船舶建造工艺课件14_船体装配
船体加工与装配

船体加工精度控制
总结词
船体加工精度控制是确保船体装配质量和船舶性能的重要环节,涉及到船体零 部件加工、组装和焊接等多个环节。
详细描述
影响船体加工精度的因素较多,如加工设备精度、工艺参数、操作技能等。为 提高加工精度,需要加强设备维护和精度校准,制定合理的加工工艺和操作规 程,加强质量检测和控制。
船体装配效率提升
03
船体加工与装配中的问题与解决方案
船体结构强度问题
总结词
船体结构强度问题主要表现在船体结构在受到外力作用时易 发生变形或断裂,影响船舶的安全性能和使用寿命。
详细描述
船体结构设计不合理、材料选用不当、焊接质量差等都可能 导致船体结构强度问题。为解决这一问题,需要优化船体结 构设计,合理选用高强度材料,加强焊接质量控制,并进行 严格的强度试验和检测。
船体结构
该型船体采用典型的三段式结构,包括艏、 舯、艉三部分。
装配流程
先进行分段装配,然后进行总段装配,最后 进行整体装配。
加工工艺
采用数控机床进行精确加工,确保各段船体 的尺寸和形状符合设计要求。
质量控制
采用严格的质量控制体系,确保船体的加工 与装配精度。
某新型船体的加工与装配案例
船体设计
该型船体采用流线型设计,以减小阻 力并提高航速。
船体装配质量检测
质量检测是确保船体装配质量的 重要环节,包括对船体结构的检 测、焊接质量的检测以及对设备
和系统的测试等。
质量检测过程中,需要采用先进 的检测技术和设备,如激光测距 仪、超声波探伤仪等,对船体的
各个部位进行全面检测。
质量检测完成后,需要对检测结 果进行分析和评估,对不合格的 部分进行整改和修复,确保船体 的质量和性能符合规范和标准。
船舶装配工艺

间隙≥12mm
加补板(按Q/SWS 52-011-2003《船体结构相
贯
切口与补板形式》)
工法室
四、肋板拉入法工法实施
(三)采用肋板拉入法部位
(1)双层底肋板 与内底板装配采 用肋板拉入法; (2)舭部肋板与 外底板装配采用 肋板拉入法; (3)下边水舱肋 板与斜底板装配 采用肋板拉入法
工法室
四、肋板拉入法工法实施 (三)采用肋板拉入法部位
029/39 719
643/53
283/93
811
826/36
825/35
19400 A/B
824/34
803
14600 A/B
823/33
9800 A/B
810
822/32
Fr315-200 801
5100 A/B
19970 Fr259+410
19500
Fr280+800
17720 Fr300+320
Fr5+100 111
110
MD02
MD01
911
144/54 二平台
901 Fr48+590
124/34
143/53 三平台
103 Fr30+200
102
123/33 122/32 101
AE01
22400 Fr14+200
Fr42+2309050Fr47+11570900
Fr14+200 18300 Fr37+1009400 Fr48+590 15970
(五)分段划分必须优化总段合拢工艺
(1)上边水舱分 段5字组、6字组 的实肋板与空心 肋板,由原来对 接在结构上改为 通过扁钢形成角 接,优化总段吊 装工艺及焊接状 态;
船舶建造工艺船体装配

