涤纶绒类织物的节能减排印染工艺
面料染色工艺的环保与节能措施

面料染色工艺的环保与节能措施1. 引言面料染色作为纺织行业中重要的一个环节,其对环境和能源的消耗非常大。
随着环保意识的增强和能源资源的紧张,如何在面料染色过程中实施环保与节能措施逐渐成为行业关注的焦点。
本文将从减少水、化学品的使用、提高能源利用效率、回收利用废水和废气等方面,探讨面料染色工艺的环保与节能措施。
2. 减少水、化学品的使用2.1 水的节约利用面料染色过程中,水的使用量很大。
为了减少水的使用,可以采取以下措施:•安装节水装置,如水流量控制器、节水型染缸等,在染色过程中减少水的流失。
•优化染色工艺,减少染色过程中的漂洗次数,合理控制染色液浓度和水温,降低染液的排放浓度。
2.2 化学品的减少使用染色工艺中,化学品的使用量相当大。
为了减少化学品的使用,可以采取以下措施:•优化染色剂的选择,选用高效、低污染的染色剂,减少废弃物的产生。
•推广使用可再生纤维素染料,减少对有毒化学品的依赖。
•推广使用催化剂和增良剂,提高染色剂的利用率和反应速度。
3. 提高能源利用效率3.1 应用高效能源设备在面料染色过程中,能源的消耗较大。
为了提高能源利用效率,可以采取以下措施:•更新染色设备,使用高效能的染色机,提高染色效率。
•应用节能照明设备,采用LED灯等低能耗照明设备。
3.2 优化染色工艺在染色工艺中,通过优化操作,可以减少能源的消耗:•优化染色时间、温度和湿度控制,减少能耗。
•采用优化的染色工艺,减少热能损失。
4. 回收利用废水和废气染色生产过程中会产生大量的废水和废气,对环境造成污染。
为了回收利用,可以采取以下措施:4.1 废水的回收利用•安装废水处理设备,如沉淀池、过滤器等,对废水进行初步处理,并将其回收利用于清洗、冲洗等环节。
•发展循环用水系统,将处理后的废水循环利用于染色过程中。
4.2 废气的处理与回收利用•安装废气净化设施,对染色过程中产生的废气进行净化处理,减少对大气的污染。
•回收废气中所含的有价值成分,如染料、溶剂等。
印染企业节能减排措施

印染企业节能减排措施随着社会发展和环境保护意识的提高,印染企业也面临着减少能源消耗和减少排放的压力。
为了实现可持续发展,印染企业需要采取各种节能减排措施。
以下是一些常见的节能减排措施:1.优化生产过程:通过对生产流程进行优化,如对染料和助剂的选择进行科学合理的配置,降低化学物质的使用量,并采用高效节能的机械和设备来取代老旧设备。
2.推广清洁能源:印染企业可以投资建设清洁能源发电设备,如太阳能、风能等,以替代传统的能源消耗方式,减少使用煤炭和石油等高碳能源。
3.安装节能设备:安装节能设备如热回收系统、热泵、LED照明等,以减少对电力和热能的需求,降低能耗。
4.提高能源利用效率:采用先进的加热、压缩和干燥技术,最大限度地提高能源利用效率,降低能源消耗。
5.加强管理和培训:加强对员工的能源管理培训,提高员工的环保意识和技能,推动能源管理工作的落实。
6.增加废弃物回收利用:印染企业应加强废弃物的分类和回收利用工作,如废水和废气的处理,废棉和废纸的再利用,减少废弃物对环境的污染。
7.加强监测和数据分析:建立有效的监测体系,及时收集并分析能耗和排放数据,掌握企业的能源和环境状况,为进一步节能减排提供数据支持。
8.推广环保技术和工艺:积极引进和推广环保技术和工艺,如水处理技术、催化剂等,以提高印染企业的环境污染治理能力。
9.加强合作交流:加强与相关政府机构、环保组织和行业协会的合作交流,共同研究并推广节能减排的新技术、新理念和新方法。
10.建立激励机制:建立激励机制,对实施节能减排措施的企业给予政策支持和奖励,增强企业的积极性和主动性,推动节能减排工作的开展。
综上所述,印染企业在节能减排方面有很多可行的措施。
通过采取这些措施,印染企业可以在提高经济效益的同时,达到节约能源、减少排放、保护环境的目标,实现可持续发展。
纺织印染行业的碳排放情况和碳减排技术
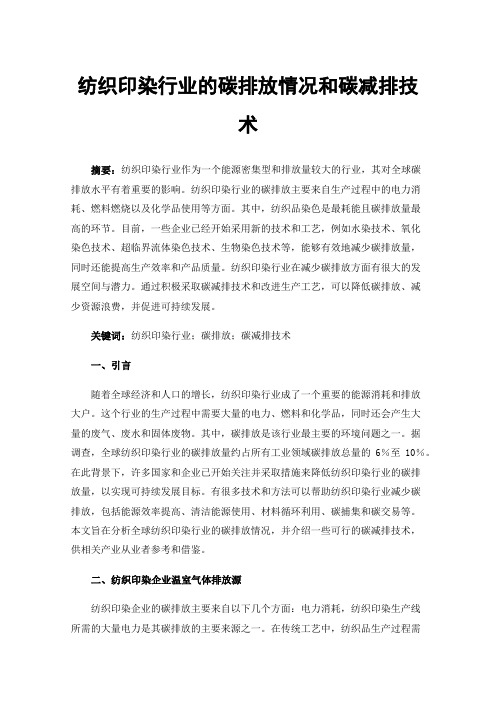
纺织印染行业的碳排放情况和碳减排技术摘要:纺织印染行业作为一个能源密集型和排放量较大的行业,其对全球碳排放水平有着重要的影响。
纺织印染行业的碳排放主要来自生产过程中的电力消耗、燃料燃烧以及化学品使用等方面。
其中,纺织品染色是最耗能且碳排放量最高的环节。
目前,一些企业已经开始采用新的技术和工艺,例如水染技术、氧化染色技术、超临界流体染色技术、生物染色技术等,能够有效地减少碳排放量,同时还能提高生产效率和产品质量。
纺织印染行业在减少碳排放方面有很大的发展空间与潜力。
通过积极采取碳减排技术和改进生产工艺,可以降低碳排放、减少资源浪费,并促进可持续发展。
关键词:纺织印染行业;碳排放;碳减排技术一、引言随着全球经济和人口的增长,纺织印染行业成了一个重要的能源消耗和排放大户。
这个行业的生产过程中需要大量的电力、燃料和化学品,同时还会产生大量的废气、废水和固体废物。
其中,碳排放是该行业最主要的环境问题之一。
据调查,全球纺织印染行业的碳排放量约占所有工业领域碳排放总量的6%至10%。
在此背景下,许多国家和企业已开始关注并采取措施来降低纺织印染行业的碳排放量,以实现可持续发展目标。
有很多技术和方法可以帮助纺织印染行业减少碳排放,包括能源效率提高、清洁能源使用、材料循环利用、碳捕集和碳交易等。
本文旨在分析全球纺织印染行业的碳排放情况,并介绍一些可行的碳减排技术,供相关产业从业者参考和借鉴。
二、纺织印染企业温室气体排放源纺织印染企业的碳排放主要来自以下几个方面:电力消耗,纺织印染生产线所需的大量电力是其碳排放的主要来源之一。
在传统工艺中,纺织品生产过程需要照明、加热、冷却等多种电力设备。
此外,在一些地区,用电不稳定也会导致能源浪费和碳排放增加。
燃料燃烧,燃料燃烧是纺织印染行业的另一个重要碳排放源。
许多企业使用煤、油和天然气等化石燃料作为主要能源来源,这些能源的燃烧过程会产生大量的CO2排放。
化学品使用,在纺织印染生产过程中,许多化学品都被用作染料、助剂和梳理剂等。
纺织印染节能减排设计范文

