FOIL1
LM10线性磁编码器系统数据表说明书
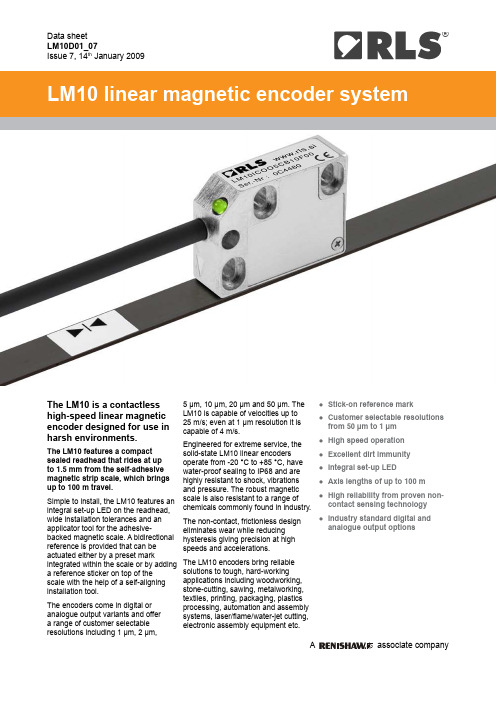
®Data sheet LM10D01_07Issue 7, 14thJanuary 2009The LM10 is a contactless high-speed linear magnetic encoder designed for use in harsh environments.The LM10 features a compact sealed readhead that rides at up to 1.5 mm from the self-adhesive magnetic strip scale, which brings up to 100 m travel.Simple to install, the LM10 features an integral set-up LED on the readhead, wide installation tolerances and an applicator tool for the adhesive-backed magnetic scale. A bidirectional reference is provided that can be actuated either by a preset markintegrated within the scale or by adding a reference sticker on top of thescale with the help of a self-aligninginstallation tool.The encoders come in digital or analogue output variants and offer a range of customer selectable resolutions including 1 µm, 2 µm,5 µm, 10 µm, 20 µm and 50 µm. The LM10 is capable of velocities up to 25 m/s; even at 1 µm resolution it is capable of 4 m/s.Engineered for extreme service, thesolid-state LM10 linear encoders operate from -20 °C to +85 °C, have water-proof sealing to IP68 and are highly resistant to shock, vibrations and pressure. The robust magnetic scale is also resistant to a range of chemicals commonly found in industry.The non-contact, frictionless design eliminates wear while reducinghysteresis giving precision at high speeds and accelerations.The LM10 encoders bring reliablesolutions to tough, hard-working applications including woodworking, stone-cutting, sawing, metalworking, textiles, printing, packaging, plasticsprocessing, automation and assembly systems, laser/flame/water-jet cutting, electronic assembly equipment etc.Stick-on reference mark●Customer selectable resolutions ●from 50 µm to 1 µm High speed operation ●Excellent dirt immunity ●Integral set-up LED ●Axis lengths of up to 100 m ●High reliability from proven non- ●contact sensing technology Industry standard digital and ●analogue output optionsData sheetLM10D01_07Dimensions and tolerances in mm.LM10 dimensionsLM10 installation tolerancesRide height0.1 - 1.5 mm®Maximum measuring length 50 m (100 m special order)Pole length2 mmAvailable resolution for digital outputs 1 µm, 2 µm, 5 µm, 10 µm, 20 µm and 50 µm Sinusoidal period length 2 mmMaximum speedFor analogue voltage and analogue current output: 25 m/s Sensor/magnetic scale gap With periodic or machined reference: 0.1 to 1.5 mm With stick-on reference: 0.5 to 1.5 mm Error band±40 µm at 20 °C Linear expansion coefficient ~ 17 × 10-6/KRepeatability Better than unit of resolution for movement in the same direction Hysteresis*< 3 µm up to 0.2 mm ride height Sub divisional error±3.5 µm for < 0.7 mm ride height (to ensure SDE remains under ±3.5 µm order option 01 that provides alarm and red LED at 0.7 mm ride height)±7.5 µm for 1 mm ride height Cable PUR high flexible cable, drag-chain compatible, double-shielded 8 × 0.05 mm 2; durability: 20 million cycles at 20 mm bend radiusReadhead (1 m cable, no connector) 56.4 g, Magnetic scale (1 m) 60 g, Cover foil (1 m) 3.5 gPower supply4.7 V to 7 V – reverse polarity protected; voltage on readhead Power consumption (without any load)< 30 mA for digital output type < 50 mA for analogue output types Voltage drop over cable 13 mV/m – without load 54 mV/m – with 120 Ω loadOutput signalsDigital – Open Collector NPN, Differential RS422, short circuit protected TemperatureOperating -10 °C to +80 °C (cable under non-dynamic conditions: -20 °C to +85 °C)Storage-40 °C to +85 °CEnvironmental sealing IP68 (according to IEC 60529)EMC ImmunityIEC 61000-6-2 (particularly: ESD: IEC 61000-4-2; EM fields: IEC 61000-4-3; Burst: IEC 61000-4-4; Surge: IEC 61000-4-5; Conducted disturbances: IEC 61000-4-6; Power frequency magnet fields: IEC 61000-4-8; Pulse magnetic fields: IEC 61000-4-9)EMC InterferenceIEC 61000-6-4 (for industrial, scientific and medical equipment: IEC 55011)Vibrations (55 Hz to 2000 Hz)300 m/s 2 (IEC 60068-2-6)Shocks (11 ms)300 m/s 2 (IEC 60068-2-27)LM10 technical specifications* Repeatable, and can be measured and compensated once installedData sheetLM10D01_07A B ZA B ZSquare wave differential line driver to EIA RS422NOTE : Set-up LED in the case of poor signal strenght is flashing red.LM10IC – Digital output signals, RS422Power supply voltage 4.7 V to 7 V – reverse polarity protected; voltage on readhead *Reverse polarity protectionIncremental signals2 square-wave signals A, B and their inverted signals A-, B-Reference signal 1 or more square-wave pulse Z and its inverted pulse Z-Signal levelDifferential line driver to EIA standard RS422:U H ≥ 2.5 V at -I H = 20 mA U L ≤ 0.5 V at I L = 20 mAPermissible loadZ O ≥ 100 Ω between associated outputs I L ≤ 20 mA max. load per output Capacitive load ≤ 1000 pFOutputs are protected against short circuit to 0 V and to +5 VAlarmHigh impedance on output lines A, B, A-, B-Switching time (10 to 90 %)t+, t- < 30 ns (with 1 m cable and recommended input circuit)Cable lengthmax. 100 mTiming diagramComplementary signals not shownRecommended signal terminationRecommended signal terminationSquare wave outputLM10IB – Digital output signals, Open Collector NPNPower supply voltage 5 V to 30 V Powerconsumption 30 mA Output signals A, B, ZReference signal 1 or more square-wave pulses Z Maximum load 20 mA Cablemax. 10 mTiming diagram* Please consider voltage drop over cable.®2 channels V1and V2differential sinusoidals (90° phase shifted)Timing diagramLM10AV – Analogue output signals (1 Vpp)Power supplyvoltage4.7 V to 7 V – reverse polarity protected;voltage on readhead *Reverse polarity protectionIncrementalsignalsAmplitude(with 120 Ω termination)0.6 Vppto 1.2 VppPhase shift90° ± 0.5°Reference signal Amplitude(with 120 Ω termination)0.8 Vppto 1.2 VppPosition45°Width45°Termination ZO= 120 Ω between associated outputsCable length max. 50 m(V1+) - (V1-)(V2+) - (V2-)(V+) - (V-) - 1.2 VppΩ0.6 Vpp- 1.2 Vppwith 120 Ωtermination0 V0 V0 V2 channels I1and I2sinusoidals (90° phase shifted)LM10AC – Analogue micro current output signals (12 µA)Power supplyvoltage4.7 V to 7 V – reverse polarity protected;voltage on readhead *Reverse polarity protectionIncrementalsignalsAmplitude7 µA to 16 µAPhase shift90° ± 0.5°Reference signal Amplitude8 µA to 12 µAPosition45°Width45°Cable length max. 10 mI1I2I0 µA0 µA0 µATiming diagram* Please consider voltage drop over cable.* Please consider voltage drop over cable.Reference markSet-up LEDProgrammingPositive direction3) Every 2 mm. The LM10 readhead should be ordered with this specific mode activated only.After the installation of the magnetic scale (see LM10 Installation guide) the readhead can be easily adjusted on the machine using the set-up LED indicator.Digital output signals – A leads BAnalogue output signals (1 V pp ) – V 1 leads V 2Analogue output signals (12 µA) – I 1 leads I 2A, B, A-, B- outputs become high impedance programming interface.NOTE : IB output type: LED flashes red.LM10 IC 010 CA 10 F 00LM10 readhead part numberingMinimum edge separation For AV and AC output types A - N/AFor IB and IC output types A - 0.12 µs (8.3 MHz)*B - 0.5 µs (2 MHz)C - 1 µs (1 MHz)D - 2 µs (0.5 MHz)E - 4 µs (0.25 MHz)ReferenceA - With referenceB - No referenceC - Periodic as per scale pitch (2 mm)Cable length10 - 1.0 m (standard)Connector option A - 9 pin D type plugB - 15 pin D type socket (for IC output type)D - 15 pin D type plug (for IC output type)L - 15 pin D type plug (for AV output type)F - Flying lead (no connector)Special requirements00 - No special requirements (standard)01 - 0.7 mm ride height alarmOutput typeIB - Incremental, Open Collector NPN; 5 V - 30 V IC - Incremental, RS422; 5 V AV - Analogue voltage, 1 V pp ; 5 V AC - Analogue micro current, 12 µA; 5 VResolution000 - for AV and AC output typesFor IB and IC output types 001 - 1 µm 002 - 2 µm 005 - 5 µm 010 - 10 µm 020 - 20 µm 050 - 50 µmPRG - Programmable from 1 µm to 50 µm (preset to 1 µm)LM10 system ReadheadScaleReadhead part number eg LM10IC010CA10F00Magnetic scale part number eg MS10B1000B0032RLS d.o.o. reserves the right to change specifications without notice.* Default for PRG option.