单磨粒的转子配流盘摩擦磨损规律研究
立轴冲击式制砂机转子部件磨损严重怎么办?维护及维修标准教给你

转子作为立轴冲击式破碎机(也称制砂机)的执行部件,其使用寿命直接决定了设备的检修周期和开机率。
虽然生产中转子不可避免会受到磨损,但对其磨损情况的正确分析、更换标准以及维修方法的制定,将极大地改善整台设备的运行情况,延长实际使用寿命。
在了解转子部件的磨损与维护之前,我们先来了解下转子的主要结构。
转子结构立轴式冲击破碎机转子主要由转子本体、分料盘、给料孔套、导料板、上磨损板、下磨损板以及顶部磨损板等部件组成。
日常维护过程中主要以磨损件的定期更换和转子本体磨损的焊补为主。
设备维护、操作人员可以通过转子各部件的磨损情况,判定出整台设备的运行状态。
转子磨损件磨损分析及维护方法1、抛料头磨损分析及维护方法(1)正常磨损抛料面磨损部位呈现中心对称圆弧形磨损凹陷。
耐磨嵌块磨损后剩余量<3mm 时,需及时更换。
(2)偏侧磨损抛料面呈现中圆弧形磨损凹陷,磨损部位偏上或偏下。
耐磨嵌块磨损最大处剩余量<3mm时,需及时更换。
同时需要调整导料板角度以及破碎腔内积料厚度,彻底解决偏侧磨损。
(3)抛料头开裂或破裂及时更换开裂或破裂的抛料头,并检查给料中是否夹铁、给料力度过大或装配面有无夹砂等,及时进行调整和清理,避免类似情况发生。
注意:转子上配套抛料头磨损到更换标准时,必须更换转子抛料头总成,不能选择性单件更换,否则将影响转子动平衡。
2、上、下磨损板磨损分析及维护方法(1)磨损板的内表面磨损磨损板的内表面至排料口处出现沟壑形磨损,磨损最大处磨损板厚度余量<3mm时,必需进行更换。
(2)上磨损板非正常磨损主要因给料筒及给料孔套磨损严重,需有针对性的检查给料筒及给料孔套的磨损情况并进行更换(上磨损板内侧边缘磨损至3mm时更换),同时观察转子抛料头磨损位置,确定是否受导料板安装位置和安装角度影响。
(3)下磨损板磨损过快需有针对性地检查分料盘的磨损情况,分料盘的磨损将直接加剧下磨损板的磨损速率(分料盘最大磨损处厚度余量<3mm或固定螺栓顶部开始磨损时必须更换),同时观察转子抛料头磨损位置,确定是否受导料板安转位置和安装角度影响。
工程硕士:磨粒有序化排布超硬砂轮磨削力工程的研究

工程硕士:磨粒有序化排布超硬砂轮磨削力工程的研究第1章绪论1.1 课题背景1.1.1 课题的提出由于普通砂轮存在着磨粒易脱落、磨削比能高、修整频繁、加工塑性金属材料易堵塞等问题,已不能完全满足在航空航天、国防军工、能源、化工、汽车等重要部门中不断涌现出的许多难加工材料进行高速、高效、高精度的加工要求,如钛合金、高温合金、TiAl、NiAl 及难熔金属硅化物等金属间化合物基高温结构材料、超高强度钢以及结构陶瓷和功能陶瓷等。
因此,致力于研究开发新型超超硬磨料成为人们研究的热点问题[3]。
与磨粒随机排布的普通砂轮相比,由于简单的制造技术,单层磨料电镀超硬砂轮表现出较为明显的优势,使超硬砂轮的份额在生产中占据相当大的比例,在高速甚至超高速磨削中的地位是不可忽视的。
单层高温钎焊超硬磨料钎焊砂轮因其具有很高的磨粒把持强度和磨粒裸露高度,在当今磨削技术中也占有不可忽视的地位。
但都存在一些问题,电镀砂轮镀层较厚时易造成堵塞、砂轮基体的结构设计及制造精度严重影响砂轮的回转精度和几何形状精度问题。
精密和超精密磨削所用砂轮会随着磨料颗粒的减小而增大控制电镀层厚度的困难程度,镀层过厚会将微磨粒完全包裹,导致磨削性能的下降。
当磨料粒度达到微米级时,对基体同轴度、平面度、圆柱度等形位误差要求更加严格,从而增加了砂轮的制造难度和成本。
更值得注意的是:无论是电镀砂轮或是钎焊超硬磨料砂轮,磨粒在砂轮基体表面大都是呈无规则的随机分布的,因此在磨削的过程中,真正去除工件材料的有效磨粒很少,大量无效的磨粒的存在使砂轮的制造成本显著增加,此外大量多余磨料的存在还使参与磨削的有效磨粒受到严重干扰,为砂轮的磨削性能造成很大的影响,如加工效率降低、加工表面质量差、砂轮寿命降低等。
为此想到,若能规划和控制磨粒在砂轮表面的数量和位置,通过对磨粒的可控排布,使磨粒在磨削接触区内按需发挥磨削作用,这样不仅可以节省大量超硬磨料,还可以有效减少砂轮堵塞、降低磨削温度等,从而获得最佳的磨削性能。
摩擦与润滑技术 教学课件 第四章 磨损原理