纺织印染节能减排设计范文1. 引言纺织印染行业是中国重要的传统产业之一,但同时也是能源消耗和环境污染较大的行业之一。
为了实现可持续发展,纺织印染行业亟需提高节能减排水平,减少对环境的负面影响。
本文将探讨纺织印染节能减排的设计方案,旨在促进行业的绿色转型和可持续发展。
2. 纺织印染节能减排设计方案2.1 设备更新与优化•更新老旧设备:采用能源消耗更低、效率更高的新型设备替代老旧设备,减少能源消耗,并提高生产效率。
•优化设备配置:通过合理配置设备,减少资源浪费和能源损耗。
例如,在染色过程中合理梳理机器布局,减少能源的不必要损耗。
2.2 制定节能减排标准与指导意见•制定行业标准:建立针对纺织印染行业的节能减排标准,明确各项指标和限值,引导企业合理选择技术与生产方式,降低对能源和环境的影响。
•提供技术指导:为企业提供节能减排的技术指导与咨询服务,帮助企业实施相应的节能措施,促进技术的创新与推广。
2.3 推动清洁生产和循环经济模式•推广清洁生产:鼓励企业采用清洁生产技术,减少生产过程中的废水、废气和废物排放。
•建设循环经济系统:推动纺织印染行业构建完整的循环经济系统,通过资源的回收再利用,最大限度地减少资源的消耗和环境的污染。
2.4 培训与教育•举办培训班和研讨会:为纺织印染从业人员提供节能减排的相关培训和教育,提高行业的整体素质和节能减排意识。
•开展技术交流:组织行业内的技术交流活动,促进各企业之间的合作与经验共享,推动行业的技术创新和进步。
3. 纺织印染节能减排设计方案的作用与影响3.1. 促进绿色转型与可持续发展通过上述的节能减排设计方案的实施,可以降低纺织印染行业的能源消耗和环境污染,并提高生产效率,促进行业的绿色转型和可持续发展。
3.2. 降低生产成本节能减排设计方案的实施可以优化生产过程和设备配置,减少能源和资源消耗,从而降低企业的生产成本。
3.3. 提升企业形象与竞争力执行节能减排设计方案可以提高企业的环境意识和社会责任感,增强企业形象,提升竞争力。
当前印染行业节能减排的主要措施

当前印染行业节能减排的主要措施1.优化生产工艺:印染企业通过改进生产工艺,减少能源消耗和废料产生。
例如,采用低温染色工艺、高效纺织设备和新型催化剂等,可以降低能源消耗和废料排放。
2.推广节能设备:企业推广使用节能设备,如高效烘干机、节能印染设备和高效电机等,以降低能源消耗。
这些设备能有效减少能源消耗和排放。
3.提高资源利用率:印染企业通过优化生产流程,减少废弃物的产生。
例如,回收和再利用废水、废渣和废气等,可以降低资源消耗和环境污染。
5.强化监管和管理:政府加强监管和管理,对印染企业的排放标准进行严格把关,推动企业遵守环境保护法规和减排要求。
同时,推动企业建立和完善环境管理体系,加强对节能减排工作的监督和评估。
6.加强技术创新和研发:印染企业加强技术创新和研发,开发和应用更加环保的印染技术和材料。
这有助于减少能源消耗和废弃物产生,提高生产效率和产品质量。
7.推动绿色供应链管理:印染企业与供应商和客户建立合作关系,共同推动绿色供应链管理。
通过对整个供应链的节能减排工作的推动,实现资源的共享和协同管理,从而减少环境影响。
8.提升员工意识和培训:印染企业提升员工的环保意识和技术水平,通过培训和教育,加强环保法规和减排要求的宣传和培训。
这有助于员工积极参与节能减排工作,提高企业的整体环保水平。
9.加强国际合作和交流:印染行业加强与国际组织和企业的合作和交流,学习和借鉴先进的节能减排经验和技术。
通过共享资源和经验,加速行业的绿色转型和可持续发展。
总之,当前印染行业在节能减排方面已经采取了多种主要措施。
这些措施涵盖了生产工艺的优化、推广节能设备、提高资源利用率、推广清洁能源、强化监管和管理、加强技术创新和研发、推动绿色供应链管理、提升员工意识和培训以及加强国际合作和交流等方面。
这些措施将帮助印染企业实现节能减排目标,减少对环境的负面影响,推动行业的绿色转型和可持续发展。
印染行业中的节能减排措施与清洁生产建议
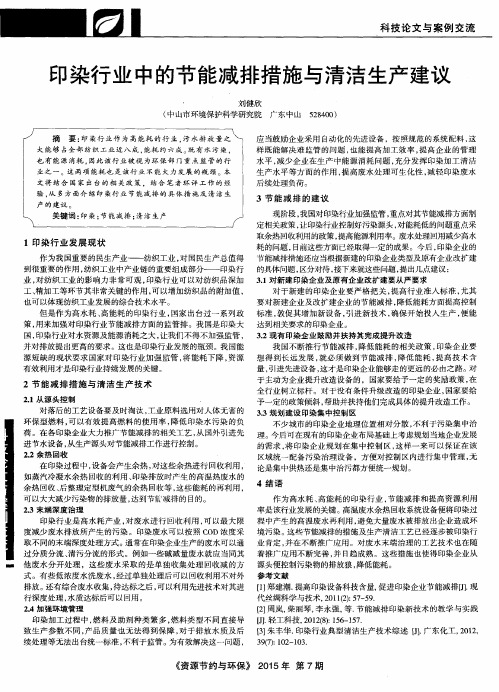
但是作为高水耗 、 高能耗 的印染行 业 , 国家 出台过一 系列政 策, 用来加强对 印染行业节 能减排方 面的监管 排。我国是印染大 国, 印染行业对水资源及能 源消耗之 大 , 让我们不得不加强监管 , 并对排放提 出更高的要求 。这也是 印染行业发展 的瓶颈 。我 国能 源短缺的现状要求 国家对 印染行 业加强监 管 , 将能耗 下降 , 资源
量, 引进先进设备 , 这才是印染企业 能够走 的更远的必由之路 。对 于主动为企业提升改造设备的 ,国家要给予一定 的奖励政策 , 在 全行业树立标杆 。对于没有条件升级改造的印染企业 , 国家要 给
2节能 减排 措施 与清 洁生产 技 术
2 . 1从 源 头控 制
予一定 的政 策倾斜 , 帮助并扶持他们完成具体的提升改造工作 。 对落后的工艺设 备要及时淘汰 , 工业 原料 选用对人体无害的 3 . 3规划建设印染集中控制 区 环保型燃料 , 可 以有效 提高燃料 的使用率 , 降低 印染水污染 的负 不少城市的印染企业地理位置相对分散 , 不 利于污染集 中治 荷 。在各印染企业大力推广节能减排 的相关工艺 , 从国外引进先 理 。 今后可在现有 的印染企业布局基础上考虑规划 当地企业发展 进节水设备 , 从生产源头对节能减排工作进行控制。 的需求 , 将印染企业规 划在集 中控制 区, 这样一来 可 以保证在 该
4结 语
作为 高水耗 、 高能耗 的印染 行业 , 节能减排 和提高 资源利用
2 . 3末 端 深 度 治理 率是该行业发展的关键 。 高温废水余热 回收系统设备便将 印染过 印染行业是 高水耗产业 , 对废 水进行 回收利用 , 可 以最大 限 程 中产生 的高温废水再利用 , 避免大量废水被排放 出企业造成环 度减少废水排放所产生 的污染 。印染废水可 以按照 C O D浓度采 境污染 。 这些节能减排的措施及生产清洁工艺已经逐步 被印染行 并在不断推广应用 。对废水末端治理 的工艺技术也在 随 取不同的末 端深度处理方式 。 通常在印染企业 生产 的废水可 以通 业肯定 ,
关于我国印染行业的能耗环保现状及节能减排技术的发展趋势

