高频淬火
高频淬火和中频淬火的区别

高频淬火和中频淬火的区别公司标准化编码 [QQX96QT-XQQB89Q8-NQQJ6Q8-MQM9N]高频淬火和中频淬火的区别1、高频淬火淬硬层浅(~2mm)、硬度高、工件不易氧化、变形小、淬火质量好、高,适用于摩擦条件下工作的零件,如一般较小的齿轮、轴类(所用材料为、);2、淬硬层较深(3~5mm),适用于承受扭曲、压力负荷的零件,如曲轴、大齿轮、磨床主轴等(所用材料为、、和球墨铸铁)高频的淬火,可以短时间的表层淬硬!晶体组织很细!结构变形小!中频表面应力比高频的要小50HZ叫工频,加热深度5~101000-10000HZ叫中频10000HZ以上叫高频“高频淬火”与“”在原理上是一样的。
利用高频率(或中频率、工频)的,使钢件表面迅速加热,随后立即冷却的一种方法。
其原理是:当在一个导体线圈中通过一定频率的交流电时,线圈内外将会产生一个频率相同的交流磁场,如果把工件放在线圈内,工件就会感应出交变电流,并使工件加热。
在工件中的分布是不均匀的,电流密度在表面最大,这种现象成为“表面效应”。
透入工件表面的深度主要取决于(周/秒),频率愈高,电流透入深度愈浅,则淬硬层愈薄,所以,可选用不同的频率来达到不同深度的淬硬层。
根据所用不同,感应加热可分为:高频感应加热(20000~1000000周/秒)、中频感应加热(5000~10000周/秒)和工频感应加热(50周/秒)。
感应加热,是利用电磁感应、集肤效应、涡流和电阻热等电磁原理,使工件表层快速加热,并快速冷却的热处理工艺感应加热时,将工件放在铜管制成的感应器内,当一定频率的交流电通过感应器时,处于交变磁场中的工件产生感应电流,由于集肤效应和涡流的作用,工件表层的高密度交流电产生的电阻热,迅速加热工件表层,很快达到淬火温度,随即喷水冷却,工件表层被淬硬感应加热时,工件截面上感应电流的分布状态与有关。
电流频率愈高,集肤效应愈强,感应电流集中的表层就愈薄,这样加热层深度与淬硬层深度也就愈薄因此,可通过调节电流频率来获得不同的淬硬层深度。
普通淬火和高频淬火有什么区别
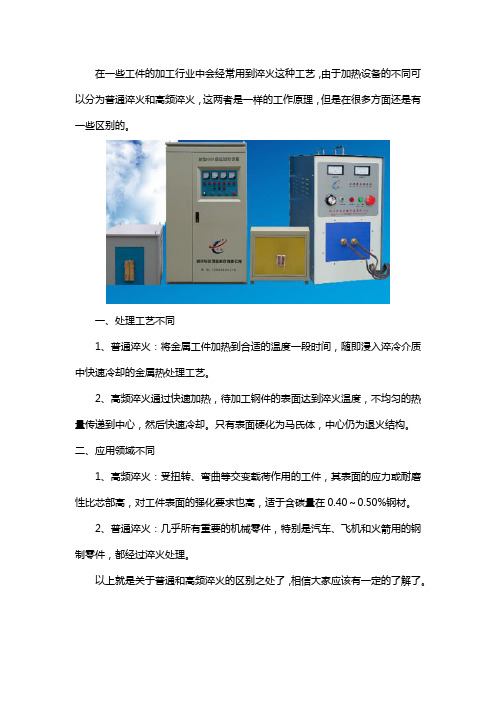
在一些工件的加工行业中会经常用到淬火这种工艺,由于加热设备的不同可以分为普通淬火和高频淬火,这两者是一样的工作原理,但是在很多方面还是有一些区别的。
一、处理工艺不同
1、普通淬火:将金属工件加热到合适的温度一段时间,随即浸入淬冷介质中快速冷却的金属热处理工艺。
2、高频淬火通过快速加热,待加工钢件的表面达到淬火温度,不均匀的热量传递到中心,然后快速冷却。
只有表面硬化为马氏体,中心仍为退火结构。
二、应用领域不同
1、高频淬火:受扭转、弯曲等交变载荷作用的工件,其表面的应力或耐磨性比芯部高,对工件表面的强化要求也高,适于含碳量在0.40~0.50%钢材。
2、普通淬火:几乎所有重要的机械零件,特别是汽车、飞机和火箭用的钢制零件,都经过淬火处理。
以上就是关于普通和高频淬火的区别之处了,相信大家应该有一定的了解了。
高频淬火和中频淬火的区别

高频淬火绝大多数是用于工业金属零件表面淬火,是使工件表面产生一定的感应电流,迅速加热零件表面,然后迅速淬火的一种金属热处理方法。
中频淬火是将金属件放在一个感应线圈内,感应线圈通交流电,产生交变电磁场,在金属件内感应出交变电流,由于趋肤效应,电流主要集中在金属件表面,所以表面的温度最高,在感应线圈下面紧跟着喷水冷却或其他冷却,由于加热及冷却主要集中在表面,所以表面改性很明显,而内部改性基本没有,可以有很特殊的热处理效果。
高频淬火和中频淬火的区别:高频淬火和中频淬火都属于表面热处理技术的一种,都是利用高频率(或中频率、工频)的感应电流,使钢件表面迅速加热,随后立即冷却的一种方法。
高频淬火和中频淬火的工作原理一样,都是感应加热原理:即工件放到感应器内,感应器一般是输入中频或高频交流电(1000-300000Hz或更高)的空心铜管。