船舶建造工艺船体装配一、船体装配的概述船舶建造工艺中的船体装配是指将船体组件逐一安装并拼接,形成一个完整的船体结构的过程。
船体装配是船舶建造中非常重要的一环,它关系到船舶的整体强度、稳定性和性能,对船舶的使用寿命和航行安全起着关键的作用。
船体装配工艺通常涉及到以下几个方面:1.部件准备:将各个船体组件按照图纸要求进行切割、冲孔、打标等加工准备工作。
2.装配顺序:根据工艺要求,按照一定的装配顺序进行船体的组装。
3.安装位置:根据船体布局,将各个组件按照设计要求的位置进行安装。
4.焊接工艺:进行组件之间的连接,常用的焊接方法包括电弧焊、气体保护焊等。
5.验收和调试:对装配完成的船体进行验收和调试,确保船体的质量和性能达到设计要求。
二、船体装配的工艺流程1. 部件准备在船体装配过程中,首先需要对各个船体组件进行准备工作。
这些组件通常是由钢板经过切割、冲孔、打标等工艺加工而成。
在准备过程中,需要做好以下几个方面的工作:•钢板切割:根据图纸要求,用切割设备将钢板切割成对应的形状和尺寸。
•冲孔:根据图纸和设计要求,在钢板上进行冲孔加工,以便后续的组装和连接。
•打标:在每个钢板上打上相应的标记,以便在组装过程中能够准确地找到对应的位置。
2. 装配顺序在船体装配过程中,需要按照一定的顺序进行组装。
一般来说,首先会将底板和侧板进行组装,然后再安装甲板和上层结构。
在装配的过程中,需要注意以下几个要点:•确定安装顺序:在进行船体装配时,需要按照一定的安装顺序进行,以保证装配的合理性和高效性。
•严格控制尺寸:在组装过程中,要严格控制各个组件的尺寸,以保证整体结构的稳定性和完整性。
•检查和调整:在组装过程中,需要进行不断的检查和调整,确保各个组件的安装位置和连接质量符合要求。
3. 安装位置在进行船体组装时,需要根据设计要求将各个组件安装到相应的位置上。
安装位置包括以下几个方面:•对齐和定位:在安装过程中,要保证各个组件的对齐和定位准确,以确保整体结构的平衡和稳定。
船体装配工艺基础知识
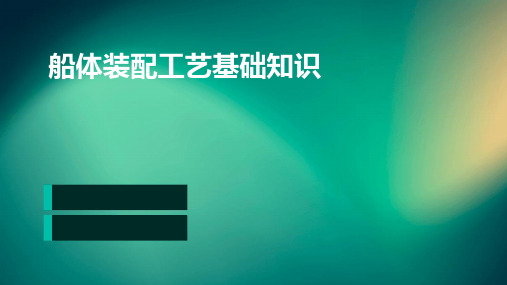
甲板结构
包括甲板横梁和纵梁,支撑甲 板面并传递载荷。
船体结构的类型ຫໍສະໝຸດ 010203
纵骨架式
船体主承力结构为纵向骨 架,适合大型船舶。
横骨架式
船体主承力结构为横向骨 架,适合小型船舶。
混合骨架式
结合纵骨架和横骨架的特 点,适用于不同类型和大 小的船舶。
螺接装配法
通过螺栓、螺母等紧固件 将船体零部件连接在一起, 适用于可拆卸结构的装配。
压合装配法
利用压力将船体零部件紧 密结合在一起,具有结构 简单、密封性能好的特点。
船体装配的工艺流程
基准定位
确定船体装配的基准线和基准 面,确保装配位置准确。
整体装配
将船体各部件按照设计要求进 行总装,形成完整的船体。
率和质量。
03
强化员工培训和管理
加强员工技能培训和素质提升,提高员工的工作能力和生产效率;同时
建立有效的激励机制和管理制度,激发员工的积极性和创造力。
生产过程中的质量控制与安全管理
1 2 3
严格把控质量标准
在船体装配过程中,应制定严格的质量标准和检 验制度,确保各阶段的工作符合质量要求。
加强质量检测与追溯
06 船体装配中的生产计划与 组织
生产计划的制定与实施
明确生产目标
