低压甲醇装置运行总结
低压甲醇合成装置试生产运行总结

表2甲醇合成催化剂RK-05-2基本物性参数表1甲醇合成塔规格参数安徽临涣化工有限责任公司二期20万t/a 甲醇合成装置采用低压甲醇合成工艺,实际生产能力为24.412万t/a ,年操作8000h ,小时产量为30.515t 。
整个装置由甲醇合成、余热回收、粗甲醇分离和弛放气洗涤等几部分组成。
分离粗甲醇后的反应气送至合成气压缩装置,补充新鲜气并加压后,返回甲醇合成塔循环利用。
以下对该装置试生产运行进行总结。
1甲醇合成工艺甲醇合成塔为华东理工大学绝热-管壳型反应器,管内及管板上部700mm 装填甲醇合成催化剂,装填量51.26m 3;反应管外为沸腾热水,利用反应热副产中压饱和蒸汽。
甲醇合成塔规格参数见表1。
甲醇合成塔装填大连瑞克生产的催化剂RK-05-2,其外观为黑色带光泽圆柱体,基本物性参数见表2。
甲醇合成工艺流程示意图见图1。
来自合成气压缩装置的新鲜合成气,先进入气气换热器预热到195℃左右,再进入甲醇合成塔,在催化剂的作用下进行甲醇合成反应,甲醇合成塔利用反应热副产中压饱和蒸汽。
合成塔出口气进入气气换热器,与合成塔入口气换热,把入口气加热到活性温度以上,同时合成塔出口气温度降至97℃,再经4台并联操作的蒸发式冷却器冷却到40℃后,进入甲醇分离器进行气液分离。
出甲醇分离器气体大部分作为循环气去合成气压缩增压并补充新鲜气,一小部分作为弛放气,进入洗醇塔底部,与塔顶喷淋下来的脱盐水逆流接触,气体中的甲醇溶解在水中,形成稀醇水从塔底排出,然后进入甲醇闪蒸槽出口洗涤段顶部,用以洗涤闪蒸气中夹带的甲醇,洗醇后的稀醇水混入粗甲醇中。
从洗醇塔顶出来的气体,压力约5.9MPa (G ),经调节阀减压至0.2MPa (G )后,送作燃料气。
甲醇分离器底部出来的粗甲醇减压至0.7MPa(G )后,送入闪蒸槽,粗甲醇中的溶解气绝大部分被释放出来,该气体经出口洗涤段回收甲醇后,用作燃料气,送转化预热炉燃烧。
甲醇闪蒸槽出口粗甲醇压力0.5MPa (G ),送往甲醇精馏。
甲醇装置设备工作总结与工作计划 煤化公司
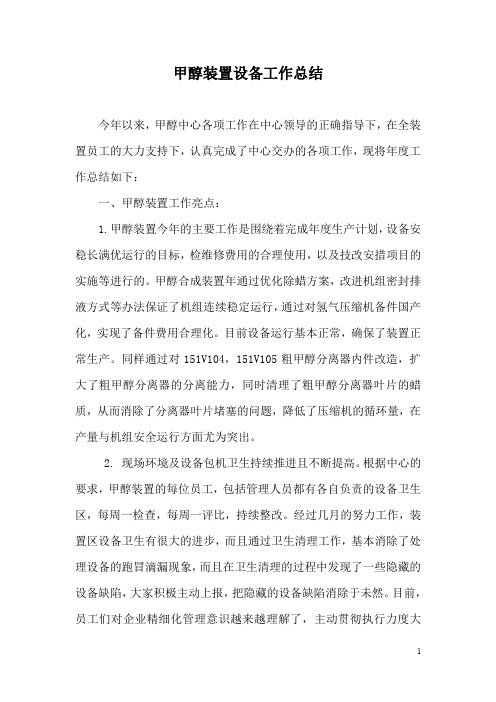
甲醇装置设备工作总结今年以来,甲醇中心各项工作在中心领导的正确指导下,在全装置员工的大力支持下,认真完成了中心交办的各项工作,现将年度工作总结如下:一、甲醇装置工作亮点:1.甲醇装置今年的主要工作是围绕着完成年度生产计划,设备安稳长满优运行的目标,检维修费用的合理使用,以及技改安措项目的实施等进行的。
甲醇合成装置年通过优化除蜡方案,改进机组密封排液方式等办法保证了机组连续稳定运行,通过对氢气压缩机备件国产化,实现了备件费用合理化。
目前设备运行基本正常,确保了装置正常生产。
同样通过对151V104,151V105粗甲醇分离器内件改造,扩大了粗甲醇分离器的分离能力,同时清理了粗甲醇分离器叶片的蜡质,从而消除了分离器叶片堵塞的问题,降低了压缩机的循环量,在产量与机组安全运行方面尤为突出。
2. 现场环境及设备包机卫生持续推进且不断提高。
根据中心的要求,甲醇装置的每位员工,包括管理人员都有各自负责的设备卫生区,每周一检查,每周一评比,持续整改。
经过几月的努力工作,装置区设备卫生有很大的进步,而且通过卫生清理工作,基本消除了处理设备的跑冒滴漏现象,而且在卫生清理的过程中发现了一些隐藏的设备缺陷,大家积极主动上报,把隐藏的设备缺陷消除于未然。
目前,员工们对企业精细化管理意识越来越理解了,主动贯彻执行力度大了,对设备操作维护的精细意识也越来越强了。
3 做好本安体系设备管理专业的工作。
①甲醇成品罐区属于甲醇装置责任区,也是每次本安体系检查和其它安全检查的重点区域。
由于项目建设标准低,遗漏下好多安全隐患,结合安全评价检查和每季度本安体系检查组专家的意见和我们日常检查发现的隐患,我们分开轻重缓急,逐步整改,年底全部完成安措项目的整改。
罐区面貌大有改观,安全隐患逐步降低。
②本年度,甲醇装置完成俩项重大安措整改项目,⑴.成品罐区甲醇成品储罐入口阀门增设电动头;⑵.甲醇装置蒸汽过热炉增加火焰检测装置,此项是集团公司级的隐患治理项目。
甲醇合成装置优化运行总结

甲醇合成装置优化运行总结甲醇是一种广泛应用的有机化工产品,其合成装置的优化运行对于提高甲醇生产效率、降低能耗、提升产品质量具有重要意义。
本次运行总结主要包括以下几个方面的内容。
针对甲醇合成反应器的优化运行。
反应器是整个合成装置的核心部分,其运行状态直接影响甲醇的合成效果。
在本次运行中,我们对反应器的温度、压力、催化剂的投料速度和搅拌速度等参数进行了优化调整。
通过合理地控制这些参数,提高了甲醇的产率和选择性,降低了副产物的生成率。
我们还注意到反应器内催化剂的老化问题,及时对老化催化剂进行更换,保证了反应的高效进行。
针对甲醇合成装置的能耗优化。
合成甲醇过程中能耗是一个重要的经济指标。
通过对装置的能耗进行全面的分析和评估,我们发现了一些能耗较高的环节,冷凝器的工作温度过高、泵的运行效率偏低等。
针对这些问题,我们采取了相应的措施,改善了能耗状况。
对冷凝器进行了维修和改造,减少了冷却水的使用量,降低了能耗。
我们还对泵进行了调试和优化,提高了泵的运行效率,降低了能耗。
针对甲醇产品质量的优化。
甲醇的产品质量对于其应用领域的不同有着不同的要求。
在本次运行中,我们注重了甲醇产品质量的监测和控制。
通过对甲醇产品进行多次的取样和分析,我们发现了一些质量问题,如杂质含量过高、甲醇含量波动较大等。
通过调整原料的配比比例、优化催化剂的选择和控制反应温度等措施,我们改善了甲醇产品的质量,满足了用户的需求。
针对安全和环保问题的优化。
在甲醇合成装置的运行中,安全和环保问题是至关重要的。
