温度控制流程图
(完整版)温度控制系统设计

温度控制系统设计目录第一章系统方案论证 (3)1.1总体方案设计 (3)1.2温度传感系统 (3)1.3温度控制系统及系统电源 (4)1.4单片机处理系统(包括数字部分)及温控箱设计 (4)1.5PID 算法原理 (5)第二章重要电路设计 (7)2.1温度采集 (7)2.2温度控制 (7)第三章软件流程 (8)3.1基本控制 (8)3.2PID 控制 (9)3.3时间最优的 PID 控制流程图 (10)第四章系统功能及使用方法 (11)4.1温度控制系统的功能 (11)4.2温度控制系统的使用方法 (11)第五章系统测试及结果分析 (11)5.1 硬件测试 (11)5.2软件调试 (12)第六章进一步讨论 (12)参考文献 (13)致谢........................................... 错误 !未定义书签。
摘要:本文介绍了以单片机为核心的温度控制器的设计,文章结合课题《温度控制系统》,从硬件和软件设计两方面做了较为详尽的阐述。
关键词:温度控制系统PID 控制单片机Abstract: This paper introduces a temperature control system that is based on the single-chip microcomputer.The hard ware compositionand software design are descried indetail combined with the projectComtrol System of Temperature.PID control Keywords: Control system of temperatureSingle-chip Microcomputer引言:温度控制是工业生产过程中经常遇到的过程控制,有些工艺过程对其温度的控制效果直接影响着产品的质量,因而设计一种较为理想的温度控制系统是非常有价值的。
过程控制仪表及控制系统课后习题答案
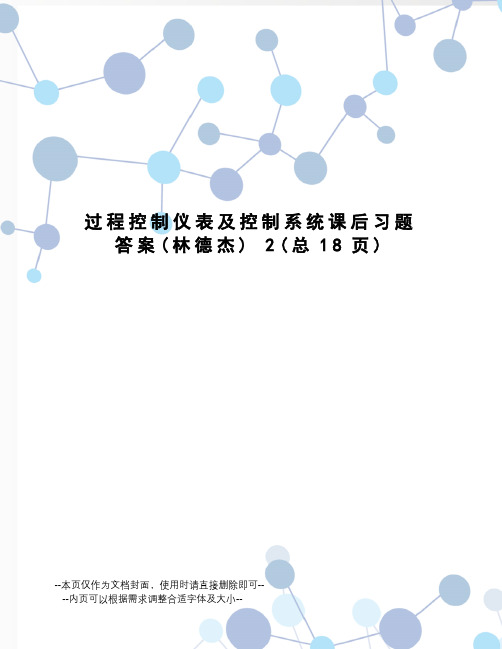
过程控制仪表及控制系统课后习题答案(林德杰)2(总18页)--本页仅作为文档封面,使用时请直接删除即可----内页可以根据需求调整合适字体及大小--lxc第一章思考题与习题1-2 图为温度控制系统,试画出系统的框图,简述其工作原理;指出被控过程、被控参数和控制参数。
解:乙炔发生器中电石与冷水相遇产生乙炔气体并释放出热量。
当电石加入时,内部温度上升,温度检测器检测温度变化与给定值比较,偏差信号送到控制器对偏差信号进行运算,将控制作用于调节阀,调节冷水的流量,使乙炔发生器中的温度到达给定值。
系统框图如下:被控过程:乙炔发生器被控参数:乙炔发生器内温度控制参数:冷水流量1-3 常用过程控制系统可分为哪几类答:过程控制系统主要分为三类:1. 反馈控制系统:反馈控制系统是根据被控参数与给定值的偏差进行控制的,最终达到或消除或减小偏差的目的,偏差值是控制的依据。
它是最常用、最基本的过程控制系统。
2.前馈控制系统:前馈控制系统是根据扰动量的大小进行控制的,扰动是控制的依据。
由于没有被控量的反馈,所以是一种开环控制系统。
由于是开环系统,无法检查控制效果,故不能单独应用。
3. 前馈-反馈控制系统:前馈控制的主要优点是能够迅速及时的克服主要扰动对被控量的影响,而前馈—反馈控制利用反馈控制克服其他扰动,能够是被控量迅速而准确地稳定在给定值上,提高控制系统的控制质量。
3-4 过程控制系统过渡过程的质量指标包括哪些内容它们的定义是什么哪些是静态指标哪些是动态质量指标答:1. 余差(静态偏差)e :余差是指系统过渡过程结束以后,被控参数新的稳定值y(∞)与给定值c 之差。
它是一个静态指标,对定值控制系统。
希望余差越小越好。
2. 衰减比n:衰减比是衡量过渡过程稳定性的一个动态质量指标,它等于振荡过程的第一个波的振幅与第二个波的振幅之比,即:n <1系统是不稳定的,是发散振荡;n=1,系统也是不稳定的,是等幅振荡;n >1,系统是稳定的,若n=4,系统为4:1的衰减振荡,是比较理想的。
管式加热炉温度-流量串级控制系统的设计

管式加热炉温度-流量串级控制系统的设计1方案选定管式加热炉是炼油、化工生产中的重要装置之一,它的任务是把原料油加热到一定温度,以保证下道工序的顺利进行。
