电渣熔铸异型件熔渣内溢现象
电渣炉

浏览字体:大中小电渣重熔摘要:本文阐述了目前国内电渣炉的使用状况,希望对冶金企业的设备改造有一些帮助。
关键词:电渣重熔炉;结晶器;模糊控制;恒电流;恒熔速。
1.前言当前,随着国家建设、航空航天及国防建设的不断发展,市场对各种高品质精细钢材的需求不断增加,电渣重熔炉的重要性日见明显,国内大部分电渣重熔炉的生产多极为繁忙,经济效益明显,但由于大部分电渣重熔炉的建造期多为70年代左右,其设备从整体上看较为陈旧,特别是控制系统更为落后,控制精度(工作电流、工作电压、冶*率、熔速等稳定性)较差,直接影响了电渣锭的质量,制约了其经济效益的进一步提高。
电渣重熔炉是对已炼成的钢或合金进行再精炼的一种电炉设备。
从发热原理来说,电渣重熔炉是一种电阻熔炼炉。
自耗电极是用被熔金属本身制成的。
熔炼电流从变压器经短网到自耗电极,再经熔渣及结晶器平台上的导电板返回。
熔炼电流在通过高电阻熔渣时产生高温熔化自耗电极,金属熔滴穿过熔渣滴入金属熔池,被水冷结晶器冷却凝结成锭坯。
在此过程中金属熔滴与熔渣充分接触,产生强烈的冶金化学反应,使金属得到精炼。
2.电渣重熔炉设备电渣重熔炉通常由三部分组成:机械系统、供电系统、控制系统。
2.1机械系统包括:电极升降立柱、电极横臂、电极旋转升降机构、电极夹头、假电极、结晶器平台(或小车)、水冷结晶器、排烟除尘等。
电渣炉的机械系统从机械结构上分有单支臂和双支臂两种。
单支臂结构方式一次性设备投资较低,但是,当冶炼坯锭较大时,由于电极行程很长,因而要求厂房高度较高,所以,当炉子容量要求较大时,设备造价虽低,但是总投资却不少;加之自耗电极较长,制作和冶炼操作都很困难,所以,单支臂结构方式一般只适合于容量较小的电渣重熔炉。
双支臂结构方式虽然设备的一次性投资较高,但由于电极行程短,厂房高度低,操作灵活,通过支臂交换,可生产较大的电渣锭,所以,在一般情况下,应采用双支臂结构方式。
电极升降立柱通常为钢板焊接而成箱型框架式结构,用以支撑固定电极横臂和电极旋转升降机构。
不锈钢电渣重熔技术
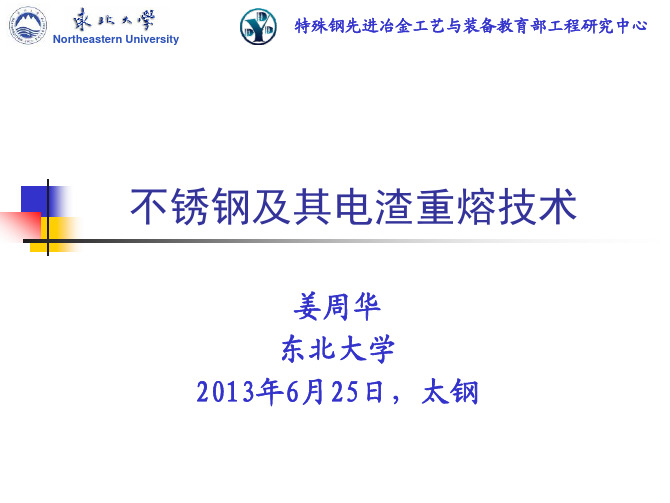
= 炉管、叶片、护环、水轮机导叶和叶片
油气开采:超级13Cr、15Cr、双相不锈钢
= 石油化工:高温、耐蚀部件(管道、阀门) = 海洋工程(海水淡化):超级双相不锈钢、超级奥氏体 = 不锈钢
特殊钢先进冶金工艺与装备教育部工程研究中心
Northeastern University
二、电渣重熔的不锈钢品种及 其应用
=
电渣重熔的起源-首个不锈钢电渣锭
的不锈钢主要钢种
马氏体不锈钢 沉淀硬化马氏体不锈钢 超级铁素体不锈钢 奥氏体不锈钢、超级奥氏体不锈钢、高 = 氮奥氏体不锈钢 双相不锈钢、超级双相不锈钢
钢渣接触条件的比较
O
采 充
= =
O L 充
问
O
问 L 充
M N
V V M
R
O
范N
目 -6 M R 活
V
它
目 s R
M
电渣重熔冶金
渣池强烈搅 拌:电动力、 电磁力、自然 对流、气体逸 出和膨胀的推 力
=
= = = = =
非金属夹杂物的去除
电渣熔铸去除钢中非金属夹杂物主要发生在电极熔化末端熔滴 = 形成的过程中 电极熔化末端熔滴形成过程的钢渣接触面积最大,达3219 mm2/ = 克,它是熔滴过程的67 倍,是金属熔池的21000 倍 电极熔化末端熔滴形成的时间较熔滴滴落时间为长,约为1.41 倍 = 电极熔化末端熔滴形成过程是最先和熔渣接触并发生反应部 = 分,钢中原始夹杂物含量最高,无疑可大量去除夹杂 小尺寸的熔滴去除非金属夹杂物效果比大尺寸强。熔滴内大颗 = 粒的非金属夹杂物的减少较小颗粒的为强
第二讲 电渣重熔

世界各国电渣技术研究中心
乌克兰巴顿电焊研究院 俄罗斯电热设备科学院вниэто 美国联邦矿业局Albany冶金研究中心 加拿大哥伦比亚大学电渣实验室 德国Max Plank研究所等 东北大学钢铁冶金研究所 特殊钢研究室 钢铁研究总院冶金工艺所
三、电渣重熔工艺
1.电渣工艺制定的基本原则 2.电渣工艺参数的分类 3.钢锭结晶质量的衡量方法 4.工艺参数对目标参数的影响 5.电渣重熔参数的优化匹配 6.ESR过程工艺参数的变化及工艺控制模型
(2)基本控制参数
渣制度:
渣系、渣量GS或渣池深度Hs
电制度:
重熔电流、重熔电压
脱氧制度:
