剪毛刀架高度控制器的研制解读
刀架的电器控制原理

刀架的电器控制原理
刀架的电器控制原理可以分为以下几个方面:
1. 开关控制:刀架的电器控制通常通过开关进行,包括启动开关、停止开关和手动控制开关等。
启动开关用于将电流送到电机,使其运转;停止开关用于切断电流,停止电机运转;手动控制开关用于人工控制刀架的运转。
2. 电动机控制:刀架通常使用电动机进行驱动,其控制原理可以通过电动机的接线方式实现。
常见的控制方式有星型连接和三角连接。
在星型连接中,电动机的三根线分别与三相电源的三个相线相连,使电动机工作在星型连接方式下;在三角连接中,电动机的三根线两两相连,使电动机工作在三角连接方式下。
3. 电器保护:为了保护刀架和电动机免受过载、过热等情况的损害,通常会在电路中添加保护装置,如过载保护器、热继电器等。
这些保护装置可以监测电流和温度等参数,并在超过设定范围时切断电流,以防止损坏。
4. 自动控制:刀架的电器控制也可以实现自动化控制。
通过传感器、控制器和执行器等组成的自动控制系统,可以根据预设的条件和程序,实现刀架的自动控制。
例如,可以通过安装位置传感器,实现刀架的自动定位和运动控制。
总体来说,刀架的电器控制原理主要是通过开关控制、电动机控制、电器保护和自动控制等手段,实现对刀架的启停、运转控制和保护。
数控刀架的工作原理
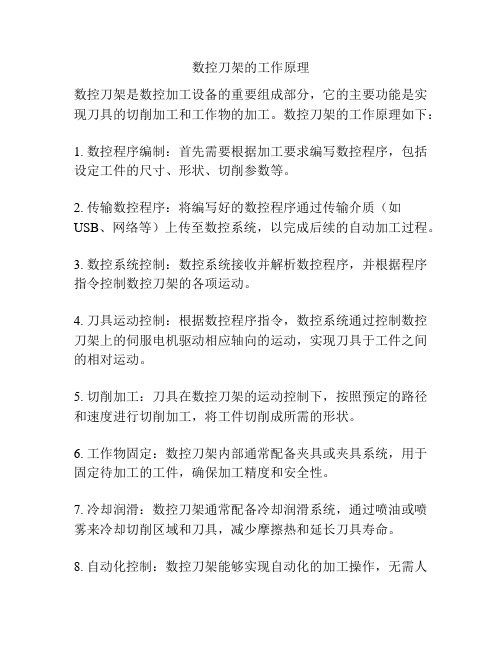
数控刀架的工作原理
数控刀架是数控加工设备的重要组成部分,它的主要功能是实现刀具的切削加工和工作物的加工。
数控刀架的工作原理如下:
1. 数控程序编制:首先需要根据加工要求编写数控程序,包括设定工件的尺寸、形状、切削参数等。
2. 传输数控程序:将编写好的数控程序通过传输介质(如USB、网络等)上传至数控系统,以完成后续的自动加工过程。
3. 数控系统控制:数控系统接收并解析数控程序,并根据程序指令控制数控刀架的各项运动。
4. 刀具运动控制:根据数控程序指令,数控系统通过控制数控刀架上的伺服电机驱动相应轴向的运动,实现刀具于工件之间的相对运动。
5. 切削加工:刀具在数控刀架的运动控制下,按照预定的路径和速度进行切削加工,将工件切削成所需的形状。
6. 工作物固定:数控刀架内部通常配备夹具或夹具系统,用于固定待加工的工件,确保加工精度和安全性。
7. 冷却润滑:数控刀架通常配备冷却润滑系统,通过喷油或喷雾来冷却切削区域和刀具,减少摩擦热和延长刀具寿命。
8. 自动化控制:数控刀架能够实现自动化的加工操作,无需人
工干预,提高加工效率和精度。
通过上述工作原理,在数控刀架的控制下,可以完成各种复杂形状的工件加工,提高生产效率和工件质量。
数控刀架原理

数控刀架原理
数控刀架是数控机床中的一个重要部件,主要用于刀具的安装和固定,可实现自动化的刀具更换和加工过程中的刀具调整。
其原理基于以下几个方面:
1. 结构设计:数控刀架通常由底座、刀臂、刀杆和夹持装置等部件组成。
