PCB微孔成孔工艺技术简介
微孔加工方法及微孔结构
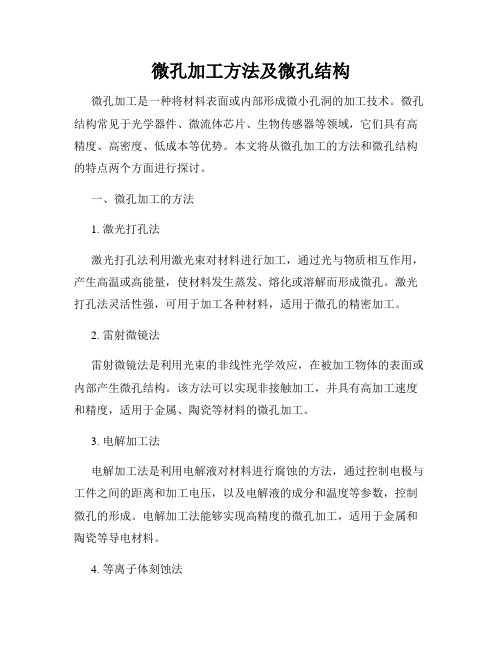
微孔加工方法及微孔结构
微孔加工是一种将材料表面或内部形成微小孔洞的加工技术。微孔结构常见于光学器件、微流体芯片、生物传感器等领域,它们具有高精度、高密度、低成本等优势。本文将从微孔加工的方法和微孔结构的特点两个方面进行探讨。
一、微孔加工的方法
1. 激光打孔法
激光打孔法利用激光束对材料进行加工,通过光与物质相互作用,产生高温或高能量,使材料发生蒸发、熔化或溶解而形成微孔。激光打孔法灵活性强,可用于加工各种材料,适用于微孔的精密加工。
2. 雷射微镜法
雷射微镜法是利用光束的非线性光学效应,在被加工物体的表面或内部产生微孔结构。该方法可以实现非接触加工,并具有高加工速度和精度,适用于金属、陶瓷等材料的微孔加工。
3. 电解加工法
电解加工法是利用电解液对材料进行腐蚀的方法,通过控制电极与工件之间的距离和加工电压,以及电解液的成分和温度等参数,控制微孔的形成。电解加工法能够实现高精度的微孔加工,适用于金属和陶瓷等导电材料。
4. 等离子体刻蚀法
等离子体刻蚀法是利用等离子体产生的精细能束,通过物理或化学
反应去除材料表面或内部的材料,形成微孔。这种方法对于刻蚀深度、形状和尺寸有较好的控制能力,可用于加工高精度和高密度的微孔结构。
二、微孔结构的特点
1. 高精度
微孔加工能够实现亚微米级的孔径和亚微米级的位置精度,通常在
纳米级别。这种高精度的特点使得微孔在光学、电子和微纳加工等领
域有着重要的应用。
2. 高密度
微孔加工可以在有限的空间内形成大量的微孔结构,从而实现高密
度的排列。这种高密度的特点能够提高器件的功能性和性能。
印制电路板微孔背钻技术研究
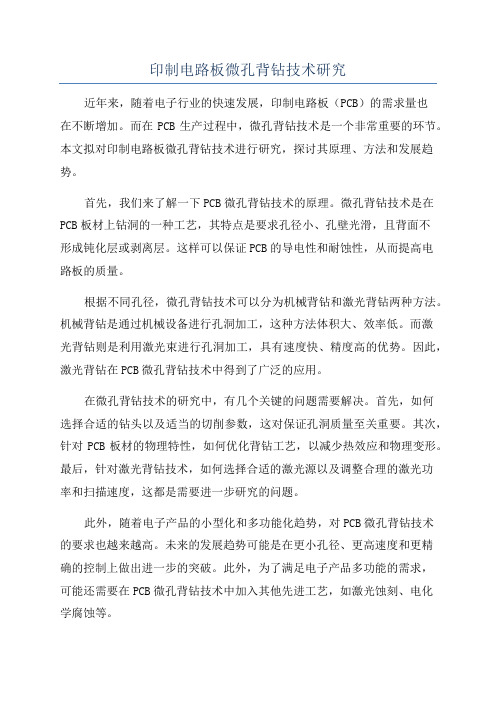
印制电路板微孔背钻技术研究
近年来,随着电子行业的快速发展,印制电路板(PCB)的需求量也
在不断增加。而在PCB生产过程中,微孔背钻技术是一个非常重要的环节。本文拟对印制电路板微孔背钻技术进行研究,探讨其原理、方法和发展趋势。
首先,我们来了解一下PCB微孔背钻技术的原理。微孔背钻技术是在PCB板材上钻洞的一种工艺,其特点是要求孔径小、孔壁光滑,且背面不
形成钝化层或剥离层。这样可以保证PCB的导电性和耐蚀性,从而提高电
路板的质量。
根据不同孔径,微孔背钻技术可以分为机械背钻和激光背钻两种方法。机械背钻是通过机械设备进行孔洞加工,这种方法体积大、效率低。而激
光背钻则是利用激光束进行孔洞加工,具有速度快、精度高的优势。因此,激光背钻在PCB微孔背钻技术中得到了广泛的应用。
在微孔背钻技术的研究中,有几个关键的问题需要解决。首先,如何
选择合适的钻头以及适当的切削参数,这对保证孔洞质量至关重要。其次,针对PCB板材的物理特性,如何优化背钻工艺,以减少热效应和物理变形。最后,针对激光背钻技术,如何选择合适的激光源以及调整合理的激光功
率和扫描速度,这都是需要进一步研究的问题。
此外,随着电子产品的小型化和多功能化趋势,对PCB微孔背钻技术
的要求也越来越高。未来的发展趋势可能是在更小孔径、更高速度和更精
确的控制上做出进一步的突破。此外,为了满足电子产品多功能的需求,
可能还需要在PCB微孔背钻技术中加入其他先进工艺,如激光蚀刻、电化
学腐蚀等。
综上所述,印制电路板微孔背钻技术是一个非常重要的研究课题,通过对其原理、方法和发展趋势的探讨,我们可以更好地理解和应用这一技术。相信随着技术的不断突破和发展,PCB微孔背钻技术将在电子行业中发挥越来越重要的作用。
pcb孔工艺技术
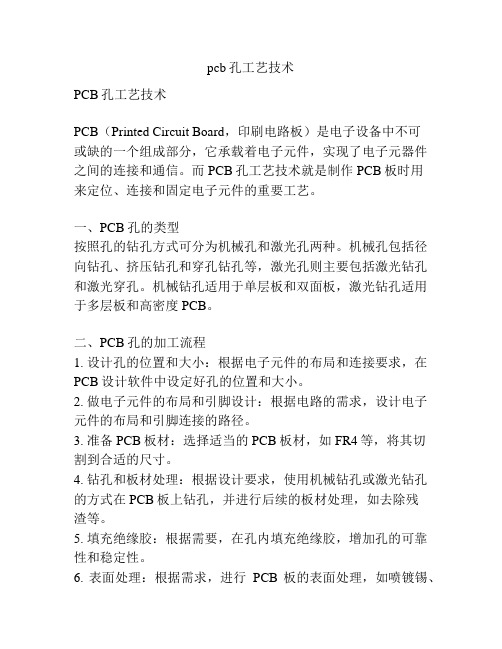
pcb孔工艺技术
PCB孔工艺技术
PCB(Printed Circuit Board,印刷电路板)是电子设备中不可
或缺的一个组成部分,它承载着电子元件,实现了电子元器件之间的连接和通信。而PCB孔工艺技术就是制作PCB板时用
来定位、连接和固定电子元件的重要工艺。
