气烧辊道窑余热发电技术方案
燃气辊道窑

50M燃气辊道窑方案第一部分技术设计说明气烧辊道窑,是我公司在消化吸收国内外窑炉技术的基础上,自行开发设计的新一代组装式窑炉,具有烧成周期短、能耗低、燃料成本少、自动化程度高等一系列优点。
在本项目技术方案设计中,我们结合近年来所接触到的国内外窑炉的先进技术及实用成功经验,将从烧成车间的工艺布置、窑炉的设计、种类设备选型及关键材料的选用等方面进行详细描述。
一、辊道窑主要技术参数序号项目单位指标备注1 产品50M辊道窑含入窑平台2M、出窑平台3M2 质量国家现行产品标准3 产品规格mm4 年产量件万件5 产品合格率% ≥986 产品优等率% ≥907 烧成周期小时4-5小时可调8 烧成温度℃≤1250℃设计温度1400℃9 单位制品热耗900kal/kg10 燃料发生炉煤气11 燃料热值≥1250kal/m312 总热耗≥1760 m3/小时13 窑有效长度M 4514 窑外有效尺寸M/M 45000L*3000W*2500H 不包含平台尺寸15 主控制柜尺寸M/M 3600L*800W*2200H14 窑体单元节1515 单元长度M 316 窑内宽M 1.4 产品宽1.217 窑内高M/M 420 产品高330mm18 进料台M 219 出料台M 320 辊棒间距mm 10021 辊棒规格mm ф6022 棍棒数量根45023 烧咀数量支4824 温度监测点点16第二部分分部功能描述一、烧成辊道窑及附属设备功能描述1、全窑共设15节单元箱体2、其中:预热带4节长12M烧成带6节长18M急冷带1节长3M冷却带3节长9M最后冷却带1节长3M采用较长的烧成区域,更适合满足烧制不同的产品以达到快速烧成的目的。
2、采用不同型号的方钢管制成窑体骨架,箱式吊顶结构,外墙装饰烤漆板。
(烤漆颜色可根据客户要求选择)。
窑体其它结构示意图1—事故处理孔2—陶瓷辊棒3—烧咀4—观察孔5—热电偶 6 —挡火墙7—挡火板8—热电偶3、窑炉传动装置包括调速电机、传动轴、斜齿轮、辊棒等装置,主传动采用45°斜齿轮分节传动,轴承固定方式为单联体。
余热发电工程施工方案

余热发电工程施工方案一、项目背景余热发电是一种利用工业生产中产生的废热来发电的技术,通过有效利用工业生产中的余热,可以减少能源浪费,降低生产成本,同时也对环境起到一定的净化作用,因此备受行业关注。
本次余热发电工程项目位于某家大型钢铁厂,该厂生产废热丰富,且经过初步分析与评估,满足余热发电的基本条件。
该项目计划利用工厂产生的高温废气进行余热发电,项目规模较大,设计总装机容量为10000KW,属于较为复杂的余热发电工程。
为了确保工程施工能够顺利进行,特制定本施工方案。
二、总体设计思路1. 技术选型根据该钢铁厂的实际情况,本项目拟采用直接循环余热发电技术,通过余热锅炉与汽轮发电机组的结合,实现废热的有效利用。
此外,还将采用先进的数控系统进行监控与管理,以确保工程运行安全稳定。
2. 工程施工方案本项目总体施工方案分为以下几个步骤:(1)前期准备首先,需要对工程现场进行勘察和测量,了解施工环境以及场地情况;其次,进行工程设计评审和技术方案论证,确定最合适的施工方案;然后,编制施工组织设计方案和施工方案,确定施工队伍和施工计划等;最后,准备必要的施工材料和设备,确保施工可以有序进行。
(2)土建施工在完成前期准备之后,需要进行土建施工。
主要包括场地平整、基础施工、设备基础浇筑等工序。
在这个过程中,需要根据当地的气候和地质条件,科学合理地设计土建方案,并保证施工质量。
(3)设备安装土建施工完成后,需要进行设备安装工作。
这是整个工程中最为重要的一个环节,需要严格按照设备安装图纸和要求进行安装,确保设备的安全和正常运行。
(4)电气接线设备安装完成后,需要进行电气接线。
这是工程的最后一个环节,需要确保电气接线的质量和安全。
三、工程施工计划1. 工程施工周期该项目总投资较大,施工任务复杂,预计施工周期为12个月。
具体的施工周期安排如下:前期准备:1个月土建施工:3个月设备安装:4个月电气接线:2个月试运行与调试:2个月2. 施工队伍组织本项目施工队伍由总包施工队伍和分包施工队伍组成,总包施工队伍负责整体施工任务的协调和管理,分包施工队伍负责具体的施工任务的执行。
辊道窑尾冷段余热利用浅析

1 1 计 算依据 .
