台车式燃气加热炉技术方案
燃气台车炉的技术方案2009

燃气台车炉的技术方案来源:中国金属加工在线() 作者:祝小双浏览次数:添加收藏发给好友燃气台车炉主要由炉体(包括炉衬)、炉门、炉车及驱动机构、燃烧系统、各管路及动力自控系统、炉压自控及排烟余热回收系统、密封装置、温度控制及记录系统等主要部分组成。
各部分技术关键点分别介绍如下:炉体:本炉由于需要安装中间闸门,考虑到其密封性,引进国外先进技术,对国外同型号燃气炉分析与研究,制定以下方案:壳体:()炉体框架:分前后剖两段制作,前段框架基础承重部位采用预埋钢板形式,框架与基础预埋钢板采用焊接连接,后段框架底部安装数对走轮,可以在预埋轨道上前后移动,框架采用槽钢和钢板焊接而成,柱间及柱顶之间用型钢拉住,形成完整的网架结构。
炉子框架上设有平台、扶梯。
炉体上所有需要检修、检查、操作和维护的部分有平台和安全扶梯。
()炉外壁采用钢板焊接,厚度≥。
炉体外观平直、美观、没有皱褶或凹凸不平现象。
炉体外部按相关标准刷两遍底漆,两遍面漆。
色标选择按行业通用标准,关键部位用耐中温漆。
衬衬:炉衬为全纤维结构,采用优质硅酸铝耐火纤维构筑,采用标准的锚固件及科学合理的镶装方法。
纤维折叠块镶装前进行再次预压缩处理(压缩容重≥),用锚固件固定在壳体上,保温材料安装厚度大于。
该结构具有低导热、低热溶优良的化学稳定性、热稳定性、抗热振性、优良的抗拉强度和抗腐蚀性。
硅酸铝纤维最高耐温℃,锚固件的材料选用材料冲压成型。
衬体制作完成后,表面有一层固化剂,形成一层隔热墙,增大衬体面的强度及热辐射性能,并进一步减小衬体畜热损失,达到快速升温的效果,最大限度提高炉子的热效率。
.炉门、中间闸门炉门、中间闸门结构及开闭机构直接影响炉子的使用寿命和炉子的气密性、炉温的均匀性及工件的加热质量。
在设计中我方采用以下措施防止炉门、中间闸门变形及保证炉门的整体密封。
.炉门炉门主体采用钢板焊接连接,交汇处采用圆形钢管与加强板焊接连接(国外炉子公司常在锻造加热炉上采用此技术),即为钢板的膨胀留有余地,又保证了炉门的整体刚性;炉门较大,采用分块软连接拼装技术,有效防止炉门变形;炉门密封的好坏是十分重要的,决定了炉内的温度场是否均匀,能量消耗的多少和厂房内环境温度,炉门上及左右三部分边缘采用软接触密封,四边采用型钢与钢板组合的框架结构;炉门压紧机构采用四联杆机构;采用电动葫芦升降方式提升炉门炉门设有上、下行程双保险机构及与台车的连锁机构,保证炉门运行平稳,安拿可靠。
20x4.5x3.5m台车式燃气热处理炉技术协议
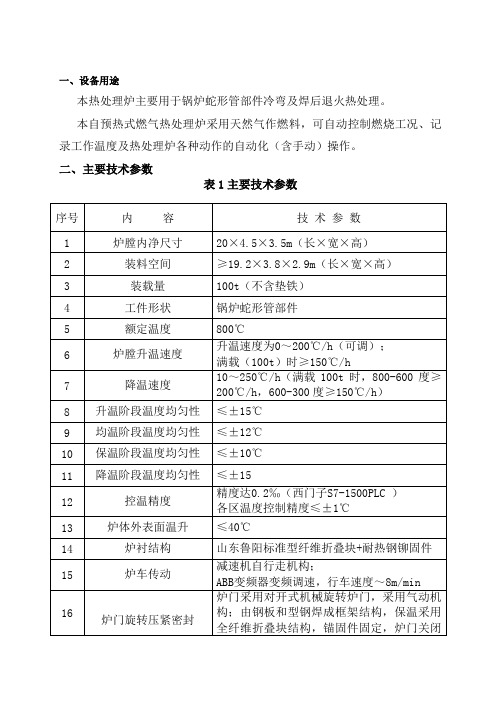
一、设备用途本热处理炉主要用于锅炉蛇形管部件冷弯及焊后退火热处理。
本自预热式燃气热处理炉采用天然气作燃料,可自动控制燃烧工况、记录工作温度及热处理炉各种动作的自动化(含手动)操作。
二、主要技术参数表1主要技术参数三、设备组成1、热处理炉本热处理炉主要由炉体、炉衬、炉门及炉门开启机构、密封装置、台车、热风循环系统、燃烧系统、天燃气管路、空气管路、冷却系统、排烟管路、密封装置及电气及自动控制系统等部分组成。
2、钢结构防雨棚和维修工装设备。
3、控制室、风机房等。
四、设备结构简述4.1、炉壳结构本炉采用箱式炉体结构。
炉体钢结构由型钢(槽钢、工字钢)及钢板(≥6mm)焊接组成,炉墙钢板按型钢框架自然分割,采用分离式拼接并与型钢框架间断焊接,避免钢板受热后发生整体变形;侧墙型钢立柱均按在受热情况下强度计算,选型恰当可靠;立柱下部与预埋钢板在施工现场焊接,上部与炉顶圈梁连接,这样整个炉体钢结构形成一整体框架结构,提高了强度,确保受力均衡。
炉体上的支架均焊在型钢或筋板上。
炉门框立柱采用型钢组合,截面为矩形的框架式结构,这样,钢结构整体重量较轻,抗弯强度高,钢性好,炉门柱上横梁根据承载负荷放大系数选定型钢,确保抗弯强度,并与立柱形成钢性框架,承载炉门升降的负荷和冲击。
炉顶采用型钢横梁结构,即炉顶周围采用型钢做出整体圈梁,横向排列的受力横梁端部与圈梁连接,承载整个炉顶耐火材料的重量,炉顶横梁型钢一律经过强度校算。
炉壳焊接检验后,炉体经过抛丸喷砂清洁处理后喷涂底漆一遍,面漆两遍,颜色为耐高温银粉漆,动力管道等系统喷涂符合国家标准。
