利用脱硫石膏年产30万吨建筑石膏粉生产线
火力发电厂固体废弃物的资源化利用
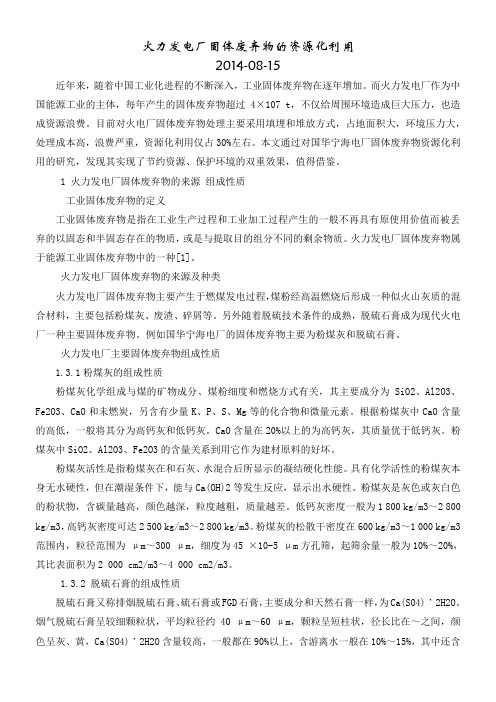
火力发电厂固体废弃物的资源化利用2014-08-15近年来,随着中国工业化进程的不断深入,工业固体废弃物在逐年增加。
而火力发电厂作为中国能源工业的主体,每年产生的固体废弃物超过4×107 t,不仅给周围环境造成巨大压力,也造成资源浪费。
目前对火电厂固体废弃物处理主要采用填埋和堆放方式,占地面积大,环境压力大,处理成本高,浪费严重,资源化利用仅占30%左右。
本文通过对国华宁海电厂固体废弃物资源化利用的研究,发现其实现了节约资源、保护环境的双重效果,值得借鉴。
1 火力发电厂固体废弃物的来源组成性质工业固体废弃物的定义工业固体废弃物是指在工业生产过程和工业加工过程产生的一般不再具有原使用价值而被丢弃的以固态和半固态存在的物质,或是与提取目的组分不同的剩余物质。
火力发电厂固体废弃物属于能源工业固体废弃物中的一种[1]。
火力发电厂固体废弃物的来源及种类火力发电厂固体废弃物主要产生于燃煤发电过程,煤粉经高温燃烧后形成一种似火山灰质的混合材料,主要包括粉煤灰、废渣、碎屑等。
另外随着脱硫技术条件的成熟,脱硫石膏成为现代火电厂一种主要固体废弃物。
例如国华宁海电厂的固体废弃物主要为粉煤灰和脱硫石膏。
火力发电厂主要固体废弃物组成性质1.3.1粉煤灰的组成性质粉煤灰化学组成与煤的矿物成分、煤粉细度和燃烧方式有关,其主要成分为SiO2、Al2O3、Fe2O3、CaO和未燃炭,另含有少量K、P、S、Mg等的化合物和微量元素。
根据粉煤灰中CaO含量的高低,一般将其分为高钙灰和低钙灰。
CaO含量在20%以上的为高钙灰,其质量优于低钙灰。
粉煤灰中SiO2、Al2O3、Fe2O3的含量关系到用它作为建材原料的好坏。
粉煤灰活性是指粉煤灰在和石灰、水混合后所显示的凝结硬化性能。
具有化学活性的粉煤灰本身无水硬性,但在潮湿条件下,能与Ca(OH)2等发生反应,显示出水硬性。
粉煤灰是灰色或灰白色的粉状物,含碳量越高,颜色越深,粒度越粗,质量越差。
年产3000万平方米综合利用脱硫石膏纸面石膏板生产线的研发与建设

年产3000 万平方米综合利用脱硫石膏纸面石膏板生产线的研发与建设1.前言2010年在公司的正确领导下,在公司项目建设委员会、石膏板事业部及相关职能部门的帮助和支持下,镇江北新项目部全体成员面对艰巨繁重的项目建设任务,全体项目建设人员同心同德、团结奋进,项目建设顺利完成,取得了优异成绩,实现了对公司和对政府的当年立项、当年施工、当年投产、当年见效益的承诺。
项目具有以下四个特点:建设周期短。
项目建设周期是8 个月20 天,项目于2010 年4 月8 日开工,2010 年12 月28 日投产,2011 年3 月29 至31 日完成项目的初步验收,2011 年6 月25 日至27 日完成项目的达产验收。
建设质量好。
项目建设研发楼的建设荣获镇江市“金山杯” 奖。
建设成本低。
项目部加强了项目可控成本的控制,成本得到有效控制,部分可控成本节省大量资金。
建设安全优。
项目建设期间零事故。
2.项目背景根据北新建材战略部署,在2010 年北新建材石膏板生产线完成10 亿平方米的产能布局,到2010 年底,北新建材石膏板产3000 万平方米利用脱硫石膏 5000 吨/ 年轻钢龙骨生产线。
2)工期目标:项目开工日期2010 年 4 月 1 日,于 2010 能达到 10 亿平方米,镇江北新建材的石膏板项目是关键项目。
因为该项目具有一定的政治性和战略性, 使该项目的建设具有如 下特点:1.项目投资大、系统复杂、涉及专业多,风险大;2.施工总工期为 9 个月,工期紧张,项目相对比较复杂;3.气候影响因素多:如台风、暴雨等;4.交叉作业多,危险因素多;5.材料价格有一定浮动。
3.项目总体目标3.1 项目目标( 1)交付成果:建设一条年产为原料的纸面石膏板生产线及配套年 12 月 30 日投产,项目建设工期 9 个月;(3)费用目标:项目总投资控制在 1.2 亿元人民币;(4)质量目标:分项工程一次验收合格率 92%,工程优良 率 95%,一次通过竣工验收,竣工资料与与工程同步移交;(5)安全环境目标:安全零事故,环境要求达国家标准。
时产30吨脱硫石膏烘干压球生产线工艺流程及方案

时产30吨脱硫石膏烘干压球生产线工艺流程及方案时产30吨脱硫石膏烘干压球生产工艺流程及图解首先:脱硫石膏由烘干到成球工艺流程图如下:除尘器脱硫石膏石膏专用供料机卧式烘干机压密机压球机成品其次:脱硫石膏烘干及成型系列配套设备特点如下:一、脱硫石膏粉:脱硫石膏是用火电厂的一种废料,加工后可做水泥缓凝剂。
二、石膏专用供料机:控制整条生产线的量,保证烘干机供料均匀,也起到把石膏湿块打散和搅拌作用。
三、卧式脱硫石膏烘干机:是把水分高于12%的石膏粉料烘干至8%-10%以下,便于成球。
四、压密机:把脱硫石膏进行加压,密实,增加石膏的密实度,便于成型的一种理想辅助设备。
压密机的加入提高脱硫石膏成球率,此设备特点如下:压密机是对不易结构成型的松散物料,预先排气加密,使物料进入成型机很好的结构成型,加密机系列有两辊加密型、四辊复式加密型,本机组装合理结构紧凑,运转平稳,性能可靠。
五、脱硫石膏压球机:把压密好的石膏进行压制成球。
脱硫石膏压球机能将脱硫石膏粉末,在不需要添加任何粘合剂情况下一次性压制成球,且成球率在95%以上,压出来的球硬度很强,搬运装卸不宜破碎,脱硫石膏球成品纯度得到保证,直接成形。
