高技术枪钻系列刀具技术应用
超大长径比深孔加工的先进工艺技术——枪钻加工技术
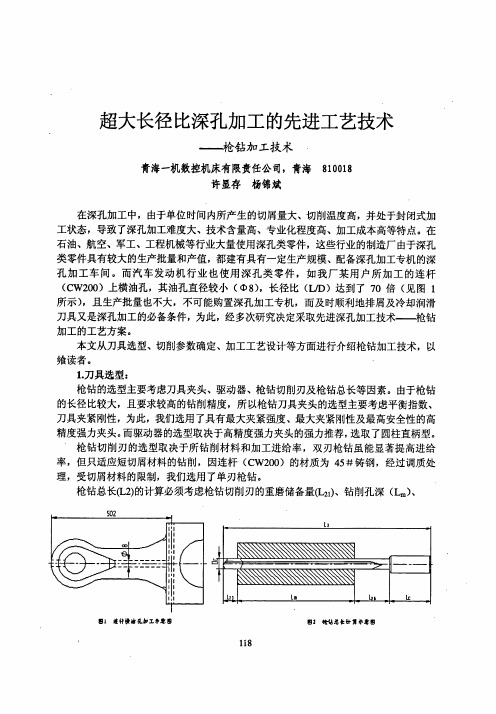
(Cw200)上横油孔,其油孔直径较小(①8),长径比(∽)达到了70倍(见图l
所示),且生产批量也不大,不可能购置深孔加工专机,而及时顺利地排屑及冷却润滑
刀具又是深孔加工的必备条件,为此,经多次研究决定采取先进深孔加工技术——枪钻
加工的工艺方案。 本文从刀具选型、切削参数确定、加工工艺设计等方面进行介绍枪钻加工技术,以 飨读者。 1.刀具选型: 枪钻的选型主要考虑刀具夹头、驱动器、枪钻切削刃及枪钻总长等因素。由于枪钻 的长径比较大,且要求较高的钻削精度,所以枪钻刀具夹头的选型主要考虑平衡指数、 刀具夹紧刚性,为此,我们选用了具有最大夹紧强度、最大夹紧刚性及最高安全性的高 精度强力夹头。而驱动器的选型取决于高精度强力夹头的强力推荐,选取了圆柱直柄型。 枪钻切削刃的选型取决于所钻削材料和加工进给率,双刃枪钻虽能显著提高进给 率,但只适应短切屑材料的钻削,因连杆(Cw200)的材质为45#铸钢,经过调质处 理,受切屑材料的限制,我们选用了单刃枪钻。 枪钻总长(L2)的计算必须考虑枪钻切削刃的重磨储备量(L21)、钻削孔深(Lm)、
120
超大长径比深孔加工的先进工艺技术——枪钻加工技术
作者: 作者单位: 许显存, 杨锦斌 青海一机数控机床有限责任公司,青海 810018
本文链接:/Conference_6524710.aspx
n=2600r/min。
3.钻削加工过程: 枪钻的钻削过程包括钻削导向孑L、钻削油孔两方面内容。因导向孔在枪钻钻削过程 中具有导向套的功效,所以导向孑L的直径和钻深要求较严,导向孔直径比枪钻直径大 0.0l~0.02,导向孔深至少有枪钻直径的2.5倍,由此看来,导向孔加工最好使用SANDVIK
CoroDrilI钻或U钻。
即完成枪钻钻削过程。
枪钻的简要介绍可达精度
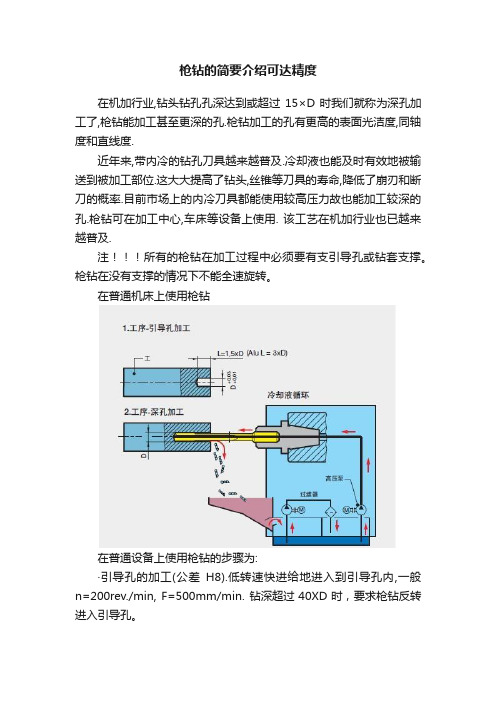
枪钻的简要介绍可达精度在机加行业,钻头钻孔孔深达到或超过15×D时我们就称为深孔加工了,枪钻能加工甚至更深的孔.枪钻加工的孔有更高的表面光洁度,同轴度和直线度.近年来,带内冷的钻孔刀具越来越普及.冷却液也能及时有效地被输送到被加工部位.这大大提高了钻头,丝锥等刀具的寿命,降低了崩刃和断刀的概率.目前市场上的内冷刀具都能使用较高压力故也能加工较深的孔.枪钻可在加工中心,车床等设备上使用. 该工艺在机加行业也已越来越普及.注所有的枪钻在加工过程中必须要有支引导孔或钻套支撑。
枪钻在没有支撑的情况下不能全速旋转。
在普通机床上使用枪钻在普通设备上使用枪钻的步骤为:·引导孔的加工(公差H8).低转速快进给地进入到引导孔内,一般n=200rev./min, F=500mm/min. 钻深超过40XD时,要求枪钻反转进入引导孔。
·打开冷却液同时提升转速.·按照正常的切削参数一次性加工到要求深度.·加工到预定深度后关闭冷却液.·停转并快速退刀.建议:· 在加工深度超过40×D时我们推荐用两支或更多枪钻由浅到深来加工·枪钻长度超过40×D时,要求枪钻反转进入引导孔.·在加工长屑材料时我们建议选用排屑槽抛光的枪钻.·单刃枪钻加工长屑铝时我们建议选用平头(180°)带冷却倒角的头部形式.· 加工Si含量<1%的铝合金,如,分段提速,最终速度Vc>160m/min.另外,要求约3XD的预钻孔。
在专机上使用枪钻单刃枪钻的精度基本公差单刃枪钻加工的孔能达到一个较紧的基本公差,因其切削刃不对称,加工时的径向切削力只能通过侧面支撑条的反作用力而抵消,而不象麻花钻径向切削力几乎为零故而易导致孔径偏大直线度因为焊硬质合金枪钻是把高精度的硬质合金头部焊在韧性极好的钢管上,故孔能达到一很高的直线度.然而,工件材料及其它不利因素都会影响到孔的精度.表面质量加工时的径向切削力通过支撑导条而作用在孔壁,可使孔表面因挤压作用而更加光亮.故支撑导条和孔壁之间的润滑就非常重要.润滑越好,孔表面光洁度就越高.同轴度例如当用麻花钻加工孔时,钻尖的修磨质量(对称性)直接影响着孔的同轴度.而单刃枪钻其不对称的径向切削力,使侧面支撑导条始终紧贴在孔表面,从而确保能达到很高的孔的同轴度.孔直线度偏差。
CNC机床加工中的钻削刀具的选择与应用

CNC机床加工中的钻削刀具的选择与应用CNC机床是现代制造业中不可或缺的重要设备之一,其高精度和高效率的加工能力使其成为各行业中的首选。
而在CNC机床的加工过程中,钻削是其中一项常见而重要的操作。
本文将重点探讨CNC机床中钻削刀具的选择与应用,帮助读者更好地了解这一领域的知识。
一、钻削刀具的选择要点选择合适的钻削刀具对于机床加工来说至关重要。
以下是几个选择刀具的要点:1. 材料选择:钻削刀具的材料种类繁多,常见的有高速钢、硬质合金、陶瓷和涂层刀具等。
根据加工材料的硬度、耐热性和切削性能等不同要求,选择相应的材料。
2. 刀柄类型:刀柄的类型有直柄和螺旋槽柄两种。
直柄适用于简单的钻削操作,而螺旋槽柄则适用于深孔钻削,可提供更好的冷却和排屑效果。
3. 刀尖形状:根据加工需要选择合适的刀尖形状,如标准点角、圆头、镗刀等。
刀尖的选择会影响到加工后的孔形和表面质量。
4. 切削边角度:根据加工材料的硬度和切削要求选择合适的切削边角度。
通常情况下,较小的切削边角度适用于硬材料的加工,而较大的切削边角度适用于软材料的加工。
二、钻削刀具的应用场景在CNC机床的加工过程中,钻削刀具具有广泛的应用场景。
下面列举几种常见的应用场景:1. 钻削孔加工:钻削刀具用于加工各种孔径和深度的孔。
在进行孔加工时,应选择合适的钻削刀具和加工参数,确保孔的精度和表面质量。
