AZ881-1A-5D中文资料
AZ943-1CH-12DE中文资料
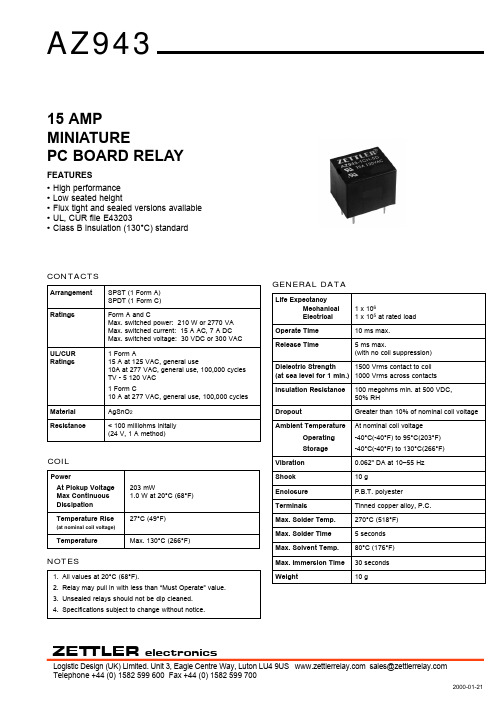
CONTACTSArrangement SPST (1 Form A)SPDT (1 Form C)RatingsForm A and CMax. switched power: 210 W or 2770 VA Max. switched current: 15 A AC, 7 A DCMax. switched voltage: 30 VDC or 300 VAC UL/CUR 1 Form ARatings15 A at 125 VAC, general use10A at 277 VAC, general use, 100,000 cycles TV - 5 120 VAC1 Form C10 A at 277 VAC, general use, 100,000 cyclesMaterial AgSnO 2Resistance< 100 milliohms initally (24 V, 1 A method)ZET TLERelectronicsTelephone +44 (0) 1582 599 600 Fax +44 (0) 1582 599 700Logistic Design (UK) Limited. Unit 3, Eagle Centre Way, Luton LU4 9US sales@ 2000-01-21GENERAL DATALife ExpectancyMechanical 1 x 106Electrical 1 x 105at rated load Operate Time 10 ms max.Release Time5 ms max.(with no coil suppression)Dielectric Strength 1500 Vrms contact to coil (at sea level for 1 min.)1000 Vrms across contacts Insulation Resistance 100 megohms min. at 500 VDC,50% RHDropoutGreater than 10% of nominal coil voltage Ambient TemperatureAt nominal coil voltage Operating -40°C(-40°F) to 95°C(203°F)Storage-40°C(-40°F) to 130°C(266°F)Vibration 0.062" DA at 10–55 Hz Shock10 gEnclosure P.B.T. polyesterTerminalsTinned copper alloy, P.C.Max. Solder Temp.270°C (518°F)Max. Solder Time 5 seconds Max. Solvent Temp.80°C (176°F)Max. Immersion Time 30 seconds Weight10 gCOILPowerAt Pickup Voltage 203 mWMax Continuous 1.0 W at 20°C (68°F)Dissipation Temperature Rise27°C (49°F)(at nominal coil voltage)TemperatureMax. 130°C (266°F)15 AMP MINIATUREPC BOARD RELAYFEATURES •High performance •Low seated height•Flux tight and sealed versions available •UL, CUR file E43203•Class B insulation (130°C) standardNOTES1.All values at 20°C (68°F).2.Relay may pull in with less than “Must Operate” value.3.Unsealed relays should not be dip cleaned.4.Specifications subject to change without notice.2000-01-21ZET TLERelectronicsTelephone +44 (0) 1582 599 600 Fax +44 (0) 1582 599 700Logistic Design (UK) Limited. Unit 3, Eagle Centre Way, Luton LU4 9US sales@ RELAY ORDERING DATASTANDARD RELAYSCOIL SPECIFICATIONSORDER NUMBERNominal CoilMax. ContinuousCoil ResistanceMust OperateUnsealed Sealed VDC VDC ±10%VDC 58.3703.8AZ943–1CH–5D AZ943–1CH–5DE 610.0100 4.5AZ943–1CH–6D AZ943–1CH–6DE 915.0225 6.8AZ943–1CH–9D AZ943–1CH–9DE 1220.04009.0AZ943–1CH–12D AZ943–1CH–12DE 1830.090013.5AZ943-1CH-18D AZ943-1CH-18DE 2440.01,60018.0AZ943–1CH–24D AZ943–1CH–24DE 4867.06,20036.0AZ943–1CH–48DAZ943–1CH–48DESubstitute “1AH” in place of “1CH” to indicate 1 Form A contact.Dimensions in inches with metric equivalents in parentheses. Tolerance: ± .010"。
AZ AQUATAR家族产品系列介绍说明书

9F3C
1F3C
PFOS
CF2 CF2 CF2 SO3OH
CF2 CF2 CF2
PFOA
CF2 F3C
CF2 CF2 CF2
C8 Telomer
CF2 CF2 CF2 CH2CH2OH CF2 CF2 CF2 CF2
CF2
CF2
CF2
COOH
AZ Electronic Materials Confidential
(1.44/1.48/1.56)
(1.40/1.43/1.45)
AQUATAR-3S (1.42/1.44/1.49)
PFOS
AQUATAR-6 (1.40/1.43/1.45)
Fluoro Polymer
AQUATAR-8A (1.41/1.45/1.52)
AQUATAR-8B
for KrF “N” resist
4
AZ, the AZ logo, BARLi, Aquatar, nLOF, Kwik Strip, Klebosol, and S5pinfil are
registered trademarks and AX, DX, HERB, HiR, MiR, NCD, PLP, Signiflow,
SWG, and TARP are trademarks of AZ Electronic Materials.
SWG, and TARP are trademarks of AZ Electronic Materials.
2.4 Resist swing reduction effect in 365nm application
Substrate TARC Develop
: Silicon with HMDS(90C/60s) : 64nm FT, NO PAB : AZ 300MIF(2.38%) , puddle 60s
CS5341-CZZR中文资料

105 dB, 192 kHz, Multi-Bit Audio A/D ConverterFeaturesAdvanced Multi-bit Delta-Sigma Architecture 24-bit ConversionSupports All Audio Sample Rates Including192kHz105dB Dynamic Range at 5V -98dB THD+N90 mW Power ConsumptionHigh-Pass Filter to Remove DC Offsets Analog/Digital Core Supplies from 3.3V to 5V Supports Logic Levels between 1.8V and 5V Auto-Detect Mode Selection in Slave Mode Auto-Detect MCLK DividerGeneral DescriptionThe CS5341 is a complete analog-to-digital converter for digital audio systems. It performs sampling, analog-to-digital conversion, and anti-alias filtering, generating 24-bit values for both left and right inputs in serial form at sample rates up to 200kHz per channel.The CS5341 uses a 5th-order, multi-bit Delta-Sigma modulator followed by digital filtering and decimation,which removes the need for an external anti-alias filter. The CS5341 is available in a 16-pin TSSOP package for Commercial (-10° to +70° C) and Automotive grades (-40° to +85° C). The CDB5341 Customer Demonstra-tion Board is also available for device evaluation and implementation suggestions. Please refer to “Ordering Information” on page 22 for complete ordering information.The CS5341 is ideal for audio systems requiring wide dynamic range, negligible distortion and low noise, such as set-top boxes, DVD-karaoke players, DVD record-ers, A/V receivers, and automotive applications.CS5341CS5341 TABLE OF CONTENTS1. CHARACTERISTICS AND SPECIFICATIONS (4)SPECIFIED OPERATING CONDITIONS (4)ABSOLUTE MAXIMUM RATINGS (4)ANALOG CHARACTERISTICS - COMMERCIAL GRADE (5)ANALOG CHARACTERISTICS - AUTOMOTIVE GRADE (6)DIGITAL FILTER CHARACTERISTICS (7)DC ELECTRICAL CHARACTERISTICS (10)DIGITAL CHARACTERISTICS (10)SWITCHING CHARACTERISTICS - SERIAL AUDIO PORT (11)2. PIN DESCRIPTION (13)3. TYPICAL CONNECTION DIAGRAM (14)4. APPLICATIONS (15)4.1 Single-, Double-, and Quad-Speed Modes (15)4.2 Operation as Either a Clock Master or Slave (15)4.2.1 Operation as a Clock Master (16)4.2.2 Operation as a Clock Slave with Auto-Detect (16)4.2.3 Master Clock (17)4.3 Serial Audio Interface (17)4.4 Power-Up Sequence (18)4.5 Analog Connections (18)4.6 Grounding and Power Supply Decoupling (18)4.7 Synchronization of Multiple Devices (18)4.8 Capacitor Size on the Reference Pin (FILT+) (19)5. PARAMETER DEFINITIONS (20)6. PACKAGE DIMENSIONS (21)THERMAL CHARACTERISTICS (21)7. ORDERING INFORMATION (22)8. REVISION HISTORY (22)CS5341 LIST OF FIGURESFigure 1.Single-Speed Mode Stopband Rejection (8)Figure 2.Single-Speed Mode Stopband Rejection (8)Figure 3.Single-Speed Mode Transition Band (Detail) (8)Figure 4.Single-Speed Mode Passband Ripple (8)Figure 5.Double-Speed Mode Stopband Rejection (8)Figure 6.Double-Speed Mode Stopband Rejection (8)Figure 7.Double-Speed Mode Transition Band (Detail) (9)Figure 8.Double-Speed Mode Passband Ripple (9)Figure 9.Quad-Speed Mode Stopband Rejection (9)Figure 10.Quad-Speed Mode Stopband Rejection (9)Figure 11.Quad-Speed Mode Transition Band (Detail) (9)Figure 12.Quad-Speed Mode Passband Ripple (9)Figure 13.Master Mode, Left-Justified SAI (12)Figure 14.Slave Mode, Left-Justified SAI (12)Figure 15.Master Mode, I²S SAI (12)Figure 16.Slave Mode, I²S SAI (12)Figure 17.Typical Connection Diagram (14)Figure 18.CS5341 Master Mode Clocking (16)Figure 19.I²S Serial Audio Interface (17)Figure 20.Left-Justified Serial Audio Interface (17)Figure 21.CS5341 Recommended Analog Input Buffer (18)Figure 22.CS5341 THD+N versus Frequency (19)LIST OF TABLESTable 1. Speed Modes and the Associated Output Sample Rates (Fs) (15)Table 2. CS5341 Mode Control (15)Table 3. Master Clock (MCLK) Ratios (17)Table 4. Master Clock (MCLK) Frequencies for Standard Audio Sample Rates (17)CS53411.CHARACTERISTICS AND SPECIFICATIONS(All Min/Max characteristics and specifications are guaranteed over the Specified Operating Conditions. Typical performance characteristics and specifications are derived from measurements taken at typical supply voltages and T A = 25°C.)SPECIFIED OPERATING CONDITIONS(GND = 0V, all voltages with respect to 0V.)Notes:1.This part is specified at typical analog voltages of 3.3 V and 5.0 V. See Analog Characteristics - Com-mercial Grade and Analog Characteristics - Automotive Grade, below, for details.ABSOLUTE MAXIMUM RATINGS(GND = 0 V, All voltages with respect to ground.) (Note 2)2.Operation beyond these limits may result in permanent damage to the device.Normal operation is not guaranteed at these extremes.3.Any pin except supplies. Transient currents of up to ±100mA on the analog input pins will not causeSRC latch-up.4.The maximum over/under voltage is limited by the input current.ParameterSymbol Min TypMaxUnitPower SuppliesAnalog Digital Logic VA VD VL 3.13.11.7(Note 1)3.33.35.255.255.25V V V Ambient Operating TemperatureCommercial AutomotiveT AC T AC-10-40--7085°C °CParameterSymbol Min Max Units DC Power Supplies:Analog Logic Digital VA VL VD -0.3-0.3-0.3+6.0+6.0+6.0V V V Input Current (Note 3)I in -10+10mA Analog Input Voltage (Note 4)V IN GND-0.7VA+0.7V Digital Input Voltage(Note 4)V IND-0.7VL+0.7VAmbient Operating Temperature (Power Applied)T A-50+95°CStorage TemperatureT stg-65+150°CCS5341ANALOG CHARACTERISTICS - COMMERCIAL GRADETest Conditions (unless otherwise specified): Input test signal is a 1 kHz sine wave; measurement bandwidth is 10 Hz to 20 kHz.5.Referred to the typical full-scale input voltageDynamic Performance for Commercial Grade VA = 5 V VA = 3.3 VSingle-Speed Mode Fs = 48kHzSymbol MinTypMaxMinTypMaxUnitDynamic RangeA-weighted unweighted 9996105102--969310299--dB dBTotal Harmonic Distortion + Noise(Note 5) -1dB -20dB -60dBTHD+N----98-82-42-92------95-79-39-89--dB dB dBDouble-Speed Mode Fs = 96kHzSymbol MinTypMaxMinTypMaxUnitDynamic RangeA-weighted unweighted40kHz bandwidth unweighted 9996-10510299---9693-1029996---dB dB dBTotal Harmonic Distortion + Noise (Note 5) -1dB -20dB -60dB40kHz bandwidth -1dBTHD+N-----98-82-42-95-92--------95-79-39-87-89---dB dB dB dBQuad-Speed Mode Fs = 192kHzSymbol MinTypMaxMinTypMaxUnitDynamic RangeA-weighted unweighted40kHz bandwidth unweighted 9996-10510299---9693-1029996---dB dB dBTotal Harmonic Distortion + Noise (Note 5) -1dB -20dB -60dB40kHz bandwidth -1dBTHD+N-----98-82-42-95-92--------95-79-39-87-89---dB dB dB dBDynamic Performance All ModesMinTypMaxUnitInterchannel Isolation-90-dBDC AccuracyInterchannel Gain Mismatch -0.1-dB Gain Error -5-+5%Gain Drift-±100-ppm/°CAnalog Input CharacteristicsFull-Scale Input Voltage 0.53*VA0.56*VA 0.59*VAVppInput Impedance-25-k ΩCS5341ANALOG CHARACTERISTICS - AUTOMOTIVE GRADETest Conditions (unless otherwise specified): Input test signal is a 1 kHz sine wave; measurement bandwidth is 10 Hz to 20 kHz.6.Referred to the typical full-scale input voltageDynamic Performance for Automotive Grade VA = 5 V VA = 3.3 VSingle-Speed Mode Fs = 48kHzSymbol MinTypMaxMinTypMaxUnitDynamic RangeA-weighted unweighted 9794105102--949110299--dB dBTotal Harmonic Distortion + Noise(Note 6) -1dB -20dB -60dBTHD+N----98-82-42-90------95-79-39-87--dB dB dBDouble-Speed Mode Fs = 96kHzSymbol MinTypMaxMinTypMaxUnitDynamic RangeA-weighted unweighted40kHz bandwidth unweighted 9794-10510299---9491-1029996---dB dB dBTotal Harmonic Distortion + Noise (Note 6) -1dB -20dB -60dB40kHz bandwidth -1dBTHD+N-----98-82-42-95-90--------95-79-39-87-87---dB dB dB dBQuad-Speed Mode Fs = 192kHzSymbol MinTypMaxMinTypMaxUnitDynamic RangeA-weighted unweighted40kHz bandwidth unweighted 9794-10510299---9491-1029996---dB dB dBTotal Harmonic Distortion + Noise (Note 6) -1dB -20dB -60dB40kHz bandwidth -1dBTHD+N-----98-82-42-95-90--------95-79-39-87-87---dB dB dB dBDynamic Performance All ModesMinTypMaxUnitInterchannel Isolation-90-dBDC AccuracyInterchannel Gain Mismatch -0.1-dB Gain Error -10-+10%Gain Drift-±100-ppm/°CAnalog Input CharacteristicsFull-Scale Input Voltage 0.50*VA0.56*VA 0.62*VAVppInput Impedance-25-k ΩCS5341DIGITAL FILTER CHARACTERISTICS7.Filter characteristics scale precisely with Fs8.Response shown is for Fs equal to 48 kHz. Filter characteristics scale with Fs.ParameterSymbol Min Typ Max UnitSingle-Speed ModePassband (-0.1 dB)(Note 7)0-0.4895Fs Passband Ripple -0.035-0.035dB Stopband(Note 7)0.5687--Fs Stopband Attenuation70--dB Total Group Delay (Fs = Output Sample Rate)t gd-12/Fs -s Double-Speed ModePassband (-0.1 dB)(Note 7)0-0.4895Fs Passband Ripple -0.025-0.025dB Stopband(Note 7)0.5604--Fs Stopband Attenuation69--dB Total Group Delay (Fs = Output Sample Rate)t gd-9/Fs -s Quad-Speed ModePassband (-0.1 dB)(Note 7)0-0.2604Fs Passband Ripple -0.025-0.025dB Stopband(Note 7)0.5--Fs Stopband Attenuation60--dB Total Group Delay (Fs = Output Sample Rate)t gd-5/Fs -s High-Pass Filter CharacteristicsFrequency Response -3.0 dB -0.13 dB (Note 8)-120--Hz Hz Phase Deviation @ 20Hz(Note 8)-10-Deg Passband Ripple--0dBFigure 1. Single-Speed Mode Stopband Rejection Figure 2. Single-Speed Mode Stopband RejectionFigure 5. Double-Speed Mode Stopband Rejection Figure 6. Double-Speed Mode Stopband RejectionCS5341Figure 7. Double-Speed Mode Transition Band (Detail)Figure 8. Double-Speed Mode Passband RippleFigure 9. Quad-Speed Mode Stopband Rejection Figure 10. Quad-Speed Mode Stopband RejectionFigure 11. Quad-Speed Mode Transition Band (Detail)Figure 12. Quad-Speed Mode Passband RippleCS5341DC ELECTRICAL CHARACTERISTICS(GND = 0V, all voltages with respect to 0V. MCLK=12.288MHz; Master Mode)9.Power-Down Mode is defined as RST = Low, with all clocks and data lines held static at a valid logiclevels.10.Valid with the recommended capacitor values on FILT+ and VQ as shown in the Typical ConnectionDiagram.DIGITAL CHARACTERISTICSParameterSymbolMinTypMaxUnitDC Power Supplies:Positive Analog Positive DigitalPositive LogicVA VD VL 3.13.11.7--- 5.255.255.25V V V Power Supply CurrentVA = 5 V (Normal Operation)VA = 3.3 V VL,VD = 5V VL,VD = 3.3VI A I A I D I D ----2118.215925.522.518.510mA mA mA mA Power Supply CurrentVA = 5V (Power-Down Mode) (Note 9)VL,VD=5VI A I D -- 1.50.4--mA mA Power Consumption VL, VD, VA = 5V (Normal Operation)VL, VD, VA = 3.3V (Power-Down Mode)------180909.5220107.2-mW mW mW Power Supply Rejection Ratio (1kHz)(Note 10)PSRR-65-dB V Q Nominal Voltage Output Impedance--VA ÷225--V k ΩFilt+ Nominal Voltage Output ImpedanceMaximum allowable DC current source/sink---VA 360.01---V k ΩmAParameterSymbolMinTypMaxUnitsHigh-Level Input Voltage (% of VL)V IH 70%--V Low-Level Input Voltage(% of VL)V IL --30%V High-Level Output Voltage at I o = 100µA (% of VL)V OH 70%--V Low-Level Output Voltage at I o =100µA (% of VL)V OL --15%V Input Leakage CurrentI in-10-+10µACS5341SWITCHING CHARACTERISTICS - SERIAL AUDIO PORT(Logic "0" = GND = 0V; Logic "1" = VL, C L = 20pF)11. For a description of speed modes, please refer to Table 1 on page 15.Parameter Symbol Min Typ Max UnitMCLK SpecificationsMCLK Periodt clkw39-45ns 78-1953ns MCLK Pulse Duty Cycle40-60%Master ModeSCLK falling to LRCKSingle-Speed t mslr-20-20ns Double-Speed -20-20ns Quad-Speed-8-8ns SCLK falling to SDOUT valid. t sdo--32ns SCLK Duty Cycle.Single-Speed -50-%Double-Speed -50-%Quad-Speed-33-%Slave ModeSingle-Speed (Note 11)LRCK Duty Cycle 405060%SCLK Period t sclkw156--ns SCLK Duty Cycle455055%SDOUT valid before SCLK rising t stp 10--ns SDOUT valid after SCLK rising t hld 5--ns SCLK falling to LRCK edget slrd -20-20ns Double-Speed (Note 11)LRCK Duty Cycle 405060%SCLK Period t sclkw156--ns SCLK Duty Cycle455055%SDOUT valid before SCLK rising t stp 10--ns SDOUT valid after SCLK rising t hld 5--ns SCLK falling to LRCK edge.t slrd-20-20ns Quad-Speed (Note 11)LRCK Duty Cycle 405060%SCLK Period t sclkw78--ns SCLK Duty Cycle29.73350%SDOUT valid before SCLK rising t stp 10--ns SDOUT valid after SCLK rising t hld 5--ns SCLK falling to LRCK edge.t slrd-8-8nsCS5341Figure 13. Master Mode, Left-Justified SAI Figure 14. Slave Mode, Left-Justified SAIFigure 15. Master Mode, I²S SAI Figure 16. Slave Mode, I²S SAICS5341 2.PIN DESCRIPTIONPin Name#Pin DescriptionM0 M1116Mode Selection (Input) - Determines the operational mode of the device.MCLK2Master Clock (Input) - Clock source for the delta-sigma modulator and digital filters. VL3Logic Power (Input) - Positive power for the digital input/output.SDOUT4Serial Audio Data Output (Output) - Output for two’s complement serial audio data. GND5,14Ground (Input) - Ground reference. Must be connected to analog ground.VD6Digital Power (Input) - Positive power supply for the digital section.SCLK7Serial Clock (Input/Output) - Serial clock for the serial audio interface.LRCK8Left Right Clock (Input/Output) - Determines which channel, Left or Right, is currently active on the serial audio data line.RST9Reset (Input) - The device enters a low power mode when low.AINL AINR 1012Analog Input (Input) - The full-scale analog input level is specified in the Analog Charac-teristics specification table.VQ11Quiescent Voltage (Output) - Filter connection for the internal quiescent reference voltage.VA13Analog Power (Input) - Positive power supply for the analog section.FILT+15Positive Voltage Reference (Output) - Positive reference voltage for the internal sampling circuits.M0M1MCLK FILT+VL REF_GNDSDOUT VAGND AINRVD VQSCLK AINLLRCK RST11634785261514131211109CS5341 3.TYPICAL CONNECTION DIAGRAMCS53414.APPLICATIONS4.1Single-, Double-, and Quad-Speed ModesThe CS5341 can support output sample rates from 2kHz to 200kHz. The proper speed mode can be de-termined by the desired output sample rate and the external MCLK/LRCK ratio, as shown in Table 1.Table 1. Speed Modes and the Associated Output Sample Rates (Fs)4.2Operation as Either a Clock Master or SlaveThe CS5341 supports operation as either a clock master or slave. As a clock master, the LRCK and SCLK pins are outputs with the left/right and serial clocks synchronously generated on-chip. As a clock slave, the LRCK and SCLK pins are inputs and require the left/right and serial clocks to be externally generated. The selection of clock master or slave is made via the Mode pins as shown in Table 2.Speed ModeMCLK/LRCKRatioOutput Sample Rate Range (kHz)Single-Speed Mode 512x 43 - 50256x 2 - 50Double-Speed Mode 256x 86 - 100128x 50 - 100Quad-Speed Mode128x 172 - 20064x*100 - 200* Quad-Speed Mode, 64x only available in Master Mode.M1 (Pin 16)M0 (Pin 1)MODE00Clock Master, Single-Speed Mode 01Clock Master, Double-Speed Mode 10Clock Master, Quad-Speed Mode 11Clock Slave, All Speed ModesTable 2. CS5341 Mode ControlCS53414.2.1Operation as a Clock MasterAs a clock master, LRCK and SCLK operate as outputs. The left/right and serial clocks are internally de-rived from the master clock with the left/right clock equal to Fs and the serial clock equal to 64x Fs, as shown in Figure 18.4.2.2Operation as a Clock Slave with Auto-DetectLRCK and SCLK operate as inputs in clock Slave Mode. It is recommended that the left/right clock be synchronously derived from the master clock and must be equal to Fs. It is also recommended that the serial clock be synchronously derived from the master clock and be equal to 64x Fs to maximize system performance.A unique feature of the CS5341 is the automatic selection of either Single-, Double- or Quad-Speed Mode when operating as a clock slave. The auto-mode select feature negates the need to configure the Mode pins to correspond to the desired mode. The auto-mode selection feature supports all standard audio sample rates from 2 to 200kHz. However, there are ranges of non-standard audio sample rates that are not supported when operating with a fast MCLK (512x, 256x, 128x for Single-, Double-, and Quad-Speed Modes, respectively). Please refer to Table 1 for supported sample rate ranges.Figure 18. CS5341 Master Mode ClockingCS53414.2.3Master ClockThe CS5341 requires a Master clock (MCLK) which runs the internal sampling circuits and digital filters.There is also an internal MCLK divider which is automatically activated based on the speed mode and frequency of the MCLK. Table 3 shows a listing of the external MCLK/LRCK ratios that are required.Table 4 lists some common audio output sample rates and the required MCLK frequency. Please note that not all of the listed sample rates are supported when operating with a fast MCLK (512x, 256x, 128x for Single-, Double-, and Quad-Speed Modes, respectively).4.3Serial Audio InterfaceThe CS5341 supports both I²S and Left-Justified serial audio formats. Upon start-up, the CS5341 will detect the logic level on SDOUT (pin 4). A 10 k Ω pull-up to VL is needed to select I²S format, and a 10 k Ω pull-down to GND is needed to select Left-Justified format. Figures 19 and 20 illustrate the I²S and Left-Justified audio formats. Please see Figures 13 through 16, for more information on the required timing for the two serial audio interface formats. Also see Application Note AN282 for a detailed discussion of the serial audioSingle-Speed ModeDouble-Speed ModeQuad-Speed ModeMCLK/LRCK Ratio256x, 512x128x, 256x64x*,128x* Quad Speed, 64x only available in Master Mode.Table 3. Master Clock (MCLK) RatiosSAMPLE RATE (kHz)MCLK (MHz)328.192 44.111.289622.57924812.28824.576648.19288.211.289622.57929612.28824.57619212.28824.576Table 4. Master Clock (MCLK) Frequencies for Standard Audio Sample RatesCS5341 4.4Power-Up SequenceReliable power-up can be accomplished by keeping the device in reset until the power supplies, clocks andconfiguration pins are stable. It is also recommended that reset be enabled if the analog or digital suppliesdrop below the minimum specified operating voltages to prevent power-glitch-related issues.4.5Analog ConnectionsThe analog modulator samples the input at half of the MCLK frequency, or nominally 6.144MHz. The digitalfilter will reject signals within the stopband of the filter. However, there is no rejection for input signals whichare multiples of the input sampling frequency (n×6.144MHz), where n=0,1,2,... Refer to Figure21, which shows the suggested filter that will attenuate any noise energy at 6.144MHz in addition to providing the op-timum source impedance for the modulators. The use of capacitors that have a large voltage coefficient(such as general-purpose ceramics) must be avoided since these can degrade signal linearity. Array4.6Grounding and Power Supply DecouplingAs with any high resolution converter, achieving optimal performance from the CS5341 requires careful at-tention to power supply and grounding arrangements. Figure17 shows the recommended power arrange-ments, with VA and VL connected to clean supplies. VD, which powers the digital filter, may be run from thesystem logic supply or may be powered from the analog supply via a resistor. In this case, no additionaldevices should be powered from VD. Decoupling capacitors should be as near to the ADC as possible, withthe low-value ceramic capacitor being the nearest. All signals, especially clocks, should be kept away fromthe FILT+ and VQ pins in order to avoid unwanted coupling into the modulators. The FILT+ and VQ decou-pling capacitors, particularly the 0.01µF, must be positioned to minimize the electrical path from FILT+ andREF_GND. Furthermore, all ground pins on CS5341 should be referenced to the same ground reference.The CDB5341 evaluation board demonstrates the optimum layout and power supply arrangements. To min-imize digital noise, connect the ADC digital outputs only to CMOS inputs.4.7Synchronization of Multiple DevicesIn systems where multiple ADCs are required, the user can achieve simultaneous sampling if the MCLK andLRCK signals are the same for all of the CS5341’s in the system. If only one master clock source is needed,one solution is to place one CS5341 in Master Mode, and slave all of the other CS5341’s to the one master.If multiple master clock sources are needed, a possible solution would be to supply all clocks from the sameexternal source and time the CS5341 reset with the inactive (falling) edge of MCLK. This will ensure that allconverters begin sampling on the same clock edge.CS53414.8Capacitor Size on the Reference Pin (FILT+)The CS5341 requires an external capacitance on the internal reference voltage pin, FILT+. The size of this decoupling capacitor will affect the low frequency distortion performance as shown in Figure 22, with larger capacitor values used to optimize low frequency distortion performance. This plot was taken using the CDB5341 evaluation platform, with the device running in Single-Speed Mode and VA=VD=VL=5 V.Figure 22. CS5341 THD+N versus Frequency47 uF100 uF22 uF10 uF6.8 uF4.7 uF3.3 uF2.2 uF1 uF5.6 uFCS5341 5.PARAMETER DEFINITIONSDynamic RangeThe ratio of the rms value of the signal to the rms sum of all other spectral components over the specified bandwidth. Dynamic Range is a signal-to-noise ratio measurement over the specified bandwidth made witha -60dBFS signal. 