Ch0901kla
可堪培拉公司产品说明书

CANBERRA CORPORATIONSAFETY DATA SHEET1. IdentificationProduct Identifier: HUSKY 1230 DISINFECTANT DEODORANTApplication or recommended use: Hard surface disinfectantRestrictions on use: Do not use in any fashion not specified on the product label.Manufacturer / supplier: Canberra Corporation3610 N. Holland-Sylvania Rd.Toledo, Ohio 43615 USATelephone: 419-841-6616Emergency phone: 866-836-88552. Hazards IdentificationGHS Classification: Classification of this mixture in accordance with paragraph (d) of §1910.1200.Flammable Aerosols - Category 1Eye Damage/Irritation - Category 2ALabel Elements:Symbol:Signal word: DANGERHazard statements: Extremely flammable aerosol. Causes serious eye irritation.Precautionary statements: Keep away from heat/sparks/open flames/hot surfaces. - No smoking. Do not spray on an openflame or other ignition source. Pressurized container: Do not pierce or burn, even after use.Wash thoroughly after handling. Wear eye/face protection.IF IN EYES: Rinse cautiously with water for several minutes. Remove contact lenses, if presentand easy to do. Continue rinsing. If eye irritation persists, get medical advice/attention.See 4. First-Aid Measures for specific treatment.Store locked up. Protect from sunlight. Do not expose to temperatures exceeding 50°C/122°F.Dispose of contents/container to an approved disposal facility.Other Hazards: None known.3. Composition / Information on IngredientsChemical characterization: Mixture of water, emulsifiers, solvents and auxiliary agents.Hazardous ingredients: The exact percentage of composition has been withheld as a trade secret.40 - 60% Ethyl Alcohol CAS 64-17-510 - 20% Butane CAS 106-97-82 - 10% Propane CAS 74-98-60.1 – 1% o-Phenylphenol CAS 90-43-74. First-aid measuresInhalation: Move to fresh air. Call a physician if symptoms develop or persist.Skin contact: Wash with plenty of soap and water. Get medical attention if irritation develops and persists.Eye contact: Immediately flush eyes with plenty of water for at least 15 minutes. Remove contact lenses, if present and easy to do. Continue rinsing. If eye irritation persists: Get medical advice/attention.Ingestion: In the unlikely event of swallowing contact a physician or poison control center. Rinse mouth thoroughly.Most important symptoms/effects, acute and delayed: Headache. Irritation of nose and throat. Severe eye irritation. Symptoms may include stinging, tearing, redness, swelling, and blurred vision. Coughing. Skin irritation.Indication of immediate medical attention and special treatment needed: Provide general supportive measures and treat symptomatically. Keep victim under observation. Symptoms may be delayed.5. Fire-fighting measuresSuitable extinguishing media: Alcohol resistant foam. Water spray. Water fog. Dry chemical. Carbon dioxide (CO2). Unsuitable extinguishing media: Do not use water jet as an extinguisher, as this will spread the fire.Specific hazards arising from the chemical: Contents under pressure. Pressurized container may explode when exposed to heat or flame. During fire, gases hazardous to health may be formed.Special protective equipment and precautions for firefighters: Self-contained breathing apparatus and full protective clothing must be worn in case of fire.Fire-fighting equipment/instructions: Move containers from fire area if you can do so without risk. Cool containers exposed to heat with water spray and remove container, if no risk is involved. Containers should be cooled with water to prevent vapor pressure build up.General fire hazards: Extremely flammable aerosol.6. Accidental release measuresPersonal precautions, protective equipment and emergency procedures: Keep unnecessary personnel away. Keep people away from and upwind of spill/leak. Keep out of low areas. Eliminate all ignition sources (no smoking, flares, sparks, or flames in immediate area). Wear appropriate protective equipment and clothing during clean-up. Do not touch damaged containers or spilled material unless wearing appropriate protective clothing. Ventilate closed spaces before entering them. Local authorities should be advised if significant spillages cannot be contained.Methods and materials for containment and cleaning up: Eliminate all ignition sources (no smoking, flares, sparks, or flames in immediate area). Keep combustibles (wood, paper, oil, etc.) away from spilled material. Stop leak if you can do so without risk. Move the cylinder to a safe and open area if the leak is irreparable. Cover with plastic sheet to prevent spreading. Absorb in vermiculite, dry sand or earth and place into containers. Scoop up used absorbent into drums or other appropriate container. Prevent entry into waterways, sewer, basements or confined areas. Following product recovery, flush area with water. Small Spills: Wipe up with absorbent material. Clean surface thoroughly to remove residual contamination. Environmental precautions: Avoid release to the environment. Avoid discharge into drains, water courses or onto the ground.7. Handling and storagePrecautions for safe handling: Pressurized container: Do not pierce or burn, even after use. Do not use if spray button is missing or defective. Do not spray on a naked flame or any other incandescent material. Do not smoke while using or until sprayed surface is thoroughly dry. Do not cut, weld, solder, drill, grind, or expose containers to heat, flame, sparks, or other sources of ignition. All equipment used when handling the product must be grounded. Do not handle or store near an open flame, heat or other sources of ignition. Avoid contact with eyes. Use only in well-ventilated areas. Wear appropriate personal protective equipment. Avoid release to the environment. Observe good industrial hygiene practices.Conditions for safe storage, including any incompatibilities: Level 2 Aerosol.Pressurized container. Protect from sunlight and do not expose to temperatures exceeding 50°C/122 °F. Do not puncture, incinerate or crush. This material can accumulate static charge which may cause spark and become an ignition source. Do not handle or store near an open flame, heat or other sources of ignition. Store in original tightly closed container. Store away from incompatible materials.8. Exposure controls/personal protectionOccupational exposure limitsUS. OSHA Table Z-1 Limits for Air Contaminants (29 CFR 1910.1000)Components Type ValueEthyl Alcohol (CAS 64-17-5) PEL 1900 mg/m3 (1000 ppm)Propane (CAS 74-98-6) PEL 1800 mg/m3 (1000 ppm)US. ACGIH Threshold Limit ValuesComponents Type ValueButane (CAS 106-97-8) STEL 1000 ppmEthyl Alcohol (CAS 64-17-5) STEL 1000 ppmUS. NIOSH: Pocket Guide to Chemical HazardsComponents Type ValueButane (CAS 106-97-8) TWA 1900 mg/m3 (800 ppm)Ethyl Alcohol (CAS 64-17-5) TWA 1900 mg/m3 (1000 ppm)Propane (CAS 74-98-6) TWA 1800 mg/m3 (1000 ppm)Appropriate engineering controls: Good general ventilation should be used. Ventilation rates should be matched to conditions. If applicable, use process enclosures, local exhaust ventilation, or other engineering controls to maintain airborne levels below recommended exposure limits. If exposure limits have not been established, maintain airborne levels to an acceptable level. Provide eyewash station.Individual protection measures, such as personal protective equipment:Eye/face protection: Wear safety glasses with side shields (or goggles).Hand protection: Wear appropriate chemical resistant gloves.Other: Wear suitable protective clothing.Respiratory protection: If permissible levels are exceeded use organic vapor cartridge or an air-supplied respirator.General hygiene considerations: When using do not smoke. Always observe good personal hygiene measures, such as washing after handling the material and before eating, drinking, and/or smoking. Routinely wash work clothing and protective equipment to remove contaminants.9. Physical and chemical propertiesAppearancePhysical state: Gas. Form: Aerosol.Color: Not available. Odor: Not available.Odor threshold: Not available. pH: Not available.Melting point/freezing point: Not available. Flash point: -156.0 °F (-104.4 °C) Propellant estimated.Evaporation rate: Not available. Initial boiling point/boiling range: 140.71 °F (60.39 °C) estimated. Flammability: Not available. Auto-ignition temperature: 856.4 °F (458 °C) estimated.Upper/lower flammability or explosive limitsFlammability limit – lower (%): 2.6 % estimated. Flammability limit – upper (%): 12.8 % estimated.Explosive limit - lower (%): Not available. Explosive limit - upper (%): Not available.Vapor pressure: 75 - 85 psig @70F estimated. Vapor density: Not available.Relative density: Not available. Specific gravity: 0.79 estimated.Solubility (water): Not available. Viscosity: Not available.Decomposition temperature: Not available.Partition coefficient (n-octanol/water): Not available.10. Stability and reactivityReactivity: The product is stable and non-reactive under normal conditions of use, storage and transport.Chemical stability: Material is stable under normal conditions.Possibility of hazardous reactions: Hazardous polymerization does not occur.Conditions to avoid: Avoid temperatures exceeding the flash point. Contact with incompatible materials.Incompatible materials: Strong oxidizing agents. Nitrates. Fluorine. Chlorine.Hazardous decomposition products: No hazardous decomposition products are known.11. Toxicological informationInformation on likely routes of exposure:Ingestion: Expected to be a low ingestion hazard.Inhalation: No adverse effects due to inhalation are expected.Skin contact: No adverse effects due to skin contact are expected.Eye contact: Causes serious eye irritation.Symptoms related to the physical, chemical and toxicological characteristics: Headache. Irritation of nose and throat. Severe eye irritation. Symptoms may include stinging, tearing, redness, swelling, and blurred vision. Coughing. Skin irritation. Information on toxicological effects:Acute toxicity: Expected to be a low hazard for usual industrial or commercial handling by trained personnel.Skin corrosion/irritation: Prolonged skin contact may cause temporary irritation.Serious eye damage/eye irritation: Causes serious eye irritation.Respiratory sensitization: Not available. Skin sensitization: This product is not expected to cause skin sensitization. Carcinogenicity: This product is not considered to be a carcinogen by IARC, ACGIH, NTP, or OSHA.IARC Monographs. Overall Evaluation of Carcinogenicity: o-Phenylphenol (CAS 90-43-7) 3 Not classifiable as to carcinogenicity to humans.OSHA Specifically Regulated Substances (29 CFR 1910.1001-1050): Not listed.Reproductive toxicity: This product is not expected to cause reproductive or developmental effects.Specific target organ toxicity - single exposure: Not classified.Specific target organ toxicity - repeated exposure: Not classified.Aspiration hazard: Not available.Chronic effects: Prolonged or repeated contact may cause drying, cracking, or irritation.12. Ecological informationEcotoxicity: Harmful to aquatic life with long lasting effects.Persistence and degradability: No data is available on the degradability of this product.Bioaccumulative potential: No data available.Partition coefficient n-octanol / water (log Kow): Butane 2.89, Ethyl Alcohol -0.31, o-Phenylphenol 3.09, Propane 2.36 Mobility in soil: No data available.Other adverse effects: No other adverse environmental effects (e.g. ozone depletion, photochemical ozone creation potential, endocrine disruption, global warming potential) are expected from this component.13. Disposal considerationsDisposal instructions Collect and reclaim or dispose in sealed containers at licensed waste disposal site. Contents under pressure. Do not puncture, incinerate or crush. Do not allow this material to drain into sewers/water supplies. Do not contaminate ponds, waterways or ditches with chemical or used container. Dispose of contents/container in accordance with local/regional/national/international regulations.Waste from residues / unused products: Dispose of in accordance with local regulations. Empty containers or liners mayretain some product residues. This material and its container must be disposed of in a safe manner.Contaminated packaging: Empty containers should be taken to an approved waste site for recycling or disposal. Emptiedcontainers may retain product residue, follow label warnings even after container is emptied.14. Transport informationDOT UN number UN1950 UN proper shipping name Aerosols, flammable Class 2.1Packing group: Not applicable.Read safety instructions, SDS and emergency procedures before handling.Packaging exceptions: This product meets the exception requirements of section 173.306 as a limited quantity andmay be shipped as a limited quantity.15. Regulatory informationUS federal regulationsFIFRA: This product is a U.S. EPA Registered pesticide, EPA Reg. No. 706-69-8155, and is subject to certain labelingrequirements under Federal pesticide law. These requirements differ from the classification criteria and hazard informationrequired for safety data sheets (SDS), and for workplace labels of non-pesticide products.This product is a "Hazardous Chemical" as defined by the OSHA Hazard Communication Standard, 29 CFR 1910.1200.All components are on the U.S. EPA TSCA Inventory List.TSCA Section 12(b) Export Notification (40 CFR 707, Subpt. D): Not regulated.CERCLA Hazardous Substance List (40 CFR 302.4): Sodium Nitrite (CAS 7632-00-0) Listed.SARA 304 Emergency release notification: Not regulated.OSHA Specifically Regulated Substances (29 CFR 1910.1001-1050): Not listed.Superfund Amendments and Reauthorization Act of 1986 (SARA):Hazard categoriesImmediate Hazard – Yes Delayed Hazard – NoFire Hazard – Yes Pressure Hazard – NoReactivity Hazard – NoSARA 302 Extremely hazardous substance: NoSARA 311/312 Hazardous chemical: NoSARA 313 (TRI reporting)Chemical name CAS number % by wt.o-Phenylphenol 90-43-7 0.1 - 1Other federal regulationsClean Air Act (CAA) Section 112 Hazardous Air Pollutants (HAPs) List: Not regulated.Clean Air Act (CAA) Section 112(r) Accidental Release Prevention (40 CFR 68.130):Butane (CAS 106-97-8) Propane (CAS 74-98-6)Safe Drinking Water Act: (SDWA): Not regulated.US state regulationsUS. Massachusetts RTK - Substance ListUS. New Jersey Worker and Community Right-to-Know ActUS. Pennsylvania Worker and Community Right-to-Know LawButane (CAS 106-97-8) Ethyl Alcohol (CAS 64-17-5) o-Phenylphenol (CAS 90-43-7) Propane (CAS 74-98-6)US. Rhode Island RTKButane (CAS 106-97-8) o-Phenylphenol (CAS 90-43-7) Propane (CAS 74-98-6)US. California Proposition 65: WARNING: This product contains a chemical known to the State of California to causecancer. o-Phenylphenol (CAS 90-43-7) Listed: August 4, 200016. Other information, including date of preparation or last revisionDate issued: 01. 02. 2015 HSK-1230 Revision: N/ADisclaimer The information provided in this Safety Data Sheet is correct to the best of our knowledge, information and beliefat the date of its publication. The information given is designed only as a guidance for safe handling, use, processing, storage, transportation, disposal and release and is not to be considered a warranty or quality specification. The information relates onlyto the specific material designated and may not be valid for such material used in combination with any other materials or inany process, unless specified in the text. We cannot anticipate all conditions under which this information and its product, orthe products of other manufacturers in combination with its product, may be used. It is th conditions for handling, storage and disposal of the product, and to assume liability for loss, injury, damage or expense due toimproper use. The information in the sheet was written based on the best knowledge and experience currently available.。
韩国LG化学有限公司LG电池 INR18650 M26 可重复使用锂离子电池说明书

