VDA FFA现场失效分析
失效分析基本常识以及操作流程

提交分析报告
任务来源 分析过程
背景描述
分析结果
记录和图片 综合评审
分析实质原因 提出纠正措施
工艺
设计结构 材料
测试方法 使用条件 质量控制
9/24/2019
21
6.0 操作流程-1
9/24/2019
22
6.0 操作流程-2
9/24/2019
23
6.0 操作流程-3
9/24/2019
24
6.0 操作流程-4
30
9.0 FA工程师因该具备的能力
1. 要懂基础的物理科学,对物理对电路都要有 一定的基础,否则无法解释一些本质现象, 思路也不宽。
2. 要熟悉产品封装工艺,这个是失效分析的基 础,不然没法给结论。
9/24/2019
31
9.0 FA工程师因该具备的能力
3. 要懂电路和机械装配图。 4. 熟悉材料科学,会分析各种材料的相关问题。 5. 要对业界的所有失效分析设备,材料分析设
9/24/2019
6
2.0 研究对象和要求
2.1 需要做失效分析的对象
现场使用的失效样品(客诉样品) 可靠性试验失效样品 生产筛选失效样品(特大异常样品)
9/24/2019
7
2.0 研究对象和要求
2.2 失效分析层次要求
任一产品或系统的构成都是有层次的,失效原因也 具有层次性,如系统-单机-部件(组件)-零件(元 件)-材料。
上一层次的失效原因即是下一层次的失效现象。 凭我们现有资源和技术能力,结合产品特性,失效 分析适宜以器件为单元建立失效模式。分析机理达到零 件(如芯片\壳体\滤波片\插芯套组件等)层次即可。
9/24/2019
8
FMEA失效分析与失效模式分析全

擦伤或损坏)。 由于横向性能差而在锻件中出现分离线的失效现象。
11
在服役条件下由于质量恶化而产生失效的原因包括
过载或未预见的加载条件。 磨损(磨蚀、因过度磨损而咬住、粘住、擦伤、气蚀)。 腐蚀(包括化学接触、应力腐蚀、腐蚀疲劳、脱锌、铸铁石
找出被分析对象的“单点故障”。所谓单点故障是指这种故障单独发 生时,就会导致不可接受的或严重的影响后果。一般说来,如果单点 故障出现概率不是极低的话,则应在设计、工艺、管理等方面采取切 实有效的措施。产品发生单点故障的方式就是产品的单点故障模式。
为制定关键项目清单或关键项目可靠性控制计划提供依据。 为可靠性建模、设计、评定提供信息。 揭示安全性薄弱环节,为安全性设计(特别是载人飞船的应急措施、
16
什么是失效分析?
失效分析:考察失效的构件及失效的情景(模式), 以确定失效的原因。
失效分析的目的:在于明确失效的机理与原因。改 进设计、改进工艺过程、正确地使用维护。
失效分析的主要内容:包括明确分析对象,确定失 效模式,研究失效机理,判定失效原因,提出预防 措施(包括设计改进)。
17
失效分析的要点?
失效模式的判断分为定性和定量分析两个方面。在一般 情况下,对一级失效模式的判断采用定性分析即可。而 对二级甚至三级失效模式的判断,就要采用定性和定量、 宏观和微观相结合的方法。
19
一级失效模式的分类
20 主要失效模式的分类与分级
21
如某型涡轮叶片在第一榫齿处发生断裂,通过断口 的宏观特征可确定一级失效模式为疲劳失效。然后 通过对断口源区和扩展区特征分析和对比,并结合 有限元应力分析等,可作出该叶片的断裂模式为起 始应力较大的高周疲劳断裂的判断,即相当于作出 了三级失效模式的判断。
现场失效分析ffa流程word版本

现场失效分析ffa流程word版本英文版On-site Failure Analysis FFA ProcessThe on-site failure analysis (FFA) process is a crucial step in ensuring the reliability and efficiency of equipment, systems, and products. This process involves a thorough investigation of failed components to determine the root cause of the failure, identify corrective measures, and prevent future occurrences.1. Preliminary InspectionUpon arrival at the site, the FFA team conducts a preliminary inspection of the failed component. This involves visual examination, checking for any obvious signs of damage or wear, and recording relevant information such as the make, model, and serial number of the component.2. Documentation and PhotographyDetailed documentation and photography of the