重熔过程向结晶器中加入脱氧剂种类、数量和方法
冷却水制度:
结晶器、底水箱冷却水的压力、流量、进水温度
(3) 目标参数
金属熔池形状及尺寸 极间距离Hem与电极埋入深度He 电极熔化速度Vm 渣池温度Tsl 渣皮厚度δs 电耗We 冷却水出口温度tw.o 局部冷却凝固时间LST 二次晶间距LⅡ
传统浇铸法与电渣重熔钢锭结构的比较
由于结晶器中的金属受到底部和侧面的强制水冷,冷 却速度很大,使金属的凝固只在很小的体积内进行, 使得固相和液相中的充分扩散受到抑制,减少了成分 偏析并有利于夹杂物的重新分配,图4 显示了用传统 的浇铸法和ESR方法生产H13热模具钢中铬和钼的比 较。同时,这种凝固方式可有效的控制结晶方向,可 以获得趋于轴向的结晶组织。因而可以看出重熔钢锭 具有以下的理想结构: 1一致的化学成分 2没有杂质、有害元素及非金属夹杂 3整个钢锭具有基本一致的结晶组织,消除了微观偏析 和气孔。
3)自下而上的顺序凝固条件保证了重熔金属锭 结晶组织均匀致密
图3 显示了传统的浇铸法与电渣重熔所获得的钢锭的 组织的区别,铸模里大量的钢液同时凝固导致了偏 析,偏析的程度取决于多相组织凝固的结晶行为,局 部非金属夹杂的累积及显微缝隙和缩孔是不可避免 的。 在电渣重熔过程中电极的熔化和熔融金属的结晶是同 时进行的。钢锭的上端始终有液态金属熔池和发热的 渣池,既保温又有足够的液态金属填充凝固过程中因 收缩产生的缩孔,可以有效的消除一般钢锭常见的疏 松和缩孔。同时金属液中的气体和夹杂也易于上浮, 所以钢锭的组织致密、均匀。
铸件常见缺陷的产生原因及防止方法
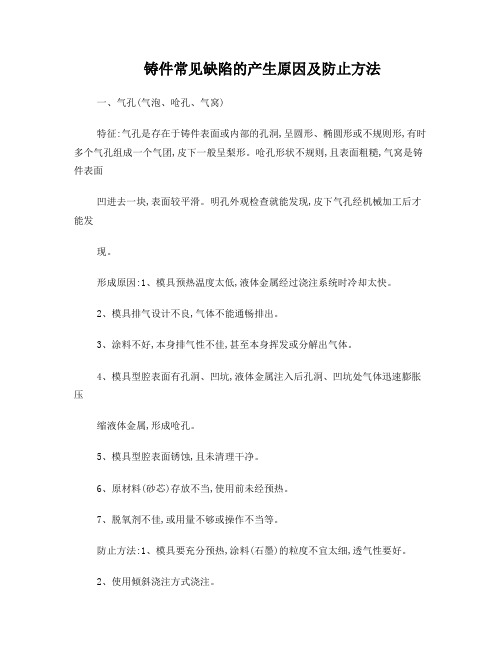
铸件常见缺陷的产生原因及防止方法一、气孔(气泡、呛孔、气窝)特征:气孔是存在于铸件表面或内部的孔洞,呈圆形、椭圆形或不规则形,有时多个气孔组成一个气团,皮下一般呈梨形。
呛孔形状不规则,且表面粗糙,气窝是铸件表面凹进去一块,表面较平滑。
明孔外观检查就能发现,皮下气孔经机械加工后才能发现。
形成原因:1、模具预热温度太低,液体金属经过浇注系统时冷却太快。
2、模具排气设计不良,气体不能通畅排出。
3、涂料不好,本身排气性不佳,甚至本身挥发或分解出气体。
4、模具型腔表面有孔洞、凹坑,液体金属注入后孔洞、凹坑处气体迅速膨胀压缩液体金属,形成呛孔。
5、模具型腔表面锈蚀,且未清理干净。
6、原材料(砂芯)存放不当,使用前未经预热。
7、脱氧剂不佳,或用量不够或操作不当等。
防止方法:1、模具要充分预热,涂料(石墨)的粒度不宜太细,透气性要好。
2、使用倾斜浇注方式浇注。
3、原材料应存放在通风干燥处,使用时要预热。
4、选择脱氧效果较好的脱氧剂(镁)。
5、浇注温度不宜过高。
二、缩孔(缩松)特征:缩孔是铸件表面或内部存在的一种表面粗糙的孔,轻微缩孔是许多分散的小缩孔,即缩松,缩孔或缩松处晶粒粗大。
常发生在铸件内浇道附近、冒口根部、厚大部位,壁的厚薄转接处及具有大平面的厚薄处。
形成原因:1、模具工作温度控制未达到定向凝固要求。
2、涂料选择不当,不同部位涂料层厚度控制不好。
3、铸件在模具中的位置设计不当。
4、浇冒口设计未能达到起充分补缩的作用。
5、浇注温度过低或过高。
防治方法:1、提高磨具温度。
2、调整涂料层厚度,涂料喷洒要均匀,涂料脱落而补涂时不可形成局部涂料堆积现象。
3、对模具进行局部加热或用绝热材料局部保温。
4、热节处镶铜块,对局部进行激冷。
5、模具上设计散热片,或通过水等加速局部地区冷却速度,或在模具外喷水,喷雾。
6、用可拆缷激冷块,轮流安放在型腔内,避免连续生产时激冷块本身冷却不充分。
7、模具冒口上设计加压装置。
8、浇注系统设计要准确,选择适宜的浇注温度。
电渣重熔工模具钢及电渣熔铸技术
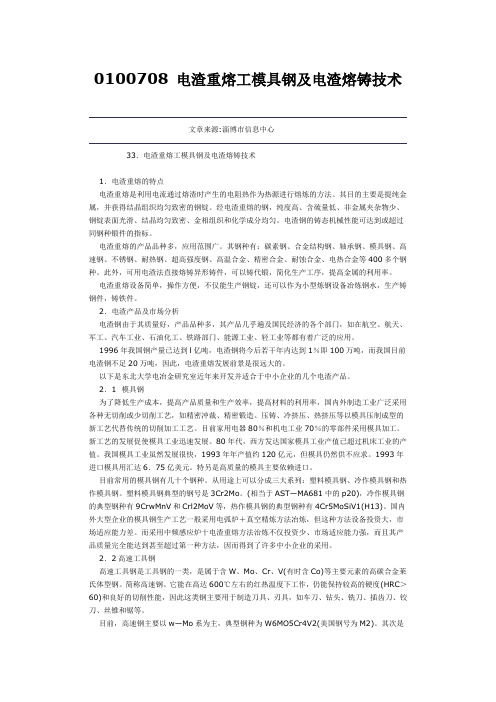
0100708 电渣重熔工模具钢及电渣熔铸技术文章来源:淄博市信息中心33.电渣重熔工模具钢及电渣熔铸技术1.电渣重熔的特点电渣重熔是利用电流通过熔渣时产生的电阻热作为热源进行熔炼的方法。
其目的主要是提纯金属,并获得结晶组织均匀致密的钢锭。
经电渣重熔的钢,纯度高、含硫量低、非金属夹杂物少、钢锭表面光滑、结晶均匀致密、金相组织和化学成分均匀。
电渣钢的铸态机械性能可达到或超过同钢种锻件的指标。