我们始终把安全和环保放在首位,采取了一系列的措施来保障生产过程的安全和环境的保护。
加强了现场人员的安全培训,提高了员工的安全意识;加强了废水和废气处理设施的运行维护,降低了对环境的污染。
通过对甲醇合成装置的优化运行,我们提高了甲醇的生产效率、降低了能耗、提升了产品质量,同时确保了生产过程的安全和环保。
仍然存在一些问题和不足之处,例如催化剂的寿命仍有待进一步提高,能耗仍有一定的改进空间。
低压甲醇工艺运行总结

作者简介:孙彩军(1982 )ꎬ男ꎬ工程师ꎬ主要从事生产管理工作ꎻsuncaijun@ajhchem.com低压甲醇工艺运行总结孙彩军ꎬ王秀荣ꎬ万武军(安徽金禾实业股份有限公司ꎬ安徽滁州㊀239200)㊀㊀摘㊀要:介绍了低压甲醇工艺流程ꎬ并将投运后的工艺效果进行对比ꎮ结果表明:低压甲醇工艺使压缩机五段㊁六段㊁七段压力均有不同程度的下降ꎬ促进了生产装置的安全稳定运行ꎮ低压甲醇装置运行稳定ꎬ出口气体CO+CO2转化率高ꎬ节约电耗ꎬ副产蒸汽ꎬ无污染物质排放ꎮ㊀㊀关键词:低压甲醇ꎻ能耗ꎻ副产蒸汽㊀㊀中图分类号:TQ54㊀㊀㊀㊀㊀文献标识码:B㊀㊀㊀㊀㊀文章编号:2096 ̄3548(2019)04 ̄0017 ̄02㊀㊀安徽金禾实业股份有限公司(简称金禾实业)是一家大型化工企业集团ꎬ位于安徽省滁州市来安县ꎬ主要从事基础化工产品和精细化工产品的生产㊁研发和销售ꎬ是国家高新技术企业ꎮ金禾实业的产品品种多ꎬ有液氨㊁甲醇㊁甲醛㊁硝酸㊁硫酸㊁三聚氰胺㊁双氧水等基础化工产品ꎻ精细化工产品有安赛蜜㊁甲基麦芽酚等食品添加剂ꎬ产销量处于国际前列ꎮ金禾实业年产合成氨18万tꎬ在合成氨产能严重过剩的今天ꎬ市场竞争异常残酷ꎬ企业要生存发展必须努力降低生产成本ꎮ笔者经多方调研㊁考察㊁论证ꎬ在合成车间新上低压甲醇技术改造ꎬ采用了南京昊安科技有限公司低压甲醇工艺[1 ̄3]ꎮ1㊀低压甲醇工艺流程低压甲醇工艺流程见图1ꎮ图1㊀低压甲醇工艺流程㊀㊀经过气体净化系统处理的半水煤气经压缩机五段加压至ɤ5.5MPaꎬ与循环机加压至ɤ5.5MPa的循环气在油水分离器前混合ꎬ形成压力ɤ5.5MPa㊁温度约为35ħ的入塔气ꎮ混合后的入塔气进入热交换器的管程ꎬ被来自合成塔反应后的出塔气加热到190ħ后ꎬ由合成塔顶部进入触媒层[4]ꎬ在ɤ5.5MPa和190~260ħ条件下ꎬCO㊁CO2与H2反应生成甲醇并放出大量的热ꎮ放出的热大部分由合成塔壳侧的沸腾水带走ꎬ通过控制汽包压力来控制触媒层温度及合成塔出口温度ꎮ从合成塔出来的热反应气进入热交换器的壳程与入塔气逆流换热ꎬ被冷却到90ħ左右ꎮ该合成气再经水冷器进一步冷凝ꎬ冷却到ɤ40ħꎬ进入甲醇分离器分离出粗甲醇ꎮ分离出粗甲醇后温度约为40ħ的气体进入洗醇塔和从洗醇塔上部来的脱盐水在填料层逆流接触ꎬ气体中少量的甲醇被吸收ꎬ吸收少量甲醇的淡醇经减压后送往精醇工序ꎬ经过醇洗洗去气体中残余的甲醇后的气体一部分在增开循环机的情况下经过循环机循环使用ꎬ另一部分回到压缩机六段ꎮ甲醇合成塔管间环隙通过汽包给水不断地打入锅炉给水ꎮ汽包与合成塔壳侧由2根下水管和4根汽液上升管连接形成一自然循环锅炉ꎬ副产2.5MPa中压蒸汽ꎬ减压至1.3MPa后送往蒸汽管网ꎮ为保证水质量ꎬ在汽包和合成塔下部均设有连续和间断排污口ꎮ2㊀低压甲醇工艺投运效果分析从低压甲醇装置投运以来ꎬ装置运行安全平稳ꎬ出口气中CO+CO2含量稳定ꎮ低压甲醇装置从设计㊁安装㊁调试㊁运行ꎬ过程合理ꎮ吨氨电耗㊁蒸汽耗对比分析见表1㊁表2(2016年9月 12月与2017年9月 12月同期相比)ꎮ表1㊀吨氨电耗对比kW h2016年2017年9月10月11月12月9月10月11月12月12801262121712111236122112121185表2㊀吨氨蒸汽耗对比t2016年2017年9月10月11月12月9月10月11月12月0.3700.3680.3680.3710.2600.2640.2610.260㊀㊀由表1㊁表2可见:2016年9月 12月平均吨氨电耗为1243kW hꎬ2017年9月 12月平均吨氨电耗为1213kW hꎬ低压甲醇投运后吨氨电耗较之前下降了30kW hꎻ2016年9月 12月平均吨氨蒸汽耗为0.37tꎬ2017年9月 12月平均吨氨蒸汽耗为0.26tꎬ低压甲醇投运后吨氨蒸汽耗较之前下降了0.11tꎮ3㊀低压甲醇工艺特征根据生产证实ꎬ低压甲醇工艺是在配置相应的低压甲醇装置和工艺控制装置ꎬ优化生产条件ꎮ低压甲醇工艺具有以下特征:(1)装置运行稳定ꎬ出口气体CO+CO2转化率高ꎻ(2)节约电耗ꎻ(3)副产蒸汽ꎻ(4)无污染物质排放ꎮ4㊀经济效益4.1㊀电耗方面在低压甲醇装置投运后ꎬ压缩机五段出口压力由6.0MPa下降至5.0MPaꎬH12 ̄57/30氢氮气压缩机的电流由120A下降至110A以下ꎬ压缩机动力能耗下降ꎬ吨氨节电约30kW hꎬ按0.6元/(kW h)计算ꎬ吨氨成本下降18元ꎮ按年产合成氨18万t计算ꎬ年电耗节约费用324万元ꎮ4.2㊀蒸汽方面按照2017年9月 12月和2016年同期相比ꎬ吨氨蒸汽消耗下降0.11tꎬ按每吨蒸汽170元计算ꎬ吨氨成本下降18.7元ꎮ按年产合成氨18万t计算ꎬ年蒸汽节约费用336万元ꎮ5㊀结语低压甲醇设备及技术投资合计约900万元ꎬ节约的电耗及蒸汽费用合计约660万元ꎬ一年零三个月时间内可收回全部投资ꎮ低压甲醇装置投运后ꎬ压缩机五段㊁六段㊁七段压力均有不同程度的下降ꎬ促进了生产装置的安全稳定运行ꎮ实施低压甲醇工艺ꎬ有利于金禾实业合成氨装置产品结构调整ꎬ甲醇产品价格上升幅度较大时ꎬ公司可以及时调整提高甲醇产量ꎬ为公司的利润增长发挥重要作用ꎮ参考文献[1]㊀黄夏威.合成氨低压联醇系统开车技术总结[J].化肥工业ꎬ2012ꎬ39(3):52 ̄55.[2]㊀陈世通ꎬ文德国ꎬ苏庆贺.焦炉煤气制甲醇联产合成氨运行总结[J].氮肥技术ꎬ2013ꎬ36(5):43 ̄45. [3]㊀李玉顺ꎬ尚广辰ꎬ王平彪ꎬ等.合成氨联产甲醇技改小结[J].河南化工ꎬ2005ꎬ22(2):45 ̄46.[4]㊀钱海林ꎬ樊飞.MK ̄121型甲醇催化剂应用总结[J].化肥工业ꎬ2010ꎬ37(3):36 ̄38.(收稿日期㊀2019 ̄03 ̄06)。