要计 算窑尾 余 热 的大 体 贮 量 , 须 确 定 一些 原 始 必 数 据 , 有这些 数据 , 没 根本 无法 计算 。
设定 : 某建 陶企 业 陶瓷砖 日产 量为 1 n , 万 f 单位 产
品质 量 为 2 g ; 0k / 测定 : 品 出 窑 在 缓 冷 段 、 尾 冷 段 时 的 温 度 为 产 进 2 0℃ ; 5 最终 出窑时 的温 度 为 10℃ ; 冷段 排 出 的空 5 尾
次性增加设备投 资 7 0 , 0元 年创效益 1.1 8 88 万元 。
关键 词 辊 道 窑 尾 冷 段 余 热 助 燃 风 经 济效 益
利用 价值 不大 , 这也许 是一 种误解 , 或者 是没有 找到合
前 言
在 陶瓷墙地 砖 生产 成 本 中 , 料成 本 所 占比重 是 燃 最大 的 , 电力 成 本所 占比重 仅 次于 原 料 排第 3位 。从 河南 省 的陶瓷 企业情 况来看 , 这两 项 ( 以生产 耐磨砖 为 例) 成本要 占到 生产成 本 的 5 %以上 。随 着能 源 价 格 0
带 走 的热量 为 :
l 窑尾 余 热 的应 用价值
窑尾快 速 冷却部 分的余 热利用 一直 没有 引起人 们 的重视 , 主要 原 因是 多数 人认 为这部 分余热 温度 较 低 ,
l 0 00 0×2 0×1 1×( 5 . 2 0—1 0 5 )=2 2×1 。k 0 J
单 位时 间带 走的热 量 为 :
的余热 利用 问题进 行粗 浅分析 , 旨在 明确利 用潜 力 , 找
出利用 方 向和 利 用 价 值 , 以期 达 到节 约能 源 、 轻 { 减 亏 染、 降低 生产成 本 以及提 高效 益之 目的。
余热发电技技术方案
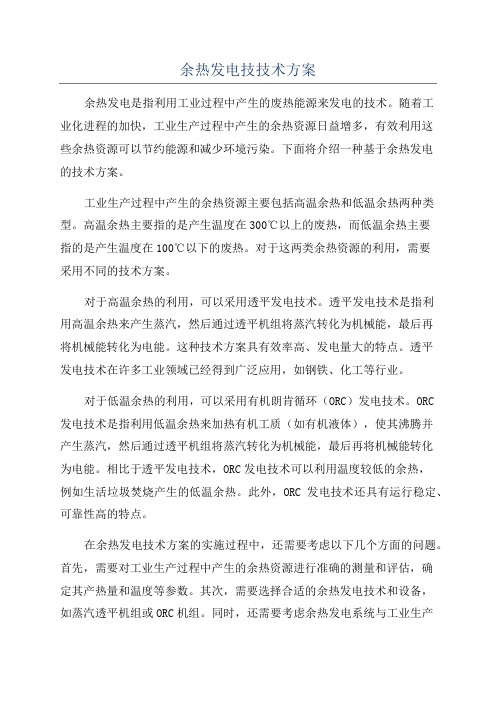
余热发电技技术方案余热发电是指利用工业过程中产生的废热能源来发电的技术。
随着工业化进程的加快,工业生产过程中产生的余热资源日益增多,有效利用这些余热资源可以节约能源和减少环境污染。
下面将介绍一种基于余热发电的技术方案。
工业生产过程中产生的余热资源主要包括高温余热和低温余热两种类型。
高温余热主要指的是产生温度在300℃以上的废热,而低温余热主要指的是产生温度在100℃以下的废热。
对于这两类余热资源的利用,需要采用不同的技术方案。
对于高温余热的利用,可以采用透平发电技术。
透平发电技术是指利用高温余热来产生蒸汽,然后通过透平机组将蒸汽转化为机械能,最后再将机械能转化为电能。
这种技术方案具有效率高、发电量大的特点。
透平发电技术在许多工业领域已经得到广泛应用,如钢铁、化工等行业。
对于低温余热的利用,可以采用有机朗肯循环(ORC)发电技术。
ORC发电技术是指利用低温余热来加热有机工质(如有机液体),使其沸腾并产生蒸汽,然后通过透平机组将蒸汽转化为机械能,最后再将机械能转化为电能。
相比于透平发电技术,ORC发电技术可以利用温度较低的余热,例如生活垃圾焚烧产生的低温余热。
此外,ORC发电技术还具有运行稳定、可靠性高的特点。
在余热发电技术方案的实施过程中,还需要考虑以下几个方面的问题。
首先,需要对工业生产过程中产生的余热资源进行准确的测量和评估,确定其产热量和温度等参数。
其次,需要选择合适的余热发电技术和设备,如蒸汽透平机组或ORC机组。
同时,还需要考虑余热发电系统与工业生产过程的协调,确保余热资源的稳定供应和发电系统的可靠运行。
最后,还需要进行经济性分析和环境影响评估,评估余热发电技术方案的可行性和效益。
总之,利用工业生产过程中产生的余热资源进行发电是一种重要的节能减排技术。
通过采用透平发电技术和ORC发电技术等余热发电技术方案,可以有效利用余热资源,提高能源利用效率,减少环境污染。
未来应继续加大对余热发电技术的研发和推广力度,进一步提高其应用水平,推动可持续发展。
辊道窑尾冷段余热利用浅析
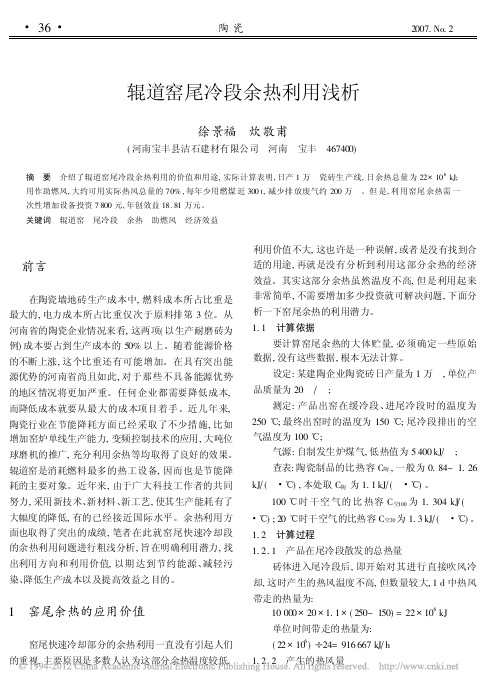
辊道窑尾冷段余热利用浅析徐景福炊敬甫(河南宝丰县洁石建材有限公司河南宝丰467400)摘要介绍了辊道窑尾冷段余热利用的价值和用途,实际计算表明,日产1万 瓷砖生产线,日余热总量为22@106kJ;用作助燃风,大约可用实际热风总量的70%,每年少用燃煤近300t,减少排放废气约200万 。
但是,利用窑尾余热需一次性增加设备投资7800元,年创效益18.81万元。
关键词辊道窑尾冷段余热助燃风经济效益前言在陶瓷墙地砖生产成本中,燃料成本所占比重是最大的,电力成本所占比重仅次于原料排第3位。
从河南省的陶瓷企业情况来看,这两项(以生产耐磨砖为例)成本要占到生产成本的50%以上。
随着能源价格的不断上涨,这个比重还有可能增加。
在具有突出能源优势的河南省尚且如此,对于那些不具备能源优势的地区情况将更加严重。
任何企业都需要降低成本,而降低成本就要从最大的成本项目着手。
近几年来,陶瓷行业在节能降耗方面已经采取了不少措施,比如增加窑炉单线生产能力,变频控制技术的应用,大吨位球磨机的推广,充分利用余热等均取得了良好的效果。
辊道窑是消耗燃料最多的热工设备,因而也是节能降耗的主要对象。