电渣重熔的产品品种多,应用范围广。
其钢种有:碳素钢、合金结构钢、轴承钢、模具钢、高速钢、不锈钢、耐热钢、超高强度钢、高温合金、精密合金、耐蚀合金、电热合金等400多个钢种。
此外,可用电渣法直接熔铸异形铸件,可以铸代锻,简化生产工序,提高金属的利用率。
电渣重熔设备简单,操作方便,不仅能生产钢锭,还可以作为小型炼钢设备冶炼钢水,生产铸钢件,铸铁件。
2.电渣产品及市场分析电渣钢由于其质量好,产品品种多,其产品几乎遍及国民经济的各个部门,如在航空、航天、军工、汽车工业、石油化工、铁路部门、能源工业、轻工业等都有着广泛的应用。
1996年我国钢产量已达到l亿吨,电渣钢将今后若干年内达到1%即100万吨,而我国目前电渣钢不足20万吨,因此,电渣重熔发展前景是很远大的。
以下是东北大学电冶金研究室近年来开发并适合于中小企业的几个电渣产品。
2.1 模具钢为了降低生产成本,提高产品质量和生产效率,提高材料的利用率,国内外制造工业广泛采用各种无切削或少切削工艺,如精密冲裁、精密锻造、压铸、冷挤压、热挤压等以模具压制成型的新工艺代替传统的切削加工工艺。
目前家用电器80%和机电工业70%的零部件采用模具加工。
新工艺的发展促使模具工业迅速发展。
80年代,西方发达国家模具工业产值已超过机床工业的产值。
我国模具工业虽然发展很快,1993年年产值约120亿元,但模具仍然供不应求。
1993年进口模具用汇达6.75亿美元。
特另是高质量的模具主要依赖进口。
常见铸件缺陷
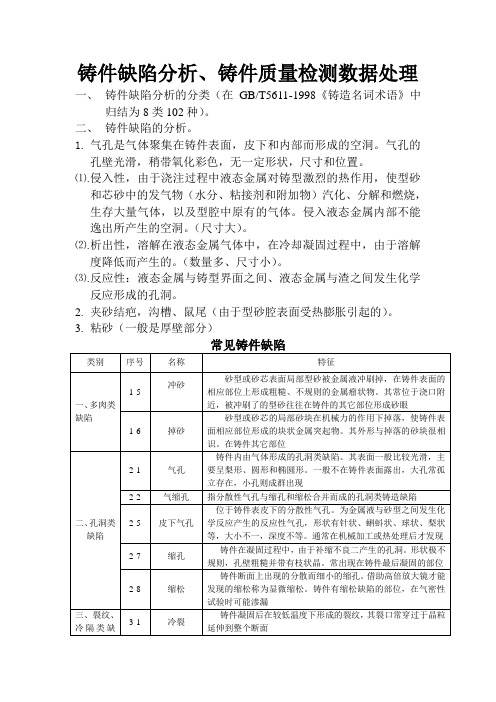
铸件缺陷分析、铸件质量检测数据处理一、铸件缺陷分析的分类(在GB/T5611-1998《铸造名词术语》中归结为8类102种)。
二、铸件缺陷的分析。
1.气孔是气体聚集在铸件表面,皮下和内部而形成的空洞。
气孔的孔壁光滑,稍带氧化彩色,无一定形状,尺寸和位置。
⑴.侵入性,由于浇注过程中液态金属对铸型激烈的热作用,使型砂和芯砂中的发气物(水分、粘接剂和附加物)汽化、分解和燃烧,生存大量气体,以及型腔中原有的气体。
侵入液态金属内部不能逸出所产生的空洞。
(尺寸大)。
⑵.析出性,溶解在液态金属气体中,在冷却凝固过程中,由于溶解度降低而产生的。
(数量多、尺寸小)。
⑶.反应性:液态金属与铸型界面之间、液态金属与渣之间发生化学反应形成的孔洞。
2.夹砂结疤,沟槽、鼠尾(由于型砂腔表面受热膨胀引起的)。
3.粘砂(一般是厚壁部分)铸件质量标准1、铸件的质量铸件的质量一般包括下述三个方面:(1)内在质量它包括铸件材料的质量(化学成分、金相组织、冶金缺陷、物理及力学性能和某些特殊性能等)和铸件的内容铸造缺陷等。
(2)外观质量外观质量一般包括铸件表面质量(表面粗糙度等)、尺寸和重量精度(尺寸公差、形位公差、重量公差等)和外表铸造缺陷等。
(3)使用质量它包括切削性、耐蚀性、耐磨性、焊接性和工作寿命等。
2、铸件的质量标准铸件的质量标准可分为下述几个方面:(1)铸件的材质标准其均由国家标准或行业标准规定,当然目前使用的标准中缺项还很多。
铸造工作者必须按产品图样中对材料的要求,严格按标准规定对材质进行检验,一般可浇注本体试块或单独浇注试块来控制铸件的力学性能。
要通过检查铸件的金相组织来间接控制铸件的力学性能,就必须找出两者之间的相互关系,由于这一过程与很多因素有关,各铸造厂只能在铸件特定的生产条件下,积累经验和数据,大体定出本厂的金相组织检查标准。
(2)铸件的精度标准其包括铸件尺寸及重量精度和铸件表面粗糙度,是铸件的一个重要质量指标。
电渣重熔锭ANF_6熔渣渣皮形成的分析
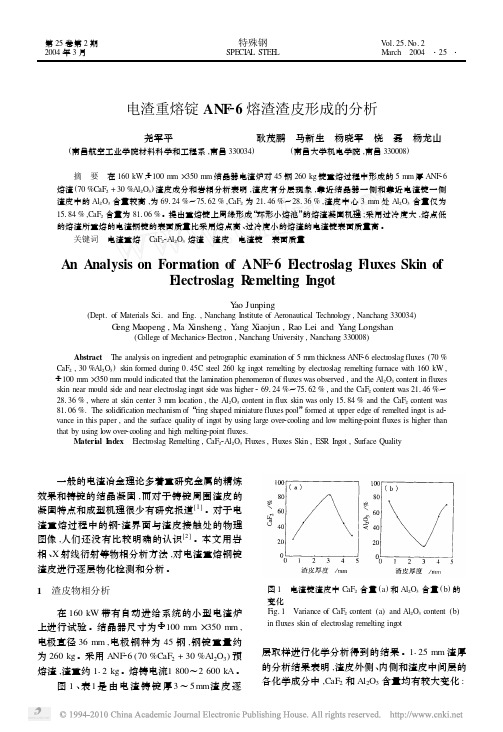
图 1 电渣锭渣皮中 CaF2 含量 (a) 和 Al2O3 含量 ( b) 的 变化 Fig. 1 Variance of CaF2 content (a) and Al2O3 content (b) in fluxes skin of electroslag remelting ingot
1 渣皮物相分析
在 160 kW 带有自动进给系统的小型电渣炉 上进行试验 。结晶器尺寸为Φ100 mm ×350 mm , 电极直径 36 mm ,电极钢种为 45 钢 ,钢锭重量约 为 260 kg。采用 ANF26 (70 %CaF2 + 30 %Al2O3) 预 熔渣 ,渣重约 112 kg。熔铸电流1 800~2 600 kA 。
