活塞加工工艺说明书剖析
第6章 活塞的加工工艺分析及夹具设计

活塞的机械加工工艺过程
6.4.2 环槽的加工
• 在技术条件中对环槽侧面的垂直度、圆跳动 ,粗糙度和槽宽的尺寸精度都有较高的要求 ,环槽加工是活塞加工中重要工序之一。 • 精切环槽的加工示意图如图6.7所示。环槽 的宽度决定于切槽刀宽度;槽间的距离决定 于夹板厚度。 • 切槽刀的形状如图6.8所示,为了保证槽宽 的尺寸精度,必须将切槽刀的宽度偏差严格 控制在0.005mm以内。为了保证槽间距离, 切槽刀和夹板两侧面都在平面磨床上磨到粗 糙度Ra≤0.63μm,使两侧面互相平行,且 夹板的厚度偏差限制在0.01mm以内。
6.4.5 活塞的检验
• 为了保证活塞达到规定的技术条件,必须在加工中及加工完 毕后进行技术检查。最后检查的项目有:
(1)检查外观和表面粗糙度; (2)检查活塞销孔的尺寸及形状偏差; (3)检查裙部的椭圆度和锥度,按裙部椭圆的长轴分组; (4)检查环槽宽度、底径、环槽侧面的垂直度和圆跳动; (5)检查销孔轴心线对裙部轴心线的垂直度和对称度,销孔轴心线到顶面 的距离; (6)称活塞的重量,并按重量分组。
典型零件工艺设计
第6章 活塞的加工工艺分析及夹具设计
【本章学习目标】
了解活塞的结构特点、材料及技术要求; 掌握活塞加工的工艺特点,活塞加工工艺规程制订; 理解活塞加工的夹具设计特点。
6.1 活塞的工作条件及结构特点
6.1.1 活塞主要结构 • 图6.1表示一个铝活塞。基本结构是由活塞的顶面、环槽、油环 槽的小孔、活塞头部、活塞裙部、锁环槽、活塞销孔及止口组成
• 但是,总的说来,铝合金的优点超过缺点,所以在高速内燃机中都用它。铝 合金毛坯采用金属模浇铸。毛坯的精度较高,活塞销孔也能铸造出,因此机 械加工余量可以相应地减少。铝合金毛坯在机械加工前要切去浇冒口,并进 行时效处理,消除铸造时因冷却不均匀而产生的内应力。时效处理是将活塞 加热至180~200℃,保温6~8小时后,自然冷却。活塞经过时效处理后还能 增加强度和硬度。
活塞结构设计及工艺设计毕业计说明书
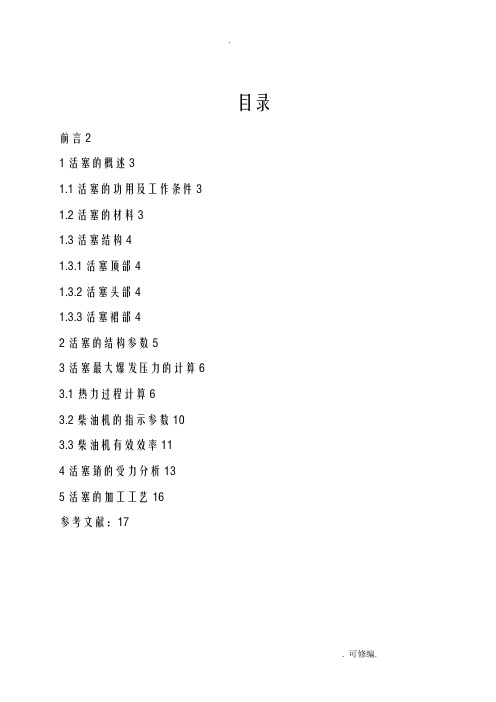
目录前言21活塞的概述31.1活塞的功用及工作条件31.2活塞的材料31.3活塞结构41.3.1活塞顶部41.3.2活塞头部41.3.3活塞裙部42活塞的结构参数53活塞最大爆发压力的计算63.1热力过程计算63.2柴油机的指示参数103.3柴油机有效效率114活塞销的受力分析135活塞的加工工艺16参考文献:17前言燃机的不断发展,是建立在主要零部件性能和寿命不断改进和提高的基础上的,尤其是随着发动机强化程度的提高、功率的增大和转速的增加,零部件尤其是直喷式柴油机活塞的工作环境变得更加恶劣了。
活塞的结构直接影响活塞的温度分布和热应力分布,因此就有必要对活塞的结构和性能作出预测和评价。
活塞是燃机上最关键的运动件,它在高温高压下承受反复交变载荷,被称为燃机的心脏,特别是坦克、舰艇和军用车船用燃机活塞则要求更高,它已成为制约燃机发展的一个突出问题。
本次课程设计的题目是发动机铝活塞的结构及工艺设计,选择利用合适的机床加工发动机活塞,通过这次课程设计,要求熟练掌握并能在实际问题中进行创新和优化其加工工艺过程。
1活塞的概述1.1活塞的功用及工作条件全套图纸及更多设计请联系QQ:360702501活塞是曲柄连杆机构的重要零件煤气主要功用是承受燃烧气体压力和惯性力,并将燃烧气体压力通过活塞销传给连杆,推动曲轴旋转对外作功。
此外,活塞又是燃烧室的组成部分。
活塞是燃机中工作条件最严酷的零件。
作用于活塞上的气体压力和惯性力都是周期变化的,燃烧瞬时作用于活塞上的气体压力很高,如增压燃机的最高燃烧压力可达14—16MPa。
而且活塞还要承受在连杆倾斜位置时侧压力的周期性冲击作用,在气体压力、往复惯性力和侧压力的共同作用下,可能引起活塞变形,活塞销座开裂,活塞侧部磨损等。
由此可见,活塞应有足够的强度和刚度,而且质量要轻。
活塞顶部直接与高温燃气接触,活塞顶部的温度很高,各部的温差很大,柴油机活塞顶部常布置有凹坑状燃烧室,使顶部实际受热面积加大,热负荷更加严重。
毕业设计---活塞设计说明书

毕业设计---活塞设计说明书毕业设计说明书专业:数控技术班级:数控3102姓名:张伟学号:41310226指导老师:李娜陕西国防工业职业技术学院目录第一部分工艺设计说明书 (1)1.零件图工艺性分析 (1)1.1零件结构功用分析 (1)1.2零件技术条件分析 (1)1.3零件结构工艺性分析 (2)2.毛坯选择 (2)2.1毛坯类型 (2)2.2毛坯余量确定 (2)2.3毛坯-零件合图草图 (2)3.机加工工艺路线确定 (3)3.1加工方法分析确定 (6)3.2加工顺序的安排 (6)3.3定位基准选择 (6)3.4加工阶段的划分说明 (7)3.5主要机加工工序简图 (7)4.工序尺寸及其公差确定 (7)4.1基准重合时工序尺寸确定 (8)5.设备及其工艺装备确定 (8)6.切削用量及工时定额确定 (8)7.工艺设计总结 (9)第二部分第XX号工序夹具设计说明书 (10)1.工序尺寸精度分析 (10)2.定位方案确定 (10)3.定位元件确定 (10)4.定位误差分析计算 (10)5.夹紧方案及元件确定 (12)6.夹具总装草图 (12)第三部分第XX号工序刀具设计说明书 (12)1.工序尺寸精度分析 (13)2.刀具类型确定 (14)3.刀具设计参数确定 (14)4.刀具工作草图 (14)第四部分第XX号工序数控编程设计说明书 (15)1.工序数控加工工艺性分析 (16)2.走刀路线的确定 (17)3.刀具及切削用量的选择 (17)4.编程原点的确定及数值计算 (18)5.程序编写及程序说明 (18)第五部分毕业设计体会 (18)第六部分参考资料 (19)第一部分工艺设计说明书1.零件图工艺性分析1.1零件结构功用分析活塞的种类一般分为:柴油机活塞,汽油机活塞,通用型活塞.活塞的结构:一般活塞都是圆形体,根据不同的发动机的工作条件和要求,活塞本身的构造有各种各样,一般将活塞这个小东西分为:头部,群部和活塞销座三部分.活塞是汽车发动机的"心脏",承受交变的机械负荷和热负荷.是发动机中工作条件最恶劣的关键零件之一,活塞的功能是承受气体压力,并通过活塞销传给连杆驱使曲柄旋转,活塞顶部还是燃烧室的组成部分.1.2零件技术条件分析活塞在高温,高压,高速,润滑不良的条件是工作的必经,活塞本身与高温气体接触,瞬时温度可达2500K以上,因此,受热严重,而散热条件有很差,所以,工作温度会很高,所以其质检特备严格,活塞的质检主要是检查裙部直径,活塞环槽高度和活塞销座孔尺寸的测量.1.3零件结构工艺性分析活塞作为典型的汽车关键零部件,在切削加工方面具有很强的工艺特点,目前,国内活塞制造行业通常使用通用机床和结合活塞工艺特点的专用设备组成的机械加工生产线,因此,专用设备就成为活塞切削加工的关键设备,其功能和精度将直接影响最终产品的关键特性的质量指标.我国活塞的研究重点居多都是对大型的柴油机的活塞进行改进,对微型汽油机的研究较少,目前,国内外对活塞的设计和改进都是围绕活塞的工作过程中承受的惹负荷和强度负荷,即要求活塞有高的热承受和机械负荷的能力.2.毛坯选择2.1毛坯类型毛抷外形为145(mm)x65(mm)的圆柱棒料,表面光滑易于装夹.2.2毛坯余量确定工件最终要求长度基本尺寸为100(mm),上偏差为+0.15,下偏差为-0.08.直径要求基本尺寸为60(mm),上偏差要求为0,下偏差为:-0.15.2.3毛坯-零件合图草图毛培图见图1-2--1;零件合图见图1-2--2;毛培图1-2--1零件合图1-2--23.机加工工艺路线确定3.1加工方法分析确定(1)外圆表面加工方法分析:在数控加工中,采用数控车床进行加工,选用百分表进行找正,用90度外圆车刀分粗车--半精车--精车三次加工至要求尺寸,最后选用切断刀直接保证要求尺寸进行切断.(2)内腔加工方法分析:选用立式加工中心进行加工,采用三爪卡盘装夹,用百分表找正,同时选用多把要求的刀具放入刀库,可以减小换刀的时间.(3)外圆孔与槽的加工方法分析:利用立式四轴加工中心就可以完成,采用一夹一顶进行钻孔,三爪装夹铣削外圆槽.所有刀具一次对刀放进刀库,减小换刀时间.3.2加工顺序的安排(1)外圆表面加工: 运用90度车刀一次装夹的情况下进行粗车--半精车--精车三次循环加工至要求尺寸,最后采用切断刀在保证长度尺寸的条件下直接切断.(2)内腔加工: 在三爪直接装夹下用百分表找正后,首先采用中心钻打中心孔,再进行钻孔,最后用扩孔刀加工至要求尺寸.再利用球头铣刀进行内倒角.(3)外圆孔与槽的加工: 运用四轴三爪定位,百分表进行找正后,首先进行钻孔循环,再进行键槽铣削.3.3定位基准选择定位基准:即在加工中工件上与夹具定位元件直接接触的点,线或面.所以在车削外圆表面时的定位基准为毛抷外表面,内腔加工的定位基准为活塞的外圆表面,而在加工槽和表面孔是的定位基准为活塞外圆表面和内腔表面.3.4加工阶段的划分说明活塞总加工分为:首先进行活塞外圆表面加工其次是对内腔的加工,最后为表面孔及槽的加工.