圆筒拉深件冲压模设计
冲压模具课程设计说明书 2
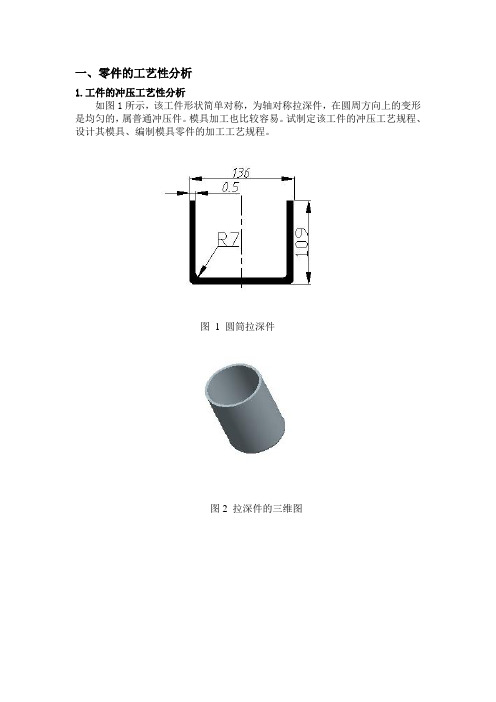
一、零件的工艺性分析1.工件的冲压工艺性分析如图1所示,该工件形状简单对称,为轴对称拉深件,在圆周方向上的变形是均匀的,属普通冲压件。
模具加工也比较容易。
试制定该工件的冲压工艺规程、设计其模具、编制模具零件的加工工艺规程。
图1 圆筒拉深件图2 拉深件的三维图2.工件材料化学成分和机械性能分析(1)材料分析工件的材料为08钢,属于优质碳素结构钢,优质沸腾钢,强度、硬度低,冷变形塑性很好,可深冲压加工,焊接性好。
成分偏析倾向大,时效敏感性大,故冷加工时应采用消除应力热处理或水韧处理,防止冷加工断裂。
08钢的主要机械性能如下:σ(兆帕) 280-390抗拉强度bσ(兆帕) 180屈服强度s抗剪强度(兆帕) 220-310延伸率δ 32%(2)结构分析工件为一窄凸缘筒形件,结构简单,圆角半径为r=7,厚度为t=0.5mm,满足筒形拉深件底部圆角半径大于一倍料厚的要求,因此,零件具有良好的结构工艺性。
(3)精度分析工件上尺寸均为未注公差尺寸,普通拉深即可达到零件的精度要求。
经上述分析,产品的材料性能符合冷冲压加工要求。
在零件工艺性分析的基础上制定其工艺路线如下:零件的生产包括落料、拉深(需计算确定拉深次数)、修边(采用机械加工)等工序,为了提高生产效率,可以考虑工序的复合,经比较决定采用落料与第一次拉深复合。
二、工件的拉深工艺分析及计算1.毛坯尺寸计算(1)计算原则相似原则:拉深前坯料的形状与拉深件断面形状相似;等面积原则:拉深前坯料面积与拉深件面积相等。
(2)计算方法由以上原则可知,旋转体拉深件采用圆形毛坯,其直径按面积相等的原则计算。
计算坯料尺寸时,先将拉深件划分为若干便于计算的简单几何体,分别求出其面积后相加,得拉深件总面积A。
图3 拉深件的坯料计算如图3所示,筒形件坯料尺寸,将圆筒件分成三个部分,每个部分面积分别为:(3)确定零件修边余量由于板料的各向异性和模具间隙不均等因素的影响,拉深后零件的边缘不整齐,甚至出现耳子,需在拉伸后进行修边。
带凸缘圆筒形件拉深模设计
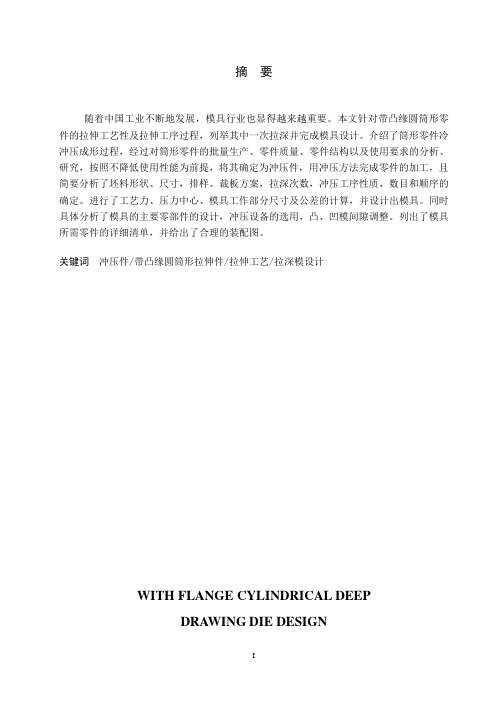
摘要随着中国工业不断地发展,模具行业也显得越来越重要。
本文针对带凸缘圆筒形零件的拉伸工艺性及拉伸工序过程,列举其中一次拉深并完成模具设计。
介绍了筒形零件冷冲压成形过程,经过对筒形零件的批量生产、零件质量、零件结构以及使用要求的分析、研究,按照不降低使用性能为前提,将其确定为冲压件,用冲压方法完成零件的加工,且简要分析了坯料形状、尺寸,排样、裁板方案,拉深次数,冲压工序性质、数目和顺序的确定。
进行了工艺力、压力中心、模具工作部分尺寸及公差的计算,并设计出模具。
同时具体分析了模具的主要零部件的设计,冲压设备的选用,凸、凹模间隙调整。
列出了模具所需零件的详细清单,并给出了合理的装配图。
关键词冲压件/带凸缘圆筒形拉伸件/拉伸工艺/拉深模设计WITH FLANGE CYLINDRICAL DEEPDRAWING DIE DESIGNABSTRACTAs China's industrial development unceasingly, the mold industry also appears more and more important. This paper belt of flange cylindrical parts stretching manufacturability and stretching process process, list one time deep drawing and complete the mold design. Cold stamping process of cylindrical parts is introduced, after mass production of the cylindrical parts, parts quality, parts structure, and use requirement analysis, research, according to not reduce the usability for the premise, to identify it for stamping parts, complete parts processing, with stamping method and the brief analysis of the blank shape, size, layout, cutting board, deep drawing, stamping process in nature, the determination of number and order. The technology force, pressure center, mold working parts dimension and tolerance of