分散染料涤纶染色工艺
分散染料涤纶染色

分散染料涤纶染色首先,我们来了解一下分散染料涤纶染色的工艺流程。
具体流程如下:1.布料预处理:对涤纶布料进行洗涤、漂白等预处理工序,以去除污渍和杂质,并提高布料的染色性能。
2.染色配方设计:根据染色要求,确定分散染料的种类、用量及其他助剂的添加量,设计染色配方。
3.染色溶液准备:按照染色配方,将染料、助剂等溶解在适量的水中,制成染色溶液。
4.染色操作:将布料放入染色机中,将染色溶液加入染色机中,控制染色时间、温度和染色速度等参数,进行染色操作。
5.染料固定:染色完成之后,将布料从染色机中取出,经过清洗、漂洗等工序,使染料与纤维结合牢固,提高染色的色牢度。
6.后处理工序:染色完成后,对染色布料进行后处理工序,如烘干、整理等,使布料具有所需的柔软、光泽和手感。
其次,我们来了解一下分散染料涤纶染色的操作步骤。
具体步骤如下:1.根据染色要求,选择合适的分散染料,并参考染色配方设计染色方案。
2.按照染色配方,将染料、助剂等称量准备好。
3.将分散染料、助剂等溶解在适量的水中,制成染色溶液。
4.将涤纶布料预处理,去除污渍和杂质,以提高染色效果。
5.将预处理后的涤纶布料放入染色机中,加入染色溶液。
6.控制染色机的温度、时间和染色速度等参数,进行染色操作。
7.染色完成后,将布料从染色机中取出,经过清洗、漂洗等工序,使染料与纤维结合牢固,提高染色的色牢度。
8.对染色布料进行后处理工序,如烘干、整理等,使布料具有所需的柔软、光泽和手感。
最后,我们来了解一下分散染料涤纶染色的注意事项。
具体注意事项如下:1.根据不同的染色要求,选择合适的分散染料种类和使用方法。
2.在染色过程中,要严格控制染色参数,如温度、时间、染色速度等,以保证染色效果和色牢度。
3.接触染料和染色助剂时,要注意个人防护,避免直接接触皮肤和吸入气体。
4.染色机和其他染色设备要保持干净,以防止杂质对染色效果的影响。
5.染色前对布料进行预处理,去除污渍和杂质,以提高染色效果。
(精选)分散染料的染色方法及其原理

二、热溶染色法原理和染色方法
• 热溶温度除和被染物的纤维性质有关外, 还应与染料的性能相适应,即不同的染料, 要求不同的热溶温度。
– 有些染料耐热性能较好,升华牢度较高,热溶 温度较高,一般得色越好。
三、热溶染色法原理和染色方法
• 热溶设备
– 热风导辊式:最常用,时间长,幅度不 易控制
– 热风针板式:可控制幅度,但热溶时间 难以保证
– 高温过热蒸汽式:相同时间,则温度可 低些;相同温度,则时间可短些
– 接触加热式:相同时间,则温度可低些; 相同温度,则时间可短些
四、载体法染色原理和染色方法
• 在染掖中加入某些酚、芳胺、联苯等称为载体或携 染剂的助剂,使分散染料在100℃左右就可以大大 加速对涤纶纤维的上染,提高上染百分率。用常压 设备进行染色。
纤维上染料
• 染料和纤维之间主要是范德华力、氢键 和电荷转移力
分散染料的上染过程
• 分散染料的悬浮液中,有少量分散染料溶 解成为单分子,因此在染料的悬浮液中存 在着大小不同的染料颗粒和染料单分子, 染料溶液呈饱和状态。
• 染色时,已溶解的染料分子到达纤维表面, 被纤维表面所吸附,并在高温下向纤维内 部扩散,随着染液料也不断释放出来,不断提供单分 子染料,再吸附、扩散,直至完成染色过 程。
二、热溶染色法
• 特点
– 热溶染色是连续生产,生产效率高,适宜于大 批量生产
– 能染浅、中色,染料利用率比高温高压法染色 低
– 对染料的升华牢度要求较高 – 织物所受张力较大
• 应用
– 主要用于涤纶机织物的染色 – 目前是分散染料染涤/棉混纺织物的主要方法
分散染料染涤纶纤维
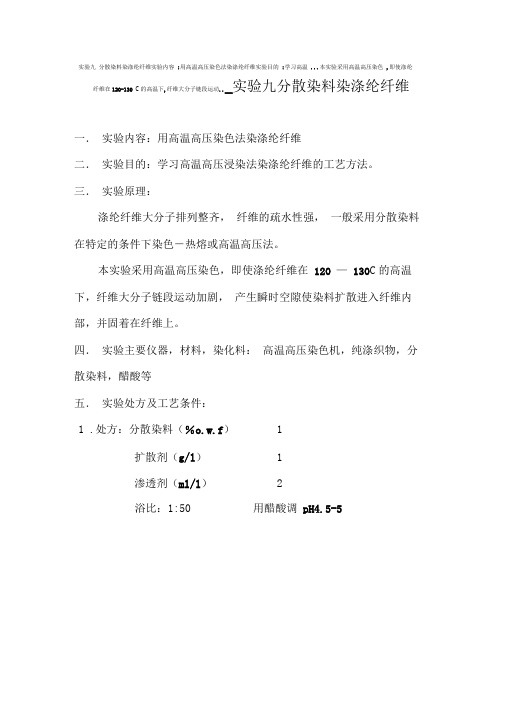
实验九分散染料染涤纶纤维实验内容:用高温高压染色法染涤纶纤维实验目的:学习高温...本实验采用高温高压染色,即使涤纶
实验九分散染料染涤纶纤维纤维在120-130 C的高温下,纤维大分子链段运动.._
一.实验内容:用高温高压染色法染涤纶纤维
二.实验目的:学习高温高压浸染法染涤纶纤维的工艺方法。
三.实验原理:
涤纶纤维大分子排列整齐,纤维的疏水性强,一般采用分散染料在特定的条件下染色-热熔或高温高压法。
本实验采用高温高压染色,即使涤纶纤维在120 —130C的高温下,纤维大分子链段运动加剧,产生瞬时空隙使染料扩散进入纤维内部,并固着在纤维上。
四.实验主要仪器,材料,染化料:高温高压染色机,纯涤织物,分散染料,醋酸等
五.实验处方及工艺条件:
1 .处方:分散染料(%o.w.f)1
扩散剂(g/l)1
渗透剂(ml/l)2
浴比:1:50 用醋酸调pH4.5-5
2 .染色曲线:
60 C入染
3.工艺流程:
织物润湿挤干-放入染杯-按升温曲线染色-取出-水洗-还原清洗-水洗-晾干
六.思考题:比较高温高压染色和热熔染色的染色效果,简单说明原因?。
涤染色的详细工艺流程

涤染色的详细工艺流程下载温馨提示:该文档是我店铺精心编制而成,希望大家下载以后,能够帮助大家解决实际的问题。
文档下载后可定制随意修改,请根据实际需要进行相应的调整和使用,谢谢!Download Tip: This document has been carefully written by the editor. I hope that after you download, they can help you solve practical problems. After downloading, the document can be customized and modified. Please adjust and use it according to actual needs. Thank you!涤纶染色详细工艺流程:①前处理:首先对涤纶织物进行去油、去污处理,提升织物的洁净度,必要时进行预缩,以去除织物内部应力,使用温度可达130℃,并可添加精炼剂去除杂质。