近年来,由于广大科技工作者的共同努力,采用新技术、新材料、新工艺,使其生产能耗有了大幅度的降低,有的已经接近国际水平。
余热利用方面也取得了突出的成绩,笔者在此就窑尾快速冷却段的余热利用问题进行粗浅分析,旨在明确利用潜力,找出利用方向和利用价值,以期达到节约能源、减轻污染、降低生产成本以及提高效益之目的。
1窑尾余热的应用价值窑尾快速冷却部分的余热利用一直没有引起人们的重视,主要原因是多数人认为这部分余热温度较低,利用价值不大,这也许是一种误解,或者是没有找到合适的用途,再就是没有分析到利用这部分余热的经济效益。
其实这部分余热虽然温度不高,但是利用起来非常简单,不需要增加多少投资就可解决问题,下面分析一下窑尾余热的利用潜力。
1.1计算依据要计算窑尾余热的大体贮量,必须确定一些原始数据,没有这些数据,根本无法计算。
辊道窑窑炉设计说明书
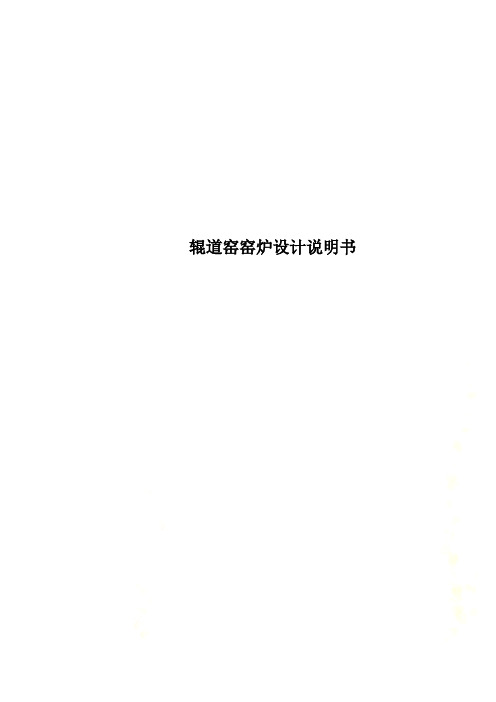
辊道窑窑炉设计说明书目录摘要 (6)前言 (8)1 设计任务书及原始资料 (9)2 烧成制度的确定 (10)2.1 温度制度的确定 (10)2.2 气氛制度 (11)2.3 压力制度 (11)3 窑体主要尺寸确定 (12)3.1窑内宽的确定 (12)3.2 窑体长度的确定 (13)3.3 各带长度的确定 (13)3.4 辊上高、辊下高的确定 (14)4 工作系统确定 (15)4.1 排烟系统 (15)4.2 烧成系统 (16)4.3冷却系统 (16)4.4窑体附属结构的布置 (17)5 窑体材料及厚度的确定 (19)6 燃料及燃烧计算 (21)6.1理论空气需要量 (21)6.2实际空气需要量 (21)6.3 用经验公式计算实际烟气生成量 (22)6.4 燃烧温度 (22)7 物料平衡 (22)7.1每小时出窑制品的质量G出 (22)7.2每小时入窑干制品的质量G干 (22)7.3每小时入窑湿制品的质量G湿 (22)7.4每小时蒸发自由水的质量G w (23)8 预热带烧成带热平衡计算 (23)8.1热平衡计算基准及范围 (23)8.2热平衡示意框图 (24)8.3热收入项目 (24)8.4热支出项目 (25)8.5热平衡方程 (30)8.6热平衡表 (31)9 冷却带平衡计算 (31)9.1热平衡计算准则: (31)9.2热平衡示意图: (32)9.3热收入 (33)9.4热支出 (33)9.5热平衡方程 (41)9.6冷却带平衡列表 (41)10 传动计算 (42)10.1 传动系统的选择 (42)10.2 传动过程 (43)10.3 辊子材质的选择 (43)10.4 辊距的确定 (43)10.5 辊子传动过程中的联接方式 (44)10.6 辊子转速的选择 (44)11管道计算、阻力计算和风机选型 (44)11.1管道计算 (44)11.2阻力计算 (45)11.3排烟风机选型 (46)11.4其他管路阻力计算: (46)12 烧嘴选型 (50)12.1每个烧嘴所需燃烧能力 (50)12.2 选用烧嘴应注意的原则 (50)12.3 烧嘴选用 (50)13 工程材料概算 (52)13.1 钢架结构所用钢材用量概算: (52)13.2 钢板用量概算: (53)13.3 耐火材料概算: (54)致谢 (57)参考文献 (58)外文翻译 (59)摘要本设计的题目是日产1.4万㎡抛光砖气烧辊道窑。
电烧辊道窑技术与装备开发及应用方案(二)
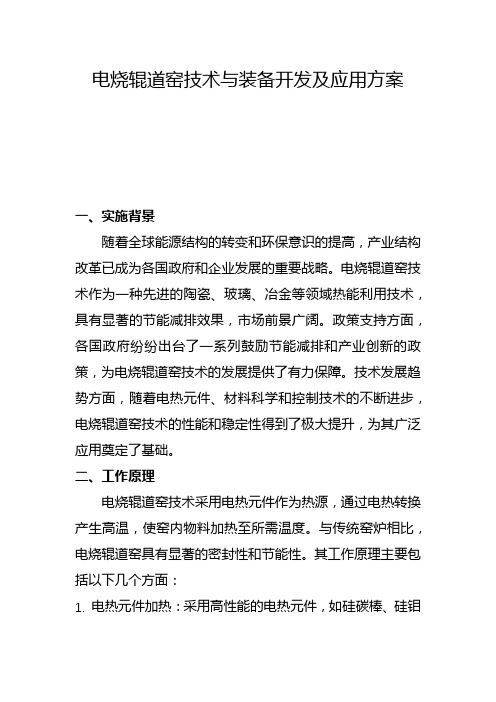
电烧辊道窑技术与装备开发及应用方案一、实施背景随着全球能源结构的转变和环保意识的提高,产业结构改革已成为各国政府和企业发展的重要战略。
电烧辊道窑技术作为一种先进的陶瓷、玻璃、冶金等领域热能利用技术,具有显著的节能减排效果,市场前景广阔。
政策支持方面,各国政府纷纷出台了一系列鼓励节能减排和产业创新的政策,为电烧辊道窑技术的发展提供了有力保障。
技术发展趋势方面,随着电热元件、材料科学和控制技术的不断进步,电烧辊道窑技术的性能和稳定性得到了极大提升,为其广泛应用奠定了基础。
二、工作原理电烧辊道窑技术采用电热元件作为热源,通过电热转换产生高温,使窑内物料加热至所需温度。
与传统窑炉相比,电烧辊道窑具有显著的密封性和节能性。
其工作原理主要包括以下几个方面:1. 电热元件加热:采用高性能的电热元件,如硅碳棒、硅钼棒等,将电能转化为热能,产生高温。
2. 密封性能:电烧辊道窑采用先进的密封技术,如耐火纤维、陶瓷纤维等,确保窑内热量不流失,提高热效率。
3. 控制系统:采用先进的温度控制系统和自动化仪表,对窑内温度、气氛等参数进行实时监测和调节,确保产品质量稳定。
4. 辊道输送:物料在窑内通过辊道输送,实现连续化生产,提高生产效率。
三、实施计划步骤电烧辊道窑技术与装备开发及应用方案的实施计划步骤如下:1. 设计阶段:进行电烧辊道窑的整体设计和电热元件、密封材料、控制系统的选型。
根据实际需求,确定窑炉尺寸、产量、能耗等参数。
2. 实施阶段:按照设计方案进行设备制造和安装。
确保设备质量符合要求,安装过程符合安全规范。
3. 调试阶段:完成设备安装后进行调试,对温度控制系统、输送系统等关键部件进行测试和优化。