底座固定在数控机床上,刀臂和刀杆可沿着底座的导轨进行移动,夹持装置用于固定刀具。
2. 控制系统:数控刀架通过连接数控系统实现自动化的刀具更换和调整。
数控系统可根据加工程序的要求,通过控制电机驱动刀架中的刀臂和刀杆进行精确定位,实现刀具的安装和调整。
3. 刀具夹持:刀架中的夹持装置根据不同的刀具类型和尺寸,采用不同的夹持方式。
常见的夹持方式包括机械夹持、液压夹持和气动夹持等。
夹持装置能够提供足够的夹持力,使刀具在加工过程中保持稳定的位置和姿态。
4. 自动换刀功能:数控刀架具备自动换刀功能,即能够根据加工程序的要求,自动选择合适的刀具进行更换。
通过数控系统的控制,刀架可以根据工艺要求选择合适的刀具,并实现自动夹紧和松开刀具。
数控刀架的使用可以大大提高加工效率和精度,减少人工操作的时间和错误。
同时,刀架的自动换刀功能也能够适应多品种、小批量的加工需求,提高生产灵活性和自动化水平。
电动剪刀升降台的设计步骤解读
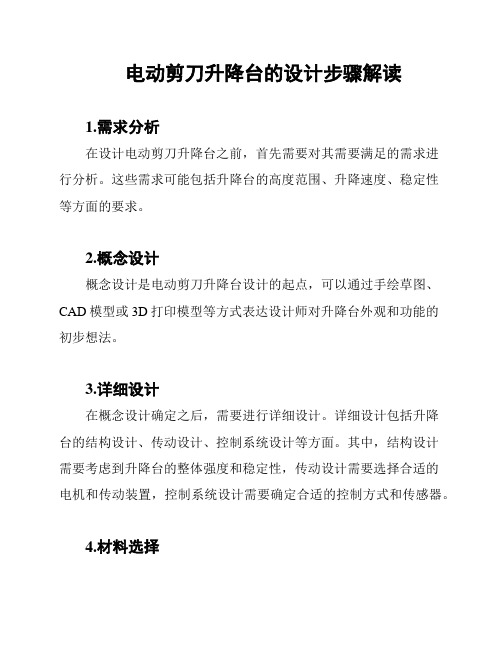
电动剪刀升降台的设计步骤解读1.需求分析在设计电动剪刀升降台之前,首先需要对其需要满足的需求进行分析。
这些需求可能包括升降台的高度范围、升降速度、稳定性等方面的要求。
2.概念设计概念设计是电动剪刀升降台设计的起点,可以通过手绘草图、CAD模型或3D打印模型等方式表达设计师对升降台外观和功能的初步想法。
3.详细设计在概念设计确定之后,需要进行详细设计。
详细设计包括升降台的结构设计、传动设计、控制系统设计等方面。
其中,结构设计需要考虑到升降台的整体强度和稳定性,传动设计需要选择合适的电机和传动装置,控制系统设计需要确定合适的控制方式和传感器。
4.材料选择在详细设计阶段,需要根据具体需求和设计要求选择合适的材料。
这些材料需要具备足够的强度、耐用性和稳定性,以确保电动剪刀升降台的工作正常。
5.制造和装配制造和装配是将设计转化为实际产品的阶段。
在这个阶段,需要考虑到工艺性和实际生产条件,选择合适的制造方法,并进行装配和调试,确保电动剪刀升降台能够正常运行。
6.测试和验证经过制造和装配后,需要对电动剪刀升降台进行测试和验证。
测试可以包括升降台的运行性能、耐久性和安全性等方面的测试。
验证则是根据之前的需求分析,对升降台的设计是否满足需求进行确认。
7.改进和优化在测试和验证的过程中,可能会发现一些不足之处。
根据测试和验证的结果,设计师需要对电动剪刀升降台进行改进和优化,以提升其性能和功能。
8.文档编写最后,根据整个设计过程,编写一份详细的文档。
文档内容应包括需求分析、概念设计、详细设计、材料选择、制造和装配、测试和验证、改进和优化等各个阶段的详细描述和相关数据。
这份文档的目的是记录整个设计过程,为今后的类似设计提供参考。
以上是电动剪刀升降台的设计步骤解读。
通过以上步骤的实施,可以有效地进行设计和开发工作,并确保最终产品的质量。
cnc数控车床的刀架结构控制系统和工作原理说明
