快速成形技术
冲压模具的快速成形技术介绍
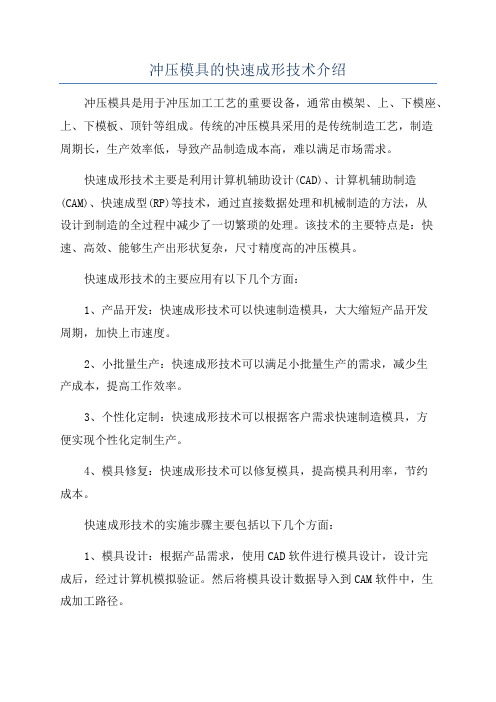
冲压模具的快速成形技术介绍冲压模具是用于冲压加工工艺的重要设备,通常由模架、上、下模座、上、下模板、顶针等组成。
传统的冲压模具采用的是传统制造工艺,制造周期长,生产效率低,导致产品制造成本高,难以满足市场需求。
快速成形技术主要是利用计算机辅助设计(CAD)、计算机辅助制造(CAM)、快速成型(RP)等技术,通过直接数据处理和机械制造的方法,从设计到制造的全过程中减少了一切繁琐的处理。
该技术的主要特点是:快速、高效、能够生产出形状复杂,尺寸精度高的冲压模具。
快速成形技术的主要应用有以下几个方面:1、产品开发:快速成形技术可以快速制造模具,大大缩短产品开发周期,加快上市速度。
2、小批量生产:快速成形技术可以满足小批量生产的需求,减少生产成本,提高工作效率。
3、个性化定制:快速成形技术可以根据客户需求快速制造模具,方便实现个性化定制生产。
4、模具修复:快速成形技术可以修复模具,提高模具利用率,节约成本。
快速成形技术的实施步骤主要包括以下几个方面:1、模具设计:根据产品需求,使用CAD软件进行模具设计,设计完成后,经过计算机模拟验证。
然后将模具设计数据导入到CAM软件中,生成加工路径。
2、快速成形:根据CAM软件生成的加工路径,使用快速成形设备进行模具的快速成形。
常用的快速成形设备有三维打印机、激光烧结机等。
3、后处理:快速成形完成后,需要进行后处理,包括清理、热处理、表面处理等。
清理主要是去除模具表面残留物质,热处理是为了提高模具的硬度和耐磨性,表面处理是为了提高模具的表面质量。
快速成形技术有以下几个优点:1、缩短制造周期:传统模具制造周期长,快速成形技术可以大大缩短制造周期,提高生产效率。
2、节约成本:快速成形技术可以减少材料浪费、人工成本等,降低模具制造成本。
3、提高产品质量:快速成形技术可以生产出形状复杂,尺寸精度高的模具,提高产品质量。
4、适应多品种、小批量生产:快速成形技术可以根据客户需求快速制造模具,适应多品种、小批量生产的需求。
2.第2章 快速成型技术及其在铸造中的应用解析
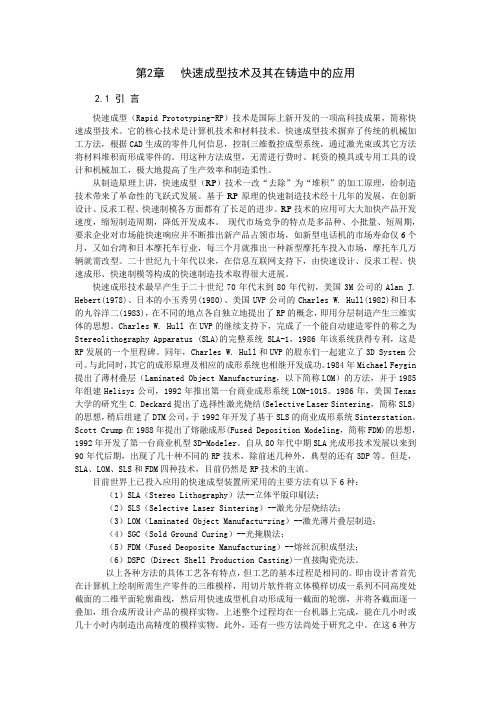
第2章快速成型技术及其在铸造中的应用2.1 引言快速成型(Rapid Prototyping-RP)技术是国际上新开发的一项高科技成果,简称快速成型技术。
它的核心技术是计算机技术和材料技术。
快速成型技术摒弃了传统的机械加工方法,根据CAD生成的零件几何信息,控制三维数控成型系统,通过激光束或其它方法将材料堆积而形成零件的。
用这种方法成型,无需进行费时、耗资的模具或专用工具的设计和机械加工,极大地提高了生产效率和制造柔性。
从制造原理上讲,快速成型(RP)技术一改“去除”为“堆积”的加工原理,给制造技术带来了革命性的飞跃式发展。
基于RP原理的快速制造技术经十几年的发展,在创新设计、反求工程、快速制模各方面都有了长足的进步。
RP技术的应用可大大加快产品开发速度,缩短制造周期,降低开发成本。
现代市场竞争的特点是多品种、小批量、短周期,要求企业对市场能快速响应并不断推出新产品占领市场,如新型电话机的市场寿命仅6个月,又如台湾和日本摩托车行业,每三个月就推出一种新型摩托车投入市场,摩托车几万辆就需改型。
二十世纪九十年代以来,在信息互联网支持下,由快速设计、反求工程、快速成形、快速制模等构成的快速制造技术取得很大进展。
快速成形技术最早产生于二十世纪70年代末到80年代初,美国3M公司的Alan J. Hebert(1978)、日本的小玉秀男(1980)、美国UVP公司的Charles W. Hull(1982)和日本的丸谷洋二(1983),在不同的地点各自独立地提出了RP的概念,即用分层制造产生三维实体的思想。
Charles W. Hull 在UVP的继续支持下,完成了一个能自动建造零件的称之为Stereolithography Apparatus (SLA)的完整系统SLA-1,1986年该系统获得专利,这是RP发展的一个里程碑。
同年,Charles W. Hull和UVP的股东们一起建立了3D System公司。
快速成型技术
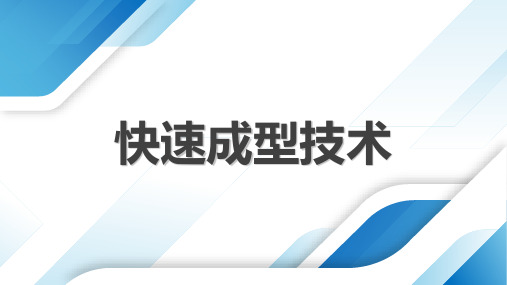
其在处理速度上都可以很好的满足需求,而且时间跨度不大,有利于实现产品开发的高速闭环反馈。 其二:集成化,快速成型技术使得设计环节和制造环节达到了很好的统一,我们知道在快速 成型的操作过程中,计算机中
