2铸造(II)
锻造成型工艺介绍

* 再结晶:
当加热温度T再: T再=0.4T熔 原子获得更多热能,开始的某些碎晶或杂质为核心 构成新晶粒,因为是通过形核和晶核长大方式进行 的,故称再结晶。
再结晶后清除了全部加工硬化。
再结晶后晶格类型不变,只改变晶粒外形。
上升, 而塑性、韧 性下降。 * 原因:滑移面附近的 晶粒碎晶块, 晶格扭曲畸变, 增大滑移阻力, 使滑移难以 进行。
● 3、金属的回复与再结晶 * 回复:
冷作硬化是一种不稳定的现象,具有自发恢复到稳定 状态的倾向。室温下不易实现。当提高温度时,原子 获得热能,热运动加剧,当加热温度T回(用K氏温标)
●加工硬化的利用、消除
*利用:冷加工后使材料强度↑硬度↑。如冷拉
钢,不能热处理强化的金属材料。
*消除:再结晶退火(P29)650—750℃
● 热变形对金属组织和性能的影响 冷变形和热变形 * 冷变形
在再结晶温度以下的变形; 冷变形后金属强度、硬度较高,低粗糙度值。但 变形程度不宜过大,否则易裂。 * 热变形 再结晶温度以上变形。 变形具有强化作用,再结晶具有强化消除作用。在热变 形时无加工硬化痕迹。 金属压力加工大多属热变形,具有再结晶组织。
模膛 飞边槽
锤头
上模
分模面,parting plane 下模
模垫
⑵ 制坯模膛 * i) 拔长模膛 增加某一部分长度。 ii)滚压模膛 减小某部分横截面积,以增大另一部分横截面积,坯料长度基本
不变。 切断金属。
此外还有成型模镗,镦粗台, 击扁面等制坯模镗。
在设计和制造零件时,应使最大正应力的方向于纤维 方向重合,最大切应力的方向于纤维方向垂直。尽量 使纤维组织不被切断。
铜合金重力铸造教程(第二部分)
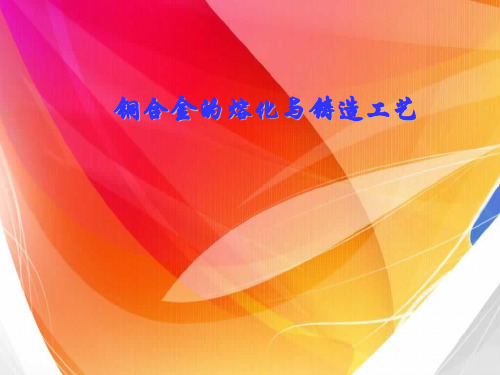
③沸腾除气法:沸腾除气是在工频有芯感 应电炉熔炼高锌黄铜时常用的一种特殊除气方 法。如熔化黄铜时锌的蒸发就可以将溶解在合 金液体中的气体去除。由于熔化温度较高超过 锌的沸点(907℃),因此在熔炼后期会出现 喷火现象,即锌的沸腾,这样有利于气体的排 除。
• (2)除渣精炼 ①静置澄清法:静置澄清过程一般是让熔 体在精炼温度下,保持一段时间使氧化及熔渣 上浮或下沉而除去。 ②浮选除渣法:浮选除渣是利用熔剂或惰 性气体与氧化物产生的某种物理化学作用,即 吸附或部分溶解作用,造成浮渣而将氧化物除 去。 ③熔剂除渣法:在熔体中加入熔剂,通过 对氧化物的吸附、溶解、化合造渣,将渣除去, 熔剂的造渣能力越强,除渣精炼的效果越好。
• 5.4.铜合金的配比
根据铁模尺寸大小要求合金配料总量为1200g
(1)黄铜(H68) 纯铜:1200g×68%=816g 锌: 1200g×32%=384g (需考虑烧损量 1.5~2%)
(2)铝青铜(QAl10) 纯铜: 1200g×90%=1080g 铝: 1200g×10%=120g
重铸基础知识
1,调整模具,清理砂筒 2,调整气压 3,漏气处贴胶 4,对准射砂口
1,增加固化时间 2,提高固化温度 3,严格按照参数混砂 1,减少固化时间 2,降低固化温度 1,仔细刮砂芯 2,射砂道小心掰掉或用锯条锯掉
夹生
焦酥
1,固化时间过长 2,固化温度过高 1,刮砂芯不仔细 2,连接射砂道敲掉后型砂表面有凹坑
4.影响铸模铸锭质量的主要因素
• (1)浇铸温度:浇铸温度过高或过低都是不 利的,因为采用较高的浇铸温度,势必就要使 炉内熔体的温度作相应的提高,这将引起铜合 金在熔化和保温过程中大量的吸气,同时也会 增加烧损,在浇铸时会使氧化加剧。此外,过 高的浇铸温度也会对铸模的寿命产生不利影响, 尤其是平模浇铸时模底板更容易遭到破坏。当 浇铸温度偏低时,熔体流动性变差,不利于气 体和夹渣上浮,也易使铸锭产生冷隔缺陷。因 此,必需根据合金的性质,结合具体的工艺熔炼时金属的损耗和氧化
金属工艺学部分课后习题解答

补充习题
下列铸件在大批量生产时,以什么铸造措施 为宜? 铝活塞金属型铸造、汽轮机叶片熔模铸造、 汽缸套离心铸造、车床床身砂型铸造、摩托车 气缸体压力铸造、汽车喇叭压力铸造、大口径 污水管离心铸造、大模数齿轮滚刀熔模铸造
压力加工:第二章 铸造
7 图示零件采用锤上模锻制造,请选择最合适旳分模面
位置? p127
I
铸造:第三章 砂型铸造
5.图示铸件在单件生产条件下该选用哪种造型措施?
方案I: 分型面为曲
面,不利于分型。
I
方案II:分型面在最
II
大截面处,且为平面,
方案可行。
铸造:第三章 砂型铸造
5.图示铸件在单件生产条件下该选用哪种造型措施?