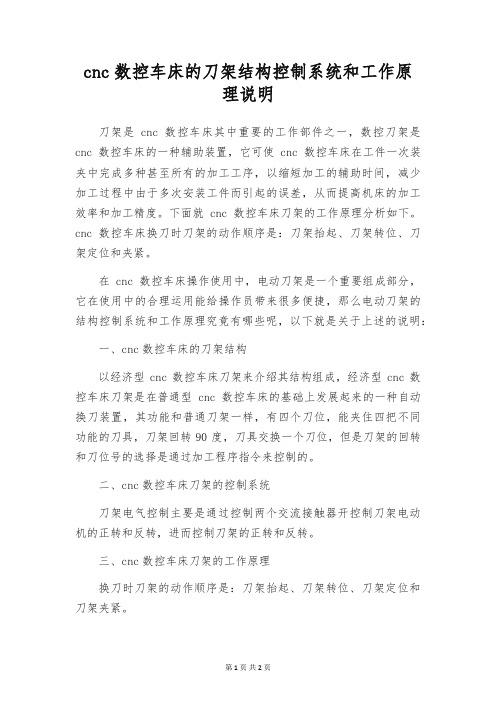
cnc数控车床的刀架结构控制系统和工作原理说明刀架是cnc数控车床其中重要的工作部件之一,数控刀架是cnc数控车床的一种辅助装置,它可使cnc数控车床在工件一次装夹中完成多种甚至所有的加工工序,以缩短加工的辅助时间,减少加工过程中由于多次安装工件而引起的误差,从而提高机床的加工效率和加工精度。
下面就cnc数控车床刀架的工作原理分析如下。
cnc数控车床换刀时刀架的动作顺序是:刀架抬起、刀架转位、刀架定位和夹紧。
在cnc数控车床操作使用中,电动刀架是一个重要组成部分,它在使用中的合理运用能给操作员带来很多便捷,那么电动刀架的结构控制系统和工作原理究竟有哪些呢,以下就是关于上述的说明:一、cnc数控车床的刀架结构以经济型cnc数控车床刀架来介绍其结构组成,经济型cnc数控车床刀架是在普通型cnc数控车床的基础上发展起来的一种自动换刀装置,其功能和普通刀架一样,有四个刀位,能夹住四把不同功能的刀具,刀架回转90度,刀具交换一个刀位,但是刀架的回转和刀位号的选择是通过加工程序指令来控制的。
二、cnc数控车床刀架的控制系统刀架电气控制主要是通过控制两个交流接触器开控制刀架电动机的正转和反转,进而控制刀架的正转和反转。
三、cnc数控车床刀架的工作原理换刀时刀架的动作顺序是:刀架抬起、刀架转位、刀架定位和刀架夹紧。
1、刀架抬起:该刀架可以安装四种不同的刀具,转位信号通过加工程序指令。
数控系统发出换刀指令后,PMC控制输出正转信号,刀架电动机正转控制继电器KA3吸合,刀架电动机正转控制接触器KM3吸合,小型电动机1启动正转,通过平键套筒联轴器2使得蜗杆轴转动,从而带动其他蜗杆轴转动。
2、刀架转位:当端面齿脱开,转位套正好转过160度,涡轮丝杠前端的转位套上的销孔正好对准球头销的位置。
3、刀架定位:刀架体转动带着电刷座转动,当转到程序的刀号,PMC释放正转信号,输出反转信号,刀架电动机反转控制继电器吸合,刀架电动机反转控制接触器进行吸合,刀架电动机反转,定位销在弹簧的作用下进入粗定位盘的槽中进行粗定位。
刀架控制原理说明

右、左侧刀架控制原理1、刀架自动与快速移动龙门刨床有右、左侧刀架,这两个刀架分别由交流电动机MY、MZ拖动,刀架的控制线路能实现刀架的快速移动和自动进给。
刀架的快速移动、自动进给及刀架运动方向,由装在刀架进刀箱上的机械手柄来选择。
刀架的进给机构采用紧张环,依靠紧张环转动角度的大小来控制每次的进刀量。
在每次进刀完成后,利用拖动发架的电动机反向旋转使紧张复位,以便为第二次进刀作好准备。
当需要刀架配合工作台自动往返工作实现自动进刀时,利用机械手柄使位置开关SY (401-403)、SZ(501-503)断开,SY(101-405)、SZ(101-505)闭合。
