八大浪费知识培训
八大浪费的培训

REPORT
06
实战演练:团队如何开展减 少浪费活动
制定减少浪费计划和目标
分析现状
对现有的生产流程、物料使用、人员配置等进行全面 分析,找出存在的浪费现象。
制定目标
根据分析结果,制定具体的减少浪费目标,如降低不 良品率、减少库存量等。
企业管理制度不健全或执行不力,导致员工行为不规范,造成资源 浪费。
REPORT
04
识别与消除浪费方法论述
现场观察法
直接观察工作流程
深入现场,实地查看工作流程,了解实际操作情况,发现 浪费现象。
与员工交流
与员工面对面交流,了解他们的想法和建议,共同发现浪 费问题。
记录并分析
详细记录观察到的浪费现象,分析原因,提出改进措施。
01
浪费概述与分类
浪费定义及影响
浪费定义
在生产和服务过程中,未能创造 价值或增加成本的活动,即资源 (时间、人力、物力、财力等) 的无效或低效使用。
浪费影响
导致企业成本增加、效率降低、 质量不稳定、客户满意度下降等 负面影响,严重制约企业的竞争 力和可持续发展。
八大浪费简介
不良、修理的浪费
01
指因产品质量问题导致的浪费,包括不良品的产生、返修、报
员工对操作不熟悉,导致动作不连贯 、效率低下。
等待时间浪费
生产计划不合理
生产计划安排不当,导致员工等待物料、设备、 上道工序等。
设备故障
设备故障频发,导致生产中断,员工需要等待设 备维修。
物料供应不及时
物料供应不及时或物料品质问题,导致生产停滞 ,员工等待物料到来。
加工过剩浪费
企业八大浪费培训ppt课件ppt
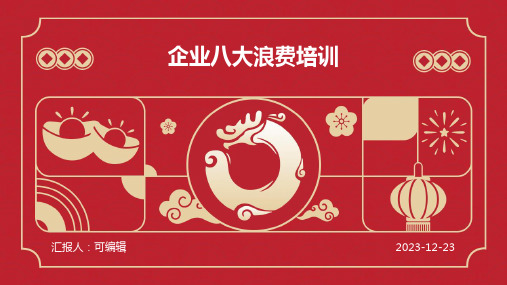
应对措施与解决方案
3. 提高员工技能水平
加强员工技能培训和技能认证,提高员工的技能水平 和操作熟练度,确保员工能够按照标准操作规程进行 生产,减少因操作不当导致的加工浪费。
表现
设备空转、操作员等待、生产流程停 滞等。
产生原因与影响
产生原因
生产计划安排不合理、设备故障率高、物料供应不及时等。
影响
降低生产效率、增加生产成本、影响产品质量和客户满意度等。
应对措施与解决方案
应对措施
优化生产计划、加强设备维护保养、提高物料供应的及时性等。
解决方案
采用精益生产管理、引入自动化和智能化设备、建立快速响应机制等。
引入自动化和智能化设备
通过自动化和智能化设备来替代人工操作, 提高生产效率。
08 管理浪费
CHAPTER
定义与表现
定义
管理浪费是指企业在管理过程中出现的资源浪费现象,如决策失误、组织结构 不合理、流程繁琐等。
表现
管理浪费通常表现为工作效率低下、资源分配不均、信息传递不畅、决策缓慢 等问题。
产生原因与影响
原因
管理浪费的产生原因主要包括管理层决策能力不足、组织结构复杂、缺乏有效的 管理制度和流程等。
影响
管理浪费会导致企业资源浪费、效率低下、竞争力下降,甚至可能导致企业破产 倒闭。
应对措施与解决方案
应对措施
提高管理层决策能力、优化组织结构 、简化流程、建立有效的管理制度和 流程等。
解决方案
引入先进的管理理念和方法,加强内 部培训和人才培养,建立科学的管理 体系和流程,提高企业整体的管理水 平。
八大浪费识别和现场改善培训

提升产品质量
通过消除生产过程中的不良品和 返工,提高产品的一次性合格率。
优化工艺和设备,减少产品缺陷 和质量问题的出现。
提高员工的质量意识和技能水平, 确保产品质量的稳定和提高。
03
现场改善的方法与技巧
5S管理
整顿
对整理后的物品进行分类、标 识、定位,方便取用和归位。
清洁
维持整理、整顿、清扫后的状 态,形成制度化、规范化的管 理。
由于产品设计或制造过程中的缺陷, 导致产品不符合要求或性能下降。
过程
过于复杂的生产流程或工作方法,导 致效率低下。
识别方法与工具
方法
观察、记录和分析生产过程中的 各种活动,识别哪些是创造附加 值的,哪些不是。
工具
包括流程图、价值流图、5S管理 (整理、整顿、清洁、清洁检查 、素养)等。