的CAD模型数据会通过软件转化的方式,自动生成数控指令,依据数据的转化实现对于部件的合理加工。由此看来设计和 制造之间的鸿沟不再存在,达到了高度的集约化。 其三:适用性,快速成型技术,适翻分层技术制造工艺,将复杂的三维切成二维来处理,极大的简化了加工流程,在不存 在三维刀具的干涉的前提下,高效的处理好复杂的中空结构。无论是从理论上来讲,还是从实践上来讲,其技术的适用性 可以应对任何的复杂构件制造。 其四:可调整性,快速成型技术,即真正意义上的数字化系统,是制造业中的利器,我们操作员仅仅需要合理设置一下相 关的参数和属性, 就可以有针对性的处理好各种产品的样品制造和小批量生产;而且在此过程中,保证了成型过程的柔韧 性。 其五:自动化,快速成型技术,实现了完全的自动化成型,只要操作人员输入相关的参数,在不需要多少干涉的情况下,实 现整个过程的自动运行。
从技术发展角度看,计算机科学、CAD技术、材料科学、激光技术的发展和普及,为新的制造技 术的产生奠定了技术物质基础。
快速成形技术发展状况与趋势

快速成形技术发展状况与趋势快速成形技术,又称为三维打印、增材制造等,是近年来新兴的一种制造技术,它可以将数字化的设计文件转化为实体物体,而且速度快、成本低,能够满足个性化定制的需求。
该技术的发展已经引起海内外制造业的广泛关注和研究,下面介绍快速成形技术的发展状况和趋势。
快速成形技术最早出现在20世纪80年代,最初被用于快速制作模型,其发展始于CAD 设计技术、计算机组成技术以及材料工程技术的发展。
20世纪90年代以后,该技术经过不断的改良和完善,应用范围逐渐扩大,主要涉及到汽车、航空、医疗、建筑等领域。
目前,全球主要的快速成形技术公司有美国Stratasys、德国EOS、瑞典Arcam和中国沃特玛等。
近年来,随着材料科技、智能制造和数字工厂的发展,快速成形技术呈现出以下几个趋势:1. 多材料、多工艺:不同快速成形技术采用不同材料和工艺,未来发展方向是多材料、多工艺的结合。
例如,增材制造可以利用多种材料打印出复杂的组件,立体光绘可以通过多重叠加实现更高的可塑性和更精细的表面质量。
2. 智能化、网络化:快速成形技术已经与计算机、互联网和智能化制造相结合,实现了数字化和智能化的设计与制造,未来将趋向于更加智能化和网络化,实现生产和流程的自动化。
例如,智能打印机具有自我诊断和自动修复的功能,可以自主管理并调节打印参数,提高设备利用率和打印效率。
3. 个性化、定制化:快速成形技术具有快速、便捷、低成本的特点,可以实现个性化和定制化的生产,未来将趋向于更加个性化和高效化。
例如,医疗领域可以利用该技术制作个性化的医疗器械、假体和植入物,满足患者的特殊需求;商品领域可以利用该技术实现全球化生产和本地化供应,提高响应速度和市场竞争力。
4. 生态可持续、绿色制造:快速成形技术采用增材制造和材料回收等技术,可以实现生态可持续和绿色制造,未来将趋向于更加环保和节能。
例如,采用生物降解材料可以实现零污染和资源循环利用,采用能源节约技术可以减少能源消耗和碳排放。
快速成形技术

快速成形技术现代成形理论是研究所有产品制造的成形方式,即研究将成形材料有序地组织成具有确定外形和特定功能的三维实体的科学,建立起产品制造的理论模型。
根据工艺可以将产品成形的过程分为如下四种:1.受迫成形成形材料受到压力的作用而成形的方法,如金属材料成形的冷冲压成形、锻压成形、挤压成形以及铸造成形等。
2.去除成形这是人类从制作工具到现代化生产一直沿用的主要成形方法,如刀具切削加工、磨削加工、电火花加工等。
3.离散/堆积成形与传统制造不同,离散/堆积成形从零件的CAD实体模型出发,通过软件分层离散和数控成形系统,用层层加工的方法将成形材料堆积而形成实体零件。
4.生长成形生长成形或称仿生成形是指模仿自然界中生物生长方式而成形的方法。
快速成形技术是基于离散/堆积思想和数字化的新型成形技术,它突破了传统的加工方式,不需机械加工设备即可快速地制造形状极为复杂的工件,被认为是近20年制造技术领域的一次重大突破。
快速成形技术是当前世界上先进的产品开发与快速工具制造技术,对制造企业的模型、原型及成型件的制造方式正产生深远的影响。
1.1快速成形技术1.1.1快速成形技术原理快速成形(RP,Rapid Prototyping)技术又称快速原型制造,诞生于20世纪80年代后期,至今已有20多年的历史,是基于材料堆积法的新型制造技术。
快速制造技术集机械工程、计算机辅助制造(CAD)、逆向工程技术、分层制造技术、数控技术、材料科学等于一身,可以自动、直接、快速、精确地将计算机上设计的模型转变为具有一定功能的原型或直接制造零件,从而为零件原型制作、新设计思想的校验等方面提供一种高效低成本的实现方法。