因此,常选原料油出口温度1tθ()为被控参数、燃料流量为控制变量,构成如图1-1所示的温度控制系统,控制系统框图如图1-2所示。
影响原料油出口温度1tθ()的干扰有原料油流量1()f t、原料油入口温度2()f t、燃料压力3()f t、燃料压力4()f t等。
该系统根据原料油出口温度1tθ()变化来控制燃料阀门开度,通过改变燃料流量将原油出口温度控制在规定的数值上,是一个简单控制系统。
图1-1 管式加热炉出口单回路温度控制系统图1-2 管式加热炉出口温度单回路控制系统框图由图1-1可知,当燃料压力或燃料热值变化时,先影响炉膛温度,然后通过传热过程逐渐影响原料油的出口温度。
从燃料流量变化经过三个容量后,才引起原料油出口温度变化,这个通道时间常数很大,约有15min ,反应缓慢。
而温度调节器1T C 是根据原料油的出口温度1()t θ与设定值的偏差进行控制。
当燃料部分出现干扰后,图1-1所示的控制系统并不能及时产生控制作用,克服干扰对被控参数1()t θ的影响,控制质量差。
当生产工艺对原料油出口温度1()t θ要求严格时,上述简单控制系统很难满足要求。
燃料在炉膛燃烧后,首先引起炉膛温度2()t θ变化,再通过炉膛与原料油的温差将热量传给原料油,中间还要经过原料油管道管壁。
显然,燃料量变化或燃料热值变化,首先使炉膛温度发生改变。
如果以炉膛温度作为被控参数组成单回路控制系统,会使控制通道容量滞后减少,时间常数约为3min ,对来自燃料的干扰3()f t 、4()f t 的控制作用比较及时,对应的控制系统如图1-3所示。
系统框图如图1-4。
但问题是炉膛温度2()t θ毕竟不能真正代表原料油出口温度1()t θ,即使炉膛温度恒定,原料油本身的流量或入口温度变化仍会影响原料油出口温度,图1-3 管式加热炉炉膛温度控制系统这是因为来自原料油的干扰1()f t 、2()f t 并没有包含在图1-4所示的控制系统(反馈回路)之内,控制系统不能克服1()f t 、2()f t 对原料油出口温度的影响,控制效果仍达不到生产工艺要求。
基于51单片机的温度控制系统设计

基于 51 单片机的水温自动控制系统引言在现代的各种工业生产中,不少地方都需要用到温度控制系统。
而智能化的控制系统成为一种发展的趋势.本文所阐述的就是一种基于 89C51 单片机的温度控制系统。
本温控系统可应用于温度范围30℃到96℃。
设计并制作一水温自动控制系统,可以在一定范围(30℃到96℃)内自动调节温度,使水温保持在一定的范围(30℃到96℃)内。
(1) 利用摹拟温度传感器检测温度,要求检测电路尽可能简单。
(2) 当液位低于某一值时,住手加热。
(3) 用 AD 转换器把采集到的摹拟温度值送入单片机。
(4) 无竞争—冒险,无颤动。
(1) 温度显示误差不超过1℃.(2) 温度显示范围为0℃—99℃。
(3) 程序部份用 PID 算法实现温度自动控制。
(4) 检测信号为电压信号。
根据设计要求和所学的专业知识,采用 AT89C51 为本系统的核心控制器件。
AT89C51 是一种带4K 字节闪存可编程可擦除只读存储器的低电压,高性能CMOS 8 位微处理器。
其引脚图如图1 所示。
显示模块主要用于显示时间,由于显示范围为0~99℃,因此可采用两个共阴的数码管作为显示元件.在显示驱动电路中拟订了两种设计方案:方案一:采用静态显示的方案采用三片移位寄存器 74LS164 作为显示电路,其优点在于占用主控系统的 I/O 口少,编程简单且静态显示的内容无闪烁,但电路消耗的电流较大。
方案二:采用动态显示的方案由单片机的 I/O 口直接带数码管实现动态显示, 占用资源少,动态控制节省了驱动芯片的成本,节省了电,但编程比较复杂,亮度不如静态的好。
由于对电路的功耗要求不大,因此就在尽量节省 I/O 口线的前提下选用方案一的静态显示.图 1 AT89C51 引脚图1 温度检测:有选用 AD590 和LM35D 两种温度传感器的方案,但考虑到两者价格差距较大,而本系统中对温度要求的精度不很高,于是选用比较便宜 LM35D。
换热器温度控制系统

1.E-0101B混合加热器设计为确保混合加热器(E-0101B)中MN(亚硝酸甲酯),CO(一氧化碳)的出口温度为408K,选用0.68Mpa,408K的加热蒸汽加热入口温度为294K的工艺介质。