甲醇合成装置优化运行总结

甲醇合成装置优化运行总结甲醇是一种重要的有机化工产品,广泛应用于化工、能源和化肥等领域。
甲醇的合成是一个复杂的工艺过程,涉及到催化剂、反应器、蒸馏塔等多个单元操作。
为了提高甲醇合成装置的运行效率和降低成本,需要对其进行优化运行。
本文将着重分析甲醇合成装置的优化运行总结,主要包括以下几个方面:一、催化剂的选择和管理催化剂是甲醇合成装置的关键组成部分,直接影响着合成反应的效率和产品质量。
为了优化甲醇合成装置的运行,需要选择合适的催化剂,并对其进行有效的管理。
需要选取活性高、稳定性好的催化剂,以提高甲醇合成的转化率和选择性。
需要对催化剂进行定期检查和维护,及时更换老化或失活的催化剂,以保证其稳定的使用和催化效果。
还需要对催化剂的再生和回收进行有效的管理,以减少催化剂的浪费和降低成本。
二、反应器操作条件的优化反应器是甲醇合成装置中的关键设备,直接影响着反应过程的效率和产品质量。
为了优化反应器的运行,需要对其操作条件进行有效的优化。
需要确保反应器的温度、压力和流速等参数处于合适的范围,以提高反应过程的效率和产品质量。
需要对反应器的热力学和动力学特性进行深入研究,以找到最佳的操作条件。
还需要对反应器进行有效的监控和控制,及时发现和解决潜在的问题,以确保其稳定的运行和高效的生产。
三、蒸馏塔的性能优化蒸馏塔是甲醇合成装置中的重要分离设备,直接影响着产品纯度和收率。
为了优化蒸馏塔的运行,需要对其性能进行有效的优化。
需要对蒸馏塔进行有效的设计和布置,以提高其分离效率和经济性。
需要对蒸馏塔的操作条件进行合理调控,以确保产品的纯度和收率。
还需要对蒸馏塔进行有效的清洗和维护,以保证其稳定的运行和高效的分离。
四、能源消耗的减少甲醇合成装置在生产过程中需要消耗大量的能源,为了降低能源成本和减少环境污染,需要对其能源消耗进行有效的管理和优化。
需要对能源消耗进行全面的分析和评估,找到能源的浪费和瓶颈,并采取有效的措施进行改善。
需要引入先进的节能技术和设备,以降低能源的消耗和提高能源利用率。
甲醇合成装置优化运行总结
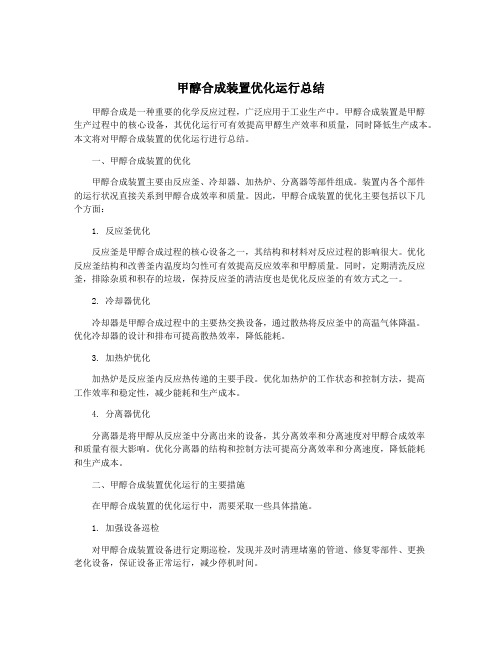
甲醇合成装置优化运行总结甲醇合成是一种重要的化学反应过程,广泛应用于工业生产中。
甲醇合成装置是甲醇生产过程中的核心设备,其优化运行可有效提高甲醇生产效率和质量,同时降低生产成本。
本文将对甲醇合成装置的优化运行进行总结。
一、甲醇合成装置的优化甲醇合成装置主要由反应釜、冷却器、加热炉、分离器等部件组成。
装置内各个部件的运行状况直接关系到甲醇合成效率和质量。
因此,甲醇合成装置的优化主要包括以下几个方面:1. 反应釜优化反应釜是甲醇合成过程的核心设备之一,其结构和材料对反应过程的影响很大。
优化反应釜结构和改善釜内温度均匀性可有效提高反应效率和甲醇质量。
同时,定期清洗反应釜,排除杂质和积存的垃圾,保持反应釜的清洁度也是优化反应釜的有效方式之一。
2. 冷却器优化冷却器是甲醇合成过程中的主要热交换设备,通过散热将反应釜中的高温气体降温。
优化冷却器的设计和排布可提高散热效率,降低能耗。
3. 加热炉优化加热炉是反应釜内反应热传递的主要手段。
优化加热炉的工作状态和控制方法,提高工作效率和稳定性,减少能耗和生产成本。
4. 分离器优化分离器是将甲醇从反应釜中分离出来的设备,其分离效率和分离速度对甲醇合成效率和质量有很大影响。
优化分离器的结构和控制方法可提高分离效率和分离速度,降低能耗和生产成本。
二、甲醇合成装置优化运行的主要措施在甲醇合成装置的优化运行中,需要采取一些具体措施。
1. 加强设备巡检对甲醇合成装置设备进行定期巡检,发现并及时清理堵塞的管道、修复零部件、更换老化设备,保证设备正常运行,减少停机时间。
2. 协调调配原材料与催化剂比例甲醇合成所需原料如氢气、碳氢化合物等比例的调配和醇/醚的组合比例也应予以调整,以提高反应的产率和避免甲醇质量下降。
3. 控制总合成压力与温度甲醇合成装置的压力和温度对反应效率和产率有直接影响。
在优化运行中,应控制总合成压力和温度,减少浮动范围,尽可能保持稳定。
4. 合理选用催化剂催化剂的选择对甲醇合成反应的效率和质量有很大影响。
甲醇合成装置优化运行总结
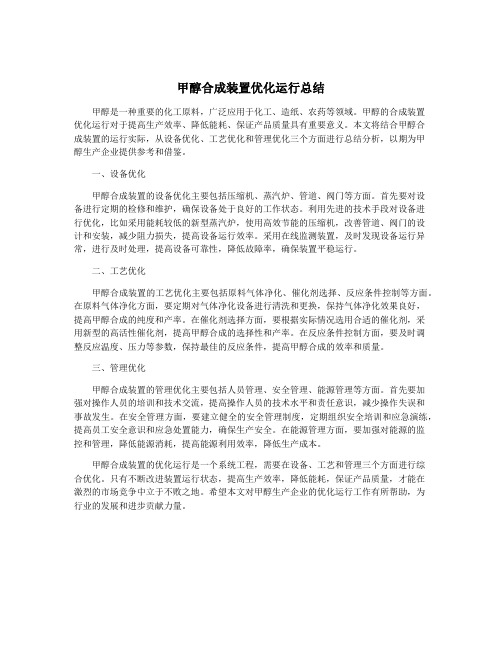
甲醇合成装置优化运行总结甲醇是一种重要的化工原料,广泛应用于化工、造纸、农药等领域。
甲醇的合成装置优化运行对于提高生产效率、降低能耗、保证产品质量具有重要意义。
本文将结合甲醇合成装置的运行实际,从设备优化、工艺优化和管理优化三个方面进行总结分析,以期为甲醇生产企业提供参考和借鉴。
一、设备优化甲醇合成装置的设备优化主要包括压缩机、蒸汽炉、管道、阀门等方面。
首先要对设备进行定期的检修和维护,确保设备处于良好的工作状态。
利用先进的技术手段对设备进行优化,比如采用能耗较低的新型蒸汽炉,使用高效节能的压缩机,改善管道、阀门的设计和安装,减少阻力损失,提高设备运行效率。
采用在线监测装置,及时发现设备运行异常,进行及时处理,提高设备可靠性,降低故障率,确保装置平稳运行。
二、工艺优化甲醇合成装置的工艺优化主要包括原料气体净化、催化剂选择、反应条件控制等方面。
在原料气体净化方面,要定期对气体净化设备进行清洗和更换,保持气体净化效果良好,提高甲醇合成的纯度和产率。
在催化剂选择方面,要根据实际情况选用合适的催化剂,采用新型的高活性催化剂,提高甲醇合成的选择性和产率。