Terry Wohlers和美国制造工程师协会(SME)对RP技术进行了定义[]:RP系统依据三维CAD模型数据、CT(计算机断层扫描,computer tomography)和MRI(核磁共振成像,magnetic resonance imaging)扫描数据和由三维实物数字化系统创建的数据,把所得数据分成一系列二维平面,又按相同序列沉积或固化出物理实体。
快速成型技术

快速成型技术1、快速成型简介快速成型(RP)技术是九十年代发展起来的一项先进制造技术,是为制造业企业新产品开发服务的一项关键共性技术, 对促进企业产品创新、缩短新产品开发周期、提高产品竞争力有积极的推动作用。
自该技术问世以来,已经在发达国家的制造业中得到了广泛应用,并由此产生一个新兴的技术领域。
RP技术是在现代CAD/CAM技术、激光技术、计算机数控技术、精密伺服驱动技术以及新材料技术的基础上集成发展起来的。
不同种类的快速成型系统因所用成形材料不同,成形原理和系统特点也各有不同。
但是,其基本原理都是一样的,那就是"分层制造,逐层叠加",类似于数学上的积分过程。
形象地讲,快速成形系统就像是一台"立体打印机"。
2、RP 技术的原理RP 技术是采用离散∕堆积成型的原理, 由CAD 模型直接驱动的通过叠加成型方出所需要零件的计算机三维曲面或实体模型, 根据工艺要求将其按一定厚度进行分层, 把三维电子模型变成二维平面信息(截面信息), 在微机控制下, 数控系统以平面加工的方式有序地连续加工出每个薄层并使它们自动粘接成型, 图1 为RP 技术的基本原理。
图1 RP 技术的基本原理。
RP 技术体系可分解为几个彼此联系的基本环节: 三维CAD 造型、反求工程、数据转换、原型制造、后处理等。
2.1立体光固化成型(SLA)该方法是目前世界上研究最深入、技术最成熟、应用最广泛的一种快速成型方法。
SLA 技术原理是计算机控制激光束对光敏树脂为原料的表面进行逐点扫描, 被扫描区域的树脂薄层( 约十分之几毫米) 产生光聚合反应而固化, 形成零件的一个薄层。
工作台下移一个层厚的距离, 以便固化好的树脂表面再敷上一层新的液态树脂, 进行下一层的扫描加工, 如此反复, 直到整个原型制造完毕。
由于光聚合反应是基于光的作用而不是基于热的作用, 故在工作时只需功率较低的激光源。
此外,因为没有热扩散, 加上链式反应能够很好地控制, 能保证聚合反应不发生在激光点之外, 因而加工精度高, 表面质量好, 原材料的利用率接近100%, 能制造形状复杂、精细的零件, 效率高。
四种常见快速成型技术
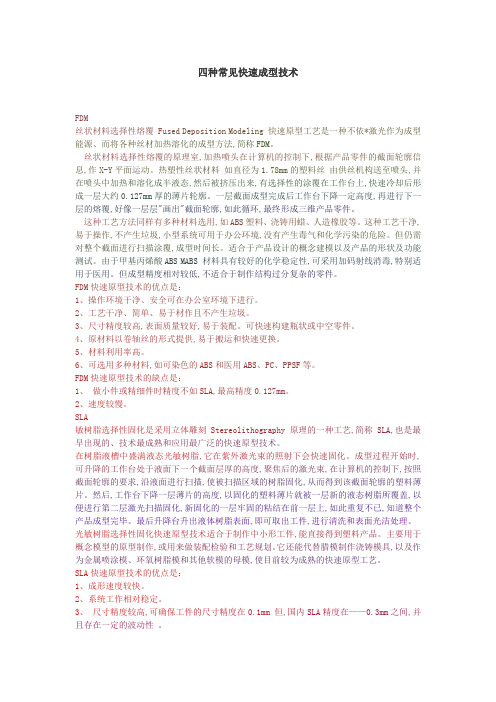
四种常见快速成型技术FDM丝状材料选择性熔覆 Fus ed Dep osi tion Mod eling 快速原型工艺是一种不依*激光作为成型能源、而将各种丝材加热溶化的成型方法,简称FDM。
丝状材料选择性熔覆的原理室,加热喷头在计算机的控制下,根据产品零件的截面轮廓信息,作X-Y平面运动。
热塑性丝状材料如直径为1.78m m的塑料丝由供丝机构送至喷头,并在喷头中加热和溶化成半液态,然后被挤压出来,有选择性的涂覆在工作台上,快速冷却后形成一层大约0.127mm厚的薄片轮廓。
一层截面成型完成后工作台下降一定高度,再进行下一层的熔覆,好像一层层"画出"截面轮廓,如此循环,最终形成三维产品零件。
这种工艺方法同样有多种材料选用,如ABS塑料、浇铸用蜡、人造橡胶等。
这种工艺干净,易于操作,不产生垃圾,小型系统可用于办公环境,没有产生毒气和化学污染的危险。
但仍需对整个截面进行扫描涂覆,成型时间长。
适合于产品设计的概念建模以及产品的形状及功能测试。
由于甲基丙烯酸ABS M AB S 材料具有较好的化学稳定性,可采用加码射线消毒,特别适用于医用。
但成型精度相对较低,不适合于制作结构过分复杂的零件。
FD M快速原型技术的优点是:1、操作环境干净、安全可在办公室环境下进行。
2、工艺干净、简单、易于材作且不产生垃圾。
3、尺寸精度较高,表面质量较好,易于装配。
可快速构建瓶状或中空零件。
4、原材料以卷轴丝的形式提供,易于搬运和快速更换。
5、材料利用率高。
6、可选用多种材料,如可染色的A BS和医用A BS、PC、PP SF等。
FDM快速原型技术的缺点是:1、做小件或精细件时精度不如SLA,最高精度0.127mm。
2、速度较慢。
SL A敏树脂选择性固化是采用立体雕刻Stereo litho gra phy原理的一种工艺,简称SLA,也是最早出现的、技术最成熟和应用最广泛的快速原型技术。
在树脂液槽中盛满液态光敏树脂,它在紫外激光束的照射下会快速固化。
快速成型技术
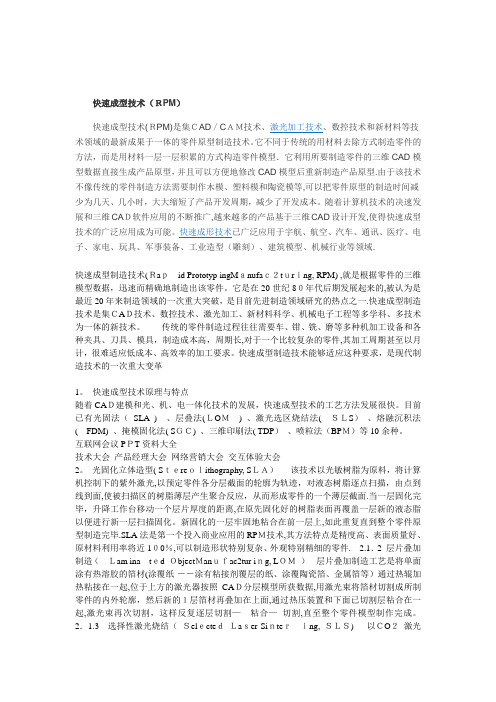
快速成型技术(RPM)快速成型技术(RPM)是集CAD/CAM技术、激光加工技术、数控技术和新材料等技术领域的最新成果于一体的零件原型制造技术。