案例分析
案例一
团队协作增强
培训后,员工之间的团队协作意识增强,能够更好地协同工 作,共同推进改善工作。
培训反馈与改进
反馈收集
通过问卷调查、面谈等方式收集员工对培训的反馈意见。
改进措施
根据员工的反馈意见,对培训内容、方式等进行调整和改进,以提高培训效果。
THANKS
感谢观看
不良品
由于产品设计或制造过程 中的缺陷,导致产品不符 合要求或性能下降。
定义与分类
等待时间
生产过程中的空闲时间, 等待原材料、零件或工具。
运输
不必要的物料和产品移动, 导致时间和资源和 成品,增加了存储和管理 成本。
定义与分类
动作
产品缺陷
不必要的操作或动作,如过多的检查、 搬运等。
料。
标准化作业
确保换模过程中的操作步骤和 作业方法标准化,提高换模效
企业八大浪费培训ppt课件ppt
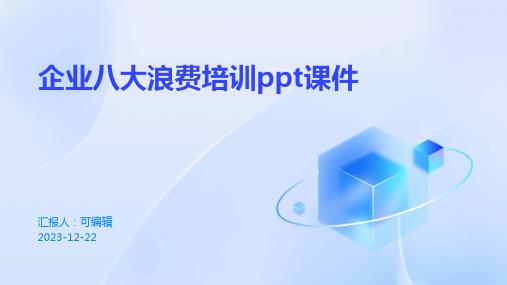
提高操作员技能水平
定期对操作员进行培训和考核,提高 操作员技能水平,减少操作误差导致 的制程问题。
优化工艺参数设置
根据实际生产情况,不断优化工艺参 数设置,减少制程中的误差和不良品 率。
THANKS
感谢观看
ABCD
预测不准确
企业对市场需求预测不准确,导致库存过多或过 少,影响生产和销售。
生产计划不准确
生产计划不准确,导致生产过剩或不足,进而影 响库存。
解决方案
制定科学合理的库存管理计划
根据企业实际情况和市场预测,制定合理的库存管理计划。
提高预测准确性
通过市场调研和数据分析,提高对市场需求的预测准确性。
提升管理水平,加强信息沟通 ,提高决策效率。
04
搬运的浪费
定义与特点
定义:搬运是指在生产过程中,将原材 料、半成品、成品等在设备、生产线、 仓库等不同地点之间进行移动和传递。
降低生产效率:搬运过程中可能会造成 物品损坏、延误生产进度等问题,影响 生产效率。
增加运输成本:需要使用运输工具和人 力进行搬运,增加了运输成本。
04
市场预测不准确
企业未能准确预测市场需求, 导致生产计划与实际需求存在 偏差,从而产生生产过剩。
生产计划不合理
企业内部生产计划安排不当, 如生产批次过小、批量过大等
,导致生产过剩。
客户需求变化
客户需求变化导致企业生产计 划调整不及时,从而产生生产
过剩。
销售能力不足
企业销售能力不足,无法及时 消化生产出的产品,导致生产
动作的浪费
定义与特点
动作浪费
指在生产过程中由于操作不当、设备故障、流程设计不合理等原因导致的资源 、时间、人力等浪费的现象。
精益生产之八大浪费培训

精益生产之八大浪费培训精益生产是一种通过持续改进和优化生产过程,减少浪费,提高效率的管理方法。
根据精益生产理念,有八大种类的浪费,分别是:过产、等待、运输、过加工、库存、运动、制造缺陷和不必要的动作。
以下是关于这八大浪费的培训内容。
1. 过产:过产是指生产数量超过需求的情况,通常是由于生产计划不准确或生产线设定不合理导致的。
培训中应教授如何制定准确的生产计划,提高生产线的灵活性,并在必要时采取合理的工序调整。
2. 等待:等待是指生产过程中的停工或停滞,可能是由于设备故障、缺少原材料或其他原因引起的。
培训中应重点介绍如何优化设备维护计划,提前准备原材料,并确保及时供应以减少生产线上的等待时间。
3. 运输:运输是指在生产过程中不必要的物料搬运和运输。
培训中应教授如何优化生产布局,减少物料的搬运距离,并合理规划物料存储位置,以降低运输的浪费。
4. 过加工:过加工是指对产品进行超出需求范围的加工。
培训中应着重介绍如何评估产品需求,制定合理的加工标准,并确保每个工序都有明确的目标和要求,避免不必要的过加工。
5. 库存:库存是指生产过程中积压的未完成产品数量,其中包括在制品、原材料和成品。
培训中应教授如何通过优化生产计划、采用just-in-time (JIT) 生产方式以及改进供应链管理来减少库存。
6. 运动:运动是指工人在生产过程中的不必要的移动和动作。