为保证生成物的产量,质量,及最终生成物的转化率,且工艺介质较稳定,蒸汽源压力较小,变化不大,因此针对此实际情况,最后确定设计一个换热器的反馈控制方案。
1.1换热器概述换热器工作状态如何,可用几项工作指标加以衡量。
常用的工作指标主要有漏损率、换热效率和温度效率。
它们比较全面的说明了换热器的特点和工作状态,在生产和科学试验中了解这些指标,对于换热器的管理和改进都是必不可少的。
换热器是将热流体的部分热量传递给冷流体的设备,又称热交换器。
换热器在化工、石油、动力、食品及其它许多工业生产中占有重要地位,其在化工生产中换热器可作为加热器、冷却器、冷凝器、蒸发器和再沸器等,应用广泛。
换热器是一种在不同温度的两种或两种以上流体间实现物料之间热量传递的节能设备,是使热量由温度较高的流体传递给温度较低的流体,使流体温度达到流程规定的指标,以满足工艺条件的需要,同时也是提高能源利用率的主要设备之一。
1.2换热器的分类适用于不同介质、不同工况、不同温度、不同压力的换热器,结构型式也不同,换热器的具体分类如下:一按传热原理分类:间壁式换热器,蓄热式换热器,流体连接间接式换热器,直接接触式换热器,复式换热器二按用途分类:加热器,预热器,过热器,蒸发器三、按结构分类:浮头式换热器,固定管板式换热器,U形管板换热器,板式换热器等此设计要求是将进料温度都为297.99K的MN(亚硝酸甲酯)和CO(一氧化碳)加热到出口温度为473K,所以我们经过调查研究,综合比较之后选择了管壳式(又称列管式) 换热器。
管壳式换热器主要有壳体、管束、管板和封头等部分组成,壳体多呈圆形,内部装有平行管束或者螺旋管,管束两端固定于管板上。
在管壳换热器内进行换热的两种流体,一种在管内流动,其行程称为管程;一种在管外流动,其行程称为壳程。
WINCC组态软件温度控

指导教师: 指导教师: 毛先萍 学生姓名: 学生姓名:钱飞 专 业:过程装备与控制工程
Wincc的简介 Wincc的简介
近代工业中Wincc的应 近代工业中Wincc的应 用以及发展 多功能性 多语言支持,全球通 用 提供通道 不受限制 实例证明 注意事项 分散过程控制的特点 工业生产过程的计算 机控制系统
工业生产过程的计算机控制系统
• 随着计算机的进步、工业生产工艺过程控制要求的提高和生产管理的
完善而不断发展。目前工业计算机控制系统按结构层次基本上划分为: 直接数字控制(DDC)系统、监督控制(SCC)系统、集散型控制系 直接数字控制(DDC)系统、监督控制(SCC)系统、集散型控制系 统(DCS)、递阶控制系统(HCS)和现场总线控制系统(FCS)等 统(DCS)、递阶控制系统(HCS)和现场总线控制系统(FCS)等 几种,其中DCS是融DDC系统、SCC系统及整个工厂的生产管理为一 几种,其中DCS是融DDC系统、SCC系统及整个工厂的生产管理为一 体的高级控制系统,该系统克服了其他控制系统中存在的“危险集中” 问题,具有较高的可靠性和实用性。但是,为了进一步适合现场的需 要,DCS也在不断更新换代,近年来,集计算机、通信、控制三种技 要,DCS也在不断更新换代,近年来,集计算机、通信、控制三种技 术为一体的第5 术为一体的第5代过程控制体系结构,即现场总线控制系统,成为国 内外计算机过程控制系统一个重要的发展方向。本文对各种工业控制 计算机系统的结构层次和特点以及发展方向作一分析研究。
表2-1
表2-1 实验值与实际值对比(单位:摄氏度) 实 际 值 测 量 值 偏 差 0 10 20 30 40 50 60 70 80
温度控制系统(课程设计)

长安大学《单片机原理及接口技术》课程设计(简易温度控制系统)专业:电气工程及其自动化学号: 2804060132姓名:任晴利指导老师:段晨东时间: 2008.12.22~2009.01.03目录目录。
题目。
摘要。
需求分析。
方案比较。
硬件设计。
硬件电路设计。
总体电路设计。
软件设计。
调试及结果分析。
附录1 电路程序。
附录2 电路总图。
题目:简易温度控制系统一.任务设计并制作一个简易的单片机温度自动控制系统(见图一)。
控制对象为自定。
图一 恒温箱控制系统二.要求设计要求如下(1)温度设定范围为40℃~90℃,最小区分度为1℃(2)用十进制数码显示实际温度。
(3)被控对象温度采用发光二极管以光柱形式和数码形式显示。
