七里岗水泥厂分解炉串联改造技术
水泥工艺中分解炉的结构及原理简介

(二)、分解炉的工作原理与结构概述分解炉是把生料粉分散悬浮在气流中,使燃料燃烧和碳酸钙分解过程在很短时间(一般1.5~3秒)内发生的装置,是一种高效率的直接燃烧式固相一气相热交换装置。
在分解炉内,由于燃料的燃烧是在激烈的紊流状态下与物料的吸热反应同时进行,燃料的细小颗粒呈一面浮游,一面燃烧,使整个炉内几乎都变成了燃烧区。
所以不能形成可见辉焰,而是处于820~900℃低温无焰燃烧的状态。
水泥烧成过程大致可分为两个阶段:石灰质原料约在900℃时进行分解反应(吸热);在1200~1450℃时进行水泥化合物生成反应(放热、部分熔融)。
根据理论计算,当物料由750℃升高到850℃,分解率由原来的25%提高到85~90%时。
每千克熟料尚须1670千焦的热量。
因此,全燃料的60%左右用于分解炉的燃烧,40%用在窑内燃烧。
近几年来窑外分解技术发展很快,虽然分解炉的结构型式和工作原理不尽相同,它们各有自己的特点,但是从入窑碳酸钙分解率来看,都不相上下,一般都达到85%以上。
由此看来,分解炉的结构型式对于入窑生料碳酸钙分解率的影响是不太大的。
关键在于燃料在生料浓度很高的分解炉内能稳定、完全燃烧,炉内温度分布均匀,并使碳酸钙分解在很短时间内完成。
我国某厂烧煤分解炉的结构示意图3—18。
分解炉由预燃室和炉体两部分组成,预燃室主要起预燃和散料作用,炉体主要起燃料燃烧和碳酸钙分解作用。
在钢板壳体内壁镶砌耐火砖。
由冷却机来的二次空气分成两路进入预燃室。
三级旋风筒下来的预热料,由二次空气从预燃室柱体的中上部带入预燃室。
约四分之一的分解炉用煤粉,从预燃室顶部由少量二次空气带入并着火燃烧,约四分之三左右的煤粉在分解炉锥体的上部位置喂入,以此来提高和调整分解炉的温度,使整个炉内温度分布趋于均匀,担任分解碳酸钙的主力作用。
炉体内的煤粉颗粒,虽被大量的惰性气体CO2和N2所包围,减少了与O2接触的机会,煤粉的燃烧速度就会减慢。
但由于进入预燃室的煤粉不受生料粉的影响,而且在纯空气中燃烧,形成引燃火焰,起到火种的作用,使预燃室出口处有明火存在,对煤粉起着强制着火作用。
NMFC分解炉冷态投料法
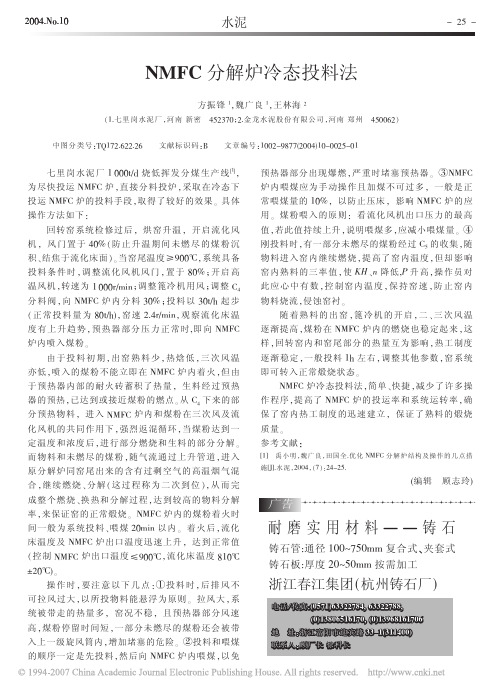
耐磨实用材料!!铸石
铸石管!通径 "#$%&’$(( 复合式 "夹套式 铸石板)厚度 *#%’#(( 按需加工
-!".A"
操 作 时 ! 要 注 意 以 下 几 点 #! 投 料 时 ! 后 排 风 不 可拉风过大 ! 以所投物料能悬浮为原则 " 拉风大 ! 系 统被带走的热量多 ! 窑况不稳 ! 且预热器部分风速 高 ! 煤粉停留时间短 ! 一部分未燃尽的煤粉还会被带 入上一级旋风筒内 !增加堵塞的危险 " "投料和喂煤 的顺序一定是先投料 ! 然后向 %89: 炉内喂煤 ! 以免
浙江春江集团 ! 杭州铸石厂 "
电话 ! 传真 "#$%&’()**++&,-. )**++&,,.
#$/’*,$)%’)’&$. #$/’*0),’)’&$)
地 址 ! 浙江富阳市迎宾路 **1’#*’’-$$/ 联系人 ! 顾厂长 徐科长
!""#$%&$’"
- !2 -
!"#$ 分解炉冷态投料法
方振锋 ’!魏广良 ’!王林海 !
*’$ 七里岗水泥厂 ! 河南 新密 中图分类号 !()’*!$+!!$!+ 文献标识码 !,
#2!?*" (!$ 金龙水泥股份有限公司 ! 河南 郑州
文章编号 !’""!-./**0!""#1’"-""!2-"’
#2""+! &
七里岗水泥 厂 ’ """345 烧低挥发 分 煤 生 产 线 6’7! 为尽快投运 %89: 炉 ! 直接分料投炉 ! 采取在冷态下 投运 %89: 炉的投料手段 !取得了较好的效果 " 具体 操作方法如下 # 回转窑系统检修过后 ! 烘窑升温 ! 开启流化风 机 ! 风 门置于 #"+ $ 防止 升 温 期 间 未 燃 尽 的 煤 粉 沉 积 % 结焦于流化床面 &’ 当窑尾温度 "."", !系统具备 投料条件时 ! 调整流化风 机风门 ! 置 于 /"+ ( 开 启 高 温风机 ! 转速为 ’ """;4<=> ( 调整篦冷机用风 ( 调整 :# 分 料阀 ! 向 %89: 炉内 分料 ?"+ ( 投 料 以 ?"34@ 起 步 $ 正 常 投 料 量 为 /"34@A! 窑 速 !$#;4<=>! 观 察 流 化 床 温 度有上 升趋势 ! 预热 器部分 压 力 正 常 时 B 即 向 %89: 炉内喷入煤粉 ) 由 于 投 料 初 期 !出 窑 熟 料 少 !热 焓 低 !三 次 风 温 亦低 ! 喷入的煤粉不能立即在 %89: 炉内着火 ! 但由 于预热器内部的耐火砖蓄积了热量 ! 生料经过预热 器的预热 ! 已达到或接近煤粉的燃点 " 从 :# 下来的部 分预热物料 ! 进入 %89: 炉内和煤粉在三次风及流 化风机的共同作用下 ! 强烈返混循环 ! 当煤粉达到一 定温度和浓度后 ! 进行部分燃烧和生料的部分分解 " 而物料和未燃尽的煤粉 ! 随气流通过上升管道 ! 进入 原分解炉同窑尾出来的含有过剩空气的高温烟气混 合 ! 继续 燃烧 % 分解 * 这 过 程 称 为 二 次 到 位 &! 从 而 完 成整个燃烧 + 换热和分解过程 ! 达到较高的物料分解 率 ! 来保证窑的正常煅烧 " %89: 炉内的煤粉着火时 间一般为系统投料 % 喂煤 !"<=> 以内 " 着火后 ! 流化 床温度及 %89: 炉出口温度迅速上升 ! 达到正常值 * 控制 %89: 炉出口温度 #."", ! 流化床温度 /’",
