注塑产品常见缺陷及解决方法
注塑常见缺陷的解决方法

注塑常见缺陷的解决方法注塑是一种常见的制造工艺,可以用于生产各种塑料制品。
然而,在注塑过程中常常会出现一些缺陷,如翘曲、气泡、短射等。
这些缺陷会降低产品的质量,影响使用效果。
因此,解决这些缺陷是注塑加工中重要的一环。
下面是一些常见缺陷的解决方法:1.翘曲:翘曲是指注塑制品的形状变形,不符合设计要求。
翘曲的原因可能是注塑温度过高、材料流动不均匀等。
解决方法包括:优化注塑工艺参数,例如调整注塑温度、压力、速度等;增加型腔冷却方式,以提高产品的冷却效果;使用合适的塑料料种,如改变注塑材料的配方,选择更具平衡性能的材料。
2.气泡:气泡是指注塑制品中出现的气体孔洞,影响了产品的外观和性能。
气泡的形成可能是由于注塑材料中的挥发性成分未完全排除、注塑机排气不良等原因。
解决方法包括:增加注塑所需的压力和温度,以促使挥发性成分完全排出;改善注塑机的排气系统,有效排除气泡。
3.短射:短射是指注塑过程中,塑料流动未能充满整个模具的情况。
短射的原因可能是注塑料温度过低、注塑机压力不足、型腔阻力过大等。
解决方法包括:提高注塑温度和压力,以增加塑料的流动性;改善模具的设计,减少型腔的阻力;检查注塑机的喷嘴和螺杆是否损坏,及时更换。
4.热流线:热流线是指注塑制品表面出现的不均匀纹路,影响产品的外观。
热流线的形成可能是由于塑料流动速度过快、模具温度不均匀等原因。
解决方法包括:调整注塑机的喷嘴和螺杆速度,控制塑料的流动速度;优化模具的冷却系统,使模具温度均匀分布。
5.尺寸偏差:尺寸偏差是指注塑制品的尺寸与设计要求不符,可能是由于模具磨损、注塑工艺参数不恰当等原因。
解决方法包括:定期检查和修复模具,以保证模具的精度;优化注塑工艺参数,例如调整注射时间、压力和温度,以控制产品的尺寸。
总的来说,解决注塑常见缺陷需要综合考虑材料、工艺和设备等方面的因素。
通过不断优化参数和改进工艺,可以改善产品的质量,提高注塑加工的效率。
此外,定期维护和保养注塑设备和模具也是预防和解决缺陷的重要措施。
注塑缺陷原因分析与解决方案
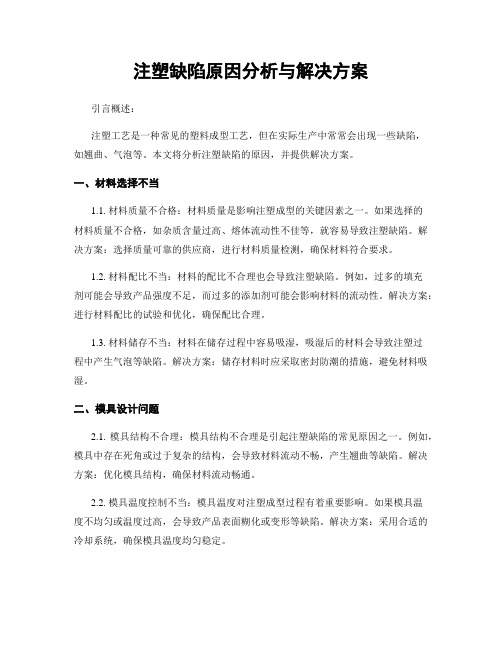
注塑缺陷原因分析与解决方案引言概述:注塑工艺是一种常见的塑料成型工艺,但在实际生产中常常会出现一些缺陷,如翘曲、气泡等。
本文将分析注塑缺陷的原因,并提供解决方案。
一、材料选择不当1.1. 材料质量不合格:材料质量是影响注塑成型的关键因素之一。
如果选择的材料质量不合格,如杂质含量过高、熔体流动性不佳等,就容易导致注塑缺陷。
解决方案:选择质量可靠的供应商,进行材料质量检测,确保材料符合要求。
1.2. 材料配比不当:材料的配比不合理也会导致注塑缺陷。
例如,过多的填充剂可能会导致产品强度不足,而过多的添加剂可能会影响材料的流动性。
解决方案:进行材料配比的试验和优化,确保配比合理。
1.3. 材料储存不当:材料在储存过程中容易吸湿,吸湿后的材料会导致注塑过程中产生气泡等缺陷。
解决方案:储存材料时应采取密封防潮的措施,避免材料吸湿。
