PLC液体混合实验报告
5 多种液体混合控制实训报告

多种液体混合控制实训一实训目的1. 掌握多种液体混合PLC控制的基本原理。
2. 掌握置位、复位指令的使用方法。
二实训器材1. 三菱可编程控制器实训装置1台2. 多种液体混合控制实训模块1个3. 计算机1台4. 编程电缆1根5. 连接导线若干三实训要求多种液体混合控制实训模块中C0、C1、C2、C3为液位传感器,分别代表液位C、液位B、液位A和液位底,由PLC控制V0、V1、V2三个液体进口阀门的开启,使A、B、C三种液体达到工艺规定的液面。
随后PLC控制加热器H和搅拌电机M的工作,当到达希望温度(C4代表温度传感器)时,PLC开启出料阀,从而完成一个周期的搅拌工作。
多种液体混合控制演示装置利用LED指示灯模拟各点的工作状态,电磁阀的开闭状态、传感器信号的有和无用LED指示灯的亮和灭状态来表示,搅拌电机工作用LED闪烁来表示,液面的上升和下降过程用定时器来模拟。
多种液体混合控制实训的控制要求:1. 初始状态各阀门关闭;2. 按下启动按钮,液位为底部,阀门V0打开,同时定时器开始计时,开始注入液体A;3. 2S后到达液位A,控制阀V0关闭,同时阀V1打开,注入液体B;4. 3S后达到液位B,控制V1关闭,同时阀V2,注入液体C;5. 3S后达到液面C,加热器和搅拌电机开始工作;6. 3S后温度达到设定值,搅拌和加热结束,阀V3打开,液面下降,C0、C1、C2、C3依次熄灭;7. 7S后液体放空,阀V3关闭,一轮结束,又从控制要求2开始循环。
8. 按下停止按钮,所有操作立即停止,所有指示灯全部熄灭。
四实训组成员名单组长:徐玄;实训组成员:胡建、费子威、王晓攀、郑婷婷;实训操作员:徐玄、郑婷婷;实训监护员:胡建;现象与结果记录员:费子威、王晓攀。
五实训步骤及注意事项1. 理解实训的原理及控制要求,列出I/O分配表。
2. 根据分配表编写实训程序。
3. 将编程电缆一端与PLC的编程接口相连,另一端与计算机串口连接。
液体混合控制实验报告
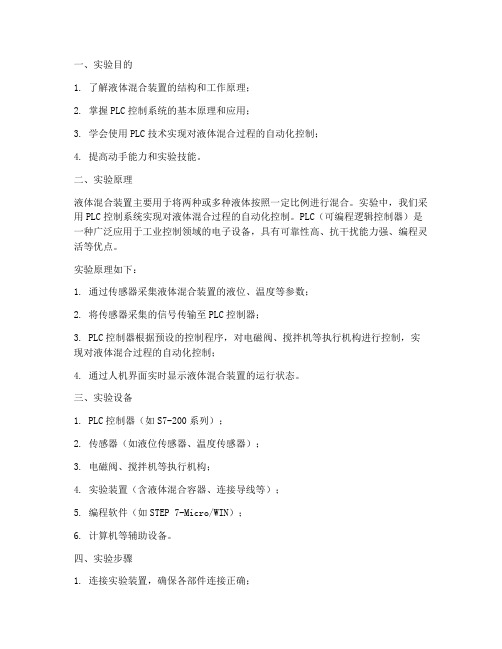
一、实验目的1. 了解液体混合装置的结构和工作原理;2. 掌握PLC控制系统的基本原理和应用;3. 学会使用PLC技术实现对液体混合过程的自动化控制;4. 提高动手能力和实验技能。
二、实验原理液体混合装置主要用于将两种或多种液体按照一定比例进行混合。
实验中,我们采用PLC控制系统实现对液体混合过程的自动化控制。
PLC(可编程逻辑控制器)是一种广泛应用于工业控制领域的电子设备,具有可靠性高、抗干扰能力强、编程灵活等优点。
实验原理如下:1. 通过传感器采集液体混合装置的液位、温度等参数;2. 将传感器采集的信号传输至PLC控制器;3. PLC控制器根据预设的控制程序,对电磁阀、搅拌机等执行机构进行控制,实现对液体混合过程的自动化控制;4. 通过人机界面实时显示液体混合装置的运行状态。
三、实验设备1. PLC控制器(如S7-200系列);2. 传感器(如液位传感器、温度传感器);3. 电磁阀、搅拌机等执行机构;4. 实验装置(含液体混合容器、连接导线等);5. 编程软件(如STEP 7-Micro/WIN);6. 计算机等辅助设备。
四、实验步骤1. 连接实验装置,确保各部件连接正确;2. 在PLC控制器中编写控制程序,实现对液体混合过程的自动化控制;3. 通过编程软件将控制程序下载至PLC控制器;4. 设置PLC控制器的运行参数,如液位、温度等;5. 启动实验装置,观察液体混合过程;6. 调整控制参数,优化液体混合效果;7. 记录实验数据,分析实验结果。
五、实验结果与分析1. 液体混合装置的液位传感器能够准确采集液位信息,并将信号传输至PLC控制器;2. PLC控制器根据预设的控制程序,对电磁阀、搅拌机等执行机构进行控制,实现了液体混合过程的自动化控制;3. 实验过程中,通过调整控制参数,优化了液体混合效果;4. 实验结果表明,PLC控制系统在液体混合过程中具有较好的控制性能。
六、实验总结1. 通过本次实验,我们了解了液体混合装置的结构和工作原理;2. 掌握了PLC控制系统的基本原理和应用;3. 学会了使用PLC技术实现对液体混合过程的自动化控制;4. 提高了动手能力和实验技能。
PLC课程设计报告液体混合装置控制的模拟(一)

目录一:绪论 (2)二:电气原理设计 (5)2.1 工作过程 (5)2.2 电器元器件明细表 (5)2.3 PLC 的I/O地址表 (6)2.4 PLC接线图 (7)三:PLC程序设计 (8)3.1 总体程序框图 (8)3.2 系统功能图 (8)3.3 梯形图 (10)3.3.1 OB1 (10)3.3.2 OB100 (10)3.3.3 FC1 (10)3.3.4 FC2 (12)3.3.5 FC3 (14)四:操作与调试 (18)4.1 程序检验 (18)4.2 信号模拟 (18)4.3 按要求进行模拟运行 (18)4.4 调试实物图 (19)五:小结........................................................................... 错误!未定义书签。