2. 镗削孔加工:在需要加工大孔径和高精度的孔时,可以使用镗削刀具进行加工。
镗削刀具具有较高的刚度和稳定性,能够满足高精度孔加工的要求。
3. 深孔加工:对于需要进行深孔加工的工件,通常采用深孔钻削刀具。
这种刀具具有内部冷却系统,可以在加工过程中提高冷却效果和排屑能力,保证加工质量。
4. 钻削面加工:除了加工孔,钻削刀具还可以进行面加工。
例如,在加工平面等工件时,可以使用适当的钻头进行铣削和切削操作。
三、常见问题及解决方法在钻削刀具的选择与应用过程中,也会遇到一些常见问题。
枪钻技术

摘要:传统上小直径深孔加工主要采用接长麻花钻,本文论述了应用枪钻在普通镗床上加工深孔的方法。
简述了枪钻的工作原理、组成结构和主要参数,以普通镗床深孔加工为对象,对枪钻和接长麻花钻进行了切削对比试验,论述了枪钻切削加工深孔的主要工装、参数确定过程和加工效果,测量了各切削参数.应用实例表明:枪钻具有加工精度高、加工时间短、钻头寿命高、排屑好的特点,在“小直径深孔加工”方面具有推广价值。
0.引言目前,带有小直径深孔的产品数量越来越多,按传统方法加工,只能采用接长麻花钻,每加工大约1~2倍直径的深度必须退刀排屑,不仅加工精度低、表面粗糙度差,加工效率低、操作劳动强度大,质量难以保证,而且很容易引起“堵屑”或折断钻头,造成更大的加工困难,因此,“大长径比小深孔加工”是困扰很多企业冷加工系统多年的难题,也是工艺人员和操作者的一块“心病”。
如何为传统制造企业何解决好小直径深孔的加工,已成为迫在眉睫的课题。
而枪钻在某传统制造企业的成功应用和推广,很好的解决了这个困扰企业多年的难题。
枪钻因最早用于兵器工业加工枪管而得名,主要用来加工φ2~φ20mm小径深孔,是目前深孔钻削中的一种优质高效工具。
美国钻科公司(DRILLMASTERS)公司作为世界上最主要的孔加工旋转切削刀具供应商之一,在枪钻的研发和制造方面具有多年的成功经验,其所研发的刀具具有切削效率高、加工精度好和刀具寿命长等特点,已广泛应用于汽车工业、航天工业、结构建筑工业、医疗器材工业、模具/刀具/冶金工业及油压、空压工业等制造业领域。
1.枪钻的工作原理专业的枪钻系统由深孔钻机、单刃或双刃的枪钻及高压冷却系统组成(见图1)。
枪钻柄部被夹持在机床主轴上,,钻头通过导引孔或导套进入工件表面,进入后,钻刃的独特结构起到自导向的作用,保证了切削精度。
这时冷却液通过钻头中间的通道到达切削部位,并将切屑从排屑槽带出工件表面,同时对钻刃进行冷却和对背部的支撑凸台进行润滑,从而获良好的加工表面和加工质量。
枪钻的设计与应用讲解

图4
二、枪钻刀头的组成、设计及几何参数
刀头是枪钻的主要部分,它直接影响加工质量,刀具寿 命。 枪钻刀头的组成:有二个切削刃,其这二个切削刃相交 处为钻尖,这二个切削刃称为内刃和外刃,分别具有内外 角。
1.内外刃的内外角与钻尖的关系
图5:枪钻刀头切削部分要素
在设计上必须保证钻削是径向力接近平 衡(图b),并使切削刃的合理分布在 钻头的两导向块之间,因此,作用在外, 内刃上的径向力分别为:
(3)刀杆外形与刀头的外形对称问题: 理论上要求对称度误差越小越好,对使用效果也越理想, 但实际上做不到其原因是: a.刀杆长度太长甚至2~3米,甚至个别还长。 b.即便刀杆不十分过长,焊后精加工刀头但圆磨加工 中也有一定误差。 c.个别由于多种原因刀头精加工后才进行焊接,这时 对称度更有困难。(见下图)
经过上面分析得出:通常刀具偏移中心距离—e=D/(35),现常取e=D/4,对于加工结构钢和铸铁取Kr2=20°, Kr1=30°~40°。
图a
图b
图c
由图a不难看出:外刃径向力过大,使作用于导向 块得挤压力加大,摩擦增大会使加工表面恶化,热量 增多。
图b内刃径向力增大,会引起孔的直线外刃径向力相等或者外刃径向力稍许大 于内刃径向力,而取e=D/4时工作状态良好,同 时又防止了钻头中心处切削速度为零,挤压被切削材 料,诸多因素钻尖e要取一个适当的距离。
刀头与刀杆对称度最好控制在0.1-0.2视直径大小 有关,因刀杆与刀头最大尺寸有一定差值,况且直径 越大其两差值也大,否则无法使用。 总之,当刀头直径在可能条件力争焊后再进行精加 工,外刃及其刃形和各部后角。 为了保证孔加工精度,其刀头上有分布合理的导向 块,形成二个导向块和外切削刃的刃带三点固定圆, 起自行导向作用,见图4:
金属切削刀具介绍----枪钻
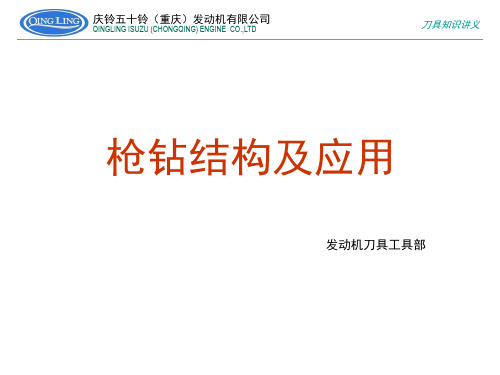
庆铃五十铃(重庆)发动机有限公司
QINGLING ISUZU (CHONGQING) ENGINE CO.,LTD
刀具知识讲义
三、枪钻应用
4、切削参数方面 ◆使用时应正确选取切削用量。一般情况下,切削速度:V=1.1-1.65 m/s, 进给量:s=0.015-0.03 mm/r,且进给量应两头小中间大。根据工件材质合 理选用切削用量,以控制切屑卷曲程度,获得有利于排屑的C形切屑。 ◆加工高强度材质工件时,应适当降低切削速度V。进给量的大小对切屑 的形成影响很大,在保证断屑的前提下,可采用较小进给量。 5、刀具方面 ◆钻尖几何参数的选择。枪钻钻削主要决定于外刃角φ外、内刃角φ内及钻 尖的偏心距。钻尖角2φ[2φ=180°-(φ外+φ内)],一般来说较硬的材料需 要用较小的钻尖角,较软的材料则需用较大的钻尖角,无论钻尖角度如何, 切削刃的交点位置距离钻头中心一般为1/4直径。根据硬质合金枪钻受力平 衡分析,要求外刃径向切削力等于内刃径向切削力,但实际加工过程中很 难保证。为了避免钻孔偏心,只有外刃径向切削力大于内刃径向切削力, 才能使径向合力始终作用于待加工表面。所以,一般用于加工铸铁和普通 钢材时取外刃角φ外=30、φ内=20。它的内、外刃前角为0º ,后角 α0=10º~15º ,并磨成双重后角。