(4)温度控制的静态误差≤2℃。
扩充功能:控制温度可以在一定范围内设定,并能实现自动调整,以保持设定的温度基本保持不变(测量温度时只要求在现场任意设置一个检测点)。
恒温箱 执行器 可编程 控制器 显示器 变送器 设置键盘 电源 220V AC 温度传感器摘要本系统以A T89S52单片机芯片为核心,组成温度测量和控制系统,采用DS18B20数字温度传感器对温度进行实时采样,并将测量结果用数码管实显示,可以运用键盘按钮对温度进行设定,并且驱动加热器或制冷器将温度调整到设定温度,其功能完善,人机界面良好,可靠性高,AbstractThe system to single-chip AT89S52 chip as the core, the composition of the control of temperature control system of the adoption of digital temperature sensor DS18B20 temperature sampling, real-time display with digital temperature control, you can use the keyboard for temperature regulation, the use of heater and cooler temperature adjustments to improve its functions, a good man-machine interface, high reliability一、需求分析根据题目的具体要求,经过阅读思考,可对题目的具体任务、功能、技术指标等作如下分析。
热交换器温度控制系统课程设计

热交换器温度控制系统一.控制系统组成由换热器出口温度控制系统流程图1可以看出系统包括换热器、热水炉、控制冷流体的多级离心泵,变频器、涡轮流量传感器、温度传感器等设备。
图1换热器出口温度控制系统流程图控制过程特点:换热器温度控制系统是由温度变送器、调节器、执行器和被控对象(出口温度)组成闭合回路。
被调参数(换热器出口温度)经检验元件测量并由温度变送器转换处理获得测量信号c,测量值c与给定值r的差值e送入调节器,调节器对偏差信号e进行运算处理后输出控制作用u。
二、设计控制系统选取方案根据控制系统的复杂程度,可以将其分为简单控制系统和复杂控制系统。
其中在换热器上常用的复杂控制系统又包括串级控制系统和前馈控制系统。
对于控制系统的选取,应当根据具体的控制对象、控制要求,经济指标等诸多因素,选用合适的控制系统。
以下是通过对换热器过程控制系统的分析,确定合适的控制系统。
换热器的温度控制系统工艺流程图如图2所示,冷流体和热流体分别通过换热器的壳程和管程,通过热传导,从而使热流体的出口温度降低。
热流体加热炉加热到某温度,通过循环泵流经换热器的管程,出口温度稳定在设定值附近。
冷流体通过多级离心泵流经换热器的壳程,与热流体交换热后流回蓄电池,循环使用。
在换热器的冷热流体进口处均设置一个调节阀,可以调节冷热流体的大小。
在冷流体出口设置一个电功调节阀,可以根据输入信号自动调节冷流体流量的大小。
多级离心泵的转速由便频器来控制。
换热器过程控制系统执行器的选择考虑到电动调节阀控制具有传递滞后大,反应迟缓等缺点,根具离心泵模型得到通过控制离心泵转速调节流量具有反应灵敏,滞后小等特点,而离心泵转速是通过变频器调节的,因此,本系统中采用变频器作为执行器。
温度控制流程图

初始化
启动温度检测开中断源自返回取数译码(七段码)
送显示 位计数清零 加键? 位计数=3? 标志位 =1? 延时1(<13mS) 加标志位清零 循环计数+1 循环计数器256溢 出归零 循环计数 器=0? AD标志=0? 加计数器清零 加计数器 >3? +3 标志位(3)=1 标志位=1 加计数器+1
位计数+1
主程序 调用显示与延时子程序 初始化 取数 开中断 译码(七段码)
调用显示与延时子程序(每 位不超过13毫秒)
送显示
延时(<13mS) 位计数+1 返回 位计数=3? 位计数清零
温度检测完成? (标志位) 读温度
中断子程序
启动温度检测 高于设定值2度? 关断 返回
低于设定值2度? 关断
主程序
中断子程序
延时2
读AD
+1 200上限 减键?