(注:脱硫石膏压球机工作原理:脱硫石膏压球机是脱硫石膏压球工艺的关键设备,其结构是否合理直接影响脱硫石膏成球质量。
成型机的主要机型是对辊成型机,它有一对轴线相互平行、直径相同、彼此间有一定间隙的圆柱形型轮,型轮上有许多形状和大小相同、排列规则的半球窝,型轮是成型机主部件。
在电动机的驱动下,两个型轮以相同速度、相反方向转动,当物料落人两型轮之间在结合处开始受压,此时原料在相应两球窝之间产生体积压缩;型轮连续转动,球窝逐渐闭合,成型压力逐渐增大当转动到两个球窝距离最小时成型压力达到最大。
然后型轮转动使球窝逐渐分离,成型压力随着迅速减小。
当成型压力减至零之前,压制成的脱硫石膏就开始膨胀脱离。
辊皮材质9铬2钼钒,洛氏硬度(HRC)55-58度,耐磨,耐用。
利用脱硫石膏年产万吨建筑石膏粉生产线

利用脱硫石膏年产30万吨建筑石膏粉生产线工艺方案(回转烘干机+沸腾流化床)1.工艺要求:a.生产能力:≥42吨/小时β型半水石膏粉。
?b.产品质量:按《建筑石膏》国标执行,满足纸面石膏板用粉要求。
?c.环保要求:粉尘排放浓度应达到GB16297-1996标准要求。
?2.工艺方案:a.煅烧:因为脱硫石膏含有超过10%的游离水,结合国内磷石膏制备建筑石膏粉的成功经验,采用二水石膏预烘干、沸腾流化床煅烧的二步法工艺煅烧建筑石膏粉。
具体为:用装载机将原料从原料堆场送至进料斗,经计量后由皮带输送机送入双筒回转烘干机烘干去除游离水(该处热源为燃煤热风炉),出料后经集料收尘器收料,经提升输送设备送入流化床煅烧(采用导热油锅炉为热源),煅烧完毕后送入球磨机进行研磨改性和冷却,然后送入熟粉料仓备用。
b.环保:烘干、油炉、煅烧系统的烟气尾气与炒制沸腾炉的热气采用旋风(多管)加电除尘(详见工艺布置图),?3.工艺布置图:附后4.主要设备介绍:A、烘干系统(回转烘干机):a、该设备采用多区段和独特的中心扬料板,可有效增加物料和热介质的接触面积,大大提高了烘干效率,起到了节能、降耗的作用。
另外因为该设备主体是建材行业标准设备,所以在技术、维修、备件维护等方面都很方便,是一台非常理想的烘干干燥设备。
b、燃烧炉:沸腾燃煤热风炉。
B、炒制沸腾炉:沸腾炉煅烧的特点:(1)设备小巧,生产能力大沸腾炉生产能力的大小实质上由热源通过加热器壁传递给物料的热量多少来决定。
沸腾炉由于物料实现了彻底的流态化,因此炉内不需要安装搅拌设备。
在炉内就可以高密度地安装很多加热管,因此尺寸不大的炉子就可以有非常大的传热面积。
另外,沸腾炉采用的热源为饱和蒸气或载热油,其传热系数比热烟气为热源的传热系数高出一个数量级。
从传热方程式就可看出,由于传热系数和传热面积都较大,总传热量也就大。
(2)结构简单,不易损坏由于物料实现了流态化,炉子就不需要有转动的部件,投产后也几乎不需要维修保养。
安徽贵航特钢有限公司
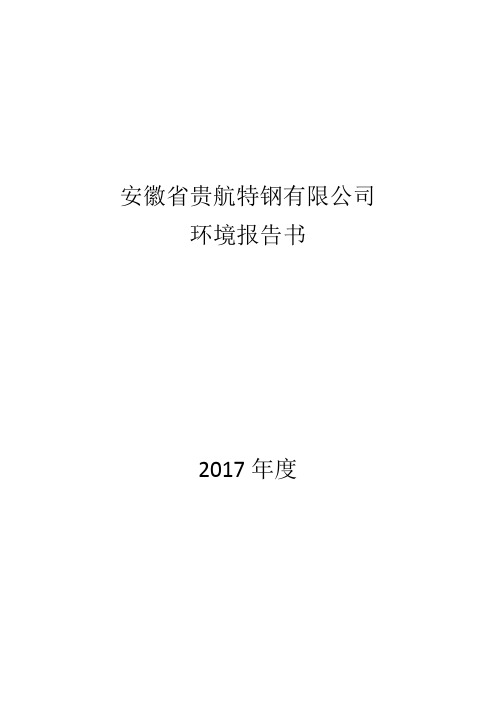
安徽省贵航特钢有限公司环境报告书2017年度一、项目基本情况安徽省贵航特钢有限公司成立于2010年4月,依托2009年底建成投产的池州市贵航金属制品有限公司,经贵池区政府招商引资,2010年4月由池州市贵航金属制品有限公司与自然人林木平、林建等人共同出资设立安徽省贵航特钢有限公司,公司位于池州市贵池区前江工业园(省级开发区)是一家从事黑色金属冶炼、高强度钢筋、抗震钢筋轧制的民营钢铁企业,法人代表林木平,公司现有资产总额约61亿元,具备年产200万吨特钢的生产能力,主要生产设备为:2台180m2烧结机、2座1080m3高炉、2台120t转炉、2条600型全连轧轧钢生产线,拥有职工2000余人,其中管理人员158人,技术人员112人。
公司于2013年11月获得钢筋混凝土用热轧钢筋生产许可证,2014年3月通过质量,环境,安全和能源管理体系认证,2014年11月入围工信部符合《钢铁行业规范条件》企业名单(第三批)。
二、环境保护基本情况公司按照《GB/T24000-IS014000环境管理系列标准》要求,建立了环境管理体系,编制了《环保制度汇编》。
公司专门成立以总经理为组长的环境保护管理领导小组,全面负责公司环境管理的领导工作。
公司下设安全环保部,负责公司日常环境保护具体工作,配备专职环保管理员14人,负责公司的环保检查、环保监测、环保设施的运行监督和环境隐患整改督査等工作,以确保公司环保体系的有效运行。
各生产单位及职能部室完全按照环境管理体系要求对生产作业进行全过程环境保护管理。
(1)废气治理公司的生产设施主要有12m2竖炉两座,180m烧结机2台,1080m高炉两座,120吨转炉两座,600轧机生产线两条,以及配套的110KV变电站,煤气发电机组。
综合原料场主要污染物为粉尘,采用挡风墙、喷水等抑尘措施。
烧结厂主要污染物为烟、粉尘、SO2,烧结机头烟气采用电除尘脱硫装置去除烟尘和SO2,烧结机尾采用电除尘收尘,烧结的配料、破碎、筛分等环节产生的粉尘由布袋除尘器收尘。
火电厂脱硫石膏的综合利用
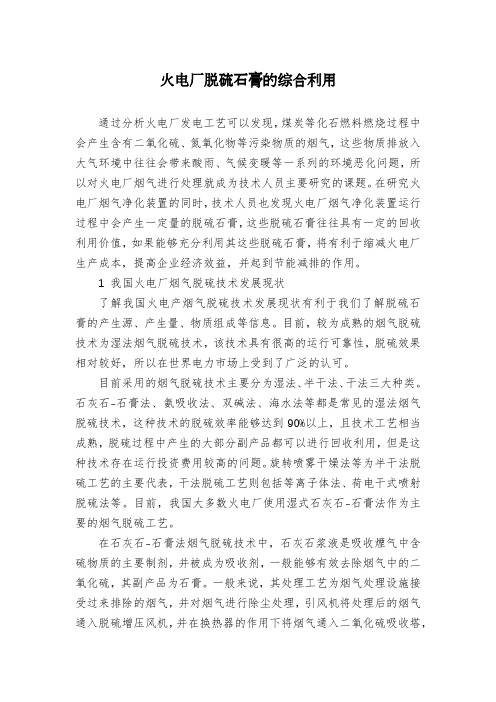
火电厂脱硫石膏的综合利用通过分析火电厂发电工艺可以发现,煤炭等化石燃料燃烧过程中会产生含有二氧化硫、氮氧化物等污染物质的烟气,这些物质排放入大气环境中往往会带来酸雨、气候变暖等一系列的环境恶化问题,所以对火电厂烟气进行处理就成为技术人员主要研究的课题。