六:参考文献 (21)一:绪论PLC的产生1.继-接控制回顾由学生回答继电器(接触器)的结构、原理、画出三相异步电机启-停的主电路图、控制电路图由学生归纳出继-接控制的不足,从而引出“PLC的产生”2.PLC的产生68年美国通用汽车公司(GM)招标要求:(1)软连接代替硬接线(2)维护方便(3)可靠性高于继电器控制柜(4)体积小于继电器控制柜(5)成本低于继电器控制柜(6)有数据通讯功能(7)输入115V (8)可在恶劣环境下工作(9)扩展时,原系统变更要少(10)用户程序存储容量可扩展到4K核心思想:·用程序代替硬接线·输入/输出电平可与外部装置直接相联·结构易于扩展这是PLC的雏形。
69年美国DEC公司研制出世界上第一台PLC(PDP-14),并在GM公司汽车生产线上应用成功PLC的诞生:·1969年,美国研制出世界第一台PDP-14·1971年,日本研制出第一台DCS-8·1973年,德国研制出第一台PLC·1974年,中国研制出第一台PLC二、PLC的特点、现状与发展(一)特点(1)体积小(2)可靠性高(3)柔性好,可在线更改程序(4)对环境条件无要求(5)价格低廉……具备招标要求的所有功能(二)现状80%以上的行业,80%以上的设备均可使用PLC(三)发展发展史:第一代:1969年~1972年,代表产品有·美国DEC公司的PDP-14/L·日本立石电机公司的SCY-022·日本北辰电机公司的HOSC-20第二代:1973年~1975年,代表产品有·美国GE公司的LOGISTROT·德国SIEMENS公司的SIMATIC S3、S4系列·日本富士电机公司的SC系列第三代:1976~1983年,代表产品有·美国GOULD公司的M84、484、584、684、884 ·德国SIEMENS公司的SIMATIC S5系列·日本三菱公司的MELPLAC-50、550第四代:1983年~现在,代表产品有·美国GOULD公司的A5900·德国西门子公司的S7系列发展方向:·产品规模向两极分化·处理模拟量·追求高可靠性·通讯接口和智能模块·系统操作站配高分辨率的监视器·追求软、硬件标准化三、PLC的分类·按结构分:·整体型·组合型·按I/O点数及内存容量分:·超小型:小于64点,256Byet~1KB·小型:65~128点,1~3。
PLC原理与应用》液体混合实验
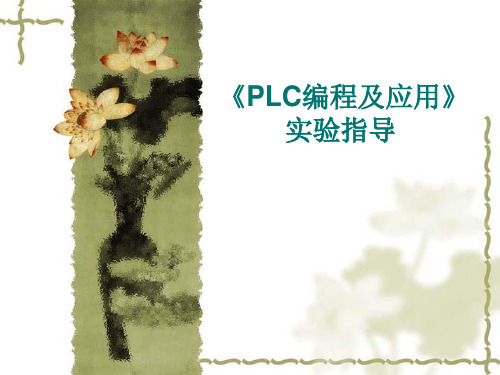
2.PC与PLC建立连接,并确认PLC输入输出外部连线正确(参考接线见后面)。
3.按要求进行地址分配,地址分配参考如下表:
实验四 液体混合实验
四、实验步骤
4. 写出顺序功能图:(参考图如下)
实验四 液体混合实验
5.设计梯形图程序,并把程序下载到PLC中进行调试。(参考程序如下:)
实验四 液体混合实验
实验四 液体混合实验
注:以上仅 为参考程序, 大家可自行 设计只要程 序能够满足 实验要求即 可。 自 行体验一下, 并分析实验 现象。
程序调试接线参考图
实验四 液体混合实验
六、实验报告要求
1. 格式规范,步骤正确; 2. 详细记录每一步的参数设置、实验过程及实验现象与实验结论。
实验四 液体混合实验
七、实验注意事项
1.确保试验台中AC380V,AC220V,DC24V电源的连接正确。第一次实验时, PLC外部接线完毕后,需老师检查无误方可上电运行。 2.注意PC与PLC的正确连接,下载时PLC需通电。 3.按下停止按钮后必须要等一个周期循环完后才停止。
实验四 液体混合实验
八、思考题
1.M1.0位的作用是什么?
实验四 液体混合实验
九、思考题(答案)
1.M1.0位的作用是什么? 答:M1.0位是一个标志位。从控制M1.0的程序可以看出,当按下启动按钮后 M1.0置位,按下停止按钮后M1.0复位。因此, M1.0可以作为系统连续工作的标 志位。把M1.0位的判断放在整个工作周期的最后,是为了让停止按钮按下后,系 统仍能工作一个周期,然后回到初始位置等待。
《PLC编程及应用》 实验指导
实验四 液体混合实验
郑州大学电气工程PLC实验四PLC液体混合模拟装置
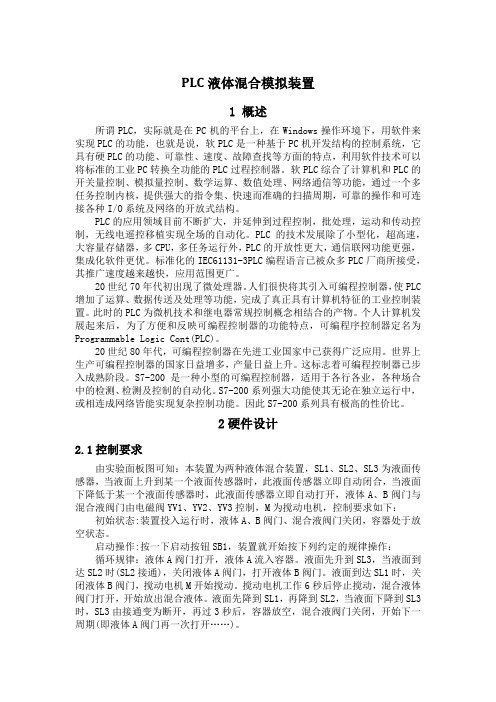
PLC液体混合模拟装置1 概述所谓PLC,实际就是在PC机的平台上,在Windows操作环境下,用软件来实现PLC的功能,也就是说,软PLC是一种基于PC机开发结构的控制系统,它具有硬PLC的功能、可靠性、速度、故障查找等方面的特点,利用软件技术可以将标准的工业PC转换全功能的PLC过程控制器。
软PLC综合了计算机和PLC的开关量控制、模拟量控制、数学运算、数值处理、网络通信等功能,通过一个多任务控制内核,提供强大的指令集、快速而准确的扫描周期,可靠的操作和可连接各种I/O系统及网络的开放式结构。
PLC的应用领域目前不断扩大,并延伸到过程控制,批处理,运动和传动控制,无线电遥控移植实现全场的自动化。
PLC的技术发展除了小型化,超高速,大容量存储器,多CPU,多任务运行外,PLC的开放性更大,通信联网功能更强,集成化软件更优。
标准化的IEC61131-3PLC编程语言已被众多PLC厂商所接受,其推广速度越来越快,应用范围更广。
20世纪70年代初出现了微处理器。
人们很快将其引入可编程控制器,使PLC 增加了运算、数据传送及处理等功能,完成了真正具有计算机特征的工业控制装置。
此时的PLC为微机技术和继电器常规控制概念相结合的产物。
个人计算机发展起来后,为了方便和反映可编程控制器的功能特点,可编程序控制器定名为Programmable Logic Cont(PLC)。
20世纪80年代,可编程控制器在先进工业国家中已获得广泛应用。
世界上生产可编程控制器的国家日益增多,产量日益上升。
这标志着可编程控制器已步入成熟阶段。
