镀铬常见故障及排除
装饰性镀铬故障处理

装饰性镀铬故障处理1.各种常见故障的产生原因及其处理方法1.1覆盖能力差1.1.1产生原因(1)镀铬中铬酸浓度过低;(2)硫酸根比值过高或过低;(3)镀液中三价铬含量过高;(4)氯离子含量过高;(5)阳极表面有氧化膜电流弱;(6)入槽时电流密度太小;(7)底层表面钝化(镍钝化时)。
1.1.2处理方法(1)分析调整铬酸(标准含量200~250g/L)与硫酸(2~2.5g/L)质量浓度之比。
铬酸的质量浓度过低,就会导致均镀能力差,并出现露黄(镍)等缺陷。
(2)分析确认硫酸根含量高,可以适当增加铬酸的质量浓度或用碳酸钡去除,一般2g/L碳酸钡可除掉1g/L硫酸。
过低时,则补加硫酸至工艺要求。
一般硫酸根比值在(80~125):1范围内。
(3)以大面积阳极和小面积阴极进行电解,将三价铬含量降至工艺要求。
镀液中三价铬含量过高,不仅会影响均镀能力,还会出现雾状和蓝膜现象。
镀液中Cr3+的含量应控制在2~5g/L。
(4)除去氯离子一般采用较经济的电解法。
镀液中氯离子质量浓度超过0.5g/L时,均镀能力、电流效率和镀层的结合力都显著下降,同时铬层出现雾状及发花。
可加入硫酸银、碳酸银、氧化银等,使氯离子与银离子发生反应成氯化银沉淀,但成本较高。
一般多采用电解处理(液温7.°C),氯离子在阳极失去电子生成滤器溢出。
为防止氯离子的积累,配制镀液和补加应使用氯离子的质量浓度一般控制在0.03g/L以下。
(5)取出阳极板将其置于稀盐酸或氢氧化钠溶液中进行清洗,以除去黄色铬酸铅(氧化膜),使其呈活化状态。
(6)增大入槽电流密度。
电流密度及溶液温度对镀液性能(如均镀能力、电流效率等)影响很大。
必须严格控制在工艺范围内。
(7)从镀镍工序着手排除。
镀铬的均镀(覆盖)能力主要取决于溶液的组成和正确的操作,但中间镀层的质量和工艺流程是否合理也会对其有一定的影响。
当镀镍液中杂质含量过高时,在镀件德低电流部位铬沉积困难。
造成镀层不均。
镀铬常见故障分析和纠正

镀铬常见故障分析和纠正1.铬层发花或发雾造成铬层发花或发雾的原因很多,其中大多是底镀层或其他外部原因引起的。
如镀镍液中糖精太多;镍层抛光时的线速度;抛光过的零件镀铬前表面有油或有抛光膏;镀镍出槽时形成双性电极;镀铬时挂具弹得不紧;铜锡合金底层中锡含量太高;镀铬时的温度太高;镀铬电源波形有问题或镀铬液中氯离子过多等。
分析故障时,可以取一批在其他镀铬液中套铬没有出现发花或发雾的零件浸入有故障的镀铬液中试镀,假使本单位没有其他镀铬液,可以将刚镀好的光亮镀镍(未经抛光)的零件,放在新配制的5%(重量)硫酸中浸2 min,进行充分的活化后直接套铬。
假如这样套铬所得的铬层良好,不出现发花或发雾现象,那么故障起源于镀铬以前,与镀铬液及镀铬电源无关。
如果起源于镀铬以前,就要根据各单位的具体情况采取不同的措施。
如采用光亮镀镍直接套铬时,应检查镀镍液中糖精是否太多;镀好光亮镍出槽时是否有双性电极现象,亮镍出槽到镀铬相隔的时间是否过长和镀铬前的硫酸活化液浓度是否太稀或过高。
镀镍液中糖精太多造成铬层发花的现象,一般在零件的尖端和边缘较明显。
这时可用电解的方法纠正n双性电极引起的铬层发花,有规则地出现在零件的一个侧面(即靠近镀镍出槽时另一阴极的侧面)。
这时要在镀镍出槽时关掉电源或把电流调至最小时取出零件,或者同时取出阴极上所有的零件进行检查和纠正。
零件镀好亮镍出槽到镀铬的时间相隔在2min之内,一般可以不必进行硫酸活化而直接套铬,若时间间隔在2min以上,那么最好用3%~5%的硫酸活化后套铬。
如果对活化液的浓度有怀疑时,可以按分析进行调整或更换新液。
假如是零件镀暗镍或半亮镍抛光后套铬,特别要注意抛光轮的大小和零件抛光后的除油和活化。
由于镍层容易钝化所以抛光时抛光轮太大、转速太快或操作者抛光时把零件压在抛光轮上的力量较大,都将使镍层在抛光时温度升高而钝化。
在钝化的镍层上套铬,会出现发花的现象。
这种现象夏天更容易出现。
抛光后的零件,必须经过除油和活化。
铜镍铬电镀常见故障原因与排除

1.焦磷酸钾过高
2.镀液有六价铬
3.镀液有残余双氧水
1.分析成分,调整P比正常范围
2.加温50℃,搅拌下加入-0.4克升保险粉,加入1-2克/升活性炭,搅拌30分钟,趁热过滤
3.加热镀液,电解30分钟
镀镍常见故障原因与排除方法
故障现象
故障原因
故障排除方法
镀层有针孔
1.前处理不良
2.镀液中有油或有机杂质过多