二、模具设计问题2.1. 模具结构不合理:模具结构不合理是引起注塑缺陷的常见原因之一。
例如,模具中存在死角或过于复杂的结构,会导致材料流动不畅,产生翘曲等缺陷。
解决方案:优化模具结构,确保材料流动畅通。
2.2. 模具温度控制不当:模具温度对注塑成型过程有着重要影响。
如果模具温度不均匀或温度过高,会导致产品表面糊化或变形等缺陷。
解决方案:采用合适的冷却系统,确保模具温度均匀稳定。
2.3. 模具磨损严重:模具长时间使用后会出现磨损,磨损严重的模具会导致产品尺寸不准确或表面粗糙等缺陷。
解决方案:定期检查和维护模具,及时更换磨损严重的模具部件。
三、注塑工艺参数设置不当3.1. 注射压力过高或过低:注射压力是影响注塑成型的关键参数之一。
如果注射压力过高,会导致产品变形或开裂,而注射压力过低则会导致产品表面光洁度不高。
解决方案:根据产品要求和材料特性,合理设置注射压力。
3.2. 注射速度不合理:注射速度对产品的充填和冷却过程有着重要影响。
如果注射速度过快,会导致产品内部产生气泡或短射,而注射速度过慢则会导致产品表面瑕疵。
注塑件常见缺陷的分析及解决办法

注塑常见缺陷分析及解决办法
C,增加注射压力或保压压力;
D,改善流道和型腔排气;
E,缩短成型周期;
F,制件采用退火方法处理。
B,熔料温度或模温偏低;
C,注塑压力或保压压力不够;
D,气体过多。
A,提高料筒温度特别是喷嘴温度,增加注射压力和速度;B,提高模温,加大流道浇口尺寸,注意抛光喷嘴孔及流道
B,控制料温,提高模温;
C,增加注射压力及熔胶背压。
A,对于投影面积大的扁平制件,要采用多点浇口,或扇形浇口及薄片浇口;
B,模具各部位冷却要均匀;
形(PE,PP,PA,POM等);
B,保压压力太高;
C,模温及冷却不均衡。
D,在允许的情况下,有些易变形胶件脱模后须用夹具定型或进行回火处理。
2尺寸:及相对位置的准确性;
3性能:与用途相关的机械性能,化学性能。
2调机问题:包括注射压力、温度和周期等;
3模具问题:包括模具设计,制造及磨损。
注塑成型缺陷及解决方法

注塑成型缺陷及解决方法注塑成型是一种常用的塑料制品生产工艺,但在实际操作过程中,难免会出现一些缺陷。
下面将介绍几种常见的注塑成型缺陷及其解决方法。
1.短射:短射指的是塑料在模腔中注入不完全,导致制品形状不完整或缺少一部分。
短射可能由于注射速度过快或进气不畅引起。
解决方法是调整注塑机的注射速度和压力,确保塑料充分进入模腔,并检查进气口是否畅通。
2.气泡:气泡是指制品表面或内部出现空洞。
气泡的形成可能由于塑料中含有水分、模具开放不当等原因。
解决方法是在注塑前将塑料干燥处理,确保塑料中不含水分,并检查模具密封性以防止气体进入模腔。
3.缩短:缩短是指制品尺寸比设计要小,可能由于塑料收缩不均匀或模具温度不稳定引起。
解决方法是通过调整模具温度和冷却系统,使塑料在注塑过程中均匀收缩,并确保模具温度稳定。
4.色差:色差是指制品表面颜色不均匀,可能由于塑料熔融不充分、颜料添加不均匀等原因。
解决方法是加长塑料的熔化时间,确保塑料充分熔融,并确保颜料充分混合均匀。