+=CF10 1000MS10 B 1000 B 0032Positive counting30 mm10 mmMachined reference mark (Ri)Position of reference markMin. distance of Ri from left edgeMin. distance of Ri from rightedgeTape length = measuring length + 25 mmMeasuring lengthMagnetic scale part numberingAccessories part numberingCover foilFoil lengthxxxx - Where xxxx equals foil length in cmStick-on reference mark LM10SRM00Applicator tool for stick-on reference markLM10ARM00Applicator tool for magnetic scale and cover foil LM10ASC00End clamp kit (2 clamps + 2 screws)LM10ECL00Precision class B - 40 µm/mTape lengthxxxx - Where xxxx equals tape length in cmCover foilA - No cover foilB - Cover foil supplied (separately - 5 cm longer than tape)C - No cover foil, ends prepared for end clampingPosition of reference mark 0000 - No reference markxxxx - Where xxxx equals position of machined referencemark in cmNOTE: Reference mark position will be within ±1 cm fromrequested position.NOTE: tape length = measuring length + 25 mmRLS d.o.o. has made considerable effort to ensure the content of this document is correct at the date of publication but makes no warranties orrepresentations regarding the content. RLS d.o.o. excludes liability, howsoever arising, for any inaccuracies in this document. © 2009 RLS d.o.o.RLS merilna tehnika d.o.o.Cesta II. grupe odredov 25SI-1261 Ljubljana - Dobrunje SloveniaT +386 1 5272100F +386 1 5272129E ***********www.rls.siHead officeAustraliaT +61 3 9521 0922E **********************AustriaT +43 2236 379790E ********************BrazilT +55 11 4195 2866E *******************CanadaT +1 905 828 0104E *******************The People’s Republic of China T +86 10 8448 5306E ********************Czech Republic T +420 5 4821 6553E ******************FranceT +33 1 64 61 84 84E *******************GermanyT +49 7127 9810E ********************Hong KongT +852 2753 0638E *********************HungaryT +36 23 502 183E ********************IndiaT +91 20 6674 6751E ******************IsraelT +972 4 953 6595E *******************ItalyT +39 011 966 10 52E ******************JapanT +81 3 5366 5316E ******************The Netherlands T +31 76 543 11 00E ********************PolandT +48 22 577 11 80E *******************RussiaT +7 495 231 1677E *******************SingaporeT +65 6897 5466E **********************SloveniaT +386 1 52 72 100E ***********South KoreaT +82 2 2108 2830E ***********************SpainT +34 93 663 34 20E ******************SwedenT +46 8 584 90 880E *******************SwitzerlandT +41 55 415 50 60E ************************TaiwanT +886 4 2473 3177E *******************UKT +44 1453 524524E ***************USAT +1 847 286 9953E ****************For all other countries Please contact RLS’ head officeT +386 1 52 72 100E ***********IssueDatePageCorrections made0229.11.2007-Minor text errors corrected, Corrected Maximum speed table data on page 330.11.20072Changed Pitch and Yaw description and image layout 15. 1. 20083, 4, 5Minor text errors corrected 0328. 2. 20081, 3, 7Removed the 100 µm option2Added the Reference mark detection side symbol 5 New reference mark images8Added the magnetic scale dimensions image 04 6. 6. 20082, 5New installation drawing-Reference mark installation moved to LM10 Installation guide 4, 6Analogue output signal specifications added6IB output type removed, AC output type and connector option L added 0525. 11. 20084, 7, 8IB output type, new magnetic scale diagram and end clamping option added 06 5. 12. 20083Hysteresis data added 0714. 1. 2009-New layoutDocument issues。
MIL-S-13949H

MILITARY
SPECIFICATION BOARD FOR
SHEET, PRINTED UIRING GENERAL SPECIFICATION
This specification is ments and Agencies 1. sCOPE
approved of the
for use by all Department of
may b Laboratory
i
[ I I
AftSC WA DISTRIBUTION
FSC 5998 STATEMENT A. Approved f or pubL ic release; distribution is unlimited.
Downloaded from on 2012-09-06T8:04:33.
4
1.2.7.1.2 thickness material .@O ind
The specified nomina( base aeteriaL Base material thickness (nominal) (see fiuure 1). shall be identified by a fixed field of four d i g i ts that indicate the thickness of the base For ex~te, 0300 represents a noainal base mterial thickness in ten-t housandths of ●n inch. (0.76 m). The lrninate thickneaa does -t inchx ie the thickness of any aetal cladding.
安德里茨压滤机中文介绍

1990-1998 1987 1852
通过下列国内外公司收购,公司得到稳定发展 :
Sprout-Bauer, Kone Wood, Jesma-Matador and Sundwig AGIV 收购安德里茨大部分股份
由 Josef K? r?si 建立一家铸造厂和机械厂
压滤机
超过 150 年的板框压滤机综合制造经验
拥有 NETZSCH 和 R&B 两大品牌后 ,安德里茨可以给用户提供 最广泛的工艺处理经验和专业的压滤机选择
Company
Foil No. 5
过滤原理
P max
过滤压力
amb
max: 最大过滤压力 amb: 外界环境压力 力
泥浆
滤液
滤饼
Foil No. 6
该类型压滤机的滤室用聚丙烯滤板和 框架联合构成。
这样产生了 5~40mm 的滤室,滤室大 小由框架的厚度决定。
板框式压滤机适用于预涂助滤剂的过 滤,这种过滤在饮料工业中,用作纯 净过滤。最大工作压力可达 6 bar.
洗涤液
滤饼 洗涤水
压滤机中滤饼的洗涤
Foil No. 11
压滤机类型
厢式压滤机
厢式压滤机在很多不同的应用中性能 可靠,坚固耐用。厢式滤板的滤室厚 度为 15 –50 mm 。厢式板的标准材 料是聚丙烯。 工作压力 : 6, 15 和 60 bar.
性的隔膜被固定在该支撑上。
隔膜材
料包括聚丙烯、合成橡胶(例
如 NBR, EPDM ) 或 热 缩 性 合 成
橡胶 ( TPE )。隔膜是不渗透的,完
成过滤工序后,用以挤压滤室内的滤
铜箔专业英语

1.铜箔 copper foil2.电解铜箔 electrodeposited copper foil(ED copper foil)3.压延铜箔 rolled copper foil4.双面处理铜箔 double treated copper foil5.高温高延伸性铜箔 high temperature elongation electrodeposited copper foil 6.低轮廓铜箔 low profile copper foil,(简称LP)7.涂树脂铜箔 resin coated copper foil(简称RCC)8.涂胶铜箔adhesive coated copper foil(简称ACC)9.锂离子蓄电池要铜箔 copper foil for lithium ion battery10.极薄铜箔 ultra thin copper foil11.箔种类 foil type12.箔型号 foil grade13.原箔raw copper foil14.表面处理 surface treatment15.粗化层处理 roughening treatment16.障壁层处理(barrier treatment)17.黑化处理 black roughening treatment18.黄化处理 yellow roughening treatment19.防锈处理anti-tarnish20.粗糙面 matte side21.光面 shiny side22.处理面 treated side23.裁剪 slitting24.切断(cutting)25.阴极cathode26.阳极 anode27.电流密度 current density28.电解槽electro forming cell29.尺寸稳定的阳极 dimensional stable anode (DSA)30.抗拉强度 tensile strength31.延伸率 elongation33.剥离强度 peel strength34.基板材料 base material35.层压板 laminate36.覆铜箔层压板 copper clad laminate (CCL)37.单面覆铜箔层压板 single- sided copper clad laminate38.双面覆铜箔层压板 copper clad laminate39.内层芯材 core material40.半固化片(预浸材料)prepreg (PP)41.预浸粘结片 preimpregnated bonding sheet42.酚醛纸基覆铜板 phenolic cellulose paper copper clad laminate43.环氧玻纤布基覆铜板 epoxide woven glass fabric copper clad laminate 44.复合基覆铜板 composite copper clad laminate45.薄型覆铜板thin copper clad laminate46.超薄型覆铜板 ultra thin copper clad laminate47.印制电路板 printed circuit board (PCB)。
Effect of cerium addition on microstructure and texture of aluminum foil for electrolytic capaci

JOURNAL OF RARE EARTHS,Vol.28,No.1,Feb.2010,p.134F j y I M I S &T y j ()I M T y R &D j W NG y (f 6@63)DOI 6S ()666Effect of cerium addition on microstr ucture and texture of aluminum foil for electr olytic capacitor sWANG Haiy an (王海燕)1,2,L I Wenx ue (李文学)1,REN Hu iping(任慧平)1,HUANG L iy in g (黄丽颖)1,WAN G Xia ngy ang(王向阳)1(1.School of Material and Metall urgy Engineering,Inner Mongolia University of Science and Technology,Baotou 014010,China;2School of Materials S cience and En-gineering,University of Science and Technology B eijing,Beijing 100083,China)Received 23October 2008;revised 27August 2009Abstract:Anode foil of aluminum electrolytic capacitor,which requires large surface area for high capacitance,were prepared by rolling,an-nealing and electrochemical etching.Effects of cerium addition on the capacitance of aluminum electrolytic capacitors were investigated.Mi-crostructure of the aluminum foil surface was observed by optical microscopy (OM)and scanning electron microscopy (SEM).Electron back scattered diffraction (EBSD)was also employed to reveal texture evolvement of cold-rolled aluminum foil after annealed.The results showed that addition of cerium contributed to higher <100>texture and higher etch pit density as well.Moreover,the distribution of etch tunnels was more uniformcompared with that without cerium addition.Perfect specificsurface area was obtained with 0.0074%addition of cerium.Keywords:electrolytic capacitor;aluminum foil;rare earthsAluminum electrolytic capacitors are widely used in all types of electronic equipments.High voltage electrolytic ca-pacitors consist of an electrolyte put on an anode made from a 40–100μm thin high-purity aluminum foil with an oxide layer serving as dielectric [1].The capacitance of dielectrics depends on the dielectric constant,the thickness,and the surface area.Among those factors,especially for aluminum electrolytic capacitors,the enlargement of the surface area is most effective from the practical viewpoint because of the trend toward capacitor size miniaturization [2,3].The effective surface can be greatly increased through an etching process that forms narrow channels along the crystallographic <001>directions into the foils.Thus,with regard to the cube-tex-ture in the aluminum foils for electrolytic capacitors,produc-tion has to be optimized so as to provide maximum number of cube-nuclei as well as good growth prospect of the cube-orientation [1,4].A strongly textured material consisting of grains with <001>direction parallel to the sheet normal is favorable.In practical application this is achieved by pro-ducing sheets with a strong cube-texture {001}<100>.To increase the surface area,investigation of pit formation seems very important.Many studies have discussed the pits using high-purity aluminum foils during DC etching in HCl solutions,including the shape,morphology of pitting corro-sion,the tunnel pit growth and the effect of impurities on etching behavior [5].In addition,since the thickness of these foils is only 100–110μm,the tunnel length must be con-trolled to less than 50μm,in order to form a non-piercing layer after etching on double surfaces of Al foil [6].Thus,it is necessary to study the principle of tunnel growth to controltunnel length of pits and maintain a non-piercing layer.It has been recognized that the solution composition in-duces certain mechanical,physical and chemical changes,which can lead to activation of chemical and electrochemical reactions,thus result in accelerated material removal and corrosion [7].In general,hydrochloric acid is used for the etching solution,but the size and distribution of etch pits are not uniform with low density as a result of high corrosive-ness.However,effect of solution composition,especially for rare earth element on pitting corrosion,has not been exten-sively or systematically studied,it can be expected that addi-tion of rare earth during electrochemical etching of alumi-num may induce optimum etch structure,and produces high surface of aluminum foil.Therefore,to increase the specific internal area by reducing the rate of dissolution concentrated on local area and producing dense etch pits,studies of rare earth addition was carried out in this work.1ExperimentalHigh-purity (>99.9972%)aluminum foils with different cerium additions of 0.006wt.