当工作台按照工作行程前进,刀具离开工件,撞块B碰撞位置开关SY、SZ时,此时:S1H常开触点(405-407)闭合KQY常闭点KHY通电吸合MY反转S1H常开触点(505-507)闭合KQZ常闭点KHZ通电吸合MZ反转带动各自的紧张环复位,为进刀作好准备当作台返回行程末了,台刀程序完成后,使K1Q常开触点(403-405)、(503-505)闭合,接触器KQY、KQZ通电吸合,拖动二个刀架的电动机MY、MZ正转,并带动三个紧张环旋转,完成二个刀架的进刀。
刀架除了上述的自动进刀外,还可以进行刀架快速移动。
这时可利用机械手柄,使相应的位置开关SY(401-403)、SZ(501-503)接通。
按下所要移动刀架的快速移动按钮SB4A 或者SB5A,相应的刀架就实现快速移动。
2、刀架控制线路的联锁机构(1)利用位置开关SY与SZ实现刀架的快速移动与自动进给的联锁。
(2)只有工作台停止自动循环工作时KH的常闭触点(101-345)闭合,刀架才能快速移动。
(3)利用位置开关S4HX与S5HX及SB6A实现与横梁的互锁。
电动剪刀升降装置的设计步骤解读

电动剪刀升降装置的设计步骤解读1.需求分析在设计电动剪刀升降装置之前,首先需要进行需求分析。
明确该装置的使用场景、使用对象以及实现的功能等方面的需求。
2.确定设计参数根据需求分析的结果,确定电动剪刀升降装置的设计参数。
包括承重能力、升降高度范围、速度要求等方面。
3.设计初步方案基于需求和设计参数,进行初步方案设计。
可以通过绘制草图或使用计算机辅助设计软件来完成。
4.材料和零部件选择根据设计方案,选择合适的材料和零部件。
考虑到装置需要承受的重压,选用高强度、耐磨损的材料,并确保零部件的质量可靠。
5.结构设计根据初步方案和已选择的材料,进行装置的结构设计。
确定主要框架、支撑结构、运动部件等的布局和连接方式。
6.动力系统设计设计装置的动力系统,包括电机、减速器和传动装置等。
确保电动剪刀升降装置运行平稳,力度适中,同时满足设计参数的要求。
7.控制系统设计选择合适的控制器和传感器,设计控制系统,实现装置的升降控制。
考虑到人机交互,可以添加按钮或触摸屏等控制装置。
8.安全保护设计考虑装置的安全性,设置适当的安全保护装置,如限位开关、过载保护等,以防止意外事故的发生。
9.试制与测试完成设计后,制作出电动剪刀升降装置的试验样品,并进行测试。
确保装置的各项功能正常运行,并满足设计参数的要求。
10.优化改进根据试制和测试的结果,对电动剪刀升降装置进行优化改进。
通过改变设计参数、调整材料和零部件等,提升装置的性能和可靠性。
11.生产制造完成优化改进后,根据最终设计方案进行生产制造。
确保生产出的电动剪刀升降装置符合设计要求,并达到预期的性能和品质水平。
12.质量控制与检验在生产过程中进行质量控制与检验,确保电动剪刀升降装置的质量符合标准,并进行相应的认证过程。
13.安装与调试根据装置的使用说明书,进行装置的安装和调试。
确保装置能够正常运行,并满足用户的需求。
14.保养与维护在使用过程中,定期进行装置的保养和维护。
清洁装置、润滑零部件、检查电机和控制系统等,以延长装置的使用寿命。