PRODUCT SPECIFICATIONCONFIDENTIALPrepared Document No. Date Rev LGC MBD / MBDC Lee, Kwan Hee LRB-PS-CY2600-M26 2015-04-28 0Approved Checked DescriptionLGC MBD / MBDC Kim, Dong Myung Lithium Ion INR18650 M26PRODUCT SPECIFICATIONRechargeable Lithium Ion BatteryModel : INR18650 M2620 YOIDO-DONG YOUNGDUNGPO-GU,SEOUL 150-721, KOREAContentsRevision History (2)Contents (3)1. General Information (4)1.1 Scope1.2 Application1.3 Product Classification1.4 Model Name2. Nominal Specification (4)2.1 Capacity2.2 Nominal Voltage2.3 Standard Charge2.4 Max. Charge Voltage2.5 Max. Charge Current2.6 Standard Discharge2.7 Max. Discharge Current2.8 Max. Temperature Limit2.9 Weight2.10 Operating Temperature2.11 Storage Temperature (for shipping state)3. Appearance and Dimension (5)3.1 Appearance3.2 Dimension4. Performance Specification (5)4.1 Standard Test Condition4.2 Electrical Specification4.3 Environmental Specification4.4 Mechanical Specification4.5 Safety Specification5. Caution and Prohibition in Handling (8)5.1 Cautions for Use and Handling5.2 Prohibitions5.3 Caution for the battery and the pack6. Exclusion of Liability (10)1. General Information1.1 ScopeThis product specification defines the requirements of the rechargeable lithium ion battery to be supplied to the customer by LG Chem.1.2 Application: Light Electric Vehicle1.3 Product classification: Cylindrical rechargeable lithium ion battery1.4 Model name: INR18650 M263. Appearance and Dimension3.1 AppearanceThere shall be no such defects as deep scratch, crack, rust, discoloration or leakage, which may adversely affect the commercial value of the cell.3.2 DimensionDiameter : Max. 18.4 mmDiameter is defined as the largest data value measured on the “A” area of a cylindrical cell.Height : 65.0 ± 0.2 mm ( Max. 65.2 mm )4. Performance Specification4.1 Standard test condition4.1.1 Standard ChargeUnless otherwise specified, “Standard Charge” shall consist of charging at constant current of 1,250mA.The cell shall then be charged at constant voltage of 4.2V while tapering the charge current. Charging shall be terminated when the charging current has tapered to 50mA. For test purposes, charging shall be performed at 25ºC ± 2ºC.4.1.2 Standard Discharge“Standard Discharge” shall consist of discharging at a constant current of 500mA to 2.75V. Discharging is to be performed at 25 ºC ± 2 ºC unless otherwise noted (such as capacity versus temperature).4.1.3 Fast Charge / discharge conditionCells shall be charged at constant current of 1,250mA to 4.2V with end current of 125mA. Cells shall be discharged at constant current of 2,500mA to 3.0V. Cells are to rest 30 minutes after charge and 30minutes after discharge.A4.2 Electrical Specification4.3 Environmental specification.* Remaining Capacity : After storage, cells shall be discharged with Std. condition(4.1.2) to measure the remaining capacity.** Recovery Capacity : After storage, cells shall be discharged with fast discharge condition(4.1.3), and then cells shall be charged with std. charge condition(4.1.1), and then discharged with Std. condition(4.1.2). This charge / discharge cycle shall be repeated three times to measure the recovery capacity.4.4 Mechanical Specification4.5 Safety Specification5. Caution and Prohibition in HandlingWarning for using the lithium ion rechargeable battery. Mishandling of the battery may cause heat, fire and deterioration in performance. Be sure to observe the following.5.1 Cautions for Use and Handling•When using the application equipped with the battery, refer to the user’s manual before usage.•Please read the specific charger manual before charging.•Charge time should not be longer than specified in the manual.•When the cell is not charged after long exposure to the charger, discontinue charging.•Battery must be charged at operating temperature range 0 ~ 45℃.•Battery must be discharged at operating temperature range -20 ~ 60℃.•Please check the positive(+) and negative(-) direction before packing.•When a lead plate or wire is connected to the cell for packing, check out insulation not to short-circuit.•Battery must be stored separately.•Battery must be stored in a dry area with low temperature for long-term storage.•Do not place the battery in direct sunlight or heat.•Do not use the battery in high static energy environment where the protection device can be damaged.•When rust or smell is detected on first use, please return the product to the seller immediately.•The battery must be away from children or pets•When cell life span shortens after long usage, please exchange to new cells.5.2 Prohibitions•Do not use different charger. Do not use cigarette jacks (in cars) for charging.•Do not charge with constant current more than maximum charge current.•Do not disassemble or reconstruct the battery.•Do not throw or cause impact.•Do not pierce a hole in the battery with sharp things. (such as nail, knife, pencil, drill)•Do not use with other batteries or cells.•Do not solder on battery directly.•Do not press the battery with overload in manufacturing process, especially ultrasonic welding.•Do not use old and new cells together for packing.•Do not expose the battery to high heat. (such as fire)•Do not put the battery into a microwave or high pressure container.•Do not use the battery reversed.•Do not connect positive(+) and negative(-) with conductive materials (such as metal, wire)•Do not allow the battery to be immerged in or wetted with water or sea-water.5.3 Caution for the battery and the packPack shall meet under condition to maintain battery safety and last long performance of the lithium rechargeable cells.5.3.1 Installing the battery into the pack-. The cell should be inspected visually before battery assembly into the pack.-. Damaged cell should not be used. (damaged surface, can-distortion, electrolyte-smell)-. Different Lot Number cells should not be packaged into the same pack.-. Different types of cells, or same types but different cell mak er’s should not be used together.5.3.2 Design of battery pack-. The battery pack should not be connected easily to any charger other than the dedicated charger.-. The battery pack has funcion not to cause external short cut easily.-. The design of battery pack and structure should be reviewed physically, mechanically and electricallynot to cause cell imbalance.-. The battery pack for multiple cells should be designed to monitor the voltage of each bank5.3.3 Charge-. Charging method is Constant Current-Constant Voltage (CC/CV).-. Charging should be operating under maximum charge voltage and current which is specified in theproduct specification. (Article. 2.4, 2.5)-. The battery should be charged under operating temperature specified in the product specification.(Article. 2.9)5.3.4 Discharge-. Discharging method is Constant Current (CC).(In case of using the battery for mobile equipment, discharging mode could be Constant Power.) -. Discharging should be operating under maximum discharge current which is specified in the productspecification. (Article. 2.7)-. Discharging should be done by cut off voltage which is specified in the product specification.(Article. 2.6)-. The battery should be discharged under operating temperature specified in the product specification.(Article. 2.9)5.3.5 Protection Circuit-. The protection circuit should be installed in the battery pack, charger.-. Charger or pack should have voltage sensing system to control over charge or discharge in order tomaintain the battery’s normal operating mode and protect cell imbalance.-. Charger or pack should have warning system for over temperature, over voltage and over current.6. Exclusion of LiabilityThe warranty shall no cover defects caused by normal wear and tear, inadequate maintenance, handling, storage faulty repair, modification to the battery or pack by a third party other than LGC ore LGC’s agent approved by LGC, failure to observe the product specification provided herein or improper use or installation, include but not limited to the following :-. Damage during transport or storage-. Incorrect installation of battery into pack or maintenance-. Use of battery or pack in inappropriate environment-. Improper, inadequate, or incorrect charge, discharge or production circuitOther than stipulated herein-. Incorrect use or inappropriate use-. Insufficient ventilation-. Ignoring applicable safety warning and instructions-. Altering or attempted repairs by unauthorized personnel-. In case of force majeure (Ex. Lightening, storm, flood, fire, earthquake, etc)There are no warranties-implied or express-other than those stipulated herein LG Chem. Shall not be liable forany consequential or indirect damage arising or in connection with the product specification, battery or pack.。
国家工程实验室621系列数据采集设备说明书

Manufacturer: National InstrumentsBoard Assembly Part Numbers (Refer to Procedure 1 for identification procedure): Part Number and Revision Description194710A-04 or later USB-6210194710A-03 or later USB-6211196203A-03L or later USB-6211 OEM197493A-03L or later USB-6212198402A-03L or later USB-6212 MASS TERMINATION190630A-01L or later USB-6212 BNC197504A-03L or later USB-6212 OEM194710A-02 or later USB-6215197493A-01L or later USB-6216198402A-01L or later USB-6216 MASS TERMINATION190631A-01L or later USB-6216 BNC197504A-01L or later USB-6216 OEM194710A-01 or later USB-6218190632A-01L or later USB-6218 BNC196203A-01L or later USB-6218 OEMVolatile MemoryTarget Data Type Size BatteryBackupUser1AccessibleSystemAccessibleSanitizationProcedureGlue logic FPGA 1 AlteraEP1C3No No Yes Cycle PowerGlue logic FPGA 2 XilinxXC3S500ENo No Yes Cycle Power Program Code SRAM 128 KB No No Yes Cycle Power Non-Volatile Memory (incl. Media Storage)Target Data Type Size BatteryBackupUserAccessibleSystemAccessibleSanitizationProcedureDevice configuration •Device information •Calibration metadata2•Calibration data EEPROM 2 KB NoNoYesNoYesYesYesNoneProcedure 2None1 Refer to Terms and Definitions section for clarification of User and System Accessible2 Calibration constants that are stored on the device include information for the device’s full operating range. Any implications resulting from partial self-calibration can be eliminated by running the full self-calibration procedure.ProceduresProcedure 1 –Board Assembly Part Number Identification:To determine the Board Assembly Part Number and Revision, refer to the “P/N” label applied to the surface of your product as shown below. The Assembly Part Number should be formatted as “P/N: ######a-vvL” where “a” is the letter revision of the Board Assembly (eg. A, B, C…) and the “vv” is the type identifier. If the product is RoHS compliant, “L” can be found at the end of the part number.USB-6210/6211/6212/6215/6216/6218/6212 MASS TERMINATION/6216 MASS TERMINATION – Label can be found on the bottom of the enclosure.USB-6211 OEM/6218 OEM – Primary SideUSB-6212 OEM/6216 OEM – Secondary SideUSB-6212 BNC/6216 BNC/6218 BNC – Label can be found on the bottom of the enclosure.Procedure 2 – Device Configuration EEPROM (Calibration Metadata):The user-accessible areas of the Device Configuration EEPROM are exposed through a calibration Applications Programming Interface (API) in LabVIEW. To clear the Calibration Metadata area, complete the following steps:1.To clear the calibration password, use the DAQmx Change External Calibration Password.vi tooverwrite the current password of the device you wish to clear.2.The user-accessible area of the Device Configuration EEPROM can be cleared using the NI DAQmx API.For instructions on how to clear these areas, go to /info and enter info code DAQmxLOV.Terms and DefinitionsCycle Power:The process of completely removing power from the device and its components and allowing for adequate discharge. This process includes a complete shutdown of the PC and/or chassis containing the device; a reboot is not sufficient for the completion of this process.Volatile Memory:Requires power to maintain the stored information. When power is removed from this memory, its contents are lost. This type of memory typically contains application specific data such as capture waveforms.Non-Volatile Memory:Power is not required to maintain the stored information. Device retains its contents when power is removed.This type of memory typically contains information necessary to boot, configure, or calibrate the product or may include device power up states.User Accessible:The component is read and/or write addressable such that a user can store arbitrary information to the component from the host using a publicly distributed NI tool, such as a Driver API, the System Configuration API, or MAX. System Accessible:The component is read and/or write addressable from the host without the need to physically alter the product. Clearing:Per NIST Special Publication 800-88 Revision 1, “clearing” is a logical technique to sanitize data in all User Accessible storage locations for protection against simple non-invasive data recovery techniques using the same interface available to the user; typically applied through the standard read and write commands to the storage device.Sanitization:Per NIST Special Publication 800-88 Revision 1, “sanitization” is a process to render access to “Target Data” on the media infeasible for a given level of effort. In this document, clearing is the degree of sanitization described.。
Bosch DWK系列抽取机用户手册说明书

Serie 2, Forno da incasso, 60 x 60cm, AcciaioHBA171BS1Accessori integrati1 x Griglia combinata, 1 x Leccarda universale smaltataAccessori opzionaliHEZ317000 Teglia per pizza, HEZ327000 Pietra per pane e pizza, HEZ333001 Coperchio per leccarda extra profonda, HEZ530000 2 leccarde slim 455x188x39 mm (LxPxA), HEZ531000 Leccarda bassa 455x375x30 mm (LxPxA), HEZ531010 Leccarda antiaderen455x375x30mm (LxPxA), HEZ532000 Leccarda profonda 455x375x38 mm (LxPxA), HEZ532010 Leccarda antiaderen 455x400x38mm (LxPxA), HEZ533000 Leccarda profonda 455x375x81 mm (LxPxA), HEZ538000 Guide telescopiche clip a 1 livello, HEZ629070 Teglia per grigliare adatta a pirolisi, HEZ633001 Coperchio per tegame professionale, HEZ633070 Tegame professionale, HEZ634000 Griglia combinata 455x375x31 mm (LxPxA), HEZ636000 Leccarda in vetro 455x364x30 mm (LxPxA), HEZ660050 Accessory, HEZ664000 Griglia combinata 455x375x59 mm (LxPxA), HEZ915003 Pirofila in vetro con coperchio 5,4 l., HEZG0AS00 Cavo di collegamento 3m • Programmi automatici di cottura: cucinare sarà semplicissimo grazie ai programmi con impostazioni già preselezionate.• Autopulizia pirolitica: pulizia del forno senza sforzo• Aria Calda 3D: distribuisce uniformemente il calore fino a tre ilivelli per risultati sempre perfetti.Dati tecniciTipologia costruttiva del prodotto: .....................................Da incasso Sistema di pulizia: .......................................................Pirolisi+Idrolisi Dimensioni del vano per l'installazione (AxLxP): 585-595 x 560-568 x 550 mmDimensioni (AxLxP): ............................................595 x 594 x 548 mm Dimensioni del prodotto imballato (AxLxP): .......675 x 660 x 690 mm Materiale del cruscotto: ...................................................acciaio inox Materiale porta: ..........................................................................vetro Peso netto: ..............................................................................37.4 kg Volume utile: .................................................................................71 l Metodo di cottura: .Grill a superficie grande, Aria calda delicata, aria calda, Riscaldamento statico, grill ventilatoMateriale della cavità: .................................................................Altro Regolazione della temperatura: .........................................elettronica Numero di luci interne: (1)Lunghezza del cavo di alimentazione elettrica: .....................120.0 cm Codice EAN: (4242005356492)Numero di vani - (2010/30/CE): (1)Classe di efficienza energetica: .........................................................A Energy consumption per cycle conventional (2010/30/EC): ........0.99 kWh/cycleEnergy consumption per cycle forced air convection (2010/30/EC):0.81 kWh/cycleIndice di efficienza energetica (2010/30/CE): ..........................95.3 % Potenza: ..................................................................................3600 W Corrente: .....................................................................................16 A Tensione: .............................................................................220-240 V Frequenza: ...........................................................................50; 60 Hz Tipo di spina: ..........................................................................Schuko Accessori inclusi: .......1 x Griglia combinata, 1 x Leccarda universale smaltataSerie 2, Forno da incasso, 60 x 60cm, AcciaioHBA171BS1- 5 programmi di cottura: MultiCottura HotAir 3D, Riscaldamento superiore e inferiore, Grill ventilato, Grill a superficie grande- Forno multi 60cm- HBA171BS1- Programmi automatici: 10- Temperatura porta max. 30 °CCaratteristiche principali- Sistema di cottura assistita: Programmi automatici- Illuminazione interna alogena, Illuminazione disinseribile- Riscaldamento rapido- Forno con ampia cavità e supporto teglie- Orologio elettronico con impostazione inizio e fine cottura- Volume cavità: 71 l- Accessori: 1 griglia combinata, 1 leccarda universale profonda smaltata- Regolazione della temperatura da 30 °C a 275 °CPulizia- Autopulizia pirolitica- Cleaning Assistance- Ventola tangenziale di raffreddamentoAltre caratteristicheInformazioni tecniche- Numero di livelli: 5 pezzo- Si prega di fare riferimento alle quote d'installazione mostrate nel disegno tecnicoEtichetta energetica- Assorbimento massimo elettrico: 3.6 kW- Lungh. cavo alimentazione: 120 cmSistema di controllo- TouchControlGriglie / GuideAccessori- Tensione: 220 - 240 VDimensioni- Dimensioni apparecchio (AxLxP): 595 mm x 594 mm x 548 mm- Dimensioni nicchia (AxLxP): 560 mm - 568 mm x 585 mm - 595 mm x 550 mm- Temperatura suggerita- Raggiungimento temperaturaSerie 2, Forno da incasso, 60 x 60cm, Acciaio HBA171BS1。
Schlumberger - Well Integrity Program 斯伦贝谢井眼完整性程序

Well Integrity Framework
Component of our “Excellence in Execution” Program
Schlumberger Confidential
Schlumberger Well Integrity Program
Hussam Al Quassar MEA WSV Technique Manager
Well Integrity
Recent industry incidents led to an increase focus on Well Integrity.
