最新整理焊接安全与检验.docx
焊接质量控制和检验

焊接质量控制和检验焊接质量控制和检验1. 引言焊接是一种常用的连接材料的方法,而焊接质量的控制和检验对于确保焊接连接的强度和可靠性至关重要。
本旨在介绍焊接质量控制和检验的相关内容,包括焊接前的准备工作、焊接过程中的控制要点、以及焊接后的检验方法。
2. 焊接前的准备工作2.1 焊接程序的制定和审核:根据焊接工艺规程,制定适合的焊接程序,并进行审核,确保焊接参数符合要求。
2.2 焊接材料的选用和检查:选择适合的焊接材料,并对材料进行质量检查,确保材料的质量符合要求。
2.3 焊接设备的检验和校准:检查焊接设备的状态,确保设备正常工作,并进行校准,以保证焊接质量的稳定性。
3. 焊接过程中的控制要点3.1 焊接操作人员的培训和资质要求:培训焊接操作人员,确保其具备必要的知识和技能,并授权其进行焊接操作。
3.2 焊接工艺参数的控制:严格控制焊接工艺参数,包括焊接电流、电压、焊接速度等,确保焊接质量稳定可靠。
3.3 焊接环境的控制:保持焊接环境的清洁,避免有害气体和杂质对焊接质量的影响。
3.4 焊接电极和焊丝的使用和管理:正确选择和使用焊接电极和焊丝,并对其进行管理,确保其质量可靠。
3.5 焊接过程的监控和记录:监控焊接过程的关键参数,记录焊接参数和焊接质量,以便进行后续的检验和分析。
4. 焊接后的检验方法4.1 可视检验:对焊缝进行可视检查,检查焊缝的形状、尺寸、缺陷等。
4.2 磁粉检验:利用磁粉检验方法检查焊缝表面的裂纹和缺陷。
4.3 超声波检验:利用超声波检验方法检查焊缝内部的缺陷,如气孔、夹杂物等。
4.4 X射线检验:利用X射线检验方法检查焊接接头的质量,发现焊缝内部的缺陷。
4.5 射线照像检验:利用射线照像检验方法对焊接接头进行全面的检查和评估。
5. 扩展内容1、本所涉及附件如下:附件1:焊接工艺规程附件2:焊接材料检验报告附件3:焊接设备校准证书附件4:焊接操作人员培训记录附件5:焊接工艺参数记录表附件6:可视检验记录表附件7:磁粉检验报告附件8:超声波检验报告附件9:X射线检验报告附件10:射线照像检验报告2、本所涉及的法律名词及注释:1)焊接工艺规程:指导焊接操作和控制焊接质量的文件。
焊接安全与检验规程
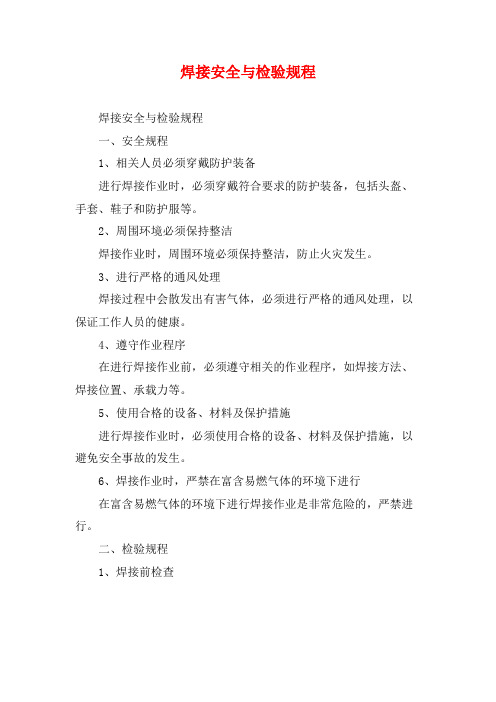
焊接安全与检验规程焊接安全与检验规程一、安全规程1、相关人员必须穿戴防护装备进行焊接作业时,必须穿戴符合要求的防护装备,包括头盔、手套、鞋子和防护服等。
2、周围环境必须保持整洁焊接作业时,周围环境必须保持整洁,防止火灾发生。
3、进行严格的通风处理焊接过程中会散发出有害气体,必须进行严格的通风处理,以保证工作人员的健康。
4、遵守作业程序在进行焊接作业前,必须遵守相关的作业程序,如焊接方法、焊接位置、承载力等。
5、使用合格的设备、材料及保护措施进行焊接作业时,必须使用合格的设备、材料及保护措施,以避免安全事故的发生。
6、焊接作业时,严禁在富含易燃气体的环境下进行在富含易燃气体的环境下进行焊接作业是非常危险的,严禁进行。
二、检验规程1、焊接前检查在进行焊接作业前,必须对焊接对象进行检查,检查焊接部位是否有缺陷、是否干净等。
同时,要检查焊接设备的工作状态是否正常,如喷枪、电焊机等。
2、焊接时检查在进行焊接作业时,要通过来回移动的方式检查焊接的效果,并要注意电极的使用状况,以避免出现质量问题。
3、焊接后检查在完成焊接作业后,必须进行焊缝的检查,包括检查焊缝是否合格、焊接强度是否达标、是否有裂纹等。