failed component are essential for later analysis. This includescapturing images from various angles, documenting the surrounding environment, and noting any specific conditions that may have contributed to the failure.3. Disassembly and InspectionThe FFA team then proceeds to disassemble the failed component, carefully examining each part for signs of damage, corrosion, or wear. This step requires meticulous attention to detail and the use of appropriate tools to avoid further damage.4. Failure AnalysisThe collected data and observations are then analyzed to determine the root cause of the failure. This may involve a combination of visual inspection, microscopy, material testing, and other diagnostic techniques.5. Corrective MeasuresBased on the findings of the failure analysis, the FFA team identifies corrective measures to address the root cause and prevent future failures. This may include replacing worn-outparts, modifying design features, or implementing new maintenance procedures.6. Reporting and Follow-upA detailed report is prepared, summarizing the findings, recommended corrective measures, and any follow-up actions required. This report is shared with relevant stakeholders for review and action. Regular follow-up and monitoring are also conducted to ensure that the implemented corrective measures are effective.ConclusionThe on-site failure analysis FFA process is a vital tool for enhancing the reliability and durability of equipment, systems, and products. By identifying the root causes of failures and implementing effective corrective measures, businesses can minimize downtime, reduce maintenance costs, and maintain the overall performance of their assets.中文版现场失效分析FFA流程现场失效分析(FFA)流程是确保设备、系统和产品可靠性和效率的关键步骤。
VDA FFA现场失效分析教学文案

VDA Field failure analysis 现场失效分析
现场失效分析过程
2.2 现场失效分析中的检验状态和检验策略:
现
场质 失保 效零 分件 析
过
程
标准检测
是
是否没有问题?
零件分析
顾客投 诉的评
估
否
问 题 解 决 过 程
A是 数
负载检测
K
据
收
是 基于
集
零件
和
是否没有问题?
分析 合格
评
否
的零 件
VDA Field failure analysis 现场失效分析
现场失效分析过程
2.3 零件分析: 对缺陷零件的功能符合其规范的程度提供明确的说明。 • 标准检测 • 负载检测,只对那些表明标准检测无缺陷的零件进行负载检测。只将那些表明负载检测无缺陷的零件才归类为基本零件分析合格。
VDA 6.3 过程审核
▪ 课程安排
序号
内容
1 前言/介绍
2
3
4
5
6
7
8 互动/反馈
方法
互动/讲解 互动/讲解 讲解/练习 讲解/练习 讲解/练习 讲解/练习 讲解