在制定生产计划时,应明确船体装配的目标、时间节点和 交付要求,以确保生产计划的合理性和可行性。
分解生产任务
将船体装配任务分解为若干个阶段和子任务,明确各阶段 的工作内容、时间安排和资源需求,以便于生产计划的实 施和管理。
协调资源分配
为确保焊接质量,需建立严格的质 量控制体系,包括工艺规程的制定、 焊接过程的监控、焊工技能培训等。
船舶建造工艺船体装配

船舶建造工艺船体装配1. 引言船体装配是船舶建造过程中的重要步骤之一,它涉及到船舶结构的组装和连接。
船体装配的质量直接影响到船舶的安全性和使用寿命。
本文将介绍船舶建造工艺中船体装配的一般流程和关键要点。
2. 船体装配的一般流程船体装配的一般流程可分为以下几个步骤:2.1 设计准备阶段在设计准备阶段,需要根据船舶设计图纸和相关要求准备所需的材料和工具。
同时,要对船体装配的工艺流程进行规划和安排,确定装配的顺序和时间节点。
2.2 前装配工艺在前装配工艺中,需要进行船舶的钢结构组装。
这包括船体的龙骨和外壳板的焊接、连接和调整。
在这个阶段,需要确保各个部件的尺寸和位置的准确性,并做好防锈和防腐的处理。
2.3 中装配工艺在中装配工艺中,需要进行船舶的设备安装。
这包括主机、辅机、电气设备、管道和绝缘材料的安装。
在这个阶段,需要按照设计要求进行设备的定位、安装和连接,确保各个系统的正常运行和协调配合。
2.4 后装配工艺在后装配工艺中,需要进行船舶的涂装和舾装工作。
这包括船体的外部涂装和舒适性设施的安装。
在这个阶段,需要使用合适的涂料和材料对船体进行保护和修饰,同时安装各种船舶内部的设施和装置。
2.5 质量检验和试航阶段在质量检验和试航阶段,需要对船体装配的质量进行全面检查和评估。
这包括对船舶结构、设备功能和舾装质量的检测。
同时,在试航过程中,需要测试船舶的性能和安全性能,确保船体装配达到设计要求。
3. 船体装配的关键要点3.1 船体装配工艺的规范性船体装配工艺需要按照相关的规范和标准进行操作。
这包括船舶设计规范、焊接规范、防腐规范等。
必须严格按照规范要求进行船舶装配,确保装配结果符合设计要求,并能满足船舶的使用需求。
3.2 船体装配的质量控制船体装配的质量控制是确保船舶结构稳定和安全的关键。
在装配过程中,需要对各个部件的尺寸、位置和连接进行严格检查和控制,确保装配的精确性和牢固性。
3.3 船体装配中的技术要点船体装配中的技术要点包括焊接技术、定位调整技术、设备安装技术等。
船舶装配工艺

17.5万吨
17.7万吨
AE31P/S
MC1 MS42P/S
LA1 MS41P/S Fr46+150
183/93
AE22 Fr5+A1E0201P/S MS32P/S AE11
MS31P/S
MS22P/S MS21P/S MS13P/SFr3M0S-1220P0/S MS11P/SMS11C
112
182/92
装配工艺讲座
工法室
一、装配基础知识 现代造船工艺流程
船舶设计
产品性能设计
产品生产设计
舾装品外购 舾装件加工
船体放样 零件号料 构件加工
部件装焊
配套
分段装焊
总组装焊
单元舾装
船体搭载
船舶下水
码头舾装
试航试验
工法室
签字交船
一、装配基础知识
船体建造是船舶建造的主要部分,它具体
包括船体放样、零件号料、构件加工、部件装
14600 A/B
FE21P/S
9800 A/B