数控刀架的工作原理
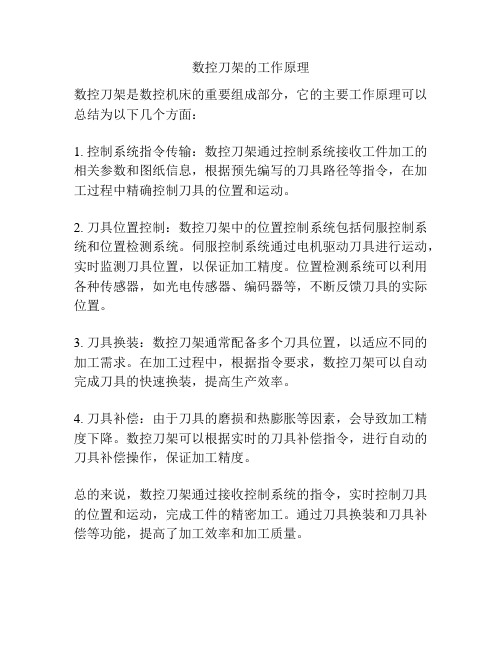
数控刀架的工作原理
数控刀架是数控机床的重要组成部分,它的主要工作原理可以总结为以下几个方面:
1. 控制系统指令传输:数控刀架通过控制系统接收工件加工的相关参数和图纸信息,根据预先编写的刀具路径等指令,在加工过程中精确控制刀具的位置和运动。
2. 刀具位置控制:数控刀架中的位置控制系统包括伺服控制系统和位置检测系统。
伺服控制系统通过电机驱动刀具进行运动,实时监测刀具位置,以保证加工精度。
位置检测系统可以利用各种传感器,如光电传感器、编码器等,不断反馈刀具的实际位置。
3. 刀具换装:数控刀架通常配备多个刀具位置,以适应不同的加工需求。
在加工过程中,根据指令要求,数控刀架可以自动完成刀具的快速换装,提高生产效率。
4. 刀具补偿:由于刀具的磨损和热膨胀等因素,会导致加工精度下降。
数控刀架可以根据实时的刀具补偿指令,进行自动的刀具补偿操作,保证加工精度。
总的来说,数控刀架通过接收控制系统的指令,实时控制刀具的位置和运动,完成工件的精密加工。
通过刀具换装和刀具补偿等功能,提高了加工效率和加工质量。
- 1、下载文档前请自行甄别文档内容的完整性,平台不提供额外的编辑、内容补充、找答案等附加服务。
- 2、"仅部分预览"的文档,不可在线预览部分如存在完整性等问题,可反馈申请退款(可完整预览的文档不适用该条件!)。
- 3、如文档侵犯您的权益,请联系客服反馈,我们会尽快为您处理(人工客服工作时间:9:00-18:30)。
剪毛刀架高度控制器的研制
概述
人造毛皮后整理联合烫剪机中剪毛刀架的定位调节,原是人工用按钮控制异步电动机正、反转,通过机械减速器(齿轮装置)后带动剪毛刀架蜗杆,使剪毛刀架做上、下运动至要求的位置。
操作烦琐,需反复测量、调整,很难恰好到位,误差大。
为此,我们用AT89C51单片机构成剪毛高度控制器,对剪毛刀架高度进行自动控制。
使用该控制器,只需由触摸开关设定工艺要求的剪毛高度(毫米数),控制器则发出相应的控制信号使剪毛刀架达到希望的高度,并可由工艺人员设置相对的机械零位。
对运行状态和参数设置进行数码显示,相应地还有剪毛刀架高度减少及增大指示,控制趋势一目了然。
一.硬件设计
根据用户要求,为不增加成本,驱动电动机仍保持原异步电动机,原机械减速器及剪毛刀架蜗杆等均不改变。
这也便于老产品改造。
系统硬件框图如图1所示。
(1)单片机控制系统
采用ATMEL公司的AT89C51作为控制器,其性价比
高。
片内含4KB闪速可编程/擦除只读存储器,128字节
RAM,32个I/O线,2个16位定时器/计数器,5个两级
中断源结构,满足系统要求。
(2)掉电保护
如脉冲状态数累计值、当前的状态等输入参数是需要掉电保护的,本系统中采用Xicor公司生产的X24C45。