培训中应教授如何优化生产布局,将相关设备和物料放置在便捷的位置,从而减少工人的移动和动作,提高生产效率。
7. 制造缺陷:制造缺陷是指在生产过程中出现的质量问题,需要重新加工或修复。
培训中应着重强调质量控制的重要性,教授如何通过使用质量管理工具和技术,如 Six Sigma 方法,以及提供员工培训和持续监测来减少制造缺陷。
8. 不必要的动作:不必要的动作是指在生产过程中不必要的工作步骤或冗余操作。
培训中应强调流程优化的重要性,通过员工参与和持续改进来识别和消除不必要的动作,从而提高生产效率。
工厂八大浪费培训

工厂八大浪费培训工厂八大浪费是根据丰田生产方式中的概念提出的,指的是在生产中可能出现的浪费现象。
这些浪费会导致资源的浪费,时间的浪费和成本的浪费。
了解这些浪费并进行相应的培训可以帮助工厂提高效率和降低成本。
下面将详细介绍工厂八大浪费以及进行培训的必要性。
1. 传送浪费(Transportation Waste)传送浪费指的是在生产过程中物料或工件的不必要的运输。
比如,将物料从一个生产部门运输到另一个生产部门时,可能因为物料的存放位置不合理或者运输方式不当,导致物料传输时间的浪费。
针对这种浪费,可以通过优化物料的存放位置和流程设计,减少物料运输的距离和时间。
2. 库存浪费(Inventory Waste)库存浪费指的是生产过程中存放的物料或产品超过实际需要的数量。
过多的库存不仅占据了工厂的空间,还增加了仓储和管理的成本。
针对这种浪费,可以通过精准计划和生产,减少库存量,并实现库存的快速周转。
3. 动作浪费(Motion Waste)动作浪费指的是生产过程中人员的不必要的移动或行动。
比如,在生产线上,操作员可能需要不停地找工具、物料或设备,导致时间的浪费。
针对这种浪费,可以通过优化工作站布局、准备好所需的工具和物料,减少操作员的移动和等待时间。
4. 等待浪费(Waiting Waste)等待浪费指的是生产过程中因为某些原因导致工作处于等待状态。
比如,等待设备维修、等待上游供应商的物料到位等,都会导致时间的浪费。
针对这种浪费,可以通过加强设备维护和管理,与供应商建立稳定的供应链关系,减少等待时间。
5. 过程浪费(Processing Waste)过程浪费指的是生产过程中不必要的加工或处理。
比如,重复的工序、多余的检查、多余的运输等,都会造成资源和时间的浪费。
针对这种浪费,可以通过优化工艺流程,合理分配工作和资源,减少不必要的加工和处理。
6. 应急浪费(Rework Waste)应急浪费指的是生产过程中因为质量问题而需要重新加工或修复的情况。
精益生产必备培训之 八大浪费(原创)

精益生产之---八大浪费
目录
1 八大浪费综述
精益生产模型
通过杜绝浪费以缩短生产流程,实现下列目标: 最佳品质、最低成本、最短的前期、最佳安全性、最高员工士气
即时生产
在正确的时间 生产正确数量 的正确零部件
•花时间规划 •持续性流程 •拉式制度 •快速切换 •整合物流作业
人员与团队
挑选
什么是浪费
• 浪费
对产品没有增值的 工作或者资源使 用
浪费
增值
活动
工作的 构成因
素
•增值活动
从客户的角度看是直接产 生价值的活动(比如部 件组装),这也是客户 愿意付钱的部分
附带活动
• 附带活动
对客户没有直接增值,但就目前的运作来 说是必须的(比如,在组装过程中为了 拿去物料而产生的手的运动)
浪费是一种增加成本但不产生价值的工作
加工过 剩浪费
是消除一切无效劳 动和浪费( M u d a )
如何记忆:
搬
不
动 在家
等 过儿
搬不
动在加 等
过
运良
作库工 待
剩
的返
的的本
的
的
浪修
浪浪身 浪
浪
费的
费费的 费
费
浪
浪
费
费
目录
2 库存、等待、搬运浪费
价值流断开的地方很容易出现这三种浪费
采购/制造:过多/过早
等待 搬运 库存 不良
加工作业
现场管理
“丰田模式”概念
浪费的定义
定义:浪费指不增加附加价值,使成本增加的一系 列活动.