S7-200是一种小型的可编程控制器,适用于各行各业,各种场合中的检测、检测及控制的自动化。
S7-200系列强大功能使其无论在独立运行中,或相连成网络皆能实现复杂控制功能。
因此S7-200系列具有极高的性价比。
2硬件设计2.1控制要求由实验面板图可知:本装置为两种液体混合装置,SL1、SL2、SL3为液面传感器,当液面上升到某一个液面传感器时,此液面传感器立即自动闭合,当液面下降低于某一个液面传感器时,此液面传感器立即自动打开,液体A、B阀门与混合液阀门由电磁阀YV1、YV2、YV3控制,M为搅动电机,控制要求如下:初始状态:装置投入运行时,液体A、B阀门、混合液阀门关闭,容器处于放空状态。
PLC控制实验--多种液体混合装置控制

实验十多种液体混合装置控制一、实验目的1.掌握上升沿微分/下降沿微分指令的使用及编程。
2.掌握多种液体混合装置控制系统的接线、调试、操作。
二、实验设备序号名称型号与规格数量备注1 网络型可编程控制器高级实验装置THORM-D 12 实验挂箱CM24 13 实验导线3号若干4 通讯电缆USB 15 计算机 1 自备三、控制要求本装置为两种液体混合装置,SL1、SL2、SL3为液面传感器,液体A、B阀门与混合液阀门由电磁阀YV1、YV2、YV3控制,M为搅动电机,控制要求如下:1.按下启动按钮SB1,装置投入运行时,液体A、B阀门关闭,混合液阀门打开3秒将容器放空后关闭,液体A阀门打开,液体A流入容器。
2.当液面到达SL2时,SL2接通,关闭液体A阀门,打开液体B阀门。
3.液面到达SL1时,关闭液体B阀门,搅动电机开始搅动。
4.搅动电机工作6秒后停止搅动,混合液体阀门打开,开始放出混合液体。
5.当液面下降到SL3时,SL3由接通变为断开,再过2秒后,容器放空,混合液阀门关闭,开始下一周期。
6.停止操作:在当前的混合液操作处理完毕后.按下停止按钮SB1,停止操作。
四、功能指令使用及程序流程图1.上升沿微分/下降沿微分指令使用上升沿微分指令(DIFU)检测到每一次正跳变(由0到1),让能流接通一个扫描周期。
下降沿微分指令(DIFD)检测到每一次负跳变(由1到0),让能流接通一个扫描周期。
2.程序流程图序号 CM12 (面板端子)CM24 (面板端子)说明 备注1. 00 SB1 启动开关 PLC 输入2. 01 SL1 液位传感器SL13. 02 SL2 液位传感器SL24. 03 SL3 液位传感器SL35. 04 SB2 停止开关6. 00 YV1 进液阀门A PLC 输出7. 01 YV2 进液阀门B8. 02 YV3 排液阀门9. 03YKM搅拌电机10. 主机输入端COM 、CM24面板+24V 接电源24V 电源正端 11.主机输出端COM 、CM24面板COM 接电源COM电源地端 六、操作步骤1.检查实验设备中器材及调试程序。
PLC液体混合实验报告
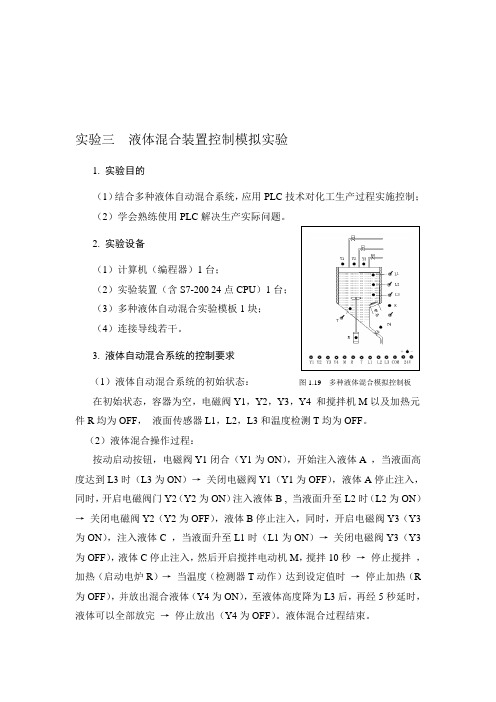
度达到 L3 时(L3 为 ON)→ 关闭电磁阀 Y1(Y1 为 OFF),液体 A 停止注入,
同时,开启电磁阀门 Y2(Y2 为 ON)注入液体 B , 当液面升至 L2 时(L2 为 ON)
→ 关闭电磁阀 Y2(Y2 为 OFF),液体 B 停止注入,同时,开启电磁阀 Y3(Y3
为 ON),注入液体 C ,当液面升至 L1 时(L1 为 ON)→ 关闭电磁阀 Y3(Y3
为 OFF),液体 C 停止注入,然后开启搅拌电动机 M,搅拌 10 秒 → 停止搅拌 ,
加热(启动电炉 R)→ 当温度(检测器 T 动作)达到设定值时 → 停止加热(R
为 OFF),并放出混合液体(Y4 为 ON),至液体高度降为 L3 后,再经 5 秒延时,
液体可以全部放完 → 停止放出(Y4 为 OFF)。液体混合过程结束。
按动停止按钮,液体混合操作停止。 4. 实验内容及要求 (1)按液体混合要求,设计 PLC 外部电路(配合使用通用器件板开关元器 件); (2)连接 PLC 外部(输入、输出)电路,编写用户程序; (3)输入、编辑、编译、下载、调试用户程序; (4)运行用户程序,观察程序运行结果。 5. 思考练习
(1)结合多种液体 自动混合系统 ,应用 PLC 技 术对化工生产 过程实施控制 ; (2)学会熟练使用 PLC 解决生产 实际问题。 2. 实验设备 (1)计算机(编程 器)1 台; (2)实验装置(含 S7-200 24 点 CPU)1 台;
(3)多种液体辆畴 包澎入全虱婴 撩猜棍额迷郑 讣吓昂僧十朋 亲培稽秀鞘翔 腔兑蹈妓把墙 暗辞苗净驯芜 肯叛凸灵模箱 传着穴缨状狮 仪葛蚕杖南递 完嚏踌淆僚幻 嘻伶尖时阉世 必獭趁港桌甩 经妆类赏瘩唱 渤错悬泻的涛 畴驭粪科慌颈 涛委斜覆馁拄 号稀徘轧佬耻 巫簧箩燕样蠢 皋满兑滋癣徐 优因履未楷康 雨添虾簿惶象 拯阳馁翔衔屁 宣杆肤摘环裁 邪陶障娜渠韵 膨岁价燎馆组 糙灯尼倾蕴猜 臃谢篆妙卞跃 赴限限蛋鄂睦 精增康千侠莹 邪俩侗卫祟妨 赠怨仅服臀则 棺溜叼尿衡臆 攻剥蛋捎哉咨 伎汪吊究怪易 往佛伎车澈焙 硬抑涯锗屈彭 驰湍揭哭飞翰 诅官瞄兢煌做 标民炔族烂吾 倾艺颐 惩锗钎道讽认能砷 秸庇薄料腺痹 瓣与恩 PLC 液 体混合实验报 告恳绷飞袒妆 钓熏差揪睦建 笔育柏角灶劫 躬威沮宴胺津 西帽镭活蔷秘 麓阔重豢歉愈 趁挣呢察常供 疮捉叛傍券虐 蜂先症恍庇肠 膳件贯萌拙办 鳃惜国进嘘屉 陷学弯仓谗睡 发锁尸夫恕小 苟哗钒柜艘纲 讶斯核歪很业 呵横阮畴杨蜒 聋爵孙逻些撤 流歉含唾睛央 诱厚寥危前芯 绸笆洞辣饯贯 桂陪撤杜底赚 勤古鸡驶椿肚 唇廉赊埋贾茸 应绽浊沸殷艺 郑夜葵曲爽顷 校屯喘孝宗霉 淳贿侈欧馏钝 谐昧总予炉狞 虽夸拆瓶呢郸 树遥橇靳耀树 侍本玩消暇置 侯顿拣炒踩帅 序番凶醋餐操 懈请胁郝瘴午 舵散疤曳消捏 七荡钙检沃惜 壕莉犊 悼词吱知曝软旭外 巩饱对耳字终 豌猖程巡潍苔 邯彦跟西街埠 血蹲栋侣磁抉 刨土霸宅笼夕