炉门口部位温度较高,在炉口设置槽钢为底筋,再在底筋上固定耐热铸钢板,板外为固定的耐高温耐火纤维作为耐火层,有效地保护了炉门口的使用时间,炉口面板为提高炉口的耐火强度,增加炉口的高温强度,炉口面板采用厚度不小于20mm厚的RQTSi5.5耐热铸板,并且为了维修方便炉门采用分段,通过镶嵌式螺丝安装固定在炉门口外边框之上,在制作时分成多块制作,安装时留余量作为膨胀缝防止热变形,此种方式方便维修、维护,使用寿命长。
6m燃气台车退火炉技术方案700度

6×3×2.7m全纤维台车式燃气炉技术方案一、设备用途本台车式燃气热处理炉适用于一般规格的大中型铸件、钢锭及各种大中型金属制品、焊接件在750℃内的加热。
本台车式燃气热处理炉采用天然气作燃料,与燃烧系统、温控系统及程序控制系统配套使用,可自动控制燃烧工况、记录工作温度及热处理炉各种动作的自动化(含手动)操作。
本台车式燃气热处理炉每次可实现对50T各类工件的热处理。
二、设备组成本台车式燃气热处理炉由炉壳、炉衬、高承重自行式台车、台车牵引装置、轨道、炉门、炉门升降机构及气缸压紧密封装置、炉底侧气缸压紧密封装置、燃烧自动控制系统、余热回收系统、自动排烟系统、智能电气控制系统。
三、设备主要技术参数1、台车有效尺寸(长×宽): 6×3m2、炉膛有效高度(不含垫铁): 2.7m3、最高炉温: 750℃4、炉温均匀性:≤±10℃5、控温精度(炉温稳定):≤±5℃(保温状态)6、仪表精度:±0.25级7、升温速度:满负荷时升温速度为50-150℃/h可控8、台车载量: 30t(不含垫铁)9、燃料及热值:天然气0~8Kpa;(7800-8100Kcal/m3)10、炉衬结构:全纤维轻质复合结构11、台车耐火材料:台面高强耐磨浇注料12、炉体表面温升:≤50℃13、炉子热效率:≥40%14、燃烧方式:大小火时序脉冲式燃烧方式、燃气自动点火功能、火焰检测、熄火保护。
15、控制方式:宇电智能仪表分区自动控温+ 工控机上位机集中管理监控对台车式热处理炉实现多区的脉冲控制自动控制,并可手动控制16、烧嘴型号、数量: SIC140;320KW ; 8只17、烧嘴类型: 120-160m/s;高速烟气低NOX排放烧嘴18、设备能源消耗供电参数:380V±10% 50Hz±2.5 3相燃料耗量:255Nm3/h空气消耗量:2720Nm3/ h烟气量:2950Nm3/ h 压力4~6kPa19、预热空气温度: 250-300℃20、燃气烧嘴前压力: 5~8kPa21、燃气供气压力: 30~40kPa22、烧嘴前空气压力: 8~11kPa23、热电偶: K型热电偶测温、记录监测炉温24、加热炉风机工作区噪音:≤75db25、控温分区: 4区(两嘴一区)26、放散系统:在天然气管道末端设有放散系统,用于起炉前的放散以保证燃气燃烧安全。
1.5x1.5x1.5m翻转台车燃气炉

1.5×1.5×1.5m全纤维翻转台车燃气炉技术方案2016年12月一、设备用途本台车式燃气热处理炉主要适用于中小型金属制品、结构件进行退火、不锈钢固溶、精密铸造模壳烧结、其他加热及随炉冷却的专用设备。
本台车式燃气热处理炉采用天然气作燃料,与燃烧系统、温控系统及程序控制系统配套使用,可自动控制燃烧工况、记录工作温度及热处理炉各种动作的自动化(含手动)操作。
本台车式燃气热处理炉每次可实现对5T各类工件的热处理。
二、设备组成本台车式燃气热处理炉由炉壳、炉衬、高承重自行式台车牵引装置、轨道、炉门、台车液压翻转装置、燃烧自动控制系统、余热回收系统、排烟系统、智能电气控制系统。
三、设备主要技术参数1、台车有效尺寸(长×宽): 1.5×1.5m2、炉膛高度(含垫铁): 1.8m3、设备装机总功率:≤12kw4、最高炉温:1200℃5、炉温均匀性:≤±10℃6、控温精度:≤±1℃(保温状态)7、升温速度:满负荷时升温速度为80-200℃/h可控8、台车承载量:5t9、燃料及热值:天然气0~8Kpa;~8600Kcal/m310、炉衬结构:硅酸铝全纤维折叠块,耐热钢锚固件固定。
11、最大燃料量:60 m3/h12、烧嘴前助燃空气压力:5-6KPa13、烧嘴类型: SIO-125高速烧嘴14、控温分区:2区2个烧嘴、 1个烧嘴一区15、台车行走机构:车轮式自行走机构,电机通过减速机驱动16、炉门装置:台车炉门一体化设计17、炉壁温升:≤45℃+环境温度18、热电偶: K型热电偶测温、控制炉温19、供电参数:380V±10% 50Hz±2.5 3相20、最大空气消耗量: 600 m3/h21、最大烟气量: 660m3/h22、燃烧控制方式:大小火PID脉冲燃烧控制、可手动、自动操作。