产生交变磁场在工件中产生出同频率的感应电流,这种感应电流在工件的分布是不均匀的,在表面强,而在内部很弱,到心部接近于0,利用这个集肤效应,可使工件表面迅速加热,在几秒钟内表面温度上升到800-1000℃,而心部温度升高很小不过加热过程中,感应电流在工件中的分布是不均匀的,不同的电流频率产生的加热效果也是不同的:1、高频淬火电流频率在100~500 kHz淬硬层浅(1.5~2mm),硬度高,工件不易氧化,变形小,淬火质量好,生产效率高,适用于摩擦条件下工作的零件,如一般较小的齿轮、轴类(所用材料为45号钢、40Cr)2、中频淬火电流频率在500~10000 Hz淬硬层较深(3~5mm),适用于承受扭曲、压力负荷的零件,如曲轴、大齿轮、磨床主轴等(所用材料为45号钢、40Cr、9Mn2V 和球墨简而言之,高频淬火和中频淬火的最大区别就是加热厚度的不同,高频淬火可以短时间的表层淬硬,晶体组织很细,结构变形小,而中频表面应力比高频的要小。
高频淬火的淬硬层深度

高频淬火的淬硬层深度(最新版)目录一、高频淬火概述二、高频淬火淬硬层深度的测量方法1.破坏性测量方法2.非破坏性测量方法三、影响淬硬层深度的因素1.感应加热电流的频率2.加热功率3.淬火温度四、如何检测高频淬火淬硬层深度1.测量工具和设备2.检测步骤五、结论正文一、高频淬火概述高频淬火是一种金属热处理方法,主要应用于工业金属零件表面淬火。
这种方法通过使工件表面产生一定的感应电流,迅速加热零件表面,然后迅速淬火,以提高工件表面的硬度和耐磨性。
二、高频淬火淬硬层深度的测量方法高频淬火淬硬层深度的测量方法主要有破坏性测量和非破坏性测量两种。
1.破坏性测量方法破坏性测量方法是通过取截面进行硬度分析来测量淬硬层深度。
这种方法可以直接得到淬硬层的深度,但会对工件造成一定的破坏。
2.非破坏性测量方法非破坏性测量方法主要是通过 X 光透射检测来测量淬硬层深度。
这种方法不会对工件造成破坏,但测量结果可能存在一定的误差。
三、影响淬硬层深度的因素淬硬层深度的影响因素主要有感应加热电流的频率、加热功率和淬火温度。
1.感应加热电流的频率感应加热电流的频率越低,淬硬层越浅;反之,频率越高,硬层越深。
2.加热功率加热功率越大,淬硬层深度越深;反之,加热功率越小,淬硬层深度越浅。
3.淬火温度淬火温度越高,淬硬层深度越浅;反之,淬火温度越低,淬硬层深度越深。
四、如何检测高频淬火淬硬层深度检测高频淬火淬硬层深度需要使用硬度计和 X 光透射设备。
具体检测步骤如下:1.测量工件的厚度或直径,查一下工件要求硬化层层深要求的下限。
2.将此下限尺寸磨去,再查一下硬度要求的下限。
3.如硬度正好是下限,测量一下现在工件的厚度或直径,将工件原尺寸减去工件的现尺寸,就是它的淬硬层。
4.如硬度偏高或偏低,重复上述操作即可。
五、结论高频淬火淬硬层深度的测量是一个重要的环节,影响着工件的使用效果。
高频淬火原理
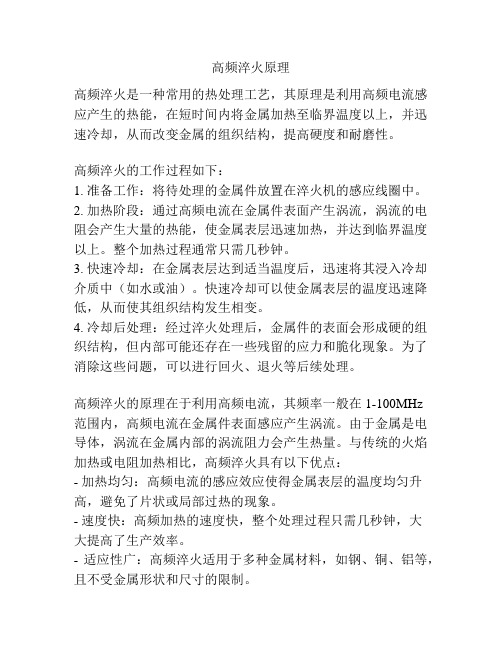
高频淬火原理
高频淬火是一种常用的热处理工艺,其原理是利用高频电流感应产生的热能,在短时间内将金属加热至临界温度以上,并迅速冷却,从而改变金属的组织结构,提高硬度和耐磨性。
高频淬火的工作过程如下:
1. 准备工作:将待处理的金属件放置在淬火机的感应线圈中。
2. 加热阶段:通过高频电流在金属件表面产生涡流,涡流的电阻会产生大量的热能,使金属表层迅速加热,并达到临界温度以上。
整个加热过程通常只需几秒钟。
3. 快速冷却:在金属表层达到适当温度后,迅速将其浸入冷却介质中(如水或油)。
快速冷却可以使金属表层的温度迅速降低,从而使其组织结构发生相变。
4. 冷却后处理:经过淬火处理后,金属件的表面会形成硬的组织结构,但内部可能还存在一些残留的应力和脆化现象。
为了消除这些问题,可以进行回火、退火等后续处理。
高频淬火的原理在于利用高频电流,其频率一般在1-100MHz
范围内,高频电流在金属件表面感应产生涡流。
由于金属是电导体,涡流在金属内部的涡流阻力会产生热量。
与传统的火焰加热或电阻加热相比,高频淬火具有以下优点:
- 加热均匀:高频电流的感应效应使得金属表层的温度均匀升高,避免了片状或局部过热的现象。