同时,也要对整个设备进行综合检查,以确定是否符合要求。
4、焊接质量评定标准在进行焊接质量评定时,必须按照相关标准进行,例如焊接强度、焊接缺陷、泄漏等等。
并且,在进行焊接检验时,也要检查其相关的文件记录是否完整。
三、结论从以上内容可以看出,焊接安全与检验规程是非常重要的,它能够保证焊接作业的质量,避免安全事故的发生。
因此,在进行焊接作业时,必须遵守相关规程,以确保焊接质量。
电焊条检验报告docx(一)2024

电焊条检验报告docx(一)引言概述:本文档旨在对电焊条的检验结果进行报告,通过对电焊条的多个方面进行全面测试和评估,以确保其质量和性能达到相关标准和要求。
正文:一、外观检验1. 检查电焊条表面是否有明显的锈蚀、凹陷或划痕2. 观察电焊条的外观颜色是否均匀一致3. 检查电焊条的粗糙度是否符合标准要求4. 检测电焊条是否有明显的弯曲或变形现象5. 确定电焊条的长度和直径是否符合规定的尺寸范围二、化学成分检验1. 采用化学分析仪器测试电焊条的主要成分含量2. 检测电焊条中金属材料的含量是否符合标准要求3. 确认电焊条中可能存在的有害物质是否超出安全限值4. 分析电焊条是否符合相关标准对成分比例的要求5. 对电焊条的成分进行定期监测,以确保生产质量的一致性三、力学性能检验1. 测试电焊条的抗拉强度和屈服强度是否符合标准值2. 检测电焊条的延伸性和硬度是否满足要求3. 确定电焊条的冲击韧性和静态弯曲强度是否达到标准4. 进行电焊条的应力松弛试验,评估其抗应力松弛性能5. 检验电焊条的金属结构和晶体缺陷情况,以评估其力学性能和可靠性四、焊接性能检验1. 进行电焊条的焊接试验,评估其引弧性和稳定性2. 测试电焊条的电弧熔化性能和焊缝形成质量3. 检测电焊条焊缝的硬度和抗裂性能是否符合标准4. 对电焊条进行热影响试验,评估其受热影响区(HAZ)的性能5. 对焊接材料进行环境适应性试验,评估其在不同工况下的焊接性能和稳定性五、包装和标识检验1. 检查电焊条的包装是否完好无损2. 确保电焊条的包装标识是否清晰可辨,包括产品型号、批号、规格等信息3. 检验包装是否符合运输和存储的要求4. 对电焊条的包装进行质量评估,防止在运输过程中损坏5. 确认电焊条的标识是否与产品实际性能一致总结:通过对电焊条进行外观检验、化学成分检验、力学性能检验,焊接性能检验,以及包装和标识检验,我们可以全面评估电焊条的质量和性能。
这些测试结果可以有效指导电焊条的选择和使用,确保焊接过程的安全和质量。
钢结构焊接安全规范与质量检验

钢结构焊接安全规范与质量检验钢结构焊接是建筑领域中常见的连接方式,它能够提供坚固的结构支撑和抵御外力的作用。
为了确保钢结构焊接的安全性和质量可靠性,制定了一系列的安全规范和质量检验标准,本文将对相关内容进行探讨。
1. 标准规范焊接是一项技术活动,需要严格按照相应的标准规范进行操作,以确保作业人员和建筑结构的安全。
下面是一些常见的焊接安全规范:(1)人员培训和认证:所有从事焊接作业的人员都应接受系统的培训课程,并通过相应的考试合格后方可上岗。
(2)焊接设备的安全:焊接设备应符合国家标准,工作状态稳定,所有接地装置应完好可靠。
(3)防护措施:在焊接现场,应配备适当的防护设备,如防火布、防护眼镜、手套等,以减少工人受伤的风险。
(4)通风系统:焊接作业产生大量有害气体和烟尘,应配置有效的通风系统,确保作业人员的健康。
2. 质量检验钢结构焊接完成后,需要进行质量检验,以确保焊缝的可靠性和整体结构的稳定性。