关键词 电渣重熔 CaF22Al2O3 熔渣 渣皮 电渣锭 表面质量
An Analysis on Formation of ANF26 Electroslag Fluxes Skin of Electroslag Remelting Ingot
Yao J unping
(Dept. of Materials Sci. and Eng. , Nanchang Institute of Aeronautical Technology , Nanchang 330034)
参考文献 1 李正邦. 电渣熔铸. 北京 :国防工业出版社 ,1982 2 Dohnson ADJ ,Hellawell A. Application of Electroslag Melting. Metal2
lurgical Tranactions ,1992 (3) :1016
尧军平 ,男 ,39 岁 ,副教授 ,博士生 。从事近净成型理论
常见压铸件缺陷解决方法
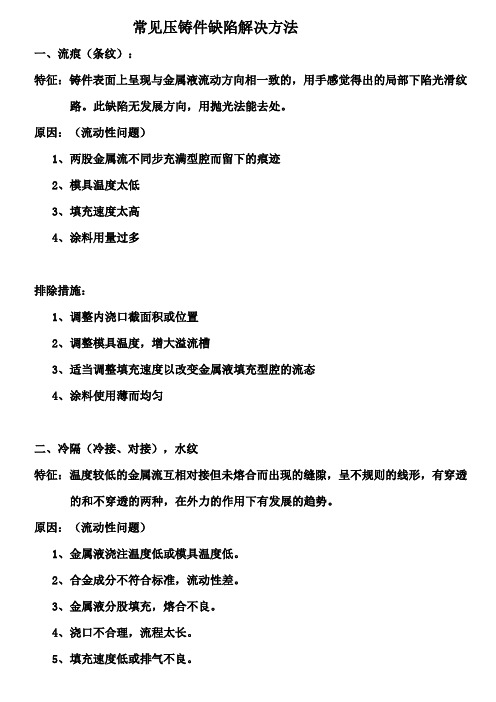
常见压铸件缺陷解决方法一、流痕(条纹):特征:铸件表面上呈现与金属液流动方向相一致的,用手感觉得出的局部下陷光滑纹路。
此缺陷无发展方向,用抛光法能去处。
原因:(流动性问题)1、两股金属流不同步充满型腔而留下的痕迹2、模具温度太低3、填充速度太高4、涂料用量过多排除措施:1、调整内浇口截面积或位置2、调整模具温度,增大溢流槽3、适当调整填充速度以改变金属液填充型腔的流态4、涂料使用薄而均匀二、冷隔(冷接、对接),水纹特征:温度较低的金属流互相对接但未熔合而出现的缝隙,呈不规则的线形,有穿透的和不穿透的两种,在外力的作用下有发展的趋势。
原因:(流动性问题)1、金属液浇注温度低或模具温度低。
2、合金成分不符合标准,流动性差。
3、金属液分股填充,熔合不良。
4、浇口不合理,流程太长。
5、填充速度低或排气不良。
6、比压偏低。
排除措施:1、适当提高浇注温度和模具温度。
2、改变合金成分,提高流动性。
3、改进浇注系统,加大内浇口速度,改善填充条件。
4、改善排溢条件,增大溢流量。
5、提高压射速度,改善排气条件。
6、提高比压三、擦伤(粘模伤痕)特征:顺着脱模方向,由于金属粘附,模具制造斜度太小而造成铸件表面的拉伤痕迹, 严重时成为拉伤面。
产生原因:(粘着现象)1、型芯、型壁的铸造斜度太小或出现倒斜度。
2、型芯、型壁有压伤痕。
3、合金粘附模具。
4、铸件顶出偏斜,或型芯轴线偏斜。
5、型壁表面粗糙。
6、涂料常喷涂不到。
7、铝合金中含铁量低于0.6%。
排除措施:1、修正模具,保证制造斜度。
2、打光压痕。
3、合理设计浇注系统,避免金属流对冲型芯、型壁,适当降低填充速度。
4、修正模具结构。
5、打光表面。
6、涂料用量薄而均匀,不能漏喷涂料。
7、适当增加含铁量至0・6〜0・8%。
四、凹陷(缩陷、塌边)特征:铸件平滑表面上出现的凹瘪的部分,其表面呈自然冷却状态。
产生原因:(模具设计、环境问题)1、铸件结构设计不合理,有局部厚实部位,产生热节。
电渣重熔渣的存在状态

电渣重熔渣的存在状态1.引言1.1 概述电渣重熔渣是在电弧炉熔炼过程中生成的一种矿渣,由于电弧炉使用电弧和高温来熔化废钢和其他金属材料,产生的熔融金属表面上会形成一层渣层。
这种渣层主要由非金属性物质组成,如氧化物、硅酸盐、氧化铁等。
电渣重熔渣的存在状态与其物理性质密切相关,这也是本文将讨论的主要内容。
在电弧炉炼钢过程中,渣层的存在是不可避免的,但其具体形成原因和物理性质还需要进一步研究。
了解电渣重熔渣的存在状态对于优化电弧炉冶炼工艺、提高金属回收率以及减少环境污染具有重要意义。
本文主要通过对电渣重熔渣的形成原因和物理性质的分析探讨,旨在揭示电渣重熔渣的存在状态及其影响因素,并对进一步研究该领域提出展望。
通过对电渣重熔渣的深入研究,可以为电弧炉冶炼过程的优化提供科学依据,同时也有助于对于资源利用和环境保护的进一步探索。
1.2文章结构文章结构的目的是为了给读者提供一个清晰的指南,使读者能够更好地理解和跟随文章的内容和逻辑顺序。
以下是本文的详细结构:1. 引言1.1 概述:介绍电渣重熔渣的背景和重要性,以及本文的研究意义。