关于我国印染行业的能耗环保现状及节能减排技术的发展趋势进入21世纪后,我国的纺织行业在生产过程中带来的资源消耗大、污染物排放量多的矛盾日益显现,国家出台的一系列政策法规已经向纺织印染行业频频发出警示:《国民经济和社会发展第十一个五年规划纲要》的22项经济和社会发展指标中,与印染行业直接相关的约束性指标是:在“十一五”期间,单位国内生产总值能源消耗降低20%左右,单位工业增加值用水量降低30%,主要污染物排放总量减少10%;2006年10月1日起,国家环保总局公布的《清洁生产标准纺织业(棉印染)》(HJ/T185-2006)正式执行,该标准从生产工艺和设备、原材料、资源消耗和污染物产生指标、生态纺织品、环境管理等各个方面提出了新的要求;国家环保总局组织的按纺织产品细分的印染行业污染物排放标准正在紧锣密鼓编制之中;国家发改委组织于2008年2月4日发布了“印染行业准入条件”(发改委2008年第14号公告)已经于2008年3月1日起实施。
节能减排已成为印染企业中使用频率最高的名词,成为各级政府和行业的管理目标,印染行业面临空前的压力!一、“十五”以来我国印染工业资源消耗和污染状况1.1 单位产品能耗和水耗量大我国纺织工业特别是印染工业存在能耗、水耗高的问题,表1反映了我国目前棉印染单位产品的平均取水量和美国1990年代棉纺织品印染加工平均用水量以及我国和加拿大90年代代表性纺织印染加工企业的综合能耗水平。
由表1可见,我国印染加工过程单位产品的能耗和水耗与先进国家与地区90年代相比,仍然有较大差距。
据2008年初对有关印染厂的调查,目前印染产品加工过程的能耗情况见表2。
注:表中数据系2008年初对江苏、浙江15家典型工厂的调查数据。
据有关资料介绍,我国台湾地区印染生产的能源消耗情况如表3所示:从调研结果来看,浸渍加工方式的水耗和能耗与先进水平相比差距比较大。
1.2 纺织印染废水排放量大2000年以来,纺织印染工业在迅速发展的同时,环境保护问题也愈发突出。
印染企业节能减排措施

印染企业节能减排措施印染企业作为传统工业部门之一,在生产过程中往往会对环境造成较大的污染和能源浪费。
因此,采取有效的节能减排措施对于印染企业来说至关重要。
以下是一些印染企业可以采取的节能减排措施,供参考:1.提高能源利用效率:-审查和改进设备的设计和使用,优化能源消耗。
-使用高效的生产设备和合适的工艺技术,减少能源浪费。
-定期检查和维护设备,确保其正常运行,减少能源的不必要消耗。
-使用节能型照明设备,合理利用自然光。
-使用节能型电动机,控制和运行设备时优化功率因数。
2.推广清洁生产技术和工艺:-研究并引入先进的清洁生产技术和工艺,减少废水、废气和固体废弃物的产生。
-采用闭路循环冷却水系统,减少水资源的使用和废水的排放。
-使用新型高效废气处理设备,减少排放物的含量。
-使用净化装置,处理废水和固体废弃物。
3.优化原材料使用:-合理选择和使用原材料,减少原材料的浪费和消耗。
-抓住绿色产品潮流,推广和使用环保原材料。
-使用替代品,减少对有毒有害物质的依赖。
4.建立环保管理与监控系统:-建立和完善环境管理体系,确保企业环保工作的有效开展。
-制定环保操作规程和作业指导书,规范生产活动。
-定期进行环境监测和检测,改进环境影响评价和污染监控技术。
5.促进员工节能减排意识:-建立节能减排意识培训体系,提高员工的环保意识和技能。
-设计并实施奖励机制,鼓励员工节约能源和减少污染物排放。
-增加员工参与环保决策和环境管理的机会,提升员工的参与度。
综上所述,印染企业要实施有效的节能减排措施,需要从多个方面入手。
通过提高能源利用效率、推广清洁生产技术和工艺、优化原材料使用、建立环保管理与监控系统以及促进员工节能减排意识等措施的综合作用,印染企业可以大幅减少对环境的影响,实现可持续发展。
涤纶机织物的碱减量加工

