LTNF常温Ni-Fe合金镀层的耐蚀原因分析
影响金属材料耐蚀性因素的研究和探讨

影响金属材料耐蚀性因素的研究和探讨摘要:金属材料对金属的发展有很重要的作用,被运用在很多的范畴。
金属材料的腐蚀是当今需要面临的一大重要难题。
无效的金属再加上装置被腐蚀而造成损耗,相当于全球大约合百分之二十的生产量。
金属材料的耐腐蚀机能,有着保护环境并且节能的作用。
本文主要对影响金属材料耐蚀性因素进行了分析研究。
关键词:金属材料;腐蚀危害;影响因素;防腐路径引言金属材料因其便利性与易得性等多种特点,被广泛应用于各个领域中,但是金属材料的易腐蚀性也同样影响到了其具体的使用效果,使得金属材料应用存在明显的局限性。
对此,可通过减少金属材料的应用,或者在应用金属材料时尽可能的避免与易产生化学反应的介质产生直接接触。
除此之外,还可以利用阴阳两极的极化作用来进行电化学腐蚀保护,提高对金属材料的保护。
这对于延长金属材料应用寿命、降低应用成本,提高应用效果都具有非常重要的现实意义。
1金属材料的腐蚀及其危害1.1金属材料的腐蚀金属材料的腐蚀是指金属材料与其周围介质接触时发生化学或电化学反应而引起的一种破坏金属材料自身的现象。
自然界中,大部分金属以其各种化合物形式存在,而金属元素的化学活性通常高于其化合物,因此这些金属会自发地演变成它们在自然界中的本身存在状态,所以金属腐蚀是自发的、普遍存在的一种现象,是不可避免的。
根据金属材料腐蚀发生的机理,通常可将腐蚀分为化学腐蚀和电化学腐蚀。
化学腐蚀是指金属材料与周围介质中存在的非电解质发生接触后,发生了氧化还原化学反应,是金属表面的原子与腐蚀介质产生直接作用而形成的腐蚀现象,如金属材料在有机溶液(芳香烃、原油等)中所发生的腐蚀。
电化学腐蚀主要是指金属材料与电解质进行接触后,金属表面与电解质溶液发生化学反应,进而形成吸氢腐蚀或析氢腐蚀的腐蚀现象,如碳钢与空气中的氧气、二氧化碳以及水等发生作用,最后变成铁锈。
1.2腐蚀的危害腐蚀会弱化金属材料的强度和机械性能,缩短其使用寿命,甚至造成金属材料无效化,造成经济损失。
金属结构材料的耐蚀性
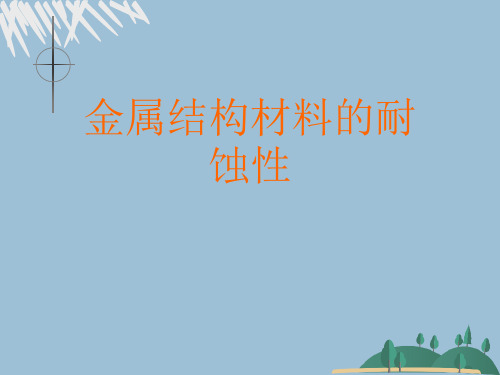
– 如果基体是阴极而第二相或合金中其它微小区域(例 如晶界)是阳极的情况下,进一步减小微阳极的面积 ,则可加大阳极极化电流密度,增加阳极极化程度
– 但是,实际合金中第二相是阳极的情况很少,绝大多 数合金中的第二相都起阴极作用(阴极相),所以, 应用这种耐蚀合金化途径的局限性很大
金属耐蚀合金化原理
金属耐蚀合金化原理
➢ 纯金属的耐蚀特性
– 金属的热力学稳定性
➢ 金属热力学稳定性的分界依据
– 当氢分压等于1atm(101325Pa)时,在中性(pH=7)水溶 液中,氢的平衡电极电位 EH2/H 0.41V4;在酸性(pH=0 )极的电水位溶分液 别中 小EH于2/H和 00时,;可在能相发应生条析件氢下腐,蚀当金属的标准电
➢ 易钝化的金属,往往作为合金元素加入钢中,使合金钝化 而获得耐蚀性
➢ 热力学不稳定的金属中,除了因钝化耐蚀外,还有因在腐 蚀过程初期或一定阶段生成致密的保护性能良好的腐蚀产 物膜耐蚀。这种化学转化膜通常为机械钝态膜
金属耐蚀合金化原理
➢ 金属耐蚀合金化的途径
– 理论依据
➢ 研究金属及其合金的耐蚀性,可从反映腐蚀速度大小的腐 蚀电流的计算式着手,寻求途径 I Ek0 EA0 PK PA R 分子是腐蚀反应的推动力,如果减少推动力,可达到防腐 蚀的目的,即设法使电极极化;分母是腐蚀反应的阻力, 如果增大阻力,也可达到防腐蚀的目的,提高耐蚀性
– 固溶处理可使阴极性杂质转入固溶体内,消除作为活 性阴极的第二相,减小阴极面积
金属耐蚀合金化原理
➢ 金属耐蚀合金化的途径
– 减弱合金的阴极活性
➢ 加入析氢超电压高的合金元素
– 往合金中加入析氢超电压高的合金元素,增大合金阴 极析氢反应的阻力,可显著降低合金在酸性介质中的 腐蚀速率。这种办法只适用于基体金属在某些介质中 不会钝化,由析氢超电压控制的析氢腐蚀过程
涂层金属的腐蚀及涂层的防护机制

涂层金属的腐蚀及涂层的防护机制发表时间:2018-03-22T16:20:24.550Z 来源:《基层建设》2017年第36期作者:许乐乐[导读] 摘要:金属材料容易被腐蚀,而涂层是有效而经济的防腐蚀方法。
中铁建电气化局集团轨道交通器材有限公司 213011摘要:金属材料容易被腐蚀,而涂层是有效而经济的防腐蚀方法。
引起金属腐蚀的因素较多,像涂层性能失效、气体污染物的侵蚀、金属沾染了可溶盐污染物质或者金属表面处理不当引起的。
涂层金属之所以老化是因为自由基原理,而金属腐蚀则是电化学反映机理。
本文主要阐述了大气环境中涂层金属的腐蚀及涂层的防护机制。
关键词:涂层金属;金属腐蚀;防护机制一.引言金属材料在大气环境中很容易被腐蚀这是一个很常识的现象。
在化学热力学原理中金属腐蚀是一种自发过程,因此要想保护金属不被腐蚀,在金属表层进行涂层是常用的方法之一。
金属涂层是一种经济有效的保护金属的材料,金属在涂层之下其电化腐蚀的几率减少,涂层阻断了金属和大气中腐蚀物质的结合来源,使得金属在涂层下保持原有的性质。
但是金属涂层的保护作用也不是万能的,军涂层金属依然有可能遭遇腐蚀,那么如何能加强有机涂层在大气环境中的防腐蚀效果,本文就金属腐蚀的规律和涂层失效的原理进行了分析和论述。
二.涂层金属腐蚀及涂层失效的机制分析(一)涂层金属腐蚀原理(二)涂层老化和失效原理金属暴露在大气中会产生腐蚀,而涂层失效的原理则是老化和失效,像一些化学成分、物理机械等外部因素的侵入都能导致金属涂层失效。
金属涂层失效会呈现出以下状态:表面色泽暗淡,颜色失真,表层碎化导致的开裂或细纹等。
导致涂层老化的原因很多,像昼夜变化引起的张力及紫外线照射等都是引起涂层老化的外界因素。
紫外线暴烈照射下的涂层其吸水率增加,暴晒后一些亲水基团会大量增加,像羟基、烷基过氧化氢、羰基等,这些都导致了涂层的吸水性增加,进而使得涂层失效引起金属腐蚀。
另外,自由基浓度也是引起金属涂层老化的一个因素。
亚磷酸体系镍磷合金电镀工艺及影响镀层耐蚀性的主因素

亚磷酸体系镍磷合金电镀工艺及影响镀层耐蚀性的主因素[摘要]为了弄清影响亚磷酸体系电镀镍磷合金层耐蚀性能的主因素,用极差法分析了各工艺参数的影响,采用SEM/EDAX考察了镍磷镀层的形貌、成分,采用电化学测试考察了镀层的耐蚀性,测定了镀层与基体的结合强度,并确定了最佳工艺条件。