calculation, and design the mold. At the same time, concrete analysis of main components of the mold design, the selection of stamping equipment, convex and concave die clearance adjustment. Lists the mould needs a detailed list of spare parts, and gives the reasonable assembly drawing.KEYWORDS stamping parts, flange cylindrical stretching, stretching, deep drawing die design process目录1 前言 (1)1.1 模具的概论 (1)1.1.1 冲压与冲模 (1)1.1.2 我国冲压现状与发展方向 (2)1.1.3 国外模具发展趋势及行业特点 (2)1.1.4 模具设计及加工技术的现状 (3)1.1.6 冲模的零部件 (4)1.2 冲压件工艺分析 (5)1.2.1 冲压加工的经济性分析 (5)1.2.2 冲压件的工艺性分析 (5)1.3 本设计要求 (6)2 工艺方案 (7)2.1 工艺性分析 (7)2.1.1 拉深件的结构与尺寸 (7)2.1.3拉深件材料 (7)2.2 设计方案的确定 (7)3 主要工艺参数计算 (8)3.1 确定排样、裁板方案 (8)3.1.1 工艺分析 (8)3.1.2 确定修边余量 (8)3.1.3 坯料直径 (8)3.1.4 排样 (9)3.1.5 压力中心的确定 (10)3.2 拉深工艺的计算 (10)3.2.1 压边 (10)3.2.2 总拉深系数 (10)3.2.3 预算拉深次数 (10)3.2.4 确定首次拉深工序件尺寸 (11)3.2.5 确定拉深次数及以后各次拉深的工序件尺寸 (12)3.2.6 第二次拉深直径和高度 (13)3.2.7 第三次拉深直径和高度 (13)3.2.8 修边 (14)3.2.9 拉深速度 (14)3.3 工艺力计算 (14)3.3.1 拉深力 (14)3.3.2 压料力 (15)3.4 压力机的选择 (16)3.4.1 初选压力机 (16)3.4.2拉深功 (16)3.4.3压力机电动机功率 (16)3.4.4功率校核 (17)4 拉深模设计 (17)4.1拉深模具结构设计 (17)4.2模具工作部分尺寸计算 (17)4.2.1 凸凹模间隙 (17)4.2.2 凸凹模圆角半径 (17)4.2.3凸凹模工作尺寸及公差 (17)4.3标准件的选取 (18)4.3.1 模架 (18)4.3.2下模座 (19)4.3.3上模座 (19)4.3.4 导柱、导套 (19)4.3.5 销钉 (19)4.3.6 螺钉 (20)4.3.7 模柄 (20)4.3.8带螺纹推杆(顶杆) (20)4.3.9 打杆 (20)4.3.10 打杆螺母 (21)4.3.11 橡胶的选取 (21)4.3.12 橡胶螺杆 (22)4.3.13 ;螺杆螺母 (22)4.3.14 模柄紧固螺钉 (22)4.4模具非标准件的设计 (22)4.4.1 拉深凸模的设计 (22)4.4.2拉深凹模的设计 (23)4.4.3 凸模固定板设计 (24)4.4.4压料圈的设计 (24)4.4.6 托板的设计 (25)5 压力机的校核 (25)6 模具装配图 (26)结束语 (27)致谢 (28)参考文献 (29)1 前言板料冲压是金属加工的一种基本方法,他用以生产各种板料零件,具有生产效率高、尺寸精度好、重量轻、成本低并易于实现机械化和自动化等特点。
圆筒形件的拉深
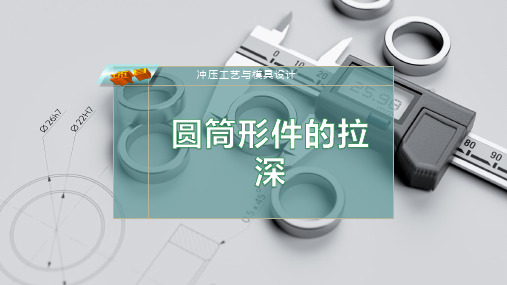
1.1 拉深系数
1) 材料的力学性能
3) 材料的表面质量
5) 润滑条件
圆筒形件的拉深
2) 材料的相对厚度 t/D
及压边圈的使用 4)
拉深次数
6) 拉深速度
1.2 拉深次数的确定
圆筒形件的拉深
拉深件一般经过几次拉深才能达到最终 尺寸形状。如果拉深件总的拉深系数 m总 大 于第一次允许的极限拉深系数 m1,即: m总> m1。
冲压工艺与模具设计
1.1 拉深系数
圆筒形件的拉深
拉深系数表示拉深后圆筒形件的直 径 d 与拉深前毛坯(或半成品)的直径 D 之比。拉深系数表示拉深时板料的变 形程度,用符号 m 表示。M 是小于1的 系数,m 值越小,说明拉深时变形程度
越大。
1.1 拉深系数
圆筒形件的拉深工件总的Fra bibliotek形系数:圆 筒 形 件 的 多 次 拉 深
说明拉深该工件的实际变形程度比第一
次容许的极限变形程度要小,工件可以一次
拉成。否则需要多次拉深才能成形。
圆筒形件的拉深
1.3 各次拉深工序尺寸的确定
圆筒形件的拉深
1.3 各次拉深工序尺寸的确定
冲压工艺与模具设计
[机械电子]圆筒形件拉深模设计