Alkali De - weighting Process of PET Woven Fabric
文 / 沈志平 贺良震
涤纶具有良好的强度、适中的刚性和较好的可染性, 因此其应用范围日益扩大。涤纶强捻织物的仿真丝绸整理 加工和涤纶新合纤的仿麂皮绒产品加工都离不开碱减量。 仿麂皮绒产品的“开纤”和其他涤纶产品轻减量的大量使 用,使研究碱减量加工工艺仍具有现实意义。
用标准酸滴定工作液中有效碱浓度的方法是可行的。
纺织导报 China Textile Leader · 2009 No.1
77
应用技术 染整及纺织化学品|Dyeing & Finishing & Textile Chemicals
稳定了碱的浓度,只要再控制住减量温度和减量时间,就可 有效控制织物减量率。控制织物的减量率也就是控制织物 的手感。练池的底部接有蒸汽管,也可给减量工作液加热。 练池减量的温度一般控制在 60 ~ 70 ℃左右。减量织物生 产的高峰期一般在夏季,夏季减量,既可以避免产生雾气, 有利于安全生产,也可以减缓练池内工作液降温的速度。
连续式减量机一般为平幅减量,特别适合于大批量的 轻薄涤纶强捻机织物。强捻麻纱、强捻花瑶和强捻雪纺织 物都适合连续加工。大批量轻薄织物减量手感的统一性是 连续减量机的加工优势。无论是练池减量、染缸减量,还是 减量机减量,都很难做到大批量轻薄强捻织物减量手感的 统一。减量重,手感要求高,是对大批量强捻轻薄涤纶机缸 减量产品基本要求。液碱利用率高,生产效率高,水洗效果 好,是连续减量机主要特点。表 1 比较了 4 种减量设备和 工艺的主要特点。
间歇式减量机是改进的减量缸,1 台减量机相当于 2 台减量缸。位于减量机顶部的液碱回收装置提高了减量残 碱利用率。减量机减量温度高于练池减量温度,可以达到 98 ℃,但仍然低于染缸减量的 125 ℃。由于加工量的提高 和液碱的有效利用,总体减量效率比较高。间歇式减量机 一经出现便受到染厂欢迎。减量温度虽低于染缸减量,却 有利于随时控制织物的手感。 1.4 连续式减量机减量
技术控高耐碱性分散染料染色工艺,涤纶超细纤维在高碱性下节能减排!
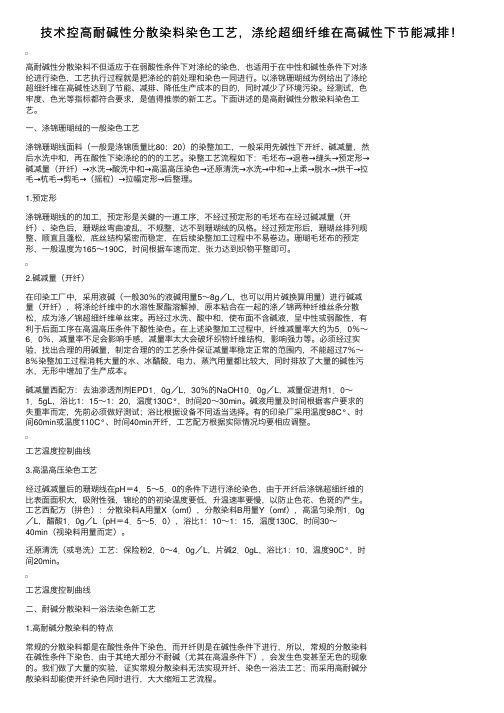
技术控⾼耐碱性分散染料染⾊⼯艺,涤纶超细纤维在⾼碱性下节能减排!⾼耐碱性分散染料不但适应于在弱酸性条件下对涤纶的染⾊,也适⽤于在中性和碱性条件下对涤纶进⾏染⾊,⼯艺执⾏过程就是把涤纶的前处理和染⾊⼀同进⾏。
以涤锦珊瑚绒为例给出了涤纶超细纤维在⾼碱性达到了节能、减排、降低⽣产成本的⽬的,同时减少了环境污染。
经测试,⾊牢度、⾊光等指标都符合要求,是值得推崇的新⼯艺。
下⾯讲述的是⾼耐碱性分散染料染⾊⼯艺。
⼀、涤锦珊瑚绒的⼀般染⾊⼯艺涤锦珊瑚线⾯料(⼀般是涤锦质量⽐80:20)的染整加⼯,⼀般采⽤先碱性下开纤、碱减量,然后⽔洗中和,再在酸性下染涤纶的的的⼯艺。
染整⼯艺流程如下:⽑坯布→退卷→缝头→预定形→碱减量(开纤)→⽔洗→酸洗中和→⾼温⾼压染⾊→还原清洗→⽔洗→中和→上柔→脱⽔→烘⼲→拉⽑→杭⽑→剪⽑→(摇粒)→拉幅定形→后整理。
1.预定形涤锦珊瑚线的的加⼯,预定形是关鍵的⼀道⼯序,不经过预定形的⽑坯布在经过碱减量(开纤)、染⾊后,珊瑚丝弯曲凌乱,不规整,达不到珊瑚绒的风格。
经过预定形后,珊瑚丝排列规整、顺直且蓬松,底丝结构紧密⽽稳定,在后续染整加⼯过程中不易巻边。
珊瑚⽑坯布的预定形,⼀般温度为165~190C,时间根据车速⽽定,张⼒达到织物平整即可。
2.碱减量(开纤)在印染⼯⼚中,采⽤液碱(⼀般30%的液碱⽤量5~8g/L,也可以⽤⽚碱换算⽤量)进⾏碱减量(开纤),将涤纶纤维中的⽔溶性聚酯溶解掉,原本粘合在⼀起的涤/锦两种纤维丝条分散松,成为涤/锦超细纤维单丝束。
再经过⽔洗、酸中和,使布⾯不含碱液,呈中性或弱酸性,有利于后⾯⼯序在⾼温⾼压条件下酸性染⾊。
在上述染整加⼯过程中,纤维减量率⼤约为5.0%~6.0%,减量率不⾜会影响⼿感,减量率太⼤会破坏织物纤维结构,影响强⼒等。
必须经过实验,找出合理的⽤碱量,制定合理的的⼯艺条件保证减量率稳定正常的范围内,不能超过7%~8%染整加⼯过程消耗⼤量的⽔、冰醋酸,电⼒、蒸汽⽤量都⽐较⼤,同时排放了⼤量的碱性污⽔,⽆形中增加了⽣产成本。
纺织行业的节能减排现状及途径与措施