结果表明:亚磷酸含量是影响镀层耐蚀性的主要因素,在240 g/L硫酸镍,45 g/L 氯化镍,30 g/L硼酸,30 g/L亚磷酸,电流密度5 A/dm2,温度40℃条件下所得镀层均匀,耐蚀性和结合力好。
[关键词]电沉积;镍磷合金;亚磷酸体系;耐蚀性能;影响因素[中图分类号]TQ153.2[文献标识码]A[文章编号]1001-1560(2011)07-0064-030·前言镍磷合金镀层耐腐蚀、耐高温、耐磨,导电性和导磁性高,原料成本低,环保性能好,在汽车、航空航天、电子、通讯等行业得到了广泛应用。
获得镍磷合金镀层的主要途径包括化学镀和电镀。
其中在沉积速率、镀液稳定性、成本、最大厚度等诸多方面,电镀法具有化学镀法不具备的优点[1~7]。
目前,电镀镍磷合金工艺和性能的报道较化学镀少,进一步了解电镀工艺参数对镀层耐蚀性的影响对于扩大电镀镍磷的应用范围很有意义。
次磷酸盐体系镍磷合金电镀层质量不稳定,温度及电流稍有变化就容易引起镀层发黑[8,9]。
本工作采用电镀方法,在亚磷酸镍盐体系中获取了镍磷合金镀层;通过正交试验优选了可获得耐蚀性好的镀层的工艺参数,并探讨了各参数对镀层耐蚀性的影响。
1·试验1.1基材前处理以纯铜片为基材,尺寸10 mm×10 mm×1 mm,用环氧树脂封装,留出施镀的面积为1 cm2。
镀前处理流程:基材磨光→水洗→除油→水洗→酸洗→水洗。
用800号水砂纸打磨基材试样至平整光滑后除油。
除油60~100 g/L Na2CO3,5~10 g/L Na3PO4·12H2O,5~15 g/L Na2SiO3,1~3 g/L OP-10乳化剂,温度80~90℃,至将油除净为止。
热处理对Ni-P化学镀层阻垢和耐蚀性能的影响 (1)
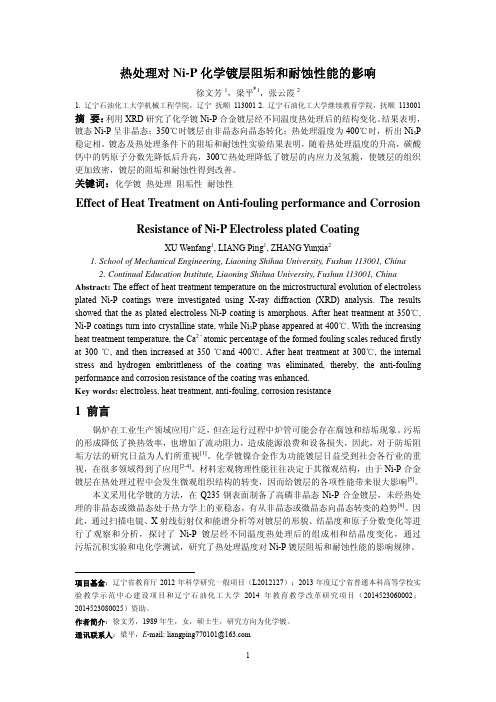
Intensity /a.u
300℃
400
200
镀态
0 10 20 30 40 50 60 70 80 90
2/ degree
图 4 污垢的 X 射线衍射图 Fig. 4 XRD patterns of fouling
4
3.4
热处理后 Ni-P 镀层的耐蚀性能变化
图 6 为镀态和经不同温度热处理后的 Ni-P 镀层试样在通入 CO2 气体的氢氧化钙溶液中 的阻抗图谱。可以看出,在交流阻抗图上只有一个容抗弧[10],随着热处理温度的升高,合 金镀层的容抗弧半径变化明显,说明热处理对合金镀层的耐腐蚀性能影响较大。 采用等效电路图对阻抗图谱进行数值拟合,镀态下 Ni-P 镀层电荷转移电阻 Rct 为 7400 Ω • cm2。300℃热处理后镀层 Rct 为 26290 Ω • cm2,是镀态下的 3.5 倍,表明其耐蚀性得到 很大改善,XRD 分析表明,此时的镀层仍为非晶结构,由于应力的释放和 H 的去除,镀层 的组织更加致密,使镀层的耐蚀性得到较大的提高[11]。350℃热处理后出现了晶界和位错等 缺陷,而且由于形成了 Ni2P 过渡相,使合金镍相中 P 含量降低,使原来的非晶态单相均匀 组织变化为 Ni 和镍磷化合物的混合组织,减少了富磷钝化膜的形成[12]。400℃热处理后镀 层中析出稳定相 Ni3P,Ni3P 在腐蚀原电池中是阴极,Ni 固溶体是阳极,因此,Ni3P 的析出 及其面积增大加速了镀层腐蚀,导致其耐蚀性低于镀态。 耐蚀性随热处理温度先提高后降低,耐蚀性与阻垢性能一致,由文献[13]可知,被腐蚀 的表面易于形成连接污垢与基体的“过渡界面”,有利于污垢离子的附着和沉淀,导致阻垢性 能降低。
1 前言
锅炉在工业生产领域应用广泛, 但在运行过程中炉管可能会存在腐蚀和结垢现象。 污垢 的形成降低了换热效率,也增加了流动阻力,造成能源浪费和设备损失,因此,对于防垢阻 垢方法的研究日益为人们所重视[1]。化学镀镍合金作为功能镀层日益受到社会各行业的重 视,在很多领域得到了应用[2-4]。材料宏观物理性能往往决定于其微观结构,由于 Ni-P 合金 镀层在热处理过程中会发生微观组织结构的转变,因而给镀层的各项性能带来很大影响[5]。 本文采用化学镀的方法,在 Q235 钢表面制备了高磷非晶态 Ni-P 合金镀层,未经热处 理的非晶态或微晶态处于热力学上的亚稳态,有从非晶态或微晶态向晶态转变的趋势[6]。因 此,通过扫描电镜、X 射线衍射仪和能谱分析等对镀层的形貌、结晶度和原子分数变化等进 行了观察和分析,探讨了 Ni-P 镀层经不同温度热处理后的组成相和结晶度变化,通过 污垢沉积实验和电化学测试,研究了热处理温度对 Ni-P 镀层阻垢和耐蚀性能的影响规律。
如何改善化学镀镍的耐腐蚀性能
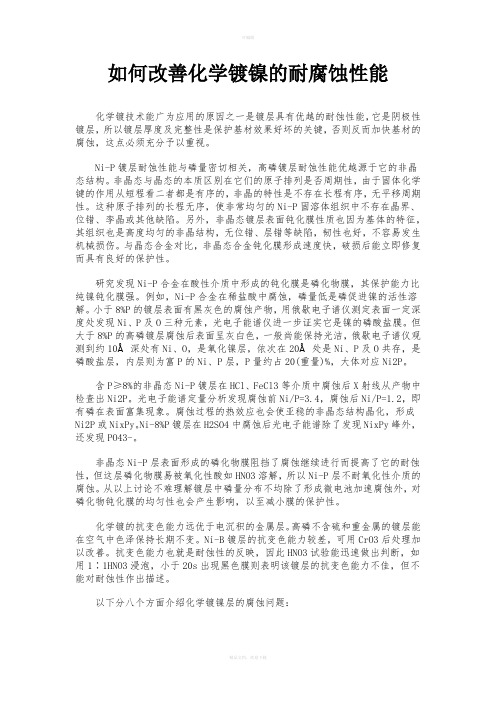
如何改善化学镀镍的耐腐蚀性能化学镀技术能广为应用的原因之一是镀层具有优越的耐蚀性能,它是阴极性镀层,所以镀层厚度及完整性是保护基材效果好坏的关键,否则反而加快基材的腐蚀,这点必须充分予以重视。
Ni-P镀层耐蚀性能与磷量密切相关,高磷镀层耐蚀性能优越源于它的非晶态结构。
非晶态与晶态的本质区别在它们的原子排列是否周期性,由于固体化学键的作用从短程看二者都是有序的,非晶的特性是不存在长程有序,无平移周期性。
这种原子排列的长程无序,使非常均匀的Ni-P固溶体组织中不存在晶界、位错、孪晶或其他缺陷。
另外,非晶态镀层表面钝化膜性质也因为基体的特征,其组织也是高度均匀的非晶结构,无位错、层错等缺陷,韧性也好,不容易发生机械损伤。
与晶态合金对比,非晶态合金钝化膜形成速度快,破损后能立即修复而具有良好的保护性。
研究发现Ni-P合金在酸性介质中形成的钝化膜是磷化物膜,其保护能力比纯镍钝化膜强。
例如,Ni-P合金在稀盐酸中腐蚀,磷量低是磷促进镍的活性溶解。
小于8%P的镀层表面有黑灰色的腐蚀产物,用俄歇电子谱仪测定表面一定深度处发现Ni、P及O三种元素,光电子能谱仪进一步证实它是镍的磷酸盐膜。
但大于8%P的高磷镀层腐蚀后表面呈灰白色,一般尚能保持光洁,俄歇电子谱仪观测到约10Å深处有Ni、O,是氧化镍层,依次在20Å处是Ni、P及O共存,是磷酸盐层,内层则为富P的Ni、P层,P量约占20(重量)%,大体对应Ni2P。
含P≥8%的非晶态Ni-P镀层在HCl、FeCl3等介质中腐蚀后X射线从产物中检查出Ni2P。
光电子能谱定量分析发现腐蚀前Ni/P=3.4,腐蚀后Ni/P=1.2,即有磷在表面富集现象。
腐蚀过程的热效应也会使亚稳的非晶态结构晶化,形成Ni2P或NixPy。
Ni-8%P镀层在H2SO4中腐蚀后光电子能谱除了发现NixPy峰外,还发现PO43-。