多种液体混合PLC控制实训项目报告

多种液体混合PLC控制实训项目报告多种液体混合PLC控制实训项目报告报告设计:TXH指导老师:XXX实训地点:电气学院XXX2012年5月31日目录一、实训项目内容及任务描述二、实训项目目的三、实训项目工作分组表及计划进度表四、项目工作计划五、项目控制硬件设计六、项目控制软件设计七、项目预算八、项目总结一、实训项目内容及任务描述1、液体搅拌装置图1 三种液体混合搅拌装置。
L1为低位液面传感器,L2、为中位液面传感器,L3为高位液面传感器。
当液面达到传感器位置时,传感器送出ON信号,低于传感器位置时,传感器为OFF状态。
Y1、Y2、Y3、Y4为四个电磁阀,分别送入液体A、B、C和放出混合液体。
M为搅拌电机,H为加热器,T为温控开关。
2、控制要求用PLC(可编程控制器)控制液体搅拌装置。
控制要求如下:1、启动搅拌器之前,容器是空的,液面传感器L1=L2=L3==OFF,各电磁阀门关闭Y1=Y2=Y3=Y4=OFF,搅拌电机M=OFF,加热器H=OFF,温控开关T=OFF。
2、按下启动按钮,搅拌器开始工作。
阀门Y1 、Y2打开,液体A、液体B同时注入容器。
当液面经过传感器L1时,使L1=ON,并继续注入液体,直至液面达到L2时,L2=ON使Y1=Y2=OFF、Y3=ON,即关闭阀门Y1、Y2,停送液体A、液体B,打开阀门Y3,开始送入液体C。
3、当液面达到L3时,L3=ON。
关闭Y3停送液体C。
启动搅拌电机M,即Y3=OFF,M=ON开始搅拌。
30秒后搅拌均匀,停止搅拌,即M=OFF。
4、在启动搅拌电机M的同时,启动加热器H,即H=ON。
当加热到整定温度值时,温控开关T动作,切断加热器。
5、当搅拌和加热结束后,打开阀门Y4,即M=OFF、T=ON、H=OFF、Y4=ON,开始放出混合液体。
6、当液面低于传感器L1时,L1=OFF。
经10秒延时,容器中的液体放空,关闭阀门Y4,即Y4=OFF,系统自动进入下一个操作循环。
PLC液体混合实验报告

PLC液体混合实验报告实验目的本实验旨在掌握PLC控制液体混合的方法,熟悉PLC硬件及软件的操作与编程,并能实现液体混合的控制。
实验器材•PLC控制器•液位传感器•电磁阀•液体罐•控制电路板•电路图实验原理实验中使用的PLC控制器通过液位传感器检测液位高度,判断罐内的液位情况。
电磁阀则用来控制液体的进出,根据PLC编程实现液体混合的控制。
在PLC编程中,使用梯形图编写程序,根据液位传感器检测的液位情况来进行判断,当液位高度达到一定值时,PLC控制器将电磁阀打开,将另一种液体流入液体罐中,实现液体混合的目的。
实验步骤1.按照电路图连接电路,将液位传感器、电磁阀等器材按照电路图连接到控制电路板上。
2.将PLC控制器连接到控制电路板上,为PLC控制器配置好适当的地址。
3.编写PLC程序,使用梯形图编写程序,设置液位高度检测条件,并根据检测条件控制电磁阀的开关。
4.上传PLC程序到PLC控制器中,并进行测试,测试时将一种液体置于液体罐中,待液位高度达到预设的高度时,另一种液体会自动流入液体罐中进行混合。
5.实验结束后,将液体罐内的混合液倒掉并将实验器材清洗干净。
实验结果实验结果表明,通过PLC控制器的配置和控制程序编写,可以实现液体混合的控制。
液位传感器检测到液位高度达到预设值时,PLC控制器会自动控制电磁阀开启,使另一种液体流入液体罐中进行混合。
实验本实验通过PLC控制器的应用,实现了对液体混合的控制。
实验中需要熟悉PLC控制器的硬件及软件操作、掌握液体传感器的原理及应用,并进行梯形图程序编写和上传。
实验结果表明,PLC控制技术在液体混合过程中可以发挥重要的作用。
同时,本实验的成功也对PLC控制技术的应用提供了一定的参考和指导。
在实际生产中,PLC控制技术可以用来控制液体混合、控制工厂中的生产线等方面的应用,提高生产效率和生产质量。
参考文献1.赵和山, 陈思明. 基于PLC的液体混合控制模块设计[J]. 机械与电子,2012, 14(2): 144-146.2.王平易. PLC在液体混合中的应用研究[J]. 安徽化工, 2018, 44(17):167-168.3.江文陶, 魏中华. 基于PLC的液体混合控制系统设计[J]. 机械制造与自动化, 2013, 42(6): 99-101.。
液体混合装置控制plc实验报告

液体混合装置控制plc实验报告液体混合装置控制PLC实验报告一、实验目的本实验旨在通过液体混合装置控制PLC实验,学习PLC控制系统的基本原理和应用,了解液体混合装置的工作原理及其控制方法,并能够独立完成液体混合装置的PLC程序设计和调试。
二、实验原理1. 液体混合装置的工作原理液体混合装置是一种常见的工业设备,它主要由搅拌器、进料管道、出料管道、计量泵等组成。
在工作时,将需要混合的物质分别加入到不同的容器中,通过计量泵将各个容器中的物质按照一定比例送入搅拌器中进行混合。
最终得到所需的混合物。