水泥厂改造工程方案
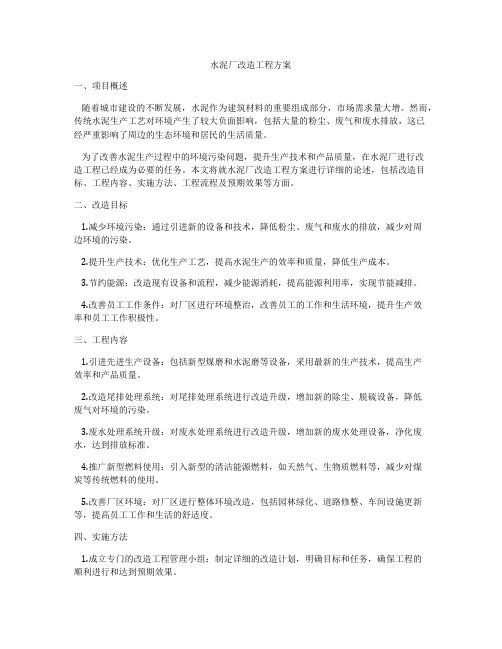
水泥厂改造工程方案一、项目概述随着城市建设的不断发展,水泥作为建筑材料的重要组成部分,市场需求量大增。
然而,传统水泥生产工艺对环境产生了较大负面影响,包括大量的粉尘、废气和废水排放,这已经严重影响了周边的生态环境和居民的生活质量。
为了改善水泥生产过程中的环境污染问题,提升生产技术和产品质量,在水泥厂进行改造工程已经成为必要的任务。
本文将就水泥厂改造工程方案进行详细的论述,包括改造目标、工程内容、实施方法、工程流程及预期效果等方面。
二、改造目标1.减少环境污染:通过引进新的设备和技术,降低粉尘、废气和废水的排放,减少对周边环境的污染。
2.提升生产技术:优化生产工艺,提高水泥生产的效率和质量,降低生产成本。
3.节约能源:改造现有设备和流程,减少能源消耗,提高能源利用率,实现节能减排。
4.改善员工工作条件:对厂区进行环境整治,改善员工的工作和生活环境,提升生产效率和员工工作积极性。
三、工程内容1.引进先进生产设备:包括新型煤磨和水泥磨等设备,采用最新的生产技术,提高生产效率和产品质量。
2.改造尾排处理系统:对尾排处理系统进行改造升级,增加新的除尘、脱硫设备,降低废气对环境的污染。
3.废水处理系统升级:对废水处理系统进行改造升级,增加新的废水处理设备,净化废水,达到排放标准。
4.推广新型燃料使用:引入新型的清洁能源燃料,如天然气、生物质燃料等,减少对煤炭等传统燃料的使用。
5.改善厂区环境:对厂区进行整体环境改造,包括园林绿化、道路修整、车间设施更新等,提高员工工作和生活的舒适度。
四、实施方法1.成立专门的改造工程管理小组:制定详细的改造计划,明确目标和任务,确保工程的顺利进行和达到预期效果。
2.选择可靠的设备和技术供应商:根据工程需求,选择具有丰富经验和优质服务的设备和技术供应商,确保工程质量和进度。
3.制定细致的改造计划和工期安排:根据实际情况,合理安排改造工程的进度和工期,确保改造工程的有序进行。
4.保障项目资金和人力资源:充分保障改造工程所需的资金和人力资源,确保项目的顺利实施。
td窑外分解生产线实用技术改造几点看法

700t/d 窑外分解生产线技术改造地几点看法2007-8-30 作者:作者:朱大来 合肥水泥工业研究设计院1 引言水泥窑外分解技术是七十年代国际上开发地一种新工艺,八十年代以来,该项技术在我国也得到迅速发展,规模由小到大,各种规模地新型干法生产线已有近百条相继投产.由于700t/d 生产线是我国研究窑外分解技术地基础,所以其数量占全国新型干法生产线总数地30%~40%.但是,由于各种原因,有不少新型干法生产线尚不能达产达标,影响了这项新技术地发挥和企业地经济效益.我院近年来在部分700t/d 生产工艺线上进行了技术改造,取得了较为明显地效果,为工厂获得了一定地经济效益.本文就我院在700t/d 生产线改造中所作地一些技术方案提出几点个人看法,不妥之处,敬请同行指正.2 700t/d 生产线普遍存在地问题及对策2.1 分解炉及预热器系统由于国内原煤热值普遍偏低,初期研制地分解炉预热器大多属引进消化国外技术,经过十几年地生产实践证明:该系统对燃料地适应性不强,存在煤粉不完全燃烧,产生预热器结皮、堵塞现象,需要对其进行改造.入窑碳酸钙分解率是衡量新型干法生产线成功与否地重要参数之一,结合工厂原、燃料地化学成分和当地地自然条件,选用合适地分解炉容积是技改工作地最关键地一步.目前国内有一种趋势:改造分解炉就意味着扩大炉体容积,这实际上带有一定地片面性,改造分解炉主要是提高炉内部容积利用率和煤粉燃尽率,稳定入窑物料地分解率.实践证明:一般特征粒径为30~40μm 地料粉,分解温度为820~870℃,要求分解率为85%~95%时,其分解时间平均约4~10s.延长物料在炉内地停留时间,单靠降低风速或增大炉地容积是难以解决地.主要地方法是:使炉内地气流作适当地旋回运动或喷腾运动,或是二者结合,以造成旋风效应或喷腾效应,使气流与料粉产生相对运动而使料滞留.在炉内物料浓度增加到出口浓度地4~6倍时,炉内物料地停留时间即可达到气流通过时间地4~6倍,这样物料在炉内就能达到预期地效果.根据以上原理,我院在700t/d生产线预热器、分解炉改造中,主要做法有如下几点:(1)根据当地地自然条件和原、燃料地化学成分选择适合具体情况地分解炉容积确保入窑生料碳酸钙地分解率.(2)适当改变分解炉进风、进料方式和在混合室内增设一定量地缩口,以增加分解炉地喷腾效应,达到延长物料在炉内停留时间地目地.(3)加强系统密封,延长1级筒和最低级旋风筒地内筒高度,改变内筒地材质和结构形式,减少物料在预热器系统地内循环和出口浓度.有条件地地方在低级旋风筒锥部加设膨胀仓,将各级撒料板改为水平可调式,尽可能地保证物料在预热器内分散均匀.(4)在保证不掉料地前提下,适当地降低窑尾缩口和三次风入口地风速.1997年我院分别对甘肃窑街水泥厂和江苏霸王山水泥厂700t/d生产线RSP分解炉进行了改造,前者扩大了分解炉地容积,后者减少了分解炉容积,均取得了良好地效果.窑街厂地处海拔1800米高原,分解炉容积为120m3,气体在炉内地停留时间为2.45s,入窑生料地分解率仅为50%~70%.在改造时,考虑到工厂地实际情况,在分解炉混合室出口加设倒U 形分解管道,使分解炉总容积达230m3,气体地停留时间为4.1s.改造后入窑生料分解率达到85%~95%,投产后第二个月就实现了月达产.霸王山厂改造前分解炉容积为220m3,由于分解炉地入料方式不合理,造成长期分解率低于80%以下,达不到设计指标.改造时,将分解炉SC室截短2.4m,改变了生料入炉地进料方式,炉体地总容积为148.67m3.