60dB is added to resulting measurement to refer the measurement to full-scale. Thistechnique ensures that the distortion components are below the noise level and do not affect the measure-ment. This measurement technique has been accepted by the Audio Engineering Society, AES17-1991, and the Electronic Industries Association of Japan, EIAJ CP-307. Expressed in decibels.Total Harmonic Distortion + NoiseThe ratio of the rms value of the signal to the rms sum of all other spectral components over the specified bandwidth (typically 10Hz to 20kHz), including distortion components. Expressed in decibels. Measured at -1 and -20dBFS as suggested in AES17-1991 Annex A.Frequency ResponseA measure of the amplitude response variation from 10Hz to 20kHz relative to the amplitude response at1kHz. Units in decibels.Interchannel IsolationA measure of crosstalk between the left and right channels. Measured for each channel at the converter'soutput with no signal to the input under test and a full-scale signal applied to the other channel. Units in deci-bels.Interchannel Gain MismatchThe gain difference between left and right channels. Units in decibels.Gain ErrorThe deviation from the nominal full-scale analog input for a full-scale digital output.Gain DriftThe change in gain value with temperature. Units in ppm/°C.Offset ErrorThe deviation of the mid-scale transition (111...111 to 000...000) from the ideal. Units in mV.DS564F121CS53416.PACKAGE DIMENSIONS1.“D” and “E1” are reference datums and do not included mold flash or protrusions, but do include moldmismatch and are measured at the parting line, mold flash or protrusions shall not exceed 0.20mm per side.2.Dimension “b” does not include dambar protrusion/intrusion. Allowable dambar protrusion shall be0.13mm total in excess of “b” dimension at maximum material condition. Dambar intrusion shall not re-duce dimension “b” by more than 0.07mm at least material condition.3.These dimensions apply to the flat section of the lead between 0.10 and 0.25mm from lead tips.THERMAL CHARACTERISTICSINCHES MILLIMETERSNOTEDIM MIN NOM MAX MIN NOM MAX A ----0.043---- 1.10A10.0020.0040.0060.05--0.15A20.033460.03540.0370.850.900.95b 0.007480.00960.0120.190.2450.302,3D 0.1930.19690.201 4.90 5.00 5.101E 0.2480.25190.256 6.30 6.40 6.50E10.1690.17320.177 4.30 4.40 4.501e --0.026 BSC ----0.65 BSC --L 0.0200.0240.0280.500.600.70µ0°4°8°0°4°8°JEDEC #: MO-153Controlling Dimension is MillimetersParameterSymbol MinTypMaxUnit Allowable Junction Temperature --135°C Junction to Ambient Thermal ImpedanceθJA-75-°C/W16L TSSOP (4.4mm BODY) PACKAGE DRAWINGEN123eb 2A1A2ADSEATING PLANE E11LSIDE VIEWEND VIEWTOP VIEW∝22DS564F1CS53417.ORDERING INFORMATION8.REVISION HISTORYProductDescription Package Pb-Free Grade Temp Range ContainerOrder #CS5341105 dB, 192 kHz, Multi-BitAudio A/D Converter 16-TSSOP YES Commercial -10° to +70° CBulk CS5341-CZZ Tape & ReelCS5341-CZZR CS5341105 dB, 192 kHz, Multi-BitAudio A/D Converter 16-TSSOP YES Automotive -40° to +85° CBulk CS5341-DZZ Tape & ReelCS5341-DZZR CDB5341 CS5341 Evaluation Board -----CDB5341ReleaseChangesA1Initial Advance releaseA2Updated serial port timing specificationsPP1Change value of capacitors in analog input buffer diagram Update Sample Rate rangeAdded Applications section on FILT+ filter capacitor Add CS5341-CZZ as part numberReplace available part number CS5341-DZ with CS5341-DZZ Initial Preliminary product releasePP2Add lead-free option to ordering information F1Remove CS5341-CZ from Ordering InformationRedefine Serial Audio Port Switching Characteristics Correct dimension “e” under Package Dimensions Update maximum current and power specifications Update Filt+ output impedance specificationContacting Cirrus Logic SupportFor all product questions and inquiries, contact a Cirrus Logic Sales Representative. To find the one nearest to you, go to .IMPORTANT NOTICECirrus Logic, Inc. and its subsidiaries ("Cirrus") believe that the information contained in this document is accurate and reliable. However, the information is subject to change without notice and is provided "AS IS" without warranty of any kind (express or implied). Customers are advised to obtain the latest version of relevant information to verify, before placing orders, that information being relied on is current and complete. All products are sold subject to the terms and conditions of sale supplied at the time of order acknowledgment, including those pertaining to warranty, indemnification, and limitation of liability. No responsibility is assumed by Cirrus for the use of this information, including use of this information as the basis for manufacture or sale of any items, or for infringement of patents or other rights of third parties. This document is the property of Cirrus and by furnishing this information, Cirrus grants no license, express or implied under any patents, mask work rights,copyrights, trademarks, trade secrets or other intellectual property rights. Cirrus owns the copyrights associated with the information contained herein and gives con-sent for copies to be made of the information only for use within your organization with respect to Cirrus integrated circuits or other products of Cirrus. This consent does not extend to other copying such as copying for general distribution, advertising or promotional purposes, or for creating any work for resale.CERTAIN APPLICATIONS USING SEMICONDUCTOR PRODUCTS MAY INVOLVE POTENTIAL RISKS OF DEATH, PERSONAL INJURY, OR SEVERE PROP-ERTY OR ENVIRONMENTAL DAMAGE (“CRITICAL APPLICATIONS”). CIRRUS PRODUCTS ARE NOT DESIGNED, AUTHORIZED OR WARRANTED FOR USE IN AIRCRAFT SYSTEMS, MILITARY APPLICATIONS, PRODUCTS SURGICALLY IMPLANTED INTO THE BODY, AUTOMOTIVE SAFETY OR SECURITY DE-VICES, LIFE SUPPORT PRODUCTS OR OTHER CRITICAL APPLICATIONS. INCLUSION OF CIRRUS PRODUCTS IN SUCH APPLICATIONS IS UNDER-STOOD TO BE FULLY AT THE CUSTOMER’S RISK AND CIRRUS DISCLAIMS AND MAKES NO WARRANTY, EXPRESS, STATUTORY OR IMPLIED,INCLUDING THE IMPLIED WARRANTIES OF MERCHANTABILITY AND FITNESS FOR PARTICULAR PURPOSE, WITH REGARD TO ANY CIRRUS PRODUCT THAT IS USED IN SUCH A MANNER. IF THE CUSTOMER OR CUSTOMER’S CUSTOMER USES OR PERMITS THE USE OF CIRRUS PRODUCTS IN CRITICAL APPLICATIONS, CUSTOMER AGREES, BY SUCH USE, TO FULLY INDEMNIFY CIRRUS, ITS OFFICERS, DIRECTORS, EMPLOYEES, DISTRIBUTORS AND OTHER AGENTS FROM ANY AND ALL LIABILITY, INCLUDING ATTORNEYS’ FEES AND COSTS, THAT MAY RESULT FROM OR ARISE IN CONNECTION WITH THESE USES.Cirrus Logic, Cirrus, and the Cirrus Logic logo designs are trademarks of Cirrus Logic, Inc. All other brand and product names in this document may be trademarks or service marks of their respective owners.I²C is a registered trademark of Philips Semiconductor.。
NOVATEK-ELECTRO LTD 产品说明书:UBZ-301(10-100A)通用感应电机保护

NOVATEK-ELECTRO LTDResearch-and-Manufacture CompanyUBZ-301 (10-100A)UNIVERSAL INDUCTIONMOTOR PROTECTION UNITUSERS MANUALCONTROLS DESCRIPTION AND DIMENSIONS DIAGRAM 4151. Control for nominal current setting, Inom;2. Control for operating current setting, Iop (% Inom);3. Control for T2 (double overload trip) delay setting;4. Combined trip adjustment control for Umin/Umax;5. Control for phase imbalance adjustment, PI;6. Control for trip threshold for the minimum current, Imin (%Inom);7. Control for automatic reset delay setting, Ton;8. Green LED indicating for the mains voltage presence;9,10,11. Red LEDs indicating faults for insulation, overload and U fault respectively;12. Green LED indicating for load energization;13. Output terminals;14. Input terminals (10,11,12 are used for the connection with the BO-01 exchange unit);15. Insulation monitoring terminal.1 APPLICATIONSThe UBZ-301(10-100A)universal induction motor protection unit is designed for the continuous monitoring of the mains voltage parameters and for RMS phase/line currents of 3-Phase AC 380V/50Hz electrical equipment monitoring, primarily, of induction motors whose power is from 5kW up to 50 kW, isolated neutral system included.The unit provides full and effective protection of electrical equipment by a magnetic starter (contactor) coil control.The unit isolates electrical equipment from the running system and/or disables its start. This is performed in the following cases:1. when the mains voltage is of poor quality (unallowable voltage jumps, phase loss, incorrect phase sequence and phase «coincidence», phase/line voltage imbalance);2. when mechanical overloads (symmetrical phase/line current overload) take place. The unit performs overload protection with a dependent time delay;3. when phase/line current asymmetrical overloads induced by faults inside the motor occur. The unit performs protection from phase current imbalance and further disables an automatic reset;4. when phase current asymmetry without overload occurs that is induced by the insulation fault inside the motor and/or the power cable;5.when motor load is lost(«dry stroke»for pumps).The unit provides the minimum start and/or operating current protection;6. when insulation level to frame is abnormally low. The unit performs insulation level test before start and if the insulation is poor the start is disabled.7.when stator winding ground-to-fault occurs during operation. The unit performs the ground leakage current protection.The UBZ-301 (10-100A) provides:•a simple and accurate electromotor nominal current setting by nominal current standard scale;•the electromotor operating current setting that differs from standard values;•overload tripping with a dependent time delay (the current-time characteristic curve is plotted for a conventionally cold motor). The motor heat balance differential equation is being solved in the operation process. This approach enables to take account of the preceding electromotor status and to make a decision on heat overload presence with the maximum validity. This method also permits to allow for a motor start heating and to restrict (at the customer’s option) amount of starts per unit time;•shift of current-time characteristic curve along the current-axis and along time-axis as well;•setting of trip thresholds for the minimum/the maximum voltage,line voltage&phase current imbalance, and also for automatic reset delay at the personal customer’s discretion;•fault type indication, the mains voltage presence indication, current range indication the unit is adjusted to, and load energization indication;•the data exchange and transfer to the local computer network according to the RS-485 MODBUS record through the BO-01 exchange unit (BO-01 is supplied on order).2 DESCRIPTIONThe unit is a microprocessor-based digital device that provides a high degree of reliability and accuracy. The unit doesn’t need any auxiliary supply because it retrieves it's energy demand out of the measurement signal: it’s self-powered by the voltage to be monitored. Simultaneous isolated independent monitoring for the mains voltage and phase currents permits to detect the type of occurring fault and to provide a different decision-making logic for each fault type. When the mains voltage faults occur the unit performs automatic load reset on return voltage parameters to normal operating conditions. If a fault is induced by abnormal condition inside the motor(phase current imbalance at the symmetrical mains voltage,leakage current presence etc.) restart is disabled.The unit is stocked with three toroidal current transducers. Two of them are the phase/line current transducers (TT1, TT2), power phase cables are pulled through them. The third transducer is the differential current transducer(DCT)that has an enlarged diameter,because