5.枝晶:枝晶是指制品表面出现树枝状的纹理,可能由于注塑温度过高或冷却时间不足引起。
解决方法是降低注塑温度,延长冷却时间,确保塑料在注塑过程中充分凝固。
6.毛刺:毛刺是指制品表面出现刺状的尖突物,可能由于模具间隙过大或模具磨损引起。
解决方法是调整模具间隙,确保模具紧密结合,并定期检查模具磨损情况。
7.烧焦:烧焦是指塑料在注塑过程中受热过度,产生发黑或炭化的现象。
烧焦可能由于注塑温度过高或注射速度过快引起。
解决方法是降低注塑温度,调整注射速度,确保塑料受热均匀。
总结起来,解决注塑成型缺陷的关键是调整注塑机参数、保证模具质量和稳定性,以及进行适当的后处理工艺。
此外,及时发现和修复模具的损坏也是避免缺陷的重要措施。
注塑成型常见的缺陷和解决方案

注塑成型常见的缺陷和解决方案
与设计有关的原因与改良措施 1、模温不稳定:提供冷却/加热均衡的模具
-
THANKS
欢迎领导来夸我
70%~80%。如在料头附近 发现注射不满,可以解 释为:流体前锋在这
物理原因:熔料的注射 压力和/或注射速度太低, 熔料在射向流长最末
候。实际上,当需要高 注射压力时,保压也应 按比例提高:正常时, 保
些点被阻挡,较厚的地 方先被充满。如此,在 模腔几乎被充满之后, 在
注塑成型常见的缺陷和解决方案
缩水。这是因为内部 仍有热量,它会穿过 外层并对外层产生加 热作用
模壁的地方先冻结, 在制品中心形成内应 力。如果应力太高, 就会导致
到模件内,在模壁和 已凝固的制品外层之 间就会形成沉降。这 些沉降通
制品内产生的拉伸应 力会使热的外层向里 沉降,在此过程中形 成收缩
注塑成型常见的缺陷和解决方案
与加工参数有关的原因与改良措施 1、保压太低:增加保压 2、保压时间太短:延长保压时间 3、模壁温度太高:降低模壁温度 4、熔料温度太高:降低熔料温度,降低料筒温度 与设计有关的原因与改良措施 1、料头横截面太小:增加料头横截面 2、料头太长:缩短料头 3、喷嘴孔太小:增加喷嘴孔径
注塑缺陷描述及解决方案

注塑缺陷描述及解决方案注塑是一种常用的塑料加工方法,通过将熔化的塑料材料注入模具中,经过冷却固化后得到所需的塑料制品。
然而,在注塑过程中,可能会出现一些缺陷,影响产品的质量和性能。
本文将详细描述常见的注塑缺陷,并提供相应的解决方案。
一、缺陷描述1. 短射(Short Shot):指注塑过程中塑料未充满模具腔体,导致制品缺少某些部分或整体不完整。
解决方案:可能的原因包括模具温度过低、注塑速度过快、塑料材料不足等。
解决方法包括增加模具温度、调整注塑速度、增加塑料材料供给量等。
2. 翘曲(Warping):指注塑制品在冷却后产生变形,失去原本的平整形状。
解决方案:可能的原因包括模具温度不均匀、冷却时间不足、注塑压力过大等。
解决方法包括优化模具设计、增加冷却时间、减小注塑压力等。
3. 气泡(Air Traps):指注塑制品中出现气泡或空洞。
解决方案:可能的原因包括塑料材料中含有水分、注塑压力不稳定、模具排气不畅等。
解决方法包括使用干燥的塑料材料、调整注塑压力、改善模具排气系统等。