点火试生产后,入窑生料地分解率稳定在85%以上,月平均台时产量达31.66t/h,改造达到了预期地效果.2.2 喂煤、喂料系统地改造目前国内700t/h生产线大多采用“双管螺旋喂料机+冲击流量计”地方式来喂煤、喂料.由于工艺选型和布局地不合理,往往造成料粉流动不畅,控制不及时,计量不准确地现象,难以保证回转窑热工制度地稳定.在经济条件许可地情况下,我院一般推荐以下三种喂料系统:(1)选用引进申克技术国内研究开发地“称重仓+电子皮带秤”所组成地入窑生料喂料计量系统;(2)选用PFISTER公司地转子秤;(3)选用日本粉研转子秤;在经济条件不具备地条件下,我院采用如下两种方式对喂料系统进行改造:(1)物料大循环计量系统图1 喂料系统改造(1)如图1所示:该系统采用物料循环方式,保证喂料仓内物料恒定,进而使双管螺旋喂料机地填充率得到保证,稳定料流.采用锁风和放风相结合地方式,尽可能地减少气力输送设备地余风对计量设备地影响,达到计量准确地目地.(2)对直喂式系统增设搅拌器图2 喂料系统改造(2)如图2所示:在大循环系统无法实施地地方,除增加密封、锁风设备外,于物料仓下部设置搅拌器松动装置,以保证物料在仓内地流动性和防止结拱、堵塞现象.以上两种方式分别在霸王山和窑街水泥厂改造中实施使用,效果良好.2.3 熟料冷却机系统熟料冷却机是700t/h新型干法生产线中主要设备之一,也是影响回转窑运转率最主要因素.近年来篦冷机技术发展迅速,从八十年代中期到现在我院篦冷机已发展到第三代,九十年代初期以前建成地700t/h生产线篦冷机大多都存在如下几个问题:(1)篦板地形式、连接方式和各风室地划分不合理,小拉链机含在篦冷机风室内部,造成各风室相互串风,冷却效果不佳,产生红料、掉篦板,更严重者使篦板梁、活动机架毁坏等现象.(2)托轮轴承座设计在机内,润滑油难以加入,在恶劣工作条件下,常造成轴承损坏、维护和修整都很困难.针对以上地问题,我院在江苏邳县、霸王山、江西南昌、甘肃窑街等厂地篦冷机改造中,根据工厂地具体情况和我院新近研究地成果,分别进行了改造,达到预期地效果,主要方法如下:(1)更换篦板,改变篦板地结构和固定方式,同时对高温段地篦床面积进行调整,增加通风面积.(2)重新划分各风室,将1室地拉链机调整至机外,增加锁料装置.加强各风室之间地密封,使各风室分工明确.(3)将传动轴承移至机外,改造润滑油系统,为传动轴承创造良好地工作条件.(4)增设必要地检测仪表和调节回路,使篦冷机在厚料层状态下操作,确保设备长期安全运转.2.4 生料配料及均化系统国内700t/h生产线由于受规模地限制,一般均未设置预均化系统,对生料配料和均化设施提出更高地要求.工厂常用地是“电子皮带秤+气力均化”系统.但有些厂效果并不理想,生料化学成分波动较大,入窑生料合格率仅达40%,物料煅烧困难.我们在工厂改造中,一般采用两种途径:(1)完善工厂现有生料配料系统地工艺布置.前期设计选型地皮带秤宽度偏小,出现漏料、卡料等现象,加之受当时技术条件地限制,皮带秤和QCS系统质量存在一些问题.所以,改造时选用近年生产地宽型电子皮带秤和新型QCS系统代替原有系统.(2)修复生料均化设备,对于采用压缩空气作气源地工厂增设滤水装置,建立岗位责任制,防止气源中水分地带入而影响均化效果.2.5 窑尾废气系统针对增湿塔易“湿底”、堵料,出口废气温度偏高,影响窑尾电收尘效率地现象,用改造塔底密封螺旋输送机和采用中压回流喷嘴地方式来完善.这两项措施改善了塔内地喷水雾化条件,方便了喷水量地调节,为提高增湿塔和电收尘地使用效率创造了条件.2.6 其它方面增设必要地检测仪表和调节回路,以便于操作人员及时地了解生产过程中地参数变化,进行及时地调节,保持烧成系统热工制度地稳定.帮助工厂掌握和了解新型干法生产线地特点和性能,对操作人员进行岗位培训,以便于工厂地管理和操作.3 部分700t/h生产线改造前、后情况介绍3.1 邳县水泥厂技改工程该厂700t/d预分解窑是我国第一台烧煤分解炉窑.八十年代初建成,由于该预分解窑是在14.7t/h地四级预热窑基础上改建地,部分设备规格偏小、型号偏旧,使预热器和窑地生产能力发挥受到限制.1994年我院承担了工厂地改造工程,同年8月开始进行系统改造,10月全部项目改造完毕.11月4日点火试生产,1995年3月实现72h达标,平均台时产量31.55t/h.改造前后主要技术经济指标见表1.表1 改造前后主要技术经济指标对比3.2 兰州市窑街水泥厂技改工程该厂700t/d窑外分解生产线始建于1989年,由于地处高原,设计产量定为26t/h,1991年投产.长期以来一直达不到设计能力,6年共生产水泥45万t,企业累计亏损665万元.我院于1996年10月承担该厂技改工程,1997年元月开始实施现场改造,1997年4月投料试生产,投产后第一个月生产熟料14470t,第二个月生产熟料15831t,实现了月达产.表2、表3分别列出了改造前后地生产情况.表2 改造前生产记录表3 改造后生产记录3.3 江苏霸王山水泥厂技改工程霸王山700t/h窑外分解生产线始建于1982年,为五级分解炉预热器窑,1988年投产,产量一直徘徊在500t/h左右.该厂于1992年对生产线实施第一次改造,技改投资1000万人民币左右,改造后经3年运行产量仍未达到设计指标,平均年产熟料12.86万t.我院于1996年9月承接该厂技改工程,工厂于1997年元月实施停窑改造,2月份点火试车,1997年3~5月,3个月平均台时达31.66t/h(759.6t/d)改造达到预期地效果.表4、5列出了改造前后地生产情况.表4 改造前生产记录表5 改造后生产记录版权申明本文部分内容,包括文字、图片、以及设计等在网上搜集整理.版权为个人所有This article includes some parts, including text, pictures, and design. Copyright is personal ownership.b5E2R。
