FMEA幻灯教材
潜在失效模式分析FMEA第五版教材ppt课件
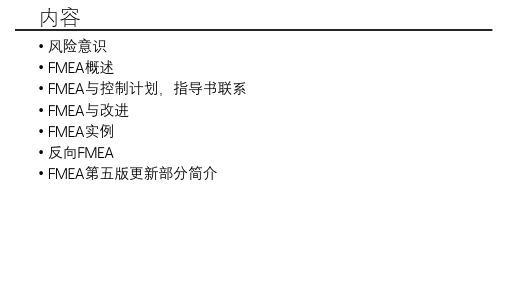
• 风险意识 • FMEA概述 • FMEA与控制计划,指导书联系 • FMEA与改进 • FMEA实例 • 反向FMEA • FMEA第五版更新部分简介
P1/30
做任何事都可能失败,所以你必须提前做好预防! 生活中:做饭糊,起晚,迟到,丢东西,感冒。。。 工作中:算错账,发错货,忙到忘记重要的工作。。。 设备:跳闸,断电,未知原因的停止工作。。。 教育训练:内容不合适,讲解不到位,学员跑神。。。
Baby拿个杯子8--更容易掉
P15/30
FMEA概述
频度(O)
P16/30
FMEA概述
探测度(D)
杯子碎了我听不见也看不见
P17/30
FMEA概述
探测度(D)
P18/30
FMEA概述
风险顺序数(RPN)
综合的考虑三要素 严重度、频度、探测度 RPN=S×O×D
P19/30
FMEA概述
替代
用
系统分析
功能分析
• 定义功能 • 转化要求 • 顾客语言转化未技
术术语
失效分析
• 识别失效及其结构 • 识别变差源(原因) • 定义风险优先级
风险分析
• 预防及探测控制 • SOD打分 • 定义风险优先级
改进措施
• 基于风险优先级确 定该叫你措施
• 风险降低 • 持续改进
失效分析及风险降低
第五版取消RPN风险顺序数,增加了AP
验证所有失效模式之 后,考虑创造和发现 PFMEA中为考虑到的 新的失效模式
是
所有的失
否
效模式都
验证了吗?
P26/30
FMEA内容(第五版)
格式变更(六步法)
范围定义:确认项目
FMEA最新实用版ppt课件
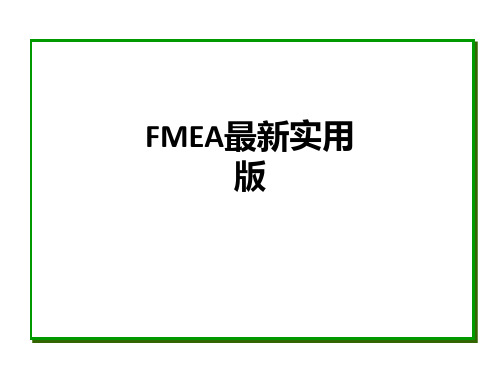
6
”我先 …… 所以没有 ”
我先 看了气象预报 所以没有 淋成落汤鸡 我先 评估金融大楼高度 所以没有 影响飞行安全 我先 设计计算机防火墙 所以没有 被黑客入侵 有些 我先 是必需的!有些 所以没有 是预期可避免的
三、FMEA实 施
6.范围或关注焦点: 新设计、新技术或新过程: 全部设计、技术或过程。 现有设计或过程的修改: 集中于对设计或过程的修改 、由于修改可能产生手工艺相互影响以及现场的历史 情况。 将现有的设计或过程用于新的环境、场所或应用(假 设对现有设计或过程已有FMEA):新环境或场所对现 有设计或过程的影响。
严重度(Severity)
那些错误是什么造成的?(失效原因) 发生之频率?
频度 (Occurrence)
有那些预防和检测?
检测方法能有多好的程度?