总之,粘着磨损是由于两摩擦物体在法向 力和切向力的联合作用下,产生金属与金 属的直接接触和塑性变形从而经历粘着 (冷焊)、剪切撕脱和再粘着的循环过程、 严重时摩擦副会咬死,粘着磨损过程中, 表面材料从一个表面转移到另一个表面, 在连续摩擦的情况下,被转移的薄片材料 由于不断的堆聚到一定程度,然后由于机 械断裂或结合链破坏抑或疲劳断裂而剥离 下来成为松散的磨屑颗粒,这些离散的磨 屑颗粒大多数在摩擦界面之间滚动,也可 能有少数颗粒再一次被粘附于摩擦表面的 可能,甚至有些颗粒还会有所增大,但这 种机遇可能不多,不一定是普通规律。因 为这些磨损颗粒,已遭到严重氧化、而且 根据粘着磨损理论分析和铁谱检验证明, 这些颗粒是一些疏松的层状颗粒,不仅溶 解的氧多,而且吸油性(润湿性)好,因 而不容易再次牢固的粘附于摩擦表面。
机械零件正常磨损过程一般可大致 分为三个阶段,如图4-1中的oabc曲 线所示。
(1)“磨合”(跑合)阶段:磨合 是磨损过程的不均匀阶段,这时由 于表面形貌发生变化,表面微凸体 相互急烈碰撞的机率逐渐减少,在 磨合期,系统是自适应过程。如图 4-1中的oa线段所示。
合理选择磨合规范、程序和润滑剂 是缩短磨合期并获得良好磨合结果 的基础。一般是采取逐级或连续递 增载荷下的磨合方法。
摩擦与润滑技术
第四章 磨损原理 武汉理工大学物流学院
董熙晨
1
耐磨性是材料抵抗磨损的一个性 能指标,可用磨损量的倒数来表示。 磨损量一般有下列几种表示方法:
(量的。也可以用线 磨损率表示,即单位滑动距离(或 单位时间)的摩擦表面法向尺寸减 少量
KL磨 滑 损 动 的 距 厚 离 度H L
(3)“急剧”磨损阶段:在长时间的稳 定磨损阶段(b点)以后,当材料的磨损 总量达到一定数值时,摩擦系统的状态可 能发生质的转变,随之摩擦现象也发生重 大变化,这时材料磨损随时间而迅速载长。 发生过程的自动加速,即一段时间间隔的 大量增长甚至会引起下一时间间隔更大的 增长,从而导致系统突然损坏,使整个系 统失效。在这种情况下,摩擦表面的员坏 一般说来,大多是由于表面疲劳,出现许 多疲劳裂纹,它们相互交连而成片剥离, 从而导致急剧磨损;或是由于表面持油能 力下降,形成不了流体油膜,从而导致金 属与金属直接接触,造成金属的剧烈粘附 磨损。当然也可能由于磨粒磨损引起急剧 磨损。实际上可能是一种主要磨损形式同 时又伴随着其它磨损形式的综合作用结果。 在急剧磨损中,磨屑颗粒的尺寸可达上百 微米以上。对于相同金属摩擦副,磨粒尺 寸会更大。
单磨粒的转子配流盘摩擦磨损规律研究

单磨粒的转子配流盘摩擦磨损规律研究摘要:航空液压泵的故障问题中,柱塞泵中转子-配油盘摩擦副对于保持液压泵的容积效率非常重要,而磨粒磨损是造成其泄漏的主要原因。
现根据磨粒磨损理论,结合转子与配流盘间的实际情况,建立了磨粒磨损理论模型,提出了配流盘上磨粒的磨损量期望的理论计算方法。
由转子配流盘间的间距仿真结果,得出转子与配流盘间的间距呈周期性起伏。
并为磨损量的实时曲线仿真提出了可行的流程方案。
进行了数值计算,通过matlab仿真模拟了磨粒在磨损过程中的压入深度变化。
关键词:磨粒磨损;转子配流盘;摩擦学引言航空液压泵是飞机起飞、操纵、起落架收放和刹车的关键部件。
飞机液压泵一旦发生故障,轻则引起飞机液压系统不正常工作,重则造成机毁人亡,带来巨大的经济损失和不良的国际影响。
据统计,航空液压泵80%以上的故障是由于磨损污染造成的。
尤其是飞机液压系统向高压化方向发展,油液污染导致的液压泵磨损愈加显著[1]。
而在这磨损之中,柱塞泵中转子-配油盘摩擦副对于保持液压泵的容积效率非常重要,试验数据表明[2],该摩擦副的泄漏量占液压泵全泵泄漏量的70%以上。
国内外大量学者都针对该摩擦副的磨损进行了大量研究工作。
一直以来,磨损是国内外摩擦学研究的重要部分。
人们对磨损机理的分析和理解也愈加成熟。
Jacobson等[3]建立了考虑多个磨粒同时作用的纯切削过程的统计学模型。
利用该模型研究了磨粒尺寸、载荷及工件表面硬度对磨损率的影响。
预测了发生接触的磨粒数量和磨损表面形貌。
方亮等人[4]为探讨三体磨料磨损中磨料颗粒粒径的分布对材料磨损性能的影响,通过试验结合正态概率分布坐标分析的方法,比较准确地得到磨料粒径的分布情况。
ArnoldIsmailov等[5]人用硬度不同的两种磨粒粉进行了磨损实验,发现对于硬度低的磨粒,滑行速度越快,越不易磨损。
对于硬度高的磨粒,速度越快,磨损越严重。
转子与配流盘间的磨粒磨损是一个非常复杂的过程,这是一个实时变化的随机过程,并且磨粒的分布也具有随机性。
单颗钎焊金刚石磨粒磨损试验研究

单颗钎焊金刚石磨粒磨损试验研究黄武;苏宏华;张昆;徐九华【摘要】采用单颗磨粒试验方法,以碳钢碟轮为修整工具,研究金刚石和 CBN 磨粒修整过程中的磨损特征。
结果表明:砂轮和修整碟轮的相对速度对金刚石磨粒的磨损有重要影响;相对速度为51.9 m/s 时,金刚石磨粒的磨损高度为50.1μm;相对速度为17.3 m/s 时,金刚石磨粒的磨损高度显著减小,为19.5μm。
通过相同条件下金刚石与 CBN 磨粒的磨损特征对比,表明金刚石磨粒在磨损过程中同碟轮之间发生化学作用,加速金刚石磨粒的磨损;对试验后金刚石磨粒进行拉曼光谱分析,并未检测到石墨物质。
%The wear characteristics of diamond and CBN grit are studied using single grit test with carbon steel plate wheel as dressing tools.The results show that the relative velocity of grinding wheel to dressing wheel has an important effect on wear of diamond grits.The abrasive wear reaches 50.1 μm when the relative velocity is 5 1.9 m∕s,and decreases to 1 9.5 μm as the relative velocity is 17.3 m∕s. After comparing grit wear characteristics of diamond and CBN,it can be concluded that chemical interaction between diamond grits and dressing wheel occurrs in the process of diamond grits wear, which accelerates the wear of diamond grits.Graphite material is not detected on the dressed grit using Raman spectra analysis.【期刊名称】《金刚石与磨料磨具工程》【年(卷),期】2016(036)002【总页数】4页(P15-18)【关键词】单层金刚石砂轮;碟轮修整;CBN;拉曼光谱【作者】黄武;苏宏华;张昆;徐九华【作者单位】南京航空航天大学机电学院,南京 210016;南京航空航天大学机电学院,南京 210016;南京航空航天大学机电学院,南京 210016;南京航空航天大学机电学院,南京 210016【正文语种】中文【中图分类】TQ164;TG74由于砂轮基体圆度误差、砂轮表面磨粒大小不一以及磨粒在砂轮工作面上位向的不同,单层超硬磨粒砂轮的磨粒等高性不一致,导致磨削加工后的工件表面粗糙度值远高于使用同等粒径磨粒的其他类型砂轮。
螺杆钻具转子表面磨损规律研究