庆铃五十铃(重庆)发动机有限公司
QINGLING ISUZU (CHONGQING) ENGINE CO.,LTD
刀具知识讲义
枪钻结构及应用
发动机刀具工具部
庆铃五十铃(重庆)发动机有限公司
QINGLING ISUZU (CHONGQING) ENGINE CO.,LTD
刀具知识讲义
一、深孔加工介绍 二、枪钻介绍 三、枪钻应用
TBT枪钻的使用
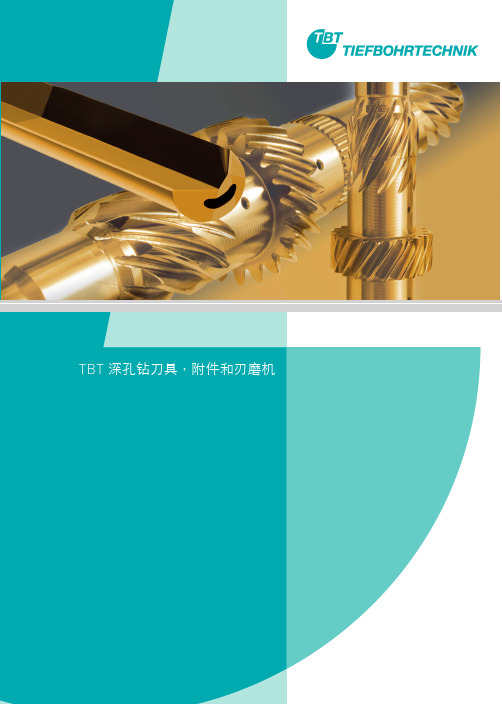
TBT枪钻刃部直径范围从0.8mm到50mm(工差直径可以精确到 0.001mm),枪钻总长可达6000mm。
加工前需要先了解被加工工件的材质,所用机床及具体加工要求,我们可 以对您的刀具进行改进和优化,根据实际情况建议您采用不同的枪钻,如 标准枪钻、扩孔钻、阶梯钻、成型钻、涂层/非涂层枪钻、PCD刀片镶入 式枪钻等。
不同于枪钻专机,加工中心很少采用 钻套进行导向。因此,要在加工中心 上使用枪钻,首先要在被加工工件上 预钻一个导向孔。
为了能达到较好的加工效果,导向孔 必须满足孔径公差,孔深等方面的要 求。我们建议您从TBT的产品中选出适 合您的产品,如单刃枪钻、阶梯钻或 整体硬质合金枪钻等。
第1步 | 引导孔 工件
进给
Ø 18,00 - 24,99 mm
0,080 - 0,110 0,080 - 0,110 0,080 - 0,110 0,080 - 0,110 0,080 - 0,110 0,080 - 0,100 0,080 - 0,110 0,080 - 0,100
0,080 - 0,100
0,080 - 0,110 0,100 - 0,130 0,100 - 0,130 0,090 - 0,120 0,060 - 0,100
zertifiziertes
ISO 9001
Qualitätsmanagement
ERTIFIZIER
ERTIFIZIER
zertifiziertes
VDA 6.4
Qualitätsmanagement
ERTIFIZIER
ERTIFIZIERT
zertifiziertes
ISO 14001
枪钻系列刀具介绍
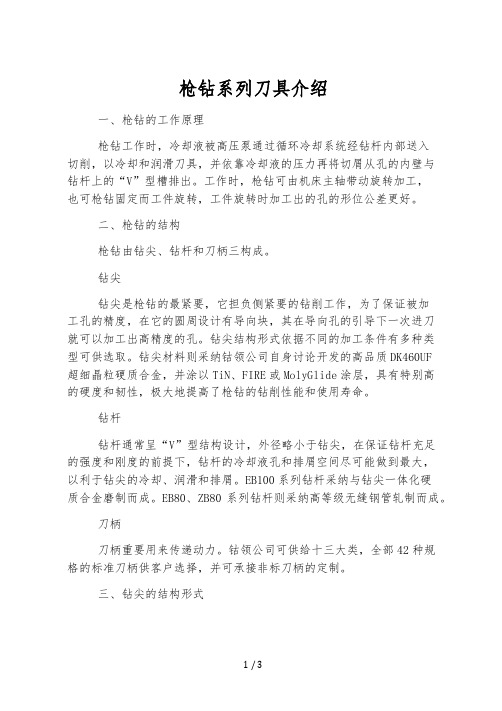
枪钻系列刀具介绍一、枪钻的工作原理枪钻工作时,冷却液被高压泵通过循环冷却系统经钻杆内部送入切削,以冷却和润滑刀具,并依靠冷却液的压力再将切屑从孔的内壁与钻杆上的“V”型槽排出。
工作时,枪钻可由机床主轴带动旋转加工,也可枪钻固定而工件旋转,工件旋转时加工出的孔的形位公差更好。
二、枪钻的结构枪钻由钻尖、钻杆和刀柄三构成。
钻尖钻尖是枪钻的最紧要,它担负侧紧要的钻削工作,为了保证被加工孔的精度,在它的圆周设计有导向块,其在导向孔的引导下一次进刀就可以加工出高精度的孔。
钻尖结构形式依据不同的加工条件有多种类型可供选取。
钻尖材料则采纳钴领公司自身讨论开发的高品质DK460UF超细晶粒硬质合金,并涂以TiN、FIRE或MolyGlide涂层,具有特别高的硬度和韧性,极大地提高了枪钻的钻削性能和使用寿命。
钻杆钻杆通常呈“V”型结构设计,外径略小于钻尖,在保证钻杆充足的强度和刚度的前提下,钻杆的冷却液孔和排屑空间尽可能做到最大,以利于钻尖的冷却、润滑和排屑。
EB100系列钻杆采纳与钻尖一体化硬质合金磨制而成。
EB80、ZB80系列钻杆则采纳高等级无缝钢管轧制而成。
刀柄刀柄重要用来传递动力。
钴领公司可供给十三大类,全部42种规格的标准刀柄供客户选择,并可承接非标刀柄的定制。
三、钻尖的结构形式钻尖的几何形状,直接影响到枪钻的切削加工性能及被加工孔的精度,钴领公司结合自身二十多年制造枪钻的成功阅历,优化了以下5种类型的钻尖外圆型式,并结合多种钻尖的不同角度磨削型式供用户选择,确保针对不同的工件材料及要求,总有一款适合您。
G型:通用型,适合加工各种材料,尤其适合加工孔公差范围较小的孔。
C型:标准型,适合加工难加工材料,如高合金钢等。
E型:专用型,适合加工各种材料,尤其适合加工孔公差范围较大的孔。
A型:专用型,适合在难以正确定位的情形下加工各种材料。
D型:专用型,特别适合加工灰铸铁。
四、枪钻的用途枪钻往往做成单刃刀头形式,它一般适用于加工2—20mm直径的小径深孔,长径比可达80倍,枪钻最长可达3000mm,被加工工件的表面粗糙度为Ra0.4—1.6,孔径精度为IT7—9级,孔的直线性高,并且孔口无毛刺,精度的重复性好。
枪钻使用技巧

( 2 )在车床上 ,按上序的顶尖孔中心找正 ,直 径还有 1 m余量 , .m 5 外圆车两段找正带; ( 3 )在枪钻上 ,按找正带找正,按修正的引导
封面图片 :由中国一重制造的四台 出口印度 BN IA反应器在一 重加氢反 应器制造基地码头待海运 用麻 花 钻加 工 细长 孔 时 ,
由于加工件内部夹渣 、气孔等缺陷导致钻头走偏的 现象。由于麻花钻是双刃切削刀具,加工中自动寻 求两刃切深均匀 ,使所受径向力相等 ,以达到平
01 . m通 孔 ; 55 m
()在 车床上 ,重新 检测后 ,内孔 与外 圆孔 同 4
() 在镗 床上 ,在孔 偏 的一端 ,按 01 m孔 1 2m 按 低 点 扩 至 01. m 55 m,5 m 深 的引 导 孔 ,精 铰 0m 引导孔 ,重 修顶尖 孔 ;
4 结 语
随着不锈钢 、耐热合金等管类产品的不 断增 加 ,枪钻的应用范围将越来越广,其使用技术也将 会不 断发展 和提 高 。
2 刃磨角度和切 削参数
()垂直角度+ 2 ; 1 3 。
21 刃磨角 度 .