>+2度? 关断 实现没256*40ms显 示一次预制温度
减标志位清零 延时3
标志位 =1? 减计数器+1 标志位=1
<-2度? 开通
减计数器清零
减计数器 >3? -3 -1 0下限
延时4
热交换器温度控制系统课程设计

热交换器温度控制系统一.控制系统组成由换热器出口温度控制系统流程图1可以看出系统包括换热器、热水炉、控制冷流体的多级离心泵,变频器、涡轮流量传感器、温度传感器等设备。
图1换热器出口温度控制系统流程图控制过程特点:换热器温度控制系统是由温度变送器、调节器、执行器和被控对象(出口温度)组成闭合回路。
被调参数(换热器出口温度)经检验元件测量并由温度变送器转换处理获得测量信号c,测量值c与给定值r的差值e送入调节器,调节器对偏差信号e进行运算处理后输出控制作用u。
二、设计控制系统选取方案根据控制系统的复杂程度,可以将其分为简单控制系统和复杂控制系统。
其中在换热器上常用的复杂控制系统又包括串级控制系统和前馈控制系统。
对于控制系统的选取,应当根据具体的控制对象、控制要求,经济指标等诸多因素,选用合适的控制系统。
以下是通过对换热器过程控制系统的分析,确定合适的控制系统。
换热器的温度控制系统工艺流程图如图2所示,冷流体和热流体分别通过换热器的壳程和管程,通过热传导,从而使热流体的出口温度降低。
热流体加热炉加热到某温度,通过循环泵流经换热器的管程,出口温度稳定在设定值附近。
冷流体通过多级离心泵流经换热器的壳程,与热流体交换热后流回蓄电池,循环使用。
在换热器的冷热流体进口处均设置一个调节阀,可以调节冷热流体的大小。
在冷流体出口设置一个电功调节阀,可以根据输入信号自动调节冷流体流量的大小。
多级离心泵的转速由便频器来控制。
换热器过程控制系统执行器的选择考虑到电动调节阀控制具有传递滞后大,反应迟缓等缺点,根具离心泵模型得到通过控制离心泵转速调节流量具有反应灵敏,滞后小等特点,而离心泵转速是通过变频器调节的,因此,本系统中采用变频器作为执行器。
图2换热器的温度控制系统工艺流程图引起换热器出口温度变化的扰动因素有很多,简要概括起来主要有:(1)热流体的流量和温度的扰动,热流体的流量主要受到换热器入口阀门的开度和循环泵压头的影响。
过程控制第5章简单控制系统设计
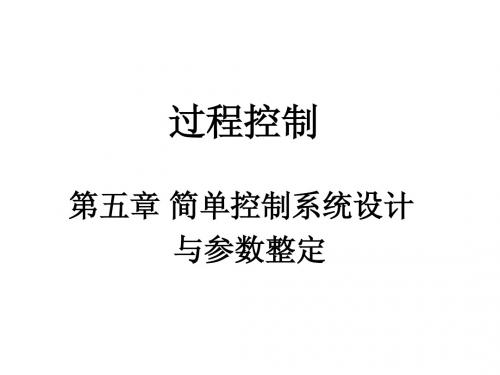
3、干扰通道动态特性的影响
干扰通道传函:
W f (s)
Kf Tf s 1
e
f s
干扰通道时间常数 Tf ? Tf越大越好,干扰对被控变量的影响越缓慢,越 有利于改善控制质量 干扰通道滞后时间τ
f
无纯滞后 有纯滞后
?
干扰通道的纯滞后τ f仅使干扰对被控变量的 影响推迟了时间τ f ,不会影响控制质量
5.1 简单控制系统的构成
PC 101
压力控制系统
压力控制系统流程图
被控变量:水泵出口压力。 控制变量:旁路流量。
5.1.2 控制系统的工程表示及方框图
工艺控制流程图: 管道、仪表流程图 在工艺设计 给出的流程 图上,按流 程顺序标注 出相应的测 量点、控制 点、控制系 统及自动信 号。
(1)图形符号
GP(S)
蒸 汽
fP
1 100S+1
1 100S+1
e-3S
e-2S (8.5S+1)(8.5S+1)(8.5S+1)
T1
乳化物干燥系统示意图
乳化物干燥系统被控对象对象方块图
fQ
fW 1 100S+1 e-3S e-2S (8.5S+1)(8.5S+1)(8.5S+1) T1
控制方案:
fQ
fP
1 100S+1
Y(S) Km TmS+1 Z(S) U(S) (TdS+1)
测量、变送装置与微分器连接示意图
U ( s) 若Td Tm时 : Km Y ( s)
但是,微分环节会放大测量、变送回路的高频噪声,使得系统稳定 性变差,因此,要合理使用。
2. 测量信号的处理
石英晶体温度传感器温度控制简介

石英晶体温度传感器温度控制简介蒋秀兰(青岛橡胶集团有限责任公司 266041) 随着科学技术的飞速发展,各种检测监控技术也发生了很大变化。
在轮胎生产中,传统的温度检测方法是采用铂电阻、铂2铑电阻等作为测温元件。
这类检测元件虽然具有精度高等优点,但其成本高,不适于周围的恶劣环境,易发生损坏,而且其属于模拟式传感器,输出信号要进行数据处理,数字显示必须通过模/数转换,电路复杂,误差增大。
因此,在实际应用中定性强、抗干扰性强的温度传感器以替代该类检测元件。
1 温控机理本研究运用石英晶体温度传感器和8031单片机进行温度的测量和监控。
