转炉炼钢工艺
转炉炼钢炼钢工艺学

2023-11-06contents •炼钢的基本原理•转炉炼钢技术•钢的分类与特性•炼钢设备与工艺技术改进•炼钢过程中的质量控制•转炉炼钢技术的发展趋势与挑战•转炉炼钢工艺的前景展望目录01炼钢的基本原理转炉炼钢的氧化反应是通过向熔融的铁水中注入氧气,将铁水中的碳、硅、锰等元素氧化成气体,形成氧化物。
炼钢的物理化学原理氧化反应为了去除铁水中的杂质,需要向熔融的铁水中加入石灰石、萤石等造渣材料,形成炉渣。
造渣为了防止钢水在凝固过程中产生气泡,需要向熔融的钢水中加入脱氧剂,如锰铁、硅铁等,以减少钢水中的氧含量。
脱氧在钢的凝固过程中,固态相变包括铁素体和奥氏体的形成和转变。
这些相变过程受到温度、成分和其他因素的影响。
固态相变在钢的熔炼过程中,液态相变包括碳和其他合金元素的溶解和扩散。
这些相变过程受到温度、成分和其他因素的影响。
液态相变钢的相变原理去除杂质为了提高钢的纯度,需要去除铁水中的杂质,如硫、磷、氮等。
这些杂质可以通过造渣或添加脱氧剂等方式去除。
合金化为了调整钢的成分和性能,需要向熔融的钢水中加入合金元素,如碳、硅、锰等。
这些元素可以通过合金铁块或废钢等方式添加。
钢的纯净化原理02转炉炼钢技术装炉将铁水、废钢等原材料装入炉内,形成铁水包和废钢包。
熔化通过高温加热铁水包和废钢包,将铁水和废钢熔化为液态。
氧化向熔化的铁水中吹入氧气,使其中的碳、硅、锰等元素氧化生成气体,去除杂质。
脱碳继续向熔化的铁水中吹入氧气,降低铁水中的碳含量,使铁的含量增加。
调整成分根据需要加入合金元素,调整铁水的成分以满足产品要求。
出钢将符合要求的铁水倒入钢包中,进行浇铸成钢坯。
转炉炼钢的工艺流程由高炉或直接还原铁熔化而成,是转炉炼钢的主要原料。
铁水由报废的钢铁制品和加工过程中的余料组成,作为添加元素加入到铁水中。
废钢用于氧化反应,将铁水中的杂质氧化成气体,提高铁水的纯度。
氧气根据产品要求,向铁水中加入不同的合金元素,调整成分以满足产品要求。
转炉炼钢工艺分析

转炉炼钢工艺分析简介转炉炼钢是一种重要的钢铁生产工艺。
它采用转炉作为熔炼设备,通过氧化钢水的方式去除杂质,从而获得高纯度的钢水。
工艺流程转炉炼钢的工艺流程一般包括以下几个步骤:1.亚稳态钢水倒入转炉中,同时注入氧气;2.氧气与铁水反应生成氧化物,从而去除杂质;3.在适当的条件下加入渣剂,将浮渣与钢水分离;4.投入合适的合金和调节剂,调节钢水的成分和性质;5.倒出钢水至铸铁机或连铸机中,制成钢材。
工艺优势相对于其他炼钢工艺,转炉炼钢具有以下优势:1.钢水纯度高,化学成分稳定,可以得到各种不同技术要求的钢材;2.工艺流程简单,可自动化控制,生产效率高;3.单次生产能力大,适用于大批量生产。
工艺不足然而,转炉炼钢也存在一些问题,主要包括:1.熔炼过程中,由于氧化反应的过程比较复杂,会产生大量的烟尘和废气污染;2.熔炼后再行铸造需要添加铝、钛等金属,也会对环境造成一定的污染。
工艺改进针对转炉炼钢存在的问题,研究人员进行了多方面的工艺改进研究。
主要包括以下几个方面:1.减少污染:采用高热效应烟气脱硫技术和洗涤重金属离子等方法,减少烟尘、废水排放,改善环境;2.提高产能:对炉况和操作条件进行优化调整,提高单次生产能力;3.提高效益:加入合适的合金和调节剂,调节钢水的成分,生产高附加值、高品质的钢材。
市场应用目前,转炉炼钢工艺已经在全球范围内广泛应用。
根据统计数据,仅中国一国的转炉炼钢产量就占全球的60%以上。
随着技术的不断进步,转炉炼钢工艺在钢铁生产中的地位将更加重要。
结论综上所述,转炉炼钢是一种重要的钢铁生产工艺,具有钢水纯度高、生产效率高等诸多优点。
但其存在烟尘、废气污染等问题。
通过改善工艺和技术手段的引入,可以实现减少污染、提高产能和效益的目标。
这一工艺在全球范围内得到广泛应用,将在未来发展中继续发挥重要作用。
转炉炼钢工艺流程

转炉炼钢工艺流程转炉炼钢是一种常用的钢铁冶炼工艺,通过高温炼炉将生铁和废钢进行冶炼,以生产高品质的钢材。
下面将详细介绍转炉炼钢的工艺流程。
1. 原料准备转炉炼钢的原料主要包括生铁和废钢。
生铁是从高炉中得到的铁水,含有较高的碳含量,而废钢则是来自废旧钢材的回收利用。
在进行炼钢之前,需要对原料进行严格的筛选和分类,确保原料的质量符合生产要求。
2. 转炉炉前准备在进行转炉炼钢之前,需要对转炉进行一系列的准备工作。
首先是清理转炉内部的残渣和杂质,确保转炉内部的清洁。
然后对转炉进行加热,使其达到适宜的工作温度。
同时,还需要准备氧气、燃料和炉渣等辅助材料,以保障炼钢过程中的顺利进行。
3. 转炉炼钢过程转炉炼钢的主要过程包括炉前处理、吹炼、脱硫、脱磷、合金加入和出钢等环节。
首先是炉前处理,将预先准备好的生铁和废钢装入转炉中。
然后启动吹炼工艺,通过吹入高压氧气和燃料,使炉内的温度迅速升高,生铁和废钢开始熔化并发生氧化还原反应。
在这个过程中,炉内的温度可以达到数千摄氏度,将原料中的杂质和不纯物质燃尽,确保钢水的纯净度。
接下来是脱硫和脱磷的过程,通过向炉内加入适量的脱硫剂和脱磷剂,将钢水中的硫和磷等有害元素去除,提高钢材的质量和纯度。
在炼钢的过程中,根据需要还可以向炉内加入一定比例的合金元素,如铬、锰、钼等,以调整钢材的化学成分和性能。
最后是出钢过程,当炼钢结束后,通过倾炉口将炼好的钢水倒入钢包中,再经过连铸、轧制等工艺,最终得到成品钢材。
4. 转炉炼钢的优点转炉炼钢相比其他炼钢工艺具有以下优点:一是能够利用废钢资源,实现资源的循环利用;二是生产成本较低,能够生产出高品质的钢材;三是炼钢过程中能够控制钢材的化学成分和性能,满足不同用途的需要。
总之,转炉炼钢是一种成熟、高效的钢铁冶炼工艺,通过严格的工艺流程和操作规范,能够生产出优质的钢材产品,满足市场和用户的需求。
第三章转炉炼钢工艺1

