, for example, in the processing of instrument IO.Testing and Debugging Your Embedded IntelligenceFigure 8 illustrates an example of the run-time panel for this instrument, accessed by double-clicking on the icon for the instrument, in the Soft Devices chain of the Devices view.Figure 8. Example instrument panel for the Custom Instrument.Features at-a-glance•Fully customizable with configuration information stored in a separate .Instrument file•Supports any number of input and output signals-Customizable naming of signals-Each signal can be configured to any number of bits-Ability to set initial value for each output signal-Defined signals can be reordered, graphically, as required•Customizable title for the instrument's panel•Ability to use customized bitmap to represent instrument in the Devices view•Configuration information can be retrieved from one of two locations:-From Project: Configuration information retrieved from .Instrument file. FPGA project must be open-From FPGA: Configuration information is downloaded with the design to the physical device, and stored in Block RAM. It is retrieved directly from here and the project need not be open•Design form for creating instrument GUI with three dedicated panels:-Palette panel: offering a range of standard scripting components and instrument-specific controls-Properties panel: for fine-tuning the presentation and/or functionality of form objects-Events panel: for hooking-up script procedures or functions to form objects•Supports use of scripting (DelphiScript), for example to manipulate signal IO to a greater degree. Script can be written: -Within a dedicated coding tab as part of the instrument's configuration dialog-Within a code-aware editor inside Altium Designer•Ability to hook signal IO to required instrument controls either directly or through use of scripting•OnReadWrite event for instrument panel form hard coded to 'fire' each time the instrument polls, allowing the synchronous calling of code which can process signal values at each poll point•Provision of special global function SignalManager, which provides access to signals within a given Custom Instrument.This function allows you to easily get and set values for signals as part of your script functions.•Can be accessed 'in the field' using the Viewer Edition of Altium DesignerFor more detailed information on this instrument, refer to the document TR0176 Custom Instrument Reference.For a tutorial that looks at using the Custom Instrument in an FPGA design, involving monitoring of input signals directly and control of output signals using scripting, refer to the document TU0135 Adding Custom Instrumentation to an FPGA Design.Testing and Debugging Your Embedded IntelligenceLogic AnalyzerThe configurable Logic Analyzer instrument is capable of supporting 8-, 16-, 32- or 64-bit capture. The instrument can be configured to use predefinedinternal storage memories for captured data, or to connect to an externalblock of RAM. In each case, the required memory size is identified for you,based on the number of samples you specify to capture.Incorporating an internal multiplexer, the instrument can be configured tomonitor any number of nets and buses – fed into the device as signal sets– with one set of signals nominated to be captured while the circuit is undertest.Up to 16 signal sets are supported and the capture width is automaticallydetermined and adjusted, based on the requirements of all defined signalsets. Indication of remaining width for a given set is provided, allowing youto quickly see how many channels you have left to 'play' with. As an addedprecaution, you are prevented from exceeding the maximum capture widthfor a set.Note: Connection of net and bus signals to the Logic Analyzer can besimplified through the use of Instrument Probe Directives. For moreinformation, see the section Instrument Probe Directive , later in thisdocument. Figure 9. Example Logic Analyzer.Triggering of the instrument can be external (hardware triggering) or internal (software triggering based on values of incoming signals). You can define any trigger pattern on any of the available sets of signals – allowing you to trigger off one set and capture data for the same or different set.The instrument also offers the ability to interpret the data being captured as the code under execution, using data disassembly.Figure 10. The LAX panel – 'control central' for software triggering of the instrument and tabular analysis of the captured data.Testing and Debugging Your Embedded IntelligenceThe signals within a signal set can be associated with a specific wave style, which will be used when displaying the generated waveforms in the Digital Waveform Viewer. The styles themselves can be defined as required, from the Wave – General page of the Preferences dialog (DXP » Preferences). Assignment of styles to signals is carried as part of the instrument's configuration, using the Configure (Logic Analyzer) dialog, an example of which is shown in Figure 11.Figure 11. Assignable signal styles – putting you in the driver's seat for captured digital waveform display!Figure 12 illustrates an example of the run-time panel for this instrument, accessed by double-clicking