②染料准备:选择适合涤纶的分散染料,根据染色要求调整染料浓度和助剂配比,如提高染料的分散稳定性,确保染色均匀。
③染色:采用高温高压染色法,将织物浸入染液中,控制温度在130~135℃,保温时间约为40~50分钟,确保染料充分渗透纤维内部。
④水洗:染色后,通过多次水洗去除未固着的浮色,直至水清,保持水质中性,防止色变。
⑤后处理:包括柔软处理、定形处理,使用定形机在一定温度下处理,固定织物形态,防止缩水,并提升手感。
⑥烘干:将湿织物送入烘干设备,控制适宜温度,彻底干燥织物。
⑦检验:对染色后的织物进行质量检验,包括色牢度、颜色一致性、布面质量等,确保符合标准。
⑧成品包装:合格产品进行折叠、打包,准备入库或出厂。
分散染料染色—涤纶结构特点和分散染料分类

O NHR
O NHR
(2)
大多数为紫色,个别为蓝
及其衍生物。 色,耐光牢度较低
O NHR'
NH2 O OH
(3)
大多数为蓝色,颜色鲜艳,耐光
及其衍生物。 牢度中等,其它性能也较好
OH O NH2
(4)
O NH2 O C
多为翠蓝色,颜色鲜艳,耐升
N CH3 C O NH2 O
华牢度高,但染料合成复杂, 成本高
CN、-OCOCH3、-OC2H5 等。
NN
R' m
Rn
N N Ar
双偶氮类
结构分类
2.蒽醌型结构染料 蒽醌类染料在整个分散染料中的比例在25%左右,
日晒、皂洗牢度及耐还原性均较偶氮型好,但升华牢度差 。以结构而言,蒽醌类分散染料可大致分为四类:
(1)
O OH
大多数为红到紫色,少数为蓝
及其衍生物。 色,色泽较鲜艳,耐光牢度好
度℃ 色泽选择范围
高温型 S 大 好
较差 慢
200-220 130
浓色
中温型 SE 中 中 中 中
190-205 120-130
中浓色
低温型 E 小 低 好 快
180-195 120-135
淡中色
按应用性能分类
2、按上染速度分: 如德司达公司的A、B、C、D型,A型上染最快,D型 上染最慢。 3、按应用对象分: 如英国卜内门公司的A类:升华牢度低,主要用于醋酯 和锦纶的染色; B、C、D类:适合于涤纶染色,相当于E、SE、S型; P类:适合于印花
R2
R4
C2H4R6
R1
NN
N
C2H4R7
R3
R5
式中,R1 多为吸电子基团,如-NO2 等;R2、R3
涤纶织物的印染工艺

涤纶织物的印染工艺
一、前处理
前处理的主要目的是去除织物上的杂质,为后续印染工艺做好准备。
这个过程包括以下步骤:
1. 退浆:涤纶织物在织造过程中,通常会使用浆料来提高纱线的性能。
退浆就是通过化学或物理方法去除这些浆料。
2. 漂白:这个步骤主要是为了去除织物中的天然色素或杂质,使织物更白。
常用的漂白剂有次氯酸钠和过氧化氢。
3. 热定型:通过热处理使织物保持所需的形状和尺寸。
二、染色
染色是印染工艺的核心步骤,它决定了织物最终的颜色和外观。
涤纶织物通常使用分散染料进行染色。
以下是染色过程的基本步骤:
1. 配制染液:根据所需的颜色和浓度,将分散染料溶解在水中,形成染液。
2. 染色:将织物浸泡在染液中,通过控制温度和时间,使染料均匀地吸附在织
物上。
3. 固色:通过化学反应使染料与织物纤维固定,防止颜色在洗涤过程中脱落。
4. 水洗:去除残留在织物上的浮色,得到最终的颜色。
三、后处理
后处理的主要目的是改善织物的手感和外观,以及提高其耐用性。
以下是后处理的基本步骤:
1. 柔软处理:通过使用柔软剂,降低织物的粗糙感,提高其舒适度。
2. 拉幅定型:通过热处理使织物保持所需的宽度和形状。
3. 抗静电处理:通过添加抗静电剂,降低织物的静电现象,提高其舒适度。
4. 成品水洗:最后的水洗步骤是为了去除残留在织物上的化学物质,提高产品的品质。
涤纶织物的印染工艺的每一步都需要精确的控制,以确保最终产品的质量和颜色满足客户的要求。
涤纶分散染料的工艺设计1
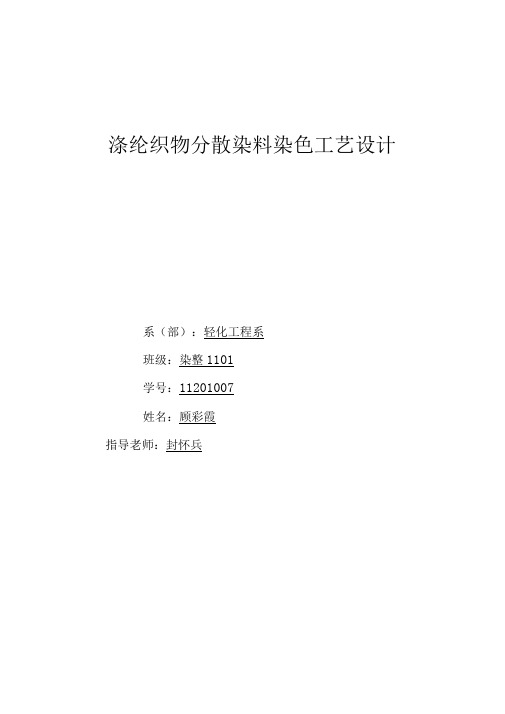
涤纶织物分散染料染色工艺设计系(部):轻化工程系班级:染整1101学号:11201007姓名:顾彩霞指导老师:封怀兵盐城工业职业技术学院涤纶织物分散染料染色工艺设计【摘要】:涤纶纤维通常具有显色性低、染色牢度差、提升性较高和上染速率快等特点,因此适合于纤维染色地分散染料,应具有颜色强度高、染色牢度高、移染性好、提升性好、匀染性好及相容性好地特点•经过实验,SE型分散染料符合要求•文中介绍了pH、时间、浴比对染色性能地影响.最终确定染色工艺配方为:分散红2%,分散剂1g/L,醋酸2g/L,pH值为5 ,染色温度为12 5〜130 C ,保温4 0mi n.关键字:分散染料涤纶染色工艺1.前言涤纶属疏水性化学纤维.即聚对苯二甲酸乙二酯.目前能对其进行工业化染色地染料.只有分散染料.分散染料对涤纶织物地上染过程.可看作是分散染料在涤纶纤维中地溶解过程.是纯粹地物理过程.染料分子与纤维主要依靠氢键、范德华力以及偶极引力而结合. 染色过程主要有3个阶段:涤纶纤维对分散染料地吸附、分散染料分子向纤维内部地扩散、分散染料地扩散与反扩散地迁移平衡2. 涤纶织物地染色特征超细涤纶地染色性能既与一般涤纶地染色性能有共同性,又有其特殊性.一般涤纶或是超细涤纶,结构都很紧密,都缺乏极性基团,而且染色困难.在用分散染料染色时,两者地染色机理都是:分散染料在染浴中分散。
染料溶解。
吸附到纤维表面上。