(探测度) Detection
我们能做什么?(建议措施) -设计变更 -过程变更 -特殊控制 -改变标准程序或指南
24
现行设 计控制 过程 功能 要求 潜在 失效 模式 潜在 失效 的后 果 严 重 级 度 数 别 S 潜在 失效 的 原因/ 机理 频 度 预 数 防
核能电厂、水库、卫星、飞机…….
有效运用 FMEA 可强化事先预防 7
如何避免以下事件…
8
一、什么是FMEA—定义
FMEA 可以描述为一组系统化的活动。其目的是: 1)认可并评价产品/过程中所有的潜在失效模式 及其失效的后果。 2)确定能够消除或减少潜在失效发生机会的措施 , 以提高产品的质量和可靠性。 3)将全部过程形成文件。 4)FMEA是对确定设计过程必须做哪些事情才能 使顾客满意这一过程的补充。
FMEA培训教材-PPT精选全文

客户要求 方便调整
舒适 移动顺畅
ቤተ መጻሕፍቲ ባይዱ
产品规格 调节高度 坐垫厚度 旋转角度 椅轮松紧
9
1
3
9
3
1
9
9
重要性 60% 30% 10%
分值
640
330
180
90
FMEA 得原理
客户要求 方便调整
舒适 移动顺畅
分值
产品规格 调节高度 坐垫厚度 旋转角度 椅轮松紧
9
1
3
9
3
1
9
9
640
330
180
90
参数
上升50CM
FMEA 得原理
一、FMEA基本知识
练习:
公司产品:车门 客户要求:
•方便开关 •噪音小 •安全
FMEA 得原理
FMEA 得原理
FMEA 得原理
客户质量要求 Input
客户质量目标
FMEA Output
CTQ 清单 CP 控制计划
FMEA
FMEA 得原理
Output
CTQ 清单
CTQ产出原则:
压 合 状 态
方法
特
样本Sample
殊 特 性 分
产品特 性/过程 参数规 格/公差
评价/ 测量技
术
容 量
频率
类
《
首检
MODULE 检验标
准》
5-20倍 显微镜
6P CS
:6PCS/ 抽检 : 每10PCS
抽1PCS
反应计
控制方法/ 统计技术
责任人
划
《CD-HFM0419701 LCM 镜检 不良明细
措施?
FMEA培训教材(PPT 99页)

DFMEA
第一版
原始稿日期
第二版
第三版
最新修订日期
DFMEA
8)核心小组 列出有权确定和/或执行任务的责任部门的 名称和个人的姓名(建议所有参加人员的姓 名、部门、电话、地址等都应记录在一张分发 表上。)
项目/功能要求 ➢ 填入被分析项目的名称和其他相关信息(如编号、零
件级别等)。利用工程图纸上标明的名称并指明设计水
察觉的现象相同。
➢ 潜在失效的后果,就是失效模式对系统功能的影响,可以使用顾客感受的语 言来描述.
➢ 要根据顾客可能发现或经历的情况来描述失效的后果,要记住顾客既可 能是内部的顾客也可能是最终用户。
➢ 如果失效模式影响可能影响安全性或对法规的符合性,要清楚地予以说 明。
➢ 失效的后果应按照所分析的具体的系统、子系统或部件来说明,还应记住 不同级别的部件、子系统和系统之间存在着一种系统层次上的关系。例 如,一个零件可能会断裂,这样会引起总成的振动、从而导致一个系统 间歇性运行。系统的间歇性运行可能会造成性能的下降并最终导致顾客 的不满。分析的意图就是在小组所拥有的知识层次上,尽可能的预测到 失效的后果。
知识的人员组成,(如设计、分析/试验、制造、装配、服务、 回收、质量及可靠性等方面有丰富经验的工程师)。 ➢ FMEA由责任单位的工程师开始启动,责任单位可能是原 设备制造厂(OEM,即生产最终产品)、供方或分承包方 ➢ FMEA工基本概念是预防为主,一定要在任何未知的设计 或制造的故障产生之前实施。 ➢ FMEA是一个重复的,周期性永不间断的改进程序
概要
FMEA的历史 20世纪50年代,美国格鲁曼公司开发了FMEA,用于飞
机制造业的发动机故障防范,取得了较好的成果.美 国航空及太空总署(NASA)实施阿波罗登月计划时, 在合同中明确要求实施FMEA.