( 2 )水平角度 0 。 , 。
用枪钻加工不锈钢和耐热合金材质产品时 ,对 刃磨角度应有特殊要求 ( 见图 1 图 5 。 一 )
图 3 钻 尖后面刃磨角度
( 1 )垂直角度+ 4 ; 1。 ()垂直角度+ 8 ; 1 1。
如 某 产 品加 工 一根 管 的 01 l中心通 孔 后 , 2mi l
发现其同轴度加工误差达到 0 m的问题 。而内 4 m 孔 最终尺 寸为 01.mm,现外 圆为 0 0m 55 5 m,外 圆 最终尺寸为 0 4 m 4 .m 。如果按常规工艺方案按内 5 孑 找正 ,则外圆必须加工到 0 2 m方可修正。 L 4 m 现采用枪钻进行修正,其工艺方法如下 :
数控机床的常见刀具及其使用

数控机床的常见刀具及其使用数控机床是一种高精度、高自动化的机床,它采用数字控制系统来控制机床的运动和加工过程。
在数控机床加工过程中,刀具的选择和使用非常重要,它直接影响着加工的质量和效率。
一、常见刀具类型1. 钻头:钻头是一种常用的切削刀具,用于在工件上钻孔。
常见的钻头有立铣钻头、中心钻头、螺旋中心钻等。
钻头采用高速旋转的方式切削工件,并通过切削沿面积分布来移除材料。
机床操作人员在使用钻头时需要注意控制进给速度和冷却液的使用,以保证钻孔质量和刀具寿命。
2. 铣刀:铣刀是一种以高速旋转的方式将工件表面上的材料进行切削的刀具。
根据铣削方式的不同,铣刀可分为立铣刀、面铣刀、以及侧铣刀等。
铣刀可用于开槽、镗孔、平面加工等各种形状的加工。
使用铣刀时,需要注意刀具的选择、刀具刃口的尺寸和形状,以及合理的切削参数。
3. 刀具夹持装置:刀具夹持装置是将刀具固定在机床主轴上的装置。
常见的刀具夹持装置有刀柄、刀套、刀头等。
合理选择和安装刀具夹持装置对于数控机床的加工效果和工件质量有着重要的影响。
二、刀具使用注意事项1. 刀具的选择:根据不同的加工要求和材料特性,选择合适的刀具非常重要。
合适的刀具能够提高加工效率、延长刀具寿命,并保证加工质量。
在选择刀具时,应考虑工件材料的硬度、切削速度、进给速度等因素,并根据加工形式和刀具性能进行选择。
2. 刀具的安装:正确安装刀具是保证加工质量的关键。
在安装刀具时,要注意刀具与主轴同心度、刀具夹持装置的紧固力、刀具刃口与工件表面的位置关系等。
安装不正确会导致加工质量下降、刀具磨损等问题。
3. 刀具的润滑和冷却:在数控机床加工过程中,刀具会因高速旋转和与工件碰撞产生摩擦热量,如果不能及时散热会导致刀具磨损和工件变形。
因此,在加工过程中,要及时给刀具提供润滑和冷却。
合理使用润滑剂和冷却液,可以提高刀具的寿命和加工质量。
4. 刀具的定期检查和更换:刀具在使用过程中会因磨损而失去切削性能,需要定期检查和更换。
枪钻概述
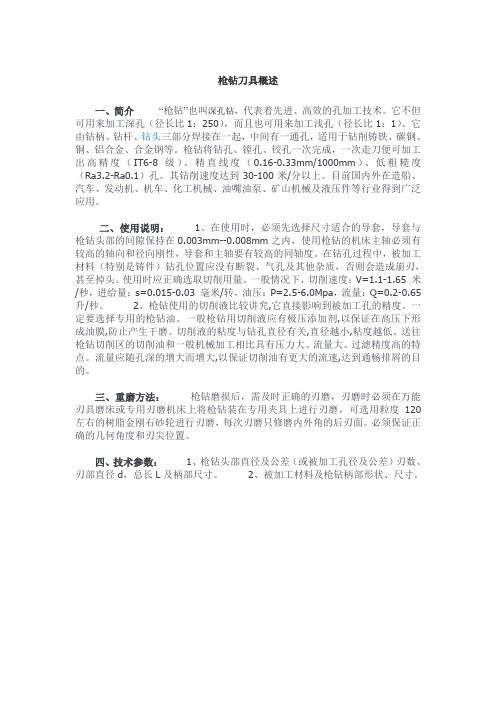
枪钻刀具概述一、简介“枪钻”也叫深孔钻,代表着先进、高效的孔加工技术。
它不但可用来加工深孔(径长比1:250),而且也可用来加工浅孔(径长比1:1)。
它由钻柄、钻杆、钻头三部分焊接在一起,中间有一通孔,适用于钻削铸铁、碳钢、铜、铝合金、合金钢等。
枪钻将钻孔、镗孔、铰孔一次完成,一次走刀便可加工出高精度(IT6-8级)、精直线度(0.16-0.33mm/1000mm)、低粗糙度(Ra3.2-Ra0.1)孔。
其钻削速度达到30-100米/分以上。
目前国内外在造船、汽车、发动机、机车、化工机械、油嘴油泵、矿山机械及液压件等行业得到广泛应用。
二、使用说明:1、在使用时,必须先选择尺寸适合的导套,导套与枪钻头部的间隙保持在0.003mm--0.008mm之内,使用枪钻的机床主轴必须有较高的轴向和径向刚性,导套和主轴要有较高的同轴度。
在钻孔过程中,被加工材料(特别是铸件)钻孔位置应没有断裂、气孔及其他杂质,否则会造成崩刃,甚至掉头。
使用时应正确选取切削用量。
一般情况下,切削速度:V=1.1-1.65 米/秒,进给量:s=0.015-0.03 毫米/转,油压:P=2.5-6.0Mpa,流量:Q=0.2-0.65 升/秒。
2、枪钻使用的切削液比较讲究,它直接影响到被加工孔的精度。
一定要选择专用的枪钻油。
一般枪钻用切削液应有极压添加剂,以保证在高压下形成油膜,防止产生干磨。
切削液的粘度与钻孔直径有关,直径越小,粘度越低。
送往枪钻切削区的切削油和一般机械加工相比具有压力大、流量大、过滤精度高的特点。
流量应随孔深的增大而增大,以保证切削油有更大的流速,达到通畅排屑的目的。
三、重磨方法:枪钻磨损后,需及时正确的刃磨,刃磨时必须在万能刃具磨床或专用刃磨机床上将枪钻装在专用夹具上进行刃磨,可选用粒度120左右的树脂金刚石砂轮进行刃磨,每次刃磨只修磨内外角的后刃面。
必须保证正确的几何角度和刃尖位置。