VDA Field failure analysis 现场失效分析
前言
▪ 德国汽车工业联合会
• 超过110年历史。 • 拥有600多个来自德国汽车工业整车厂和供应商的公司和
估
零件/系统/过程 不合格
问题分析
根本原因 措施验证
现场失效分析过程的持续改进过程
NTF 过程
系统检测
过程研究
系 统 过 程 合 格
否
是符 合 协 议 规 定 的 信 息 交 换 和 零 件 处 理
VDA6.3考题样卷及答案

一、判断题(正确以“T”表示,错误以“F”表示,每题2分,共40分)1.(T)VDA6.3过程审核以产品风险为关注点,因此审核前必须收集过程文件和信息。
2.(F )过程审核是对过程规划的符合性进行的检查。
3.(T )批量生产过程审核时,关于生产条例P6的审核必须针对每一道加工过程。
4.(T )VDA6.3 过程审核中发现严重风险,必要时需要暂停审核,以制订紧急措施。
5.(T )实施VDA6.3过程审核中,我们需要首先考虑过程绩效的表现,然后从结果出发,评估各个过程要素的表现。
6.(F)VDA6.3过程审核标准中X2是指项目管理要素部分。
7.(F )过程审核可以由第三方进行认证,并颁发第三方审核认证证书。
8.(F )审核员的资质分为专业培训证明和专业知识二部分组成。
9.(F)VDA6.3内部过程审核人员的专业培训证明方面需要提供VDA6.3审核员卡和证书,这是最低要求。
10.(F)VDA6.3过程审核是基于VDA6.3标准“提问表”作为审核员的“检查表”实施现场对被审核方的评估11.(F)实施VDA6.3过程审核中,当某一个要素的符合率只有低于75%时,在定级时必须实施降级到B。
12.(F)实施VDA6.3过程审核中,只要总符合率达到A级就不需要实施相应的改进。
13.(T)实施VDA6.3过程审核中,若企业没有产品设计开发的功能,对于产品设计开发条例审核不适用,可以不审核,但仍要关注和转化顾客要求为具体的产品要求。
14.(F)实施VDA6.3 过程审核中,P6部分输出评估结果包括P6.1-P6.6等六个子要素。
15.(F)知识储备库中的知识来源是可以来至此前出现过的经验教训,关于来至知识储备库的提问可以超越合同约定范围。
16.(F)VDA6.3过程审核P1 潜力分析条例,只针对组织新增供方实施潜力分析审核,不适合对合格供方新项目的审核。
17.(T)应用VDA6.3过程审核中如发现提问条不适用时,应标注“n.b 或n.a”,但每一要素或子要素审核提问至少达到三分之二以上,方可确认本次审核有效。
VDA FFA现场失效分析PPT演示课件

缺陷标识
接口
接口
根本原因分析和失效消除过程
NTF 过程
数
据
系统检测
收
集
和评
过程研究
估
现场失效分析过程是一个不断升级的检测概念,希望确保在符合经济条款下实施。
2020/3/20
8
VDA Field failure analysis 现场失效分析
现场失效分析过程
持续改进过程涵盖整个现场失效分析过程。可以处理包括触发准则在内的零件分析过程和NTF(未发现故障)过程的任何必要调整。
力度进行零件分析。
失效分析过程成本的数倍,不能从经济层面对其进行证明。未确定的缺陷,
拖延的分析结果或不充分的根本原因分析,会引起较高成本。
• 缺乏普遍而综合的现场失效分析的概念,导致不同的期望和要求。
• 基本上说,现场失效分析中没有计划在产品开发过程中,通常很晚或 根本不实施现场失效分析过程。
• 对于新车型或系统投产必须进行快速,可靠的分析,尤其在爬坡阶段, 以消除概念和功能失效的短板。
2020/3/20
7
VDA Field failure analysis 现场失效分析
现场失效分析过程
2.1 现场失效分析过程的概念
标准检测
共同确定 的检测
标准检 测的基 础上合
格
零件分析
顾客投诉
是1 否2
持续改进 现场失效分析过程
接
负载检测
口
1.失效导向的 2.共同确认的测试
基于零件分析 合格的零件
集
零件
和
是否没有问题 ?
否
分析 合格 的零
件
评 估
零件/系统/过程 不合格
问题分析
VDAFFA现场失效分析报告

基本原则,一旦供方进行现场失效分析中揭示了一项缺陷,就必须申报为缺陷零件,即使该缺陷不能被再现。 对于能够诊断的产品,出现内部失效,即使缺陷不能再现,也必须申报为缺陷零件。内部装置失效是一种由可疑装置本身造成的失效输入并且能明确 说明失效由装置本身引起的。
对于维修时,不被破坏就不能拆除的零件,QEM和供方之间必须规定特殊安排。
VDA Field failure analysis 现场失效分析
现场失效分析过程
持续改进过程涵盖整个现场失效分析过程。可以处理包括触发准则在内的零件分析过程和NTF(未发现故障)过程的任何必要调整。
VDA Field failure analysis 现场失效分析
现场失效分析过程
2.2 现场失效分析中的检验状态和检验策略:
现
场质 失保 效零 分件 析
过
程
标准检测
是
是否没有问题?
零件分析
顾客投 诉的评
估
否
问 题 解 决 过 程
A是 数
负载检测
K
据
是 基于
收 集
Байду номын сангаас
零件
和
是否没有问题?