FMEA培训教材(ppt)(2024)

后果分析
针对每种失效模式,分析 其可能对产品功能、安全 性、可靠性等方面造成的 影响和后果。
风险评估
对每种失效模式及其后果 进行风险评估,确定其严 重度、发生度和检测度等 级。
14
评估风险等级并采取预防措施
风险等级评估
综合考虑严重度、发生度 和检测度等级,对每种失 效模式进行风险等级评估 。
2024/1/30
4
FMEA发展历程
起源
FMEA起源于20世纪40年代的军事领域,当 时主要用于评估武器系统的可靠性。
发展
随着工业技术的进步,FMEA逐渐应用于民 用领域,如汽车、航空航天、电子、医疗等 。
标准化
为了规范FMEA的实施,国际标准化组织( ISO)和美国汽车工程师学会(SAE)等制定 了相应的标准和指南。
。
2024/1/30
可靠性增长
在产品设计阶段,通过不断测试和 验证,提高产品的可靠性和稳定性 ,降低失效模式的发生概率。
持续改进
在产品设计和生产过程中,持续关 注失效模式的变化和趋势,及时采 取改进措施,确保产品质量的持续 改进和提升。
16
04
FMEA在生产过程控制中应用
2024/1/30
17
识别生产过程中潜在失效模式及后果
通过引入先进设备、优化工艺流程、提高员工技能等手段 ,提升生产过程的能力和效率,降低潜在失效模式的发生 概率。
风险管理机制完善
建立完善的风险管理机制,包括风险识别、评估、预防、 监控和应对等环节,形成闭环管理,确保生产过程风险的 有效控制和持续改进。
20
05
FMEA在设备维护保养中应用
2024/1/30
21
FMEA讲义幻灯片

19
潜在失效模式及后果分析(FMEA)的理解与实施
• ●建议的措施 • ◆针对高RPN及高S的项目,准备采取的措施。 • ◆采取措施的目的:降低S/O/D,从而降低RPN。 • ◆提出建议措施的顺序:降低S 降低O 降低D。 • ◆建议措施的类别: • · 降低严重度S:改变设计结构。 • · 降低频度O:改度设计结构、改变设计参数,改变 • 使用材料,改变预防类控制方法。 • · 降低探测度D: • 若控制方法充分,则增加控制程度。 • 若控制方法不充分,则增加/改变控制方法。
WHEN YOU NEED TO BE SURE
15
潜在失效模式及后果分析(FMEA)的理解与实施
• ●频度(O) • ◆失效起因引起失效模式发生的可能性。用来评估失 • 效模式出现的概率。 • ◆级别的分类:1~10级,O越大,失效模式出现的可 • 能性越大。 • 如:10级:失效率≥10%,持续性失效。 • 8级:失效率≥2%,经常性失效。 • 6级:失效率≥0.5%,偶然性失效。 • ◆确定频度O时,要分析: • · 维修经验 • · 新材料,新技术,新结构的采用量 • · 预期的使用寿命
WHEN YOU NEED TO BE SURE
17
潜在失效模式及后果分析(FMEA)的理解与实施 • ●探测度(D) • ◆通过控制方法识别潜在失效起因或防止失效 • 起因发生的难易程度。用来评估设计控制方 • 法 的有效性。 • ◆级别分类:1~10级,D越大,失效起因识别 • 越困难。 • 如: • 10级:设计控制不能找到起因/无控制方法。 • 6级:设计控制有较少机会找到起因及模式。
WHEN YOU NEED TO BE SURE
FMEA培训教材-PPT文档资料-课件

FMEA & FMECA
FMEA: Failure Mode and Effects Analysis
失效模式及其影响的分析
FMECA:
Failure Mode, Effects and Criticality Analysis
失 效 模 式, 影 响 及 其 关 键 性 的 分 析
14
FMEA
Pa rt/Pro d u ct Own er: Pro cess Own er:
Part/ Proce s s
Failure Mode
S E Failure Effects V
Caus es
O C C Controls
Prep a red By : FM EA Da te (Orig ):