非晶态Ni-P层表面形成的磷化物膜阻挡了腐蚀继续进行而提高了它的耐蚀性,但这层磷化物膜易被氧化性酸如HNO3溶解,所以Ni-P层不耐氧化性介质的腐蚀。
铝上化学镀镍层耐蚀性研究

摘要 :采用中性盐雾腐蚀试验方法对铝上化学镀镍层的耐蚀性进行了研究 ,重点比较和讨论了 镀层厚度和镀层含磷量以及镀覆工艺对化学镀 Ni - P 合金层耐蚀性的影响 。
关键词 :铝 ;化学镀镍 ;耐蚀性 中图分类号 : TG42 文献标识码 :A 文章编号 :1001 - 3474 (2003) 06 - 0254 - 03
层腐蚀后的电镀试样的评级 。
解质 ,将沿着表面孔隙渗进内层 ,发生纵向微电池腐
2 结果与讨论
蚀 ,内层为阳极 ,形成针状孔蚀点 。另外 ,有作者对
2. 1 在相同厚度 (22μm~25μm) 条件下 ,高磷化学 Ni - P 镀层表面的不均匀胞状凸起物采用电子探针
镀镍层 (1 组 、2 组) 的耐盐雾腐蚀的能力明显优于中 研究后发现 ,凸起物中心磷含量略高于边缘部位 ,由
表 1 试验结果 ,说明厚度为 25 μm 的铝上高磷 化学镀镍层 (1 、2 组) 和 25μm 铝上中磷化学镀镍层 + 化学钝化 (5 、6 组) 能满足 MIL - C - 26074E 要求 。 而厚度为 25μm 的钢上中磷化学镀镍层 (9 组) 能满 足 AMS2404D 要求 。 2. 3 铝上中磷化学镀镍层经化学钝化处理后 (5 、6 组) ,其耐盐雾腐蚀的能力明显高于相同厚度的普通 中磷化学镀镍层 (3 、4 组) ,并可以和相同厚度的高 磷化学镀镍层 (1 、2 组) 相媲美 。同样 , (8) 组耐盐雾 腐蚀能力也优于 (7) 组 。由于铝上化学镀镍层属于
电沉积Ni-Fe合金工艺及镀层耐蚀性的研究

性 ; 张郁 彬 等 研 究 表 明 , 3 5 氯 化 钠 溶 液 在 .% 中 , 着 镍一 合 金 中 铁 含 量 的 升 高 , 粒 细 化 , 随 铁 晶 ( e 为 3 % 的镍 . 合 金 耐 蚀 性 最 佳 , 以在 防 F) 6 铁 可
hg e tc ro in r ssa c . ih s o r so e itn e
Ke wor y ds:NiFe a ly c ai g;ee to e o i o — lo o tn l cr d p st n;c ro in r ssa c i o so e it n e
引 言
N .e合金 具 有 不 同 于单 质 铁 、 金 属 粉 末 的 i F 镍 特殊 性能 和 软 磁 性 , 吸 波 材 料 、 性 材 料 及 硬 质 在 磁 合金 等领 域 具 有 广 泛 的 应 用 前 景 , 合 金 镀 层 其 不但 具有 优 良的焊 接 性 , 可 作 为 纯 镍 镀 层 的替 代 还
中 图分类 号 : Q 5 . T 132
文献标 识 码 : A
Elc r d p st0 c n l g n r o i n Re it n e o e t 0 e 0 ii n Te h o o y a d Co r so ssa c f
NiFe Al y Co tn — l a ig o C E G H a U o gxa WA u ,WA G C e A G Y nh i H N u ,G O H n —i , NG Q n N h ,T N u —u
采 用 L 2 0 A电化学 工作 站 ( 津兰力 科 化 学 K 05 天 电子 高技术公 司 ) 测定 所 制 备 的 N—e 金 镀 层 在 i 合 F
腐蚀与防护-第十二章 金属及其合金的耐蚀性

铁和铁基合金的耐蚀性
(1)钢铁的基本知识
• 纯铁的同素异构转变 • 铁碳相图
(2)铁基合金的耐蚀性
纯铁及其同位素转变
1538
液态
纯铁的同素异构转变
温度/℃
1394
δ-Fe 体心 立方
金属的多晶型性(同素异构现象)
多晶型性转变(同素异构转变)
纯铁的同素异构转变 δ-Fe
1394 ℃
γ-Fe 面心立方 912 770 无磁性的 α-Fe 体心立方 有磁性的 α-Fe 体心立方 0 时间/min
性能:σ b≈750MPa
40J/cm
2
HBS=180
δ ≈20%~25%
ak=30~
综合性能
莱氏体
定义:A与 Fe3C 所形成的机械混合物(平均含碳量:4.3%)
性能:硬而脆
马氏体
• 碳在α—Fe中的过饱和固溶 • 钢经淬火所得高硬度相 • 在Fe—Ni、Fe—Mn合金以及许多有色金属 及合金中也发现了马氏体转变 • 马氏体转变时能在预先磨光的试样表面上 形成有规则的表面浮凸
铁素体(F或α)
定义:碳溶于α-Fe中所形成的间隙固溶体 晶格结构:bcc 最大溶解度:0.02%(727℃)
性能: σ b=180~230MPa σ δ =30%~50%
ψ =70%~80%
ak=160~200J/cm
δ-铁素体:碳溶于δ-Fe中所形成的间隙固溶体,最大溶解度:
(2)自钝性
• 在热力学不稳定的金属中,有不少金属在适宜的 条件下,由活化态转为钝化态而耐蚀。
• 最容易钝化的金属有Zr、Ti、Ta、Nb、Al、Cr、 Be、Mo、Mg、Ni、Co等。 • 多数可钝化的金属都是在氧化性介质中易钝化, 如在HNO3及强烈通空气中的溶液; • 当介质中含有活性离子( Cl-、Br-、F-)时,以及 在还原性介质中大部分金属的钝态会受到破坏。
铝合金耐蚀性的研究

氯离子破坏表面氧化膜后到达基体,产生腐蚀,常见的腐蚀 类型包括点蚀、晶间腐蚀等。 2.2.1 点蚀
提高工业纯铝的耐蚀性,一方面需要从它的表面氧化膜入 手,铝及铝合金在空气中都会被氧化形成一层致密的氧化薄膜, 但是氯离子的存在对自然形成的氧化膜威胁很大,自然形成的 氧化薄膜很容易被氯离子穿透,造成腐蚀。
根据文献表明 [10] 氯离子并不是均匀渗透膜的表面,而是选 择性渗透。选择性渗透是由于钝化膜的固有非均质微观结构引 起的,并取决于沿纳米晶体 / 非晶界面形成的路径的性质和路 径之间的相互联系。当一条连接的路径横穿钝化膜的整个厚度 时,通过这些路径隧穿的氯离子最终将到达基质 / 钝化膜的界 面。当不存在任何连接路径或所有路径都被缩短的情况下,氯离 子无法通过,因此基质 / 钝化膜的界面将不受干扰。我们可以从 这个方面入手,如何阻止或者破坏这个特殊的晶界,减少氯离子 的输送通道,从而保护金属材料。换句话说,我们想要形成一个 具有完全无定形结构的氧化膜,以便没有用于物种扩散和运输 的隧道。