活塞外圆表面分为:先粗后半精最后为精加工三个阶段,内腔的加工分为:先钻孔后进行扩孔最后进行倒内角,而对于外圆表明面的轮廓,其中钻孔与铣键槽都可分为先后加工,但必须保证其尺寸要求.3.5主要机加工工序简图工序图一1-3--5 工序图四1-3--6 4.工序尺寸及其公差确定4.1基准重合时工序尺寸确定下图为活塞毛抷与最终加工余量的关系如:表1-4--1.外圆加工工艺路线粗车--半精车--精车工序名称余量/mm 精度工序尺寸粗车 0.05 IT7(-0.15) Φ60 半精车0.1 IT10(0.012) Φ60.5 精车4.85 IT12(0.30) Φ60.15 --+/-1.0Φ655.设备及其工艺装备确定下表为活塞在全部加工过程中各工序所用设备及其工装:机床,刀具,夹具,量具的选择.表1-5--1工序号加工内容刀具夹具量具机床01通过找正,保证工件的夹持量大小,X.Y向工件原点设置工件轴心,Z向设置于顶面0~10百分表02 活塞外圆表面的加工:分为粗车--半精车--精车--切断四段加工90度车刀切断刀三爪卡盘游标卡尺卧式车床03 活塞内腔的加工:分为钻孔--扩孔--倒角三段加工Φ6中心钻Φ30钻头Φ10球头铣刀三爪卡盘游标卡尺立式加工中心04 活塞外圆表面孔与槽的加工:分为槽(粗--半精--精铣三段)和孔(钻--铰孔两段)的加工Φ6中心钻Φ9.8钻头Φ6铣刀Φ10铰刀一夹一顶(三爪卡盘与顶尖)游标卡尺立式四轴加工中心6.切削用量及工时定额确定(背吃刀量=工序余量/2)根据<工艺设计手册>选取切削用量,时间定额由辅助时间和基本时间计算而来.具体切削用量见下表.表1-6--1活塞加工切削用量工序号工步号加工内容刀号刀具量规格/mm主轴转速/(r/min)进给速度/(mm/min)切削深度(mm)1 找正0-10 百分表2 1粗车外圆T0190度车刀500 0.17 2.4 2精车外圆T0290度车刀600 0.17 0.13 1打中心孔T1Φ6中心钻1000 80 5 2 钻孔T2Φ16中心钻800 80 403 扩孔T3 扩孔刀1000 804 粗倒角T4Φ1球头铣刀01200 1005 精倒角T4Φ10球头铣刀1500 100 0.14 1 找正0-10百分表2粗铣键槽T5Φ6平底铣刀1500 100 4.9 3精铣键槽T5Φ6平底铣刀1500 100 0.1 1打中心孔T6Φ6中心钻1000 80 52 钻孔T7 800 80 203 铰孔T8 1200 80 0.2 5 1 去毛刺锉刀6 1 检查入库7.工艺设计总结一个月的时间匆匆而过,感觉接到毕业设计题目就仿如昨天,在这一个月里我全身心的投入在了活塞的设计中,有过急躁,有过兴奋,有过感动......刚接到题目,一脸的疑惑与不相信,我甚至对它想象过很多很多,但我当看到时我真的迷惑了,真的觉得乱无头绪,我根本不知道从何下手,结果只是一头扎进了图书馆,盲目的找相同的例题,结果过失望了,又是去网吧网上查阅找寻,找了老师简单的问了下,就自信满满的手写了一份自认为是完美之作的设计上交了,结果当听取了老师的讲解后彻底明白自己所写的和设计有多大的差距,经过老师的讲解,我又一次分析了毕业设计的题目,再看了要求的格式,我甚至对自己有点羞愧,对大学的最后一课作业就那么马虎去对待,所以我和同组同学认真分析,相互探讨自己的理解,做了笔记,接着再一次走进了图书馆与网吧,认真去查阅,有时还问问老师,听取老师对我们的理解是否能够肯定,这样才慢慢进入了设计作业这个角色,慢慢开始了我的作业,活塞,一个感觉生活熟悉的词,当真正去设计时感觉真的是无从下手,但是我还是没有因此退宿,从开始的盲目到现在我发现我想去挑战,因为我不服输,我觉得自己行,在学习中我想让自己永远做强者.我首先通过了解活塞的应用:它是汽车发动机的"心脏"承受交变的机械负荷和热负荷,是发动机中工作最恶劣的部件之一,所以对于选材必须要讲求抗压能力强,因为存在要求气压能力强,所以我在设计它的精度时必须要好,它在气缸的活动速度可以达到(8-12m/s)往复运动,且速度还在不断变化,所以就上述要求都必须方方面面的考虑,所以毕业设计不仅是对三年所学知识的总结,更重要的是对考虑的细节全面的考察,所以要不断的去了解查阅,这又是对自己解决问题的能力的考察,一份看似简单的作业,它真实的练习了学校与生活真实的连接,所以我花了自己十二份的努力,我也真实的感觉到自己学到的是自己在课堂之中怎么也学习不到的东西.在此,我衷心的感谢为我们设计作业辛勤付出的老师和同学们,正因为你们的指导,你们的努力,才使我对毕业设计渐渐从最开始的反感到现在的喜欢,这一切都离不开你们的教导,在毕业之际你们尽可能的把一切恨不得献出来给我们,老师谢谢你们,我们会用行动告诉你们我们是最好的.第二部分第04号工序夹具设计说明书1.工序尺寸精度分析计算工序尺寸是工艺规程指定的主要工作之一,存在以下几种情况:(1)工艺基准与设计基准重合时的情况,对于加工过程中基准面没有交换的情况,工序尺寸的确定比较简单,在决定了各工序余量和工序所能达到的经济精度之后,就可以有最后一道工序推算.(2)工艺基准与设计基准不重合时的情况,在复杂零件的加工过程中,常常出现定位基准和设计基准,测量基准不重合或加工过程中需要多次转换,工序尺寸的计算就复杂的多了.综上两种情况说明,活塞在进行环槽与孔的加工属于第一种情况,三爪与顶尖共同定位,其基准都为外圆表面,固此重合.2.定位方案确定根据加工选用加工中心四轴加工,所以必然选择三爪装夹,但是为了工件的表面粗糙度质量,所以在装夹时在工件外圆用纸巾均匀缠绕再夹持工件,为了不使工件变形夹持量不要过大防止工件变形,钻孔时为了稳定,选用顶尖固定工件的另一边,但是在加工环形槽时禁止使用顶尖,防止工件扭伤.3.定位元件确定根据元件的外形与加工工序,选择加工中心四轴上三爪定位,附加圆头顶尖共同定位工件,保证限制了工件五个自由度加工.4.定位误差分析计算用调整法加工一批零件时,工件在定位工程中,由于工件的工序基准与定位基准不重合,以及工件的定位基准面与家具定位元件的定位表面存在制造误差,都会引起工件的工序基准偏离理想位置,而使产生定位误差,用符号表示为: 它由定位基准与工序基准不重合误差和定位副制造不准确引起工序基准的位移误差两部分所组成其大小是两项误差在工序尺寸方向上的代数和,即:当工序基准位置与多个定位基准有关时,以上两个误差方向和工序尺寸方向便可能不一致,根据加工误差不等式,定位误差不超过两件误差的1/5~1/3.5.夹紧方案及元件确定采用一夹一顶的方式装夹加工.6.夹具总装草图夹具总装见下图夹具总装草图2-6--1 第三部分第04号工序刀具设计说明书1.工序尺寸精度分析计算工序尺寸是工艺规程指定的主要工作之一,存在以下几种情况:(1)工艺基准与设计基准重合时的情况,对于加工过程中基准面没有交换的情况,工序尺寸的确定比较简单,在决定了各工序余量和工序所能达到的经济精度之后,就可以有最后一道工序推算.(2)工艺基准与设计基准不重合时的情况,在复杂零件的加工过程中,常常出现定位基准和设计基准,测量基准不重合或加工过程中需要多次转换,工序尺寸的计算就复杂的多了.综上两种情况说明,刀具在加工中直接影响着基准重合和基准不重合时的精度,在加工过程中尽可能的采用刀具磨耗,边加工边测量利用磨耗做修改,直到达到最终的尺寸要求范围中为合格.2.刀具类型确定机用铰刀,切断刀.3.刀具设计参数确定选择机用铰刀作为参数分析确定,具体见表3-3--1.表3-3--1 机用铰刀设计参数导锥角Φ Φ=45度刃倾角一般情况下为0度,加工韧性较大材料时为15~20度. 前脚一般情况下为0度,粗铰韧性较大材料时为5~10度.螺旋角一般情况下为0度(直齿),加工深孔或断续表面时,可用螺旋齿铰刀,加工盲孔取右旋;加工通孔取左旋;加工灰铸铁,淬硬钢为7~8度;加工可锻铸铁,钢时为12~20度;加工铝和轻金属时为35~45度.主偏角加工铸铁等脆性材料时,K=3~5度;加工钢等塑性材料时,K=12~15度;加工盲孔时K 取45度. 后角与刃带直径d/mm1~3 >3~10 >10~18 >18~30 >30~50 >50~80 后角(度)14~1810~14 8~12 6~10 6~10 6~10 刃带0.05~0.10.1~0.150.15~0.25 0.2~0.30.25~0.40.3~0.5倒锥量直径<2.8 >2.8~6 >6~18 >18~32>32~50>50~80 倒锥量0.005~0.020.02~0.040.03~0.050.04~0.06 0.05~0.070.06~0.08第五部分第03号工序数控编程设计说明书1.工序数控加工工艺性分析活塞的工作要求了它必须要有特别好的精度,因为存在密封,所以必须要有最好的压力,故此将内腔放在了外圆的加工之后,因为在钻孔与扩孔及倒角时,外面的表面都保证了特别好的精度,对于内腔,倒角可以很好地防止了曲柄在内腔的连接处产生过多的摩擦,这样因为活塞本身的运动就决定了它的运动剧烈,所以在内部加工完成后,必须进行很好的热处理,更重要的是材料的选择.加工环节的每一步都要严格按照粗--半精--精加工的顺序完成,因为他可以保证材料的质量,不使材料产生硬化或者过切现象,特别是在保证加工表面精度方面有很好的效果.2.