DR EP T N Actions
量。
16
FMEA
FMEA 的 等 级
步骤#1
过程-第一阶层
步骤 #2
步骤 #3
步骤 #1
过程-第二阶层
步骤 #2
步骤 #3
FMEA - 第一阶 层
FMEA - 第 二阶 层
步骤 #1
过 程 - 第三 阶 层
步骤 #2
步骤 #3
FMEA - 第 三阶 层
17
FMEA
FMEA 类 型
设计/产品
用 于 分 析 产 品,鉴 别 潜 在 的 在 发 展 周 期 早 期 与 设 计 意 图 相 关 的 产 品 失 效 模 式(部件,次装配)。
控制图
4
特殊起因
3
统 计 的 过 程 控 制 (SPC) 方 式: 当 特 殊 起 因 发 生 和 消 除 时 确 认 它 们。
FMEA培训教材ppt完整版

FMEA培训教材ppt完整版•FMEA概述与基本原理•失效模式识别与评估方法•故障原因分析技巧与工具应用•风险等级划分标准与应对措施制定目录•FMEA在产品设计阶段应用实践•FMEA在生产过程监控和持续改进中作用•总结回顾与展望未来发展趋势01FMEA概述与基本原理FMEA定义及发展历程FMEA定义故障模式与影响分析(FailureModes and Effects Analysis)发展历程起源于军事领域,后广泛应用于航空、汽车、电子等各个行业FMEA核心思想与目标核心思想预防性分析,识别潜在故障模式及其对系统的影响,提前采取措施降低风险目标提高产品可靠性、减少维修成本、增强客户满意度032. 功能分析识别系统或部件的功能及潜在故障模式01适用范围产品设计、生产过程、服务流程等各个环节021. 定义范围明确分析对象及目标评估故障模式对系统性能、安全、经济等方面的影响3. 故障影响分析综合考虑故障发生概率、严重度及可检测性,对故障模式进行风险等级排序4. 风险等级评估针对高风险故障模式,制定预防措施和应急计划5. 制定措施定期回顾FMEA 结果,更新措施并持续改进6. 跟踪与持续改进02失效模式识别与评估方法产品无法实现设计功能或性能不达标,如电子设备无法开机、机械部件卡滞等。
功能性失效安全性失效可靠性失效产品存在安全隐患,可能导致人身伤害或财产损失,如汽车刹车失灵、电器短路引发火灾等。
产品在规定条件下和规定时间内无法完成规定功能,如电池寿命短、设备频繁故障等。
030201常见失效模式类型介绍失效模式识别技巧与工具技巧了解产品工作原理及结构特点分析历史故障数据及维修记录•运用头脑风暴等方法集思广益工具故障树分析(FTA)事件树分析(ETA)因果图(Cause-Effect Diagram)01020304•方法选择:根据失效模式的性质和影响程度选择合适的评估方法,如风险矩阵、风险指数等。
实施流程1. 明确评估目标和范围2. 收集相关数据和信息3.选择合适的评估方法并建立评估模型4.对失效模式进行定量或定性评估5.根据评估结果制定相应的改进措施并跟踪验证03故障原因分析技巧与工具应用故障树分析法概述故障树的建立故障树的定性分析故障树的定量分析故障树分析法(FTA )原理及应用01020304介绍FTA 的基本概念、原理、作用及适用范围。
FMEA培训教材(ppt 191页)

评估设计FMEA 、过程FMEA,系统FMEA的应用以及控制计 划的合理性
*
29
7.实施FMEA的影响--跟踪和持续改进
产品开发
顾客要求和 顾客抱怨
初版DFMEA 更新DFMEA
过程开发
产品规范和 工程内不良
初版PFMEA 更新PFMEA
量产控制
工程内不良 和顾客抱怨 更新DFMEA 更新PFMEA
验收
使用
*
6
2.何谓失效
在规定条件下(环境、操作、时间)不能完成 既定功能 在规定条件下,产品参数值不能 维持在规定的上下限之间;
产品在工作范围内,导致零组件的破裂、断 裂、卡死等损坏现象。
*
7
2.何谓失效
产品失效一般的表现形式如下: 硬式失效:产品非常明显表达一种功能停止 现象实体破坏
*
3
0. 生活的现象--默菲定律
默菲定律:所有可能出错的地方都将会出错 ! 那么,在产品制造之前我们都担心一些什么 呢?