它不同于传统的用材料去除方式制造零件的方法,而是用材料一层一层积累的方式构造零件模型.它利用所要制造零件的三维CAD模型数据直接生成产品原型,并且可以方便地修改CAD模型后重新制造产品原型.由于该技术不像传统的零件制造方法需要制作木模、塑料模和陶瓷模等,可以把零件原型的制造时间减少为几天、几小时,大大缩短了产品开发周期,减少了开发成本。
随着计算机技术的决速发展和三维CAD软件应用的不断推广,越来越多的产品基于三维CAD设计开发,使得快速成型技术的广泛应用成为可能。
快速成形技术已广泛应用于宇航、航空、汽车、通讯、医疗、电子、家电、玩具、军事装备、工业造型(雕刻)、建筑模型、机械行业等领域.快速成型制造技术(Rapid Prototyp ingManufac2turing, RPM) ,就是根据零件的三维模型数据,迅速而精确地制造出该零件。
它是在20世纪80年代后期发展起来的,被认为是最近20年来制造领域的一次重大突破,是目前先进制造领域研究的热点之一.快速成型制造技术是集CAD技术、数控技术、激光加工、新材料科学、机械电子工程等多学科、多技术为一体的新技术。
传统的零件制造过程往往需要车、钳、铣、磨等多种机加工设备和各种夹具、刀具、模具,制造成本高,周期长,对于一个比较复杂的零件,其加工周期甚至以月计,很难适应低成本、高效率的加工要求。
快速成型制造技术能够适应这种要求,是现代制造技术的一次重大变革1。
快速成型技术原理与特点随着CAD建模和光、机、电一体化技术的发展,快速成型技术的工艺方法发展很快。
目前已有光固法(SLA )、层叠法(LOM) 、激光选区烧结法(SLS)、熔融沉积法(FDM) 、掩模固化法( SGC) 、三维印刷法( TDP)、喷粒法(BPM)等10余种。
快速成形技术
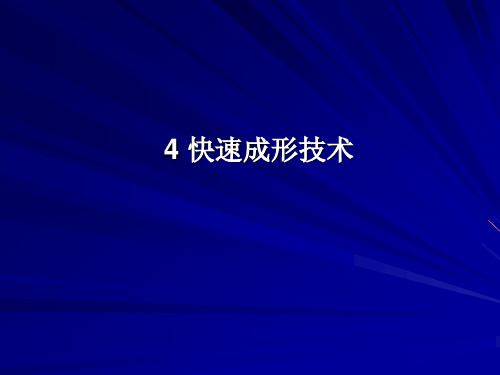
4.2.3 选择性激光烧结
1986年,美国Texas大学的研究生C.Deckard提出了选择性烧 结(Selected Laser Sintering,SLS)的思想,稍后组建了DTM 公司,于1992年推出SLS成形机。 选择性激光烧结 的成形过程是:由CAD模型各层切片的平面 几何信息生成X-Y激光扫描器在 每层粉末上的数控运动指令,铺 粉器将粉末一层一层地撒在工作台上,再用滚筒将粉末滚平、压 实,每层粉末的厚度均对应于CAD模型的切片厚度。各层铺粉二 氧化碳激光器选择性烧结到基体上,而未被激光扫描、烧结的粉 末仍留在原处起支撑作用,直至烧结出整个零件。
利用分层技术制造了金属冲裁 模、成形模和注塑模
20世纪70年代末到80年代初,美国3M公司的Alan J. Hebert(1978年)、日本的小玉秀男(1983年) 、美国UVP公司的Charles W. Hull(1982年)和日 本的丸谷洋二(1983年)各自独立的首次提出了RP 的概念
Chares W.Hull在UVP地资助下,完成了第一个RP 系统——Stereolithography Apparatus(SLA) 1986年该系统获得专利,这是RP发展的一个里程碑
(5)制造原型的复制性、互换性高;
(6)加工周期短、成本低,成本与产品复杂程度无关,一般 制造费用降低50% ,加工周期节约70%以上;
(7)加工过程中无振动、噪声和切削废料;
4.2 RP技术的主要工艺方法
快速成形技术经过20年左右的发展,其工艺已经逐步完善, 发展了许多成熟的加工工艺及成形系统。快速成形技术发展至今 以其技术的高集成性、高柔性、高速性而得到了迅速发展。目前 快速成形的工艺方法已有几十种之多,其中主要工艺有五种基本 类型:光固化成型法、分层实体制造法、选择性激光烧结法和熔 融沉积制造法,三维印刷工艺。
快速成型技术的种类

快速成型技术的种类
快速成型技术是一种以数字化模型为基础,通过逐层堆积材料,实现快速制造物品的技术。
快速成型技术的种类很多,常见的有以下几种:
1. 光固化快速成型技术:通过紫外线或激光束照射光敏树脂,使其固化成所需形状。
2. 喷墨式快速成型技术:通过喷墨头控制液体喷射,将粉末材料逐层喷涂并加固。
3. 熔融沉积式快速成型技术:将金属丝或粉末熔化,通过火焰或电弧喷射,逐层沉积成型。
4. 熔化层压式快速成型技术:将塑料或金属粉末加热或熔化,通过喷嘴或挤出机,逐层堆叠并加固。
5. 粉末烧结式快速成型技术:将粉末压缩成形,然后通过高温处理或激光束烧结,实现快速成型。
以上是常见的几种快速成型技术,它们各有优劣,可以根据具体需求选择合适的技术。
- 1 -。
快速成形技术及其发展
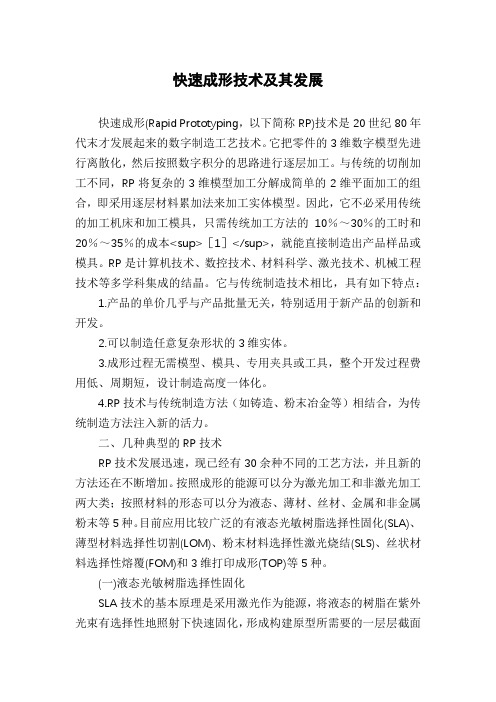
快速成形技术及其发展快速成形(Rapid Prototyping,以下简称RP)技术是20世纪80年代末才发展起来的数字制造工艺技术。