在研究火电厂烟气净化装置的同时,技术人员也发现火电厂烟气净化装置运行过程中会产生一定量的脱硫石膏,这些脱硫石膏往往具有一定的回收利用价值,如果能够充分利用其这些脱硫石膏,将有利于缩减火电厂生产成本,提高企业经济效益,并起到节能减排的作用。
1 我国火电厂烟气脱硫技术发展现状了解我国火电产烟气脱硫技术发展现状有利于我们了解脱硫石膏的产生源、产生量、物质组成等信息。
目前,较为成熟的烟气脱硫技术为湿法烟气脱硫技术,该技术具有很高的运行可靠性,脱硫效果相对较好,所以在世界电力市场上受到了广泛的认可。
目前采用的烟气脱硫技术主要分为湿法、半干法、干法三大种类。
石灰石-石膏法、氨吸收法、双碱法、海水法等都是常见的湿法烟气脱硫技术,这种技术的脱硫效率能够达到90%以上,且技术工艺相当成熟,脱硫过程中产生的大部分副产品都可以进行回收利用,但是这种技术存在运行投资费用较高的问题。
旋转喷雾干燥法等为半干法脱硫工艺的主要代表,干法脱硫工艺则包括等离子体法、荷电干式喷射脱硫法等。
目前,我国大多数火电厂使用湿式石灰石-石膏法作为主要的烟气脱硫工艺。
在石灰石-石膏法烟气脱硫技术中,石灰石浆液是吸收煙气中含硫物质的主要制剂,并被成为吸收剂,一般能够有效去除烟气中的二氧化硫,其副产品为石膏。
一般来说,其处理工艺为烟气处理设施接受过来排除的烟气,并对烟气进行除尘处理,引风机将处理后的烟气通入脱硫增压风机,并在换热器的作用下将烟气通入二氧化硫吸收塔,烟气以逆流而上的形式与吸收塔上部喷淋下来的吸收剂进行充分接触,并完成相关化学梵音,从而实现烟气含硫物质的消除,这个过程中会生成亚硫酸钙溶液,亚硫酸钙溶液流入吸收塔的氧化槽中,并通过鼓入空气的方法让亚硫酸钙强制氧化,并生成石膏,随后通过脱水设备的处理,湿石膏会变成固态石膏。
年产5万吨脱硫石膏粉生产线工艺方案0

T 中控室p jj年产5万吨脱硫石膏粉生产线工艺方案一、工艺要求:1.1生产能力:±6.9吨/小时B型建筑石膏粉。
脱硫石膏原料附着水:10-12%。
处理原料:10-11吨/小时。
1.2产品质量:按照《建筑石膏》国标(GB/T9776-2008)执行,满足石膏砂浆、石膏砌块等石膏建筑用品用粉要求。
1.3环保要求:符合国家环保要求(粉尘排放<20mg/m3,无污水排放,无有害气体排放)。
1.4蒸汽条件:热电厂低压蒸汽1.2T.5Mpa饱和蒸汽。
1.5蒸汽使用量:±83吨/天(±2.49万吨/每年)二、工艺方案:利用电厂低压蒸汽作为热源;采用预烘干、煅烧两步法工艺。
2.1工艺流程图:2.2工艺顺序介绍:上料铲车将原料送入进料斗,进料斗配备振打电机和计量皮带机,计量皮带机会根据预先输入设计好的参数进行送料,误差不超过0.5吨/小时。
脱硫石膏原料通过皮带输送机进入回转混合干燥机,回转混合干燥机适用于利用煅烧炉回料进行烘干。
经过烘干后的原料通过提升机进入煅烧炉内煅烧,该煅烧炉采用流态化煅烧,保证了煅烧的均匀性。
煅烧后的半成品进入环磨机改性粉磨,再通过气流输送机进入成品仓。
最后包装机完成成品包装。
生产过程中产生的粉尘由脉冲布袋除尘器集中进行处理,确保生产车间无粉尘排放。
粉尘通过螺旋输送机输送机和提升机再次回到煅烧炉,实现生产零废料。
2.3组成部分该设备由原料系统、预干燥系统、煅烧系统、供热系统、控制系统、除尘系统、成品储存系统组成,各工段以提升输送、管道等相连接,最终将二水脱硫石膏煅烧为合格的半水石膏。
2.3.1原料系统:原料系统是供给设备二水脱硫石膏原料的,主要有上料斗、辅助振动器、计量皮带、原料输送带、除铁器、湿料喂料器及电控部分等组成。
它的作用是按设备的煅烧要求,根据原料湿度和流量,输送给设备相应的二水石膏原料。
2.3.2预干燥系统:预系统采用回转混合干燥机进行原料干燥。
该机主要由W形壳体和两根桨叶轴及传动装置组成,中心轴上均匀排布叶片。
我国脱硫石膏利用现状

我国脱硫石膏利用现状截至2008年年底,我国火电厂建成投产的脱硫机组容量达3.6亿千瓦,年产出脱硫石膏达4000万吨。
预计到“十一五”末,脱硫石膏年产出量将达6000万吨左右。
目前,我国脱硫石膏利用率仅为30%,大量脱硫石膏被堆放或填海,不仅占用大量土地,而且脱出来的硫又回到地面,造成二次污染。
国内外的研究和应用情况表明,脱硫石膏是天然石膏的良好替代品,可广泛用于建材、土壤改良剂或工业原料。
目前,欧美等发达国家已形成较为完善的研究、开发和应用体系。
日本脱硫石膏利用率接近100%,德国几乎所有的石膏建材企业均以脱硫石膏为原料,美国脱硫石膏年产量约1200万吨,综合利用率为75%。
与发达国家相比,我国脱硫石膏利用发展缓慢,尚未形成工业化、规模化和专业化生产。
主要存在3个方面的问题。
首先,缺少配套适用的经济技术政策。
现有脱硫石膏综合利用优惠政策力度较小,如水泥产品享受增值税即征即退的优惠范围仅限于“在生产原料中掺有不少于30%的煤矸石、石煤、粉煤灰、烧煤锅炉的炉底渣(不包括高炉水渣)及其他废渣生产的水泥”。
而脱硫石膏作为水泥调凝剂,其掺量只有3%~5%,远远达不到政策规定标准,不能享受税收优惠政策。
对于其他利用脱硫石膏生产的建材产品,也缺少相应的政策支持。
从技术政策看,脱硫石膏及生产建材产品的相关标准有待完善,缺少脱硫石膏环境污染防治技术政策和技术指南,难以从源头上控制二次污染。
其次,脱硫石膏品质达不到设计要求。
脱硫石膏要达到一定质量要求,经改性后才能满足生产建材原料的需要,提高综合利用率。
再次,电力和建材部门之间缺乏沟通与合作。
脱硫石膏的主要用途是水泥、石膏板等建材生产,属规模大、附加值低的行业,要实现较好的盈利,必须依靠大规模销量,否则难以调动企业积极性。