以下是一些常见的质量检验方法:(1)目测检验:焊接完成后,首先进行目测检验,通过观察焊缝表面的平整度、边缘是否完整等来评估焊接质量。
(2)超声波检测:利用超声波技术对焊缝进行检测,可以检测焊缝中存在的缺陷或裂纹,确保焊接质量。
(3)磁粉检测:通过在焊缝表面喷撒磁粉,利用磁化技术检测焊缝中是否存在裂纹或其他缺陷。
(4)拉伸试验:钢结构焊接后,可以进行拉伸试验,测试焊缝的强度和可靠性,确保其能够承受正常的荷载。
3. 潜在风险与预防措施在钢结构焊接过程中,存在一些潜在的风险,及时采取预防措施可以降低事故的发生概率。
(1)火灾风险:焊接作业会产生明火和火花,易引发火灾。
应保持作业现场干燥,定期清理焊接区域的可燃物,配备灭火器材。
(2)电击风险:焊接过程中使用的电焊机产生高电压,操作人员应穿戴好防护用具,并确保焊接设备的接地良好。
(3)有害气体风险:焊接过程中产生一些有害气体,应配备适当的通风设备,并加强作业人员的防护意识。
《焊接检验准则》word版

1 目的规定焊接产品表面质量、配合、焊接质量、扭矩的检验准则,确保产品满足顾客的要求。
2 适用范围适用于焊接产品的质量认可。
3 定义无4 责任生产部门、质量保证部负责按照本准则对焊接产品进行检验。
5 规定5.1 焊接产品检验区域划分。
5.2 焊接产品焊接表面质量的检验方法和标准5.2.1点焊表面质量检验方法和标准5.2.1.1 点焊缺陷数量的评价见下表1(当规定点焊数量是5个或更少时,不允许出现缺陷点焊,然而当焊点数量大于等于6个时,设计中应根据表1允许有一定的焊点缺陷。
)表1最小有效焊点数设计图中规定的焊点数最小的有效焊点数最大应用焊点数1-5n n6-10n-1n+111-20n-2n+221-30n-3n+331-40n-4n+441+n-12%n+12%n为工程设计图中规定的实际焊点数;焊点数为一次点焊工序中必须的数量。
5.2.1.2点焊质量评价见下表缺陷名称缺陷说明评定结论图示漏焊少于工艺要求的焊点数量不允许,必须返工(按原工艺要求补焊)无烧穿焊点表面有穿孔现象不允许,必须返工(在不影响表面质量的情况下按原工艺返工,或选择其他补焊方式,如锡补、CO2补等)位置半点焊不允许,超过要求焊点数的10%时必须返工(按原工艺要求补焊)焊点间距不均匀具体评价见5.2.1.3飞溅焊点边毛刺、凸起等焊接产品可见部分不允许有焊接飞溅;其它不可见部分允许有轻微焊接飞溅,但不能破坏螺纹,不能影响下道工序略凹陷焊点压痕太深具体评价见5.3.2.3倾斜/不平整压痕形状不均匀造成母材倾斜、不平整倾斜角度大于30°不允许,必须返工板材厚度比t v0.5-0.6>0.6-0.8>0.8-1.0>1.0-1.1>1.1-1.2>1.2-1.5最小点距e101215181824最小边缘距离V5 5.5 6.5778板材厚度比t v>1.6-2.0>2.0-2.5>2.5-3.0>3.0-3.5>3.5-3.8>3.8-4.0最小点距e273645546363最小边缘距离V910111213132CO2保护焊的表面质量评价主要是对焊缝外观的评价,看是否焊缝均匀,是否有假焊、飞溅、焊渣、裂纹、焊穿、缩孔、咬边等缺陷,以及焊缝的数量、长度及位置是否符合工艺要求。
焊接、切割后的安全检查范文(二篇)
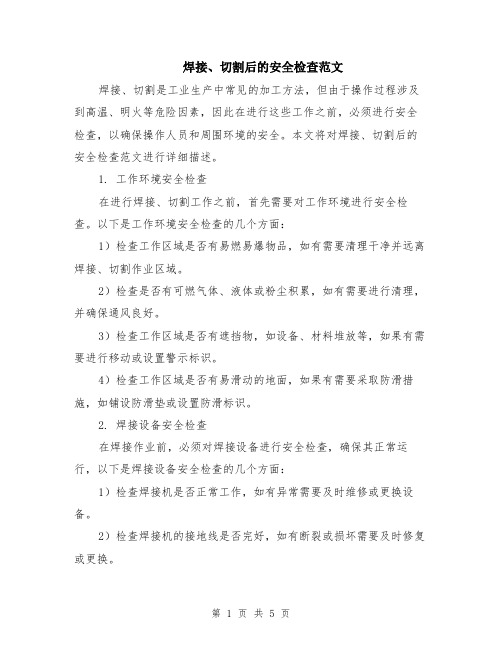
焊接、切割后的安全检查范文焊接、切割是工业生产中常见的加工方法,但由于操作过程涉及到高温、明火等危险因素,因此在进行这些工作之前,必须进行安全检查,以确保操作人员和周围环境的安全。