铁水和废钢配比是根据热平衡计算确定。
通常,铁水配比为70~90%,其值取决于铁水温度和成 分、炉容量、冶炼钢种、原材料质量和操作水平等。
炉容比:
指转炉内自由空间的容积(V)与金属装入量(t)之比 (V/t , m3/t)。
它通常波动在0.83~1.0,它与铁水成分、冷却剂类型、 氧枪喷头结构和供氧强度等因素有关。
区)和光亮较弱的狭窄外围(二次反应区)所构成 。
反应区的温度在2000~2700℃之间(高温、高氧浓度) 。
穿透深度和冲击面积是 凹坑特征的主要标志。
枪位:喷嘴在静止 液面上的高度。
转炉炼钢供氧制度
熔池的搅拌程度与氧射流的冲击强度密切相关:
氧射流冲击力大(硬吹),则射流的穿透深度大 ,冲击面积小,对熔池的搅拌强烈;
厂名 太钢 二炼
吨位/t 50
炉容 0.97 比 /m3.t-1
首钢三 炼
80
攀钢 120
0.84 0.90
本钢二 炼
120
鞍钢三 首钢二
炼
炼
150 210
宝钢一 炼
300
0.91
0.86 0.97
1.05
第三节 转炉炼钢供氧制度
一.氧射流及其对熔池的相互作用
1.氧射流 顶部氧射流是转炉炼钢最重要的供氧渠道。 顶氧射流是通过水冷氧枪将高压、高纯的氧气从出
(3-1) (3-2) (3-3)
(3-4) (3-5)
(3-6) (3-7)
(3-8) (3-9)
反应(3-9)的发展程度取决于C、Si、Mn的浓度。
转炉炼钢供氧制度
②
在一次反应区以外的二次反应区,主要是间
接氧化; [Fe]+ 1/2{O2 } =(FeO)
转炉炼钢工艺

转炉炼钢工艺1转炉炼钢的原材料引言转炉炼钢所用原材料可分为金属料和非金属料两大类。
原材料质量的好坏,不仅关系到吹炼操作的难易,而且会影响钢的产量、质量和生产成本。
1.1 金属料转炉炼钢的金属料主要是铁水、废钢和铁合金。
1.1.1铁水1 作用:转炉炼钢的主原料,一般占装入量的70%以上。
2 要求铁水应符合一定要求,以简化和稳定操作并获得良好技术经济指标。
1)温度≥1250℃而且稳定铁水温度的高低,标志着其物理热的多少。
较高的铁水温度,不仅能保证转炉吹炼顺利进行,同时还能增加废钢的配加量,降低生产成本。
因此,希望铁水的温度尽量高些,一般应保证入炉时仍在1250℃~1300℃以上。
另外,还希望铁水温度相对稳定,以利于冶炼操作和生产调度。
2)成分合适而且波动小转炉炼钢的适应性较强,可将各种成分的铁水吹炼成钢。
但是,为了方便转炉操作及降低生产成本,铁水的成分应该合适而稳定。
(1)铁水的含磷量≤0.4%:磷会使钢产生“冷脆”现象,是钢中的有害元素之一。
转炉单渣法冶炼时的脱磷效果为85%~95%,普碳钢的含磷量通常要求≤0.04%,因此,国标规定铁水的含磷量小于0.4%。
需要指出的是,高炉内不能去磷,如果铁水的含磷量超过0.4%,或者吹炼低磷钢,则需采用双渣法冶炼或对铁水进行预脱磷处理。
(2)铁水的含硫量≤0.07%:硫会使钢产生“热脆”现象,也是钢中的有害元素。
转炉的脱硫效果不理想,单渣法冶炼时的脱硫率仅为30%~35%,而通常要求钢液的含硫量在0.05%以下,因此国标规定铁水含硫量≤0.07%。
如果铁水含硫量超过0.07%或吹炼低硫钢,则需采用双渣法冶炼或对铁水进行预脱硫处理。
(3)铁水的含硅量:铁水中的硅是转炉炼钢的主要发热元素之一,含硅量每增加0.1%,废钢比可增加1.3%~1.5%。
对于大、中型转炉,铁水含硅量以0.5%~0.8%为宜。
小型转炉的热损较大,铁水的含硅量可以高些。
若含硅量低于0.5%,铁水的化学热不足,会导致废钢比下降,小容量转炉甚至不能正常吹炼;反之,如果铁水含硅量高于0.8%,不仅会增加造渣材料的消耗,而且使炉内的渣量偏大,过多的渣量容易引起喷溅,增加金属损失。
转炉炼钢的工艺流程
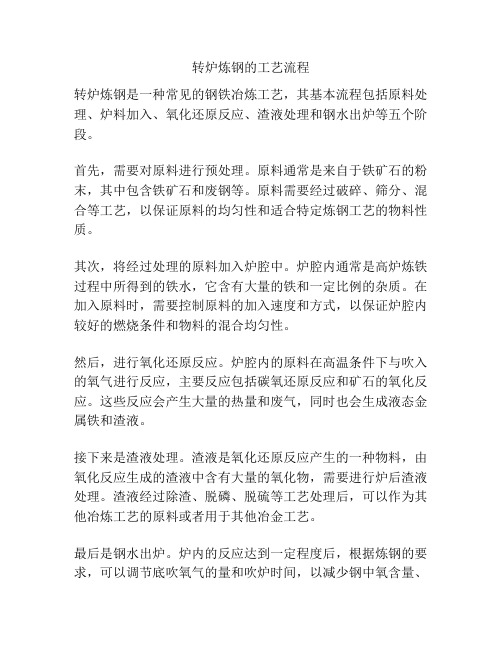
转炉炼钢的工艺流程转炉炼钢是一种常见的钢铁冶炼工艺,其基本流程包括原料处理、炉料加入、氧化还原反应、渣液处理和钢水出炉等五个阶段。
首先,需要对原料进行预处理。
原料通常是来自于铁矿石的粉末,其中包含铁矿石和废钢等。
原料需要经过破碎、筛分、混合等工艺,以保证原料的均匀性和适合特定炼钢工艺的物料性质。
其次,将经过处理的原料加入炉腔中。
炉腔内通常是高炉炼铁过程中所得到的铁水,它含有大量的铁和一定比例的杂质。
在加入原料时,需要控制原料的加入速度和方式,以保证炉腔内较好的燃烧条件和物料的混合均匀性。
然后,进行氧化还原反应。
炉腔内的原料在高温条件下与吹入的氧气进行反应,主要反应包括碳氧还原反应和矿石的氧化反应。
这些反应会产生大量的热量和废气,同时也会生成液态金属铁和渣液。
接下来是渣液处理。
渣液是氧化还原反应产生的一种物料,由氧化反应生成的渣液中含有大量的氧化物,需要进行炉后渣液处理。
渣液经过除渣、脱磷、脱硫等工艺处理后,可以作为其他冶炼工艺的原料或者用于其他冶金工艺。
最后是钢水出炉。
炉内的反应达到一定程度后,根据炼钢的要求,可以调节底吹氧气的量和吹炉时间,以减少钢中氧含量、降低杂质含量和改善钢水中的成分均匀性。
一段时间后,钢水可以从转炉中出炉,经过连铸工艺可以制成各种形状的钢材。
总体而言,转炉炼钢工艺流程包括原料处理、炉料加入、氧化还原反应、渣液处理和钢水出炉等五个阶段。
这一工艺在现代钢铁冶炼中得到广泛应用,能够实现大规模的、高效的钢铁生产。
同时,随着技术的不断发展,该工艺也在不断地改进和优化,为钢铁行业的可持续发展做出了重要贡献。
转炉炼钢工艺流程