111 石英晶体温度传感器石英晶体温度传感器是一种以频率为输出信号的数字式传感器,具有很高的稳定性、准确度和良好的线性。
本研究采用激光焊接,温度适用范围为0~200℃,另外,石英晶体的谐振性与其切型有很大关系。
所谓切型是将石英晶体按一定方位角切成薄片,再在薄片两侧加装电极及引线,切型不同,谐振器的特性也不相同。
在此选定石英晶体为LC切型,设定其频率分辨率为1Hz,温度分辨率为01001℃,则温度灵敏度为1000Hz·℃-1,LC切型的基本谐振频率(f)为:f=10003514×10-6图1 测温及数据处理图2 温度控制流程图QD—切断加热电路;J T—接通加热电路403 轮 胎 工 业 1999年第19卷有许多不利因素。
为在恶劣的生产环境中实现温度的准确测量和自动控制,需要寻找一种稳=28(MHz)式中,3514×10-6为一次温度因数。
用此方法制成的温度传感器的回归方程为:f=1015θ+28014707式中 θ———温度,℃。
该传感器灵敏度为1015Hz·℃-1,线性误差为±01078℃,可很好地满足生产的要求。
112 信号处理及温度控制利用石英晶体传感器进行测温,数据采集与处理过程见图1。
由于8031单片机具有信号采集、处理、控制等多种功能,因此石英晶体谐振器采集到的信号经过混频、滤波、整形放大等过程[1]输送到8031单片机上。
蔬菜大棚温度控制系统设计
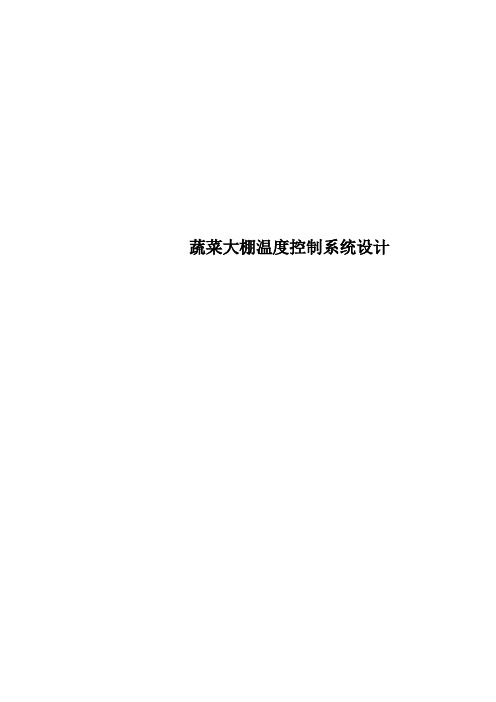
蔬菜大棚温度控制系统设计太原科技大学毕业设计(论文)目录摘要.................................................................................................................................................... ABSTRACT ...................................................................................................................................... 第1章绪论 01.1 选题背景 01.2 国内发展现状及水平 01.3 设计目的及意义 01.4 本章小结 (1)第2章系统功能需求分析及方案选择 (2)2.1 设计要求 (2)2.2 系统的功能需求分析 (2) (2) (4)2.3 工作原理 (3)2.4 控制方案 (3) (3) (5) (4) (5)2.5 系统控制方案的确定 (6)2.6 本章小结 (7)第3章硬件电路设计 (9)3.1主控制器AT89C51单片机电路 (9) (9) (9)3.2 温度采集电路 (10) (10) (11) (12)3.4键盘输入模块电路 (13) (13)3.5 机械控制电路模块 (14) (15) (15)3.6 蜂鸣器报警电路 (16)3.7 电源输入部分 (17)3.8 本章小结 (17)第4章系统软件设计 (19)4.1 系统主程序流程 (19)4.2 DS18B20测温读取子程序 (20)4.3 LCD1602显示子程序 (21)4.4 机械控制子程序 (21)4.5 定时器子程序 (22)4.6 本章小结 (23)第5章系统调试与仿真 (26)5.1 系统调试 (26)5.2 系统仿真 (26)5.3仿真结果 (27)第6章结论 (27)致谢 (29)参考文献 (31)附录 (33)附录1 硬件电路原理图 (33)附录2 元件清单表 (34)附录3 源程序清单 (35)摘要本设计完成了蔬菜大棚温度控制系统的系统设计。
51单片机设计数字温度计(流程图+源码+实物图片)
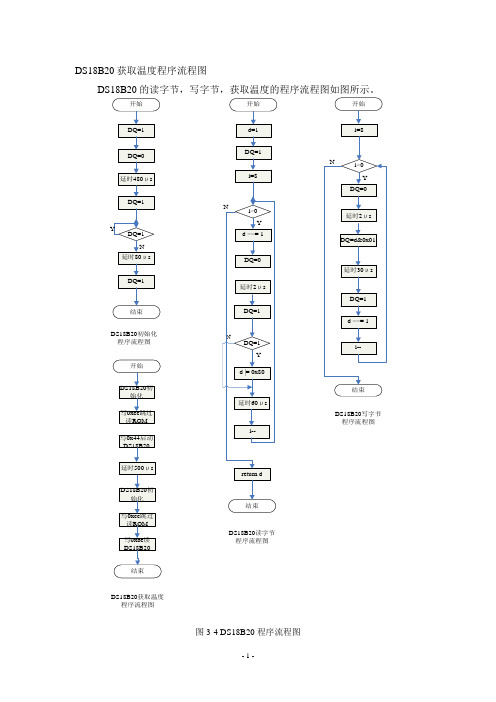
DS18B20获取温度程序流程图DS18B20的读字节,写字节,获取温度的程序流程图如图所示。
DS18B20初始化程序流程图DS18B20读字节程序流程图DS18B20写字节程序流程图DS18B20获取温度程序流程图图3-4 DS18B20程序流程图显示程序设计显示电路是由四位一体的数码管来实现的。
由于单片机的I/O 口有限,所以数码管采用动态扫描的方式来进行显示。
程序流程图如图所示。
图显示程序流程图按键程序设计按键是用来设定上下限报警温度的。
具体的程序流程图如图所示。