O
RK
Permanent packer and seal assembly
O
RK
A25 Tubing/Completion String
K
OK
K
A29 Completion String Component
K* K* O
KK
RK
R
Gas lift valves
K
RK
O
Side pocket mandrels
K
OK
A22 Casing Cement
O
K
RKKKK
A24 Cement Plug
O K*
K K*
KKRKKKK
Shoe track
O K*
K K*
KKRKKKK
A33 Surface Production Tree
K*
K
Mini-Circuits RUDAT-6000-30产品说明书

RUDAT-6000-30Key FeaturesProgrammable AttenuatorUSB / RS232Case Style: MS1813Software PackageThe Big Deal• Attenuation range, 30 dB• Fine attenuation resolution, 0.25 dB• Short attenuation transition time (650 ns)• Compact size, 2.0 x 3.0 x 0.6”• USB and RS232 control50Ω 0 – 30 dB, 0.25 dB step 1 to 6000 MHzProduct OverviewMini-Circuits’ RUDAT-6000-30 is a general purpose, single channel programmable attenuator suitable for a wide range of signal level control applications from 1 MHz to 6 GHz. The Attenuator provides 0 to 30 dB attenuation in 0.25 dB steps. Its unique design maintains linear attenuation change per dB, even at the highest attenuation settings.The attenuator is housed in a compact and rugged package with SMA female connectors on the bi-directional input and output RF ports, a standard 9 pin D-Sub and a USB type Mini-B power and control ports.The attenuator can be controlled via USB or RS232 (via D-Sub connector). Full software support is provided and can be downloaded from our website any time at /softwaredownload/patt.html . The package includes our user-friendly GUI application for Windows ® and a full API with programming instructions for Windows ® and Linux ® environments (both 32-bit and 64-bit systems).Trademarks: Windows is a registered trademark of Microsoft Corporation in the United States and other countries. Linux is a registered trademark of Linus Tor-valds. Mac is a registered trademark of Apple Corporation. Pentium is a registered trademark of Intel Corporation. Neither Mini-Circuits nor the Mini-Circuits RUDAT-series attenuators are affiliated with or endorsed by the owners of the above referenced trademarks.Mini-Circuits and the Mini-Circuits logo are registered trademarks of Scientific Components Corporation.Rev. KECO-008003EDR-10982/5Applications• Automated Test Equipment (ATE)• WiMAX, 3G, 4G, LTE, DVB Fading Simulators • Laboratory Instrumentation • Handover system Evaluation • Power level cyclingIncluded AccessoriesModel No.DescriptionQty.MUSB-CBL-3+2.6 ft. USB cable11 Attenuator RF ports are interchangeable, and support simultaneous, bidirectional signal transmission, however the specifications are guaranteed forthe RF in and RF out as noted on the label. There may be minor changes in performance when injecting signals to the RF Out port. 2 Max accuracy defined as ±[absolute error+% of attenuation setting] for example when setting the attenuator to 18 dB attenuation the maximum error will be: ±(0.95+0.02x18)= ±(0.95+0.36)= ± 1.31 dB.3 Total operating input power from both RF In and RF Out out ports. Compression level not noted as it exceeds max safe operating power level.4 Isolation is defined as max attenuation plus insertion loss; this is the path loss through the attenuator when initially powered up. After a brief delay (~0.5 sec typically) the attenuator will revert to a user defined “power-up” state (either max attenuation or a pre-set value).5 Tested with 1 MHz span between signals.6 Minimum Dwell Time is the time the RUDAT will take to respond to a command to change attenuation states without communication delays. In PC control add communication delays (on the order of msec for USB) to get actual response time.7Attenuation Transition Time is specified as the time between starting to change the attenuation state and settling on the requested attenuation state.8 Supply voltage +5V at Pin#1 of D-sub connector applies to units with S/N 11405010010 and greater.9 Power on sequence for RS232 control: Connect 5V power followed by the control lines.Absolute Maximum RatingsPermanent damage may occur if any of these limits are exceeded. Operation in the range between the max operating power and the absolute maximum rating for extended periods of time may result in reduced life and reliability.Operating Temperature 0°C to 50°C Storage Temperature-20°C to 85°C Voltage input at RS232 receive pin -30V to +30V Voltage input at RS232 transmit pin 0V to +4V Voltage input at RS232 Pin#1-1V to +6VV USB Max.6V DC voltage at RF port16V Total RF power for RF In & RF Out @ 1 to 10 MHz +13 dBm @ 10 to 6000 MHz+23 dBm10 Block diagram and connection shown apply to units with S/N 11405010010 and greater, for units with lowerS/N see archive section on page 9.11 Pin#1 can be used as supply voltage (+) pin instead of USB connection. When USB power is connected,Pin#1 may be connected to GND or supply voltage (+) or remain disconnected.12 Power on sequence for RS232 control: Connect 5V power followed by the control lines.Block Diagram 10USBSimultaneous, bidirectional RF signal transmission with symmetrical performanceNot ConnectedRS232Transmit (2)Receive (3)NC (4)GND (5)(6)(7)(8)(9)Supply voltage (1)*9 Pin D-SubPin Connections 10PIN NumberFunction2Transmit 3Receive 5GND 1+5 V DC 11,124,6-9Not ConnectedConnectionsRF IN (SMA female)RF OUT (SMA female)USB (USB type Mini-B female)RS232*(9 Pin D-Sub female)The 5V DC the D-Sub port.inch2X SMA FEMALEBracket OptionQTop ViewBottom View4X #2-56 UNCInstruction for mounting bracket:1. Tool required: Phillips head screwdriver2. Mount the bracket over threaded holes on the bottom side with the fasteners provided with the bracket.Attenuation Accuracy @ +25°Cvs. Frequency over Attenuation settings-1.0-0.50.00.51.01.50100020003000400050006000Frequency (MHz)A c c u r a c y(d B)Attenuation Accuracy @ 0°Cvs. Frequency over Attenuation settingsFrequency (MHz)A c c u r a c y (dB )Attenuation Accuracy @ +50°Cvs. Frequency over Attenuation settingsFrequency (MHz)A c c u r a c y (d B )Attenuation relative to I.L @ +25°C vs. Frequency over Attenuation settings0.010.020.030.040.00100020003000400050006000Frequency (MHz)Attenuation relative to I.L @ 0°C vs. Frequency over Attenuation settingsFrequency (MHz)A t t e n u a t i o n (dB )Attenuation relative to I.L @ +50°C vs. Frequency over Attenuation settings Frequency (MHz)A t t e n u a t i o n (dB )A t t e n u a t i o n (dB )1 1000 2000 3000 4000 5000 60001 1000 2000 3000 4000 5000 6000Attenuation relative to Insertion Loss @ +25°C vs. Frequency over Attenuation settings Attenuation relative to Insertion Loss @ 0°C vs. Frequency over Attenuation settings Attenuation relative to Insertion Loss @ +50°C vs. Frequency over Attenuation settingsInput VSWR @ +25°Cvs. Frequency over Attenuation settings1.01.21.41.61.82.00.001000.002000.003000.004000.005000.006000.00Frequency (MHz)I n p u t V S W R (:1)Ouput VSWR @ +25°Cvs. Frequency over Attenuation settings1.01.21.41.61.82.00.001000.002000.003000.004000.005000.006000.00Frequency (MHz)O u t p u t V S W R (:1)Insertion Loss @ Input Power=0dBm 0123450100020003000400050006000Frequency (MHz)I n s e r t i o n L o s s (d B )Insertion Loss @ Input Power +20 dBmvs. Frequency over Temperatures Insertion Loss @ Input Power=+23dBm123450100020003000400050006000Frequency (MHz)I n s e r t i o n L o s s (d B )Insertion Loss @ Input Power 0dBm vs. Frequency over Temperatures11000 2000 3000 4000 5000 6000 101000 2000 3000 4000 5000 6000 1 1000 2000 3000 4000 50006000 1 1000 2000 3000 4000 5000 6000Output VSWR @ +25°C vs. Frequency over Attenuation settings Input VSWR @ +25°C vs. Frequency over Attenuation settings IP3 @ 0dB AttenuationFrequency (MHz)I P 3 (d B m )Input IP3 @ 0dB Attenuationvs. Frequency over Temperatures Attenuation Setting (dB)A t t e n u a t i o n A c c u r a c y (dB )• Mini-Circuits’ full software and support package including user guide, Windows GUI, DLL files, programming manual and examples can be downloaded free of charge from /softwaredownload/patt.html • Please contact ****************************** for supportGraphical User Interface (GUI) for Windows Key Features:• Manual attenuation setting• Sweep and Hop attenuation sequences directed from the PC, or entire sequence loaded into RUDAT.• Attenuator address configuration and Firmware upgrade • Attenuation at power up may be set to selected attenuation level or last attenuation state recorded.• USB or RS232 control of RUDATApplication Programming Interface (API)Windows Support:• API DLL files exposing the full switch functionality See programming manual at https:///softwaredownload/Prog_Manual-6-Programmable_Attenuator.pdf for details • ActiveX COM DLL file for creation of 32-bit programs • .Net library DLL file for creation of 32 / 64-bit programs• Supported by most common programming environments (refer to application note AN-49-001 for summary of tested environments)Linux Support:• Full switch control in a Linux environment is achieved by way of USB interrupt commands. See programming manual at https:///softwaredownload/Prog_Manual-6-Programmable_Attenuator.pdf for detailsModelDescriptionRUDAT-6000-30USB/RS232 Programmable AttenuatorAdditional NotesA. Performance and quality attributes and conditions not expressly stated in this specification document are intended to be excluded and do not form a part of this specification document.B. Electrical specifications and performance data contained in this specification document are based on Mini-Circuit’s applicable established test performance criteria and measurement instructions.C. The parts covered by this specification document are subject to Mini-Circuits standard limited warranty and terms and conditions (collectively, “Standard Terms”); Purchasers of this part are entitled to the rights and benefits contained therein. For a full statement of the Standard Terms and the exclusive rights and remedies thereunder, please visit Mini-Circuits’ website at /MCLStore/terms.jspIncluded Accessories Part No.DescriptionMUSB-CBL-3+2.6 ft (0.8 m) USB Cable: USB type A(Male) to USB typeMini-B(Male)Optional AccessoriesDescriptionUSB-AC/DC-5 13,14AC/DC 5V DC Power Adapter with US, EU, IL, UK, AUS, and China power plugsMUSB-CBL-3+ (spare) 2.6 ft (0.8 m) USB Cable: USB type A(Male) to USB type Mini-B(Male)MUSB-CBL-7+ 6.6 ft (2.0 m) USB Cable: USB type A(Male) to USB type Mini-B(Male)D-SUB9-MF-6+ 6 ft RS232 Cable: 9 pin D-sub(Male) to 9 pin D-sub(Female)BKT-3901+Bracket kit including 3.75” x 2.00” bracket, mounting screws and washers13 Not used in USB control. USB-AC/DC-5 can be used to provide the 5VDC power when control is via RS232; units with S/N11405010010 and greater can also accept DC supply voltage at Pin#1 of the D-sub connector.14 Power plugs for other countries are also available, Plugs for other countries are also available, if you need a power plug for a country not listed please contact ******************************Block DiagramUSBSimultaneous, bidirectional RF signal transmission with symmetrical performanceNot ConnectedRS232Transmit (2)Receive (3)NC (4)GND (5)(6)(7)(8)(9)NC (1)ConnectionsRF IN (SMA female)RF OUT (SMA female)USB (USB type Mini-B female)RS232*(9 Pin D-Sub female)*9 Pin D-SubPin Connections 16Pin NumberFunction2Transmit 3Receive 5GND 1,4,6-9Not Connected16 Supply voltage can be provided via USB port only. When using RS232 control, powermust be provided to the USB port via either USB-AC/DC-5 power adaptor or a USB bus.。
ICP DAS I-7017R 8-ch Voltage and Current Input DAQ