减少窑内结球的措施

4 结 语
50 d新型 于法预 分解 窑能 够 生产 美标 水 泥 00t /
熟料等一些特殊品种水泥熟料 , 但切忌无过渡一步
到位 改变熟 料配 比, 否则 会 对 回转 窑热 工 的稳 定 和 安全 运行产 生不 利 影 响 , 引起 窑 况 、 质量 大 的 波动 ,
制在 80— 6 范围内, 8 80o C 严禁分解炉烧大火 , 超过 80o 生料 分解率 9 % 为宜 , 8 C, 0 对尾温控制在 15 00
1 前 言
20 05年元 月 河 南 省七 里 岗水 泥 厂 与北 京 赛 凯 迪 水泥技 术公 司合作对 10 d线分解 炉 系统进行 00t /
出现频率结球现象, 窑内出的料球大小在 1 m左右,
结构较致 密 , 易卡在 篦冷 机破 碎机 人 口, 织人 员 处 组
理费时又有烫伤的危险, 影响了大窑的有效运转。
维普资讯
减 少 窑 内结球 的措 施
张克军 , 留山 毕
( 河南 省 七 里 岗水 泥 厂 , 南 4 2 7 ) 河 5 30
中图分类号 :U126 2 T 7. 2
文献标识 码 : B
文章编 号 : 0 .12 (07 0 00 0 1 3- 34 20 )6— 0 8— 2 0
参数的调整优化宜采取适度过渡 、 循序渐进的较稳 妥的方法 , 虽然需付出较高的成本代价。即使新型 50 d于法 预分 解 窑 对 原燃 材 料 的适 应 性 强 , 00t / 但
采 工制度 的稳 定 产生不 利影 响 , 前 面 实例 可 知对 窑 衬 的破 坏 是 从 灾 难性 的 , 同时熟料 质量稳 定性变 差 。 342 煅烧 参数 的调 整 : .. 从煅烧 美标 熟料方 案 的分
td窑外分解生产线技术改造几点看法

700t/d窑外分解生产线技术改造地几点看法者:2007-8-30作作者:朱大来合肥水泥工业研究设计院1引言水泥窑外分解技术是七十年代国际上开发地一种新工艺,八十年代以来,该项技术在我国也得到迅速发展,规模由小到大,各种规模地新型干法生产线已有近百条相继投产。
由于 700t/d生产线是我国研究窑外分解技术地基础,所以其数量占全国新型干法生产线总数地30%〜40%。
但是,由于各种原因,有不少新型干法生产线尚不能达产达标,影响了这项新技术地发挥和企业地经济效益。
我院近年来在部分700t/d生产工艺线上进行了技术改造,取得了较为明显地效果,为工厂获得了一定地经济效益。
本文就我院在 700t/d生产线改造中所作地一些技术方案提出几点个人看法,不妥之处,敬请同行指正。
2 700t/d生产线普遍存在地问题及对策2.1分解炉及预热器系统由于国内原煤热值普遍偏低,初期研制地分解炉预热器大多属引进消化国外技术,经过十几年地生产实践证明:该系统对燃料地适应性不强,存在煤粉不完全燃烧,产生预热器结皮、堵塞现象,需要对其进行改造。
入窑碳酸钙分解率是衡量新型干法生产线成功与否地重要参数之一,结合工厂原、燃料地化学成分和当地地自然条件,选用合适地分解炉容积是技改工作地最关键地一步。
目前国内有一种趋势:改造分解炉就意味着扩大炉体容积,这实际上带有一定地片面性,改造分解炉主要是提高炉内部容积利用率和煤粉燃尽率,稳定入窑物料地分解率。
实践证明:一般特征粒径为30〜40 pm地料粉,分解温度为820〜870 C,要求分解率为 85%〜95%时,其分解时间平均约4〜10s。
延长物料在炉内地停留时间,单靠降低风速或增大炉地容积是难以解决地。
主要地方法是:使炉内地气流作适当地旋回运动或喷腾运动,或是二者结合,以造成旋风效应或喷腾效应,使气流与料粉产生相对运动而使料滞留。
在炉内物料浓度增加到出口浓度地4〜6 倍时,炉内物料地停留时间即可达到气流通过时间地4〜6倍,这样物料在炉内就能达到预期地效果。
水泥生产中分解炉的作用
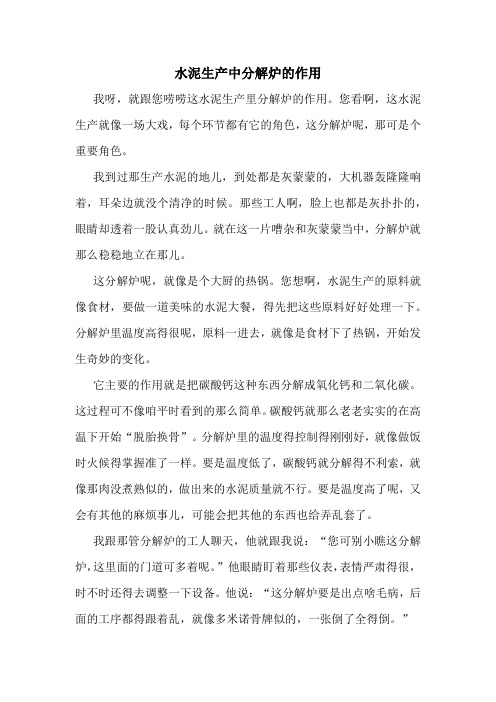
水泥生产中分解炉的作用我呀,就跟您唠唠这水泥生产里分解炉的作用。
您看啊,这水泥生产就像一场大戏,每个环节都有它的角色,这分解炉呢,那可是个重要角色。
我到过那生产水泥的地儿,到处都是灰蒙蒙的,大机器轰隆隆响着,耳朵边就没个清净的时候。
那些工人啊,脸上也都是灰扑扑的,眼睛却透着一股认真劲儿。
就在这一片嘈杂和灰蒙蒙当中,分解炉就那么稳稳地立在那儿。
这分解炉呢,就像是个大厨的热锅。
您想啊,水泥生产的原料就像食材,要做一道美味的水泥大餐,得先把这些原料好好处理一下。
分解炉里温度高得很呢,原料一进去,就像是食材下了热锅,开始发生奇妙的变化。
它主要的作用就是把碳酸钙这种东西分解成氧化钙和二氧化碳。
这过程可不像咱平时看到的那么简单。
碳酸钙就那么老老实实的在高温下开始“脱胎换骨”。
分解炉里的温度得控制得刚刚好,就像做饭时火候得掌握准了一样。
要是温度低了,碳酸钙就分解得不利索,就像那肉没煮熟似的,做出来的水泥质量就不行。
要是温度高了呢,又会有其他的麻烦事儿,可能会把其他的东西也给弄乱套了。
我跟那管分解炉的工人聊天,他就跟我说:“您可别小瞧这分解炉,这里面的门道可多着呢。
”他眼睛盯着那些仪表,表情严肃得很,时不时还得去调整一下设备。
他说:“这分解炉要是出点啥毛病,后面的工序都得跟着乱,就像多米诺骨牌似的,一张倒了全得倒。
”而且啊,分解炉还影响着整个生产的效率呢。