确保设备运行稳定,满足生产工艺要求。
4. 验收阶段:组织专家对电烧辊道窑进行验收,评估其性能、能耗等指标是否达到设计要求。
根据验收结果进行调整和优化。
四、适用范围电烧辊道窑技术及装备适用于陶瓷、玻璃、冶金等领域。
在陶瓷行业,电烧辊道窑可用于烧制瓷砖、卫生洁具、日用陶瓷等产品;在玻璃行业,可用于熔制平板玻璃、容器玻璃等;在冶金行业,可用于冶炼钢铁、有色金属等。
带尾气处理装置的燃气辊道窑炉的制作技术

本技术新型属于烧结设备技术领域,涉及一种带尾气处理装置的燃气辊道窑炉,预热段的顶部设有与尾气处理装置的进气管连接的排烟支管,烧成段内设有与燃气管相连的烧嘴,烧嘴的一侧设有助燃风管,冷却段内设有冷风管,冷却段的顶部设有抽热风管,抽热风管通过抽热风机与换热器的内进气口连接;进气管与窑炉顶部的排烟支管连接,进气管上设有风机,进气管与燃烧室的进气口相连,燃烧室的出气口与换热器的内进气口相连,换热器的内出气口与排气管相连,换热器的外出气管上设有引风机二;燃烧室内的烧嘴与燃气管连接;排气管上设有排烟蝶阀;对窑炉预热段和降温段尾气中的热量实现回收利用,节约能源;尾气处理设备简单,操作方便,安全可靠。
技术要求1.一种带尾气处理装置的燃气辊道窑炉,包括窑体包括依次相连的预热段(1)、烧成段(2)和冷却段(3),所述预热段(1)的顶部设有排烟支管(12),排烟支管(12)与尾气处理装置的进气管(41)连接,排烟支管(12)上设有调节阀(11);所述烧成段(2)内设有烧嘴(21),烧嘴(21)与燃气管一(22)相连,每个烧嘴(21)的一侧设有助燃风管,助燃风管与助燃风机(23)相连;所述冷却段(3)内设有冷风管(31),冷风管(31)与冷风机相连,冷却段(3)的顶部设有抽热风支管(38),抽热风支管(38)汇集于抽热风管(37),其特征在于:抽热风管(37)通过抽热风机(34)与换热器的内进气口连接;所述尾气处理装置,包括进气管(41)、燃烧室(47)、换热器(412)和排气管(45),所述进气管(41)与窑炉预热段的排烟支管(12)连接,进气管(41)上设有风机(410),进气管(41)与燃烧室(47)的进气口相连,进气管(41)与燃烧室(47)进气口之间设有主调节阀(42);所述燃烧室(47)的出气口与换热器(412)的内进气口相连,换热器(412)的底部设有排水口(415),换热器(412)的内出气口通过引风机(413)与排气管(45)相连,换热器(412)的外出气管(414)上设有引风机二(411);燃烧室(47)内设有烧嘴(43),烧嘴(43)与燃气管(48)连接;燃气管(48)的一侧设有助燃管;排气管(45)上设有排烟蝶阀。
余热发电技术攻关方案

余热发电技术攻关方案一、技术攻关的目的通过成立技术攻关小组,加强熟料生产中控室与余热发电中控室之间的协调,解决窑系统与余热发电系统的技术难题,提高余热发电量。
二、技术攻关的思路坚持以提高熟料产质量、余热发电量的原则,通过领导注重、操作人员参与等方法。
通过技术管理层提供支持,通过操作人员的全面参与,重点从工艺操作参数完善、操作人员技能提升、人员意识强化、过程持续监控等方面入手,促进系统过程能力。
三、技术攻关的组织方式1、技术攻关小组组长:杜立云副组长:王彦明、柳军红、李保柱、王东亮组员:窑中控操作员、余发电操作员2、技术攻关小组具体职责窑操作由柳军红、李保柱具体负责,包括对系统漏风的治理、窑系统工艺参数完善、监督窑操作员日常操作稳定性等,避免出现低产量、低发电量运行。
窑操作员具体负责按照工艺指定的操作参数进行操作,满足余热发电对温度、风量的需求。
余热发电由王彦明具体负责,包括对系统漏风的治理、余热发电系统工艺参数完善、监督余热发电操作员日常操作稳定性等、避免出现事故停车。
余热发电操作员负责按照工艺制定的操作参数进行操作,保证设备安全正常运行。
四、技术攻关的目标保证窑正常运行的情况下,余热发电日发电量不低于10.2万度。
五、技术攻关奖罚事项1、目标:日发电量≥10.2万度(力争大于11.2万度)2、奖罚:超1度奖0.1元,欠1度罚0.05元3、按照日发电量10.2万度三班平均分配,每班发电量34000度,当班窑中控操作员与余热发电操作员为一组,月底对发电量最高的班组额外奖励300元,最低班组罚款100元,窑操作员与余热发电操作员各一半(主操作员60%,副操作员40%)4、本奖罚措施按日计算,月底兑现,所有奖罚款项由技术攻关小组制定详细分配方案进行分配。
奖罚方案详细分配办法:(考核人数共20人)按日发电量大于10.2万度,超1度奖0.1元,欠1度罚0.05元为基础。
组长承担奖罚的5%副组长承担奖罚的25%组员承担奖罚的70%(奖)例如:11.2-10.2=1(万度)*0.1元/度=1000元组长奖50元副组长共奖250元组员共奖700元(罚)例如:10.2-9.5=0.7(万度)*0.1元/度=700元组长罚35元副组长共罚175元组员共罚490元5、本措施从即日起开始到仓满停车停止。
辊道窑助燃风加热改造初步方案

2.具体改造方案