![[机械电子]圆筒形件拉深模设计](https://img.taocdn.com/s3/m/9afb6e40856a561253d36f83.png)
按功能分类
(1)经济型数控车床 采用步进电动机和单片机对普通车床 的进给 系统进 行改造 后形成 的简易 型数控 车床, 成本较 低,但 自动化 程度和 功能都 比较差 ,车削 加工精 度也不 高,适 用于要 求不高 的回转 类零件 的车削 加工。
(2)普通数控车床 根据车削加工要求在结构上进行专门 设计并 配备通 用数控 系统而 形成的 数控车 床,数 控系统 功能强 ,自动 化程度 和加工 精度也 比较高 ,适用 于一般 回转类 零件的 车削加 工。这 种数控 车床可 同时控 制两个 坐标轴 ,即X轴 和Z轴 。
圆筒形件拉深模设计
学习目的与要求:
1.了解拉深变形规律及拉深件质量影响因素; 2.掌握拉深工艺计算方法。 3.掌握拉深工艺性分析与工艺设计方法; 4.认识拉深模典型结构及特点,掌握拉深模工作零件设计方 法; 5.掌握拉深工艺与拉深模设计的方法和步骤。
圆筒形件拉深模设计
本学习情境重点:
1.拉深变形规律及拉深件质量影响因素; 2.拉深工艺计算方法; 3.拉深工艺性分析与工艺方案制定; 4.拉深模典型结构与结构设计; 5.拉深工艺与拉深模设计的方法和步骤。
热处理的高速钢,又叫作白钢。
硬质合金 硬质合金由难熔材料的碳化钨、碳 化钛和 钴的粉 末,在 高压下 成形, 经1350-1560摄氏度 高温烧
结而成的。具有极高的硬度,常温下 可达HR A92, 仅次于 金刚石 ;红硬 性很好 ,在1000摄氏 度左右 仍能保 持良好 的切削 机能; 具有较 高使用 强度, 抗弯
圆筒形件拉深模设计
第一节 拉深基本原理
(2)网格变化
① 筒底 无变化
② 筒壁 无变化
③ 凸缘区 径向伸长,切向压缩。
(2)拉深变形特点
第一节 圆筒形零件拉深讲解
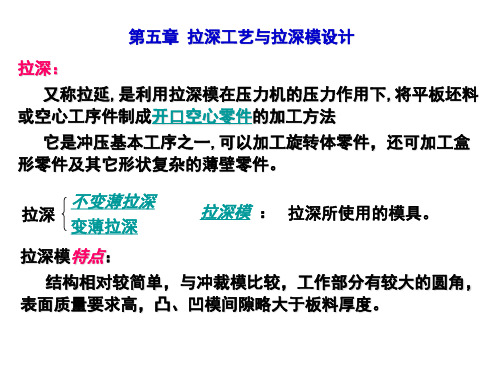
筒壁传力区拉裂: 由于拉应力超过抗拉强度引起板料断裂。
一、无凸缘圆筒形零件拉深 4、圆筒形零件拉深成形的缺陷及防止措施
1)凸缘变形区的起皱 主要决定于:
切向压应力σ3的大小,越大越容易失稳起皱; 凸缘区板料本身的抵抗失稳的能力。
凸缘宽度越大,厚度越薄,材料弹性模量和硬化模量越小, 抵抗失稳能力越差。
第n次拉深系数: mn=dn/dn-1
6、拉深系数的确定 1)拉深系数的概念
拉深系数m 表示拉深前后坯料(工序件)直径的变化率.
m 愈小,说明拉深变形程度愈大,相反变形程度愈小. 拉深件的总拉深系数等于各次拉深系数的乘积,即
若m 取得过小,会使拉深件起皱、断裂或严重变薄超差。 极限拉深系数: 工件在危险断面不至拉破时,所能达到的最小拉深系数mmin。
压料装置产生的压料力Fy大小应适当;
在保证变形区不起皱的前提下,尽量选用小的压料力。 理想的压料力是随起皱可能性变化而变。
9、圆筒形零件拉深的压料力和拉深力
2)拉深力与压力机的公称压力 ①拉深力F
按经验公式可计算出圆筒形件带压料装置和不带压料装置的 首次拉深和以后各次拉深的拉深力。 ②压力机的公称压力
②金属的流动过程 工艺网格实验 材料转移:高度、厚度发生变化。
③拉深变形过程
外力
凸缘产生内应力: 径向拉应力σ1;切向压应力σ3
凸缘塑性变形: 径向伸长,切向压缩,形成筒壁
直径为d高度为H的圆筒形件(H>(D-d)/2)
拉深单元变形动画
一、无凸缘圆筒形零件拉深
2、圆筒形零件拉深过程中坯料内的应力与应变状态 拉深过程中某一瞬间坯料所处的状态
当筒壁拉应力超过筒壁材料的抗拉强度时,拉深件就会在 底部圆角与筒壁相切处——“危险断面”产生破裂。
课程设计带凸缘筒形件首次拉深的拉深模设计
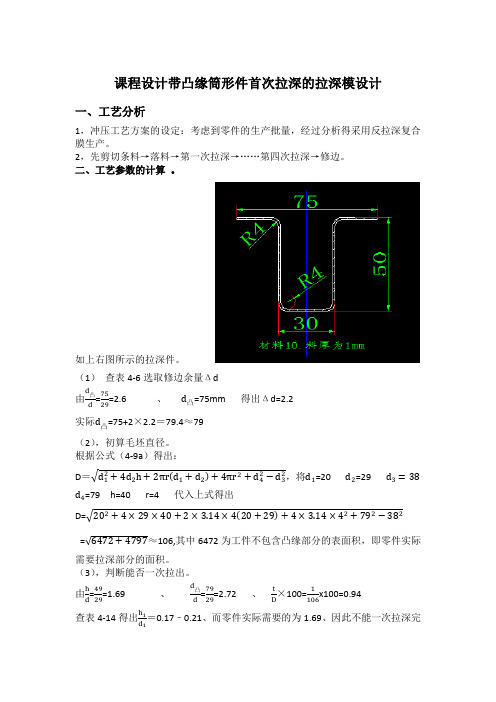
课程设计带凸缘筒形件首次拉深的拉深模设计一、工艺分析1,冲压工艺方案的设定:考虑到零件的生产批量,经过分析得采用反拉深复合膜生产。
2,先剪切条料→落料→第一次拉深→……第四次拉深→修边。
二、工艺参数的计算 。
如上右图所示的拉深件。
(1) 查表4-6选取修边余量Δd 由d 凸d=7529=2.6 、 d 凸=75mm 得出Δd=2.2实际d 凸=75+2×2.2=79.4≈79 (2),初算毛坯直径。
根据公式(4-9a )得出:D =√d 12+4d 2h +2πr (d 1+d 2)+4πr 2+d 42−d 32,将d 1=20 d 2=29 d 3=38d 4=79 h=40 r=4 代入上式得出D=√202+4×29×40+2×3.14×4(20+29)+4×3.14×42+792−382 =√6472+4797≈106,其中6472为工件不包含凸缘部分的表面积,即零件实际需要拉深部分的面积。
(3),判断能否一次拉出。
由h d =4929=1.69 、d 凸d=7929=2.72 、 t D ×100=1106x100=0.94查表4-14得出h1d 1=0.17﹣0.21、而零件实际需要的为1.69、因此不能一次拉深完成。
(4),计算拉深次数及各工序的拉深直径。