FMEA:将问题扼杀在摇篮之中
*
4
1.关于潜在的理解
潜在意味着:
*
5
1. 预防观念
问题
优质企业 总数
项目
策划
项目 实施
验收
使用
问题 劣质企业 总数
项目 策划
项目 实施
功能、性能方面 可靠性、维护性方面 安全性方面 经济性方面 操作性方面 修复性方面 环境方面 公共安全方面 废弃方面等
后果的分类
*
10
4 风险是否存在
渔夫与秀才的故事 通过这样的故事,在面对一件事时,给我
们的思考是什么?
*
11
5. 对FMEA理解
FMEA全套PPT教程
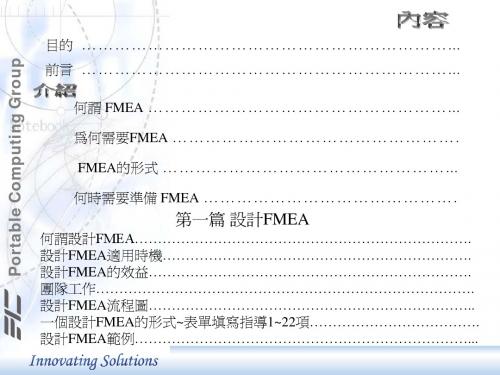
P or t ab l e C ompu ti ng G roup
產品設計的FMEA
P or t ab l e C ompu ti ng G roup
失敗模式
沒有冷 卻效果
效應
食物腐敗
原因
冷媒充 填不足
矯正措施
修訂扭 力規格
製程設計的FMEA
失敗模式
冷媒充 填不足
效應
食物腐敗
原因
充填周 期太短
矯正措施
何時需要準備 FMEA ……………………………………….
第一篇 設計FMEA
何謂設計FMEA………………………………………………………………. 設計FMEA適用時機…………………………………………………………. 設計FMEA的效益……………………………………………………………. 團隊工作………………………………………………………………………. 設計FMEA流程圖…………………………………………………………….. 一個設計FMEA的形式~表單填寫指導1~22項………………………………. 設計FMEA範例………………………………………………………………...
P or t ab l e C ompu ti ng G roup
何謂 FMEA
同時 , 每一 個問題 , 都有可能造成顧客不滿。
為何需要 FMEA
P or t ab l e C ompu ti ng G roup
FMEA培训教材ppt
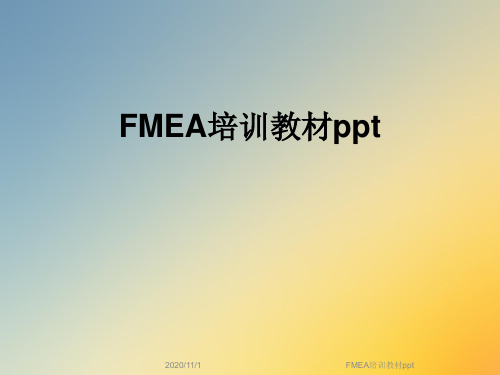
FMEA培训教材ppt
制程失效定义: 产品在经过一制造程序时,因制程而造成 其特性无法满足产品规格或甚至损坏者,即为制程失效.