走刀路线的确定走刀路线及顺序的安排:1). 先进行中心钻打中心孔,为钻孔做准备.2). 进行钻孔循环,利用扩孔刀对所钻孔进行扩孔循环,在结束时必须要产生让刀,否则将会在抬刀时产生抬刀痕,影响表面加工的粗糙度.3). 最后进行球头刀倒角,球头刀必须从中心下刀慢慢向外加工去除余量,利用不同的转速及进给分粗--半精--精加工三个阶段加工.3.刀具及切削用量的选择活塞内腔加工刀具及切削用量零件图号001零件名称活塞材料牌号45刚毛抷种类模锻件毛抷件数 1工序号工步号工步内容刀号长度补偿号半径补偿号刀具量规格/mm主轴转速/(r/min)进给速度/(mm/min)03 1 为活塞内孔钻孔打中心孔T02 H02Φ6中心钻1000 802 钻活塞内孔T03 H03 600 803 为上道工序的钻孔扩孔至设计要求的尺寸T04 D04 1000 1004 粗铣活塞内孔的R10的内角保留0.1的余量T05 D05 1000 805 半精铣活塞内孔R10的内角保留设计尺寸的0.05余量T05 D05 1500 1006 精铣活塞内孔R10的内角至设计要求的尺寸范围T05 D05 2000 1204.编程原点的确定及数值计算1) 程序原点的确定:原点设置于工件的轴心,Z轴中心定在工件底,将此作为程序的编程原点.2) 在钻孔加工中,工件的长度为100mm,所以安全高度定于Z轴105mm处,钻孔深度为40mm处,粗加工全部保留0.10mm余量,半精加工保留0.05mm余量,精加工至要求的尺寸范围内.5.程序编写及程序说明程序程序注释O2601 程序名N10 G00G17G40G80G90G54Z300; 设置程序起始状态N15 M03S800; 主轴转速800(r/min)的速度N20 G98G81X0.Y0.Z105.R10.F80; 进行钻孔循环开始N25 G00Z50.; 抬刀N30 G00G80; 钻孔循环取消N35 M05; 主轴停止N40 M30; 程序结束钻孔程序程序注释O2602 程序名N10 G00G17G40G80G90G54Z300; 设置程序起始状态N15 M03S800; 主轴转速800(r/min)的速度N20 M03S800; 主轴转速800(r/min)的速度N25 MO8 切削液开启N30 G98G81X0.Y0.Z105.R10.F80; 进行钻孔循环开始N35 G00Z50.; 抬刀N40 G00G80; 钻孔循环取消N45 M05; 主轴停止N50 M09 切削液关闭N55 M30 程序结束倒内角程序程序注释O2603 程序名N10 G00G17G40G80G90G54Z300; 设置程序起始状态N15 M03S1000; 主轴转速1000(r/min)的速度N20 M08 切削液开启N25 G43 H0 Z100. 进行长度补偿N30 Z50. 下刀N35 G1 Z40. F1000 开始加工N40 X-8.528 Z40.02 F2000N45 X-8.989 Z40.084N50 X-9.453 Z40.193N55 X-9.915 Z40.35N60 X-10.367 Z40.555N65 X-10.802 Z40.808........N255 M05 主轴停止N260 M09 切削液关闭N265 M30 程序结束第六部分毕业设计体会毕业设计作为我走出大学校门的最后一个作业,考察着我对大学三年所学专业课程和实际操作的能力.当我从开始的第一字到此时的完成我都存在一份认真仔细的心去完成,因为我也想去考验自己,问自己---你学到了吗?接到毕业设计题目的时候,真是茫无头绪,全传动机构就一个尺寸和一个大体图样,我真有着说不出的乱,一天两三天都没有动,开始也就是乱看,但经过仔细的分析,经过对老师分解的任务在图书馆的查询,开始对自己的任务活塞有了进一步的了解,为有更深层次的了解,我去了户县的机械专卖场请老师傅给我看了真实的各种活塞,回来和同学共同讨论,对题目做了分析,在对同组同学的意见进行了分析,我逐渐进入了角色,开始了这份毕业设计的制作.首先通过这份作业我要说老师真的是给了我们一份实实在在的考验,也使我真正认识到我所学习的知识太过于散乱.通过这份作业我也将这三年所学的专业知识有了一个真正的归纳总结,不再是零散的,同时也将我们所学与真正的实体联系起来了,真有着说不出的收获.由于设计的需要,我仔细研究了零件图,但因为自己经验不足,遇到了很多实际问题,使我体会到了在现场实习.仅证明可不可以实干,而不能代表能不能干好,所以我积极地与同学沟通,相互交流,同时受到各位老师的指导,这一切问题显得那么迎刃而解.其次就是考察了我们对综合复杂的问题能去动手查阅的能力,去分析分解一个复杂的问题,从不同的角度去完成,这也是我最为喜悦的,通过毕业设计我真正认识到理论和实践相结合的重要性,并培养了我综合运用所学理论知识和所学实际操作知识去理性的分析和解决实际工作中的一般技术工程问题的能力,使我建立了正确的设计思想,掌握了工艺设计的一般程序,规范和方法.并进一步巩固,深化的吸收和运用了所学的基本理论知识和基本操作技能.还有,他提高了我设计计算,绘图,编写技术文件和程序的能力.更培养了我勇于创新的精神和严谨的学风及工作的作风.最后真的感谢老师,老师在这一份作业中所对我们投入的心思.离校之际, 感谢您们这三年来对我们的点滴教育,衷心的对您说声:"您们辛苦了!我们会用行动与成果告诉您,我们成材了".第七部分参考资料[1] 陆剑中,孙家宁. 数控加工工艺编程.北京:北京理工大学出版社,2005[2] 崔永茂. 金属切削原理与刀具. 北京:北京机械工业出版社,1991[3] 卢并恒. 机械制造技术.西安:西安交通大学出版社,1992[4] 吴玉华. 机床夹具设计大连: 大连理工大学出版社2005[5] 孙自立. 数控铣床加工中心重庆:重庆大学出版社2008[6] 周昌治,杨忠键,赵志远. 数控机床加工培训教程北京:北京理工大学出版社,2005[7] 吴国华. 数控加工工艺. 重庆:重庆大学出版社2008[8] 惠明达. 机床夹具制造北京:北京理工大学出版社,2005[9] 朱正鑫. 公差与配合技术北京:北京理工大学出版社,2005[10] 于俊毅. 机床原理与设计. 重庆:重庆大学出版社2008[11] 刘永寿. 机械制造与自动化技术大连: 大连理工大学出版社2005[12] 周长志. 机械加工工艺手册北京:北京理工大学出版社,2005[13] 文月娟. 机械制造工艺学北京:北京理工大学出版社,2005[14] 王先奎. 实用工具手册. 北京:北京理工大学出版社,2005[15] 吴玉华. 机床夹具设计大连: 大连理工大学出版社 2009[16] 杨忠键,赵志远. 数控机床加工培训教程北京:北京理工大学出版社,2005。
活塞杆加工工艺说明书

活塞杆加工工艺说明书
活塞杆是内燃机中的重要零部件之一,它承受着往复运动时的巨大冲击力和复杂的摩擦力,因此加工工艺的好坏直接影响着活塞杆的使用寿命和性能。
下面将为您介绍活塞杆加工的工艺说明书。
一、材料选择
活塞杆的材料要求比较高,一般选用高品质的合金钢或不锈钢材料,这些材料具有高强度、高耐磨性、高耐腐蚀性和良好的韧性等优点。
二、车削加工
活塞杆的车削加工是其主要的加工工艺之一,其目的是为了保证活塞杆的精度和平滑度。
首先需要在车床上进行粗车,根据活塞杆的尺寸和要求进行车削,要求车削顺序、深度、切削速度和切削深度等参数合理,确保加工精度和表面质量。
三、磨削加工
在车削加工的基础上,还需要进行磨削加工,以提高加工精度和表面平滑度。
磨削工艺一般采用球墨铸铁磨轮,磨削前需进行准备工作,如清洗、校准、结构调整等,以确保磨削的精度和效果。
四、热处理
活塞杆在加工完成后还需要进行热处理,目的是为了消除内部应
力和提高杆的硬度、耐磨性和耐腐蚀性。
热处理方法一般采用淬火加
温处理,加热温度、保温时间、淬火介质和淬火温度等参数需要精确
控制,以确保处理后的活塞杆性能稳定。
五、检验质量
加工完成后的活塞杆需要进行质量检验,检验项目包括尺寸精度、表面平滑度、硬度和耐磨性等指标,以确保产品质量符合标准和要求。
一般采用量具、显微镜、硬度计和摩擦试验机等检测设备进行检验。
在活塞杆加工中,要注意机器设备的维护保养和操作规范,选材、加工和处理要严格按照要求执行,以确保生产出具有优良性能和寿命
长久的活塞杆。
活塞加工工艺及金属膜设计说明书含CAD图活塞加工工艺卡片

摘要汽车发动机的活塞是发动机中的要紧配件之一,它与活塞环、活塞销等零件组成活塞组,与气缸盖等一起组成燃烧室,经受燃气作使劲并通度日塞销和连杆把动力传给曲轴,以完成内燃发动机的工作进程。
油气燃烧所产生的热由活塞的顶部所吸收,并传至气缸壁,而燃烧后气体膨胀所产生的力量也必需经由活塞来吸收,活塞会把燃烧气体压力及惯性力经由连杆传到曲轴上,利用连杆的作用将活塞的线性往复运动转换曲轴的旋转运动。
活塞的功用是经受气体压力,井通度日塞销传给连杆差遣曲轴旋转,活塞项部仍是燃烧室的组成部份。
活塞在高温、高压、高速、润滑不良的条件下1二作。