%,0.0074wt.%,and 0.012wt.%were used.The impurities in the aluminum are as follows (wt.%):Fe 0.00071,Si 0.00070,Cu 0.00125,Zn 0.00014,and Ti 0.00005.The thickness of aluminum ingot was 18mm,after homogenized treatment,reheating,hot rolling and reversibly cold rolling with a thickness reduction of as much as 98%to a final thickness of 0.11mm.Finally,all speci-mens were isothermally annealed for various times in salt bath furnace.For DC electrolytic etching test,specimensound at ion it em:P ro e ct supported b the nne r ongolia mporta nt cie nc e e chnolog Pro ec t 20071911a nd nner ongolia e chnolog ese arch evelopment Pro ec tCorre sponding a uthor :A H ai an E-ma il:w ind :10.101/1002-07210900-1WANG Haiyan et al.,Effect of cerium addition on microstructure and texture of aluminum foil for electrolytic capacitors 135were cut into 10mm ×55mm,and exposed with an area of 1cm 2to the etching solution.The rest of the specimen was masked with polyester tape.All the specimens were pre-treated in HCl+H 2SO 4(3:1)solution and then rinsed with deionized water before electrolytic etching test.Surface morphology of the recrystallized foils and etch tunnels were observed by means of optical microscopy and scanning electron microscopy (SEM).The evolution of cube-texture during isothermal annealing of the cold rolled foils was tracked by crystallographic texture using electron back scattered diffraction (EBSD)micro texture analysis [8].2Results and discussionFig.1(a –d)show the shape and distribution of the etch pit formed in the solutions with cerium additions of 0wt.%,0.006wt.%,0.0074wt.%,and 0.012wt.%respectively.It is found that there are noticeable differences in the morpholo-gies of etch pits,depending on the additive.The intensity of the cube-orientation {001}<100>changed with the increas-ing of cerium content.As shown in Fig.1(a),when cerium is not applied,about 20%of the tunnels observed at 15μm become alive in the process of tunnel growth,while more tunnels are observed with cerium addition and the survival rate increases in Fig.1(b),(c)and (d).Compared with those with additives,the density of etch pits is low in pure alumi-num foil.The length,widths and depths of individual pits weremeasured for each specimen.As shown in Fig.1,under the conditions without additive and with 0.006wt.%Ce,0.0074wt.%Ce,and 0.012wt.%Ce,the density of etch pit is 0.9×105,3.2×105,4.3×105and 6.1×105pits/cm 2,and the av-erage size is 14.0,12.2,9.0and 8.6μm,respectively.The number of etch pits generated in the etching solutions with rare earth additives is about twice as much as that formed without additive as shown in Fig.1(a).This system is typical of the Al-RE (rare earth)series.Ce-rium exists as stable intermetallic compounds in aluminum,and with a negative enthalpy of mixing in the liquid phase [9].There are some kinds of micro impurity,such as Fe,Si,Mn in aluminum,Ce will form compound of CeFe 2Al 10,CeSi 2A13,CeMn 4Al 8,Ce 2Mn 7Al 10,(CeMg)Al 2,etc.[10]These com-pounds can purify the matrix and eliminate the obstruction of impurity,especially the effect of Fe on nucleation and growth of cube orientation grains during annealing process,and thus increase the cube orientation of aluminum foil,which agrees with the etch pits measurement shown in Fig.1.Fig.2shows the texture evolution of samples with differ-ent rare earth contents cold-rolled and annealed at 530°C for 600s.In Fig.2(a),some minor intensities of cube-orienta-tion {001}<100>are observed.By contrast,with cerium addition,the texture has changed in Fig.2(b).The ODF (ΔΦ=5°)is characterized by very sharp cube-orientation dominating over the rolled texture,for the aluminum foil with 0.0074wt.%pare to the Fig.2(b),the 0.019wt.%Ce addition showed weaker cube-orientationtextureFig.1Recrystallized microstructureof aluminumfoil without Ce (a),with 0.006wt.%Ce (b),with 0.0074wt.%Ce(c)and with 0.012wt.%Ce(d)F T x f f 53f 6(),%()%()ig.2e tureevolution o the samples a terannealed at 0o C or 00s without Ce a with 0.0074wt.Ce b and with 0.012wt.Ce c136JOURNAL OF RARE EARTHS,Vol.28,No.1,Feb.2010(Fig.2(c)).To sum up,annealed samples with cerium addi-tion have higher intensity of cube-orientation {001}<100>and the cube texture reaches the maximum with 0.0074wt.%Ce.With further addition of Ce,cube texture density weak-ens.In order to develop greater understanding of texture evolvement,{111}pole figures,determined from EBSP,for the above specimens with different rare earth contents cold-rolled and annealed at 530°C,are shown in Fig.3,where separate measurements were made on small and large grains.The sample of cold rolled and annealed high purity alu-minum had a random texture with few grains exhibiting cube,S and Cu orientations (see Fig.3(a)),while addition of 0.0074wt.%cerium resulted in sharp cube texture,i.e.,more than 90%{100}<001>orientations with little other texture component are observed in Fig.3(b).With more Ce addi-tions,Fig.3(c)indicates that the orientations are similar to those of the grains shown in Fig.3(b),i.e.,cube texture with minor other texture components.However,the cube texture is less sharp,the contour line tend to sparse,with other ori-entations starting to be presented.It is known that addition of rare earth can refine crys-tal [11,12],and induce boundary corrosion,since higher bound-ary density reduces segregation of impurity atoms and dis-tribution inhomogeneity of current density.Therefore,it is possible to increase the specific electric capacity through de-creasing the grain size under special corrosion conditions [4].With increasing rare earth content,higher defect density and corresponding local concentration of corrosion current den-sity around grain boundaries induce preferred corrosion of rge corrosion holes or channels will appear frequently along the grain boundaries,which lead to the in-homogeneity of corroded structure.Taking the microstructure and texture evolution into ac-count,we conclude that control of cerium addition produces different recrystallization textures during annealing of cold-rolled aluminum,from which the favorite corrosion orienta-tion can be found.When aluminum is electrochemically etched,cubic pits are initially formed and turned into tunnels as the pits grow up.The SEM images of the aluminum etched pit shown in Fig.4corroborate the microstructural evolvement.Fig.4(a)shows that the tunnel length is approximately 20μm.Fig.4(b)indicates that many dark and small tunnels distribute along the tunnel depth in the etched aluminum foils with 0.0074wt.%Ce addition.It is easy to verify that cerium additive induces higher density of small etch pits and contributes their further growth into tunnels by enhancing the mass transport inside one-dimensional tunnel structure.Uniform tunnel length distribution increases the surface area which favors capacitance.It should be noted,however,that large etch pit forms in Fig.4(c)which is rooted in the connections of many small pits ,thus the tunnel wall along its depth will pare to the smaller pits,the surface of tunnel will decrease,as a result of blocking of small pits or tunnels by oxides with the increasing of cerium.The specific capaci-tance obtained by using alternating current impedance [13]shows that the capacitance at first increases,and then de-creases with increasing rare earth addition,it means that the content of rare earth should be controlled to certain extent,and the highest specific surface area was obtained from the specimen with 0.0074wt.%Ce.The effect of cerium on the corrosion of aluminum has been investigated by incorporating cerium into aluminum substrates and observing the subsequent anodic oxidation behavior of the alloys [14].The corrosion resistance of alumi-Fig.3{111}pole figures for sample after annealed at 530°C for600s without Ce (a),with 0.0074wt.%Ce (b)and with 0.012wt.