染料扩散进入纤维内部咼温咼压染色分散染料地高温高压染色方法是一种重要地方法,适合升华牢度低和分子量较小地低温型染料品种.用这类染料染色匀染性好,色泽浓艳, 手感良好,织物透芯程度高,适合于小批量、多品种生产,常用于涤棉混纺织物地染色.高温高压染色通常在130C左右温度下染色,该温度高于涤纶地玻璃态转变温度,纤维无定形区地分子链运动剧烈,纤维分子间自由体积增多增大,同时染料分子地动能增加.随着染料颗粒聚集,染料单分子被纤维吸附,并迅速扩散进入纤维内部.然后随着染色温度降低,纤维分子链段运动停止,自由体积缩小,染料与纤维分子间以氢键、范德华力以及机械作用而固着.染料要求:良好地分散稳定性、化学稳定性和较高地耐升华牢度,以保证均匀、鲜艳地染色效果.分散染料地高温高压染色可在高温高压卷染机和喷射、溢流染色机上进行,适宜于染深浓色泽,染色pH值一般控制在5~6,常用醋酸和磷酸二氢铵来调节pH值.为使染浴保持稳定,染色时尚需加入分散剂和高温匀染剂. 一、工程设计思路和原则实验方案表1工程实施方案二、实验准备仪器与材料地选定:仪器设备:高温高压染色小样机、烧杯(200mL )、量筒(100mL)、移液管(10mL、5mL)染化药品:分散剂NNO、分散红、醋酸实验材料:涤纶织物(重2g)三、操作步骤坯布一前处理一高温高压染色一降温80 C溢流水洗一水洗一还原清洗一溢流水洗一水洗一氧化水洗一水洗一出布实验操作步骤:①根据实验方案计算染料及助剂用量,并配置染液.②移取染液置于高温高压染色小样机地不锈钢染杯中,布样用水润湿并挤干,挂在染杯地芯架上,放入染杯,加盖拧紧.③按如下工艺曲线染色:④把染杯装入小样机内,启动小样机,按工艺曲线运行.⑤程序完成关闭电源,用夹子取出染杯,放入自来水中冷却后取出⑥水洗,烘干.染色过程:1)40C温水化料,过滤.2)慢慢升温至120~130 C,再升至染色转变温度以上时,上染速率迅速提高,应严格控制升温速率,3)保证染料均匀上染.4)继续保温染色45~60min.5)然后降温,进行还原清洗,水洗等后处理,彻底去除浮色,以提高染色产品地染色牢度和鲜艳度染色温度选择在120〜130 C为宜,温度不能超过145 C,否则纤维会造成损伤,特别是毛涤混纺织物染色温度控制分三个阶段:(1)染色升温阶段:在70〜110 C温度区间,染料上染速率很快,要严格控制1〜2 C /min,保证染料均匀吸附( 2)染色保温阶段染料向纤维内部扩散,并增进染料移染,染匀染透( 3)降温阶段在玻璃化温度以上,降温速率应适当慢些,其后快速降温,避免引起织物产生折皱和手感粗糙,pH值控制在5〜6之间,色光纯正、色泽鲜艳上染百分率高;高温碱性,染料水解,碱性太强,织物损伤大,手感差,但酸性染色,齐聚物容易沉积在织物表面,浴比小,节能节水,但易使织物产生折皱、擦伤、染色不匀,耗能耗水.四大样实例1. 工艺流程配锅T接头T前处理T 染色f水洗- f 脱水f理布f缝头f烘干、定型T检验T 打卷、包装f入库.2. 染色处方消泡剂0.25% 染色处方:匀染剂S S -972.5% 防皱剂1% N N O 0.5% H A C 适量(调节 P H 值至5)分散红S E - G F L 0.04%方还原清洗处氢氧化钠 2 3 g / L保险粉4g/L工艺升温曲线见图1.3. 工艺措施①控制匀染性②防止折痕疵点③染色后还原清洗④脱水设备:脱水设备采用真空脱水机,可防止织物擦伤.五、总结通过这次实验,我们学会了如何进行分散染料上染涤纶织物,同时掌握了涤纶纤维地染色工艺.在整个工艺中了解了分散染料地性质、特点、染色原理、染色性能以及染色方法.六、参考文献马正升,宋心远。
(工艺技术)分散染料涤纶染色工艺

分散染料涤纶染色工艺纤维中不同区域的玻璃化温度不同无定形区约为67℃结晶区约为81 ℃结晶又取向区域约为125 ℃经不同温度预热定形处理的涤纶织物,玻璃化温度不同定形温度Tg 定形温度Tg未定形75 90 105120 123 150 125180 122 210 115230 105 245 90实际染色时,染色温度应高于染色转变温度,此时纤维无定形区的大分子链段发生剧烈运动,产生瞬间孔穴。
一般染色转变温度比玻璃化温度高十几度,染料分子量越大,二者相差越大涤纶微结构影响染色性能1.高温高压染色染色织物色泽鲜艳、手感好织物品种适应性好,适用的染料范围广,染料利用率高对设备要求高,需密闭间歇式,染色时间长,生产效率较低染液中含有分散染料、分散剂、高温匀染剂、pH调节剂等高温高压染色,染料易出现晶型转变温度控制不匀,出现晶体增长现象高温染色,表面易析出低聚物部分染料发生水解或还原染料要求:良好的分散稳定性、化学稳定性和较高的耐升华牢度,以保证均匀、鲜艳的染色效果染色过程(1)40 ℃温水化料,过滤(2)慢慢升温至120~130 ℃,在升至染色转变温度以上时,上染速率迅速提高,应严格控制升温速率,保证染料均匀上染(3)继续保温染色45~60min(4)然后降温,进行还原清洗,水洗等后处理,彻底去除浮色,以提高染色产品的染色牢度和鲜艳度染色温度选择在120~130℃为宜,温度不能超过145℃,否则纤维会造成损伤,特别是毛涤混纺织物染色温度控制分三个阶段:(1)染色升温阶段:在70~110℃温度区间,染料上染速率很快,要严格控制1~2℃/min,保证染料均匀吸附(2)染色保温阶段染料向纤维内部扩散,并增进染料移染,染匀染透(3)降温阶段在玻璃化温度以上,降温速率应适当慢些,其后快速降温,避免引起织物产生折皱和手感粗糙pH值控制在5~6之间,色光纯正、色泽鲜艳,上染百分率高;高温碱性,染料水解,碱性太强,织物损伤大,手感差但酸性染色,齐聚物容易沉积在织物表面浴比:小,节能节水,但易使织物产生折皱、擦伤、染色不匀大,耗能耗水匹染:10:1~30:1分散剂影响匀染剂(载体、非离子型活性剂)(1)缓染剂通过助剂对染料或纤维亲和力,延缓染料上染,使染料能均匀地吸附在纤维的各个部分,从而染色均匀,但会导致上染百分率下降(2)移染匀染剂一般为载体、非离子型聚氧乙烯类表面活性剂载体有毒非离子表面活性剂在染色温度高于浊点,会产生沉淀,一般需与阴离子表面活性剂复配2.