- 速度快:高频加热的速度快,整个处理过程只需几秒钟,大
大提高了生产效率。
- 适应性广:高频淬火适用于多种金属材料,如钢、铜、铝等,且不受金属形状和尺寸的限制。
总的来说,高频淬火利用高频电流感应产生的热能,实现了金属表层的快速加热和冷却,从而获得更高的硬度和耐磨性。
作为一种高效的热处理工艺,高频淬火在金属制造业中广泛应用。
高频淬火和中频淬火的区别

1、高频淬火淬硬层浅(1.5~2mm)、硬度高、工件不易氧化、变形小、淬火质量好、生产效率高,适用于摩擦条件下工作的零件,如一般较小的齿轮、轴类(所用材料为45号钢、40Cr);2、中频淬火淬硬层较深(3~5mm),适用于承受扭曲、压力负荷的零件,如曲轴、大齿轮、磨床主轴等(所用材料为45号钢、40Cr、9Mn2V和球墨高频的淬火,可以短时间的表层淬硬!晶体组织很细!结构变形小。
中频表面应力比高频的要小。
50HZ叫工频,加热深度5-10,1000-10000HZ叫中频,10000HZ以上叫高频。
“高频淬火”与“中频淬火”在原理上是一样的。
利用高频率(或中频率、工频)的感应电流,使钢件表面迅速加热,随后立即冷却的一种方法。
其原理是:当在一个导体线圈中通过一定频率的交流电时,线圈内外将会产生一个频率相同的交流磁场,如果把工件放在线圈内,工件就会感应出交变电流,并使工件加热。
感应电流在工件中的分布是不均匀的,电流密度在表面最大,这种现象成为“表面效应”。
感应电流透入工件表面的深度主要取决于电流频率(周/秒),频率愈高,电流透入深度愈浅,则淬硬层愈薄,所以,可选用不同的频率来达到不同深度的淬硬层。
根据所用电流频率不同,感应加热可分为:高频感应加热(20000~1000000周/秒)、中频感应加热(5000~10000周/秒)和工频感应加热(50周/秒)。
感应加热表面淬火,是利用电磁感应、集肤效应、涡流和电阻热等电磁原理,使工件表层快速加热,并快速冷却的热处理工艺。
感应加热表面淬火时,将工件放在铜管制成的感应器内,当一定频率的交流电通过感应器时,处于交变磁场中的工件产生感应电流,由于集肤效应和涡流的作用,工件表层的高密度交流电产生的电阻热,迅速加热工件表层,很快达到淬火温度,随即喷水冷却,工件表层被淬硬感应加热时,工件截面上感应电流的分布状态与电流频率有关。
电流频率愈高,集肤效应愈强,感应电流集中的表层就愈薄,这样加热层深度与淬硬层深度也就愈薄。
高频是指高频淬火

高频是指高频淬火。
对工件进行高频电流感应加热,然后淬硬。
高频淬火主要用于表面淬火,比如齿轮的淬火。
调质是指把金属加热到一定温度,保持一定时间,缓慢冷却。
作用是把金属的硬度调整到某一范围,使其既具有一定的硬度,又具有良好的加工性能。
调质钢为含碳量0.30-0.60%的中碳碳结钢和合金结构钢。
一般在调质状态下使用,也有再经高频感应加热表面淬火,提高表面硬度,用以制造在重载荷和冲击条件下工作的耐磨件。
常用钢号有:30、35、40、45、50制造螺母、螺栓及各类轴;30Mn、40Mn、45Mn、35Mn2、45Mn2制造重要螺母、螺栓、支重轮轴和导向轮轴;30Cr、40Cr、45Cr制造转向齿轮轴、传动齿轮等。
35CrMo、42CrMo制造重型汽车曲轴及连杆等。
调质(quenching and high temperature tempering)调质即淬火和高温回火的综合热处理工艺。
调质件大都在比较大的动载荷作用下工作,它们承受着拉伸、压缩、弯曲、扭转或剪切的作用,有的表面还具有摩擦,要求有一定的耐磨性等等。
总之,零件处在各种复合应力下工作。
这类零件主要为各种机器和机构的结构件,如轴类、连杆、螺栓、齿轮等,在机床、汽车和拖拉机等制造工业中用得很普遍。
尤其是对于重型机器制造中的大型部件,调质处理用得更多.因此,调质处理在热处理中占有很重要的位置。
在机械产品中的调质件,因其受力条件不同,对其所要求的性能也就不完全一样。
一般说来,各种调质件都应具有优良的综合力学性能,即高强度和高韧性的适当配合,以保证零件长期顺利工作。
调质处理淬火+高温回火=调质钢的热处理工艺包括退火、正火、淬火、回火和表面热处理等方法。