I-7017R - 8-ch Voltage and Current Input DAQ Module - QuickStart (May/2020)ICP DAS USA, Inc. | | 1-310-517-9888 | 24309 Narbonne Ave. Suite 200. Lomita, CA 90717I-7017R8 Channels Voltage & Current InputData Acquisition ModuleQuick Start GuideProduct Website:https:///i_7017_r.html/dcon_utility_pro.htmlIntroductionThe I-7017R is an 8-channel analog input module with an extremely high quality protection mechanism where the overvoltage protection is 240 Vrms. The input type includes both voltage and current. The sampling rate of the I-7017R is adjustable, meaning that either fast mode or normal mode can be selected. The I-7017R also has 4 kV ESD protection as well as 3000 VDC intra-module isolation. The I-7017R-A5 is an 8-channel analog input module that is especially designed for high voltage input, and has an input range of between -50 V ~ +50 V or -150 V ~ +150 V.Packing ListI-7017RPlastic RailCDQuick Start GuideI-7017R - 8-ch Voltage and Current Input DAQ Module - QuickStart (May/2020)ICP DAS USA, Inc. | | 1-310-517-9888 | 24309 Narbonne Ave. Suite 200. Lomita, CA 90717⏹Internal I/O Structure < I-7017R >⏹Pin Assignments < I-7017R, I-7017R >⏹Internal I/O Structure (I-7017R)⏹Modbus Table (M-7017R only)Address Description R/W 10129 ~Over/under range status of channel 0R 10136to 7 for 4 ~ 20mA or 0 ~ 20mA ranges 00129 ~0013630001 ~Analog input value of channel 0 to 7R 3000840001 ~4000840481Firmware version (low word)R 40482Firmware version (high word)R 40483Module name (low word)R 40484Module name (high word)R 40485Module address, valid range: 1 ~ 247R/W 40486Bits 5:0R/WBaud rate, 0x03 ~ 0x0ACode0x030x040x050x06Baud1200240048009600Code0x070x080x090x0ABaud192003840057600115200Bits 7:600: no parity, 1 stop bit01: no parity, 2 stop bit10: even parity, 1 stop bit11: odd parity, 1 stop bit40487Type code R/W Address Description R/W 40488Modbus response delay time in ms,R/W valid range: 0 ~ 3040489Host watchdog timeout value, 0 ~R/W 255, in 0.1s40490Channel enable/disable, 00h ~ FFh R/W 40492Host watchdog timeout count, write 0R/W to clear00257Protocol, 0: DCON, 1: Modbus RTU R/W 00259Filter setting, 0: 60Hz rejection, 1:R/W 50Hz rejection002611: enable, 0: disable host watchdog R/W 00269Modbus data format, 0: hex, 1:R/W engineering00270Host watch dog timeout status, write R/W1 to clear host watch dog timeoutstatus002711: enable, 0: disable fast mode R/W 00273Reset status, 1: first read after R powered on, 0: not the first read afterpowered on⏹DCON ProtocolFunctions Command Response NotesRead module name$AAM!AA(Data)AA: address number Read module firmware version$AAF!AA(Data)Read all analog input data#aa>(data)Read analog input data of each channel (<=16 channel)#aai>(data)i: channel number (Hex) Read analog input data of each channel (>16 channel)#aaii>(data)ii: channel number (Hex) If you want to know the detail DCON protocol, please check it from CD or webCD path: \\napdos\7000\manual\Web: ftp:///pub/cd/8000cd/napdos/7000/manual/I-7017R - 8-ch Voltage and Current Input DAQ Module - QuickStart (May/2020)ICP DAS USA, Inc. | | 1-310-517-9888 | 24309 Narbonne Ave. Suite 200. Lomita, CA 90717I-7017R - 8-ch Voltage and Current Input DAQ Module - QuickStart (May/2020)ICP DAS USA, Inc. | | 1-310-517-9888 | 24309 Narbonne Ave. Suite 200. Lomita, CA 90717⏹Module test and configurationStep 1: INIT switch Operation Step 2: Install & Run DCON Utility 1. Please Install DCON Utility firstYou can find the software in the CD.CD path:<Driver>:\napdos\driver\dcon_utility\Web link:/pub/cd/8000cd/napdos/driver/dcon_utility/ 2. Run DCON utility1. Find out the INIT switch( back of the module),and turn to INIT.2. Reboot the moduleStep 3: Set search configuration & search module Select COM Port Number1. Click “COM Port”2. Assign the communication information and click“OK”Module Default Setting COM Port Refer converter Port Number Baud Rate 9600ProtocolDCON for I-7000Modbus RTU for M-7000Parity Option N,8,13. Click “Search” and select “Start Searching”Software will search the modules from COM Port 4. Click “Search“ and select “stop searching”Manual stop when the modules searchedNote:When no module can be searched, please check the wire and communication informationStep 4: Select Module for testing and configurationDouble click “select module”Step 5: Configuration Settings & Channel SettingsChannel StatusModule SettingsProtocol DCON / ModbusAddress1~255 (0:INIT)Baud rate1200~115200Parity option N,8,1Input range Depends on signalsourcesStep 6: Change to normal mode and keep the settings1.Turn the INIT Switch to Normal.2.Reboot the moduleI-7017R - 8-ch Voltage and Current Input DAQ Module - QuickStart (May/2020)ICP DAS USA, Inc. | | 1-310-517-9888 | 24309 Narbonne Ave. Suite 200. Lomita, CA 90717Trouble ShootingQ1. How to do when forgot module address or baud rate?Please turn to INIT mode, and run DCON Utility to search.The module supports DCON protocol at the INIT mode.And the address is 0. The communication setting is “9600,N,8,1”.Q2. How to configure the I-7000 and M-7000 modules?ICP DAS provide DCON Utility to configure I-7000 and M-7000 modules.Please download the last version from: /pub/cd/8000cd/napdos/driver/dcon_utility/Q3. How to calibrate the analog input module?Usually it is not necessary to calibrate the analog input module.However, in case you need to perform this operation, we provide a function to calibrate the module.Please refer to user manual 1.10.Notice:1.Please update DCON Utility to version 5.2.3 or more.2.Keep the module running more than 30 minutes to warm-up.Q4. How to measure the current?I-7017R and I-7017R require optional external resistance (125Ω) for current measurement.Please refer wired connections diagram.And then select a suitable input range by DCON Utility.Or please use our I-7017RC or I-7017RC modules.Q5. How to programming with I-7000 or M-7000 by C#, VB, VC?ICP DAS I-7000 and M-7000 series both support DCON protocol. And Only M-7000 series supports Modbus protocol.For DCON protocol, please download SDK and Demo from:/pub/cd/8000cd/napdos/driver/dcon_dll_new/For Modbus protocol, please refer this web link:/products/PAC/i-8000/modbus.htmIfthereisanyotherquestion,pleasefeelfreetocontactus.Email:******************Website: /contact_us/contact_us.htmlI-7017R - 8-ch Voltage and Current Input DAQ Module - QuickStart (May/2020)ICP DAS USA, Inc. | | 1-310-517-9888 | 24309 Narbonne Ave. Suite 200. Lomita, CA 90717。
超低功耗微型超声时间差测距传感器CH101说明书
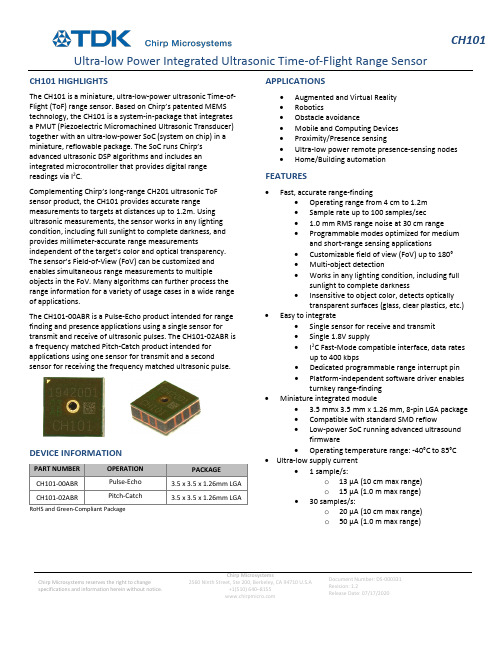
CH101 Ultra-low Power Integrated Ultrasonic Time-of-Flight Range SensorChirp Microsystems reserves the right to change specifications and information herein without notice.Chirp Microsystems2560 Ninth Street, Ste 200, Berkeley, CA 94710 U.S.A+1(510) 640–8155Document Number: DS-000331Revision: 1.2Release Date: 07/17/2020CH101 HIGHLIGHTSThe CH101 is a miniature, ultra-low-power ultrasonic Time-of-Flight (ToF) range sensor. Based on Chirp’s patented MEMS technology, the CH101 is a system-in-package that integrates a PMUT (Piezoelectric Micromachined Ultrasonic Transducer) together with an ultra-low-power SoC (system on chip) in a miniature, reflowable package. The SoC runs Chirp’s advanced ultrasonic DSP algorithms and includes an integrated microcontroller that provides digital range readings via I2C.Complementing Chirp’s long-range CH201 ultrasonic ToF sensor product, the CH101 provides accurate range measurements to targets at distances up to 1.2m. Using ultrasonic measurements, the sensor works in any lighting condition, including full sunlight to complete darkness, and provides millimeter-accurate range measurements independent of the target’s color and optical transparency. The sensor’s Field-of-View (FoV) can be customized and enables simultaneous range measurements to multiple objects in the FoV. Many algorithms can further process the range information for a variety of usage cases in a wide range of applications.The CH101-00ABR is a Pulse-Echo product intended for range finding and presence applications using a single sensor for transmit and receive of ultrasonic pulses. The CH101-02ABR is a frequency matched Pitch-Catch product intended for applications using one sensor for transmit and a second sensor for receiving the frequency matched ultrasonic pulse.DEVICE INFORMATIONPART NUMBER OPERATION PACKAGECH101-00ABR Pulse-Echo 3.5 x 3.5 x 1.26mm LGA CH101-02ABR Pitch-Catch 3.5 x 3.5 x 1.26mm LGA RoHS and Green-Compliant Package APPLICATIONS•Augmented and Virtual Reality•Robotics•Obstacle avoidance•Mobile and Computing Devices•Proximity/Presence sensing•Ultra-low power remote presence-sensing nodes •Home/Building automation FEATURES•Fast, accurate range-finding•Operating range from 4 cm to 1.2m•Sample rate up to 100 samples/sec• 1.0 mm RMS range noise at 30 cm range•Programmable modes optimized for medium and short-range sensing applications•Customizable field of view (FoV) up to 180°•Multi-object detection•Works in any lighting condition, including full sunlight to complete darkness•Insensitive to object color, detects opticallytransparent surfaces (glass, clear plastics, etc.) •Easy to integrate•Single sensor for receive and transmit•Single 1.8V supply•I2C Fast-Mode compatible interface, data rates up to 400 kbps•Dedicated programmable range interrupt pin•Platform-independent software driver enables turnkey range-finding•Miniature integrated module• 3.5 mmx 3.5 mm x 1.26 mm, 8-pin LGA package•Compatible with standard SMD reflow•Low-power SoC running advanced ultrasound firmware•Operating temperature range: -40°C to 85°C •Ultra-low supply current• 1 sample/s:o13 µA (10 cm max range)o15 µA (1.0 m max range)•30 samples/s:o20 µA (10 cm max range)o50 µA (1.0 m max range)Table of ContentsCH101 Highlights (1)Device Information (1)Applications (1)Features (1)Simplified Block Diagram (3)Absolute Maximum Ratings (4)Package Information (5)8-Pin LGA (5)Pin Configuration (5)Pin Descriptions (6)Package Dimensions (6)Electrical Characteristics (7)Electrical Characteristics (Cont’d) (8)Typical Operating Characteristics (9)Detailed Description (10)Theory of Operation (10)Device Configuration (10)Applications (11)Chirp CH101 Driver (11)Object Detection (11)Interfacing to the CH101 Ultrasonic Sensor (11)Device Modes of Operation: (12)Layout Recommendations: (13)PCB Reflow Recommendations: (14)Use of Level Shifters (14)Typical Operating Circuits (15)Ordering Information (16)Part Number Designation (16)Package Marking (17)Tape & Reel Specification (17)Shipping Label (17)Revision History (19)SIMPLIFIED BLOCK DIAGRAMFigure 1. Simplified Block DiagramABSOLUTE MAXIMUM RATINGSPARAMETER MIN. TYP. MAX. UNIT AVDD to VSS -0.3 2.2 V VDD to VSS -0.3 2.2 V SDA, SCL, PROG, RST_N to VSS -0.3 2.2 V Electrostatic Discharge (ESD)Human Body Model (HBM)(1)Charge Device Model (CDM)(2)-2-5002500kVV Latchup -100 100 mA Temperature, Operating -40 85 °C Relative Humidity, Storage 90 %RH Continuous Input Current (Any Pin) -20 20 mA Soldering Temperature (reflow) 260 °CTable 1. Absolute Maximum RatingsNotes:1.HBM Tests conducted in compliance with ANSI/ESDA/JEDEC JS-001-2014 Or JESD22-A114E2.CDM Tests conducted in compliance with JESD22-C101PACKAGE INFORMATION8-PIN LGADESCRIPTION DOCUMENT NUMBER CH101 Mechanical Integration Guide AN-000158CH101 and CH201 Ultrasonic Transceiver Handling andAssembly Guidelines AN-000159Table 2. 8-Pin LGAPIN CONFIGURATIONTop ViewFigure 2. Pin Configuration (Top View)PIN DESCRIPTIONSPIN NAME DESCRIPTION1 INT Interrupt output. Can be switched to input for triggering and calibration functions2 SCL SCL Input. I2C clock input. This pin must be pulled up externally.3 SDA SDA Input/Output. I2C data I/O. This pin must be pulled up externally.4 PROG Program Enable. Cannot be floating.5 VSS Power return.6 VDD Digital Logic Supply. Connect to externally regulated 1.8V supply. Suggest commonconnection to AVDD. If not connected locally to AVDD, b ypass with a 0.1μF capacitor asclose as possible to VDD I/O pad.7 AVDD Analog Power Supply. Connect to externally re gulated supply. Bypass with a 0.1μFcapacitor as close as possible to AVDD I/O pad.8 RESET_N Active-low reset. Cannot be floating.Table 3. Pin DescriptionsPACKAGE DIMENSIONSFigure 3. Package DimensionsELECTRICAL CHARACTERISTICSAVDD = VDD = 1.8VDC, VSS = 0V, T A = +25°C, min/max are from T A = -40°C to +85°C, unless otherwise specified.PARAMETER SYMBOL CONDITIONS MIN TYP MAX UNITSPOWER SUPPLYAnalog Power Supply AVDD 1.62 1.8 1.98 V Digital Power Supply VDD 1.62 1.8 1.98 VULTRASONIC TRANSMIT CHANNELOperating Frequency 175 kHzTXRX OPERATION (GPR FIRMWARE USED UNLESS OTHERWISE SPECIFIED)Maximum Range Max Range Wall Target58 mm Diameter Post1.2(1)0.7mm Minimum Range Min Range Short-Range F/W used 4(2)cm Measuring Rate (Sample/sec) SR 100 S/s Field of View FoV Configurable up to 180º deg Current Consumption (AVDD +VDD) I SSR=1S/s, Range=10 cmSR=1S/s, Range=1.0mSR=30S/s, Range=10 cmSR=30S/s, Range=1.0m13152050μAμAμAμA Range Noise N R Target range = 30 cm 1.0 mm, rms Measurement Time 1m max range 18 ms Programming Time 60 msTable 4. Electrical CharacteristicsNotes:1.Tested with a stationary target.2.For non-stationary objects. While objects closer than 4cm can be detected, the range measurement is not ensured.ELECTRICAL CHARACTERISTICS (CONT’D)AVDD = VDD = 1.8VDC, VSS = 0V, T A = +25°C, unless otherwise specified.PARAMETERSYMBOL CONDITIONS MINTYP MAX UNITS DIGITAL I/O CHARACTERISTICS Output Low Voltage V OL SDA, INT,0.4 V Output High Voltage V OH INT 0.9*V VDD V I 2C Input Voltage Low V IL_I2C SDA, SCL 0.3*V VDDV I 2C Input Voltage High V IH_I2C SDA, SCL 0.7*V VDD V Pin Leakage Current I L SDA,SCL, INT(Inactive), T A =25°C±1μA DIGITAL/I 2C TIMING CHARACTERISTICSSCL Clock Frequencyf SCLI 2C Fast Mode400kHzTable 5. Electrical Characteristics (Cont’d)TYPICAL OPERATING CHARACTERISTICSAVDD = VDD = 1.8VDC, VSS = 0V, T A = +25°C, unless otherwise specified.Typical Beam Pattern – MOD_CH101-03-01 Omnidirectional FoV module(Measured with a 1m2 flat plate target at a 30 cm range)Figure 4. Beam pattern measurements of CH101 moduleDETAILED DESCRIPTIONTHEORY OF OPERATIONThe CH101 is an autonomous, digital output ultrasonic rangefinder. The Simplified Block Diagram, previously shown, details the main components at the package-level. Inside the package are a piezoelectric micro-machined ultrasonic transducer (PMUT) and system-on-chip (SoC). The SoC controls the PMUT to produce pulses of ultrasound that reflect off targets in the sensor’s Field of View (FoV). The reflections are received by the same PMUT after a short time delay, amplified by sensitive electronics, digitized, and further processed to produce the range to the primary target. Many algorithms can further process the range information for a variety of usage cases in a wide range of applications.The time it takes the ultrasound pulse to propagate from the PMUT to the target and back is called the time-of-flight (ToF). The distance