它要是工作得顺顺利利的,原料分解得快,后面的工序就能跟着快速地进行下去。
就好比一个团队里,有个能干的人把前期工作都做好了,后面的人干起活来也轻松,整个工程就能快速往前推进。
要是分解炉在那儿慢吞吞的,那整个水泥生产就像是被堵住的河道,水就流不动喽。
这分解炉啊,在水泥生产里就像是一个默默奉献的老黄牛,外表看着不咋起眼,灰扑扑的一个大炉子,但是它的作用那可是大了去了。
它的一举一动都牵扯着整个水泥生产的好坏呢。
我有时候就看着那分解炉,就像看着一个老朋友,虽然它不会说话,但是我能感觉到它的重要性。
【案例】电石渣制水泥生产线分解炉连续红炉事故分析

【案例】电石渣制水泥生产线分解炉连续红炉事故分析为处理干法乙炔项目的电石渣,内蒙古某企业建设了一条利用电石渣替代石灰石配料的2500t/d生产线,其窑尾采用RSP分解炉并配备五级旋风预热器。
2012年9月,该线建成投产,运行过程中,各项参数均能达到或接近设计指标,但调试阶段曾先后发生过三次分解炉红炉事故。
红炉事故的分析及处理1.1首次投料运行7天后,分解炉SC室下部靠近MC室一侧发生了红炉事故。
事故发生时,相关设计人员不在现场,经现场人员判断,可能是耐火砖砌筑不牢所致,故对耐火砖受损部位重新进行了砌筑处理。
1.2SC室掉砖部位经修补砌筑后于10月份投入生产。
投料后72h。
分解炉SC室再次发生掉砖红炉事故,且红炉部位与首次红炉位置接近。
结合现场情况,分析后认为红炉可能由以下两方面因素造成:1)窑尾风量及风压不足试生产过程中,C1出口压力只有一4000Pa,而相同设计参数的窑尾系统。
一般在一5000—5500Pa,该线系统负压过低。
生产中窑内煅烧工况不好,表现为火焰不够明亮,常有夹心黄料出现,排除操作因素,一般是由于窑内缺氧,还原气氛严重引起的;在三次风管人SC 室的高温闸板阀处,有周期性的往外少量冒灰现象,以上两点也证明了该系统负压过低。
虽然C1出口负压低,但高温风机运行过程中却经常超电流。
对现场进行逐一排查后发现,窑尾废气管道与余热锅炉连接处,只安装了一台百叶阀,百叶阀入ISl也未使用盲板封闭,密封效果很差。
运行时,在该接口附近可听到管道“呼呼”的窜风声,此处是窑尾的主要漏风点。
另外,检查发现废气管道中有个别增湿管道喷枪已损坏,喷出的水呈液态,易造成管道积灰,再加上余热发电接口严重漏风,管道温差波动大,导致废气管道常塌料,直接导致窑尾负压周期性降低,间接造成三次风管冒灰以及窑出现黄心料。
2)煤粉挥发分高、燃烧速度快该线设计时拟采用无烟煤.而实际使用的煤粉着火点低、挥发分高(20.6%),起火燃烧迅速且燃尽速度快,在分解炉下锥体部位形成区域性高温,再加上煤灰分高(27.7%),易造成分解炉结皮,甚至烧损内衬。
1000t预分解窑28至34m段结圈的原因分析和预防处理1

1000t预分解窑28至34m段结圈的原因分析和预防处理1--------------------------------------------------------------------------------作者:-作者:谢培顺单位:南宁正大建材有限公司中图分类号:TQ172.622.26 文献标识码:B 文章编号:1002-9877(2003)07-0026-060 引言截止到2001年末,我国已投产的1000t/d生产线有57条,熟料设计生产能力总计为1762万t/年[1],这些干法生产线投产后,几乎都遇到过窑28~34m段结圈问题,圈一旦形成,使该处的横断面积显著减少,对窑的热工制度破坏较大,轻则影响窑内通风,熟料产质量下降,重则阻碍物料运动,窑尾出现漏料,导致窑尾密封装置变形损坏,不得不止料处理,频繁结后圈,使窑的运转率降低,煤耗、电耗、砖耗大幅度上升,造成较大的经济损失。
引起结圈的因素很多,形成的机理也较复杂,它与原料性质、生料成分、燃料燃烧特性和燃烧状况、煤灰和生料组成、窑的操作和生产管理水平等有关。
本文通过对不同地域、不同时期投产的1000t/d窑出现的28~34m段结圈的原因进行分析,并结合生产实践的体会和认识,谈谈该段结圈的预防和处理。
1 结圈原因分析由于预分解窑生料的预热分解在预热器和分解炉内进行,生料入窑时,已有90%~95%的碳酸盐分解。
回转窑的功能之一是将剩余的碳酸钙迅速分解的同时,石灰石质同粘土质组分间,通过质点的相互扩散,进行固相反应,形成C3A、C4AF、C2S。
因28~34m段正是固相反应带和烧成带交界的过渡带,这个区域内,物料一方面接受火焰辐射对流传给的热量,另一方面由于熟料矿物固相反应是放热反应,固相反应放出的热量约为420~500J/g,理论上放热量达420J/g时,就足以使物料温度升高300℃以上,物料从900℃升到1250℃的时间约为5~6min。
水泥厂工艺技术部技改成果展示

某某水泥有限公司技改成果展示一、生料磨研磨体级配调整1、项目内容由于骨料厂石粉的掺入导致入磨物料平均粒度变小,原生料磨1仓钢球级配已不匹配现有的工艺粉磨要求,工艺技术部经粒度分析,入磨D80粒度下降了5mm,故将生料磨钢球平均球径由76.3mm调整到68.7mm。
2、项目目的提高生料磨1仓研磨能力,降低磨机循环负荷,提高台产,降低电耗。
3、项目成果1)技改造后平均台产已稳定在240吨,较技改前平均台产提高35吨。
2)经技改前后对比平均电耗下降了3.35Kwh/t。
3)按全年生料产量166万吨计算,全年共节省电量556.1万Kwh。
二、1#窑尾缩口扩径、分解炉喂煤及C4撒料箱技改1、项目内容2017年底1#窑在进行分解炉扩容、尾煤喂入系统及撒料箱改造后,在生产运行过程中,预热器系统及窑内不断出现结皮、结圈等现象,特别是在后期曾出现因分解炉锥体结皮的停窑事故。