three power phase cables are pulled through it. By the 6, 7, 8, 9 terminals the unit is connected in parallel to the mains supply to be monitored. The unit output is provided with N.O. and N. C. contacts (the 1, 2, 3, 4 terminals). The output 3-4 terminals are connected in series with the starter coil power supply (with control circuit). The5terminal is designed to monitor the insulation level. The unit wiring diagram is shown below.When the unit trips the load is de-energized by a break in the magnetic starter coil power circuit through the N. C. 3-4 contacts.Table 1 - The 1-2-3-4 output contacts specificationMax. current for~ 250 V A. C.Max. powerMax sustained safevoltage ~Max. current for U = 30V D.C.Cosφ = 0.43A 2000VA 460V 3ACosφ = 1.05ANominal parameters and trip thresholds are set by front-panel screwdriver potentiometers.Nominal current setting. Nominal current is set by № 1 potentiometer. There are eleven positions of the potentiometer. Each position corresponds to the specific standard nominal current scale value (see below Table of Nominal Currents). Each position is characterized by the specific number of blinks that the green «On» LED makes. To set the nominal current one needs to bring out potentiometer control arm to a corresponding position; when the unit is energized the number of blinks «On» LED must correspond to the Table below. One needs to take into account that there are «dead bands» between the positions where «On» LED glows without blinks and where the nominal current is indefinite.In order to set operating value which is different from the nominal one that is specified in the nominal current table, it’s recommended the № 1 potentiometer to set to the position corresponding to the nearest value from the nominal current scale, and by the № 2 potentiometer one can increase or decrease the necessary value in % from the set value.Table 2 - Nominal current tablePotentiometer №1 devisionsNom. current, АGreen LED «On» blink1101bl.- pause 212,52bl.- pause 3163bl.- pause 4204bl.- pause 5255bl.- pause 6326bl.- pause 7407bl.- pause 8508bl.- pause 9639bl.- pause 108010bl.- pause 1110011bl.- pauseNOTE S:1.Continuous green «On» LED glow means that the potentiometer is set in «dead band». One needs to set the potentiometer so as the green LED blinked and the number of blinks corresponded to the set nominal current.2.Nominal currents setting is to be performed correcting for load connections (Wye/Delta), according to ratings of engine.Controls and adjustmentsThe unit has seven independent controls. For user’s convenience screwdriver slots of adjusting potentiometers are brought out to the unit front panel.•№1 – «Inom» - nominal current setting; there are eleven positions and each position corresponds to the specific current from the nominal currents table;•№2 – «Iop» - operating current; it is set in ± 15 percent of nominal current, it has ten scale marks;•№3 – «T2» - overload trip delay when there is double overload for operating current set; in the central position T2 ≈ 58-60 seconds The minimum time delay is 10 seconds, the maximum time delay is 100 seconds. The control shifts current-time characteristic dependence along time axis;•№4 – «Unom(%)» - combined control for Umax/Umin threshold in percent of the nominal voltage; according to this setting before the load energization the unit is checking the mains voltage level and, depending on its value, permits or forbids the load energization; after the load has been energized the voltage monitoring is going on but the load de-energization decision is made for currents;•№5 – «PI%» - trip threshold control for line voltage imbalance and RMS phase current imbalance; it has ten scale marks. The parameter is calculated as the difference between the maximum and the minimum values, in percent of the maximum value. If current imbalance percentage is twice as much as voltage imbalance percentage then it’s supposed that the imbalance is induced by fault conditions inside the motor. The automatic reset is forbidden and the unit is disabled;•№6 – «Imin» - trip threshold control for the minimum operating current, in percent of operating current set. It has ten scale marks from 0% to 75%: in «0» position this control is off;•№7 – «Ton» - automatic reset delay, it is within 0 – 600 seconds range; the scale is logarithmic.Indication•the green «ON» LED indicates that voltage exists in the mains. In the blink mode of glow the blink number between pauses corresponds to the specific nominal current from the nominal current table; there is a continuous glow in a «dead band». One needs to set a nominal current in the blink mode of operation;•the green «Load» LED indicates that the load is energized (the 3-4 terminals are closed);•the red «Insulation» LED lights up with continuous glow before the start if the stator/ power cable winding insulation level is abnormally low (less than 500 kOhms), and also during operation when there is a tripping for differential current; the unit is disabled;•the red «U Fault» LED glows when the mains voltage fault has occurred. The blink mode of operation switches on when there is undervoltage/overvoltage, phase imbalance for the mains voltage, voltage is not present on all three phases;•incorrect phase sequence or phase coincidence induces the mode of operation when all three red LEDs are blinking in turn;•the red «Overload» LED blinks when the average phase current exceeds the nominal one. After the unit has tripped for overload this LED comes to glow during 0.9 AR (automatic reset) delay.4 TECHNICAL BRIEFNominal line voltage, V380Mains frequency, Hz45-55Nominal current range in UBZ-301 10-100, А10-100Operating current setting range, % of nominal±15Double overload delay adjustment range, sec10-100Voltage threshold adjustment range, % of nominal±(5-20)Phase imbalance adjustment range, %5-20Trip threshold adjustment range for the minimum current, % of nominal0-75Automatic reset delay adjustment range ( Тon), sec0-600First energization load delay when Тon= 0, sec2-3Trip delay for current overload According to current-time characteristic curveTrip delay for voltage fault, sec2Trip delay for current fault (overload excluded), sec2 Fixed trip point for leakage current, А 1.0 Insulation resistance threshold, kОhms500±20 Voltage hysteresis, V10/17 Heat hysteresis, % of stored-up heat after load de-energization33Trip threshold accuracy for current, % of nominal current, not more than2-3 Trip threshold accuracy for voltage, V, not more than3 Phase imbalance accuracy, %, not more than 1.5 Operating voltage range, % of nominal one50-150 Power consumption (under load), VA, not more than 3.0 Maximum switched current of output contacts, A5 Output contact life:- under 5A load , operations, no less than - under 1A load , operations, no less than 100 000 1 000 000Enclosure:- apparatus- terminal block IP40 IP20Operating temperature range, °C from -35 to +55 Storage temperature, °C from -45 to +70 Weight, kg, not more than0.200Case dimensions 4 modules of S-typeMounting standard 35 mm DIN-railMounting position arbitrary5 OPERATION1. After supply voltage has been applied to the unit and before the output relay is energized the unit checks:•a stator winding insulation level to frame. If insulation resistance is below 500±20 kOhms, the load is not energized. The red «Insulation» LED glows;•the mains voltage quality,i.e.if voltage is present on all three phases,if the mains voltage is symmetrical, what the RMS line voltage value is like. When any of inhibit factors is present, the load is not energized, the red «U Fault» LED blinks;•a correct phase sequence, and phase «non-coincidence». When any of inhibit factors is present, the load is not energized, all red LEDs are blinking in turn; If all the parameters are normal, the outlet relay will be energized after Ton delay has expired (the 3-4 contacts are being closed and the 1-2 contacts are being opened) - the green «Load» LED glows. If load currents are absent (there are no less 2% of nominal one) the reason is that the load is de-energized. Voltage monitoring and insulation level is going. Output relay of unit is de-energized if inhibit factors are present in pause without currents;2. After the load is energized the unit performs voltage and current monitoring. The decision on load de-energization is made according to the following factors:•RMS current exceeds the nominal (operating) current (set by №№ 1, 2, 3 potentiometers); if there is current overload without heat overload the red «Overload» LED blinks but the load is not de-energized. If current overload induces heat overload the load is de-energized. The red «Overload»LED glows and is ON during 0.9Ton. The automatic reset is permitted;•current imbalance (set by №5 potentiometer) is twice exceeds the mains voltage imbalance; the load is de-energized, all red LEDs glow, the unit is disabled, the automatic reset is forbidden. To enable the unit one needs to remove supply voltage from the unit. It’s supposed that this type of fault is induced by abnormal conditions inside the motor;•current imbalance (set by №5 potentiometer) is less than twice exceeds voltage imbalance; the load is de-energized, the red «U Fault» LED glows, the automatic reset is permitted;•current imbalance (set by №5 potentiometer) is less than voltage imbalance; the load is de-energized, the red «U Fault» LED blinks, the automatic reset is permitted;•the average current value is less than Imin (set by №6 potentiometer); the load is de-energized, all red LEDs blink simultaneously, the unit is disabled, the automatic reset is forbidden. To enable the unit one needs to remove the supply voltage from the unit.Electromotor protection against heat overloadThe electromotor heat balance equation is being solved as the work advances. It’s supposed that:•the motor was cold before start;•during operation the motor releases the heat which is proportional to the current square;•after the stop the motor cools down exponentially.Below is the current-time characteristic curve with different T2 values (set by №3 potentiometer), where:•I/In – current ratio relative to the nominal current;•T/T2 -- actual trip delay relative to T2 (set by № 3 potentiometer).Current-time characteristic dependenceThe current-time characteristic dependence shown in the tables below is given for the standard recommended T2 value (the №3 potentiometer middle position corresponds to 60 seconds when double overload occurs):I/Inom 1.1 1.2 1.4 1.72 2.73456781015Тsec36524714888.66036.424.613.58.5 5.9 4.3 3.3 2.10.9After the load has been de-energized owing to the heat overload it will automatically be energized again:•according to heat hysteresis if time delay Ton=0, i. e. the motor must cool down 33% of the stored up heat;•according time delay Ton (№ 7 potentiometer) if Ton isn’t equal 0.By suitable selection of different Ton values, heat hysteresis considered, one can reduce number of starts per time unit because in the intermittent cycle the unit stores heat quantity released at the start of the motor.6 PRELIMINARY STARTING PROCEDURE AND SERVICE MANUALThe unit produced is completely ready for operation and needs no special pre-starting procedure measures. Owing to digital technology all the unit settings are aligned quite accurate, so no control devices are needed to adjust them. Use of the unit according to specifications above and the present service manual, continuous work included, relieves of preventive maintenance during service life. To put the unit in operation one must follow operating instructions given below:1.To set nominal (operating) current, trip thresholds, trip delays and reset delay by potentiometer's contact arms.2.To connect the unit according to the wire diagram given below:•by the 6(L1), 7(L2), 8(L3), 9(N) terminals the unit is connected in parallel to the mains supply to be monitored;•two current