to the target is found by multiplying the time-of-flight by the speed of sound and dividing by two (to account for the round-trip). The speed of sound in air is approximately 343 m/s. The speed of sound is not a constant but is generally stable enough to give measurement accuracies within a few percent error.DEVICE CONFIGURATIONA CH101 program file must be loaded into the on-chip memory at initial power-on. The program, or firmware, is loaded through a special I2C interface. Chirp provides a default general-purpose rangefinder (GPR) firmware that is suitable for a wide range of applications. This firmware enables autonomous range finding operation of the CH101. It also supports hardware-triggering of the CH101 for applications requiring multiple transceivers. Program files can also be tailored to the customer’s application. Contact Chirp for more information.CH101 has several features that allow for low power operation. An ultra-low-power, on-chip real-time clock (RTC) sets the sample rate and provides the reference for the time-of-flight measurement. The host processor does not need to provide any stimulus to the CH101 during normal operation, allowing the host processor to be shut down into its lowest power mode until the CH101 generates a wake-up interrupt. There is also a general-purpose input/output (INT) pin that is optimized to be used as a system wake-up source. The interrupt pin can be configured to trigger on motion or proximity.APPLICATIONSCHIRP CH101 DRIVERChirp provides a compiler and microcontroller-independent C driver for the CH101 which greatly simplifies integration. The CH101 driver implements high-level control of one or more CH101s attached to one or more I2C ports on the host processor. The CH101 driver allows the user to program, configure, trigger, and readout data from the CH101 through use of C function calls without direct interaction with the CH101 I2C registers. The CH101 driver only requires the customer to implement an I/O layer which communicates with the host processor’s I2C hardware and GPIO hardware. Chirp highly recommends that all designs use the CH101 driver.OBJECT DETECTIONDetecting the presence of objects or people can be optimized via software, by setting the sensor’s full-scale range (FSR), and via hardware, using an acoustic housing to narrow or widen the sensor’s field-of-view. The former means that the user may set the maximum distance at which the sensor will detect an object. FSR values refer to the one-way distance to a detected object.In practice, the FSR setting controls the amount of time that the sensor spends in the listening (receiving) period during a measurement cycle. Therefore, the FSR setting affects the time required to complete a measurement. Longer full-scale range values will require more time for a measurement to complete.Ultrasonic signal processing using the CH101’s General Purpose Rangefinder (GPR) Firmware will detect echoes that bounce off the first target in the Field-of-View. The size, position, and material composition of the target will affect the maximum range at which the sensor can detect the target. Large targets, such as walls, are much easier to detect than smaller targets. Thus, the associated operating range for smaller targets will be shorter. The range to detect people will be affected by a variety of factors such as a person’s size, clothing, orientation to the sensor and the sensor’s field-of-view. In general, given these factors, people can be detected at a maximum distance of 0.7m from the CH101 sensor.For additional guidance on the detection of people/objects using the NEMA standard, AN-000214 Presence Detection Application Note discusses the analysis of presence detection using the Long-Range CH201 Ultrasonic sensor.INTERFACING TO THE CH101 ULTRASONIC SENSORThe CH101 communicates with a host processor over the 2-wire I2C protocol. The CH101 operates as an I2C slave and responds to commands issued by the I2C master.The CH101 contains two separate I2C interfaces, running on two separate slave addresses. The first is for loading firmware into the on-chip program memory, and the second is for in-application communication with the CH101. The 7-bit programming address is0x45, and the 7-bit application address default is 0x29. The application address can be reprogrammed to any valid 7-bit I2C address. The CH101 uses clock stretching to allow for enough time to respond to the I2C master. The CH101 clock stretches before the acknowledge (ACK) bit on both transmit and receive. For example, when the CH101 transmits, it will hold SCL low after it transmits the 8th bit from the current byte while it loads the next byte into its internal transmit buffer. When the next byte is ready, it releases the SCL line, reads the master’s ACK bit, and proceeds accordingly. When the CH101 is receiving, it holds the SCL line low after it receives the 8th bit in a byte. The CH101 then chooses whether to ACK or NACK depending on the received data and releases the SCL line.The figure below shows an overview of the I2C slave interface. In the diagram, ‘S’ indicates I2C start, ‘R/W’ is the read/write bit, ‘Sr’ is a repeated start, ‘A’ is acknowledge, and ‘P’ is the stop condition. Grey boxes indicate the I2C master actions; white boxes indicate the I2C slave actions.Figure 5. CH101 I2C Slave Interface DiagramDEVICE MODES OF OPERATION:FREE-RUNNING MODEIn the free-running measurement mode, the CH101 runs autonomously at a user specified sample rate. In this mode, the INT pin is configured as an output. The CH101 pulses the INT pin high when a new range sample is available. At this point, the host processor may read the sample data from the CH101 over the I2C interface.HARDWARE-TRIGGERED MODEIn the hardware triggered mode, the INT pin is used bi-directionally. The CH101 remains in an idle condition until triggered by pulsing the INT pin. The measurement will start with deterministic latency relative to the rising edge on INT. This mode is most useful for synchronizing several CH101 transceivers. The host controller can use the individual INT pins of several transceivers to coordinate the exact timing.CH101 BEAM PATTERNSThe acoustic Field of View is easily customizable for the CH101 and is achieved by adding an acoustic housing to the transceiver that is profiled to realize the desired beam pattern. Symmetric, asymmetric, and omnidirectional (180° FoV) beam patterns are realizable. An example beam pattern is shown in the Typical Operating Characteristics section of this document and several acoustic housing designs for various FoV’s are available from Chirp.LAYOUT RECOMMENDATIONS:RECOMMENDED PCB FOOTPRINTDimensions in mmFigure 6. Recommended PCB FootprintPCB REFLOW RECOMMENDATIONS:See App Note AN-000159, CH101 and CH201 Ultrasonic Transceiver Handling and Assembly Guidelines.USE OF LEVEL SHIFTERSWhile the use of autosense level shifters for all the digital I/O signal signals is acceptable, special handling of the INT line while using a level shifter is required to ensure proper resetting of this line. As the circuit stage is neither a push-pull nor open-drain configuration (see representative circuit below), it is recommended that level shifter with a manual direction control line be used. The TI SN74LVC2T45 Bus Transceiver is a recommended device for level shifting of the INT signal line.Figure 7. INT Line I/O Circuit StageTYPICAL OPERATING CIRCUITSFigure 8. Single Transceiver OperationFigure 9. Multi- Transceiver OperationORDERING INFORMATIONPART NUMBER DESIGNATIONFigure 10. Part Number DesignationThis datasheet specifies the following part numbersPART NUMBER OPERATION PACKAGE BODY QUANTITY PACKAGING CH101-00ABR Pulse-Echo 3.5 mm x 3.5 mm x 1.26 mmLGA-8L 1,000 7” Tape and ReelCH101-02ABR Pitch-Catch 3.5 mm x 3.5 mm x 1.26 mmLGA-8L 1,000 7” Tape and ReelTable 6. Part Number DesignationCH101-xxABxProduct FamilyProduct Variant Shipping CarrierR = Tape & Reel 00AB = Pulse-Echo Product Variant02AB = Pitch-Catch Product VariantCH101 = Ultrasonic ToF SensorPACKAGE MARKINGFigure 11. Package MarkingTAPE & REEL SPECIFICATIONFigure 12. Tape & Reel SpecificationSHIPPING LABELA Shipping Label will be attached to the reel, bag and box. The information provided on the label is as follows:•Device: This is the full part number•Lot Number: Chirp manufacturing lot number•Date Code: Date the lot was sealed in the moisture proof bag•Quantity: Number of components on the reel•2D Barcode: Contains Lot No., quantity and reel/bag/box numberDimensions in mmDEVICE: CH101-XXXXX-XLOT NO: XXXXXXXXDATE CODE: XXXXQTY: XXXXFigure 13. Shipping LabelREVISION HISTORY09/30/19 1.0 Initial Release10/22/19 1.1 Changed CH-101 to CH101. Updated figure 7 to current markings.07/17/20 1.2 Format Update. Incorporated “Maximum Ratings Table” and “Use of LevelShifters” section.This information furnished by Chirp Microsystems, Inc. (“Chirp Microsystems”) is believed to be accurate and reliable. However, no responsibility is assumed by Chirp Microsystems for its use, or for any infringements of patents or other rights of third parties that may result from its use. Specifications are subject to change without notice. Chirp Microsystems reserves the right to make changes to this product, including its circuits and software, in order to improve its design and/or performance, without prior notice. Chirp Microsystems makes no warranties, neither expressed nor implied, regarding the information and specifications contained in this document. Chirp Microsystems assumes no responsibility for any claims or damages arising from information contained in this document, or from the use of products and services detailed therein. This includes, but is not limited to, claims or damages based on the infringement of patents, copyrights, mask work and/or other intellectual property rights.Certain intellectual property owned by Chirp Microsystems and described in this document is patent protected. No license is granted by implication or otherwise under any patent or patent rights of Chirp Microsystems. This publication supersedes and replaces all information previously supplied. Trademarks that are registered trademarks are the property of their respective companies. Chirp Microsystems sensors should not be used or sold in the development, storage, production or utilization of any conventional or mass-destructive weapons or for any other weapons or life threatening applications, as well as in any other life critical applications such as medical equipment, transportation, aerospace and nuclear instruments, undersea equipment, power plant equipment, disaster prevention and crime prevention equipment.©2020 Chirp Microsystems. All rights reserved. Chirp Microsystems and the Chirp Microsystems logo are trademarks of Chirp Microsystems, Inc. The TDK logo is a trademark of TDK Corporation. Other company and product names may be trademarks of the respective companies with which they are associated.©2020 Chirp Microsystems. All rights reserved.。
哈凯产品有限公司产品说明书

T9-I.T9-L1.T9-2LFrom...American Hakko Products, Inc.28920 N. Avenue Williams.Valencia, CA 91355 Tel: (661) 294-0090 Fax: (661) 294-0096 AHP14 Rev 2000-01For pricing information, please contact your local American Hakko representative or our customer service department at (661) 294-0090.American Hakko Products, Inc.P R O D U C T B U L L E T I NBulletin No: PB260Issue Date: November 5, 2007 Product:FM-203 Dual Port Soldering StationPart No:FM203-01 FM203-DPComments:The Hakko FM-203 is a Dual Port high performance soldering station. Even when soldering lead-free solders the high performance allows loweroperating temperatures. The soldering station can operate any of the following hand pieces, FM-2027 Soldering Iron, FM-2022 Parallel Remover (SMD tweezer), FM-2023 Mini Parallel Remover (SMD mini tweezer), FM-2024 Desoldering Module, and/or FM-2026 Nitrogen Soldering Iron. The soldering iron and desolder tool can be used in either or both ports and the tweezers are limited to one port with a soldering or desoldering iron in the other port.The station features a programmable sleep mode of 0-29 minutes or auto-power shut off at 30 minutes. Sleep mode, auto power shut off and tip temperature can be programmed separately for each port. The sleep mode reduces the tip temperature to approximately 200ºC (400ºF) after the programmed time (0-29 minutes). The lower tip temperature will reduce oxidation of the tip and improve the tip performance. When in sleep mode the tip will quickly return to temperature after the iron is removed from the holder.When utilizing the FM-2027 Soldering Iron the station uses the T15 series composite tip. The composite tip is a soldering tip in which a heating element and sensor are integrated with ceramic. Despite its highly compact design, the tip offers superior thermal response and greatly improved thermal recovery. T15 series tips are available in a wide variety of tip shapes and can also be used with the Hakko FM-203, FP-102 and FM-202 soldering stations. Any tip can be operated at temperatures 200 - 450ºC (400 - 840ºF). The station includes a card lock