本文将对焊接、切割后的安全检查范文进行详细描述。
1. 工作环境安全检查在进行焊接、切割工作之前,首先需要对工作环境进行安全检查。
以下是工作环境安全检查的几个方面:1)检查工作区域是否有易燃易爆物品,如有需要清理干净并远离焊接、切割作业区域。
2)检查是否有可燃气体、液体或粉尘积累,如有需要进行清理,并确保通风良好。
3)检查工作区域是否有遮挡物,如设备、材料堆放等,如果有需要进行移动或设置警示标识。
4)检查工作区域是否有易滑动的地面,如果有需要采取防滑措施,如铺设防滑垫或设置防滑标识。
2. 焊接设备安全检查在焊接作业前,必须对焊接设备进行安全检查,确保其正常运行,以下是焊接设备安全检查的几个方面:1)检查焊接机是否正常工作,如有异常需要及时维修或更换设备。
2)检查焊接机的接地线是否完好,如有断裂或损坏需要及时修复或更换。
3)检查焊接机的通风系统是否正常运行,如有故障需要及时维修。
4)检查焊接机的电源线是否完好,如有破损或裸露需要进行修复或更换。
3. 个人防护安全检查在进行焊接、切割作业之前,操作人员必须正确佩戴个人防护设备,以下是个人防护安全检查的几个方面:1)检查焊工是否佩戴防护面具,确保能够有效遮挡高温辐射和飞溅物。
2)检查焊工是否穿戴防火服和防火手套,确保能够有效抵御高温烧伤。
3)检查焊工是否戴上防护眼镜,确保能够防止眼部受伤。
4)检查焊工是否戴上防护耳塞或耳罩,确保能够防止噪音对听力的损害。
4. 防火安全检查在进行焊接、切割作业时,需要做好防火安全工作,以下是防火安全检查的几个方面:1)检查焊接、切割作业区域是否设置了灭火器,确保能够及时扑灭起火。
2)检查焊接、切割作业区域是否设置了防火布,并且是否正确使用。
3)检查起重机械、吊装工具等设备是否符合安全要求,并且是否有防火措施。
最新整理在密闭空间内进行焊接或切割的安全注意事项.docx
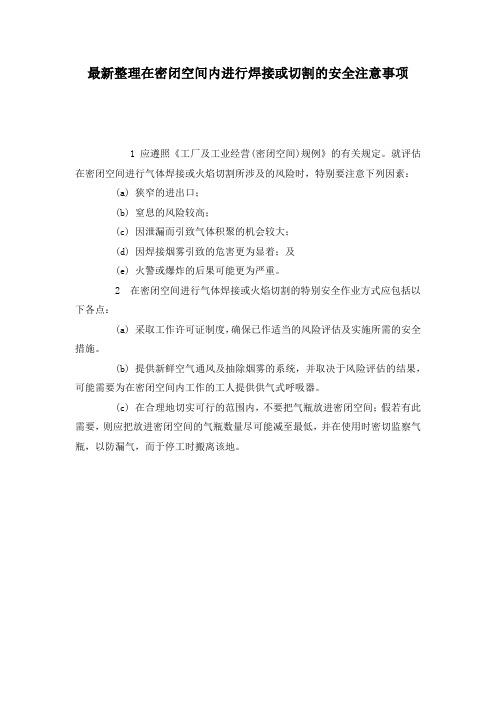
最新整理在密闭空间内进行焊接或切割的安全注意事项
1 应遵照《工厂及工业经营(密闭空间)规例》的有关规定。
就评估在密闭空间进行气体焊接或火焰切割所涉及的风险时,特别要注意下列因素:
(a) 狭窄的进出口;
(b) 窒息的风险较高;
(c) 因泄漏而引致气体积聚的机会较大;
(d) 因焊接烟雾引致的危害更为显着;及
(e) 火警或爆炸的后果可能更为严重。
2 在密闭空间进行气体焊接或火焰切割的特别安全作业方式应包括以下各点:
(a) 采取工作许可证制度,确保已作适当的风险评估及实施所需的安全措施。
(b) 提供新鲜空气通风及抽除烟雾的系统,并取决于风险评估的结果,可能需要为在密闭空间内工作的工人提供供气式呼吸器。
(c) 在合理地切实可行的范围内,不要把气瓶放进密闭空间;假若有此需要,则应把放进密闭空间的气瓶数量尽可能减至最低,并在使用时密切监察气瓶,以防漏气,而于停工时搬离该地。
焊接检验整理

二、焊接缺陷的分类
✓ 第一类 裂纹 ✓ 第二类 孔穴 ✓ 第三类 固体夹杂 ✓ 第四类 未熔合和未焊透 ✓ 第五类 形状缺陷 ✓ 第六类 其它缺陷
2-2 焊接缺陷的特征及分布
一、焊接裂纹
焊接裂纹是指金属在焊接应力及其它致脆因 素共同作用下,焊接接头中局部地区金属原子 结合力遭到破坏而形成的新界面所产生的缝隙 。具有尖锐的缺口和长宽比大的特征,是焊接 结构(件)中最危险的缺陷。