失效效应的严重等级分为四級:
(A).I级:致命失效
此类失效模式发生可能会导致整个系統
FMEA培训教材ppt
2020/11/1
FMEA培训教材ppt
目录
•什么叫FMEA •FMEA分类和特点 •FMEA技术的发展与应用 •RPN评价 •FMEA的应用(以PFMEA为 例)
FMEA培训教材ppt
FMEA由来
AIAG 全称Automotive Industry Action Group,即汽车工业行动小组。该组织 成立于1982年,由美国三大汽车公司通用、福特和克莱斯勒共同创建,是全 球公认的著名的非盈利组织。
3
- 第二章﹕過程FMEA (Process Failure Mode & Effect Analysis )
PFMEA分析方法的流程 先期规划 主流程 结果应用
FMEA培训教材ppt
组成FMEA团队 资料收集
制定执行方案
先期规划
产品设计 制造工艺 使用维修 环境
表格格式 分析层次 失效定义 成果整合
注意
不要混淆 DFMEA与PFMEA的起因和失效
过程潜在的失效模式及后果分析
过程FMEA(PFMEA)
PFMEA简介
1.确定与产品相关的过程潜在失效模式 2.评价失效对顾客的潜在影响 3.确定潜在或装配过程失效的起因﹐确 定减少失效发生或找出失效条件的过程 控制变量 4.编制潜在失效模式分级表﹐然后建立 考虑纠正措施的优选体系 5.将制造或装配过程的结果编制成文件
F M E A培训教材PPT课件

FMEA简介
起源于六十年代中期 首先在航天工业界应用 美国汽车业界作为管理的必备工具
(QS9000的参考手册之一)
FMEA 推行的原因
产品的日趋复杂和精密使由于产品失效带 来的损失越来越大
70年代的产品责任法失产品失效及潜在失 效所引起的生产商的损失剧增.
如何识别产品潜在失效的危害并防止其发 生成为企业的一件重要工作.
致的失效及后果 PFMEA:考虑由于过程设计的缺陷而可能导致的失效及后果FMA 的时间顺序DFMEA
PFMEA
概念
初始设计 设计完成 样件制造 设计/过程 生产开始 确认
DFMEA 开始早于过程,完成时间在早期的图样完成但任何工具 的制造开始之前
PFMEA 开始于基本的操作方法讨论完成时,完成时间早于生产 计划制定和生产批准之前
FMEA 是其中发展的一项技能 越来越多的客户将实施FMEA作为对供应商
管理的内容
失效案例
通用汽车在一件由于汽车碰撞引起的爆炸 起火的赔偿诉讼中被判赔付几十亿美金(非 最终裁决)
东芝由于笔记本电脑存在FDC缺陷而潜在 可能发生存盘错误,在美国由于诉讼而赔付 10亿美金
1986年前苏联切而诺贝而核电站由于过热 产生爆炸造成31人死亡,造成非常严重的污 染
风险顺序度数 RPN (Risk priority Number)
RPN = ( S ) x ( O ) x ( D ) • S=Severity 严重度 O=Likelihood of Occurrence 频度数 D=Likelihood of Detection 探测度
FMEA的顺序
过程 功能 要求
DFMEA的分析方法
功能框图 从上到下,列出产品的项目/功能---系统,子系
FMEA培训教材演示文稿幻灯片

对组织和管理层的影响
• FMEA是企业内的一项重要活动,涉及整个产品实 现过程;
• FMEA很费时,而且需要有足够的资源; • 明确FMEA的职责以及高层管理者的承诺至关重要; • 要实施FMEA全面的培训,包括:管理层、使用者、
供方、推动者。
基本架构 Basic Structure
本手册所描述的建议FMEA格式的目的是为了组织收集和展 示相关FMEA信息,具体的格式可以根据组织的需要和顾客 的要求变化。