对于JIT来讲,凡是超出增加产品价值所绝对必 须的最少量的物料、设备、人力、场地和时间的 部分都是浪费。这里有两层含义﹕
精益生产之八大浪费培训

精益生产之八大浪费培训1. 简介精益生产是一种管理和生产理念,旨在通过优化流程和减少浪费来提高生产效率。
八大浪费是精益生产中常见的浪费现象,包括过产、库存、运输、动作、待料、修理、不用的员工天赋和等待。
本文将对这八大浪费进行详细介绍和培训,帮助读者理解并应用于实际生产中。
2. 过产过产是指在生产过程中,产品的切换造成的停工和不良品产生。
过产不仅浪费时间和资源,还可能导致产品质量下降。
为了减少过产带来的浪费,可以采取标准化工作流程、优化设备设置、精确的计划和排程等措施。
3. 库存库存是指储存在仓库中的未使用物料或产品。
过多的库存不仅需要占用仓库空间,还可能导致物料过期或过时。
为了减少库存带来的浪费,可以采取精确的预测和计划、实行“拉动生产”而非“推动生产”的方式等措施。
4. 运输运输是指物料和产品在不同环节之间的转移和搬运。
不合理的运输方式可能导致时间和资源的浪费,并增加产品受损或遗失的风险。
为了减少运输带来的浪费,可以优化运输路线、改进物料搬运设备、实行“单件流”等措施。
5. 动作动作是指工人在生产过程中进行的不必要的动作或重复动作。
不必要的动作增加了工作时间和劳动强度,降低了工作效率。
为了减少动作带来的浪费,可以通过工作站优化、自动化技术应用、培训和教育工人等措施来提高工作效率和减少工作负担。
6. 待料待料是指在生产过程中等待物料或工具的时间。
等待时间的增加会导致生产周期延长和生产效率下降。
为了减少待料带来的浪费,可以进行供应链管理的优化、设备和物料配套的改进、生产过程的优化等措施。
7. 修理修理是指产品或设备出现故障时的修复过程。
频繁的修理不仅浪费时间和资源,还可能导致产品质量下降和工作环境恶化。
为了减少修理带来的浪费,可以进行定期维护和保养、优化设备使用和操作流程等措施。
8. 不用的员工天赋不用的员工天赋是指员工在生产过程中没有得到充分发挥的机会。
员工不仅是生产线上的劳动力,他们还拥有丰富的经验和创新能力。
精益生产培训八大浪费

八.管理浪费
(二)浪费的产生:
管理能力﹕素质;执行力(速度/准度/精度); 技朮层次﹕认知高度﹔把握度﹔ 标准化﹕ 可行度﹔推广度﹔ 企业素质﹕整体素质
严格来讲: 前7大浪费未很好改善,都是管理上的浪费
消除浪费,创造
八.管理浪费
(三) 浪费的消除:
培训﹕理论与案例培训考核 认知﹕标准化﹔获利压力﹔可改善性﹔ 检知﹕执行绩效﹔量化分析﹔ 奖惩﹕奖则﹔罚则﹔执行制度﹔
没有“实时”生效,就是浪费;
消除浪费,创造价值
如何认识浪费
*什么是附加价值? 客户愿意付钱的作业内容。 * 产生附加价值的过程﹕ 改变成想要的形状﹔改变成想要的性质﹔组装 (或组合)﹔增加功能﹔
消除浪费,创造价值
不均勻
如何认识浪费-浪费的三种形态
1.勉强:
勉強
浪費
合適
超过能力界限的超负荷状态; (会导致设备故障,品质低下, 人员不安全)
消除浪费,创造价值
三.等待浪费
(二) 浪费的产生原因:
1.标准作业工时不平衡(Design) 2.人员不熟练 3.作业方法不当 4.机台设备限制
消除浪费,创造价值
三.等待浪费
(三) 浪费的消除: 1.生产线平衡 2.按作业标准要求培训 3.建立新员工上岗对应办法 4.问题处理标准化,防止再发
消除浪费,创造价值
七.库存浪费
(三)浪费的消除: 1.产能不均衡 线平衡(ECRS)﹐使用共同CT﹔设备小型化﹑考虑前后 工程产能﹔ 2.计划不同步(Schedule)﹕ 直通流程﹔同步排配﹔信息集成化﹔前后工程计划协 调平台﹔
消除浪费,创造价值
八.管理浪费
(一) 浪费的定义:
由管理造成生产力、周期、资源利用等浪费﹔
企业八大浪费培训ppt课件ppt

通过合理安排生产计划,减少生 产过程中的瓶颈,提高整体产出
。
减少生产过程中的浪费,可以降 低生产成本,从而增加企业的利
润。
降低成本
减少浪费可以降低企业的原材料、能 源和水等资源的消耗,从而降低生产 成本。
减少浪费可以提高企业的生产效率, 从而降低企业的运营成本。
通过优化生产流程和减少不良品等浪 费,可以降低企业的维修和替换成本 。
等待时间的浪费
因生产不平衡、设备故障 等原因导致的等待现象。
搬运的浪费
不必要或不合理的物料、 半成品、成品移动。
八大浪费的具体定义
过度加工的浪费
超出客户需求或产品功能 要求的加工。
库存的浪费
过多库存导致资金占用、 管理成本增加。
动作的浪费
不必要或不合理的操作动 作。
八大浪费的具体定义
不良品的浪费
培养节约习惯