活塞在气缸内以很高的速度往复运动,且速度在不断地转变,这就产生了专门大的惯性力,使活塞受到专门大的附加载荷。
活塞在这种恶劣的条件’卜工作,会产生变形并加速磨损,还会产生附加载荷和热应力,同时受到燃气的化学侵蚀作用。
现代的活塞设计要紧有铸造和锻造两种,而铸造又比锻造简单廉价,但却不及锻造活塞能经受较大的热度和压力。
由于活塞与活塞环都必需在高温、高压、高速及临界润滑的状态’卜工作,因此长期以来,发动机设计者都为提供一个最正确的设计而不断尽力,进而能够从活塞方而来提高引擎的性能。
关键词:活塞气缸盖燃烧室曲轴惯性力附加载荷AbstractThe piston of car motor is one of the main accessorieses in the motor ,it and the piston wreath ,piston sell etc .the spare parts constitute a piston set and cover with air cylinder etc. Constitute combustion room together , bear gas function the dint also sell through a piston and connect the pole motive song stalk to complete inside the work process of ran oil annoys the combustion produce of hot from the coping of piston absorb , and spread to air cylinder wall , and combustion empress thestrengh produced by air inflation have to also absorb through the piston , the piston will chase combustion air pressure and inertial dint through connect the spread to song stalk up , make use of connect the function of pole exercise the line back and forth of piston to convert revolving of song stalk sport.The effect of piston bears air pressure , and sell to pass to connect a pole to order about song stalk to revolve through a piston , constituting of the piston a coping still a combustion room part .piston under the condition that heat ,high pressure , high speed , lubricate bad work . The piston is exercised with very high speed back and forth in the air cylinder , and speed at constantly variety , this produced very greatly inertial inertial dint and made the piston been subjected to very big of the affixture carry a lotus . The piston is under this bad condition work , will produce to transform and accelerate towear away , also produce affixture to carry lotus and heat in response to the dint , be subjected to chemistry of the gas corrosion function in the meantime . Modern of the piston design to mainly have the foundry forging 2 kinds , but cast again than forging simple cheapness , but cannot compare with forging piston can bear bigger heat and pressure . Piston and piston wreaths have to work under the appearance of the heat , high pressure and high speed and the critical lubrication , therefore for long time , the motor designs all continuously make great effort for providing a design , then can raise the function of from the piston .Keywords:Piston The air cylinder covers Burnable room Song stalk Inertial dint Additional carry a lotus目录摘要 (1)Abstract (2)目录 (3)需要全套设计(含CAD图,活塞加工工艺卡片,开题报告) (5)承接各类设计群7 (5)1 绪论 (5)本课题的研究意义 (5)本课题的大体内容 (5)本课题采纳的研究手腕和可行性分析 (6)2 活塞结构特点 (7)活塞的工作环境及经受的作使劲 (7)活塞的结构特点 (7)5 活塞组的设计 (10)活塞组的设计要求 (10)活塞的材料 (10)活塞各部份尺寸 (11)5.3.1活塞高度H (11)5.3.2活塞头部的设计 (11)5.3.3活塞顶和环断面 (13)5.3.4活塞裙部的设计 (16)活塞总尺寸 (19)6 活塞加工 (20)7 活塞铸造方式的选取及优缺点 (21)铸造方式的比较 (21)铝合金的铸造方式的选取及优缺点 (22)8 金属型的设计 (24)冒口的设计 (24)8.1.1冒口的作用 (24)8.1.2设计冒口的原那么 (24)8.1.3冒口的补缩原理 (24)8.1.4冒口的形式与种类 (25)8.1.5冒口尺寸的确信 (26)浇注系统的设计 (26)金属型的设计 (28)8.3.1金属型的要紧结构形式及应用 (28)8.3.2金属型的结构设计 (29)8.3.3金属型的排气系统设计 (31)8.3.4金属型的导向与定位 (31)8.3.5金属型的锁紧机构 (32)8.3.6金属型材料的选择 (32)8.3.7金属型的冷却 (32)金属型芯的设计 (33)9 总结 (34)设计体会 (34)前景展望 (34)参考文献 (36)附录:英文技术资料及其翻译 (37)需要全套设计(含CAD图,活塞加工工艺卡片,开题报告)承接各类设计群71 绪论本课题的研究意义活塞是发动机中的重要零件之一。
活塞杆的机械加工工艺规程

1.活塞杆的工艺性分析1.1零件图样的分析mm×770mm自身圆度公差为0.005mm。
(1)φ500-025.0mm中心线的同轴度公差为φ0.05mm。
(2)左端M39×2-6g螺纹与活塞杆φ500.0025-mm中心线的同轴度公差为φ0.02mm。
(3)1:20圆锥面轴心线与活塞杆φ500-.0025(4)1:20圆锥面自身圆跳动公差为0.005mm。
(5)1:20圆锥面涂色检查,接触面积不小于80%。
mm×770mm表面渗氮,渗氮层深度0.2~0.3mm,表面硬度62~65HRC。
(6)φ500-025.0材料38CrMoALA是常用的渗氮处理用钢。
1.2零件的工艺分析(1)活塞杆在正常使用中,承受交变载荷作用,φ500mm×770mm处有密封装置往-025.0复摩擦其表面,所以该处要求硬度高又耐磨。
mm×770mm部分经过调质处理和表面渗氮后,芯活塞杆采用38CrMoALA材料,φ500-.0025部硬度为28~32HRC,表面渗氮层深度0.2~0.3mm,表面硬度为62~65HRC。
这样使活塞杆既有一定的韧性,又具有较好的耐磨性。
(2)活塞杆结构比较简单,但长径比很大,属于细长轴类零件,刚性较差,为了保证加工精度,在车削时要粗车、精车分开,而且粗、精车一律使用跟刀架,以减少加工时工件的变形,在加工两端螺纹时要使用中心架。
(3)在选择定位基准时,为了保证零件同轴度公差及各部分的相互位置精度,所有的加工工序均采用两中心孔定位,符合基准统一原则。
(4)磨削外圆表面时,工件易产生让刀、弹性变形,影响活塞杆的精度。