它工具之间的联系。
5. 对严重度、频度、探测度的打分表进行了改进,以便对实际的分析和 利用更有意义。
6. 引进了当前行业中正在被运用的可供选择的几种方法:增加了包含样 表和在特殊情况下运用的FMEA的附录;从以前关注“标准格式”改 变为几种代表当前行业中使用的FMEA的选择。
7. RPN不再被建议作为评价风险的首要方式,修订了改进的需求,包含 了一个附加的方法,而且明确说明了不建议使用RPN限值的方法。
什么是FMEA
在产品设计阶段和过程设计阶段,对构成产 品的子系统、零件,对构成过程的各个工序 逐一进行分析,找出所有潜在的失效模式, 并分析其可能的后果,从而预先采取必要的 措施,以提高产品的质量和可靠性的一种系 统化的活动。
FMEA的类型
SFMEA —— 对产品开发、过程策划综合评估,通过系统、 子系统不同层次展开,自上而下逐级分析,更注重整体性、 逻辑性。
• 20世纪70年代后期FMEA被美国汽车工业界所引用,作为设计评审的一 种工具。
• 1993年2月美国三大汽车公司联合编写了FMEA手册,并正式出版作为 QS-9000质量体系要求文件的参考手册之一,1995年2月出版了第二版, 2001年7月出版了第三版。
- 1、下载文档前请自行甄别文档内容的完整性,平台不提供额外的编辑、内容补充、找答案等附加服务。
- 2、"仅部分预览"的文档,不可在线预览部分如存在完整性等问题,可反馈申请退款(可完整预览的文档不适用该条件!)。
- 3、如文档侵犯您的权益,请联系客服反馈,我们会尽快为您处理(人工客服工作时间:9:00-18:30)。
第 1 章 概论
1.2 FMEA的历史
20世纪 60年代,美国宇航界首次研究开发FMEA; 1974年,美国海军建立第一个 FMEA 标准; 1976年,美国国防部首次采用 FMEA 标准; 70年代后期,美国汽车工业开始运用 FMEA; 80年代中期,美国汽车工业将 FMEA 运用于生产过程中; 90年代,美国汽车工业将 FMEA 纳入 QS9000标准 FMEA还被广泛应用于其他行业,如粮食、卫生、运输、 燃气等部门。
2003.5
FMEA
9
第 1 章 概论
1.3 为什么要进行FMEA?
FMEA有助于对设计中问题的早期发现,从而避
免和减少晚期修改带来的损失,使开发的成本下 降。 产品设计的FMEA还有助于可制造性和装配性的 早期考虑,利于实施同步工程技术。 FMEA有助于采用更有利的设计控制方法,为制 定试验计划、质量控制计划提供正确的、恰当的 根据。
2003.5
FMEA
11
第 1 章 概论
1.3 为什么要进行FMEA?
FMEA给出的失效模式的风险评估顺序,提供改
进设计的优先控制系统,从而引导资源去解决需 要优先解决的问题。 FMEA的文件化,使它成为重要设计文件之一, 并成为设计评审的重要内容。
2003.5
FMEA
12
第 1 章 概论
1.9 FMEA与QS9000质量体系要求的联系
2003.5 FMEA 3
第 1 章 概论
潜在失效模式及后果分析(英文Potential Failure Mode and Effects Analysis.简称FMEA)。 FMEA是在产品/过程/服务等的策划设计阶段,对构 成产品的各子系统,零部件,对构成过程,服务的 各个程序逐一进行分析,找出潜在的失效模式,分 析其可能的后果,评估其风险,从而预先采取措施 ,减少失效模式的严重程度,降低其可能发生的概 率,以有效地提高质量与可靠性,确保顾客满意的 系统化活动。
2003.5
FMEA
16
1.5 什么时候做FMEA?