在日常工作中,员工应养成节约的习惯,减少不必要的浪费,提高 工作效率。
互相监督与学习
员工之间应相互监督和学习,共同提高减少浪费的能力和意识。
THANKS
感谢观看
数据分析法
对生产数据进行分析,找出浪费的原 因和规律。
消除浪费的策略
优化生产流程
通过改进生产流程,减少不必要 的环节和操作,提高生产效率。
引入自动化设备
利用自动化设备替代人工操作,降 低人为因素导致的浪费。
制定节约措施
针对不同的浪费现象,制定相应的 节约措施,如减少用水、用电等。
实施消除浪费的步骤
提升产品质量
减少生产过程中的不良品和缺陷 品的产生,提高产品的合格率和
质量。
通过优化生产流程和提高员工技 能等措施,提高企业的产品质量
精益生产之现场八大浪费培训教材

成本可以无限下降 ——改善无止境 成本取决于制造的方法
通过改善消除浪费,提高附加价值实现
精益生产的简单系统
竞争力提升
品质提升
合理化成本降低
形象提升 动作改善、作业流程改善、物流改善、设 备模夹治具改善、品质改善、管理改善等
改
善
消除浪费 标 准 化 现场5S
八大浪费、三无工程等
动作标准化、作业流程标准化、操作流程 标准化、包装运输标准化等 整理、整顿、清扫、清洁、素养等
J IT 生 产 方 式
适 时 的 生 产
1.制造过多的浪费
制造过多是一种浪费的原因:
八大浪费
•只是提前用掉了费用(材料费、人工费)而已,并 无其它好处 •会把等待的浪费隐藏起来,掩盖稼动不够的问题
•会使制程间积压在制品,制程时间变长,现场工作
空间变大 •会产生搬运、堆积的浪费 •使先进先出的工作产生困难 •会造成库存空间的浪费
浪费的层次
过多人员 过剩设备 过剩物料 过剩厂房 制造过剩 库存过剩 多余仓库 多余库存管理 多余搬运 多余搬运设备
精益生产
第一层次:过剩生产能力
第二层次:工作进度过度
第三层次: 第四层次:
隐藏等待 隐藏等待
1.制造过多的浪费
无法保证可卖出的产品做了太多
八大浪费
是浪费的源头
表现形式:
•物流阻塞 •库存、在制品增加 •产品积压造成不良发生 •资金回转率低 •材料、零件过早取得 •影响计划弹性及生产系统的适应能力
实现多品种、小批量,低成本的生产
精益生产概念
精益生产
精益-LEAN
什么是精益生产方式
精益生产
精益生产(准时生产)其核心是消除一切无效劳动
八大浪费培训教材课件
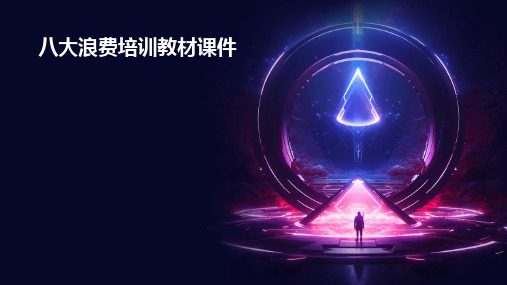
根据企业实际情况制定判定标准 ,明确哪些行为或现象属于八大 浪费,哪些不属于。判定标准应 具体、可操作,并具有约束力。
八大浪费的危害与影响
危害
八大浪费会导致企业资源浪费、效率 低下、成本增加、市场竞争力下降等 危害。
影响
八大浪费会影响企业的可持续发展, 降低员工的工作积极性和生产效率, 增加企业的经营风险。
企业缺乏明确的管理制度和流程,导致员工在工 作中无法遵循统一的标准和规范,造成管理上的 浪费。
决策失误
管理者在决策过程中缺乏充分的市场调研和数据 分析,导致决策失误,造成资源浪费和管理效率 低下。
人员素质不足
员工和管理者缺乏必要的专业知识和技能,无法 有效地完成工作任务,导致管理成本的增加和管 理效率的降低。
生产管理
生产计划安排不合理,导致半 成品或成品库存增加。
销售预测
对市场需求预测不准确,导致 库存积压或缺货。
表现形式
原材料库存
原材料、零部件等库存过多, 占用企业资金和仓储空间。
在制品库存
生产过程中的半成品、待加工 品等库存过多。
成品库存
已完成生产但未销售的成品库 存过多。
呆滞物料
长期未使用或无法再利用的物 料,形成无效库存。
无效搬运
搬运过程中存在无效操作,如手动 翻转、重新排列等。
改善方法
优化生产布局
合理规划生产线,使物料流动更加顺 畅。
减少过度生产
根据实际需求调整生产计划,减少库 存和搬运量。
采用合适的搬运方式
根据物料特性和数量选择合适的搬运 设备和技术,提高搬运效率。
引入自动化和智能化技术
通过引入自动化和智能化技术,减少 人工搬运和重复劳动,提高生产效率 。
11-八大浪费知识培训
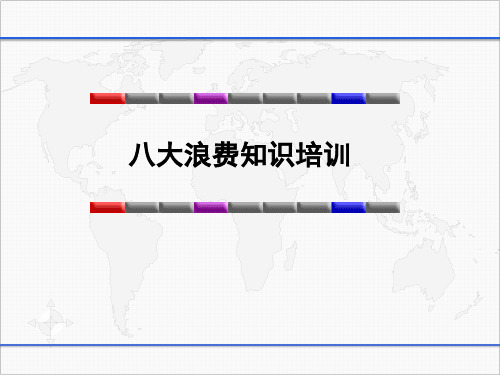
5.加工本身的浪费
过程浪费
原因
改善方法
没有过程更改的工程更改 新技术的利用不当 由不适当级别的人做决定 无效的政策和程序 缺乏客户要求的输入
流程﹕ 简化生产流程 提高系统柔性 改变工作台面布置﹑摆放 方式﹑参数设定 “缩短距离﹑减少阻力﹑ 简化程序﹑精减过程”
1.搬运的浪费
产生的原因
工厂布局(Layout)﹕ 物流线路设计不合理 设备局限 现场布局 前后工序断点作业 设计兼容性(Compatibility): 业务扩充→新增工序或设备 设备或物料变换→不适合 前景不明→未作整体规划