点蚀是指铝合金暴露在海洋大气环境中受海水中氯离子的 侵蚀在铝合金表面产生的点状、孔状的一种腐蚀形态。氯离子使 表面氧化膜局部被破坏,在氧化膜破口处金属表面氧化膜与内 层的金属具有电位差,产生电流,并且金属的电位高,成为阳极, 所以腐蚀可以快速的向内部的金属扩展,形成蚀孔。铝合金发生 点蚀的部位会生成白色粉末状物质覆盖,对铝合金基体有保护 作用。 2.2.2 晶间腐蚀
金属防腐的影响因素

金属防腐的影响因素一般讲,金属的腐蚀是多种因素共同作用的结果,而其中某种因素在腐蚀过程中起着重要的作用。
金属表面喷漆形成涂装保护层,其金属发生腐蚀的区域是在涂装漆膜与金属表面的界面区域,并不断向金属基体深处侵蚀扩张。
金属的防腐蚀过程目前分为三大类:金属的阳极保护;金属的阴极保护;以及金属表面的非金属涂装保护。
金属的阳极保护是指在某种金属表面镀覆一种电极电位较低的金属材料,在腐蚀环境中电位较低的金属材料首先被腐蚀而起到一种保护作用(如:钢铁表面镀覆金属锌);金属的阴极保护是指在金属表面镀覆一种电位较高的耐腐蚀金属材料,在腐蚀环境中将低电位金属完全包覆,把低电位金属与腐蚀性物质隔绝开来(如:钢铁表面镀铜);喷漆涂装金属腐蚀因素分析和预防的方法1金属材质等因素的影响喷漆涂装金属的腐蚀与金属材质本身耐蚀性有很大关系。
用于以喷漆涂装的金属有钢铁材料,铝合金,铜合金或镁合金等,无疑金属材质的不同,金属喷漆涂装的抗蚀防腐性能也不尽相同。
金属材料表面状态的差异,经喷漆涂装,其涂层的防腐抗蚀保护效果有明显的不同。
比如将经喷砂净化处理的钢板材零件和自然锈蚀的同牌号钢板零件进行同类喷漆涂装保护,由于锈蚀的不利影响,天然锈蚀钢板零件较经喷砂的钢板零件其腐蚀速率高出数十倍,其抗蚀防护效果明显低于后者。
金属表面所存在的缺陷如夹杂、微裂、应力等和大气中水分及活性离子(Cl-、Br-等)的吸附都会不同程度地影响甚至加速喷漆涂装金属的腐蚀。
金属表面喷漆涂装前的净化脱脂,活化除锈等前处理及表面处理工艺的应用都可以有效地改善喷漆涂装金属的防腐抗蚀性能。
生产实践证明喷漆涂装金属防腐性的优劣与其涂装前基体前处理质量的好坏影响极大,金属(尤其是铸件)表面涂装前所进行的有效除油脱脂,除锈或采用喷砂喷丸等可以引起净化活化表面,保证涂装漆膜与基体金属良好的结合力,对提高喷漆涂装金属的耐腐蚀性能是十分有益的。
钢铁材料涂装前处理工序的磷化处理是广泛地做为喷漆涂装的底层,对提高涂装层附着力和提高涂装金属的防腐抗蚀性能是无可非议的。
镍基合金的耐蚀性
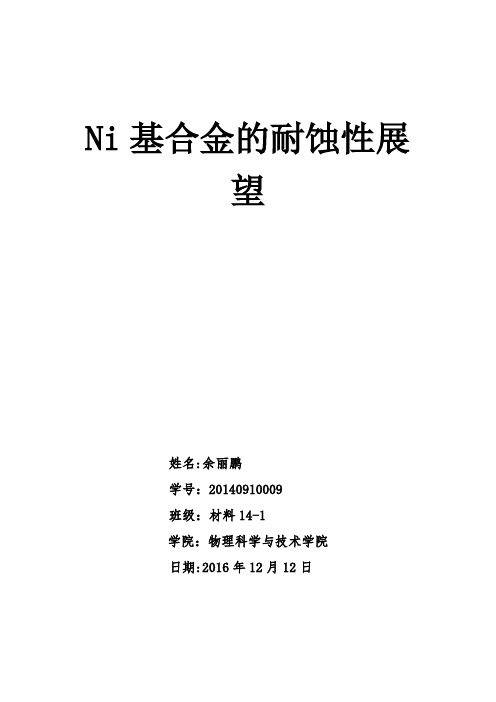
Ni基合金的耐蚀性展望姓名:余丽鹏学号:20140910009班级:材料14-1学院:物理科学与技术学院日期:2016年12月12日摘要:在我们的生产生活中镍基合金对腐蚀性环境具有有效的抵抗能力,基于防腐蚀问题,镍基合金的介绍,,镍合金的化学成分,各类镍合金耐腐蚀性能,及与其它材料耐腐蚀性能的比较,对不同环境选用不同镍合金提出了建议。
一.腐蚀对经济社会的影响例1.2006年3月某核电站土建处执行设备腐蚀状态检查时发现,除盐水分配系统除盐水箱的地脚螺栓出现严重的腐蚀,锈蚀掉已接近的1/3,地脚螺栓腐蚀与地面接触腐蚀若进一步加剧,则影响设备的稳定性和抗震性,带来严重的安全隐患,将会影响电站的安全运行。
例2.2010年7月22日上午,贵州某化工厂车间工作人员发现变换工段管道有泄漏现象,随后组织公司安全检修人员到现场查看,并制定处理方案,之后不久,变换系统副线管道泄漏气体处突然发生空间爆炸,造成现场5人死亡、6人受伤,预计经济损失约500万元。
腐蚀带来的危害是多方面的,而大部分腐蚀是从渐变到突变,是“慢性病”,不易引起人们的重视,等积累到一定程度成为破坏性突发事故,才引起人们的关注。
以上少数案例提醒我们腐蚀问题不容人们忽视。
2003年出版的《中国腐蚀调查报告》中指出:中国的腐蚀损失占GDP的5%(加上间接损失2001年约为5000亿人民币),2012年我国GDP为519,322亿人民币,以此计算腐蚀造成的损失25,966亿元人民币。
据世界腐蚀组织(WCO)在《对于材料破坏和腐蚀控制世界必须进行知识传播与研究发展》的《白皮书》中指出:“在全世界,腐蚀对经济和环境的破坏方面(包括公路、桥梁、油气设施、建筑、水系统等)。
目前,世界年腐蚀损失可达1.8万亿美元”,约合人民币11万亿元。
腐蚀给人类带来的损失是很大的,据有关资料统计,世界上每年因腐蚀而报废的金属材料和设备约相当于生产量的20%以上,在受力情况下钢结构被腐蚀后,若腐蚀1%,其强度下降10~15%。
含硫介质中化学镀Ni-P合金镀层耐蚀性研究

定稿日期:2005210225基金项目:陕西省教育厅基金项目“高硫原油炼制设备的腐蚀与防护”(02jc15)作者简介:冯拉俊,1957年生,男,博士,教授,研究方向为金属的腐蚀与防护含硫介质中化学镀Ni -P 合金镀层耐蚀性研究冯拉俊 马小菊 雷阿利(西安理工大学材料科学与工程学院西安710048)摘要:用场发射扫描电子显微镜、X 射线光电子能谱仪及X 射线衍射仪分析Ni -P 合金镀层表面的形貌、组成及结构,用恒电位极化曲线法研究了Ni -P 合金镀层在Na 2S 溶液中的腐蚀行为,通过重量法测试了Ni -P 合金镀层在不同温度、不同质量分数Na 2S 溶液中的腐蚀速率.结果表明:Ni -P 合金镀层为非晶态镀层,表面具有胞状结构;在Na 2S 质量分数一定的条件下,Ni -P 合金镀层腐蚀的阳极过程随着温度的升高,钝化区域逐渐变窄.关键词:化学镀 镍磷合金 非晶态 腐蚀速率中图分类号:TG 146 文献标识码:A 文章编号:100524537(2006)03201572031前言近年来,我国从中东地区进口大量原油,进口原油中硫含量高达210%[1],在运输、贮存、加工过程中对原有的碳钢设备造成严重的腐蚀.化学镀Ni -P 合金镀层具有较高的硬度、较好的耐磨性和耐蚀性,并且化学镀设备简单,成本低廉,目前广泛地应用于电子、石油、化工、机械、宇航及原子能等工业[2].因此,研究化学镀Ni -P 合金镀层在含硫介质中的耐蚀性有较大的现实意义和使用价值.针对这一实际,本文主要研究化学镀Ni -P 合金镀层在含硫介质中的耐蚀性,为化学镀镍磷合金镀层在防止硫腐蚀方面的应用提供理论依据.2试验方法采用Φ34mm ×5mm 的45#钢作为本实验的基体材料.