目前,电力和建材部门缺乏沟通与合作,电厂因技术、煤种等种种原因不太重视脱硫石膏的质量,建材部门因石膏质量难以保证,不敢依赖电厂的脱硫石膏。
脱硫石膏蒸汽二步法生产建筑石膏粉工艺简介

(3)回转式烘干机。内部按照圆周方向设置多根换热管 道,蒸汽通过换热管道,在窑体的转动下不断接触原料,热量
·102·
第 4 期(总第 216 期)
生产技术■
传递给原料,以达到烘干的目的。优点是生产能力较大,管道 基本不受其他外力作用,不易损坏,故障少,维修费用低;缺 点是投入成本高,占地面积大,物料的温度不容易控制,无搅 拌功能,原料进入设备时粘性较大,容易粘成团,使有效换热 面积变小,蒸发效率低;适用于物料粘性较低的生产线。 2.3 煅烧工序
(1)桨叶烘干机。设备内部轴上密集排列着中空桨叶,蒸 汽通过中空桨叶,使湿物料在桨叶的搅动下,与热表面充分 接触,从而与石膏换热干燥。优点是热量利用率高,设备结构 紧凑,占地面积小,投资低;缺点是浆叶在滚筒旋转时受力, 容易磨损开裂,维护维修量较大,物料粘性较强,若不及时清 理的情况,会影响干燥效果和设备干燥能力,产能较低;适用 于单体产能要求不高的生产线。
目前脱硫石膏生产建筑石膏粉主要以蒸汽、天然气、煤 等为热源。其中以煤炭为最便宜,但污染严重;天然气较清 洁,但成本较高;蒸汽清洁又经济,但周边需有供热电厂。由 于脱硫石膏主要是由电厂烟气脱硫得到的副产品,紧邻电 厂,所以主要选择蒸汽作为热源。以蒸汽为热源的生产工艺 分为一步法和二步法两类。一步法是将石膏的干燥、煅烧两 个工艺过程在一台装备中完成。该工艺生产适用于规模小、 附着水含量多在 10%以内的脱硫石膏。生产工艺流程具有简 单、热损失小、投资成本少等特点;二步法是把石膏的干燥、 煅烧两个工艺过程分别在二台装备中完成。烘干 + 煅烧的二 步法模式,对于采用蒸汽作为热源、大规模(年单机产能大于 10 万 t)及高含水量(附着水含量大于 10%)的生产线,具有较 明显的优势。以下主要对脱硫石膏蒸汽二步法生产建筑石膏 粉工艺进行简介。
浅谈我国脱硫石膏环保资源化综合利用现状

烟气脱硫石膏(简称脱硫石膏或FGD 石膏),是对火力发电厂燃煤烟气进行脱硫净化处理产生的工业副产物,其主要成分是二水硫酸钙。
正常技术条件下,火力发电厂烟气脱硫过程中,每脱除1t 二氧化硫约生成2.7t 脱硫石膏。
随着我国电厂烟气脱硫工艺的全面普及,作为工业副产物的脱硫石膏,其产量呈现逐年大幅提高的趋势。
据有关部门数据估计,2021年我国脱硫石膏产量约为1.61亿t ,而利用量约1.16亿t ,利用率仅为65%,与日本、德国、美国等国家相比较还存在很大差距。
弃置不用的脱硫石膏会占用大量土地资源,其中的有害物质会随雨水进入地下水系,极易造成土壤和水环境的污染。
国家相关部门已出台相关激励政策,促进脱硫石膏的资源化综合利用。
按照国家发改委关于“十四五”大宗固体废弃物综合利用的指导意见,国家支持利用脱硫石膏等工业副产石膏生产新型建材产品、制备石膏晶须等新材料,鼓励绿色建筑使用以脱硫石膏为原料生产的新型墙体材料、装饰装修材料,要求扩大脱硫石膏的高附加值的资源化综合利用规模。
1脱硫石膏理化性能电厂产生的原状脱硫石膏的外观颜色多呈灰色或黄色,pH 值为中性或略偏碱性,无放射性;其晶体的微观形貌多为短柱状细颗粒,晶体长径比在1.5~2.5之间;原状脱硫石膏的主要成分为二水硫酸钙,含量一般在93%以上,游离水含量一般在10%~15%范围内,所含杂质多为飞灰、有机碳、碳酸钙、亚硫酸钙及由钠、钾、镁的硫酸盐或氯化物组成的可溶性盐。
脱硫石膏是一种高纯度的工业副产石膏,其与天然石膏在物理及化学性能上存在着诸多异同之处,具体比较如下:(1)脱硫石膏与天然石膏性能上的相同点①脱硫石膏和天然石膏的主要物相组成均为二水硫酸钙,晶形转化后的五种形态(二水石膏、半水石膏、I 型硬石膏、II 型硬石膏、III 硬石膏)、七种变体(二水石膏、α半水石膏、β半水石膏、I 型硬石膏、II 型硬石膏、α-III 硬石膏、β-III 硬石膏)的理化性能相同。
安徽贵航特钢有限公司
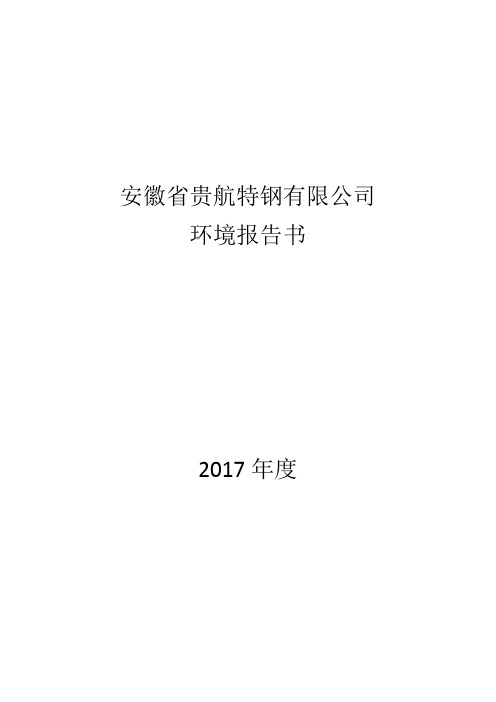
安徽省贵航特钢有限公司环境报告书2017年度一、项目基本情况安徽省贵航特钢有限公司成立于2010年4月,依托2009年底建成投产的池州市贵航金属制品有限公司,经贵池区政府招商引资,2010年4月由池州市贵航金属制品有限公司与自然人林木平、林建等人共同出资设立安徽省贵航特钢有限公司,公司位于池州市贵池区前江工业园(省级开发区)是一家从事黑色金属冶炼、高强度钢筋、抗震钢筋轧制的民营钢铁企业,法人代表林木平,公司现有资产总额约61亿元,具备年产200万吨特钢的生产能力,主要生产设备为:2台180m2烧结机、2座1080m3高炉、2台120t转炉、2条600型全连轧轧钢生产线,拥有职工2000余人,其中管理人员158人,技术人员112人。
公司于2013年11月获得钢筋混凝土用热轧钢筋生产许可证,2014年3月通过质量,环境,安全和能源管理体系认证,2014年11月入围工信部符合《钢铁行业规范条件》企业名单(第三批)。
二、环境保护基本情况公司按照《GB/T24000-IS014000环境管理系列标准》要求,建立了环境管理体系,编制了《环保制度汇编》。
公司专门成立以总经理为组长的环境保护管理领导小组,全面负责公司环境管理的领导工作。