热熔染色在185~215℃干热条件下使染料在纤维上发生固着的连续轧染的染色方法连续化生产,生产效率高,用水量少,污水少,使用的染料要求耐升华牢度较高染色时织物所受张力较大,织物手感及色泽鲜艳度不及高温高压染色法一般多用于涤棉混纺织物中涤纶染色浸轧液含有分散染料、分散剂、渗透剂、防泳移剂等染料颗粒要特别匀细,渗透性及分散稳定性要好二浸二轧,室温,涤棉织物轧余率一般为50~60%焙烘固色(热熔)温度根据染料升华牢度来选择,一般为180~220℃,时间2~1min染色工艺条件(1)润湿剂或渗透剂润湿剂可以排除织物中的空气,有利于染料渗透到织物内部织物前处理充分,可不加(2)泳移现象及防止因染料对涤纶缺乏亲和力,容易发生烘干现象合理烘干方式提高浸轧效果,减少带液率,涤棉带液率降低到20%~30%后,不会发生明显泳移加入适量防泳移剂热熔染色时间和时间选择织物烘干后,染料停留在纤维表面,没有与纤维发生固着,通过高温热焙烘,染料向纤维内部扩散,把纤维染透,完成固色——热熔固色温度高——染料升华较多拼色时,染料耐升华性应相近3.载体染色利用载体助剂对涤纶的增塑膨化性能,在常压100℃条件下染色设备简单,适合毛涤织物染色另外,载体对染料具有亲和性,对染料溶解能力高,提高染料浓度,提高吸附和扩散;过高,也不好但载体有毒性,存在环境污染,残留载体不易洗净,影响染色牢度分散染料染色原理及工艺分散染料是一类水溶性较低的非离子型染料。
染整工艺原理:第五节 分散染料的染色

(本部分内容不作为考试内容)
一、高温高压染色法(卷染)工艺
1、工艺流程及主要条件 冷水进缸→温水2道(60~65℃,2道) →60℃起染色2道→1道升温至100℃→ 1道升 温至110℃→ 1道升温至120℃→1道升温至 130℃→130℃保温染色6道→冷水洗2道→还 原清洗(38% NaOH 3ml/L、85%保险粉 2.5g/L、表面活性剂3g/L,70~80℃,2道) →水洗 (40~50℃,1道)→冷水洗→出缸
散纤维、毛条、纱——高温高压染纱机 针织物——溢流或喷射染色机
(一)、高温高压染色法
为什么选用高温高压染色法? ∵高温、高湿效应提高了涤纶的染色性能
高温利于染料上染
纤维分子链段运动加剧,分子间微隙增大 染料溶解度提高,染料分子运动动能增加
高湿利于染料上染
水的增塑作用,使纤维分子间微隙增大
分散染料的上染过程
分散染料的悬浮液中,有少量分散染料溶解成 为单分子,因此在染料的悬浮液中存在着大小 不同的染料颗粒和染料单分子,染料溶液呈饱 和状态。
染色时,已溶解的染料分子到达纤维表面,被 纤维表面所吸附,并在高温下向纤维内部扩散, 随着染液中染料单分子被吸附,染液中的染料 颗粒不断溶解,分散剂胶束中的染料也不断释 放出来,不断提供单分子染料,再吸附、扩散, 直至完成染色过程。
一、涤纶的结构特点
涤纶纤维分子链上无大的侧链和侧基,线形 状态良好,分子排列整齐,结晶度高,无定 形区结构比较紧密,纤维分子间的微隙小, 没有适当容纳染料分子的空隙,在纤维表面 还有结构紧密的表皮层。
一、涤纶的结构特点
涤纶属于热塑性纤维 Tg:结晶度↑,Tg↑
分散染料染色—分散染料的染色工艺
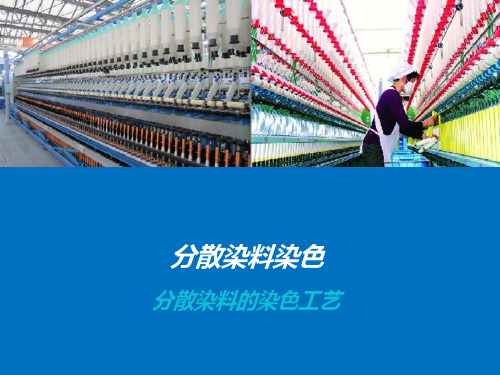
•染色温度太低,上染百分率低 •染色温度太高,对设备要求高 染色最适合温度为130℃,此时上染率高,色光鲜艳, 匀染性好,浮色少。
水洗后处理
2、处方:
分散染料
x(对织物重)
磷酸二氢铵
1 g/L
载体
3-4 g/L
3、注意:
1)采用载体预处理,使纤维膨化充分,有利于染料上染。
2)载体的用量应适当,不同载体使用方法不同。
3)染后载体必须去除干净,否则对色光和牢度都有影响。
2)pH值 pH值过高(>6),染料分解,色光发暗,涤纶受损; pH过低(<5),影响色光和上染百分率。 分散染料高温高压染色,pH值须稳定,并控制在弱酸性,
即pH值为5~6。常采用醋酸,也可用磷酸氢二铵作缓冲剂。 3)染色时间
•40-60min
4)助剂选用 ①分散剂
高温染色中加分散剂可防止染料凝聚沉淀,有助于染浴 的稳定。 注意:分散剂用量一般1~2g/L,深色少加,浅色多加。 ②匀染剂
4、注意问题
4)后处理:
去除浮色,保证色光纯正和染色牢度
处方:
烧碱(36°Be′) 2.5-5mL/L保险粉(来自5%) 1-2g/L净洗剂
1-2mL/L
70-80℃处理,10-20min
4、注意问题
5)焦油化问题 焦油化问题是分散染料高温高压染色中易产生又不易解
决的问题。焦油化物乃是染液中齐聚物、染料、分散剂和纤 维屑杂质聚集而成的黏稠物,沾附在织物上造成难以纠正的 染疵,沾附在设备上形成难以去除又易沾污织物的积垢。
分散染料涤纶染色工艺

分散染料涤纶染色工艺纤维中不同区域的玻璃化温度不同无定形区约为67℃结晶区约为81 ℃结晶又取向区域约为125 ℃经不同温度预热定形处理的涤纶织物,玻璃化温度不同定形温度Tg 定形温度Tg未定形75 90 105120 123 150 125180 122 210 115230 105 245 90实际染色时,染色温度应高于染色转变温度,此时纤维无定形区的大分子链段发生剧烈运动,产生瞬间孔穴。