因为窑尾热风中烟气含量不大,主要成分为热空气,所以可直接从窑尾热风中分流一部分热风到助燃风机进口处,混合少量冷风后作为助燃风进窑。同时加装风量测量装置和温度监测点,作为设备调试和运行监测使用,使窑内燃烧处于最佳工况,对现有风机无需变动。改造后烟风系统见图2。
瓷砖带出热量: (0.260Kcal/Kg.℃) X (5400Kgห้องสมุดไป่ตู้h) X 1000℃
=1404000 Kcal/h占总热量的68.8%
4. 窑体散失的热量
2040000–(294243+1404000)
=341757占总热量的16.7%
5. 成品在冷却段从1100℃降温到250℃所放出的热量计算
2
急冷风机
11832NM3/h
8915 Pa
40℃
3
助燃风机
11832NM3/h
8915 Pa
40℃
4
窑头排烟风机
39122NM3/h
4648 Pa
360℃
5
干燥窑抽湿风机
40012NM3/h
4648 Pa
140℃
二.基本热力计算
1. 辊道窑总燃烧热240(M3/h) X 8500 (Kcal/ M3)
=294243Kcal/h占总热量的14.4%
3. 瓷砖带出热量
瓷砖的比热: 0.260Kcal/Kg.℃ ;
瓷砖的密度 : 2700Kg/ M3
小时出砖量计算值(瓷砖厚度按10mm计):
200M2X 0.01M X 2700Kg/ M3
=5400Kg/h
瓷辊道窑炉的节能和燃烧效能提高方案

瓷辊道窑炉的节能和燃烧效能提高方案随着我国社会经济的发展,城市市政建设越来越受到重视。
混凝土路面砖作为市政基础建设的重要组成部分,其技术质量水平的高低直接影响到城市大街小巷的观瞻,因此路面砖的技术质量水平状况越来越受到各地的关注和重视。
市场的需求量也越来越大,所以给各地面砖生产厂家提高生产能力,降低生产成本,有效提高窑炉的生产效益,降低窑炉燃料的损耗是各面砖厂目前急需要解决的问题。
一.窑炉烧结合理温度与坯料关系温度制度以温度曲线表示,它表明在烧成过程中温度随时间的变化关系。
温度曲线一般分为四个阶段,即由预热升温、最高焙烧温度、保温时间和冷却曲线所组成。
温度曲线应根据制品在焙烧过程中的物理化学反应特性、原料质量、泥料成分、窑炉结构和窑内温度分布的均匀性等各方面因素等综合确定。
A.预热带缓慢升温砖坯慢速脱水。
根据砖坯的干燥情况,确定隧道窑第一个车位的温度。
因为隧道干燥窑的热风入口温度控制在105℃~120℃,因此,第一个车位的温度应严格控制,不超过100℃~105℃,而以后5~6个车位的温度就要缓慢升温。
砖坯在300℃以前的低温阶段的升温速度是关键,在此温度范围内主要是排除坯体内的残余水分。
如果在此阶段升温过快,坯体内的水分急剧蒸发,产生过热蒸汽的压力,会造成坯体开裂,一般为表面裂纹,严重时会造成坯体爆裂,甚至发生砖坯塌车事故。
?? 按窑炉窑内温度的划分,低于600℃属于预热带,当坯体水分排出后,在500℃前可以较快升温,一般升温速度可以控制在80℃/h左右,但在573℃时,由于β-石英转化为α-石英,同时产生0.8%的体积膨胀,所以此阶段要特别注意缓慢升温,以防止制品产生裂纹。
B.焙烧温度和保温。
烧结砖的最高烧成温度一般定为1020℃左右。
但是,在较低温度下,较长时间的保温也可以完成对烧成的要求。
最高焙烧温度适当低些,高温车位多些,保温时间长些,使燃烧的热量能够得到充分的利用,制品烧成比较均匀。
焙烧温度较高时,容易发生砖坯软化,特别是砖垛下层的制品可能变形和熔结。
余热发电项目实施方案
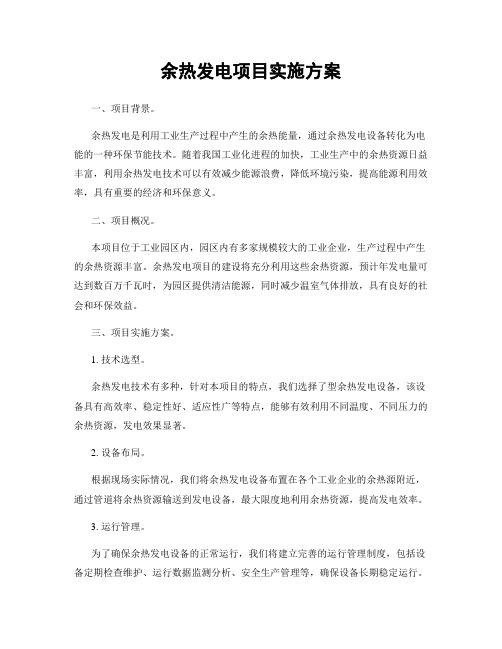
余热发电项目实施方案一、项目背景。
余热发电是利用工业生产过程中产生的余热能量,通过余热发电设备转化为电能的一种环保节能技术。
随着我国工业化进程的加快,工业生产中的余热资源日益丰富,利用余热发电技术可以有效减少能源浪费,降低环境污染,提高能源利用效率,具有重要的经济和环保意义。
二、项目概况。
本项目位于工业园区内,园区内有多家规模较大的工业企业,生产过程中产生的余热资源丰富。
余热发电项目的建设将充分利用这些余热资源,预计年发电量可达到数百万千瓦时,为园区提供清洁能源,同时减少温室气体排放,具有良好的社会和环保效益。
三、项目实施方案。
1. 技术选型。
余热发电技术有多种,针对本项目的特点,我们选择了型余热发电设备,该设备具有高效率、稳定性好、适应性广等特点,能够有效利用不同温度、不同压力的余热资源,发电效果显著。
2. 设备布局。
根据现场实际情况,我们将余热发电设备布置在各个工业企业的余热源附近,通过管道将余热资源输送到发电设备,最大限度地利用余热资源,提高发电效率。
3. 运行管理。
为了确保余热发电设备的正常运行,我们将建立完善的运行管理制度,包括设备定期检查维护、运行数据监测分析、安全生产管理等,确保设备长期稳定运行。
4. 项目效益。
余热发电项目的建设将为园区提供清洁能源,减少温室气体排放,同时也能为企业节约能源成本,提高企业经济效益。
项目建成后,预计年发电量可达到数百万千瓦时,为园区和企业带来可观的经济和环保效益。
四、项目进展。
目前,余热发电项目已完成前期可行性研究和初步设计,相关手续已经办理完毕,项目建设进入了实施阶段。
我们将严格按照项目实施方案,加快项目建设进度,确保项目能够按时投产,为园区和企业带来实实在在的经济和环保效益。