on the icon for the instrument, in the Soft Devices chain of the Devices view.Testing and Debugging Your Embedded IntelligenceFigure 12. Instrument panel for the configurable Logic Analyzer.Features at-a-glance•Ability to define up to 16 signal sets for monitoring•Supports 8-, 16-, 32- or 64-bit capture width – how many signal channels each defined signal set can contain – automatically selected based on the requirements of all defined signal sets•Ability to store captured samples in internal or external memory, with an indication of the memory size required -Internal Memory: Choose from 1K, 2K or 4K samples-External Memory: Choose from 16 samples all the way up to 1024K samples (4 to 20 bit address bus respectively) •Indication of used width for a signal set and prevention to exceed the maximum 64-bit capture width•Ability to assign wave styles to signals (for display in the Digital Waveform Viewer)•Ability to trigger off one signal set and capture data from same or different signal set•Ability to use each configuration in split mode•External (Hardware) or internal (Software) triggering•Ability to capture data at rate of system clock•Ability to keep the instrument 'armed' indefinitely•Ability to disassemble captured data•Analog and digital waveform generation-Support for continuous data capture from within waveform views-Cursor synchronization between waveform views-Pan and zoom synchronization between waveform viewsFor more detailed information on this instrument, refer to the document CR0158 LAX Configurable Logic Analyzer.A number of legacy logic analyzer instruments are also available. For more information, refer to the document CR0103LAX_x Logic Analyzer.How do I setup and use the LAX instrument? – this video looks at how the Logic Analyzer can be used to store and observe signals from within the FPGA.Testing and Debugging Your Embedded IntelligenceDigital I/O ModuleThe configurable Digital I/O instrument provides separated inputs andoutputs, allowing you to monitor and display signal levels, as well as definecontrol signals for use elsewhere in the design.Any number of signals may be added, and any number of bits can beassigned to a single signal. You may also have different numbers of inputand output signals.The instrument also supports a variety of graphical formats in which theFigure 13. Example Digital I/O Module.inputs and outputs can be displayed.Configuration of the instrument is carried out using the Digital I/O Configuration dialog, an example of which is shown in Figure 14.Figure 14. Configuration dialog for the Digital I/O Module.Figure 15 illustrates an example of the run-time panel for this instrument, accessed by double-clicking on the icon for the instrument, in the Soft Devices chain of the Devices view.Figure 15. Example instrument panel for the configurable Digital IO Module.Testing and Debugging Your Embedded IntelligenceFeatures at-a-glance•Supports any number of input and output signals•Each signal can be configured to any number of bits (typically 8, 16, 32)•Customizable naming of input and output signals•Defined signals can be reordered, graphically, as required•Two-level display of inputs- Hexadecimal value-configurable graphic display – Numeric, LEDs, LED Digits, Bar•Two-level control of outputs-Hexadecimal entry of entire value-Configurable graphic control – Numeric, LEDs, LED Digits, Slider•Ability to set initial value for each output signalFor more detailed information on this instrument, refer to the document CR0179 DIGITAL_IO Configurable Digital IO Module.A number of legacy digital I/O instruments are also available. For more information, refer to the document CR0102 IOB_xDigital IO Module.How do I use the Digital IO instrument? – this video looks at using the Digital IO Module as a set of virtual switches and LEDs in your design.Testing and Debugging Your Embedded IntelligenceCrosspoint Switch ModuleThe Crosspoint Switch instrument facilitates signal switching within an FPGAdesign. It allows you to specify any number of input and output blocks, all ofwhich share a common signal block structure – the external input signalsinvolved – which is definable as part of the instrument's configuration.The interconnection between input and output blocks is completelyconfigurable. Initial connections can be defined as part of design-timeconfiguration, but can be changed on-the-fly at run-time, from the device'sassociated instrument panel. The latter enables you to switch signals withouthaving to resynthesize and download the entire design to the FPGA.Configuration of the instrument is carried out using the Crosspoint SwitchConfiguration dialog, an example of which is shown in Figure 17. Figure 16. Example Crosspoint Switch Module.Figure 17. Configuration dialog for the Crosspoint Switch Module.Figure 18 illustrates an example of the run-time panel for this instrument, accessed by double-clicking on the icon for the instrument, in the Soft Devices chain of the Devices view.Figure 18. Instrument panel for the Crosspoint Switch Module.Features at-a-glance•Supports any number of input and output blocks-Customizable naming of input and output blocks-Defined blocks can be reordered as required•Block structure (the external input signals) defined and shared by all I/O blocks-Customizable naming of block signals-Each signal can be configured to any number of bits (typically 8, 16, 32)-Defined signals in block can be reordered as required•Ability to define initial interconnection of I/O blocks•Ability to change interconnection of I/O blocks at run-time through the instrument panel•Unconnected output blocks will retain the previous value that was output from themFor more detailed information on this instrument, refer to the document CR0182 CROSSPOINT_SWITCH Configurable Signal Switching Module.Terminal ModuleConsole I/O is a common way of debugging processor systems. The Terminal instrumentprovides you with a debug console with which to interact with your system directly. It allowsyou to type text directly in its associated instrument panel, which is then sent directly to theprocessor in your design, to be handled by the embedded software code running therein.Conversely, it allows the display of text sent from that processor.Although classed as one of Altium Designer's virtual instruments, the debug consoleinstrument is really a hybrid – part instrument and part Wishbone-compliant slave peripheral.Whereas other instruments are configured and operated directly from a GUI, the debugconsole instrument requires interaction at the code level, to initialize internal registers and towrite to/read from its internal storage buffers.In terms of functionality as a peripheral, the Terminal instrument is similar to the WB_UART8Serial Communications Port peripheral. Whereas the WB_UART8 facilitates serialcommunication between a processor and a remote device, the Terminal instrument is, inessence, the remote device as well as the facilitator of communications. The processorsimply communicates directly (and serially) with the Terminal instrument. Figure 19. Terminal Module.Figure 20 illustrates an example of the run-time panel for this instrument, accessed by double-clicking on the icon for the instrument, in the Soft Devices chain of the Devices view.Figure 20. Instrument panel for the Terminal Module.Features at-a-glance• Based on, and functionally similar to, the WB_UART8 peripheral• Type and send text to processor directly from instrument panel• Receive text from the processor and display in instrument panel• Full Duplex• Ability to save text to a log file• Ability to copy selected text to the clipboard•Wishbone-compliantFor more detailed information on this instrument, refer to the document CR0180 TERMINAL Debug Console Instrument .Frequency Generator ModuleThe frequency generator instrument takes a reference clock as its input (time-base)and produces output frequencies that are even divisors of this frequency. By wiringthe generator up to have a higher frequency time-base, a greater range of outputfrequencies can be generated, and with greater accuracy.Predefined frequencies can be chosen at the click of a button. You can also choosefrom a range of common Baud Rates. For even greater control, you have the option tospecify your own required frequency – the actual frequency generated in each casewill be displayed directly on the panel. If the required frequency is not an even divisorof the time base frequency, the nearest frequency that is will be used, and the percentage difference also shown.Figure 21. Frequency Generator Module.The option to use a 50/50 duty cycle for the generated output is also provided.Figure 22 illustrates an example of the run-time panel for this instrument, accessed by double-clicking on the icon for the instrument, in the Soft Devices chain of the Devices view.Figure 22. Instrument panel for the Frequency Generator Module.Features at-a-glance•Ability to request common predefined frequencies at the touch of a button-Common frequencies in Hz, kHz and MHz ranges• User-definable frequency requests•Ability to select from a range of common Baud Rate frequencies•Option to set 50/50 Duty cycle•Generated frequency output can be inverted (180 Degree phase shift).For more detailed information on this instrument, refer to the document CR0100 CLKGEN Frequency Generator.How do I use the Signal Generator instrument? – this video looks at how the Frequency Generator Module can be used tocreate a periodic signal at a prescribed frequency.Counter ModuleThe Counter instrument provides a two-channel, three-mode frequency counter. Foreach input signal, the device counts the number of edges – rising or falling – detectedwithin a specified gating period. Depending on the mode of operation selected, eachchannel can display the frequency of the signal, its period, or the total number ofedges counted.Figure 24 illustrates an example of the run-time panel for this instrument, accessed bydouble-clicking on the icon for the instrument, in the Soft Devices chain of theFigure 23. Counter Module.Devices view.Figure 24. Instrument panel for the Counter Module.Features at-a-glance•2-Channel, 3-Mode counter-Frequency Mode (with a range of 0 to (TIMEBASE / 2))-Period Mode (with a resolution of 1 / (TIMEBASE / 2) Seconds)-Event (edge) Counter Mode (able to count up to 9,999,999,999 edges)• Selectable gating period•Ability to count rising or falling edges of