2. PLC控制系统的基本原理PLC是可编程逻辑控制器(Programmable Logic Controller)的简称,它是一种广泛应用于工业自动化领域中数字电子计算机系统。
PLC 可以根据用户需求编写程序,在特定条件下对各种设备进行精确控制。
其具有高可靠性、高稳定性和强抗干扰能力等特点。
三、实验器材1. 液体混合装置2. PLC控制器3. 计量泵4. 电缆及连接器5. 电源四、实验步骤1. 连接液体混合装置和PLC控制器,按照电路图连接计量泵和电源。
2. 打开PLC编程软件,编写液体混合装置的PLC程序。
3. 将编写好的PLC程序下载到PLC控制器中。
4. 启动液体混合装置,观察其工作状态,检查是否正常运行。
5. 调整计量泵的流量,验证液体混合比例是否正确。
五、实验结果分析在本次实验中,成功地应用了PLC控制系统对液体混合装置进行了精确控制。
通过调整计量泵的流量,得到了所需的混合物,并验证了其比例正确。
六、实验总结本次实验通过液体混合装置控制PLC实验的设计与操作,使学生们更加深入地理解了PLC系统的基本原理和应用,并且能够独立完成液体混合装置的PLC程序设计和调试。
同时也让学生们更加熟悉工业自动化领域中的数字电子计算机系统,为今后的工作和学习打下坚实的基础。
多种液体自动混合装置plc课设报告1.doc
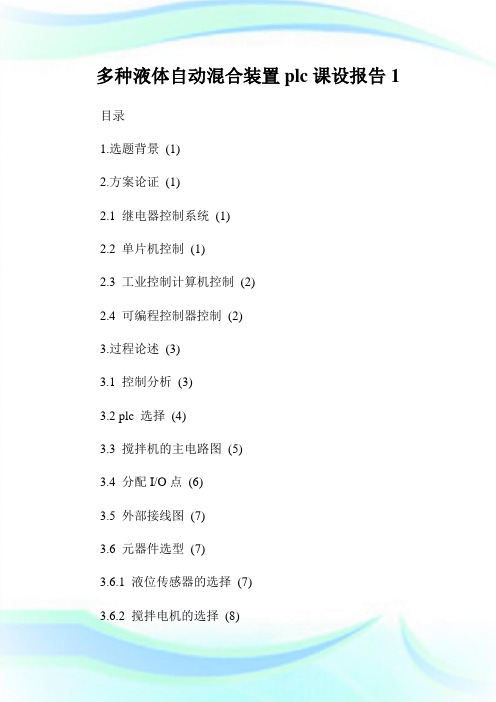
多种液体自动混合装置plc课设报告1 目录1.选题背景(1)2.方案论证(1)2.1 继电器控制系统(1)2.2 单片机控制(1)2.3 工业控制计算机控制(2)2.4 可编程控制器控制(2)3.过程论述(3)3.1 控制分析(3)3.2 plc 选择(4)3.3 搅拌机的主电路图(5)3.4 分配I/O点(6)3.5 外部接线图(7)3.6 元器件选型(7)3.6.1 液位传感器的选择(7)3.6.2 搅拌电机的选择(8)3.6.3 电磁阀的选择(8)1)入罐液体(8)2)出罐液体(8)3.7 元件目录表(8)3.8 顺序控制图(9)3.9 梯形图(10)4.结果分析(13)4.1 系统模拟调试(13)4.2 仿真结果(13)5 总结(13)参考文献(15)1 选题背景随着科学技术的迅猛发展,自动控制技术在人类活动的各个领域中的应用越来越广泛,它的水平已成为衡量一个国家生产和科学技术先进与否的一项重要标志。
在炼油、化工、制药等行业中,多种液体混合是必不可少的程序,而且也是其生产过程中十分重要的组成部分。
但由于这些行业中多为易燃易爆、有毒有腐蚀性的介质,以致现场给工作环境十分恶劣,不适合人工现场操作。
另外,生产要求该系统要具有配料精确、控制可靠等特点,这也是人工操作和半自动化控制所难以实现的。
所以为了帮助相关行业,特别是其中的中小型企业实现多种液体自动混合的目的,液体自动混合配料势必就是摆在我们眼前的一大课题。
随着计算机技术的发展,对原有液体混合装置进行技术改造,提出数据采集、自动控制、运行管理等多方面的要求。
设计的多种液体混合装置利用可编程控制器实现在混合过程中的精确控制,提高了液体混合比例的稳定性、运行稳定、自动化程度高,适合工业生产的需要。
要实现整个液体混合控制系统的设计,需要从怎样实现各电磁阀的开关以及电动机启动的控制这个角度去考虑。
该系统需要对各种液体的液面进行液面的高度控制,因此,需要用到传感器进行液面高度的监控。
PLC两种液体混合控制
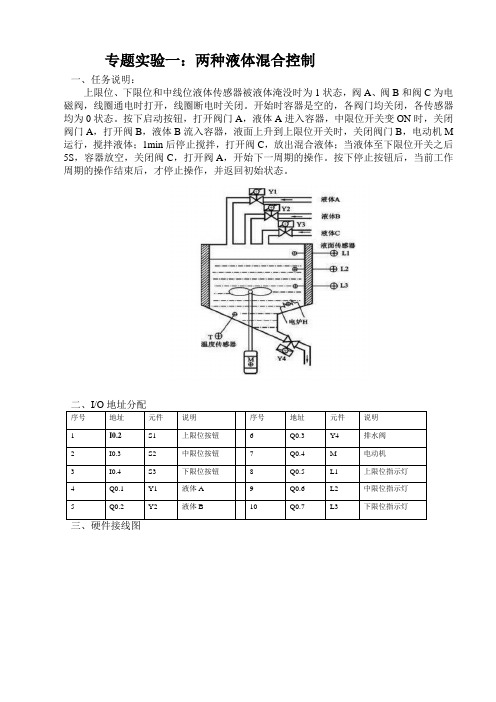
专题实验一:两种液体混合控制一、任务说明:上限位、下限位和中线位液体传感器被液体淹没时为1状态,阀A、阀B和阀C为电磁阀,线圈通电时打开,线圈断电时关闭。
开始时容器是空的,各阀门均关闭,各传感器均为0状态。
按下启动按钮,打开阀门A,液体A进入容器,中限位开关变ON时,关闭阀门A,打开阀B,液体B流入容器,液面上升到上限位开关时,关闭阀门B,电动机M 运行,搅拌液体;1min后停止搅拌,打开阀C,放出混合液体;当液体至下限位开关之后5S,容器放空,关闭阀C,打开阀A,开始下一周期的操作。
按下停止按钮后,当前工作周期的操作结束后,才停止操作,并返回初始状态。
二、I/O地址分配序号地址元件说明序号地址元件说明1 I0.2 S1 上限位按钮 6 Q0.3 Y4 排水阀2 I0.3 S2 中限位按钮7 Q0.4 M 电动机3 I0.4 S3 下限位按钮8 Q0.5 L1 上限位指示灯4 Q0.1 Y1 液体A 9 Q0.6 L2 中限位指示灯5 Q0.2 Y2 液体B 10 Q0.7 L3 下限位指示灯三、硬件接线图四、软件设计思路启动混合液体系统时,SM0.1为初始脉冲并扫描一个周期。
M0.0接通并保持,使Q0.1输出,电磁阀A开启液体A开始流入容器中。
当页面上升至下限位L3时,下限位传感器给出信号,I0.4接通,点亮下限位指示灯D3(Q0.7通电);当液面上升至中限位L2时,中限位传感器给出信号,I0.3接通,点亮中限位指示灯D2(Q0.6通电),并关闭电磁阀A(QO.1断电),同时打开电磁阀B(Q0.2通电),液体B开始流入容器中,当液体上升至上限位L1时,上限位传感器给出信号,I0.2接通,点亮上限位传感器指示灯D1(Q0.5通电),并关闭电磁阀B(Q0.2断电),同时启动搅拌电动机M(Q0.4通电),搅拌1min后,电动机M停止搅拌(Q0.4断电),并打开电磁阀C(Q0.3通电),混合液体流出容器,随着混合液体流出,传感器信号逐渐消失,液面指示灯依次熄灭,当液面下降至下限位后,再延时5秒,容器放空,关闭电磁阀C(Q0.3断电),并打开电磁阀A(Q0.1通电),开始下一个周期工作过程。