公司下设安全环保部,负责公司日常环境保护具体工作,配备专职环保管理员14人,负责公司的环保检查、环保监测、环保设施的运行监督和环境隐患整改督査等工作,以确保公司环保体系的有效运行。
各生产单位及职能部室完全按照环境管理体系要求对生产作业进行全过程环境保护管理。
(1)废气治理公司的生产设施主要有12m2竖炉两座,180m烧结机2台,1080m高炉两座,120吨转炉两座,600轧机生产线两条,以及配套的110KV变电站,煤气发电机组。
综合原料场主要污染物为粉尘,采用挡风墙、喷水等抑尘措施。
烧结厂主要污染物为烟、粉尘、SO2,烧结机头烟气采用电除尘脱硫装置去除烟尘和SO2,烧结机尾采用电除尘收尘,烧结的配料、破碎、筛分等环节产生的粉尘由布袋除尘器收尘。
昆明市工业固体废物资源化利用工作方案
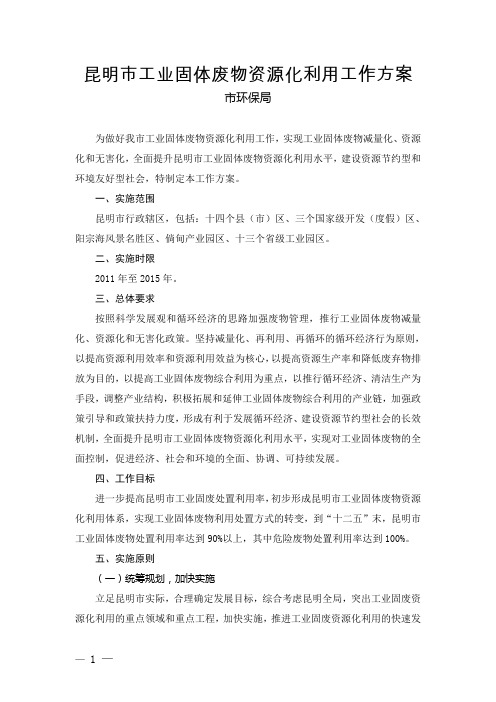
昆明市工业固体废物资源化利用工作方案市环保局为做好我市工业固体废物资源化利用工作,实现工业固体废物减量化、资源化和无害化,全面提升昆明市工业固体废物资源化利用水平,建设资源节约型和环境友好型社会,特制定本工作方案。
一、实施范围昆明市行政辖区,包括:十四个县(市)区、三个国家级开发(度假)区、阳宗海风景名胜区、倘甸产业园区、十三个省级工业园区。
二、实施时限2011年至2015年。
三、总体要求按照科学发展观和循环经济的思路加强废物管理,推行工业固体废物减量化、资源化和无害化政策。
坚持减量化、再利用、再循环的循环经济行为原则,以提高资源利用效率和资源利用效益为核心,以提高资源生产率和降低废弃物排放为目的,以提高工业固体废物综合利用为重点,以推行循环经济、清洁生产为手段,调整产业结构,积极拓展和延伸工业固体废物综合利用的产业链,加强政策引导和政策扶持力度,形成有利于发展循环经济、建设资源节约型社会的长效机制,全面提升昆明市工业固体废物资源化利用水平,实现对工业固体废物的全面控制,促进经济、社会和环境的全面、协调、可持续发展。
四、工作目标进一步提高昆明市工业固废处置利用率,初步形成昆明市工业固体废物资源化利用体系,实现工业固体废物利用处置方式的转变,到“十二五”末,昆明市工业固体废物处置利用率达到90%以上,其中危险废物处置利用率达到100%。
五、实施原则(一)统筹规划,加快实施立足昆明市实际,合理确定发展目标,综合考虑昆明全局,突出工业固废资源化利用的重点领域和重点工程,加快实施,推进工业固废资源化利用的快速发展。
(二)政府引导,企业实施按照谁产生,谁负责,谁处理的原则,产生固废的企业和单位是固废资源化利用的责任主体;充分发挥政府的组织、推动、引导、监管作用,加大公共财政投入,提供良好的政策环境和公共服务;运用市场机制,调动企业和社会力量参与的积极性,建立多元化的投融资机制和平台,有效调动社会资本参与工业固废资源化利用基础设施建设、运营、投资,培育市场主体,推动工业固废资源化利用的发展。
中国石膏工业的现状及发展方向

中国石膏工业的现状及发展方向丁大武行业现状1. 石膏矿山60年代末、70年代初,由于新型建筑材料的引进和发展,国家十分重视石膏工业的基础——石膏矿山的建设,大量投资,南京石膏矿、大汶口石膏矿、平邑石膏矿、大为石膏矿、荆门石膏矿、灵石石膏矿等大中型石膏矿山陆续建成投产。
这批石膏矿山规模较大,机械化程度较高,承担了我国石膏矿石牛产总量的40%左右。
1995年全国石膏产量1780万吨,2000年约1800万吨。
但与国外工业国家相比,有很大差距。
由于管理问题、未开发深加工产品、市场竞争及机制等原因,矿山效益不好,甚至破产。
随着国企改革、机制转换、资产重组及新品开发等一系列变革之后,石膏矿山有望获得发展。
2. 建筑石膏生产规模从年产几千吨到10~20万吨的大型自动化程度较高的生产线,从简单的β-半水石膏到几十种不同性能、多种用途的石膏胶结料。
目前,已能生产部分取代进口的模型石膏粉、自流平材料、黏结剂等高档材料,国产粉刷石膏已在北京、上海等地得到推广应用。
建筑石膏粉的产品质量有很大的提高,建筑石膏、模型石膏的国家或行业标准制定并进行了多次修订。
生产工艺由早期的先烧(脱水)后磨工艺发展到先磨后烧及脱水粉磨一体化的新工艺,生产设备也由土炒锅、小回转窑发展到大型的脱水粉磨一体化的立式磨,水泥生产中先进的旋风预热器在山东省泰和集团得到了很好的应用,节能、高效的自磨机、立式细磨机及油锅炉等先进设备也在一些企业推广应用。
3. 纸面石膏板2000年,纸面石膏生产能力已突破1亿平方米。
据不完全统计,加上外资或合资企业纸面石膏板总生产能力将达到4亿平方米。
产品质量提高,品种和功能增多,已逐步开拓国内市场,并批量出口。
纸面石膏板的成本大幅下降,纸面和石膏板的复合应用技术有了很大的进步,市场竞争能力和占有率大大提高。
值得一提的是,山东省泰和集团充分利用股份制企业优势和员工的积极性,完全依靠自己的力量改造3条年产1000万平方米的纸面石膏板生产线,扩建1条面纸生产线,兴建1条年产20万吨磷石膏生产线,有自己的改性淀粉厂、发泡剂厂、玻璃纤维加工厂等。
工信部等四部门发布《国家工业资源综合利用先进适用工艺技术设备目录(2023年版)》

工信部等四部门发布《国家工业资源综合利用先进适用工艺技术设备目录(2023年版)》近日,工业和信息化部、国家发展委、科技部、生态环境部等四部委共同发布《国家工业资源综合利用先进适用工艺技术设备目录(2023年版)》,旨在加快工业资源综合利用先进适用技术装备推广应用,持续提高资源利用效率和水平。