分析 合格
评
否
的零 件
估
零件/系统/过程 不合格
问题分析
根本原因 措施验证
现场失效分析过程的持续改进过程
NTF 过程
系统检测
过程研究
系 统 过 程 合 格
事件,供方对失效零件进行分析。如果确认为失效零件,则供方可以 对拒收的零件进行根本原因分析,并确定是谁引起的。根据谁引起了 问题,OEM和/或供方可以启动问题解决过程。
VDA Field failure analysis 现场失效分析
售后退货产品分析管理办法

3.1
4.14.2
5.15.25.35.4
NTF :No Trouble Found 首字母缩写,指某些产品可能存在问题而导致不合格,但这些问题不能通过已制订的检测
规范准确的复现,需要执行例外管理。
采购部:负责处理有关供应商责任的退货,协助落实供应商相关的整改措施。
4.术语和定义
售后退货:指产品已经整车厂装车后出售,并在与主机厂协议要求的三包期内并因质量问题退货的产品。
5.职责
销售部:负责现场认定退货产品及信息,产品接收,信息的收集和传递。
质量管理部:组织退货产品的责任判定,分析发生原因及措施跟踪,组织NTF管理流程。
研发技术部:负责问题分析、解决过程的技术支持,负责相关文件的更新。
1.目的
2.适用范围适用于顾客售后退货中我公司生产的产品,对供应商的退货有异议时可参照执行。
3.引用标准
VDA手册 使用现场失效分析(VDA FFA)。
规范顾客售后退货产品的分析、处理,并明确NTF 管理流程,以:
A.明确产品未知问题(包括一些间歇性出现的问题)的处理;
B.使顾客/供应商与公司内部间对问题产品的判断趋向一致;
C. 帮助改进测试检验技术;
D.为未来类似问题处理留下证据。
6.17附加说明:
质量管理部每年在应根据顾客要求的变化,确定当年度的NTF指标纳入管理,适用时应分顾客、车型。
7.。
DFMEA失效分析简介

1.1 失效和失效分析
产品丧失规定的功能称为失效。
判断失效的模式,查找失效原因和机理,提出预防再失效的对策的技术活动和管理活动称为失效分析。
1.2 失效和事故
失效与事故是紧密相关的两个范畴,事故强调的是后果,即造成的损失和危害,而失效强调的是机械产品本身的功能状态。失效和事故常常有一定的因果关系,但两者没有必然的联系。
2 .参与分析检讨的人员要足够
为防止分析时的偏差导致失之毫厘,差之千里的谬误并能收集思广益之功,一定的人数参与是必要的,至于多少人才算足够,当视分析对象的特征或公司能力而定。对这一点,固然在量上面要足够,质方面也要考量各个层面的代表性,每个功能别组织要有,专业技术和管理人员都有则能更具周延性。
对于初次导入失效模式分析手法的企业而言,也许延聘外部顾问或指导者,进行人员训练、执行协助等是一项可行的作法。
3.考虑开发计划时间上的整合
由于绝大部分进行此类分析的人员,都有既定的原本任务,一方面要能进行日常工作,另一方面要能顺遂分析工作,因此开发时间的妥善安排是非常重要的,可以专案性工作组织来进行失效模式分析可以获得更有利的分工。
同时,也要明示设计审查的检讨对象,界定谁有权利作最后定案的人。
4.实施结果要加以追踪
(6)修理品使用阶段的失效分析 对失效的修理品进行失效分析。
失效分析
可靠性工程中研究产品失效现象的特征和规律、分析失效产生的原因并提出相应对策的一种系统分析方法。产品丧失规定的功能称为失效,可修复的失效称为故障。失效分析可以为可靠性设计、可靠性试验和可靠性评价提供使用现场的信息以及分析数据。
简史19世纪以来随着近代科学技术的发展开始对产品失效作系统的科学的分析研究。人类在生产与科学实践活动中经常遇到严重的产品事故,如火车运行中车轴断裂、桥梁的脆性破裂、飞机的失事、导弹和运载火箭的失控爆炸等。为了查明产生事故的原因,寻求防止产品失效的方法,曾作了大量试验和研究工作,在此过程中发展了失效分析技术。随着产品日趋复杂,失效分析工作也日益受到重视。现代大型产品往往是由上万个、甚至上百万个零部件组成的复杂系统,这类产品的失效或故障会造成巨大的灾害和经济损失。1986年 1月28日美国航天飞机“挑战者”号第10次飞行中因固体助推器密封环失效而引起空中爆炸,造成直接经济损失近20亿美元,7名航天员死亡,航天飞机的飞行也被迫中断近2年。现在失效分析的研究已不限于已发生的事故,而更重视产品失效的潜在因素,探索防止失效的措施,以杜绝事故。
CQI-14保修管理过程NTF降低过程

VDA-FIELD FAILURE ANALYSቤተ መጻሕፍቲ ባይዱS VDA现场失效分析过程
为了有效执行《现场失效分析过程》,组织应对这个一过程进行必要策划,并确 保必要的资源(人员与必要的测试设备) 组织(供应商)与主机厂-OEM客户之间的接口必须明确规定,以便对各种信息的 交换受控管理(法律作用,某些信息不能为第三方所知。。。) 应对保修过程进行持续的业绩监控(建议的KPI指标)以保证持续改进
The organization routinely investigates NTF in relation to the system environment.
The organization establishes yearly improvement targets and places higher priority on issues with high incident rates (vs. cost).