其中回火又包括调质处理和时效处理。
钢的回火:将已经淬火的钢重新加热到一定温度,再用一定方法冷却称为回火。
其目的是消除淬火产生的内应力,降低硬度和脆性,以取得预期的力学性能。
回火分高温回火、中温回火和低温回火三类。
高频淬火频率范围

高频淬火频率范围
摘要:
一、高频淬火频率范围的概念
二、高频淬火频率范围的具体数值
三、高频淬火频率范围的影响因素
四、高频淬火频率范围的选择与应用
正文:
高频淬火频率范围,是指在淬火工艺中,所采用的高频电流的频率范围。
高频淬火频率范围的选择,直接影响到淬火的效果和质量。
在我国,高频淬火频率范围通常在100kHz-1MHz 之间。
在这个频率范围内,高频电流能够有效地穿透金属,产生快速而均匀的加热效果,从而实现快速淬火。
高频淬火频率范围受多种因素影响,包括淬火材料的性质、淬火设备的类型、淬火工艺的要求等。
例如,对于不同种类的钢材,可能需要采用不同的高频淬火频率范围,才能达到最佳的淬火效果。
高频淬火频率范围的选择,需要结合具体的淬火工艺和材料特性进行。
一般来说,淬火频率越高,淬火速度越快,但过高的频率可能会导致材料过热,影响淬火质量。
因此,合理选择高频淬火频率范围,是保证淬火效果和质量的关键。
高频淬火热处理
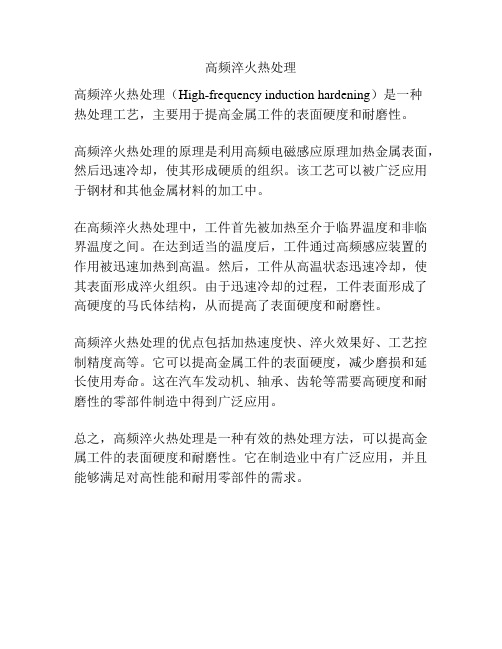
高频淬火热处理
高频淬火热处理(High-frequency induction hardening)是一种
热处理工艺,主要用于提高金属工件的表面硬度和耐磨性。
高频淬火热处理的原理是利用高频电磁感应原理加热金属表面,然后迅速冷却,使其形成硬质的组织。
该工艺可以被广泛应用于钢材和其他金属材料的加工中。
在高频淬火热处理中,工件首先被加热至介于临界温度和非临界温度之间。
在达到适当的温度后,工件通过高频感应装置的作用被迅速加热到高温。
然后,工件从高温状态迅速冷却,使其表面形成淬火组织。
由于迅速冷却的过程,工件表面形成了高硬度的马氏体结构,从而提高了表面硬度和耐磨性。
高频淬火热处理的优点包括加热速度快、淬火效果好、工艺控制精度高等。
它可以提高金属工件的表面硬度,减少磨损和延长使用寿命。
这在汽车发动机、轴承、齿轮等需要高硬度和耐磨性的零部件制造中得到广泛应用。
总之,高频淬火热处理是一种有效的热处理方法,可以提高金属工件的表面硬度和耐磨性。
它在制造业中有广泛应用,并且能够满足对高性能和耐用零部件的需求。
高频淬火与中频淬火

高频淬火与中频淬火
高频淬火的频率高,淬火层浅。
如齿轮的轮齿表面淬火。
中频淬火频率低一些,淬火层要厚一些。
主要适用于轴类零件。
基本原理:工件放入感应器(线圈)内,当感应器中通入一定频率的交变电流时,周围即产生交变磁场。
交变磁场的电磁感应作用使工件内产生封闭的感应电流──涡流。
感应电流在工件截面上的分布很不均匀,工件表层电流密度很高,向内逐渐减小, 这种现象称为集肤效应。
工件表层高密度电流的电能转变为热能,使表层的温度升高,即实现表面加热。
电流频率越高,工件表层与内部的电流密度差则越大,加热层越薄。
在加热层温度超过钢的临界点温度后迅速冷却,即可实现表面淬火。
三维网技术论坛0 {# r* ?* b# d; ^
根据交变电流的频率高低,可将感应加热热处理分为超高频、高频、超音频、中频、工频5类。
①超高频感应加热热处理所用的电流频率高达27兆赫,加热层极薄,仅约0.15毫米,可用于圆盘锯等形状复杂工件的薄层表面淬火。
②高频感应加热热处理所用的电流频率通常为200~300千赫,加热层深度为0.5~2毫米,可用于齿轮、汽缸套、凸轮、轴等零件的表面淬火。
③超音频感应加热热处理所用的电流频率一般为20~30千赫,用超音频感应电流对小模数齿轮加热,加热层大致沿齿廓分布,粹火后使用性能较好。
④中频感应加热热处理所用的电流频率一般为2.5~10千赫,加热层深度为2~8毫米,多用于大模数齿轮、直径较大的轴类和冷轧辊等工件的表面淬火。
⑤工频感应加热热处理所用的电流频率为50~60赫,加热层深度为10~15毫米,可用于大型工件的表面淬火。