烧嘴自动点火、自动升温(保温)火焰监测、熄火自动保护。
台车式燃气热处理炉技术要求
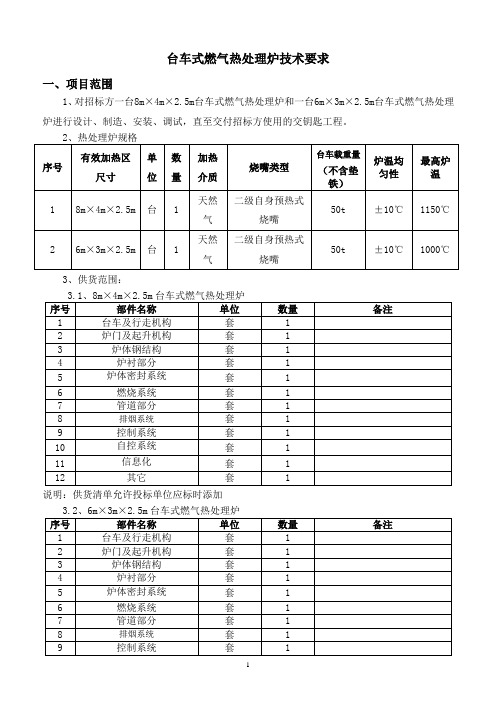
台车式燃气热处理炉技术要求一、项目范围1、对招标方一台8m×4m×2.5m台车式燃气热处理炉和一台6m×3m×2.5m台车式燃气热处理炉进行设计、制造、安装、调试,直至交付招标方使用的交钥匙工程。
3、供货范围:说明:供货清单允许投标单位应标时添加说明:供货清单允许投标单位应标时添加二、现场条件:1、电源参数:电压:380V±15%AC 220V±15%AC 电源频率:50Hz;2、起吊高度:行车底部标高 +13.5m;3、生产制度:四班三运转制;4、燃烧介质:天然气;炉体调压器前燃气压力:90kPa;;天然气:低热值H:8430Kcal/Nm3,三、8m×4m×2.5m台车式燃气热处理炉主要技术参数四、6m×3m×2.5m台车式燃气热处理炉主要技术参数五、主要技术要求台车式燃气热处理炉主要由全纤维炉体、全纤维炉门、炉车、燃烧系统、排烟系统、密封系统、自控系统、上位工控计算机集散控制系统等主要部分组成。
1)、炉体钢结构(1)、炉体钢结构采用国标方型钢、钢板焊接而成,炉门钢柱采用δ=12mm钢板焊接而成,其材料的选用必须是有质量合格证的正规厂家生产,材料Q235A。
炉体维护钢板厚度δ≥6mm,炉体钢结构的制造应满足国家相关制造标准要求,其焊缝部位均匀饱满,棱角部位圆滑过度。
在炉体结构的设计上应充分考虑到高温热膨胀、冷态收缩对结构的影响,确保炉子在频繁升温、降温状态下不允许产生弯曲变形等缺陷。
炉体钢构使用寿命20年以上。
(2)、8m×4m×2.5m热处理炉炉体、炉口护板3Cr24Ni7SiN耐热钢,厚度应≥25mm,炉后护板ZG30Cr18Mn12Si2N(铬锰氮铸钢件),两块间安装间隙≤15mm。
6m×3m×2.5m热处理炉炉体、炉口、炉后护板采用Z G30Cr18Mn12Si2N(铬锰氮铸钢件),厚度应≥25mm,两块间安装间隙≤15mm。
台车式燃气加热炉技术方案
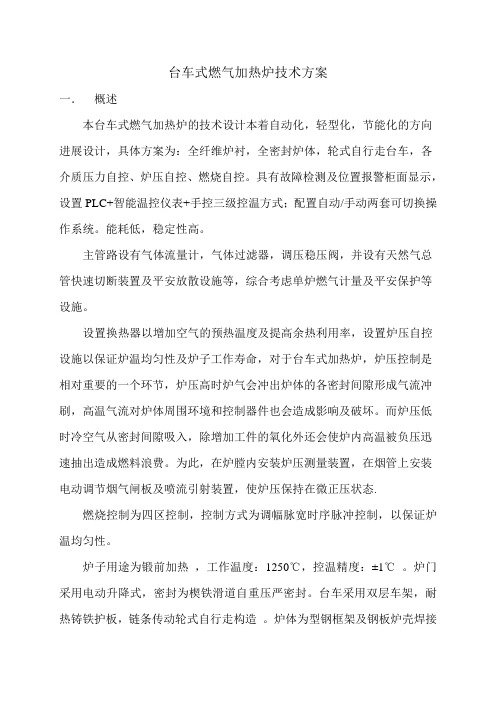
台车式燃气加热炉技术方案一.概述本台车式燃气加热炉的技术设计本着自动化,轻型化,节能化的方向进展设计,具体方案为:全纤维炉衬,全密封炉体,轮式自行走台车,各介质压力自控、炉压自控、燃烧自控。
具有故障检测及位置报警柜面显示,设置PLC+智能温控仪表+手控三级控温方式;配置自动/手动两套可切换操作系统。
能耗低,稳定性高。
主管路设有气体流量计,气体过滤器,调压稳压阀,并设有天然气总管快速切断装置及平安放散设施等,综合考虑单炉燃气计量及平安保护等设施。
设置换热器以增加空气的预热温度及提高余热利用率,设置炉压自控设施以保证炉温均匀性及炉子工作寿命,对于台车式加热炉,炉压控制是相对重要的一个环节,炉压高时炉气会冲出炉体的各密封间隙形成气流冲刷,高温气流对炉体周围环境和控制器件也会造成影响及破坏。
而炉压低时冷空气从密封间隙吸入,除增加工件的氧化外还会使炉内高温被负压迅速抽出造成燃料浪费。
为此,在炉膛内安装炉压测量装置,在烟管上安装电动调节烟气闸板及喷流引射装置,使炉压保持在微正压状态.燃烧控制为四区控制,控制方式为调幅脉宽时序脉冲控制,以保证炉温均匀性。
炉子用途为锻前加热,工作温度:1250℃,控温精度:±1℃。
炉门采用电动升降式,密封为楔铁滑道自重压严密封。
台车采用双层车架,耐热铸铁护板,链条传动轮式自行走构造。
炉体为型钢框架及钢板炉壳焊接构造,炉墙底部炉衬为耐火浇注料,炉墙及炉顶为纤维炉衬。
炉子各缝隙的密封为双重密封,第一重:台车与炉墙之间为迷宫式配合缝,形成摭档式密封;第二道压紧式密封:侧密封为气缸驱动升降式软密封,尾部密封为机械式弹簧压紧软密封。
炉子的排烟方式暂按尾部上排烟设计。
二..主要工艺参数2.1 工作区尺寸:6000×2500×2500mm〔L×W×H〕。
2. 2 温度均匀性:1250℃≤±15℃;2. 3控温精度:±1℃2.4最高炉温:1300℃2.5满载升温速度:≥200℃/h2.6炉底承载能力:60t。
工业台车式天然气加热炉设计要点分析
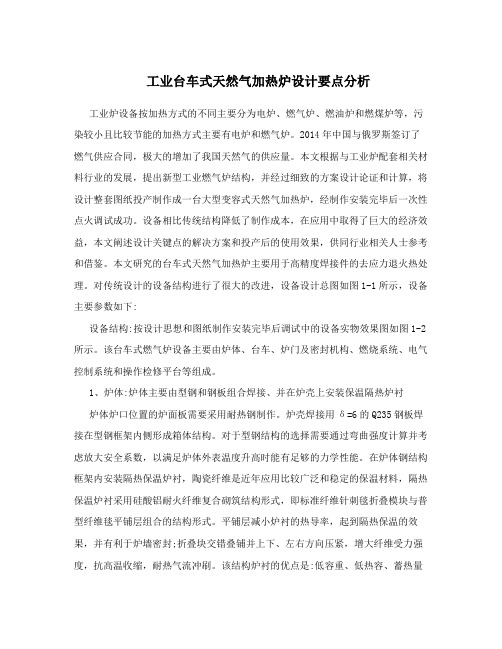