为了防止Ni -P 合金镀层在含硫介质中发生孔蚀,要求镀层的孔隙率为零,并且具有较好的耐蚀性和均匀性,根据这一要求,经过正交实验筛选,得出无孔隙镀层的化学镀工艺如下:NiSO 4・6H 2O 25g/L ,NaH 2PO 2・H 2O 30g/L ,加速剂15g/L ,NaAc 5g/L ,p H 值为4~5,温度为88℃~92℃,施镀时间为3h ,装载量1dm 2/L.化学镀工艺:化学除油—水漂洗—盐酸活化—去离子水清洗—非晶态镀膜—冷水清洗—后处理—风干.用AXISUL TRA X 射线光电子能谱仪测定镀层磷含量.用J SM -6700F 场发射扫描电子显微镜观察表面形貌,XRD -7000S 型X 射线衍射仪分析镀层结构,试验采用Cu 靶.将制备好的试样与一根导线连接,在试样表面留出1cm 2作为研究面,其余部分用环氧树脂密封.硫腐蚀在低温下主要发生电化学腐蚀,在低温轻油中腐蚀主要由S 2-引起[3,4].本文主要研究的是低温条件下,硫含量及温度对化学镀Ni -P 合金镀层腐蚀性的影响,因此实验溶液由Na 2S ・9H 2O (分析纯)与蒸馏水配制而成.动电位扫描极化曲线测定采用三电极体系,以铂电极为辅助电极,饱和甘汞电极为参比电极.动电位扫描装置由GX -1给定信号发生器、HDV -7C 恒电位仪、LM20A -200X -Y 记录仪组成.测定自腐蚀电位的时间为15min ~20min ,扫描速率为2mV/s.温度控制采用D K -98-I 电子恒温水浴锅.文中电极电位均相对于饱和甘汞电极电位.腐蚀速率测定采用重量法,根据腐蚀前后试样质量的变化计算出腐蚀速率.3结果与讨论311Ni -P 合金镀层表面形貌分析图1为含11198mass %P 的合金镀层的表面形貌.可知,表面具有许多大小不一的胞状物,这是由于基体材料上的位错、露头、气孔、裂纹和划痕等会成为Ni -P 合金的沉积中心,先以这些中心开始沉积,然后逐渐外延分层长大,随着镀层的生长和增厚,逐渐长成了具有圆丘状的外形,即表面形成许多胞状物[5].还可知,Ni -P 合金镀层并没有形成一个很平整的表面,这是由基体加工较为粗糙所致.图2为含11198mass %P 镀层的X 射线衍射图.可知,Ni -P第26卷第3期2006年6月 中国腐蚀与防护学报Journal of Chinese Society for Corrosion and Protection Vol 126No 13J un 12006合金镀层为典型的非晶态结构,通常非晶态合金是单相体系,具有均匀的结构,原子间呈短程有序结构,不存在成分偏析、夹杂和第二相,也就不存在晶界和位错等缺陷[6,7],因此具有较好的化学和电化学均匀性,具有非常高的耐蚀性.312Ni-P镀层在N a2S溶液中的耐蚀性31211N a2S含量对Ni-P镀层极化行为的影响 图3是20℃、Na2S(mass%)分别为110%、115%、210%、215%的介质中Ni-P镀层的极化曲线.可知,随着Na2S含量的增加,极化曲线右移,腐蚀电流增加,在阳极极化区出现钝化现象.当电压增加到-012V附近时,腐蚀电流开始减小,电压增加到0V左右,若继续增加,电流基本不变化,出现稳态钝化区,表明电压增加到一定值时,在Ni-P镀层表面形成钝化态.Na2S含量的增加加速了腐蚀反应的阴极过程,可以认为Ni-P镀层在Na2S介质中的腐蚀为阴极极化控制的腐蚀过程.31212温度对Ni-P镀层极化行为的影响 图4为215mass%Na2S、温度为20℃、40℃、60℃、80℃时Ni-P镀层的极化曲线.可知,随着温度的升高,腐蚀电流增大.在阳极极化区发现:当温度为20℃、40℃时,阳极极化区出现钝化,钝化区域随温度升高而变窄.这主要是由于温度升高,腐蚀速度提高,阳极腐蚀产生的金属离子与S2-结合,在金属表面生成钝化膜.当温度升高到60℃、80℃时,阳极极化曲线明显右移,腐蚀电流增加,腐蚀加速.阳极极化曲线告知,在60℃、80℃时钝化现象不明显,这是因为温度较高情况下,介质的电导率升高, O2和S2-的扩散加速,使得金属表面的溶解速度加快,加速了腐蚀.31213Ni-P镀层腐蚀速率测定 利用重量法测定不同温度、不同质量分数Na2S溶液中Ni-P镀层的腐蚀速率见图5.可见,20℃条件下Ni-P合金镀层的腐蚀速率在整个实验过程中变化不大,是非常耐Na2S腐蚀的材料.在60℃、80℃条件下,随着Na2S质量分数的增加,Ni-P合金镀层的腐蚀速率出现先降低后升高的变化趋势,这主要是由于在Na2S<115mass%的范围内,Na2S质量分数的增加加速了Ni-P合金镀层钝化膜的形成,当Na2S达到115mass%后继续增加,沉积的膜开裂,使得沉积851中国腐蚀与防护学报第26卷Fig.5Corrosion rates of Ni -P coatings in Na 2S solution at dif 2ferent temperatures and mass percent for 240h (corrosion time is 1512h at 20℃)膜保护作用减弱,腐蚀速率反而上升.即使在温度为80℃,Na 2S 含量为215mass %条件下,Ni -P 合金镀层的腐蚀速率仍在10-3g/(m 2・h )数量级范围,属于非常耐蚀的材料.4结论(1)在本文制定的化学Ni -P 镀工艺配方条件下制备的化学镀层,磷含量为11198%,镀层为非晶态镀层,表面具有胞状物结构.(2)Ni -P 镀层在Na 2S 溶液中的腐蚀属于阴极极化控制的电化学过程.室温条件下,当阳极电位大于-012V (相对于饱和甘汞电极)时,阳极出现钝化现象.温度升高,致钝电流减小,自腐蚀电位降低,钝化区域变窄.(3)Na 2S 含量小于215mass %时,随着温度升高,镀层的腐蚀速率增加,但在80℃时该镀层的腐蚀速率仍在10-3g/(m 2・h )数量级范围内,属于非常耐蚀的材料.参考文献:[1]Bu Q M ,Wen L ,Jiang H ,et al.On high sulfur crude oil induced cor 2rosion of processing equipment and countermeasures[J ].Corr.Sci.Prot.Technol.,2002,14(6):362-364(卜全民,温力,姜虹等.炼制高硫原油对设备的腐蚀与安全对策[J ].腐蚀科学与防护技术,2002,14(6):362-364)[2]Jiang X X ,Shen W.The Fundamental and Practice of ElectrolessPlating[M ].Beijing :Defence Industry Press ,2000,6:1-4(姜晓霞,沈伟.