什么是高频淬火、中频淬火以及两者有什么不同

淬火设备在我们的生活中应用是越来越广泛了,很多我们常用的物品都需要通过高频淬火,比如:斧子、菜刀、汽车上的配件,甚至是金银首饰也需要用到淬火原理,那么你了解淬火吗?你知道什么是高频淬火?什么是中频淬火?你可以区分开高频淬火和中频淬火吗?下面一起来看看吧。
什么是高频淬火?高频淬火绝大多数是用于工业金属零件表面淬火,是使工件表面产生一定的感应电流,迅速加热零件表面,然后迅速淬火的一种金属热处理方法。
什么是中频淬火?中频淬火是将金属件放在一个感应线圈内,感应线圈通交流电,产生交变电磁场,在金属件内感应出交变电流,由于趋肤效应,电流主要集中在金属件表面,所以表面的温度也高,在感应线圈下面紧跟着喷水冷却或其他冷却,由于加热及冷却主要集中在表面,所以表面改性很明显,而内部改性基本没有,可以有很特殊的热处理效果。
高频淬火和中频淬火有什么区别?在了解区别前先了解一下它们的相同性。
郑州星川感应技术有限公司介绍:高频淬火和中频淬火都属于表面热处理技术的一种,都是利用高频率(或中频率、工频)的感应电流,使钢件表面迅速加热,随后立即冷却的一种方法。
高频淬火和中频淬火的工作原理一样,都是感应加热原理:即工件放到感应器内,感应器一般是输入中频或高频交流电(1000-300000Hz或更高)的空心铜管。
产生交变磁场在工件中产生出同频率的感应电流,这种感应电流在工件的分布是不均匀的,在表面强,而在内部很弱,到心部接近于0,利用这个集肤效应,可使工件表面迅速加热,在几秒钟内表面温度上升到800-1000℃,而心部温度升高很小。
不过加热过程中,感应电流在工件中的分布是不均匀的,不同的电流频率产生的加热效果也是不同的,那么,高频淬火和中频淬火的区别就来了:1、高频淬火电流频率在100~500 kHz淬硬层浅(1.5~2mm)高频淬火后的优势:硬度高,工件不易氧化,变形小,淬火质量好,生产效率高高频淬火适用于摩擦条件下工作的零件,如一般较小的齿轮、轴类(所用材料为45号钢、40Cr)2、中频淬火电流频率在500~10000 Hz淬硬层较深(3~5mm)中频淬火适用于承受扭曲、压力负荷的零件,如曲轴、大齿轮、磨床主轴等(所用材料为45号钢、40Cr、9Mn2V和球墨简而言之,高频淬火和中频淬火的一大明显区别就是加热厚度的不同,高频淬火可以短时间的表层淬硬,晶体组织很细,结构变形小,而中频表面应力比高频的要小。
中频淬火与高频淬火的淬火不同有哪些?

中频淬火与高频淬火的淬火不同有哪些?
在热处理行业中的淬火领域中,一般采用高频感应加热设备或中频感应加热电源对
工件进行淬火,简称高频淬火或中频淬火。
那么在淬火方面二者的区别有哪些呢?了解二者区别,有助于对感应加热设备进行选择及具体的选型,简单概括有一下几点:
高频淬火与中频淬火的相同点:
二者都是应用于对金属材料的热加工、透热、淬火热处理、热装配及焊接、熔炼。
高频淬火与中频淬火的不同点:
二者除了有设备频率不同,谐振输出方式不同,变频器件不同外,在对工件进行淬
火时,最主要的是淬火深度不同,由于频率越低,透热性越好,淬火层越深,高频感应加热淬火层在:0.5~2mm 主要用于要求淬硬层较薄的中、小型零件,如小模数齿轮、中小型轴等小金属工件的加热。
淬火,焊接等。
中频感应加热淬火层在3~6mm主要用于要求淬
硬层要求较深的零件,如中大模数的齿轮、直径较大的轴等。
中频用于大金属工件的加热、透热、淬火等。
实际生产中要根据技术要求和工件的几何特征(形状)及整体或局部特点选择适宜的
频率或淬火深度的感应加热设备,以达到最好的效果。
高频淬火原理及应用
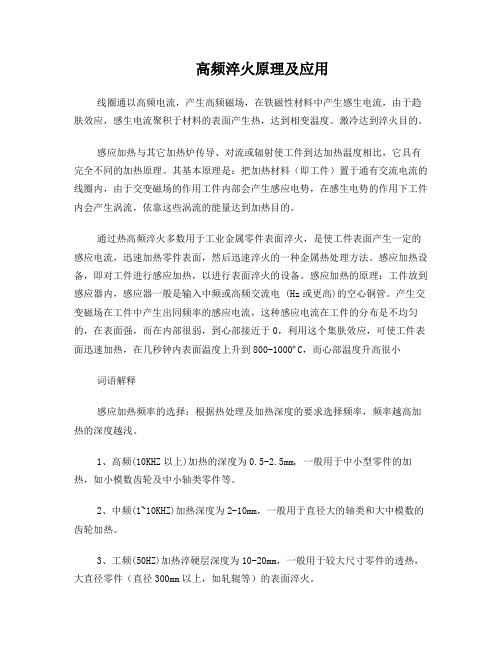
高频淬火原理及应用线圈通以高频电流,产生高频磁场,在铁磁性材料中产生感生电流,由于趋肤效应,感生电流聚积于材料的表面产生热,达到相变温度。
激冷达到淬火目的。
感应加热与其它加热炉传导、对流或辐射使工件到达加热温度相比,它具有完全不同的加热原理。