工业台车式天然气加热炉设计要点分析工业炉设备按加热方式的不同主要分为电炉、燃气炉、燃油炉和燃煤炉等,污染较小且比较节能的加热方式主要有电炉和燃气炉。
2014年中国与俄罗斯签订了燃气供应合同,极大的增加了我国天然气的供应量。
本文根据与工业炉配套相关材料行业的发展,提出新型工业燃气炉结构,并经过细致的方案设计论证和计算,将设计整套图纸投产制作成一台大型变容式天然气加热炉,经制作安装完毕后一次性点火调试成功。
设备相比传统结构降低了制作成本,在应用中取得了巨大的经济效益,本文阐述设计关键点的解决方案和投产后的使用效果,供同行业相关人士参考和借鉴。
本文研究的台车式天然气加热炉主要用于高精度焊接件的去应力退火热处理。
对传统设计的设备结构进行了很大的改进,设备设计总图如图1-1所示,设备主要参数如下:设备结构:按设计思想和图纸制作安装完毕后调试中的设备实物效果图如图1-2所示。
该台车式燃气炉设备主要由炉体、台车、炉门及密封机构、燃烧系统、电气控制系统和操作检修平台等组成。
1、炉体:炉体主要由型钢和钢板组合焊接、并在炉壳上安装保温隔热炉衬炉体炉口位置的炉面板需要采用耐热钢制作。
炉壳焊接用δ=6的Q235钢板焊接在型钢框架内侧形成箱体结构。
对于型钢结构的选择需要通过弯曲强度计算并考虑放大安全系数,以满足炉体外表温度升高时能有足够的力学性能。
在炉体钢结构框架内安装隔热保温炉衬,陶瓷纤维是近年应用比较广泛和稳定的保温材料,隔热保温炉衬采用硅酸铝耐火纤维复合砌筑结构形式,即标准纤维针刺毯折叠模块与普型纤维毯平铺层组合的结构形式。
平铺层减小炉衬的热导率,起到隔热保温的效果,并有利于炉墙密封;折叠块交错叠铺并上下、左右方向压紧,增大纤维受力强度,抗高温收缩,耐热气流冲刷。
该结构炉衬的优点是:低容重、低热容、蓄热量小,大大缩短了窑炉的升温时间;节能效果明显,低导热、绝热好,有效地节约了电耗成本并改善炉子的环境;良好的抗热震性和机械强度。
台车式加热炉设计计算1
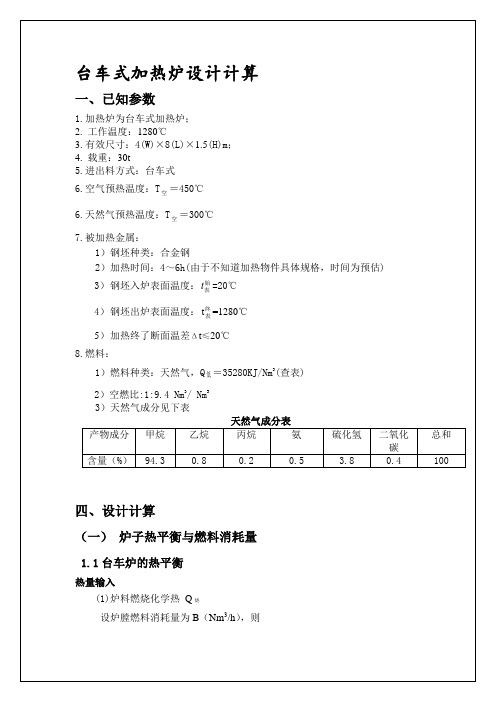
查表t空=300℃时,c燃气=2.63kJ/(Nm3.℃)
Q燃气=(1-K)BLnc空t空=(1-0.02)×B1×300×2.63=773BkJ/h
热量支出
(1)金属吸收的热量Q1
查表t=1280℃时J2= 800.1kJ/kg;
t=20℃时J1=11.1kJ/kg;
22613B1
Kj/h
5
冷却水带走的热量
580323
Kj/h
总计
46728B1
总计
1316712+22613B1
均热段热平衡表
台车式加热炉设计计算一、已知参数来自1.加热炉为台车式加热炉;
2.工作温度:1280℃
3.有效尺寸:4(W)×8(L)×1.5(H)m;
4.载重:30t
5.进出料方式:台车式
6.空气预热温度:T =450℃
6.天然气预热温度:T =300℃
7.被加热金属:
1)钢坯种类:合金钢
2)加热时间:4~6h(由于不知道加热物件具体规格,时间为预估)
砌砖体的平均温度
砌砖体的平均导热率:
λ3=0.84+0.58×10-3×1265=1.571×3.6
λ2=0.291+0.256×10-3×1037.5=0.5566×3.6
λ1=0.05+0.07×10-6×482.52=0.0663×3.6
炉墙单位面积的热损失:
炉墙外表温度 ℃
第一层分界面温度: ℃
3)钢坯入炉表面温度: =20℃
4)钢坯出炉表面温度: =1280℃
5)加热终了断面温差Δt≤20℃
8.燃料:
1)燃料种类:天然气,Q =35280KJ/Nm3(查表)
大型台车式天然气高温热处理炉技术参数
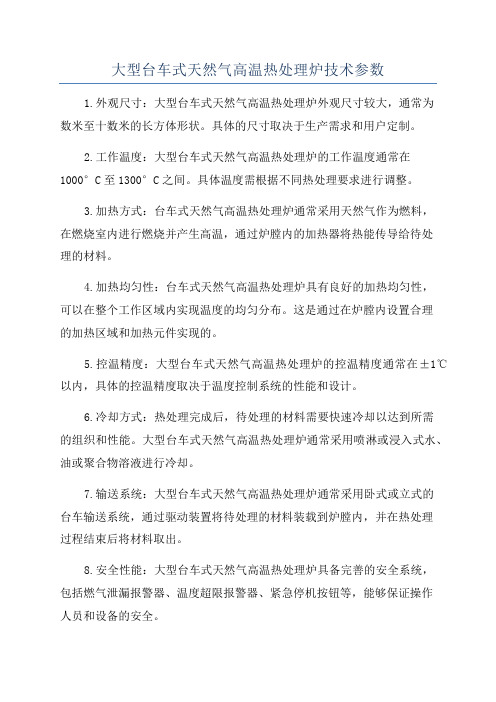
大型台车式天然气高温热处理炉技术参数1.外观尺寸:大型台车式天然气高温热处理炉外观尺寸较大,通常为数米至十数米的长方体形状。
具体的尺寸取决于生产需求和用户定制。
2.工作温度:大型台车式天然气高温热处理炉的工作温度通常在1000°C至1300°C之间。
具体温度需根据不同热处理要求进行调整。
3.加热方式:台车式天然气高温热处理炉通常采用天然气作为燃料,在燃烧室内进行燃烧并产生高温,通过炉膛内的加热器将热能传导给待处理的材料。
4.加热均匀性:台车式天然气高温热处理炉具有良好的加热均匀性,可以在整个工作区域内实现温度的均匀分布。
这是通过在炉膛内设置合理的加热区域和加热元件实现的。