一、PCB孔的类型
按照孔的钻孔方式可分为机械孔和激光孔两种。机械孔包括径向钻孔、挤压钻孔和穿孔钻孔等,激光孔则主要包括激光钻孔和激光穿孔。机械钻孔适用于单层板和双面板,激光钻孔适用于多层板和高密度PCB。
二、PCB孔的加工流程
1. 设计孔的位置和大小:根据电子元件的布局和连接要求,在PCB设计软件中设定好孔的位置和大小。
2. 做电子元件的布局和引脚设计:根据电路的需求,设计电子元件的布局和引脚连接的路径。
3. 准备PCB板材:选择适当的PCB板材,如FR4等,将其切
割到合适的尺寸。
4. 钻孔和板材处理:根据设计要求,使用机械钻孔或激光钻孔的方式在PCB板上钻孔,并进行后续的板材处理,如去除残
渣等。
5. 填充绝缘胶:根据需要,在孔内填充绝缘胶,增加孔的可靠性和稳定性。
6. 表面处理:根据需求,进行PCB板的表面处理,如喷镀锡、
喷镀金等。
7. 完成PCB孔加工:最后对PCB板进行检查和测试,确保孔
的质量和可靠性。
三、PCB孔工艺技术的发展趋势
随着电子设备的迅速发展,对PCB板的要求也越来越高,
PCB孔工艺技术也在不断发展和创新。以下是一些发展趋势:1. 高密度PCB孔:随着电子元器件尺寸的不断减小和连接的
要求不断提高,PCB孔的密度也在不断增加,如微型孔和盲
微孔电沉积介绍
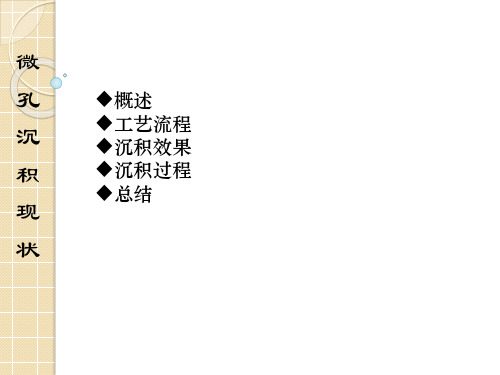
概述 工艺流程 沉积效果 沉积过程 总结
微 孔 沉 积 现 状
概述
孔金属化是PCB制造工艺的核心,孔径的减小使得孔 的厚径比越来越大,进行封孔镀铜也变得越来越困 难。在微孔区域内电流密度分布的不均匀性导致微 孔表面铜的沉积速率大于孔壁和底部的沉积速率, 因此,极易在沉积过程中形成孔洞或接缝,这一结 果为PCB板的使用增加了很多不可靠因素。研究表明, 添加剂的加入会改善沉积效果,使微孔底部的沉积 速率高于表面的沉积速率,最终得到理想的填充效 果。
抑制剂与cl-协同可以抑制铜的电沉积,减少高低电流区 的差异使得铜能够均匀沉积。抑制剂同时也可以充当润湿剂, 降低界面的表面张力,让镀液能更容易进入孔内,增加传质效 果
源自文库
微 孔 沉 积 现 状
沉积过程
整平剂:
整平剂,是高强度的电镀抑制剂,与其它添加剂 协同作用可明显减小镀层的晶粒尺寸,起到整平作 用
微 孔 沉 积 现 状
沉积效果
亚等角沉积、等角沉积和超等角沉积
微 孔 沉 积 现 状
等角沉积: 沉积厚度在孔中个点速度相同时,在开端最 终会导致接缝形成,如果孔低是凹的,则会形成 孔洞。 亚等角沉积: 微孔底部的厚度小于顶部的厚度,会形成孔 洞。 超等角沉积: 铜的沉积速度沿着孔的侧壁向下逐渐增加, 在底部沉积速度最快。
微 孔 沉 积 现 状
pcb 钻孔 沉铜 线路 工艺
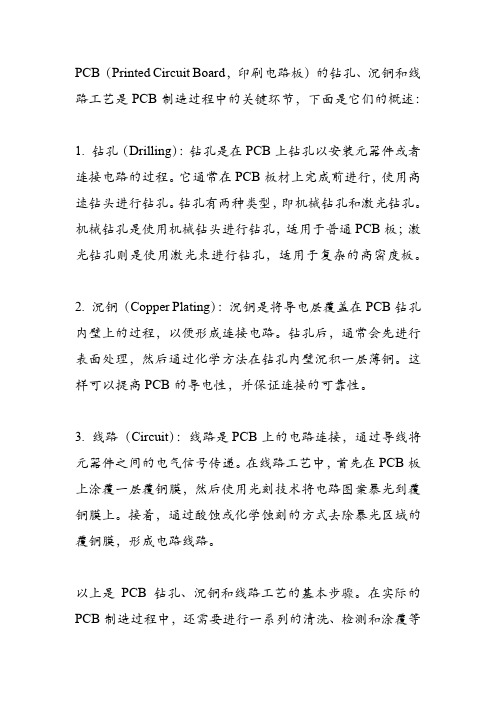
PCB(Printed Circuit Board,印刷电路板)的钻孔、沉铜和线路工艺是PCB制造过程中的关键环节,下面是它们的概述:
1. 钻孔(Drilling):钻孔是在PCB上钻孔以安装元器件或者连接电路的过程。它通常在PCB板材上完成前进行,使用高速钻头进行钻孔。钻孔有两种类型,即机械钻孔和激光钻孔。机械钻孔是使用机械钻头进行钻孔,适用于普通PCB板;激光钻孔则是使用激光束进行钻孔,适用于复杂的高密度板。
2. 沉铜(Copper Plating):沉铜是将导电层覆盖在PCB钻孔内壁上的过程,以便形成连接电路。钻孔后,通常会先进行表面处理,然后通过化学方法在钻孔内壁沉积一层薄铜。这样可以提高PCB的导电性,并保证连接的可靠性。
3. 线路(Circuit):线路是PCB上的电路连接,通过导线将元器件之间的电气信号传递。在线路工艺中,首先在PCB板上涂覆一层覆铜膜,然后使用光刻技术将电路图案暴光到覆铜膜上。接着,通过酸蚀或化学蚀刻的方式去除暴光区域的覆铜膜,形成电路线路。
以上是PCB钻孔、沉铜和线路工艺的基本步骤。在实际的PCB制造过程中,还需要进行一系列的清洗、检测和涂覆等