1.2 文章结构:概述本文的结构和各个部分的内容。
1.3 目的:说明本文的研究目标和意图。
2. 正文2.1 电渣重熔渣的形成原因:探讨电渣重熔渣产生的主要原因,可能涉及到的工艺参数和条件。
2.2 电渣重熔渣的物理性质:详细描述电渣重熔渣的物理性质,例如化学成分、晶体结构、密度、粒径分布等。
3. 结论3.1 电渣重熔渣的存在状态总结:总结电渣重熔渣的存在状态,包括其在工业生产中的应用和影响。
3.2 对电渣重熔渣的进一步研究展望:展望未来对电渣重熔渣的研究方向,提出可能的改进和应用前景。
通过以上结构,读者可以清晰地了解本文的内容和组织形式,并能够更好地理解和消化文章所要传达的信息。
1.3 目的本文的目的是探讨电渣重熔渣的存在状态。
通过对电渣重熔渣的形成原因和物理性质进行研究分析,旨在深入了解电渣重熔渣在工业生产中的实际应用和存在状态。
常见铸造缺陷的成因与消除

常见铸造缺陷的成因与消除任何铸造缺陷都直接影响着企业的经济效益与社会效益。
可惜的是,未有一个铸造厂是没有铸造缺陷的。
现列出几种主要(常见)的铸造缺陷,如气孔,缩孔,夹渣及球化不良等来分析它们产生的原因并提出消除措施,与诸君共议。
一气孔(Gas hole)1、产生原因金属液中的气体未彻底释放出来和铸型内的气体侵入进金属液中,从而滞留在凝固后的铸件之内(图1)。
(1)金属液中的气体来源 g 劣质炉料含泥沙、油垢、锈蚀及湿气等,熔炼中生成大量的O、H、N等气体和渣釉;炉温低;精练不够;浇注温度低,浇注时间长及浇注速度慢、浇包潮湿等。
上述因素,都促使金属液表面过早形成氧化膜而凝固,气体虽然挣扎着向外逃逸但却无法实现。
反映在铸件上则成为向上的“梨形”气泡,梨把朝内。
气孔表面光滑。
通常称这种气孔为“析出性气孔”(图2)。
在薄壁件的表皮下或外观形成密集的小圆孔或针孔(图3)。
(2)型腔内气体来源砂型水分≥4.5%,死灰>12%,透气性差;水玻璃砂未干透(仅吹C O2是不够的);树脂砂的树脂量>1.8%,固化剂量也多;消失模厚大,比重大又未干透,涂料层>2㎜且未干透;粗大砂芯樁的过实,未中空,气体未引出型外;合箱后等待浇注时间>8h,或过夜等,使铸型和砂芯返潮。
(3)工艺设计不合理直浇道粗大,金属液不能很快充满或断流而将气体卷入;内浇口喷射,金属液紊乱;冒口处低位,排气孔少;底注,温度场为上低下高,导致金属液迅速形成氧化膜而快速凝固。
上述(2)、(3)所产生的气体在排气不畅且型内压力大的情况下,气体被卷入或钻入未凝固的金属液内。
通称这种气孔为“侵入性气孔”(图4)。
气孔也似梨状而梨把朝外。
2 消除方法消除金属液中可能产生气体的一切因素;提供气体从金属液内和铸型(砂芯)中容易逸出的机会或条件。
应当着重指出的是,彻底排出金属液中的气体是第一位的!具体做法:选用优质、干净干燥的炉料,提高熔炼温度(灰铁1520℃,铸钢1650℃,不锈钢1680℃),充分精炼脱气与静置,高温且快速浇注,消失模浇注温度比砂铸高50℃,因为泡沫燃烧是一个吸热过程,充型前沿的金属液温降比随后之金属液的温降大得多。
电渣重熔原理

2 电渣重熔原理2.1 渣池电渣重熔工艺的核心部分是熔池。
金属从熔池上方进入渣池,然后被加热、熔化、精炼和过热,并且承受振动、搅拌和电化学作用。
因此,形成渣池并使其保持在合适的条件下,显然是很重要的。
渣有如下几方面的作用。
(1)发热元件的作用重熔过程中热量通过焦耳效应产生,也就是通常的电阻发热定律。
因此,应该确保渣阻与供给功率的电压、电流之间的正确平衡。
所用的大多数渣的电阻率在熔炼温度下为0.2.0.ssl-cm ,熔炼温度通常比金属熔化温度高200 -- 3001C。
显然,在该温度下,渣既要呈液态,又要稳定,所以重熔电流、电压、渣池深度和渣电阻率之间的关系很复杂。
好的电渣重熔操作必须把它们调到最佳值。
(2)熔渣对于非金属材料来说是熔剂当金属电极进入到渣池中时,电极端部达到其熔化温度,就会形成金属熔化膜。
当熔化金属与熔渣接触时,熔化的金属在汇聚成熔滴的同时,暴露的非金属夹杂将溶解在渣里。
因此,渣的成分必须能溶解杂质而又不影响其性质,为此,在重熔时必须采取连续调整渣成分的步骤。
(3)渣是电渣重熔工艺的精炼剂重熔过程中的化学反应主要部位是电极端部渣/金界面,这里金属膜条件对于快速反应是最理想的。
(4)涟起保护金属免受污染的作用渣对于反应成分来说,起着传递介质的作用。