转炉炼钢工艺流程转炉炼钢工艺是一种重要的钢铁生产工艺,常用于中小型钢铁企业。
下面将为大家介绍转炉炼钢工艺的基本流程。
转炉炼钢是一种冶炼方法,它的主要原理是利用高温将生铁中的杂质氧化并脱除,使得铁中含碳量减少,从而生产出合格的钢铁产品。
该工艺主要分为以下几个步骤:首先,将生铁预处理。
生铁经过预处理之后,可以去除一部分含硫、磷等杂质。
预处理包括短暂的高温还原、碳酸钙煅烧等过程。
然后,将预处理后的生铁装入转炉内。
转炉是一个直立式圆形容器,内壁有耐火材料保护。
生铁装入转炉后,开始吹氧气。
吹氧气的目的是将生铁中的碳氧化为二氧化碳,使得含碳量降低。
接着,通过添加石灰石和硅石等脱硫剂。
这些脱硫剂被放入炉内,与融化的生铁反应,吸附并氧化掉生铁中的硫。
硫气随着炉排出,从而达到去除硫杂质的目的。
然后,再进行除磷。
除磷是利用石灰石、蛋白石等物质进行,它们可以与熔融的生铁反应,将磷杂质转化为更容易被吸附和排出的化合物。
通过这种方式,可以有效降低钢中的磷含量。
接下来,加入适量的合金元素。
根据需要生产的不同钢种,可以加入一些合金元素,如锰、铬、镍等。
这些合金元素的加入可以提升钢的性能和品质。
最后,进行温度调整和取样分析。
钢液需要在一定的温度范围内冷却,然后将一定的钢液放入真空状态下进行取样分析,以确定钢液中主要成分的含量。
根据取样分析结果,可以对转炉炼钢过程进行调整,以获得所需的合格产品。
总而言之,转炉炼钢工艺流程包括生铁预处理、吹氧、脱硫、除磷、加入合金元素、温度调整和取样分析等步骤。
通过这些步骤,可以将生铁中的杂质去除,并得到合格的钢铁产品。
这种工艺流程简单可行,因此被广泛应用于中小型钢铁企业。
转炉炼钢的五大工艺制度

转炉炼钢的五大工艺制度引言:转炉炼钢是一种常见的冶炼工艺,通过炼钢炉中高温条件下的氧气吹吹炼,将铁水和废钢等原料加工成高质量的钢材。
为了提高炼钢效率和质量,转炉炼钢采用了多种工艺制度。
本文将介绍转炉炼钢的五大工艺制度,包括氧枪喷吹工艺、钢包倾吊工艺、渣氧平衡工艺、碱性炉温保护工艺和连续浇铸工艺。
一、氧枪喷吹工艺氧枪喷吹工艺是转炉炼钢的核心工艺之一。
该工艺通过氧气喷吹,使铁水中的杂质和不良元素在高温条件下被氧化和吹出,从而提高钢材的纯度和质量。
在氧枪喷吹工艺中,需要控制氧气的流量和喷吹位置,以确保各种元素的氧化速率和炉温的控制。
二、钢包倾吊工艺钢包倾吊工艺是转炉炼钢的关键环节之一。
在钢包倾吊过程中,将经过炼钢炉炼制的钢水倾倒到钢包中,然后再将钢包倾倒到连铸坑中进行连铸。
倾吊时需要注意钢水的温度控制和倾吊速度,以确保钢水的质量和均匀性。
三、渣氧平衡工艺渣氧平衡工艺是转炉炼钢中用于控制渣铁比和氧气利用率的重要工艺。
通过合理控制渣铁比,可以提高转炉炼钢的冶炼效率和钢材质量。
同时,通过优化氧气利用率,可以减少能耗和炼钢成本。
渣氧平衡工艺需要根据具体炼钢情况进行调整,以达到最佳的效果。
四、碱性炉温保护工艺转炉炼钢中的高温条件对炉衬的腐蚀和寿命造成了严重挑战。
为了保护炉衬,常采用碱性炉温保护工艺。
该工艺通过添加适量的碱性物质,形成一层保护性的渣膜,减少炉衬的腐蚀和磨损。
碱性炉温保护工艺的成功应用,延长了转炉炼钢炉衬的使用寿命,降低了生产成本。
五、连续浇铸工艺连续浇铸工艺是转炉炼钢生产线的最后一个环节,也是实现高效率生产和优质钢材的关键。
在连续浇铸中,将炼制好的钢水连续地注入到均质的结晶器中,并通过提拉辊、冷却器等设备进行快速冷却和连续成形。
这种工艺既提高了钢材的质量,又提高了生产效率,逐渐成为转炉炼钢的主流工艺。
结论:转炉炼钢的五大工艺制度,即氧枪喷吹工艺、钢包倾吊工艺、渣氧平衡工艺、碱性炉温保护工艺和连续浇铸工艺,共同构成了转炉炼钢生产线的关键环节。
转炉炼钢 工艺流程