%Ce(c)F S M f f (),%()%()ig.4E images o the aluminum oil without Ce a with 0.0074wt.Ce b and with 0.012wt.Ce cWANG Haiyan et al.,Effect of cerium addition on microstructure and texture of aluminum foil for electrolytic capacitors137num in aqueous media can be attributed to rapid formation of surface oxide film[15].Hydrochloric acid is used as etching solution,and Cl–plays an important role in spot corrosion and development,which has great effect on the oxide scale dissolution of the aluminum foil surface.Cl–is adsorbed on the special location of oxide surface,dissolves the oxide scales and formed Al(OH)2Cl,Al(OH)Cl2,AlCl2+,AlCl3, Al(OH)Cl+,finally produces etch pits on the surface of Al. Cerium and aluminium are oxidized at the alloy/film inter-face and incorporated into the anode film.In general,the oxide layer spread over the macroscopic surface,improves active hole forming[16],thus increases the specific internal area.However,when the content of cerium keeps increasing, the distribution inhomogeneity induces the substantial in-crease of chemistry activity,and results in large number of etching pits,which generates film breakdown over alumi-num surface.During the growth of tunnel,metal dissolution occurs from its surface,while the tunnel sidewalls are cov-ered with oxide film which restrain corrosion,which results in inferior capacitance[17].As mentioned above,we can estimate that the introduction of cerium reduces the thickness of oxide film on aluminum metal and induces the nucleation of etch pits.Therefore,ad-dition of rare earth has certain potential to be used for the application of aluminum electrolytic capacitors,and the in-volved researches are still underway to be carried out.3ConclusionsCerium was introduced to control the etch pits and tunnel length distribution on aluminum foil for electrolytic capaci-tors.The dissolution of cerium during electrochemical etch-ing might induce the optimum etch structure,produce high surface area and finally increase the capacitance,since addi-tion of cerium prohibited initial oxide film formation during etching but favors the formation of corrosion pits.In this work,the most perfect surface area was obtained when the addition of Ce reached0.0074wt.%.References:[1]Engler O,Huh M Y.Evolution of the cube texture in high pu-rity aluminum capacitor foils by continuous recrystallization and subsequent grain growth.Mater.Sci.Eng.A,1999,271(1): 371.[2]Scherer J,Magnussen O M,Ebel T,Behm R J.Initial stages ofthe anodic etching of aluminum foils studied by atomic force microscopy.Corros.Sci.,1999,41(1):35.[3]Oh H J,Lee J H,Ahn H J,Jeong Y S,Park N J,Kim S S,ChiC S.Etching characteristics of high-purity aluminum in hy-drochloric acid solutions.Mater.Sci.Eng.A,2007,449-451(25):348.[4]Mao Weimin,Chen Lei,Sa Liman,Yu Yongning,Li Yunfeng.Influence of grain boundaries on corrosion structure of low voltage aluminum foil.T he Chinese Journal of Nonferrous Metals(in Chin.),2004,14(1):1.[5]Osawa N,Fukuoka K.Pit nucleation behavior of aluminiumfoil for electrolytic capacitors during early stage of DC etching.Corros.Sci.,2000,42(3):585.[6]Wang Mei,He Yedong.Growth and passivation of aluminumetch tunnels at on-off controlling direct current in6wt.%HCl solution.Rare Metals,2008,27(2):205.[7]Liu Guili,Zhang Guoying,Li Rongde.Electronic theoreticalstudy of the interaction between rare earth elements and impu-rities at grain boundaries in steel.J.Rare Earths,2003,21(3): 372.[8]Baker I,Li J.An EBSP study of isothermally-annealed cold-rolled nickel.Microscopy Research and T echnique,2004,63: 289.[9]Kang Y B,Peltona A D,Chartranda P,Fuerst C D.Criticalevaluation and thermodynamic optimization of the Al-Ce,Al-Y, Al-Sc and Mg-Sc binary put.Coupling Phase Diagrams Thermochem.,2008,32:413.[10]Deng Yunlai,Zhang Xinmin,Liu Chunming,Chen Zhiyong,Zhou Zhuoping.The effect of trace RE on the evolution of tex-tures in high voltage aluminum capacitor foils.Functional Material,2002,33(1):60.[11]Li Chunlong,Wang Yunsheng,Chen Jianjun,Liu Chengjun,Jiang Maofa.Effects of rare earth on structure and mechanical properties of clean BNbRE steel.J.Rare Earths,2005,23(4): 470.[12]Lin Qin,Guo Feng,Zhu Xingyuan.Behaviors oflanthanum and ce-rium on grain boundaries in carbon manganese clean steel.J.Rare Earths,2007,25(4):485.[13]Wang Xiangyang.Study of the Electrolytic Etching of Ce Alumi-num Foil for Gigh Voltage Anode of Electrolytic Capacitor.Inner mongolia:InnerMongoliaUniv.Sci.&Tech.,2008.5.[14]Tomcsany L,V arga K,Bartik Ietal.Study of the interaction ofCl–with A passive film on Al and initiation of pitting corrosion.Electrochim.A cta,1989,34(5):855.[15]Mishra A K,Balasubramaniam R.Corrosion inhibition of alu-minium by rare earth chlorides.Mater.Chem.Phy s.,2007, 103(2-3):385.[16]Crossland A C,Thompson G E,Skeldon P,Wood G C,SmithC J E,Habazaki H,Shimizu K.Anodic oxidation of Al-Ce Al-loys and inhibitive behavior of Cerium species.Corros.Sci., 1998,40(6):871.[17]Kang J W,Shin Y H,Tak Y S.Growth of etch pits formedduring sonoelectrochemical etching of aluminum.Electro-chimica A cta,2005,51(5):1012.。
铝箔英文版的MSDS

铝箔英文版的MSDS Aluminum Foil MSDS (Material Safety Data Sheet) 1. IdentificationProduct Name: Aluminum FoilChemical Formula: AlCAS Number: 7429-90-5Synonyms: Aluminium foil, al-foilEmergency Phone Number: [Emergency Phone Number] 2. Hazard IdentificationClassification:- Eye Irritation (Category 2A)- Skin Irritation (Category 2)- Acute Toxicity – Inhalation (Category 4)- Chronic Aquatic Toxicity (Category 3)Potential Hazards:- Causes eye irritation.- May cause skin irritation.- Can be harmful if inhaled.- May cause long-term adverse effects in the aquatic environment.Chemical Name: Aluminum foilCAS Number: 7429-90-5Concentration: 100%4. First Aid Measures- Eye Contact: Rinse thoroughly with water for several minutes, remove contact lenses if present and easy to do. Seek medical attention if irritation persists.- Skin Contact: Wash with soap and water. Seek medical attention if irritation occurs or persists.- Inhalation: Remove to fresh air. If experiencing respiratory symptoms, seek medical attention.- Ingestion: Rinse mouth, do NOT induce vomiting. Seek medical attention if necessary.5. Firefighting Measures- Suitable Extinguishing Media: Water spray, foam, dry chemical, or carbon dioxide.- Specific Hazards Arising from the Chemical: Aluminum may form explosive mixtures with oxidizing agents (e.g., chlorine, fluorine).- Special Protective Equipment and Precautions for Firefighters: Wear full protective clothing and self-contained breathing apparatus (SCBA).6. Accidental Release Measures- Personal Precautions: Wear appropriate protective equipment (gloves, safety glasses, and respiratory protection) when handling and cleaning spills.- Environmental Precautions: Avoid release into the environment. Contain and collect any spilled material.- Clean-up Procedures: Sweep up or vacuum spills carefully. Avoid generating dust. Place material in appropriate containers for disposal.7. Handling and Storage- Handling: Avoid eye and skin contact. Use in a well-ventilated area. Wash hands thoroughly after handling.8. Exposure Controls/Personal Protection- Engineering Controls: Use local exhaust ventilation to maintain airborne concentrations below occupational exposure limits.- Personal Protective Equipment:- Eye/Face Protection: Safety glasses or goggles.- Skin Protection: Wear gloves and protective clothing to minimize skin contact.- Respiratory Protection: Use a NIOSH-approved respirator if airborne concentrations exceed the occupational exposure limits.9. Physical and Chemical Properties- Appearance: Silver metal foil- Odor: Odorless- Melting Point: 660.32°C (1220.58°F)- Boiling Point: 2470°C (4478°F)- Solubility: Insoluble in water- Density: 2.70 g/cm³- Vapor Pressure: Not applicable10. Stability and Reactivity- Stability: Stable under normal conditions.11. Toxicological Information- Acute Toxicity: Low acute toxicity by inhalation, ingestion, and dermal exposure.- Eye/Skin Irritation: May cause moderate irritation to the eyes and skin.- Sensitization: No data available.- Carcinogenicity: Aluminum is not classified as a human carcinogen by IARC, NTP, or OSHA.- Chronic Toxicity: Prolonged or repeated exposure may cause adverse effects in the aquatic environment.12. Ecological Information- Ecotoxicity: Toxic to aquatic organisms. May cause long-term adverse effects in aquatic environments.13. Disposal Considerations- Disposal: Dispose of the material and its container in accordance with local, regional, or national regulations.14. Transportation Information- Not a dangerous good according to transport regulations.15. Regulatory Information- Listed on the TSCA inventory.16. Other Information- This MSDS contains valuable information critical to the safe handling, storage, and disposal of the product.。
1983-Analysis of Gas-Lubricated Foil Journal Bearings

2.1 Assumptions. In formulating the equations governing the elastohydrodynamics of the foil bearing, the following assumptions are made: (a) The stiffness of the foil is taken to be uniformly
H. Heshmat J. A. Walowit 0. Pinkus
Mechanical Technology Inc., Latham, N.Y. 12110
Analysis of Gas-Lubricated Foil Journal Bearings
This work is concerned with an evaluation of the performance of a gas journal bearing using a spring supported compliant foil as the bearing surface. The analysis, conducted for both single and multipad configurations, is concerned with the effects that the various structural, geometric, and operational variables have on bearing behavior. Following the solution of the relevant differential equation, tabular or graphical solutions are provided for a range of relevant geometric and operational parameters. The solutions include values of the colinear and crosscoupled spring coefficients due to both structural and hydrodynamic stiffness. Desirable design features with regard to start of bearing arc, selection of load angle, number ofpads and degree of compliance are discussed.