其基本原理是:把加热材料(即工件)置于通有交流电流的线圈内,由于交变磁场的作用工件内部会产生感应电势,在感生电势的作用下工件内会产生涡流,依靠这些涡流的能量达到加热目的。
通过热高频淬火多数用于工业金属零件表面淬火,是使工件表面产生一定的感应电流,迅速加热零件表面,然后迅速淬火的一种金属热处理方法。
感应加热设备,即对工件进行感应加热,以进行表面淬火的设备。
感应加热的原理:工件放到感应器内,感应器一般是输入中频或高频交流电 (Hz或更高)的空心铜管。
产生交变磁场在工件中产生出同频率的感应电流,这种感应电流在工件的分布是不均匀的,在表面强,而在内部很弱,到心部接近于0,利用这个集肤效应,可使工件表面迅速加热,在几秒钟内表面温度上升到800-1000ºC,而心部温度升高很小词语解释感应加热频率的选择:根据热处理及加热深度的要求选择频率,频率越高加热的深度越浅。
1、高频(10KHZ以上)加热的深度为0.5-2.5mm, 一般用于中小型零件的加热,如小模数齿轮及中小轴类零件等。
2、中频(1~10KHZ)加热深度为2-10mm,一般用于直径大的轴类和大中模数的齿轮加热。
3、工频(50HZ)加热淬硬层深度为10-20mm,一般用于较大尺寸零件的透热,大直径零件(直径300mm以上,如轧辊等)的表面淬火。
感应加热淬火表层淬硬层的深度,取决于交流电的频率,一般是频率高加热深度浅,淬硬层深度也就浅。
频率f与加热深度δ的关系,有如下经验公式:δ=20/√f(20°C);δ=500/√f(800°C)。
式中:f为频率,单位为Hz;δ为加热深度,单位为毫米(mm)。
淬火之中频淬火与高频淬火
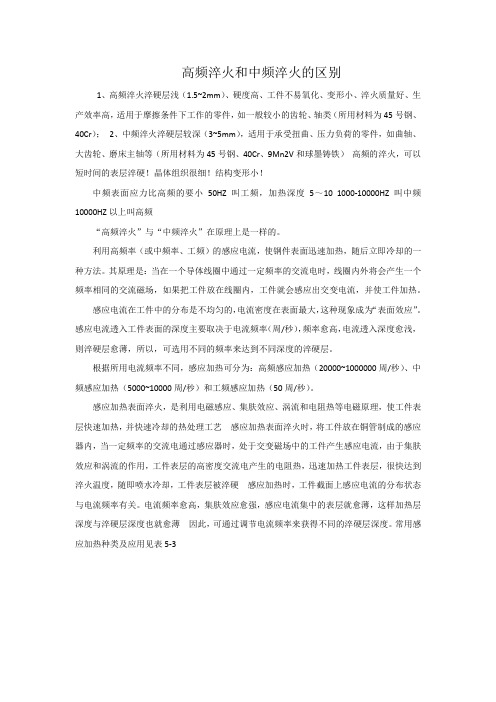
高频淬火和中频淬火的区别1、高频淬火淬硬层浅(1.5~2mm)、硬度高、工件不易氧化、变形小、淬火质量好、生产效率高,适用于摩擦条件下工作的零件,如一般较小的齿轮、轴类(所用材料为45号钢、40Cr);2、中频淬火淬硬层较深(3~5mm),适用于承受扭曲、压力负荷的零件,如曲轴、大齿轮、磨床主轴等(所用材料为45号钢、40Cr、9Mn2V和球墨铸铁)高频的淬火,可以短时间的表层淬硬!晶体组织很细!结构变形小!中频表面应力比高频的要小50HZ叫工频,加热深度5~10 1000-10000HZ叫中频10000HZ以上叫高频“高频淬火”与“中频淬火”在原理上是一样的。
利用高频率(或中频率、工频)的感应电流,使钢件表面迅速加热,随后立即冷却的一种方法。
其原理是:当在一个导体线圈中通过一定频率的交流电时,线圈内外将会产生一个频率相同的交流磁场,如果把工件放在线圈内,工件就会感应出交变电流,并使工件加热。
感应电流在工件中的分布是不均匀的,电流密度在表面最大,这种现象成为“表面效应”。
感应电流透入工件表面的深度主要取决于电流频率(周/秒),频率愈高,电流透入深度愈浅,则淬硬层愈薄,所以,可选用不同的频率来达到不同深度的淬硬层。
根据所用电流频率不同,感应加热可分为:高频感应加热(20000~1000000周/秒)、中频感应加热(5000~10000周/秒)和工频感应加热(50周/秒)。
感应加热表面淬火,是利用电磁感应、集肤效应、涡流和电阻热等电磁原理,使工件表层快速加热,并快速冷却的热处理工艺感应加热表面淬火时,将工件放在铜管制成的感应器内,当一定频率的交流电通过感应器时,处于交变磁场中的工件产生感应电流,由于集肤效应和涡流的作用,工件表层的高密度交流电产生的电阻热,迅速加热工件表层,很快达到淬火温度,随即喷水冷却,工件表层被淬硬感应加热时,工件截面上感应电流的分布状态与电流频率有关。
电流频率愈高,集肤效应愈强,感应电流集中的表层就愈薄,这样加热层深度与淬硬层深度也就愈薄因此,可通过调节电流频率来获得不同的淬硬层深度。
高频淬火机理

高频淬火机理
高频淬火机理是一种将金属加热到高温状态,再通过高频电流进行快速淬火处理的方法。
它主要适用于工业生产中金属材料的硬化和强化加工,机理如下:
一、表面效应
高频淬火时,由于高频电流穿过金属表面时会产生局部热量,因此表面会迅速升温并达到高温状态。
表面升温后,在冷却过程中会优先形成淬火组织,从而得到更高的硬度和强度。