I II
两方案均可, 但型芯头形状 不同。
铸造:第三章 砂型铸造
铸造:第一章 铸造工艺基础
8.试用下面异形梁铸钢件分析其热应力旳形成原 因,并用虚线表达出铸件旳变形方向。p49
形成原因:壁厚不均匀。
铸造:第三章 砂型铸造
5.图示铸件在单件生产条件下该选用哪种造型措施?
p73
I方案存在错箱可能。 该零件不算太高,故 方案II稍好,从冒口
II
安放来看,II方案轻 易安放。
焊接措施: 手工电弧焊、二氧化碳气体保护焊
端面车刀
6.图示铸件有几种分型方案?在大批量生产中应选择 哪种方案? p73
应采用方案I,方案II
I
型芯稳定,但φ40凸台
阻碍拔模。
II
铸造:第三章 砂型铸造
6.图示铸件有几种分型方案?在大批量生产中应选择 哪种方案? p73
I
III II
应采用方案III,方案I需要活块,且下面活 块难以取出;方案II需要挖砂。
铸造工艺设计优化

铸造工艺设计模拟优化CASTsoft在核屏蔽箱体铸钢件的生产应用市沙湾长兴铸钢有限责任公司(614900)罗建君北方恒利科技发展(100089)宋彬摘要:本文介绍北方恒利科技开发的铸造工艺设计及模拟优化CASTsoft CAD/CAE在核屏敝箱体铸钢件工艺设计及优化方面的应用,同时介绍了水玻璃七0砂型(石灰石水玻璃砂型)在核屏敝箱体铸钢件上的应用;证明了用先进的科学技术,合理的铸造工艺,控制生产关健环节,采用铬铁矿砂作坭芯面砂能生产出要求较高的探伤核屏敝铸钢件。
关键词:铸造工艺设计 CASTsoft 铸造工艺模拟浇注温度工艺优化核屏蔽铸钢件水玻璃七0砂型漂珠保温冒口套The casting process simulation and optimization CASTsoft in the nuclear shielding box of steelcasting production applicationsLeshan City, Sandy Bay, Changxing Cast Steel Co., Ltd.(614900)Luo JianjunBeijing North Fangheng Li Technology Development Co., Ltd. (100089) Song Bin Abstract :This article describes the casting process design and simulation and optimization of Beijing North the Hengli Technology Co., Ltd. developed CASTsoft CAD / CAE in the design and optimization of the nuclear shielding box for Steel Casting, also introduced water glass 70 sand (limestone water glass sand) on the nuclear shielding box steel castings; proved that advanced science and technology, casting process, production of key aspects of the use of chromite sand Cement core surface sand can produce higherflaw nuclear shielding steel castings.Keywords:Casting Process Design CASTsoft Casting process simulation Pouring temperature Process optimization Nuclear shielding of steel castings Floating Beadsriser一、前言目前,在川多数铸造企业采用传统水玻璃七0砂型(石灰石水玻璃砂型)工艺进行铸件生产。
铸造考试题
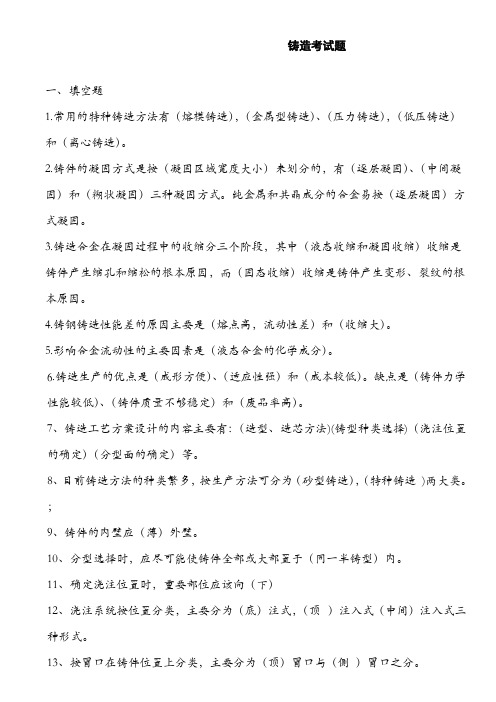
铸造考试题一、填空题1.常用的特种铸造方法有(熔模铸造),(金属型铸造)、(压力铸造),(低压铸造)和(离心铸造)。
2.铸件的凝固方式是按(凝固区域宽度大小)来划分的,有(逐层凝固)、(中间凝固)和(糊状凝固)三种凝固方式。
纯金属和共晶成分的合金易按(逐层凝固)方式凝固。
3.铸造合金在凝固过程中的收缩分三个阶段,其中(液态收缩和凝固收缩)收缩是铸件产生缩孔和缩松的根本原因,而(固态收缩)收缩是铸件产生变形、裂纹的根本原因。
4.铸钢铸造性能差的原因主要是(熔点高,流动性差)和(收缩大)。
5.影响合金流动性的主要因素是(液态合金的化学成分)。
6.铸造生产的优点是(成形方便)、(适应性强)和(成本较低)。
缺点是(铸件力学性能较低)、(铸件质量不够稳定)和(废品率高)。
7、铸造工艺方案设计的内容主要有:(造型、造芯方法)(铸型种类选择)(浇注位置的确定)(分型面的确定)等。
8、目前铸造方法的种类繁多,按生产方法可分为(砂型铸造),(特种铸造)两大类。
;9、铸件的内壁应(薄)外壁。
10、分型选择时,应尽可能使铸件全部或大部置于(同一半铸型)内。
11、确定浇注位置时,重要部位应该向(下)12、浇注系统按位置分类,主要分为(底)注式,(顶)注入式(中间)注入式三种形式。
13、按冒口在铸件位置上分类,主要分为(顶)冒口与(侧)冒口之分。
14、确定砂芯基本原则之一,砂芯应保证铸件(内腔)尺寸精度。