它把零件的3维数字模型先进行离散化,然后按照数字积分的思路进行逐层加工。
与传统的切削加工不同,RP将复杂的3维模型加工分解成简单的2维平面加工的组合,即采用逐层材料累加法来加工实体模型。
因此,它不必采用传统的加工机床和加工模具,只需传统加工方法的10%~30%的工时和20%~35%的成本<sup>[1]</sup>,就能直接制造出产品样品或模具。
RP是计算机技术、数控技术、材料科学、激光技术、机械工程技术等多学科集成的结晶。
它与传统制造技术相比,具有如下特点:1.产品的单价几乎与产品批量无关,特别适用于新产品的创新和开发。
2.可以制造任意复杂形状的3维实体。
3.成形过程无需模型、模具、专用夹具或工具,整个开发过程费用低、周期短,设计制造高度一体化。
4.RP技术与传统制造方法(如铸造、粉末冶金等)相结合,为传统制造方法注入新的活力。
二、几种典型的RP技术RP技术发展迅速,现已经有30余种不同的工艺方法,并且新的方法还在不断增加。
按照成形的能源可以分为激光加工和非激光加工两大类;按照材料的形态可以分为液态、薄材、丝材、金属和非金属粉末等5种。
目前应用比较广泛的有液态光敏树脂选择性固化(SLA)、薄型材料选择性切割(LOM)、粉末材料选择性激光烧结(SLS)、丝状材料选择性熔覆(FOM)和3维打印成形(TOP)等5种。
(一)液态光敏树脂选择性固化SLA技术的基本原理是采用激光作为能源,将液态的树脂在紫外光束有选择性地照射下快速固化,形成构建原型所需要的一层层截面轮廓,然后依次将每一层截面轮廓叠加成三维的原型,如图1所示。
其主要过程是:1.容器中装有光敏树脂,升降平台低于液面,表面铺有一层(0.1mm)树脂;2.通过透镜聚焦和扫描镜扫描后的激光束,在计算机控制系统的操纵下,按照截面的轮廓形状对液面进行扫描,从而形成一层固化的制件轮廓截面;3.升降平台下降一层(0.1mm)高度,刮平器将液面刮平,形成新的液面,激光束再固化一层轮廓;4.如此循环不已,直至原型制作完成。
快速成形实训报告

一、实训目的本次快速成形实训旨在使学生了解快速成形技术的原理、设备操作流程以及实际应用,培养学生的动手能力和创新意识。
通过实训,使学生掌握快速成形的基本操作方法,熟悉快速成形设备的使用,并能够根据实际需求进行快速成形模型的制作。
二、实训内容1. 快速成形技术原理快速成形技术(Rapid Prototyping,简称RP)是一种以数字模型为基础,通过材料堆积的方式快速制造出实体模型的技术。
其主要原理包括:分层制造、材料堆积、光固化、热熔、喷墨打印等。
2. 快速成形设备操作本次实训主要使用的是光固化快速成形设备,其操作流程如下:(1)准备:将数字模型导入设备,调整参数,如切片厚度、填充密度、打印速度等。
(2)预热:打开设备,预热光固化材料,使其达到一定温度。
(3)打印:设备开始分层打印,每层厚度约为0.1mm,打印速度约为10mm/s。
(4)固化:紫外光照射材料,使材料固化。
(5)脱模:打印完成后,将模型从设备中取出。
3. 快速成形模型制作根据实际需求,设计并制作一个简单的快速成形模型。
具体步骤如下:(1)设计:使用CAD软件进行三维建模,将设计好的模型导出为STL格式。
(2)切片:将STL格式的模型导入设备,进行切片处理。
(3)打印:按照设备参数进行打印,直至模型成型。
(4)后处理:将打印好的模型进行打磨、抛光等后处理,使其达到预期效果。
三、实训过程1. 实训前期:学习快速成形技术原理,了解快速成形设备操作流程,熟悉快速成形材料。
2. 实训中期:根据实训要求,设计并制作一个快速成形模型,进行实际操作。
3. 实训后期:对制作的模型进行评价,总结实训过程中的经验教训。
四、实训结果通过本次实训,我们成功制作了一个简单的快速成形模型,掌握了快速成形设备的基本操作方法。
以下是实训过程中取得的主要成果:1. 熟悉了快速成形技术原理,了解了快速成形设备的使用。
2. 掌握了快速成形模型的设计、制作、后处理等基本技能。
先进制造技术——快速成型技术-PPT

FDM 原理 图
二、特点
优点:
1、采用热熔挤压头专利技术,系统结构原理和操作简 单,且使用无毒的原材料,设备可安装在办公环境中。
2、成型速度快。不需要SLA中的刮板工序。 3、用蜡成型的零件原型,可以直接用于熔模铸造。 4、可以成型任意复杂程度的零件。如复杂的内腔、孔 等。 5、原材料在成型过程中无化学变化,制件的翘曲变形 小。 6、原材料利用率高。 7、支撑去除简单。
快速成形技术
概述:
快速成形技术(Rapid Prototyping,简称RP)20世 纪80年代发展起来的,它综合了机械工程、CAD、 数控技术、激光技术及材料科学技术,可以自动、 直接、快速、精确地将设计思想转变为具有一定功 能的原型或直接制造零件,从而大大缩短产品的研 制周期。因而,被认为是近20来制造领域的一个重 大突破。影响力与数控技术相当。
SLS工艺是利用粉末材料(金属粉末或非金属粉末) 在激光照射下烧结的原理,在计算机控制下层层堆积 成形。
SLS原理图
工作台上均匀铺上一 层很薄(0.1~0.2mm) 的粉末,激光束在计算 机的控制下按照零件分 层轮廓有选择性地进行 烧结,一层完成后再进 行下一层烧结。全部烧 结完成后去掉多余的粉 末,再进行打磨、烘干 等处理便获得零件。
又称熔丝沉积,它是将丝状的热熔性材料加热融化, 通过带有一个微细喷嘴的喷头挤喷出来。喷头沿零件截 面轮廓和填充轨迹运动,挤出的材料迅速固化并与周围 材料粘结,层层堆积而成。
主要适用于模具行业新产品开发和医疗、考古等基 于数字成像技术的三维实体模型制造。
FDM工艺由美国学者Dr.Scott Crump于1988年研制 成功,并由美国Stratasys公司推出商品化的机器。1993 年开发第一台FDM1650机型后,先后推出FDM2000、 FDM3000、FDM8000等。
快速成形制造技术

一、快速成形的基本原理
快速成形是一种基于离散/堆积成形思想的新型成
形技术,是将计算机设计产生的实体模型,由层层
堆积的方式,以快速、自动化的流程制作出来。
所有PR制造的本质:模型离散与层片制作步骤
1、通过三维CAD软件建立物理实体的三维CAD数字模 型; 2、按照一定的准则将该模型离散为一系列有序的单元, 通常在Z向将其按一定的厚度 进行离散,使原来的三维实体模型 离散为一系列的层片模型; 3、根据每个层片的轮廓信息,加入 加工参数,生成NC代码; 4、由快速成形机制造出一系列层片 并将它们连接起来,得到一个三维 物体。
(四)、快速成形技术的应用
1、新产品开发过程中的设计验证与功能验证
PR技术可快速地将产品设计模型转换成实物或零件, 这样可方便地验证设计人员的设计思想和产品结构的合 理性、可装配性、美观性,发现设计问题可及时修改。 2、可制造性、可装配性检验和供货询价、市场宣传 对有限空间的复杂系统,如汽车、卫星、导弹的可 制造性和可装配性用PR方法进行检验和设计,将大大降 低此类系统的设计制造难度,对于难以确定的复杂零件, 可以用PR技术进行试生产以确定最佳的合理的工艺。此 外,PR原型还是产品从设计到商品化各个环节中进行交 流的有效手段。比如为客户提供产品样件,进行市场宣 传等。
紫外激光 器 成形零件 光敏树脂 刮平 器 液面 升降台 Z
立体印刷的工 艺原理
(2)叠层实体制造LOM(Laminated Object Manufacturing) 通过CO2 激光切割很薄的纸、塑 料薄膜、金属薄带等逐层叠加堆积成形。
成形过程:根据CAD模型各层 切片的平面几何信息驱动激光 头,对涂覆有热敏胶的纤维纸 (厚度0.1mm或0.2mm)进行 分层实体切割;随后工作台下 降一定高度,送进机构又将新 的一层材料铺上并用热压滚筒 压,使其紧粘在已经成形的基 体上,激光头再次进行切割运 动切除第二层平面轮廓;如此 重复直至整个三维零件制作完 成。
- 1、下载文档前请自行甄别文档内容的完整性,平台不提供额外的编辑、内容补充、找答案等附加服务。
- 2、"仅部分预览"的文档,不可在线预览部分如存在完整性等问题,可反馈申请退款(可完整预览的文档不适用该条件!)。
- 3、如文档侵犯您的权益,请联系客服反馈,我们会尽快为您处理(人工客服工作时间:9:00-18:30)。
快速成形技术(RapidPrototyping,简称RP)是二十世纪八十年代末九十年代初兴起并迅速发展起来的新的先进制造技术.是由CAD模型直接驱动的快速制造任意复杂形状三维物理实体的技术总称,其基本过程是:首先设计出所需零件的计算机三维模型(数字模型、CAD模型),然后根据工艺要求,按照一定的规律将该模型离散为一系列有序的单元,通常在Z向将其按一定厚度进行离散(习惯称为分层),把原来的三维CAD 模型变成一系列的层片;再根据每个层片的轮廓信息,输入加工参数,自动生成数控代码;最后由成形机成形一系列层片并自动将它们联接起来,得到一个三维物理实体。
目录[隐藏]∙1 原理∙2 工艺过程∙3 特征∙4 分类∙5 应用∙6 产品展示∙7 相关词条∙8 参考文献快速成型技术原理快速成型技术(RP)的成型原理是基于离散-叠加原理而实现快速加工原型或零件.这里所说的快速加工原型是指能代表一切性质和功能的实验件,一般数量较少,常用来在新产品试制时作评价之用.而这里所说的快速成型零件是指最终产品,已经具有最佳的特性,功能和经济性.快速成型技术工艺过程l)产品三维模型的构建。