工艺,以确保PCB的质量和可靠性。
PCB制作工艺流程简介
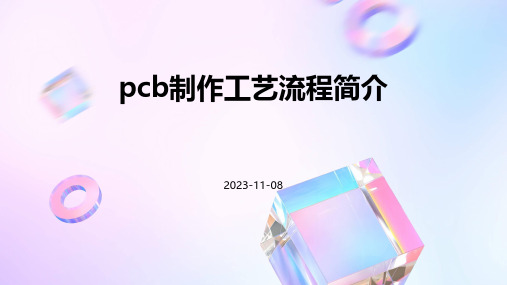
2023-11-08
•pcb制作概述
•pcb设计
•pcb制作的前期准备
•pcb制作过程
•pcb制作完成后的处理
目
•pcb制作中的注意事项及常见问题
•pcb制作的发展趋势及未来展望录
01 pcb制作概述
pcb基本概念
Printed Circuit Board
PCB是印刷电路板,是一种用于将电子器件连接在一起的基板,通常由绝缘材料制成。
电路板组成
PCB通常由导电层、绝缘层和支撑层组成,其中导电层用于传输电信号,绝缘层用于隔离导电层,支撑层则用于支撑整个电路板。
设计电路图制作裸板光绘与刻板
将铜箔粘贴在绝缘材料上,形成导电层。使用光绘机将电路图绘制在铜箔上,形成电路图形。03
pcb制作流程简介
02 01
根据产品需求,使用EDA
设计软件绘制电路图。
通过蚀刻工艺将不需要的铜箔去除,形成所
需的电路图形。
蚀刻与去膜
在电路导线上沉积一层锡/金,以提高导电性能和耐腐蚀性。
沉锡/金
在电路板上涂抹阻焊剂,以防止焊接时短路。
印阻焊剂
对电路板进行成型和钻孔加工,以满足实际应用需求。
成型与钻孔
pcb制作流程简介
实现电子设备的小型化和高效化
PCB是实现电子设备内部器件连接的关键部件,其制作质量直接影响到电子设备的性能和
可靠性。
pcb制作的重要性
保障电子设备的稳定性和安全性
PCB的制作质量直接关系到电子设备的稳定性和安全性,因为一旦出现短路或信号干扰等
问题,就可能导致设备故障或损坏。
提升电子设备的品质和降低成本
优秀的PCB制作工艺可以提高电子设备的品质和性能,同时降低制作成本和时间成本,提
高市场竞争力。
02 pcb设计
高密度电路板技术与应用.pcb先进制造技术_概述及解释说明
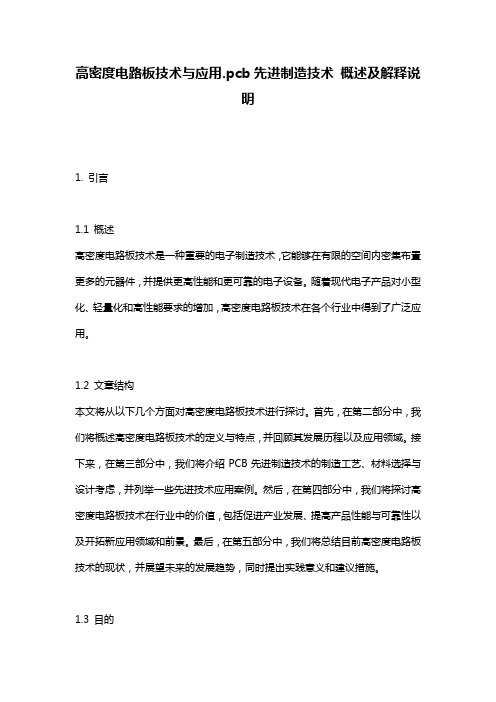
高密度电路板技术与应用.pcb先进制造技术概述及解释说
明
1. 引言
1.1 概述
高密度电路板技术是一种重要的电子制造技术,它能够在有限的空间内密集布置更多的元器件,并提供更高性能和更可靠的电子设备。随着现代电子产品对小型化、轻量化和高性能要求的增加,高密度电路板技术在各个行业中得到了广泛应用。
1.2 文章结构
本文将从以下几个方面对高密度电路板技术进行探讨。首先,在第二部分中,我们将概述高密度电路板技术的定义与特点,并回顾其发展历程以及应用领域。接下来,在第三部分中,我们将介绍PCB先进制造技术的制造工艺、材料选择与设计考虑,并列举一些先进技术应用案例。然后,在第四部分中,我们将探讨高密度电路板技术在行业中的价值,包括促进产业发展、提高产品性能与可靠性以及开拓新应用领域和前景。最后,在第五部分中,我们将总结目前高密度电路板技术的现状,并展望未来的发展趋势,同时提出实践意义和建议措施。
1.3 目的
本文的目的是全面介绍高密度电路板技术及其应用,在读者对该领域有一个整体了解的基础上,进一步深入探讨其制造工艺、材料与设计考虑以及先进技术应用案例。同时,本文还将重点分析高密度电路板技术在产业中的价值,包括其对产业发展、产品性能与可靠性的提升,以及新应用领域和前景的拓展。最后,我们还将总结目前高密度电路板技术的现状,并为未来发展趋势提出展望,并给出实践意义和建议措施。通过阅读本文,读者将能够更好地了解高密度电路板技术,并对其在相关行业中的应用与发展有一个更清晰的认识。
2. 高密度电路板技术概述
2.1 定义与特点
有关盲孔埋孔制作工艺
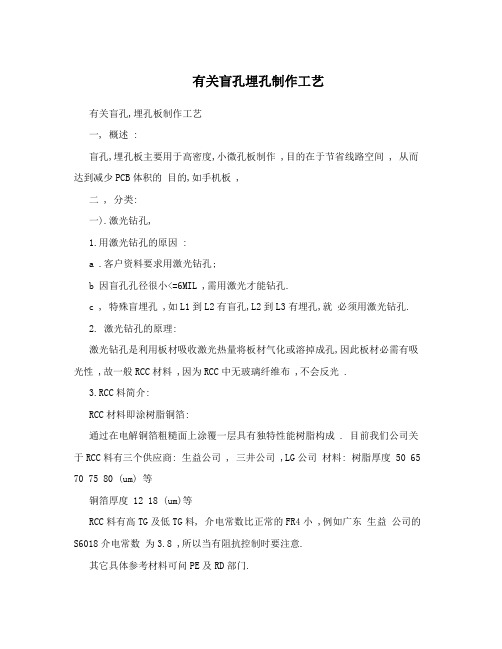
有关盲孔埋孔制作工艺
有关盲孔,埋孔板制作工艺
一, 概述 :
盲孔,埋孔板主要用于高密度,小微孔板制作 ,目的在于节省线路空间 , 从而达到减少PCB体积的目的,如手机板 ,
二 , 分类:
一).激光钻孔,
1.用激光钻孔的原因 :
a .客户资料要求用激光钻孔;
b 因盲孔孔径很小<=6MIL ,需用激光才能钻孔.