15、封闭式浇注系统,内浇口应置于横浇口(下)部。
16、开放式浇注系统,内浇口应置于横浇口(上)端。
17、根据原砂的基本组成,铸造原砂可分为(石英砂)和(非石英砂或特种砂)两类。
18、镁砂是菱镁矿高温锻烧冉经破碎分选得到的,主要成分是(氧化镁mgo)。
《19、铬铁矿砂是将铬铁矿破碎得到的砂粒,主要矿物有铬铁矿、镁铬铁矿和铝镁铬!矿,因此也决定了它的主要化学成分是(cr2o3 )。
20、蒙脱石和高岭石结构中有两个基本结构单位,即(硅氧四面体)和(铝氧八面体)。
铸造-应力、变形、冷裂
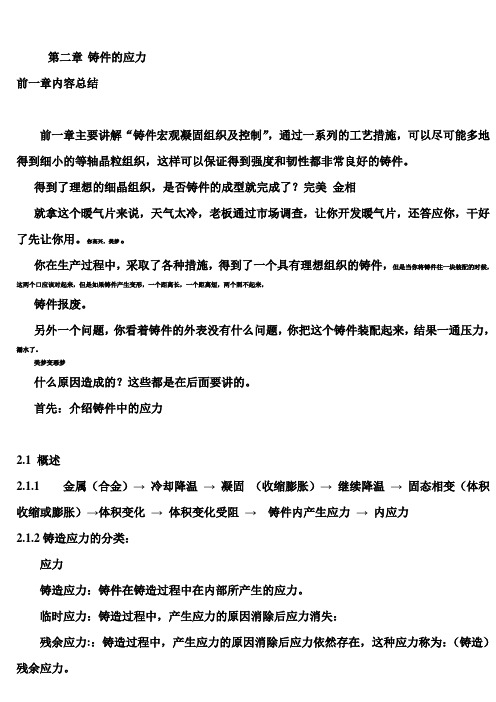
第二章铸件的应力前一章内容总结前一章主要讲解“铸件宏观凝固组织及控制”,通过一系列的工艺措施,可以尽可能多地得到细小的等轴晶粒组织,这样可以保证得到强度和韧性都非常良好的铸件。
得到了理想的细晶组织,是否铸件的成型就完成了?完美金相就拿这个暖气片来说,天气太冷,老板通过市场调查,让你开发暖气片,还答应你,干好了先让你用。
你高兴,美梦。
你在生产过程中,采取了各种措施,得到了一个具有理想组织的铸件,但是当你将铸件往一块装配的时候,这两个口应该对起来,但是如果铸件产生变形,一个距离长,一个距离短,两个照不起来,铸件报废。
另外一个问题,你看着铸件的外表没有什么问题,你把这个铸件装配起来,结果一通压力,漏水了。
美梦变恶梦什么原因造成的?这些都是在后面要讲的。
首先:介绍铸件中的应力2.1 概述2.1.1 金属(合金)→冷却降温→凝固(收缩膨胀)→继续降温→固态相变(体积收缩或膨胀)→体积变化→体积变化受阻→铸件内产生应力→内应力2.1.2铸造应力的分类:应力铸造应力:铸件在铸造过程中在内部所产生的应力。
临时应力:铸造过程中,产生应力的原因消除后应力消失:残余应力::铸造过程中,产生应力的原因消除后应力依然存在,这种应力称为:(铸造)残余应力。
以上两种应力是从时间上分类的。
按应力产生的原因有以下三种:热应力、相变应力、机械阻碍应力、关于这几种应力,我们在后面将逐一给以详细的介绍。
2.1.3应力对铸件的影响低于弹性极限:铸件中产生应力,同时在应力的作用下,产生有限的变形(弹性变形)高于屈服极限:铸件产生塑性变形;高于强度极限:铸件中出现裂纹。
因此,在这一章中,将应力、变形、裂纹放在一起讲解。
在应力的作用下,铸件如何变形和出现裂纹,也将在后面相应的章节中介绍。
2.2热应力:2.2.1概念热应力:铸件冷却过程中,由于各部分冷却速度不同,收缩时间及收缩量不同,铸件由于结构所限,相互制约,不能完成各自的理论变形,结果:在铸件内所产生的应力。
铸件外观标准

DKBA 技术有限公司内部技术规范铸件质量要求Specification for Casting Part’s Quality修订声明Revision declaration 本规范拟制与解释部门:整机工程部本规范的相关系列规范或文件:无相关国际规范或文件一致性:无替代或作废的其它规范或文件:压铸件技术规范相关规范或文件的相互关系:无目录Table of Contents1铸件的分类62铸件的缺陷定义63质量要求83.1铸件的化学成分及力学性能 (8)3.2铸件尺寸 (9)3.3铸件的表面质量 (10)3.4铸件的内部质量 (11)3.4.1压铸件内部质量113.4.2金属型铸件内部质量113.5铸件修补及矫正 (12)3.5.1压铸件的浸渗、整形和修补123.5.2金属型铸件的修补及矫正124试验方法和检验规则124.1检验项目 (12)4.1.1压铸件检验项目124.1.2金属型铸件检验项目124.2化学成分 (13)4.3力学性能 (13)4.4铸件尺寸 (13)4.5铸件重量 (13)4.6外观质量 (14)4.7内部质量 (14)4.7.1压铸件内部质量144.7.2金属型铸件内部质量145质量保证146铸件的交付、包装、运输与储存147参考文献Reference Document 15表目录List of Tables表1 铸件常见缺陷特征6表2 压铸铝合金化学成分和力学性能表8表3 压铸锌合金化学成分和力学性能表8表4 金属型铸造铝合金化学成分和力学性能表9表5 铸件尺寸公差数值(mm)9表6 压铸件平面度公差(mm)9表7 压铸件的平行度公差(mm)9表8 压铸件同轴度公差(mm)9表9 铸件表面质量要求表10表10 压铸件加工后加工面上允许孔穴缺陷表10表11 金属型铸件表面孔洞限量11表12 铸件机械加工后螺纹允许孔穴的规定11表13 内部缺陷允许级别11表14 压铸件检验项目12表15 金属型铸件检验项目12表16 铸件化学成分的检验13表17 铸件力学性能的检验13表18 回炉料分级标准14表19 回炉料与合金锭的配比14铸件质量要求Specification for Casting Part’s范围Scope:本标准规定了鴻富錦公司铸件毛坯的质量保证、验证方法及检验规则和交货条件。
带轮铸造工艺说明书

带轮铸造工艺说明书带轮铸造工艺设计说明书一、过程分析1、审阅零件图仔细阅读零件图,熟悉零件图,提供的零件图必须清晰、正确,尺寸齐全,标记齐全。
零件名称:滑轮工艺方法:铸造零件材料:HT300零件重量:9kg毛重:2.85kg生产批量:10000件/年,为大批量生产仔细审查图样。
注意零件图的结构是否符合铸造工艺的两个方面的要求:(1)审查零件结构是否符合铸造工艺的要求。
(2)在既定的零件结构条件下,考虑铸造过程中可能出现的主要缺陷,在工艺2、零件技术要求未注圆角r3-r8做静平衡实验倒角1*45铸件的重要工作面不允许有气孔、砂眼、渣孔等缺陷。