system to lock the preset soldering temperature. With the card removed operators can not adjust the working temperature.The FM-2022 uses T16 tips, The FM-2023 uses T9 tips, The FM-2024 uses N3 nozzles and The FM-2026 uses T17 tips.Documentation Provided By HMC ElectronicsFrom...American Hakko Products, Inc.28920 N. Avenue Williams.Valencia, CA 91355 Tel: (661) 294-0090 Fax: (661) 294-0096 AHP14 Rev 2000-01Specifications:FM-203 Soldering Station Power Consumption 140W 120VTemperature Range 200 - 450ºC (400 - 840ºF) Temperature Stability ±5ºC (±9ºF) Temperature Accuracy±15ºC (±27ºF)Soldering Iron (No.FM-2027) Power Consumption 70W (24V) Tip to Ground Resistance < 2Ω Tip to Ground Potential < 2mV Cord Length1.2m (47 in.) Total Length (w/o Cord)with 2.4D soldering tip attached 188mm (7.4 in.) Weight (w/o Cord)with 2.4D soldering tip attached30g (1.0 oz.)StationOutput 24V Dimensions 120(W) x 120(H) x 190(D)mm (4.7 x 4.7 x 7.5 in.) Weight (w/o cord)2.7kg (5.9 lb.) Contents:Part No.NameFM203-01 FM203-DPN/AFM-203 soldering station1 1 FM2027-02 Connector 12B2387 Power cord 1 1 B2972 Control card 1 1 B3219 Sleeve assembly, Green, anti-bacterial 1 1 B3216 Sleeve assembly, Yellow, anti-bacterial 0 1 B2300 Heat-resistant pad 1 2 FH200-01Iron Holder, Sleep, w/ 599B12B3253 Connecting cable 1 2 B2756 Tip tray1 1 N/A Instruction manual1 1The FM2023-DP includes two FM-2027 connectors and sleep holders. Tips not included.Documentation Provided By HMC ElectronicsFrom...American Hakko Products, Inc.28920 N. Avenue Williams.Valencia, CA 91355 Tel: (661) 294-0090 Fax: (661) 294-0096 AHP14 Rev 2000-01Accessories/Replacement Parts:Part No. NameSpecificationFM2027-01 HAKKO FM-2027 w/ Yellow Sleeve Assembly Does not include tip or holder B3216 Sleeve Assembly Yellow (Lock-type, Antibacterial) B3217 Sleeve Assembly Orange (Lock-type, Antibacterial) B3218 Sleeve Assembly Blue (Lock-type, Antibacterial) B3219Sleeve Assembly Green (Lock-type, Antibacterial)A1536 Cleaning sponge GreenFM2022-05 Conversion kit FM-2022 Parallel Remover with sleep holder and cable. Tips not included. FM2023-05 Conversion kit FM-2023 Mini Parallel Remover with sleep holder and cable. Tips included. FM2024-21 Conversion kit/120 V FM-2024 Desoldering Module with sleep holder and cable. Nozzle not included. FM2026-06 Conversion kit FM-2026 Nitrogen Iron with sleep holder and cable. Tips not included.FM2027-03Conversion kitFM-2027 Soldering Iron with sleep holder and cable. Tips not included.Tips and Nozzles:See PB258 for T15 tip list for HAKKO FM-2027Tips for HAKKO FM-2022Part No. Part Name SpecificationsT16-1001 Tip / CHIP 0.5I T16-1002 Tip / CHIP 0.5C T16-1003 Tip / CHIP 1L T16-1004 Tip / CHIP 2L T16-1005 Tip / SOP 6L T16-1006 Tip / SOP 8L T16-1007 Tip / SOP 10L T16-1008 Tip / SOP 13L T16-1009 Tip / SOP 16L T16-1010 Tip / SOP 20L T16-1011 Tip / SOP 25L T16-1012 Tip / SOP 18L T16-1013Tip / CHIP 3LDocumentation Provided By HMC ElectronicsFrom...American Hakko Products, Inc.28920 N. Avenue Williams.Valencia, CA 91355 Tel: (661) 294-0090 Fax: (661) 294-0096 AHP14 Rev 2000-01Tips for HAKKO FM-2023Part No. Part Name SpecificationsT9-I Tip / CHIP I T9-L1 Tip / CHIP 1L T9-L2Tip / CHIP 2LNozzles for HAKKO FM-2024Part No. Part NameSpecificationsN3-06 Nozzle / 0.6mm (0.02 in.) N3-08 Nozzle / 0.8mm (0.03 in.) N3-10 Nozzle / 1.0mm (0.04 in.) N3-13 Nozzle / 1.3mm (0.05 in.) N3-16 Nozzle / 1.6mm (0.06 in.) N3-20 Nozzle / 2.0mm (0.08 in.) N3-23 Nozzle / 2.3mm (0.10 in.)N3-L10 Long Nozzle / 1.0mm (0.04 in.)Tips for HAKKO FM-2026Part No. Part NameSpecificationsT17-B2 SHAPE-0.5B Conical T17-BC1 SHAPE-1BC Bevel T17-BC2 SHAPE-2BC Bevel T17-BC3 SHAPE-3BC BevelT17-BCF1 SHAPE-1BC Bevel Tinned on the soldering surface onlyT17-BCF2 SHAPE-2BC Bevel Tinned on the soldering surface onlyT17-BCF3 SHAPE-3BC BevelTinned on the soldering surface only T17-BL SHAPE-B Long Shape Conical T17-D08 SHAPE-0.8D Chisel T17-D16 SHAPE-1.6D Chisel T17-D24 SHAPE-2.4D Chisel T17-J02 SHAPE-0.2J Bent T17-KF SHAPE-KF Knife T17-KR SHAPE-KR Knife T17-KUSHAPE-KU KnifeAvailable:November 6, 2007Documentation Provided By HMC ElectronicsT9-I.T9-L1.T9-2L。
HOCHIKI ANALOG SENSORS BASES 安装指南说明书
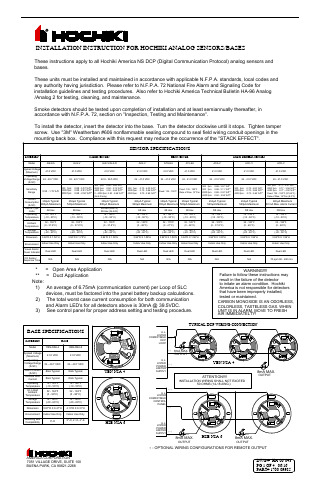
Visual Alarm/ Power Indicator
CO Sensor Response Time
Dual LED N/A
Indoor Use Only Dual LED N/A
Indoor Use Only Dual LED N/A
Indoor Use Only Dual LED N/A
Indoor Use Only Indoor Use Only
) &
) &
350ȝ$7\SLFDO ȝ$0D[LPXP
88 Hex ) &
) &
) &
350ȝ$7\SLFDO ȝ$0D[LPXP
41.0 VDC
41.0 VDC
41.0 VDC
41.0 VDC
24 - 41.0 VDC
24 - 41.0 VDC
24 - 41.0 VDC
24 - 41.0 VDC
300 fpm: 2000 fpm: 4000 fpm:
0.70 - 4.00 %/ft* 0.70 - 3.86 %/ft** 0.70 - 2.65 %/ft**
BASE
Model
YBN-NSA-4
Applied Voltage (Maximum)
41.0 VDC
Operating Voltage Range
(S-SC) Alarm Current
(S-SC)
Remote LED Current Operating
Temperature
UL Listed Ambient Temperature
Current Consumption
(S-SC)
Device Type Code
NorthStar Rim Tach 6200 Digital Tachometer 使用说明书

NorthStar T M brandInstruction ManualRim Tach® 6200Digital TachometerDesigned for use in4.5” 56C-Face, Coupled, Foot Mounted,or Pulley Driven ApplicationsCustomer Service: Tel.: +1.800.873.8731 Fax: +1.847.662.4150 custserv@ Technical SupportTel.: +1.800.234.8731Fax: +1.847.782.5277northstar.techsupport@d Website: *791-1003-00*Table of ContentsChapter/Paragraph/Illustration Page 1 Introduction (4)Safety Summary (4)1.0General (5)1.11.2 Description (5)Figure 1: 6200 Dimensional Drawing (5)Safety Summary (6)1.32 Installation (7)2.0 Inspection and Unpacking (7)Figure 2: 6200 Spare Parts (7)2.1 Painting Considerations (8)2.2 56 C-Face Bracket Mounting (8)Figure 3: Model 6200 56 C Bracket Mounting (8)2.3 Foot Mounting (9)Figure 4: Model 6200 Foot Mounting (9)2.4 Pulley Mounting (10)Figure 5: Model 5200 Pulley Mounting (10)2.5 Sensor Module Installation (11)Figure 6: Sensor Module Installation (11)Figure 7: Sensor Module Installation (Continued (12)Electrical Installation (13)2.62.6.1 Quick Release Connector Hood Wiring (13)Figure 8: Quick Release Connector Installation (14)Methods and apparatus disclosed and described herein have been developed solely on company funds of Dynapar No government or other contractualsupport or relationship whatsoever has existed which in any way affects or mitigates proprietary rights of Dynapar in these developments. Methods andapparatus disclosed herein may be subject to U.S. Patents existing or applied for. Dynapar reserves the right to add, improve, modify, or withdraw functions,design modifications, or products at any time without notice. Dynapar shall not be liable for errors contained herein or for incidental or consequentialdamages in connection with furnishing, performance, or use of this material.CHAPTER 1INTRODUCTION1.0 Safety SummaryHigh current, voltage, and rotating parts can cause serious or fatal injury. The use of electric machinery, like all other uses of concentrated power and rotating equipment, may be hazardous. Only qualified personnel should install, operate, and maintain electric machinery in accordance with applicable provisions of the National Electrical Code and sound local practices. Failure to comply with these precautions or with specific warnings elsewhere in this manual violates safety standards of design, manufacture, and intended use of the instrument. Dynapar assumes no liability for the customer's failure to comply with these requirements.Rotating MachineryAvoid contact with rotating parts. Avoid by-passing or rendering inoperative any safety guards or protection devices. Avoid extended exposure in close proximity to machinery with high noise levels. Use proper care and procedures in handling, lifting, installing, operating and maintaining the equipment.Before InstallationSafe maintenance practice with qualified personnel is imperative. Before starting maintenance procedures, be positive that, (1) equipment connected to the shaft will not cause mechanical rotation, (2) main machine windings have been disconnected and secured from all electrical power sources, and (3) all accessory devices associates with the work area have been de-energized. If high potential insulation test is required, follow procedures and precautions outlined in NEMA standards MG-1. GroundingImproperly grounding the frame of the machine can cause serious or fatal injury to personnel. Grounding of the machine frame and structure should comply with the National Electrical Code and with sound local practices. Check wiring diagram before connecting power.Do Not Operate In An Explosive AtmosphereDo not operate the instrument in the presence of flammable gases or fumes. Operating any electrical instrument in such an environment constitutes a definite safety hazard.Keep Away From Live CircuitsOperating personnel must not remove instrument covers. Qualified maintenance personnel must make component replacement and internal adjustments. Do not replace components with power cable connected. To avoid injuries, always disconnect power and discharge circuits before touching them.Do Not Substitute Parts Or Modify InstrumentDo not install substitute parts or perform any unauthorized modification to the instrument. Introducing additional hazards is dangerous. Return the instrument to an authorized Dynapar representative for service and repair to ensure that safety features are maintained.Dangerous Procedure CautionsA CAUTION heading precedes potentially dangerous procedures throughout this manual. Instructions in the warnings must be followed.1.1 GeneralThese instructions do not claim to cover all details of variation in equipment or to provide for every possible contingency or hazard met in connection with installation, operation, and service. If further information is desired or should particular problems arise which are not covered sufficiently for the purchaser’s purposes, please contact Dynapar, or one of its designated representatives.1.2 DescriptionThe RIM Tach® 6200 is a high performance and reliable Digital Tachometer, designed to provide position and velocity feedback from both AC and DC electric motors with pulse counts ranging from 60 through 2048 pulses per revolution. The RIM Tach6200 utilizes rugged ductile iron casting construction and provides interchangeable sensor modules and a magneto-resistive technology capable of withstanding the harshest industrial environments. This ensures precise and consistent digital motor speed feedback.The NorthStar RIM Tach® 6200 is mounted in a variety of ways and utilizes a patented, heavy-duty, one piece, magneto-resistance sensor module with encapsulated surface mount electronics. The encapsulation provides resistance to water, oil mist, dirt, high temperatures, and other harsh environments. The sensor module includes a 10-pin quick connector requiring only a screwdriver for final electrical installation. The non-contact magneto-resistive sensor and rugged magnetized pulse wheel are designed and machined to function properly without any adjustments. The RIM Tach 6200 provides precise, reliable speed signals for many monitoring and control applications, and is a standard feedback device for AC and DC variable speed drives. The unit is bi-directional providing square wave outputs.Figure 1: 6200 Dimensional Drawing1.3 SpecificationsElectrical SpecificationsFrequency Response 0 - 120 kHzPulse Code A, B, Z (Index), and complements (A, B, Z)Output Phases A phase, B phase @ quadrature 90°, Z phase: Once per rev. (gated) Pulse Duty Cycle 50 ± 15% (within defined mechanical specifications) Quadrature Accuracy 90 ± 22° (within defined mechanical specifications)Output Type High speed, differential line driverRise and Fall Time Less than 1µs @ 10,000 pf typical loadCurrent Consumption 45 mA typical plus line driver loadOutput Current 150 mA maximum continuousESD Protection 2kVMechanical SpecificationsEnclosure Configurations 4.5-inch diameter, 56 C motor face or accessory flange to meetNEMA MG1-4 standards; foot mount with 4 slotted bolt holes Material Ductile iron cast enclosure, stainless steel probe moduleShaft Interfacing 0.625 inch diameter x 1.87 inch long, 3/16” square-parallel key,optional double ended shaft, optional 14 mm shaft with metric key Maximum Operational Speed 7,000 RPM (120khz)Axial, Radial Load 15 lbf axial, 50 lbf radialSlew Rate 3600 RPM/secondApproximate Box Weight 28lbs.Box Dimensions 21” x 10” x 10”Environmental SpecificationsOperational Temperature -40° to +80° COperational Humidity Range Maximum of 90%Chemical Resistance Salt spray, most solvents, mild acids and basesVibration Minimum 18 g’s RMS, 5-2000 Hz shock spectrumShock (Sensor Module) 1 meter drop tested, min. 30g’sInterface SpecificationsPower +5.0 to +15.0 VDCOutput Differential output swinging between Vcc - 0.6V and ground Connector 10 pin industrial latching connector with ½ inch NPT fitting,IP-65 NEMA 4, 12 ratedSuggested Cable 22 - 16 AWG, 10 conductor, shielded, twisted pairSpecifications subject to change without notice.CHAPTER 2INSTALLATION2.0 Inspection and UnpackingInspect shipping container for external damage. All claims for damage (apparent or concealed) or partial loss of shipment must be made in writing to Dynapar within (5) days from receipt of goods. If damage or loss is apparent, please notify the shipping agent immediately.Open shipping container and locate the packing list. The packing list is included to verify that all components, accessories, and manual were received. Please use the packing list to check off each item as the unit is unpacked. Inspect for damage. We recommend that the shipping container be retained for future shipping, storage, or return to factory purposes.If any equipment was damaged in transit, be sure to file proper claims promptly with the carrier and insurance company. Please advise us of such filing. In case of part shortages, advise us immediately. Dynapar cannot be responsible for any missing parts unless notified within 60 days of shipment.The RIM Tach® 6200 utilizes a modular construction that permits the user to configure the unit as a one or two signal output tachometer. Sensor modules are universal and interchangeable. If one output requires replacement, simply remove four screws, and replace with a new sensor module. No electrical adjustment or alignment is required. After unpacking the unit and verifying receipt of the items listed in the packing list, you may proceed with mechanical installation.The Model 6200 has no user maintainable components. The bearings are permanently lubricated and sealed for the operational life of the unit. The Pulse Wheel also needs no service. Disassembly of the unit will void the Warranty. The magnetoresistive sensor end electronics modules need no adjustment, but can be replaced by the user in case of failure.Figure 2: 6200 Spare Parts2.1 Painting ConsiderationsThe enclosure may be painted. Please pay attention to the following considerations.NOTECorrosion preventative coating has been applied to the enclosure. Standard degreasingpractices must be followed before applying paint.