transducers (each one of them is put on two power phase wires that carry the load) are connected to the 13, 14, 15, 16 terminals; in connecting one has to consider the transducers grading;1st transducer– the beginning – the 13 terminal, the end – the 14 terminal;2nd transducer– the beginning – the 15 terminal, the end – the 15 terminal;•a differential current transducer that is put on the three power phase wires must be connected to the 17, 18 terminals (the connection grading is unimportant);•the 5 insulation monitoring terminal is connected to one of the MS output contacts;•output contacts (the 3-4 terminals) are connected to the MS coil power supply circuit (control circuit);•the BO-01 exhange and date transfer unit is connected to the 10, 11, 12 terminals (this unit is supplied on order).3.To apply a voltage to the unit. The correct setting of nominal current is checked by the number of blinks that the green LED makes. After Ton has expired (if there are no factors that can forbid energizing) the output relay of the unit is energized. If Ton=0, the first energizing will occur after 2-3 sec delay has expired.NOTE - The unit must be connected subject to the safety regulations. To set settings is recommended in «off» state. To set settings alive is permitted in the test conditions subject to the safety regulations.ATTENTION!If immediately after the load has been energized the unit de-energizes it and disables it for current imbalance,the incorrect polarity of the current transducers TT1or TT2 connection may be a reason. Then it’s recommended to change one of the transducers connection by reversing the places“the beginning-the end”of the13-16terminals.If the effect pointed above repeats when the load is re-energized it means that the transducers were connected correctly and the imbalance arose from EM and/or power cable fault.NOTES:1 Transducers are mounted by plastic clamps (they are component parts of supplies).2 The phase wires which are passing through the differential transducer to try to symmetrize in the centerof the transducer.WIRING DIAGRAMDT–differential current transducer (differential current transformer);CT1,CT2–current--transducers;BO-01– exchange and date transfer unit (on order)NOTE:1 “START”-button and “STOP”-button can be connected to MSC power supply circuit if necessary;2 The 220V MSC connection is shown here. The 380V MSC power supply circuit is analogous, coil power is applied from different phases through the 3-4 contacts;3 If BO-01 is absent the 10, 11, 12 terminals are not used.7 STORAGE AND SHIPPING CONDITIONSThe unit in manufacturer package should be stored in enclosed rooms at –45 to +70 °C and exposed to no more than 80% of relative humidity when there are no fumes in the air that exert a deleterious effect on package and the unit material. The Buyer must provide the protection of the unit against mechanical damages in transit.8 WARRANTYNovatek-Electro LTD. Company warrants a trouble-free operation of the UBZ-301 (10-100A) unit manufactured by it within 36 months from the date of sale, provided:•the proper installation;•the safety of the inspection quality control department seal;•the integrity of the case, no traces of an opening, cracks, spalls etc.。
电子负载IT8811-艾德克斯
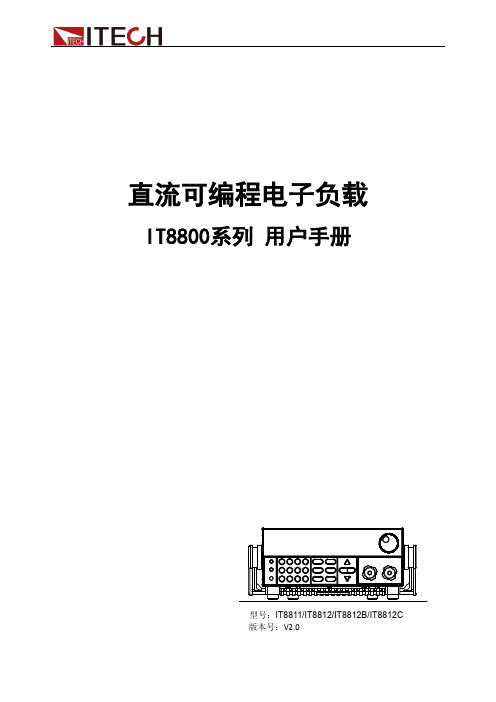
252.227-7015(技术数据-商业制品)
和 DFARS 227.7202-3(商业计算机软件 或计算机软件文档中的权限)。
IT8800 用户手册
安全声明
小心标志表示有危险。它要求在 执行操作步骤时必须加以注意, 如果不正确地执行或不遵守操作 步骤,则可能导致产品损坏或重 要数据丢失。在没有完全理解指 定的条件且不满足这些条件的情 况下,请勿继续执行小心标志所 指示的任何不当操作。
安全标志
直流电 交流电 既有直流也有交流电 保护性接地端子
ON(电源合) OFF(电源断) 电源合闸状态 电源断开状态
接地端子
参考端子
危险标志
正接线柱
警告标志(请参阅本手册了解 具体的“警告”或“小心”信 息)
负接电子有限公司
i
IT8800 用户手册
安全注意事项
IT8800 用户手册
认证与质量保证
IT8800 系列电子负载完全达到手册中所标称的各项技术指标。
保固服务
ITECH 公司对本产品的材料及制造,自出货日期起提供一年的质量保固服务(保固服 务除以下保固限制内容)。 本产品若需保固服务或修理,请将产品送回 ITECH 公司指定的维修单位。
若需要送回 ITECH 公司作保固服务的产品,顾客须预付寄送到 ITECH 维修部的 单程运费,ITECH 公司将负责支付回程运费。
版权所有 © 艾德克斯电子有限公司
iii
IT8800 用户手册
1 本产品仅在非居民区内使用,在居民区内使用可能造成电磁干扰。 2 当该设备与测试对象连接时,可能产生超过此标准要求的辐射级别。 3 为确保符合上面列出的 EMC 标准,应使用高质量的屏蔽接口电缆。 4 在 IEC 61000-4-3 测试条件下,可包括峰-峰值不超过 4 格的光迹噪声(Trace bloom)。 5 在 IEC 61000-4-6 测试条件下,可包括峰-峰值不超过 1 格的光迹噪声(Trace bloom)。 6 性能标准 C 应用于 70%/25 周期电压跌落以及 0%/250 周期电压中断测试水平(IEC 61000-4-11)。
HIOKI儀器產品選購指南说明书

Ⴍ 高速20通道/變壓器L/C/Z/DCR/圈數/短路/平衡掃描測試功能 高速80通道/變壓器L/C/Z/DCR/圈數/短路/平衡掃描測試功能
20通道/變壓器L/C/Z/DCR/圈數/短路/平衡掃描測試功能 3250加LCR錶分析功能 3252 1MHz版
3302加通訊參數測量功能
ٜࠠݴᛌཥݴ๕ / ༊ӻ୕፯ᒅܸی
Ꮠ͜Ⴍ LCD Inverter變壓器(陶瓷電容、線材、PCB)
耐久性測試/耐壓測試/崩潰電壓測試 外部電極螢光燈管(EEFL),背光耐久性/燈管電流測試 交換式電源供應器(SMPS)主變壓器與主動式功率因素修正器
(Active PFC) Choke耐久性測試與電氣特性分析 醫療設備高頻漏電流安規檢驗
ࠫϣ 12-34 12-34 12-34 12-34 12-35 12-35
0.1mΩ ~ 100MΩ 0.1mΩ ~ 100MΩ 0.1mΩ ~ 100MΩ 0.01mΩ ~ 100MΩ 0.01mΩ ~ 100MΩ
3252
20Hz~200kHz
0.1mΩ ~ 100MΩ
3302
20Hz~1MHz
0.1mΩ ~ 100MΩ
Ⴍ 電容量高速檢測 全數位分類,比較器功能,可選無10kHz版 全數位分類,比較器功能
提供高頻高壓交流與直流電源供應的功能,供平面螢光燈(FFL) 與表面傳導電子發射顯示器(SED)裝置分析使用
直流/直流轉換器SMD Power Choke溫昇測試 (直流重疊電流與交流漣波電壓)與電氣特性分析
緩衝電容壽命測試 高壓電容壽命測試 LCD Inverter變壓器(陶瓷電容、線材、PCB)生產線耐壓測試 醫療設備高頻漏電流安規檢驗 車用驅動馬達生產線電暈(Corona)放電檢驗 被動元件(換流器變壓器、陶瓷電容、高壓線材、PCB等) 高頻高壓壽命測試
电子元器件az764fh-1ae-6d中文资料_数据手册_IC数据表
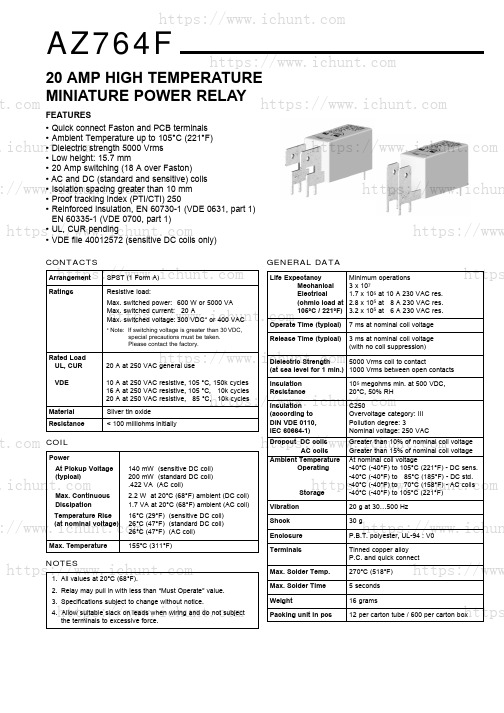
GENERAL DATALife ExpectancyMinimum operations Mechanical 3 x 107Electrical1.7 x 105at 10 A 230 VAC res.(ohmic load at2.8 x 105at 8 A 230 VAC res.105°C / 221°F)3.2 x 105at 6 A 230 VAC res.Operate Time (typical)7 ms at nominal coil voltage Release Time (typical)3 ms at nominal coil voltage (with no coil suppression)Dielectric Strength 5000 Vrms coil to contact(at sea level for 1 min.)1000 Vrms between open contactsInsulation105megohms min. at 500 VDC,Resistance 20°C, 50% RHInsulation C250(according to Overvoltage category: III DIN VDE 0110, Pollution degree: 3IEC 60664-1)Nominal voltage: 250 VACDropout DC coilsGreater than 10% of nominal coil voltage AC coilsGreater than 15% of nominal coil voltage Ambient TemperatureAt nominal coil voltageOperating-40°C (-40°F) to 105°C (221°F) - DC sens.-40°C (-40°F) to 85°C (185°F) - DC std.-40°C (-40°F) to 70°C (158°F) - AC coils Storage-40°C (-40°F) to 105°C (221°F)Vibration 20 g at 30…500 Hz Shock 30 gEnclosure P.B.T. polyester, UL-94 : V0TerminalsTinned copper alloy P.C. and quick connect Max. Solder Temp.270°C (518°F)Max. Solder Time 5 seconds Weight16 gramsPacking unit in pcs12 per carton tube / 600 per carton box20 AMP HIGH TEMPERATURE MINIATURE POWER RELAYFEATURES •Quick connect Faston and PCB terminals •Ambient Temperature up to 105°C (221°F)•Dielectric strength 5000 Vrms •Low height: 15.7 mm•20 Amp switching (18 A over Faston)•AC and DC (standard and sensitive) coils •Isolation spacing greater than 10 mm •Proof tracking index (PTI/CTI) 250•Reinforced insulation, EN 60730-1 (VDE 0631, part 1)EN 60335-1 (VDE 0700, part 1)•UL, CUR pending•VDE file 40012572 (sensitive DC coils only)CONTACTSArrangement SPST (1 Form A)RatingsResistive load:Max. switched power:600 W or 5000 VA Max. switched current:20 AMax. switched voltage:300 VDC* or 400 VAC* Note: If switching voltage is greater than 30VDC,special precautions must be taken.Please contact the factory.Rated Load UL, CUR 20 A at 250 VAC general useVDE10 A at 250 VAC resistive, 105 °C, 150k cycles 16 A at 250 VAC resistive, 105 °C, 10k cycles 20 A at 250 VAC resistive, 85 °C, 10k cycles Material Silver tin oxide Resistance< 100 milliohms initiallyCOILPowerAt Pickup Voltage 140 mW (sensitive DC coil)(typical)200 mW (standard DC coil).422 VA (AC coil)Max. Continuous 2.2 W at 20°C (68°F) ambient (DC coil)Dissipation1.7 VA at 20°C (68°F) ambient (AC coil)Temperature Rise 16°C (29°F) (sensitive DC coil)(at nominal voltage)26°C (47°F) (standard DC coil)26°C (47°F) (AC coil)Max. Temperature155°C (311°F)NOTES1.All values at 20°C (68°F).2.Relay may pull in with less than “Must Operate” value.3.Specifications subject to change without notice.4. Allow suitable slack on leads when wiring and do not subject the terminals to excessive force.https://https://https://https://httpshttps://https://https://wwwhttps:// :// https://www.ichunhttps://www.ichun://https://https://wwwhttps://https://httpshttps://* Substitue “FV” for “FH” for vertical quick connect terminals.COIL SPECIFICATIONS - AC COILORDER NUMBER*Nominal CoilMust OperateMax. ContinuousNominal CurrentCoil Resistance VACVACVACmA ± 10%Ohm ± 10%129.018.063.0100AZ764FH–1AE–12A 2418.036.031.3400AZ764FH–1AE–24A 11586.3172.5 6.59,600AZ764FH–1AE–115A 230172.5345.03.338,500AZ764FH–1AE–230A 240180.0360.03.142,500AZ764FH–1AE–240ARELAY ORDERING DATACOIL SPECIFICATIONS - DC COILORDER NUMBER*Nominal CoilMust OperateMax. ContinuousCoil Resistance VDCVDCVDCOhm ±10%5 3.512.760 AZ764FH–1AE–5D6 4.215.390AZ764FH–1AE–6D9 6.322.9200AZ764FH–1AE–9D128.430.6360 AZ764FH–1AE–12D1812.645.9710AZ764FH–1AE–18D 2416.861.21,440 AZ764FH–1AE–24D4833.6122.05,700AZ764FH–1AE–48D 6042.0153.07,500AZ764FH–1AE–60D11077.0280.025,200AZ764FH–1AE–110DCOIL SPECIFICATIONS - DC COIL SENSITIVE VERSIONORDER NUMBER*Nominal CoilMust OperateMax. ContinuousCoil Resistance VDCVDCVDCOhm ±10%5 3.7515.0102 AZ764FH–1AE–5DS6 4.518.0144AZ764FH–1AE–6DS 9 6.7527.0330 AZ764FH–1AE–9DS 107.530.0400AZ764FH–1AE–10DS129.036.0580 AZ764FH–1AE–12DS 2418.072.02,300 AZ764FH–1AE–24DShttps://https://https://https://httpshttps://https://www://https://www.ichunhttps:// https://httpshttpshttps://https://https://www.ichunhttps://wwwhttps。
RM1A, RM1B AC固态继电器 产品说明书

RM1A, RM1B• Zero switching (RM1A) or instant-on switching (RM1B) AC Solid State Relay • Direct copper bonding (DCB) technology • LED indication • Built-in varistor• Clip-on IP 20 protection cover • Self-lifting terminals• Housing free of moulding mass• 2 input ranges: 3-32* VDC and 20-280VAC/22-48VDC • Operational ratings: Up to 100AACrms and 600VACrms • Blocking voltage: Up to 1400V p • Opto-isolation: > 4000VACrmsProduct De s cript ion The industrial, 1-phase relay with antiparallel thyristor output is the most widely used indus t rial SSR due to its multiple application possibilities. The relay can be used for resis t ive, inductive and capacitive loads. The zero switching relay switches ON when the sinusoidal curve crosses zero and switches OF F when the current crosses zero. The instant-on relay with DC control input can be used for phase control. The built-in varistor secures transient protection for the heavy industrial applications, and the LED indicates the status of the control input. The clip-on cover is securing touch protection to IP 20. Protected output terminals can handle cables up to 16mm 2.Type SelectionS witching mode Rated operational Control voltage Rated operational voltage currentA: Zero Switching (ZC)23: 230VACrms A: 20-280VAC / 22-48VDC 25: 25AACrms B: Instant-on switching (IO) 40: 400VACrms D: 3-32VDC*50: 50AACrms 48: 480VACrms *4 to 32VDC for 400, 480 and 600VAC types 75: 75AACrms60: 600VACrms*4 to 32VDC for RM1B types100: 100AACrmsSolid State RelaysIndustrial, 1-Phase ZS (IO) w. LED and Built-in Varistor Types RM 23, RM 40, RM 48, RM 60Rated opera- Blocking ControlRated op e r a t ion a l current with suitable heatsink tional voltage, voltage voltage 25A 50A 75A 100A Switching mode230VACrms, 650V p 3 - 32VDCRM1A23D25 RM1A23D50 RM1A23D75 RM1A23D100ZC 20 to 280VAC RM1A23A25 RM1A23A50 RM1A23A75 RM1A23A100 22 to 48VDC 400VACrms, 800V p 4 - 32VDC RM1A40D25 RM1A40D50 RM1A40D75 RM1A40D100ZC 20 to 280VAC RM1A40A25 RM1A40A50 RM1A40A75 RM1A40A10022 to 48VDC 480VACrms, 1200V p 4 - 32VDC RM1A48D25 RM1A48D50 RM1A48D75 RM1A48D100ZC 20 to 280 VAC RM1A48A25 RM1A48A50 RM1A48A75 RM1A48A10022 to 48VDC 600VACrms, 1400V p 4 - 32VDC RM1A60D25 RM1A60D50 RM1A60D75 RM1A60D100ZC 20 to 280VAC RM1A60A25 RM1A60A50 RM1A60A75 RM1A60A10022 to 48VDCSelection GuidesInput SpecificationsGeneral Spec i f i c a t ions* Heatsink must be connected to groundRated opera- Blocking Control Rated op e r a t ion a l current with suitable heatsink tional voltage, voltage voltage 25A 50A 75A 100A Switching mode230VACrms, IO 650V p 4 - 32VDC RM1B23D25 RM1B23D50 RM1B23D75 RM1B23D10020 - 280VAC/ RM1B23A25 RM1B23A50 RM1B23A75 RM1B23A100 22 - 48VDC 400VACrms, IO 800V p 4 - 32VDC RM1B40D25 RM1B40D50 RM1B40D75 RM1B40D100480VACrms, IO 1200V p 4 - 32VDC RM1B48D25 RM1B48D50 RM1B48D75 RM1B48D100600VACrms, IO 1400V p 4 - 32VDC RM1B60D25 RM1B60D50 RM1B60D75 RM1B60D100 20 - 280VAC/ RM1B60A25 RM1B60A50 RM1B60A75 RM1B60A10022 - 48VDCSelection GuideNote: For AC control, IO switching part numbers will be created on requestOutput SpecificationsNote: UL requirement for General Use Endurance testing is 6,000 cyclesElectromagnetic CompatibilityHousing SpecificationsRelayMounting screws M5Mounting torque1.5-2.0NmConnection SpecificationsStripping length (X) 12 mm 8 mmConnection Type M5 screw with captivated washerM3 screw with captivated washer1x 2.5 - 6.0 mm²1x 1.0 - 4.0 mm² X Connection terminalsL1, T1A1, A2Notes:- Use of AC solid state relays may, according to the application and the load current, cause conducted radio interferences. Use of mains filters may be neces-sary for cases where the user must meet E.M.C requirements. The capacitor values given inside the filtering specification tables should be taken only as indi-cations, the filter attenuation will depend on the final application.