转炉炼钢工艺流程
转炉炼钢是一种重要的炼钢工艺,主要用于生产各种类型的钢材。
它的工艺流程包括预处理、炉内冶炼和炉外精炼等几个环节。
首先是预处理环节。
在转炉炼钢之前,需要对原料进行预处理,以确保炉内的冶炼过程能够顺利进行。
这包括原料的装料和计量,以及加入合适的石灰和矿渣等辅料来调节炉内的化学成分。
接下来是炉内冶炼。
转炉炼钢时,首先将预处理好的原料装入转炉中,并通过高温燃烧器将煤气喷入转炉底部,使炉内温度升高。
同时,通过转炉顶部的吹氧管向炉内喷入高压氧气,以促进原料的燃烧和脱碳反应。
在冶炼过程中,还会根据需要加入适量的合金元素,以调整炉内的化学成分和物理性能。
在炉内冶炼完成后,还需要进行炉外精炼。
精炼过程主要是通过在转炉炉顶加装精炼装置,如真空搅拌炉、中间接钢重复纯化和CAS-OB联合炉等,对炉内钢液进行精炼处理。
通过精炼,可以进一步控制钢液的成分和净化度,提高钢材的质量。
最后是钢液的出炉和连铸。
炼钢结束后,将炉内的钢液倒入包括倒钢车和连铸机在内的后续工艺设备中。
在连铸中,钢液被注入到结晶器中,在冷却过程中逐渐凝固成坯料。
然后坯料经过一系列的加工和处理,最终成为各种规格和形状的钢材。
总的来说,转炉炼钢的工艺流程较为复杂,但由于其高效、灵活和适应性强等优点,受到了广泛的应用。
通过精细控制每个
环节的参数和操作,可以获得高质量的钢材,满足不同行业和领域的需求。
转炉炼钢工艺介绍
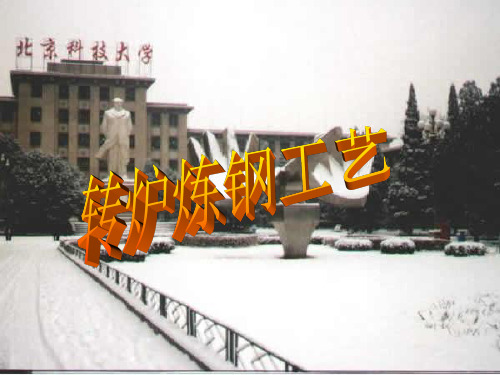
供氧制度
氧气流量大小(Nm3/h): 氧气流量大小 : 装入量,C、Mn、Si的含量,由物料平衡 计算得到,50-65Nm3/h。 氧压(Mpa) 喷头的喉口及马赫数一定,P大, 氧压 流量大,有一范围 0.8-1.1Mpa。 枪位, 枪位,由冲击深度决定,1/3-1/2。 供氧强度(Nm3/t.min) 决定冶炼时间,但太大, 供氧强度 喷溅可能性增大,一般3.0-4.0。
顶吹氧气转炉吹炼过程的操作制度
装料制度
装料是指装铁水及废钢。装入量是由炉容比 /t)决定的 装入量过大,喷溅增加, 决定的。 (V/T,m3/t)决定的。装入量过大,喷溅增加,冶炼时间 延长。装入量小生产能力下降,通常炉容比为0 05。 延长。装入量小生产能力下降,通常炉容比为0.7-1.05。 定量装入 优点:便于稳定操作,自动控制,适合大型 优点:便于稳定操作,自动控制, 转炉。一定的物料量。缺点:前期熔池深,后期熔池浅, 转炉。一定的物料量。缺点:前期熔池深,后期熔池浅, 氧枪不易控制。 氧枪不易控制。 定深装入 优点:主要是熔池深度不变,氧枪操作稳定 优点:主要是熔池深度不变, 缺点:装入量变化,辅料也变。 缺点:装入量变化,辅料也变。 分阶段定量装入 分阶段定量装入。 1-50炉,51-200 分阶段定量装入。 - 炉 - 炉以上, 炉,200炉以上,枪位每天要校正。交接班看枪位。 炉以上 枪位每天要校正。交接班看枪位。
废钢量的确定
转炉炼钢不需要外来热源; 转炉炼钢不需要外来热源; 热量来源于: 热量来源于: 铁水物理热及元素氧化化学热。 铁水物理热及元素氧化化学热。 铁水及废钢的合理配比须根据炉子的热平衡 计算确定。 计算确定。 硅的作用 优点:因发热量大,增大废钢加入量, 优点:因发热量大,增大废钢加入量,一般铁 水中Si增加0.1% 废钢比增大1% Si增加0.1%, 1%。 水中Si增加0.1%,废钢比增大1%。 缺点:增大渣量,侵蚀炉衬一般控制在0.4 0.4- 缺点:增大渣量,侵蚀炉衬一般控制在0.4- 0.6%以下。 0.6%以下。
转炉炼钢工艺流程

转炉炼钢工艺流程转炉炼钢是一种常用的钢铁生产工艺,它通过将废钢和其他金属材料作为原料,在转炉中进行加热、冶炼和精炼,最终得到所需的高质量钢材。
下面将介绍转炉炼钢的详细工艺流程。
第一步是准备原料。
转炉炼钢的原料主要包括废钢、废铁、废钢水、废铁水以及其他合金。
这些原料需要经过分类、清洗和处理,以确保其符合炼钢的要求,并且可以安全投入到转炉中。
第二步是预热转炉。
在进行炼钢之前,需要先将转炉加热至所需的温度。
这是为了确保炉料可以充分熔化,并且提供足够的温度和条件进行冶炼和精炼。
第三步是装料。
在转炉预热完成后,需要将准备好的原料投入到转炉中。
这时,要注意根据配比要求准确计量原料的比例,并控制好料层的高度,以确保冶炼过程的稳定性和效果。
第四步是炉料的熔化和脱氧。
一旦装料完成,加热火焰会加热转炉内的料层,使料层逐渐熔化。
在炉料熔化的过程中,加入适量的脱氧剂,主要是铝、硅等元素。
脱氧剂的作用是除去熔化金属中的氧气,并形成夹杂物,以提高钢材的质量。
第五步是冶炼和精炼。
炉料熔化之后,会形成炉渣和炼钢渣。
在冶炼的过程中,需要加入石灰等辅助材料,以调整炉渣的成分和性质,从而获得所需的炼钢渣。
同时,还要通过加热火焰的调整等方式,控制炉温和氧气的供应,以达到冶炼和精炼的最佳条件。
第六步是调整成分和温度。
在冶炼和精炼过程中,可能需要根据钢的规格要求,进行调整成分和温度。
这可以通过加入特定的合金元素、对炉渣进行再加工等方式实现。
第七步是出钢和排渣。
当钢液的成分和温度达到要求后,可以通过倾转转炉或者自动排渣装置,将钢水和炉渣分离。
钢水会被收集到相应的容器中,用于后续的铸造或加工。
而炉渣则可以作为矿渣或再利用。
第八步是后处理。
出钢后,可能需要对钢水进行加工和提纯,以进一步提高其质量。
这包括真空处理、脱氧处理、除杂、调整成分等工序。
最后一步是检测和质量控制。
转炉炼钢完成后,需要对钢材的成分、组织和性能进行检测和评价。
通过各种检测手段和设备,包括化学分析、力学测试等,将钢材的质量评估和控制到符合要求的范围之内。
转炉炼钢原理及工艺

转炉炼钢原理及工艺
转炉炼钢是通过加热合金材料,然后将其在氧气中抽出到转炉,形成一个旋转坩埚里,再使材料在转炉内不断熔化、混合、渣滓沉淀,达到钢的熔化和净化,最后冷却固化,即可获得均匀的高质量的钢的过程。
转炉炼钢的工艺路径主要包括:原料进炉、熔炼、净化、合金添加、出炉等步骤。
1、原料进炉:将碳钢和合金料装入转炉,加热至溶化温度,开始熔融。
2、熔炼:转炉内熔融的温度受多种因素的影响,如加料量、加料温度、炉气系统的平衡性、熔炼时间等。
3、净化:即清洁熔化渣滓,消除杂质,把金属液中的杂质置于渣滓中,让金属液纯度升高。
4、合金添加:将净化后的钢液入合金添加系统,加入合金钢料,使钢液按照要求的成分,营造钢种具有相应的技术性能。
5、出炉:金属液改变形态,冷却成指定的形状和尺寸,经过纯化后形成高质量钢。
转炉炼钢工艺流程