VDA-FIELD FAILURE ANALYSIS VDA现场失效分析过程
VDA-FIELD FAILURE ANALYSIS VDA现场失效分析过程
持续改进过程
标准测试
现场失效分析过程
零件分析测试
负载-加严测试
NTF分析降低过程
根本原因分析与失效消除过程
VDA-FIELD FAILURE ANALYSIS VDA现场失效分析过程
VDA-FIELD FAILURE ANALYSIS VDA现场失效分析过程
OEM收据收集与分析
供应商数据收集与分析
可能的分析建议
系统测试要求
过程分析
软件分析
沟通与文件
NTF结论
问题分析与解决
现场失效分析策划
VDA6.3 check list
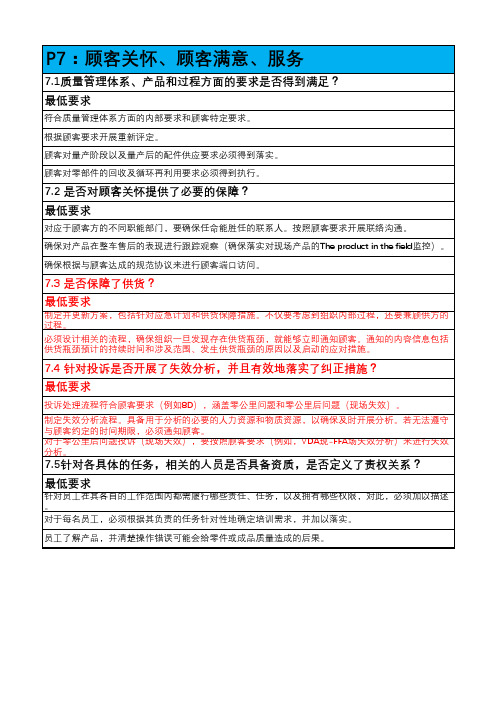
7.5针对各具体的任务,相关的人员是否具备资质,是否定义了责权关系? 最低要求
针对员工在其各自的工作范围内都需履行哪些责任、任务,以及拥有哪些权限,对此,必须加以描述 。 对于每名员工,必须根据其负责的任务针对性地确定培训需求,并加以落实。 员工了解产品,并清楚操作错误可能会给零件或成品质量造成的后果。
ห้องสมุดไป่ตู้
7.4 针对投诉是否开展了失效分析,并且有效地落实了纠正措施? 最低要求
投诉处理流程符合顾客要求(例如8D),涵盖零公里问题和零公里后问题(现场失效)。 制定失效分析流程。具备用于分析的必要的人力资源和物质资源,以确保及时开展分析。若无法遵守 与顾客约定的时间期限,必须通知顾客。 对于零公里后问题投诉(现场失效),要按照顾客要求(例如,VDA现-FFA场失效分析)来进行失效 分析。
对应于顾客方的不同职能部门,要确保任命能胜任的联系人。按照顾客要求开展联络沟通。 确保对产品在整车售后的表现进行跟踪观察(确保落实对现场产品的The product in the field监 控)。 确保根据与顾客达成的规范协议来进行顾客端口访问。
7.3 是否保障了供货? 最低要求
制定并更新方案,包括针对应急计划和供货保障措施。不仅要考虑到组织内部过程,还要兼顾供方的 过程。 必须设计相关的流程,确保组织一旦发现存在供货瓶颈,就能够立即通知顾客。通知的内容信息包括 供货瓶颈预计的持续时间和涉及范围、发生供货瓶颈的原因以及启动的应对措施。
P7:顾客关怀、顾客满意、服务
7.1质量管理体系、产品和过程方面的要求是否得到满足? 最低要求
符合质量管理体系方面的内部要求和顾客特定要求。 根据顾客要求开展重新评定。 顾客对量产阶段以及量产后的配件供应要求必须得到落实。 顾客对零部件的回收及循环再利用要求必须得到执行。
FMEA失效模式及影响分析 AIAGVDA -2019-1.0版

FMEA内容(第1.0版)
P61/30
FMEA内容(第五版)
P62/30
FMEA内容(第1.0版)
FMEA第1.0版案例分析1
根据以下提供的信息,分组讨论并完成电磁线圈的2-4步结构分析、功能分析、失 效分析:
FMEA内容(第1.0版)
FMEA内容(第1.0版)
P66/30
FMEA内容(第1.0版)
FMEA
失效模式及影响分析 Failure Mode and Effects Analysis
AIAG/VDA 2019年第1.0版
FMEA
失效模式及影响分析 Failure Mode and Effects Analysis
AIAG/VDA 2019年第1.0版
FMEA目录
u风险意识 uFMEA发展历史 uFMEA简介 uFMEA第1.0版最新变化 uFMEA七步法详解 uFMEA案例分析
系统 (项目)
系统要素/相 零部件要素(项目
关接口
/接口)
系统的功能,要求 及预期输出
系要统求要及素预的期功输能出,零要部求及件,特的预性功期能输出,
失效影响
严重度