FE11P/S FE12
5000 A/B Fr315-200 FE01
18640Fr279-200
18200
10000
Fr299-200 Fr311-200
19500
029/39 719
643/53
283/93
811
826/36
825/35
19400 A/B
824/34
803
14600 A/B
823/33
9800 A/B
810
822/32
Fr315-200 801
5100 A/B
Fr280+800
船体建造工艺讲座PPT课件

所需的实际形状。 1)板材加工
-冷加工 用于加工单向曲度的板 水(油)压机、三星辊等
-热加工 用于加工曲度很大的双曲度板 需要制作压模,周期长、成本高
-水火弯板 用于加工曲度较小的双曲度板 利用热胀冷缩产生的内应力是钢板产生变形, 成本低,对施工人员要求较高
第24页/共34页
船体建造工艺
第25页/共34页
第19页/共34页
船体建造工艺
第20页/共34页
第21页/共34页
船体建造工艺
激光切割 优点:-能量密度高、热量输入低、热 影响区小、易于控制 是未来造船钢板切割的发展方向
水射流切割 分为--纯水射流切割 --添加磨料的水射流切割
第22页/共34页
船体建造工艺
*机械剪切和冲裁 由于剪切和冲裁边缘受到外力作用产生塑
造船工艺
一、以前-1、船体建造工艺 2、舾装工艺
第1页/共34页
造船工艺
二、现在-1、船体建造工艺 2、舾装工艺 3、涂装工艺
理由:1、自进入20世纪70年代以来,由于船 舶大型化导致涂装工程大量增加 2、质量要求不断提高 3、涂装技术得到迅速发展 涂装作业从舾装作业中分离开来
船体装配工培训课件
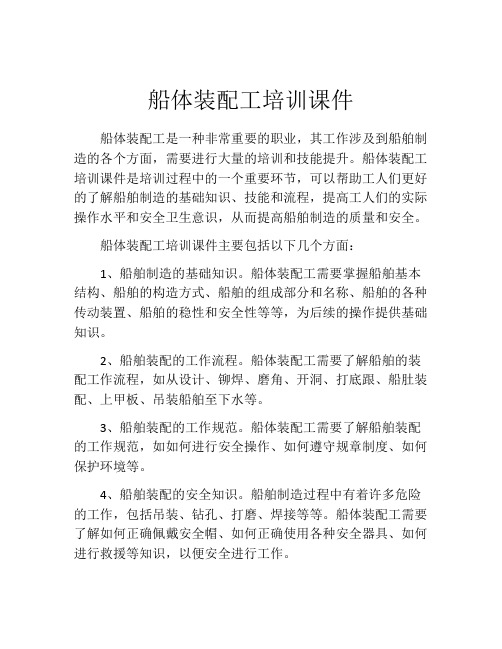
船体装配工培训课件船体装配工是一种非常重要的职业,其工作涉及到船舶制造的各个方面,需要进行大量的培训和技能提升。
船体装配工培训课件是培训过程中的一个重要环节,可以帮助工人们更好的了解船舶制造的基础知识、技能和流程,提高工人们的实际操作水平和安全卫生意识,从而提高船舶制造的质量和安全。
船体装配工培训课件主要包括以下几个方面:1、船舶制造的基础知识。
船体装配工需要掌握船舶基本结构、船舶的构造方式、船舶的组成部分和名称、船舶的各种传动装置、船舶的稳性和安全性等等,为后续的操作提供基础知识。
2、船舶装配的工作流程。
船体装配工需要了解船舶的装配工作流程,如从设计、铆焊、磨角、开洞、打底跟、船肚装配、上甲板、吊装船舶至下水等。
3、船舶装配的工作规范。
船体装配工需要了解船舶装配的工作规范,如如何进行安全操作、如何遵守规章制度、如何保护环境等。
4、船舶装配的安全知识。
船舶制造过程中有着许多危险的工作,包括吊装、钻孔、打磨、焊接等等。
船体装配工需要了解如何正确佩戴安全帽、如何正确使用各种安全器具、如何进行救援等知识,以便安全进行工作。
5、机器设备的使用和维护。
许多操作需要机器设备的辅助,包括切割、焊接等,机器设备的使用需要进行正确的操作和维护,包括液压油的添加、电器设备的检查和调整等。
船体装配工培训课件不仅仅是一份资料,更是一种系统的教育方式,可以帮助工人们进行理论和实践的结合,快速提高工人们的技能水平。