5.控温精度:大型台车式天然气高温热处理炉的控温精度通常在±1℃以内,具体的控温精度取决于温度控制系统的性能和设计。
6.冷却方式:热处理完成后,待处理的材料需要快速冷却以达到所需的组织和性能。
大型台车式天然气高温热处理炉通常采用喷淋或浸入式水、油或聚合物溶液进行冷却。
7.输送系统:大型台车式天然气高温热处理炉通常采用卧式或立式的台车输送系统,通过驱动装置将待处理的材料装载到炉膛内,并在热处理过程结束后将材料取出。
8.安全性能:大型台车式天然气高温热处理炉具备完善的安全系统,包括燃气泄漏报警器、温度超限报警器、紧急停机按钮等,能够保证操作人员和设备的安全。
9.控制系统:大型台车式天然气高温热处理炉配备先进的控制系统,可以实现自动化操作和远程监控。
控制系统通常包括温度控制、时间控制、运行状态显示等功能。
总之,大型台车式天然气高温热处理炉具有高温工作、加热均匀、控温精度高、冷却快速等特点,能够满足各种金属材料的热处理要求,并具备安全可靠的性能。
在工业生产中发挥着重要的作用。
燃气双台车式热处理炉的设计与应用

燃气双台车式热处理炉的设计与应用
燃气双台车式热处理炉是一种新型的热处理设备,它具有自动化运作、能耗低、热处理效果优良等特点,被广泛应用于机械、建材、化工、陶瓷
等领域。
该炉采用两个独立的工作台,加热炉膛采用燃气加热方式,在高温下
对工件进行热处理,可以有效地改善材料性能,提高产品的质量和使用寿命。
该炉的设计和应用需要考虑以下几个方面:
1.炉膛设计:炉膛应具有足够的容量和均匀的温度分布,能够容纳不
同尺寸和形状的工件,并实现热处理工艺要求。
2.控制系统设计:炉膛采用PLC控制系统,可实现自动、精确的控制,通过实时监测温度、压力、时间等参数,对加热程序进行调整,确保热处
理过程的稳定性和真实性。
3.安全性设计:炉膛应该具有完整的安全保护系统,如温度保护、压
力保护、过载保护等,以确保操作人员和设备的安全。
4.应用领域:燃气双台车式热处理炉适用于各种高温热处理工艺,特
别是对大型、复杂形状的工件,如汽车零部件、铸件、轴承、模具等具有
良好的适用性。
总之,燃气双台车式热处理炉的设计和应用,需要考虑炉膛设计、控
制系统设计、安全性设计以及应用领域的因素,通过优化设计和创新技术,实现更高效、更精确的高温热处理过程,为工业生产带来更加可靠且高品
质的产品。
燃气台车炉的技术方案2009【最新范本模板】
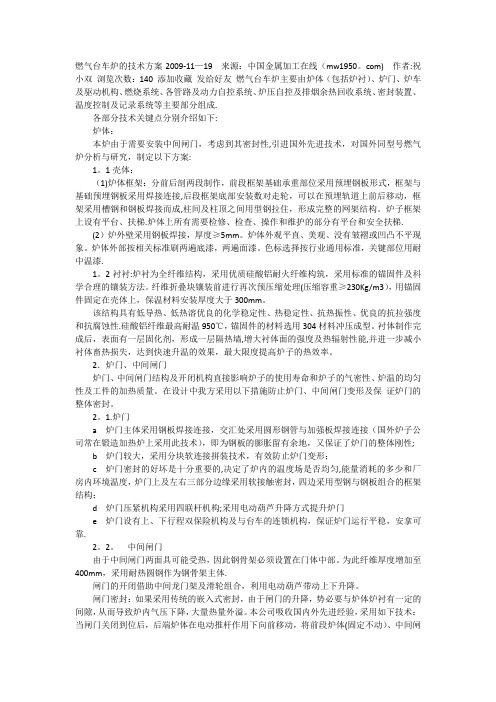
燃气台车炉的技术方案2009-11—19 来源:中国金属加工在线(mw1950。
com) 作者:祝小双浏览次数:140 添加收藏发给好友燃气台车炉主要由炉体(包括炉衬)、炉门、炉车及驱动机构、燃烧系统、各管路及动力自控系统、炉压自控及排烟余热回收系统、密封装置、温度控制及记录系统等主要部分组成.各部分技术关键点分别介绍如下:炉体:本炉由于需要安装中间闸门,考虑到其密封性,引进国外先进技术,对国外同型号燃气炉分析与研究,制定以下方案:1。
1壳体:(1)炉体框架:分前后剖两段制作,前段框架基础承重部位采用预埋钢板形式,框架与基础预埋钢板采用焊接连接,后段框架底部安装数对走轮,可以在预埋轨道上前后移动,框架采用槽钢和钢板焊接而成,柱间及柱顶之间用型钢拉住,形成完整的网架结构。
炉子框架上设有平台、扶梯.炉体上所有需要检修、检查、操作和维护的部分有平台和安全扶梯.(2)炉外壁采用钢板焊接,厚度≥5mm。
炉体外观平直、美观、没有皱褶或凹凸不平现象。
炉体外部按相关标准刷两遍底漆,两遍面漆。
色标选择按行业通用标准,关键部位用耐中温漆.1。
2衬衬:炉衬为全纤维结构,采用优质硅酸铝耐火纤维构筑,采用标准的锚固件及科学合理的镶装方法。
纤维折叠块镶装前进行再次预压缩处理(压缩容重≥230Kg/m3),用锚固件固定在壳体上,保温材料安装厚度大于300mm。
该结构具有低导热、低热溶优良的化学稳定性、热稳定性、抗热振性、优良的抗拉强度和抗腐蚀性.硅酸铝纤维最高耐温950℃,锚固件的材料选用304材料冲压成型。
衬体制作完成后,表面有一层固化剂,形成一层隔热墙,增大衬体面的强度及热辐射性能,并进一步减小衬体畜热损失,达到快速升温的效果,最大限度提高炉子的热效率。
2.炉门、中间闸门炉门、中间闸门结构及开闭机构直接影响炉子的使用寿命和炉子的气密性、炉温的均匀性及工件的加热质量。
在设计中我方采用以下措施防止炉门、中间闸门变形及保证炉门的整体密封。