- The control terminals A1, A2 (RM1..A) shall be supplied by a secondary circuit where power is limited by a transformer, rectifier, voltage divider, or similar device that derives power from a primary circuit, and where the short-circuit limit between conductors of the secondary circuit or between conductors and ground is 1500 VA or less. The short-circuit volt ampere limit is the product of the open circuit voltage and the short circuit ampere.- Control input lines must be installed together to maintain products’ susceptibility to Radio Frequency interference.- Performance Criteria 1: No degradation of performance or loss of function is allowed when the product is operated as intended.- Performance Criteria 2: During the test, degradation of performance or partial loss of function is allowed. However, when the test is complete the productshould return operating as intended by itself.- Performance Criteria 3: Temporary loss of function is allowed, provided the function can be restored by manual operation of the controls.Connection DiagramDimensionsFunctional Diagram * Varistor across input applies to AC control versions only.Heatsink Dimensions (load current versus ambient temperature)RM..25Junction to ambient thermal resistance, R th j-a < 20.0 °C/W Junction to case thermal resistance, R th j-c < 0.80 °C/W Case to heatsink thermal resistance, R th c-s 2 < 0.20 °C/W Maximum allowable case temperature 100 °C Maximum allowable junction temperature 125 °C T AAmbient temp. [°C]Thermal resistance [°C/W]Loadcurrent [A]25.0 2.70 2.34 1.98 1.61 1.250.8922.5 3.10 2.69 2.28 1.86 1.45 1.0420.0 3.61 3.13 2.65 2.18 1.70 1.2317.5 4.26 3.70 3.14 2.59 2.03 1.4715.0 5.14 4.47 3.80 3.14 2.47 1.8012.5 6.38 5.56 4.73 3.91 3.09 2.2710.08.257.19 6.14 5.08 4.02 2.977.511.49.948.497.04 5.59 4.145.017.715.413.211.08.74 6.512.5----18.213.6203040506070RM..50Junction to ambient thermal resistance, R th j-a < 20.0 °C/W Junction to case thermal resistance, R th j-c < 0.50 °C/W Case to heatsink thermal resistance, R th c-s 2 < 0.20 °C/W Maximum allowable case temperature 100 °C Maximum allowable junction temperature 125°CJunction to ambient thermal resistance, R th j-a < 20.0 °C/WJunction to case thermal resistance, R th j-c < 0.72 °C/W Case to heatsink thermal resistance, R th c-s 2 < 0.10 °C/W Maximum allowable heatsink temperature 100 °C Maximum allowable junction temperature 125 °C Junction to ambient thermal resistance, R th j-a < 20.0 °C/WJunction to case thermal resistance, R th j-c < 0.35 °C/W Case to heatsink thermal resistance, R th c-s 2 < 0.10 °C/W Maximum allowable heatsink temperature 100 °C Maximum allowable junction temperature 125 °CRM1.60..50T AAmbient temp. [°C]Thermal resistance [°C/W]Loadcurrent [A]50.00.990.810.630.440.260.0845.0 1.28 1.070.860.650.440.2340.0 1.64 1.40 1.150.910.670.4235.0 2.11 1.82 1.54 1.250.960.6730.0 2.60 2.25 1.90 1.55 1.200.8525.0 3.30 2.86 2.43 1.99 1.55 1.1120.0 4.36 3.79 3.22 2.65 2.08 1.5115.0 6.1 5.4 4.6 3.77 2.97 2.1810.09.768.527.3 6.0 4.8 3.545.0----15.4712.8510.247.6203040506070RM..75T AAmbient temp. [°C]Thermal resistance [°C/W]Loadcurrent [A]75.00.910.780.650.520.390.2667.5 1.100.960.810.660.510.3660.0 1.34 1.17 1.000.830.660.4952.5 1.60 1.40 1.20 1.000.800.6045.0 1.93 1.68 1.44 1.200.960.7237.5 2.38 2.08 1.78 1.49 1.190.8930.0 3.06 2.68 2.30 1.91 1.53 1.1522.5 4.21 3.68 3.16 2.63 2.10 1.5815.0 6.51 5.70 4.88 4.07 3.26 2.447.513.511.7710.098.41 6.73 5.04203040506070T AAmbient temp. [°C]Thermal resistance [°C/W]Loadcurrent [A]50.0 1.030.860.700.530.370.2045.0 1.27 1.320.900.710.520.3340.0 1.54 1.59 1.100.890.670.4535.0 1.85 1.95 1.34 1.080.820.5730.0 2.26 2.47 1.65 1.34 1.030.7225.0 2.85 3.24 2.08 1.70 1.320.9420.0 3.73 3.24 2.75 2.26 1.77 1.2715.0 5.22 4.54 3.86 3.19 2.51 1.8310.08.217.16 6.11 5.05 4.00 2.955.017.215.012.910.78.51 6.33203040506070Heatsink Dimensions (load current versus ambient temperature) (cont.)• Heatsinks and fans• 5.40o C/W to 0.12o C/W thermal resistance • DIN, panel or thru wall mounting • Single or multiple SSR mountingHeatsink SelectionHeatsink Range Overview:https:///images/PIM/DATASHEET/ENG/SSR_Accessories.pdf Heatsink Selector Tool:https:///nsc/hq/en/solid_state_relaysOrdering KeyRHS..2. Thermal resistance case to heatsink valves are applicable upon application of a fine layer of silicon based thermal paste HTS02S from Electrolube between SSR and heatsink.Junction to ambient thermal resistance, R th j-a < 20.0 °C/WJunction to case thermal resistance, R th j-c < 0.30 °C/W Case to heatsink thermal resistance, R th c-s 2 < 0.10 °C/W Maximum allowable heatsink temperature 100 °C Maximum allowable junction temperature 125 °CRM..100T AAmbient temp. [°C]Thermal resistance [°C/W]Loadcurrent [A]100.00.540.450.360.270.180.0990.00.680.580.470.370.270.1780.00.860.740.620.500.380.2670.0 1.080.940.800.660.520.3860.0 1.37 1.20 1.030.850.680.5150.0 1.70 1.49 1.28 1.060.850.6440.0 2.21 1.93 1.66 1.38 1.100.8330.0 3.06 2.68 2.30 1.91 1.53 1.1520.0 4.78 4.18 3.59 2.99 2.39 1.7910.09.988.737.49 6.24 4.99 3.74203040506070Thermal SpecificationsShort Circuit ProtectionProtection Co-ordination, Type 1 vs. Type 2:Type 1 protection implies that after a short circuit, the device under test will no longer be in a functioning state. In type 2 co-ordination the device under test will still be functional after the short circuit. In both cases, however, the short circuit has to be interrupted. The fuse between enclosure and supply shall not open. The door or cover of the enclosure shall not be blown open. There shall be no damage to conductors of terminals and the conductors shall not separate from terminals. Therese shall be no breakage or cracking of insulating bases to the extent that the integrity of the mounting of live parts is impaired. Discharge of parts or any risk of fire shall not occur.The product variants listed in the table hereunder are suitable for use on a circuit capable of delivering not more than 65,000A rms Symmetrical Amperes, 600Volts maximum when protected by fuses. Tests at 65,000A were performed with Class J, fast acting: please refer to the table below for maximum allowed ampere rating of the fuse. Use fuses only.Co-ordination type 1 (UL508)Part No. Prospective short Max. fuse size [A] Class/ Model Voltage [VAC]circuit current [kArms]RM1..25.. 65 30 J or CC 600RM1..50.. 65 30 J 60020 HSJ20 (Mersen*) 600RM1..75.. 65 80 J 60060 HSJ60 (Mersen*) 600RM1..100.. 65 80 J 60060 HSJ60 (Mersen*) 600Co-ordination type 2 (IEC/EN60947-4-3)Part No. Prospective short Max. fuse Brand Model Sizecircuit current [kArms] size [A]RM1.xx.25.. (xx = 23, 40 or 48) 10 25 Mersen* 6.9 gRB 10-25 10.3 x 38 RM1.60.25.. 10 20 Mersen* 6.9 gRB 10-20 10.3 x 38 RM1.xx.50.. (xx = 23 or 40) 10 50 Mersen* 6.9zz CP gRC 14x51/50 14 x 51 RM1.xx.50.. (xx = 48 or 60) 10 50 Mersen* 6.9zz CP gRC 22x58/50 22 x 58 RM1.xx.75.. (xx = 23, 40, 48 or 60) 10 63 Mersen* 6.9zz CP gRC 22x58/63 22 x 58 RM1.xx.100.. (xx = 23, 40, 48 or 60) 10 100 Mersen* 6.9zz CP gRC 22x58/100 22 x 58zz = 00, without fuse trip indicationzz = 21, with fuse trip indication* Formerly Ferraz ShawmutType 2 Protection with Miniature Circuit Breakers (M.C.B.s)Solid State Relay ABB Model no. for ABB Model no. for Wire cross Minimum length oftype Z - type M. C. B. B - type M. C. B. sectional area [mm2] Cu wire conductor [m]* (rated current) (rated current)RM1..25.. 1-poleS201-Z4 (4A) S201-B2 (2A) 1.0 21.0S201-Z6 UC (6A) S201-B2 (2A) 1.0 21.01.5 31.5RM1..50.. 1-poleS201-Z10 (10A) S201-B4 (4A) 1.0 7.61.5 11.42.5 19.0S201-Z16 (16A) S201-B6 (6A) 1.0 5.21.5 7.82.5 13.04.0 20.8S201-Z20 (20A) S201-B10 (10A) 1.5 12.62.5 21.0S201-Z25 (25A) S201-B13 (13A) 2.5 25.04.0 40.02-poleS202-Z25 (25A) S202-B13 (13A) 2.5 19.04.0 30.4 RM1..75.. 1-poleS201-Z20 (20A) S201-B10 (10A) 1.5 4.22.5 7.04.0 11.2S201-Z32 (32A) S201-B16 (16A) 2.5 13.04.0 20.86.0 31.22-poleS202-Z20 (20A) S202-B10 (10A) 1.5 1.82.53.04.0 4.8S202-Z32 (32A) S202-B16 (16A) 2.5 5.04.0 8.06.0 12.010.0 20.0S202-Z50 (50A) S202-B25 (25A) 4.0 14.86.0 22.210.0 37.0 RM1..100.. 1-poleS201-Z50 (50A) S201-B25 (25A) 4.0 4.86.07.210.0 12.016.0 19.2S201-Z63 (63A) S201-B32 (32A) 6.0 7.210.0 12.016.0 19.2* Between MCB and Load (including return path which goes back to the mains).Note: A prospective current of 6kA and a 230/400V power supply system is assumed for the above suggested specifications. For cables with different cross section than those mentioned above please consult Carlo Gavazzi’s Technical Support Group.25The declaration in this section is prepared in compliance with People’s Republic of China Electronic Industry Standard SJ/T11364-2014: Marking for the Restricted Use of Hazardous Substances in Electronic and Electrical Products.Part NameToxic or Harardous Substances and Elements Lead (Pb)Mercury (Hg)Cadmium (Cd)Hexavalent Chromium (Cr(Vl))Polybrominated biphenyls (PBB)Polybrominated diphenyl ethers(PBDE)Power Unit AssemblyxOOOOOO: Indicates that said hazardous substance contained in homogeneous materials fot this part are below the limit require-ment of GB/T 26572.X: Indicates that said hazardous substance contained in one of the homogeneous materials used for this part is above the limit requirement of GB/T 26572.Environmental Information环境特性这份申明根据中华人民共和国电子工业标准SJ/T11364-2014:标注在电子电气产品中限定使用的有害物质零件名称有毒或有害物质与元素铅(Pb)汞(Hg)镉(Cd)六价铬(Cr(Vl))多溴化联苯(PBB)多溴联苯醚(PBDE)功率单元xOOOOOO:此零件所有材料中含有的该有害物低于GB/T 26572的限定。
SAQ8818 中文资料
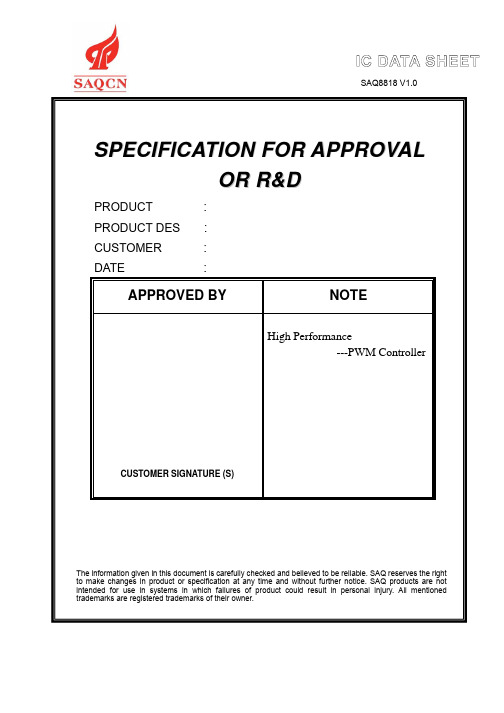
5 SLECT
管脚定义:
16
SAQ8818 V1.0
9
SAQ8818
1
8
分类信息:
产品型号 SAQ8818 SAQ8818
封装 16-DIP 16-SOP
工作温度
0~+700C
管脚描述:
PIN.NO Symbol
1
P OUT1
2
P OUT2
3
N OUT2
4
VCC
5
SLECT
6
VREF
7
PR SLECT
SAQ8818 V1.0
Copyright © 2006 by SHENZHEN SAQCN INOVATION TECHNOLOGIES CO., LTD. The information appearing in this Data Sheet is believed to be accurate at the time of
SAQ8818 V1.0
产品概述:
z SAQ8818 及其运用是一个功能强大的开关电源方案,采用独到的技术,根据不同 的设计适合液晶产品用 CCFL 背光、EEFL 背光、LED 背光的管理,以及电脑 电源、家电、通信产品等开关电源的 DC-DC 转换控制,产品功能全,兼容性 高。
z 该产品包含单端 PWM、双端 PWM、推挽、半桥、全桥电路,效率高达 90% 以上。
EA 阈值电压 内部下拉电阻
VDD=12V,Ta=25℃
输出特性
输出阻抗
上升时间
VDD=5V,1000pF
下降时间
SAQ8818 V1.0 最小值 典型值 最大值 单位
2.0
V
20
1955581资料