FOIL算法演示

age gain income gain credit-rating gain
<=30 0.322 low -0.279 fair 0.966
31~40 0.322
>40 -0.526 medium 0.322 excellent -0.678
所以当p={credit-rating=‘fair’}时有最大的FOIL_Gain。 执行 append p to r 那么规则r ={ student=‘yes’AND credit-rating=‘fair’}; 移除P’、N’中不满足规则r的元组,这时,|N’|=0,内循环停止
31…40
<=30 >40
low
low medium
yes
yes yes
excellent
fair fair
yes
yes yes
我们按照同样的方法,算出R={
(age=‘<=30’ AND student=‘no‘) OR (credit_rating=‘excellent AND age=‘>40’) } 那么综合以上所求的两个规则R,我们可以从十条训练集中学习出以下结论: IF (student=‘yes’ AND credit-rating=‘fair’) THEN buys_computer=‘yes’; IF (age=’31~40 ) THEN buys_computer=‘yes’; IF (income=‘medium’ AND age=‘>40 ’) THEN buys_computer=‘yes’; IF (age=‘<=30’ AND student=‘no‘) THEN buys_computer=‘no’; IF (credit_rating=‘excellent AND age=‘>40’ ) THEN buys_computer=‘no’; 现在有个问题,就是提取出来的规则集的准确率有多高呢? 这时,我们需要通过检验集来验证规则集的准确率,检验集如下所示:
安德里茨压滤机中文介绍(20200522025615)

液压闭合 “拉式闭合 ”(pull to close)
最大过滤压力可达 50 bar
- 最大滤板尺寸 : 2000x3000 mm
Foil No. 20
Foil No. 7
过滤原理
将不同工艺阶段组合在一个操作单元 中,独立控制以实现最佳功能。
滤饼脱水性、渗透性,操作温度和压
力变化梯度等要素在资金投入和操作
压力
成本中十分重要。
予挤压
外围设备如进料泵、清洗泵和隔膜挤 压系统的正确设计和控制是优化成本 投入的必要条件。
进料和过滤
中心反吹 后挤压
洗涤
循环时间
安德里茨集团
我们的目标 : 成为造纸,钢 铁,分离技术等行业高科技产品系统的全球市场先锋
Foil No. 1
安德里茨里程碑
2005 2003/2004
2002
收购连恩舍( LENSER )滤板公司
收购 IDEAS Simulation Inc., Acutest Oy, Fiedler,
Bird Machine,
Foil No. 17
压滤机设计
压滤机结构有以下两种:侧杠式 设计和悬梁式设计
- 侧杠式设计 -
- 悬梁式设计 -
Foil No. 18
压滤机设计
侧杠式设计
简单手动到全自动设备一应俱全 对于粘度极 高滤饼可实现最大程度自动化控制 结构重量轻 最高过滤压力可达 50 bar 可供应的最大尺寸可至 2000x2000 mm
Foil No. 12
过滤过程 –厢式压滤机
压滤机充满物料 开始形成滤饼
部分形成滤饼 过滤阻力增加
完全形成滤饼 过滤阻力大
中心吹泥 排出滤饼
Foil No. 13
1997-FOIL AIRGAS BEARING TECHNOLOGY ~ AN OVERVIEW
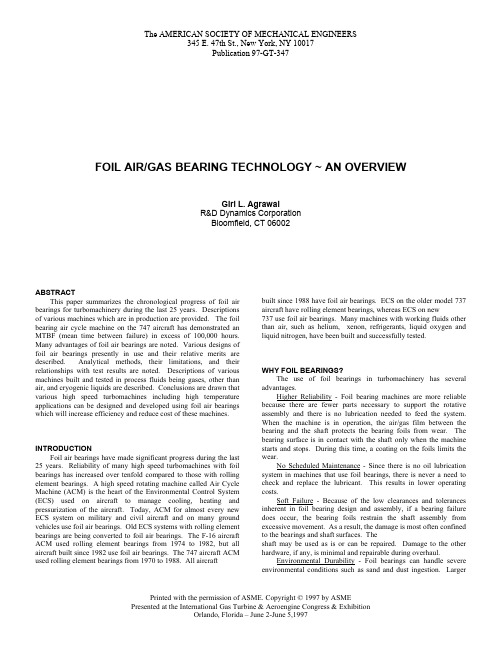
The AMERICAN SOCIETY OF MECHANICAL ENGINEERS345 E. 47th St., New York, NY 10017Publication 97-GT-347FOIL AIR/GAS BEARING TECHNOLOGY ~ AN OVERVIEWGiri L. AgrawalR&D Dynamics CorporationBloomfield, CT 06002ABSTRACTThis paper summarizes the chronological progress of foil air bearings for turbomachinery during the last 25 years. Descriptions of various machines which are in production are provided. The foil bearing air cycle machine on the 747 aircraft has demonstrated an MTBF (mean time between failure) in excess of 100,000 hours. Many advantages of foil air bearings are noted. Various designs of foil air bearings presently in use and their relative merits are described. Analytical methods, their limitations, and their relationships with test results are noted. Descriptions of various machines built and tested in process fluids being gases, other than air, and cryogenic liquids are described. Conclusions are drawn that various high speed turbomachines including high temperature applications can be designed and developed using foil air bearings which will increase efficiency and reduce cost of these machines. INTRODUCTIONFoil air bearings have made significant progress during the last 25 years. Reliability of many high speed turbomachines with foil bearings has increased over tenfold compared to those with rolling element bearings. A high speed rotating machine called Air Cycle Machine (ACM) is the heart of the Environmental Control System (ECS) used on aircraft to manage cooling, heating and pressurization of the aircraft. Today, ACM for almost every new ECS system on military and civil aircraft and on many ground vehicles use foil air bearings. Old ECS systems with rolling element bearings are being converted to foil air bearings. The F-16 aircraft ACM used rolling element bearings from 1974 to 1982, but all aircraft built since 1982 use foil air bearings. The 747 aircraft ACM used rolling element bearings from 1970 to 1988. All aircraft built since 1988 have foil air bearings. ECS on the older model 737 aircraft have rolling element bearings, whereas ECS on new737 use foil air bearings. Many machines with working fluids other than air, such as helium, xenon, refrigerants, liquid oxygen and liquid nitrogen, have been built and successfully tested.WHY FOIL BEARINGS?The use of foil bearings in turbomachinery has several advantages.Higher Reliability - Foil bearing machines are more reliable because there are fewer parts necessary to support the rotative assembly and there is no lubrication needed to feed the system. When the machine is in operation, the air/gas film between the bearing and the shaft protects the bearing foils from wear. The bearing surface is in contact with the shaft only when the machine starts and stops. During this time, a coating on the foils limits the wear.No Scheduled Maintenance - Since there is no oil lubrication system in machines that use foil bearings, there is never a need to check and replace the lubricant. This results in lower operating costs.Soft Failure - Because of the low clearances and tolerances inherent in foil bearing design and assembly, if a bearing failure does occur, the bearing foils restrain the shaft assembly from excessive movement. As a result, the damage is most often confined to the bearings and shaft surfaces. Theshaft may be used as is or can be repaired. Damage to the other hardware, if any, is minimal and repairable during overhaul.Environmental Durability - Foil bearings can handle severe environmental conditions such as sand and dust ingestion. Largerparticles do not enter into the bearing flow path because of a reversed pitot design at the cooling flow inlet and smaller particles are continually flushed out of the bearings by the cooling flow. This ability to withstand contamination eliminates the need for filters in the airflow.High Speed Operation - Compressor and turbine rotors have better aerodynamic efficiency at higher speeds. Foil bearings allow these machines to operate at the higher speeds without any limitation as with ball bearings. In fact, due to the hydrodynamic action, they have a higher load capacity as the speed increases.Low and High Temperature Capabilities - Many oil lubricants cannot operate at very high temperatures without breaking down. At low temperature, oil lubricants can become too viscous to operate effectively. Foil bearings, however, operate efficiently at severely high temperatures, as well as at cryogenic temperatures.Process Fluid Operations - Foil bearings have been operated in process fluids other than air such as helium, xenon, refrigerants, liquid oxygen and liquid nitrogen. For applications in vapor cycles, the refrigerant can be used to cool and support the foil bearings without the need for oil lubricants that can contaminate the system and reduce efficiency.HISTORYGarrett AiResearch (now Allied Signal) has done the pioneering work on foil air bearings. Several laboratory and prototype machines were built in the mid 60’s. The first production ACM using foil air bearings was designed and developed for the DC-10 ECS system in 1969. Field experience proved that the unit was far more reliable then previous 727 ball bearing units. Further research and laboratory testing to increase load capacity and damping continued. In 1972, a 125 kw turbo-alternator-compressor (TAC) supported on foil bearings was built by AiResearch for NASA Lewis, which worked well. In 1974, under pressure from the Navy to increase the reliability of the A7E air cycle machine, AiResearch converted existing ball bearing machines to foil bearing machines on three A7E aircraft. These aircraft were flown by the Navy off the Coral Sea during the Vietnam War for evacuation of Americans from South Vietnam. These units worked extremely well and proved to be much more reliable than previous ball bearing units. As a result, after Vietnam was over, the Navy gave a contract to AiResearch to convert the entire fleet of A7E to foil bearing units. This program gave high confidence to AiResearch management in foil bearing technology even for a military aircraft. In 1976, when the F-18 program was launched by Northrop, AiResearch decided to proceed with foil air bearings from the start. The unit successfully passed vibration and shock load testing. This was the first military unit with foil air bearings to go into production.In 1978, AiResearch developed a small foil air bearing supported ACM for the commuter plane Cessna-550. This unit since then is also used on other aircraft e.g. EMB-120, ATR-42, ATR-72 and others. In 1979, a new commercial aircraft 767/757 was launched by Boeing. By now the success of foil air bearings was well known; hence Boeing required that ECS on 767/757 use foil air bearings. AiResearch successfully developed a foil air bearing supported ACM for 767/757. Based on the successful testing, they won the contract and went into production. In 1979AiResearch developed a foil air bearings supported ACM for Navy F-14 aircraft which was also flight tested on Air Force F-15 aircraft with some modifications. Later AiResearch, by making necessary modifications, used existing machines on various other ECS systems. They also developed a small foil air bearing supported machine for the M-1 tank.While substantial advancement in foil air bearing technology was being made by AiResearch in the 70’s, their competitor Hamilton Standard started lagging behind in ECS business. At the same time, Mechanical Technology Inc. (MTI), a research and development company, came up with their own concept of a foil bearing design called Hydresil. Hamilton signed a contract with MTI to use Hydresil bearings. Hydresil had comparable load capacity, but had low