五、总结。
余热发电项目是一项具有重要经济和环保意义的项目,通过充分利用工业生产中的余热资源,实现了能源的再生利用,减少了对传统能源的依赖,降低了环境污染,为企业和社会带来了双重效益。
余热发电方案说明

余热发电方案说明余热发电是指利用工业生产中产生的余热作为能源,通过热能转化装置将其转化为电能的一种发电方式。
余热发电具有能够充分利用废热资源、提高能源利用效率和减少环境污染等优点,被广泛应用于许多行业和领域。
本文将从余热发电的原理、应用、技术和前景等方面进行详细的说明。
一、余热发电的原理余热发电的原理是利用工业生产过程中产生的废热,通过热能转化装置将其转化为电能。
工业生产中的许多过程都会产生大量的废热,如冶金、化工、纺织、电力等行业。
这些废热通常以高温的形式存在,如果不进行有效利用就会直接排放到环境中,造成能源浪费和环境污染。
余热发电的主要装置是余热锅炉和汽轮发电机组。
余热锅炉是将废热通过燃料燃烧或者传热的方式转化为蒸汽,然后通过汽轮发电机组将蒸汽产生的动力转化为电能。
余热发电过程中,烟气中的废热被捕获,传导给锅炉中的工质(如水或空气),使其发生相应的温度升高,并将工质蒸发为蒸汽,然后通过汽轮发电机组转化为电能。
这样,就可以将工业生产中的废热转化为可供使用的电能。
二、余热发电的应用余热发电广泛应用于许多行业和领域,尤其是对于高能耗、高温废气、废水的工业企业。
一方面,余热发电可以提高能源的利用效率,降低生产成本。
另一方面,余热发电可以减少废气和废水的排放,减少环境污染,符合环保要求。
以下是几个常见的应用领域:1.钢铁冶炼行业:钢铁冶炼是一个高温高能耗的过程,会产生大量的废热。
利用余热发电技术,可以将冶炼过程中的废热转化为电能,提高能源利用效率,降低生产成本。
2.化工行业:化工行业的许多工艺过程也会产生大量的废热。
通过余热发电技术,可以将废热转化为电能,提高能源利用效率,减少排放,降低生产成本。
3.纺织印染行业:纺织印染过程中需要用大量的热能。
通过余热发电技术,可以将生产过程中产生的废热转化为电能,提高能源利用效率,降低生产成本。
4.电力行业:电力行业是一个庞大的耗能行业,电厂在发电过程中会产生大量废热。
余热发电项目技术方案

目录1.概述2.热力系统及装机方案3.冷却水系统4.化学水处理系统5.给排水系统6.电力系统7.电气8.热工自动化9.电气设施防火要求10.建筑及结构11.附图1概述1.1项目建设范围本工程项目范围包括:汽轮发电机房;窑头余热锅炉;窑尾余热锅炉;化学水处理;循环水泵站及冷却塔;室外汽水管线;电站内的供配电、控制、通讯、照明等;电站内的给排水、消防系统等;1.2设计界限:窑尾:C1出口到锅炉的管道(含阀门)到发电系统(含开口);窑头:篦冷机出风口到锅炉的管道(含阀门)到发电系统(含开口及筑炉)。
系统:余热锅炉系统;凝汽式汽轮发电机系统;给水系统;除氧器系统;凝结水系统;疏水系统;补给水系统;抽真空系统;锅炉排污系统;循环水系统;工业水系统;电气系统;化学水处理系统;锅炉水处理系统;循环冷却水处理系统;热工控制系统(含DCS系统)。
其他:含电气保护装置(接入系统除外)、电控设备、电缆、防雷接地。
水源:主水管由甲方负责引到用水点30米范围之内(超出30米增加的费用甲方承担)。
阀门井由乙方负责。
电气系统分界线:总降联络柜开关的下端口为电气分界线。
到总降的电缆由乙方负责提供。
2热力系统及装机方案2.1余热条件及生活用热需求根据水泥生产线工艺流程,水泥熟料生产线的废气余热主要来源于窑头熟料冷却机和窑尾预热器两个部分。
可利用余热资源如下:窑头余热锅炉进口废气: 67,600Nm3/h-400℃;窑尾C1出口废气: 164,600Nm3/h-320℃;因此,本技术方案基于如上余热条件及范围,其中窑头锅炉从冷却机中部取风,窑尾烘干废气温度为200℃,因此SP锅炉废气出口温度按200℃设计。
2.2装机方案的确定由于水泥熟料生产线的废气余热量是随熟料产量、煤质、原料、能耗等条件运行工况而变化的。
当水泥窑废气温度波动时,相应的余热锅炉产汽量也随之发生变化。
发电系统装备的选择应能够适应废气参数波动,装机方案也应该适应这种波动。
科技成果——陶瓷辊道窑热风增压助燃技术
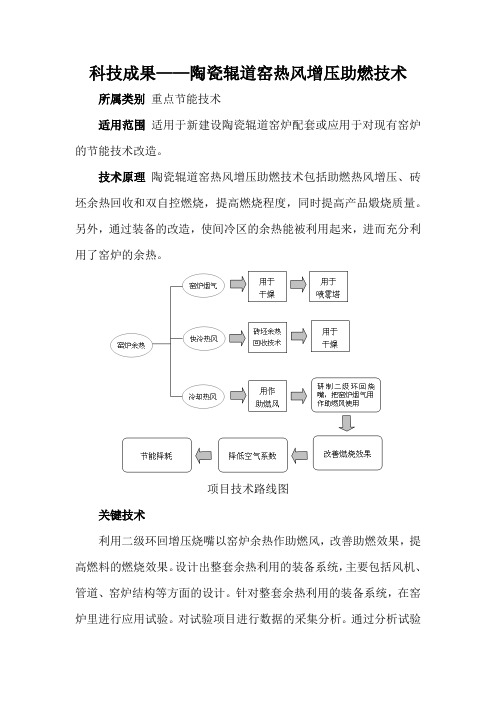
科技成果——陶瓷辊道窑热风增压助燃技术所属类别重点节能技术适用范围适用于新建设陶瓷辊道窑炉配套或应用于对现有窑炉的节能技术改造。
技术原理陶瓷辊道窑热风增压助燃技术包括助燃热风增压、砖坯余热回收和双自控燃烧,提高燃烧程度,同时提高产品煅烧质量。
另外,通过装备的改造,使间冷区的余热能被利用起来,进而充分利用了窑炉的余热。
项目技术路线图关键技术利用二级环回增压烧嘴以窑炉余热作助燃风,改善助燃效果,提高燃料的燃烧效果。
设计出整套余热利用的装备系统,主要包括风机、管道、窑炉结构等方面的设计。
针对整套余热利用的装备系统,在窑炉里进行应用试验。
对试验项目进行数据的采集分析。
通过分析试验的数据,来完善整个余热利用技术系统,并将其规范化。
研发出一套与整套余热利用装备相匹配的煅烧工艺技术。