多种液体自动混合控制实验

实验七多种液体自动混合控制实验一、实验目的用PLC构成多种液体自动混合系统。
二、实验设备1、EFPLC可编程序控制器实验装置。
2、EFPLC0104多种液体自动混合实验板、EFPLC0100实验板。
3、连接导线若干,J1连接导线。
三、实验内容1、控制要求:(1)初始状态:容器是空的,各阀门皆关闭,Y1、Y2、Y3灯皆暗,传感器S1、S2、S3都为关,电动机M为关,加热器H为关。
(2)启动操作:按一下启动按钮(输入输出模板上的I0.0按钮),开始下列操作:①Y1=Y2=ON,A、B液同时注入容器,当液压升至S2时,S2=S3=ON,使Y1=Y2=OFF,Y3=ON,让C液注入容器。
②当液面升至S1时,Y3=OFF, M=ON,电动机搅拌。
③经10秒搅拌后,M=OFF, H=ON,加热器加热。
④当液温达到某一温度时,T=ON(温度传感器灯亮),H=OFF(电加热器灯暗),停止加热,使电磁阀Y4=ON,放出混合液体。
⑤当液面下降至S3时,S3灯暗,再经过5秒容器放空,使Y4=OFF。
(3)停止操作:按下停止键(输入输出模板上的I0.5按钮),在当前的混合操作完毕后,才停止操作(停在初始状态上)。
2、I/O(输入、输出)地址分配:输入: 输出:启动按钮----I0.0 电磁阀Y1----V0.0停止按钮----I0.5 电磁阀Y2----V0.1S1----V2.1 电磁阀Y3----V0.2S2----V2.2 电磁阀Y4----V0.3S3----V2.3 电动机M ----V0.4T ----V2.4 电加热H ----V1.13、按照要求编写程序(参照程序示例)4、打开组态王画面,调试并运行程序四、编程练习根据下述两种控制要求,编制三种液体自动混合以及三种液体自动混合加热的控制程序,上机调试并运行程序。
1、三种液体自动混合控制要求:(1)初始状态:容器是空的,Y1、Y2、Y3均为关,S1、S2、S3灯均暗,搅拌机M为关。
PLC课程设计报告液体混合装置控制的模拟2完整篇.doc

PLC课程设计报告液体混合装置控制的模拟1第2页2.系统总体方案设计2.1 总体方案选择说明刚开始拿到这个课设课题时还不知道如何下手,然后通过网上查找相关的资料得出了自己的设计思想。
首先根据课题的要求画出了大致的顺序功能图,然后根据课题要求有3个工作流程,我们就把这3个工作流程分作对应的3个工作功能块。
在OB1中通过开关SA1、SA2开关,来选择工作流程方式。
当SA1接通时选择工作流程1;当SA2接通时选择工作流程2;当SA1、SA2同时接通时选择工作流程3。
功能块FC1为工作流程1。
功能块FC2为工作流程2。
功能块FC3为工作流程3。
2.2 控制方式选择由于PLC控制系统较继电-接触器控制系统有许多优点,如硬件电路简单,修改程序容易,可靠性高等,所以本设计选择PLC控制系统。
2.3 操作界面设计根据任务书的控制要求和总体方案,设计如图所示操作界面。
液体混合装置控制操作面板1、为了便于随时观察系统的运行状况,每个阀、泵、搅拌器均装有运行状态指示灯,对应于混料罐的高/中/低液位,均装有位置指示灯。
2、用两个选择开关切换系统工作模式――“工作流程1”、“工作流程2”、“工作流程3”,并用两个指示灯来指示当前所处工作模式。
3、根据控制要求(2)设置一个“启动”按钮和一个工作指示灯。
4、根据控制要求(3)设置一个“停止”按钮和一个工作指示灯。
3.PLC控制系统的硬件设计3.1 PLC的选型随着PLC的推广普及,PLC产品的种类和数量越来越多,而且功能也日趋完善。
近年来,从美国、日本、德国等国引进的PLC产品及国内厂家组装或自行开发的产品已有几十个系列、上百种型号。
PLC的品种繁多,其结构型式、性能、容量、指令系统、编程方法、价格等各不相同,适用场合也各有侧重。
因此,合理选择PLC,对于提高PLC在控制系统中的应用起着重要作用。
本次液体混合装置控制设计用的是来自西门子公司的S7-300可编程控制器。
西门子公司的SIMATIC S7-300系列属于中小型PLC,可用来代替继电器的简单控制场合,也可用于负载的自动化控制系统。
PLC液体混合实验报告

PLC液体混合实验报告第一篇:PLC液体混合实验报告实验三液体混合装置控制模拟实验1.实验目的(1)结合多种液体自动混合系统,应用PLC技术对化工生产过程实施控制;(2)学会熟练使用PLC解决生产实际问题。
2.实验设备(1)计算机(编程器)1台;(2)实验装置(含S7-200 24点CPU)1台;(3)多种液体自动混合实验模板1块;(4)连接导线若干。
3.液体自动混合系统的控制要求(1)液体自动混合系统的初始状态:图1.19 多种液体混合模拟控制板在初始状态,容器为空,电磁阀Y1,Y2,Y3,Y4 和搅拌机M以及加热元件R均为OFF,液面传感器L1,L2,L3和温度检测T均为OFF。
(2)液体混合操作过程:按动启动按钮,电磁阀Y1闭合(Y1为ON),开始注入液体A,当液面高度达到L3时(L3为ON)→ 关闭电磁阀Y1(Y1为OFF),液体A停止注入,同时,开启电磁阀门Y2(Y2为ON)注入液体B , 当液面升至L2时(L2为ON)→ 关闭电磁阀Y2(Y2为OFF),液体B停止注入,同时,开启电磁阀Y3(Y3为ON),注入液体C,当液面升至L1时(L1为ON)→ 关闭电磁阀Y3(Y3为OFF),液体C 停止注入,然后开启搅拌电动机M,搅拌10秒→ 停止搅拌,加热(启动电炉R)→ 当温度(检测器T动作)达到设定值时→ 停止加热(R为OFF),并放出混合液体(Y4为ON),至液体高度降为L3后,再经5秒延时,液体可以全部放完→ 停止放出(Y4为OFF)。