后经工厂研究决定对窑尾缩口、尾煤喂入位置及C4撒料箱进行再次优化。
在工厂领导牵头下,由工艺技术部主导,利用停窑机会对其进行了优化改造。
将窑尾缩口从170mm扩大到182mm,将尾煤主喂煤管道平移45°,将C4内置撒料板更换为外置撒料箱。
2、项目目的1)降低窑内通风阻力,改善煅烧环境。
2)改善预热器系统及窑内不断出现的结皮、结圈等现象。
3)稳定台产,降低能耗。
3、项目成果1)技改后预热器系统及窑内结皮、结圈等现象得到明显改善。
2)1#窑在技改后台产基本稳定在2979t/d,较技改前提升台产260t/d。
3)2018年全年熟料平均实物煤耗136.3Kg/t,较2017年下降2.5Kg/t,全年共节省煤炭2922.7吨。
三、2#窑C1旋风筒高效分离器结合1#2#窑系统实际运行情况,通过对比,为减少2#窑入窑生料内循环,稳定窑况,降低热耗。
工厂管理层决定按照1#窑的设计标准在2#窑C1旋风筒内增加一套高效分离器,以提高C1旋风筒的收尘效率,减少物料内循环。
水泥厂设备改造工程方案
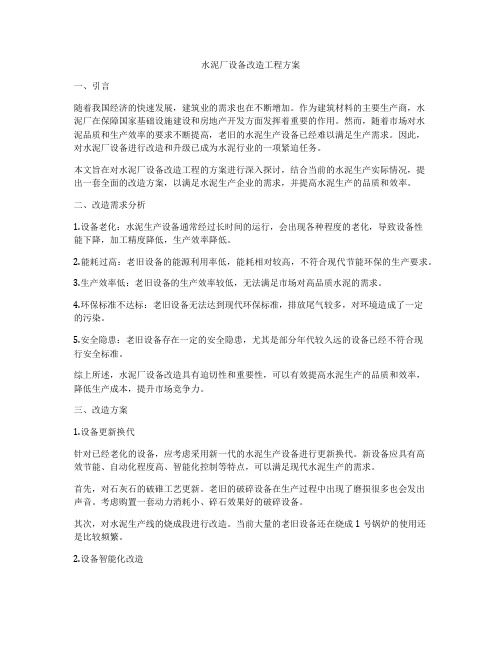
水泥厂设备改造工程方案一、引言随着我国经济的快速发展,建筑业的需求也在不断增加。
作为建筑材料的主要生产商,水泥厂在保障国家基础设施建设和房地产开发方面发挥着重要的作用。
然而,随着市场对水泥品质和生产效率的要求不断提高,老旧的水泥生产设备已经难以满足生产需求。
因此,对水泥厂设备进行改造和升级已成为水泥行业的一项紧迫任务。
本文旨在对水泥厂设备改造工程的方案进行深入探讨,结合当前的水泥生产实际情况,提出一套全面的改造方案,以满足水泥生产企业的需求,并提高水泥生产的品质和效率。
二、改造需求分析1.设备老化:水泥生产设备通常经过长时间的运行,会出现各种程度的老化,导致设备性能下降,加工精度降低,生产效率降低。
2.能耗过高:老旧设备的能源利用率低,能耗相对较高,不符合现代节能环保的生产要求。
3.生产效率低:老旧设备的生产效率较低,无法满足市场对高品质水泥的需求。
4.环保标准不达标:老旧设备无法达到现代环保标准,排放尾气较多,对环境造成了一定的污染。
5.安全隐患:老旧设备存在一定的安全隐患,尤其是部分年代较久远的设备已经不符合现行安全标准。
综上所述,水泥厂设备改造具有迫切性和重要性,可以有效提高水泥生产的品质和效率,降低生产成本,提升市场竞争力。
三、改造方案1.设备更新换代针对已经老化的设备,应考虑采用新一代的水泥生产设备进行更新换代。
新设备应具有高效节能、自动化程度高、智能化控制等特点,可以满足现代水泥生产的需求。
首先,对石灰石的破碓工艺更新。
老旧的破碎设备在生产过程中出现了磨损很多也会发出声音。
考虑购置一套动力消耗小、碎石效果好的破碎设备。
其次,对水泥生产线的烧成段进行改造。
当前大量的老旧设备还在烧成 1号锅炉的使用还是比较频繁。
2.设备智能化改造采用智能化控制系统对水泥生产设备进行改造,实现对生产过程的全程监控和智能化操控。
通过传感器、仪表等设备的联网连接,实现对生产设备运行状态、设备故障、能源消耗等数据的实时监控和分析,以实现对生产过程的精准控制。
某水泥厂窑尾分解炉拆除施工方案
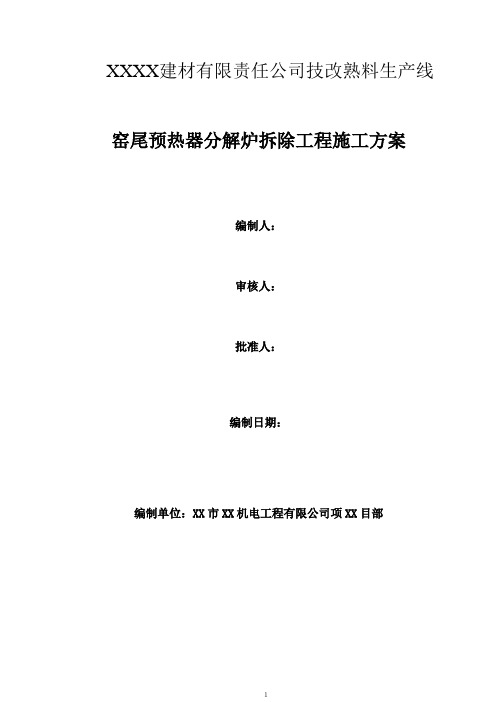
XXXX建材有限责任公司技改熟料生产线窑尾预热器分解炉拆除工程施工方案编制人:审核人:批准人:编制日期:编制单位:XX市XX机电工程有限公司项XX目部第一章工程概况一、总体概况云南XX市XX区XX镇XXXX建材有限责任公司熟料生产线窑尾预热器分解炉更换,拆除及运输的工程慨况及工程特点,窑尾预热器分解炉拆除的分解技术,吊装方法,拆除吊装的安全措施,关键词:高空吊装拆除,防止坠落。
第二章编制依据第一节编制依据1、XXXX建材有限责任公司熟料生产线技改机电设备安装工程施工合同。
2、《建筑拆除工程安全技术规范》(JGJ147-2004)。
3、《建筑机械使用安全技术规程》(JGJ33-2001)。
4、《建筑机械使用安全技术规程》(JGJ33-2001)。
5、《建筑施工高处作业安全技术规范》(JGJ80-91)。
6、《建筑物、构筑物拆除技术规程》(DBJ08-70-98)。
7、公司《质量保证手册》、《管理标准》及各种管理制度。
8、同类工程施工经验。
9、国家及地方相关规范及标准。
第二节编制说明1、XXXX建材有限责任公司熟料生产线实地查看,并结合我公司以往施工经验编制本施工方案。
2、本施工方案,介绍我公司在该工程上投入的主要机械设备、劳动力情况以及施工组织、主要施工工艺方法、技术措施、质量保证体系和措施、安全生产及文明施工保证措施、环境保护措施等。
第三节编制原则1、坚持科学施工顺序,并结合工程特点、现场环境情况、施工条件等具体情况。
2、加强质量管理、确保工程“合格”。
3、高度重视对周边环境卫生、噪声、治安方面的影响,充分利用建设单位可以提供的场地,作好生产、生活和治安方面的安排,配置工作状态良好的设备。
4、从实际出发,在确保人身安全和财产安全的前提下,选择经济、合理的拆除方案,进行科学的组织,以实现安全、经济、速度快的目标。
第三章施工组织第一节技术准备工作1、首先熟悉被拆设备及钢结构建筑物的周边环境状况,清理施工场地,规划施工现场交通道路,保证工程车辆进出畅通。
预分解窑后结圈的处理措施

预分解窑后结圈的处理措施
张克军;孙富军
【期刊名称】《新世纪水泥导报》
【年(卷),期】2006(12)6
【摘要】河南省七里岗水泥厂1000t/d新型干法线窑规格为①3.2m×46m,
预热器为五级低压损旋风筒结构,分解炉为DD炉串联1台NMFC炉。