技术水平本技术由广州市能源检测研究院测试,获取佛山市科学技术局科技成果鉴定证书:佛科成登字[2012]063号并获得佛山市科技技术三等奖。
申报了实用新型专利及发明专利证书201220662980.8。
典型案例新型节能辊道窑通过助燃热风增压技术、砖坯余热回收技术和双自控燃烧技术的创新应用,解决了行业内降低燃烧系统空气系数的难题,减少窑内局部温差,同时亦减少产品的后期变形,提高了产品的煅烧质量。
经窑炉热平衡测试得,助燃空气带入窑炉的物理热量达3800MJ/h,占窑炉热量收入的17.37%。
较采用同样风量的常温助燃空气(带入窑炉的物理热量为180.37MJ/h,占窑炉热量收入的0.97%)增加了16.40%;另一方面,通过计算,窑炉内的空气过剩系数亦得到了降低,从改造前的1.76降低到改造后的1.38。
从而大大地减少了窑炉燃烧需用煤气燃料量。
市场前景本技术2011年起应用于佛山市居之美陶瓷有限公司、江门市和氏陶瓷有限公司、新兴县东骏陶瓷有限公司、肇庆市新顺兴陶瓷有限公司、广西博白新盈邦陶瓷有限公司,节能效果较好,可在陶瓷行业内扩大应用。
辊筒式炉排炉的烟气尾部余热利用技术

辊筒式炉排炉的烟气尾部余热利用技术辊筒式炉排炉是一种常见的燃煤热能利用设备,由于其结构特点,炉内的烟气尾部余热利用成为了提高能源利用效率的关键课题。
本文将介绍辊筒式炉排炉的烟气尾部余热利用技术,并探讨其在工业生产中的应用前景。
一、烟气尾部余热的利用意义烟气中的余热能量是指燃料燃烧过程中,未能转化为热效率的能量。
辊筒式炉排炉的烟气中所含的煤粉不完全燃烧产生的高温烟气,如果得不到合理利用,将会造成巨大的能量浪费。
而通过对烟气尾部余热的充分利用,可以实现能源的节约与环境的保护,具有重要的经济和环境效益。
二、辊筒式炉排炉的烟气尾部余热利用技术1. 预热锅炉给水辊筒式炉排炉烟气中的热量可以通过预热锅炉给水的方式进行利用。
烟气中的高温热量可以通过换热器传递给锅炉给水,将其预热至一定温度。
这样可以降低锅炉给水的进口温度,提高热效率,减少燃料消耗量。
2. 余热发电利用烟气中的余热通过热交换器发电是一种较为常见的技术。
通过热交换器将烟气中的热量传递给工作介质(一般为水蒸汽),产生高温高压的蒸汽,然后驱动汽轮发电机组发电。
这种方法不仅可以实现较高效率的能源利用,还具有明显的经济和环境效益。
3. 联合循环利用辊筒式炉排炉的烟气余热还可以与其他工艺热源进行联合循环利用。
通过将烟气中的热量传递给其他工艺装置,如蒸汽发生器、干燥设备等,实现能源的综合利用。
这种方式不仅能够提高热效率,还可以降低整体能源消耗,提高生产效率。
三、辊筒式炉排炉的烟气尾部余热利用技术应用前景1. 节能环保辊筒式炉排炉的烟气尾部余热利用技术可以有效降低能源消耗,提高能源利用效率,实现节能减排。
这符合国家节能环保政策的要求,有助于保护生态环境,改善大气质量。
2. 经济效益辊筒式炉排炉的烟气尾部余热利用技术可以提高生产效率,减少燃料消耗,降低生产成本。
通过余热发电等方式,还可以获得额外的经济效益。
这对企业的可持续发展具有重要意义。
3. 技术创新在辊筒式炉排炉的烟气尾部余热利用技术中,涉及到热交换、热动力、控制系统等多个领域的技术问题。
- 1、下载文档前请自行甄别文档内容的完整性,平台不提供额外的编辑、内容补充、找答案等附加服务。
- 2、"仅部分预览"的文档,不可在线预览部分如存在完整性等问题,可反馈申请退款(可完整预览的文档不适用该条件!)。
- 3、如文档侵犯您的权益,请联系客服反馈,我们会尽快为您处理(人工客服工作时间:9:00-18:30)。
气烧辊道窑余热发电技术方案
一、辊道窑余热发电概述
余热发电技术是利用企业的高品位热量进行回收,并集中转化为电力供企业自用的技术。
我国从上世纪“八五”期开始,对余热发电技术和装置进行系统的研制开发,经过十多年的开发、研究和若干实际工程投产运行,余热发电技术和国产化设备都已成熟可靠,总体上的技术水平已经赶上国际先进工业国家。
国家也把利用余热发电,作为节能降耗,实现循环发展的重要措施之一,给予大力支持和发展,使我国的余热发电技术应用领域不断扩大。
但在建筑陶瓷、卫生陶瓷行业生产领域,辊道窑余热发电方面是个空白。
根据国家发展改革委节能中长期专项规划[发改环资[2004]2505号]精神,在“十一五”期间,辊道窑是陶瓷行业推广的技术。
由于国内对辊道窑余热利用技术的研究起步较晚,余热利用率较低,除部份企业把余热用于原料烘干外,大部份企业是把高品位的辊道窑排烟热量(温度400~800℃)和产品冷却热量(温度950~1200℃)直接废弃,从而造成大量的能源浪费和热源污染。
陶瓷企业的余热利用,国内外先进企业主要是将辊道窑烟气和产品冷却产生的热风,通过风机送到原料干燥塔,对陶瓷原料进行干燥,以减少干燥塔一次能源消耗量,使陶瓷企业获得一定的经济效益。
由于陶瓷原料的干燥主要是蒸发原料中的水份,利用辊道窑100~400℃的余热足够干燥所需热量;若直接利用辊道窑高品位余热(排烟温度400~800℃和产品冷却温度650~1200℃)用于干燥,则会导致干燥塔热量过剩,同时大大地降低余热的利用价值,使辊道窑的能源浪费转移到干燥塔,干燥塔能源损失量大,而能量品位又低,散失了余热再利用的价值。