化学镀理论及实践[M ].北京:国防工业出版社,2000,6:1-4)[3]Zhou P R ,Jia P L ,Xu S Q ,et al.C orrosion protection technologies inprocessing crude oils[J ].T otal C orrosion C ontrol ,2003,17(3):1-7(周培荣,贾鹏林,许适群等.加工高硫原油与高酸原油的防腐蚀技术[J ].全面腐蚀控制,2003,17(3):1-7)[4]Huang L P.A tentative analysis of sulfide corrosion and protectingtechnology during processing sour crude oil[J ].Jinshan Oil Chemical Fiber ,2002,21(1):45-50(黄丽萍.含硫原油加工中的硫化物腐蚀与防护技术探悉[J ].金山油化纤,2002,21(1):45-50)[5]Yu Y ,Xu G Y ,Huang H.Study on the structure and property of Ni-P alloy layer by chemical plating[J ].Journal of Liaoning Normal University (Natural Science ),1998,21(1):58-61(于媛,徐桂英,黄虹.化学镀Ni -P 合金层组织结构与性能的研究[J ].辽宁师范大学学报(自然科学版),1998,21(1):58-61)[6]Hu W b ,Liu L ,Wu Y T.Electroless Plating Ni Technology of Diffi 2cult Plating Materials[M ].Beijing :Chemical Industry Press ,2003,7:9-11(胡文彬,刘磊,仵亚婷编.难镀基材的化学镀镍技术[M ].北京:化学工业出版社,2003,7:9-11)[7]Y an H.The New T echnology of Present E lectroless Plating Ni and C om 2posite Plating[M].Beijing :Defence Industry Press ,1999,10-16(闫洪编著.现代化学镀镍和复合镀新技术[M ].北京:国防工业出版社,1999,10-16)CORR OSION RESISTANCE OF E L ECTR OL ESS PLATINGNi -P ALLOY COATING IN SU LFUR -BEARING SOL UTIONFEN G Lajun ,MA Xiaoju ,L EI Ali(School of M aterials Science and Engineering ,Xi ’an U niversity of Technology ,Xi ’an 710048)Abstract :Surface morphologies ,ingredients and structure of electroless plating Ni -P alloy coatings were inves 2tigated using field emission scanning electron microscope ,X -ray photoelectron spectrometer and X -ray diffrac 2tion instrument ,the corrosion behavior of Ni -P alloy coatings in Na 2S solution was studied by potentiostatic po 2larization method and the corrosion rate of Ni -P alloy coatings was measured in different concentration of Na 2S solutions at different temperatures by gravimetric method.Experiment results indicate that the amorphous Ni -P plating is deposited with cellular structure on the surface.In the same concentration of Na 2S solution ,the passiva 2tion area of the anodic process of corrosion reaction of the Ni -P alloy coatings narrowed gradually with increas 2ing temperature.K ey w ords :electroless ,Ni -P alloy ,amorphous ,corrosion rate9513期冯拉俊等:含硫介质中化学镀Ni -P 合金镀层耐蚀性研究 。
镍磷化学镀层的耐蚀性及其与磷含量的关系
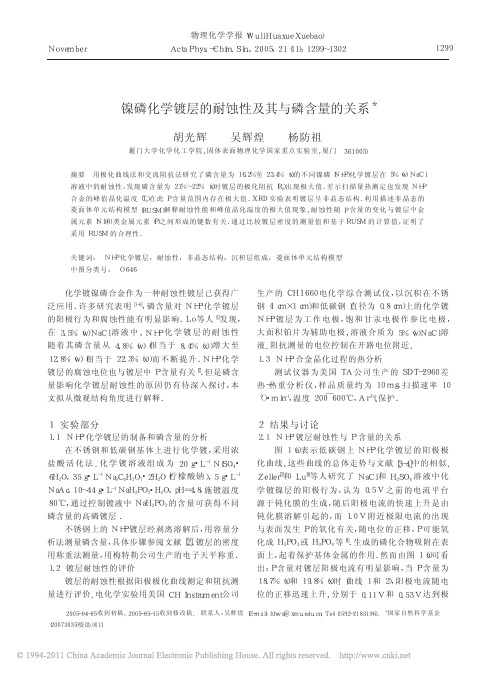
Vol.21
xP(%)
图 1 (a )Ni-P 化学镀层在 5% (w ) Na Cl 溶液中的伏安曲线, (b )不同电位下的腐蚀电流和 P 含量的关系 F ig.1 (a)Volt am m et r ic cu r ves of elect r oless Ni-P d ep osit s in 5% (w )NaCl solu t ion , (b ) r elat ion of cor r osion
!!!(b ) r elat ion of t h e p olar izat ion r esist an ce Rp t o t h e P con t en t !!!!The Rp values were obtained from the curve fitting based on the equivalent circuit given in the literature[1]. !!!!The P contents of 1 to 7 are the same as Fig.1.