6.加温60-70℃,在搅拌下加入氢氧化钙,搅拌30分钟,静止过滤
镀层有针孔
1.基体表面粗糙
2.镀液有油或有机杂质
3.铜含量过低或氰化钠含量过高
4.阴极电流密度过大
5.阳极面积太小
1.加强抛光
2.活性炭粉处理
3.分析成分,调整正常范围
4.降低电流密度
5.增加阳积面积
沉积速度慢
深镀能力差
1.阴极电流密度太小
镀层有麻点
镀层粗糙
1.预镀层太薄或粗糙
2.阳极磷铜含磷少
3.有一价铜或铜粉
4.硫酸铜含量过高
5.温度过高
6.挂具钩子上的铬层未彻底退除
1.加强预镀层质量
2.更换阳极
3.加少许双氧水,方法同上
4.冲稀镀液,调整各成分
5.建议用冷冻
6.彻底清除挂具残余镀层
镀层有条纹
1.镀液中氯离子过多
2.光剂比列失调
3.预镀层有条纹
2.镀前活化
3.检查线路
4.分析成分,调节成分至正常值
5.电解处理,阳极面积大大于阴极
6.电解法除去
铬层的光亮度差
容易出现烧焦现象
1.铬酸或硫酸含量太低
2.三价铬含量太低或
高
3.异金属杂质过多
镀铬常见故障及处理
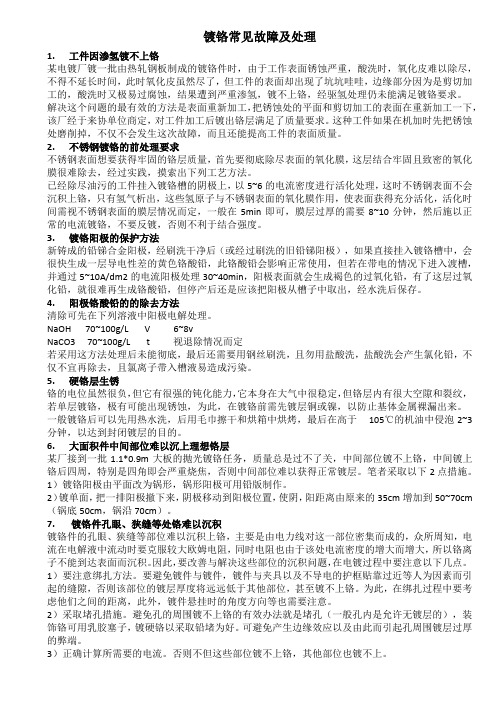
镀铬常见故障及处理1. 工件因渗氢镀不上铬某电镀厂镀一批由热轧钢板制成的镀铬件时,由于工作表面锈蚀严重,酸洗时,氧化皮难以除尽,不得不延长时间,此时氧化皮虽然尽了,但工件的表面却出现了坑坑哇哇,边缘部分因为是剪切加工的,酸洗时又极易过腐蚀,结果遭到严重渗氢,镀不上铬,经驱氢处理仍未能满足镀铬要求。
解决这个问题的最有效的方法是表面重新加工,把锈蚀处的平面和剪切加工的表面在重新加工一下,该厂经于来协单位商定,对工件加工后镀出铬层满足了质量要求。
这种工件如果在机加时先把锈蚀处磨削掉,不仅不会发生这次故障,而且还能提高工件的表面质量。
2. 不锈钢镀铬的前处理要求不锈钢表面想要获得牢固的铬层质量,首先要彻底除尽表面的氧化膜,这层结合牢固且致密的氧化膜很难除去,经过实践,摸索出下列工艺方法。
已经除尽油污的工件挂入镀铬槽的阴极上,以5~6的电流密度进行活化处理,这时不锈钢表面不会沉积上铬,只有氢气析出,这些氢原子与不锈钢表面的氧化膜作用,使表面获得充分活化,活化时间需视不锈钢表面的膜层情况而定,一般在5min即可,膜层过厚的需要8~10分钟,然后施以正常的电流镀铬,不要反镀,否则不利于结合强度。
3. 镀铬阳极的保护方法新铸成的铅锑合金阳极,经刷洗干净后(或经过刷洗的旧铅锑阳极),如果直接挂入镀铬槽中,会很快生成一层导电性差的黄色铬酸铅,此铬酸铅会影响正常使用,但若在带电的情况下进入渡槽,并通过5~10A/dm2的电流阳极处理30~40min,阳极表面就会生成褐色的过氧化铅,有了这层过氧化铅,就很难再生成铬酸铅,但停产后还是应该把阳极从槽子中取出,经水洗后保存。
4. 阳极铬酸铅的的除去方法清除可先在下列溶液中阳极电解处理。
NaOH 70~100g/L V 6~8vNaCO3 70~100g/L t 视退除情况而定若采用这方法处理后未能彻底,最后还需要用钢丝刷洗,且勿用盐酸洗,盐酸洗会产生氯化铅,不仅不宜再除去,且氯离子带入槽液易造成污染。
铜镍铬电镀常见故障原因与排除

镀层有针孔
1.基体表面粗糙
2.镀液有油或有机杂质
3.铜含量过低或氰化钠含量过高
4.阴极电流密度过大
5.阳极面积太小
1.加强抛光
2.活性炭粉处理
3.分析成分,调整正常范围
4.降低电流密度
5.增加阳积面积
沉积速度慢
深镀能力差
1.阴极电流密度太小
2.阳极钝化或阳极面积太小
3.游离氰化钠太高
4.溶液中有铬酸盐
1.提高电流密度
2.增加阳极面积或提高氰化钠或提高镀液温度
3.调整成分
4.同上处理方法
镀层疏松
孔隙多
1.阳极钝化
2.镀液中碳酸盐过多或有粘胶状的杂质
3.锌-铝合金基体中铝含量过高
1.同上处理方法
2.同上处理方法
3.要经过二次浸锌后再进行镀铜
高
3.异金属杂质过多
4.温度太低
5.阴极电流密度太大
6.阳极导电不良
7.镀液中有少量的硝酸根
1.分析成分,调整成分至正常值
2.电解法控制三价铬成分
3.电解法去除
4.提高温度
5.降低电流密度
6.检查线路
7.电解法处理
铬层有明显的裂纹
1.温度太低且阴极电流密度太高2.镀铬硫酸过高或铬酸含量过低
3.氯离子过多
镀镍常见故障原因与排除方法
故障现象
故障原因
故障排除方法
镀层有针孔
1.前处理不良
2.镀液中有油或有机杂质过多
3.湿润剂不够
4.镀液中铁等异金属