由于金属在渣下熔化和凝固,被熔化的金属绝不会与大气接触而被直接氧化,而这种氧化在常规工艺中是不可避免的。
另一方面,由于熔渣可以传递反应物质,如氧和水蒸气,所以使用惰性气体做保护气氛非常必要。
(5)位形成结晶器衬由于结晶器壁温度维持在渣熔点以下,那么熔渣和结晶器壁之间必定有凝固渣壳。
这层渣壳起着结晶器衬的作用,金属锭在衬里形成并凝固,至少在稳定操作条件下,渣壳起着上述作用。
在环形结晶器(短模)情况下,锭表面渣皮很少。
可能存在差异。
为了实现上述作用,渣必须具有某些相当明确的性质。
一般情况下,它的熔化温度应在被熔化金属的熔化温度以下。
操作温度显然高于金属熔点,一般约高200 -- 300℃。
电渣熔铸
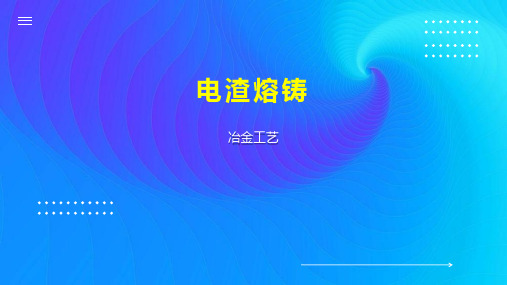
谢谢观看
设备
电渣熔铸的基本设备包括电渣炉、结晶器,电源变压器;辅助设备包括熔化及浇注渣装置,装配及焊接自耗 电极设备等与电渣重熔完全相同。惟有其结晶器的结构与电渣重熔的结晶器差别很大,通常在电渣熔铸中也称之 为铸模。它具有两种功能:一是不断地消耗自耗电极金属而聚集液态金属;二是将金属液凝固铸造成型。它的形 状、尺寸及复杂程度根据具体零件的形状、尺寸及选定的电渣熔铸工艺方案来决定,归纳起来可分为4类:
原理
电渣熔铸过程与电渣重熔基本相同。如图1所示,来自短的电流通过自耗电极进入渣池,产生电阻热将渣加热 至高温,自耗电极的顶部被渣池逐渐加热熔化形成金属熔滴,金属熔滴从电极端头脱落,穿过渣池进入金属熔池, 由于水冷结晶器的冷却作用,液态金属在铜制异型水冷结晶器内逐渐形成异型铸件。
图1电渣熔铸原理图
电渣熔铸
冶金工艺
01 原理
目录
02 冶金特点
03 设备
04 产品
05 产品的铸态性能
电渣熔铸(electroslag casting)是一种使金属精炼和铸造成型一次完成,生产优质合金铸件的电渣冶金工 艺。它是利用电流通过液渣所产生的电阻热,不断地将金属电极熔化,熔化的金属汇聚成滴,穿过渣层滴入金属 熔池,同时在异型水冷模内凝固成铸件的技术。
图2带熔合坯的电渣熔铸示意图
(3)金属转注结晶器的电渣熔铸。自耗电极熔化的钢液聚集在活动熔化室中,熔化室中的液态金属部分或全 部地转移浇注到结晶器(铸模)型腔,通常称为金属转注电渣熔铸法或简称电渣转注。自耗电极与铸件不在同一 轴线上,熔铸过程中熔化装置相对于固定的铸模移动,直到铸模中充满电渣金属为止。用此方法可以获得复杂的 异型铸件,不受自耗电与铸件之间截面比等条件的限制,而且可能制造双金属或多层金属铸件。
电渣重熔
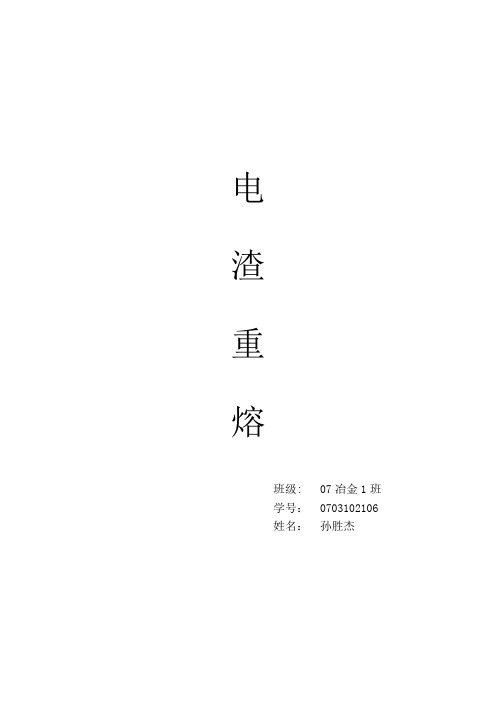
电渣重熔班级: 07冶金1班学号: 0703102106姓名:孙胜杰电渣重熔孙胜杰关键词:电渣重熔摘要:电渣重熔(electroslag remelting简称ESR)是把转炉、电弧炉或感应炉等冶炼的钢铸造或锻压成为电极,通过熔渣电阻热进行二次重熔的精炼工艺。
其主要目的是提纯金属并获得洁净组织均匀致密的钢锭。
经电渣重熔的钢,纯度高、含硫低、非金属夹杂物少、钢锭表面光滑、洁净均匀致密、金相组织和化学成分均匀。
电渣钢的铸态机械性能可达到或超过同钢种锻件的指标。
电渣钢锭的质量取决于合理的电渣重熔工艺和保证电渣工艺的设备条件。
正文:电渣重熔是利用电流通过熔渣时产生的电阻热作为热源进行熔炼的方法。
其主要目的是提纯金属并获得洁净组织均匀致密的钢锭。
经电渣重熔的钢,纯度高、含硫低、非金属夹杂物少、钢锭表面光滑、洁净均匀致密、金相组织和化学成分均匀。
电渣钢的铸态机械性能可达到或超过同钢种锻件的指标。
电渣钢锭的质量取决于合理的电渣重熔工艺和保证电渣工艺的设备条件。
电渣重熔的产品品种多,应用范围广。
其钢种有:碳素钢、合金结构钢、轴承钢、模具钢、高速钢、不锈钢、耐热钢、超高强度钢、高温合金、精密合金、耐蚀合金、电热合金等400多个钢种。
此外,可用电渣法直接熔铸异形铸件,可以铸代锻,简化生产工序,提高金属的利用率。
电渣熔铸工艺从根本上解决了一般铸造工艺的主要矛盾,它综合了电渣重溶-获得高冶金质量的金属和铸造-浇铸异型零件精化毛坯的长处,并具有与普通冶炼的变形金属相近的致密组织以及无各向异性的特点。
与普通锻件相比,电渣熔铸件的各项性能指标完全达到同钢种的变型金属指标,甚至还避免了锻件的一些不足之处。