damping. Several ACM with Hydresil bearings were flight tested by Hamilton on 747 aircraft from 1975 to 1979. During flight testing those units lasted only four hours to fifty hours. In 1979, Hamilton launched their own program for foil bearing research. They came up with their own design concept and patented it. In 1982, Hamilton successfully flight tested a foil bearing ACM based on their own foil bearing design on F-16 aircraft. The same machine with minor changes went into production for B-1B aircraft and B-2 aircraft. Later the same machine was successfully flight tested on two F-18 aircraft. Based on successful flight test experience, the Navy qualified the machine for the F-18 without formal qualification testing. Hamilton also developed, qualified and produced a machine for L-1011 aircraft. Under pressure from various airlines, Boeing adopted the same machine with some changes for 747-400 aircraft which went into production in 1988. This machine has shown MTBF (mean time between failure) of over 100,000 hours. Between 1983 and 1988, Hamilton developed several other prototype machines supported on foil air bearings. In 1991, Hamilton developed, qualified and started producing a machine for SAAB 2000 aircraft. The same machine is being used for EMB-145 aircraft.In 1993, Hamilton developed, qualified and started producing the world’s first four-wheel ACM supported on foil air bearings for 777 aircraft. The unit passed 36,000 start-stop cycle to simulate a 30 year life.Various other companies such as Sunstrand, British Aerospace, ABG-Semca (France) and Tupolev (Russia) have done limited work on foil air bearing technology.FOIL BEARING TECHNOLOGYThe principle of an air or gas bearing is simple. As shown in Fig. 1, when two surfaces form a wedge, and one surface moves relative to the other surface, pressure is generated between the surfaces due to the hydrodynamic action of the fluid which carries load.Fig. 1: Principle of an Air BearingJournal BearingIn a journal bearing, the shaft deflects and a wedge is formed due to the eccentricity between the shaft center and the bearing center. The resulting hydrodynamic pressure generation is shown in Fig. 2. Even though, the principle of an air bearing is simple,application is complex. Usually running radial clearance between the shaft and the bearing is less than 0.0005 inch for a 2 inch diameter shaft running at 36,000 rpm. But the shaft growth due to temperature and centrifugal force could be 0.0020 in. Hence a bearing can not be made to work at various speeds and temperatures.In addition, damping is required to suppress any whirl instability,and there could be misalignment between various rotating parts and stationary parts. These problems are resolved by foil bearings.While stationary, there is a small amount of preload between the shaft and the bearing. As the shaft turns, a hydrodynamic pressure is generated, which pushes the foils away from the shaft and the shaft becomes completely airborne. This phenomenon occurs instantly during start-up at a very low speed. When the shaft is airborne, friction loss due to shaft rotation is very small. As the shaft grows, the foils get pushed further away keeping the film clearance relatively constant. In addition, foils provide coulomb damping due to relative sliding, which is essential for stability of themachine. Various concepts of foil bearings have been tested.Fig. 2: Hydrodynamic Pressure GenerationThe Multipad concept is shown in Fig. 3, which has been pursued by AiResearch since the days of the DC-10. Multiple pads form an iris and provide a preload when the shaft is not running.During starting, the iris expands and a cushion of air is formed between the bearing and the shaft. Later versions such as for 767/757 have a supportive spring behind each pad which increases the load capacity significantly. The top foil is coated with Teflon-Sor a polyimide coating to provide lubricity during starts and stops.Fig. 3: Multipad Foil Journal Bearing SchematicFigure 4 is a Reversed Multilayer journal bearing concept which has been pursued by Hamilton Standard in 747, B-1B, B-2,SAAB-2000, 777 and other aircraft. The single corrugated (bump)foil which has a bilinear spring characteristic is restrained in an axial keyway in the outer shell along one edge. The intermediate and top foils are attached to a key along one edge and are wound in opposite directions. The top foil has a thin coating which provides lubricity during startup and shutdown. As the shaft rotates, a wedge is formed due to the radial displacements of the shaft. Hydrodynamic action draws the working gas into the wedge where it is locally compressed. The corrugated foil acts as a spring which accommodates expansion, excursions and any misalignment. It also provides a flow path for the cooling air to remove parasitic heat from the bearing. In the Reversed Multilayer foil bearing, the adjacent foils move in opposite directions. The net result is that relative movement is additive, which in turn produces high coulombdamping.Fig. 4: Reversed Multilayer Foil Journal BearingSchematicFigure 5 is a Hydresil foil journal bearing. It has been pursued by Mechanical Technology Inc. (MTI). Both the bump foil and the foil are spot welded to the sleeve. Various versions have been patented. The load capacity of the Hydresil is comparable to the Multipad or Reversed Multilayer foil bearing, but it has lowdamping.Fig. 5: Hydresil Foil Journal Bearing SchematicThe damping characteristic of three types of bearings is shown in Fig. 6, where orbits are shown when 27 lbs. of shock load is applied to a 2 inch diameter shaft rotating at 36,000 rpm. It is obvious that the Reversed Multilayer concept is the most stable andit is least affected by shock loads.Fig. 6: Orbits of Various Foil Journal Bearings under 27 lbs. of Shock LoadEven though Reversed Multilayer concept has high damping,the foils have a tendency to protrude like a telescope during assembly. In addition, manufacturing is costly because all bendsnear the keyway have tight tolerances. A new concept called Reversed Multipad shown in Fig. 7 has been patented by R&D Dynamics Corporation. It has benefits of both Multipad and Reversed Multilayer designs. It has high damping as well as it requires low preload. Lower preload makes the machine start at alower torque. Due to multipad design, the tolerances are not tight.Fig. 7: Reversed Multipad Foil Journal Bearing SchematicThrust BearingsThrust bearings withstand axial loads in a rotating machinery.They work on the same hydrodynamic principle as journal bearings shown in Fig. 1. In a journal bearing the wedge action comes from eccentricity between the center of the rotating shaft and the center of the bearing itself, whereas in a thrust bearing the wedge is built in taking into account any deflection due the axial load.A radial spring type thrust bearing is shown in Fig. 8. It was invented by AiResearch and has been followed since 1970 when first used for the DC-10. There are multiple radial springs which transfer the load to the housing. Foils between the springs deflect under pressure forming the wedge required for the hydrodynamic action. During the last 20 years many versions of the same design,usually for the manufacturing reasons mostly by AiResearch, have been used. In some designs instead of a separate spring being spot welded to the main bearing plate, it is formed by chemical etching out of the bearing plate. It reduces manufacturing cost, butsomewhat compromises performance in some instances.Fig. 8: Radial Spring Foil Thrust BearingA dual spring thrust bearing is shown in Fig. 9. It was invented by Hamilton Standard. In this concept the bearing consists of two washer shaped plates similar to radial spring bearings. The coated pads, welded to the top plate, are supported on stiff bump foil springs to optimize the wedge shape required for load capacity and lift-off. The bottom plate has several softer bump foil springs welded to it, required to optimize the overall spring rate and damping of the bearing. The dual spring rate thrust bearings have approximately 15% higher load capacity than the radial springbearings, but they are more expensive to manufacture.Fig. 9: Dual Spring Foil Thrust BearingCoatings Both journal and thrust bearings apply a small amount of preload on the shaft when the machine is not running. The foil face which is touching the shaft is coated for lubricity during startup and shutdown. A typical DC-10, machine which runs at 48,000 rpm, is fully airborne at about 2,000 rpm. Several foil coatings are used.Most commercial aircraft use Teflon-S made by DuPont which isgood up to 475o F. Most military aircraft ACM use a polyimide coating, whose basic research was performed by NASA Lewis. Both AiResearch and Hamilton have modified the basic formula and the application process to suit their needs. The coating is good up to 700o F. Extensive high temperature coating research has been performed, mostly by NASA Lewis, Air Force Wright Laboratory, AiResearch (Phoenix Division) and Mechanical Technology Inc. A partial list of various coatings, which have been considered, is given below:Coating ProcessFOIL:BN/Pt, BN/Pd Electrophoretic DepositionBN/Pt Chemical Vapor InfiltrationBN/SiO2, BN/ZrO2 Sol GelBN/Ni-Cr,ZrO2/Ni-Cr Mechanical AlloyingBN/Ni Electroless