质
5.硼酸含量不足
6.温度太低
1.加强前处理
镀铬常见缺陷及其原因
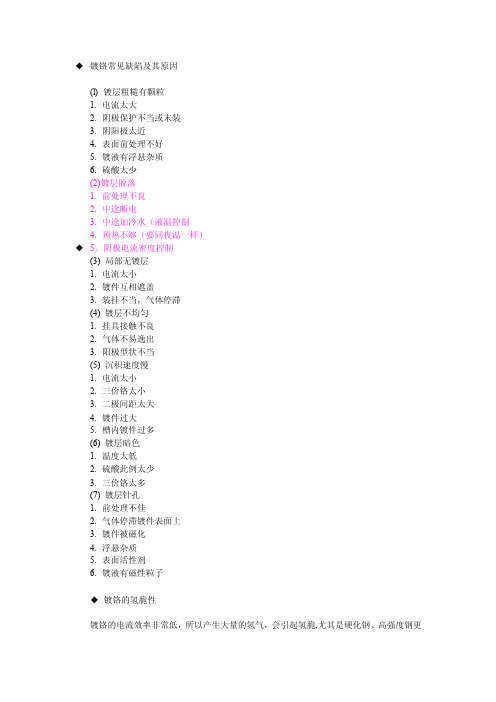
◆镀铬常见缺陷及其原因(l) 镀层粗糙有颗粒1. 电流太大2. 阴极保护不当或末装3. 阴阳极太近4. 表面前处理不好5. 镀液有浮悬杂质6. 硫酸太少(2)镀层脱落1. 前处理不良2. 中途断电3. 中途加冷水(液温控制4. 预热不够(要同夜温一样)◆5。
阴极电流密度控制(3) 局部无镀层1. 电流太小2. 镀件互相遮盖3. 装挂不当,气体停滞(4) 镀层不均匀1. 挂具接触不良2. 气体不易逸出3. 阳极型状不当(5) 沉积速度慢1. 电流太小2. 三价铬太小3. 二极间距太大4. 镀件过大5. 槽内镀件过多(6) 镀层暗色1. 温度太低2. 硫酸此例太少3. 三价铬太多(7) 镀层针孔1. 前处理不佳2. 气体停滞镀件表面上3. 镀件被磁化4. 浮悬杂质5. 表面活性剂6. 镀液有磁性粒子◆镀铬的氢脆性镀铬的电流效率非常低,所以产生大量的氢气,会引起氢脆,尤其是硬化钢、高强度钢更需注意。
去除氢脆方法有:(l) 镀前先做应力消除(stress relieving) : 镀铬表面必须没有应力存在,一般镀件经机械加工、研磨,或硬化热处理都有残留应力( residual stress),可加热150至230℃消除残留应力。
(2) 镀后烘箱去氢: 根据工件大小和镀层厚度确定温度和时间,通常选择的温度为150~250℃,时间0.5~5h。
铬是一种微带天蓝色的银白色金属。
电极电位虽然很负,但它有很强的钝化性能,在大气中很快钝化,显示出具有贵金属的性质,所以钢铁零件镀铬层是阴极镀层。
铬层在大气中很稳定,能长期保持其光泽,在碱、硝酸、硫化物、碳酸盐以及有机酸等腐蚀介质中非常稳定,但可溶于盐酸等氢卤酸和热的浓硫酸中。
铬层硬度高(HV800~110kg/mm2),耐磨性好,反光能力强,有较好的耐热性。
在500℃以下光泽和硬度均无明显变化;温度大于500℃开始氧化变色;大于700℃时才开始变软。
由于镀铬层的优良性能,广泛用作防护—装饰性镀层体系的外表层和机能镀层。
电镀装饰铬常见故障及其处理方法:镀铬层结合力差
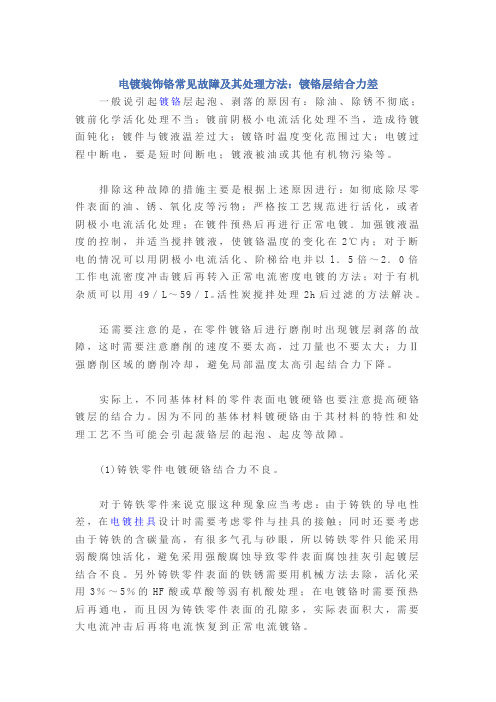
电镀装饰铬常见故障及其处理方法:镀铬层结合力差一般说引起镀铬层起泡、剥落的原因有:除油、除锈不彻底;镀前化学活化处理不当;镀前阴极小电流活化处理不当,造成待镀面钝化;镀件与镀液温差过大;镀铬时温度变化范围过大;电镀过程中断电,要是短时间断电;镀液被油或其他有机物污染等。
排除这种故障的措施主要是根据上述原因进行:如彻底除尽零件表面的油、锈、氧化皮等污物;严格按工艺规范进行活化,或者阴极小电流活化处理;在镀件预热后再进行正常电镀.加强镀液温度的控制,并适当搅拌镀液,使镀铬温度的变化在2℃内;对于断电的情况可以用阴极小电流活化、阶梯给电并以l.5倍~2.0倍工作电流密度冲击镀后再转入正常电流密度电镀的方法;对于有机杂质可以用49/L~59/I。
活性炭搅拌处理2h后过滤的方法解决。
还需要注意的是,在零件镀铬后进行磨削时出现镀层剥落的故障,这时需要注意磨削的速度不要太高,过刀量也不要太大;力Ⅱ强磨削区域的磨削冷却,避免局部温度太高引起结合力下降。
实际上,不同基体材料的零件表面电镀硬铬也要注意提高硬铬镀层的结合力。
因为不同的基体材料镀硬铬由于其材料的特性和处理工艺不当可能会引起菠铬层的起泡、起皮等故障。
(1)铸铁零件电镀硬铬结合力不良。
对于铸铁零件来说克服这种现象应当考虑:由于铸铁的导电性差,在电镀挂具设计时需要考虑零件与挂具的接触;同时还要考虑由于铸铁的含碳量高,有很多气孔与砂眼,所以铸铁零件只能采用弱酸腐蚀活化,避免采用强酸腐蚀导致零件表面腐蚀挂灰引起镀层结合不良。
另外铸铁零件表面的铁锈需要用机械方法去除,活化采用3%~5%的HF酸或草酸等弱有机酸处理;在电镀铬时需要预热后再通电,而且因为铸铁零件表面的孔隙多,实际表面积大,需要大电流冲击后再将电流恢复到正常电流镀铬。
(2)不锈钢电镀硬铬结合力不良。
由于不锈钢零件表面容易生成氧化膜,所以在电镀铬前必须要将表面的氧化膜去除并且活化才能确保镀层的结合力。
不锈钢电镀硬铬工艺的流程为:化学除油+电解除油+阴极活化+镀冲击镍+镀硬铬。
化学镀铬故障及排除
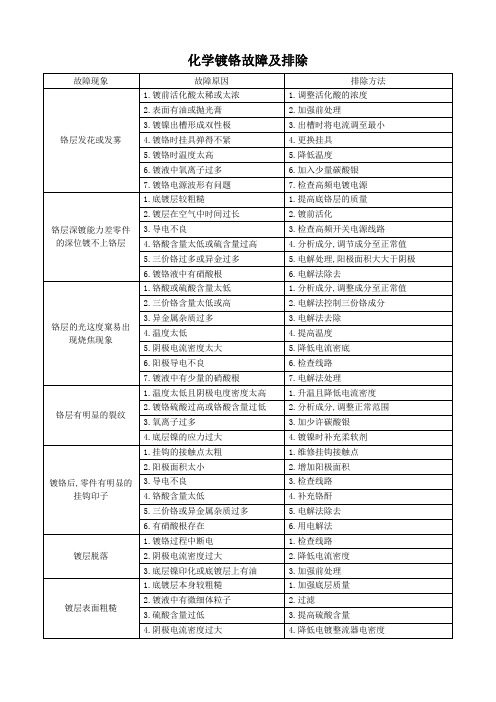