四、技术参数:1、枪钻头部直径及公差(或被加工孔径及公差)刃数、刃部直径d,总长L及柄部尺寸。
浅谈枪钻在不锈钢材料深孔加工中的应用
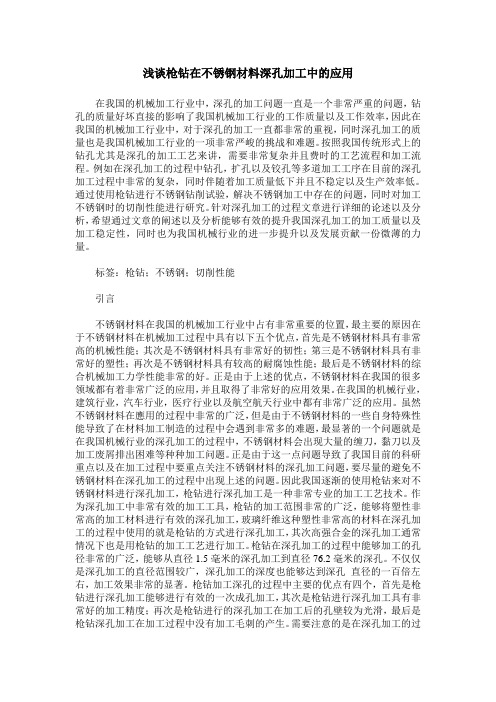
浅谈枪钻在不锈钢材料深孔加工中的应用在我国的机械加工行业中,深孔的加工问题一直是一个非常严重的问题,钻孔的质量好坏直接的影响了我国机械加工行业的工作质量以及工作效率,因此在我国的机械加工行业中,对于深孔的加工一直都非常的重视,同时深孔加工的质量也是我国机械加工行业的一项非常严峻的挑战和难题。
按照我国传统形式上的钻孔尤其是深孔的加工工艺来讲,需要非常复杂并且费时的工艺流程和加工流程。
例如在深孔加工的过程中钻孔,扩孔以及铰孔等多道加工工序在目前的深孔加工过程中非常的复杂,同时伴随着加工质量低下并且不稳定以及生产效率低。
通过使用枪钻进行不锈钢钻削试验,解决不锈钢加工中存在的问题,同时对加工不锈钢时的切削性能进行研究。
针对深孔加工的过程文章进行详细的论述以及分析,希望通过文章的阐述以及分析能够有效的提升我国深孔加工的加工质量以及加工稳定性,同时也为我国机械行业的进一步提升以及发展贡献一份微薄的力量。
标签:枪钻;不锈钢;切削性能引言不锈钢材料在我国的机械加工行业中占有非常重要的位置,最主要的原因在于不锈钢材料在机械加工过程中具有以下五个优点,首先是不锈钢材料具有非常高的机械性能;其次是不锈钢材料具有非常好的韧性;第三是不锈钢材料具有非常好的塑性;再次是不锈钢材料具有较高的耐腐蚀性能;最后是不锈钢材料的综合机械加工力学性能非常的好。
正是由于上述的优点,不锈钢材料在我国的很多领域都有着非常广泛的应用,并且取得了非常好的应用效果。
在我国的机械行业,建筑行业,汽车行业,医疗行业以及航空航天行业中都有非常广泛的应用。
虽然不锈钢材料在應用的过程中非常的广泛,但是由于不锈钢材料的一些自身特殊性能导致了在材料加工制造的过程中会遇到非常多的难题,最显著的一个问题就是在我国机械行业的深孔加工的过程中,不锈钢材料会出现大量的缠刀,黏刀以及加工废屑排出困难等种种加工问题。
正是由于这一点问题导致了我国目前的科研重点以及在加工过程中要重点关注不锈钢材料的深孔加工问题,要尽量的避免不锈钢材料在深孔加工的过程中出现上述的问题。
论枪钻技术在普通镗床深孔加工中的应用
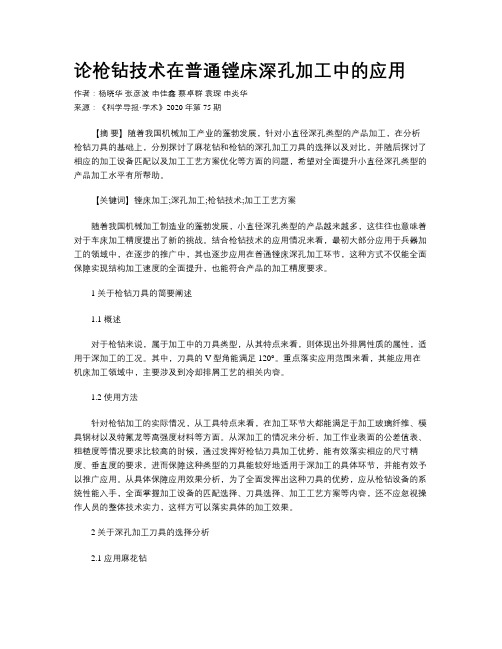
论枪钻技术在普通镗床深孔加工中的应用作者:杨晓华张彦波申佳鑫蔡卓群袁琛申炎华来源:《科学导报·学术》2020年第75期【摘要】随着我国机械加工产业的蓬勃发展,针对小直径深孔类型的产品加工,在分析枪钻刀具的基础上,分别探讨了麻花钻和枪钻的深孔加工刀具的选择以及对比,并随后探讨了相应的加工设备匹配以及加工工艺方案优化等方面的问题,希望对全面提升小直径深孔类型的产品加工水平有所帮助。
【关键词】镗床加工;深孔加工;枪钻技术;加工工艺方案随着我国机械加工制造业的蓬勃发展,小直径深孔类型的产品越来越多,这往往也意味着对于车床加工精度提出了新的挑战。
结合枪钻技术的应用情况来看,最初大部分应用于兵器加工的领域中,在逐步的推广中,其也逐步应用在普通镗床深孔加工环节,这种方式不仅能全面保障实现结构加工速度的全面提升,也能符合产品的加工精度要求。
1 关于枪钻刀具的简要阐述1.1 概述对于枪钻来说,属于加工中的刀具类型,从其特点来看,则体现出外排屑性质的属性,适用于深加工的工况。
其中,刀具的V型角能满足120°。
重点落实应用范围来看,其能应用在机床加工领域中,主要涉及到冷却排屑工艺的相关内容。
1.2 使用方法针对枪钻加工的实际情况,从工具特点来看,在加工环节大都能满足于加工玻璃纤维、模具钢材以及特氟龙等高强度材料等方面。
从深加工的情况来分析,加工作业表面的公差值表、粗糙度等情况要求比较高的时候,通过发挥好枪钻刀具加工优势,能有效落实相应的尺寸精度、垂直度的要求,进而保障这种类型的刀具能较好地适用于深加工的具体环节,并能有效予以推广应用。
从具体保障应用效果分析,为了全面发挥出这种刀具的优势,应从枪钻设备的系统性能入手,全面掌握加工设备的匹配选择、刀具选择、加工工艺方案等内容,还不应忽视操作人员的整体技术实力,这样方可以落实具体的加工效果。
2 关于深孔加工刀具的选择分析2.1 应用麻花钻在开展深孔加工环节,麻花钻应用时间比较早,其具有较为广泛的应用空间。
德国Hartner高技术枪钻系列

德国Hartner高技术枪钻系列
德国Hartner公司
【期刊名称】《航空制造技术》
【年(卷),期】2009(000)023
【摘要】@@ 一般情况下,钻削孔深与孔径之比大于10的孔,被称为深孔钻削.由于长径比较大,采用一般的麻花钻来钻削时,排屑、冷却、润滑和导向就成了难以解决的问题,孔的质量要求也很难达到.