1.搬运的浪费
优化厂布局 (Layout)
改善方法
精度﹕ 系统稳定性 制订强度标准 明确操作要求 过程防呆……
6.等待的浪费
定义:由于生产原料供应中断、作业不平衡和生产计划安 排不当等原因造成的无事可做的等待,被称为等待的浪费, 未满负荷。
表现
原因
人等机器 机器等人 人等人 不平衡的操作 有人过于忙乱 计划外的停机
工序能力不平衡 人机配合效果差 生产布局不合理 生产切换时间长 产品质量缺陷 生产计划安排不当 管理控制点多
1. 双手并用 2. 对称反向 3. 排除合并 4. 降低动作等级 5. 减少动作限制 6. 避免动作突变 7. 保持轻松节奏 8. 利用惯性 9. 手脚并用 10. 利用工具 11. 工具万能化 12. 易于操纵 13. 适当位置 14. 安全可靠 15. 照明通风 16. 高度适当
4.在库的浪费
2.不良的浪费
不良品浪费
产生的原因
精益生产之八大浪费培训共121页文档
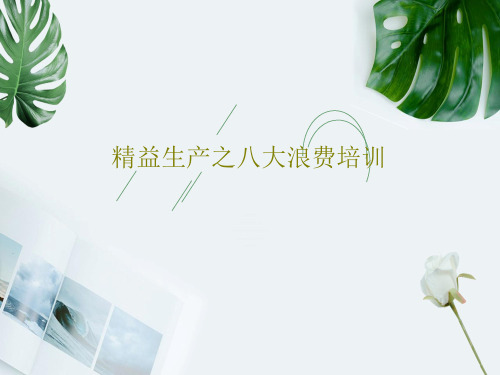
▪
26、要使整个人生都过得舒适、愉快,这是不可能的,因为人类必须具备一种能应付逆境的态度。——卢梭
▪
27、只有把抱怨环境的心情,化为上进的力量,才是成功的保证。——罗曼·罗兰
▪
28、知之者不如好之者,好之者不如乐之者。——孔子
▪
29、勇猛、大胆和坚定的决心能够抵得上武器的精良。——达·芬奇
▪
30、意志是一个强壮的盲人,倚靠在明眼的跛子肩上。——叔本华
谢谢!
121
精益生产之八大浪费培训
56、极端的法规,就是极端的不公。 ——西 塞罗 57、法律一旦成为人们的需要,人们 就不再 配享受 自由了 。—— 毕达哥 拉斯 58、法律规定的惩罚不是为了私人的 利益, 而是为 了公共 的利益 ;一部 分靠有 害的强 制,一 部分靠 榜样的 效力。 ——格 老秀斯 59、假如没有法律他们会更快乐的话 ,那么 法律作 为一件 无用之 物自己 就会消 灭。— —洛克
八大浪费知识培训

12
二﹑动作浪费
(二) 浪费的产生:
操作不经济(Handling):动作不精简;动作多余 设计不合理(Design): 可同时完成但未同时; 不必要但被增加; 可同规格但不同; 未考虑调整/转换/取放 物料需要翻找;
(三) 浪费的消除: 操作不经济 (Handling): 按经济原则设计并标准化 ; 制订Check list发现并消除; 设计不合理(Design):合理设计;变成设计要素;设计 验证与稽核;符合人体工效设计;
方案:可以使用采用对各个工站的动作要素分析, 对整个生产 加工进行线平衡
19
B.IE分析标准工具
建立有效动作要素标准数据
问题分析及分类
序号
1 2 3 4 5
问题点
连接主板 电源板 锁主板螺 丝 WB测试 上治具 画面检查
对策
工站调整合并 工站调整合并 工站优化 开发新治具 重新优化
20
C.案例改善后狀況
勉強
能力限度
合適
浪費
不均勻
5
八大浪费
TPS:精益生产的核心 不良修 正浪费 制造过 多(过早) 动作浪费 浪费 8种浪费 加工过 等待浪费 剩浪费 在库量 搬运 过多浪费 浪费 是消除一切无效劳 动和浪费 (Muda)
6
管理 浪费
精: 精干; 益: 效益 精益: 投入少,产出多
一﹑管理浪費
(一)管理浪费的定义: 是由思维﹑政治及企业文化陈旧﹑ 用人不当﹑培训不足﹑低薪高流动策 略等管理问题造成的人员使用方面 ( 脑 力﹑创造力﹑体力﹑技能等)的浪费。 (二) 管理的概念 三个和尚的故事 组织的存在导致了管理的产生
17
三﹑等待的浪费
消除等待浪费 1. 单元制生产方式; 2. 生产线平衡法; 3. 人机工作分离; 4. 全员生产性维护(TPM); 5. 切换的改善; 6. 稼动率,可动率的持续提升
- 1、下载文档前请自行甄别文档内容的完整性,平台不提供额外的编辑、内容补充、找答案等附加服务。
- 2、"仅部分预览"的文档,不可在线预览部分如存在完整性等问题,可反馈申请退款(可完整预览的文档不适用该条件!)。
- 3、如文档侵犯您的权益,请联系客服反馈,我们会尽快为您处理(人工客服工作时间:9:00-18:30)。
上料电梯
IQC
待验 区
不良 品仓
办公 区 被动 区 PCB 仓
新机 种仓
主貴 倉
下料电梯
30
五.搬运的浪费
(一) 定义:
是由工场布局不合理﹑生产流程理解不当﹑生产批 量大﹑生产前置期长﹑储存区域大等造成的物料搬 运的浪费。
搬运是一种不产生附加价值的 动作.若分解开来又分为:放置,堆积, 移动 , 整列等动作浪费 , 由此而带来 物品移动所需空间的浪费、时间的 浪费和人力工具的占用等不良后果 .