在船舶制造行业中,良好的船体装配工培训课件是提高生产效率和船舶质量的必备条件,也是保障工人们安全的最佳途径。
总之,船体装配工培训课件是提高船舶制造品质、提高生产效率和保障船员生命安全的重要措施,可以帮助工人们提高技能、提高安全意识、提高质量意识、提高效率,更好地为船舶制造行业发展做出了重要贡献。
船舶建造工艺课件船体装配

2.胎架型值的确定
• 首先在肋骨型线图上作出胎架
基面的投 影线 • 或胎架基 面与各肋 骨剖面的 交线
求胎架支柱点型值
• 根据胎架 支柱间距, 在胎架基 面投影线 上求出支 柱点
胎架型值的确定
套管式胎架的整体图示
• 由于支柱的调节范围有限,故适合于建 造各类平直和小曲形分段
三、胎架基面与胎架型值确定
1.胎架基面的确定
• 胎架基面是用来决定胎架工作面曲 面型值的基准面切胎架
• 胎架基面平行或垂直于基线面,并 且垂直于肋骨剖面
• 过支柱点沿胎架基面投影线的垂直 方向,量取到对应肋骨线的距离
• 减去板厚,即得到胎架的高度型值 • 对于正斜、斜斜切基面 • 应该首先过基面投影线上的支柱点
作出纵向剖面线 • 过基面纵向投影线上的支柱点量取
至船体型线的垂直距离
正斜、斜斜切胎架
四、胎架结构形式的确定与制作
1.胎架结构形式的确定
正造法——分段建造时的位置与其 在实船上的位置一致
反造法——分段建造时的位置与其 在实船上的位置相反
侧(卧)造法——分段建造时的位置 与其在实船上的位置成一定的角度 或垂直
分段建造方法的比较
建造方
法
优点
缺点
适用范围
正造法 施工条件好 胎架复杂划 单底分段,机舱 型线易保证 线工作量大 分段批量生产
• 制作胎架需消耗许多材料和工时
• 在单件和小批量造船生产中,对生产 成本和造船周期的影响极大
• 尽量使用通用胎架,以降低生产成本
1.专用胎架
• 专供某种分段使用,如底部、舷侧、甲板分 段和首、尾柱分段等
船体建造工艺学

船体建造工艺学一、培训目的及要求:通过本课程近44学时的讲解,使学员初步了解船体建造工程中的主要阶段、施工程序,掌握船体装配的基本技术理论。
初步具备一定的分析和解决船体技术方面的能力。
二、课时分配表第一章船体分段的划分(4学时)第二章船体分段的划分(4学时)培训要求:了解船体建造过程中,分段划分的原则和各种典型船舶产品的分段划分方法。
掌握我公司分段划分的具体方法。
培训内容:1、分段划分的原则2、分段划分的工艺性要求3、我公司分段划分的具体方法第三章胎架的制造(4学时)培训要求:掌握胎架的种类和胎架基准面的切取方法。
了解各种胎架的制造方法。
培训内容:1、胎架的作用和分类2、胎架基准面的切取方法3、各种典型分段胎架的制造4、我公司胎架利用的实际情况第四章部件装配及制造(8学时)培训要求:掌握船体部件的装配定位方法,了解部件装配的原理。
培训内容:1、部件装配的原理2、板架结构的装配方法3、T型梁的装配4、肋骨框架的装配5、带缆桩的装配6、部件装配变形及控制7、我公司的装配场地及实际装配情况第五章分段装配及制造(8学时)培训要求:掌握分段制造的装配方法。
培训内容:1、底部分段的装配2、底部水舱的装配3、舷侧分段的装配4、艏艉立体分段的装配5、总段的制造方法第六章船台装配(8学时)培训要求:了解船台装配的类型及工艺装备,掌握船台装配的几种方法培训内容:1、船台类型及其工艺设备2、船台装配方式和准备工作3、底部分段的船台安装4、舷侧分段的船台安装5、甲板分段的船台安装6、船台装配焊接变形及处理方法7、我公司船台装配的介绍第七章船舶下水(4学时)培训要求:了解船舶下水的方式,掌握不同下水方式的优缺点。