因此,在加工时应修研中心孔,并保证中心孔的清洁,中心孔与顶尖间松紧程度要适宜,并保证良好的润滑。
砂轮一般选择:磨料白刚玉 (WA),粒度60#,硬度中软或中、陶瓷结合剂,另外砂轮宽度应选窄些,以减小径向磨削力,加工时注意磨削用量的选择,尤其磨削深度要小。
活塞杆加工工艺规程设计说明书
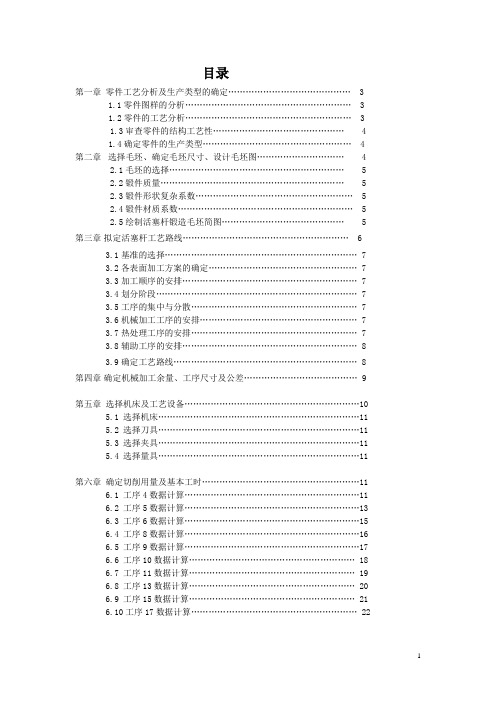
目录第一章零件工艺分析及生产类型的确定 (3)1.1零件图样的分析 (3)1.2零件的工艺分析 (3)1.3审查零件的结构工艺性 (4)1.4确定零件的生产类型 (4)第二章选择毛坯、确定毛坯尺寸、设计毛坯图 (4)2.1毛坯的选择 (5)2.2锻件质量 (5)2.3锻件形状复杂系数 (5)2.4锻件材质系数 (5)2.5绘制活塞杆锻造毛坯简图 (5)第三章拟定活塞杆工艺路线 (6)3.1基准的选择 (7)3.2各表面加工方案的确定 (7)3.3加工顺序的安排 (7)3.4划分阶段 (7)3.5工序的集中与分散 (7)3.6机械加工工序的安排 (7)3.7热处理工序的安排 (7)3.8辅助工序的安排 (8)3.9确定工艺路线 (8)第四章确定机械加工余量、工序尺寸及公差 (9)第五章选择机床及工艺设备 (10)5.1 选择机床 (11)5.2 选择刀具 (11)5.3 选择夹具 (11)5.4 选择量具 (11)第六章确定切削用量及基本工时 (11)6.1 工序4数据计算 (11)6.2 工序5数据计算 (13)6.3 工序6数据计算 (15)6.4 工序8数据计算 (16)6.5 工序9数据计算 (17)6.6 工序10数据计算 (18)6.7 工序11数据计算 (19)6.8 工序13数据计算 (20)6.9 工序15数据计算 (21)6.10工序17数据计算 (22)第一章零件工艺分析及生产类型的确定1.1零件图样的分析mm×770mm自身圆度公差为0.005mm。
(1)φ500-.0025mm中心线的同轴度公差为φ0.05mm。
(2)左端M39×2-6g螺纹与活塞杆φ500-.0025(3)1:20圆锥面轴心线与活塞杆φ500mm中心线的同轴度公差为φ0.02mm。
-.0025(4)1:20圆锥面自身圆跳动公差为0.005mm。
(5)1:20圆锥面涂色检查,接触面积不小于80%。
汽车发动机活塞加工工艺及夹具设计讲解
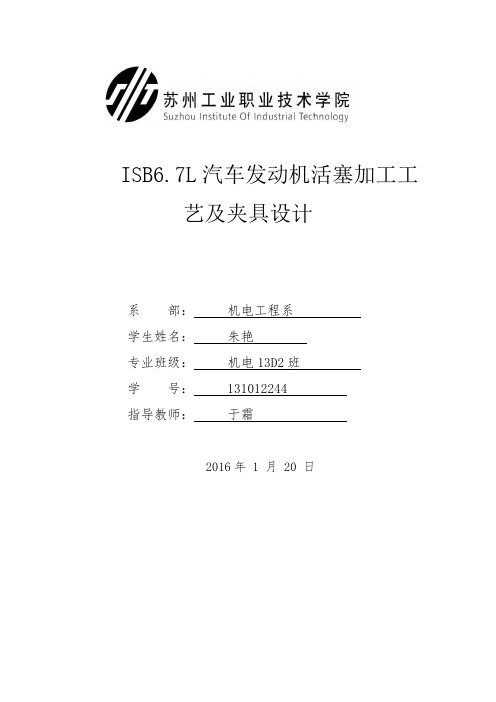
ISB6.7L汽车发动机活塞加工工艺及夹具设计系部:机电工程系学生姓名:朱艳专业班级:机电13D2班学号: 131012244指导教师:于霜2016年 1 月 20 日声明本人所呈交的ISB6.7L汽车发动机活塞加工工艺及夹具设计,是我在指导教师、公司领导、同事的指导下独立进行分析研究所取得的成果。
本论文不包含其他个人已经发表或撰写过的研究成果。
对本文的研究做出重要贡献的个人和集体,均已在文中作了明确说明并表示谢意。
作者签名:日期:【摘要】现在敏捷制造、快速原型制造、快速模具工装制造技术已经成为内燃机零件工业特别是活塞行业竞争的焦点。
因此,针对各种内燃机活塞机械加工工艺过程的广泛探索,从而缩短或简化工艺流程、提高产品质量、降低生产制造成本也变得越来越重要。
本毕业设计论文通对分析活塞加工技术的发展、活塞的结构特点、活塞各个工作面的加工特征及其工作环境,确定了ISB6.7L活塞的加工方案及加工过程。
并对精镗销孔夹具定位与夹紧进行了设计,分析其工作原理,以及在夹具设计过程中应该注意的问题。
并分析论证其可行性。
关键词:发动机活塞加工工艺夹具设计Title The Engine Piston Processing Technology and Fixture Design Of ISB6.7L AutomobileAbstractNow the agile manufacturing, rapid prototyping and rapid tooling die & mould manufacturing technology has become the focus of internal combustion engine parts industry, especially the piston industry competition.Therefore, in view of all kinds of internal combustion engine piston machining process widely, thus shortening or simplified technological process, improve product quality, reduce the production cost is also becoming more and more important.The graduation design paper through the analysis of the piston processing technology development, the structure characteristics of piston, piston each working face processing characteristics and its working environment, determine the processing scheme and processing process of ISB6.7L piston.And the fine boring and pin hole positioning and clamping jig design, analyzes its working principle, and the problems should be noticed in the process of fixturedesign.And analyzed its feasibility.Key words Engine piston processing fixture design目次1 绪论........................................................1.1选题的背景及意义.................................................................1.2本课题主要内容...................................................................2 ISB6.7L活塞结构及加工工艺分析...............................2.1 ISB6.7L活塞结构.................................................................2.2 铸造工艺.........................................................................2.3 活塞加工特征分析.................................................................3 ISB6.7L活塞机加工工艺.......................................3.1 毛坯选择.........................................................................3.2 定位基准的选择...................................................................3.3 活塞加工工艺制订.................................................................4 ISB6.7L活塞的表面处理.......................................4.1 活塞的清洗.......................................................................4.2 活塞的丝网印刷...................................................................4.3 活塞的固化.......................................................................4.4 活塞的铸铁圈防护.................................................................4.5 活塞的烘干.......................................................................5 精镗销孔夹具设计 ............................................5.1 活塞销孔夹具定位及误差分析.......................................................5.2 工件的夹紧装置的设计.............................................................5.3 标准间的选用.....................................................................5.4 夹具体的设计.....................................................................5.5 精镗销孔夹具工作原理............................................................. 