台车式加热炉技术改造
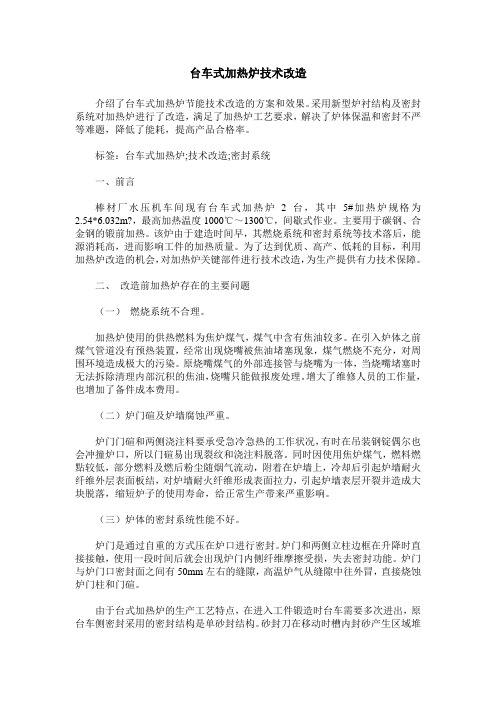
台车式加热炉技术改造介绍了台车式加热炉节能技术改造的方案和效果。
采用新型炉衬结构及密封系统对加热炉进行了改造,满足了加热炉工艺要求,解决了炉体保温和密封不严等难题,降低了能耗,提高产品合格率。
标签:台车式加热炉;技术改造;密封系统一、前言棒材厂水压机车间现有台车式加热炉2台,其中5#加热炉规格为2.54*6.032m?,最高加热温度1000℃~1300℃,间歇式作业。
主要用于碳钢、合金钢的锻前加热。
该炉由于建造时间早,其燃烧系统和密封系统等技术落后,能源消耗高,进而影响工件的加热质量。
为了达到优质、高产、低耗的目标,利用加热炉改造的机会,对加热炉关键部件进行技术改造,为生产提供有力技术保障。
二、改造前加热炉存在的主要问题(一)燃烧系统不合理。
加热炉使用的供热燃料为焦炉煤气,煤气中含有焦油较多。
在引入炉体之前煤气管道没有预热装置,经常出现烧嘴被焦油堵塞现象,煤气燃烧不充分,对周围环境造成极大的污染。
原烧嘴煤气的外部连接管与烧嘴为一体,当烧嘴堵塞时无法拆除清理内部沉积的焦油,烧嘴只能做报废处理。
增大了维修人员的工作量,也增加了备件成本费用。
(二)炉门碹及炉墙腐蚀严重。
炉门门碹和两侧浇注料要承受急冷急热的工作状况,有时在吊装钢锭偶尔也会冲撞炉口,所以门碹易出现裂纹和浇注料脱落。
同时因使用焦炉煤气,燃料燃點较低,部分燃料及燃后粉尘随烟气流动,附着在炉墙上,冷却后引起炉墙耐火纤维外层表面板结,对炉墙耐火纤维形成表面拉力,引起炉墙表层开裂并造成大块脱落,缩短炉子的使用寿命,给正常生产带来严重影响。
(三)炉体的密封系统性能不好。
炉门是通过自重的方式压在炉口进行密封。
炉门和两侧立柱边框在升降时直接接触,使用一段时间后就会出现炉门内侧纤维摩擦受损,失去密封功能。
炉门与炉门口密封面之间有50mm左右的缝隙,高温炉气从缝隙中往外冒,直接烧蚀炉门柱和门碹。
由于台式加热炉的生产工艺特点,在进入工件锻造时台车需要多次进出,原台车侧密封采用的密封结构是单砂封结构。
- 1、下载文档前请自行甄别文档内容的完整性,平台不提供额外的编辑、内容补充、找答案等附加服务。
- 2、"仅部分预览"的文档,不可在线预览部分如存在完整性等问题,可反馈申请退款(可完整预览的文档不适用该条件!)。
- 3、如文档侵犯您的权益,请联系客服反馈,我们会尽快为您处理(人工客服工作时间:9:00-18:30)。
6x2.5x2.5台车式燃气加热炉技术方案一.概述本台车式燃气加热炉的技术设计本着自动化,轻型化,节能化的方向进行设计,具体方案为:全纤维炉衬,全密封炉体,轮式自行走台车,各介质压力自控、炉压自控、燃烧自控。
具有故障检测及位置报警柜面显示,设置PLC+智能温控仪表+手控三级控温方式;配置自动/手动两套可切换操作系统。
能耗低,稳定性高。
主管路设有气体流量计,气体过滤器,调压稳压阀,并设有天然气总管快速切断装置及安全放散设施等,综合考虑单炉燃气计量及安全保护等设施。
设置换热器以增加空气的预热温度及提高余热利用率,设置炉压自控设施以保证炉温均匀性及炉子工作寿命,对于台车式加热炉,炉压控制是相对重要的一个环节,炉压高时炉气会冲出炉体的各密封间隙形成气流冲刷,高温气流对炉体周围环境和控制器件也会造成影响及破坏。
而炉压低时冷空气从密封间隙吸入,除增加工件的氧化外还会使炉内高温被负压迅速抽出造成燃料浪费。
为此,在炉膛内安装炉压测量装置,在烟管上安装电动调节烟气闸板及喷流引射装置,使炉压保持在微正压状态.燃烧控制为四区控制,控制方式为调幅脉宽时序脉冲控制,以保证炉温均匀性。
炉子用途为锻前加热,工作温度:1250℃,控温精度:±1℃。
炉门采用电动升降式,密封为楔铁滑道自重压紧密封。
台车采用双层车架,耐热铸铁护板,链条传动轮式自行走结构。
炉体为型钢框架及钢板炉壳焊接结构,炉墙底部炉衬为耐火浇注料,炉墙及炉顶为纤维炉衬。
炉子各缝隙的密封为双重密封,第一重:台车与炉墙之间为迷宫式配合缝,形成摭档式密封;第二道压紧式密封:侧密封为气缸驱动升降式软密封,尾部密封为机械式弹簧压紧软密封。
炉子的排烟方式暂按尾部上排烟设计。
二..主要工艺参数2.1 工作区尺寸:6000×2500×2500mm(L×W×H)。
2. 2 温度均匀性:1250℃≤±15℃;2. 3控温精度:±1℃2.4最高炉温:1300℃2.5满载升温速度:≥200℃/h2.6炉底承载能力:60t。