转炉炼钢工艺流程
炼钢是现代钢铁行业中至关重要的环节之一,而转炉炼钢工艺是其中一种主要
的炼钢方法。
转炉炼钢是利用转炉进行钢水冶炼的工艺过程,其主要特点是生产能力大、生产成本低、生产效率高等优点,因而在钢铁行业中占有重要地位。
在转炉炼钢工艺流程中,首先需要准备炼钢原料。
炼钢原料一般包括废钢、生铁、废钢等,各种原料按一定比例经过预处理后,被送入转炉进行炼钢。
转炉通常由熔炼室和吹氧室组成,熔炼室用于炉内的熔炼过程,吹氧室则用于吹送氧气进入转炉,与炉内的金属物质进行反应。
在转炉炼钢的过程中,主要分为三个阶段:氧吹阶段、脱碳阶段和保温混炼阶段。
首先是氧吹阶段,主要是将转炉内的废钢等原料加热至熔化状态,同时通过吹送氧气,将废钢中的杂质氧化,从而提高钢水的纯度。
接着是脱碳阶段,通过加入适量的脱碳剂,将炼钢中的碳含量控制在一定范围内,以满足钢材的力学性能要求。
最后是保温混炼阶段,主要是控制转炉内的温度和成分均匀性,确保生产出合格的钢水。
转炉炼钢工艺流程的优点在于生产效率高、产品质量稳定、生产能力大等,被
广泛应用于钢铁行业的生产中。
然而,转炉炼钢过程中也存在一定的问题与挑战,例如转炉炼钢比较耗能,废气排放量较大等环境问题,因此随着环保意识的提高,炼钢行业也在不断探索新的炼钢技术与工艺。
总的来说,转炉炼钢工艺是钢铁生产中一种重要的炼钢方法,其工艺流程复杂,涉及多方面的技术知识与操作技巧。
随着科技的进步和环保意识的提高,转炉炼钢工艺也在不断创新与改进,以满足不断提高的生产需求和环保要求。
转炉炼钢工艺流程

转炉炼钢工艺流程这种炼钢法使用的氧化剂是氧气。
把空气鼓入熔融的生铁里,使杂质硅、锰等氧化。
在氧化的过程中放出大量的热量(含1%的硅可使生铁的温度升高200摄氏度),可使炉内达到足够高的温度。
因此转炉炼钢不需要另外使用燃料。
转炉炼钢是在转炉里进行。
转炉的外形就像个梨,内壁有耐火砖,炉侧有许多小孔(风口),压缩空气从这些小孔里吹炉内,又叫做侧吹转炉。
开始时,转炉处于水平,向内注入1300摄氏度的液态生铁,并加入一定量的生石灰,然后鼓入空气并转动转炉使它直立起来。
这时液态生铁表面剧烈的反应,使铁、硅、锰氧化(FeO,SiO2 , MnO,) 生成炉渣,利用熔化的钢铁和炉渣的对流作用,使反应遍及整个炉内。
几分钟后,当钢液中只剩下少量的硅与锰时,碳开始氧化,生成一氧化碳(放热)使钢液剧烈沸腾。
炉口由于溢出的一氧化炭的燃烧而出现巨大的火焰。
最后,磷也发生氧化并进一步生成磷酸亚铁。
磷酸亚铁再跟生石灰反应生成稳定的磷酸钙和硫化钙,一起成为炉渣。
当磷与硫逐渐减少,火焰退落,炉口出现四氧化三铁的褐色蒸汽时,表明钢已炼成。
这时应立即停止鼓风,并把转炉转到水平位置,把钢水倾至钢水包里,再加脱氧剂进行脱氧。
整个过程只需15分钟左右。
如果空气是从炉低吹入,那就是低吹转炉。
随着制氧技术的发展,现在已普遍使用氧气顶吹转炉(也有侧吹转炉)。
这种转炉吹如的是高压工业纯氧,反应更为剧烈,能进一步提高生产效率和钢的质量。
转炉一炉钢的基本冶炼过程。
顶吹转炉冶炼一炉钢的操作过程主要由以下六步组成:(1)上炉出钢、倒渣,检查炉衬和倾动设备等并进行必要的修补和修理;(2)倾炉,加废钢、兑铁水,摇正炉体(至垂直位置);(3)降枪开吹,同时加入第一批渣料(起初炉内噪声较大,从炉口冒出赤色烟雾,随后喷出暗红的火焰;3~5min后硅锰氧接近结束,碳氧反应逐渐激烈,炉口的火焰变大,亮度随之提高;同时渣料熔化,噪声减弱);(4)3~5min后加入第二批渣料继续吹炼(随吹炼进行钢中碳逐渐降低,约12min 后火焰微弱,停吹);(5)倒炉,测温、取样,并确定补吹时间或出钢;(6)出钢,同时(将计算好的合金加入钢包中)进行脱氧合金化。
转炉炼钢工艺流程介绍

转炉炼钢工艺流程介绍
转炉炼钢是一种常见的钢铁生产工艺,下面是其工艺流程的介绍:
1. 铁水预处理:首先,将铁水经过除渣工序,去除其中的杂质和非金属物质,提高炉内的纯净度和质量。
2. 转炉兑炉:之后,将预处理后的铁水加入转炉中,同时加入适量的废钢、废铁等回收材料。
这些回收材料能够提供多种元素和合金,有助于调整并优化转炉内的化学成分。
3. 吹氧气:然后,通过吹氧装置向转炉中喷吹氧气。
氧气与铁水中的杂质反应生成氧化物,如氧化碳、氧化硅等,这些氧化物随废气排出转炉。
4. 炼钢反应:转炉内的铁水经过吹氧反应后,温度升高,同时炉内的化学反应也进行着。
在高温和高氧气作用下,铁水中的碳、硅等元素会逐渐氧化和燃烧,生成气体和渣。
5. 加入合金:根据需要,再加入一定量的合金,如镍、铬、锰等。
合金的加入可以调整钢的成分和性能,改善钢的质量。
6. 钢包炉脱氧:在转炉炼钢过程中,钢中可能还含有一定量的氧气。
为了降低钢中的氧含量,通常还需将钢浇入预先加入了脱氧剂的钢包炉中,并进行搅拌。
脱氧剂能与钢中的氧气反应生成气体,进一步减少钢中的氧含量。
7. 出钢和连铸:最后,将炼制好的钢浇入连铸机中,进行连续铸造,制成钢坯。
这些钢坯经过后续的轧制和加工,可制成各种形状和规格的钢材。
值得注意的是,转炉炼钢是一个复杂的过程,涉及到许多工艺参数和控制指标,操作人员需要根据实际情况进行调整和控制,以达到所需的钢材质量。
转炉炼钢原理及工艺介绍
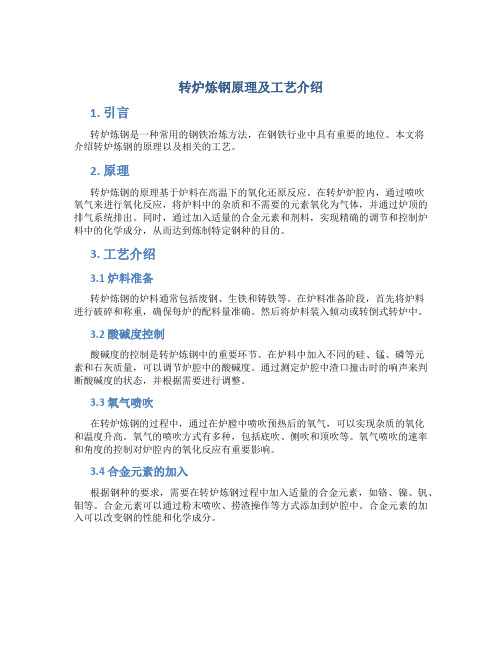
转炉炼钢原理及工艺介绍1. 引言转炉炼钢是一种常用的钢铁冶炼方法,在钢铁行业中具有重要的地位。
本文将介绍转炉炼钢的原理以及相关的工艺。
2. 原理转炉炼钢的原理基于炉料在高温下的氧化还原反应。
在转炉炉腔内,通过喷吹氧气来进行氧化反应,将炉料中的杂质和不需要的元素氧化为气体,并通过炉顶的排气系统排出。
同时,通过加入适量的合金元素和剂料,实现精确的调节和控制炉料中的化学成分,从而达到炼制特定钢种的目的。
3. 工艺介绍3.1 炉料准备转炉炼钢的炉料通常包括废钢、生铁和铸铁等。
在炉料准备阶段,首先将炉料进行破碎和称重,确保每炉的配料量准确。
然后将炉料装入倾动或转倒式转炉中。
3.2 酸碱度控制酸碱度的控制是转炉炼钢中的重要环节。
在炉料中加入不同的硅、锰、磷等元素和石灰质量,可以调节炉腔中的酸碱度。
通过测定炉腔中渣口撞击时的响声来判断酸碱度的状态,并根据需要进行调整。
3.3 氧气喷吹在转炉炼钢的过程中,通过在炉膛中喷吹预热后的氧气,可以实现杂质的氧化和温度升高。
氧气的喷吹方式有多种,包括底吹、侧吹和顶吹等。
氧气喷吹的速率和角度的控制对炉腔内的氧化反应有重要影响。
3.4 合金元素的加入根据钢种的要求,需要在转炉炼钢过程中加入适量的合金元素,如铬、镍、钒、钼等。
合金元素可以通过粉末喷吹、捞渣操作等方式添加到炉腔中。
合金元素的加入可以改变钢的性能和化学成分。
3.5 钢渣处理在转炉炼钢过程中,钢渣是产生的副产物。
钢渣中含有大量的氧化物和杂质,需要进行适当的处理。
一般采用钢渣保温、捞渣、保护渣、中性渣等措施来处理钢渣,以确保钢渣中的氧化元素被充分还原并排出炉外。
3.6 出钢经过一系列的氧化还原反应和调度控制,转炉中的炼钢过程逐渐接近尾声。
当出钢温度达到要求后,打开炉底的出钢口,将液态钢水流入连铸机进行继续加工。
4. 总结转炉炼钢是一种重要的钢铁冶炼方法,其原理是基于氧化和还原反应。
通过适当的酸碱度控制、氧气喷吹和合金元素的加入,可以实现炼制特定钢种的目的。
转炉炼钢工艺