4.阴极电流密度过大
4.降低电镀整流器电密度
4.铬酸含量太低
4.补充铬酐
5.三价铬或异金属杂质过多
5.电解法除去
6.有硝酸根存在
6.用电解法
镀层脱落
1.镀铬过程中断电
1.检查线路
2.阴极电流密度过大
2.降低电流密度
3.底层镍印化或底镀层上有油
3.加强前处理
镀层表面粗糙
1.底镀层本身较粗糙
1.加强底层质量
2.镀液中有微细体粒子
2.过滤
3.硫酸含量过低
化学镀铬故障及排除
故障现象
故障原因
排除方法
铬层发花或发雾
1.镀前活化酸太稀或太浓
1.调整活酸的浓度
2.表面有油或抛光膏
2.加强前处理
3.镀镍出槽形成双性极
3.出槽时将电流调至最小
4.镀铬时挂具弹得不紧
4.更换挂具
5.镀铬时温度太高
5.降低温度
6.镀液中氧离子过多
6.加入少量碳酸银
7.镀铬电源波形有问题
1.温度太低且阴极电度密度太高
1.升温且降低电流密度
2.镀铬硫酸过高或铬酸含量过低
2.分析成分,调整正常范围
3.氧离子过多
3.加少许碳酸银
4.底层镍的应力过大
4.镀镍时补充柔软剂
镀铬后,零件有明显的挂钩印子
1.挂钩的接触点太粗
1.维修挂钩接触点
2.阳极面积太小
2.增加阳极面积
3.导电不良
3.检查线路
铬层的光这度窠易出现烧焦现象
1.铬酸或硫酸含量太低
1.分析成分,调整成分至正常值
2.三价铬含量太低或高
2.电解法控制三份铬成分
镀装饰铬常见故障及纠正方法

镀装饰铬常见故障及纠正方法光亮度不足a)温度低或电流密度过高b)硫酸根含量低c)三价铬高d)铁杂质含量高a)升温,检查电流是否在工艺范围b)分析补充c)大阳极,小阴极电解d)用离子交换或隔膜电解覆盖能力差a)温度高而电流密度低b)硫酸含量高,c)三价铬不足d)锌、铜、铁杂质多a)降低,检查电流是否在工艺范围b)分析后用BaCO3,除去部分硫酸根;c)大阴极,小阳极电解d)离子交换或隔膜电解处理局部无铬层a)孔眼未堵塞b)装挂不当,产生气袋或导电不良c)零件形状复杂,未使用辅助阳极d)零件互助屏蔽e)镀件表面有油污f)挂具未绝缘a)用塑料管堵塞b)改用挂具c)选择适当的辅助阳极d)少挂零件e)对镀件进行重新处理f)改进挂具绝缘镀铬层同镀镍层一起剥皮a)镀前处理不彻底b)镀镍层内应力大a)加强镀前处理b)调整镀镍溶液铜锡合金镀层上镀铬时出现黑花a)溶液温度低b)镀铬前处理不彻底c)通电过快或过慢e)铜锡合金中含锡量过高a)升高温度b)加强镀铬前处理c)改进操作e)调整铜锡合金镀硬铬镀层剥落a)镀前处理不良b)镀铬过程中途断电c)零件进槽预热时间短d)溶液温度或阴极电流密度变化太大e)硫酸含量过高a)加强镀前处理b)重新镀铬时,进行阳极处理或阴极小电流活化处理c)加长预热时间d)严格控制溶液温度和阴极电流密度e)加碳酸钡处理铸铁件镀不上铬层,仅有析氢反应a)镀前浸蚀过度b)进行阳极处理时,造成石墨裸露c)阴极电流密度过低a)重新全加工后再镀b)重新全加工后再镀c)提高阴极电流密度镀层粗糙,有铬瘤a)阴极电流密度过大b)阴、阳极间距离太近c)零件形状外凸,没有使用保护阴极d)硫酸根过高a)降低阴极电流密度b)放宽阴、阳极间距离c)使用合适的保护阴极d)加碳酸钡处理镀层或底层金属上有明显裂纹钢在淬火时有应力镀前将零件回火消除应力。
影响镀铬品质问题点及附图
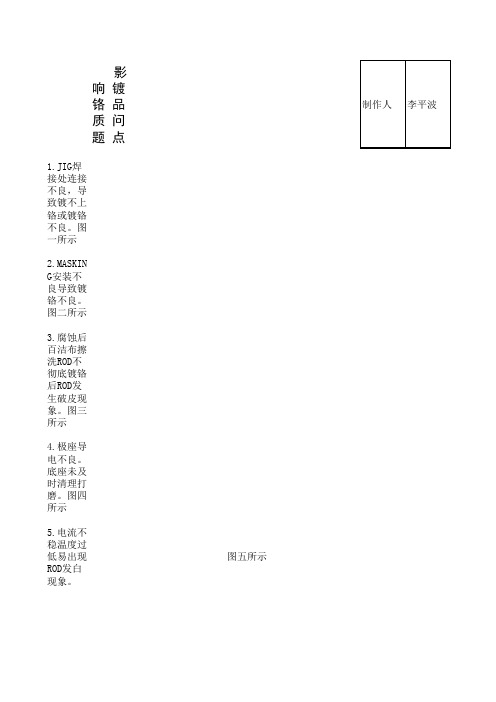
影 响 镀 铬 品 质 问 题 点制作人李平波
1.JIG焊接处连接不良,导致镀不上铬或镀铬不良。
图一所示
2.MASKING安装不良导致镀铬不良。
图二所示
3.腐蚀后百洁布擦洗ROD不彻底镀铬后ROD发生破皮现象。
图三所示
4.极座导电不良。
底座未及时清理打磨。
图四所示
5.电流不稳温度过低易出现ROD发白现象。
图五所示
6.BF1抛光毛坯(外协)螺纹及表面沾付很多油污,镀铬前清理不洁净镀铬时影响镀铬液质量,建议在抛
7.镀铬人员流动性大,操作者对镀铬作业注意事项不完全了解应及时进行教育。
图 一图 二
图 四
图 五图 六
量,建议在抛光处增加螺纹清洗设备。
图六所示。
装饰性镀铬常见故障以及排除方法
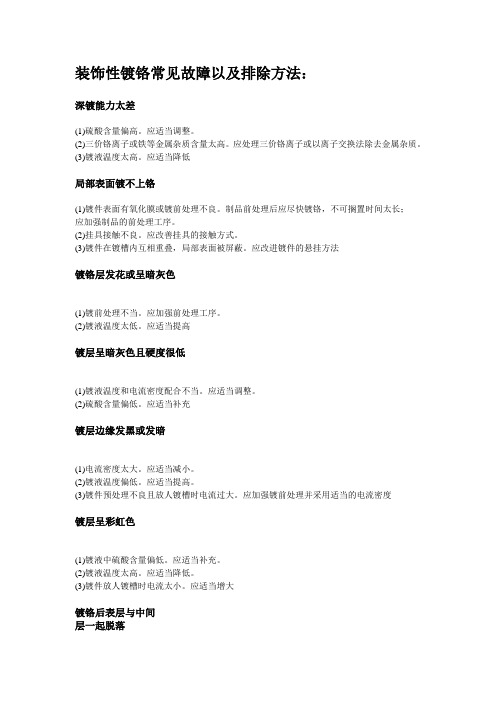
装饰性镀铬常见故障以及排除方法:深镀能力太差(1)硫酸含量偏高。
应适当调整。
(2)三价铬离子或铁等金属杂质含量太高。
应处理三价铬离子或以离子交换法除去金属杂质。