式与续的 方改目 法善的为 追的以实 求基彻现 制础底企 造上杜业 产采绝对 品用浪员 合准费工 理时的、 性化思社 的与想会 一自为、 种动目和 生化标产 产方在品 负 方式连3 责
TPS:
.
,
, ,
,
浪费的定义
定义 : 浪费指不增加附加价值 , 使成本增加 的一系列活动. 对于JIT 来讲 ,凡是超出增加产品价值所绝对 必须的最少量的物料、设备、人力、场地和时间 的部分都是浪费。这里有两层含义﹕ 不增加价值的活动﹐是浪费﹔
13
二﹑动作浪费
四﹑动作经济原则
原则1:两手同时开始及完成动作。 原则2:除休息时间外,两手不应同时空闲。 原则3:两臂之动作应反向同时对称。 原则4:尽可能以最低级动作工作 原则5:物体之”动量”尽可能利用之,但如需用肌力制止 时,则应将其减至最小度。 原则6:连续曲线运动较方向突变直线运动为佳 原则7:弹道式运动较轻快 原则8:动作宜轻松有节奏 原则9:工具物料应置于固定处所 原则10:双手可及原则 原则11:利用各种盛具送至工作点,愈近愈佳
14
二﹑动作浪费
四﹑动作经济原则
原则12:工具物料应依最佳的工作顺序排列 原则13:利用重力墬送 原则14:应有适当的照明,使视觉舒适 原则15:工作台及座椅的高度,应保证工作者坐立舒适(升降 椅) 原则16:工作椅样式及高度,应能使工作者保持良好姿势 原则17:尽量解除手的工作,而以夹具或脚踏工具代替(缝纫 机) 原则18:可能时,应将两种工具合并使用(万用表,圆珠笔) 原则19:工具物料应尽可能预防在工作位置上 原则20:手指分别工作时,其各指负荷应按照其本能予以分配 原则21:手柄接触面尽可能加大 原则22:操作杆应尽可能少变更姿势
32
PCBA搬运浪费改善案
A.背景介紹
1. 此为PCBA生产线,为了供应前工站的焊接载具需求,需将用 后的载具人工回流至前工站,每线需人力一名每线每班1人, 共32人 2. 此处存在搬运浪费,可考虑用鱼骨图分析找出问题原因
33
C.案例改善后狀況
改善方案选择
NANHONG-WS450LF
Pb
上坡线体
12
二﹑动作浪费
(二) 浪费的产生:
操作不经济(Handling):动作不精简;动作多余 设计不合理(Design): 可同时完成但未同时; 不必要但被增加; 可同规格但不同; 未考虑调整/转换/取放 物料需要翻找;
(三) 浪费的消除: 操作不经济 (Handling): 按经济原则设计并标准化 ; 制订Check list发现并消除; 设计不合理(Design):合理设计;变成设计要素;设计 验证与稽核;符合人体工效设计;
36
喷剂面积过大改善案
15
16
三﹑等待的浪费
定义﹕是由工作负荷不平衡﹑保养计划不完善﹑换线频繁﹑自 动化应用不当﹑前工站质量问题﹑生产计划未平准化等造成人 员和设备空闲带来的浪费。表现形式: 1. 生产线机种切换; 2. 时常缺料而使人员﹑机器闲置;
3. 生产线未能取得平衡,工序间经常发生等待;
4. 每天的工作量变动很大; 5. 机器设备时常发生故障; 6. 开会等非生产时间占用过多; 7. 共同作业时,劳逸不均衡(人-机,人-人).
11.岗位职责说明书; 2.有效激励; 3.有效沟通; 4.作业标准化; ……
11
二﹑动作浪费
(一)动作浪费的定义:
是由人机匹配效率不高﹑作业方法未标准 化﹑设施布局不合理﹑工场组织与后勤差﹑等待 时额外“瞎忙”等造成的不为产品或服务带来任 何价值的人机动作浪费.
31
五.搬运的浪费
(二) 浪费的产生:
工厂布局(Layout):
物流动线设计;设备局限;工作地布局;前后工程分离; 设计兼容性(Compatibility): 1.业务扩充→新增工序或设备; 2.设备或物料变换→不适合;
3.前景不明→未作整体规划;
(三)改善方向:
1. 合理化布局;
2. 搬运手段的合理化.