一.电渣重熔的工作原理其原理是电流通过液态渣池渣阻热,将金属电极熔化,熔化的金属汇集成熔滴,滴落时穿过渣层进入金属熔池,然后于水冷结晶器中结晶凝固成钢锭。
二.电渣重熔的基本过程在铜制水冷结晶器内盛有熔融的炉渣,自耗电极一端插入熔渣内。
电炉铸造中常见缺陷防治方法汇总
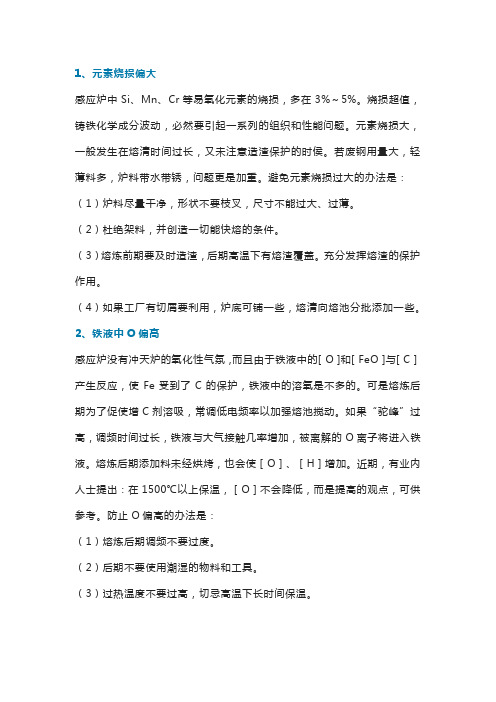
1、元素烧损偏大感应炉中Si、Mn、Cr等易氧化元素的烧损,多在3%~5%。
烧损超值,铸铁化学成分波动,必然要引起一系列的组织和性能问题。
元素烧损大,一般发生在熔清时间过长,又未注意造渣保护的时侯。
若废钢用量大,轻薄料多,炉料带水带锈,问题更是加重。
避免元素烧损过大的办法是:(1)炉料尽量干净,形状不要枝叉,尺寸不能过大、过薄。
(2)杜绝架料,并创造一切能快熔的条件。
(3)熔炼前期要及时造渣,后期高温下有熔渣覆盖。
充分发挥熔渣的保护作用。
(4)如果工厂有切屑要利用,炉底可铺一些,熔清向熔池分批添加一些。
2、铁液中O偏高感应炉没有冲天炉的氧化性气氛,而且由于铁液中的[O]和[FeO]与[C]产生反应,使Fe受到了C的保护,铁液中的溶氧是不多的。
可是熔炼后期为了促使增C剂溶吸,常调低电频率以加强熔池搅动。
如果“驼峰”过高,调频时间过长,铁液与大气接触几率增加,被离解的O离子将进入铁液。
熔炼后期添加料未经烘烤,也会使[O]、[H]增加。
近期,有业内人士提出:在1500℃以上保温,[O]不会降低,而是提高的观点,可供参考。
防止O偏高的办法是:(1)熔炼后期调频不要过度。
(2)后期不要使用潮湿的物料和工具。
(3)过热温度不要过高,切忌高温下长时间保温。
3、铁液C量低于预期铁液温度超过平衡温度,反应SiO2+2C=Si+2CO向右进行,造成铁液降C增Si。
所以配料时不能忘了补C。
要掌握本厂的降C量,把C量如数补足。
还要提醒一点,灰铸铁后期调整成分,要采取先Mn再C后Si的顺序。
4、铸件机加工后,发现有裂隙状气孔裂隙状气孔是N气孔的特征。
当[N]超限时容易发生,铁液中非金属夹杂物多,发生的几率更高。
“病从口入”,所以要限制电弧炉废钢用量,电弧炉废钢的[N]高,而转炉废钢则不然。
更要防止混入含N高的废合金钢料,如高锰钢、耐热的高铬铁素体钢和铬锰氮钢,以及奥化体钢等。
当然这些合金钢带来的Mn、Cr、N、Ni对于铁素体球铁也是忌讳的。
铸件“渣眼”缺陷分析及其应对措施

铸件“渣眼”缺陷分析及其应对措施浇注的时候,熔渣随液体金属进入型腔,形成了铸件的“渣眼”缺陷。
在铸造生产中,有很多铸件(如图1)都是因为出现“渣眼”而报废的,尤其是在一些要求较高的机床液压件的生产上。
铸件出现渣眼的原因很多,有熔炼、浇注操作、造型工艺方面的原因,也有浇注系统设置方面的因素等。
下文分析一下原因以及应对措施。
1.熔炼过程中除渣措施铸铁在熔炼过程会有许多渣子产生,人们总希望在铁液进入浇包之前能彻底地实现渣、铁分离。
一方面,渣子进入浇包也就增加了被冲入型腔的危险,另一方面在浇包中进行扒渣操作会降低铁液的温度,因此铸铁熔炼过程中的放渣操作就显得特别重要。
在冲天炉内,由焦炭的灰分、砂粒及炉衬剥落耐火材料等熔成黏度很大的熔渣,不易排出。
在熔炼时加入适量的石灰石造渣剂,在炉内遇热分解为CaO后,与炉渣反应生成低熔点的盐类物质即熔渣,这些熔渣会随着铁液一起流到前炉中,由于密度不同,会发生分层,铁液在下,熔渣漂在上部,熔炼一段时间后应及时打开前炉上的出渣孔进行放渣,实现渣、铁分离。
如果造渣剂不足,渣子会变得粘稠,不易流出。
熔炼过程中,应适当提高铁液温度。
铁液温度低,渣子粘稠不易放出;另外,铁液的温度太低,悬浮在金属液中的渣子,要上浮至金属液的上部而遇到的阻力较大,也难去除掉。
2.浇注前及浇注过程的中除渣措施铁液由前炉流入浇包,部分渣子难免会随之而入。
那么浇注前,必须把浇包中的熔渣全部除尽,以免熔渣进入铸型造成渣眼缺陷。
具体地说就是在浇包中进行“扒渣”作业。
进行扒渣操作时,比较有效的办法是首先要在浇包金属液的表面撒集渣剂,使渣子与半熔的集渣剂粘在一起,即可用铁棍挑出或扒出。
常用的集渣剂主要是珍珠岩或火山灰。
珍珠岩是较理想的集渣剂,我国南方一些工厂习惯用稻草灰作集渣剂,稻草灰对金属液有保温作用,但对炉渣的集渣效果较差(对炉渣有轻微的激冷作用)。