(3)镀液温度太高。
应适当降低局部表面镀不上铬(1)镀件表面有氧化膜或镀前处理不良。
制品前处理后应尽快镀铬,不可搁置时间太长;应加强制品的前处理工序。
(2)挂具接触不良。
应改善挂具的接触方式。
(3)镀件在镀槽内互相重叠,局部表面被屏蔽。
应改进镀件的悬挂方法镀铬层发花或呈暗灰色(1)镀前处理不当。
应加强前处理工序。
(2)镀液温度太低。
应适当提高镀层呈暗灰色且硬度很低(1)镀液温度和电流密度配合不当。
应适当调整。
(2)硫酸含量偏低。
应适当补充镀层边缘发黑或发暗(1)电流密度太大。
应适当减小。
(2)镀液温度偏低。
应适当提高。
(3)镀件预处理不良且放人镀槽时电流过大。
应加强镀前处理并采用适当的电流密度镀层呈彩虹色(1)镀液中硫酸含量偏低。
应适当补充。
(2)镀液温度太高。
应适当降低。
(3)镀件放人镀槽时电流太小。
应适当增大镀铬后表层与中间层一起脱落(1)中间层与基体金属结合不良。
应加强中间镀层的镀前处理工作。
(2)中间镀层性能不良。
应检查中间层的镀液是否符合工艺要求镀层呈暗色且镀槽铅衬溶解镀液中有硝酸污染。
应先将镀液中硝酸除去,然后用大电流处理镀液镀层呈暗色并有紫褐色斑点镀液中铁杂质含量太高。
应处理或更换部分镀液,使铁杂质含量降低镀层沉积速度太慢(1)镀件悬挂不当。
应改进悬挂方式。
(2)硫酸含量过高或过低。
应精确测定镀液中的硫酸含量后进行调整无铬层沉积(1)电路电极接反。
应检查电极的接法。
(2)导电不良或镀件前处理不当。
应改善导电或加强镀前的处理工作镀层呈青灰色(发乌)(1)镀液中各种组分的比值不当。
应按工艺要求进行调整。
(2)镀液温度太高。
应适当降低。
(3)电镀时间太长或电流过大。
应缩短电镀时间或将电流调整到15—20A/dm2范围内镀层表面有明显的裂纹(1)镀液温度太低。
镀硬铬故障分析:镀铬层分层脱落
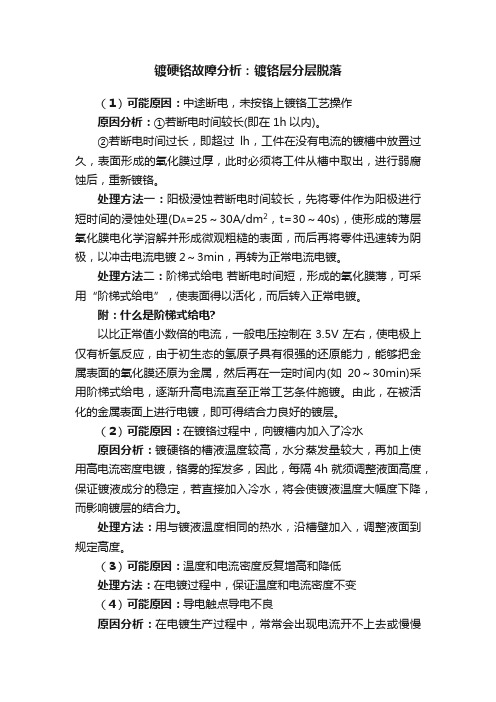
镀硬铬故障分析:镀铬层分层脱落(1)可能原因:中途断电,未按铬上镀铬工艺操作原因分析:①若断电时间较长(即在1h以内)。
②若断电时间过长,即超过lh,工件在没有电流的镀槽中放置过久,表面形成的氧化膜过厚,此时必须将工件从槽中取出,进行弱腐蚀后,重新镀铬。
处理方法一:阳极浸蚀若断电时间较长,先将零件作为阳极进行短时间的浸蚀处理(D A=25~30A/dm2,t=30~40s),使形成的薄层氧化膜电化学溶解并形成微观粗糙的表面,而后再将零件迅速转为阴极,以冲击电流电镀2~3min,再转为正常电流电镀。
处理方法二:阶梯式给电若断电时间短,形成的氧化膜薄,可采用“阶梯式给电”,使表面得以活化,而后转入正常电镀。
附:什么是阶梯式给电?以比正常值小数倍的电流,一般电压控制在3.5V左右,使电极上仅有析氢反应,由于初生态的氢原子具有很强的还原能力,能够把金属表面的氧化膜还原为金属,然后再在一定时间内(如20~30min)采用阶梯式给电,逐渐升高电流直至正常工艺条件施镀。
由此,在被活化的金属表面上进行电镀,即可得结合力良好的镀层。
(2)可能原因:在镀铬过程中,向镀槽内加入了冷水原因分析:镀硬铬的槽液温度较高,水分蒸发量较大,再加上使用高电流密度电镀,铬雾的挥发多,因此,每隔4h就须调整液面高度,保证镀液成分的稳定,若直接加入冷水,将会使镀液温度大幅度下降,而影响镀层的结合力。
处理方法:用与镀液温度相同的热水,沿槽壁加入,调整液面到规定高度。
(3)可能原因:温度和电流密度反复增高和降低处理方法:在电镀过程中,保证温度和电流密度不变(4)可能原因:导电触点导电不良原因分析:在电镀生产过程中,常常会出现电流开不上去或慢慢自动下降,此类异常主要是有镀槽日常清洁维护不善,造成线路电阻和镀液欧姆电阻增大而引起的,比如:a.(阴)阳极铜棒和端头接线处,锈蚀严重,接触不良;b.端头接线与整流器的接线柱接触不良,锈蚀;c.阴极导电杆、阳极导电杆、挂具的挂钩、阳极挂钩等锈蚀、不洁,接触不良。
镀硬铬常见故障及处理

镀硬铬常见故障及处理镀硬铬,听着高大上,其实就是把金属表面镀上一层铬,像给铁皮穿上了金色的外衣,既美观又耐磨,简直是机械界的时尚达人。
不过,事情总有不如意的时候,镀硬铬也有可能出问题,今天就来聊聊那些常见的故障和处理方法,保证让你听得懂,甚至乐呵乐呵。
镀硬铬的表面有时会出现“泡泡”,这可就尴尬了。
想象一下,刚镀完,就像一块精致的蛋糕上冒出了气泡,这视觉效果简直是零分。