它是串行256位NVRAM,按16×16组织,包括一个256位的SRAM和一个256位的EEPROM,并且RAM和EEPROM阵列位对位重叠,上电时数据可自动从EEPROM调到SRAM
中。
X24C45还具有自动存储特性,即
系统正常工作时,数据放在SRAM中,
掉电时数据自动保存到EEPROM中。
本
系统中X24C45、X5045与AT89C51的
接口如图2所示。
(3)参数设定及看门狗电路
刀架相对于机械零位的高度、产
品类型等参数可由用户设定,采用串
行EEPROM X5045存放用户参数。
它是
美国Xicor公司的产品,将三种功
能:看门狗定时器、EEPROM和电压监
控组合在单个芯片之内。
X5045是高电
平复位信号输出,正好满足本系统中
CPU(AT89C51)复位信号的要求;管
脚数仅与一片MAX706或X24C04管脚
数相同,简化了电路设计,降低了控
制器成本。
其与AT89C51接口如图2
所示。
(4)触摸开关
三位触摸开关为状态、增加、减小开关。
组合用于选择产品类型(对于不同的蜗杆,如有的产品类型为:蜗杆转过20转,剪毛刀架升或降1mm;有的产品类型为:蜗杆转过40转,剪毛刀架升或降1mm;等等);用于设置要求的刀架高度,其范围为0~99mm;用于将当前的刀架高度确定为工作刀架高度的机械零位;用于启动工作。
(5)数码显示
数码显示在控制器运行状态时,动态显示实际的剪毛刀架高度;在控制器参数设置状态时,显示用户设置的刀架高度给定值、产品类型等参数,以便用户设置、修改参数。
通过测量刀架蜗杆转过的角度来间接测量剪毛刀架高度(如一种典型产品类型为:蜗杆转过20转,剪毛刀架升或降1mm)。
在刀架蜗杆上安装一半圆凸轮,同时相对垂直地安装一对霍耳传感器a、b。
当凸轮金属部分接近霍耳传感器时,传感器输出为“1”;当凸轮金属部分远
离传感器时,其输出为“0”。
由于
a、b正交,所以不仅可测量蜗杆转
过的转数,还可以判断电动机目前
是正转还是反转。
刀架蜗杆逆时针
转一圈,凸轮与a、b霍耳传感器相
对位置、ab输出逻辑表、波形如图
3所示;顺时针时情况如图4所
示。
a、b霍耳传感器输出通过光电
耦合器送至单片机。
二.软件设计
由前图3、图4可见逆时针
时,a、b逻辑表顺序为3,2,0,
1,...,顺时针时顺序为3,1,0,2,...。
因此在存储器中,设置一表格。
将本次读入的a、b状态及上次读入的a、b状态与表格相比较,即可判断出当前电动机的转向;从波形图还可以看出,a、b状态改变一次对应蜗杆转过90°(即1/4周),由此及产品类型号即可换算出脉冲状态数与剪毛刀架实际高度之间的比例系数。
因为驱动电机为异步电动机,所以在控制中设置了一误差带,避免系统产生振荡。
实际调试,当实际状态数与给定状态数之差为4时最佳。
运行证明,完全满足用户要求。
刀架高度上、下变动40次,积累误差小于0.5mm。
系统主要运行程序框图如图5所示。
三.结语
该控制器结构简单,成本低,抗干扰能力强,可靠性高,尤其可方便地用于老产品改造,有一定的推广价值。