培训内容:1、船舶下水的方式2、滑道下水和牛油下水的对比3、我公司船舶下水的实际情况课程复习(4学时)培训要求:对本门课程进行系统复习,学员对船舶建造有一个整体印象,加深对船舶建造的了解,具备一定的船舶工程技术人员的基础知识。
船体装配

(3)主向构件间距在整体分段内应相同, 非对称型钢构件的翼缘应朝向同一侧; (4)平面分段的骨架应布置在板列的同一 侧; (5)设计时应尽量扩大平面分段的数量, 甲板舷弧和梁拱应采用折线型,采用平直的 上层建筑围壁和甲板,舭部曲线半径应小于 双层底高度,避免底部升高。
二、曲面分段制造机械化的研究 如图5-26所示是日本研究试验时采用 的曲形外板自动装焊模拟试验装置示 意图,它可进行数控调节胎架工作曲 面,外板对接缝自动焊接等试验。 如图5-27所示是日本研制的自行式曲 面装焊机示意图。 如图5-28所示是日本研究的适用于曲 面分段框架组装试验装置示意图。
图5-33 吊环形式
图5-34 吊环尺寸与吊运重量的关系图
起重吊环的允许负荷按下式计算: CW P n 吊环剪切强度校核公式: P A min
当采用的吊环材料不同时,应采用以下公式
' P' P
吊环的布置应满足以下条件: (1)吊环安装位置应与分段重心对称,以 保证安装后采用碱性焊条焊接,并保证吊 环负荷均衡,保持分段吊运平稳和吊装状 态正确; (2)吊环安装位置一般设在分段的纵、横 骨架交叉或在分段的刚性构件上; (3)吊环安装方向应与受力方向一致,以 免吊环产生扭矩; (4)采用落地翻身方法时,吊环位置应尽 量设在分段重心平面内。
图5-12 a)正切胎架
图5-12 b)正斜切胎架
图5-12 c)斜切胎架
图5-12 d)斜斜切胎架
2.胎架型值的确定 首先在肋骨型线图上作出胎架基面的投影 线,再根据胎架支柱间距在胎架基面投影线 上求出支柱点,然后过这些支柱点沿胎架基 面投影线垂直方向,量取到对应肋骨线的距 离,并减去板厚,即得到胎架的高度型值。
图5-23 中间甲板的划分
船体装配
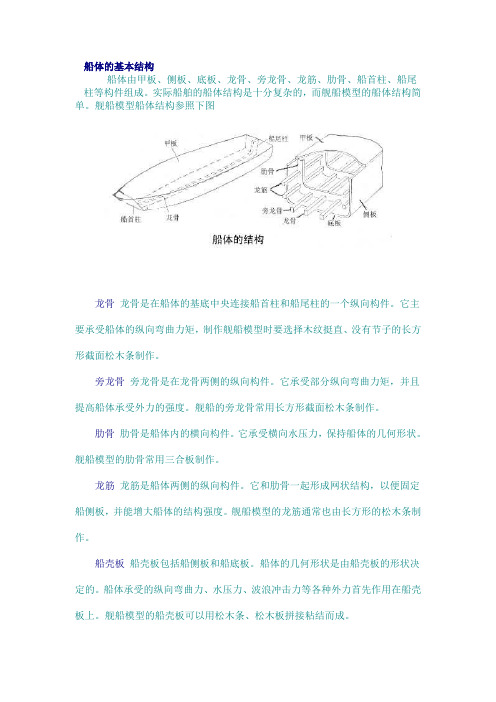
船体的基本结构船体由甲板、侧板、底板、龙骨、旁龙骨、龙筋、肋骨、船首柱、船尾柱等构件组成。
实际船舶的船体结构是十分复杂的,而舰船模型的船体结构简单。
舰船模型船体结构参照下图龙骨龙骨是在船体的基底中央连接船首柱和船尾柱的一个纵向构件。
它主要承受船体的纵向弯曲力矩,制作舰船模型时要选择木纹挺直、没有节子的长方形截面松木条制作。
旁龙骨旁龙骨是在龙骨两侧的纵向构件。
它承受部分纵向弯曲力矩,并且提高船体承受外力的强度。
舰船的旁龙骨常用长方形截面松木条制作。
肋骨肋骨是船体内的横向构件。
它承受横向水压力,保持船体的几何形状。
舰船模型的肋骨常用三合板制作。
龙筋龙筋是船体两侧的纵向构件。
它和肋骨一起形成网状结构,以便固定船侧板,并能增大船体的结构强度。
舰船模型的龙筋通常也由长方形的松木条制作。
船壳板船壳板包括船侧板和船底板。
船体的几何形状是由船壳板的形状决定的。