c , 特殊盲埋孔 ,如L1到L2有盲孔,L2到L3有埋孔,就必须用激光钻孔.
2. 激光钻孔的原理:
激光钻孔是利用板材吸收激光热量将板材气化或溶掉成孔,因此板材必需有吸光性 ,故一般RCC材料 ,因为RCC中无玻璃纤维布 ,不会反光 .
3.RCC料简介:
RCC材料即涂树脂铜箔:
通过在电解铜箔粗糙面上涂覆一层具有独特性能树脂构成 . 目前我们公司关于RCC料有三个供应商: 生益公司 , 三井公司 ,LG公司材料: 树脂厚度 50 65 70 75 80 (um) 等
铜箔厚度 12 18 (um)等
RCC料有高TG及低TG料, 介电常数比正常的FR4小 ,例如广东生益公司的S6018介电常数为3.8 ,所以当有阻抗控制时要注意.
其它具体参考材料可问PE及RD部门.
4. 激光钻孔的工具制作要求:
A).激光很难烧穿铜皮,故在激光钻孔前要在盲孔位蚀出跟完成孔径等大的Cu Clearance .
B). 激光钻孔的定位标记加在L2/LN-1层,要在MI菲林修改页注明。 C).蚀盲孔点菲林必须用LDI制作,开料要用LDI板材尺寸。
5.生产流程特点:
A). 当线路总层数为N , L2—Ln-1 层先按正常板流程制作完毕, B). 压完板,锣完外围后流程改为:
印制电路板(PCB)微盲孔填充及通孔金属化技术
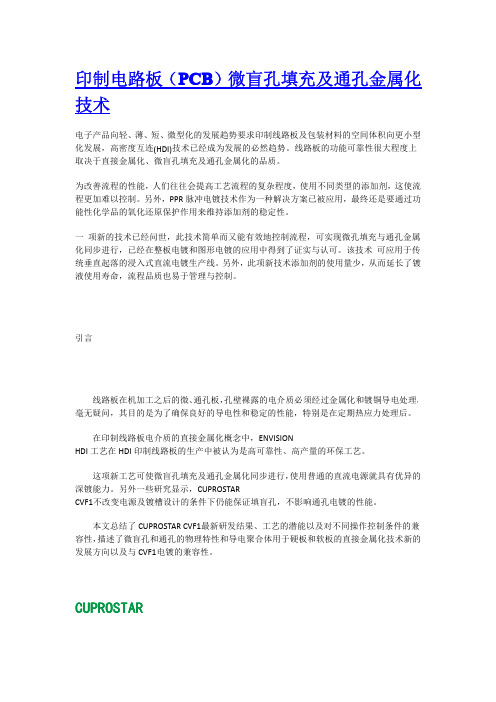
印制电路板(PCB)微盲孔填充及通孔金属化技术
电子产品向轻、薄、短、微型化的发展趋势要求印制线路板及包装材料的空间体积向更小型化发展,高密度互连(HDI)技术已经成为发展的必然趋势。线路板的功能可靠性很大程度上取决于直接金属化、微盲孔填充及通孔金属化的品质。
为改善流程的性能,人们往往会提高工艺流程的复杂程度,使用不同类型的添加剂,这使流程更加难以控制。另外,PPR脉冲电镀技术作为一种解决方案已被应用,最终还是要通过功能性化学品的氧化还原保护作用来维持添加剂的稳定性。
一项新的技术已经问世,此技术简单而又能有效地控制流程,可实现微孔填充与通孔金属化同步进行,已经在整板电镀和图形电镀的应用中得到了证实与认可。该技术可应用于传统垂直起落的浸入式直流电镀生产线。另外,此项新技术添加剂的使用量少,从而延长了镀液使用寿命,流程品质也易于管理与控制。
引言
线路板在机加工之后的微、通孔板,孔壁裸露的电介质必须经过金属化和镀铜导电处理,毫无疑问,其目的是为了确保良好的导电性和稳定的性能,特别是在定期热应力处理后。
在印制线路板电介质的直接金属化概念中,ENVISION
HDI工艺在HDI印制线路板的生产中被认为是高可靠性、高产量的环保工艺。
这项新工艺可使微盲孔填充及通孔金属化同步进行,使用普通的直流电源就具有优异的深镀能力。另外一些研究显示,CUPROSTAR
CVF1不改变电源及镀槽设计的条件下仍能保证填盲孔,不影响通孔电镀的性能。
本文总结了CUPROSTAR CVF1最新研发结果、工艺的潜能以及对不同操作控制条件的兼容性,描述了微盲孔和通孔的物理特性和导电聚合体用于硬板和软板的直接金属化技术新的发展方向以及与CVF1电镀的兼容性。
PCB钻孔培训教材
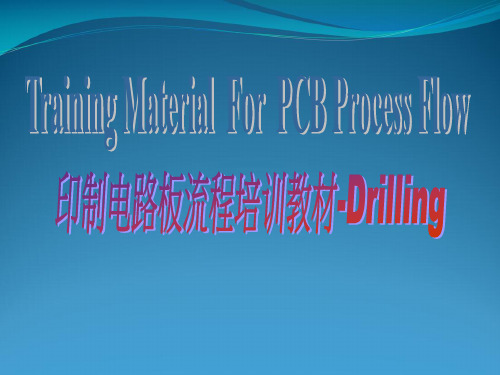
钻针每旋转一周后所能刺进的吋数(in/R)。
In/min
CL=
R/min
Drilling -钻孔
B. 旋转速度(Speeds) 一 每分钟所旋转 圈数(Revolution Per Minute RPM)
钻针线性速度(尺/分)×12 RPM=
钻针直径×3.14
Drilling -钻孔
通常转数约为6万-8万RPM,转速太高 时会造成积热及磨损钻针。 当进刀速度约 为120in/min左右,转速为6万RPM时,其 每一转所能刺入的深度为其排屑量。
因为多块一钻,所以钻之前先以pin将每块板子固定住,此动作由上pin机 (pinning maching)执行之. 双面板很简单,大半用靠边方式,打孔上pin连 续动作一次完成.多层板比较复杂,另须多层板专用上PIN机作业.