DepositionCr2O3 SputteringTiC SputteringA12O3 SputteringTiN SputteringTribaloy-400 SputteringJOURNAL:NASA PS212 Plasma SprayKAMAN DES Chemically AdherentTiAlN/TiA1 SputteringWC-9Co D-GunCr2O3-4OCr D-GunAnalysis and TestingThe analysis of foil air bearings requires simultaneous solutions or iteration methods to solve foil elasticity equations and fluid hydrodynamic equations. Foil elasticity equations are nonlinear and involves large deformation theory. A foil can deform as much as five times its own thickness. Hence most finite element or finite difference methods, do not provide satisfactory results. Hydrodynamic equations are nonlinear Reynolds’ equations with continuously changing boundary conditions. Many papers analyzing foil bearings have been published. In some papers, predicted results vary as much as 500% from the actual test results. What seems to work and provide reasonable results are semi-empirical methods. Sufficient test data are collected by varying geometrical parameters and test parameters of the bearing. Results are correlated using a multiple regression method. Then a model is prepared using coefficients of the multiple regression analysis. Hydrodynamic equations are solved using the preferred final geometry. Then an inverse method is used to design the foil geometry in the unloaded position. In the above described procedure, the complex problem is decoupled into many simple problems using both analytical methods and the test results.The above described approach has been used both by AiResearch (Los Angeles) and Hamilton Standard to design and develop successfully many foil air bearing machines which are flying today. Others have taken more conventional approach and have not succeeded. Design of the machine parameters such as static and dynamic loads, critical speed, thrust loads, rotor clearance, seals, cooling flow etc. must be correlated with the design of the foil air bearings.A satisfactory design method requires reliable test data. Successful test rigs to test journal bearings, thrust bearings and coatings have been designed and developed. Typical rigs presently being used at R&D Dynamics Corporation are shown in Figs. 10, 11and 12.Fig. 10: Journal Bearing Test Rig(R&D Dynamics Corp.)Fig. 11: Thrust Bearing Test Rig(R&D Dynamics Corp.)Fig. 12: Coating Wear Test Rig(R&D Dynamics Corp.)APPLICATIONSDC-10 - The DC-10 was the first production foil air bearing machine. It was designed and developed by AiResearch and went into production in 1970. The same machine is also used for Airbus A-300. A photograph of the machine is shown in Fig. 13. The rotating assembly has three rotors: a turbine, a compressor and a fan. The machine runs at 48,000 rpm. To date, over 80 millionhours have been accumulated on this machine.Fig. 13: DC-10 Foil Bearing Air Cycle Machine(Developed by AiResearch)F-18 - The F-18 is the first military production machine aftersuccessful modifications of the A7E machine from ball bearings to air bearings. The F-18 machine was designed and developed by AiResearch in 1976. A cross section of the machine is shown in Fig. 14. It has two rotors: a turbine and a compressor. Themachine runs at about 95,000 rpm.Fig. 14: F-18 Foil Bearing Air Cycle Machine(Developed by AiResearch )Cessna-550 - In 1977 AiResearch developed a small two-wheel air cycle machine for commuter aircraft such as the Cessna-550.The machine is shown in Fig. 15. It runs at 105,000 rpm. The same machine is being used for EMB-120, ATR-42 and ATR-72 aircraftwith minor modifications.Fig. 15: Cessna-550 Foil Bearing Air Cycle Machine (Developed by AiResearch)F-15/F-14 - Following success of the F-18, AiResearch developed a slightly larger two-wheel air cycle machine for F-15 aircraft in 1977. The same machine with slight modifications was used for F-14 aircraft in 1978. Photograph of F-14 machine is shown in Fig.16.Fig. 16: F-14 Foil Bearing Air Cycle Machine(Developed by AiResearch)767/757 - The 767/757 aircraft was launched by Boeing in 1979. Knowing the success of DC-10 ACM, Boeing required that 767/757 ACM must have foil air bearings. This was the first aircraft where the customer required a foil bearing ACM. Cross section of the machine developed by AiResearch is shown in Fig. 17. It is also a three-wheel machine like the DC-10, but the design is muchsimpler.Fig. 17: 767/757 Foil Bearing Air Cycle Machine(Developed by AiResearch)F-16 - The F-16 aircraft is built by General Dynamics. Its production was started in 1974. An air cycle machine with a ball bearing design was built by Hamilton Standard. In 1982, due to additional electronics on the aircraft, the Air Force required a new air cycle machine. AiResearch modified the existing F-18 machine and qualified for F-16 aircraft, which is now in production. A photoof the F-16 ACM is shown in Fig. 18.Fig. 18: F-16 Foil Bearing Air Cycle Machine(Developed by AiResearch)M1A1 - AiResearch also developed a foil air bearing air cycle machine for the M1A1 tank environmental control system. The machine has a turbine and a fan on a common shaft. The machine worked well during the last Gulf War in spite of heavy sand and dustin the desert. The machine is shown in Fig. 19.Fig. 19: M1A1 Tank Foil Bearing Air Cycle Machine(Developed by AiResearch)L-1011 - The L-1011 machine was the first production foil bearing machine produced by Hamilton Standard. As can be seen in Fig. 20, it is a three-wheel machine with fan, compressor and turbine rotors. These ACMs were placed on the last five production L-1011 aircraft and have been performing well. Figure 21 shows an L-1011 flight test unit that was returned for inspection after 13,000 hours of service at Saudia. The unit was in excellent working condition despite being heavily contaminated by sand, cement and oil. This shows the ability of the foil bearings to operate in severe environmental conditions.Fig. 20: L-1011 Foil Bearing Air Cycle Machine(Developed by Hamilton Standard)Fig. 21: L-1011 Foil Bearing Air Cycle MachineAfter 13,000 Hours in Saudia Aircraft 747 - Hamilton Standard supplies the ECS on the 747 aircraft. Aircraft production started in 1970. Air cycle machines on all aircraft built until 1987 are ball bearing units. Under pressure from the airlines, Boeing and Hamilton Standard decided to change the ECS system to incorporate foil air bearing ACMs. All 747 aircraft built since 1988 have foil bearing ACMs. Over 1000 machines are flying successfully. These machines are performing well in the field, and to date, over 12 million flight hours have been accumulated. The machine has shown an MTBF (mean time between failure) of over 100,000 hours in the field. A photograph of the 747 machine is shown in Fig. 22.Fig. 22: 747 Foil Bearing Air Cycle Machine(Developed by Hamilton Standard)B-1B - The foil bearing machine shown in Fig. 23 was developed for use on the B-1B aircraft by Hamilton Standard. The unit runs at 95,000 rpm. To date, this two-wheel foil bearing machine has logged over 120,000 flight hours. One hundred production units and thirty spares were delivered for use on this longrange bomber.Fig. 23: B-1B Foil Bearing Air Cycle Machine(Developed by Hamilton Standard)B-2 - Hamilton Standard builds the ECS system on the Air Force B-2 Stealth bomber. The system contains a high speed foil air bearing supported ACM. The B-2 ACM, shown in Fig. 24, completed a rigorous qualification program in 1989. After one test that included 7500 start/stop cycles, the bearings were inspected and found to be in like-new condition. The hardware for this machine is shown in Fig. 25. Another test included 1600 hours of endurance running. These tests show the durability of the foil bearings. Many B-2aircraft are flying successfully using foil air bearing ACMs.Fig. 24: B-2 Foil Bearing Air Cycle Machine(Developed by Hamilton Standard)Fig. 25: B-2 Foil Bearing Air Cycle Machine After 7,500Start-StopsASME Publication 97-GT-347Printed with the permission of ASME. Copyright © 1997 by ASME11SAAB-2000 - Hamilton Standard has designed, developed and qualified a midsize foil air bearing ACM for use on SAAB-2000commuter aircraft. Many aircraft with these units are flying successfully. Shown in Fig. 26, this three-wheel machine will alsobe used on other large commuter aircraft.Fig. 26: SAAB-2000 Foil Bearing Air Cycle Machine (Developed by Hamilton Standard)777 - Hamilton Standard has developed and qualified an ECS system on the latest Boeing aircraft 777. The system uses the world’s first four-wheel air bearing ACM. All of the previous machines are either two-wheel or three-wheel machines. The unit has successfully passed 36,000 start-stop cycles, which is equivalent to 30 years life of the machines. Many 777 aircrfat are flying with production ACMs. Approximately 300 aircraft have already been sold and will be delivered in the near future. A cross section of theACM is shown in Fig. 27.Fig. 27: 777 Foil Bearing Air Cycle Machine(Developed by Hamilton Standard)ADDITIONAL APPLICATIONSMany applications of foil air/gas bearings other than air cycle machines have been built and successfully tested, but nothing appears to be in production at this time. AiResearch successfully tested a vapor cycle machine on Navy P-3 aircraft with Freon as the working fluid. A machine similar to this will be built for F-22aircraft. A cryogenic foil bearing turbo pump