✓液体和气体介质不能承受切应力,只有固体介质能够承受切应 力,因而横波只能在固体介质中传播,不能在液体和气体介质 中传播
返回
超声波传播中的反射、折射和透射
超声波在无限大的媒质中传播仅在理论上是可能的,实 际上,任何媒质总有一个边界,超声波在非均匀性组织 内传播或从一种组织传播到另一种组织,由于组织声阻 抗不同,在声阻抗改变的分界面上便产生了反射、折射 和透射现象。
返回
磁力检测分类
➢磁力检测是通过对铁磁材料进行磁化所产生的漏磁场来发 现其表面或近表面缺陷的无损检测方法。 ➢磁力检测分类
(1)磁粉检测法:利用磁粉的聚集显示铁磁性材料及其工 件表面和近表面缺陷的无损检测方法称为磁粉检测法。 ✓ 在磁化后的工件表面撒上磁粉,磁粉粒子便会吸附在缺 陷区域,显示出缺陷的位置、磁痕的形状和大小。 ✓ 磁粉有干式粉末和悬乳液类型的湿式粉末。 ✓ 磁粉法可用于任何形状的被检测件,但不能测出缺陷沿 板厚方向的尺寸。 ✓ 磁粉法提供的缺陷分布和数量是直观的,并且可以用光 电式照相法将其摄制下来。应用广泛。
无损检测 的目的
无损检测的目的
质量管理 在役检测 质量鉴定
对原材料、零部件提供质量控制,如控制冶金 质量、加工质量、组织状态、缺陷的大小、方 位与分布等。将信息反馈到设计与工艺部门, 促使其改进设计与制造工艺,从而降低成本、 提高质量和生产效率。还可用于合理控制质量
焊接质量、试验与检验标准(doc13页)完美版

焊接质量、试验与检验标准(doc13页)完美版焊接质量、试验及检验标准1.钢材试验★ GB1954-1980 镍铬奥氏体不锈钢铁素体含量测定方法★ GB6803-1986 铁素体钢的无塑性转变温度落锤试验方法★ GB2791-1982 碳素钢和低合金钢断口试验方法2.焊接性试验★ GB4675.1-1984 焊接性试验斜Y型坡口焊接裂纹试验方法★ GB4675.2-1984 焊接性试验搭接接头( CTS )焊接裂纹试验方法★ GB4675.3-1984 焊接性试验T型接头焊接裂纹试验方法★GB4675.4-1984 焊接性试验压板对接(FISCO ) 焊接裂纹试验方法★ GB4675.5-1984 焊接热影响区最高硬度试验方法★ GB9447-1988 焊接接头疲劳裂纹扩展速率试验方法★ GB2358-1980 裂纹张开位移(COD)试验方法★ GB7032-1986 T 型角焊接头弯曲试验方法★ GB9446-1988 焊接用插销冷裂纹试验方法★ GB4909.12-1985 裸电线试验方法镀层可焊性试验焊球法★ GB2424.17-1982 电工电子产品基本环境试验规程锡焊导则★ GB4074.26-1983 漆包线试验方法焊锡试验★ JB/ZQ3690 钢板可焊性试验方法★ SJ1798-1981 印制板可焊性测试方法3.力学性能试验方法★ GB2649-1989 焊接接头力学性能试验取样方法★ GB2650-1989 焊接接头冲击试验方法★ GB2651-1989 焊接接头拉伸试验方法★ GB2652-1989 焊缝及熔敷金属拉伸试验方法★ GB2653-1989 焊接接头弯曲及压扁试验方法★ GB2654-1989 焊接接头及堆焊金属硬度试验方法★ GB2655-1989 焊接接头应变时效敏感性试验方法★ GB2656-1981 焊接接头和焊缝金属的疲劳试验方法★ GB11363-1989 釺焊接头强度试验方法★ GB8619-1989 釺缝强度试验方法4. 