在反应条件控制方面,要及时调整反应温度、压力等参数,保持最佳的反应条件,提高甲醇合成的效率和质量。
三、管理优化甲醇合成装置的管理优化主要包括人员管理、安全管理、能源管理等方面。
首先要加强对操作人员的培训和技术交流,提高操作人员的技术水平和责任意识,减少操作失误和事故发生。
在安全管理方面,要建立健全的安全管理制度,定期组织安全培训和应急演练,提高员工安全意识和应急处置能力,确保生产安全。
在能源管理方面,要加强对能源的监控和管理,降低能源消耗,提高能源利用效率,降低生产成本。
甲醇合成装置的优化运行是一个系统工程,需要在设备、工艺和管理三个方面进行综合优化。
只有不断改进装置运行状态,提高生产效率,降低能耗,保证产品质量,才能在激烈的市场竞争中立于不败之地。
希望本文对甲醇生产企业的优化运行工作有所帮助,为行业的发展和进步贡献力量。
甲醇合成装置优化运行总结

甲醇合成装置优化运行总结甲醇合成装置是煤炭化工产业中的一种重要装置,其稳定运行对提高产能和降低能耗具有重要意义。
近期,本单位对甲醇合成装置进行了优化运行,将优化结果总结如下。
一、优化前情况甲醇合成装置优化前,存在以下问题:1. 产能低下。
甲醇产量较低,不能满足市场需求。
2. 能耗较高。
甲醇合成过程中的能源消耗较大,能源利用率不高。
二、优化措施针对以上问题,我们采取了以下优化措施:1. 增加催化剂活性。
更换新的催化剂,并进行合理的催化剂喂料量控制,提高催化剂的利用率和活性。
2. 优化反应条件。
通过调整反应温度、压力等参数,优化反应条件,提高反应速率和选择性。
3. 改进热平衡。
优化换热器的设计和操作,增强热交换效果,降低能耗。
4. 提高原料纯度。
优化原料预处理流程,降低杂质含量,减少催化剂中毒,提高甲醇合成效率。
三、优化结果通过对甲醇合成装置的优化运行,取得了如下结果:1. 产能提升。
甲醇合成装置的产能得到明显提升,可以满足市场需求。
2. 能耗降低。
采取的优化措施使能耗明显降低,能源利用效率得到提高。
3. 产品质量稳定。
优化后,甲醇合成产品的纯度和稳定性得到提升,符合相关标准要求。
四、存在问题及改进方案在优化运行过程中,也发现了一些问题:1. 催化剂寿命较短。
催化剂的使用寿命较短,需要频繁更换。
2. 反应器压力波动。
反应器内压力存在波动现象,影响了反应效果。
针对上述问题,我们拟定了如下改进方案:1. 寻找更优催化剂。
加大催化剂研发力度,寻找具有更长寿命和更高活性的催化剂。
2. 优化反应器控制策略。
改进反应器的控制系统,提高压力稳定性,减少波动。
五、未来工作展望针对以上问题和改进方案,我们将继续开展以下工作:1. 加强与科研机构的合作。
与科研机构合作,共同开展催化剂研发和反应器技术研究,提升装置性能。
2. 大力推行节能减排。
通过技术改造和管理创新,进一步提高能源利用效率,减少对环境的影响。
3. 加强运行监控。
甲醇合成装置优化运行总结

甲醇合成装置优化运行总结随着科学技术的不断发展,甲醇合成技术也得到了很大的提升。
甲醇合成装置作为发展甲醇技术的核心要素之一,在生产中的运行优化显得尤为重要。
本文将对甲醇合成装置进行优化运行总结,以期在生产中更好地利用优化技术,确保生产效益的最大化。
一、合理调整甲醇合成装置工艺流程甲醇合成装置的工艺流程直接影响着催化剂的选择、催化反应的效率、设备运行的稳定性等因素,因此对工艺流程的调整非常重要。
首先,要考虑反应的温度、压力、气体比等因素,使之达到最合适的条件。
甲醇反应的适宜温度一般在240-300摄氏度之间,适宜压力在40-100Mpa之间,而对H2和CO的配比也会影响反应的效率。
其次,可以通过调整催化剂,改变反应物质在催化剂上的反应势能,提高反应速率和选择性。
最后,通过适当的工艺流程调整,合理地设置中间设备,并对设备进行优化加工,提高流程的连续性、稳定性和运行效率。
二、优化甲醇合成装置的控制策略甲醇合成装置的控制策略主要包括温度、压力、反应物配比等因素的控制。
针对这些控制因素,可以通过优化控制系统,实现动态优先、优先采用最佳控制以及最大化控制等控制策略,以进一步提高甲醇合成装置的运行效率。
例如,在控制温度方面,通过实时反馈温度数据,并自动调整温度控制器的调节参数,以达到更加准确的控制。
在控制压力方面,可以使用PID控制算法,控制压力在设定值范围内波动,实现压力稳定控制。
在控制反应物配比方面,可以采用组合控制策略,结合模糊控制、神经网络控制等多种控制算法,以实现最优控制。
三、加强甲醇合成装置的设备维护甲醇合成装置中设备的状态对反应的效率和装置的运行稳定性至关重要。
因此,加强设备的维护保养显得尤为重要。
首先,要对设备进行定期维护保养,掌握设备的运行状态和健康状况,及时检修、更换受损部件。
其次,要加强设备监测、数据采集和分析,及时响应生产状况的变化,小范围调整装置产量和质量。
最后,对设备耗材要有严格的管理控制,确保耗材的质量稳定且使用寿命有保障,从而确保设备的正常靠谱运行。
甲醇合成装置优化运行总结
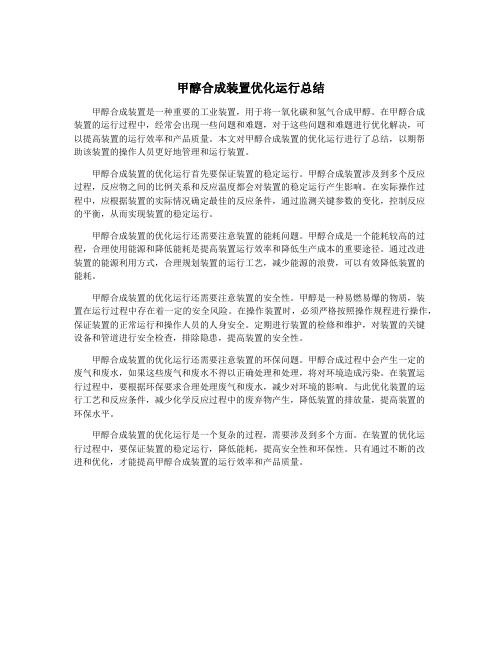
甲醇合成装置优化运行总结甲醇合成装置是一种重要的工业装置,用于将一氧化碳和氢气合成甲醇。
在甲醇合成装置的运行过程中,经常会出现一些问题和难题,对于这些问题和难题进行优化解决,可以提高装置的运行效率和产品质量。
本文对甲醇合成装置的优化运行进行了总结,以期帮助该装置的操作人员更好地管理和运行装置。
甲醇合成装置的优化运行首先要保证装置的稳定运行。
甲醇合成装置涉及到多个反应过程,反应物之间的比例关系和反应温度都会对装置的稳定运行产生影响。
在实际操作过程中,应根据装置的实际情况确定最佳的反应条件,通过监测关键参数的变化,控制反应的平衡,从而实现装置的稳定运行。