4. 热缩(Shrinkage):指注塑制品在冷却后出现尺寸缩小的现象。
解决方案:可能的原因包括模具温度过高、冷却时间不足、塑料材料收缩率不合理等。
解决方法包括降低模具温度、增加冷却时间、选择合适的塑料材料等。
5. 热裂纹(Hot Cracks):指注塑制品在冷却过程中出现裂纹。
解决方案:可能的原因包括注塑温度过高、冷却速度过快、塑料材料选择不当等。
解决方法包括降低注塑温度、控制冷却速度、选择合适的塑料材料等。
二、解决方案1. 优化模具设计:合理设计模具结构,确保充模充型均匀,避免短射、翘曲等缺陷的发生。
2. 控制注塑工艺参数:包括模具温度、注塑速度、注塑压力等。
通过调整这些参数,可以解决短射、翘曲、气泡等缺陷。
3. 选择合适的塑料材料:不同的塑料材料具有不同的性能和特点,选择合适的材料可以避免热缩、热裂纹等缺陷的发生。
4. 增加冷却时间:适当延长注塑制品的冷却时间,有助于避免翘曲、热缩等缺陷的产生。
注塑缺陷及其解决方法
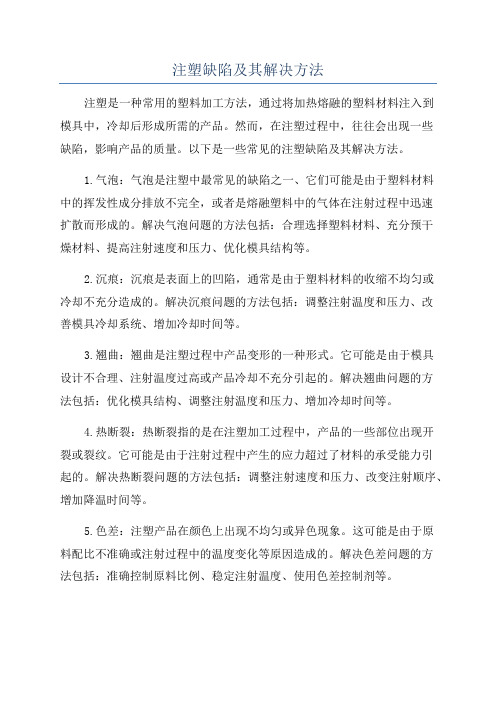
注塑缺陷及其解决方法注塑是一种常用的塑料加工方法,通过将加热熔融的塑料材料注入到模具中,冷却后形成所需的产品。
然而,在注塑过程中,往往会出现一些缺陷,影响产品的质量。
以下是一些常见的注塑缺陷及其解决方法。
1.气泡:气泡是注塑中最常见的缺陷之一、它们可能是由于塑料材料中的挥发性成分排放不完全,或者是熔融塑料中的气体在注射过程中迅速扩散而形成的。
解决气泡问题的方法包括:合理选择塑料材料、充分预干燥材料、提高注射速度和压力、优化模具结构等。
2.沉痕:沉痕是表面上的凹陷,通常是由于塑料材料的收缩不均匀或冷却不充分造成的。
解决沉痕问题的方法包括:调整注射温度和压力、改善模具冷却系统、增加冷却时间等。
3.翘曲:翘曲是注塑过程中产品变形的一种形式。
它可能是由于模具设计不合理、注射温度过高或产品冷却不充分引起的。
解决翘曲问题的方法包括:优化模具结构、调整注射温度和压力、增加冷却时间等。
4.热断裂:热断裂指的是在注塑加工过程中,产品的一些部位出现开裂或裂纹。
它可能是由于注射过程中产生的应力超过了材料的承受能力引起的。
解决热断裂问题的方法包括:调整注射速度和压力、改变注射顺序、增加降温时间等。
5.色差:注塑产品在颜色上出现不均匀或异色现象。
这可能是由于原料配比不准确或注射过程中的温度变化等原因造成的。
解决色差问题的方法包括:准确控制原料比例、稳定注射温度、使用色差控制剂等。
6.熔接线:熔接线是由于注塑模具的设计和操作问题导致两个或多个熔融塑料部分相互连接而形成的。
解决熔接线问题的方法包括:调整模具结构,避免部件交汇点过多,调整注射速度和压力等。
总之,注塑缺陷的解决方法主要包括调整材料配比、优化模具结构、控制注射温度和压力、增加冷却时间等。
同时,及时调整机器参数、进行模具维护和清洁,以保证注塑过程的稳定性和可靠性。
通过以上的措施,可以有效减少注塑缺陷,提高产品质量。
注塑常见缺陷及解决方法