Drilling -钻孔
6.4.1钻孔机
钻孔机的型式及配备功能种类非常多,以下List评估重点 A. 轴数:和产量有直接关系 B. 有效钻板尺寸 C. 钻孔机台面:选择振动小,强度平整好的材质。 D. 轴承(Spindle) E. 钻盘:自动更换钻头及钻头数
Drilling -钻孔
作业注意事项 A、转数、进刀数的设定,应依实际的作业状况,机器所
附手册上的条件仅为参考,仍须修正
B、定期测量转数、进刀数,Run out等数值.
PCB钻孔的流程、分类和技巧
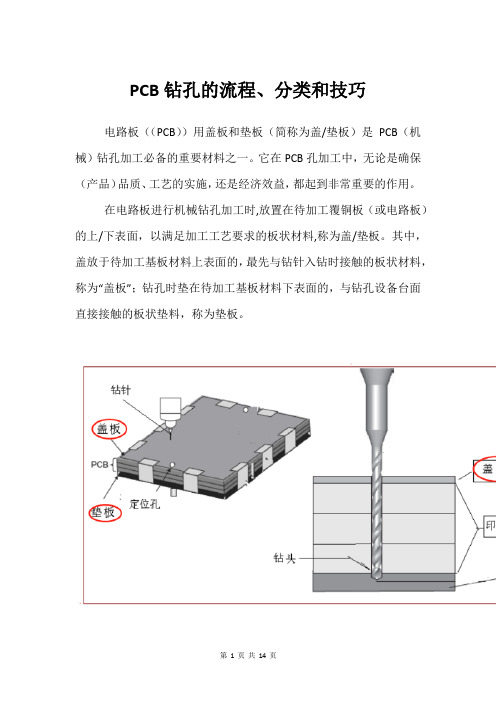
PCB钻孔的流程、分类和技巧
电路板((PCB))用盖板和垫板(简称为盖/垫板)是PCB(机械)钻孔加工必备的重要材料之一。它在PCB孔加工中,无论是确保(产品)品质、工艺的实施,还是经济效益,都起到非常重要的作用。
在电路板进行机械钻孔加工时,放置在待加工覆铜板(或电路板)的上/下表面,以满足加工工艺要求的板状材料,称为盖/垫板。其中,盖放于待加工基板材料上表面的,最先与钻针入钻时接触的板状材料,称为“盖板”;钻孔时垫在待加工基板材料下表面的,与钻孔设备台面直接接触的板状垫料,称为垫板。
钻孔是PCB制造中最昂贵和最耗时的过程。PCB钻孔过程必须小心实施,因为即使是很小的错误也会导致很大的损失。钻孔工艺是PCB制造过程中最关键的工艺。钻孔工艺是通孔和不同层之间连接的基础,因此钻孔技巧十分重要。
PCB钻孔
一、PCB钻孔技术
主要有2 种PCB 钻孔技术:机械钻孔和激光钻孔。
PCB钻孔技术
1、机械钻孔
机械钻头的精度较低,但易于执行。这种钻孔技术实现了钻头。这些钻头可以钻出的最小孔径约为6密耳(0.006 英寸)。
机械钻孔的局限性
当用于FR4 等较软的材料时,机械钻可用于800 次冲击。对于密度比较大的材料,寿命会减少到200 计数。如果PCB 制造商忽视这一点,则会导致出现错误的孔,从而导致电路板报废。
2、激光钻孔
另一方面,激光钻可以钻出更小的孔。激光钻孔是一种非接触式工艺,工件和工具不会相互接触。激光束用于去除电路板材料并创建精确的孔,可以毫不费力地控制钻孔深度。
激光技术用于轻松钻出受控深度的过孔,可以精确钻出最小直径为2 密耳(0.002”)的孔。
pcb过孔制作工艺
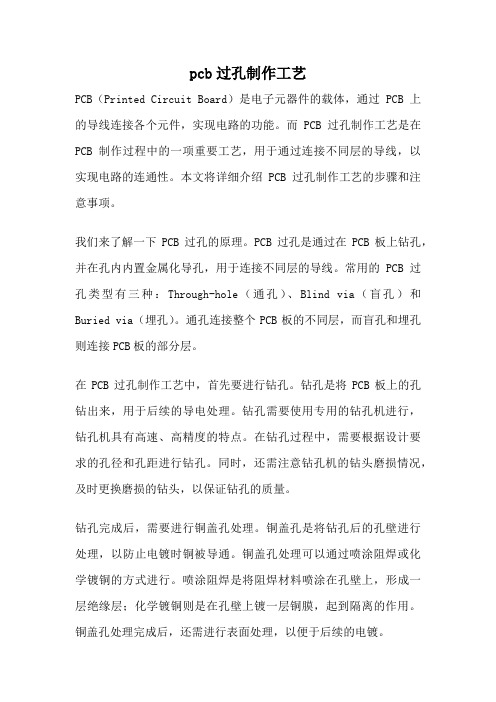
pcb过孔制作工艺
PCB(Printed Circuit Board)是电子元器件的载体,通过PCB上的导线连接各个元件,实现电路的功能。而PCB过孔制作工艺是在PCB制作过程中的一项重要工艺,用于通过连接不同层的导线,以实现电路的连通性。本文将详细介绍PCB过孔制作工艺的步骤和注意事项。
我们来了解一下PCB过孔的原理。PCB过孔是通过在PCB板上钻孔,并在孔内内置金属化导孔,用于连接不同层的导线。常用的PCB过孔类型有三种:Through-hole(通孔)、Blind via(盲孔)和Buried via(埋孔)。通孔连接整个PCB板的不同层,而盲孔和埋孔则连接PCB板的部分层。
在PCB过孔制作工艺中,首先要进行钻孔。钻孔是将PCB板上的孔钻出来,用于后续的导电处理。钻孔需要使用专用的钻孔机进行,钻孔机具有高速、高精度的特点。在钻孔过程中,需要根据设计要求的孔径和孔距进行钻孔。同时,还需注意钻孔机的钻头磨损情况,及时更换磨损的钻头,以保证钻孔的质量。
钻孔完成后,需要进行铜盖孔处理。铜盖孔是将钻孔后的孔壁进行处理,以防止电镀时铜被导通。铜盖孔处理可以通过喷涂阻焊或化学镀铜的方式进行。喷涂阻焊是将阻焊材料喷涂在孔壁上,形成一层绝缘层;化学镀铜则是在孔壁上镀一层铜膜,起到隔离的作用。铜盖孔处理完成后,还需进行表面处理,以便于后续的电镀。
接下来是电镀工艺。电镀是将钻孔后的孔壁镀上一层金属,以实现导电连接。常用的电镀方法有湿法电镀和干法电镀。湿法电镀是将PCB板浸泡在电镀槽中,通过电解的方式进行电镀。而干法电镀则是将PCB板放入真空室中,通过物理气相沉积的方式进行电镀。电镀后的PCB板要进行清洗和烘干,以去除表面的杂质和水分。