船体承受的纵向弯曲力、水压力、波浪冲击力等各种外力首先作用在船壳板上。
舰船模型的船壳板可以用松木条、松木板拼接粘结而成。
舭龙骨有些船体还装有舭龙骨,它是装在船侧和船底交界的一种纵向构件。
它能减弱船舶在波浪中航行时的摇摆现象。
舰船模型的舭龙骨可以用厚0.5~1毫米的铜片或铁片制作。
船首柱和船尾柱船首柱和船尾柱分别安装在船体的首端和尾部,下面同龙骨连接,它们能增强船体承受波浪冲击力和水压力,还能承受纵向碰撞和螺旋桨工作时的震动。
船体部件装配教学要求:了解船体预装配的工艺装备内容;理解船体部件装焊过程;掌握胎架设计方法。
重点: 胎架设计、部件装焊。
难点:有斜升基面的胎架设计。
教学内容:船体装配工艺随着造船材料和连接技术的发展而变化,目前的钢质船舶焊接船体的装配过程,大致由下列4个步骤组成:1.将各个船体零件装配焊接成船体部件。
2.由船体零件和部件装配焊接成各种船体分段或总段。
3.由平面分段、曲面分段和零、部件装焊成大型立体分段或总段。
4.在船台上(或造船坞内)将分段、大型立体分段和总段组装成整个船体。
- 1、下载文档前请自行甄别文档内容的完整性,平台不提供额外的编辑、内容补充、找答案等附加服务。
- 2、"仅部分预览"的文档,不可在线预览部分如存在完整性等问题,可反馈申请退款(可完整预览的文档不适用该条件!)。
- 3、如文档侵犯您的权益,请联系客服反馈,我们会尽快为您处理(人工客服工作时间:9:00-18:30)。
起吊高度校核及起吊能力校核和数量配置
• 分段翻身方法按起吊形式分为空中翻身和 落地滚翻两种
起吊高度
分段空中翻身
分段落地滚翻
中间甲板的划分
2.首、尾总段装焊工艺
• 一般而言,首尾总段型线曲率变化大,底部 较瘦削,为便于施工,常采用整体建造法
首、尾总段装焊工艺
• 大多数首总段的底部型 线瘦削 • 反造时,底部工作空间 狭窄,装焊施工条件差 • 将首总段底部划分一个 独立的托底分段预先在 胎架上制造 • 再吊运到总段上安装。
首、尾总段装焊工艺
• 满挡板是首总段反造时最 后安装的一块外板 • 其上、下纵缝均要留有余 量收缩,减小焊接应力 • 为了便于划线,可在外板周围事先划出距接缝50~ 100mm的辅助线
• 满挡板初定位后,先修割上纵缝和横缝并定位施 焊(先焊横缝后焊上纵缝,最后焊外板与肋骨的角 焊缝),然后修割下纵缝并定位施焊 • 目的是便于焊接时自由收缩,减小焊接应力
四、分(总)段装配方法的选择
• 对于一个分段或总段,往往可采用几种不 同的装焊方法进行制造 • 作业环境、施工质量、制造成本和制造周 期的不同 • 在生产准备阶段就应对分(总)段的装配方 法进行认真分析和选择 • 获得产品的最佳制造方法
三个主要因素
• 1、分(总)段结构和型线特点的影响
分段的型式和结构特点,对确定制造方法和制订 装焊顺序起着极为重要的作用,在分板、评价和 选择分(总)段的装配方法时应充分重视
第四章
船体装配
三、总段装焊工艺
• 总段是指主船体沿船长方向划分的 其深度和宽度等于该处型深和型宽 的环形立体段 • 为扩大舾装作业面,实现壳舾涂一 体化的区域建造,也常把两个或两 个以上分段组合而成的大型立体分 段称为总段 • 典型的总段有首、尾总段,上层建 筑总段等
总段的两种制造过程
• 分段建造法
二、 吊环数量、规格及安装位置