泡泡出现的原因,可能是表面清理不干净,或者镀铬的液体中杂质太多。
处理方法嘛,咱们可以先把表面清理得干干净净,再重新镀一层。
这个时候,像对待小朋友一样,耐心点儿,慢慢来,确保每个细节都到位。
再说说“剥落”问题,真的是让人气得想抓墙。
镀层一层一层地剥落,就像秋天的树叶掉了一地,心疼得不行。
剥落的原因一般是底材处理不当,或者镀铬液体温度不合适。
解决这个问题得先找出原因,搞清楚后,再好好处理底材,确保附着力强,重新镀的时候,温度也得合适,这样才能保证镀层紧紧地贴在金属上。
还有个问题就是“发黑”,乍一看,像个小黑胖子,心里可不美滋滋。
发黑的原因很多,可能是因为镀铬后的氧化,或者是电流不稳定。
想要解决这个问题,咱们可以试试使用一些特殊的化学品来清理表面,避免氧化,再重新镀一次。
不过,清理的过程要小心,别弄坏了底材,结果得不偿失。
有些小伙伴可能会遇到“表面粗糙”的情况,就像是吃了颗沙粒,心里难受。
粗糙的原因可能是镀铬液中的颗粒物太多,或者电流过大。
处理这问题的方法简单粗暴,先检查镀铬液,确保液体干净,再调节电流,慢慢来,别急。
镀完之后,用砂纸打磨一下,效果会好很多。
说到“颜色不均”,简直就是在给镀铬作品画个“马赛克”,可难看了。
颜色不均的原因往往是镀铬工艺不稳定,或者液体中的成分分布不均。
处理这个问题,首先要调整工艺参数,确保镀铬时各个位置都能均匀受力,然后再考虑更换镀液。
咱们的目标是让每一寸都光滑如新,毕竟谁不想有个颜值爆表的金属件呢?得提提“光泽差”的问题,这就像是洗车后没擦干,表面显得黯淡无光,真让人心里一阵咯噔。
镀铬常见故障及处理
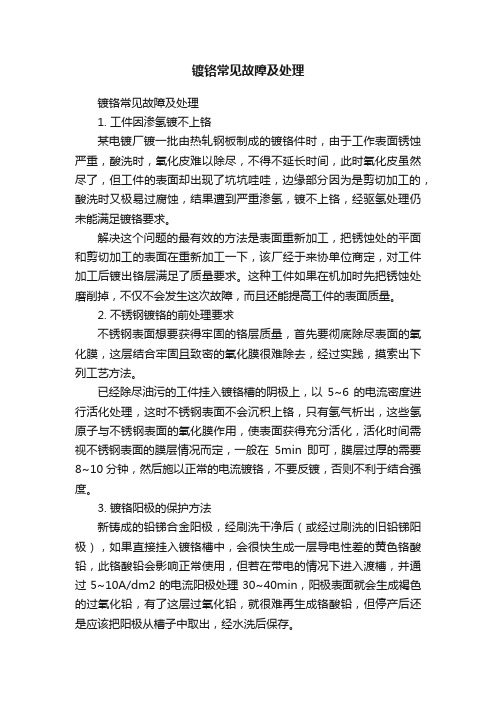
镀铬常见故障及处理镀铬常见故障及处理1. 工件因渗氢镀不上铬某电镀厂镀一批由热轧钢板制成的镀铬件时,由于工作表面锈蚀严重,酸洗时,氧化皮难以除尽,不得不延长时间,此时氧化皮虽然尽了,但工件的表面却出现了坑坑哇哇,边缘部分因为是剪切加工的,酸洗时又极易过腐蚀,结果遭到严重渗氢,镀不上铬,经驱氢处理仍未能满足镀铬要求。
解决这个问题的最有效的方法是表面重新加工,把锈蚀处的平面和剪切加工的表面在重新加工一下,该厂经于来协单位商定,对工件加工后镀出铬层满足了质量要求。
这种工件如果在机加时先把锈蚀处磨削掉,不仅不会发生这次故障,而且还能提高工件的表面质量。
2. 不锈钢镀铬的前处理要求不锈钢表面想要获得牢固的铬层质量,首先要彻底除尽表面的氧化膜,这层结合牢固且致密的氧化膜很难除去,经过实践,摸索出下列工艺方法。
已经除尽油污的工件挂入镀铬槽的阴极上,以5~6的电流密度进行活化处理,这时不锈钢表面不会沉积上铬,只有氢气析出,这些氢原子与不锈钢表面的氧化膜作用,使表面获得充分活化,活化时间需视不锈钢表面的膜层情况而定,一般在5min即可,膜层过厚的需要8~10分钟,然后施以正常的电流镀铬,不要反镀,否则不利于结合强度。
3. 镀铬阳极的保护方法新铸成的铅锑合金阳极,经刷洗干净后(或经过刷洗的旧铅锑阳极),如果直接挂入镀铬槽中,会很快生成一层导电性差的黄色铬酸铅,此铬酸铅会影响正常使用,但若在带电的情况下进入渡槽,并通过5~10A/dm2的电流阳极处理30~40min,阳极表面就会生成褐色的过氧化铅,有了这层过氧化铅,就很难再生成铬酸铅,但停产后还是应该把阳极从槽子中取出,经水洗后保存。
4. 阳极铬酸铅的的除去方法清除可先在下列溶液中阳极电解处理。
NaOH 70~100g/L V 6~8vNaCO3 70~100g/L t 视退除情况而定若采用这方法处理后未能彻底,最后还需要用钢丝刷洗,且勿用盐酸洗,盐酸洗会产生氯化铅,不仅不宜再除去,且氯离子带入槽液易造成污染。
电镀铬层发花、发灰的常见故障与解决方法
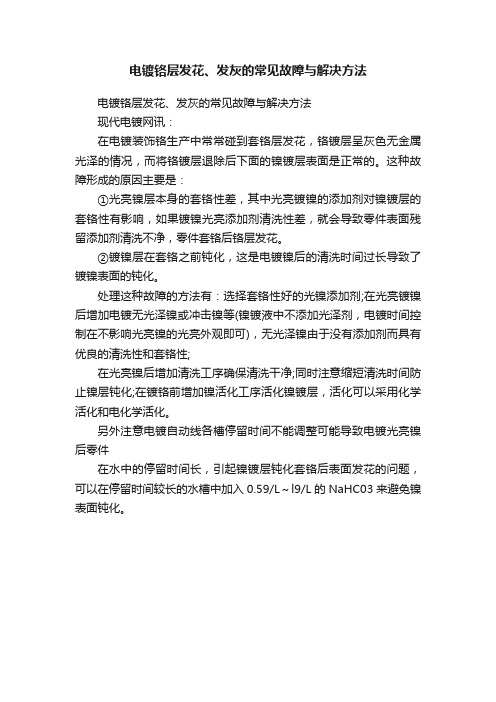
电镀铬层发花、发灰的常见故障与解决方法
电镀铬层发花、发灰的常见故障与解决方法
现代电镀网讯:
在电镀装饰铬生产中常常碰到套铬层发花,铬镀层呈灰色无金属光泽的情况,而将铬镀层退除后下面的镍镀层表面是正常的。
这种故障形成的原因主要是:
①光亮镍层本身的套铬性差,其中光亮镀镍的添加剂对镍镀层的套铬性有影响,如果镀镍光亮添加剂清洗性差,就会导致零件表面残留添加剂清洗不净,零件套铬后铬层发花。
②镀镍层在套铬之前钝化,这是电镀镍后的清洗时间过长导致了镀镍表面的钝化。