结论........................................................ 致谢........................................................ 参考文献 ................................................... 附录A ............................................................................... 附录B ...............................................................................1 绪论制造业是国民经济的支柱产业,其发展程度体现了一个国家科学技术和生产力的发展水平。
活塞的机械加工工艺规程设计说明

目录1.零件的分析 (1)1.1零件的作用 (1)1.2.零件的工艺分析及其技术要求 (1)2.工艺规程设计 (3)2.1. 确定毛坯的制造形式及毛坯尺寸确定的 (3)2.2. 基面的选择 (4)2.3. 制定工艺路线 (5)2.4. 机械加工余量、工序尺寸 (6)2.5. 确定切削用量及基本工时 (8)总结 (13)参考文献 (14)1.零件的分析1.1零件的作用活塞是曲柄连杆机构中的重要零件之一,是发动机的心脏,它主要有三个作用。
第一是使发动机作功;第二是密封,它能使发动机活塞顶以上的空间保持密封,使发动机能连续工作;第三是传热,它能将发动机点燃爆发时的高温传给气缸,再由气缸壁外侧水套的循环水将热量带走。
1.2.零件的工艺分析及其技术要求图1-1零件图1.2.1.零件的工艺分析1)时效处理是为了消除铸件的应力,第二次时效处理是为了消除粗加工和铸件残余应力。
以保证加工质量。
2)活塞环槽的加工,分粗加工和精加工,这样可以减少切削力对环形槽尺寸的影响,以保证加工质量。
3)活塞环槽的加工,装夹方法可采用心轴,在批量时可提高生产效率,保证质量。
4)活塞环槽mm 02.008+尺寸检验,采用片塞规进行检查,片塞规分为通端和止端两种。
片塞规具有综合检测功能,即能检查尺寸精度,同时也可以检查环槽两面是否平行,如不平行,片塞规在环槽不能平滑移动。
5)活塞环侧面与mm 034.0080+Φ轴心线的垂直度检验,可采用心轴装夹工件,再将心轴装夹在两顶尖之间,这时转动心轴,用杠杆百分表测每一环槽的两个侧面,所测读数最大与最小差值,即为垂直度误差。
6)活塞外圆008.0134-Φmm 与034.0080+Φmm 轴心线的同轴度检验,可采用心轴装夹工件,再将心轴装夹在两顶尖之间,这时转动心轴,用百分表测出活塞外圆跳动的读数最大与最小差值,即为同轴度误差。
1.2.2.零件的技术要求(1)活塞环槽侧面与034.0080+Φmm 轴心线的垂直度公差为0.02mm ; (2)活塞外圆008.0134-Φmm 与034.0080+Φmm 轴心线的同轴度公差为0.04mm ; (3) 左右两端90Φmm 端面与034.0080+Φmm 轴心线的同轴度公差为0.02mm ;(4) 由于活塞环槽与活塞环配合精度要求较高,所以活塞环槽加工精度相对要求较高;(5) 活塞上环槽02.008+入口处的倒角为0451⨯;(6) 材料HT200,铸造后时效处理; (7)未注明倒角0451⨯。
活塞的数控加工工艺设计说明书
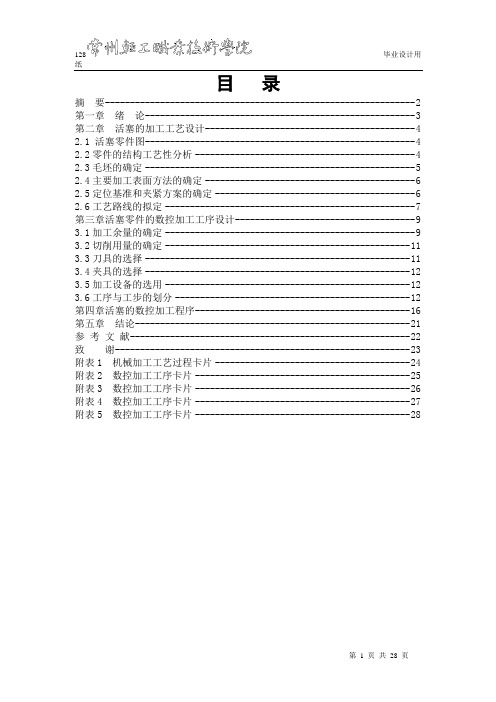
目录摘要-------------------------------------------------------------- 2 第一章绪论------------------------------------------------------ 3 第二章活塞的加工工艺设计------------------------------------------ 4 2.1 活塞零件图------------------------------------------------------ 4 2.2零件的结构工艺性分析-------------------------------------------- 4 2.3毛坯的确定------------------------------------------------------ 5 2.4主要加工表面方法的确定------------------------------------------ 6 2.5定位基准和夹紧方案的确定---------------------------------------- 6 2.6工艺路线的拟定-------------------------------------------------- 7 第三章活塞零件的数控加工工序设计------------------------------------ 9 3.1加工余量的确定-------------------------------------------------- 9 3.2切削用量的确定------------------------------------------------- 11 3.3刀具的选择----------------------------------------------------- 11 3.4夹具的选择----------------------------------------------------- 12 3.5加工设备的选用------------------------------------------------- 12 3.6工序与工步的划分----------------------------------------------- 12 第四章活塞的数控加工程序------------------------------------------- 16 第五章结论------------------------------------------------------- 21 参考文献-------------------------------------------------------- 22 致谢----------------------------------------------------------- 23 附表1 机械加工工艺过程卡片--------------------------------------- 24 附表2 数控加工工序卡片------------------------------------------- 25 附表3 数控加工工序卡片------------------------------------------- 26 附表4 数控加工工序卡片------------------------------------------- 27 附表5 数控加工工序卡片------------------------------------------- 28摘要在数控编程中,工艺分析和工艺设计是至关重要的,无论是手工编程还是自动编程,在加工前都要对所加工零件进行工艺分析,拟定加工方案,选择加工设备、刀具、夹具,确定切削用量,安排加工顺序,制定走刀路线等。
浅析发动机活塞加工工艺

浅析发动机活塞加工工艺摘要:近些年来我国的科学技术和经济水平都得到了蓬勃的发展,在这样一个快节奏的时代背景之下,我国社会生活当中的各行各业都在紧随时代发展趋势不断地进行着与时俱进的创新和变革。
在很多机械设计制造工作过程当中,能够使得整个机械的灵活驱动与控制效果得到显著提升的一个工艺内容就是活塞的优越性能,能够帮助汽车的发动机和内燃机在实际的工作运转过程当中发挥出诸多方面的优良性能,从而能够使得整个汽车的驱动装置得到全面的优化改进和完善调整,不仅如此,相关的技术管理人员还能够通过对于活塞的质量把控,实现整个汽车机械制造效率效果和质量水平的提升。