【总页数】2页(P102-103)
【作者】德国Hartner公司
【作者单位】(Missing)
【正文语种】中文
【相关文献】
1.高技术枪钻系列刀具的特点及应用 [J], 谢志鲁
2.高技术产品需要高技术回收德国金炼公司金属废料处理厂简介 [J], 罗德先
3.DeepTriDrill可转位式枪钻系列 [J],
4.油泵油嘴行业世界最大的专业枪钻设备制造商──德国TBT深孔钻技术有限公司[J],
5.油泵油嘴行业世界最大的专业枪钻设备制造商——德国TBT深孔钻技术有限公司 [J],
因版权原因,仅展示原文概要,查看原文内容请购买。
深孔加工技术的主体——枪钻

深孔加工技术的主体——枪钻硬质合金枪钻简介枪钻!枪钻不但可用来加工深孔(长径比>10),而且也可用来加工精密浅孔。
枪钻一般由钻柄、钻杆、钻头三部分焊接在一起。
枪钻中间有一通孔,是切削液进入切削区的通道。
钻头是整个枪钻的关键部分。
材料为硬质合金。
其独特科学的组合结构,保证在完成切削工作同时还起到自导向的作用,可以通过一次贯穿得到一个高精度的深孔。
钻柄在机床和钻头间传递扭矩,密封高压油。
钻柄和钻杆之间的高回转精度,能避免额外的振动,提高加工精度和可靠性。
钻柄与刀杆相接的颈部处,有消除应力的光滑弧状凹槽以避免因应力集中而产生破坏。
钻杆采用优质合金钢材,经轧制成形、热处理、校直等多道工序制成。
钻杆轧有118°~120°的“V”型槽,用于排屑。
为保证钻削孔的直线度和偏斜度,钻杆必须有足够的强度,以便在较小的扭转变形下,提供切削所需的扭力矩。
同时,刀身也必须有足够的韧性,这样才能吸收刀身高速旋转产生的震动。
因此,钻杆的材料选择、热处理、轧制工艺要求非常严苛。
钻头有外角和内角两个基本角度(参见枪钻刃磨角度)。
可以根据被切削工件的材料及孔径来选择最恰当的组合,以便于工作中更好的平衡切削力和断屑,并将切削力传递给支撑凸肩,保证良好的直线度和同轴度。
钻头有很小的倒锥,直径较刀杆略大。
可以保证钻杆在切削孔内自由旋转而不会磨擦孔内壁。
枪钻的使用枪钻加工为强制排屑。
高压切削油由钻柄进入枪钻内孔,到达切削区,对钻刃进行冷却润滑。
铁屑及切削油沿着钻杆“V”型槽排出。
也称之为外排屑。
枪钻加工的材料范围很广。
从玻璃纤维、特氟龙等塑料到碳钢、合金钢、有色金属再到高强度合金钢(如高温耐热合金、钛合金)都可用其进行深孔加工。
因卓越的孔加工性能,枪钻在造船、汽车、发动机、机车、军工、化工机械、油嘴油泵、矿山机械及液压件等行业得到广泛应用。
枪钻的加工精度采用适宜的深孔加工机床及切削参数,可以达到如下加工效果:孔径尺寸: IT6~IT611内孔粗糙度:Ra0.2~Ra6.3偏斜度:1/1000 ×孔深工件固定,刀具旋转0.5/1000×孔深工件旋转,刀具反向旋转枪钻加工效率因为枪钻特殊的刀具结构,在深孔加工时,无需退屑,一次加工到深度。
枪钻几何角度参数及其应用
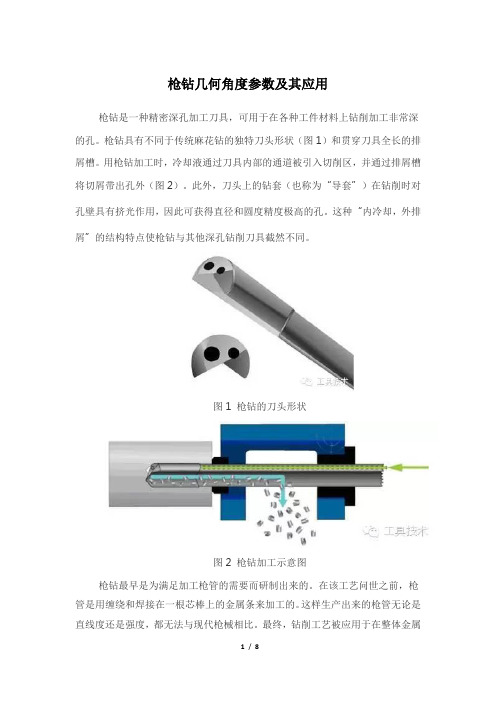
枪钻几何角度参数及其应用枪钻是一种精密深孔加工刀具,可用于在各种工件材料上钻削加工非常深的孔。
枪钻具有不同于传统麻花钻的独特刀头形状(图1)和贯穿刀具全长的排屑槽。
用枪钻加工时,冷却液通过刀具内部的通道被引入切削区,并通过排屑槽将切屑带出孔外(图2)。
此外,刀头上的钻套(也称为“导套”)在钻削时对孔壁具有挤光作用,因此可获得直径和圆度精度极高的孔。
这种“内冷却,外排屑”的结构特点使枪钻与其他深孔钻削刀具截然不同。
图1 枪钻的刀头形状图2 枪钻加工示意图枪钻最早是为满足加工枪管的需要而研制出来的。
在该工艺问世之前,枪管是用缠绕和焊接在一根芯棒上的金属条来加工的。
这样生产出来的枪管无论是直线度还是强度,都无法与现代枪械相比。
最终,钻削工艺被应用于在整体金属材料上加工枪管。
不过,早先使用的麻花钻需要多次走刀加工,因此孔的圆度和直线度精度都不高。
用枪钻加工成功解决了孔的圆度和直线度问题。
随着这种钻削工艺的不断改进以及枪钻专用加工设备的开发,该工艺被证明在枪械和兵器行业以外的许多其他行业也可以大显身手。
枪钻加工小直径精密深孔的能力使其被广泛应用于能源、汽车、航空、模具等行业。
随着加工技术的不断发展,其应用范围还在不断拓展。
刀具特点现代枪钻的结构型式可分为整体硬质合金式、焊接式和可转位刀片式,加工时不需要使用额外的钻管。
刀具的非切削端有一个供枪钻加工机床使用的标准尺寸驱动柄(图3)。
图3 枪钻结构枪钻通常通过一个圆形孔来输送冷却液,但有时为了增大冷却液流量,也可以采用多个冷却液孔或肾形孔。
排屑槽设计为V形槽,从而使冷却液能高效、干净地将切屑冲出孔外,因此枪钻也被称为单槽钻头。
枪钻具有特定的几何形状,其刃形设计使其能获得最佳的切削能力、加工精度以及成屑和排屑效率。
刀具廓形参数包括磨制的外周和钻尖几何形状、冷却液孔形状、刀头长度、钻套形状及位置。
加工车间主要根据工件材料和精度要求来选择枪钻。
许多标准的枪钻几何形状已通过大量试验,确定了其最佳尺寸参数。
BEST公司PDC钻头新技术及应用
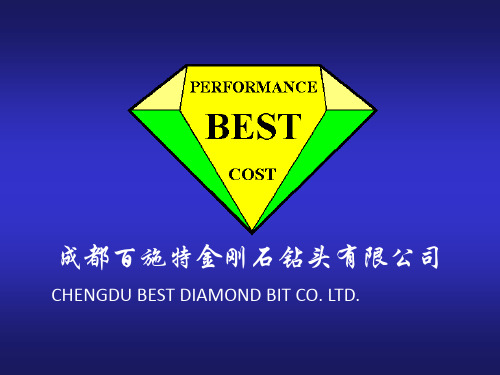
冲击性试验
• 切削齿以15°后倾角固定于金属 装置上
• 切削齿与坚硬的金属板相冲击 • 每个齿以给定的能量冲击十次, 然后记录金刚石层上的损失 • 当金刚石表面有30%失去或 冲击十次后便停止试验
模拟钻头冠型的岩石力学有限元分析切削齿布齿, 后倾角及侧倾角的考虑
多元化的产品结构
• 尺寸范围: 3”—17-1/2” • 钻头体的方式:胎体式,钢体式 • 切削齿的类型:PDC,巴拉斯,天然金刚石, 孕镶块,变体式孕镶块. • 钻头种类:全面钻进钻头,取芯钻头,特殊 作业用井下工具.