注塑常见缺陷及解决方法1. 引言在注塑过程中,由于材料、设备、工艺等多种因素的影响,常常会出现一些缺陷。
这些缺陷不仅会影响产品的质量,还可能导致产品性能下降甚至无法使用。
因此,了解注塑常见缺陷及其解决方法对于提高产品质量至关重要。
2. 注塑常见缺陷2.1 短射短射是指注塑过程中,塑料无法充满模具腔体的情况。
造成短射的原因可能是模具设计不合理、注塑机参数设置不当等。
解决方法包括优化模具结构、增加注射压力等。
2.2 气泡气泡是注塑过程中常见的缺陷之一。
气泡的出现可能是由于塑料中含有气体、注塑过程中存在气体进入等原因。
解决方法包括在塑料中加入消泡剂、提高注射速度等。
2.3 热胀冷缩热胀冷缩是指注塑过程中,塑料在冷却过程中由于体积收缩而导致产生应力。
这种缺陷会导致产品变形、尺寸不稳定等问题。
解决方法包括优化模具结构、增加冷却时间等。
2.4 毛刺毛刺是指注塑制品表面出现的突起或凹陷。
毛刺的产生可能是由于模具表面不光滑、注塑过程中存在杂质等原因。
解决方法包括优化模具表面处理、提高注射速度等。
3. 注塑常见缺陷的解决方法3.1 优化模具结构优化模具结构是解决注塑常见缺陷的重要方法之一。
通过对模具的设计进行改进,可以减少短射、热胀冷缩等缺陷的发生。
3.2 控制注射参数注塑过程中的注射参数设置对于产品质量至关重要。
合理的注射压力、注射速度等参数可以有效地解决短射、气泡等缺陷。
3.3 加入添加剂在注塑过程中,可以加入一些添加剂来改善产品的性能。
例如,在塑料中加入消泡剂可以有效地解决气泡缺陷。
3.4 提高冷却时间热胀冷缩是注塑过程中常见的缺陷之一。
通过增加冷却时间,可以使塑料充分冷却,减少热胀冷缩导致的尺寸变化。
4. 结论注塑过程中常见的缺陷包括短射、气泡、热胀冷缩、毛刺等。
通过优化模具结构、控制注射参数、加入添加剂、提高冷却时间等方法,可以有效地解决这些缺陷,提高产品质量。
在实际生产中,需要根据具体情况选择合适的解决方法,并进行不断的改进和优化,以提高注塑产品的质量和竞争力。
- 1、下载文档前请自行甄别文档内容的完整性,平台不提供额外的编辑、内容补充、找答案等附加服务。
- 2、"仅部分预览"的文档,不可在线预览部分如存在完整性等问题,可反馈申请退款(可完整预览的文档不适用该条件!)。
- 3、如文档侵犯您的权益,请联系客服反馈,我们会尽快为您处理(人工客服工作时间:9:00-18:30)。
LOGO
INJELIC
▪ 4、冷料银丝:喷嘴中的冷料注入模腔或堵塞浇口而产
生的 银丝,这种银丝出
2、料的预热 3、排汽通道
压缩段功用: 1、压缩塑化
计量段功用: 1、搅拌、均化
背压功用: 1、增密
2、排气
喷嘴 螺杆头 止逆环 介子 计量段 压缩段
170-200℃
200-220℃
进料段 170-190℃
LOGO
背压的产生
INJELIC
LOGO
注射工艺过程
INJELIC
LOGO
注射工艺过程
INJELIC
速度位置
时间
注射
喷嘴形式 多级注射
压力
级数
保压
开合模
速度 时间 转换方式/时间
冷却
开模速度 冷却时间
背压
级数