《工程概论》研究报告:转子发动机能耗和磨损问题浅析

《工程概论》研究报告转子发动机能耗及磨损问题浅析专业:班级:姓名:学号:日期:2015.5.28转子发动机能耗及磨损问题浅析【摘要】:一次偶然的机会,我在图书馆里的一本书上看到了转子发动机的介绍,书中介绍了转子发动机的工作原理和它与普通的往复式发动机的区别,这种特别的发动机瞬间吸引了我的目光。
发动机是汽车最为关键的部分,是决定车子性能的最重要的因素,犹如人的心脏。
大部分人都知道我们日常用的是活塞往复式发动机,又分为两冲程发动机和四冲程发动机,但是还有一种不为大部分人所熟知的发动机,那就是转子发动机,又叫汪克尔发动机。
我们日常经常看到的为活塞往复运动形式的发动机,即活塞在汽缸内作往复的直线运动,通过曲轴把活塞的直线运动转化为曲轴的旋转,而转子发动机没有这个转化过程,它是通过活塞在汽缸内的旋转来带动发动机主轴(即普通发动机的曲轴,因为不是弯曲的故不再叫曲轴)旋转的,故两者有着很大的区别。
转子发动机的工作原理是什么?与传统的内燃机相比,转子发动机的优点缺点分别有哪些?怎样改进它的缺点以实现它的广泛利用?针对其高油耗,高排放的特点,以及发动机的磨损问题,我进行了一些探究。
转子发动机的高能耗问题,可以采用分层燃烧的方法,这种方法在转子发动机上可以广泛应用。
而转子发动机的磨损问题,则要分析其原因并且提出可行的解决方案。
在《工程概论》课上,我初略了解了关于机械,车辆乃至发动机等的基础知识,同时我在课外利用网络和图书馆的资源收集资料,完成了这份研究报告。
【目录】第一节绪论第二节转子发动机的工作原理第三节关于转子发动机的能耗和排放问题第四节关于转子发动机“鬼爪”问题的思考第五节转子发动机的应用前景第一节绪论目前在商品汽车上普遍使用往复式活塞发动机。
还有一种知名度很高,但应用很少的发动机,这就是三角活塞旋转式发动机。
转子发动机又称为米勒循环发动机。
它采用三角转子旋转运动来控制压缩和排放,与传统的活塞往复式发动机的直线运动迥然不同。
螺杆钻具转子特性与磨损规律研究

测试不同泥浆作用下, 高速运动转子的表面材料径ห้องสมุดไป่ตู้磨损单位高度所需要
的时 间。 将 所得 试验 数据 绘制 图表 , 以表 面处 理加工 工 艺试验 材料 类型 ( p e A~E ) 为 横轴 , 磨损 耗 时(mi n )为纵 轴 。 通 过试 验结 果 可 以看 出 : ( 1 )等离 子 喷涂 碳化 钨 (T y p e A)和 氧化 铝 ( T y p e B )处 理 后 的转 子试 样 , 在 各 种 工 况下 耐磨 效果 明显 好于 其它 工 艺处 理 的转子 , 而 以等离 子喷 涂碳 化钨 ( T y p e A)效果 最 佳 , 电镀硬 铬 ( T y p e c )效果 最差 ; ( 2 ) 钻 井 液 中蕴 藏 的固 相对 化 学镀 镍( p e D ) 和 喷焊硬 质 合金 ( T y p e E )的影 响明显 , 对 其 他加 工处 理 工 艺 不构 成 影 响 , ( 3 )盐 水泥 浆 对喷 焊镍 基 合金 工 艺(T y p e E )和 电镀硬 铬 工 艺 (T y p e C) 处理 的转 子 试件 的腐 蚀作 用 明显 , 对 其 它处 理工 艺处 理 转子 试 件 影响 不大 ; ( 4 ) 在 各种 井下 工 况下 , 各种 螺 杆钻 具转 子表 面材 料 加工 处理 工 艺 与材 料耐磨 性能 逐渐 降低 ( A~E ), 而 各种 工艺 与材 料对井 下环 境 的敏感 程
螺杆 钻具是 目前 国内外应用最 广泛的 一种井 下动力钻具 , 其 应用领域遍 布 常规 、 非常规 油气资 源钻井 , 地质 勘探和 地下工程 。 定 转子构 成的马 达是螺杆 钻 具的核 心部件 之一 , 可 以把通 过二者 间隙 的泥浆 中蕴 藏 的动 能转化 成钻头破 岩 钻进所 需的机 械能 。 马达结 构复杂 , 暴 露在恶劣 的泥浆环 境 中, 受 到磨蚀等 作用 影响, 失 稳 失效 问题 也 日趋 普遍 , 严重 影响着 螺杆 钻 具的整 体 寿命 。 1转 子表 面 毫损过 程 相互接 触 的物体在 相对 运动 中 , 表 层材料 不 断损失 、 转移 或产 生残余 变形 的现 象称为磨 损 , 它是伴 随着摩 擦而产 生的必 然结果 , 包括 粘着磨损 、 腐蚀 磨损 和 磨料磨 损 等 。 据 统计 , 约有 8 0 % 左右 的机械 零件 是 由于磨 损而 报废 或失效 , 马 达转子 也不例 外。 转 子相对 于定子高 速旋转 , 做 类似于纯 滚动 的复杂运动 , 井
单颗磨粒的冲击磨损理论及实验研究

w e a r wi t h p i e c e s o f me t a l a t i f n a l ,i t wo u l d b e a h i g h e r ma t e i r a l r e mo v a l w h e n p a r t i c l e i mp a c t wi t h i n a
并对颗 粒 的冲击磨 损特性 进行 了实 验研 究。 结果表 明 : 对 于弹 塑性金 属材料 , 撞 击初 期主 要是 发 生
弹 塑性 变形 。 形成 压坑 与变形 唇 。 经 多次 碰 撞 挤压 后 。 最 终 以小块 金 属 剥落 而 产 生磨 损 。在 一定 冲 击角度 ( 颗粒 冲击 轨迹 与水 平面 的夹 角 ) 下工件 表 面材 料磨 损量 较 高 , 随着磨 粒 碰 撞速 度 和碰 撞 次
ma t e ia r l b a s e d o n Si n g l e— p a ti r c l e, a n d s t u d y e x p e r i me n ta c t we a r . Th e r e s ul t s
摘 要: 针 对螺 旋式约 束磨 粒流抛 光 的机理 研究 , 基于 A NS YS建 立 了单颗 磨粒 的 冲击 模 型 , 选 用 铝合 金 作 为工件 的材料 。 并 建立相 应 的 J o h n s o n—C o o k弹 塑性模 型 , 分析 单颗 磨 粒对 材 料 的冲 击磨 损 情 况 。
s h o w t h a t t h e i n i t i a l i mp a c t O C C H I T e S ma i n l y a s e l a s t i c— — p l a s t i c d e f o r ma t i o n a n d or f m p i t a n d d e f o me r d l i p
单颗磨粒磨削碳化硅陶瓷磨削力与比能研究