北方的某些小厂习惯在浇包内金属液表面撒干砂,干砂虽然对漂浮的熔渣有一定的激冷作用,使渣子开始凝结,但干砂完全不熔,对炉渣的集渣作用甚小。
电渣重熔 熔渣的 物理化学 性能简介
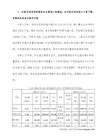
电渣重熔熔渣的物理化学性能简介张东泽(power)熔渣的物理化学性能简介一、电渣熔铸对渣的要求在电渣熔铸过程中,液态渣具有十分重要的作用,其功能主要为:1、熔铸热源2、控制熔铸金属的化学成分3、净化作用4、绝缘隔热质作用5、创造了一个温度高于金属熔池的贮热地渣在电渣熔铸过程中起着十分重要的作用,为了满足各项技术经济指标的要求,必须从相图、界面张力、粘度、比电导、密度、比热、蒸汽压、透气性等项物理化学性质进行综合考虑,才能选中合理的渣型。
二、相图电渣熔铸的渣系主要组成是CaF2?CaO、MgO和Al2O3,也有包含镁和钡的氟化物及钡、钛氧化物,当重熔低熔点的金属或合金时也有采用氟化渣系,电渣按成分分类可分为:(1)仅由氟化物组成的;(2)由氟化物及氧化物组成;(3)仅由氧化物组成的。
而在电渣铸熔中普遍应用氟化物-氧化物渣系,它有指化钙-氧化钙、氟化钙-氧化铝、氟化钙-氧化钙-氧化铝、氟化钙-氧化镁-氧化铝等渣系1、氟化物单元系渣⑴氟化钙:氟化钙或是萤石可在电渣炉、电弧炉或感应炉内用石墨坩埚精精炼,去除其中的氢、硫和部分硅,除氢过程可使氧化钙增加2%,甚至5%纯氟化钙的熔点是1419℃,工业萤石的熔点约为1380℃。
在电渣炉中使用萤石的含量因其电阻值低而受到限制,如采用单一氟化渣时,氟化钙较为合适,因其电阻在氟化物中是最高的一种。
⑵氟化镁:具有比氟化钙高的蒸气压和稍低的熔点(1263℃),因之热稳定性较差又由于电性能不合适,帮不能单独使用,一般如使用氟化镁其含量不得超过20~30%,氟化镁一般含有结晶水10%,使用前需将其去除,去除结晶水将带来的氧化镁它比萤石水解生成的氧化钙脱硫能力差,因此当熔铸需要保硫材料时,可采用氟化镁-氟化钙渣系。
2、二元渣系⑴氟化钙-氟化镁:低共熔温度为945℃,低共熔成分为51%的氟化镁,49%的氟化钙,利用此渣系按其低共熔成分配渣重熔有色金属。
氟化镁的热稳定性差,一般不超过20~30%。
1.铁水和熔渣喷溅与爆炸
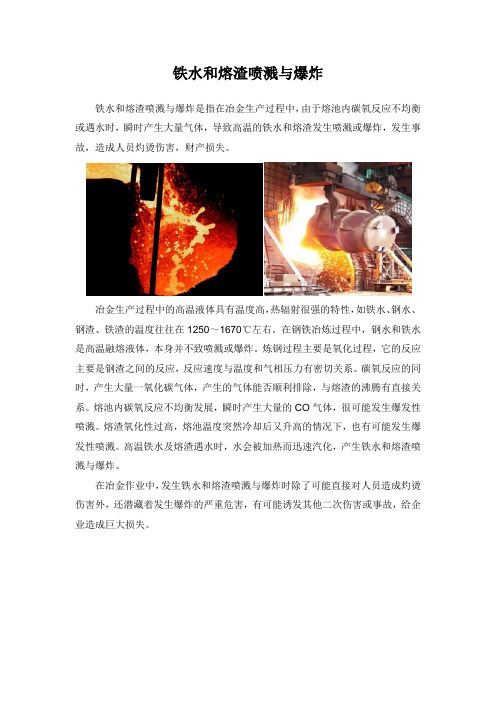
铁水和熔渣喷溅与爆炸铁水和熔渣喷溅与爆炸是指在冶金生产过程中,由于熔池内碳氧反应不均衡或遇水时,瞬时产生大量气体,导致高温的铁水和熔渣发生喷溅或爆炸,发生事故,造成人员灼烫伤害,财产损失。
冶金生产过程中的高温液体具有温度高,热辐射很强的特性,如铁水、钢水、钢渣、铁渣的温度往往在1250~1670℃左右。
在钢铁冶炼过程中,钢水和铁水是高温融熔液体,本身并不致喷溅或爆炸。
炼钢过程主要是氧化过程,它的反应主要是钢渣之间的反应,反应速度与温度和气相压力有密切关系。
碳氧反应的同时,产生大量一氧化碳气体,产生的气体能否顺利排除,与熔渣的沸腾有直接关系。
熔池内碳氧反应不均衡发展,瞬时产生大量的CO气体,很可能发生爆发性喷溅。
熔渣氧化性过高,熔池温度突然冷却后又升高的情况下,也有可能发生爆发性喷溅。
高温铁水及熔渣遇水时,水会被加热而迅速汽化,产生铁水和熔渣喷溅与爆炸。
在冶金作业中,发生铁水和熔渣喷溅与爆炸时除了可能直接对人员造成灼烫伤害外,还潜藏着发生爆炸的严重危害,有可能诱发其他二次伤害或事故,给企业造成巨大损失。
1、产生铁水和熔渣喷溅与爆炸的原因是:(1)在熔池中熔渣过多、渣子粘,流动性不好以及熔池沸腾差的情况下,便加入氧化剂。
由于碳氧反应产生大量一氧化碳气体,因溶渣的粘性太大,使气体不能顺利排除,同时促使溶池产生巨大压力,在此瞬间形成大喷溅或大爆炸。
(2)由于低温操作,在熔池尚未形成一定性能的碱性渣或温度低的情况下,就急于集中往炉内加入氧化剂,所加入的氧化剂未完全起作用浮在熔渣中,当熔池温度上升或从炉门抽管吹氧时,达到碳氧反应条件,突然进行急剧的碳氧化反应,产生大量气体,这些气体不能顺利排除,导致产生大喷溅或爆炸。
(3)由于熔池温度过高或熔池的上下温差大。
当炉子倾动或抽管吹氧时,促使熔池形成对流作用而引起激烈反应,产生大喷溅或爆炸。
(4) 高温铁水及熔渣遇水时,水会被加热而迅速汽化,产生铁水和熔渣喷溅与爆炸。