纺织行业的节能减排现状及途径与措施纺织行业是我国重要的制造业之一,但由于其高能耗和高污染的特征,使得纺织行业成为环境保护的重点目标之一、因此,节能减排成为纺织行业发展的重要课题。
本文将通过分析纺织行业的节能减排现状,介绍一些节能减排的途径与措施。
首先,纺织行业的节能减排现状主要体现在以下几个方面:1.能源消耗高:纺织行业是典型的能源密集型行业,其能源消耗主要集中在电力、燃料和水的使用上。
数据显示,纺织行业用电量的占比约为全国工业用电的1/3,燃料消耗量的占比约为全国工业的1/52.碳排放量大:纺织行业的碳排放量主要来自于能源消耗过程中产生的二氧化碳排放,占工业碳排放总量的相当大比例。
据统计,中国纺织行业碳排放量约为全球纺织行业碳排放的1/43.水资源消耗大:纺织行业是水消耗量很大的行业,主要集中在染整过程中。
染整过程需要消耗大量的水资源,同时也会产生大量的废水,对水环境造成污染。
接下来,我们将介绍一些纺织行业节能减排的途径与措施:1.提高能源利用效率:通过技术改造和设备更新,提高纺织企业的能源利用效率。
可以采用高效的电机、节能的照明设备和传动装置,减少能源的消耗。
2.推广清洁能源使用:鼓励纺织企业采用清洁能源,如风能、太阳能等,替代传统的煤炭和石油等化石能源。
同时,加大清洁能源的研发和应用,推动纺织行业从传统能源向清洁能源转型。
3.优化生产工艺:通过改进纺织生产工艺,实现资源的高效利用和能耗的降低。
例如,采用先进的染整工艺,减少水的消耗和废水的排放;控制生产温度和湿度,减少能源的消耗。
4.加强废弃物综合利用:将纺织生产过程中产生的废弃物进行资源化利用,如废弃棉纱、废弃纺织品等可以进行再生利用,减少废物的排放。
5.加强管理和监管:加强对纺织企业的管理和监管力度,推动纺织企业建立和落实环境保护责任制。
加大对不符合环保要求的纺织企业的处罚和惩处力度,提高环境保护的意识和行动力。
总之,纺织行业的节能减排是一项系统工程,需要纺织企业、政府以及相关部门共同努力。
涤纶织物的印染工艺

涤纶织物的印染工艺涤纶织物的印染工艺一、概述涤纶织物是一种由聚酯纤维制成的合成纤维织物,具有耐磨性、耐用性和易护理的特点。
印染是涤纶织物加工的重要环节,通过对织物进行印花和染色,可以为其增添丰富的色彩和图案,提升其价值和美观度。
涤纶织物的印染工艺具有丰富的技术手段和方法,本文将从深度和广度两个方面,对涤纶织物的印染工艺进行全面评估,并分享对相关主题的个人观点和理解。
二、涤纶织物印染工艺的深度探讨1.印花工艺印花是一种将染料或颜料通过一定的工艺方法印在织物上的技术,涤纶织物的印花工艺主要包括传统印花、数字印花和激光印花等。
传统印花是使用模板或者刻板对织物进行印花,具有工艺复杂、生产效率低的特点,适用于量小且复杂图案的织物印花。
数字印花则是借助计算机控制喷墨技术,可以将任意图案直接印在织物上,具有高效率、低成本和无限色彩选择的优势。
激光印花是通过激光技术将染料直接印在织物上,不需要任何模板或刻板,具有快速、高精度和环保的特点。
2.染色工艺染色是将染料与纤维进行反应,使纤维吸收染料颜色的工艺。
涤纶织物的染色工艺主要包括直接染色、间接染色和水染色等。
直接染色是将染料直接与织物接触,通过热力和压力将染料上浆到织物上,具有色牢度好、色彩鲜艳的特点。
间接染色是首先将染料与载体结合,然后经过一系列的工艺将染料转移到织物上,适用于特殊效果和复杂色彩的要求。
水染色则是将织物浸泡在染料溶液中,通过渗透和扩散将染料染入纤维内部,具有染色均匀、色彩鲜艳的特点。
三、涤纶织物印染工艺的广度分析1.印花效果涤纶织物的印花效果受多种因素的影响,包括织物纹理、印花图案和染料选择等。
织物纹理的多样性决定了印花效果的多样性,可以通过调整印花压力和温度来控制纹理在织物上的表达。
印花图案的复杂程度和图案的细节决定了印花效果的精细度,可以通过数字印花技术实现更加精确的图案表达。
染料的颜色和稳定性对印花效果也有很大影响,可以通过选择具有良好色牢度的染料来增加印花效果的持久性。
印染企业节能减排措施方式解析

印染企业节能减排措施方式解析印染企业节能减排措施方式解析通过制定节能降耗奖罚制度,加强员工节能降耗意识的培养,全员参与,千方百计减少汽耗、电耗、水耗以及染化料消耗。
下面是店铺为大家分享印染企业节能减排措施方式解析,欢迎大家阅读浏览。
一、加强生产管理,减少资源浪费通过制定节能降耗奖罚制度,加强员工节能降耗意识的培养,全员参与,千方百计减少汽耗、电耗、水耗以及染化料消耗。
不少企业在各生产车间分别安装电表、水表,实行染化料消耗日报制度,各部门对单位用电量、单位用水量、染化料单位消耗进行评比奖励,调动全体员工节能降耗的积极性。
应用计算机管理技术,在生产线关键的工艺点上加装在线自动测控系统;配备助剂、色浆、染化料自动称量、化料及配送系统;配备蒸汽自动控制系统、布面含潮自动测控系统等,按工艺所需实现精准的控制,并减少对人工的依赖,对节能、节水、节约染料助剂等均能发挥出很好的作用。
二、采用印染新技术、新工艺达到节能减排在前处理方面,采用新型设备、使用高效助剂缩短工艺流程,在不降低处理品质的情况下,降低了用水量、节约蒸汽和电,达到了节能减排的效果。
从八十年代中期开始,我国印染行业已经从工艺和设备两方面进行短流程前处理工艺的研究。
各种高效水洗机、高给液浸渍机、组合式蒸箱等前处理设备为缩短流程提供了设备基础,各种新型高效前处理助剂如:高效精炼剂、非硅双氧水稳定剂及各种前处理酶制剂使短流程技术趋于成熟。
目前前处理技术和原来传统的碱碱氧工艺相比已发生了革命性的变化,生物酶复配物加双氧水的一步法前处理工艺正在被广泛应用于棉及其混纺织物的前处理工艺中。
冷轧堆前处理工艺和冷轧堆染色工艺技术近年来发展很快,冷轧堆前处理工艺已在实际生产中得到广泛应用。
织物经过浸轧前处理工作液后堆置一定时间,再经过短蒸和高效水洗达到去除杂质、提高白度、改善织物毛效等前处理效果。
与常规三步法前处理工艺相比,大大节约了蒸汽消耗和用水量,同时前处理废水COD也明显下降。
印染行业节能减排先进技术分析