焊机材料试验★ GB3731-1983 涂料焊条效率、金属回收率和熔敷系数的测定★ GB3965-1983 电焊条熔敷金属中扩散氢测定方法★ GB8454-1987 焊条用还原钛铁矿粉中亚铁量的测定★ GB5292.1-1985 熔炼焊剂化学分析方法重量法测定二氧化硅量★ GB5292.2-1985 熔炼焊剂化学分析方法电位滴定法测定氧化锰量★ GB292.3-1985 熔炼焊剂化学分析方法高锰酸盐光度法测定氧化锰量★GB5292.4-1985 熔炼焊剂化学分析方法EDTA容量法测定氧化铝量★ GB5292.5-1985 熔炼焊剂化学分析方法磺基水杨酸光度法测定氧化铁量★ GB5292.6-1985 熔炼焊剂化学分析方法热解法测定氧化钙量★GB5292.7-1985 熔炼焊剂及化学分析法氟氯化铅-EDTA容量法测定氟化钙量★ GB5292.8-1985 熔炼焊剂及化学分析法钼蓝光度法测定磷量★ GB5292.9-1985 熔炼焊剂及化学分析方法火焰光度法测定氧化钠、氧化钾量★ GB5292.10-1985 熔炼焊剂及化学分析法燃烧-库伦法测定碳量★ GB5292.11-1985 熔炼焊剂及化学分析法燃烧-碘量法测定流量★ GB5292.12-1985 熔炼焊剂及化学分析法EDTA容量法测定氧化钙、氧化镁量★ GB11364-1989 钎焊材料铺展性及填缝性试验方法★GB4907.1-1985 电子器件用金、银及其合金釺焊料试验方法清洁性检验方法★GB4907.2-1985 电子器件用金、银及其合金釺焊料试验方法溅散性试验方法★ JB3169-1982 喷焊合金粉末硬度力度检测★ JB3170-1982 喷焊合金粉末化学成分分析方法5.焊接检验★ GB/T12604.1-2005 无损检测术语超声检测★ GB/T12604.2-2005 无损检测术语射线检测★ GB/T12604.3-2005 无损检测术语渗透检测★ GB/T12604.4-2005 无损检测术语声发射检测★ GB/T12604.5-2005 无损检测术语磁粉检测★ GB/T12604.6-2005 无损检测术语涡流检测★ GB5618-1985 线性象质计★ GB3323-1987 钢熔化对接接头射线照相和质量分级★ GB/T12605-1990 钢管环缝熔化焊对接接头射线透照工艺和质量分级★ GB11343-1989 接触式超声斜射探伤方法★ GB11344-1989 接触式超声波脉冲回波法测厚★ GB11345-1989 钢焊缝手工超声波探伤方法和探伤结果的分级★ GB2970-1982 中厚钢板超声波探伤方法★ JB1152-1981 锅炉和钢制压力容器对接焊缝超声波探伤★ CB827-1980 船体焊缝超声波探伤★ GB10866-1989 锅炉受压元件焊接接头金相和断口检验方法★ GB11809-1989 核燃料棒焊缝金相检验★ ZBJ04005-1987 渗透探伤方法★ ZBJ04003-1987 控制渗透探伤材料质量的方法★ JB3965-1985 钢制压力容器磁粉探伤★ EJ187-1980 磁粉探伤标准★ EJ186-1980 着色探伤标准★ JB/ZQ3692 焊接熔透量的钻孔检验方法★ JB/ZQ3693 钢焊缝内部缺陷的破断试验方法★ GB11373-1989 热喷涂涂层厚度的无损检测方法★ EJ188-1980 焊缝真空盒检漏操作规程★ JB1612-1982 锅炉水压试验技术条件★ GB9251-1988 气瓶水压试验方法★ GB9252-1988 气瓶疲劳试验方法★ GB12135-1989 气瓶定期检查站技术条件★ GB12137-1989 气瓶密封性试验方法★ GB11639-1989 溶解乙炔气瓶多孔填料技术指标测定方法★ GB7446-1987 氢气检验方法★ GB4843-1984 氩气检验方法★ GB4845-1984 氮气检验方法6.