Extract from the onlinecatalogCCV 2,5/ 8-G-5,08 P26THRR56Order No.: 1955581http://eshop.phoenixcontact.de/phoenix/treeViewClick.do?UID=1955581Taped headers, pin length: 2.6 mm, tape width: 56 mm, 5.08 mm pitch, 8-pos.http://Please note that the data givenhere has been taken from theonline catalog. For comprehensiveinformation and data, please referto the user documentation. TheGeneral Terms and Conditions ofUse apply to Internet downloads. Technical dataDimensions / positionsPitch 5.08 mmDimension a35.56 mmNumber of positions8Pin dimensions 1 x 1 mmPin spacing 5.08 mmHole diameter 1.6 mmTechnical dataInsulating material group IIIaRated surge voltage (III/3) 4 kVRated surge voltage (III/2) 4 kVRated surge voltage (II/2) 4 kVRated voltage (III/2)320 VRated voltage (II/2)400 VConnection in acc. with standard EN-VDENominal current I N12 ANominal voltage U N250 VMaximum load current12 A (per position)Insulating material LCPInflammability class acc. to UL 94V0Certificates / ApprovalsApproval logoCULNominal voltage U N300 VNominal current I N10 AULNominal voltage U N300 VNominal current I N10 ACertification CUL, ULAccessoriesItem Designation DescriptionGeneral1954362CR-MSTB NAT HT HT coding section, is pushed into the recess on the header beforethe reflow process, made of highly temperature-resistant, beigeinsulating materialMarking1051993B-STIFT Marker pen, for manual labeling of unprinted Zack strips, smear-proof and waterproof, line thickness 0.5 mm0804303SK 5,08/3,8: 0-9Marker card, printed horizontally, self-adhesive, 10-section markerstrip, 12 identical decades marked 0-9, sufficient for 120 terminalblocks0804293SK 5,08/3,8:FORTL.ZAHLEN Marker card, printed horizontally, self-adhesive, 12 identicaldecades marked 1-10, 11-20 etc. up to 91-(99)100, sufficient for120 terminal blocks0805085SK 5,08/3,8:SO Marker card, special printing, self-adhesive, labeled acc. tocustomer requirements, 12 identical marker strips per card, max.25-position labeling per strip, color: white0805412SK 5,08/3,8:UNBEDRUCKT Marker cards, unprinted, with pitch divisions, self-adhesive, 10-section marker strips, 12 strips per card, can be labeled with theM-PENPlug/Adapter1734401CR-MSTB Coding section, inserted into the recess in the header or theinverted plug, red insulating materialDrawingsApplication drawingDrilling diagramDimensioned drawingBottom view, free space for solder paste, 0.55mm deepDirection of the arrow = feeding directionAddressPHOENIX CONTACT GmbH & Co. KGFlachsmarktstr. 832825 Blomberg,GermanyPhone +49 5235 3 00Fax +49 5235 3 41200http://www.phoenixcontact.de© 2008 Phoenix ContactTechnical modifications reserved;。
ADI电路笔记 CN-0359说明书

电路笔记CN-0359Circuits from the Lab® reference designs are engineered and tested for quick and easy system integration to help solve today’s analog, mixed-signal, and RF design challenges. For more information and/or support, visit /CN0359.连接/参考器件AD825310 MHz、20 V/μs、G = 1、10、100、1000、i CMOS可编程增益仪表放大器ADuCM360集成双通道Σ-Δ型ADC和ARM Cortex-M3的低功耗精密模拟微控制器ADA4627-1 30 V、高速、低噪声、低偏置电流JFET运算放大器AD8542CMOS轨到轨通用放大器ADA4000-1 低成本、精密JFET输入运算放大器ADP2300 1.2 A、20 V、700 kHz/1.4 MHz异步降压型稳压器ADA4638-1 30 V、零漂移、轨到轨输出精密放大器ADP1613 650 kHz/1.3 MHz升压PWM DC-DC开关转换器ADA4528-2 精密、超低噪声、RRIO、双通道、零漂移运算放大器ADG1211低电容、低电荷注入、±15 V/+12 V iCMOS四通道单刀单掷开关ADA4077-2 4 MHz、7 nV/√Hz、低失调和漂移、高精度放大器ADG1419 2.1 Ω导通电阻、±15 V/+12 V/±5 V、iCMOS单刀双掷开关AD8592 CMOS、单电源、轨到轨输入/输出运算放大器,具有关断功能ADM3483 3.3 V限摆率、半双工、RS-485/RS-422收发器全自动高性能电导率测量系统Rev. 0Circuits from the Lab® reference designs from Analog Devices have been designed and built by AnalogDevices engineers. Standard engineering practices have been employed in the design andconstruction of each circuit, and their function and performance have been tested and veri ed in a labenvironment at room temperature. However, you are solely responsible for testing the circuit and determining its suitability and applicability for your use and application. Accordingly, in no event shall Analog Devices be liable for direct, indirect, special, incidental, consequential or punitive damages due to any cause whatsoever connected to the use of any Circuits from the Lab circuits. (Continued on last page)One Technology Way, P.O. Box 9106, Norwood, MA 02062-9106, U.S.A. Tel: 781.329.4700 Fax: 781.461.3113 ©2015 Analog Devices, Inc. All rights reserved.评估和设计支持电路评估板CN-0359电路评估板(EVAL-CN0359-EB1Z)设计和集成文件原理图、源代码、布局文件、物料清单电路功能与优势图1中的电路是一个完全独立自足、微处理器控制的高精度电导率测量系统,适用于测量液体的离子含量、水质分析、工业质量控制以及化学分析。
IDEC ARN系列单杠开关产品介绍说明书

k No. of Contact Blocks —
l Lever Action m Contact Arrangement
Blocked Maintained Spring Return No contacts 1 NO contact 1 NC contact 1 NO and 1 NC contact 2 NO contacts 2 NC contacts
UL Listed File No. E68961
CSA Certified File No. LR48366
Specifications
Operating Temperature Insulation Resistance
Rated Voltage: Current Contact Rating
Insulation Voltage Rated Thermal Current Electrical Life
ARNO
M3.5 Terminal Screw
Panel Thickness 0.8 to 6
Dimensions — ARN Series
ARNSO
M3.5 Terminal Screw
Panel Thickness 0.8 to 6
30
ø42
51
ø22
30
6 23
83
51
1 block: 47, 2 blocks: 70 3 blocks: 93, 4 blocks: 116
ARNB-B
1705151134
800-262-IDEC (4332) • USA & Canada
781
Terminal Blocks
Circuit Breakers
AO8814;中文规格书,Datasheet资料
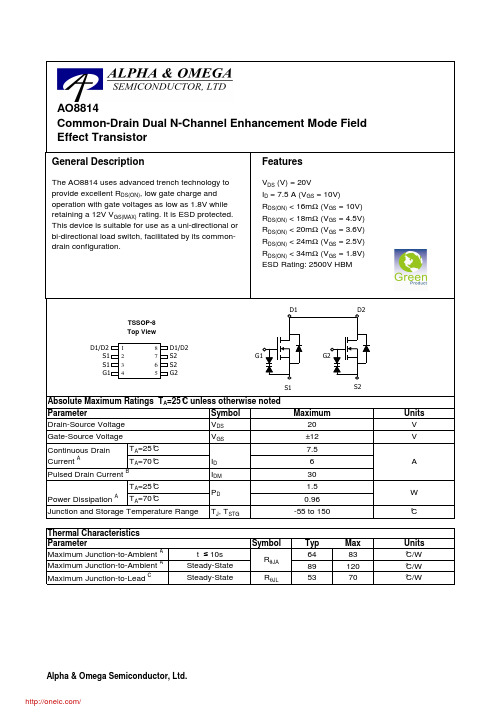
Symbol V DS V GSI DM T J , T STG SymbolTyp Max 648389120R θJL5370Junction and Storage Temperature Range AP D °CT A =70°CI D Pulsed Drain Current BPower Dissipation AT A =25°CContinuous Drain Current AUnits Parameter T A =25°C T A =70°CAbsolute Maximum Ratings T A =25°C unless otherwise noted V V Gate-Source Voltage Drain-Source Voltage °C/W Maximum Junction-to-Ambient A Steady-State °C/W W Maximum Junction-to-Lead CSteady-State°C/WThermal CharacteristicsParameterUnits Maximum Junction-to-Ambient A t ≤ 10sR θJA AO8814Common-Drain Dual N-Channel Enhancement Mode Field Effect TransistorG1S1S1D1/D2G2S2S2D1/D212348765TSSOP-8Top ViewGeneral DescriptionThe AO8814 uses advanced trench technology to provide excellent R DS(ON), low gate charge and operation with gate voltages as low as 1.8V while retaining a 12V V GS(MAX) rating. It is ESD protected.This device is suitable for use as a uni-directional or bi-directional load switch, facilitated by its common-drain configuration.SymbolMin TypMaxUnits BV DSS 20V 1T J =55°C 5I GSS 10µA BV GSO ±12V V GS(th)0.50.711V I D(ON)30A 101316T J =125°C14182211.51518m Ω1316.820m Ω151924m Ω202634m Ωg FS 30S V SD 0.741V I S2.5A C iss 1390pF C oss 190pF C rss 150pF R g1.5ΩQ g 15.4nC Q gs 1.4nC Q gd 4nC t D(on) 6.2ns t r 11ns t D(off)40.5ns t f 10ns t rr 15ns Q rr5.1nCTHIS PRODUCT HAS BEEN DESIGNED AND QUALIFIED FOR THE CONSUMER MARKET. APPLICATIONS OR USES AS CRITICAL COMPONENTS IN LIFE SUPPORT DEVICES OR SYSTEMS ARE NOT AUTHORIZED. AOS DOES NOT ASSUME ANY LIABILITY ARISING OUT OF SUCH APPLICATIONS OR USES OF ITS PRODUCTS. AOS RESERVES THE RIGHT TO IMPROVE PRODUCT DESIGN,FUNCTIONS AND RELIABILITY WITHOUT NOTICE.Maximum Body-Diode Continuous CurrentInput Capacitance Output CapacitanceGate-Source Breakdown Voltage V DS =0V, I G =±250uA V GS =3.6V, I D =6A Turn-On DelayTime DYNAMIC PARAMETERSV GS =0V, V DS =10V, f=1MHz Gate Drain Charge Turn-On Rise Time Turn-Off DelayTime V GS =5V, V DS =10V, R L =1.3Ω,R GEN =3ΩGate resistanceV GS =0V, V DS =0V, f=1MHzTurn-Off Fall TimeSWITCHING PARAMETERS Total Gate Charge V GS =4.5V, V DS =10V, I D =7.5AGate Source Charge m ΩV GS =2.5V, I D =6A I S =1A,V GS =0VV DS =5V, I D =7.5A V GS =1.8V, I D =5AV GS =4.5V, I D =7A R DS(ON)Static Drain-Source On-ResistanceForward Transconductance Diode Forward VoltageI DSS µA Gate Threshold Voltage V DS =V GS I D =250µA V DS =16V, V GS =0VZero Gate Voltage Drain Current V DS =0V, V GS =±10V Gate-Body leakage current Electrical Characteristics (T J =25°C unless otherwise noted)STATIC PARAMETERSParameterConditions Body Diode Reverse Recovery TimeBody Diode Reverse Recovery Charge I F =7.5A, dI/dt=100A/µsDrain-Source Breakdown Voltage On state drain currentI D =250µA, V GS =0V V GS =4.5V, V DS =5V V GS =10V, I D =7.5AReverse Transfer Capacitance I F =7.5A, dI/dt=100A/µsA: The value of R θJA is measured with the device mounted on 1in 2 FR-4 board with 2oz. Copper, in a still air environment with T A =25°C.The value in any given application depends on the user's specific board design. The current rating is based on the t ≤ 10s thermal resistance rating.B: Repetitive rating, pulse width limited by junction temperature.C. The R θJA is the sum of the thermal impedence from junction to lead R θJL and lead to ambient.D. The static characteristics in Figures 1 to 6,12,14 are obtained using <300 µs pulses, duty cycle 0.5% max.E. These tests are performed with the device mounted on 1 in 2 FR-4 board with 2oz. Copper, in a still air environment with T A =25°C. The SOA curve provides a single pulse rating.Rev 5: Feb 2010分销商库存信息: AOSAO8814。
AZ21001-1A-5D中文资料
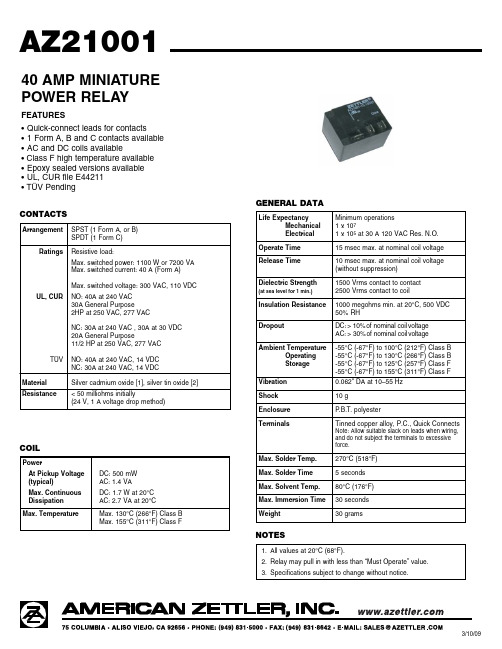
CONTACTSArrangement SPST (1 Form A, or B)SPDT (1 Form C)Ratings Resistive load:Max. switched power: 1100 W or 7200 VAMax. switched current: 40 A (Form A)Max. switched voltage: 300 VAC, 110 VDC UL, CUR NO: 40A at 240 VAC30A General Purpose2HP at 250 VAC, 277 VACNC: 30A at 240 VAC , 30A at 30 VDC20A General Purpose11/2 HP at 250 VAC, 277 VACTÜV NO: 40A at 240 VAC, 14 VDCNC: 30A at 240 VAC, 14 VDCMaterial Silver cadmium oxide [1], silver tin oxide [2] Resistance< 50 milliohms initially(24 V, 1 A voltage drop method)GENERAL DATALife Expectancy Minimum operationsMechanical 1 x 107Electrical 1 x 105at 30 A 120 VAC Res. N.O. Operate Time 15 msec max. at nominal coil voltage Release Time 10 msec max. at nominal coil voltage(without suppression)Dielectric Strength1500 Vrms contact to contact(at sea level for 1 min.)2500 Vrms contact to coilInsulation Resistance1000 megohms min. at 20°C, 500 VDC50% RHDropout DC:> 10%of nominal coil voltageAC:> 30%of nominal coil voltageAmbient Temperature-55°C (-67°F) to 100°C (212°F) Class B Operating-55°C (-67°F) to 130°C (266°F) Class BStorage-55°C (-67°F) to 125°C (257°F)Class F-55°C (-67°F) to 155°C (311°F) Class F Vibration0.062" DA at 10–55 HzShock10 gEnclosure P.B.T. polyesterTerminals Tinned copper alloy, P.C., Quick ConnectsNote: Allow suitable slack on leads when wiring,and do not subject the terminals to excessiveforce.Max. Solder Temp.270°C (518°F)Max. Solder Time 5 secondsMax. Solvent Temp.80°C (176°F)Max. Immersion Time30 secondsWeight30 grams40 AMP MINIATUREPOWER RELAYFEATURES•Quick-connect leads for contacts•1 Form A, B and C contacts available•AC and DC coils available• Class F high temperature available•Epoxy sealed versions available•UL, CUR file E44211• TÜV PendingCOILPowerAt Pickup Voltage DC: 500 mW(typical)AC: 1.4 VAMax. Continuous DC: 1.7 W at 20°CDissipation AC: 2.7 VA at 20°CMax. Temperature Max. 130°C (266°F) Class BMax. 155°C (311°F) Class FNOTES1.All values at 20°C (68°F).2.Relay may pull in with less than “Must Operate” value.3.Specifications subject to change without notice.3.3¡À0.50.1300.023.30.5RELAY ORDERING DATACOIL SPECIFICATIONS – DC CoilNominal CoilMust OperateMax. ContinuousNominal CurrentCoil ResistanceORDER NUMBER*VDC VDC VDC mA ± 10%± 10%32.253.930010AZ21001–1A–3D 5 3.75 6.517928AZ21001–1A–5D 6 4.507.815040AZ21001–1A–6D 9 6.7511.710090AZ21001–1A–9D 129.0015.675160AZ21001–1A–12D 1510.2519.560250AZ21001–1A–15D 1813.523.450360AZ21001–1A–18D 2418.031.238640AZ21001–1A–24D 4836.062.4192,560AZ21001-1A–48D 11082.50143813,445AZ21001–1A–110DCOIL SPECIFICATIONS – AC Coil 50/60 HzNominal CoilMust OperateMax. ContinuousNominal Coil Coil ResistanceORDER NUMBER*VAC VAC VAC Power VA ± 10%12915.62.027AZ21001–1A–12A 241831.2 2.0120AZ21001–1A–24A 12090156 2.03,040AZ21001–1A–120A 2201652862.013,490AZ21001–1A–240A*Substitute “-1B” or “-1C” in place of “-1A” for 1 Form B or 1 Form C respectively. For silver tin oxide contacts substitute “-1AE” or “-1CE” in place of “-1A” or “-。
S1D13305中文资料
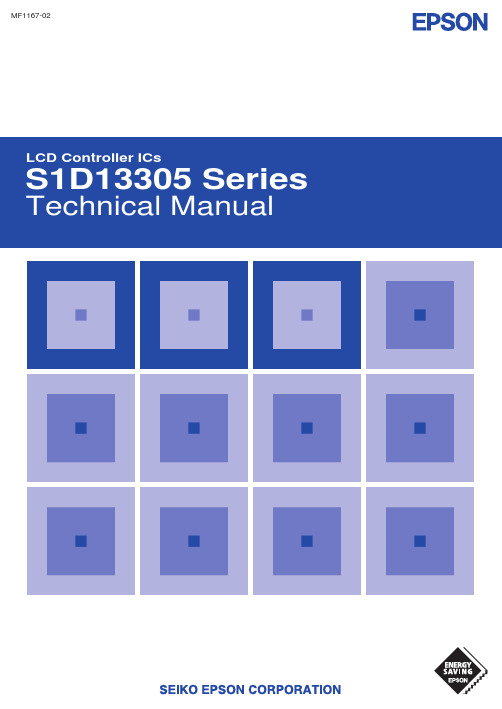
元器件交易网
The information of the product number change
Starting April 1, 2001, the product number will be changed as listed below. To order from April 1, 2001 please use the new product number. For further information, please contact Epson sales representative.
SDU1374#0C SDU1375#0C SDU1376#0C SDU1376BVR SDU1378#0C
• S1D1380x Series New No. Previous No.
SDU1386#0C
New No.
S5U13806P00C
S5U13503P00C S5U13504P00C S5U13505P00C S5U13506P00C
S1D13305 Series S1D13305D00A S1D13305F00A S1D13305F00B
S1D1370x Series S1D13704F00A S1D13705F00A S1D13706B00A S1D13706F00A S1D13708 Series
• S1D1350x Series Previous No.
S5U13704P00C S5U13705P00C S5U13706P00C S5U13706B32R S5U13708P00C
• S1D13A0x Series Previous No.
SDU13A3#0C SDU13A4#0C
New No.