incoming signalsFor more detailed information on this instrument, refer to the document CR0101 FRQCNT2 Frequency Counter.How do I use the Frequency Counter instrument? – this video looks at how the Counter Module can be used to capture periodic signals or count events.Additional Hardware Monitoring ToolsIn addition to the range of virtual instrumentation available for use in an FPGA design, there are also tools available to interrogate the activity at the pins of the physical FPGA device, or to probe nets within the design. The following sections take a closer look at these tools.Monitoring the State of Device Pins - LiveOnce the design has been downloaded to the FPGA, the Hard Devices JTAG chain can be used to monitor the state of the FPGA pins, in real-time. This is achieved using the device's associated JTAG Viewer panel (accessible from its instrument panel), set to operate in Live Update mode (Figure 25).Figure 25. Enable the Live Update option in the device's associated JTAG Viewer panel to monitor the state of the FPGA pins in real-time!Where high-density component packaging makes physical probing of device pins impossible, the JTAG Viewer panel facilitates physical design debugging, 'virtual-style'. It uses the JTAG communications standard to interrogate the state of the pins in any JTAG compliant device in your design, not just the FPGAs. It presents the state of each pin, and includes an image of both the schematic symbol and the footprint, helping you to analyze and debug your design.Analyzing Design NetsAs part of its LiveDesign methodology, Altium Designer provides you with the ability to analyze nets in an FPGA design, while it is running on the target physical device. Where a design net is connected directly to a pin of the physical device, you have the ability to monitor the status of that pin – in real-time. By using a virtual instrument, such as a logic analyzer, you can gain valuable operational information about your design.The ability to 'reach in' and interactively analyze design nets can give you the edge needed to finalize development prior to manufacture, leading to shorter time-to-market and making a good product great.To aid in this analysis, Altium Designer provides the Probe and Instrument Probe directives.Probe DirectiveThe days of being able to attach fly-lead probes physically to the pins ofa chip and analyze states is fast nearing the doors of antiquity. Devices –especially FPGAs – are becoming pin-saturated beasts which, even ifyou could 'see' the pins, they are undoubtedly too finely pitched toaccess externally. So how about monitoring pins from within the design –directly from the schematic sheet? It's a vision made real with LiveDesignand a well-placed Probe directive.Place a Probe directive on any net (wire or bus) in the design thatconnects directly to a pin of the physical FPGA device. Once the designhas been programmed into the device, the state of such a pin can bemonitored, in real-time, directly on the schematic sheet (Figure 26).Figure 26. FPGA pin status monitoring using Probe directives. The key to the pin-state display is the directive's ProbeValueDisplay parameter. In fact you could place a Parameter Set directive instead, andas long as this parameter is defined for it, the result would be the same.For the pin state to be updated in real-time on the schematic, the source FPGA design must be downloaded to the physical FPGA device and the associated JTAG Viewer panel (see previous section) for that device must be open and remain open. Instrument Probe DirectiveProbing device pins from the schematic is great, but what about being able to analyze andpotentially fault-find further back into the design circuitry? No problem. Simply place anInstrument Probe directive, which allows you to monitor any point in a design – not just thestatus of FPGA device pins. Placed on a net object, such as a wire or bus, it instructs thesystem to connect the associated net directly to the input of a monitoring instrument (e.g. alogic analyzer) – without having to explicitly wire that net up through the design hierarchy tothe sheet with the instrument on it. The key element that turns this directive from being a simple probe into a powerful point-monitoring aid, is its possession of the additional InstrumentProbe parameter. Once the directive is placed at the point of interest, it is this parameter that is used to effectively 'link' that point to the monitoring device. Simply enter a meaningful name for the probe point – such as the name of the associated net or the particular signal being monitored – then connect a wire to the required input of the monitoringinstrument and attach a net label to the wire, the name of which is the same name you have defined for the InstrumentProbeparameter (Figure 27).Figure 27. Monitoring select points in a design without excessive wiring overhead.Measurement information obtained through the directive's ProbeValueDisplay parameter is, like the Probe directive, displayed in real-time, over the Hard Devices JTAG chain. In contrast, measurement information obtained through the directive's InstrumentProbe parameter is ONLY displayed after compilation, over the Soft Devices JTAG chain.。