由于RP系统是由三维CAD模型直接驱动,因此首先要构建所加工工件的快速成型技术三维CAD模型。
该三维CAD模型可以利用计算机辅助设计软件(如Pro/E,I-DEAS,SolidWorks,UG等)直接构建,也可以将已有产品的二维图样进行转换而形成三维模型,或对产品实体进行激光扫描、CT断层扫描,得到点云数据,然后利用反求工程的方法来构造三维模型。
2)三维模型的近似处理。
由于产品往往有一些不规则的自由曲面,加工前要对模型进行近似处理,以方便后续的数据处理工作。
由于STL格式文件格式简单、实用,目前已经成为快速成型领域的准标准接口文件。
它是用一系列的小三角形平面来逼近原来的模型,每个小三角形用3个顶点坐标和一个法向量来描述,三角形的大小可以根据精度要求进行选择。
STL 文件有二进制码和ASCll码两种输出形式,二进制码输出形式所占的空间比ASCII码输出形式的文件所占用的空间小得多,但ASCII码输出形式可以阅读和检查。
典型的CAD软件都带有转换和输出STL格式文件的功能。
3)三维模型的切片处理。
根据被加工模型的特征选择合适的加工方向,在成型高度方向上用一系列一定间隔的平面切割近似后的模型,以便提取截面的轮廓信息。
间隔一般取0.05mm~0.5mm,常用0.1mm。
间隔越小,成型精度越高,但成型时间也越长,效率就越低,反之则精度低,但效率高。
4)成型加工。
根据切片处理的截面轮廓,在计算机控制下,相应的成型头(激光头或喷头)按各截面轮廓信息做扫描运动,在工作台上一层一层地堆积材料,然后将各层相粘结,最终得到原型产品。
5)成型零件的后处理。
从成型系统里取出成型件,进行打磨、抛光、涂挂,或放在高温炉中进行后烧结,进一步提高其强度。
快速成型技术特征快速成型技术(RapidPrototyping&Manufacturing,缩写为RP)其特点是可以不需机加工设备或者模快速成型技术即可快速制造形l)可以制造任意复杂的三维几何实体。
由于采用离散/堆积成型的原理.它将一个十分复杂的三维制造过程简化为二维过程的叠加,可实现对任意复杂形状零件的加工。
越是复杂的零件越能显示出RP技术的优越性此外,RP技术特别适合于复杂型腔、复杂型面等传统方法难以制造甚至无法制造的零件。
2)快速性。
通过对一个CAD模型的修改或重组就可获得一个新零件的设计和加工信息。
从几个小时到几十个小时就可制造出零件,具有快速制造的突出特点。
3)高度柔性。
无需任何专用夹具或工具即可完成复杂的制造过程,快速制造工模具、原型或零件。
4)快速成型技术实现了机械工程学科多年来追求的两大先进目标.即材料的提取(气、液固相)过程与制造过程一体化和设计(CAD)与制造(CAM)一体化。
5)与反求工程(Reverse Engineering)、CAD技术、网络技术、虚拟现实等相结合,成为产品决速开发的有力工具。
快速成型技术分类快速成型技术根据成型方法可分为两类:基于激光及其他光源的成型技术(LaserTechnology),例如:光固化成型(SLA)、分层实体制造(LOM)、选域激光粉末烧结(SLS)、形状沉积成型(SDM)等;基于喷射的成型技术(JettingTechnoloy),例如:熔融沉积成型(FDM)、三维印刷(3DP)、多相喷射沉积(MJD)。
下面对其中比较成熟的工艺作简单的介绍。
SLA技术是基于液态光敏树脂的光聚合原理工作的。
这种液态材料在一定波长和强度的紫外光照射下能迅速发生光聚合反应,分子量急剧增大,材料也就从液态转变成固态。
SLA原理SLA工作原理:液槽中盛满液态光固化树脂激光束在偏转镜作用下,能在液态表而上扫描,扫描的轨迹及光线的有无均由计算机控制,光点打到的地方,液体就固化。
成型开始时,工作平台在液面下一个确定的深度.聚焦后的光斑在液面上按计算机的指令逐点扫描,即逐点固化。
当一层扫描完成后.未被照射的地方仍是液态树脂。
然后升降台带动平台下降一层高度,已成型的层面上又布满一层树脂,刮板将粘度较大的树脂液面刮平,然后再进行下一层的扫描,新周化的一层牢周地粘在前一层上,如此重复直到整个零件制造完毕,得到一个三维实体模型。
SLA方法是目前快速成型技术领域中研究得最多的方法.也是技术上最为成熟的方法。
SLA工艺成型的零件精度较高,加工精度一般可达到0.1mm,原材料利用率近100%。
但这种方法也有白身的局限性,比如需要支撑、树脂收缩导致精度下降、光固化树脂有一定的毒性等。
优点:(1)成型过程自动化程度高(2)尺寸精度高。
(3)表面质量优良。
(4)可以制作结构十分复杂的模型。
(5)可以直接制作面向熔模精密铸造的具有中空结构的消失型。
缺点:(1)成型过程中伴随着物理和化学变化,所以制件较易弯曲,需要支撑,(2)设备运转及维护成本较高。
(3)可使用的材料种类较少。