一般染色转变温度比玻璃化温度高十几度,染料分子量越大,二者相差越大涤纶微结构影响染色性能1.高温高压染色染色织物色泽鲜艳、手感好织物品种适应性好,适用的染料范围广,染料利用率高对设备要求高,需密闭间歇式,染色时间长,生产效率较低染液中含有分散染料、分散剂、高温匀染剂、pH调节剂等高温高压染色,染料易出现晶型转变温度控制不匀,出现晶体增长现象高温染色,表面易析出低聚物部分染料发生水解或还原染料要求:良好的分散稳定性、化学稳定性和较高的耐升华牢度,以保证均匀、鲜艳的染色效果染色过程(1)40 ℃温水化料,过滤(2)慢慢升温至120~130 ℃,在升至染色转变温度以上时,上染速率迅速提高,应严格控制升温速率,保证染料均匀上染(3)继续保温染色45~60min(4)然后降温,进行还原清洗,水洗等后处理,彻底去除浮色,以提高染色产品的染色牢度和鲜艳度染色温度选择在120~130℃为宜,温度不能超过145℃,否则纤维会造成损伤,特别是毛涤混纺织物染色温度控制分三个阶段:(1)染色升温阶段:在70~110℃温度区间,染料上染速率很快,要严格控制1~2℃/min,保证染料均匀吸附(2)染色保温阶段染料向纤维内部扩散,并增进染料移染,染匀染透(3)降温阶段在玻璃化温度以上,降温速率应适当慢些,其后快速降温,避免引起织物产生折皱和手感粗糙pH值控制在5~6之间,色光纯正、色泽鲜艳,上染百分率高;高温碱性,染料水解,碱性太强,织物损伤大,手感差但酸性染色,齐聚物容易沉积在织物表面浴比:小,节能节水,但易使织物产生折皱、擦伤、染色不匀大,耗能耗水匹染:10:1~30:1分散剂影响匀染剂(载体、非离子型活性剂)(1)缓染剂通过助剂对染料或纤维亲和力,延缓染料上染,使染料能均匀地吸附在纤维的各个部分,从而染色均匀,但会导致上染百分率下降(2)移染匀染剂一般为载体、非离子型聚氧乙烯类表面活性剂载体有毒非离子表面活性剂在染色温度高于浊点,会产生沉淀,一般需与阴离子表面活性剂复配2.热熔染色在185~215℃干热条件下使染料在纤维上发生固着的连续轧染的染色方法连续化生产,生产效率高,用水量少,污水少,使用的染料要求耐升华牢度较高染色时织物所受张力较大,织物手感及色泽鲜艳度不及高温高压染色法一般多用于涤棉混纺织物中涤纶染色浸轧液含有分散染料、分散剂、渗透剂、防泳移剂等染料颗粒要特别匀细,渗透性及分散稳定性要好二浸二轧,室温,涤棉织物轧余率一般为50~60%焙烘固色(热熔)温度根据染料升华牢度来选择,一般为180~220℃,时间2~1min染色工艺条件(1)润湿剂或渗透剂润湿剂可以排除织物中的空气,有利于染料渗透到织物内部织物前处理充分,可不加(2)泳移现象及防止因染料对涤纶缺乏亲和力,容易发生烘干现象合理烘干方式提高浸轧效果,减少带液率,涤棉带液率降低到20%~30%后,不会发生明显泳移加入适量防泳移剂热熔染色时间和时间选择织物烘干后,染料停留在纤维表面,没有与纤维发生固着,通过高温热焙烘,染料向纤维内部扩散,把纤维染透,完成固色——热熔固色温度高——染料升华较多拼色时,染料耐升华性应相近3.载体染色利用载体助剂对涤纶的增塑膨化性能,在常压100℃条件下染色设备简单,适合毛涤织物染色另外,载体对染料具有亲和性,对染料溶解能力高,提高染料浓度,提高吸附和扩散;过高,也不好但载体有毒性,存在环境污染,残留载体不易洗净,影响染色牢度分散染料染色原理及工艺分散染料是一类水溶性较低的非离子型染料。
技术控高耐碱性分散染料染色工艺,涤纶超细纤维在高碱性下节能减排!
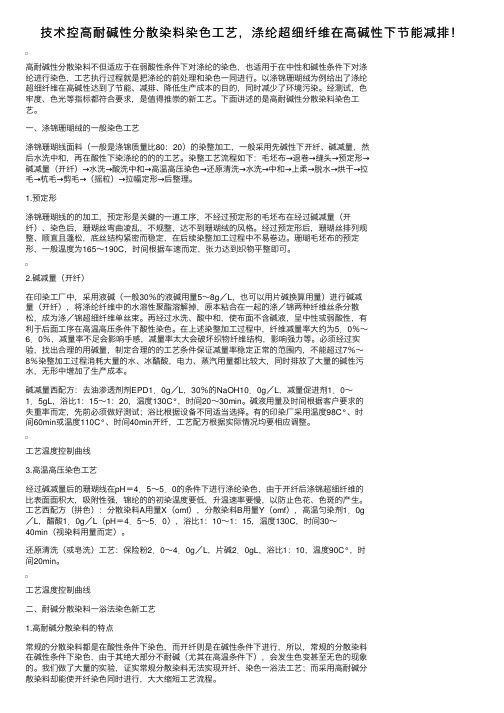
技术控⾼耐碱性分散染料染⾊⼯艺,涤纶超细纤维在⾼碱性下节能减排!⾼耐碱性分散染料不但适应于在弱酸性条件下对涤纶的染⾊,也适⽤于在中性和碱性条件下对涤纶进⾏染⾊,⼯艺执⾏过程就是把涤纶的前处理和染⾊⼀同进⾏。
以涤锦珊瑚绒为例给出了涤纶超细纤维在⾼碱性达到了节能、减排、降低⽣产成本的⽬的,同时减少了环境污染。
经测试,⾊牢度、⾊光等指标都符合要求,是值得推崇的新⼯艺。
下⾯讲述的是⾼耐碱性分散染料染⾊⼯艺。
⼀、涤锦珊瑚绒的⼀般染⾊⼯艺涤锦珊瑚线⾯料(⼀般是涤锦质量⽐80:20)的染整加⼯,⼀般采⽤先碱性下开纤、碱减量,然后⽔洗中和,再在酸性下染涤纶的的的⼯艺。
染整⼯艺流程如下:⽑坯布→退卷→缝头→预定形→碱减量(开纤)→⽔洗→酸洗中和→⾼温⾼压染⾊→还原清洗→⽔洗→中和→上柔→脱⽔→烘⼲→拉⽑→杭⽑→剪⽑→(摇粒)→拉幅定形→后整理。
1.预定形涤锦珊瑚线的的加⼯,预定形是关鍵的⼀道⼯序,不经过预定形的⽑坯布在经过碱减量(开纤)、染⾊后,珊瑚丝弯曲凌乱,不规整,达不到珊瑚绒的风格。
经过预定形后,珊瑚丝排列规整、顺直且蓬松,底丝结构紧密⽽稳定,在后续染整加⼯过程中不易巻边。
珊瑚⽑坯布的预定形,⼀般温度为165~190C,时间根据车速⽽定,张⼒达到织物平整即可。
2.碱减量(开纤)在印染⼯⼚中,采⽤液碱(⼀般30%的液碱⽤量5~8g/L,也可以⽤⽚碱换算⽤量)进⾏碱减量(开纤),将涤纶纤维中的⽔溶性聚酯溶解掉,原本粘合在⼀起的涤/锦两种纤维丝条分散松,成为涤/锦超细纤维单丝束。
再经过⽔洗、酸中和,使布⾯不含碱液,呈中性或弱酸性,有利于后⾯⼯序在⾼温⾼压条件下酸性染⾊。
在上述染整加⼯过程中,纤维减量率⼤约为5.0%~6.0%,减量率不⾜会影响⼿感,减量率太⼤会破坏织物纤维结构,影响强⼒等。
必须经过实验,找出合理的⽤碱量,制定合理的的⼯艺条件保证减量率稳定正常的范围内,不能超过7%~8%染整加⼯过程消耗⼤量的⽔、冰醋酸,电⼒、蒸汽⽤量都⽐较⼤,同时排放了⼤量的碱性污⽔,⽆形中增加了⽣产成本。
分散染料涤纶染色工艺

分散染料涤纶染色工艺纤维中不同区域的玻璃化温度不同无定形区约为67℃结晶区约为81 ℃结晶又取向区域约为125 ℃经不同温度预热定形处理的涤纶织物, 玻璃化温度不同定形温度 Tg 定形温度 Tg未定形 75 90 105120 123 150 125180 122 210 115230 105 245 90实际染色时, 染色温度应高于染色转变温度, 此时纤维无定形区的大分子链段发生剧烈运动, 产生瞬间孔穴。