失效模式
失效原因
风险分析 识别针对失效原因和失效模式的控制方法
现行预防控制
发生度
现行探测控制
探测度
AP(行动优先 级)
筛选符号
预防措施
优化 确认减少风险的必要措施
FMEA七步法(第1.0版)
FMEA七步法(第1.0版)
FMEA内容(第1.0版)
格式发生变化(七步法)
策划和准备
启动准备工作:项目计划,分析边界,经验教训,结构基础 ,分析步骤
结构分析
VDA6.3新版过程FMEA六步法
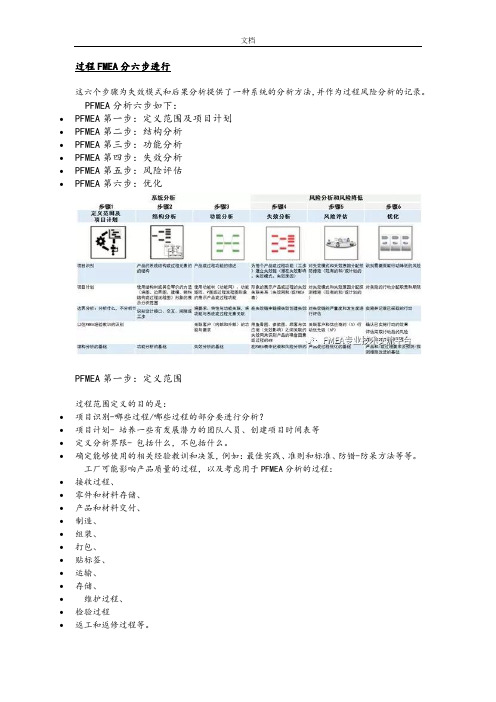
过程FMEA分六步进行这六个步骤为失效模式和后果分析提供了一种系统的分析方法,并作为过程风险分析的记录。
PFMEA分析六步如下:∙PFMEA第一步:定义范围及项目计划∙PFMEA第二步:结构分析∙PFMEA第三步:功能分析∙PFMEA第四步:失效分析∙PFMEA第五步:风险评估∙PFMEA第六步:优化PFMEA第一步:定义范围过程范围定义的目的是:∙项目识别-哪些过程/哪些过程的部分要进行分析?∙项目计划- 培养一些有发展潜力的团队人员、创建项目时间表等∙定义分析界限- 包括什么,不包括什么。
∙确定能够使用的相关经验教训和决策,例如:最佳实践、准则和标准、防错-防呆方法等等。
工厂可能影响产品质量的过程,以及考虑用于PFMEA分析的过程:∙接收过程、∙零件和材料存储、∙产品和材料交付、∙制造、∙组装、∙打包、∙贴标签、∙运输、∙存储、∙维护过程、∙检验过程∙返工和返修过程等。
图确定过程范围PFMEA第二步:结构分析过程结构分析的主要目标是:∙结构化产品或过程元素∙可视化分析范围∙确定工步∙作为功能分析步骤的基础流程图是结构分析的输入文件。
图过程流程图结构树按层次排列系统元素,并通过结构连接说明关联关系。
这个形象化的结构考虑了过程项目、工步和过程工作要素之间的关系。
图结构分析-结构树示例(电机组装线)工步是PFMEA分析的重点!图工步影响工步失效的潜在原因,其类别数量由4M、5M、6M等决定4M类别:机人材料(间接)环境(环境)其他类别但不限于:方法测量图结构分析扩展表格示例PFMEA第三步:功能分析过程工作要素功能通过实现工步来反应过程/产品的特性。
示例:用手从滑槽中取出烧结轴承示例:将磨损的轴承压入定子壳内功能和结构逻辑连接时,应该问以下这些问题:“发生了什么”?如何从左到右实现产品/过程要求-(过程项目- 工步- 过程工作元素)“为什么”?为什么从右到左实施产品过程的要求-(过程工作元素-工步- 过程项目)功能网可视化过程项目功能、工步功能和过程工作元素功能之间的交互通过链接来可视化:功能网、功能结构、功能树、功能矩阵或用PFMEA工具软件进行的功能分析。
VDA6.3新版过程FMEA六步法

过程FMEA分六步进行这六个步骤为失效模式和后果分析提供了一种系统的分析方法,并作为过程风险分析的记录。
PFMEA分析六步如下:∙PFMEA第一步:定义范围及项目计划∙PFMEA第二步:结构分析∙PFMEA第三步:功能分析∙PFMEA第四步:失效分析∙PFMEA第五步:风险评估∙PFMEA第六步:优化PFMEA第一步:定义范围过程范围定义的目的是:∙项目识别-哪些过程/哪些过程的部分要进行分析?∙项目计划- 培养一些有发展潜力的团队人员、创建项目时间表等∙定义分析界限- 包括什么,不包括什么。
∙确定能够使用的相关经验教训和决策,例如:最佳实践、准则和标准、防错-防呆方法等等。
工厂可能影响产品质量的过程,以及考虑用于PFMEA分析的过程:∙接收过程、∙零件和材料存储、∙产品和材料交付、∙制造、∙组装、∙打包、∙贴标签、∙运输、∙存储、∙维护过程、∙检验过程∙返工和返修过程等。
图确定过程范围PFMEA第二步:结构分析过程结构分析的主要目标是:∙结构化产品或过程元素∙可视化分析范围∙确定工步∙作为功能分析步骤的基础流程图是结构分析的输入文件。