working in liquid oxygen was built by AiResearch and successfully tested by NASA.Both AiResearch and Hamilton Standard have built foil bearing high speed fans for the Space Station. Several cryogenic foil bearing turboexpanders for air separation plants for the Navy have been built. AiResearch built a high temperature foil bearing APU (Auxiliary Power Unit) for B-2 aircraft in 1985. The unit ran successfully, but could not pass the endurance test. It was concluded that coating wear at high temperature was the cause.Since then much research has been done in the areas of foil coating and bearing design. Recently R&D Dynamics jointly with Allison Engine Company built a missile engine with a hot end foil bearing good up to 1000 o F.CONCLUSIONSFoil bearings have been extremely successful for air cycle machines. They have increased the reliability of these machines up to tenfold. Even though several machines have been built for other applications, the work has not been pursued by the same vigor and commitment for various reasons. Foil bearings have strong potential for the following applications:A.A small general aviation gas turbine engine supported on foil bearings will be more reliable and cost less than existing engines.B.Oil free cryogenic turboexpanders supported on foil bearings will be more reliable and increase efficiency of gas separation plants.C.Highly reliable and less expensive APU’s can be built for various aerospace and ground vehicles using foil bearings.D.Recent concept of foil bearings provide potential for low cost bearings using automated manufacturing methods for commercial applications; e.g. automobile gas turbine engines, vapor cycle centrifugalcompressors and commercial air/gas compressors.ACKNOWLEDGMENTSThe materials presented here have been compiled from various sources including those from airlines and military customers. Some cross sections and photos were reproduced or redrawn frompreviously published material or sales brochures. Some photos were retaken from hardware available with various customers.。
安德里茨压滤机中文介绍

安德里茨集团我们的目标:成为造纸,钢铁,分离技术等行业高科技产品系统的全球市场先锋Foil No. 1安德里茨里程碑20052003/200420022000/200119991990-199819871852收购连恩舍(LENSER)滤板公司收购IDEASSimulationInc.,AcutestOy,Fiedler, BirdMachine,耐驰压滤机(NETZSCH),Fluidized Bed Drying Systems of VA Tech WABAG, Otto Kaiser GmbH收购 SELAS SAS 和 ABB Drying初步公开销售安德里茨证券收购Ahlstrom 机械集团收购 UMTCarlyle / Custos 私人基金 / UIAG 获得安德里茨通过下列国内外公司收购,公司得到稳定发展:Sprout-Bauer, Kone Wood, Jesma-Matador and SundwigAGIV 收购安德里茨大部分股份由Josef K?r?si建立一家铸造厂和机械厂Foil No. 2全球性业务安德里茨集团总部位于奥地利的格拉茨市,是一个业务遍及全球的技术型集团公司。
安德里茨集团研究和开发高科技产品系统,专门为不同标准的和高度专业化的产品提供工业化工艺程序解决办法。
集团全球约有5,600名员工,15个生产和服务基地,以及100多个分支机构。
Foil No. 3五大战略业务领域集团业务主要集中在以下五个领域:纸浆、造纸业轧机及带钢表面处环境和工艺料技术水力机器理处理部造纸行业的先锋不锈钢轧钢行固液分离行业动物饲料的先业的先锋的先锋锋安德里茨集团2007年总销售额= 亿欧元FoilNo. 4压滤机超过150年的板框压滤机综合制造经验拥有NETZSCH和R&B两大品牌后,安德里茨可以给用户提供最广泛的工艺处理经验和专业的压滤机选择FoilNo. 5过滤原理Pmax过滤压力ambmax: 最大过滤压力 amb: 外界环境压力力泥浆滤液滤饼滤布Foil No. 6压滤机用于固液分离,可以取得极好的过滤效果,并获取很高含固率的滤饼根据滤饼过滤原理可以获得最大的过滤效果随着滤饼的不断增厚,滤布和滤饼对水流形成逐渐增加的阻力(压力损失)可以进行滤饼洗涤压滤结束,固体留在滤室内,被挤压形成坚硬的滤饼压滤机的自动化程度由用户决定Foil No. 7将不同工艺阶段组合在一个操作单元中,独立控制以实现最佳功能。
FLEXIBLE FOIL MOVEABLE BY NON-MECHANICAL MEANS
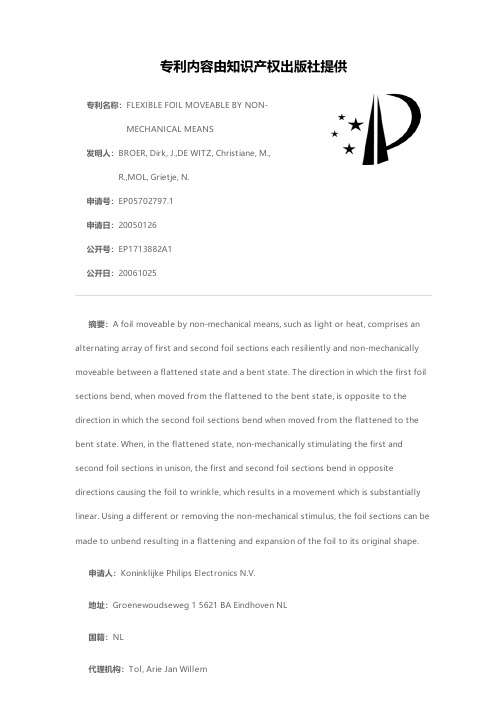
专利名称:FLEXIBLE FOIL MOVEABLE BY NON-MECHANICAL MEANS发明人:BROER, Dirk, J.,DE WITZ, Christiane, M., R.,MOL, Grietje, N.申请号:EP05702797.1申请日:20050126公开号:EP1713882A1公开日:20061025专利内容由知识产权出版社提供摘要:A foil moveable by non-mechanical means, such as light or heat, comprises an alternating array of first and second foil sections each resiliently and non-mechanically moveable between a flattened state and a bent state. The direction in which the first foil sections bend, when moved from the flattened to the bent state, is opposite to the direction in which the second foil sections bend when moved from the flattened to the bent state. When, in the flattened state, non-mechanically stimulating the first and second foil sections in unison, the first and second foil sections bend in opposite directions causing the foil to wrinkle, which results in a movement which is substantially linear. Using a different or removing the non-mechanical stimulus, the foil sections can be made to unbend resulting in a flattening and expansion of the foil to its original shape.申请人:Koninklijke Philips Electronics N.V.地址:Groenewoudseweg 1 5621 BA Eindhoven NL国籍:NL代理机构:Tol, Arie Jan Willem更多信息请下载全文后查看。
2019年Scott公路车Addict、Foil新款上市

2019 New ScottRoad Bikes Addict and Foil Launched新款上市Scott对其2019款高端公路自行车进行了重大改进。
Scott 2019款公路自行车放弃了炫丽的涂装,但是整体更加优雅,因为Scott认为购买高级公路自行车是一种“奢侈”,是一种全新生活方式的体现。
深色、金属色漆涂装的Scott 公路自行车虽然低调,却掩饰不了它们出众的性能。
亮光涂装、黄边胎和与边胎同色的皮座垫,让自行车的“颜值”满足当前的审美趋势。
2019年Scott 公路车Addict 、Foil整理/清风2019款Addict RC顶级碟刹公路车Addict 是Scott 公路车产品线中的翘楚,其2019款车型也得到了符合古典美学的外观设计升级。
该车配备了优质轻量的HMX 碳纤维车架前叉、Shimano Dura-Ace Di2变速套件、Syncros 碳纤维把组三件套、DT Swiss PRC 1100 Dicut db 轮组。
高达9 500欧元的价位,使得Addict RC 顶级碟刹版战车对于普通消费者而言有些遥远。
2019款Addict RC 15 碟刹版,外观采用古典风格设计,车架采用耐力几何设计,次顶级HMF 碳纤维车架组、Ultegra Di2变速套件。
非RC 版Addict 则配备有:碟刹Addict SE、碟刹Addict 20以及次顶级HMF 碳纤维车架组。
如果你想要传统的亮光漆和高对比度的标识涂装,可以选择2019款圈刹版的Addict 以及Addict RC Pro 或Addict RC 10碟刹公路车。
84PRODUCT AND TECHNOLOGY 产品 • 技术2019款Scott Addict Gravel 10 碟刹公路车,采用了HMX 碳纤维车架组搭配SRAM Force 1x 变速液压碟刹套件、Syncros 把组及RP2.0碟刹轮组,并且拥有简单的双色涂装。
锡纸造型流程

锡纸造型流程The process of creating aluminum foil shapes is a fascinating and intricate one. In order to produce these shapes, skilled artisans carefully manipulate the aluminum foil using various tools and techniques. The first step in the process is to select the appropriate thickness of aluminum foil. This is crucial, as the thickness of the foil will determine how easily it can be molded into different shapes.在创造铝箔造型的过程中,需要熟练的工匠运用各种工具和技术来精心操纵铝箔。
这个过程的第一步是选择适当的铝箔厚度。
这一步至关重要,因为铝箔的厚度将决定它可以被塑造成不同形状有多容易。
Once the appropriate thickness of aluminum foil has been selected, the next step is to cut the foil into the desired shape. This can be done using sharp scissors or a cutting tool specifically designed for working with aluminum foil. Care must be taken during this step to ensure that the edges of the foil are clean and precise, as any imperfections will be visible in the final product.一旦选定了合适的铝箔厚度,下一步就是将铝箔切割成所需的形状。
中高压化成箔生产工艺流程

中高压化成箔生产工艺流程英文回答:High Voltage Electrochemical Capacitor Foil Manufacturing Process.The manufacturing process of high voltage electrochemical capacitor foil involves several key steps:1. Slitting and Annealing.Aluminum sheets are slit into narrower strips (foil).The foil is annealed to soften it and improve its flexibility.2. Etching.The foil surface is etched with a chemical solution to create a porous structure.This porous structure increases the surface area and capacitance of the foil.3. Anodizing.The foil is electrochemically anodized in an electrolyte solution.This process forms a thin, insulating oxide layer on the foil surface.4. Formation.The anodized foil is subjected to a voltage that causes the oxide layer to grow further.The thickness of the oxide layer determines the voltage rating of the capacitor.5. Impregnation.The foil is impregnated with an electrolyte, such as boric acid or potassium tetraborate.The electrolyte fills the pores in the oxide layer and provides conductivity.6. Slitting and Winding.The impregnated foil is slit into smaller strips.These strips are wound into capacitors using a winding machine.7. Sealing.The capacitors are sealed to protect them from moisture and contaminants.This can be done using various methods such as epoxy encapsulation or hermetic sealing.8. Testing.The capacitors undergo rigorous testing to ensure their performance meets specifications.Tests include capacitance, voltage rating, leakage current, and equivalent series resistance (ESR).中文回答:中高压化成箔生产工艺流程。
tinfoil使用指南

tinfoil使用指南Tinfoil是一款用于任天堂游戏机的软件,以下是Tinfoil使用指南:1. 下载所需文件:Tinfoil-最新版,将压缩包里的swich文件夹全部放到TF卡的根目录(放心覆盖)。
2. 进入相册,启动Tinfoil,会自动安装Tinfoil程序到桌面。
3. 设置中文:左侧进入Options,进入Region,按A键确认后,往上翻找,找到HK,按A键确认区域。
进入Language,选择zh,按A键确认程序语言,然后返回左侧菜单,耐心等待重载结束,返回桌面,关闭程序,通过桌面图标再次启动进入Tinfoil,即可发现界面已经变为中文。
4. 基本设置:左侧进入Options,然后选择假连接任天堂线上账号即可。
5. 免签设置:左侧进入Options,下翻,找到安装未签署代码,按A键进入,输入密码:上上下下左右左右BA,启用免签功能。
6. xci 设置:下翻Options选项,找到从xci安装更新和从xci安装DLC,都设置为是。
7. USB安装游戏:Tinfoil启动后,只需要将USB线连接Swtich和电脑,即会自动启用MTP模式,在主控台会输出MTP run字样。
之后,电脑上就会出现switch设备,进入后,如果需要USB传输文件,进入microSD 卡即可当优盘操作内存卡。
安装游戏,则进入安装,将要安装的游戏文件拖拽到Drag nsp, NSZ, xciand XCZ files here to install,即可自动通过USB安装游戏到设备中。
8. 重置版本:确保需要修改的游戏已经安装到设备中。
启动Tinfoil,已安装菜单的右侧,选中要处理的游戏图标,按X键,进入卸载功能,卸载高版本的补丁或者DLC,按Y键,重置补丁所需系统版本,之后即可正常启动旧版本游戏。
allegro foil叠法
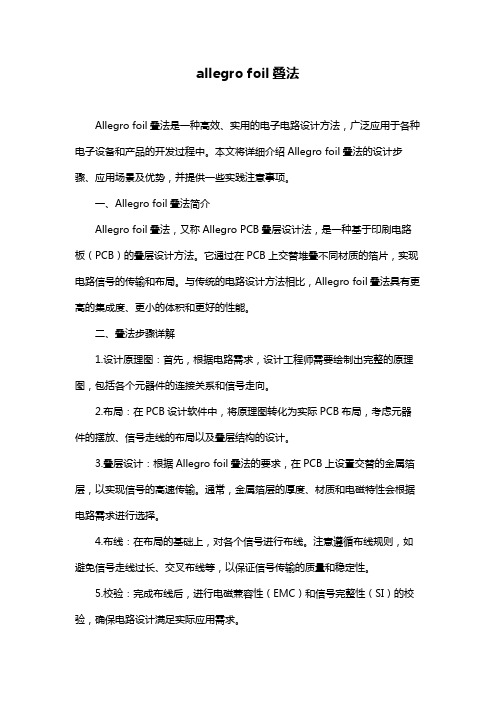
allegro foil叠法Allegro foil叠法是一种高效、实用的电子电路设计方法,广泛应用于各种电子设备和产品的开发过程中。
本文将详细介绍Allegro foil叠法的设计步骤、应用场景及优势,并提供一些实践注意事项。
一、Allegro foil叠法简介Allegro foil叠法,又称Allegro PCB叠层设计法,是一种基于印刷电路板(PCB)的叠层设计方法。
它通过在PCB上交替堆叠不同材质的箔片,实现电路信号的传输和布局。
与传统的电路设计方法相比,Allegro foil叠法具有更高的集成度、更小的体积和更好的性能。
二、叠法步骤详解1.设计原理图:首先,根据电路需求,设计工程师需要绘制出完整的原理图,包括各个元器件的连接关系和信号走向。
2.布局:在PCB设计软件中,将原理图转化为实际PCB布局,考虑元器件的摆放、信号走线的布局以及叠层结构的设计。
3.叠层设计:根据Allegro foil叠法的要求,在PCB上设置交替的金属箔层,以实现信号的高速传输。
通常,金属箔层的厚度、材质和电磁特性会根据电路需求进行选择。
4.布线:在布局的基础上,对各个信号进行布线。
注意遵循布线规则,如避免信号走线过长、交叉布线等,以保证信号传输的质量和稳定性。
5.校验:完成布线后,进行电磁兼容性(EMC)和信号完整性(SI)的校验,确保电路设计满足实际应用需求。
6.制作与测试:将设计好的PCB发送至生产厂家进行制作,并对成品进行性能测试,验证电路设计的正确性。
三、应用场景及优势1.高频高速电路:Allegro foil叠法适用于高频高速电路的设计,如射频电路、数据通信电路等,能有效减小信号传输的损耗和延迟。
2.紧凑型设备:在体积有限的设备中,Allegro foil叠法可以实现更高密度的电路布局,提高设备性能。
3.电磁兼容性要求严格的场合:Allegro foil叠法通过交替叠层,可以有效抑制电磁干扰,提高电路的稳定性。