pcb生产机械加工及激光钻孔工艺基础
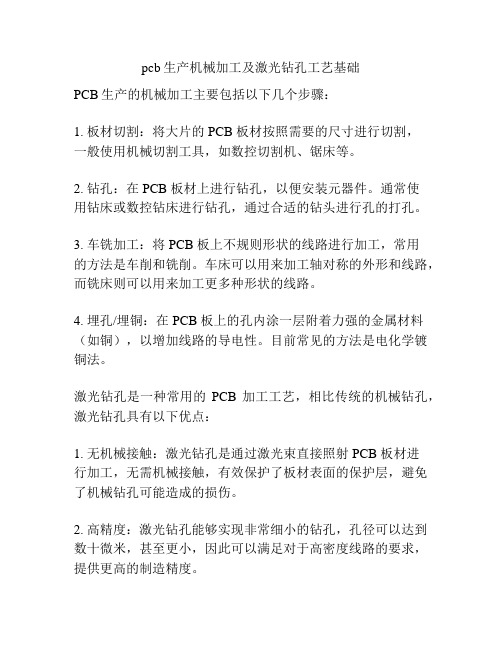
pcb生产机械加工及激光钻孔工艺基础
PCB生产的机械加工主要包括以下几个步骤:
1. 板材切割:将大片的 PCB 板材按照需要的尺寸进行切割,
一般使用机械切割工具,如数控切割机、锯床等。
2. 钻孔:在 PCB 板材上进行钻孔,以便安装元器件。通常使
用钻床或数控钻床进行钻孔,通过合适的钻头进行孔的打孔。
3. 车铣加工:将 PCB 板上不规则形状的线路进行加工,常用
的方法是车削和铣削。车床可以用来加工轴对称的外形和线路,而铣床则可以用来加工更多种形状的线路。
4. 埋孔/埋铜:在 PCB 板上的孔内涂一层附着力强的金属材料(如铜),以增加线路的导电性。目前常见的方法是电化学镀铜法。
激光钻孔是一种常用的PCB 加工工艺,相比传统的机械钻孔,激光钻孔具有以下优点:
1. 无机械接触:激光钻孔是通过激光束直接照射 PCB 板材进
行加工,无需机械接触,有效保护了板材表面的保护层,避免了机械钻孔可能造成的损伤。
2. 高精度:激光钻孔能够实现非常细小的钻孔,孔径可以达到数十微米,甚至更小,因此可以满足对于高密度线路的要求,提供更高的制造精度。
3. 布线灵活:激光钻孔可以实现任意位置的钻孔,布线更加灵活,可以为设计者提供更多的设计自由度。
4. 加工速度快:相比传统的机械钻孔,激光钻孔的速度通常更快,可以提高 PCB 加工的效率。
总体来说,机械加工和激光钻孔是 PCB 生产中常用的工艺基础,根据具体的需求和要求,可以选择不同的加工方法来进行PCB 的制造。
HDI板微孔工艺介绍
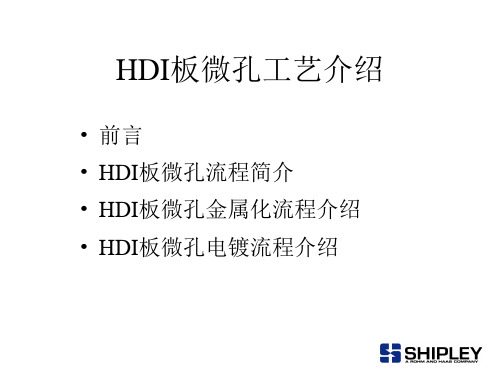
良好的输出波形,是得到最佳PPR镀铜的保证。
板先在高温环境中(约90℃),以KMnO4进行氧化性的整 孔处理,使孔壁上先形成MnO2层,再浸入含Pyrrole (聚吡咯)的稀释液中反应生成导电膜。
四. HDI板微孔电镀流程介绍
由于HDI板微孔特性,孔内传质效果差,所以孔内 电镀困难度较一般通孔要大。为改善孔内电镀层 品质,主要采用如下措施: • 降低电流密度,延长电镀时间。 • 优化镀液参数和电镀槽液计。 • 改垂直挂镀为水平挂镀。 • 改用反脉冲电镀。
• 碳黑基工艺(如 麦德美的BLACKHOLE)
碳黑基工艺与石墨基工艺相似。碳黑系统不需要选择 固定剂。 流程: 清洁剂 清洁剂 碳 碳 黑 黑 空气刀/干燥 空气刀/干燥
微
蚀
• 导电聚合物(如DMS-E)
该工艺是在树脂及玻璃纤维表面上形成有机导电层。 流程: 溶剂调整 催 化剂 高锰酸钾 固 定 清 干 洗 燥
锡-钯工艺是用锡来稳定钯胶体,在锡-钯胶体吸附到表 面上后,锡便剥离了(使用含铜的加速剂,使铜沉积到 钯颗粒上,钯导电性更好。
• 石墨基工艺(如 Shadow)
流程: 清洁剂/调整剂 空气刀/干燥 石 墨 加 速 固定剂
调整液在树脂和玻璃表面上产生正电荷,然后吸附带 负电荷的石墨颗粒,使石墨颗粒从溶液中凝聚出来而 覆于PCB表面上。
二. HDI流程简介
电路板钻孔制程介绍
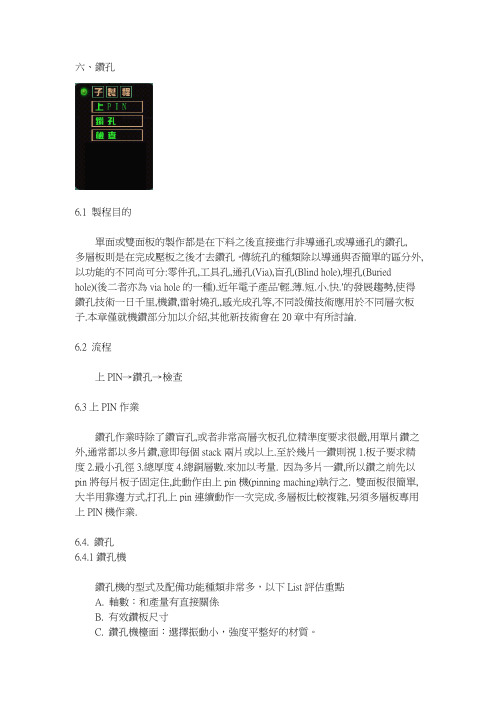
六、鑽孔
6.1製程目的
單面或雙面板的製作都是在下料之後直接進行非導通孔或導通孔的鑽孔,
多層板則是在完成壓板之後才去鑽孔。傳統孔的種類除以導通與否簡單的區分外,以功能的不同尚可分:零件孔,工具孔,通孔(Via),盲孔(Blind hole),埋孔(Buried
hole)(後二者亦為via hole的一種).近年電子產品'輕.薄.短.小.快.'的發展趨勢,使得鑽孔技術一日千里,機鑽,雷射燒孔,感光成孔等,不同設備技術應用於不同層次板子.本章僅就機鑽部分加以介紹,其他新技術會在20章中有所討論.