当前,推动绿色增长是全球制造业的共同选择,资源能源利用效率成为衡量一个国家制造业竞争力的重要因素。
加快节能减排先进适用技术的推广和应用,是推进印染行业绿色发展、提升印染行业国际竞争力的重要举措和必然途径。
中国印染行业协会自2007年起,在全行业内开展节能减排技术推广工作,共发布16批468项先进、适用的节能减排先进技术,有力地促进了行业节能减排工作。
本报告就发布的16批印染行业节能减排先进技术进行分类汇总,通过汇总,从各类技术占比来看,设备类技术占比最大,每年申报的节能少水染色设备最多,其次是环保类技术,主要包括废水、废气处理技术与资源综合利用技术,详见表1~2。
工艺类和助剂染料类技术中,棉织物及其混纺、涤纶织物节能减排技术,棉织物及其混纺织物前处理助剂、活性染料和分散染料相关技术申报较多。
印染行业节能减排先进技术分析摘要:汇总印染行业节能减排先进技术推荐目录,分析技术申报情况,并分析热点节能减排先进技术现状,提出下一步发展趋势。
关键词:印染行业;节能减排;绿色发展中图分类号:TS193.5;TS194.4;TQ615文献标志码:A 文章编号:1005-9350(2023)06-0007-06Abstract:The recommended catalogue of advanced technologies for energy savings and emission reduction in print⁃ing and dyeing sector is summarized,the technology application situation is analyzed,and the future development trend based on the current situation analysis is proposed.Key words:printing and dyeing industry;energy conservation and emission reduction;green developmentAnalysis of advanced technologies for energy conservation andemission reduction in printing and dyeing industry收稿日期:2023-04-23作者简介:刘添涛(1987—),女,山西人,硕士,主要研究印染行业节能减排技术,E-mail :**********************。
纺织印染企业节能减排对策分析

纺织印染企业节能减排对策分析随着世界经济的发展和人们生活水平的提高,纺织印染行业作为重要的制造业领域,对环境造成了严重的影响。
纺织印染企业在生产过程中会产生大量的废水、废气和废渣,对水源、大气和土壤造成污染。
为了保护环境,推动可持续发展,纺织印染企业需要采取节能减排措施。
本文将从技术、管理和政策三个方面对纺织印染企业节能减排对策进行分析。
一、技术方面。
1.引入先进的生产工艺和设备。
纺织印染企业可以引进先进的低中温染色设备和高效节能的印花设备,降低能源消耗和排放。
采用直接染色技术和印染一体化工艺,减少染色过程中的中间环节,减少废水和废气的产生,提高资源利用率。
2.推广水性染料和染料回收技术。
水性染料相对于传统的溶剂型染料来说更环保,它们在染色过程中所产生的废水中的染料可以更容易地去除和回收利用。
通过回收废水中的染料,可以降低环境污染和经营成本,并节约能源和原材料。
3.采用高效处理废水和废气的技术。
纺织印染企业可以采用生物处理、膜分离、活性炭吸附等先进的废水处理技术,将废水净化后再进行排放。
同时,可以利用废水中的能量和化学物质,提高资源的回收利用率。
对废气的治理可以采用烟气脱硫、脱硝和粉尘捕集等技术,减少有害气体的排放。
二、管理方面。
1.加强能源管理和节能意识。
纺织印染企业可以建立健全的能源管理体系,对每个生产环节的能源使用情况进行监控和记录,及时发现和解决能源浪费的问题。
同时,需要提高员工的节能意识,加强培训和教育,鼓励员工提出节能减排的建议,并给予奖励。
2.完善废物管理制度。
纺织印染企业应制定详细的废物分类、储存和处置方案,将废物进行有效分离、收集和处理。
可以与专业的废物处理企业合作,进行废物的回收和资源化利用,减少对环境的影响。
3.推行生态设计和绿色采购。
纺织印染企业在产品设计和原材料采购环节中应考虑生态和环境因素,并选择符合环保要求的原材料和供应商。
通过推行绿色采购,可以减少对环境的影响,提高企业形象。
纺织企业如何节能降耗

本文摘自再生资源回收-变宝网()纺织企业如何节能降耗纺织行业是一个生产工序多、工艺要求高、用工多、利润薄的传统劳动密集型行业。
在激烈的市场竞争中提高产品质量的同时,更要注重节能降耗,我们公司采取的一些措施介绍如下。
一、节约用电,避峰用谷头吸棉风机、细纱节能锭子使用、空调系统、各吹吸风清洁间歇式工作等改造。
络筒空锭空车。
优化各工艺风量,使用变频调节,杜绝“大马拉小车”;优化各机速度,实现高产节能。
是政策节能,利用好峰、谷、平电价差。
峰、谷差达0.774元/kW·h,是一项可观的节约收益,要“开足谷时、避开峰时、合理运用平时”,提高变压器功率因素节能等。
二、原料使用要注重因质而用要认真分析用户订单质量要求,合理配棉,做到质量达标、不过剩。
同时要尽量提高各工序制成率。
率确保达98%以上,控制梳棉回条、回卷率;控制粗纱头率,保证粗纱不坏纱,细纱换粗纱时控制粗纱剩余圈数;控制回丝率,保证细纱不碰钢领、磨钢领,减少坏纱,确保细纱成形良好。
络筒时不留尾纱脚纱,合理确定清纱参数,有效控制络筒回丝。
多落杂、少落白;梳棉要多落杂、少损伤纤维,多排棉结,控制短绒增长幅度,保证棉网清晰、成条良好。
精梳确保少落棉、多排短绒和棉结。
三、注重管理创新,节约用工动。
如将落下的粗纱直接挂到备用吊锭上或运转吊锭上,减少中间环节的劳动。
设备包干,包机到人,改善用工环境。
实施精细化定额定编,满负荷工作,增强员工责任心。
可减少2/3落纱工,细纱与络筒之间的用工可全部省去。
一般细纱机采用自动集体落纱或智能落纱小车,以节约用工。
“顶管接法”,降低技术难度,利用络筒机上电子清纱装置清除接头疵点,缩短接头时间,减少员工培训时间,增加工人看台,减少用工。
达到高产低耗,减少用工。
本文摘自变宝网-废金属_废塑料_废纸_废品回收_再生资源B2B交易平台网站;变宝网官网:/?qxb买卖废品废料,再生料就上变宝网,什么废料都有!。
涤纶印染面料单位产品能源消耗限额