(4)液态树脂具有气味和毒性,并且需要避光保护,以防止提前发生聚合反应,选择时有局限性。
(5)需要二次固化。
(6)液态树脂同化后的性能尚不如常用的工业塑料,一般较脆、易断裂,不使进行机加工。
LOM(LaminatedObjectManufacturing,LOM)工艺LOM工艺称叠层实体制造或分层实体制造,由美国Helisys公司的MichaelFeygin于1986年研制成功。
LOM工艺采用薄片材料,如纸、塑料薄膜等。
片材表面事先涂覆上一层热熔胶。
加工时,热压辊热压片材,使之与下面已成型的工件粘接。
用CO2激光器在刚粘接的新层上切割出零件截面轮廓和工件外框,并在截面轮廓与外框之间多余的区域内切割出上下对齐的网格。
激光切割完成后,工作台带动已成型的工件下降,与带状片材分离。
供料机构转动收料轴和供料轴,带动料带移动,使新层移到加工区域。
工作合上升到加工平面,热压辊热压,工件的层数增加一层,高度增加一个料厚。
再在新层上切割截面轮廓。
如此反复直至零件的所有截面粘接、切割完。
最后,去除切碎的多余部分,得到分层制造的实体零件。
LOM工艺只需在片材上切割出零件截面的轮廓,而不用扫描整个截面。
因此成型厚壁零件的速度较快,易于制造大型零件。
工艺过程中不存在材料相变,因此不易引起翘曲变形。
工件外框与截面轮廓之间的多余材料在加工中起到了支撑作用,所以LOM工艺无需加支撑。
缺点是材料浪费严重,表面质量差。
SLS(SelectiveLaserSintering)工艺SLS工艺称为选域激光烧结,由美国德克萨斯大学奥斯汀分校的C.R.Dechard于1989年研制成功。
SLS工艺是利用粉末状材料成型的。
SLS原理其原理是将材料粉末铺洒在已成型零件的上表面,并刮平,用高强度的CO2激光器在刚铺的新层上扫描出零件截面,材料粉末在高强度的激光照射下被烧结在一起,得到零件的截面,并与下面已成型的部分连接。
当一层截面烧结完后,铺上新的一层材料粉末,有选择地烧结下层截面。
烧结完成后去掉多余的粉末,再进行打磨、烘干等处理得到零件。
优点:(1)精度高。
制件在X 和y方向的精度可达±0.1~0.2mm,Z方向的精度可达±0.2~0.3mm。
(2)实体制造中无需设计和制作支撑,所以制作效率高、速度快、成本低。
缺点:(1)特别是薄壁件的抗拉强度和弹性不够好;(2)易吸湿膨胀,成型后应尽快进行表面防潮处理;(3)件表面有台阶纹,其高度等于材料的厚度(通常为0.1mm左右)SLS工艺的特点是材料适应面广,不仅能制造塑料零件,还能制造陶瓷、蜡等材料的零件,特别是可以制造金属零件。
这使SLS工艺颇具吸引力。
SLS工艺无需加支撑,因为没有烧结的粉末起到了支撑的作用。
优点是(1)可采用多种材料。
(2)制造工艺比较简单。
(3)高精度。
依赖于使用的材料种类和粒径、产品的几何形状和复杂程度,该工艺一般能够达到工件整体范围内±(0.05~2.5)mm的公差。
当粉末粒径为0.1mm以下时,成型后的原型精度可达±l%。
(4)材料利用率高,价格便宜,成本低。
(5)无需支撑结构。
3DP(ThreeDimensionPrinting)工艺三维印刷工艺是美国麻省理工学院E-manualSachs等人研制的。
已被美国的Soligen公司以DSPC(DirectShellProductionCasting)名义商品化,用以制造铸造用的陶瓷壳体和型芯。
3DP工艺与SLS工艺类似,采用粉末材料成型,如陶瓷粉末、金属粉末。
所不同的是材料粉末不是通过烧结连结起来的,而是通过喷头用粘结剂(如硅胶)将零件的截面“印刷”在材料粉来上面。
3DP的原理如图所示,左面是3DP原理储粉筒,材料被放置在快速成型过程的起始位置。
零件是由粉末和胶水组成的。
右面就是部件制作的地方。
在工作平台的里面是一个平整的金属盘,上面一层层微细的粉末由滚筒铺开,然后在制作过程中由打印头喷出粘着剂进行粘结.其优点:(1)速度快,(2)是和制造复杂形状的零件,(3)可用与制造复合材料或非均匀材料的零件,(4)可是和制造小批量零件,(5)无污染,是绿色化的办公室设计。
缺点:(1)零件精度差,表面粗糙度差(2)零件易变性甚至出现裂纹。
FDM(FusedDepostionModeling)工艺熔融沉积制造(FDM)工艺由美国学者ScottCrump于1988年研制成功。
FDM的材料一般是热塑性材料,如蜡、ABS、尼龙等。
以丝状供料。
材料在喷头内被加热熔化。
喷头沿零件截面轮廓和填充轨迹运动,同时将熔化的材料挤出,材料迅速凝固,并与周围的材料凝结。
FDM工艺原理如图所示。
FDM原理与上述工艺不同,FDM不采用激光,成型材料为丝状的高分子聚合物;在开始成型之前,丝状材料需要先在液化管中被加热到略高于其软化点以将其熔化。