N图按键程序流程图附1 源程序代码/********************************************************************* 程序名; 基于DS18B20的测温系统* 功能:实时测量温度,超过上下限报警,报警温度可手动调整。
K1是用来* 进入上下限调节模式的,当按一下K1进入上限调节模式,再按一下进入下限* 调节模式。
在正常模式下,按一下K2进入查看上限温度模式,显示1s左右自动* 退出;按一下K3进入查看下限温度模式,显示1s左右自动退出;按一下K4消除* 按键音,再按一下启动按键音。
在调节上下限温度模式下,K2是实现加1功能,* K1是实现减1功能,K3是用来设定上下限温度正负的。
* 编程者:ZPZ* 编程时间:2009/10/2*********************************************************************/#include<AT89X52.h> //将AT89X52.h头文件包含到主程序#include<intrins.h> //将intrins.h头文件包含到主程序(调用其中的_nop_()空操作函数延时)#define uint unsigned int //变量类型宏定义,用uint表示无符号整形(16位)#define uchar unsigned char //变量类型宏定义,用uchar表示无符号字符型(8位)uchar max=0x00,min=0x00; //max是上限报警温度,min是下限报警温度bit s=0; //s是调整上下限温度时温度闪烁的标志位,s=0不显示200ms,s=1显示1s左右bit s1=0; //s1标志位用于上下限查看时的显示void display1(uint z); //声明display1()函数#include"ds18b20.h" //将ds18b20.h头文件包含到主程序#include"keyscan.h" //将keyscan.h头文件包含到主程序#include"display.h" //将display.h头文件包含到主程序/***********************主函数************************/void main(){beer=1; //关闭蜂鸣器led=1; //关闭LED灯timer1_init(0); //初始化定时器1(未启动定时器1)get_temperature(1); //首次启动DS18B20获取温度(DS18B20上点后自动将EEPROM中的上下限温度复制到TH和TL寄存器)while(1) //主循环{keyscan(); //按键扫描函数get_temperature(0); //获取温度函数keyscan(); //按键扫描函数display(temp,temp_d*0.625);//显示函数alarm(); //报警函数keyscan(); //按键扫描函数}}/********************************************************************* 程序名; __ds18b20_h__* 功能:DS18B20的c51编程头文件* 编程者:ZPZ* 编程时间:2009/10/2* 说明:用到的全局变量是:无符号字符型变量temp(测得的温度整数部分),temp_d* (测得的温度小数部分),标志位f(测量温度的标志位‘0’表示“正温度”‘1’表* 示“负温度”),标志位f_max(上限温度的标志位‘0’表示“正温度”、‘1’表* 示“负温度”),标志位f_min(下限温度的标志位‘0’表示“正温度”、‘1’表* 示“负温度”),标志位w(报警标志位‘1’启动报警‘0’关闭报警)。
基于MCGS和S7-1200的温度控制系统设计

(4)选 择“ 单 回 路 控 制 实 验 ”下 拉 菜 单 中 的“ 温 度 控 制 实 验 ”。
图7 控制界面图 (5)点击“参数设置”,出现如图8所示的界面。 将 AI0 量 程 设置 为 0 ~100,点 击 退 出 ,参 数 设 置 完毕。 观察锅炉水标,水位在水标的2/3以上,将手动阀 门1V1关闭。 在控制柜面板上打开加热器开关。 设定初值和PID各个系数并选择PLC控制方式。 记录的温度曲线如图9所示。 由图9可以看出,温度曲线趋于稳定的速度很快, 并且波动小,可以精确有效地控制锅炉内温度。