该目录共涉及88项工艺技术设备,包括工业固废减量化、工业固废综合利用、再生资源回收利用及再制造四个领域,数十个涉及建材行业的工艺技术设备入选。
汇总如下:1. 基于工业固废的二氧化碳矿化养护混凝土砌块工艺与装备技术装备简介:该技术使用增压的CO 对混凝土砌块进行矿化养护。
利用工业固废制CO 矿化低碳胶凝材料,并在矿化养护装备中,应用梯级均压工艺(压力范围为0.5~1MPa)生产低碳混凝土建材,实现二氧化碳封存与大宗固废处置。
关键技术:CO 矿化低碳胶凝材料技术;梯级均压矿化养护技术。
主要技术指标:CO 原料气浓度10%~100%,CO 转化利用率90%以上,产品全生命周期碳减排70%以上,原料固废利用率60%以上。
具体适用范围:CO 资源化利用;工业固废资源化利用;混凝土预制件生产。
2. 铸造粘土废砂综合利用成套技术技术装备简介:通过去除废砂表面的粘土和树脂残留物,使其性能接近新砂,同时以高性能环保硫氧镁胶凝体系为无机粘结剂,以铸造废砂再生副产物为掺合料及骨料,制备得到防火板材,实现废砂全面综合利用。
关键技术:铸造废砂微湿法再生技术;硫氧镁装饰板成型、养护、直贴三胺纸饰面技术。
主要技术指标:再生砂酸耗值≤5、含泥量≤0.3%、细粉含量≤0.6%;硫氧镁装饰板固废使用率≥40%,表面胶合强度≥1.0MPa,单位产品能耗≤3.5kgce/m。
具体适用范围:铸造废砂综合利用3. 水泥窑协同处置飞灰技术和成套装备技术装备简介:飞灰经漂洗分离获得水洗液和水洗飞灰,水洗液经水质净化和蒸发结晶处理后,制成工业盐;水洗飞灰经高温窑炉煅烧后,飞灰中的重金属固化于熟料晶格中,二噁英分解,实现飞灰无害化处置和资源化利用。
我国脱硫石膏的综合利用

我国脱硫石膏的综合利用作者:赵向鹏来源:《中小企业管理与科技·下旬刊》2016年第07期摘要:简要介绍我国脱硫石膏综合利用的主要途径,以及正在开发研究的脱硫石膏的一些其他利用途径。
关键词:脱硫石膏;石膏制品;综合利用中图分类号: X773 文献标识码: A 文章编号: 1673-1069(2016)21-180-20 引言脱硫石膏是火电厂或其他锅炉对烟气采用石灰石/石灰-石膏湿法脱硫时产生的工业副产物。
脱硫石膏为二水石膏,主要成份为二水硫酸钙。
其外观为含水率为10%~20%的潮湿松散的细小颗粒。
灰白色,颗粒集中,大部分在40~60μm之间,比表面积为45m2/kg,纯度也比较高。
杂质主要是灰尘、氧化铝和氧化硅,另有方解石或石英、氧化镁和长石等。
烟气脱硫石膏的化学成分及细度见表1、表2。
在国外,脱硫石膏主要用来生产各种建筑石膏制品和用于水泥生产的缓凝剂。
近年来,我国对脱硫石膏的预处理和深加工工艺技术装备逐步成熟,脱硫石膏的应用处在非常迅猛发展阶段。
在没有天然石膏资源但有大量脱硫石膏的长江三角洲地区,脱硫石膏的应用发展最快,上海、浙江和江苏等地有许多新建或筹建以脱硫石膏为原料的大型纸面石膏板生产线。
在一些其他地区脱硫石膏的综合利用也正在建设或者规划之中。
从已经规模化、工业化生产的工业实例来说,我国脱硫石膏综合利用主要为以下几项:1 用作水泥缓凝剂如果脱硫石膏的游离水含量低,有害杂质少,可直接用作水泥缓凝剂。
如天瑞集团汝州水泥公司使用游离水含量为4%~5%的脱硫石膏与天然石膏搭配使用,生产出的水泥在平顶山地区的房屋建筑和道路建设中得到了应用。
用户反应水泥质量稳定,富余去爱你孤独高,施工性能好。
但我国脱硫石膏的游离水含量一般在10%~20%,如果直接用作水泥缓凝剂,不仅在运输、储存过程中会出现粘结、堵料现象,而且还会造成计量不准、生产不稳定,影响水泥质量。
另外过多的水分也会影响球磨机的产量。
因此在用作水泥缓凝剂前,需要低温烘干,通过造粒将脱硫石膏制成球状。
工业副产石膏综合利用及技术开发现状
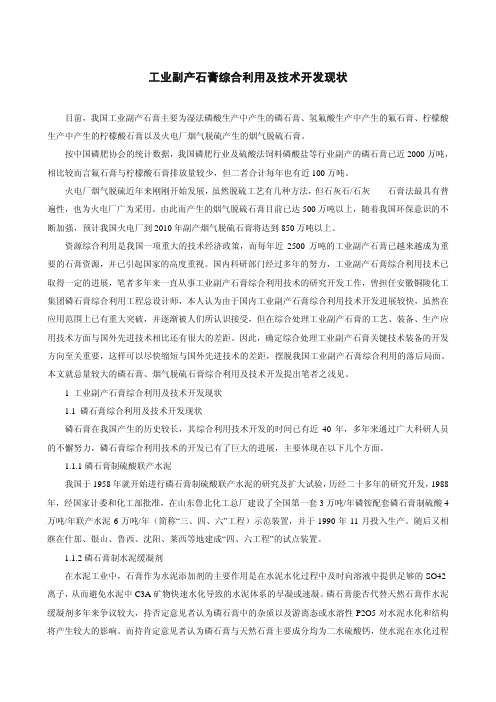
工业副产石膏综合利用及技术开发现状目前,我国工业副产石膏主要为湿法磷酸生产中产生的磷石膏、氢氟酸生产中产生的氟石膏、柠檬酸生产中产生的柠檬酸石膏以及火电厂烟气脱硫产生的烟气脱硫石膏。
按中国磷肥协会的统计数据,我国磷肥行业及硫酸法饲料磷酸盐等行业副产的磷石膏已近2000万吨,相比较而言氟石膏与柠檬酸石膏排放量较少,但二者合计每年也有近100万吨。
火电厂烟气脱硫近年来刚刚开始发展,虽然脱硫工艺有几种方法,但石灰石/石灰——石膏法最具有普遍性,也为火电厂广为采用。
由此而产生的烟气脱硫石膏目前已达500万吨以上,随着我国环保意识的不断加强,预计我国火电厂到2010年副产烟气脱硫石膏将达到850万吨以上。
资源综合利用是我国一项重大的技术经济政策,而每年近2500万吨的工业副产石膏已越来越成为重要的石膏资源,并已引起国家的高度重视。
国内科研部门经过多年的努力,工业副产石膏综合利用技术已取得一定的进展,笔者多年来一直从事工业副产石膏综合利用技术的研究开发工作,曾担任安徽铜陵化工集团磷石膏综合利用工程总设计师,本人认为由于国内工业副产石膏综合利用技术开发进展较快,虽然在应用范围上已有重大突破,并逐渐被人们所认识接受,但在综合处理工业副产石膏的工艺、装备、生产应用技术方面与国外先进技术相比还有很大的差距。
因此,确定综合处理工业副产石膏关键技术装备的开发方向至关重要,这样可以尽快缩短与国外先进技术的差距,摆脱我国工业副产石膏综合利用的落后局面。
本文就总量较大的磷石膏、烟气脱硫石膏综合利用及技术开发提出笔者之浅见。
1 工业副产石膏综合利用及技术开发现状1.1 磷石膏综合利用及技术开发现状磷石膏在我国产生的历史较长,其综合利用技术开发的时间已有近40年,多年来通过广大科研人员的不懈努力,磷石膏综合利用技术的开发已有了巨大的进展,主要体现在以下几个方面。