转炉炼钢工艺引言转炉炼钢工艺是一种常用的钢铁生产工艺,其原理是使用巨大的转炉进行冶炼,通过高温燃烧将生铁中的杂质熔化分离,得到高品质的钢铁产品。
本文将详细介绍转炉炼钢工艺的过程、设备和优势。
工艺过程转炉炼钢工艺主要由以下几个步骤组成:1.加炉:在转炉中加入一定数量的生铁和废钢,根据不同的钢种和质量要求控制添加比例。
2.预热:通过燃料燃烧加热炉体,将炉体温度升至一定的范围,为后续冶炼做准备。
3.唤氧:将预先加入的氧气注入转炉中,氧气与炉内的碳、硫等元素发生反应,使其氧化生成气体冒出炉口。
4.碱性脱硫:在钢水中加入一定量的含碱性物质的脱硫剂,使浸渍在钢水中的硫元素氧化为气体并脱出。
5.酸性脱磷:在钢水中加入一定量的含酸性物质的脱磷剂,使浸渍在钢水中的磷元素氧化为气体并脱出。
6.合金化:根据需要,在钢水中加入一定量的合金元素,如铬、锰等,以调节钢的性能。
7.保温装钢:将炉中冶炼好的钢水倒入铸钢坑、铸型等装置中进行冷却和凝固。
设备转炉炼钢工艺需要使用专用的转炉设备,该设备主要由以下几个组成部分:1.转炉本体:转炉本体是整个工艺最关键的部分,它承载着冶炼过程的全部任务。
转炉一般采用大型圆筒形设计,底部有一定数量的喷孔以供氧气进入。
2.转炉支承:转炉支承是将转炉本体固定在地基上的部分,以保证炉体的稳定运行。
3.强制鼓风系统:由鼓风机、风箱等组成,用于向转炉中供给氧气,促进燃烧和炉内反应的进行。
4.喷吹系统:包括氧枪、煤粉喷吹器等,用于将氧气、燃料喷入转炉中,以调节炉内的温度和氧气含量。
5.出渣系统:用于将炉内产生的渣料排出转炉,保持炉内清洁。
工艺优势转炉炼钢工艺相比于其他炼钢工艺具有以下优势:1.生产能力强大:转炉炼钢工艺灵活可调,产能大。
转炉设备可以进行批量生产,快速完成大批量的钢水冶炼,满足市场需求。
2.冶炼效率高:转炉炼钢工艺采用高温燃烧和强制鼓风系统,能够快速将生铁中的杂质熔化脱除,同时还可以进行合金化调节,提高钢的质量和性能。
转炉炼钢的生产流程

转炉炼钢的生产流程转炉炼钢是一种重要的冶金工艺,被广泛应用于钢铁行业。
它通过加热和加氧化剂引入熔融金属中来减少金属的碳含量,从而得到高品质的钢材。
本文将介绍转炉炼钢的生产流程,包括前处理、炉区处理、后处理等环节,总共约2000字。
一、前处理1. 取样转炉炼钢首先需要取样,用于对生铁进行分析。
根据分析结果,生产人员可以得出目标钢品的成分和质量等要求,进而调整转炉冶炼过程。
2. 预热生铁虽然已经经过高温处理,但与转炉的温度相差较大,如果直接加入炉中容易导致转炉窑身破裂。
因此需要对生铁进行预热,以逐渐提高温度,减缓温度差,从而防止炉身爆裂。
3. 拉钢拉钢是指将电炉或其他熔炼炉中的钢水,利用转炉进行进一步脱碳脱硫,调整成分等处理的一种前处理技术。
在拉钢时,还会掺入一些铁合金、废钢和矿渣等材料,以改变金属的成分和质量。
二、炉区处理1. 装料装料是指将经过预处理的生铁/钢水和其他掺杂物料等投入到转炉中进行炉区处理的一种操作。
转炉一般采用叶片式料斗,使得物料能够均匀地分布在炉身中。
2. 加料加料在转炉炼钢中也是一种常规操作,用于控制钢水的碳含量和改变金属的成分。
一般的加料包括生铁、废钢、蒸馏铁等,它们都会影响炉内的氧化还原反应和金属的物理性能。
3. 加热加热是指将转炉炉内的物料进行预热和加热,以达到合适的操作温度。
炉胆内的加热方式主要有三种:氧燃烧加热、燃气加热和电炉加热。
氧燃烧加热的方式最为常见,可以在短时间内提高炉内的温度。
4. 氧吹氧吹是指向转炉炉内喷氧并形成氧气流,以使炉内物料氧化、燃烧和熔化的过程。
氧吹的目的是通过加入氧气来移除金属中的不想要的杂质(如碳、硅、锰等)。
氧吹还可以逐渐提高炉内物料的温度和浓度,并促进金属内部组织的再分布。
5. 碱度/酸度控制炉区处理过程中,炉内物料的碱度或酸度也需要得到控制。
通过氧化反应,转炉炉内会产生一定量的氧化钙、氧化铁等碱性物质。
这些碱性物质需要与掺入的酸性物料(如蒸馏铁、锰矿等)进行反应,以控制炉内物料的酸碱程度。
转炉炼钢原理及工艺介绍