单颗磨粒磨削碳化硅陶瓷磨削力与比能研究于腾飞;苏宏华;戴剑博;周文博【摘要】为探索磨削速度和单颗磨粒最大未变形切厚对碳化硅陶瓷高速磨削材料去除过程的影响规律,进行了切向进给单颗磨粒高速磨削试验,研究了磨削力、磨削比能与磨削速度以及单颗磨粒切厚的关系.研究结果表明,单颗磨粒切厚为0.03和1 μm时,磨削力和磨削比能均随着速度的增加而减小,而当切厚为0.3 μm时,磨削力和磨削比能随着磨削速度先增加后减小,磨削速度80 m/s为其转折点.磨削力随着单颗磨粒切厚的增大整体上呈上升趋势,但是当切厚小于某一临界值时,磨削力变化并不明显,磨削比能却急剧降低,而且磨削速度提高,该临界值变大.因此,磨削速度的提高有利于降低磨削力和磨削比能,适当增加单颗磨粒未变形切厚并不会恶化加工质量.%To explore the influence of grinding speed and maximum undeformed chip thickness(M-UCT) on material removal mechanisms in high-speed grinding process,a single grit grinding experiment is car-ried out on silicon carbide(SiC)ceramics with tangential infeed grinding method.The grinding force and the specific grinding energy are analyzed.The results show that the grinding force and the specific grinding energy tend to decrease with the increase of grinding speed at M-UCT of 0.03 and 1 μm.How-ever,when M-UCT is 0.3 μm,the grinding force and the specific grinding energy firstly increase and then decrease as the grinding speed rises,and 80 m/s is the turning point.The grinding force shows the periodic grow th with the gradually increasing M-UCT.When the M-UCT is less than a critical value, the grinding force varies slowly.Nevertheless,the specific grinding energy declines quickly.The critical M-UCT value increaseswith the increase of grinding speed.High speed grinding can significantly reduce the grinding force and the specific grinding energy,and appropriate increment of M-UCT can not worsen the grinding quality.【期刊名称】《南京航空航天大学学报》【年(卷),期】2018(050)001【总页数】6页(P120-125)【关键词】磨削力;磨削比能;磨削速度;单颗磨粒最大未变形切厚;碳化硅陶瓷【作者】于腾飞;苏宏华;戴剑博;周文博【作者单位】南京航空航天大学机电学院,南京,210016;南京航空航天大学机电学院,南京,210016;南京航空航天大学机电学院,南京,210016;南京航空航天大学机电学院,南京,210016【正文语种】中文【中图分类】TN958碳化硅陶瓷因为具有良好的热稳定性、耐磨性、耐蚀性、高硬度以及低的膨胀系数等优越性能而被广泛应用于航空航天等工程领域[1]。
螺杆钻具转子特性与磨损规律研究

螺杆钻具转子特性与磨损规律研究作者:冯相尧来源:《中国科技博览》2014年第06期摘要:转子是螺杆钻具的核心部件,与定子相配合,决定了螺杆钻具的工作效率和动力性能。
主要研究不同泥浆固相含量和添加剂对螺杆钻具转子表面磨损的影响,设计专用试验装置以模拟近井下条件工作时螺杆钻具转子的表面磨损情况,对其磨损规律开展研究,探索了转子在不同泥浆条件下的磨损规律,并结合相关磨损机理进行了进一步分析。
初步发现了对硬铬镀层损伤较大的因素是泥浆固相与盐类添加剂,进而确定了硬铬镀层磨损的主要形式是腐蚀磨损,从而形成了对转子的制造工艺及使用方法的有益建议。
关键词:螺杆钻具;转子;硬铬镀层;工作寿命;试验分析;磨损规律;腐蚀磨损中图分类号:TH327螺杆钻具是目前国内外应用最广泛的一种井下动力钻具,其应用领域遍布常规、非常规油气资源钻井,地质勘探和地下工程。
定转子构成的马达是螺杆钻具的核心部件之一,可以把通过二者间隙的泥浆中蕴藏的动能转化成钻头破岩钻进所需的机械能。
马达结构复杂,暴露在恶劣的泥浆环境中,受到磨蚀等作用影响,失稳失效问题也日趋普遍,严重影响着螺杆钻具的整体寿命。
1 转子表面磨损过程相互接触的物体在相对运动中,表层材料不断损失、转移或产生残余变形的现象称为磨损,它是伴随着摩擦而产生的必然结果,包括粘着磨损、腐蚀磨损和磨料磨损等。
据统计,约有 80% 左右的机械零件是由于磨损而报废或失效,马达转子也不例外。
转子相对于定子高速旋转,做类似于纯滚动的复杂运动,井下工作时,转子与定子暴露在井下泥浆环境中,同时还要受到来自泥浆中对转子有害的化学物质的腐蚀和固态颗粒的磨蚀。
这些有害化学物质主要包括为了满足其它钻井工艺需要而添加的各种添加剂和未被有效分离的地层中固有矿物质,而固态颗粒主要是由难以被有效分离的破碎岩屑组成。
由于定转子材料不同,转子表面材料强度较高,故粘着磨损轻微,主要磨损原因是腐蚀磨损和磨料磨损,而这二者都来自泥浆作用。
轴向柱塞泵配流盘摩擦副材料的磨损实验研究
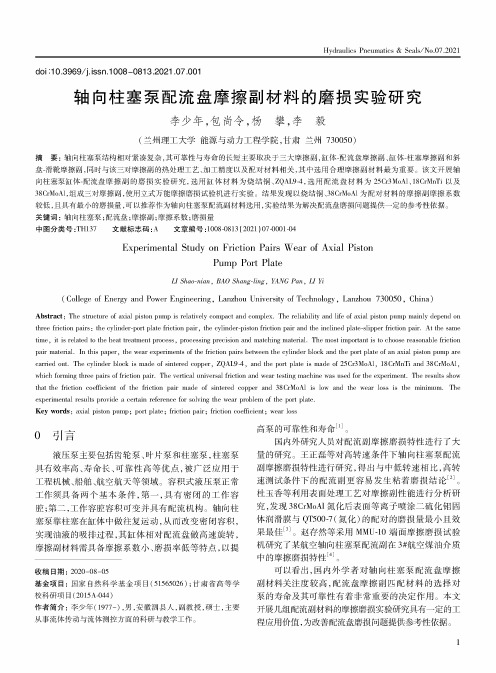
1
液压气动与&'/2021 (第07期
1实验系统与原理
1.1实验材料 针对轴向柱塞泵配流副摩擦特性要求,选用目前
Experimental Study on Friction Pairs Wear oO Axial Piston Pump Pori Plato
LI Shao-nian,Shang-ling,YANG Pan,LI Yi
(College of Enegy and Powes Engineering,Lanzhou University of Technology, Lanzhou 730050, China)
为48.0 m/。下试件平均磨损量为- 1.34610 x 10 一7
m//(N・m),磨损量为-0.7m/。摩擦副的总磨损量
为 47.3 m/。
时上下试件表
生轻微的刮擦磨损,下试
磨损量值为负,且负值 ,此时试 该处于一
非 的磨损情况,磨损量值可能 于零。摩擦
副对磨时摩擦
一
的 ,且波动
度
大,综合上下试件的轻微刮擦以及下试件
系。 后,通
向盘转动频率、车速、伺服阀频率
上接第
下试件磨损量 上试件磨损量
聲 蚤 «
第一组
第二组
第三组
图6上下试件磨损量统计
烧结铜,配流盘材料为氮化处理的38CrMoAl时,摩擦
副对磨时摩擦
一
的趋势,且上
销—盘法摩擦磨损实验的影响因素研究