6.2流程
上PIN→鑽孔→檢查
6.3上PIN作業
鑽孔作業時除了鑽盲孔,或者非常高層次板孔位精準度要求很嚴,用單片鑽之外,通常都以多片鑽,意即每個stack兩片或以上.至於幾片一鑽則視1.板子要求精度2.最小孔徑3.總厚度4.總銅層數.來加以考量.因為多片一鑽,所以鑽之前先以pin將每片板子固定住,此動作由上pin機(pinning maching)執行之.雙面板很簡單,大半用靠邊方式,打孔上pin連續動作一次完成.多層板比較複雜,另須多層板專用上PIN機作業.
6.4.鑽孔
6.4.1鑽孔機
鑽孔機的型式及配備功能種類非常多,以下List評估重點
A.軸數:和產量有直接關係
B.有效鑽板尺寸
C.鑽孔機檯面:選擇振動小,強度平整好的材質。
D.軸承(Spindle)
E.鑽盤:自動更換鑽頭及鑽頭數
F.壓力腳
G.X、Y及Z軸傳動及尺寸:精準度,X、Y獨立移動
H.集塵系統:搭配壓力腳,排屑良好,且冷卻鑽頭功能
I.Step Drill的能力
PCB钻孔工艺详解
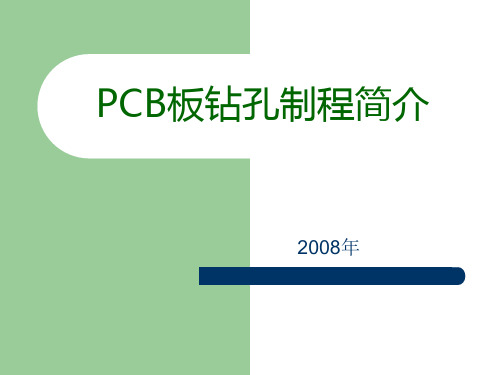
PCB板钻孔制程简介
2008年
目的:了解钻孔制程及品质要求
内容点:
①PCB钻孔的作用
②PCB钻孔板的品质缺陷及解决对策
③钻孔品质及其鱼骨图分析
④钻咀及相关辅料阐述
⑤钻、锣带制作知识的介绍
一、PCB钻孔的作用
1、PCB板制作流程
以双面板喷锡板工艺流程为例:
开料→钻孔→沉铜→板电(加厚铜)→
图形转移→电铜电锡→蚀刻退锡→
检验→印阻焊→印字符→喷锡→成形
→测试→成品检查→包装
一、PCB钻孔的作用
2、钻孔的作用
钻孔就是在覆铜板上钻出所需的过孔。
PCB过孔按金属化与否,分为
a、电镀孔( PTH ),也叫金属化孔
b、非电镀孔(NPTH),也叫非金属化孔
按工艺制程分为
a、盲孔(多层板)
b、埋孔(多层板)
c、通孔
过孔主要提供电气连接与用作器件的固定或定位的作用。
二、PCB钻孔板的品质缺陷及解决对策
品质缺陷原因分析解决对策
断钻(孔损)下钻速或回刀速过快更改加工参数
压脚问题检查或更换压脚
机床不稳定检查固定座
钻咀有缺陷或超孔限更换钻咀类型或检查钻咀叠板过厚或叠板过松减少叠板数或叠紧
盖板材料不对更换盖板
加工深度过深更改合理的深度
胶纸未贴好将胶纸贴好贴牢固
二、PCB钻孔板的品质缺陷及解决对策
品质缺陷原因分析解决对策
断钻(孔损)板间有杂物保持板面及板间清洁
孔壁粗糙,毛刺,
钉头钻头钝或钻头有缺口更换钻头
压脚压力过小检查压脚及气压设置加工参数过快或过慢调整参数设置
叠板太松或太厚贴紧板或更改叠板厚度板间有杂物保持板面及板间清洁多层板层压固化不良需层压或板材协助解决盖板不平、太薄等更换盖板材料
烤板时间或温度不够按要求重新烤板
- 1、下载文档前请自行甄别文档内容的完整性,平台不提供额外的编辑、内容补充、找答案等附加服务。
- 2、"仅部分预览"的文档,不可在线预览部分如存在完整性等问题,可反馈申请退款(可完整预览的文档不适用该条件!)。
- 3、如文档侵犯您的权益,请联系客服反馈,我们会尽快为您处理(人工客服工作时间:9:00-18:30)。
PCB微孔成孔工艺技术简介
1.引言
孔在PCB中的主要作用是实现层间互连或安装元件,几乎所有的PCB需要孔。随着电子产品越来越复杂,PCB上的孔越来越密,技术难度越来越高,设备投入越来越大,因此成孔技术越来越重要,值得深入研究。业界常以导通与否把孔分为电镀孔(PTH)、非电镀孔(NPTH)两类;以孔两侧可见与否把孔分为通孔(Through hole)、盲孔(Blind via)、埋孔(Buried via,埋孔通常是由通孔经层压而来),见图1。
就成孔方式来看,PCB业界采用过的成孔方式有:机械钻孔、机械冲孔、激光成孔、光致成孔、化学蚀刻、等离子蚀孔、导电柱穿孔等,目前应用相对较为广泛和成熟的成孔技术为:机械钻孔和激光成孔(注:业界常用“激光钻孔”,而非“激光成孔”,实际上“激光成孔”一词更要准确些(因为这是“光”加工的过程,不是“钻”加工的过程,故本文采用“激光成孔”这一说法)。
就目前PCB的技术发展状况而言,一般将孔径在0.3mm及以下的孔称为微孔(Micro-via),本文将对此类微孔进行探讨。对于微孔成孔,目前最常用的工艺有机械钻孔、CO2激光成孔、UV激光成孔三种。简单来说,微孔中的盲孔多采用激光成孔(CO2激光成较大孔,UV激光成较小孔);通孔(含埋孔)则多采用机械钻孔。
2.机械钻微孔技术
PCB机械钻微孔属超高速机械加工,目前主轴最高转速可达35万转/分。一般30万转/分的机械钻孔机每分钟可钻500个左右的 0.1mm的孔(注:此数据仅供参考,不同的加工条件钻孔速度差异较大)。一般机械钻孔可用于各种类型的PCB 微孔加工(如HDI、芯片级封装载板、FPC等)。下文将从钻头(物料)、工艺和质量三方面展开阐述。
2.1钻头