甲醇合成装置的优化运行还需要注意装置的能耗问题。
甲醇合成是一个能耗较高的过程,合理使用能源和降低能耗是提高装置运行效率和降低生产成本的重要途径。
通过改进装置的能源利用方式,合理规划装置的运行工艺,减少能源的浪费,可以有效降低装置的能耗。
甲醇合成装置的优化运行还需要注意装置的安全性。
甲醇是一种易燃易爆的物质,装置在运行过程中存在着一定的安全风险。
在操作装置时,必须严格按照操作规程进行操作,保证装置的正常运行和操作人员的人身安全。
定期进行装置的检修和维护,对装置的关键设备和管道进行安全检查,排除隐患,提高装置的安全性。
甲醇合成装置的优化运行还需要注意装置的环保问题。
甲醇合成过程中会产生一定的废气和废水,如果这些废气和废水不得以正确处理和处理,将对环境造成污染。
在装置运行过程中,要根据环保要求合理处理废气和废水,减少对环境的影响。
与此优化装置的运行工艺和反应条件,减少化学反应过程中的废弃物产生,降低装置的排放量,提高装置的环保水平。
甲醇合成装置的优化运行是一个复杂的过程,需要涉及到多个方面。
在装置的优化运行过程中,要保证装置的稳定运行,降低能耗,提高安全性和环保性。
只有通过不断的改进和优化,才能提高甲醇合成装置的运行效率和产品质量。
甲醇合成装置优化运行总结

甲醇合成装置优化运行总结为确保甲醇合成装置的优化运行,我们需要不断总结经验并进行不断的改进。
本文将总结甲醇合成装置的优化运行经验,并提出相关改进意见。
1. 技术装备优化:优化设备组合、改进工艺流程、调整设备参数等方面,不断开展技术装备优化,确保生产效率和产品质量。
2. 生产操作优化:优化生产操作流程,不断改进操作技能和操作标准,提高操作效率和工作质量。
同时,加强设备保养和维护,确保设备的稳定运行。
3. 数据监测系统建设:建立全面、准确的数据监测系统,对整个生产过程进行实时监测,及时发现问题并迅速解决。
4. 质量管控体系建立:建立完善的质量管控体系,从设备操作、生产技术、产品质量等多个方面对生产过程进行管控,确保产品质量达到标准要求。
5. 紧急故障处理方案制定:建立完善的紧急故障处理方案,及时应对突发问题。
同时,加强员工培训和技能提升,提高对各类故障的诊断和排除能力。
1. 加强装置自动化程度:加强自动化控制,提高数据采集和处理的准确性和速度,进一步实现系统网络化、信息化和智能化。
2. 熟练掌握工艺参数及设备运行规律:生产操作人员要深入了解工艺参数及设备运行规律,熟练掌握设备操作方式和技能方法,做到“细节决定成败”,不断提高运行效率。
3. 加强质量管理:在加强生产运行的同时,要进一步强化质量管理,增强标准化生产水平,加强质量检测和管控,提高产品质量和工艺指标。
4. 引入新技术:不断引入新技术,加强研发创新,提高生产自动化水平和生产效率,实现工程化、自动化和数字化生产。
5. 建立长效机制:建立长效机制,开展持续运营管理,持续推进优化运行,不断提高生产效率和产品质量,保障生产安全和环境保护。
甲醇合成装置优化运行总结
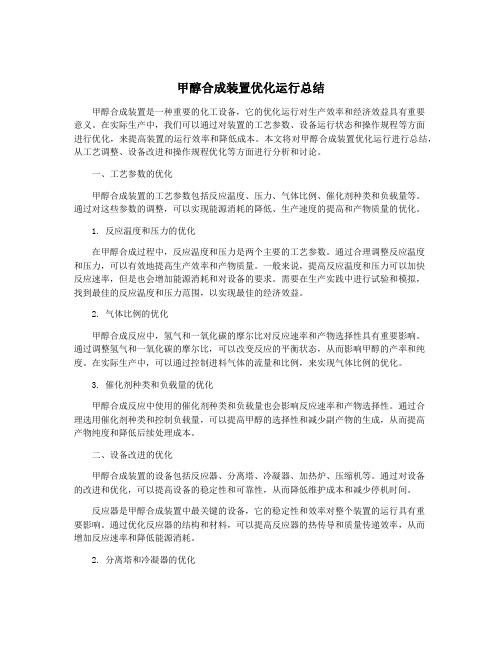
甲醇合成装置优化运行总结甲醇合成装置是一种重要的化工设备,它的优化运行对生产效率和经济效益具有重要意义。
在实际生产中,我们可以通过对装置的工艺参数、设备运行状态和操作规程等方面进行优化,来提高装置的运行效率和降低成本。
本文将对甲醇合成装置优化运行进行总结,从工艺调整、设备改进和操作规程优化等方面进行分析和讨论。
一、工艺参数的优化甲醇合成装置的工艺参数包括反应温度、压力、气体比例、催化剂种类和负载量等。
通过对这些参数的调整,可以实现能源消耗的降低、生产速度的提高和产物质量的优化。
1. 反应温度和压力的优化在甲醇合成过程中,反应温度和压力是两个主要的工艺参数。
通过合理调整反应温度和压力,可以有效地提高生产效率和产物质量。
一般来说,提高反应温度和压力可以加快反应速率,但是也会增加能源消耗和对设备的要求。
需要在生产实践中进行试验和模拟,找到最佳的反应温度和压力范围,以实现最佳的经济效益。
2. 气体比例的优化甲醇合成反应中,氢气和一氧化碳的摩尔比对反应速率和产物选择性具有重要影响。
通过调整氢气和一氧化碳的摩尔比,可以改变反应的平衡状态,从而影响甲醇的产率和纯度。
在实际生产中,可以通过控制进料气体的流量和比例,来实现气体比例的优化。
3. 催化剂种类和负载量的优化甲醇合成反应中使用的催化剂种类和负载量也会影响反应速率和产物选择性。
通过合理选用催化剂种类和控制负载量,可以提高甲醇的选择性和减少副产物的生成,从而提高产物纯度和降低后续处理成本。
二、设备改进的优化甲醇合成装置的设备包括反应器、分离塔、冷凝器、加热炉、压缩机等。
通过对设备的改进和优化,可以提高设备的稳定性和可靠性,从而降低维护成本和减少停机时间。
反应器是甲醇合成装置中最关键的设备,它的稳定性和效率对整个装置的运行具有重要影响。
通过优化反应器的结构和材料,可以提高反应器的热传导和质量传递效率,从而增加反应速率和降低能源消耗。
2. 分离塔和冷凝器的优化在甲醇合成过程中,需要进行多级分离和冷凝操作,以实现产物的纯度和回收。
低温甲醇洗装置原始开车总结

低温甲醇洗装置原始开车总结一、引言:低温甲醇洗装置是一种具有很高经济效益和环保性质的新型设备。
它主要通过接受低温甲醇洗涤技术,对自然气中的硫化氢、二硫化碳等有毒、有害物质进行有效去除。
本总结将谈论在开车过程中遇到的问题、解决方案,以及对设备进行优化改进的建议。
二、问题分析及解决方案:1. 设备启动问题:开车过程中,我们遇到了设备启动困难的问题。
经过系统性的排查,我们发现这主要是由于低温甲醇洗涤塔的冷凝液压不稳造成的。
解决方案是在启动前事先调整冷凝液流量和温度,保持压力稳定,确保启动顺畅。