东北大学硕士学位论文第1章绪论最佳的强韧性配合。
黄维刚等的研究表明f24】,在中低碳和中高碳低合金钢中,含适量下贝氏体的马氏体/贝氏体双相组织与马氏体组织相比,钢的强度少许下降,韧性明显改善。
综上所述,中低合金耐磨钢具有较高硬度,足够韧性的综合性能。
首先,在硬度大于50HRC的情况下,韧性值可达20--,40J/伽2,可在较大范围内控制硬度和韧性的匹配关系,在各类磨料磨损工况均可获得较好的耐磨性。
其次,它们具有良好淬透性,适当调整合金元素,可使不同尺寸工件淬透,也为空冷淬硬简化热处理工艺提供条件。
第三,其生产灵活易行,视工厂条件,可铸、可锻、也可轧制生产。
第四,这种合金耐磨钢的价格相对低廉,经济效益较高。
因而,中低合金耐磨钢有广阔的应用前景和重要的推广价值。
低合金耐磨钢由于具有较高硬度和足够韧性等综合性能,作为耐磨材料已引起人们的广泛重视。
研究人员通过调整成分与热处理工艺,能在较大范围内控制低合金耐磨钢硬度和韧性的合理匹配,使其满足不同磨损工况的需要【251。
中低合金耐磨钢成分的设计【26J:碳:它是决定材料硬度和韧性的最为主要的因素。
碳的含量直接影响马氏体组织的含量和形态。
另外,碳还起到固溶强化作用,是马氏体强化的主要微观机制,固溶强化的碳保证耐磨钢有较高的力学性能。
硅:硅可以降低钢的临界冷却速度,提高钢的淬透性。
它对钢的影响主要体现在硬度和冲击值方面。
硅固溶在铁素体或奥氏体中,起到了很好的固溶强化的作用。
、;锰:锰是扩大奥氏体相区元素,它除了降低共析温度外,还降低共析点的含碳量。
因此,相同含碳量及冷却速度下,随钢中含锰量的增加,显微组织中的珠光体不但细化,而且数量亦增多,从而导致钢的强度和硬度上升。
另外,A3温度下降使先共析铁素体在更低的温度下析出而细化。
Al温度下降,能抑制碳化物在过冷奥氏体晶界上的析出,使钢保持较高的塑性,降低钢的韧.脆性转变温度。
考虑锰的作用和研究对钢组织和性能的要求,锰的含量设计为O.7 ̄1.6%左右,锰含量不宜过高,容易增加钢的过热敏感性,使晶粒急剧增长。
风电密封件的摩擦学性能与耐磨机理分析

风电密封件的摩擦学性能与耐磨机理分析摩擦学性能和耐磨机理是影响风电密封件性能和寿命的重要因素。
风电密封件是风力发电装备中的关键部件,它的正常运行与否直接影响风力发电系统的效率和可靠性。
因此,对风电密封件的摩擦学性能和耐磨机理进行分析和研究,有助于提高其性能和寿命,进而促进风力发电技术的发展。
一、摩擦学性能分析1.1 摩擦学性能指标风电密封件的摩擦学性能可以通过摩擦系数、摩擦功率、摩擦磨损等指标进行评估。
摩擦系数是指摩擦力与法向力之比,它反映了密封件在摩擦过程中所受到的阻力大小。
摩擦功率是指单位时间内摩擦力所做的功,它在密封件的设计和运行过程中起着重要作用。
摩擦磨损是指摩擦过程中密封件表面的磨损程度,它直接影响密封件的使用寿命。
1.2 影响摩擦学性能的因素影响风电密封件摩擦学性能的因素主要包括密封材料的选择、表面粗糙度、润滑方式等。
密封材料的选择是影响摩擦学性能的关键因素之一。
不同材料具有不同的摩擦系数和磨损特性,正确选择合适的密封材料对于提高摩擦学性能非常重要。
表面粗糙度是影响摩擦学性能的另一个重要因素。
适当的表面粗糙度可以改善密封件的密封效果,降低摩擦系数,减少摩擦磨损。
润滑方式也对摩擦学性能有着重要影响。
合理选择润滑方式可以降低摩擦系数,减少磨损,延长密封件的使用寿命。
1.3 摩擦学性能的测试与评估对风电密封件的摩擦学性能进行测试与评估,可以通过实验方法和数值模拟方法来进行。
实验方法主要是通过摩擦试验、磨损试验等来获取摩擦学性能的相关数据。
数值模拟方法主要是利用计算机模拟软件对风电密封件的摩擦学性能进行预测与分析。
两种方法都可以提供有关摩擦学性能的重要参数,并为改进密封件设计和优化密封系统提供依据。
二、耐磨机理分析2.1 密封件的磨损形态风电密封件在使用过程中会受到磨损的影响,磨损形态主要包括磨粒磨损、表面接触磨损和疲劳磨损等。
磨粒磨损是指由于杂质和颗粒物在摩擦过程中引起的密封件表面磨损。
表面接触磨损是指由于密封接触部位的相对滑动引起的磨损现象。
单颗团聚CBN_磨粒磨削TC4_钛合金表面创成机制