一般染色转变温度比玻璃化温度高十几度, 染料分子量越大, 二者相差越大涤纶微结构影响染色性能1.高温高压染色染色织物色泽鲜艳、手感好织物品种适应性好, 适用的染料范围广, 染料利用率高对设备要求高, 需密闭间歇式, 染色时间长, 生产效率较低染液中含有分散染料、分散剂、高温匀染剂、 pH调节剂等高温高压染色, 染料易出现晶型转变温度控制不匀, 出现晶体增长现象高温染色, 表面易析出低聚物部分染料发生水解或还原染料要求: 良好的分散稳定性、化学稳定性和较高的耐升华牢度, 以保证均匀、鲜艳的染色效果染色过程( 1) 40 ℃温水化料, 过滤( 2) 慢慢升温至120~130 ℃, 在升至染色转变温度以上时, 上染速率迅速提高, 应严格控制升温速率, 保证染料均匀上染( 3) 继续保温染色45~60min( 4) 然后降温, 进行还原清洗, 水洗等后处理, 彻底去除浮色, 以提高染色产品的染色牢度和鲜艳度染色温度选择在120~130℃为宜, 温度不能超过145℃, 否则纤维会造成损伤, 特别是毛涤混纺织物染色温度控制分三个阶段:( 1) 染色升温阶段: 在70~110℃温度区间, 染料上染速率很快, 要严格控制1~2℃/min, 保证染料均匀吸附( 2) 染色保温阶段染料向纤维内部扩散, 并增进染料移染, 染匀染透( 3) 降温阶段在玻璃化温度以上, 降温速率应适当慢些, 其后快速降温, 避免引起织物产生折皱和手感粗糙pH值控制在5~6之间, 色光纯正、色泽鲜艳, 上染百分率高;高温碱性, 染料水解,碱性太强, 织物损伤大, 手感差但酸性染色, 齐聚物容易沉积在织物表面浴比:小, 节能节水, 但易使织物产生折皱、擦伤、染色不匀大, 耗能耗水匹染: 10: 1~30: 1分散剂影响匀染剂( 载体、非离子型活性剂)( 1) 缓染剂经过助剂对染料或纤维亲和力, 延缓染料上染, 使染料能均匀地吸附在纤维的各个部分, 从而染色均匀, 但会导致上染百分率下降( 2) 移染匀染剂一般为载体、非离子型聚氧乙烯类表面活性剂载体有毒非离子表面活性剂在染色温度高于浊点, 会产生沉淀, 一般需与阴离子表面活性剂复配2.热熔染色在185~215℃干热条件下使染料在纤维上发生固着的连续轧染的染色方法连续化生产, 生产效率高, 用水量少, 污水少, 使用的染料要求耐升华牢度较高染色时织物所受张力较大, 织物手感及色泽鲜艳度不及高温高压染色法一般多用于涤棉混纺织物中涤纶染色浸轧液含有分散染料、分散剂、渗透剂、防泳移剂等染料颗粒要特别匀细, 渗透性及分散稳定性要好二浸二轧, 室温, 涤棉织物轧余率一般为50~60%焙烘固色( 热熔) 温度根据染料升华牢度来选择, 一般为180~220℃, 时间2~1min染色工艺条件( 1) 润湿剂或渗透剂润湿剂能够排除织物中的空气, 有利于染料渗透到织物内部织物前处理充分, 可不加( 2) 泳移现象及防止因染料对涤纶缺乏亲和力, 容易发生烘干现象合理烘干方式提高浸轧效果, 减少带液率, 涤棉带液率降低到20%~30%后, 不会发生明显泳移加入适量防泳移剂热熔染色时间和时间选择织物烘干后, 染料停留在纤维表面, 没有与纤维发生固着, 经过高温热焙烘, 染料向纤维内部扩散, 把纤维染透, 完成固色——热熔固色温度高——染料升华较多拼色时, 染料耐升华性应相近3.载体染色利用载体助剂对涤纶的增塑膨化性能, 在常压100℃条件下染色设备简单, 适合毛涤织物染色另外, 载体对染料具有亲和性, 对染料溶解能力高, 提高染料浓度, 提高吸附和扩散; 过高, 也不好但载体有毒性, 存在环境污染, 残留载体不易洗净, 影响染色牢度分散染料染色原理及工艺分散染料是一类水溶性较低的非离子型染料。
分散染料涤纶染色工艺

分散染料涤纶染色工艺分散染料是一种适用于涤纶纤维染色的染料类型。
涤纶是一种合成纤维,具有优异的耐热性、耐磨性和耐久性,因此广泛应用于纺织行业。
然而,由于其化学结构的特殊性,涤纶纤维与传统染料之间的相互作用较弱,导致染色效果较差。
针对这一问题,分散染料涤纶染色工艺应运而生。
分散染料是一类具有高色牢度的染料,能够均匀地分散在涤纶纤维中,从而实现良好的染色效果。
分散染料具有较小的分子尺寸和较低的溶解度,因此能够充分渗透进入涤纶纤维内部,实现染料与纤维的良好结合和牢固性。
此外,分散染料具有较高的耐光性、耐洗涤性和耐摩擦性,使得染料颜色能够长期保持鲜艳。
涤纶染色工艺中使用的分散染料通常为粉末状,通过溶解和悬浮在水中,并在高温下进行染色。
主要的染色步骤包括预处理、染色和固色。
首先,在预处理阶段,涤纶纤维需要进行去浆和漂白处理以去除杂质和造成染色不均的因素。
去浆过程中,可以使用氧漂剂或还原漂剂,将纤维表面的染料残留物和杂质溶解或还原。
漂白过程中,可以使用氧漂剂和高温,通过氧化或还原反应使纤维变白。
接下来是染色阶段。
分散染料被溶解在热水中,并添加助剂以帮助染料与纤维相互结合。
然后,将染料溶液与纤维一同放入染缸中,并在高温下进行染色。
在染色过程中,通过搅拌和上下流动的水流,使染料充分渗透到纤维内部。
最后,固色是确保染料与纤维牢固结合的重要步骤。
固色阶段通常包括升温、持温和冷却三个步骤。
升温过程中,水温会逐渐升高以活化染料分子,并加强与纤维的结合。
持温过程中,固色剂会添加到染料中,促使染料与纤维发生反应,并形成染色复合物。
冷却过程中,水温会逐渐降低,使染料分子和纤维结合更加牢固。
总而言之,分散染料涤纶染色工艺是一种能够有效改善涤纶纤维染色效果的方法。
通过合理的工艺流程和使用合适的染料和助剂,可以实现染纤维的均匀染色和色牢度的提高。
这种工艺不仅适用于涤纶纤维的染色,还可以应用于其他合成纤维的染色,成为纺织行业中不可或缺的染色技术之一。
《分散染料涤纶染色》PPT课件

2、工艺处方
分散染料
x%(对织物重)
分散剂NNO(或胰加漂T)
0~0.5g/L
冰HAC
0.5ml/L(调节PH=5~6)
二、热溶染色法工艺
1、工艺流程及主要条件
浸轧染液(二浸二轧,轧余率65%,20~40℃)→预烘 (80~120℃) →热溶(180~210℃,1~2min)→后处理(或 套染棉)
1.