,因此需要用试凑法计算利用表4-14来进行计算,但由于有两个未知数m和d td1拉深直径。
下面用逼近法来确定第一的拉深直径。
的值为由于实际拉深系数应该比极限拉伸系数稍大,才符合要求,所以上表中d td11.5、1.6、1.7的不合适。
因为当d t的值取1.4的时候,实际拉深系数与极限拉深系数接近。
故初定第一次d1拉深直径d1=56.因以后各次拉深,按表4-8选取。
故查表4-8选取以后各次的拉深系数为当m2=0.77时d2=d1×m2=56×0.77=43mm当m2=0.79时d3=d2×m3=43×0.79=34mm当m3=0.81时d4=d3×m4=34×0.81=27mm<29mm因此以上各次拉程度分配不合理,需要进行如下调整。
17809-冲压工艺与模具设计-电子教案-模块4
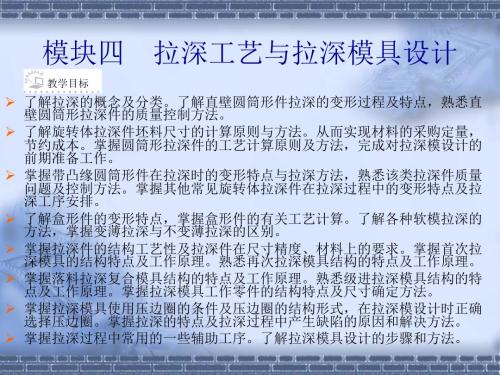
盒形件拉深时的应力分布
项目一 拉深工艺
低盒形件拉深件的毛坯
项目一 拉深工艺
高盒形件拉深件的毛坯
项目一 拉深工艺
任务八 其他拉深方法 变薄拉深件图
项目一 拉深工艺
液体凸模拉深的变形过程
项目一 拉深工艺
聚氨酯橡胶拉深模 强制润滑拉深
项目一 拉深工艺
变薄拉深
项目一 拉深工艺
项目二 拉深模具结构及工作原理
任务一 首次拉深模具的结构及工作原理
1. 无压边首次拉深模具
2. 有压边的首次拉深模具
项目二 拉深模具结构及工作原理
无压边装置的首次拉深模具 工作时,毛坯在定位圈3中 定位,拉深结束后,工件由 凹模底部的台阶完成脱模, 并由下模座底孔落下。由于 模具没有采用导向机构,故 模具安装时由校模圈2完成 凸、凹模的对中,保证间隙 均匀,工作时将校模圈移走。 该模具结构简单,制造方便, 通常用于材料塑性好、相对 厚度较大的零件拉深。由于 其凸模要深入凹模,所以只 适用于浅拉深。
项目二 拉深模具结构及工作原理
任务一 首次拉深模具的结构及工 作原理 任务二 再次拉深模具的结构及工 作原理
模块小结
项目一 拉深工艺
任务一 拉深概念及分类 典型拉深件
项目一 拉深工艺
拉深件的分类
项目一 拉深工艺
不变薄拉深
项目一 拉深工艺
变薄拉深
项目一 拉深工艺
任务二 直壁圆筒形件拉深的变形过程及特点 圆筒形拉深件
项目二 拉深模具结构及工作原理
无压边圈的再次拉深模具
项目二 拉深模具结构及工作原理
带弹性压边圈的再次拉深模具
项目二 拉深模具结构及工作原理
拉深工艺及拉深模设计

拉深工艺及拉深模设计本章内容简介:本章在分析拉深变形过程及拉深件质量影响因素的基础上,介绍拉深工艺计算、工艺方案制定和拉深模设计。
涉及拉深变形过程分析、拉深件质量分析、圆筒形件的工艺计算、其它形状零件的拉深变形特点、拉深工艺性分析与工艺方案确定、拉深模典型结构、拉深模工作零件设计、拉深辅助工序等。
学习目的与要求:1.了解拉深变形规律、掌握拉深变形程度的表示;2.掌握影响拉深件质量的因素;3.掌握拉深工艺性分析。
重点:1. 拉深变形特点及拉深变形程度的表示;2.影响拉深件质量的因素;3.拉深工艺性分析。
难点:1.拉深变形规律及拉深变形特点;2.拉深件质量分析;3.拉深件工艺分析。
拉深:利用拉深模将一定形状的平面坯料或空心件制成开口空心件的冲压工序。
拉深工艺可以在普通的单动压力机上进行,也可在专用的双动、三动拉深压力机或液压机上进行。
拉深件的种类很多,按变形力学特点可以分为四种基本类型,如图5-1所示。
图5-1 拉深件示意图5.1 拉深变形过程分析5.1.1 拉深变形过程及特点图5-2所示为圆筒形件的拉深过程。
直径为D、厚度为t的圆形毛坯经过拉深模拉深,得到具有外径为d、高度为h的开口圆筒形工件。
图5-2 圆筒形件的拉深1.在拉深过程中,坯料的中心部分成为筒形件的底部,基本不变形,是不变形区,坯料的凸缘部分(即D-d的环形部分)是主要变形区。
拉深过程实质上就是将坯料的凸缘部分材料逐渐转移到筒壁的过程。
2.在转移过程中,凸缘部分材料由于拉深力的作用,径向产生拉应力,切向产生压应力。
在和的共同作用下,凸缘部分金属材料产生塑性变形,其“多余的三角形”材料沿径向伸长,切向压缩,且不断被拉入凹模中变为筒壁,成为圆筒形开口空心件。
3.圆筒形件拉深的变形程度,通常以筒形件直径d与坯料直径D的比值来表示,即m=d/D(5-1)其中m称为拉深系数,m越小,拉深变形程度越大;相反,m越大,拉深变形程度就越小。
5.1.2 拉深过程中坯料内的应力与应变状态拉深过程是一个复杂的塑性变形过程,其变形区比较大,金属流动大,拉深过程中容易发生凸缘变形区的起皱和传力区的拉裂而使工件报废。
圆筒形件冲压工艺设计

3.3凸、凹模工作部分的尺寸
• (1)凹模圆角半径rd
• 查表4-6,rd1取12t,即6mm。
• (2)凸模圆角半径rp
• 可取rp=rd,最后一道拉深时rp等于零件的圆角半径, 3个圆角半径分别为6mm,4.5mm,2mm。
• (3)凹、凸模间隙c
• 不用压边圈拉深时,c=(1~1.1)tmax • 取c为0.5mm。
1.冲压件特点
该冲压件为圆筒形件 尺寸不大,精度要求 较高材料较薄