第52卷第8期表面技术2023年8月SURFACE TECHNOLOGY·309·精密与超精密加工单颗团聚CBN磨粒磨削TC4钛合金表面创成机制赵彪1,2,章敏秀2,丁文锋2,李海3(1.重庆大学 机械传动国家重点实验室,重庆 400044;2.南京航空航天大学 机电学院, 南京 210016;3.中国航发南方工业有限公司,湖南 株洲 412002)摘要:目的提出一种兼具耐磨性好、自锐性能优异的新型团聚CBN磨粒研制方法,解决单晶CBN磨粒因其力学特性各向异性而极易出现沿解理面大块破碎的问题,进而提升加工效率和磨削性能。
方法利用模压成形和高温液相烧结技术,制备了综合性能优异的新型团聚CBN磨粒,探究磨粒结合界面形成机制,并通过单颗磨粒磨削TC4钛合金试验,综合对比团聚CBN磨粒与单晶CBN磨粒的磨损状态和磨痕形貌,探明团聚CBN磨粒的磨削性能优势。
结果团聚CBN磨粒烧结界面新生成了TiB2、TiB和TiN;优选的烧结工艺参数为800 ℃,保温时间为10 min;相比于单晶CBN磨粒,团聚CBN磨粒的耐磨性和锋利度显著提升,磨削加工效率和质量明显改善。
结论由于团聚CBN磨粒内部微晶颗粒间金属结合剂的存在,提高了磨粒的断裂韧性,降低了因磨粒内部裂纹扩展而引起的宏观裂纹损伤深度,有效提升了磨粒的加工性能;磨削过程中随着磨粒的不断磨损,未出露的CBN晶粒逐渐参与磨削,确保了磨粒工作面有效磨粒数的动态平衡,有助于提升磨粒整体自锐能力。
关键词:团聚CBN磨粒;TC4钛合金;微切削刃;磨痕形貌;锋利度中图分类号:TG580.6 文献标识码:A 文章编号:1001-3660(2023)08-0309-10DOI:10.16490/ki.issn.1001-3660.2023.08.025Grinding Surface Formation Mechanism of TC4 Titanium Alloywith a Single-aggregated CBN GrainZHAO Biao1,2, ZHANG Min-xiu2, DING Wen-feng2, LI Hai3(1. State Key Laboratory of Mechanical Transmissions, Chongqing University, Chongqing 400044, China;2. College of Mechanical and Electrical Engineering, Nanjing University of Aeronautics and Astronautics,Nanjing 210016, China; 3. AECC South Industry Co., Ltd., Hunan Zhuzhou 412002, China)收稿日期:2022-10-19;修订日期:2023-02-10Received:2022-10-19;Revised:2023-02-10基金项目:机械传动国家重点实验室开放基金资助(SKLMT-MSKFKT-202101);航空发动机及燃气轮机基础科学中心项目(P2023-B-IV- 003-001);国家自然科学基金青年项目(52205475);江苏省自然科学基金青年项目(BK20210295)Fund:Open Foundation State Key Laboratory of Mechanical Transmissions (SKLMT-MSKFKT-202101); Science Center for Gas Turbine Project (P2023-B-IV-003-001); National Natural Science Foundation of China (52205475); Natural Science Foundation of Jiangsu Province (BK20210295)作者简介:赵彪(1991—),男,博士,副研究员,主要研究方向为难加工材料磨削机理与过程优化。
采油单螺杆泵转子偏心率对碰摩系统的响应研究

第47卷第4期化工机械485采油单螺杆泵转子偏心率对碰摩系统的响应研究李大奇杨令仪祖海英魏雪形魏玉芬(东北石油大学机械科学与工程学院)摘要采油单螺杆泵在井下采油工作时,随着转速的提升存在运行不平稳的现象,针对这一问题建立了采油单螺杆泵转子偏心碰摩非线性系统动力学特性的数学模型。
将1/4导程的螺杆泵转子等效到单截面内进行建模。
通过数值计算,利用转子轴心轨迹图、相平面图、庞加莱图和振幅谱详细分析了转速比和偏心率对转子碰摩系统响应特性的影响,提高了对采油单螺杆泵转子系统碰摩规律的认识。
关键词采油单螺杆泵转子动力学转子偏心率中图分类号TQ051.21文献标识码A采油单螺杆泵是油田中重要的采油设备!单螺杆泵凭借对介质的适应性强、流量平稳、压力脉动小及自吸能力强等优点,广泛应用于油田中[1]!但是,单螺杆泵在高转速工作情况下存在运行不平稳的问题,这就需要对单螺杆泵的转子动力学进行研究!针对采油螺杆泵振动问题,张越等对地面驱动螺杆泵的抽油杆柱能耗制动进行分析,得出高阶固有频率对杆柱自由端振动影响较小,并给出杆柱受外力载荷时的主振动方程[2];许蕾对地面驱动单螺杆泵工况预测工作进行了数学模型的建立,解决了工作过程中相关工艺参数的预报问题⑶;吕彦平等建立了单螺杆泵采油系统启动扭矩动力学模型,并取得良好的现场使用效果,为提高螺杆泵采油系统效率和工况诊断提供了理论基础[4];廖金军等根据工业现场螺杆泵异常振动情况进行分析,给出了从确定原因到消除异常工况的办法[5]!根据当前转子动力学方向的研究进展,侯兰兰和向玲建立碰摩力作用下参数不确定转子系统的动力学模型,得出偏心量取中等值时系统的运行状态最复杂['];赵道利等分析了混合偏心对不平衡磁拉力作用下偏心转子-轴承系统振动特性影响,得出净偏心量碰摩系统数值模拟文章编号0254-6094(2020)04-0485-06与转子重力夹角值越大系统越趋于稳定[7];徐学平等通过建立不平衡磁拉力、静载荷、不平衡质量共同作用下转子系统运动微分方程,分析得出净偏心方向影响轴心轨迹的位置分布,且净偏心量过大会加剧振动[8];花纯利等在对转子-橡胶轴承系统的分析研究中,首次考虑橡胶轴承的非线性,建立了转子碰摩系统动力学模型,并分析了系统参数对转子系统动力学行为的影响[9];何鹏等推导出考虑转子轴向温度分布的有限元模型,体现转子轴向温度分布对刚度矩阵的影响,提高高温工作转子临界转速计算精度[10]!当前国内外对采油螺杆泵振动方向的研究多集中于抽油杆柱的振动和泵体外部振动,因采油单螺杆泵定转子相对运动形式的特殊性,尚没有针对采油单螺杆泵转子系统动力学方向的研究,因采油单螺杆泵实际工作过程中需要反复进行转子相对定子的半圆周纯滚动和直线运动,笔者针对定子橡胶发生溶胀之前定转子之间尚有预留间隙,采油单螺杆泵转子相对定子进行圆周运动阶段,将1/4导程的运动简化在一个单截面内建立转子系统动力学模型,利用数值积分的方法求解并进行动力学响应特性的分析!研究了转速、偏心率对作者简介:李大奇(1978-),副教授,从事采油螺杆泵理论及应用技术研究、石油机械装备设计及开发工作通讯作者:祖海英(1979-),副教授,从事采油螺杆泵理论及疲劳寿命研究,**********************。
高转速条件下轴向柱塞泵配流副摩擦磨损特性