变矩 性 能一 般 由 转 速 比 i、变 矩比 K 两 个 指 标 来 评 定 ,其 中 i与K的值越大,变矩器的性能越好。但是二者不能够同时取到 最大值,所以尽可能在其中一个参数(i或K)保持不变时,尽可 能增大另一参数。 3.2 经济性能
经 济 性 能是 指 液 力变 矩 器 在 传 递 能 量 过 程 中 的 效 率 ,它 可以用无因次效率特性浊=(f i)来表示。
图2 温度控制流程图 其 中 PLC的 核 心 程 序 包 括 PID 算 法 程 序 和 I/O 模 块 程 序 , PID梯形图如图3所示,I/O模块梯形图如图4、图5所示。
图1 温度控制系统工艺流程图
2 温度控制系统功能实现
S7-1200系列是一款功能强大、成本低廉的可编程逻辑控 制 器 ,是 S7-200 的升 级 版 ,延 续 了 200 紧 凑 型 设 计 的 同 时 节 省 了控制面板的空间。S7-1200还进行了功能上的升级,在研发 过程中充分考虑了系统、控制器、人机交互界面的完美协调, 因此它可以满足各种中小型自动化系统的要求[1]。MCGS是基 于 Windows平 台 的 组 态 软 件 系 统 ,它 可 以 快 速 构 造 并 生 成 上 位机监控系统,具有功能完善、操作简便、可视性好等特点[2]。
高三化学一轮复习温度的控制在工艺流程图中的应用

2019-2020年一轮复习温度的控制在工艺流程图中的应用温度控制是影响化学反应的一项重要条件,对产品质量、生产效率、安全生产及节约能源等方面有着重要的意义。
温度条件的选择,可从物质性质和反应原理两个角度角度:一:物质的性质1. 从原料的物理、化学性质出发,考虑物质的挥发性和热稳定性、易水解、氧化还原性等特性。
①用到双氧水、氨水、铵盐、硝酸盐等易分解的物质,控温的目的是防止物质分解;②产物或者反应物中含有醛类、酚类等物质,控温的目的是防止其被氧化;②实验室保存或者制备液溴、一溴乙烷等沸点较低物质,需要加冰水或冷冻,目的是防止物质的挥发;④海水提Br2过程中,出溴口的温度控制在80-90℃,目的是要使Br2挥发出来而又减少水蒸气混入Br2中。
2. 从物质的溶解度出发,考虑温度对晶体析出的影响以及对溶解在溶液中气体(如氧气、氯气)的影响。
二:化学反应原理3. 从化学动力学角度出发,考虑温度对反应速率或固体溶解速率的影响;如溶液中制备物质,常使用加热的方法加快反应速率4. 从热力学角度分析,考虑温度对反应平衡转化率的影响;如制取乙酸乙酯的实验中,及时分离乙酸乙酯,有利于乙酸乙酯产率的提高5. 从催化剂的使用出发,考虑温度与催化剂活性的相关性;工业合成氨选择的温度是500℃左右,原因之一就是使催化剂的活性达到最高,生产效率最高6. 从反应的复杂性角度分析,考虑副反应的发生;如实验室制取乙烯、制硝基苯,控制温度,都是防止发生副反应例1、(2019年江苏)实验室以工业废渣(主要含CaSO4·2H2O,还含少量SiO2、Al2O3、Fe2O3)为原料制取轻质CaCO3和(NH4)2SO4晶体,其实验流程如下:废渣浸取在如图所示的装置中进行。
控制反应温度在60~70 ℃,搅拌,反应3小时。
温度过高将会导致CaSO4的转化率下降,其原因是________答案:温度过高,(NH4)2CO3分解例2、【2018北京卷】磷精矿湿法制备磷酸的一种工艺流程如下:已知:磷精矿主要成分为Ca5(PO4)3(OH),还含有Ca5(PO4)3F和有机碳等。
化学反应自动控制流程图

图6.1泵的出口阀门开度控制方案
6.2
通过监测换热器的出料温度来控制载热流体(冷却剂或加热剂)的入口阀,调节载热流体的流量(压力)进而控制换热器的物料出口温度。被控物料的温度为主变量,载热流体的流量为副变量。如图6.2所示。
图6.2换热器串级控制载热流体流量方案
6.4
通过泵的出口阀门开度控制进料流量和出料流量,通过控制进料量、回流量和出料量来完成反应器的液位控制。通过控制蒸馏温度来控制反应器的塔压。通过控制载热流体的流量来完成反应器的温度控制。如图6.4所示。
1.
通过泵的出口阀门开度控制进料流量和出料流量,通过控制进料量和出料量来完成反应器的串级液位控制。通过控制输入反应器的氮气、反应温度以及空气进料量来控制反应器的塔压。通过控制载热流体的流量来完成反应器的温度控制。如图6.3所示。
图的流量调节通过控制泵的出口阀门开度来控制。泵的流量控制与反应器或分离器的液位控制联锁,通过控制泵的流量来控制反应器的液位。如图6.1所示。