焊接质量★ GB6416-1986 影响钢熔化焊接头质量的技术因素★ GB6417-1986 金属熔化焊焊缝缺陷分类及说明★ TJ12.1-1981 建筑机械焊接质量规定★ JB/ZQ3679 焊接部位的质量★ JB/ZQ3680 焊缝外观质量★ JB/TQ330-1983 通风机焊接质量检验★ CB999-1982 船体焊缝表面质量检验方法★ JB3223-1983 焊条质量管理规程7.其他★ GB8923-1983 涂装前钢材表面锈蚀等级和除锈等级★ GB1223-1975 不锈耐酸钢晶间腐蚀倾向试验方法★ GB4334.1-1984 不锈钢10%草酸浸蚀试验方法★ GB4334.2-1984 不锈钢硫酸-硫酸铁腐蚀试验方法★ GB4334.3-1984 不锈钢65%硝酸腐蚀试验方法★ GB4334.4-1984 不锈钢硝酸-氢氟酸腐蚀试验方法★ GB4334.5-1984 不锈钢硫酸-硫酸铜腐蚀试验方法★ GB4334.6-1984 不锈钢5%硫酸腐蚀试验方法★ GB4334.7-1984 不锈钢三氯化铁腐蚀方法★ GB4334.8-1984 不锈钢42%氯化镁腐蚀试验方法★ GB4334.9-1984 不锈钢点蚀电位测定法焊接技术条件、质量检验、工艺评定标准集本篇是《焊接材料资料汇编》第五篇。
电焊作业现场安全检查范文

电焊作业现场安全检查范文一、前言电焊作业是工程建设和维护过程中常见的一项操作, 但由于其涉及高温、高压和高强度的工作环境, 存在较多的安全风险。
为保障作业人员的生命安全和财产安全, 必须加强对电焊作业现场的安全检查和管理。
本文将详细介绍电焊作业现场的安全检查范文, 以供参考。
二、电焊作业现场的安全检查1.安全标识的设置是否合规电焊作业现场的安全标识设置应符合国家相关标准要求, 包括警示标志、禁止标志、指示标志等。
安全标志应醒目明显, 能够起到提醒、警示作用。
检查时需留意是否存在破损、模糊、不清晰等情况, 如有问题应及时更换、修复。
2.电焊设备及附件的检查电焊设备及附件是电焊作业的核心, 其安全工作状况直接关系到作业人员的安全。
检查时需重点关注以下几个方面: (1)电焊机是否正常工作, 是否存在损坏、老化等情况。
如有问题应及时维修或更换。
(2)电焊面具是否完好, 是否存在损坏、破裂等情况。
如有问题应及时更换。
(3)焊条是否符合要求, 是否存放在规定的地方, 是否存在变形、湿润等问题。
如有问题应及时调整。
3.电焊作业现场的整洁与卫生电焊作业现场的整洁与卫生直接关系到安全生产和作业人员的身体健康。
检查时需留意以下几个方面:(1)作业现场是否整洁, 有无杂物、垃圾堆积。
如有问题需及时清理、清理。
(2)作业现场的通风是否良好, 以防止毒气蔓延和窒息情况。
(3)作业人员是否佩戴防护设备, 如防护手套、防护面具、防护鞋等。
4.灭火设备和应急疏散通道的设置电焊作业现场安全检查范文中还应关注灭火设备和应急疏散通道的设置情况。
检查时需留意以下几点:(1)灭火器的数量、类型是否符合要求, 是否处于有效期。
(2)应急疏散通道是否畅通, 是否划定了明显的应急疏散标志。
(3)现场人员是否熟悉应急疏散路线以及动火报警的流程。
三、安全检查后的处理措施在进行电焊作业现场的安全检查后, 如发现问题应及时处理。