涤纶印染面料单位产品能源消耗限额导言涤纶印染面料是一种常用的纺织材料,广泛应用于服装、家纺等领域。
然而,印染过程中的能源消耗一直是制约涤纶印染面料行业可持续发展的瓶颈之一。
为了提高能源利用效率、降低生产过程中的环境影响,中国政府制定了涤纶印染面料单位产品能源消耗限额。
本文将深入探讨该限额政策的背景、目标、实施情况及未来发展方向。
背景涤纶印染面料在中国的生产量日益增加,但同时也带来了巨大的能源消耗与环境问题。
随着节能减排的重要性日益凸显,中国政府开始采取措施限制涤纶印染面料的能源消耗。
目标制定涤纶印染面料单位产品能源消耗限额的目标是降低行业能耗水平,实现资源的高效利用。
通过限额政策的实施,可以推动企业减少能源的消耗,提高生产效率,同时减少环境污染。
实施情况制定标准中国政府通过相关部门联合制定了涤纶印染面料单位产品能源消耗限额的标准。
该标准主要包括生产过程中各个环节的能源消耗限制,以及对产品质量的要求。
标准制定过程中充分考虑了行业现状、技术条件和市场需求,确保了标准的科学性和可操作性。
推动实施为了推动涤纶印染面料单位产品能源消耗限额的实施,中国政府采取了一系列措施。
首先,加强宣传,增强企业对限额政策的认识和理解。
其次,鼓励技术创新,提供技术支持和资金支持,推动企业采用更加节能的生产工艺和设备。
再次,建立监测体系,定期对企业进行能源消耗情况的检查和评估,确保限额政策的执行情况。
效果评估限额政策的实施对涤纶印染面料行业的能源消耗情况产生了积极影响。
根据相关数据显示,限额政策的实施使涤纶印染面料的能源消耗得到了明显的降低。
同时,企业也借助限额政策的引导,采取了多种节能措施,如优化生产工艺、改进设备、提高能源利用率等,大大降低了能源消耗。
未来发展方向完善标准随着技术的发展和行业的变化,涤纶印染面料单位产品能源消耗限额的标准需要与时俱进。
相关部门应密切关注行业的发展动态,及时修订和完善限额标准,确保其科学性和有效性。
涤纶机织物碱减量加工