硝基二苯胺类
主要为黄色,日晒牢度优良,但消光系数小。
C.I.分散黄33 C.I.分散黄42
R1 NRH2
HH
H
NO2
R1 SO2N
R2
2. 苯并咪唑类 主要为鲜艳的黄、橙色,但耐升华牢度差。
O
C
分散N荧光黄Ⅱ
C N
OCH3
3. 苯乙烯类
主要为绿光黄色品种,耐光性能优良,但升华牢度较差,在高温下不稳定,遇碱 易水解。
分散黄RGFL (E型)
分散红玉SE-2R (SE型N) N
NN
OH
分散红玉2GFL (S型)
O2N
Cl NN
C2H5 N
C2H4CN
Cl
O2N
NN
N(C2H4OCOCH3)2
NHCOCH3
(2)按结构分类 偶氮型:其中单偶氮类约占分散染料的50%以上,
双偶氮类约占10%。
蒽醌型:约占分散染料的25%左右。
偶氮染料 εmax=10000~15000 蒽醌型染料 εmax=3000~4000
1.
1,4-二氨基蒽醌及其衍生物
一般为紫色,个别为蓝色,染料耐光牢度较低。
分散紫E-BL 分散蓝2G
O NH2 Br
O NH2
O NHCH3
分散染料染涤纶染色工艺

涤纶筒子纱染色工艺涤纶织物由于强度高,回弹性好,耐磨性优良,尺寸稳定性好,抗皱性好,而被广泛应用于各种纺织品及服装面料.涤纶筒子纱线染色是采用高温高压染色法在高温高压筒子纱染色机上进行的。
由于聚酯纤维结构紧密,分散染料在低温条件下几乎不上染。
只有将温度提高至90℃以上,染料的上染逐渐增加。
达到110℃以上时,涤纶纤维中无定型区高分子链段的运动加剧,增加了微隙,降低了染料分子扩散进入纤维内部的阻力,提高了染料分子扩散速度,使分散染料的上染速率迅速加大。
至130℃才能获得满意的染色效果,染料利用率达到90﹪以上,得色丰满,各种染色牢度优良。
1.涤纶筒子纱染色工艺1.1生产材料及设备涤纶100D网络丝、染料、冰醋酸、匀染剂、还原清洗剂、抗静电剂、RY-1180V 型高温高压染样机1.2工艺流程及条件及处方:原纱进厂—松筒—倒角—装笼-进入染缸—前处理(退浆、煮练、漂白合一,在100℃条件下处理20min,皂洗剂1g/L去油)—水洗—染色缸加入已溶解好的染料和助剂依次侵入染槽—加入纱线染色(1℃/1min)升温至70℃匀染10min—(1℃/1min)升温至100℃匀染10min-(1℃/min)升温至130℃保温45-60min—高温排水—洗水—还原清洗(100℃处理30min,对于深色而言)—洗水—醋酸中和—洗水(上抗静电剂)—脱水—烘干。
染色处方(按织物重量):分散染料(o.w.f。
)x冰醋酸 1.2g/L匀染剂 1.2g/L还原清洗处方冰醋酸 1。
5g/L还原清洗剂 1。
5g/L抗静电剂处方 1。
0g/L2.质量问题产生原因分析及解决措施2.1松筒涤纶筒子纱线染色前需先松筒,松筒首选不锈钢弹簧管,其优点是有效穿透面积特别大,对获得匀染非常有利.可自由压缩,对不同数量批号的订单有极强的适应能力。
筒纱卷绕密度大小是很重要的,考虑到染色机械的泵的扬程高度,涤纶筒纱的卷绕密度以0.33—0。
39g/立方厘米为宜。
分散染料新型涤纶染色技术
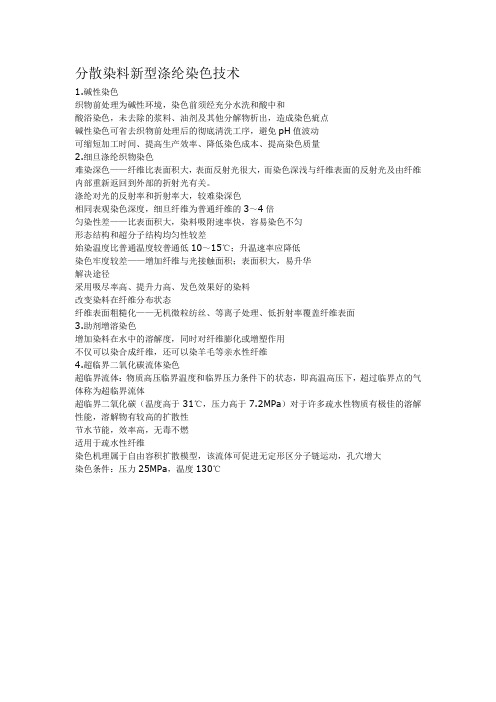
分散染料新型涤纶染色技术
1.碱性染色
织物前处理为碱性环境,染色前须经充分水洗和酸中和
酸浴染色,未去除的浆料、油剂及其他分解物析出,造成染色疵点
碱性染色可省去织物前处理后的彻底清洗工序,避免pH值波动
可缩短加工时间、提高生产效率、降低染色成本、提高染色质量
2.细旦涤纶织物染色
难染深色——纤维比表面积大,表面反射光很大,而染色深浅与纤维表面的反射光及由纤维内部重新返回到外部的折射光有关。
涤纶对光的反射率和折射率大,较难染深色
相同表观染色深度,细旦纤维为普通纤维的3~4倍
匀染性差——比表面积大,染料吸附速率快,容易染色不匀
形态结构和超分子结构均匀性较差
始染温度比普通温度较普通低10~15℃;升温速率应降低
染色牢度较差——增加纤维与光接触面积;表面积大,易升华
解决途径
采用吸尽率高、提升力高、发色效果好的染料
改变染料在纤维分布状态
纤维表面粗糙化——无机微粒纺丝、等离子处理、低折射率覆盖纤维表面
3.助剂增溶染色
增加染料在水中的溶解度,同时对纤维膨化或增塑作用
不仅可以染合成纤维,还可以染羊毛等亲水性纤维
4.超临界二氧化碳流体染色
超临界流体:物质高压临界温度和临界压力条件下的状态,即高温高压下,超过临界点的气体称为超临界流体
超临界二氧化碳(温度高于31℃,压力高于7.2MPa)对于许多疏水性物质有极佳的溶解性能,溶解物有较高的扩散性
节水节能,效率高,无毒不燃
适用于疏水性纤维
染色机理属于自由容积扩散模型,该流体可促进无定形区分子链运动,孔穴增大
染色条件:压力25MPa,温度130℃。
分散染料染涤纶工艺流程

分散染料染涤纶工艺流程
朋友们!今天来跟你们唠唠分散染料染涤纶的工艺流程。
咱先说说这涤纶啊,它可不好对付,我刚开始接触的时候,那叫一个头疼!不过后来慢慢摸出了门道。
你知道吗?有一回我在染的时候,温度没控制好,那染出来的效果,简直没法看!这可是我犯的大错,从那以后我就长记性啦。
说回正题哈,这第一步呢,得把涤纶布料准备好,要干净,不能有啥杂质。
这就好比做饭,食材得新鲜干净不是?