图过程流程图结构树按层次排列系统元素,并通过结构连接说明关联关系。
这个形象化的结构考虑了过程项目、工步和过程工作要素之间的关系。
图结构分析-结构树示例(电机组装线)工步是PFMEA分析的重点!图工步影响工步失效的潜在原因,其类别数量由4M、5M、6M等决定4M类别:机人材料(间接)环境(环境)其他类别但不限于:方法测量图结构分析扩展表格示例PFMEA第三步:功能分析过程工作要素功能通过实现工步来反应过程/产品的特性。
示例:用手从滑槽中取出烧结轴承示例:将磨损的轴承压入定子壳内功能和结构逻辑连接时,应该问以下这些问题:“发生了什么”?如何从左到右实现产品/过程要求-(过程项目- 工步- 过程工作元素)“为什么”?为什么从右到左实施产品过程的要求-(过程工作元素-工步- 过程项目)功能网可视化过程项目功能、工步功能和过程工作元素功能之间的交互通过链接来可视化:功能网、功能结构、功能树、功能矩阵或用PFMEA工具软件进行的功能分析。
- 1、下载文档前请自行甄别文档内容的完整性,平台不提供额外的编辑、内容补充、找答案等附加服务。
- 2、"仅部分预览"的文档,不可在线预览部分如存在完整性等问题,可反馈申请退款(可完整预览的文档不适用该条件!)。
- 3、如文档侵犯您的权益,请联系客服反馈,我们会尽快为您处理(人工客服工作时间:9:00-18:30)。
VDA Field failure analysis 现场失效分析
引言
1.1 初始状况:
• 车辆开发负责 • 周期短 • 车型变化 • 质保期变长 • 全球质保成本达到数十亿欧元
现状:
• 高比例的失效,但是却未在零件分析中发现缺陷。 • 一种是没有考虑具有该结果的零件,一种是没有方法性程序用于检测产
和
的零
否
件
评
零件/系统/过程 不合格
是否没有问题
?
问题分析
估
根本原因 措施验证
现场失效分析过程的持续改进过程
- 10/23 -
NTF 过程
系统检 测
过程研 究
系 统 过 程 合 格
否
是符 合 协 议 规 定 的 信 息 交 换 和 零 件 处 理
VDA Field failure analysis 现场失效分析
据 收
NTF 过程
系统检
测
集 过程研
和究
评
现场失效分析过根程本是接口原一因个分不析断和升失级效的消检接口除测过概估程念,希望确保在符合
经济条款下实施。 - 8/23 -
VDA Field failure analysis 现场失效分析
现场失效分析过程
持续改进过程涵盖整个现场失效分析过程。可以处理包括触发准则在内的零件分析过程和NTF(未发现故障)过程的任何必要调整。
- 2/23 -
VDA Field failure analysis 现场失效分析
VDA 6.3 过程审核
课程安排
序号
内容
1 前言/介绍
2
3
4
5
6
7
8 互动/反馈
- 3/23 -
方法
互动/讲解 互动/讲解 讲解/练习 讲解/练习 讲解/练习 讲解/练习 讲解
VDA Field failure analysis 现场失效分析
- 6/23 -
VDA Field failure analysis 现场失效分析
目的
1.2 目的: • 现场失效分析的有关的核心过程和支持过程及其接口。 • 尤其是经过检验过程表明产品无缺陷的零件,描述了方法性程序,以
识别从车辆上拆除零件的原因。为此,数据分析必须得到从顾客,经 销商,OEM,返回供方整个过程和/或系统的支持。 • 必须有必要的过程和资源。一个计划过程。 • 规定OEM 和 供方之间的接口,基于关键的绩效指标和持续改进CIP, 持续监控过程及改进来确保业绩能力。 • 采用共同语言和共同的理解,透明度,关注现场相关的质量问题。
- 11/23 -