涤纶机织物减减量加工一、前言涤纶纤维以其良好的强度、适中的刚性、较好的可染性,被越来越多地使用。
产量的迅速提高,又促进了涤纶本身的迅速发展。
如果粗略的对涤纶机织物进行分类,大致可分为常规织物、强捻织物、弹力织物和混纺织物。
其中涤纶强捻织物的仿真丝绸整理,就是通过涤纶织物的碱碱量加工实现的。
而涤纶新合纤仿麂皮绒产品的加工,也离不开碱减量。
虽然近几年涤纶强捻减量织物的比例逐渐减少,但在染整加工过程中减量工序出现的频率并没有降低。
“开纤”和轻减量的大量使用,使得研究碱减量加工工艺,仍具有重要的现实意义。
涤纶^碱量处理目的和原理三、涤纶分子由于主链上含有苯环,从而使大分子链旋转困难,分子柔顺性差。
同时苯核与羰基平面几乎平行于纤维轴,使之具有较高的几何规整性,因而分子间作用力强,分子排列紧密,纺丝后取向度和结晶性高,纤维弹性模量高,手感硬,刚性大,悬垂性差。
在一定温度下,涤纶纤维在烧碱溶液中于纤维表面产生的水解现象,也叫做涤纶的“剥皮”。
涤纶纤维被碱溶液剥皮以后,纱线就会变细,物纱线之间移动的空间就会变大,涤纶丝的刚性就会降低,织物的手感会得到明显改善。
在热碱溶液作用下克重减轻、手感变软的过程就是涤纶机织物的碱减量。
众所周知,在织物设计过程中一般采用增加经纬密来提高织物单位面积的重量,以此提高涤纶织物的悬垂性。
同时也可以通过增加经纱和纬纱的捻度来增加织物的硬挺度和刚性。
但是,为了体现织物成品的飘逸性并产生“糯”性手感,又不得不通过碱减量的方式使纱线“剥皮”,以此来降低纱线强度和刚性,增加纱线之间相互滑动的空间。
经过碱减量以后存留下来的强度和刚性可以体现涤纶织物“柔中带刚”的身骨;增加了滑动空间的纱线由于强度和刚性的下降,就会使得涤纶织物整体上呈现出既有一定的悬垂性,又有较好的飘逸性,还有不错的回弹性。
这样的手感就是涤纶织物碱减量所要追求的手感、涤纶碱减量加工设备及工艺1.间歇式碱减量加工L精练槽。
精练槽为长方形练桶,生产时一般以五只练桶为组。
节能减排型毛用染料的发展和应用
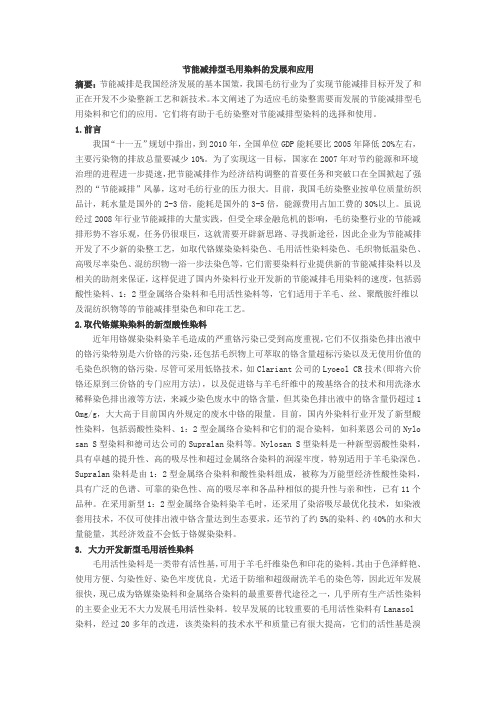
节能减排型毛用染料的发展和应用摘要:节能减排是我国经济发展的基本国策,我国毛纺行业为了实现节能减排目标开发了和正在开发不少染整新工艺和新技术。
本文阐述了为适应毛纺染整需要而发展的节能减排型毛用染料和它们的应用。
它们将有助于毛纺染整对节能减排型染料的选择和使用。
1.前言我国“十一五”规划中指出,到2010年,全国单位GDP能耗要比2005年降低20%左右,主要污染物的排放总量要减少10%。
为了实现这一目标,国家在2007年对节约能源和环境治理的进程进一步提速,把节能减排作为经济结构调整的首要任务和突破口在全国掀起了强烈的“节能减排”风暴,这对毛纺行业的压力很大。
目前,我国毛纺染整业按单位质量纺织品计,耗水量是国外的2-3倍,能耗是国外的3-5倍,能源费用占加工费的30%以上。
虽说经过2008年行业节能减排的大量实践,但受全球金融危机的影响,毛纺染整行业的节能减排形势不容乐观,任务仍很艰巨,这就需要开辟新思路、寻找新途径,因此企业为节能减排开发了不少新的染整工艺,如取代铬媒染染料染色、毛用活性染料染色、毛织物低温染色、高吸尽率染色、混纺织物一浴一步法染色等,它们需要染料行业提供新的节能减排染料以及相关的助剂来保证,这样促进了国内外染料行业开发新的节能减排毛用染料的速度,包括弱酸性染料、1:2型金属络合染料和毛用活性染料等,它们适用于羊毛、丝、聚酰胺纤维以及混纺织物等的节能减排型染色和印花工艺。
2.取代铬媒染染料的新型酸性染料近年用铬媒染染料染羊毛造成的严重铬污染已受到高度重视,它们不仅指染色排出液中的铬污染特别是六价铬的污染,还包括毛织物上可萃取的铬含量超标污染以及无使用价值的毛染色织物的铬污染。
尽管可采用低铬技术,如Clariant公司的Lyoeol CR技术(即将六价铬还原到三价铬的专门应用方法),以及促进铬与羊毛纤维中的羧基络合的技术和用洗涤水稀释染色排出液等方法,来减少染色废水中的铬含量,但其染色排出液中的铬含量仍超过1 0mg/g,大大高于目前国内外规定的废水中铬的限量。
- 1、下载文档前请自行甄别文档内容的完整性,平台不提供额外的编辑、内容补充、找答案等附加服务。
- 2、"仅部分预览"的文档,不可在线预览部分如存在完整性等问题,可反馈申请退款(可完整预览的文档不适用该条件!)。
- 3、如文档侵犯您的权益,请联系客服反馈,我们会尽快为您处理(人工客服工作时间:9:00-18:30)。
涤纶绒类织物
●节能减排印染工艺 ●●病疵分析
高介平
1、台板胶选择
丙烯酸酯不干胶 或不干型热熔胶
一次施胶
加热
PVA胶
连续施胶
连续 加热
冷却
热台板 印花
冷台板 印花
不干型胶一次施胶重复使用、不需要持续加热、污水容易处理 PVA胶连续施胶、持续加热、污水处理负担重
底面 79.30
78.21
按上述配比配置100g轧染液, 取五块10g纯涤法兰绒浸轧, 轧余率100%, 130℃×30min模拟大生产情况, 验证了红的亲和力最强,
而黄的亲和力最弱,测色结果如表
经研究探索的新轧染工艺处方
GFL 红
0.0018%
RL 黄
0.0103%
2R 蓝
0.0024%
化学增稠剂
0.0175 0.032 0.0112 0.003
咖啡色(浸染%owf)
S-5BL红 S-4RL黄(橙) HGL蓝
0.152 0.44 0.085
无轧可匀
偏
黄
深 色 色 浅
偏 红
总之:染料可以随意拼
超细纤维专用染料的秘密及解决方案
纤维细、染 座少、染深 性差的解决 方案:蒽醌 类与偶氮类 混拼
3、高效逆流水洗
出水 50℃-----60℃-65℃还原--70℃ 进水
进布
两格 平幅 浸泡
一格 堆置 浸泡
八格蛇状洗 (还原) (加软)
出布
常州某涤纶毛毯厂投资152万自行设计的高效逆流水洗线
!!! 水耗:10吨/吨 ??? 60℃-65℃还原清洗确保白底无沾污
V
46.57 69.57
GFL2 红 绒面 706..050018% 65.96
RL 黄 底面 709..085103% 74.66
2R3 蓝 绒面
化学增稠底剂面
4 绒面
水
底面
总量5 绒面
706..026024% 63.67
719..53%7
77.06
7余9.量37
75.30 64.11 76.57
7180.051克 71.69
解决轧染前后色差方案:
如:由龙盛分散染料
GFL 红
0.00018%
RL 黄
0.00103%
2R 蓝
0.00024%
涤纶法兰绒 10g
浴比
1:20
在高温高压浸染得到的
是浅米色,经测色得到
L
H
绒毛面 79.11 85.29
背面 78.94 79.35
L
H
1 绒面 73.28
采用轧染底工面 艺时7:8.90
H 84.73 80.90 84.74 80.88 84.75 80.89 84.76 80.91 84.73 80.88
从表中可以看出前后色光得到了有效控制。用轧染法代替浸染法后,每吨涤纶 毛毯染色费用节约1000元,更主要是省水、省电、省汽,且提高了生产效率。来自驼色 四拼色浸染%owf
92﹟红 SE-3R黄 2BLN蓝 S-6G嫩黄
涤纶绒类织物预烘除油、预定温度不能过高,除油不能 过多(影响风格手感),所以热台板还会引起对花不准
2、素色缸染改轧染
耗水
缸染 ~20吨/吨
轧染 ~1吨/吨
耗汽
10-12吨/吨
3-4吨/吨
耗时 耗力
长(间歇) 用人多
短(连续) 用人多
易乱毛,增加后道 后道梳、烫、剪方便 梳、烫、剪难度
轧染会造成的病疵:前后色差
1.5%
轧可匀
1%
水
余量
按上述配比配置100g轧染液, 取五块10g纯涤法兰绒浸轧, 轧余率100%, 130℃×30min模拟大生产情况, 测色结果如表
1 绒面 底面
2 绒面 底面
3 绒面 底面
4 绒面 底面
5 绒面 底面
L 80.27 78.50 80.27 78.54 80.30 78.53 80.26 78.52 80.30 78.54