2. 洗涤效率低下:在初期开车过程中,我们发现洗涤效率较低,一些硫化氢无法完全被洗除。
经过详尽分析,我们发现主要是由于甲醇和气体的流速不匹配所致。
解决方案是适当调整甲醇和气体的流速,使其达到最佳匹配,从而提高洗涤效率。
3. 设备压力不稳定:在运行过程中,我们发现设备存在压力波动较大的问题。
经过检查,发现主要原因是冷凝液中含有杂质的问题,导致管道堵塞,影响了系统的稳定性。
解决方案是增加冷凝液的过滤环节,以铁网过滤杂质,有效提高设备的稳定性。
4. 隔膜泵故障:在操作过程中,我们发现隔膜泵屡屡出现漏液、运行不稳定等问题。
通过修理人员的检查发现,这主要是由于泵体磨损导致的。
解决方案是增加泵体材质的密度,提高其耐磨性能,延长使用寿命,确保设备顺畅运行。
三、设备优化改进建议:在总结开车过程中遇到的问题和解决方案的基础上,我们还提出了以下改进建议,以进一步提高矮温甲醇洗装置的运行效率和稳定性:1. 设备参数调整:进一步优化甲醇和气体的流速匹配,使其能够更好地发挥洗涤效果。
2. 质量控制:进一步加强冷凝液的过滤处理,保证杂质的排除,缩减设备故障发生率。
3. 定期维护:加强对隔膜泵的定期检修和更换,确保设备的正常运行。
4. 进一步探究创新:成立科研团队,加强技术研发,探究更加高效、节能的低温甲醇洗装置设计方案。
但我深知以上建议并不适用于全部状况,详尽的优化改进需要依据现场实际运行状况和问题的迫切性综合思量。
甲醇合成装置优化运行总结
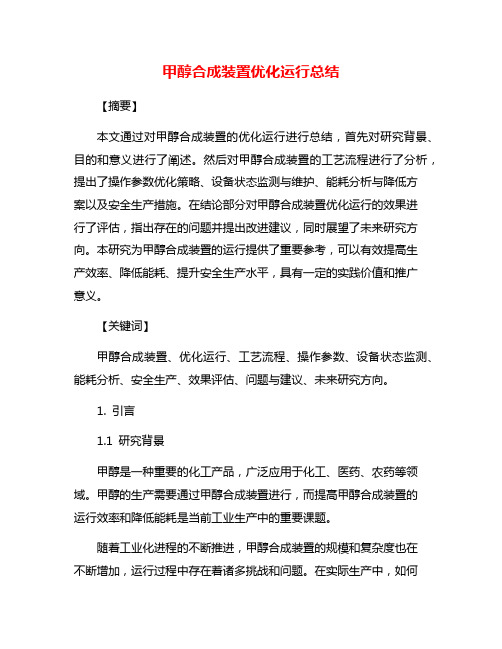
甲醇合成装置优化运行总结【摘要】本文通过对甲醇合成装置的优化运行进行总结,首先对研究背景、目的和意义进行了阐述。
然后对甲醇合成装置的工艺流程进行了分析,提出了操作参数优化策略、设备状态监测与维护、能耗分析与降低方案以及安全生产措施。
在结论部分对甲醇合成装置优化运行的效果进行了评估,指出存在的问题并提出改进建议,同时展望了未来研究方向。
本研究为甲醇合成装置的运行提供了重要参考,可以有效提高生产效率、降低能耗、提升安全生产水平,具有一定的实践价值和推广意义。
【关键词】甲醇合成装置、优化运行、工艺流程、操作参数、设备状态监测、能耗分析、安全生产、效果评估、问题与建议、未来研究方向。
1. 引言1.1 研究背景甲醇是一种重要的化工产品,广泛应用于化工、医药、农药等领域。
甲醇的生产需要通过甲醇合成装置进行,而提高甲醇合成装置的运行效率和降低能耗是当前工业生产中的重要课题。
随着工业化进程的不断推进,甲醇合成装置的规模和复杂度也在不断增加,运行过程中存在着诸多挑战和问题。
在实际生产中,如何科学合理地优化甲醇合成装置的运行,提高生产效率和质量,降低能耗和成本,保障生产安全,已成为当前甲醇行业亟待解决的问题。
为了更好地解决甲醇合成装置优化运行的问题,本文对甲醇合成装置的工艺流程进行了深入分析,探讨了操作参数优化策略、设备状态监测与维护、能耗分析与降低方案以及安全生产措施等方面,旨在为甲醇生产企业提供更有效的优化运行方案。
1.2 研究目的甲醇合成装置是重要的化工生产设备,其优化运行对降低生产成本、提高生产效率具有重要意义。
本次研究的目的在于通过对甲醇合成装置的工艺流程分析、操作参数优化策略、设备状态监测与维护、能耗分析与降低方案以及安全生产措施等方面的研究,探讨如何使甲醇合成装置的运行更加稳定、高效。
通过对甲醇合成装置优化运行的效果评估,及存在的问题与改进建议的分析,为今后的生产提供重要参考。
未来研究方向展望将在继续优化甲醇合成装置的运行模式、提高产品质量和生产效率的基础上,进一步探索更加环保和节能的生产工艺,为甲醇合成装置的长期可持续发展提供科学依据。
甲醇合成装置优化运行总结

甲醇合成装置优化运行总结(一)技术方面1、温度控制合成甲醇是一个吸热反应,反应温度的控制对于甲醇的产量和质量至关重要。
适当提高反应温度可以提高甲醇的产量,但过高的温度会导致甲醇产率下降和二甲醇等副产物的生成。
因此,优化甲醇合成装置的温度控制是提高甲醇产量和质量的重要措施之一。
2、压力控制在甲醇合成反应中,高压有利于提高甲醇产量和降低反应的平衡常数。
但是,过高的压力不仅增加了设备的成本,还增加了设备的维护成本和安全风险,因此,合适的压力控制可以帮助提高甲醇产量和节约能源。
3、催化剂的性能和选择催化剂是甲醇合成反应的核心,催化剂的活性和选择性直接影响甲醇的质量和产量。
在使用催化剂时,需要考虑催化剂的选择、稳定性和再生性。
同时,需要合理控制催化剂的初温度、硫化等参数,保障催化剂的性能稳定和持久的反应。
(二)经济方面经济效益是对甲醇合成装置优化运行最直接和重要的衡量标准之一。
对于优化装置的经济效率,主要从以下几个方面进行考虑:1、能源消耗甲醇合成反应是一个高能耗的过程,如何合理控制能源的消耗可以降低成本并提高经济效益。
一些具体的优化措施包括:利用余热回收技术,优化温度、压力等操作参数,针对谷氨酸结晶工艺等进行优化。
2、原材料选择甲醇生产所需要的原材料主要包括煤、天然气、重油等,对于原材料的选择需从经济、安全、生态等多个方面进行考虑。
同时,应当根据成本、可获得性和环境保护要求进行权衡,以选择最优原材料。
3、技术装备的选择和升级甲醇合成装置的优化需要针对不同的工厂和工艺特点,从而制定合适的升级方案,选择最合适的技术装备,以达到更加经济的效益。
(三)环境方面甲醇合成过程中产生的废水、废气等对环境产生了一定的影响。
如何优化甲醇合成装置的运行从而减少环境污染,避免对环境造成不良影响,成为了近年来行业关注的重点。
应对环境方面进行优化,可以从以下几个方面进行:1、臭氧监测在甲醇合成过程中,二氧化碳和一氧化碳等物质可能导致甲醇质量的降低和二甲醚等有毒物质的产生。
甲醇装置工作总结范文