转炉炼钢原理及工艺介绍引言转炉炼钢是一种常用的钢铁生产工艺,具有高效、灵活、环保等特点。
本文将介绍转炉炼钢的原理及工艺流程。
一、转炉炼钢原理转炉炼钢是通过在高温下将生铁与废钢等原料进行反应,去除杂质,调整合金成分来生产钢铁。
其原理基于以下几个重要的化学反应步骤:1.氧化反应:在高温下,将生铁中的杂质氧化为气体或溶于渣中。
主要的氧化反应有:Fe+C+O2=FeO+CO、Mn+C+O2=MnO+CO等。
2.还原反应:在氧化反应的基础上,通过还原剂(如脱氧剂)来还原产生的氧化物。
主要还原反应有:FeO+CO=Fe+CO2、MnO+CO=Mn+CO2等。
3.合金化反应:在还原反应的基础上,通过加入适量合金元素来调整合金成分。
合金化反应可以通过添加合金块、废钢等方式实现。
通过以上化学反应的组合,转炉炼钢可以控制合金成分、去除杂质、调整温度等,从而得到符合要求的钢铁产品。
二、转炉炼钢工艺介绍转炉炼钢的工艺可以分为以下几个主要步骤:1.预处理:生铁、废钢等原料经过破碎、除尘等处理后,进入转炉炉前料斗。
2.加料:原料从炉前料斗通过螺旋输送机被输送至转炉炉缸中。
3.预热:将炉缸中的原料进行预热,以提高反应效果。
4.吹炼:将炉底引入的高纯氧吹入炉缸中,通过氧化反应和还原反应去除杂质、调整合金成分。
5.加料:在吹炼过程中,适量添加合金块、废钢等调整合金成分。
6.测温:通过测温仪器监测和调节炉内温度。
7.出渣:通过倾炉装置将产生的渣浆从转炉中排出。
8.抽炉:将炉内得到的钢液通过倾炉装置倾出,并进行钢液处理(如脱氧、出气、精炼等)9.浇铸:将经过处理的钢液进行浇铸,得到需要的钢铁产品。
三、转炉炼钢的优势转炉炼钢工艺具有以下几个优势:1.高效:转炉炼钢的操作灵活,能够快速调整合金成分和生产规格,生产效率高。
2.资源利用:转炉炼钢可以利用废钢等再生资源,减少资源浪费。
3.环保:转炉炼钢排放的烟尘、废气等污染物可以通过环保设施进行处理,达到环保要求。
转炉炼钢工艺(主要是热平衡计算)
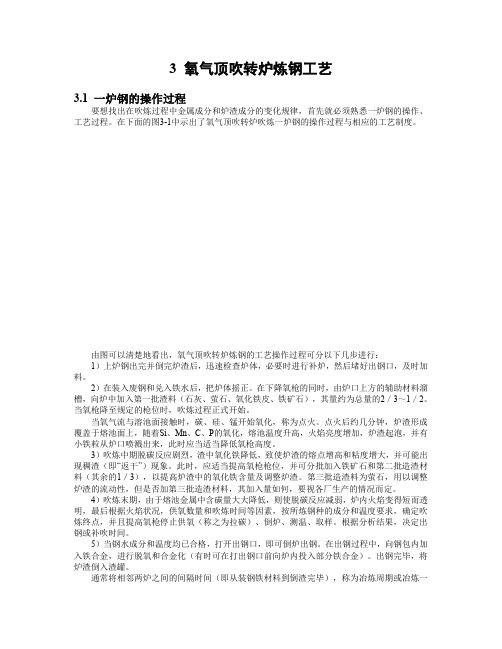
3 氧气顶吹转炉炼钢工艺3.1 一炉钢的操作过程要想找出在吹炼过程中金属成分和炉渣成分的变化规律,首先就必须熟悉一炉钢的操作、工艺过程。
在下面的图3-1中示出了氧气顶吹转炉吹炼一炉钢的操作过程与相应的工艺制度。
由图可以清楚地看出,氧气顶吹转炉炼钢的工艺操作过程可分以下几步进行:1)上炉钢出完并倒完炉渣后,迅速检查炉体,必要时进行补炉,然后堵好出钢口,及时加料。
2)在装入废钢和兑入铁水后,把炉体摇正。
在下降氧枪的同时,由炉口上方的辅助材料溜槽,向炉中加入第一批渣料(石灰、萤石、氧化铁皮、铁矿石),其量约为总量的2/3~1/2。
当氧枪降至规定的枪位时,吹炼过程正式开始。
当氧气流与溶池面接触时,碳、硅、锰开始氧化,称为点火。
点火后约几分钟,炉渣形成覆盖于熔池面上,随着Si、Mn、C、P的氧化,熔池温度升高,火焰亮度增加,炉渣起泡,并有小铁粒从炉口喷溅出来,此时应当适当降低氧枪高度。
3)吹炼中期脱碳反应剧烈,渣中氧化铁降低,致使炉渣的熔点增高和粘度增大,并可能出现稠渣(即“返干”)现象。
此时,应适当提高氧枪枪位,并可分批加入铁矿石和第二批造渣材料(其余的1/3),以提高炉渣中的氧化铁含量及调整炉渣。
第三批造渣料为萤石,用以调整炉渣的流动性,但是否加第三批造渣材料,其加入量如何,要视各厂生产的情况而定。
4)吹炼末期,由于熔池金属中含碳量大大降低,则使脱碳反应减弱,炉内火焰变得短而透明,最后根据火焰状况,供氧数量和吹炼时间等因素,按所炼钢种的成分和温度要求,确定吹炼终点,并且提高氧枪停止供氧(称之为拉碳)、倒炉、测温、取样。
根据分析结果,决定出钢或补吹时间。
5)当钢水成分和温度均已合格,打开出钢口,即可倒炉出钢。
在出钢过程中,向钢包内加入铁合金,进行脱氧和合金化(有时可在打出钢口前向炉内投入部分铁合金)。
出钢完毕,将炉渣倒入渣罐。
通常将相邻两炉之间的间隔时间(即从装钢铁材料到倒渣完毕),称为冶炼周期或冶炼一炉钢的时间。
- 1、下载文档前请自行甄别文档内容的完整性,平台不提供额外的编辑、内容补充、找答案等附加服务。
- 2、"仅部分预览"的文档,不可在线预览部分如存在完整性等问题,可反馈申请退款(可完整预览的文档不适用该条件!)。
- 3、如文档侵犯您的权益,请联系客服反馈,我们会尽快为您处理(人工客服工作时间:9:00-18:30)。
布袋式除尘器
反吹管传动
反吹风机
滤袋 尘粒出口
5.3 转炉炼钢工艺制度
冶炼过程概述
从装料到出钢,倒渣, 转炉一炉钢的冶炼过程 包括装料、吹炼、脱氧 出钢、溅渣护炉和倒渣 几个阶段。
活动烟罩
操作简单,运行安全。处 理烟气量大(是未燃法的 4~6倍),系统设备庞大 基建投资高;颗粒细小, 除尘效率低。
α <1( α =0.08 )
以 CO(转炉煤气)为主
以 Fe O 为主,颗粒较大
汽化冷却
活动烟罩和炉口压力调节法或 氮幕法(OG法)
烟气量(α 很小),设备体积小, 投资省(仅为燃烧法的 50%~ 60%);且可回收煤气;颗粒 较大,除尘效率高;烟气成分 以 CO为主,系统运行安全性 差,易发生爆炸事故。故要求 系统的密封性要好。