• 吊环是分段和翻身的主要属具,一般用钢 板制成 • 吊环的数量需根据分段形状及吊运翻身的 方式来决定 • 吊环强度只需校核其剪切强度,不必考虑 其抗拉强度 • 吊环尺寸和类型的决定,取决于分段总重 量和吊环数量
吊环的布置应满足以下要求
• 吊环安装位置应与分段重心对称,以保证吊环 负荷均衡,保持分段吊运平稳和吊装状态正确 • 吊环安装位置一般设在分段的纵、横骨架交叉 处或在分段的刚性构件上
• 2、产品批量的影响
不同的制造方法,所需要的工艺装备和数量不同, 成本不同。 以分(总)段制造的综合成本为目标、 选择制造方法
• 3、船厂技术条件的影响
船台类型,起重能力,内、外场作业区域的位置 大小等
第三节 船体分段制造生产线
• 分段制造机械化和自动化,存在产品多样、 批量小、制造方法繁杂等困难 • 归纳起来有四个方面
1.船中总段装焊工艺
(1)底部分段完工程度的两种情况 • 一种是在胎架上正造,不进行翻身封底焊及 纵横骨架与内底板间的焊接便进行总段组装 • 一种是底部分段制造竣工,经完工验收后再 进行总段组装 • 前者在分段制造时不必进行翻身和重新调整 定位,但总段翻身比底部分段困难;因此, 总段组装后还需进行大量的仰焊作业,导致 总段的焊接变形量增大,显然不及后者合理, 应采用后一种方法进行总段组装
由零、部件→分段→分段舾装+零 部件→总段→总段舾装
此方法是以底部分段为基础,在其 上安装舱壁、舷侧和甲板等分段, 并进行总段舾装 这种方法主要用于装配船中总段
总段的两种制造过程
• 整体(框架)建造法
零、部件→总段→总段舾装
最常见的是以甲板胎架为基础,以甲板 为基准面反造而成 先装甲板、肋骨框架舱壁和纵向构件, 再安装船体外板,最后进行总段舾装 这种方法主要用于装配首、尾总段
专用传送滚道、载运设备、装配机械和自 动焊接设备
平行作业 大型化 综合机械化
第四节 分段的临时加强及吊运翻身 一、 分段的临时加强
• 安装临时加强材增大分段的刚性,使其能 承受翻身和搁置时的外力保持分段的正确 形状 • 由于分段的形状和结构各不相同,翻身方 向和方式也不一样,其受力情况较为复杂 • 临时加强材的布置视各分段具体情况决定
• 吊环安装方向应与受力方向一致,以免吊环产 生扭矩
• 采用落地翻身方法时,吊环位置应尽量设在分 段重心平面内 • 吊环安装处的船体内部构件应有长约1m的双面 连续焊
三、 船体分段的翻身方法
• 分段翻身前的准备工作
分段的临时加强
吊环及索具卸扣等的选定
吊点布置及吊环装焊
翻身场地选择及布置分段搁置墩木
船中总段装焊工艺问题讨论
(2)保证总段装配质量的技术关键,在于各
分段的准确定位
• 肋骨检验线决定分段长度方向的相对位置
• 中心线(或纵剖线)决定分段在宽度方向的 相对位置
• 水平检验线(某一水线)决定分段在高度方 向上的相对位置和分段水平 • 将分段控制在正确的位置上
船中总段装焊工艺问题讨论
(3)带有中间甲板的总段装焊工艺 • 先装中间甲板分段,需对甲板分段作临时 支撑,有利于舷部分段的定位 • 对嵌进肋骨之间的甲板边板要加工成小块 板件,在总段组装时散装,增加了总段内 的零、部件装焊工作量 • 先装舷部分段,可将中间甲板的边缘部分 装焊在舷侧分段上 • 避免了吊装中间甲板分段时插入装配,又 增加了舷部分段的吊运刚性