2.工程应用举例
• 饭盆,脸盆,圆桶,易拉罐等筒形容器 • 液化气罐等压力容器
3.工艺计算及其模具设计
3.1工艺分析
• (1)冲压件的形状和尺寸
• 该零件为圆筒形拉深件件,材料很薄,拉深高度较 大,需多次拉深。内壁圆角半径大于料厚的5倍, 不用增加整形工序。
• (2)冲压件精度
• 查表7-10和7-11可知,圆筒件径向精度可以达到, 但高度尺寸精度相差太大,无法达到,且板料太 薄,影响拉深质量。
(3)尺寸标注
图中要求保证外壁尺寸,高度方向尺寸以底部为 基准高度尺寸容易保证。
(4)生产批量
图中没有给出要求,冲压生产宜采用大批量生产 方式,以取得经济效益。
• (4)凹、凸模尺寸及制造公差
• 凹模尺寸:
• 凸模尺寸:
• 3.4拉深力计算 • 3.5拉深功
3.6 工艺方案
• 方案一: (1)落料和首次拉深。 (2)第二次拉深。 (3)第三次拉深。
方案二:(1)落料和首次拉深。 (2)两次拉深同时进行。
经比较,选择方案二。
3.7 模具结构形式的确定
3.6 设备选择
结论:该圆筒件要进行冲压生产,需要增加 料厚,取0.5mm,多次拉深,降低高度方向 精度要求,且大批量生产才合理。
无凸缘圆筒件D62设计

制件壁部与底 部都呈现黄色 和淡黄色,都 处于安全的范 围之内。
底部圆角部分呈红色
,减薄比较严重,如图, 在所取点中,第四点厚 度减薄最严重。
圆筒底部边缘部分为
蓝色,圆边部分呈深蓝 色,增厚比较严重,从 圆角两边到直边中间, 增厚逐渐严重。如图, 第四点厚度最后,增厚 最严重。
控制措施
• 控制起皱的措施
具体零件工艺计算过程
力的计算 拉深力
F
拉
dt
k
b
1
3 . 14 60 2 400 1 150 . 70 KN
2
压边力 F 压 落料力
2 D
4
d t 2 r
P 3 . 14 115 4
2
60 2 2 6 2 . 8 17 . 00 KN
参考文献
【1】《金属薄板成形技术》王先进、陈鹤铮,兵器工业出 版社,1993. 【2】《板料冲压成形CAE实用教程》龚红英主编,北京-化 学工业出版社,2010. 【3】《板料成型基础》胡城立,武汉理工大学出版社, 2009
谢谢观看
第一章 零件工艺性分析
1、材料分析
2、结构分析
3、精度分析
材料分析:
本工件材质为DQSK36(Drawing quality special killed),属于冷拔 优质的特殊镇静钢,又称优质的冲 压特殊镇静钢,为低碳钢,属于深 拉深级别的材料,具有良好的拉深 成形性能。
圆筒件拉深模具设计

圆筒件拉深模具设计拉深是主要的冲压工序之一,而圆筒件又是最典型的拉深件。
本论文以外胆下壳零件为例,介绍了拉深零件工艺的制定、模具设计过程。
从毛坯尺寸的确定,拉深系数和拉深次数的选择,凸凹模尺寸的计算,拉深方式的选择到模具结构的最终敲定,从而建立了拉深模设计的基本过程。
本次设计的模具及工艺在生产实践中切实可行,取得了较好的经济效果。
标签:圆筒件拉深;拉深件工艺;凸凹模计算;模具结构1 零件毛坯尺寸的确定旋转体零件系采用圆形毛坯,其直径按面积相等原则计算。
以前,计算毛坯尺寸时,先将零件划分为若干便于计算的简单几何体,分别求出其面积后相加。
计算量大且容易出错,现在,利用计算机三维软件,如SolidWorks等,可以方便准确的计算出零件总表面积。
零件如图1所示,材料为3A21。
本零件相对高度为,参考《航空工艺装备设计手册-冷冲模设计》的表4-2 ,选取修边余量δ=11mm。
加上修边余量,在SolidWorks中设计出零件图,得出其总表面积ΣA=180950mm2。
毛坯直径:2 拉深系数和次数毛坯的相对厚度,(t为毛坯厚度)。
4 持续改进4.1 第二道拉深模的改进为了减小金属流动的阻力,凹模口部做成锥形。
这样,拉深毛坯的过渡形状呈曲面,具有了更大一些的抵抗塑性失稳的能力,使得起皱的趋向有所减小,其拉深效果比圆筒形好。
4.2 反拉深凹模的改进反拉深的凹模如果为整体,高度比较高,浪费比较贵的模具钢,加工难度大,需热处理的材料也多。
若改成三段组合,则比较节省。
5 模具结构设计参考文献:[1]王孝培.冲压手册(第二版)[M].机械工业出版社,2000.[2]《冲模设计手册》编写组.冲模设计手册—模具手册之四[M].机械工业出版社,1988.[3]郑家贤.冲压工艺与模具设计实用手册[M].机械工業出版社,2005.[4]《航空工艺装备设计手册》编写组.航空工艺装备设计手册—冷冲模设计[M].国防工业出版社,1998.基金资助:河南工程学院.机械基础与工程训练河南省实验教学示范中心(省级项目,编号508906)作者简介:黄宏俊(1981-),男,河南平顶山人,本科,讲师,研究方向:机械设计制造及其自动化。
冲压模课程设计圆筒形
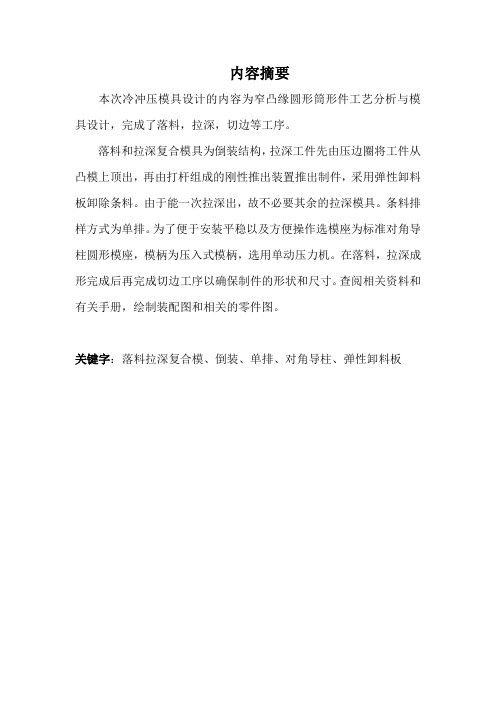
内容摘要本次冷冲压模具设计的内容为窄凸缘圆形筒形件工艺分析与模具设计,完成了落料,拉深,切边等工序。
落料和拉深复合模具为倒装结构,拉深工件先由压边圈将工件从凸模上顶出,再由打杆组成的刚性推出装置推出制件,采用弹性卸料板卸除条料。