1.1.1磷石膏制硫酸联产水泥我国于1958年就开始进行磷石膏制硫酸联产水泥的研究及扩大试验,历经二十多年的研究开发,1988年,经国家计委和化工部批准,在山东鲁北化工总厂建设了全国第一套3万吨/年磷铵配套磷石膏制硫酸4万吨/年联产水泥6万吨/年(简称“三、四、六”工程)示范装置,并于1990年11月投入生产。
用烟气脱硫石膏制备建筑石膏的工艺技术

用烟气脱硫石膏制备建筑石膏的工艺技术【用烟气脱硫石膏制备建筑石膏的工艺技术】一、引言其实啊,在现代建筑领域,各种创新的材料和工艺层出不穷。
今天咱们就来聊聊一项挺有意思的工艺技术——用烟气脱硫石膏制备建筑石膏。
这可不是什么生僻冷门的东西,它和咱们的生活还息息相关呢!二、历史1. 起源与发展其实啊,烟气脱硫石膏制备建筑石膏这项工艺可不是凭空出现的。
早在上个世纪,随着工业的快速发展,大量的含硫废气被排放到空气中,这不仅污染了环境,还对人们的健康造成了威胁。
为了解决这个问题,科学家们就想出了烟气脱硫的办法,在这个过程中就产生了大量的副产物——烟气脱硫石膏。
刚开始的时候,这些脱硫石膏大多被当作废弃物堆积起来,不仅占用土地,还可能造成二次污染。
但是,聪明的人类怎么会让这些东西白白浪费呢?经过不断的研究和尝试,人们发现这些脱硫石膏经过一定的处理,可以变成非常有用的建筑石膏。
2. 重要的里程碑说白了就是,在这个发展过程中,有几个关键的时刻和突破。
比如说,某一年,某位科学家发现了一种特别有效的处理方法,让脱硫石膏的性能得到了极大提升;又或者是某家企业成功地大规模应用了这项技术,让建筑石膏的成本大大降低,从而推动了整个行业的发展。
三、制作过程1. 原材料的收集与预处理首先呢,得把那些烟气脱硫石膏收集起来。
这就好比是做饭前要先把食材准备好。
这些脱硫石膏可不是直接就能用的,它们里面可能会有一些杂质,比如石头、沙子啥的,得先把这些杂质给去除掉。
然后,还得对它们进行干燥处理。
想象一下,湿哒哒的衣服穿在身上不舒服,湿哒哒的石膏也没法好好发挥作用呀,所以得把它们弄干。
2. 煅烧环节接下来就是关键的煅烧步骤啦。
这就好像是把生米煮成熟饭。
把经过预处理的脱硫石膏放进煅烧炉里,用适当的温度和时间进行煅烧。
这一步可讲究了,温度高了低了,时间长了短了,都不行,得恰到好处,才能让石膏变成我们想要的样子。
3. 粉磨与陈化煅烧好的石膏还得经过粉磨,把它们变成细细的粉末。
- 1、下载文档前请自行甄别文档内容的完整性,平台不提供额外的编辑、内容补充、找答案等附加服务。
- 2、"仅部分预览"的文档,不可在线预览部分如存在完整性等问题,可反馈申请退款(可完整预览的文档不适用该条件!)。
- 3、如文档侵犯您的权益,请联系客服反馈,我们会尽快为您处理(人工客服工作时间:9:00-18:30)。
利用脱硫石膏年产30万吨建筑石膏粉生产线
工艺方案(回转烘干机+沸腾流化床)
1.工艺要求:
a.生产能力:≥42吨/小时β型半水石膏粉。
b.产品质量:按《建筑石膏》国标执行,满足纸面石膏板用粉要求。
c.环保要求:粉尘排放浓度应达到GB16297-1996标准要求。
2.工艺方案:
a.煅烧:因为脱硫石膏含有超过10%的游离水,结合国内磷石膏制备建筑石膏粉的成功经验,采用二水石膏预烘干、沸腾流化床煅烧的二步法工艺煅烧建筑石膏粉。
具体为:用装载机将原料从原料堆场送至进料斗,经计量后由皮带输送机送入双筒回转烘干机烘干去除游离水(该处热源为燃煤热风炉),出料后经集料收尘器收料,经提升输送设备送入流化床煅烧(采用导热油锅炉为热源),煅烧完毕后送入球磨机进行研磨改性和冷却,然后送入熟粉料仓备用。
b.环保:烘干、油炉、煅烧系统的烟气尾气与炒制沸腾炉的热气采用旋风(多管)加电除尘(详见工艺布置图),
3.工艺布置图:附后
4.主要设备介绍:
A、烘干系统(回转烘干机):
a、该设备采用多区段和独特的中心扬料板,可有效增加物料和热介质的接触面积,大大提高了烘干效率,起到了节能、降耗的作用。
另外因为该设备主体是建材行业标准设备,所以在技术、维修、备件维护等方面都很方便,是一台非常理想的烘干干燥设备。
b、燃烧炉:沸腾燃煤热风炉。
B、炒制沸腾炉:
沸腾炉煅烧的特点:
(1)设备小巧,生产能力大
沸腾炉生产能力的大小实质上由热源通过加热器壁传递给物料的热量多少来决定。
沸腾炉由于物料实现了彻底的流态化,因此炉内不需要安装搅拌设备。
在炉内就可以高密度地安装很多加热管,因此尺寸不大的炉子就可以有非常大的传热面积。
另外,沸腾炉采用的热源为饱和蒸气或载热油,其传热系数比热烟气为热源的传热系数高出一个数量级。
从传热方程式就可看出,由于传热系数和传热面积都较大,总传热量也就大。
(2)结构简单,不易损坏
由于物料实现了流态化,炉子就不需要有转动的部件,投产后也几乎不需要维修保养。
由于用的是低温热源,炉子在任何情况下都没有被烧坏的危险,设备使用寿命也特别长。
(3)设备紧凑,占地少
沸腾炉是立式布置的设备,设备非常紧凑。
(4)能耗较低
沸腾炉的热能消耗和电能消耗都较低。
热能方面:从热源传递给物料的热能,除了小部分用于加热炉底鼓入的冷空气以及少量的炉体散热损失外,几乎都有效地用于物料的脱水分解。
炉子本身的热效率在95%以上。
当然沸腾炉使用的是二次热源,最终的热效率还要将炉子的热效率乘上锅炉的热效率。
但蒸气锅炉或热油锅炉都是很成熟的热工设备,其热效率是比较高的。