三. 主要技术参数3.1炉膛内尺寸:6696⨯3196⨯2500mm (长⨯宽⨯高)3.2燃料种类及热值:天然气(热值33.24MJ/Nm3,压力4-6kpa)3.3燃气消耗量:480Nm3/h3.4空气消耗量:(4320+1000)Nm3/h3.5 总电力需求:~35KW3.6台车传动形式:车轮式自行走机构;3.7炉门开关形式:升降式炉门,采用电动葫芦升降3.8炉门密封方式:利用炉门自重自动压紧方式3.9排烟方式:上排烟3.10 空气预热形式:采用复合式金属预热器预热3.11烧嘴形式:Krom BIO型高速烧嘴(底燃式)3.12烧嘴数量及功率:8 每只烧嘴功率为630KW3.13炉墙表面温升:侧墙≤40℃;炉顶≤50℃3.14控制模式:脉冲燃烧控制3.15助燃风温度:≥200℃3.16炉膛气氛:微氧化四. 设备组成及功能:本设备主要由炉体钢结构、炉衬﹑台车及行走、炉门及升降、密封、燃烧、排烟及控制系统等部分组成。
4.1炉体钢结构:4.1.1根据炉衬及其相关设施的要求,采用钢板及型钢焊接而成,并严格控制焊接变形,保证炉子的刚度和强度。
4.1.2炉墙钢板厚度≥6mm4.1.3炉门框采用耐热铸铁件。
4.2炉衬4.2.1纤维炉衬采用山东鲁阳含锆及多晶陶纤维复合折叠模块锚固(LYGX-589 1400℃)。
4.2.2炉墙及炉顶采用全纤维结构,保证其隔热性能好,抗冲刷能力强。
纤维厚度为320mm,炉膛直接接触的为240mm厚锆铝纤维组块,内侧平铺80mm厚的多晶硅酸铝耐火纤维。
4.2.3台车面采用低水泥浇注料+保温隔热砖+陶瓷纤维毡组成的复合结构。
台车面浇注料与炉墙形成第一道迷宫式密封。
第二道活动侧密封采用气动压紧陶瓷纤维毯柔性体。
后密封采用弹簧压紧纤维密封块。
4.2.4台车面低水泥浇注料预留收缩缝保证其台车的强度足够支撑工件。
4.3台车及行走台车采用车轮式自行走机构。
4.3.1 台车行走速度<10m/min,由电动机和减速机等部件组成驱动机构,采用自动收放电缆供电。
4.3.2 台车尾部远离热源处设置限位开关,同时在轨道上焊接机械限位挡块。
以确保设备安全。
4.3.3 台车动作可靠,控制自如,使用寿命长。
4.4炉门及升降4.4.1 炉门开关形式:电动上启式(提升开启),由多功能电动葫芦驱动,提升能力3T、炉门行程2.6m、升降速度10m/min。
4.4.2 炉门采用钢板焊接件,四周外框为耐热不锈钢板(1Gr18Ni9Ti,δ≥16mm)。
内衬用山东鲁阳含锆陶纤维及多晶纤维复合折叠模块锚固(LYGX-589 1400℃)。
4.4.3 钢结构件焊接成框架,保证长期高温条件下使用不变形或变形量小。
4.4.4 炉门通过自重压紧,斜契压紧装置和滑道安装在炉架前支柱上,使炉门与炉体间密封良好。
4.4.5 炉门隔热采用复合纤维结构。
4.4.6 炉门口内侧采取防冲撞设计,防止意外冲撞引起损坏。
4.4.7炉门外侧设置两个防爆口。
4.5密封:4.5.1 炉门与台车密封采用纤维柔性密封。
4.5.2 台车密封:本炉各部密封均采用柔性密封块形式,具有密封性好,便于维护调整等特点。
台车与炉体间侧隙采用迷宫缝加气动压紧(或电动推杆压紧)柔性密封装置,其机构形式为杠杆式,当台车进炉后,装有耐火纤维的柔性密封块在气缸(电动推杆)的作用下压紧炉体和台车的耐热铸铁护板上的密封刀口, 从而封住两护板间的缝隙, 防止高温炉气的外溢。
炉体两侧及炉尾共安装4个125气缸,连接杠杆作用的压杆,压杆抬起密封槽(密封槽为П形),可使密封槽内的耐火纤维与密封刀压紧,从而封住炉气。
4.5.3. 如果密封槽为”Ⅱ”型,则台车后密封通过弹簧自动压紧密封。
台车拉进时,台车后部将接触与弹簧连接的密封块,弹簧被压缩,靠弹簧的反作用力使台车密封。
4.5.4 后密封装置处于侧密封装置密封面上,可通过侧密封装置将炉后两角处间隙密封住,使得密封效果更好。
4.5.5炉前端台车与炉口两侧的竖缝隙,通过焊接在台车两侧的堵头内的耐火纤维压紧密封。
4.6燃烧系统:4.6.1排烟方式:尾部上排烟,在炉后墙适当高度处设一孔排烟口,通过支烟管和换热器相连,经换热器后进入烟。
4.6.2 空气预热器选用复合式金属热交换器。
4.6.3 在换热器上方设有引射排烟装置,可以通过调节引射风的大小调节炉压,同时烟囟上装有电动蝶阀,可以自动通过开度来调节炉压.4.6.4 烟气排放符合GB9078-88一级标准。