处理这种故障的方法有:选择套铬性好的光镍添加剂;在光亮镀镍后增加电镀无光泽镍或冲击镍等(镍镀液中不添加光泽剂,电镀时间控制在不影响光亮镍的光亮外观即可),无光泽镍由于没有添加剂而具有优良的清洗性和套铬性;
在光亮镍后增加清洗工序确保清洗干净;同时注意缩短清洗时间防止镍层钝化;在镀铬前增加镍活化工序活化镍镀层,活化可以采用化学活化和电化学活化。
另外注意电镀自动线各槽停留时间不能调整可能导致电镀光亮镍后零件
在水中的停留时间长,引起镍镀层钝化套铬后表面发花的问题,可以在停留时间较长的水槽中加入0.59/L~l9/L的NaHC03来避免镍表面钝化。
镀硬铬常见故障分析与排除

镀硬铬常见故障分析与排除镀硬铬常见故障排除一、镀层粗糙1.工件基体表面粗糙:镀硬铬的工件镀前表面粗糙度值应低于Ra0.2μm,所以镀前应进行多次磨光或精磨加工,已得到较高的表面光亮度。
表面越光亮平滑,镀层也越细致光亮。
2.电流密度过大:应精确计算工件的受镀面积,在一定的温度下,选择适当的阴极电流密度电镀,防止电流密度过大。
3.工件距离阳极太近或工件凸起部位未安装保护阴极:适当增大阴、阳极之间的距离,工件的凸起部位应安装合适的保护阴极。
4.镀液不清洁,有机械杂质:应定期过滤镀液,保持镀液清洁。
二、镀层厚度不均匀1.工件悬挂位置不适当,各部位与阴极距离不均等:调整工件在镀槽中的悬挂位置,根据工件形状安装合适辅助阳极及保护阴极。
2.阳极分布不均匀或阳极长短与工件受镀面不协调:合理布置阳极,阳极长度应比阴极稍短些。
大工件可采用不同长度的阳极相间悬挂,以使电力线能在工件受镀面上均匀分布。
3.某些阳极不导电或导电不良:检查阳极导电情况,对不导电的阳极应取出刷洗干净,并清洗挂钩,使之导电良好。
4.镀液分散能力差:化验镀液成分,根据分析结果,调整镀液,使之达到工艺范围内。
三、低电流密度区镀不上铬1.冲击电流过小:加大冲击电流后施镀,并适当延长冲击镀的时间。
2.阳极处理时间过长,或阶梯式给电小电流时间过长:适当缩短阳极处理时间,一般工件控制在15~30s,或不进行阳极处理。
工件预热后,用大于正常电流密度2倍的电流密度冲击镀2~5min,然后在恢复到正常电流密度施镀。
采用阶梯式给电方式时,应在3~5min 内升至正常的电流密度。
3.镀液中硫酸含量过高:化验镀液,根据分析结果补加铬酐或加入碳酸钡除去多于的硫酸根,使之达到工艺范围之内。
四、镀层结合力不好,镀铬层在磨光时产生剥离现象1.镀前处理不良:加强镀前处理,务必将油、锈去除干净,保证工件表面没有油污、锈斑或氧化皮。
2.工件预热时间过短:适当延长预热时间,对于薄壁工件预热3~10min,对于大工件预热5~15 min。
镀铬件常见故障及解决方案

镀铬件常见故障及解决方案1.故障现象:光亮度不足产生的原因:a)温度低或电流密度过高b)硫酸根含量低c)三价铬高d)铁杂质含量高纠正方法:a)升温,检查电流是否在工艺范围b)分析补充c)大阳极,小阴极电解d)用离子交换或隔膜电解2. 故障现象:覆盖能力差产生的原因:a)温度高而电流密度低b)硫酸含量高,c)三价铬不足d)锌、铜、铁杂质多纠正方法:a)降低,检查电流是否在工艺范围b)分析后用BaCO3,除去部分硫酸根;c)大阴极,小阳极电解d)离子交换或隔膜电解处理3. 故障现象:局部无铬层产生的原因:a)孔眼未堵塞b)装挂不当,产生气袋或导电不良c)零件形状复杂,未使用辅助阳极d)零件互助屏蔽e)镀件表面有油污f)挂具未绝缘纠正方法:a)用塑料管堵塞b)改用挂具c)选择适当的辅助阳极d)少挂零件e)对镀件进行重新处理f)改进挂具绝缘4. 故障现象:镀铬层同镀镍层一起剥皮产生的原因:a)镀前处理不彻底b)镀镍层内应力大纠正方法:a)加强镀前处理b)调整镀镍溶液5. 故障现象:铜锡合金镀层上镀铬时出现黑花产生的原因:a)溶液温度低b)镀铬前处理不彻底c)通电过快或过慢e)铜锡合金中含锡量过高纠正方法:a)升高温度b)加强镀铬前处理c)改进操作e)调整铜锡合金6. 故障现象:镀层剥落产生的原因:a)镀前处理不良b)镀铬过程中途断电c)零件进槽预热时间短d)溶液温度或阴极电流密度变化太大e)硫酸含量过高纠正方法:a)加强镀前处理b)重新镀铬时,进行阳极处理或阴极小电流活化处理c)加长预热时间d)严格控制溶液温度和阴极电流密度e)加碳酸钡处理7. 故障现象:铸铁件镀不上铬层,仅有析氢反应产生的原因:a)镀前浸蚀过度b)进行阳极处理时,造成石墨裸露c)阴极电流密度过低纠正方法:a)重新全加工后再镀b)重新全加工后再镀c)提高阴极电流密度8. 故障现象:镀层粗糙,有铬瘤产生的原因:a)阴极电流密度过大b)阴、阳极间距离太近c)零件形状外凸,没有使用保护阴极d)硫酸根过高纠正方法:a)降低阴极电流密度b)放宽阴、阳极间距离c)使用合适的保护阴极d)加碳酸钡处理9.故障现象:镀层或底层金属上有明显裂纹产生的原因:钢在淬火时有应力纠正方法:镀前将零件回火消除应力。