•Do not hinder the latches on the connector if the connector is painted.•If the enclosure is painted before the sensor module(s) is added, be sure to mask off the area where the sensor module(s) will be placed. The module must mate directly to the enclosure with nothing between. Failure to do this will degrade the alignment of the system and may cause it to fail.•Ensure excess paint runoff does not clog enclosure drain holes.2.2 56 C-Face / Bracket MountingFlexible couplings are generally used to couple the Model 6200 to its driver (NorthStar part number RIMFLEX-5858). There are a wide variety of speeds, loads, environment, and alignment conditions found in various applications. If there is doubt to suitability, we recommend you consult the flexible coupling manufacturer on your particular application requirement. One simple design of coupling can not fulfill all potential applications or conditions.1.Mount the C-Face adapter bracket (not supplied) onto the motor per manufacture’s instructions. See Figure 3. Be surethe 4.5 inch C-Face is concentric to the motor shaft.2.Insert flexible coupling onto the motor shaft. Do not tighten at this time.3.Place the Model 6200 onto the4.5 inch C-Face. Insert and tighten four 3/8-16 UNC bolts. Be sure it is seated flat againstthe mounting bracket.4.Connect flexible coupling onto the Model 6200 shaft and tighten per manufacturer’s specifications.5.Rotate the shaft by hand to ensure free rotation.6.Place or replace appropriate safety shields.Figure 3: Model 6200 56 C Face/ Bracket Mounting2.3 Foot MountingFoot mounting brackets are included on the bottom of the Model 6200. The bolt hole pattern in slotted to permit a measure of adjustment. Flexible couplings are generally used to couple the Model 6200 to its driver (NorthStar part number RIMFLEX-5858). There are a wide variety of speeds, loads, environment, and alignment conditions found in various applications. If there is doubt to suitability, we recommend you consult the flexible coupling manufacturer on your particular application requirement. A simple coupling design can not fulfill all potential applications or conditions.1.Place the Model 6200 mounting bracket in the approximate final position.NOTEThe mounting should be strong enough to sufficiently support the weight of the Model6200 ( approximately 25 pounds) without excessive deflection due to load orvibration. Deflection can cause erroneous outputs and shorten the operational life ofthe unit.2. Insert, but do not tighten, four 3/8-16 UNC bolts into the mounting bracket holes.3. Insert and connect flexible coupling onto the motor and Model 6200 shaft per manufacture’s specifications.NOTEThe life expectancy of the flexible coupling and Model 6200 are influenced by theaccuracy to which the shafts are aligned in this step.4. Tighten mounting bolts to nominal 30 foot-pounds.5. Rotate shaft by hand to ensure free rotation.6. Place or replace appropriate shields.Figure 4: Model 6200 Foot Mounting2.4 Pulley Mounting1. Mounting the Model 6200 onto mounting bracket with four 3/8-16 UNC bolts through foot mounting bracket holes.NOTEThe mounting bracket should be strong enough to sufficiently support the weight of the Model 6200 (approximately 25 pounds) without excessive deflection of play due to load or excessive vibration. Deflection can cause erroneous outputs and shorten operational life of the unit.2. Mount and connect 5/8 inch I.D. pulley on to the Model 6200 input shaft.3. Install a tension belt according to the manufacturer’s specifications. If the belt tension is too light it can cause pulleyslippage or backlash, thereby creating an erroneous signal output. However, for maximum operational life of the Model 6200, a belt tension loading of less than 40 pounds should be used.Model6200Figure 5: Model 6200 Pulley Mounting2.5 Sensor Module InstallationTo install the sensor Module, perform the following steps. See Figure 6.1. Remove sensor module and mating connector from packaging.CAUTION!Although the device is protected from Electrostatic Discharges up to 2000 Volts, standard ESDprecautions should be followed.2. Separate mating connector from sensor module by releasing the two latches.CAUTION!Use caution when handling the sensor module. The sensor at the end of the module can be easilydamaged by sharp objects. The sensor module can be damaged by sudden shocks (dropping,hammer blows, etc.).3. Insert sensor module into opening in enclosure. The sensor assembly is keyed to ensure proper.4. Locate four shoulder screws. Insert shoulder screws through clearance holes in sensor module and into tapped holes inenclosure. Tighten to a nominal 5 inch-pounds.CAUTION!There should not be a gap between the lip on the housing and the enclosure. The stainless steelsensor module is designed to seat in metal to metal contact with the enclosure. Ensure that nogaskets, paint, dirt, etc., interferes with the complete seating of the module in the enclosure.Figure 6: SensorModule InstallationSensor Must Mate Directlyto Enclosure Surface Figure 7: Sensor Module Installation (Continued)2.6 Electrical InstallationElectrical connections are made to the sensor module through a standard 1/2 inch NPT liquid tight flexible conduit. The nipple length may be changed to extend the outlet box if desired. Interconnection cable recommendations are as follows: stranded copper, 22 through 16 gage, braided or foil with drain wire shielding 0.05 µF maximum total mutual or direct capacitance, outer sheath insulated. Shrink tubing may be placed over any wires without insulation. For lengths over 100 feet, use 18 gage or larger, to a maximum of 1000 feet. If shielded twisted pair wire is used, do not cross channels. Keep each pair of complementary channel outputs together in a single twisted pair (e.g., A and A complement).CAUTION!Reversing power and common will not damage the unit. However, applying power toany of the sensor outputs may cause damage.Table 1. Signal Coding TableSignal Connector Pin Pigtail Cable MS 3102E18-IT#CommonBAZ *No Connection Vcc (5-15 VDC) /B/A/Z *Shield12345678910BlackGreenBlueViolet-----RedYellowGrayOrangeBraidAEDC-----BHGIJ* Applies only to units with index pulse capability.# Pinouts are for the sensors with the MS 3102E18IT connectorNOTEThe shield in the sensor module is isolated from the frame of the encoder for maximumnoise immunity. The shield wire or pin should be connected to the shield of the cable andthat of the drive or other receiving device.2.7 Quick Release Connector Hood WiringTo install the Quick Release Connector, perform the following steps.1.Remove the four screws from the mating connector housing that hold the terminal block in place. Remove terminalblock from housing.2.Insert wiring through liquid tight flexible seal and mating connector housing. Leave enough wire exposed tocomfortably reach the terminal block. Wire to terminal block according to wire code in Table 1. A similar wiring list is attached to enclosure.NOTEThere are two orientations of the connector hood. The terminal block can be insertedeither way so the connector hood points up or down. Choose the direction best for yourapplication.4. Tighten Liquid Tight fitting on housing. OPTIONAL: In some hostile environments, seal between connector body andSensor Module can be improved by smearing a sealant (silicone grease, etc.) on the neoprene seal of the connector. 5. Mate connector into place on sensor mount and snap the two latches into place. If only one sensor is being installed, ensure cover plate is installed over other sensor hole.Terminal BlockFigure 8: Quick Release Connector InstallationCustomer Service: Tel.: +1.800.873.8731 Fax: +1.847.662.4150 custserv@d Technical SupportTel.: +1.800.234.8731Fax: +1.847.782.5277northstar.techsupport@d Website: 。
赛米控丹佛斯 SEMIPACK 晶闸管 二极管模块 SKKH 107 16 E 数据表

Rev. 3.0–31.05.20221®1SKKHThyristor / Diode ModulesSKKH 107/16 E Features*•Heat transfer through aluminium oxide ceramic insulated metal baseplate •UL recognized, file no. E63532Typical Applications•Rectifier for motor drives •Process control•Rectifier for power suppliesAbsolute Maximum Ratings SymbolConditions Values UnitChip I T(AV)sin. 180°T j =130°C T c =85°C 119A T c =100°C 91A I TSM 10ms T j =25°C 2250A T j =130°C 1900A i 2t10ms T j =25°C 25313A²s T j =130°C18050A²s V RSM T j =25°C 1700V V RRM T j =25°C 1600V V DRM T j =25°C 1600V (di/dt)cr T j =130°C 140A/µs (dv/dt)cr T j =130°C1000V/µs T j -40...130°C Module T stg -40 (125)°C V isola.c.; 50 Hz; r.m.s.1min 3000V 1s3600VCharacteristics SymbolConditions min.typ.max.UnitChip V T T j =25°C,I T =300A 1.6 1.75V V T(TO)T j =130°C 0.80.90V r T T j =130°C2.803.35m ΩI DD ;I RD T j =130°C,V DD = V DRM ; V RD = V RRM 20mA t gd T j =25°C,I G =1A, di G /dt =1A/µs 1µs t gr V D = 0.67 * V DRM 2µs t q T j =130°C 200µs I H T j =25°C150250mA I L T j =25°C,R G =33Ω300600mA V GT T j =25°C,d.c. 2.5V I GT T j =25°C,d.c.100mA V GD T j =130°C, d.c.0.25V I GD T j =130°C, d.c.4mA R th(j-c)continuous DC per chip 0.15K/W per module 0.075K/W R th(j-c)sin. 180°per chip 0.2K/W per module 0.1K/W R th(j-c)rec. 120°per chip 0.21K/W per module0.105K/WModule R th(c-s)chip 0.09K/W module 0.05K/W M s to heatsink M5 4.25 5.75Nm M t to terminals M52.553.45Nm a 5 * 9.81m/s²w75g2Rev. 3.0–31.05.2022© by SEMIKRON© by SEMIKRON Rev. 3.0–31.05.202234Rev. 3.0–31.05.2022© by SEMIKRONThis is an electrostatic discharge sensitive device (ESDS) due to international standard IEC 61340.*IMPORTANT INFORMATION AND WARNINGSThe specifications of SEMIKRON products may not be considered as guarantee or assurance of product characteristics("Beschaffenheitsgarantie"). The specifications of SEMIKRON products describe only the usual characteristics of products to be expected inSKKHtypical applications, which may still vary depending on the specific application. Therefore, products must be tested for the respective application in advance. Application adjustments may be necessary. The user of SEMIKRON products is responsible for the safety of their applications embedding SEMIKRON products and must take adequate safety measures to prevent the applications from causing a physical injury, fire or other problem if any of SEMIKRON products become faulty. The user is responsible to make sure that the application design is compliant with all applicable laws, regulations, norms and standards. Except as otherwise explicitly approved by SEMIKRON in a written document signed by authorized representatives of SEMIKRON, SEMIKRON products may not be used in any applications where a failure of the product or any consequences of the use thereof can reasonably be expected to result in personal injury. No representation or warranty is given and no liability is assumed with respect to the accuracy, completeness and/or use of any information herein, including without limitation, warranties of non-infringement of intellectual property rights of any third party. SEMIKRON does not assume any liability arising out of the applications or use of any product; neither does it convey any license under its patent rights, copyrights, trade secrets or other intellectual property rights, nor the rights of others. SEMIKRON makes no representation or warranty of non-infringement or alleged non-infringement of intellectual property rights of any third party which may arise from applications. Due to technical requirements our products may contain dangerous substances. For information on the types in question please contact the nearest SEMIKRON sales office. This document supersedes and replaces all information previously supplied and may be superseded by updates. SEMIKRON reserves the right to make changes.5。