二、温度梯度效应
高频电流穿过金属内部时,不同深度的金属材料会受到不同程度的热量影响,形成温度梯度效应。
深度较大的地方升温较慢,在冷却速度相同的情况下,内部的金属会形成较为均匀的淬火组织。
三、结构变化效应
高频淬火还能通过电磁场的作用,使金属内部的组织结构发生变化。
当金属被高频电流加热到一定温度时,晶粒就会发生再结晶现象,冷却后形成细小的晶粒,从而提高硬度和强度。
四、应力效应
高频淬火的加热和冷却过程中,金属内部还会受到应力的影响。
这些应力能够消除材料内部的微观缺陷,同时也能够引起材料内部的塑性变形。
塑性变形可以使金属的晶粒更加细小,进而提高金属材料的硬度和强度。
综上所述,高频淬火机理主要通过表面效应、温度梯度效应、结构变化效应和应力效应来实现金属材料的硬化和强化。
这种技术已经广泛应用于各个领域的金属加工中,成为工业生产过程中不可或缺的一部分。
内孔高频淬火处理

内孔高频淬火处理摘要:一、内孔高频淬火处理简介1.内孔高频淬火的定义2.内孔高频淬火的作用二、内孔高频淬火处理方法1.内孔高频淬火的工艺流程2.常用内孔高频淬火设备三、内孔高频淬火处理的应用领域1.内孔高频淬火在机械制造业的应用2.内孔高频淬火在汽车制造业的应用四、内孔高频淬火处理的优势与局限1.优势a.提高工件的硬度和耐磨性b.优化工件的机械性能c.减少变形和裂纹2.局限a.对设备的要求较高b.处理过程中可能产生的问题五、内孔高频淬火处理的发展趋势1.新技术的研发与应用2.环保与节能的考虑正文:内孔高频淬火处理是一种金属热处理技术,通过高频电磁感应原理,使工件内部产生涡流,迅速加热至淬火温度,然后进行快速冷却,以改变工件的组织结构和性能。
这种处理方法在提高工件的硬度和耐磨性、优化工件的机械性能、减少变形和裂纹等方面具有显著优势,被广泛应用于机械制造业和汽车制造业等领域。
内孔高频淬火处理的方法主要包括:预热、高频加热、淬火、回火和冷却。
其中,高频加热是内孔高频淬火处理的关键环节,通过高频电磁感应原理,使工件内部产生涡流,迅速加热至淬火温度。
而淬火则需要快速冷却,通常采用油冷或水冷等方式。
回火则是对淬火后的工件进行加热,以消除内应力和改善工件的性能。
内孔高频淬火处理在机械制造业和汽车制造业等领域具有广泛应用。
例如,在汽车制造业中,内孔高频淬火处理可以提高发动机零件、齿轮、传动轴等部件的性能,从而提高汽车的整体性能和使用寿命。
在机械制造业中,内孔高频淬火处理可以提高模具、刀具、螺纹轴等产品的使用寿命和质量。
然而,内孔高频淬火处理也存在一些局限。
例如,对设备的要求较高,需要精确控制加热和冷却过程,以保证处理效果。
此外,处理过程中可能产生的问题,如过热、过冷、变形和裂纹等,也需要在实际操作中加以克服。
随着科技的发展,内孔高频淬火处理技术也在不断进步。
未来,内孔高频淬火处理将更加注重环保与节能,研发新型设备和方法,提高处理效果和降低处理成本。
高频淬火频率范围
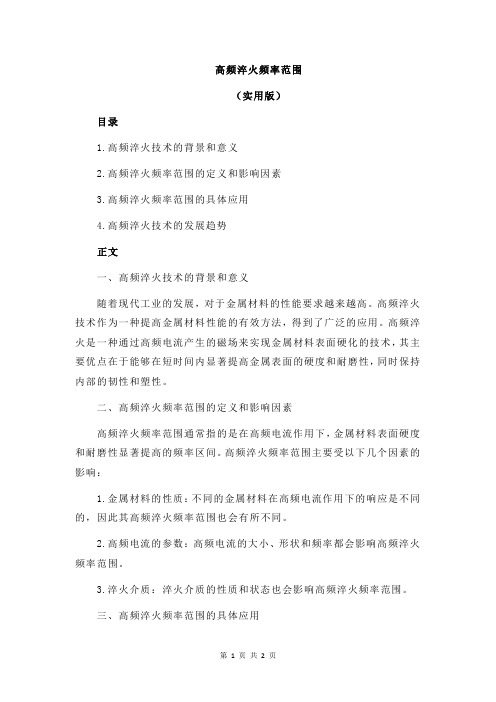
高频淬火频率范围
(实用版)
目录
1.高频淬火技术的背景和意义
2.高频淬火频率范围的定义和影响因素
3.高频淬火频率范围的具体应用
4.高频淬火技术的发展趋势
正文
一、高频淬火技术的背景和意义
随着现代工业的发展,对于金属材料的性能要求越来越高。
高频淬火技术作为一种提高金属材料性能的有效方法,得到了广泛的应用。
高频淬火是一种通过高频电流产生的磁场来实现金属材料表面硬化的技术,其主要优点在于能够在短时间内显著提高金属表面的硬度和耐磨性,同时保持内部的韧性和塑性。
二、高频淬火频率范围的定义和影响因素
高频淬火频率范围通常指的是在高频电流作用下,金属材料表面硬度和耐磨性显著提高的频率区间。
高频淬火频率范围主要受以下几个因素的影响:
1.金属材料的性质:不同的金属材料在高频电流作用下的响应是不同的,因此其高频淬火频率范围也会有所不同。
2.高频电流的参数:高频电流的大小、形状和频率都会影响高频淬火频率范围。
3.淬火介质:淬火介质的性质和状态也会影响高频淬火频率范围。