5510说明书

(2)起升机构工作前,应通电空载检查,调整制动片与制动轮之间的间隙,再满负荷调整,通电后间隙调整在0.5-1mm之间为宜。
(3)使用前,应检查减速器的油量是否合适,油质是否符合要求,否则必须添加或更换润滑油。
牵引机构
速度
电机型号
功率
转速
40.5/20m/min
YDEJ132S-4/8
3.3/2.2KW
710/1440 r/min
顶升机构
速度
电机型号
功率
转速
工作压力
0.7m/min
Y132S-4
5.5KW
1440 r/min
20MPa
平衡重
臂长55米
14.5t 用七块 2.2t×6+1.3t
臂长50米
13.2t用六块 2.2t×6
6.3、各种安全装置的调整……………………………………………………51
七、塔机的使用与维护保养…………………………………………………56
7.1、塔机的安全使用须知……………………………………………………56
7.2、塔机的维护保养…………………………………………………………57
7.3、塔机的工作条件和工作环境……………………………………………59
3.2、套架………………………………………………………………………15
3.3、回转支承座………………………………………………………………15
3.4、回转塔身节………………………………………………………………16
3.5、司机室……………………………………………………………………16
3.6、塔帽………………………………………………………………………16
AZ2150-1A-12DE中文资料
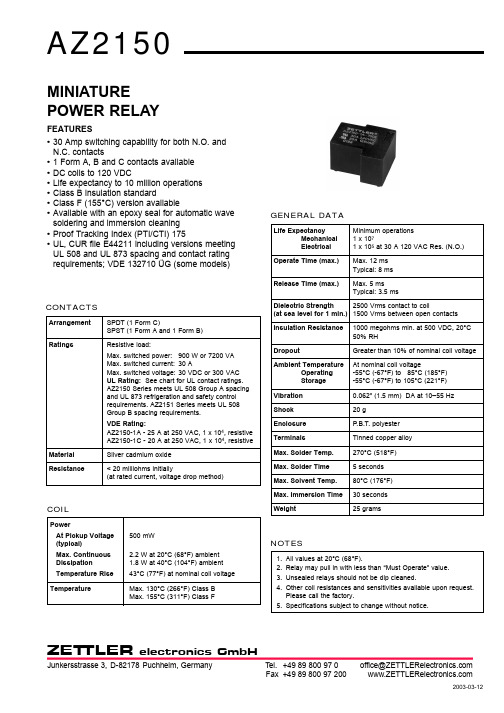
ZET TLERelectronics GmbHFax +49 89 800 97 200 office@ 0 97 800 89 +49 Tel. GermanyPuchheim, D-82178Junkersstrasse 3, 2003-03-12GENERAL DATALife ExpectancyMinimum operations Mechanical 1 x 107Electrical 1 x 105at 30 A 120 VAC Res. (N.O.)Operate Time (max.)Max. 12 ms Typical: 8 ms Release Time (max.)Max. 5 ms Typical: 3.5 msDielectric Strength 2500 Vrms contact to coil(at sea level for 1 min.)1500 Vrms between open contacts Insulation Resistance 1000 megohms min. at 500 VDC, 20°C 50% RHDropoutGreater than 10% of nominal coil voltage Ambient TemperatureAt nominal coil voltageOperating -55°C (-67°F) to 85°C (185°F)Storage -55°C (-67°F) to 105°C (221°F)Vibration 0.062" (1.5 mm) DA at 10–55 Hz Shock 20 gEnclosure P .B.T. polyester TerminalsTinned copper alloy Max. Solder Temp.270°C (518°F)Max. Solder Time 5 seconds Max. Solvent Temp.80°C (176°F)Max. Immersion Time30 seconds Weight25 gramsMINIATURE POWER RELAYFEATURES•30 Amp switching capability for both N.O. and N.C. contacts•1 Form A, B and C contacts available •DC coils to 120 VDC•Life expectancy to 10 million operations •Class B insulation standard•Class F (155°C) version available•Available with an epoxy seal for automatic wave soldering and immersion cleaning •Proof Tracking Index (PTI/CTI) 175•UL, CUR file E44211 including versions meeting UL 508 and UL 873 spacing and contact rating requirements; VDE 132710 ÜG (some models)CONTACTSArrangement SPDT (1 Form C)SPST (1 Form A and 1 Form B)RatingsResistive load:Max. switched power:900 W or 7200 VA Max. switched current: 30 AMax. switched voltage: 30 VDC or 300 VAC UL Rating:See chart for UL contact ratings.AZ2150 Series meets UL 508 Group A spacing and UL 873 refrigeration and safety control requirements. AZ2151 Series meets UL 508Group B spacing requirements.VDE Rating:AZ2150-1A - 25 A at 250 VAC, 1 x 104, resistive AZ2150-1C - 20 A at 250 VAC, 1 x 104, resistiveMaterial Silver cadmium oxideResistance< 20 milliohms initially(at rated current, voltage drop method)COILPowerAt Pickup Voltage 500 mW(typical)Max. Continuous 2.2 W at 20°C (68°F) ambient Dissipation 1.8 W at 40°C (104°F) ambient Temperature Rise 43°C (77°F) at nominal coil voltage TemperatureMax. 130°C (266°F) Class B Max. 155°C (311°F) Class FNOTES1.All values at 20°C (68°F).2.Relay may pull in with less than “Must Operate” value.3.Unsealed relays should not be dip cleaned.4.Other coil resistances and sensitivities available upon request.Please call the factory.5.Specifications subject to change without notice.2003-03-12ZET TLERelectronics GmbHFax +49 89 800 97 200 office@ 0 97 800 89 +49 Tel. GermanyPuchheim, D-82178 Junkersstrasse 3, RELAY ORDERING DATASTANDARD RELAYS: 1 Form A (SPST); 508 Group A; UL 873 VersionCOIL SPECIFICATIONS ORDER NUMBER*Nominal Max.CoilMust Coil Continuous Resistance Operate Unsealed SealedVDC VDC±10%VDC57.327 3.75AZ2150–1A–5D AZ2150–1A–5DE 68.940 4.5AZ2150–1A–6D AZ2150–1A–6DE 913.997 6.75AZ2150–1A–9D AZ2150–1A–9DE 1217.51559.0AZ2150–1A–12D AZ2150–1A–12DE 1522.525611.25AZ2150–1A–15D AZ2150–1A–15DE 1827.438013.5AZ2150–1A–18D AZ2150–1A–18DE 2436.166018.0AZ2150–1A–24D AZ2150–1A–24DE 4868.42,56036.0AZ2150–1A–48D AZ2150–1A–48DE 70104.45,50052.5AZ2150–1A–70D AZ2150–1A–70DE 110163.213,45082.5AZ2150–1A–110D AZ2150–1A–110DESTANDARD RELAYS: 1 Form A (SPST); UL 508 Group B VersionCOIL SPECIFICATIONS ORDER NUMBER*57.327 3.75AZ2151–1A–5D AZ2151–1A–5DE 68.940 4.5AZ2151–1A–6D AZ2151–1A–6DE913.997 6.75AZ2151–1A–9D AZ2151–1A–9DE1217.51559.0AZ2151–1A–12D AZ2151–1A–12DE1522.525611.25AZ2151–1A–15D AZ2151–1A–15DE1827.438013.5AZ2151–1A–18D AZ2151–1A–18DE2436.166018.0AZ2151–1A–24D AZ2151–1A–24DE4868.42,56036.0AZ2151–1A–48D AZ2151–1A–48DE70104.45,50052.5AZ2151–1A–70D AZ2151–1A–70DE 110163.213,45082.5AZ2151–1A–110DAZ2151–1A–110DE * Substitute “1B” or “1C” in place of the “1A” to indicate 1 Form B and 1 Form C respectively.To indicate Class F version, add suffix “F”.MECHANICAL DATA。
AZ881中文资料

COILPowerAt Pickup Voltage 192 mW (single side stable, 2 coil latching)(typical)96 mW (1 coil latching)Max. Continuous 0.75 W at 20°C (68°F) ambient Dissipation Temperature Rise 30°C (54°F) at nominal coil voltage 130°C (266°F) Class B, 155°C (311°F)Class FCONTACTSArrangement SPST (1 Form A), DPST (2 Form A)DPST (1 Form A and 1 Form B)RatingsResistive load:Max. switched power:150 W or 2000 VA (SPST) 150 W or 1250 VA (DPST)Max. switched current: 8 A (SPST)5 A (DPST)Max. switched voltage:150 VDC or 380 VAC**Note: If switching voltage is greater than 30 VDC,special precautions must be taken. Please contact the factory.Rated Load SPSTUL, CUR 8 A at 250 VAC resistive, 100k cycles5 A at 30 VDC resistive, 100k cycles 1/6 HP at 250 VAC5 A at 250 VAC resistive, 100k cycles 5 A at 30 VDC resistive, 100k cycles1/6 HP at 250 VACMaterial Silver nickel, gold plating optionalResistance< 50 milliohms initially (6 V 1 A voltage drop method)Max. TemperatureGENERAL DATALife ExpectancyMinimum operations Mechanical 1 x 107Electrical 1 x 105at 8 A 250 VAC resistive (SPST)Operate Time (typical) 5 ms at nominal coil voltage Release Time (typical) 3 ms at nominal coil voltage (with no coil suppression)Set Time (typical)5 ms at nominal coil voltage Reset Time (typical) 4 ms at nominal coil voltage Dielectric Strength 4000 Vrms contact to coil(at sea level)1000 Vrms between open contacts 2000 Vrms between contact sets Insulation Resistance 1000 megohms min. at 20°C 500 Vdc 50% RHDropoutGreater than 10% of nominal coil voltage Ambient TemperatureAt nominal coil voltageOperating -40°C (-40°F) to 70°C (158°F)Storage -40°C (-40°F) to 130°C (266°F)Vibration 0.078” DA at 10 to 55 Hz Shock 20 g functional 100 g destructive Enclosure P.B.T. polyesterTerminalsTinned copper alloy, P.C.Max. Solder Temp.270°C (518°F)Max. Solder Time 5 seconds Max. Solvent Temp.80°C (176°F)Max. Immersion Time30 seconds Weight4.7 grams8 A SPST / 5 A DPST POLARIZED SUBMINIATURE POWER RELAYSINGLE SIDE STABLE (NON-LATCHING)AND BISTABLE (LATCHING)FEATURES •Dielectric strength 3000 Vrms•Single and dual coil latching versions available •Epoxy sealed version available •8 Amp switching•Class B (130°C) insulation standard •Class F (155°C) insulation available •UL, CUR file E44211NOTES1.All values at 20°C (68°F).2.Relay may pull in with less than “Must Operate” value.3.Relay has fixed coil polarity.4.For complete isolation between the relay’s magnetic fields, it is recom-mended that a .197" (5.0 mm) space be provided between adjacent relays.5.Relay adjustment may be affected if undue pressure is exertedon relay case.6.Specifications subject to change without notice.DPSTAZ881P1RELAY ORDERING DATA AZ881AZ881P2COIL SPECIFICATIONS - DUAL COIL LATCHINGORDER NUMBER*Nominal Must.Max. ContinuousCoil1 Form ACoil Operate VDCResistance 1 Form A 2 Form A 1 Form B VDC VDC ± 10%32.4 4.730 AZ881P2-1A-3D AZ881P2-2A-3D AZ881P2-1AB-3D 5 4.07.983 AZ881P2-1A-5D AZ881P2-2A-5D AZ881P2-1AB-5D 6 4.89.5120 AZ881P2-1A-6D AZ881P2-2A-6D AZ881P2-1AB-6D 97.214.2270 AZ881P2-1A-9D AZ881P2-2A-9D AZ881P2-1AB-9D 129.619.0480 AZ881P2-1A-12D AZ881P2-2A-12D AZ881P2-1AB-12D 2419.237.91920 AZ881P2-1A-24DAZ881P2-2A-24D AZ881P2-1AB-24D*Add suffix “E” for epoxy sealed version. Add suffix “A” for gold plated contacts. Add suffix “R” for reversed polarity coil. Add suffix “F” for class F insulation.MECHANICAL DATA。
- 1、下载文档前请自行甄别文档内容的完整性,平台不提供额外的编辑、内容补充、找答案等附加服务。
- 2、"仅部分预览"的文档,不可在线预览部分如存在完整性等问题,可反馈申请退款(可完整预览的文档不适用该条件!)。
- 3、如文档侵犯您的权益,请联系客服反馈,我们会尽快为您处理(人工客服工作时间:9:00-18:30)。
COIL
Power
At Pickup Voltage 192 mW (single side stable, 2 coil latching)(typical)
96 mW (1 coil latching)
Max. Continuous 0.75 W at 20°C (68°F) ambient Dissipation Temperature Rise 30°C (54°F) at nominal coil voltage 130°C (266°F) Class B, 155°C (311°F)Class F
CONTACTS
Arrangement SPST (1 Form A), DPST (2 Form A)DPST (1 Form A and 1 Form B)Ratings
Resistive load:Max. switched power:
150 W or 2000 VA (SPST) 150 W or 1250 VA (DPST)
Max. switched current: 8 A (SPST)
5 A (DPST)
Max. switched voltage:150 VDC or 380 VAC*
*Note: If switching voltage is greater than 30 VDC,special precautions must be taken. Please contact the factory.
Rated Load SPST
UL, CUR 8 A at 250 VAC resistive, 100k cycles
5 A at 30 VDC resistive, 100k cycles 1/
6 HP at 250 VAC
5 A at 250 VAC resistive, 100k cycles 5 A at 30 VDC resistive, 100k cycles
1/6 HP at 250 VAC
Material Silver nickel, gold plating optional
Resistance
< 50 milliohms initially (6 V 1 A voltage drop method)
Max. Temperature
GENERAL DATA
Life Expectancy
Minimum operations Mechanical 1 x 107
Electrical 1 x 105at 8 A 250 VAC resistive (SPST)Operate Time (typical) 5 ms at nominal coil voltage Release Time (typical) 3 ms at nominal coil voltage (with no coil suppression)Set Time (typical)
5 ms at nominal coil voltage Reset Time (typical) 4 ms at nominal coil voltage Dielectric Strength 4000 Vrms contact to coil
(at sea level)
1000 Vrms between open contacts 2000 Vrms between contact sets Insulation Resistance 1000 megohms min. at 20°C 500 Vdc 50% RH
Dropout
Greater than 10% of nominal coil voltage Ambient Temperature
At nominal coil voltage
Operating -40°C (-40°F) to 70°C (158°F)Storage -40°C (-40°F) to 130°C (266°F)Vibration 0.078” DA at 10 to 55 Hz Shock 20 g functional 100 g destructive Enclosure P.B.T. polyester
Terminals
Tinned copper alloy, P.C.Max. Solder Temp.270°C (518°F)Max. Solder Time 5 seconds Max. Solvent Temp.80°C (176°F)Max. Immersion Time
30 seconds Weight
4.7 grams
8 A SPST / 5 A DPST POLARIZED SUBMINIATURE POWER RELAY
SINGLE SIDE STABLE (NON-LATCHING)AND BISTABLE (LATCHING)
FEATURES •Dielectric strength 3000 Vrms
•Single and dual coil latching versions available •Epoxy sealed version available •8 Amp switching
•Class B (130°C) insulation standard •Class F (155°C) insulation available •
UL, CUR file E44211
NOTES
1.All values at 20°C (68°F).
2.Relay may pull in with less than “Must Operate” value.
3.Relay has fixed coil polarity.
4.
For complete isolation between the relay’s magnetic fields, it is recom-mended that a .197" (5.0 mm) space be provided between adjacent relays.5.Relay adjustment may be affected if undue pressure is exerted
on relay case.
6.Specifications subject to change without notice.
DPST
AZ881P1
RELAY ORDERING DATA AZ881
AZ881P2
COIL SPECIFICATIONS - DUAL COIL LATCHING
ORDER NUMBER*
Nominal Must.Max. Continuous
Coil
1 Form A
Coil Operate VDC
Resistance 1 Form A 2 Form A 1 Form B VDC VDC ± 10%
3
2.4 4.730 AZ881P2-1A-3D AZ881P2-2A-3D AZ881P2-1AB-3D 5 4.07.983 AZ881P2-1A-5D AZ881P2-2A-5D AZ881P2-1AB-5D 6 4.89.5120 AZ881P2-1A-6D AZ881P2-2A-6D AZ881P2-1AB-6D 97.214.2270 AZ881P2-1A-9D AZ881P2-2A-9D AZ881P2-1AB-9D 129.619.0480 AZ881P2-1A-12D AZ881P2-2A-12D AZ881P2-1AB-12D 24
19.2
37.9
1920 AZ881P2-1A-24D
AZ881P2-2A-24D AZ881P2-1AB-24D
*Add suffix “E” for epoxy sealed version. Add suffix “A” for gold plated contacts. Add suffix “R” for reversed polarity coil. Add suffix “F” for class F insulation.
MECHANICAL DATA。