然后就是选染料啦,这可重要得很!我记得好像有一次,选错了染料,染出来的颜色完全不是我想要的,那叫一个郁闷呐!
接下来就是调配染料溶液,这比例可得拿捏准喽。
要是弄不好,哼哼,那就等着出岔子吧!
染色的时候,温度和时间那是关键中的关键。
我跟你们说,有一回我就因为跟旁边的同事聊天,一不留神时间过了,哇,那结果,别提多糟糕了!
染完之后的清洗也不能马虎,不然残留的染料会影响效果。
嗯...这一步就像是给做好的菜收尾,得收拾干净。
我这说着说着,好像有点乱了,不过没关系,咱继续。
我听说最近行业里出了个新的染色技术,我还不太明白呢,不知道效果咋样。
对了,以前我们厂里有个老师傅,他染色那技术,真是绝了!我从他那儿可学到不少窍门。
你们想想,如果在染色过程中突然停电了,那可咋办?哈哈,是不是很头疼?
反正这分散染料染涤纶的工艺流程,说简单也不简单,说难也不难,就看你够不够细心,有没有耐心。
我刚开始也是手忙脚乱的,慢慢就熟练啦。
好啦,我能想到的就这么多,剩下的就得靠你们自己去摸索摸索啦!。
- 1、下载文档前请自行甄别文档内容的完整性,平台不提供额外的编辑、内容补充、找答案等附加服务。
- 2、"仅部分预览"的文档,不可在线预览部分如存在完整性等问题,可反馈申请退款(可完整预览的文档不适用该条件!)。
- 3、如文档侵犯您的权益,请联系客服反馈,我们会尽快为您处理(人工客服工作时间:9:00-18:30)。
分散染料涤纶染色工艺
纤维中不同区域的玻璃化温度不同
无定形区约为67℃
结晶区约为81 ℃
结晶又取向区域约为125 ℃
经不同温度预热定形处理的涤纶织物,玻璃化温度不同
定形温度Tg 定形温度Tg
未定形75 90 105
120 123 150 125
180 122 210 115
230 105 245 90
实际染色时,染色温度应高于染色转变温度,此时纤维无定形区的大分子链段发生剧烈运动,产生瞬间孔穴
一般染色转变温度比玻璃化温度高十几度,染料分子量越大,二者相差越大
涤纶微结构影响染色性能
1.高温高压染色
染色织物色泽鲜艳、手感好
织物品种适应性好,适用的染料范围广,染料利用率高
对设备要求高,需密闭
间歇式,染色时间长,生产效率较低
染液中含有分散染料、分散剂、高温匀染剂、pH调节剂等
高温高压染色,染料易出现晶型转变
温度控制不匀,出现晶体增长现象
高温染色,表面易析出低聚物
部分染料发生水解或还原
染料要求:良好的分散稳定性、化学稳定性和较高的耐升华牢度,以保证均匀、鲜艳的染色效果
染色过程
(1)40 ℃温水化料,过滤
(2)慢慢升温至120~130 ℃,在升至染色转变温度以上时,上染速率迅速提高,应严格控制升温速率,保证染料均匀上染
(3)继续保温染色45~60min
(4)然后降温,进行还原清洗,水洗等后处理,彻底去除浮色,以提高染色产品的染色牢度和鲜艳度
染色温度选择在120~130℃为宜,温度不能超过145℃,否则纤维会造成损伤,特别是毛涤混纺织物
染色温度控制分三个阶段:
(1)染色升温阶段:在70~110℃温度区间,染料上染速率很快,要严格控制
1~2℃/min,保证染料均匀吸附
(2)染色保温阶段
染料向纤维内部扩散,并增进染料移染,染匀染透
(3)降温阶段
在玻璃化温度以上,降温速率应适当慢些,其后快速降温,避免引起织物产生折皱和手感粗
糙
pH值
控制在5~6之间,色光纯正、色泽鲜艳,上染百分率高;
高温碱性,染料水解,
碱性太强,织物损伤大,手感差
但酸性染色,齐聚物容易沉积在织物表面
浴比:
小,节能节水,但易使织物产生折皱、擦伤、染色不匀
大,耗能耗水
匹染:10:1~30:1
分散剂影响
匀染剂(载体、非离子型活性剂)
(1)缓染剂
通过助剂对染料或纤维亲和力,延缓染料上染,使染料能均匀地吸附在纤维的各个部分,从而染色均匀,但会导致上染百分率下降
(2)移染
匀染剂一般为载体、非离子型聚氧乙烯类表面活性剂
载体有毒
非离子表面活性剂在染色温度高于浊点,会产生沉淀,一般需与阴离子表面活性剂复配2.热熔染色
在185~215℃干热条件下使染料在纤维上发生固着的连续轧染的染色方法
连续化生产,生产效率高,用水量少,污水少,使用的染料要求耐升华牢度较高
染色时织物所受张力较大,织物手感及色泽鲜艳度不及高温高压染色法
一般多用于涤棉混纺织物中涤纶染色
浸轧液含有分散染料、分散剂、渗透剂、防泳移剂等
染料颗粒要特别匀细,渗透性及分散稳定性要好
二浸二轧,室温,涤棉织物轧余率一般为50~60%
焙烘固色(热熔)温度根据染料升华牢度来选择,一般为180~220℃,时间
2~1min 染色工艺条件
(1)润湿剂或渗透剂
润湿剂可以排除织物中的空气,有利于染料渗透到织物内部
织物前处理充分,可不加
(2)泳移现象及防止
因染料对涤纶缺乏亲和力,容易发生烘干现象
合理烘干方式
提高浸轧效果,减少带液率,涤棉带液率降低到20%~30%后,不会发生明显泳移
加入适量防泳移剂
热熔染色时间和时间选择
织物烘干后,染料停留在纤维表面,没有与纤维发生固着,通过高温热焙烘,染料向纤维内部扩散,把纤维染透,完成固色——热熔固色
温度高——染料升华较多
拼色时,染料耐升华性应相近
3.载体染色
利用载体助剂对涤纶的增塑膨化性能,在常压100℃条件下染色
设备简单,适合毛涤织物染色
另外,载体对染料具有亲和性,对染料溶解能力高,提高染料浓度,提高吸附和扩散;过高,也不好
但载体有毒性,存在环境污染,残留载体不易洗净,影响染色牢度。