散状料
地位料仓
皮带运输机(皮带走廊)
斗式提升机
皮带运输等
高位料仓 电磁振动给料器 自动称量漏斗 汇总漏斗 溜槽 转炉炉口
氧气顶吹转炉设备
➢ 废气处理系统 ✓ 转炉烟气净化及回收处理的意义 ——防止环境污染、回收能源。 ✓ 烟气的处理方式有燃烧法与未燃法两种 ✓ 烟尘的净化方式也有两种,即湿式净化与干式净化。 o 目前绝大多数顶吹转炉的烟气是采用未燃法(氮幕法)、湿
第五章 转炉炼钢工艺
5.1 现代转炉炼钢发展趋势 5.2 氧气转炉炼钢及设备特点 5.3 转炉炼钢工艺制度 5.4 复吹转炉炼钢工艺 5.5 转炉的其他冶炼工艺介绍 5.6 转炉典型钢种的冶炼及其质量 5.7 转炉炼钢过程自动控制 5.8 转炉溅渣护炉技术
5.1 现代转炉炼钢发展趋势
自 供 热 转 炉 的 发 展 演 变 过 程
趋势
采用该法除尘且回收煤气
90度弯头脱水器 上部安全阀
放散烟囱
汽化冷却烟道
上烟罩 上烟罩 烟裙
一级文氏管 丝网除雾气
二级文氏管
下部安全阀
测定孔
流
V形水封
量
风 旁 三 水封逆止阀
计
机通通
阀阀
煤气柜
OG系统的流程示意图
OG系统的流程:
烟气→烟罩→汽化冷却烟道→一级文氏管→90度弯头脱水器→二级文氏管 → 90度弯头脱水器→丝网脱水器→
◆在吹炼末期要降枪,主要目的是熔池钢水成分和温度均匀, 加强熔池搅拌,稳定火焰,便于判断终点,同时使降低渣中 Fe含量,减少铁损,达到溅渣的要求。
回收→三通阀→水封逆止阀→V形水封→煤气柜 风机
放散→旁通阀→放散烟囱
LT法净化、回收系统工艺流程
LT法净化、回收系统工艺流程
未燃烟气(800~1000 ℃ )→活动罩裙→冷却烟道(或余热锅炉)→蒸发冷却器
(蒸发冷却塔)→煤气冷却(150~200℃) 、干燥(水雾蒸发)、除粗尘→
干粗尘
回收→三通阀→冷却塔→煤气柜
电除尘器(除细尘)→风机(I D)→切换站
(73 ℃ )
干细尘
放散→放散烟囱(氮气引射装置)
热压块设备(压块)→转炉
静电除尘器的主要特点:
• 除尘效率高(净化效率高),可达99.9%,而且稳 定,不受烟气量波动的影响,最适宜捕集小于1μm 的烟尘;
• 处理烟气量大,阻力损失小(一般在30毫米水柱以 下),可用于高温烟气;
炉顶料仓
振动给料器 电子称
带式运输机
密封料仓
传动机构 实 心溜 轴槽
电动机
支架
汽包
氧
烟
枪
道
风
文氏管
机
脱水器
洗 涤 塔
沉淀池
渣吸 罐滤
池
转 炉
不 回 收 时 放 空
回收煤气
进入煤气柜
水封逆止阀
送往高炉利用
氧气顶吹转炉及其附属设备示意图
➢转炉炉体结构及倾动机构
炉帽(锥形):
水冷炉口(顶部)
出钢口(炉帽与炉身交界处)
• 维护费用较低,使用寿命长。
• 但一次性投资高(设备投资费用大),设备庞大, 占地面积大。
• 选用时要考虑设置增湿塔,降低烟尘电阻率后再进 入静电除尘器,才能发挥其特性(电除尘器适宜烟 尘电阻率为108~1011Ω·m )。
布袋式除尘器工作原理
布袋式除尘器是干式除
尘设备 ,由许多单体布
袋组成。工作原理如下:
炉壳
档渣板(环形伞状)
炉身(圆筒形)
筒球型
炉底(球形) 锥球型
炉体金属结构 托圈
截锥型
耳轴
转炉
轴承座
工作层
炉衬——炉膛内腔 填充层
永久层
倾动机构 ——电动机、减速装置(减速机、制动装置等)
氧气顶吹转炉设备
✓ 散状料供应系统主要设备组成及其作用
❖主要设备有地面料仓、提升运输设备、高位料仓、 称量和加料设备。生产流程如下:
由传统供热向外加燃料联合供热转炉的发展演变过程
转炉炼钢功能的发展和完善
5.2 氧气顶吹转炉炼钢及设备特点
氧气转炉炼钢的特点 • 生产率高、钢中气体含量少,钢质量好; • 可炼品种多、原料适应性强; • 成本低、投资少、建厂快; • 生产较均衡,利于与连铸配合,利于实现生产的自动控制; 氧气顶吹转炉设备 ➢ 炉体结构及倾动机构 ➢ 供氧系统 ➢ 供料系统 ➢ 废气处理系统
一炉钢的吹氧时间通
常为12-18min,冶炼周 期为30min左右。
冶炼过程概述
上炉钢出完钢后,倒净炉渣,堵出钢口,兑铁水和加废 钢,降枪供氧,开始吹炼。
在送氧开吹的同时,加入第一批渣料,加入量相当于全 炉总渣量的三分之二,开吹4-6分钟后,第一批渣料化好, 再加入第二批渣料。如果炉内化渣不好,需加入第三批 萤石渣料。
吹炼过程中的供氧强度: 小型转炉为2.5-4.5m3/(t·min); 120t以上的转炉一般为2.8-3.6m3/(t·min)。
冶炼过程概述
◆开吹时氧枪枪位采用高枪位,目前是为了早化渣,多去磷, 保护炉衬;
◆在吹炼过程中适当降低枪位的保证炉渣不“返干”,不喷溅, 快速脱碳与脱硫,熔池均匀升温为原则;
法净化回收系统,称OG系统; o 有的也采用未燃、干式净化回收系统,又称LT系统。 o 烟气除尘设备——洗涤除尘器(文氏管)、静电除尘器、布
袋除尘器等。
燃烧法与未燃法除尘特性比较
项目
燃烧法
未燃法
空气燃烧系数 烟气成分 烟尘成分 冷却方式
控制α的方法
优缺点
α>1(α=1.2 或3~4 )
以 CO2、N2 为主 以 Fe2O3 为主,颗粒细小 废热锅炉法( α=1.2 )空 气冷却法( α=3~4 )