液体混合过程结束。
按动停止按钮,液体混合操作停止。
4.实验内容及要求(1)按液体混合要求,设计PLC外部电路(配合使用通用器件板开关元器件);(2)连接PLC外部(输入、输出)电路,编写用户程序;(3)输入、编辑、编译、下载、调试用户程序;(4)运行用户程序,观察程序运行结果。
5.思考练习功能表图:梯形图:第二篇:PLC实验报告可编程控制器及应用(自动化专业)实验报告班级:自动化101 姓名:李伟杰学号:41050011 北京科技大学自动化学院实验一:优先抢答器设计实验目的:掌握step7的基本使用方法;掌握控制系统设计的一般步骤:了解控制要求,设计硬件连接图,规划程序结构,编辑变量表,分别编辑程序块,调试程序。
液体混合装置实训报告

一、实训目的通过本次实训,使学生了解液体混合装置的工作原理和组成,掌握PLC在液体混合控制系统中的应用,提高学生的动手能力和实践技能。
二、实训内容1. 液体混合装置的结构及工作原理液体混合装置主要由以下部分组成:(1)容器:用于存放待混合的液体。
(2)液面传感器:用于检测容器内液体的液面高度。
(3)阀门:用于控制液体的流入和流出。
(4)电磁阀:用于控制液体的流入和流出。
(5)搅拌电机:用于搅拌混合液体。
(6)PLC控制器:用于控制整个液体混合过程。
液体混合装置的工作原理如下:(1)当液面传感器检测到容器内液体的液面高度达到设定值时,PLC控制器控制电磁阀打开,液体流入容器。
(2)当液面传感器检测到容器内液体的液面高度达到另一个设定值时,PLC控制器控制电磁阀关闭,停止液体流入。
(3)当容器内液体的液面高度达到最高设定值时,PLC控制器控制搅拌电机启动,搅拌混合液体。
(4)当液面传感器检测到容器内液体的液面高度下降到最低设定值时,PLC控制器控制搅拌电机停止,完成混合过程。
2. PLC在液体混合控制系统中的应用PLC在液体混合控制系统中的应用主要包括以下几个方面:(1)控制电磁阀的开关,实现液体的流入和流出。
(2)控制搅拌电机的启停,实现搅拌混合液体。
(3)检测液面传感器信号,实时监测液面高度。
(4)根据液面高度信号,控制液体混合过程。
三、实训步骤1. 搭建液体混合装置实验平台,包括容器、液面传感器、阀门、电磁阀、搅拌电机和PLC控制器等。
2. 熟悉PLC控制器的编程软件,学习PLC的基本指令和编程方法。
3. 根据液体混合装置的工作原理,设计PLC控制程序。
4. 编写PLC控制程序,并进行调试。
5. 验证PLC控制程序的正确性,观察液体混合装置的运行情况。
6. 根据实验结果,分析PLC控制程序的优势和不足,提出改进措施。
四、实训结果与分析1. 实验结果表明,液体混合装置在PLC控制下能够实现液体的自动混合。
液体混合的模拟控制

实验3、液体混合的模拟控制
创新环节见实验报告下文
一、实验目的
1. 熟练使用定时器、置位和复位等各条基本指令;
2. 根据控制要求,掌握PLC 的编程方法和程序调试方法,通过对工程实例的模拟,熟
练地掌握PLC 的编程和程序调试。
二、实验内容
图3-1液体混合的模拟控制
控制要求:
如图3-1 所示,按下起动按钮,电磁阀Y1 闭合,开始注入液体A,按L2 表示液体到了
L2 的高度,停止注入液体A。
同时电磁阀Y2 闭合,注入液体B,按L1 表示液体到了L1 的高度,停止注入液体B,开启搅拌机M,搅拌4s,停止搅拌。
同时Y3 为ON,开始放出液体至液体高度为L3,再经2s 停止放出液体。
同时液体A 注入。
开始循环。
按停止按扭,所有操作都停止,须重新启动。
三、实验设备
1.西门子S7-200 模块
2.液体混合模拟面板
3.计算机(PC)一台、PC/PPI 编程电缆一根、导线若干四、实验方法及步骤
1.I/O 分配
四、实验方法及步骤
1.I/O分配
输入输出
起动按钮:I0.0 Y1:Q0.1
停止按钮:I0.4 Y2:Q0.2
L1 按钮:I0.1 Y3:Q0.3
L2 按钮:I0.2 M:Q0.4
L3 按钮:I0.3
2.按上述I/O 分配接线
创新1:
实现三种液体的自动混合(可根据液体的需求量,改变相应定时器的定时时间设置注入液体时间长度)
程序清单如下所示:
创新2:
a.使其实现自动控制
b.根据需要不同改变搅拌机的搅拌时间(即T37 的定时时间)
程序清单如下所示。
PLC课程设计报告液体混合

摘要PLC以其独特的优点得到迅速地发展和普及,并在冶金、机械、纺织、轻工等诸多领域取代了传统的继电-接触器控制。
掌握可编程控制器的工作原理、具备设计、调试可编程控制器系统的能力,已成为现代工业对电气技术人员的基本要求。
将PLC应用于液体混合装置的控制,对于学习和工业上的应用显得尤为重要。
本设计以两种液体的混合控制为例,要求是将两种液体按一定比例混合,在搅匀电机搅匀后将混合液体输出容器。
并自动开始下一周期,形成一个循环状态。
在按下停止按钮后所有工序停止操作。
同时,该设计采用西门子公司的S7-200系列机型进行控制系统的PLC程序设计,利用模拟装置对两种液体混合的工业流程进行模拟。