装饰性镀铬故障处理

装饰性镀铬故障处理1.各种常见故障的产生原因及其处理方法1.1覆盖能力差1.1.1产生原因(1)镀铬中铬酸浓度过低;(2)硫酸根比值过高或过低;(3)镀液中三价铬含量过高;(4)氯离子含量过高;(5)阳极表面有氧化膜电流弱;(6)入槽时电流密度太小;(7)底层表面钝化(镍钝化时)。
1.1.2处理方法(1)分析调整铬酸(标准含量200~250g/L)与硫酸(2~2.5g/L)质量浓度之比。
铬酸的质量浓度过低,就会导致均镀能力差,并出现露黄(镍)等缺陷。
(2)分析确认硫酸根含量高,可以适当增加铬酸的质量浓度或用碳酸钡去除,一般2g/L碳酸钡可除掉1g/L硫酸。
过低时,则补加硫酸至工艺要求。
一般硫酸根比值在(80~125):1范围内。
(3)以大面积阳极和小面积阴极进行电解,将三价铬含量降至工艺要求。
镀液中三价铬含量过高,不仅会影响均镀能力,还会出现雾状和蓝膜现象。
镀液中Cr3+的含量应控制在2~5g/L。
(4)除去氯离子一般采用较经济的电解法。
镀液中氯离子质量浓度超过0.5g/L时,均镀能力、电流效率和镀层的结合力都显著下降,同时铬层出现雾状及发花。
可加入硫酸银、碳酸银、氧化银等,使氯离子与银离子发生反应成氯化银沉淀,但成本较高。
一般多采用电解处理(液温7.°C),氯离子在阳极失去电子生成滤器溢出。
为防止氯离子的积累,配制镀液和补加应使用氯离子的质量浓度一般控制在0.03g/L以下。
(5)取出阳极板将其置于稀盐酸或氢氧化钠溶液中进行清洗,以除去黄色铬酸铅(氧化膜),使其呈活化状态。
(6)增大入槽电流密度。
电流密度及溶液温度对镀液性能(如均镀能力、电流效率等)影响很大。
必须严格控制在工艺范围内。
(7)从镀镍工序着手排除。
镀铬的均镀(覆盖)能力主要取决于溶液的组成和正确的操作,但中间镀层的质量和工艺流程是否合理也会对其有一定的影响。
当镀镍液中杂质含量过高时,在镀件德低电流部位铬沉积困难。
造成镀层不均。
- 1、下载文档前请自行甄别文档内容的完整性,平台不提供额外的编辑、内容补充、找答案等附加服务。
- 2、"仅部分预览"的文档,不可在线预览部分如存在完整性等问题,可反馈申请退款(可完整预览的文档不适用该条件!)。
- 3、如文档侵犯您的权益,请联系客服反馈,我们会尽快为您处理(人工客服工作时间:9:00-18:30)。
2、镀液有悬浮物 2、过滤除去悬浮物
3、除油及清洗不当 3、检查清洗流程
灰色镀层 1、硫酸和或催化剂含量过低 1、补加到合适范围
2、镀液温度高 2、降低温度,检查调温器
微裂纹数少 硫酸或催化剂含量低 调整到合适的范围
9、表面有碳挂灰 9、镀前擦洗表面
镀层烧焦 1、电流密度高 1、降低电流密度或升高温度
2、温度过低 2、升高温度,检查调温器
3、阳极太靠近零件 3、增加阴阳极间距离
2、金属杂质含量高 2、废弃部分镀液,稀释后重新调整
3、漏电流 3、检查杂散电流或短路
4、保护阴极消耗过多电流 4、重新设计阴极保护,清除其上的铬瘤
5、电流密度过低 5、提高电流密度
4、氯离子含量高 4、检查并降低
分散能力差 1、电流密度低 1、提高电流密度,检查接触
2、阳极钝态 2、清洁阳极,用高电流密度重新活化至均匀析出气体,检查阳极接触
沉积速度慢 1、导电杆与夹具接触电阻大 1、清理接触点,降低接触电阻
5、铬酸含量过高 5、取出部分镀液后稀释
6、零件带有磁性 6、退磁
7、镀液有磁性微粒 7、用磁铁吸除
8、除油或清洗不良 8、检查清洗流程及除油溶液
故障现象 可能原因 排除方法
铬从基体上剥落 镀铬除油不良或有污染 确保零件镀前除油、吹砂、清洗等质量
结合力差 1、镀铬前未经浸蚀或浸蚀不足 1、确保零件镀前浸蚀良好,检查浸蚀电流密度及温度
2、零件有污染 2、确保零件前处理清洁
3、电接触间断 3、检查电接触
铬层粗糙有铬瘤 1、硫酸含量过低 1、调整硫酸含量
2、温度低 2、升高温度,检查调温器
3、电流密度高 3、降低电流密度或升高温度
4、表面太粗糙 4、改善表面光洁度