高转速条件下轴向柱塞泵配流副摩擦磨损特性王正磊; 吴玉程; 黄家海【期刊名称】《《液压与气动》》【年(卷),期】2019(000)008【总页数】6页(P27-32)【关键词】轴向柱塞泵; 配流副; 高转速; 摩擦磨损【作者】王正磊; 吴玉程; 黄家海【作者单位】太原理工大学新型传感器与智能控制教育部重点实验室山西太原030024; 太原理工大学教育部新材料界面科学与工程重点实验室山西太原030024; 太原理工大学机械与运载工程学院山西太原030024【正文语种】中文【中图分类】TH137引言轴向柱塞泵具有工作压力高、效率高、寿命长以及易于变量控制等优点,被广泛应用于工程机械、船舶和航空航天等领域。
轴向柱塞泵配流副不仅要同时满足支撑、密封和配流多重功能,同时还需具备摩擦系数小、磨损率低等特点,以提高整泵的工作效率和使用寿命。
国内外研究人员对轴向柱塞泵配流副摩擦磨损特性开展了大量研究[1]。
赵存然等[2]采用 MMU-10端面摩擦磨损试验机研究了某航空轴向柱塞泵配流副(材料为PEEK-38CrMoAlA)在3#航空煤油介质中的摩擦磨损特性。
ZHU等[3]研究了低速工况下表面形貌对配流副摩擦磨损特性的影响规律,结果表明表面光滑的硬材料可以防止软材料附着,显著提升摩擦副的摩擦磨损性能。
韩国航空航天大学科研团队在基体材料为AISI 4340的配流盘表面添加PVDTiN[4], duplex TiN[5],CrSiN[6] 和 Cr-X-N (X=Si,Zr) [7] 涂层,并利用摩擦磨损试验机测试其摩擦特性,实验结果表明在低速条件下配流副摩擦特性得到改善。
周杰等[8]就海水径向柱塞泵陶瓷摩擦副的摩擦学性能开展研究,得出ZrO2与17-4PH配对适合作为海水环境中接触摩擦副配对材料。
李阳等[9]利用自行研制的配流副摩擦磨损试验机在150~750 r/min 转速范围内研究了织构化配流副的摩擦磨损特性,研究结果表明:设计合理的表面织构能有效减小摩擦系数和磨损量。
基于圆柱型表面织构的配流盘摩擦特性研究

基于圆柱型表面织构的配流盘摩擦特性研究
王宇帆;江滔;郑国财;李小静;刘汗青
【期刊名称】《中国农机装备》
【年(卷),期】2024()3
【摘要】建立了带有圆柱型微观织构配流盘的油膜弹流润滑模型,采用有限差分法求解雷诺方程,迭代之后求得符合误差允许的离散近似解。
将得到的数值解导入MATLAB中绘制出微观织构配流副油膜特性云图。
通过对比不同工况下带有微观
织构与不带微观织构的配流盘之间的油膜摩擦特性差异,发现织构表面的配流盘能
有效提高油膜的承载力,减少配流盘与缸体之间的接触,减小摩擦系数,改善润滑条件。
【总页数】6页(P10-15)
【作者】王宇帆;江滔;郑国财;李小静;刘汗青
【作者单位】合肥职业技术学院汽车工程学院
【正文语种】中文
【中图分类】G63
【相关文献】
1.织构化轴向柱塞泵配流副的摩擦特性试验研究
2.浮杯泵织构化配流副表面的承载特性仿真分析
3.热流固耦合下微观织构配流副摩擦特性的研究
4.盘式摩擦副沟槽
织构摩擦磨损特性研究5.激光加工表面织构对配流盘重载摩擦副摩擦磨损特性的
影响
因版权原因,仅展示原文概要,查看原文内容请购买。
转子压缩机摩擦副的磨损预测及试验验证