三、高频淬火频率范围的具体应用
高频淬火频率范围在许多工业领域都有广泛的应用,例如:
1.轴承行业:高频淬火技术可以提高轴承的耐磨性和寿命。
2.齿轮行业:高频淬火技术可以提高齿轮的硬度和耐磨性。
3.刀具行业:高频淬火技术可以提高刀具的硬度和耐磨性,从而提高其使用寿命。
四、高频淬火技术的发展趋势
随着科技的进步和工业的发展,高频淬火技术也在不断地发展和完善。
高频淬火和普通淬火应用场合

高频淬火和普通淬火应用场合
高频淬火和普通淬火的应用场合因具体需求和工件特性而异。
高频淬火通常适用于表面耐磨性要求高、硬度要求较高的工件。
在汽车工业中,发动机零件如曲轴、凸轮轴等需要高硬度和耐磨性,高频感应加热淬火被广泛用于这些零件的处理。
在机械制造中,大型齿轮、轴类零件需要淬硬层较深,中频感应加热淬火成为重要的工艺。
在航空航天领域,飞机引擎零件、陀螺仪零件等对硬度和耐磨性要求严格,高频与中频淬火技术有广泛应用。
普通淬火则适用于对表面硬度要求不高,但需要整体淬硬的工件。
在能源领域,石油、天然气开采中的钻头、管道以及核电设备零件等,也借助这些技术提高耐磨性。
在医疗器械中,手术器械、种植物件需要表面硬度,以确保安全和长寿命。
在电子行业中,电机、变压器、感应加热设备等需要使用高频感应加热淬火以提高性能。
总之,高频淬火和普通淬火的应用场合因具体需求和工件特性而异,需要根据实际情况进行选择。
- 1、下载文档前请自行甄别文档内容的完整性,平台不提供额外的编辑、内容补充、找答案等附加服务。
- 2、"仅部分预览"的文档,不可在线预览部分如存在完整性等问题,可反馈申请退款(可完整预览的文档不适用该条件!)。
- 3、如文档侵犯您的权益,请联系客服反馈,我们会尽快为您处理(人工客服工作时间:9:00-18:30)。
在汽车、机床等机械设备的制造和生产中,有许多传动机构的工件需要承受较大的载荷及频繁的启停,因此就需要其表面具有高的硬度、强度以及耐磨性,而心部又需要较好的韧性。
比如:齿轮,凸轮轴,气门杆,前进杆,汽车半轴,花键轴,链轮、光轴、导轨、仿形件等。
所以需要对这些工件进行表面热处理,传统的表面热处理有:表面渗碳、渗氮;碳氮共渗;表面淬火等,表面淬火相比于其他热处理工艺成本更低,效率更高,而且变形量小,操作更简单,优势十分明显,在工业生产中应用十分广泛。
感应加热是一项先进的金属加热技术,是国家倡导的节能减排技术之一。
它是利用金属导体在交变磁场作用下产生的感应电流引起自身发热,而到达加热金属的目的。
广泛应用于金属热处理、淬火、透热、熔炼、焊接、热套等众多领域。
感应加热具有非接触、速度快、效率高、工序简单、容易实现自动化等显著优点,并具有零排放、无污染和节能等优势,对国民经济发展具有重要意义。
表面淬火按照加热频率可分为:中频淬火(<10KHZ),超音频淬火
(20-100KHZ),高频淬火(>100KHZ);按照加热部分又可分为:外表面淬火和内表面淬火(内孔);按照淬火方式又可分为:同时加热淬火法、连续扫描式淬火法。
2 表面淬火与普通淬火比具有如下优点
1、工件表面硬度高,经高、中频感应加热表面淬火的工件,其表面硬度往往比普通淬火高2~3个单位(HRC)。
缺口敏感性小,冲击韧性、疲劳强度以及耐磨性等均有很大提高。
有利于发挥材料地潜力,节约材料消耗,提高零件使用寿命;
2、工件因不是整体加热,变形小;
3、工件加热时间短,表面氧化脱碳量少;
4、热源在工件表层,加热速度快,热效率高;
5、设备紧凑,使用方便,劳动条件好;
6、便于机械化和自动化;
感应表面淬火后的性能:
1、表面硬度:经高、中频感应加热表面淬火的工件,其表面硬度往往比普通淬火高2~3个单位(HRC)。
2、耐磨性:高频淬火后的工件耐磨性比普通淬火要高。
这主要是由于淬硬层马氏体晶粒细小,碳化物弥散度高,以及硬度比较高,表面的高的压应力等综合的结果。
3、疲劳强度:高、中频表面淬火使疲劳强度大为提高,缺口敏感性下降。
对同样材料的工件,在一定范围内,随硬化层深度增加而疲劳强度增加,但硬化层深度过深时心部韧性下降,疲劳强度反而下降,并使工件脆性增加。