本篇文章将针对这一点做出简要分析以供参考。
关键词:发动机;活塞加工;工艺浅析我国成功研制的第一台航空发动机实际上就是一个活塞式的发动机,而小型飞机则是现阶段国外的众多航空发动机当中的活塞式发动机应用类型,我国全国范围内应用这种活塞式的航空发动机并不是很多,这也是因为国内在这方面的技术研究还不够成熟。
而相应的国防科工委也就针对这一点进行了诸多方面工作内容的部署和安排,对置活塞式发动机的空白对于我国来说是一项刻不容缓的研制开发方向,这也不容置疑地被纳入了国防科工委所提出的诸多重点工作内容之一。
再整个活塞式发动机当中有一个极为关键的重要部件,就是安装节,相关的技术管理人员想要提升我国活塞式发动机的生产效果,就必须要严格把控安装节的复杂型状结构和高水平的尺寸精度。
一、活塞加工的一般技术要求所谓的活塞加工实际上包含着很多种类型,这也与时代不断地进步更迭紧密相关。
铝活塞实际上是应用最为广泛的一种工业性活塞,这种工业应用级别的活塞已经被我国的官方科技委员会认定机构制定了相应的技术条件的国家标准,相关的技术管理人员在实际的活塞式发动机的安装和设计制造过程当中,一定要严格按照国家的相关要求和标准贯彻和开展,确保铝活塞各个组成部分的尺寸能够得到严谨认真的精确把控,以此来提升设计加工制造的效率效果和质量水平。
最新活塞加工工艺说明书剖析
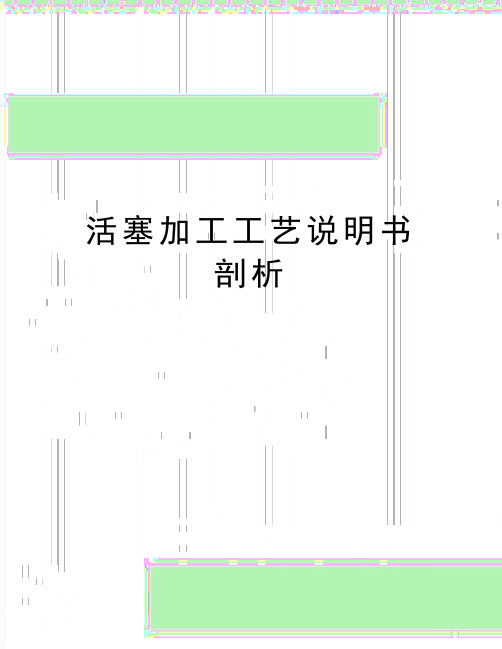
活塞加工工艺说明书剖析课程设计题目活塞加工工艺设计专业机械设计与制造姓名付中望学号17号指导教师曹晓峰二O 一三年九月二十六日重庆工业职业技术学院目录前言1、零件的分析 (1)1.1活塞的功用、结构特点及工作条件分析 (2)1.2活塞的主要加工表面及技术要求 (3)2、活塞工艺规程设计 (4)2.1活塞的毛坯材料及制造方法 (5)2.2定位基准的选择 (6)2.3制定活塞加工工艺路线 (7)2.3.1选择各表面加工方法 (8)2.3.2各表面加工顺序确定 (9)2.4工艺路线方案 (10)2.5工艺路线方案分析 (11)2.6机械加工余量及工序尺寸 (12)2.7致谢…………………………………………………………………132.8参考文献 (14)前言我国的制造业飞速发展,在液压的系统的在汽车、机床、航天各领域的使用也越来越多,其中活塞是液压系统传动当中不可缺少的一部分,它的工作情况直接影响到液压系统的动力冲动效率,所以,如何能使活塞的生产效率、高质量、省成本、省时间是我们今天汽车行业的努力方向。
随着汽车、机床、等的动力性、经济性、环保性及可靠性的要求越来越严格,活塞已发展成为集轻质高强度新材料、异型外圆复合型面、异型销孔等多项新技术于一体的高技术含量的产品,以保证活塞的耐热性、耐磨性、平稳的导向性和良好的密封功能,减少摩擦损失,降低油耗、噪声和排放。
为满足以上的功能要求,为提高活塞的承载能力,所以对对活塞的加工精度要求比较高。
活塞作为典型的液压系统关键零部件,在切削加工方面具有很强的工艺特点。
目前,国内活塞制造行业通常是由通用机床和结合活塞工艺特点的专用设备组成机加工生产线,因此,专用设备就成为活塞切削加工的关键设备,其功能和精度将直接影响最终产品的关键特性的质量指标。
1、零件分析:1.1活塞的作用及结构形式由于活塞在液体压力的作用下沿缸筒往复滑动,因此,它与缸筒的配合应适当,既不能过紧,也不能间隙过大。
汽车发动机活塞加工工艺讲解

毕业设计(论文)题目汽车发动机活塞加工工艺及其夹具设计系(院)自动化系专业机械设计制造及其自动化班级2008级1班学生姓名学号指导教师季德生职称讲师二〇一二年六月二十日独创声明本人郑重声明:所呈交的毕业设计(论文),是本人在指导老师的指导下,独立进行研究工作所取得的成果,成果不存在知识产权争议。
据我所知,除文中已经注明引用的内容外,本设计(论文)不含任何其他个人或集体已经发表或撰写过的作品成果。
对本文的研究做出重要贡献的个人和集体均已在文中以明确方式标明。
本声明的法律后果由本人承担。
作者签名:二〇一一年月日毕业设计(论文)使用授权声明本人完全了解滨州学院关于收集、保存、使用毕业设计(论文)的规定。
本人愿意按照学校要求提交学位论文的印刷本和电子版,同意学校保存学位论文的印刷本和电子版,或采用影印、数字化或其它复制手段保存设计(论文);同意学校在不以营利为目的的前提下,建立目录检索与阅览服务系统,公布设计(论文)的部分或全部内容,允许他人依法合理使用。
(保密论文在解密后遵守此规定)作者签名:二〇一一年月汽车发动机活塞加工工艺及夹具设计摘要提高产量、降低成本、准时交付、快速响应,使产品快速占领市场,已经越来越成为现在制造业中企业所追求的目标。
现在敏捷制造、快速原型制造、快速模具工装制造技术已经成为内燃机零件工业特别是活塞行业竞争的焦点。
因此,针对各种内燃机活塞机械加工工艺过程的广泛探索,从而缩短或简化工艺流程、提高产品质量、降低生产制造成本也变得越来越重要。
本毕业设计论文通对分析活塞加工技术的发展、活塞的结构特点、活塞各个工作面的加工特征及其工作环境,确定了活塞的加工过程及加工方案,其中主要包括:材料的选用、毛坯制造工艺、加工基准的选择、各道工工序切削用量及其加工余量的确定和工序安排等。
并且进一步设计了活塞加工过程中用到的一套典型的夹具,精镗销孔夹具设计,其主要内容包括:定位方案与夹紧方案的设计、夹具的工作原理以及在夹具设计过程中应该注意的问题。
活塞加工工艺
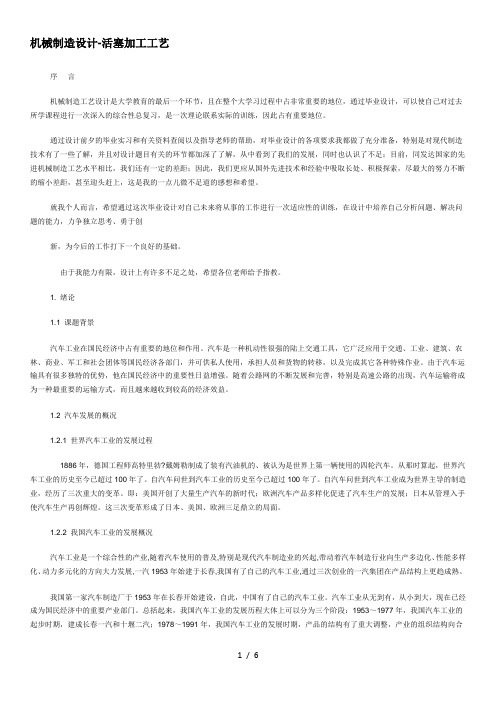
机械制造设计-活塞加工工艺序言机械制造工艺设计是大学教育的最后一个环节,且在整个大学习过程中占非常重要的地位,通过毕业设计,可以使自己对过去所学课程进行一次深入的综合性总复习,是一次理论联系实际的训练,因此占有重要地位。
通过设计前夕的毕业实习和有关资料查阅以及指导老师的帮助,对毕业设计的各项要求我都做了充分准备,特别是对现代制造技术有了一些了解,并且对设计题目有关的环节都加深了了解,从中看到了我们的发展,同时也认识了不足;目前,同发达国家的先进机械制造工艺水平相比,我们还有一定的差距;因此,我们更应从国外先进技术和经验中吸取长处、积极探索,尽最大的努力不断的缩小差距,甚至迎头赶上,这是我的一点儿微不足道的感想和希望。
就我个人而言,希望通过这次毕业设计对自己未来将从事的工作进行一次适应性的训练,在设计中培养自己分析问题、解决问题的能力,力争独立思考、勇于创新,为今后的工作打下一个良好的基础。
由于我能力有限,设计上有许多不足之处,希望各位老师给予指教。
1. 绪论1.1 课题背景汽车工业在国民经济中占有重要的地位和作用。
汽车是一种机动性很强的陆上交通工具,它广泛应用于交通、工业、建筑、农林、商业、军工和社会团体等国民经济各部门,并可供私人使用,承担人员和货物的转移,以及完成其它各种特殊作业。
由于汽车运输具有很多独特的优势,他在国民经济中的重要性日益增强。
随着公路网的不断发展和完善,特别是高速公路的出现,汽车运输将成为一种最重要的运输方式,而且越来越收到较高的经济效益。
1.2 汽车发展的概况1.2.1 世界汽车工业的发展过程1886年,德国工程师高特里勃?戴姆勒制成了装有汽油机的、被认为是世界上第一辆使用的四轮汽车。
从那时算起,世界汽车工业的历史至今已超过100年了。
自汽车问世到汽车工业的历史至今已超过100年了。
自汽车问世到汽车工业成为世界主导的制造业,经历了三次重大的变革。
即:美国开创了大量生产汽车的新时代;欧洲汽车产品多样化促进了汽车生产的发展;日本从管理入手使汽车生产再创辉煌。
- 1、下载文档前请自行甄别文档内容的完整性,平台不提供额外的编辑、内容补充、找答案等附加服务。
- 2、"仅部分预览"的文档,不可在线预览部分如存在完整性等问题,可反馈申请退款(可完整预览的文档不适用该条件!)。
- 3、如文档侵犯您的权益,请联系客服反馈,我们会尽快为您处理(人工客服工作时间:9:00-18:30)。
课程设计题目活塞加工工艺设计专业机械设计与制造姓名付中望学号17号指导教师曹晓峰二O 一三年九月二十六日重庆工业职业技术学院前言1、零件的分析 (1)1.1活塞的功用、结构特点及工作条件分析 (2)1.2活塞的主要加工表面及技术要求 (3)2、活塞工艺规程设计 (4)2.1活塞的毛坯材料及制造方法 (5)2.2定位基准的选择 (6)2.3制定活塞加工工艺路线 (7)2.3.1选择各表面加工方法 (8)2.3.2各表面加工顺序确定 (9)2.4工艺路线方案 (10)2.5工艺路线方案分析 (11)2.6机械加工余量及工序尺寸 (12)2.7致谢 (13)2.8参考文献 (14)我国的制造业飞速发展,在液压的系统的在汽车、机床、航天各领域的使用也越来越多,其中活塞是液压系统传动当中不可缺少的一部分,它的工作情况直接影响到液压系统的动力冲动效率,所以,如何能使活塞的生产效率、高质量、省成本、省时间是我们今天汽车行业的努力方向。
随着汽车、机床、等的动力性、经济性、环保性及可靠性的要求越来越严格,活塞已发展成为集轻质高强度新材料、异型外圆复合型面、异型销孔等多项新技术于一体的高技术含量的产品,以保证活塞的耐热性、耐磨性、平稳的导向性和良好的密封功能,减少摩擦损失,降低油耗、噪声和排放。