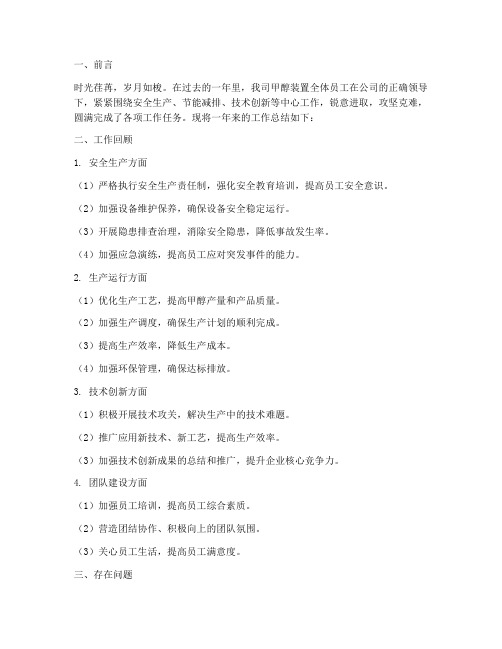
一、前言时光荏苒,岁月如梭。
在过去的一年里,我司甲醇装置全体员工在公司的正确领导下,紧紧围绕安全生产、节能减排、技术创新等中心工作,锐意进取,攻坚克难,圆满完成了各项工作任务。
现将一年来的工作总结如下:二、工作回顾1. 安全生产方面(1)严格执行安全生产责任制,强化安全教育培训,提高员工安全意识。
(2)加强设备维护保养,确保设备安全稳定运行。
(3)开展隐患排查治理,消除安全隐患,降低事故发生率。
(4)加强应急演练,提高员工应对突发事件的能力。
2. 生产运行方面(1)优化生产工艺,提高甲醇产量和产品质量。
(2)加强生产调度,确保生产计划的顺利完成。
(3)提高生产效率,降低生产成本。
(4)加强环保管理,确保达标排放。
3. 技术创新方面(1)积极开展技术攻关,解决生产中的技术难题。
(2)推广应用新技术、新工艺,提高生产效率。
(3)加强技术创新成果的总结和推广,提升企业核心竞争力。
4. 团队建设方面(1)加强员工培训,提高员工综合素质。
(2)营造团结协作、积极向上的团队氛围。
(3)关心员工生活,提高员工满意度。
三、存在问题1. 安全生产方面:个别员工安全意识淡薄,存在违章操作现象。
2. 生产运行方面:部分设备老化,维护保养不到位。
3. 技术创新方面:技术创新能力有待提高。
四、下一步工作计划1. 深入开展安全生产教育培训,提高员工安全意识。
2. 加强设备维护保养,提高设备运行效率。
3. 积极开展技术创新,提高企业核心竞争力。
4. 加强团队建设,提高员工综合素质。
总之,过去的一年,甲醇装置全体员工在公司的正确领导下,取得了显著的成绩。
在新的一年里,我们将继续努力,以更加饱满的热情、更加务实的作风,为实现公司发展目标而努力奋斗。
甲醇合成装置优化运行总结
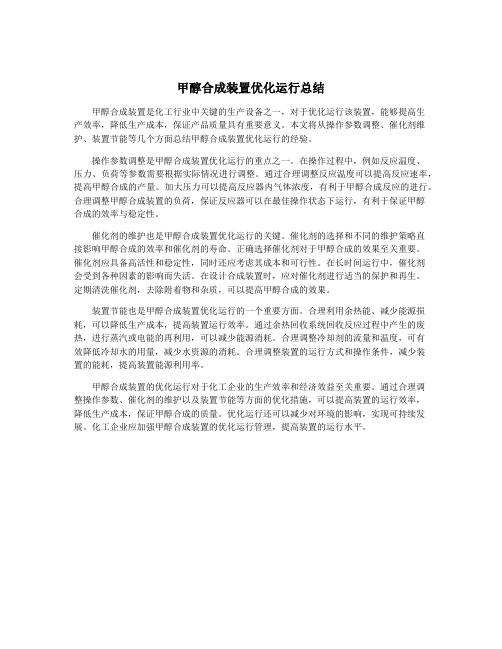
甲醇合成装置优化运行总结甲醇合成装置是化工行业中关键的生产设备之一,对于优化运行该装置,能够提高生产效率,降低生产成本,保证产品质量具有重要意义。
本文将从操作参数调整、催化剂维护、装置节能等几个方面总结甲醇合成装置优化运行的经验。
操作参数调整是甲醇合成装置优化运行的重点之一。
在操作过程中,例如反应温度、压力、负荷等参数需要根据实际情况进行调整。
通过合理调整反应温度可以提高反应速率,提高甲醇合成的产量。
加大压力可以提高反应器内气体浓度,有利于甲醇合成反应的进行。
合理调整甲醇合成装置的负荷,保证反应器可以在最佳操作状态下运行,有利于保证甲醇合成的效率与稳定性。
催化剂的维护也是甲醇合成装置优化运行的关键。
催化剂的选择和不同的维护策略直接影响甲醇合成的效率和催化剂的寿命。
正确选择催化剂对于甲醇合成的效果至关重要。
催化剂应具备高活性和稳定性,同时还应考虑其成本和可行性。
在长时间运行中,催化剂会受到各种因素的影响而失活。
在设计合成装置时,应对催化剂进行适当的保护和再生。
定期清洗催化剂,去除附着物和杂质,可以提高甲醇合成的效果。
装置节能也是甲醇合成装置优化运行的一个重要方面。
合理利用余热能、减少能源损耗,可以降低生产成本,提高装置运行效率。
通过余热回收系统回收反应过程中产生的废热,进行蒸汽或电能的再利用,可以减少能源消耗。
合理调整冷却剂的流量和温度,可有效降低冷却水的用量,减少水资源的消耗。
合理调整装置的运行方式和操作条件,减少装置的能耗,提高装置能源利用率。
甲醇合成装置的优化运行对于化工企业的生产效率和经济效益至关重要。
通过合理调整操作参数、催化剂的维护以及装置节能等方面的优化措施,可以提高装置的运行效率,降低生产成本,保证甲醇合成的质量。
优化运行还可以减少对环境的影响,实现可持续发展。
化工企业应加强甲醇合成装置的优化运行管理,提高装置的运行水平。
甲醇合成装置优化运行总结
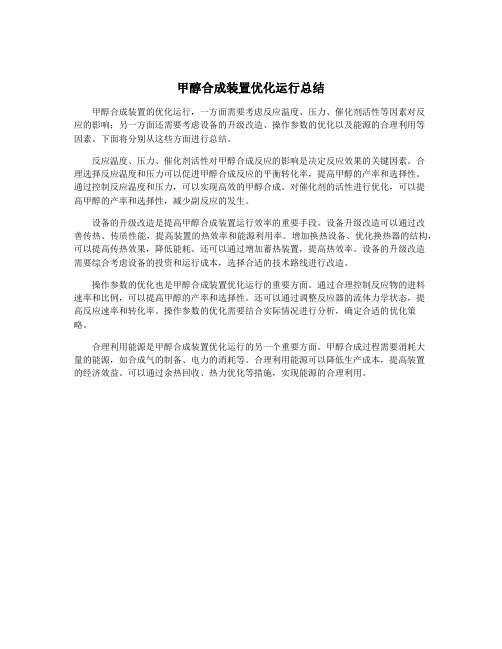
甲醇合成装置优化运行总结
甲醇合成装置的优化运行,一方面需要考虑反应温度、压力、催化剂活性等因素对反
应的影响;另一方面还需要考虑设备的升级改造、操作参数的优化以及能源的合理利用等
因素。
下面将分别从这些方面进行总结。
反应温度、压力、催化剂活性对甲醇合成反应的影响是决定反应效果的关键因素。
合
理选择反应温度和压力可以促进甲醇合成反应的平衡转化率,提高甲醇的产率和选择性。
通过控制反应温度和压力,可以实现高效的甲醇合成。
对催化剂的活性进行优化,可以提
高甲醇的产率和选择性,减少副反应的发生。
设备的升级改造是提高甲醇合成装置运行效率的重要手段。
设备升级改造可以通过改
善传热、传质性能,提高装置的热效率和能源利用率。
增加换热设备、优化换热器的结构,可以提高传热效果,降低能耗。
还可以通过增加蓄热装置,提高热效率。
设备的升级改造
需要综合考虑设备的投资和运行成本,选择合适的技术路线进行改造。
操作参数的优化也是甲醇合成装置优化运行的重要方面。
通过合理控制反应物的进料
速率和比例,可以提高甲醇的产率和选择性。
还可以通过调整反应器的流体力学状态,提
高反应速率和转化率。
操作参数的优化需要结合实际情况进行分析,确定合适的优化策
略。
合理利用能源是甲醇合成装置优化运行的另一个重要方面。
甲醇合成过程需要消耗大
量的能源,如合成气的制备、电力的消耗等。
合理利用能源可以降低生产成本,提高装置
的经济效益。
可以通过余热回收、热力优化等措施,实现能源的合理利用。
- 1、下载文档前请自行甄别文档内容的完整性,平台不提供额外的编辑、内容补充、找答案等附加服务。
- 2、"仅部分预览"的文档,不可在线预览部分如存在完整性等问题,可反馈申请退款(可完整预览的文档不适用该条件!)。