18.0
0.87
井喷埋井
迪那22井、迪那2井钻头对比
• 在迪那2井使用的基础上,针对22井的地层,对M1953SG 又作了改进,调整了切削齿的后倾角,尖园齿混合布置 (P表示),提高了钻头的攻击性,同样地层钻速明显提高.
井号
尺寸型 号 M1953 SG M1953 SGP M1953 SGP 地 层
HD1-12H井PDC钻头使用资料
入井 序号 1 地层 N,E N,J, T 合计 3 4 C C 4466.5120.0 4884.5092.0 井段 1852.2354.0 2982.4100.0 进尺 502.0 纯钻 时间 13.0 平均 钻速 38.62 备注 卡钻起钻
2
1118.0
1620.0 654.0 208.0
621.9
376.0
1.65
23天
LG30
549.5
185.8
2.96
10天
LG16、LG18、LG30
石炭系钻速对比
3 2.5 2 1.5 1 0.5 0
LG16
LG18
LG30
LG16、LG18、LG30
深孔加工的王者,枪钻!
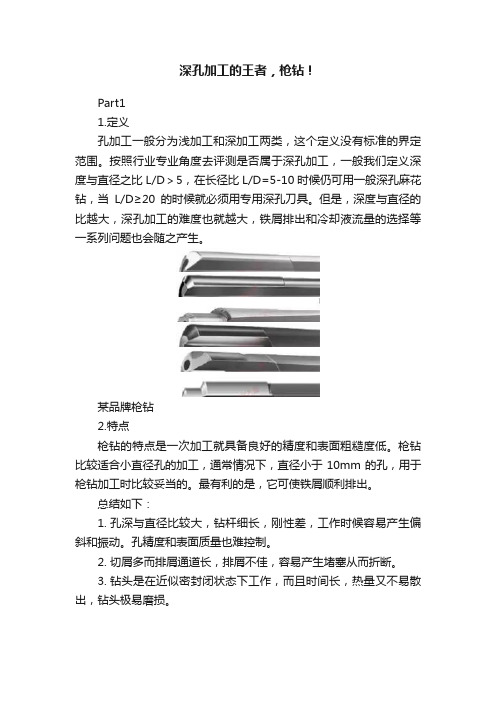
深孔加工的王者,枪钻!Part11.定义孔加工一般分为浅加工和深加工两类,这个定义没有标准的界定范围。
按照行业专业角度去评测是否属于深孔加工,一般我们定义深度与直径之比L/D>5,在长径比L/D=5-10时候仍可用一般深孔麻花钻,当L/D≥20的时候就必须用专用深孔刀具。
但是,深度与直径的比越大,深孔加工的难度也就越大,铁屑排出和冷却液流量的选择等一系列问题也会随之产生。
某品牌枪钻2.特点枪钻的特点是一次加工就具备良好的精度和表面粗糙度低。
枪钻比较适合小直径孔的加工,通常情况下,直径小于10mm的孔,用于枪钻加工时比较妥当的。
最有利的是,它可使铁屑顺利排出。
总结如下:1.孔深与直径比较大,钻杆细长,刚性差,工作时候容易产生偏斜和振动。
孔精度和表面质量也难控制。
2.切屑多而排屑通道长,排屑不佳,容易产生堵塞从而折断。
3.钻头是在近似密封闭状态下工作,而且时间长,热量又不易散出,钻头极易磨损。
专机实际应用Part23.结构枪钻是由枪头,枪杆和钻柄构成。
枪头常用的是硬质合金材料,枪杆是有高强度的合金管压制而成,枪柄是将钻头和机床连接起来的部分。
枪钻有两条主切削刃和一跳副切削刃,靠近钻心的叫内刃,另一条称之为外刃,其交点称之为钻尖。
专业名称4.角度钻尖几何参数的选择。
枪钻钻削主要取决于外刃角φ外,内刃角φ内及钻尖的偏心距。
钻尖角2φ[2φ=180°-(φ外+φ内)],一般来说较硬的材料需要用较小的钻尖角,较软的材料则需要交大的钻尖角,无论钻尖角度如何,外刃角和内刃角的选用必须保证钻头在切削时的径向分离和主切削力能合理的作用在钻头的支撑区上,以便起到挤光孔表面的作用。
切削刃的交点位置距离钻头中心一般为1/4直径。
根据硬质合金枪钻受力平衡分析,要求外刃径向切削力等于内刃径向切削力,但实际加工过程中很难保证。
为了避免钻孔偏心,只有外刃径向切削力大于内刃径向切削力,才能使径向合力始终作用于待加工表面。
双刃枪钻应用场景
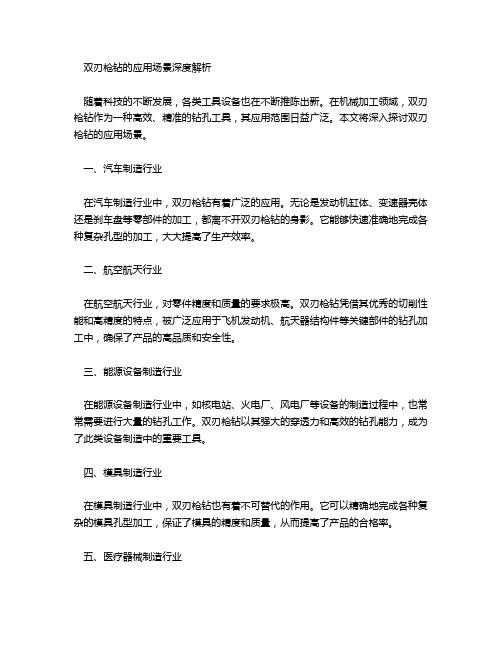
双刃枪钻的应用场景深度解析
随着科技的不断发展,各类工具设备也在不断推陈出新。
在机械加工领域,双刃枪钻作为一种高效、精准的钻孔工具,其应用范围日益广泛。
本文将深入探讨双刃枪钻的应用场景。
一、汽车制造行业
在汽车制造行业中,双刃枪钻有着广泛的应用。
无论是发动机缸体、变速器壳体还是刹车盘等零部件的加工,都离不开双刃枪钻的身影。
它能够快速准确地完成各种复杂孔型的加工,大大提高了生产效率。
二、航空航天行业
在航空航天行业,对零件精度和质量的要求极高。
双刃枪钻凭借其优秀的切削性能和高精度的特点,被广泛应用于飞机发动机、航天器结构件等关键部件的钻孔加工中,确保了产品的高品质和安全性。
三、能源设备制造行业
在能源设备制造行业中,如核电站、火电厂、风电厂等设备的制造过程中,也常常需要进行大量的钻孔工作。
双刃枪钻以其强大的穿透力和高效的钻孔能力,成为了此类设备制造中的重要工具。
四、模具制造行业
在模具制造行业中,双刃枪钻也有着不可替代的作用。
它可以精确地完成各种复杂的模具孔型加工,保证了模具的精度和质量,从而提高了产品的合格率。
五、医疗器械制造行业
在医疗器械制造行业中,双刃枪钻则可以用于精密仪器和植入物等小口径、深孔的加工,满足了医疗器械对精度和表面质量的高要求。
总的来说,双刃枪钻因其出色的性能和广泛的适用性,已经在各个行业中发挥了重要的作用。
未来,随着科技的进步,我们有理由相信,双刃枪钻将会在更多的应用场景中发挥更大的作用。
北京理工大学科技成果——深孔高速枪镗、枪铰刀具
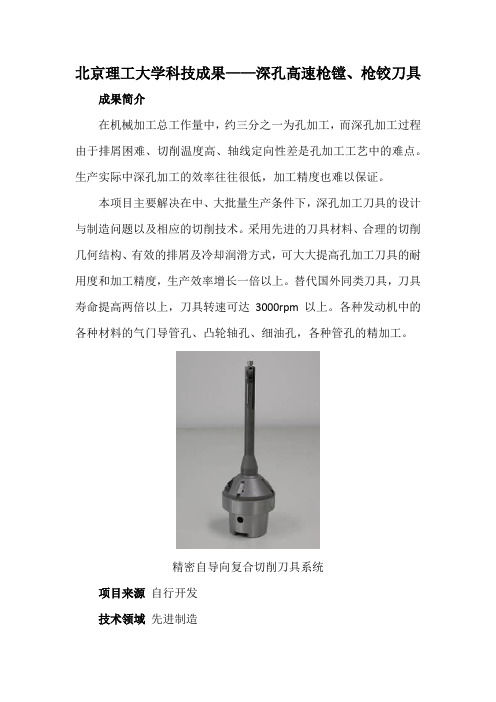
北京理工大学科技成果——深孔高速枪镗、枪铰刀具成果简介
在机械加工总工作量中,约三分之一为孔加工,而深孔加工过程由于排屑困难、切削温度高、轴线定向性差是孔加工工艺中的难点。
生产实际中深孔加工的效率往往很低,加工精度也难以保证。