为满足以上的功能要求,为提高活塞的承载能力,所以对对活塞的加工精度要求比较高。
活塞作为典型的液压系统关键零部件,在切削加工方面具有很强的工艺特点。
目前,国内活塞制造行业通常是由通用机床和结合活塞工艺特点的专用设备组成机加工生产线,因此,专用设备就成为活塞切削加工的关键设备,其功能和精度将直接影响最终产品的关键特性的质量指标。
1、零件分析:1.1活塞的作用及结构形式由于活塞在液体压力的作用下沿缸筒往复滑动,因此,它与缸筒的配合应适当,既不能过紧,也不能间隙过大。
配合过紧,不仅使最低启动压力增大,降低机械效率,而且容易损坏缸筒和活塞的滑动配合表面;间隙过大,会引起液压缸内部泄漏,降低容积效率,使液压缸达不到要求的设计性能。
液压力的大小与活塞的有效工作面积有关,活塞直径应与缸筒内径一致。
所以,设计活塞时,主要任务就是确定活塞的结构型式。
活塞常见的结构形式可分为整体式和分体式两种。
1、整体式活塞要在活塞圆周上开沟槽以安装密封件和支承环,结构简单,但是活塞加工困难,另外密封件安装时也容易拉伤和扭曲,影响密封件的密封性能能和使用寿命。
2、分组式活塞大多数可以多次拆装,密封件使用寿命长。
在通常情况下,支承环是活塞件的不可缺的构件,它不但可以精确导向,还可以吸收活塞运动时随时产生的侧向力,因而大多数密封件都与支承环联合使用,大大减低了活塞加工成本,活塞形式如下:1.2活塞技术要求和重要加工表面分析:活塞的宽度B一般为活塞外径D的(0.6-1)倍,因为活塞的外径D等于钢筒的内径,所以活塞的宽度B取50mm。
另外也要根据密封件的形式、数量、安装导向环的沟槽尺寸进一步细化,使上述原件间距适当。
由于采用橡胶密封件,活塞外径公差取f19,与活塞杆配合的内孔公差等级取H17、活塞外圆表面粗糙度要优于Ra0.32内孔粗糙度要优于Ra0.8m。
活塞的具体参数为:活塞的主要加工表面及技术要求:φ45H内孔、φ100h10和φ125f7外圆及台阶表面2、活塞工艺规程设计2.1活塞的毛坯材料及制造方法活塞是密封保压件,要求具有良好的耐磨性、弹性和致密性,目前钢与铸铁已成为制造活塞的基本材料,而铸铁活塞具有价格低廉、生产流程较短的特点,应用范围越来越广,材质可以是灰铸铁,球墨铸铁,可锻铸铁,高合金铸铁,低合金铸铁等。
而灰铸铁活塞材料适合单体铸造,也适合筒体铸造,是一种适用的经济型活塞材料。
由于单体铸造活塞在铸态下组织稳定性差,硬度均匀性差,通常采用热处理方法来改善活塞的热稳定性和硬度均匀性。
而热处理不仅增加投资成本,而且破坏了活塞铸态下的应力分布,降低了活塞的抗腐蚀性和耐磨性。
在开发试验阶段及小批量生产过程中,经常会出现同一件产品硬度差波动较大、热稳定性较差、组织中特殊石墨量无法得到有效控制、出现针状组织、材质废品率较高等情况。
为了解决这些问题,分别从原材料、化学成分、熔炼工艺、孕育处理、浇注系统以及造型工艺等方面进行有效控制,成功生产出满足要求的灰铸件活塞铸件。
2.2定位基准的选择1、定位基准的选择根据零件的结构形状和加工精度的要求,正确选择零件加工时的定位基准是制订加工工艺规程时应先考虑的主要问题之一。
零件加工的第一道工序只能用毛坯的表面来定位,这种定位基准成为粗基准。
在以后的工序中用已加工表面来定位,称精基准。
基准按功用不同分为设计基准和工艺基准1. 设计基准在零件图上用来确定其他点、线、面位置的基准。
2.工艺基准在加工和装配过程中使用的基准。
按作用不同又分为(1) 定位基准。
在加工中使用工件在机床或夹具上占有正确的位置所采用的基准。
(2)测量基准。
零件检验时,用以测量已加工表面尺寸和位置所用的基准。
(3)装配基准。
在装配时用以确定零件或部件在机械产品中位置的基准。
2、粗基准的选择原则:(1) 保你证加工表面与不加工表面之间的相互位置尺寸要求,应选用不加工作为粗基准。
(2)多加工表面或不加工表面与加工表面之间相互之间位置要求不严格的零件,粗基准的选择应能保证合理地分配各加工表面的余量。
(3)作为粗基准的毛坯表面应尽量光滑平整,以便零件夹紧可靠。
(4)粗基准一般不能重复使用。
精基准的选择原则:选择精基准时。
主要考虑保证零件加工精度,同时考虑装夹准确、可靠和方便,而且夹具简单。
在选择精基准时应遵循以下原则:1)基准重合原则2 )基准统一原则3)便于装夹原则(5)粗基准的选择粗基准的选择应能保证精基准加工面之间的位置精度,合理分配各加工面的余量,为后续工序提供精基准,所以为了更便于定位,装夹和加工,可选择该毛坯的外圆柱面作为加工粗基准。
(6)精基准的选择根据零件的加工方便,装夹方便,定位准确,误差少的原则,选择零件的已加工外圆柱面,内圆柱面及两端面作为精基准。
由于毛坯的精度较高,所以毛坯的外表面、内圆及顶面可直接作为粗基准,如粗车外圆、及端面。
活塞属薄壁筒形零件,径向刚度很差,而主要表面尺寸精度及个主要表面之间的位置精度要求又较高,所以在产品设计时就针对活塞的结构特点,设计了专供加工时定位用的辅助精基准——止口内孔及端面。
在外圆、端面、孔等加工时,就采用了该精基准定位。
这不仅符合“基准统一”和“工序集中”原则,而且便于轴向夹紧,可采用一套夹具即可。
但以此作为精基准不仅不符合“基准重合”原则,而且还为此增加了工序和设备。
由于活塞销孔沿活塞轴线方向位置尺寸的设计基准是顶面,所以精镗削孔时以顶面为轴向定位基准,而止口的精加工以顶面为定位基准,这样可以减少因基准不重合而产生的定位误差。
在钻、扩孔时采用了以外端作为角向定位基面。
这是因为若采用销孔自定位,定位元件不易布置,夹具结构复杂。
而由于活塞毛坯精度较高,以此作为角定位可以满足加工要求做到基准重合原则。
2.3制定活塞加工工艺路线:1、确定重要加工表面及部位:2、选择各表面的加工方法:3、加工阶段的划分①划分的原因:保证加工余量合理,划分加工阶段能合理地使用机床设备,便与热处理工序的安排,便于及时的发现毛坯的缺陷。
②阶段的划分:由于该毛坯为铸件毛坯,内孔可直接形成,并且毛坯的厚度较大。
因此,易形成各种缺陷,因此,粗加工内外圆柱面及两端的加工,然后进行二次时效处理,到了半精加工因此,精加工时采用工序集中加工,精加工内圆柱面右端面,半精加工外圆柱面。
2.4初步拟定传动轴机械加工工艺路线:工艺路线使用设备第一步:车右端面 CA6140 第二步:车φ125外圆CA6140 第三步:掉头车左端面 CA6140 第四步:粗车φ100和φ125外圆留余量 CA6140 第五步:掉头车右端φ100和φ125外圆留余量 CA6140 第六步:调质处理专用设备第七步:加工孔φ45h7钻孔、扩孔、绞孔到尺寸并倒角钻床第八步:半精车外圆φ100和φ125外圆留精加工余量 CA6140第九步:精加工φ100和φ125外圆到尺寸 CA6140 第十步:精加工件长度到尺寸 CA6140 第十一步:测量检验专用工具第十二步:终检2.5工艺方案的比较与分析从方案来看此方案是先加工表面在加工孔,然后再以孔为基准加工外圆,这样做到了基准重合原则所以加工出的尺寸精度很高可以满足加工的要求,并适合大批量生产,所以此方案比较合理2.6机械加工余量及工序尺寸余量:1.钻活塞孔:φ45H70025.0+mm 3.粗车外圆、环槽、裙部及端面 外圆 :φ125f7043.0083.0--mm φ100h100410.0-mm 工序尺寸:致谢通过这次的课程设计,它提供了我们一个用自己所学知识的机会,及相关资料到对零件精度分析计算和运用所学的软件制图、工艺图表、等软件进行运用。
都对我们所学的知识进行了检验,这次的课程设计有苦有甜,让我记忆深刻。
设计思路是重要的,只要设计思路是成功的,那么一个设计就会事半功倍,因此通过这次的设计,我们也学会了做事情之前都应该有充分的准备,为事情的成功打下基础。
制作的过程是一个考验我们耐心的过程,不能有丝毫的急躁和马虎,要一步一步来。
通过这次的设计,我们基本掌握了零件的加工过程分析、工艺文件的编制方法和步骤,学会查阅相关手册,选择使用相关工艺装备等等。
总的来说,这次设计让我们在基本理论的综合运用及正确解决实际问题等方面得到了一次较好的训练,提高了我们思考问题、解决问题、创新设计的能力,为以后更好的设计大侠了基础。
通过这次的设计,我感受到了团队合作的重要性,在团队里,我们两个进行了分工合作,我知道在以后的和工作中还会有许多合作,所以我们一定要互相学习和帮助,让团队的力量发挥到最大。
由于我们的能力有限,设计之中指导老师给我们提供了很多的帮助,才使得我们的设计得以顺利的完成,在此特别感谢关老师的指导。
我相信在以后的时间里,我们会再接再厉,争取做到更好。
参考文献[1] 《机床夹具设计》第3版薛源顺主编机械工业出版社 2012.1[2] 《机床夹具设计手册》(第三版—电子档)上海科学技术出版社2006.6[3] 《金属机械加工工艺人员手册》(第四版)赵如福主编上海科学技术出版社2006.[4] 《机械制造工艺及设备设计手册》机械制造工艺及设备设计手册编写组编机械工业出版社1990.11。