陶瓷企业的余热利用除原料干燥以外,其它方式的余热利用量很小,利用价值很低(如加热浴室用热水等),相当多的企业根本就不利用而直接废弃。
根据陶瓷企业余热利用的现状,如何有效地提高余热的利用效率和利用价值,是本项目研究的目的。
电力作为二次能源,价值高且使用方便。
如果将陶瓷企业辊道窑高品位余热(400~800℃的排烟余热和650~1200℃的产品冷却余热)收集转化为价值更高的电力能源,而品位较低、余热锅炉难以利用的余热(100~400℃)再用于原料干燥,既可满足陶瓷生产的需求,并充分利用好现有干燥设备,提高陶瓷企业辊道窑余热利用的价值和效率,解决陶瓷企业余热过剩的问题,将大大地降低企业的生产成本,并节约资源,从而推动陶瓷企业的循环经济发展。
辊道窑消耗的一次能源(煤、油或天然气),除炉窑散热、产品水份蒸发、烧结等必须消耗的能量外,约70%的能量是随排烟热损失和产品冷却热损失而浪费。
在这些浪费的热量(简称余热)中,采用余热干燥原料的方式,可利用余热的20%,20%因品位低无法利用,另有60%左右的余热还没有得到充分利用。
以一条每小时耗标准煤1400Kg的气烧辊道窑为例,进入炉窑总的热量为41×106KJ/h,有12.3×106KJ/h热量直接用于陶瓷生产,有28.7×106KJ/h余热;其中5.74×106KJ/h热量可用于原料干燥,有17.22×106KJ/h热量没有得到充分利用,5.74×106KJ/h热量不能利用。
若将17.22×106KJ/h热量通过余热锅炉转化为蒸汽的热量,余热锅炉效率为85%,则可产生2.5MPa、400℃的蒸汽(蒸汽焓为3214KJ/Kg)2380Kg/h,利用凝汽式汽轮发电机发电,其汽耗率为5.6Kg/KWh,则这条炉窑的余热可发电370KW。
按平均电价0.55元/度计算,这条炉窑每小时可额外回收203.5元的电,经济效益显著。
若
选用排汽压力0.3MPa的小型背压式汽轮发电机发电,汽耗率为26Kg/KWh,则这条炉窑的余热可发电91.5KW,发电的经济效益比凝汽式机组更低,但可利用汽轮机排汽用于陶瓷原料低温干燥或其它工业、生活用汽,提高余热利用的经济效益。
利用辊道窑余热发电的关键,在于开发出适合陶瓷生产的余热锅炉技术和分散热源热工监控技术。
设计的余热锅炉不能影响陶瓷的正常生产(即不影响产品的产量和质量),也不增加一次能源消耗量,余热锅炉产汽压力、温度稳定、可控。
本项目以公司“辊道窑余热发电装置”专利技术为核心,集合我国余热发电的先进技术,自主研制开发出煤烧辊道窑余热发电技术和装置。
项目经过近一年的反复研制开发,以及陶瓷生产企业的使用,在技术上有较大的突破。
创新的“满足辊道窑生产工艺需要的分段换热技术”、“辊道窑余热锅炉过热蒸汽恒温技术”、“辊道窑消烟除尘技术”、“分散热源能量回收热力系统热工监控技术”,较好地解决了煤烧辊道窑余热吸收、收集、能量转换、汽轮机排汽利用、安全运行等技术问题。
同时集合现有成熟的“分散热源能量回收汇集技术”、“钠离子交换水处理技术”、“余热锅炉技术”、“蒸汽发电技术”和“热工仪表监控保护技术”,使整套余热利用装置达到余热利用率高、发电量大(平均每条炉窑可发电266万度/年)、节能降耗效果显著、无烟尘和热源污染、企业经济效益提高(平均每条炉窑可为企业节约近120万元/年的电费开支)的目标。
与余热用于原料干燥技术相比,节能效果更好,技术更先进,有利于陶瓷企业循环经济的发展。
二、气烧辊道窑余热发电能量平衡概算
二条气烧辊道窑,日耗煤85吨(低位发热量5500Kcal/kg),日产瓷砖17000m2(10 kg/m2),产品烧成温度1100℃,窑头排烟温度400~500℃,其中可利用余热量:
1、急冷带(1100℃冷却至600℃和400℃冷却至200℃)余热:
0.26 Kcal/(kg.℃)×17000m2/d×10 kg/m2÷24 h/d×[(1100-600)+(400-200)] ℃=128.92万Kcal/h
2、排烟余热(烟气温度400℃冷却至200℃):
(3970-1930)Kj/kg×85×103 kg/d÷24 h/d÷4.18Kj/Kcal=172.8万Kcal/h
3、合计:128.92万Kcal/h +172.85万Kcal/h=301.77万Kcal/h,折合标准煤431.1 kg/h,余热锅炉效率85%。
可产生2.5 MPa、390℃的蒸汽(焓值为769 Kcal/ kg)
431.1×104Kcal/h×0.85÷769Kcal/ kg=4765 kg/h
采用进汽参数2.35 MPa、390℃的次中压凝汽式机组,汽耗率为5.6 kg/KWh,可发电
4765kg/h÷5.6kg/KWh =851KW
4、由于实际生产过程中,炉窑保温性能差异和炉管积灰等因素,致使余热利用率会下降10~15%,实际发电量为:
次中压(2.35MPa、390℃)参数:851KW×0.85=723KW
因此,根据该厂炉窑保温情况和维护上的关系,采用次中压参数运行时发电量为700~850KW,装置自用电量40~50KW,供电量为650~800KW。