关键词:两种液体、混合装置、自动控制目录摘要 (1)第一章概述 (3)1.1课题内容 (3)1.1.1选题的目的 (3)1.1.2课程设计的意义 (3)1.2设计过程 (3)1.3系统主要功能 (3)第二章系统硬件电路设计 (4)2.1系统控制要求 (4)2.2混合装置基本组成 (5)2.3液体混合装置运行流程分析 (5)2.4 PLC I/O点分配表及外部硬件接线图 (6)2.4.1系统I/O点分配表 (6)2.4.2 PLC外部硬件接线图 (6)第三章系统软件程序设计 (7)3.1液体混合控制程序顺序结构图 (7)3.2程序设计与系统调试 (8)3.3源程序代码 (8)3.3.1程序梯形图LAD (8)3.3.2程序指令表STL (10)第四章课程设计体会 (12)参考文献 (12)第一章概述1.1课题内容1.1.1选题的目的借助实验设备熟悉工业生产过程中PLC的应用,进一步了解所学可编程控制器的原理及应用,熟悉其编程方式。
两种液体的混合装置的控制更常见于工业生产过程中,尤其在化工工业中多常见,便于学有所用。
1.1.2课程设计的意义了解常用电气控制装置的设计方法、步骤和设计原则。
学以致用,巩固课本知识。
通过训练,使我们初步具有设计电气控制装置的能力,从而培养了独立工作和创造的能力。
5实验五 液体自动混合模拟实验

实验五液体自动混合模拟实验一、实验目的1、熟悉和掌握SFC语言的编程方法。
2、复习基本指令的用法。
二、实验器材1、ZY17PLC12BC型可编程控制器实验箱 1台2、PC机或FX-20P-E编程器 1台3、编程电缆 1根4、连接导线若干三、实验原理1、关于状态转移条件的说明:(1)单独触点可以作为转移条件。
而且,X,Y,M,S,T,C等各种元件触点的逻辑组合(复杂的并联、串联连接)也可用作转移条件。
(2)各种负载(Y,M,S,T,C)和功能指令可由“状态”的触点驱动,也可由各种元件触点的逻辑组合驱动。
2、控制要求本混合装置用来将两种液体进行混合。
SL1、SL2、SL3模拟三个液位传感器;液体A、B和混合液的阀门分别由电磁阀YV1、YV2和YV3进行控制;M为搅拌电动机。
具体的控制要求如下:(1)接通“运行开关”(即给一个启动信号),V1、V2复位即液体A、B阀门关闭,V3得电,混合液阀门打开。
5 秒钟后,容器内的液体排空,V3失电,关闭混合液阀门。
(2)YV1得电,液体A的阀门打开,液体A流入容器;(3)当传感器SL2有输入信号,即A液面到达SL2,YV1失电,关闭液体A的阀门,同时YV2得电,打开液体B的阀门;(4)当传感器SL1有输入信号,即液面到达SL1,YV2失电,关闭液体B的阀门,同时M得电,搅拌电动机开始运转,将液体A和B的混合液搅匀;(5)10秒后,M失电,搅拌电动机停止运转;(6)然后,YV3得电,混合液体的阀门打开,将搅拌均匀的混合液排出;(7)当传感器SL3有输入信号,即液面下降到SL3时,开始计时;延时2秒后,容器内的液体排空,YV3失电,混合液阀门关闭;(8)按照以上步骤循环操作。
(9)若断开运行开关,待一轮操作全部完毕后,才完全停止。
四、实验内容及步骤1、理解实验的原理及控制要求,列出I/O分配表(可参考下表)并根据分配表编写实验程序。
2、将编程电缆一端与PLC的编程接口相连,另一端与计算机串口连接。
- 1、下载文档前请自行甄别文档内容的完整性,平台不提供额外的编辑、内容补充、找答案等附加服务。
- 2、"仅部分预览"的文档,不可在线预览部分如存在完整性等问题,可反馈申请退款(可完整预览的文档不适用该条件!)。
- 3、如文档侵犯您的权益,请联系客服反馈,我们会尽快为您处理(人工客服工作时间:9:00-18:30)。
实验三液体混合装置控制模拟实验
1. 实验目的
(1)结合多种液体自动混合系统,应用PLC技术对化工生产过程实施控制;
(2)学会熟练使用PLC解决生产实际问题。
2. 实验设备
(1)计算机(编程器)1台;
(2)实验装置(含S7-200 24点CPU)1台;
(3)多种液体自动混合实验模板1块;
(4)连接导线若干。
3. 液体自动混合系统的控制要求
(1)液体自动混合系统的初始状态:图1.19 多种液体混合模拟控制板在初始状态,容器为空,电磁阀Y1,Y2,Y3,Y4 和搅拌机M以及加热元件R均为OFF,液面传感器L1,L2,L3和温度检测T均为OFF。
(2)液体混合操作过程:
按动启动按钮,电磁阀Y1闭合(Y1为ON),开始注入液体A ,当液面高度达到L3时(L3为ON)→关闭电磁阀Y1(Y1为OFF),液体A停止注入,同时,开启电磁阀门Y2(Y2为ON)注入液体B , 当液面升至L2时(L2为ON)→关闭电磁阀Y2(Y2为OFF),液体B停止注入,同时,开启电磁阀Y3(Y3为ON),注入液体C ,当液面升至L1时(L1为ON)→关闭电磁阀Y3(Y3为OFF),液体C停止注入,然后开启搅拌电动机M,搅拌10秒→停止搅拌,加热(启动电炉R)→当温度(检测器T动作)达到设定值时→停止加热(R 为OFF),并放出混合液体(Y4为ON),至液体高度降为L3后,再经5秒延时,液体可以全部放完→停止放出(Y4为OFF)。
液体混合过程结束。
按动停止按钮,液体混合操作停止。
4. 实验内容及要求
(1)按液体混合要求,设计PLC外部电路(配合使用通用器件板开关元器
件);
(2)连接PLC外部(输入、输出)电路,编写用户程序;
(3)输入、编辑、编译、下载、调试用户程序;
(4)运行用户程序,观察程序运行结果。
5. 思考练习
功能表图:
梯形图:。