扭矩 转速 计量装置
塑化
位置
形式
速度
顶出
结构 尺寸
材料
刚度
浇口形式/尺寸 流道尺寸
浇道系统
型腔数
热流道温度
型腔精度
分型面精度
结构 壁厚
制品
平行度
模具温度
精度
模具 模温 控制
模温
方式
控制
Hale Waihona Puke 精度操作者1、气泡来自原料
2、气泡来自料筒
3、气泡来自注射过程
INJELIC
LOGO
制品银丝
INJELIC
▪ 1、水解银丝:因原料潮湿而产生的银丝,分布在整个制品中;
▪ 2、分解银丝:在成型过程中因原料分解而 产生,在制品表面分 布成彗星状,没有固定位置,有时会伴随变色、黑纹等分解现象
就产生原因分:胶料在料筒中分解;胶料流经喷嘴和浇口 时分解;胶料在型腔内过剪切分解。
制品品质
熟练程度 知识
LOGO
INJELIC
注塑机螺杆
螺杆三段:进料段、压缩段、计量段 长径比:螺杆有效长度和直径比
压缩比:进料段体积和计量段体积比
喷嘴 螺杆头 止逆环 介子 计量段 压缩段
进料段
170-200℃
200-220℃
170-190℃
LOGO
塑化过程理论
INJELIC
进料段功用: 1、料的输送
降低保压压力 优化保压切换点 缩短保压时间 提高注塑速度、提高模温(料温)
LOGO
顶针痕
▪ 1、顶针过短缩水
▪ 2、顶针过长缩水
▪ 3、顶针过大的弹性 形变缩水
LOGO
欠注-注塑压力不稳定
INJELIC
制品正常生产时 忽然缺料
230℃
200℃
加大压力后正常
忽然又涨模 减小压力
30℃
PA 、POM 、ABS 这几种材料会产生这种问题
现在浇口附近。
▪ 5、塑化银丝:塑化量过大塑化不良;背压不足;料筒温 度低塑化不良;塑化下料不良;
▪ 6、排气银丝:在充模过程中,如果模腔内的气体不能顺 利排除而形成银丝,一般会在该处有一个很深的熔接痕 。
▪ 7、工艺银丝:当射退过大时,在制品的浇口附近会出现 银丝,减小射退(抽胶)银丝消失。
LOGO
喷射痕
产生原因: 浇口直对深型腔,因注射速度
过快所产生 解决方法: 1、降低注射速度 2、提高料温降低胶料粘度 3、调整浇口位置和形式
INJELIC
LOGO
困气
解决方法:
1、调整注射速度 2、修改模具过度位置
的倒角
困气点
INJELIC
银丝 气勾纹 气体压出
LOGO
烧焦痕
产生原因:模具排气不良
解决方法:1、降低注射压力速度
2、降低模 温和料温
3、改善模 具排气
4、降低锁 模力
INJELIC
LOGO
飞边
产生原因:过量注射
解决方法:1、降低注射量
2、采用 多级注射
3、降低 注射、保
力和速度
压压
4、优化 转保压位置
INJELIC
LOGO
顶出坑纹(脱伤)
INJELIC
1、制品包模力过大(优化注射压力、保压转换点、保压压力、时间) 2、模具分型面毛刺 3、拔模斜度过低
INJELIC
常见产品缺陷及解决方法
塑料成型部
B版 2011年12月
LOGO
INJELIC
注塑工艺教程
LOGO
影响塑料制品品质的因素
INJELIC
原料
干燥方式
含湿率
结晶型/非结晶型
干燥时间 粘度
种类