3.材料选择的合理性铸件所选材料是否合理,一般可以结合零件的使用要求、车间设备情况、技术状况和经济成本等,参考常使用的铸造合金类型(如铸钢、灰铸铁、球墨铸铁、可锻铸铁、蠕墨铸铁、铸造铝合金、铸造铜合金等)牌号、性能、工艺特点、价格和应用等,进行综合分析,判断所选的合金是否合理。
4.审查铸件的结构可制造性铸件壁厚不小于最小壁厚5-6又在临界壁厚20-25以下。
二、工艺方案的确定1.铸造方法的确定铸造方法包括:造型方法、造芯方法、铸造方法及铸型种类的选择(1)造型方法、造芯方法的选择根据手工建模和机械建模的特点,选择了手工建模。
(2)铸造方法的选择根据零件的各参数,对照表格中的项目比较,选择砂型铸造。
(3)铸型种类的选择根据模具的特点和用途,选用自硬砂。
2、浇注位置的确定根据浇注位置选择的四个主要规则,选择铸件的最大截面,即底面。
3、分型面的选择铸件采用双箱造型。
根据分型面的选择原则,分型面取最大截面,即底面。
3、过程参数查询1、加工余量的确定根据建模方法和物料类型进行查询。
发现加工余量等级为11~13级,加工余量等级为12级。
根据零件基本尺寸、加工余量等级进行查询。
查得铸件尺寸公差数值为10。
根据零件尺寸公差、公差等级进行查询。
查得机械加工余量为5.5。
2、起模斜度的确定根据表面类型,测量的表面高度为140,模具启动角度为0°25 min(0.42°)。
2砂型铸造
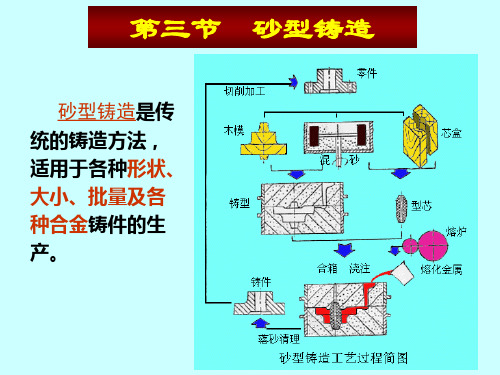
4. 需安放冒口的部位应放在分型面附近的上部或侧面
为了便于安放冒口,以实现自下而上的顺序 凝固。 厚部在 上 上,便 中 于补缩
定 向 凝 固
中 下 图2-40 卷扬筒的浇注位置
二. 铸型分型面的选择原则
——简化造型工艺 1. 分型面尽量选用平直面,以便于造型操作和降 低模板制造费用
弯曲分型面
二、 机械加工余量 ——指在铸件表面留出的准备切削去的金属层厚 度。加工余量过大切削加工费工,浪费金属;过小则 加工达不到要求而造成报废。见P37,表1-11。 浇注时朝上的表面,其加工余量应比底面和侧 面大; 铸件尺寸越大,其加工余量应随之增大; 手工造型的加工余量应比机器造型的大。
中
下 图2-40 卷扬筒的浇注位置
例如:卷扬筒的圆周表面质量要求高,不允许有明 显缺陷,为重要加工面,因此,浇注其处于侧立的 位置。
2. 铸件的大平面应朝下
可保证质量,避免产生夹砂缺陷。对于平板、. 面积较大的薄壁部位应朝下
可避免浇不足、冷隔缺陷。
第三节
砂型铸造是传 统的铸造方法, 适用于各种形状、 大小、批量及各 种合金铸件的生 产。
砂型铸造
铸造工艺图——是在零件图上用各种工艺符号
及参数表示出铸造工艺方案的图形。其中包括: 浇注位置、铸型分型面、型芯的数量、形状、尺 寸及其固定方法、加工余量、收缩率、浇注系统、 起模斜度、冒口和冷铁的尺寸和布置等。
三、 拔模斜度
垂直于分型面的侧壁均应留一定斜度,以便 于起模。 • 手工造型
– 15′~3 °
• 机器造型
– 3 ° ~10°
四、 最小铸出孔和槽 铸件上较小的孔和槽一般不铸出,用机加工的 方法加工。见P38,表1-12。 • 最小铸孔尺寸
工程材料-(砂型铸造)

技术方案确定:
造型方法
铸造工艺
思考题
P210 8-7
习题8-7a 轴承 铸件分型方案 (大批量)
下 下
上 上
上下
?
上 下
? 活块造 型
下 下
上 上
大批量生产宜 采用机器造型, 机器造型为两 箱造型。
下 上
浇注位置示意(水平浇铸)
习题8-7b 调整座 分型方案(大批量)
方案1
方案1
第一步:型(芯)砂的制备
型(芯)砂由原砂、粘结剂、水及其它附加物混制 分为:粘土砂、水玻璃砂、树脂砂 (P180) 技术要求:型(芯)砂
具有一定的强度、透气性、 退让性和溃散性等。
砂型质量的影响因素:
A. 型砂的影响:
a) 原砂的粒度状况、形状
一般认为:粒度在小尺寸范围呈正态分布,有利于
砂型强度的提高,但透气性较差。
➢ 具有所要求的化学成分 ➢ 杂质含量低 ➢ 具有所需要的温度
常用设备:冲天炉、反射炉、
A. 铸铁的熔炼 电弧炉、工频炉等。
冲天炉
冲天炉熔炼:通过焦炭的燃 烧放热使固体金属炉料熔化 并过热后成为液态金属。
出炉以浇注
B. 铸钢合金的熔炼
常用设备:电弧炉、感应电炉、平炉
C. 有色合金的熔炼
对设备要求:
B. 最小铸出孔:最小孔直径和经济性原则。
C. 起模斜度:取决于立壁高度、造型方法和模样材 料等因素,一般15’-3°。 内外壁有分(内壁3-10° )。
铸件的起模斜度示意
D. 收缩率:模样尺寸放大率K=(Lp-Lc)/Lp*100%
➢ 经验数据(HT:0.7-1%;ZG1.3-2.0 % )
E. 型芯头:芯头关系到装配的工艺性和稳定性。
铸造机械化知识要点

第一章型砂紧实的测量主要采用三种方法:紧实度法、硬度法、紧实率法。
1、紧实度法A紧实度一单位体积内型砂的重量即为型砂紧实度5=G/V §型砂紧实度 G型砂重量V型砂体积B.测量方法:取所测部位型砂试样(用圆柱钢管取)称量计算。
特点是:测虽值为平均紧实度时容易测呈:、局部较难,易损坏砂型。
2、硬度法硬度法测量特点:比较方便、不破坏砂型,内部紧实度不能测;在§髙时灵敏度不均匀;对化学硬化,干砂型不适用;紧实度较高时硬度值变化不显著。
3、紧实率法紧实率(J )型砂紧实后的体积变化量与原体积之比。
紧实率的大小不仅表示型砂的紧实程度,还表示型砂的可紧实性或成型性对紧实度的工艺要求:1、砂型紧实的要有一泄的强度①搬运翻转不脱落②型腔表而抵抗浇注铁水的冲刷压力③铁水凝固过程的膨胀压力2、紧实后的砂型要容易起模3、具有必要的透气性,避免产生气孔等缺陷。