本项目主要解决在中、大批量生产条件下,深孔加工刀具的设计与制造问题以及相应的切削技术。
采用先进的刀具材料、合理的切削几何结构、有效的排屑及冷却润滑方式,可大大提高孔加工刀具的耐用度和加工精度,生产效率增长一倍以上。
替代国外同类刀具,刀具寿命提高两倍以上,刀具转速可达3000rpm以上。
各种发动机中的各种材料的气门导管孔、凸轮轴孔、细油孔,各种管孔的精加工。
精密自导向复合切削刀具系统
项目来源自行开发
技术领域先进制造
应用范围以难加工材料为对象的机械加工或刀具制造企业。
现状特点居国内先进水平。
所在阶段批量生产
成果转让方式技术转让、合作开发、技术服务、产品销售。
- 1、下载文档前请自行甄别文档内容的完整性,平台不提供额外的编辑、内容补充、找答案等附加服务。
- 2、"仅部分预览"的文档,不可在线预览部分如存在完整性等问题,可反馈申请退款(可完整预览的文档不适用该条件!)。
- 3、如文档侵犯您的权益,请联系客服反馈,我们会尽快为您处理(人工客服工作时间:9:00-18:30)。
高技术枪钻系列刀具技术及应用
高技术枪钻系列刀具技术及应用
关键字:刀具技术加工刀具
一般钻削孔深与孔径之比大于10的孔,被称为深孔钻削。
由于长径比较大,采用一般的麻花钻来钻削时,排屑、冷却、润滑和导向就成了难以解决的问题,孔的质量要求也很难达到。
德国钴领刀具有限公司集百年专业生产孔加工刀具的丰富经验及二十多年深孔加工领域的专业枪钻制造为基础,开发出以下具有深孔加工领域领先技术的枪钻系列刀具:
EB100单刃整体硬质合金枪钻:加工范围:Ф1.2-5.0mm,最大槽长300mm,几乎适用于所有材料加工。
EB80单刃焊硬质合金刀头枪钻:加工范围:Ф2-40mm,总长最大达3000mm,几乎适用于所有材料加工。
ZB80双刃焊硬质合金刀头枪钻:加工范围:Ф6-27mm,总长最大达1000mm,适用于铸铁、铝和短铁屑非金属材料的加工。
一、枪钻的工作原理枪钻工作时,冷却液被高压泵通过循环冷却系统经钻杆内部送入切削部分,以冷却和润滑刀具,并依靠冷却液的压力再将切屑从孔的内壁与钻杆上的“V”型槽排出。
工作时,枪钻可由机床主轴带动旋转加工,也可枪钻固定而工件旋转,工件旋转时加工出的孔的形位公差更好。
二、枪钻的结构枪钻由钻尖、钻杆和刀柄三部分组成。
钻尖:钻尖部分是枪钻的最重要部分,它担负着重要的钻削工作,为了保证被加工孔的精度,在它的圆周部分设计有导向块,其在导向孔的引导下一次进刀就可以加工出高精度的孔。
钻尖结构形式根据不同的加工条件有多种类型可供选取。
钻尖材料则采用钴领公司自身研究开发的高品质DK460UF超细晶粒硬质合金,并涂以TiN、FIRE或MolyGlide涂层,具有非常高的硬度和韧性,极大地提高了枪钻的钻削性能和使用寿命。
钻杆:钻杆通常呈“V”型结构设计,外径略小于钻尖,在保证钻杆足够的强度和刚度的前提下,钻杆的冷却液孔和排屑空间尽可能做到最大,以利于钻尖部分的冷却、润滑和排屑。
EB100系列钻杆采用与钻尖一体化硬质合金磨制而成。
EB80 、ZB80系列钻杆则采用高等级无缝钢管轧制而成。
刀柄:刀柄部分主要用来传递动力。
钴领公司可提供十三大类,总共42种规格的标准刀柄供客户选择,并可承接非标刀柄的定制。
三、钻尖部分的结构形式钻尖部分的几何形状,直接影响到枪钻的切削加工性能及被加工孔的精度,钴领公司结合自身二十多年制造枪钻的成功经验,优化了以下5种类型的钻尖外圆型式,并结合多种钻尖的不同角度磨削型式供用户选择,确保针对不同的工件材料及要求,总有一款适合您。
G型:通用型,适合加工各种材料,尤其适合加工孔公差范围较小的孔。
C型:标准型,适合加工难加工材料,如高合金钢等。
E型:专用型,适合加工各种材料,尤其适合加工孔公差范围较大的孔。
A型:专用型,适合在难以正确定位的状况下加工各种材料。
D型:专用型,特别适合加工灰铸铁。
四、枪钻的用途枪钻往往做成单刃刀头形式,它一般适用于加工Φ2-Φ20mm直径的小径深孔,长径比可达80倍,枪钻最长可达3000mm,被加工工件的表面粗糙度为Ra0.4-1. 6,孔径精度为IT7-9级,孔的直线性高,并且孔口无毛刺,精度的重复性好。
广泛适用于汽
车制造业、飞机船舶制造业和机床制造等行业,主要加工对象为:缸体、缸盖、曲轴和各种引擎零件等。
钴领系列枪钻可应用于深孔加工专机、加工中心、车削中心等满足枪钻冷却及导向等要求的设备上对碳钢、不锈钢、铸铁、有色金属及木材、塑料等材料进行加工,钴领公司可针对客户的机床状况,提供最优化的切削工艺参数,确保发挥枪钻最高的切削性能。
为了使枪钻能长期稳定可靠地工作,钴领公司还为本公司系列枪钻匹配有小巧可靠的台式修磨枪钻系列装置:TBM116、TBV116;这两套修磨夹具结构紧凑,占地面积小,简便易用,通过短暂的培训,用户就可以用该夹具修磨出接近原刀的几何参数尺寸,确保修磨后的枪钻达到接近新刀的加工性能及质量。
配套提供的粗、精磨一体化金钢石砂轮:DSS125,可以保证枪钻在一次装夹中完成粗、精修磨,极大地提高了修磨的效率及质量。
配套的刀具附件:钻套、密封套和支撑座等,则为枪钻的顺利钻削保驾护航。