不锈钢上的 Ni-P 镀层经剥离溶解后, 用容量分 析法测量磷含量, 具体步骤参阅文献[2]. 镀层的密度 用称重法测量, 用梅特勒公司生产的电子天平称重. 1.2 镀层耐蚀性的评价
镀层的耐蚀性根据阳极极化曲线测定和阻抗测 量进行评价. 电化学实验用美国 CH Instrument 公司
2 结果与讨论
摘要 用极化曲线法和交流阻抗法研究了磷含量为 16.2%至 23.4% (x)的不同镍磷(Ni-P)化学镀层在 5%(w) NaCl 溶液中的耐蚀性, 发现磷含量为 21%~22% (x)时镀层的极化阻抗(Rp)出现极大值. 差示扫描量热测定也发现 Ni-P 合 金的峰值晶化温度(Tp)在此 P 含量范围内 存 在 极 大 值. XRD 实 验 表 明 镀 层 呈 非 晶 态 结 构. 利 用 描 述 非 晶 态 的 菱面体单元结构模型(RUSM)解释耐蚀性能和峰值晶化温度的极大值现象, 耐 蚀 性 随 P 含 量 的 变 化 与 镀 层 中 金 属元素(Ni)和类金属元素(P)之间形成的键数有关. 通 过 比 较 镀 层 密 度 的 测 量 值 和 基 于RUSM 的 计 算 值, 证 明 了 采用 RUSM 的合理性.
影响化学镀镍层耐蚀性能原因分析

影响化学镀镍层耐蚀性能原因分析
1 基材质量:基材的批锋,沙眼及基材金属中硫化物的含量直接影响镀层孔隙率;
2 前处理:
a 除油不彻底或缓蚀剂膜的处理不好,不仅会降低结合力,还会产生针孔而降低耐蚀性;
b 酸洗或活化过度,使得基材表面粗糙,会使镀层孔隙率增加。
3 镀液及施镀工艺:
a 镀液的组分:不同的络合剂和稳定剂其耐蚀性不同;
b 施镀工艺:一般情况下,温度,PH值及镀液循环周期(MTO)直接影响镀层的磷含
量(磷含量越高,耐蚀性越高),另外,沉积速率越快,孔隙率就越大,耐蚀性越差
4 镀层的后处理:
a 镀层表面钝化;
b 镀后低温热处理(200℃)1小时,不仅除氢,还增加了硬度,降低了孔隙率。
电沉积Ni_Fe合金工艺及镀层耐蚀性的研究
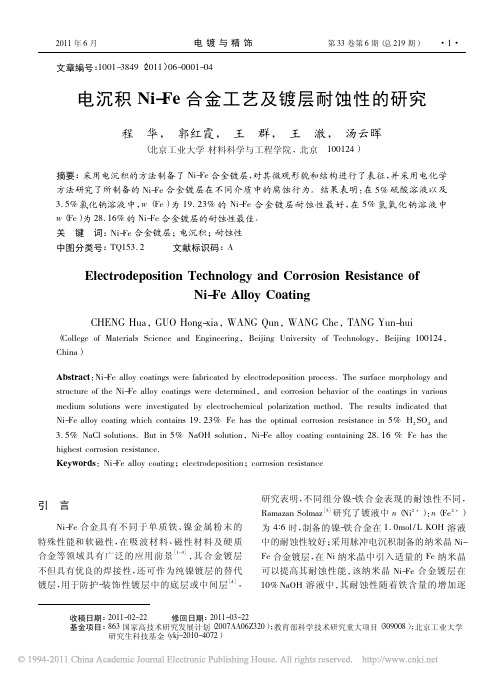
收稿日期: 2011-02-22
修回日期: 2011-03-22
基金项目: 863 国家高技术研究发展计划( 2007AA06Z320) ; 教育部科学技术研究重大项目( 309008) ; 北京工业大学
研究生科技基金( ykj-2010-4072)
·2· Jun. 2011
Plating and Finishing
1实验
1. 1 电沉积镍-铁合金工艺 Ni-Fe 合金镀层采用直流电沉积的方法制备,
阳极为镍板,阴极为 δ = 40μm 的紫铜片。具体操作 流程为: 清洗→化学除油→清洗→酸腐蚀→清洗→ 装挂→电镀镍-铁合金→冷水清洗→烘干。
试验中所用试剂均为分析纯,镀液用去离子水 配制。镀液组成为: 200g / L NiSO4·6H2 O,40 g / L 硼 酸,4g / L 糖精,40 g / L 柠檬酸钠,1 g / L 抗坏血酸,依 次为 0、10、20 和30 g / L FeSO4·7H2 O,镀液的 pH 控 制在 3. 0 ~ 3. 5,θ 为 60 ~ 65℃ ,极板间距 6 cm,Jκ = 3A / dm2 。 1. 2 镀层成分、形貌和微观结构分析
目前,对于 Ni-Fe 合金镀层的耐腐蚀性能有一 定的研究,但 是 其 基 体 大 多 集 中 在 不 锈 钢 板[6]、冷 轧铜板[7]或 铝 合 金[9] 等 材 料 上。 随 着 电 子 产 品 的 发展,Ni-Fe 合金箔在电子工业上作为记忆、记录和 计算机储存装置而得到一定规模的应用。采用电 沉积方法在铜箔上获得镍-铁磁性合金薄膜材料,突 破了传统磁屏蔽材料的应用局限,铜箔基体上得到 的镍-铁合金薄膜是一种新型的柔性基体复合磁屏 蔽材料,拓 宽 了 材 料 的 使 用 范 围。 但 是,关 于 这 种 新型的柔性基体复合磁屏蔽材料的腐蚀性能却很 少报道。因此本文以直流电沉积的方法在铜箔基 体上制备了纯 Ni 和不同铁含量的 Ni-Fe 合金镀层, 并采用电化学方法系统研究了该合金镀层在 5% 的 硫酸溶液、3. 5% 的氯化钠溶液以及 5% 的氢氧化钠 溶液中的腐蚀行为,分析了 Ni-Fe 合金镀层中 Fe 元 素对其耐蚀性能的影响。
耐蚀性机理分析
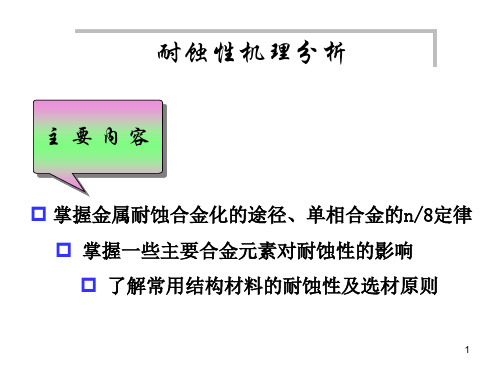
加入易钝化的金属
工程上广泛采用的是碳钢及铁基合金,为提高耐 蚀性,往往向其中加入易钝化元素,Al、Ni、Cr等提 高合金整体钝化性能。如,向铁中加入18%左右的Cr, 8%左右的Ni制得不锈钢。 加入阴极合金促进阳极钝化 对于可钝化材料,加入强阴极性元素,由于阴极 反应过程加剧,促使腐蚀电流增大,随着电流不断增 大,阳极不断极化,电位变正进入钝化区,阳极出现 钝化现象,其腐蚀电流急剧下降,达到防腐目的。这 种方法极具前途。
铝在非氧化性酸、碱中易腐蚀。
敏感于卤素离子,易发生小孔腐蚀。 液流冲击会破坏钝化膜,输送腐蚀介质应 v<1.5m/s,输送清水时,v<6m/s。 铝耐硫和硫化物的腐蚀。
18
铝的强度低,常加入Cu、Mg、Mn、Si 等使铝强化。 纯铝耐孔蚀,加入Mg、Mn 后耐孔蚀性能也较好。
8
腐蚀速度/(g/m2·h)
0.4
0.3 0.2 0.1
典型例子 Cu-Ni合金在氨溶 液中的耐蚀性
0
25
50
75 Ni %
n/8定律:在给定介质中一种耐蚀组元和另一种不 耐蚀组元组成的固溶体合金,其中耐蚀组元的含量等 于12.5%、25%、37.5%、50% .......的原子分数,即 1/8、2/8、3/8……n/8时,合金的耐蚀性将出现突然 的阶梯式升高,合金的电位也随之升高。其中n称为稳 定性台阶。 9
Mo使合金耐还原性介质的腐蚀和抗氯离子引起的 孔蚀。 Mo抗孔蚀主要是生成氧化物,它较稳定,不 易与Cl -作用;或者生成MoO42-离子,它是很有效的孔 蚀缓蚀剂。
13