添加剂 颗粒形状 收缩率
厂家
设定值
油温
注塑机
控制系统
温度
控制方式/精度
螺杆
结构
锁模力
模板平行度
压力 料垫
填充阶段:把胶料注入 模具型腔内。
P
压实阶段:增密
P
保压阶段:补缩
倒流阶段
LOGO
1
压 力
2 3
4=制品末端
4
0
Ta Tb Tc
Td
Te
Tf
时间
2=喷嘴 1=计量室
LOGO
模具温度对塑料制品的影响
▪ 模温功能:均匀冷却制品,缩
期、提高
短成型周
制品质量 ;
▪ 模温对制品品质的影响;
1、模温决定注射时间
间 4、降低熔体温度 5、降低注射速度 6、更改模具结构
缩孔
INJELIC
LOGO
制品内黑点
1、原料中有杂物(在制品
中,黑 点不规则)
2、模具表面杂物(在制品 表面)
3、原料分解(伴随制品变 黄)
INJELIC
LOGO
制品银丝
▪ 银丝产生机理:胶料中的气泡被压 到模具表面,气体压出后在制品表 面残留的白色的片层
LOGO
▪ 产生机理是胶 料在模腔内流 速过慢冷却速 度过快,冻结 后的胶料没有 办法贴紧模具 。
波浪形流痕
INJELIC
硬壳强度高
PS!
接近模壁的流动波 峰已经冷却
冷却了的外层阻 碍其他熔料流向 模壁
LOGO
解决方法: 1、提高注射速度 2、提高模具温度 3、提高料筒温度
4、适当增加射咀孔径或浇口
2、模温决定注射速度
3、模温决定注射压力
LOGO
保压设置
1、多级保压设定原则:不缩水、不 顶白、不出飞边、不出现顶出坑纹 、制品重量稳定;
2、保压结束的标志为制品浇口的冻 结;
3、时间转保压、位置转保压;
( 克 )
重 量
有效保压时间
时间(S)
LOGO
▪ 顶白
制品缺陷处理
LOGO
顶白产生原因:除去模具原因,制品包模力过大是主要原因。 解决方法:降低注射压力
INJELIC
LOGO
熔接痕
INJELIC
▪ 产生机理是在流动末端胶料温度很低结合性较差压力传 递弱,这样使两股料流结合不紧密。
解决方法: 1、提高注射压力、速度 2、提高模温 3、提高料温 4、改善模具 排气
LOGO
缩孔
INJELIC
LOGO
缩孔
▪ 制品内部泡是真空泡,是 因为缩水产生的。
▪ 解决方法: 1、提高注射压力 2、提高模具温度 3、提高保压压力、时
LOGO
混色不均
INJELIC
LOGO
▪ 解决方法: 1、检查色母是否匹配 2、如是色粉,用混料机混合 3、检查料粒 3、提高背压 4、提高料温
INJELIC
LOGO
INJELIC
制品冷料斑
▪ 冷料斑:制品局部发亮、发暗、粗糙等;
冷 料
LOGO
▪ 解决方法: 1、查看型腔表面是否有光泽、粗糙、异物; 2、提高料温、模温、注射速度; 3、注射速度快,进料口小,使融料气化,呈
乳白色薄层 4、模具浇口处加冷料井。
LOGO
欠注
INJELIC
LOGO
INJELIC
1、料在模腔内流动慢(常规缺料):注射速度 慢、
压力小、模温低、料温低等 2、排气不良:料在模腔内流动速度快
LOGO
INJELIC
学无 止境、刻苦研究
!
LOGO
INJELIC
LOGO
感谢下 载