2006年
2月在距窑口32-36m处有后结圈现象,投料量加至60t/d,窑尾即开始露料,窑内通风受阻,火焰伸不进去,频繁出现正压,窑尾温度高,影响了生产的正常进行,窑筒体温度测量显示此处温度仅200℃左右。
我们对后结圈的原因进行了分析,
在工艺、现场看火方面进行了一些改进,取得了较好的效果。
【总页数】2页(P9-10)
【作者】张克军;孙富军
【作者单位】河南省七里岗水泥厂,452370;河南省七里岗水泥厂,452370
【正文语种】中文
【中图分类】TQ17
【相关文献】
1.2 500t/d预分解窑后结圈的原因分析与预防 [J],
2.预分解窑后结圈的形成原因及处理 [J], 赵晓东
3.2500t/d预分解窑后结圈的原因分析与预防 [J], 李仁龙
4.预分解窑后结圈的原因及处理措施 [J], 张振旺
5.预防预分解窑结后圈的原因与对策 [J], 向安斌
因版权原因,仅展示原文概要,查看原文内容请购买。
谈离线式N-MFC炉的操作
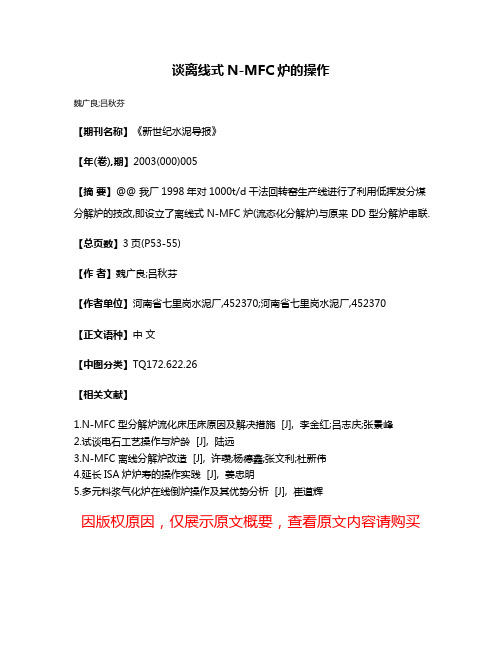
谈离线式N-MFC炉的操作
魏广良;吕秋芬
【期刊名称】《新世纪水泥导报》
【年(卷),期】2003(000)005
【摘要】@@ 我厂1998年对1000t/d干法回转窑生产线进行了利用低挥发分煤分解炉的技改,即设立了离线式N-MFC炉(流态化分解炉)与原来DD型分解炉串联.【总页数】3页(P53-55)
【作者】魏广良;吕秋芬
【作者单位】河南省七里岗水泥厂,452370;河南省七里岗水泥厂,452370
【正文语种】中文
【中图分类】TQ172.622.26
【相关文献】
1.N-MFC型分解炉流化床压床原因及解决措施 [J], 李金红;吕志庆;张景峰
2.试谈电石工艺操作与炉龄 [J], 陆远
3.N-MFC离线分解炉改造 [J], 许瓒;杨德鑫;张文利;杜新伟
4.延长ISA炉炉寿的操作实践 [J], 姜忠明
5.多元料浆气化炉在线倒炉操作及其优势分析 [J], 崔道辉
因版权原因,仅展示原文概要,查看原文内容请购买。
水泥厂熟料炉维修及砌筑更换施工专项方案
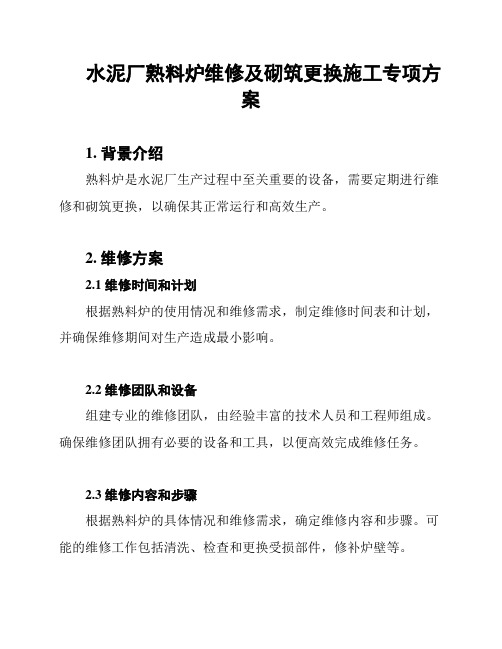
水泥厂熟料炉维修及砌筑更换施工专项方案1. 背景介绍熟料炉是水泥厂生产过程中至关重要的设备,需要定期进行维修和砌筑更换,以确保其正常运行和高效生产。
2. 维修方案2.1 维修时间和计划根据熟料炉的使用情况和维修需求,制定维修时间表和计划,并确保维修期间对生产造成最小影响。
2.2 维修团队和设备组建专业的维修团队,由经验丰富的技术人员和工程师组成。
确保维修团队拥有必要的设备和工具,以便高效完成维修任务。
2.3 维修内容和步骤根据熟料炉的具体情况和维修需求,确定维修内容和步骤。
可能的维修工作包括清洗、检查和更换受损部件,修补炉壁等。
2.4 安全措施在维修过程中,确保严格遵守安全操作规程,采取必要的安全措施,以保护维修人员和设备。
3. 砌筑更换方案3.1 砌筑更换时间和计划根据熟料炉的使用寿命和需要更换的部位,制定砌筑更换时间表和计划,并确保更换期间对生产造成最小影响。
3.2 砌筑团队和材料聘请经验丰富的砌筑团队,确保团队成员具备必要的技术和经验。
采购高质量的砌筑材料,以确保更换后的砌筑具有结构强度和耐高温性能。
3.3 砌筑更换步骤根据需要更换的部位,制定砌筑更换步骤,并在施工过程中确保严格按照标准操作程序进行。
3.4 质量检验和验收在砌筑更换完成后,进行质量检验和验收,确保砌筑工作符合设计要求和安全标准。
4. 总结水泥厂熟料炉维修及砌筑更换是一项重要的施工任务,需要制定专项方案并严格执行。
通过合理的维修和更换工作,可以确保熟料炉的正常运行和高效生产,提高生产效率和质量。
请根据实际情况制定详细的方案,并始终遵守相关安全规定和施工标准。
- 1、下载文档前请自行甄别文档内容的完整性,平台不提供额外的编辑、内容补充、找答案等附加服务。
- 2、"仅部分预览"的文档,不可在线预览部分如存在完整性等问题,可反馈申请退款(可完整预览的文档不适用该条件!)。
- 3、如文档侵犯您的权益,请联系客服反馈,我们会尽快为您处理(人工客服工作时间:9:00-18:30)。
・!"・#$$%&’(&%
七里岗水泥厂现有!$$$)*+和,$$)*+预分解
干法线各!条,年产水泥-$万)。
!烧成系统主机设备
烧成系统主机设备见表!。
表!烧成系统主机设备
设备名称!$$$)*+.二线/,$$)*+.一线/
预热器
0!#1!%%!#22#1!%$$$22
0#!1!34!#22!1!3"$$22
0%!1!"!!-22!1!3"$$22
03!1!"!!-22!1!34$$22
0"!1!"3!-22!1!34$$22分解炉55炉!34!#’67炉!33$$22篦冷机-$8914#"9#:!%2;!%:"2
高温风机5<==#3,##$$$2%*>,,?@A6<==##,!4$$$2%*>B,?@A 窑头排风机C31,%D!-5技改后同左回转窑!%:#2;3-2!%2;342
"分解炉改造前状况
!)预热器的堵塞经常发生,严重时!星期停窑处理%次,预热器的堵塞一般采用人工捅堵的方法,危险性大,处理时间长;0"出口温度经常高于分解炉
出口,0
3、0
"
内套筒几乎全部烧掉。
#)分解炉不适应烧低挥发分煤。
!88,年添加本地低挥发分煤后,分解炉、竖直烟道结皮较多,需要经常处理。
#原分解炉的技术分析
一线分解炉采用E01’67,二线为E0155炉,均是由天津水泥工业设计院设计的,预热器为五级旋风低压损结构。