2. JIT库存管理---广告牌管理 3. 控制在库金额. 4. 定期盘点. 5. 库存警示方法.
27
仓储空间及物流规划改善
A.背景介绍
1.仓库来料种:小型电子物料、散热片,主贵物料等 2.来料性质: HUB仓物料、转厂物料、海外进口物料 3.来料特点:类型繁多,规格不同、包装方式不同, 储存方式不同
25
四﹑库存浪费
精益生产方式
存货水位降低时,有助于发掘需要关注的地方, 以及迫使要去面对处理的问题.此即是及时生产 体系所追求的目标:当存货的水位持续下降至 “一个流”的生产线时,“改善”就成为每日必行 的活动.
26
四﹑库存浪费
(三)改善在库过多的方法
1. 分类管理法---根据生产计划及交货期分批 购入原材料,保证最低库存量;通用性生产物料 考虑实时生产或实时送货的方式,降低库存.
7
一﹑管理浪费
管理的定义
管理是同别人一起 , 或通过别人使活动完成 的更有效的过程; 效率是指输入与输出的关系; 过程就是利用拥有的资源 , 将它转换为另一 组彼此相关资源的活动; 管理主要是体现对过程的控制 , 有效的管理 就是对过程的有效控制 , 就是建立一种机制 , 尽可能用较少的资源获得较大的增值.
23
四﹑库存浪费
JIT的观点认为,库存是 没有必要的,甚至认为库 存是万恶之源.
库 存 三 不
不大批量生产 不大批量搬运 不大批量采购
24
四﹑库存浪费
传统生产方式
存货有时被比作为隐藏问题的水库. 当库存的水位高涨时,管理者就感受不到 问题的严重性,像质量的问题、机器故障、 及员工缺勤,也因此而失去了改善的机会.
序号
1 2 3 4 5 6 7 8
动作(机1)
流水板流动 連接信号线 Start test Adjust 6500K Adjust 9300K Check WB Max bright Pass Pass
机1
3
人
机2
2.27
动作(机2)
Max bright Pass Pass 拔线 & stop下降
1.3 5.05 2.75 2.61 1.09 2.27 0.73 1.3 0.5
八大浪費
2013年8月
1
起源
1973年:中东战争爆发 1992年:改变世界的机器 1996年:精益思想 1945年:丰田喜一郎: 生产力:日本:德国=1:3 德国:美国=1:3 日本:美国=1:9 大野耐一:只要杜绝浪费,生产效率就有可能 提高10倍
2
丰田生产方式
品质、成本、交期
准 时 化 自 动 化 5S管理/持续改善
勉強
能力限度
合適
浪費
不均勻
5
八大浪费
TPS:精益生产的核心 不良修 正浪费 制造过 多(过早) 动作浪费 浪费 8种浪费 加工过 等待浪费 剩浪费 在库量 搬运 过多浪费 浪费 是消除一切无效劳 动和浪费 (Muda)
6
管理 浪费
精: 精干; 益: 效益 精益: 投入少,产出多
一﹑管理浪費
(一)管理浪费的定义: 是由思维﹑政治及企业文化陈旧﹑ 用人不当﹑培训不足﹑低薪高流动策 略等管理问题造成的人员使用方面 ( 脑 力﹑创造力﹑体力﹑技能等)的浪费。 (二) 管理的概念 三个和尚的故事 组织的存在导致了管理的产生
上下水位 报警裝置
1.重新Layout后对各货架实行店面管理及分类管理 保证先进先出,及时来料及时交付生产,降低库存. 2.设置防呆的报警系统,货架上下水位报警,使仓库 人员及时对其进行仓储管控。
29
C.案例改善后狀況
通过导入广告牌管理及分类管理和防呆的报 警系统,使空间利用率及货架利用率大大提高. 在重新的布局Layout使物流线路不再杂乱,不 再出现堵塞现象.人员作业效率也提高. 改善绩效: 1.一次性节约仓库布局变更建造费用200元 /m2*1428m2=284800元 五金 2.节约物料架成本:2500元/个*10个=25000元 仓
0.73
3
流水板流动 連接信号线
5.05 2.75 2.61
Start test Adjust 6500K Adjust 9300K
9
Total
拔线 & stop下降
WB工站 17.5
0.5
3.6
1.09
17.5
Check WB
20.5%
有效工时由原来的10.2%提高到20.5% 提高了一倍,平衡了作业时间,减少等待浪费
8
一﹑管理浪费
(三)管理上的问题: 1. 管理工作不能“等” 2. 拒绝“低效”反复发生 3. 协调不力,企业丧失凝聚力 4. 让闲置的“动”起来
5. 把无序变有序
6. 管理必须真正有“理”可依
9
一﹑管理浪费
(四)浪费的产生: 管理能力:素质;执行力(速度/准度/精度);(相互) 技朮层次:认知高度;把握度;(相对) 标准化: 可行度;推广度; 企业素质:整体素质
17
三﹑等待的浪费
消除等待浪费 1. 单元制生产方式; 2. 生产线平衡法; 3. 人机工作分离; 4. 全员生产性维护(TPM); 5. 切换的改善; 6. 稼动率,可动率的持续提升