压实过程的三个阶段:第一阶段:P增加很小砂粒间的大孔隙被压没,H下降很多。
第二阶段:砂粒间位移变成较紧密的排列,砂粒间摩擦力和粘结力对型砂的进一步紧实起阻碍作用,P 增加较大增加不大。
第三阶段:髙比压阶段,当P继续增加,砂粒本身由于应力过大而破碎。
一般石英砂,破碎比压2Mpa 以上,P增加很大,§增加很小。
使压实实砂紧实度均匀化的方法:1、减小压缩比的差別1)应用成型压头2)压膜造型3)应用多触头压头4)应应用模样退缩装程2、模板加压与对压法1)模板加压法2)对压法3、提髙压前的填砂紧实度 1 )控制型砂紧实率2 )提高填砂紧实度,重力填砂3)复合实砂或压实前将砂预紧实。
4、多次加压与顺序加压1)应用成型压头2)应用多触头压头3)压膜造型4)应用模样退缩装置微震实砂特点:能实现压震一一微震和压实组合起来有四种实砂方法。
单纯微震、预丧加压实,单纯压丧先预丧后压震。
射砂过程:1、射砂过程的分段:a .射前期:射孔打开,型砂尚未射岀,时间0. OO&O.Ol 1左右,气压约50k Pab.自由射砂阶段:砂粒以气砂流的形式穿过射孔填入芯盒(8 0 %-9 0 %)c .压砂团紧实阶段:芯盒上部气压差使砂团相互推压形成密集流2、射砂过程气压梯度、流化区、搭棚、波动和空穴的形成3、彫响射砂的因素(1)射砂气压及气压梯度提高射砂气压,能提高气压梯度,加强气流渗透,使砂能顺利射出。
2-1 铸造工艺基础
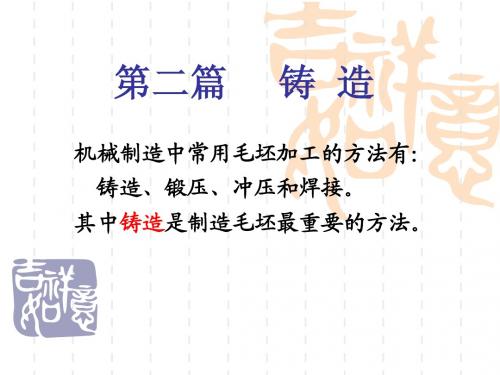
下一页
17
浇 不 足
后 退
18
冷
隔
后 退
19
三、影响充型能力的因素
1.合金性质——合金流动性:决定于合金种类与 化学成分。合金种类0.77
2.11
4.3
C%
2.浇注条件
浇注温度
对液态金属的充型能力有决定性的影响。
温度高,充型能力就强。这是因为浇注温度提高,合金液的粘度 就降低,浇注以后保持液态的时间也就延长,传给铸型的热量就 增多,这就使铸型和金属液的冷却速度就降低,从而使合金的充 型能力增强。 对于薄壁铸件,适当提高浇注温度是改善充型能力、防止产生浇 不到、冷隔的重要措施。这些措施在生产中经常采用,也比较方 便。
空腔中填充的金属。
冷铁:为了增加铸件局部的冷却速度,在砂型中安放的
金属物。
40
冒口补缩示意图
浇注系统 冒口
冷铁
设臵冒口,是我们在工艺上防止缩孔和缩松形成的非 常有效的一项措施。 铸件按照规定的方向顺序凝固,铸件的每一部分的收 缩都会得到在以后凝固的金属液的补充,这样使得缩 孔最后转移到冒口当中去,清理时将冒口切除即可。
有利于液态金属中的气体和熔渣的上浮 与排除。
有利于合金凝固收缩时的补缩等。
16
2.合金充型能力差,铸件容易产生浇不足、冷隔、气 孔、夹渣、缩孔等铸造缺陷,不能得到完整的零件。
浇不足: 铸件残缺,轮廓不完整,或轮廓可能
完整但边角圆而且光亮。
冷隔:在铸件上穿透或不穿透,边缘呈圆角状的
机械制造2-1 铸造工艺基础知识
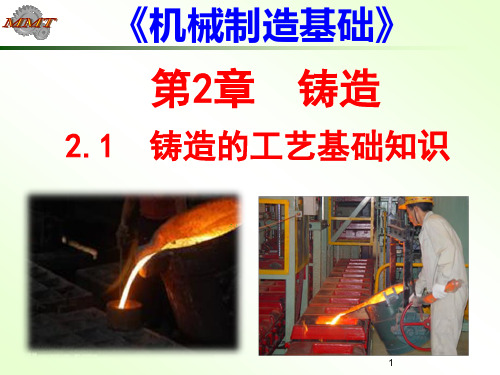
10
2.1
铸造的工艺基础知识
• 2.1.1 液态合金的充型 合金流动性的定义
流动性是指液态(熔融)金属的流动能力。 它是影响液态金属充型能力的主要因素之一, 也是合金的主要铸造性能之一。
11
2.1
铸造的工艺基础知识
• 2.1.1 液态合金的充型 合金流动性的测量方法
常用浇注标准螺旋形试样的方法进行测定。 螺旋形试样的长度越长,则液态合金的流动性越好。 常用合金的螺旋形试样的长度数值见P11表2-1。
22
充型能力的影响因素
主要影响因素:铸型条件和浇注条件 2.浇注条件:
浇注条件又与浇注系统结构、浇注温度和充型压力有关。 (2)浇注温度: 浇注温度越高,合金保持液态的时 间越长,金属液粘度降低,杂质容 易上浮或溶解,故合金流动性好, 充型能力强。但浇注温度过高,液 态合金收缩增大,吸收气体多,氧 化严重,流动性反而会下降。因此 在保证流动性的前提下,浇注温度 应尽可能低一些。
25
砂型铸造的充型压力由 直浇道的静压力产生。
2.1
铸造的工艺基础知识
• 2.1.2 铸件的凝固与收缩
浇入铸型型腔的液态金属在冷凝过程中,如果其 液态收缩和凝固收缩得不到补充,铸件将产生缩孔 或缩松等铸造缺陷。因此,必须合理地控制铸件的 凝固过程。 1. 铸件的凝固方式 铸件的凝固: 液态合金转变为固态铸件的过程称为铸件的凝固。
阶段的收缩。用体收缩率表示。合金的结晶温度范围越大, 体收缩率也越大。液态收缩和凝固收缩时金属液体积缩小, 是形成缩孔和缩松的基本原因。
a)
a) 合金状态图
b)
c)
b) 一定温度范围合金 c) 共晶合金
图2-6 铸造合金收缩过程示意图
铸造工艺设计方案

要求:①掌握铸造工艺方案的制定,
铸造工艺参数确定的原则;② 熟悉浇注系统的组成以及冒口的作用; ③了解冒口尺寸的计算方法。
重点:砂型铸造工艺图的绘制; 难点:浇注位置及分型面的选择。
砂型铸造工艺设计:
为获得好的铸件,减少工 作量,降低成本,合理制订铸 造工艺方案,绘制铸造工艺图。
√
×
2.分型面的选择原则
重要性:
①恰当与否会影响铸件质量; ②使制模、造型、造芯、合箱或清理 等工序复杂化; ③甚至还可增大切削加工的工作量。
1)便于起模,使造型工艺简化
尽量使分型面平直、数量少,避 免不必要的活块和型芯。 √
×
起重臂的分型面
√
大平面还常产生夹砂缺陷,故对平板、圆盘类铸件,大平面应朝下。