由于能一次拉深出,故不必要其余的拉深模具。
条料排样方式为单排。
为了便于安装平稳以及方便操作选模座为标准对角导柱圆形模座,模柄为压入式模柄,选用单动压力机。
在落料,拉深成形完成后再完成切边工序以确保制件的形状和尺寸。
查阅相关资料和有关手册,绘制装配图和相关的零件图。
关键字:落料拉深复合模、倒装、单排、对角导柱、弹性卸料板目录设计题目 (1)第1章绪论 (1)1.1冲压设计概论 (1)1.2冲压设计的基本内容 (2)1.3冲压设计的一般工序 (3)第2章工艺分析 (3)2.1产品冲裁工艺分析 (3)2.1.1 产品结构形状分析工艺分析 (3)2.1.2产品尺寸精度、断面质量分析 (3)第3章工艺方案的确定及工艺计算 (4)3.1 工艺方案分析 (5)3.2主要工艺参数的计算 (5)3.2.1确定修边余量 (5)3.2.2计算毛坯直径D (5)3.2.3判断能否一次拉成 (5)3.2.4验证拉深系数 (5)3.2.5 落料工序 (5)3.3确定排样图 (6)3.4.1压边力的的计算 (6)3.4.2 拉深力的计算力的的计算 (7)3.4.3落料力的计算 (8)3.4.4冲压设备的确定 (8)3.4.5压力机功率的核算 (9)3.5模具压力中心的确定 (10)3.6拉伸模工作部分结构和尺寸设计 (10)第4章模具的结构与主要零部件尺寸 (12)4.1模具结构选择 (12)4.2凸模工作尺寸 (12)4.3料凹模工作尺寸 (13)4.4凸凹模工作尺寸 (14)4.5压边圈工作尺寸 (14)4.6固定零件设计 (15)4.7卸料零件设计 (15)4.8定位零件设计 (15)4.9模架设计 (16)4.10弹顶器的弹性元件的选取 (16)4.11模具的工作过程 (17)4.12模具装配总图 (18)第5设计体会和小结 (19)参考文献 (20)设计题目:桶形件拉伸模设计1、冲裁件下图1所示所示。
落料—拉深复合冲压模具课程设计【完整版】

落料—拉深复合冲压模具课程设计【完整版】(文档可以直接使用,也可根据实际需要修订后使用,可编辑放心下载)零件简图:如右图所示生产批量:大批量材料:08钢材料厚度:2mm1.冲压件工艺性分析该工件属于典型圆筒形件拉深,形状简单对称。
所有尺寸均为自由公差,尺寸容易保证。
高度尺寸91mm可在拉深后采用修边到达要求。
2.冲压工艺方案确实定该工件包括落料、拉深两个根本工序。
可有以下三种工艺方案:方案一:先落料,后拉深。
采用单工序模生产。
方案二:落料—拉深复合冲压。
采用复合模生产。
方案三:拉深级进冲压。
采用级进模生产。
方案一模具结构简单,但需两道工序两副模具,生产效率低,难以满足该工件大批量生产的要求。
方案二只需一副模具,生产效率较高,尺管模具结构较方案一复杂,但由于零件的几何形状简单对称,模具制造并不困难。
方案三也只需一副模具,生产效率高,但模具结构比拟复杂,送进操后不方便,加之工件尺寸偏大。
通过对上述三种方案的分析比拟,该件假设能一次拉深,那么其冲压生产采用方案二为佳。
3.主要设计计算(1)毛坯尺寸计算根据外表积相等原那么,用解析法求该零件的毛坯直径DD=√ ̄〔d2* d2+4*d2H-1.72rd2-0.56r*r〕D=√ ̄(160*160+4*160*91-1.72*12*160-0.56*12*12)D=283.65 mm(2)排样及相关计算采用有废料直排的排样方式,相关如下示冲裁件面积A=∏*D*D/4=∏=63159平方毫米条料宽度B=D+2a+C=283.65+2*1.8+1=288.25 mma——侧搭边值,查冲压教程表得最小侧搭边值a=1.8mmc——导料板与最宽条料之间的间隙,其最小值查冲压教程表得c=1步距s=D+a=283.65+1.5=285.15 mm式中a1——工件间搭边值,查冲压教程表得a1=1.5mm一个步进距的材料利用率∩=A/BS*100℅∩℅∩=76.8℅式中:A——一个步距内冲裁件的实际面积B———条料宽度S———步距〔3〕成形次数确实定该工件为简单圆筒形拉深件,求出拉深相对高度H/h=91/160=0.57。
圆筒件落料拉深冲压模具课程设计说明书解读

课程设计课程名称材料成型工艺及设计题目名称圆筒件的模具设计专业班级材控112 学号33311227学生姓名张孝富指导教师聂信天夏荣霞徐秀英2014年 9 月 25日目录课程设计任务书 (3)产品图及设计说明 (3)序言 (4)第1章制件的工艺性分析 (5)1.1 圆筒件工艺性分析 (5)1.2 零件工艺方案的确定 (5)第2章工艺方案的制定及分析比较 (6)第3章圆筒形拉深件工艺计算 (7)3.1 工艺尺寸的计算 (7)3.2 拉深力的确定 (9)3.2.1首次拉深 (9)3.2.2第二次拉深 (10)3.2.3第三次拉深 (10)3.2.4第四次拉深 (10)3.2.5确定压力中心 (11)3.3 拉深模间隙 (11)3.4 凸凹模工作部分的尺寸及公差的确定 (11)3.4.1第一次拉深 (11)3.4.2第二次拉深 (11)3.4.3第三次拉深 (12)3.4.4第四次拉深 (12)3.5 落料拉深复合模其它工艺计算 (12)3.6 排样图设计及材料利用率计算 (13)3.7 压边的橡胶计算 (14) (15)3.8 卸料装置的设计 (15)3.8.1刚性卸料装置 (15)3.8.2弹性卸料装置 (15)3.8.3橡皮的选用 (16)3.8.4卸料板 (16)3.8.5推件装置 (16)3.8.6卸料螺钉第4章模具结构的确定 (17)4.1模具的形式 (17)4.1.1 正装式特点 (17)4.1.2 倒装式特点 (17)4.2 定位装置 (17)4.3 卸料装置 (17)4.3.1 条料的卸除 (17)4.3.2 工件的卸除 (17)4.4 导向零件 (17)4.5 模架 (17)4.5.1标准模架的选用 (18)第5章编写工艺卡片 (18)结束语 (19)参考文献 (20)课程设计任务书题目名称圆筒件的模具设计专业班级材控112姓名张孝富学号33311227产品图及设计说明零件简图:如右图所示。
第四章 拉深工艺与模具设计
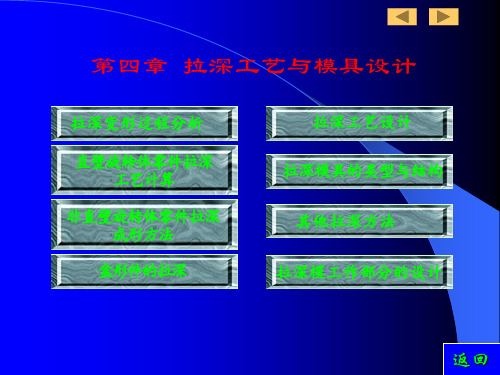
t D
Ky (1
m1 )
以后各次拉深中制件不起皱的条件是: 实践证明:
t di1
K
y
(
1 m1
1)
直壁圆筒形件的首次拉深中起皱最易发生的时刻:拉深的初期
(二)拉裂 当筒壁拉应力超过筒壁材料的抗拉强度时,拉深件就会在底部圆角与 筒壁相切处——“危险断面”产生破裂。
为防止拉裂,可以从以下几方面考虑: (1)根据板材成形性能,采用适当的拉深比和压边力; (2)增加凸模表面粗糙度;改善凸缘部分的润滑条件; (3)合理设计模具工作部分形状;选用拉深性能好的材料等。
第四章 拉深工艺与模具设计
拉深变形过程分析
直壁旋转体零件拉深 工艺计算
非直壁旋转体零件拉深 成形方法
盒形件的拉深
拉深工艺设计 拉深模具的类型与结构
其他拉深方法 拉深模工作部分的设计
返回
拉伸:
拉深是利用拉深模具将冲裁好的平板毛坯压制成各种开口的空心工 件,或将已制成的开口空心件加工成其它形状空心件的一种冲压加 工方法。拉深也叫拉延。
(二)筒壁传力区的受力分析
1.压边力Q引起的摩擦力:
m
2Q dt
2.材料流过凹模圆角半径产生弯曲变形的阻力
w
1 4
b
rd
t t
/
2
3.材料流过凹模圆角后又被拉直成筒壁的反向弯曲w 力 仍按上式进行计
算,拉深初期凸模圆角处的弯曲应力也按上式计算
w
w
1 4
b
rd
t t
2)筒底圆角半径rn
筒底圆角半径rn即是本道拉深凸模的圆角半径rp,确定方法如下:
r r 一般情况下,除末道拉深工序外,可取 pi = di。 对于末道拉深工序:
无凸缘圆筒形件的落料——拉深复合模具设计
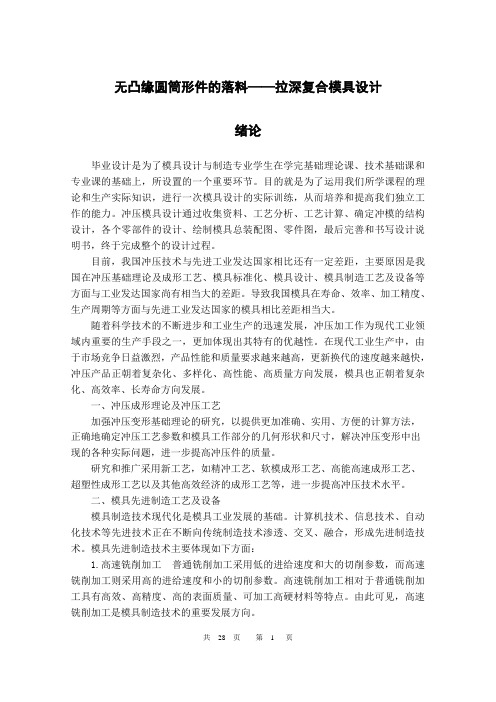
无凸缘圆筒形件的落料——拉深复合模具设计绪论毕业设计是为了模具设计与制造专业学生在学完基础理论课、技术基础课和专业课的基础上,所设置的一个重要环节。
目的就是为了运用我们所学课程的理论和生产实际知识,进行一次模具设计的实际训练,从而培养和提高我们独立工作的能力。
冲压模具设计通过收集资料、工艺分析、工艺计算、确定冲模的结构设计,各个零部件的设计、绘制模具总装配图、零件图,最后完善和书写设计说明书,终于完成整个的设计过程。
目前,我国冲压技术与先进工业发达国家相比还有一定差距,主要原因是我国在冲压基础理论及成形工艺、模具标准化、模具设计、模具制造工艺及设备等方面与工业发达国家尚有相当大的差距。
导致我国模具在寿命、效率、加工精度、生产周期等方面与先进工业发达国家的模具相比差距相当大。
随着科学技术的不断进步和工业生产的迅速发展,冲压加工作为现代工业领域内重要的生产手段之一,更加体现出其特有的优越性。
在现代工业生产中,由于市场竞争日益激烈,产品性能和质量要求越来越高,更新换代的速度越来越快,冲压产品正朝着复杂化、多样化、高性能、高质量方向发展,模具也正朝着复杂化、高效率、长寿命方向发展。
一、冲压成形理论及冲压工艺加强冲压变形基础理论的研究,以提供更加准确、实用、方便的计算方法,正确地确定冲压工艺参数和模具工作部分的几何形状和尺寸,解决冲压变形中出现的各种实际问题,进一步提高冲压件的质量。
研究和推广采用新工艺,如精冲工艺、软模成形工艺、高能高速成形工艺、超塑性成形工艺以及其他高效经济的成形工艺等,进一步提高冲压技术水平。
二、模具先进制造工艺及设备模具制造技术现代化是模具工业发展的基础。
计算机技术、信息技术、自动化技术等先进技术正在不断向传统制造技术渗透、交叉、融合,形成先进制造技术。
模具先进制造技术主要体现如下方面:1.高速铣削加工普通铣削加工采用低的进给速度和大的切削参数,而高速铣削加工则采用高的进给速度和小的切削参数。
筒形件落料、拉深、冲孔、复合模模具课程设计剖析