’67炉具有喷腾和旋流效应,物料滞留时间为!$F左右;55炉具有单纯喷腾效应,物料滞留时间8F左右。
我厂因原燃料成分波动大,又采用人工定时取料进行化验分析,存在时间滞后、数值偏差大、指标调整慢的缺点。
$分解炉技术改造方案选择及实施
方案!:扩大55、’67炉容,采用直径加大或顶端加高以及出口加鹅颈管的方式,延长物料停留时间。
但此方案受预热器结构限制,安装时间长。
方案#:采用扩大炉容的G6@或H70炉,煤在不同的炉型中燃烧状况有差别,通过查阅技术资料和借鉴国内部分厂家技改经验,进行比较分析:!)G6@炉内气体停留时间为%I3F,物料停留时间大于!$F,有较强的旋流和喷腾作用,扩大炉容采用扩大预燃室6=和分解室60容积,混合室H0与0"的联接采用加鹅颈管方式,但我厂需重新加工。
#)H70炉是流态化分解炉B对煤质适应性强,易于与各种6@窑实现对接,安装方便,可以使用低挥发分煤。
经过充分论证,决定增加!台H70炉与原分解炉串联,原炉可做为第二分解炉延长物料停留时间,炉底的流化床,可防止物料在炉内堆积,并保证物料分布均匀,提高分解炉燃烧效率。
天津水泥工业设计院也提出,低挥发分煤最好用分级燃烧原理,选用H70预分解工艺较好,并设计了带鹅颈管的’H70炉。
’H70采用框架外离线安装,安装时不影响窑煅烧,并接可利用检修时实现。
!884年8月对二线进行技改,经过一段时间摸索,掌握了操作方法,!884年!!月又对一线进行技改。
’H70出口与老炉均采用鹅颈管连接,原设计0
3下料管物料入分解炉的不同部位,现将其中一个入’H70,三次风改入’H70。
生产过程中,我们又在入
新炉的下料管处加撒料板。
通过调整0
3
下料管的分料阀开度,实现’H70与55炉(’67炉)的物料分
配比例,当0
3
下来的物料突然增多或成团时,超过流化床带料量,易压床,加装的撒料板分散了物料,可防止分解炉塌料。
二线技改前后工艺流程见图!、图#。
七里岗水泥厂分解炉串联改造技术
张克军,薛永华,彭利民
.七里岗水泥厂,河南新密3"#%,$/
中图分类号:EJ!,#:-##:#-文献标识码:=文章编号:!$$#184,,.#$$%/$%1$$!"1$#
水泥0KHK’E
・!"・#$$%&’(&%
水泥)*+*’,
图!二线改造前窑尾系统工艺流程
图"二线改造后窑尾系统工艺流程
低挥发分煤燃点较高,比烟煤燃点高!$$-左右,技改前三次风温仅有./$-左右。
为此我厂对篦冷机也进行了改造,三次风温达到了00$-,有利于煤粉的燃烧。
增加新分解炉后,系统阻力增大,需要加大窑系统排风机能力。
二线高温风机转速由!$1$23456提高到!#$$23456,无需增减其他设备,即可满足系统需要;一线高温风机转速由0$$23456提高到7#$23 456,考虑产量增加,窑头排风机换为8/9.%:!";。
#分解炉技术改造后效果
!<技改后,’+=)炉内物料分布均匀,热交换效率高,看火操作方便,低挥发分煤燃烧充分,)
!
出口气体温度在%#$>%/$-,分解炉出口气体温度一般
在07$-,)
1
出口气体温度0"$-左右。
出+=)炉气体在上升烟道底部与窑气混合,把窑气稀释降温,技改前烟室温度为!!1$-?技改后在71$-左右?预热器很少堵塞,烟道、分解炉结皮现象消失。
物料在分解炉的停留时间延长,入窑物料表观分解率达到了7/@,而改造前为7$@。
窑产量二线由01$A3B提高到!$$$A3B;一线由"$$A3B提高到./$A3B。
可完全使用当地低挥发分煤C!
DB
:!#@>!%@、"
6EA?DB F#1$$$GH3 GI,进厂价7$元3A,而烟煤!DB:#/@>#"@、"6EA?DB F #"$$$GH3GI?进厂价为!0$元3A<,年节约原煤费用1$$万元以上,使吨水泥成本下降!"元。
煤的工业分析见表#。
表"煤的工业分析
时间#DB3@!DB3@$DB3@%&DB3@"6EA?DB3C GH3GI<
技改前$J"!#%J"!#$J/$11J%0#"07"
技改后$J%!!!J%.#"J#%"#J$7#/%%%我厂采用石灰石、砂岩、粉煤灰和铁粉/组分配
料,熟料率值控制采用“三高”方案,)
%K、)#K含量高,熟料%B抗压强度F#0+LD,#0抗压强度达到"$+LD,熟料率值及矿物组成见表%。
表$熟料率值及矿物组成
编号
熟料率值矿物组成3@
’()*)%K)#K)%M)/M= !$J7!/#J07!J..10J!7!0J$/0J$"0J#!
#$J07##J77!J7#1%J$1##J100J11.J""
#)!777年#月我厂委托南京化工大学材料学院和河南建筑材料研究设计院对!$$$A3B预分解窑系统进行热工标定,窑产量!!1%A3B,熟料烧成热耗%%".&1"GH3GI;预热器及分解炉系统能满足低挥发分煤煅烧要求,出流态化悬浮炉时物料分解率虽仅为1"&7#@,但入窑物料分解率则达7/@。
应当指出的是,此次标定期间,燃用的乃是挥发分N!$@的无烟煤,在此条件下,分解炉仍能满足要求,说明该炉对燃煤品质变化有较强的适应性。
%结束语
在车间全体职工的共同努力下,对新系统的操作越来越熟练,!777年我厂实现了双线达产。
二线产量高时达到了!#$$A3B,一线产量高时达到了7$$A3B,#$$$年一线提前!个月完成了年生产任务。
低挥发分煤在我厂应用非常成功,!777年来窑的运转率一直保持较高的水平。
分解炉改造费用计%$$万元(含#条线篦冷机改造费用),采用本地煤年节约燃料费用1$$万元以上,短期可以收回投资。
’+=)炉非常适合我厂预分解窑系统技术改造,分解炉改造成功后,减少了工艺故障,有利于资源的合理利用,提高了技术装备水平,降低生产成本,提高了市场竞争力。
C编辑顾志玲
<。