机械钻微孔中用到的主要物料为钻头(又名钻刀、钻针、钻嘴,“钻针”相对比较准确,本文沿用习惯用“钻头”这一称呼),它是机械钻微孔过程中用到的切削刀具。
PCB用钻头,一般刃部采用钨钴类合金(属硬质合金材料,目前钻头的制造有整体式、插入式和焊接式三种,插入式和焊接式的钻头柄部为不锈钢;刃部多采用外周倒锥和钻心倒锥的设计结构)。该合金以碳化钨(WC)粉末(88-94%,注:碳化钨已从原来的90%降到88%)[1]为基体,以钴(Co)(6-12%)为粘结剂,经高温、高压烧结而成,具有高硬度(主要来自碳化钨,硬度在92.5HRA以上,抗弯强度在4000N/mm2以上)和高耐磨性。调整碳化钨和钴的配比和碳化钨颗粒度大小,可以改变钻头的性能,微孔钻头一般钴含量要较其他钻头多一些。钴含量变化引起钻头性能变化的状况见表1。
资料来源:《现代印制电路基础》目前,PCB常用微孔钻头(有时简称微钻)刃部直径规格有0.075、0.1、0.15、0.2、0.25和0.3mm等,也有0.05mm及其他特殊直径规格,但相对较少。图2为日本佑能公司的钻头能力状况,其在2008年宣布可以试制Φ0.007mm的钻头(实际可供应的最小钻头直径为Φ0.02mm;中国大陆的金洲公司在2020年初宣布其突破Φ0.01mm的钻头,注:成年人头发直径约Φ0.07mm,Φ0.007mm的钻头直径是头发直径的十分之一)。
图2为日本佑能公司的钻头能力状况
资料来源:佑能官网微孔钻头柄径有两种:Φ2.0和Φ3.175mm,一般主轴转速30万转/分及以上的钻孔机多使用Φ2.0mm的钻头柄径;钻头刃部多为UC型(对钻头刃部进行修磨,以
减少棱刃与孔壁的摩擦);为了分散微孔钻头的应力集中现象,一般在钻头柄部与刃部之间加入了缓冲段,做成阶梯状。
微孔钻头的发展趋向是碳化钨晶粒度由目前的0.2μm向纳米级减小,结构上由双排屑改为单排屑(或者改为单刃型设计),增大螺旋角度,减小钻尖角等,以提高抗扭矩力和韧性,并保证硬度。另外,为了提高钻头硬度,减小摩檫,降低切削温度,目前正在开发微孔钻头表面强化(或者涂层)技术(此技术在大钻应用比较成熟),具体有电弧离子镀、离子注入、化学气相沉积(将特硬的碳化钛或氮化钛等化学沉积到碳化钨基体表面)和磁控溅射等技术[2]。
2.2工艺
机械钻微孔中需要关注的工艺参数主要有以下6个:
①转速/切削速度
转速:每分钟主轴旋转的圈数
切削速度:每分钟切削距离
②进刀速度/进刀量
进刀速度(也称作落速):每分钟主轴下降的距离
进刀量:主轴每旋转一圈所钻入的距离
③退回速度
退回速度(也称作提速):每分钟主轴提升的距离
④叠板数
影响叠板数的因素有:板层数、板厚、最小钻孔孔径、孔位公差要求、内层铜厚、孔环等,主要需要关注板层数、板厚、最小钻孔孔径。
⑤钻头状态
钻头状态包括钻头的研磨次数和钻孔数。随着微孔钻头的研磨次数增加,钻孔质量将逐渐变差,故钻孔数需要减少。由于更小的微孔钻头(如Φ0.1mm和Φ0.075mm的钻头)比较难研磨,故PCB厂家多数情况下使用一次就报废处理(最多可研磨一次,但相应的孔数要减少)。
⑥有效行程
有效钻孔行程是钻头下限值(Down值)和上限值(Up值)之间的差值;这一点有时易被忽略,但应注意:增加0.5mm的无效钻孔行程,对微孔钻孔可能会造成15%以上的产能损失。
机械钻孔工艺参数(钻削条件)对微孔加工、加工质量的影响见表2和3。
曾经有些公司推出了可进行盲孔加工的机械钻孔机(最精准的孔深精度控制在±12μm,见图3),但是随着激光成孔机的技术成熟和效率大幅提升,机械钻盲孔的应用愈来愈少(注:控制深度机械钻孔技术目前应用愈来愈多(高层板的背钻),但孔深精度要求不如钻盲孔高)。
图3 机械钻盲孔资料来源:The HDI Handbook(第一版)[4]
2.3质量缺陷机械钻微孔常见的质量缺陷有:孔大、孔小、多钻、漏钻、未钻透、偏孔、钉头(内层铜面两侧延伸的厚度大于铜厚的100%)、孔壁粗糙度超标、孔内毛刺、内层拉盘、内层破盘等。质量缺陷常用的检验工具有:①塞规:检查孔径大小;②标准胶片/底片:检查钻孔位置及有无多钻、少钻;③放大镜:检查孔口、孔壁状况;④检孔机:检查孔数量、孔径、孔位置精度;一般用在高层次PCB(例如载板)上的机械钻微孔的孔形(如孔壁粗糙度控制在≤25μm)、孔径(如孔径公差控制在+10μm/-20μm以内)、孔位(如孔位精度控制在≤±40μm(甚至≤±30μm))等质量要求普遍比较高。
3激光成孔技术
激光成孔兴起的主要原因是PCB布线越来越密,但传统的机械钻孔无法快速、稳定量产微盲孔的加工(减少通孔,增加盲孔是提高PCB密度的最有效的方法之一)等。下文将从激光原理、工艺和质量缺陷三方面展开阐述。
3.1激光原理
激光(Laser)是英语Light Amplification by Stimulated Emission of Radiation (通过受激辐射实现光放大)的缩写。世界上第一台激光器诞生于1960年。60多年