目录序言 (2)第一部分冲压成形工艺设计 (5)Ⅰ明确设计任务,收集相关资料 (5)Ⅱ冲压工艺性分析 (6)Ⅲ制定冲压工艺方案 (6)Ⅳ确定毛坯形状,尺寸和主要参数计算 (10)第二部分冲压模具设计 (15)rⅡ计算工序压力,选择压力机 (16)Ⅲ计算模具压力中心 (19)Ⅴ、弹性元件的设计 (25)Ⅵ模具零件的选用 (27)Ⅶ冲压设备的校核 (29)Ⅷ其他需要说明的问题 (30)Ⅸ模具装配 (32)设计总结 (35)参考文献 (36)序言目前我国模具工业与发达国家相比还相当落后。
主要原因是我国在模具标准化,模具制造工艺及设备等方面与工业发达国家相比差距很大。
随着工业产品质量的不断提高,模具产品生成呈现的品种、少批量、复杂、大型精密更新换代速度快。
模具设计与技术由于手工设备,依靠人工经验和常规机加工,技术向以计算机辅助设计,数控编程切屑加工,数控电加工核心的计算机辅助设计(CAD/CAM)技术转变。
模具生产制件所表现出来的高精度,高复杂程度,高生产率,高一致性和抵消耗是其它制造加工方面所不能充分展示出来,从而有好的经济效益,因此在批量生产中得到广泛应用,在现代工业生产中有十分重要的地位,是我国国防工业及民用生产中必不可少的加工方法。
随着科学技术的不断进步和工业生产的迅速发展,冲压零件日趋复杂化,冲压模具正向高效、精密、长寿命、大型化方向发展,冲模制造难度日益增大。
模具制造正由过去的劳动密集、依靠人工的手工技巧及采用传统机械加工设备的行业转变为技术密集型行业,更多的依靠各种高效、高精度的NC机床、CNC机床、电加工机床,从过去的单一的机械加工时代转变成机械加工、电加工以及其他特种加工相结合的时代。
模具制造技术,已经发展成为技术密集型的综合加工技术。
本专业以培养学生从事模具设计与制造工作能力的核心,将模具成型加工原理、设备、工艺、模具设计与制造有机结合在一起,实现理论与实际相结合,突出实用性,综合性,先进性。
- 1、下载文档前请自行甄别文档内容的完整性,平台不提供额外的编辑、内容补充、找答案等附加服务。
- 2、"仅部分预览"的文档,不可在线预览部分如存在完整性等问题,可反馈申请退款(可完整预览的文档不适用该条件!)。
- 3、如文档侵犯您的权益,请联系客服反馈,我们会尽快为您处理(人工客服工作时间:9:00-18:30)。
题目:圆筒拉深件:如下图,材料;spcen生产批量年产20万件。
请设计其冲压之总装配图及模具主要零件的各零件图(任选一副模具,如:首次拉深模或后续拉深模)。
圆筒拉深件目录1 引言···································1.1冲压模具发展历史和国外冲压模具发展状况···············1.2 冲压模具行业发展现状及技术趋势···················1.3 我国模具水平与国际先进水平的差距··················2 工艺分析····························2.1材料····························2.2生产批量··························2.3 形状与尺寸·························2.4 精度·························3 工艺尺寸的计算····························3.1 确定切边余量····························3.2 计算毛胚直径····························3.3 拉升系数···························3.4 拉深工序的直径···························3.5 拉深工序的高度··························3.6 拉深模间隙··························4生产方案··························5排样方案和计算材料利用率··························6计算落料和每次拉深的刃口尺寸··························7凸凹模圆角半径的确定··························8冲压力的计算·························4.1 落料力·························4.2 卸料力·························4.3 压边力·························4.4 拉深力·························9冲压设备的选择·························10拉深的工件序图························5.1 首次拉深························5.2 第二次拉深························11 零件图························6.1 凹模和凸模························6.2 总装配图························1.引言1.1冲压模具发展历史和国外冲压模具发展状况我国考古发现,早在2000多年前,我国已有冲压模具被用于制造铜器,证明了中国古代冲压成型和冲压模具方面的成就就在世界领先。