加工表面上的起模斜度应结合加工 余量直接表示出,而不加工表面上的 斜度(结构斜度)仅需用文字注明。
熟悉浇注系统的组成以及冒口的作用; 分型面:砂箱间的接触表面。 §4-1 铸造工艺方案的确定 □大批量生产条件下,采用机器造型,需要改用图中所示的环状型芯,使铸型简化成只有一个分型面。 一般大量生产的定型产品、特殊重要的单件生产的铸件,铸造工艺设计订得细致,内容涉及较多。 共型芯:增加型芯稳定性、提高模板和砂箱利用率。 熟悉浇注系统的组成以及冒口的作用; 铸钢件:表面粗糙,余量比铸铁大 ①选择铸件的浇注位置及分型面。 铸件的孔、槽是否铸出,不仅取决于工艺上的可能性,还须考虑其必要性。 3)尽量使型腔及主要型芯位于下型 单件、小批生产的一般性产品,铸造工艺设计内容可以简化。 不加工的特形孔、价格较贵的非铁金属铸孔,尽量铸出。 它是制造模样和铸型,进行生产准备和铸件检验的依据(基本工艺文件)。 三、砂芯形状、个数及分块 a)垂直芯头 b)水平芯头 三、砂芯形状、个数及分块 尽量使分型面平直、数量少,避免不必要的活块和型芯。 方案III:从B面分型,铸件全部置于下型。 采用分型方案I时的铸造工艺图 1)铸件的重要加工面应朝下或位于侧面。
铸造造型工考题

一、填空1. 铸造成型的优点有____________,____________ ,等;缺点有____________ ____________,____________,等。
2. 金属凝固组织对其物理性能力学性能影响很大,金属结晶时冷却速度越快,则晶粒__________,材料的强度和硬度越____________ ,塑性和韧性____________ 。
逐层凝固合金,其充型能力较____________ 。
3. 影响铸件凝固组织的的因素主要有____________ 等。
(举3个)4. 铸件的三种凝固方式是____________ ,那种凝固易于出现缩松____________ ,那种易于出现缩孔,那种缺陷容易消除,采取____________ 方法。
哪种铁碳合金易于出现逐层凝固?5. .常见的铸造方法有砂型铸造、___________、___________、___________、___________等。
6. 合金的收缩可分为三个阶段,各是____________,____________,____________ 。
____________是铸件产生内应力,变形和裂纹的主要原因。
7. 常用的特种铸造方法有熔模铸造、壳型铸造、消失模铸造和压力铸造等。
8. 设计铸件时,凡垂直于分型面的非加工面应设计__斜度9. 铸件在固态收缩阶段若收缩受阻,便在铸件内部产生内应力。
这种内应力是铸件产生__________和__________的主要原因。
10. 铸件各部分的壁厚差异过大时,在厚壁处易产生__________缺陷,在薄壁与厚壁的连接处因冷却速度不一致易产生__________缺陷。
当铸件壁厚不均时,凝固成形后的铸件易在壁厚处产生_______应力。
11. 常见的铸造方法有砂型铸造、压力铸造、______、______、______等。
在各种铸造方法中,适应性最广的是___________,生产率最高的是___________,易于获得较高精度和表面质量的是___________,对合金流动性要求不高的是___________。
铸造-气孔及夹杂、偏析
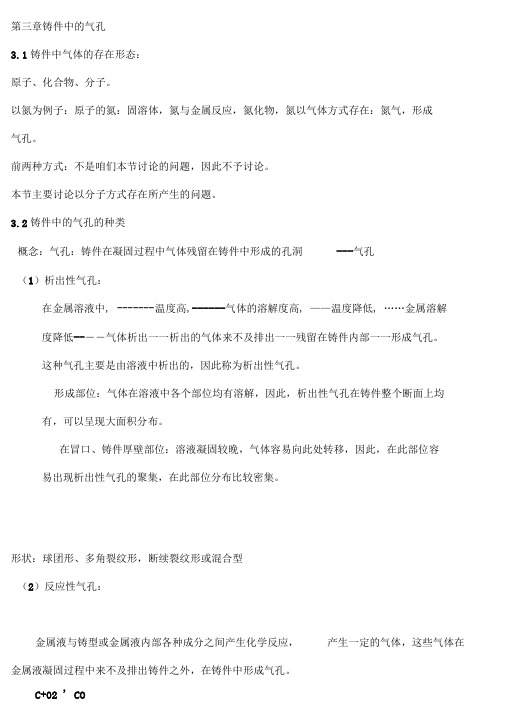
第三章铸件中的气孔3.1铸件中气体的存在形态:原子、化合物、分子。
以氮为例子:原子的氮:固溶体,氮与金属反应,氮化物,氮以气体方式存在:氮气,形成气孔。
前两种方式:不是咱们本节讨论的问题,因此不予讨论。
本节主要讨论以分子方式存在所产生的问题。
3.2铸件中的气孔的种类概念:气孔:铸件在凝固过程中气体残留在铸件中形成的孔洞---气孔(1)析出性气孔:在金属溶液中, ------- 温度高,------气体的溶解度高, ——温度降低, ……金属溶解度降低--――气体析出一一析出的气体来不及排出一一残留在铸件内部一一形成气孔。
这种气孔主要是由溶液中析出的,因此称为析出性气孔。
形成部位:气体在溶液中各个部位均有溶解,因此,析出性气孔在铸件整个断面上均有,可以呈现大面积分布。
在冒口、铸件厚壁部位:溶液凝固较晚,气体容易向此处转移,因此,在此部位容易出现析出性气孔的聚集,在此部位分布比较密集。
形状:球团形、多角裂纹形,断续裂纹形或混合型(2)反应性气孔:金属液与铸型或金属液内部各种成分之间产生化学反应,产生一定的气体,这些气体在金属液凝固过程中来不及排出铸件之外,在铸件中形成气孔。
C+02 ' CON2+H2 气体是由化学反应造成的,因此成为反应性气孔。
产生部位:主要原因:与铸型之间NH3的反应:因此一般在铸件表面或铸件表面1~3 毫米以下。
出现在铸件表面以下:一般称为皮下气孔。
(主要原因:金属液与助兴之间的反应产生)金属液内部各成分之间产生的反应,在整个断面上出现,因此,气孔也出现在整个断面上。
形状:一般应该为圆形,产生后有向铸件外逸出的趋势,因此在向外逸出的过程中(3)侵入性气孔金属液外部的气体进入到金属液内部,在金属液凝固过程中来不及逸出到金属液外部而残留在铸件内部,所形成的气孔,称为侵入性气孔。
最主要原因:水分:受热后液态变为气态,体积大大膨胀,产生非常高的压力,在压力作用下进入金属液内部。
特点:在整个铸件断面上分布,但靠近铸件表面分布密集。
caesarII关于三通的介绍

1.Reinforced tee这是一个可加强预制三通。