CH9121网络和UART透明传输芯片说明书
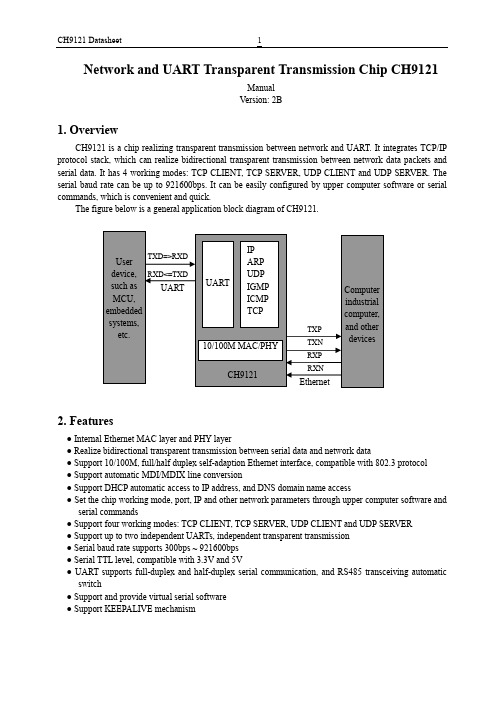
Network and UART Transparent Transmission Chip CH9121ManualVersion: 2B1.OverviewCH9121 is a chip realizing transparent transmission between network and UART. It integrates TCP/IP protocol stack, which can realize bidirectional transparent transmission between network data packets and serial data. It has 4 working modes: TCP CLIENT, TCP SERVER, UDP CLIENT and UDP SERVER. The serial baud rate can be up to 921600bps. It can be easily configured by upper computer software or serial commands, which is convenient and quick.The figure below is a general application block diagram of CH9121.2.Features●Internal Ethernet MAC layer and PHY layer●Realize bidirectional transparent transmission between serial data and network data●Support 10/100M, full/half duplex self-adaption Ethernet interface, compatible with 802.3 protocol●Support automatic MDI/MDIX line conversion●Support DHCP automatic access to IP address, and DNS domain name access●Set the chip working mode, port, IP and other network parameters through upper computer software andserial commands●Support four working modes: TCP CLIENT, TCP SERVER, UDP CLIENT and UDP SERVER●Support up to two independent UARTs, independent transparent transmission●Serial baud rate supports 300bps ~ 921600bps●Serial TTL level, compatible with 3.3V and 5V●UART supports full-duplex and half-duplex serial communication, and RS485 transceiving automaticswitch●Support and provide virtual serial software●Support KEEPALIVE mechanism3.PackageChipPackageName DescriptionCH9121 LQFP64M LQFP package; 64 pins; package body 10 x10mm 4.PinsCH9121 Pin No.PinNamePin Type Pin description2, 12, 17, 21, 29, 40, 42, 45, 63 VCC33 Power3.3V positive power input, require an external 0.1uF powerdecoupling capacitor6, 19, 28, 43, 54, 64 VCC18 Power1.8V positive power input, require an external 0.1uF powerdecoupling capacitor3, 9, 13, 18, 20,37, 41, 44, 48GND Power Common ground14, 15, 16, 22,23, 24, 25, 26,27, 34, 35, 38,39, 47, 49, 50,61, 62NC - Reserved, suspended1 RSETE Input Connected with an external 18K resistor to ground4 RXP EthernetsignalEthernet RXP signal5 RXN Ethernet Ethernet RXN signalsignal7 TXP EthernetsignalEthernet TXP signal8 TXN EthernetsignalEthernet TXN signal10 XI Input Input of the crystal oscillator, requires an external 30MHzcrystal11 XO Output Inverted output of crystal oscillator, requires an external 30MHzcrystal30 TCPCS1 Output In TCP client mode, connection status indicator of port 1, activeat low level31 RUN Output CH9121 running status indicator pin, multiplexed as ISPupgrade pin32 CFGEN Input Network configuration enable pin, detects when power-up, configuration disabled when at low level33 TCPCS2 Output In TCP client mode, connection status indicator of port 2, activeat low level36 RSTI Input External reset input, active at low level, built-in pull-up resistor 46 DIR2 Output Used to control RS485 receiving/transmitting switch of UART251 DIR1 Output Used to control RS485 receiving/transmitting switch of UART152 ACT# Output Ethernet connection communication indicator LED drive pin53 LINK# Output PHY connection indicator LED, active low55 RXD2 Input Serial data input of UART2, built-in pull-up resistor(Off by default)56 TXD2 Output Serial data output of UART2 (Off by default)57 RXD1 Input Serial data input of UART1, built-in pull-up resistor(On by default)58 TXD1 Output Serial data output of UART1 (On by default)59 RESET InputRestore factory settings, chip power-on detection, active at low level60 CFG0 InputUART configuration mode set pin, built in pull-up. If low level is detected, enter UART configuration mode. Exit the mode if high level is detected5.Function5.1. Function DescriptionCH9121 is a chip for transparent transmission between network and UART, and realizes bidirectional transparent transmission of serial data and network data. It supports 4 working modes (TCP CLEINT/SERVER, UDP CLIENT/SERVER), and the serial baud rate supported ranges from 300bps to 921600bps. Before use, the network parameters and UART parameters of the chip shall be configured by upper computer software NetModuleConfig.exe or serial commands. After the configuration is completed, CH9121 will save the configuration parameters to the internal storage space. And after the chip is reset, CH9121 will work according to the saved configuration value.The basic parameters of CH9121 include: name, MAC address display, dynamic access IP address setting, manual IP address setting (including CH9121 IP address, subnet mask, default gateway), and UART negotiation configuration.The name is mainly for the convenience of CH9121 module management within the LAN, with the length of not more than 20 bytes. The MAC address field shows the MAC address of the currently selectedmodule. There are two ways for CH9121 to set network parameters. 1) DHCP, that is, it automatically obtains network parameters from the gateway device with DHCP SERVER function; 2) manual setting. UART negotiation configuration function is to enter serial configuration mode by handshaking through the UART, which is disabled by default.CH9121 port parameters include: network mode, local port, target IP/domain name, destination port, serial baud rate/data bit/stop bit/parity check bit, network cable disconnection processing, RX packet length, RX packet timeout interval, network connection operation.The network mode (TCP SERVER/CLIENT, UDP SERVER/CLIENT), destination IP address, and local/destination port are the basic parameters of network communication. The destination IP address can also be accessed by domain name. The serial baud rate ranges from 300bps to 921600bps (the baud rate error of the serial port transmitting signal is less than 0.3%, and the allowable baud rate error of the serial port receiving signal is not less than 2%). It supports 5/6/7/8 data bits, 1/2 stop bits, odd/even/no parity check, blank 0, and mark 1 check mode. The network cable disconnection processing means that when the network cable is disconnected, CH9121 actively closes the connection or does not take any action. The length range of RX packet is 1-1024, which means that when the length of CH9121 UART receiving data reaches the set length, CH9121 will immediately packet the serial data and send it out via network. The timeout time setting range is 0-200, and the timeout unit is about 5ms. For example, when the timeout is 1, the data length of the serial port receiving buffer does not reach the length of the RX packet, and the serial port does not receive a new one in more than 5ms, the serial port timeout will occur. After the serial port timeout occurs, CH9121 will send the data received by the serial port over the network. When the timeout time is set to 0, the internal hardware timeout mechanism will be enabled (no new data is received after 4 data times), which is suitable for occasions where real-time requirements are high and large quantities of data are sent and received. Clear serial port buffer setting refers to how the data received by the serial port is processed before the network connection is established, the data is cleared (discarded) or retained after TCP connection.5.2. Default ConfigurationWhen CH9121 leaves factory, port 2 is closed and port 1 works in TCP CLIENT mode by default. The default parameters related to the network are as follows:(1)Device IP: 192.168.1.200(2)Subnet mask: 255.255.255.0(3)Default gateway: 192.168.1.1(4)Module port: 2000(5)Destination IP: 192.168.1.100(6)Destination port: 1000(7)Number of reconnection: unlimitedUART related default parameters are:(1)Baud rate: 9600(2)Timeout: 0(3)Data bit: 8. Stop bit: 1. Parity check bit: No(4)Clear UART buffer: Never6.Parameters6.1. Absolute Maximum ValueCritical value or exceeding the absolute maximum value may cause the chip to work abnormally or even be damaged.Name Parameter description Min. Max. UnitTA Ambient temperature during operation VCC33=3.3VVCC18=1.8V-40 85 ℃TS Ambient temperature during storage -55 125 ℃VCC33 Supply voltage (VCC33 connects to power, GND to ground) -0.4 4.2 V VCC18 Supply voltage (VCC18 connects to power, GND to ground) -0.4 2.3 V VIO Voltage on input or output pins -0.4 VCC33+0.4 V VIO5 Voltage on input or output pins that support 5V withstand voltage -0.4 5.4 V6.2. Electrical ParametersTest Conditions: TA=25℃, VCC33=3.3V, VCC18=1.8VName Parameter description Min. Typ. Max. UnitVCCxx Supply voltage VCC33 2.7 3.3 3.6V VCC18 1.65 1.8 1.95ICC Total supply current duringoperationVCC33=3.3V 160 190 mAVIL Low level input voltage -0.4 0.7 V VIH High level input voltage 2.0 VCC33+0.4 V VOL Low level output voltage (4mA draw current) 0.4 V VOH High level output voltage (4mA output current) VCC33-0.4 VIUP Input current at the input terminal with built-inpull-up resistor20 40 100 uAIDN Input current at the input terminal with built-inpull-down resistor-20 -40 -100 uAVR Voltage threshold when power-on reset 1.4 1.5 2.5 V7.Applications7.1 Hardware Circuit DesignNote: Due to space limitations, the circuit of the power supply and decoupling capacitors near the 3.3V and 1.8V pins is omitted in the figure, which must be added when designing the circuit. The detailed circuit reference file: CH9121PCB (please download in our official website).U1 is the main control chip CH9121. TXD1 and RXD1 are compatible with 3.3V and 5V level, and the RS485 control pin DIR can be suspended if not used.P1 is RJ45 port, with built-in network transformer, used to connect network equipments such as switches and router. It contains two pairs of Ethernet differential signals.When actually making a PCB, R5-R8, C6, and C7 should be as close as possible to the 5th pin of P1. The 0.1 uF decoupling capacitors for 3.3V and 1.8V pins are omitted in the figure. TXOP (RXIP) and TXON. (RXIN) are differential signals. When wiring, they should be wired close to parallel, and try to provide ground wire or copper coating on both sides to reduce external interference. The length of relevant signals of crystals XI and XO should be shortened as much as possible. In order to reduce the interference of high-frequency clock for the outside, the baselines should be surrounded or copper should be clad around relevant components.。
Christie RF80-K Service Bulletin 082808说明书

RF80-K Service Bulletin 082808 August 28, 2008 P/N 121630-001, 121630-006Subject: Concerns about use of NAVAIR 17-20-AX-930 RF80-K Calibration ProcedureRef: NAVAIR 17-20-AX-930, TD-661, TD-650 Operator’s Manual_________________________________________________________________________________ NAVAIR 17-20-AX-930figure 3 shows connection of a current shunt across the RF80-K output. This can cause serious damage to the RF80-K and will void the warranty. TheRF80-K should be turned on only with a battery connected or to a special test fixture during calibration used only by the factory or authorized Christie Service Center.Steps 4.1.2 through 4.1.13 instruct the technician to run 25-35 amps directly through an external current shunt. This procedure can seriously damage the RF80-K power devices and render the unit unserviceable.Steps 4.2.19 through 4.2.24 instructs the technician to apply between 45-65 volts DC using an external power supply. This exceeds the power rating of the RF80-K components. The RF80-K battery volts metering has a maximum reading of 48 volts which is limited by components on the control PC board. Furthermore, the C1 output capacitor is rated for a maximum of 60 volts DC, exceeding the capacitor’s voltage can cause it to explode.This unauthorized calibration procedure does not address critical areas such as the Discharge Termination Voltages and Reflex Points which are verified using the procedures listed in the TD-650 and TD-661. If these are out of alignment, these need to be adjusted as necessary by the factory or authorized Christie Service Center.The RF80-K Operator’s Manual TD-650 and TD-661 include a simple bench-top calibration procedure which when performed, allows continued service of the unit without removal from the battery shop. Refer to section 5 in the operator’s manual for the specific instructions.In the event the RF80-K fails the bench-top calibration test or has performance problems, we suggest it be sent to the factory or an authorized Christie Service Center for repair, calibration, functional testing and re-certification.We strongly suggest that use of the NAVAIR 17-20-AX-930 RF80-K Calibration be immediately discontinued and users be directed to the operator’s manual for proper calibration procedures.Marvel Aero International, Inc.Christie Distribution & Service Center20381 Lake Forest Drive, Suite B3Lake Forest, CA 91630 USATel: +1 949 829 8264 Fax: +1 949 829 8394********************。