FMEA旨在及早识别出潜在的失效,因此愈早开
始愈好。一般说来,在一个设计概念形成,设计 方案初步确定时应该开始FMEA初稿的编制。 随着设计活动的展开,在设计的各个重要阶段, 对FMEA的初稿进行评审,不断进行修改。 FMEA作为设计活动的一部分,应该在设计任务 完成(如设计图样完成、过程设计文件完成)之 时完成FMEA工作。
2003.5 FMEA 7
第 1 章 概论
1. 1 什么是FMEA?
FMEA按其应用的领域可分成以下多种:
SFMEA–
系统FMEA DFMEA– 设计FMEA PFMEA– 过程FMEA AFMEA—应用FMEA SFMEA—服务FMEA PFMEA—采购FMEA
2003.5 FMEA 8
1.4 由谁来做FMEA?
由负责设计的工程师或工程师小组负责,组成一 个包括设计、制造、装配、售后服务、质量及可 靠性方面的专家小组。与设计有关的上游(如供 方、材料、上一个相关系统设计师)和下游(如 下一个相关系统设计师)的部门也将被吸收参加 小组的工作。
2003.5EA 4
1. 1 什么是FMEA?
第 1 章 概论
1. 1 什么是FMEA?
FMEA是一种系统分析的方法,在分析过程中使问 题得到合理化解决的工具。 FMEA就是及早地指出根据经验判断出的弱点和可 能产生的缺陷,及其造成的后果和风险,并在决策 过程中采取措施加以消除。 FMEA是目前全世界最行之有效的预防手段,其准 则是 “避免缺陷产生较之以后发现缺陷,而不得不 加以排除,显得更合理,更经济”。 FMEA是用于评定风险的一种按优先次序排列的矩 阵工具。
2003.5 FMEA 14
第 1 章 概论
1.5 什么时候做FMEA?
FMEA是一个动态文件,在整个产品寿命周期内,
根据反馈信息,在进行设计修改时对FMEA进行 重新评审和修改。
2003.5
FMEA
15
第 1 章 概论
1.6 失效链
一个潜在的失效事件的发生,如果没有采取或 来不及采取或事实上不可能采取措施,而使 之引起下游系统或相关系统产生连锁失效事 件,我们称之为“失效链”。
FMEA 潜在失效模式及后果分析
第1章 第2章 第3章 第4章 概论 D-FMEA P-FMEA 总结
2003.5
FMEA
1
FMEA 潜在失效模式及后果分析
第一章
概论
2003.5
FMEA
2
第 1 章 概论
1.1 什么是FMEA? 1.2 FMEA的历史? 1.3 为什么要进行FMEA? 1.4 由谁来做FMEA? 1.5 什么时候做FMEA? 1.6 失效链 1.7 顾客的广义概念 1.8 DFMEA与PFMEA的联系
2003.5 FMEA 6
第 1 章 概论
1. 1 什么是FMEA?
FMEA与FTA(Failure Tree Analysis)失效 树分析的区别:
FMEA从局部失效入手,分析其对上一级系统、
相关部分、下游程序以及总体系统的后果。分析 路径“由下至上”。 FTA一般由系统的失效模式入手、分析造成该失 效产生的原因。分析路径“由上至下”。
2003.5 FMEA 10
第 1 章 概论
1.3 为什么要进行FMEA?
由多方面人员组成的小组所进行的FMEA能够发
挥集体的经验与智慧,使设计表现出组织的最佳 水平,提供一个公开谈论的机会。 FMEA是一个组织的经验积累,为以后的设计开 发项目提供了宝贵的参考。 FMEA还是识别特殊特性的重要工具,FMEA的 结果也是用来制订质量控制计划。
2003.5 FMEA 5
第 1 章 概论
1. 1 什么是FMEA?
FMEA 与FMA(Failure Mode Analysis)失效 模式分析的区别:
FMEA是一种事前行为 FMA是一种事后行为,是对产品/过程已经发生的
失效模式分析其产生的原因,评估其后果及采取 纠正措施的一种活动。FMA是进行FMEA的重要 的资料。