可以带补强板或鞍座,其形式为主管上开孔,直管插入并焊接成型,补强板或鞍座环绕连接处起加强作用,其应力增大系数及形式可参考B31.1、B31.3附录D(或相关规范的相关章节)2.Unreinforced这是一个无补强预制三通。
结构同1,但是没有补强板或鞍座加强,其应力增大系数及形式可参考B31.1、B31.3附录D(或相关规范的相关章节)3.Welding T ee这是一个按照ASME B16.9规范制造的锻制(或铸造)焊接三通(尺寸要求符合ASME B16.9),由于连接处具有光滑的轮廓,其应力分布较好,SIF较小。
其应力增大系数及形式可参考B31.1、B31.3附录D(或相关规范的相关章节)4.Sweepolet这是一种嵌入式焊接管座。
其结构为主管上开大开孔,用以嵌入一个支管座,两者以焊接连接,由于支管座具有光滑的轮廓并适当加强,其应力分布类似于3号Welding Tee。
其应力增大系数及形式可参考B31.1、B31.3附录D(或相关规范的相关章节)5.Weldolet这是一种整体加强的焊接支管座。
其结构为主管上开孔,支管座配合连接,加强部位与主管焊接。
也可以理解为一类加强三通。
其应力增大系数及形式可参考B31.1、B31.3附录D(或相关规范的相关章节)6.Extruded Welding T ee这是一个挤压成型三通。
其形式为直管管壁沿径向方向进行挤压形成支管接口。
应力增大系数及形式可参考B31.1、B31.3附录D(或相关规范的相关章节)7.Butt Welded joint这不是三通。
这是管道或管件之间的对焊接头。
具体形式见B31.1附表D-1(或相关规范章节)8、9.Socket/unfin这不是三通。
这是管道或管件之间的角焊接(承插焊)接头、法兰。
Socket weld(No undercut)无根切承插焊接(支管台)Socket weld (As weld)与B16.9焊接三通类似的承插支管台10.Tapered这不是三通。
- 1、下载文档前请自行甄别文档内容的完整性,平台不提供额外的编辑、内容补充、找答案等附加服务。
- 2、"仅部分预览"的文档,不可在线预览部分如存在完整性等问题,可反馈申请退款(可完整预览的文档不适用该条件!)。
- 3、如文档侵犯您的权益,请联系客服反馈,我们会尽快为您处理(人工客服工作时间:9:00-18:30)。
将与铸件尺寸形状相似的石蜡或泡沫模型粘结组合成模型
簇, 刷涂耐火涂料并烘干后, 埋在干石英砂中振动造型, 在负压下浇注,
使模型气化,
液体金属占据模型位置, 凝固冷却后形成铸件的新型铸造方法。
24
25
26
第二节 铸件外观质量检验方法
常见铸造缺陷的特征及识别
图10-2 飞翅、毛刺示意图 a)飞翅 b)毛刺 c)脉纹
合而形成的接缝。
1)预热金属型:有利于金属液的充型。生产铸铁件,金属型 预热至250-350℃;生产有色金属件预热至100-250℃。
9
2)型腔须喷刷耐火涂料:保护其免受金属液直接冲蚀和热击,
可调节铸件各部分的冷却速度。 3)浇注温度应比采用砂型高出20-30℃,铸铁件的壁厚不小 于15mm,以防白口组织。 白口铸铁:白口铸铁中的碳全部以渗透碳体(Fe3C)形式
(3)能够铸造各种合金铸件。
(4)生产批量不受限制。 但工序繁多,生产周期较长,铸件不能太长、太大,铸件 成本比砂型铸件高。
应用实例
主要用于生产汽轮机、水轮机上小型的叶片和叶轮、切削刀具 及汽车、拖拉机、船舶、机床和风动工具上的小型零件等。
7
二、 金属型铸造 Permanent Mold Casting
铸
造(II)
特种铸造 Special casting processes
熔模铸造
压力铸造
低压铸造
特种铸造
金属型 铸造
六 种 常 见 的 特 种 铸 造 方 法
消失模铸造
离心铸造
2
一、熔模铸造 Investment Casting
定义:在易熔材料(如蜡料)制成的模样上包覆若干层耐火涂 料,待其干燥硬化后熔出模样而制成型壳,型壳经高温培烧后 即可浇注的铸造方法。
图10-7 白点示意图 a)纵向断面 b)横向腐蚀断面 图
图10-6 热裂示意
a)
a)一般冷隔
b) 图10-8冷隔示意图 b)断流冷隔
c) c)熔合不良
图 10-9鼠尾、沟槽、夹砂结疤 a)鼠尾 b)沟槽 c)夹砂结疤
4.表面缺陷 表面缺陷主要有:由砂型膨胀引起的夹砂类缺陷 (包括鼠尾、沟槽、夹砂结巴等);由金属液对砂 型表面的热作用、化学作用和机械渗透作用引起的 粘砂类缺陷(包括化学粘砂、机械粘砂、热粘砂、 表面粗糙等),以及皱皮和缩陷等。
b) 图10-12 变形示意图 b)铸形变形 c)铸件变形
c)
图10-14 错芯示意图
图10-16金属夹杂物示意图
a) b) 图10-15 偏芯(漂芯)示意图 a)水平砂芯上浮 b) 凸出砂台断裂
图10-16金属夹杂物示意图(下图)
2.尺寸检查
尺寸检查是以图样为依据,测量铸件尺寸是
否在公差范围之内,以发现形状与尺寸的误 差。 3.材料检查 汽车铸件材料应根据使用目的来选定。为了 保证材料的性能,应进行化学分析、金相检 验与机械性能试验。普通铸铁(片状石墨)与球 墨铸铁(球状石墨)可从其共振频率求得抗拉强 度。
图 10-10 粘砂和表面粗糙度示意图 a)机械粘砂 b)化学粘砂 c)热粘砂 糙度
d)表面粗
5.形状及重量差错类缺陷 这类缺陷指的是铸件的尺寸、形状和重量 与图样或技术条件的规定不符,主要有:尺寸和 重量差错、变形、错形(错箱)、偏芯(漂芯)、 椿移等。
图10-11 尺寸和重量差错示意图
a) a) 模样变形
1.熔模(失蜡)铸造的工艺Байду номын сангаас程
3
4
5
三、型壳的制造