VDA Field failure analysis 现场失效分析
前言
德国汽车工业联合会
• 超过110年历史。 • 拥有600多个来自德国汽车工业整车厂和供应商的公司和
企业。 • 旨在研究和生产面向未来的清洁安全汽车。
• VDA 代表汽车整车厂和供应商,确保持续提高企业的竞 争里。
• VDA 为汽车整车厂和供应商的广泛合作建立了独一无二 的平台。
• VDA 在国内和国际上代表整个德国汽车工业的利益,在 经济,运输,环境政策,技术立法,标准化和质量保证 等方面通过其活动支持德国汽车工业的发展。
现场失效分析过程
检验状态 始终以适当的方式对缺陷零件的说明(例如附带的文件,电子码或条形码),表明已经进行了哪些过程操作。零件分析,等,以及这些过程产生哪些 结果,检验状态可以确保现场失效分析过程的透明性和可追溯性。 规定关键绩效指标 基本原则,一旦供方进行现场失效分析中揭示了一项缺陷,就必须申报为缺陷零件,即使该缺陷不能被再现。 对于能够诊断的产品,出现内部失效,即使缺陷不能再现,也必须申报为缺陷零件。内部装置失效是一种由可疑装置本身造成的失效输入并且能明确 说明失效由装置本身引起的。 对于维修时,不被破坏就不能拆除的零件,QEM和供方之间必须规定特殊安排。
对拒收的零件进行根本原因分析,并确定是谁引起的。根据谁引起了
问题,OEM和/或供方可以启动问题解决过程。
- 5/23 -
VDA Field failure analysis 现场失效分析
引言
• 由于存在不统一的内部和外部要求,因此以非常各自的方式和不同的 一般情况下,由于没有早期识别及消除缺陷,其引起的成本将是基于现场
- 9/23 -
VDA Field failure analysis 现场失效分析
现场失效分析过程
现 2.2 现场失效分析中的检验状态和检验策略:
场 失 效 分 析过程问题解
质 保 零 件
零件分析
标准
检测 是
顾客投 诉的评
估
否
是否没有问题 ?
决
过
数
A是 据
负载 K 收
检测 是 基于 零件
集
分析 合格
VDA Field failure analysis 现场失效分析
供应链中的联合质量管理 市场和服务 现场失效分析
德国汽车工业管理
第一版,2009年7月德国汽车工业联合会(VDA) - 1/23 -
VDA Field failure analysis 现场失效分析
VDA 6.3 过程审核 注意事项 相互认识
- 7/23 -
VDA Field failure analysis 现场失效分析
现场失效分析过程
2.1 现场失效分析过程的概念现场持Leabharlann 续效改分进析过程 数标准检测
共同确定 的检测
标准检 测的基 础上合
格
零件分析
顾客投诉
是1 否2
缺陷标识
负载检测
1.失效导向的 2.共同确认的测试
接
口
基于零件分析 合格的零件
品,过程或系统中的失效。
• 无法再现报告中所述缺陷的零件,通常可以避免质保成本,但同时在物 流和分析中耗费大量事件和努力,却没有可比的经济价值。
• 但是,在车辆使用中,仍可能出现预期性能的偏差。 • 质量和成本之间有矛盾时,现场返回的缺陷零件和现场失效分析发挥
了基本和多重作用。
• 全球范围内,适当数量的缺陷零件返回制造商,以代表市场上的失效 事件,供方对失效零件进行分析。如果确认为失效零件,则供方可以
力度进行零件分析。
失效分析过程成本的数倍,不能从经济层面对其进行证明。未确定的缺陷
,拖延的分析结果或不充分的根本原因分析,会引起较高成本。
• 缺乏普遍而综合的现场失效分析的概念,导致不同的期望和要求。
• 基本上说,现场失效分析中没有计划在产品开发过程中,通常很晚或 根本不实施现场失效分析过程。
• 对于新车型或系统投产必须进行快速,可靠的分析,尤其在爬坡阶段 ,以消除概念和功能失效的短板。