Mo对不锈钢耐应力腐蚀的影响
4. Si
硅的作用:耐氯化物腐蚀破裂、耐孔蚀、耐浓热硝 酸、抗氧化、耐海水腐蚀。 不锈钢中,Si 含量增加,可改善耐应力腐蚀破裂性 能。这主要依靠 Si 形成保护膜。 不锈钢中, Si 能改善耐孔蚀性能,这是由于提高了 钢的钝态稳定性。如:00Cr17Ni14Mo2Si3
金属耐蚀合金化原理.正式版PPT文档

但是,在硝酸及强烈通空气的溶液中,当有活性离子(F-,Cl- , Br-)存在时和在还原性介质中大部分金属的钝化态会受到破坏, 产生局部腐蚀。这主要是络合效应所致。
ห้องสมุดไป่ตู้ 耐蚀材料
3、腐蚀产物的性质
⑴金属表面生成难溶的和保护性良好的腐蚀产物膜可提高耐蚀性。
根据腐蚀控制因素(主要分为阴极控制、阳极控制、电阻控 制),耐蚀合金化途径有下列四个方面:
耐蚀材料
这种方法是向本来不耐蚀的纯金属或合金中加入热力学稳定性 高的合金元素,形成固溶体,以提高合金的电极电位。
1、热力学稳定性高的元素,往往是一些贵金属(见前面表中。如 :Au、Ni、Pt、Cu等)。
2、要显著提高合金的热力学稳定性,元素的加入量必须达到一定 值,最低含量一般要使合金中贵金属原子数达到合金中总原子数的 1/8、2/8、4/8……即满足“n/8定律”要求,才能明显提高合金的 耐蚀性。塔曼法则
注:这种方法只适用于不产生钝化的且为阴极控制的腐蚀过程(主 要是在非氧化性或氧化性不强的酸中的活性溶解过程)。
耐蚀材料
1、减少阳极相的面积;
2、加入容易钝化的合金元素; 3、加入阴极性合金元素促进阳极钝化。
原理:在能够建立钝态的情况下,向金属或合金中加入少量强阴极 性元素,由于电化学作用,使阳极电势升高,进入稳定钝化区,从 而使合金达到钝化状态,提高耐蚀性。(进一步解释:强阴极性元 素之所以能够提高阳极的电势,是由于在腐蚀初期,强阴极元素( 一般是电位高,化学性质稳定的元素)在合金表面富集,使表面阳 极电势升高,形成钝化效果。)
⑴去除能形成有效阳极的杂质,可提高耐蚀性。
⑵去除金属中含有的少量氢或电位较高的金属杂质,或避免正电性 金属沉积在腐蚀金属的表面上,都可显著提高金属的耐蚀性。
第5章材料的耐蚀性解读

A.钛 易生成 TiO2 钝化膜,稳定性高于铝和不锈钢生成 的氧化膜 。 钛是耐海水腐蚀之王,对许多含氧的化合物都耐 腐蚀;耐王水腐蚀,耐湿氯气腐蚀,在各种硝酸中都 耐蚀。但钛在发烟硝酸中和甲醇溶液中会发生晶间腐 蚀,在高浓度硫酸和盐酸中不耐腐蚀。 钛在高温下很不稳定,能剧烈地与氧,硫,卤族元 素,碳,甚至和氮,氨化合。 钛在某些强氧化性环境中,发生自燃爆炸事故。
• 6.4.淡水:铝及铝合金、钛及钛合金、高硅 铸铁、不锈钢、铜及铜合金、铅及铅合金、 镍等。 • 6.5.硫酸:高硅铸铁、低浓度用铅、高浓度 用Fe-C合金。 • 6.6.硝酸:钛及钛合金、高硅铸铁、低浓度 用不锈钢、高浓度用铝。
6.7 .盐酸:高硅铸铁、加钼高硅铁、哈氏 合金。 6.8 .磷酸: 18-8Mo 不锈钢、铅及铅合金、 高硅铸铁、铜及铜合金。 6.9 .醋酸:高硅铸铁、 18-8Mo 不锈钢、铜 及青铜、铝。 6.10.氢氧化钠:镍及镍合金、高镍铸铁、 18-8不锈钢、铜及铜合金、钛及钛合金。 6.11.氟水:Fe-C合金、高硅铸铁、不锈钢、 铝及铝合金、钛及钛合金。
不锈钢在具有优良耐蚀性能的同时还具有良好的力学性能及工艺性能冶炼加工焊接等因此自二十世纪初问世以来获得了迅速的发展在化学石油化工核能轻纺食品等现代工业中得到了极广泛的应用
第5章 材料的耐蚀性
1.纯金属的耐蚀性
虽然工程中使用的金属绝大多数是 合金,纯金属较少。 但出于耐蚀的目的, 纯金属的用途也在不断地增多,同时, 各种合金也是以纯金属为组元形成的, 因此,有必要全面了解纯金属的耐蚀性。
2.提高金属材料耐腐蚀性的合金化
工业上以纯金属作为耐蚀材料使用的情况 有限,应用较多的则是Fe、Cu、Ni、Ti、 Al、Mg等金属的合金。因而,了解如何 通过合金化来提高金属材料的耐蚀性十 分必要。
金属耐腐蚀合金化原理

金属耐腐蚀合金化原理§5-1 金属耐腐蚀合金化原理工业上所用的金属材料中,纯金属并不多,应用较多的则是铁、铜、镍、钛、铝、镁等各类金属的合金。
本节讨论如何通过合金化与热处理等途径,从成分与组织上使合金具有高的耐蚀性,并阐明其作用原理。
一、提高金属的热力学稳固性以热力学稳固性高的元素进行合金化,向不耐蚀的合金中加入热力学稳固性高的合金元素进行合金化,可在合金表面形成由贵金属组元构成的连续保护层,提高其耐蚀性。
比如,铜中加金,镍中加铜,铬中加镍等。
但是其应用是有限的。
由于,一方面要耗费大量的贵金属,经济上昂贵;另一方面,由于合金组元在固态中的溶解度是有限的,许多合金要获得具有多组元的单一固溶体是比较困难的。
二、降低阴极活性在阴极操纵的金属腐蚀中,可用进一步加强阴极极化的办法来降低腐蚀速度。
如金属在酸中的活性溶解就能够用降低阴极活性的方法减少腐蚀。
具体方法是:1.减小金属或者合金中的活性阴极面积金属或者合金在酸中腐蚀时,阴极析氢过程优先在氢超电压低的阴极相或者夹杂物上进行。
假如减少合金中的阴极相或者夹杂物,减小了活性阴极面积,增加了阴极极化电流密度,增加阴极极化程度,阻碍阴极过程的进行,提高耐蚀性。
比如,当铝中铁含量减少时,其在盐酸中的耐蚀性提高,如P128图1。
这是由于铁能形成阴极相。
关于阴极操纵的腐蚀过程,使用固溶处理获得单相固溶体组织,可提高耐蚀性。
反之,退火或者时效处理降低其耐蚀性。
2.加入氢超电压高的元素加入氢超电压高的元素,可提高阴极析氢超电压,显著降低合金在酸中的腐蚀速度。
但它只适用于不产生钝化的析氢腐蚀。
如金属在非氧化性或者氧化性低的酸中的活性溶解过程。
比如,在锌中含有铁、铜等电位较高的金属杂质时,加入氢超电压高的镉、汞,可使锌在酸中腐蚀速度显著降低。
又如,在含有较多杂质铁的工业纯镁中,添加0.5-1%锰可大大降低其在氯化物水溶液中的腐蚀速度,这是由于锰比铁高得多的析氢超电压之故。