- 3、如文档侵犯您的权益,请联系客服反馈,我们会尽快为您处理(人工客服工作时间:9:00-18:30)。
低压 甲醇装置原始开车和生产运行情况看 , 湖南 安 淳公 司低压 甲醇 合成 技 术 具 有 升 温还 原 容 易 、 生产 能 力 可调 范 围大 、 统 阻力 小 、 产成 本 低 、 系 生
易操 作控 制 和运行 比较平 稳 等优点 。
热水(. MP ) 3 a 0
外 送 蒸 13MP ) . a 升 温 蒸 汽 f. a 30MP )
分 塔 ) 粗 甲醇 分 离 下 来 经 闪蒸 槽 送 往 精 醇 工 将
进 一步 降低 合成 氨 的 综 合成 本 , 提升 整 体 的 盈利 能 力 , 定 提 高 甲醇产 量 、 大 醇 氨 比 的调 控 范 决 扩 围, 以此 解决 出现 尿素 和 甲醇市场行 情 大 幅变化 ,
能 够通过 调整 尿素 和 甲醇相 互之 间 的产量实 现整
器再 次 分离 , 体 出水 分 离器 后 回到 高压 机二 段 气 人 口, 一部分 气体 经循 环机 加压 与原料 气混 合 , 另
在 系统 内继续 进行 循环 。
恒 温悬挂 水 管式 甲醇 合 成 塔 。该 工 程 于 20 08年
8月 1 日开 工 ,0 9年 5月 1 0 20 9日建 成 投 运 。从
时 , 始将 烃化 后 的合 格 气 体 通 过 事前 配 置 的管 开
道 引到低 压 甲醇 系统 , 原则 上 根 据 升 温 还 原 的 要 求 向低 压 甲醇 系统 内间 断补 加烃化 合 格气 。升 温
还原 全过 程依 照 “ 温不 提 氢 , 氢 不提 温 ” 原 提 提 的
汽包
L
水 分 布
高压机二段入口 d卜 循环机 —— _ l 圣1
循
环
田
气
油 分 离 器
醇 塔
蒸 发 式 冷 凝
[ 一
低压机一 段入口
新鲜气来 自低压机一段 入 口
蓝 精醇工段 L一
图 1 低 压甲醇工艺流程
小氮肥
第3 9卷
第 7期
21 0 1年 7月
网, 锅炉给水补 充到汽包 中 , 成一个 闭路水循 环 。 构
2 低 压 甲醇 装置主要设备
低 压 甲醇装 置 主要设 备见 表 1 。
表 1 低 压 甲醇 装 置 主 要 设 备
设 备 名 称
甲醇 塔 热 交 换 器
结束 , 共计 耗 时 17h 3 。此 次低 压 甲醇催 化剂 升温 还 原采 用低 氢 还原 法 , 首先 用 纯 度为 9 . 9 ( 9 9 % 体 积分数 ) 的合 格 氮 气 将 低 压 甲. 系 统 压 力 升 至 醇 07M a 始 升 温 , . P 开 当催 化 剂 层 温 度 升 到 1 0 c 7 C
l 7
的水进入水 室 , 匀进 入各 内管 , 均 由上 而 下在 管 的 底端折转 到外 管 , 吸收管外 反应 热 , 部分 水被 汽化 , 密度较小 的汽水 混 和物上 升 到汽 室再 由连接 管 上
为 3 . 11 ) 催 化 剂 筐 容 积 利 用 率 为 9 . 8 。 5 2 I , T 98% 存在 的 主要 问题 : ①催 化剂 在筛 选过 程 中 , 化剂 催 粉未 清 除 干净 ; 催 化 剂 在 装 填 时 , ② 出现 同格 内
1 低 压 甲醇工艺流程
低 压 甲醇工 艺流程 见 图 1 自压缩 机 来 的压 。
力 为 50MP . a左右 原 料气 与循 环 气 汇 合 , 经热 交 换 器后 被热 反应 气加 热 至 20o 右 , 后进 入 0 C左 然 甲醇塔 , 反应 后 的热 气 体 进入 热交 换 器 管 内 与管 问冷气 体换 热 , 降温至 8 0℃左右再 进入 蒸发 式冷 凝器 降 温到 4 0℃ 以下 , 然后 进 入 净 醇塔 下 段 ( 醇
l 6
小 氮肥
第3 9卷
第 7期
21年7 01
低 压 甲醇 装 置 运 行 总 结
朱 江 波
( 南心连心 化肥有 限公 司 新 乡4 3 3 限公 司 ( 称 心 连 心 公 简
司) l 3 ” “ 8・ 0 工程 于 2 0 0 6年 9月 5日建 成投 运 , 20 0 6年底达 产达 标 , 已具 备年 产合 成氨 2 0k 、 现 6 t 甲醇 8 t 0k 和颗粒 尿 素 4 0k 的生 产 能力 。为 了 3 t
段, 分离 后 的气 体进 入净 醇 塔 的上 段 ( 洗 塔 ) 醇 通
过 喷水将 未分 离 的 醇洗 涤 下 来 , 后 进入 水 分 离 然
体利 益最 大 化 。经 过 反 复论 证 和 考察 , 心连 心 公 司决 定采 用湖 南安 淳公 司 的低压 甲醇合 成技 术新
建 6 ta低压 甲醇装 置 , 核 心技术 为 JD低 压 0k / 其 J
圈 、 圈催 化 剂高 度不 一 。 外 3 2 催化 剂升 温还 原情 况 . 20 0 9年 5月 1 日9 O 开 始 低压 甲醇 催 化剂 0 :0 升温 还原 , 5月 1 至 6日2 0 催 化 剂升 温还 原 全部 :0
升到水分 布器 , 分离后进入 汽包 。蒸 汽外送 蒸汽 管
JD悬 挂水 管 式 甲 醇 塔 内流 程 : 反 应 气 体 J 未 自甲醇塔 下部 三 通 旁侧 进 入 内外筒 环 隙 , 由下 而 上径 向流过催 化 剂 床层 , 应 后 气 体 经 中心 集 气 反
管, 自上 而下 由塔 下部 出塔 。塔 内换 热器 与汽 包 构成 一个 饱 和水 和 蒸 汽 的循 环 闭路 , 汽 包 下来 从
主 要 参 数
D 28 0m x1 2 11】台 N 0 m 54 011 1 , 1 D 18 8lI×1 0 t, N 7 ll 57 0I 1台 /l n o 5 5MP , . a 2台
2 6 0 m × 18 0 f l 1台 0 m 2 0 1l [ , l