1、制造型壳用的材料
▓ 耐火材料-石英、刚玉和硅酸铝耐火材料;
▓ 粘结剂-硅酸溶胶(H2SiO3) 2、制壳工艺 ▓ 模组的除油和脱脂 ▓ 涂挂涂料和挂砂
▓ 型壳层的干燥和硬化
▓ 脱模 ▓ 焙烧
6
特点
(1)可生产形状复杂、轮廓清晰、薄壁铸件。 (2)铸件精度高,表面质量好。
4.耐压防漏检查 检查铸件中从里到外连续存在的细微裂纹与
缩孔、气孔群,是一种对能承受压力的零件 或产品广泛使用的方法。一般采用水压试验, 也可用油压或气压做精密试验, 5.无损探伤检查 利用仪器进行声波试验、渗透探伤、磁粉探 伤、涡流探伤、超声探伤和放射性探伤,在 保证铸件质量上起着重要的作用。
1.多肉类缺陷 多肉类缺陷主要有:飞翅(飞边、披缝)、毛 刺、抬型(抬箱)、胀砂、冲砂、掉砂和外渗物 (外渗豆)。 2.孔洞类缺陷 孔洞类缺陷主要有气孔、针孔、缩孔、缩松和疏松。
a) b) 图 10-4缩孔、缩松、疏松示意图 a)缩孔 b)缩松、疏松
图10-5 冷裂示意图
3.裂纹、冷隔类缺陷 主要有冷裂、热裂、白点(发裂)、冷隔和热处 理裂纹。发现这类缺陷时,铸件一般应予以报废。
双金属铸造:为了满足同一铸件不同部件有截然不同的性能的要求, 以及为了节约贵合金和降低成本而采用双金属铸造。 它是把两种成分不同、性能各异的金属熔铸在一起的铸造方法。把第一 种成分的金属液浇入铸型后,待结成外壳,在预定时间内再把第二种成
分的金属液浇入,并把内部未凝的第一种金属顶出来。
14
离心铸件最大直径可达3米以上,最大长度8米, 最大重量达几公斤到十多吨。
3、压力铸造的适用范围:
航空航天、汽车、仪器仪表、医疗器械等,大批量生产有色合金 铸件;压铸件应尽量避免机加工,以防内部孔洞外露。
18
压铸件不宜热处理,并尽量避免切削加工 。(为什么?)
答:由于压铸的金属液注入和凝固速度过
快,型腔气体难以及时完全排出,壁厚处难
以进行补缩,故铸件内部易存有气孔、缩孔
15
四、压力铸造
High Pressure Die Casting
定义:压力铸造是指金属液在高压下高速充型,并在压力下 凝固的铸造方法。
16
压力铸造的基本原理
(a)浇入液态金属;
1、冷室压铸机
(b)加压; (c)顶出铸件
压室与保温炉分开
用于大型厚壁铸件的生产
1-顶杆
2-金属铸型 3-加压活塞 4-铸件
17
2、压力铸造的特点 优点: 1)铸件质量好,尺寸精度高;
2)压铸件的强度和表面硬度较高; 3)生产效率高,操作简便,易于实现自动化。
缺点:
1) 充型速度快,型腔中的空气很难完全排出,且厚 壁处也很难补缩;
2)压铸件不宜进行热处理或在高温下使用;Why?
3)可压铸的合金种类受到限制; 4)设备投资大,压铸型的制造成本高
定义:在重力作用下将熔融金属浇入金属型而获得铸件的方法
1、金属型的结构
金属型用铸铁和铸钢制成;
铸件的内腔既可用金属型芯、也可用砂芯。
8
2、金属型铸造的工艺特点
金属型的导热速度快和无退让性,使铸件易产生浇不足、冷隔、 裂纹等缺陷。 浇不足: 指铸件的形状不完整。 冷隔:指铸件上某处由于两股或两股以上金属液流未熔
主要用来铸造一些质量要求高的铝合金和镁合金铸件,如气缸体、缸盖、和高 速内燃机的铝活塞等薄壁件。
21
22
六、实型铸造(气化模造型或消失模铸造 )
采用聚苯乙烯发泡材料制得的模型代替木模造型,不用起模直接
将金属液浇注到气化模上,使其燃烧、气化并形成空腔来容纳金
属液,从而获得铸件的方法。
23
消失模铸造(又称实型铸造):
13
特点及适用范围
1、适用于旋转体铸件的生产,省去浇冒口,金属利用率提
高;不用造型、制芯,节省了相关材料及设备投入。 2、金属补缩效果好,铸件致密,机械性能好; 3、可以实现双金属铸造, 5、易产生偏析,内表面不易控制。
在离心力作用下, 密度大的金属液被 推往外壁。而密度 小的气体、熔渣向 自由表面移动
11
三、离心铸造 Centrifugal Casting
定义:将金属液浇入绕水平、倾斜或立轴高速旋转的铸型, 在离心力作用下充型和凝固的铸造方法。
铸件的各部分冷却速度相同,壁厚均匀。主要用来生产长 度大于直径的套、管类铸件。污水管
12
金属液的自由表面在离心力作用下呈抛物面,主要生产高 度小于直径的盘、环类铸件。
存在,因断口呈亮白色。故称白口铸铁,由于有大量硬而
脆的Fe3C,白口铸铁硬度高、脆性大、很难加工。因此, 在工业应用方面很少直接使用。
10
3、金属型铸造的优缺点 (1)优点: 1)金属型铸造一型多铸,生产率高,劳动条件好; 2)铸件的组织致密、晶粒细小,机械性能高; 3)铸件精度高、表面粗糙度值低。 (2)缺点: 1)不宜铸造结构复杂、薄壁或大型铸件; 2)铸型寿命短,灰铸铁件铸造时还易于白口组织; 3)成本高,周期长,需批量生产。 4、金属型铸造的应用: 主要用于成批生产铝、铜合金等的中、小型铸件, 如活塞、缸体、液压泵壳体、轴瓦和轴套等。
和缩松等铸造缺陷。
19
五、低压铸造 Low pressure Die Casting
低压铸造是采用较压力铸造低的压力(一般为0.02-0.06 Mpa),将金属液从铸型的底部压入,并在压力下凝固获 得铸件的方法。
20
低压铸造的特点及应用:
1、浇注及凝固时的压力容易调整、适应性强,可用于各种铸型、各种合金 及各种尺寸的铸件。 2、底注式浇注充型平稳,减少了金属液的飞溅和对铸型的冲刷,可避免气 孔缺陷。 3、铸件在压力下充型和凝固,其浇口能提供金属液来补缩,因此铸件轮廓 清晰,组织致密。 4、低压铸造的金属利用率高,约90%以上。 5、设备简单,劳动条件较好,易于机械化和自动化。