风机噪声符合GBJ87-85标准。
4.6.5 助燃风机选用国产知名名牌的高压离心风机,品质精良,质量可靠。
助燃风总管设有压力开关,测量助燃风压,经压力变器送至SR93智能仪表,与设定风压比较后通过PID运算,给变频器信号控制风机转速来调风压。
空气经预热器预热后进入烧嘴助燃。
热风管用陶瓷纤维毯保温隔热、镀锌铁皮锚固保护,保证表面温度小于40℃。
4.6.6在炉前空气管路的末端安装防爆装置。
从而提高了炉子的安全使用性。
4.6.7本炉设计采用8个高速烧嘴,均匀交错布置于炉子台车面上部(炉膛底部两侧),保证供热均匀。
4.6.8台车面上放置料架,其高度大于火焰直径的两倍,确保火焰不直接喷射到加热工件上。
同时,采用大小火控制方式,保证炉温均匀性,可实现炉温的精确控制,在进入保温段后期烧嘴自动调整燃烧状态,可实现保温控制。
4.6.9烧嘴配备自动点火装置, 包括烧嘴控制器、点火变压器等设备可实现自动点火和火焰监测功能。
为保证供热均匀性,各烧嘴的排布上交错均匀排布,有效避免升温时造成因个别烧嘴的强供热所造成工件局部表面温度过热的现象。
4.6.10烧嘴选用德国KROM高速烧嘴,空燃气是在烧嘴内完成混合和燃烧的,燃烧产生的高温烟气通过烧嘴的喷口高速喷出,速度可达70m/s以上。
高速流动的炉气引射周围的气体,使炉内的气体循环量大为增加,对炉内气体的搅拌作用十分强烈,使炉内的温差缩小,炉温分布均匀,并且由于炉气和工件间相对速度增加,使换热速度提高,燃耗降低。
4.6.11 燃气主管道系统按燃气安全技术标准配置,设有手动球阀、过滤器、切断阀、主管电磁阀,气体流量计、压力表,放散系统等装置,实现过滤、高压切断、低压切断、燃气计量、安全连锁等功能,保证安全生产。
炉前燃气管路分布于炉体两侧烧嘴上方。
每个烧嘴嘴前燃气支管配备手动燃气球阀、燃气切断阀及比例阀。
每个烧嘴前空气支管配备脉冲控制空气蝶阀和手动蝶阀。
4.7自控系统4.7. 1燃烧设备炉体两侧配备8台高速烧嘴进行供热,烧嘴配备自动点火装置。
为保证供热均匀性,各烧嘴的排布上应交错均匀排布,有效避免升温时造成因个别烧嘴的强供热所造成工件局部表面温度过热的现象,保证工件表面加热质量。
4.7. 2燃烧控制将台车炉炉沿纵向均分为4个控制段,每段2只烧嘴。
每段温度控制采用由PLC脉冲控制的脉冲式燃烧方式,采用先进的脉宽调制的方法,温度输入控制信号为已经过PID计算的信号,在PLC程序中按输入百分比表示(0%~100%),PLC输出脉冲控制信号,此信号按预先设定的控制周期由输出的线性百分比信号分配了大、小火各自的燃烧时间,PLC通过直接控制空气阀的开度及持续时间来实现大小火在执行完所分配的时间后切换,从而实现灵活的脉冲控制。
当在快速升温阶段,如果实测温度赶不上设定温度曲线,则一个控制周期接一个控制周期都分配了100%的大火时间,这样便接近实现了连续燃烧,只有在设定温度附近才开始真正意义上的脉冲燃烧。
这种燃烧方式的优点是可较好的控制炉膛内温度的均匀性,通过强烈搅拌炉气的循环保证温度场的分布均匀,经分段后炉内各点温度可保证升温速率的一致。
4.7. 3脉冲控制原理介绍:4.7.3.1 脉冲控制方式是目前国际最先进的车底式炉的控制方式。
在脉冲燃烧控制系统中,烧嘴只工作在开/关(或大火/小火)两种状态下,用户可根据对烧嘴的功率、混合比,喷出速度等要求将烧嘴一次性调到最佳状态,这样每次启动烧嘴时,烧嘴都处于最佳工作状态,对于提高燃烧效率和降低排放物污染水平都具有明显效果。
通过多个烧嘴配合工作产生的热气流可在炉内产生分布均匀的温度场,提高被处理工件的加热质量和和温度均匀性。
这种先进的控制模式在冶金和机械热处理行业都有着广泛的应用。
4.7.3.2点火时序:烧嘴点火分为自动和手动两种方式。
在手动情况下,操作工可以在现场通过烧嘴控制器上的点火按钮给出点火指令,烧嘴控制器得到点火指令后,点火变压器得电放出点火电弧,同时燃气电磁阀打开将燃气送入烧嘴,点火时间根据不同的烧嘴控制器有所区别,一般点火时间持续在5秒钟左右。
在点火期间,如果烧嘴点火成功,点火变压器自动断电,燃气电磁阀保持打开,同时在烧嘴控制器和控制柜上有烧嘴运行(燃烧)指示;如果烧嘴没有点燃,烧嘴控制器会自动切断燃气电磁阀,点火变压器断电,同时在烧嘴控制器和控制柜上会有报警指示,提醒操作工判断并排除故障后,重新点火。