转子压缩机摩擦副的磨损预测及试验验证
黄之敏
【期刊名称】《家电科技》
【年(卷),期】2024()2
【摘要】转子压缩机面临新型制冷剂和新领域的快速拓展,以及客户使用条件的日趋严苛,对可靠性要求越来越高的挑战,但业内没有成熟的摩擦副磨损预测方法。
针
对某R290热泵专用压缩机,以叶片-叶片槽这一摩擦副为例,从边界润滑、混合润滑、流体润滑的基本模型入手,综合压缩机运行过程中负载、油-制冷剂的混合物性、转速等影响因子,采用经典的Archard模型,建立了转子压缩机摩擦副的磨耗量预测理论模型,仿真结果与长期可靠性试验后实测磨耗量相印证,具有较好的一致性;该方法的建立,有助于转子压缩机快速可靠性预测,提升开发速度。
【总页数】5页(P58-62)
【作者】黄之敏
【作者单位】上海海立电器有限公司
【正文语种】中文
【中图分类】TB114.3;TH455
【相关文献】
1.旋转式压缩机定转子摩擦副材料的配伍性试验
2.新能源汽车电动涡旋压缩机摩擦副的磨损及改善
3.压缩机摩擦副磨损强度计算
4.基于制动器摩擦副销-盘试验的第
三体摩擦磨损特性研究5.1种双配副摩擦试验机及其在多孔聚酰亚胺摩擦磨损测试方面的应用
因版权原因,仅展示原文概要,查看原文内容请购买。
- 1、下载文档前请自行甄别文档内容的完整性,平台不提供额外的编辑、内容补充、找答案等附加服务。
- 2、"仅部分预览"的文档,不可在线预览部分如存在完整性等问题,可反馈申请退款(可完整预览的文档不适用该条件!)。
- 3、如文档侵犯您的权益,请联系客服反馈,我们会尽快为您处理(人工客服工作时间:9:00-18:30)。
单磨粒的转子配流盘摩擦磨损规律研究
摘要:航空液压泵的故障问题中,柱塞泵中转子-配油盘摩擦副对于保持液压泵的容积效率非常重要,而磨粒磨损是造成其泄漏的主要原因。
现根据磨粒磨损理论,结合转子与配流盘间的实际情况,建立了磨粒磨损理论模型,提出了配流盘上磨粒的磨损量期望的理论计算方法。
由转子配流盘间的间距仿真结果,得出转子与配流盘间的间距呈周期性起伏。
并为磨损量的实时曲线仿真提出了可行的流程方案。
进行了数值计算,通过matlab仿真模拟了磨粒在磨损过程中的压入深度变化。
关键词:磨粒磨损;转子配流盘;摩擦学
引言
航空液压泵是飞机起飞、操纵、起落架收放和刹车的关键部件。
飞机液压泵一旦发生故障,轻则引起飞机液压系统不正常工作,重则造成机毁人亡,带来巨大的经济损失和不良的国际影响。
据统计,航空液压泵80%以上的故障是由于磨损污染造成的。
尤其是飞机液压系统向高压化方向发展,油液污染导致的液压泵磨损愈加显著[1]。
而在这磨损之中,柱塞泵中转子-配油盘摩擦副对于保持液压泵的容积效率非常重要,试验数据表明[2],该摩擦副的泄漏量占液压泵全泵泄漏量的70%以上。
国内外大量学者都针对该摩擦副的磨损进行了大量研究工作。
一直以来,磨损是国内外摩擦学研究的重要部分。
人们对磨损机理的分析和理解也愈加成熟。
Jacobson等[3]建立了考虑多个磨粒同时作用的纯切削过程的统计学模型。
利用该模型研究了磨粒尺寸、载荷及工件表面硬度对磨损率的影响。
预测了发生接触的磨粒数量和磨损表面形貌。
方亮等人[4]为探讨三体磨料磨损中磨料颗粒粒径的分布对材料磨损性能的影响,通过试验结合正态概率分布坐标分析的方法,比较准确地得到磨料粒径的分布情况。
ArnoldIsmailov等[5]人用硬度不同的两种磨粒粉进行了磨损实验,发现对于硬度低的磨粒,滑行速度越快,越不易磨损。
对于硬度高的磨粒,速度越快,磨损越严重。
转子与配流盘间的磨粒磨损是一个非常复杂的过程,这是一个实时变化的随机过程,并且磨粒的分布也具有随机性。
所以多年以来,对于转子与配流盘间的磨粒磨损研究主要集中在实验基础上。
探索不同磨粒对应的磨损情况,泄漏量与磨损量的关系等,而少有人对转子与配流盘间的磨粒磨损有直接的计算及研究磨损规律。
本文参考了前人的研究方法和一些结论,针对转子配流盘间的具体情况,提出了自己的理论计算。
研究了磨粒在转子配流盘摩擦磨损规律。
1.液压泵转子配流盘摩擦磨损机理分析
1.1结构及工作原理
柱塞泵是液压系统的一个重要装置。
它依靠柱塞在缸体中往复运动,使密封工作容腔的容积发生变化来实现吸油、压油。
目前,大部分的民用飞机大部分依然使用的是轴向柱塞泵,来满足其高压、大流量和流量易调节的需求。
如图2.1所示,轴向柱塞泵主要由传动轴、配流盘、缸体、斜盘等组成。
轴向柱塞泵按结构分类,主要有斜盘式轴向柱塞泵和斜轴式轴向柱塞泵。
图1轴向柱塞泵结构图
2.转子配流盘磨粒磨损分析
为了方便计算,对磨粒磨损做如下假设:
(1)假设磨粒为刚性小球。
(2)磨粒位置随机。
(3)转子的硬度大于配流盘的硬度,因此磨损的状况主要发生在配流盘上,只考虑在配流盘上的磨损。
2.1不考虑材料的变化的摩擦磨损
(1)平均压强的计算
在接触力学中,如果发生磨损,可以分为弹性磨损和塑性磨损。
假设产生磨损的临界进入深度为。
根据接触力学理论[6]。
当,材料屈服开始。
当,开始发生塑性变形。
而对于压力P的求解,可根据压入深度求解。
图2磨粒压入示意图
由上图的几何关系,可以求解出,D为磨粒的直径,为压入深度。
,当,为完全弹性变形,由得。
,当,弹塑变形。
,当,完全塑性变形。
由得。
然而,这样的载荷计算只限于光滑平面上的磨损,而实际中,磨损是在粗糙平面上进行的。
需要加入一个修正系数
A为实际接触面积,为光滑平面接触面积。
与表面形貌有关,是一个不确定量。
(2)弹性变形和塑性变形的判断
克拉盖尔斯基(Kragelskii)提出,假定用尖端半径为d的球形磨粒在金属表面压入深度并划动,根据的比值不同,即接触特性的不同,可以将磨粒和表面的相互作用划分为如下几类,对于铁基合金,当
弹性变形
塑性变形
切削
磨损量比例与有关。
越大即压入越深,越大。
可以假设成线性关系:
,
由牛顿第二定律知:。
3.结论
转子与配流盘间的间距存在周期性的正弦起伏变化。
由于出油高压区的间距较小,高压区附近的磨损最为严重。
通过理论推导与计算,得到了磨粒在转子配流盘间的磨损期望计算公式。
另外,本文为磨损的实时曲线仿真提出了可行的流程方案。
计算了粒径为的磨粒随转子转动,在配流盘配流盘上的压入深度曲线。
在弹性变形区域,可见压入深度随着转子配流盘间的高度减小而快速增长。
当进入塑性变形区域,压入深度减慢。
参考文献:
[1]葛薇,王少萍.航空液压泵磨损状况预测[N].北京航空航天大学学报,2011-11.
[2]张文超,王少萍,赵四军.柱塞泵三对摩擦副对回油流量的影响分析[C].第五届全国流体传动与控制学术会议暨2008年中国航空学会液压与气动学术会议论文集,2008:965-970
[3]JacobsonS,WallenP,HogmarkS.Fundamentalaspectsofabrasivewearstudiedbyanewnumericalsimulationmo
del[J].Wear,1998,123:207-223.
[4]杜道山,方亮,李从心.三体磨料磨损中磨料粒径分布测定试验研究.润滑与密封,总第167期,2005年1月.。