尤其是电厂使用尾蒸汽,沸腾炉总的热效率是比较高的,采用单独的蒸气锅炉,可达57-67%;采用热油,可达67-76%。
一般的外热式煅烧设备虽然直接使用一次热源,但热效率很少超过50%。
国内沸腾炉的热耗指标为
7.7×105KJ/t建筑石膏。
电能方面:沸腾炉不需要转动,也没有搅拌机,物料主要是靠石膏脱水产生
的水蒸气来实现流态化的,需要在炉底鼓入的空气也很有限,因此鼓风机的功率也很小,因此沸腾炉的电能消耗比传统的煅烧设备少得多。
(5)操作方便,容易实现自动控制
流化床有一个特点,就是床层中同断面的物料温度基本一致。
因此操作中只要控制物料一个设定温度,就可以连续稳定地生产出合格产品。
单一的控制参数,很容易实现自动控制。
(6)产品质量好,熟石膏相组成比较理想,物理性能稳定
由于采用低温热源,石膏不易过烧,只要控制出料温度合适,成品中不含二水石膏,无水石膏Ⅲ也只在5%以内,其余均为半水石膏。
这样的相组成很理想,物理性能也很稳定。
(7)基建投资省,运行费用低
由于沸腾炉设备小巧、结构简单、占地少,因此基建投资较同等生产规模的其他类型煅烧设备节省。
投产后,由于能耗较低、维修工作量少、使用寿命长,因此运行费用也较省。
总功率:75kW
C.石膏粉的该性和冷却:
5.主要工艺设备功率:
6、电气控制系统说明
根据制粉生产线工艺特点和目前自控行业的发展趋势,该线电器控制系统采用先进的DCS控制系统(集散控制系统),主要元器件采用国际知名品牌产品,其中PLC(可编程控制器)、变频器选用德国西门子产品,并采用了PROFBUS-DP现场总线技术,将分散于各处的设备集中控制,本系统自动
化程度高,适合于制粉行业已得到广泛的推广,在整套电控系统中共设有三种操作方式,即CRT 自动操作方式、CRT手动操作方式和现场操作方式:
CRT自动操作方式:当操作控制条件和工艺设备都符合要求时在中控室发出命令,现场按照程序要求运行;
CRT 手动操作方式:人工依照工艺要求分别对工艺设备进行操作,在中控室发出命令,(如调整皮带秤流量即调整进粉量,调整温度等);
现场手动操作方式:在设备现场对设备进行操作。
采用先进的人机界面,实时监控生产情况,完善的报警程序,能在发生故障时立即通知操作人员,使维修人员及时发现问题解决问题。
6.1自动化系统的设计思想:
a.本着能集中则集中,不能集中则分散的原则,整条生产线分为集散与单机相结合的控制方式,集散控制主要负责过程控制,单机控制主要负责逻辑控制;
b.系统采用计算机分级控制,设备级的自动控制和过程的自动化级监控,后者可采用数学模型、优化分析等先进技术,建立生产过程数据库和历史数据记录,为提高生产技术创造条件;
c.系统尽可能收集更多信息,提供更多易懂、易看、易解析、易操作的画面,为有效的控制创造条件;
d.整个系统以自动操作为重点,但在设计上充分考虑CRT手动等各种后备手段以保证各种情况下生产的正常进行
2.2控制系统配置原则
a.控制系统硬件设备的性能先进、可靠。
能够满足生产线上各工艺控制,保证5年以上连续稳定运行;
b.过程级系统硬件设备和系统软件的控制功能,能够满足电仪(EIC)一体化的性能要求,管理级采用的网络设备及其通讯平台软件和人机操作接口平台软件能够实现操作监视集中化、共享化;
c.所有选定模块为集中安装式,分部式控制;
d.在使系统具有高可靠性、高稳定性、可操作性和功能完整性的同时,使系统具有方便可扩展和可维护的性能;
e.提供完整的、规范的系统设计资料(包括图纸、标准印刷品)和技术支持。
2.3应用软件设计原则要求
a. 最大程度满足工艺要求;
b. 具有较高的容错功能;
c. 具有较高的系统安全性;
d. 具有较高的可视性、可读性;
e.具有方便,快捷的可操作性;
具有完善的故障处理和报警功能。
7、现场服务、试生产指导、培训、售后服务
7.1现场服务
合同签定后,我方会派技术人员到贵厂搜寻相关技术资料带回公司以供设计之需,待按合同约定交付相关图纸后,我方会派人参与贵厂的设备招标工作和与设备厂家、土建施工单位、设备安装单位的技术交底,在合同履行过程中,我方会派驻1名工程技术人员,协助甲方作好技术层面的各项工作,善意、积极的履行合同,圆满的完成项目建设。
7.2试生产指导、培训
在设备单机试车成功完成后,我指导贵方人员进行设备的联动试车、带料试车和负责相关岗位操作工人的岗位培训工作,并提供各岗位操作规程和操作指导书,在非设备原因达产达标后,我方撤回各类人员。
7.3售后服务
我方承诺:对该项目实行终生跟踪服务,合同履行完毕后,因设计原因而出现的问题,我方接到电话后做出合理判断,48小时内到达贵方现场;随着脱硫石膏处理技术的进步出现的新技术、新工艺、新型设备改造方案,我方会在第一时间电话知会贵方,如贵方感兴趣,我们会尽快做出书面意见,提交贵厂,以供参考。
8、主要技术经济指标
利用本工艺,可达到的主要技术指标如下:
1、工作制度:300×24=7200小时
2、建筑石膏:42吨/时,年产302,400吨
3、脱硫石膏:按含水率12%计,55吨/时,年需396,000吨
4、煤:发热量按5000大卡/千克煤、
烘干煤耗为32千克/吨熟粉,煅烧煤耗为35千克/吨熟粉,
综合煤耗:2.814吨/时,日需67.536吨,年需20261吨
5、电: 综合电耗19KWh/吨熟粉,总装机功率1023Kw。
6、水:主要是风机冷却和冲洗用,可重复使用
9、基本岗位定员:8人/班,其中
送料烘干工段: 3人/班
煅烧工段: 3人/班
铲车司机: 1人/班
中控(班长): 1人/班。