具体处理措施包括:1.及时修复或更换损坏的安全标识。
焊接、切割后的安全检查范文
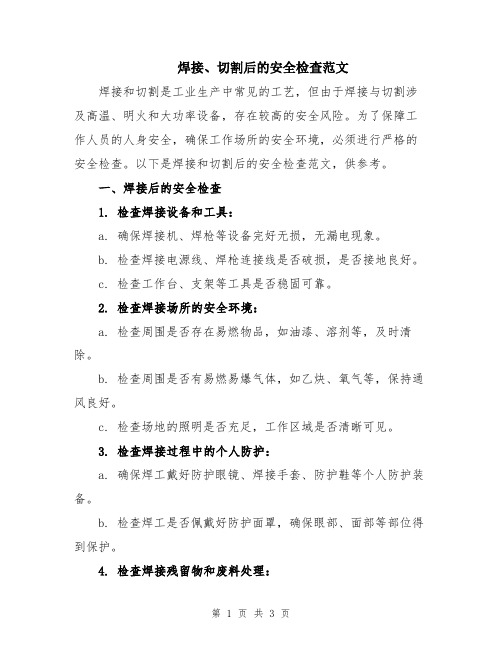
焊接、切割后的安全检查范文焊接和切割是工业生产中常见的工艺,但由于焊接与切割涉及高温、明火和大功率设备,存在较高的安全风险。
为了保障工作人员的人身安全,确保工作场所的安全环境,必须进行严格的安全检查。
以下是焊接和切割后的安全检查范文,供参考。
一、焊接后的安全检查1. 检查焊接设备和工具:a. 确保焊接机、焊枪等设备完好无损,无漏电现象。
b. 检查焊接电源线、焊枪连接线是否破损,是否接地良好。
c. 检查工作台、支架等工具是否稳固可靠。
2. 检查焊接场所的安全环境:a. 检查周围是否存在易燃物品,如油漆、溶剂等,及时清除。
b. 检查周围是否有易燃易爆气体,如乙炔、氧气等,保持通风良好。
c. 检查场地的照明是否充足,工作区域是否清晰可见。
3. 检查焊接过程中的个人防护:a. 确保焊工戴好防护眼镜、焊接手套、防护鞋等个人防护装备。
b. 检查焊工是否佩戴好防护面罩,确保眼部、面部等部位得到保护。
4. 检查焊接残留物和废料处理:a. 检查焊接完成后的焊渣、焊缝残留物等是否清理干净。
b. 检查废弃的焊接材料、残留的焊条等是否妥善处理。
5. 检查焊接质量和焊缝强度:a. 检查焊接的外观质量,是否均匀、牢固。
b. 检查焊接缺陷、气孔、裂纹等,确保焊缝的强度符合要求。
6. 检查焊接设备的外观:a. 检查焊接设备是否有明显的破损或变形,及时进行修理或更换。
二、切割后的安全检查1. 检查切割设备和刀具:a. 确保切割机、刀片等设备完好无损,无漏电现象。
b. 检查切割电源线、刀片连接线是否破损,是否接地良好。
c. 检查切割机的刀盘、切割刀片是否锋利,是否有磨损。
2. 检查切割场所的安全环境:a. 检查周围是否存在易燃物品,如油漆、溶剂等,及时清除。
b. 检查周围是否有易燃易爆气体,保持通风良好。
c. 检查场地的照明是否充足,工作区域是否清晰可见。
3. 检查切割过程中的个人防护:a. 确保操作人员戴好防护眼镜、防护手套等个人防护装备。
焊接质量检验
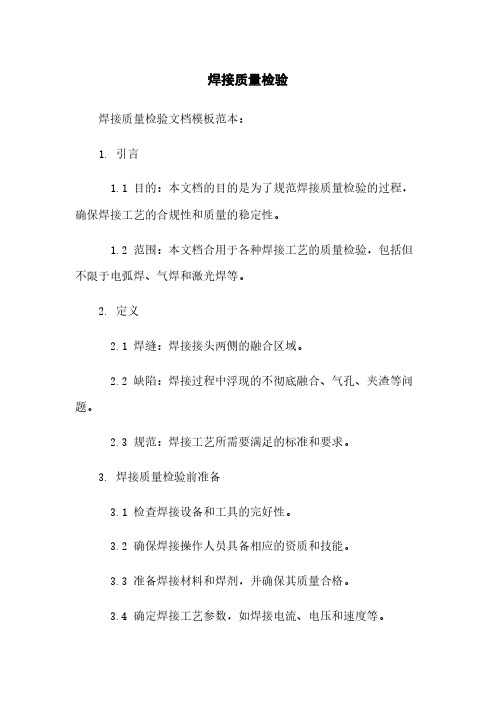
焊接质量检验焊接质量检验文档模板范本:1. 引言1.1 目的:本文档的目的是为了规范焊接质量检验的过程,确保焊接工艺的合规性和质量的稳定性。
1.2 范围:本文档合用于各种焊接工艺的质量检验,包括但不限于电弧焊、气焊和激光焊等。
2. 定义2.1 焊缝:焊接接头两侧的融合区域。
2.2 缺陷:焊接过程中浮现的不彻底融合、气孔、夹渣等问题。
2.3 规范:焊接工艺所需要满足的标准和要求。
3. 焊接质量检验前准备3.1 检查焊接设备和工具的完好性。
3.2 确保焊接操作人员具备相应的资质和技能。
3.3 准备焊接材料和焊剂,并确保其质量合格。
3.4 确定焊接工艺参数,如焊接电流、电压和速度等。
4. 焊接质量检验过程4.1 目测检验:对焊缝外观进行检查,包括焊接接头的形状、颜色和表面是否平整等。
4.2 尺寸检验:对焊接接头的尺寸进行测量,包括焊缝宽度、高度和长度等。
4.3 超声波检验:利用超声波设备检测焊接接头的内部缺陷,如夹渣、气孔和裂纹等。
4.4 X射线检验:利用X射线设备对焊接接头进行扫描,以检测内部缺陷的位置和大小。
4.5 磁粉检验:通过涂抹磁粉和施加磁场,检测焊接接头表面的裂纹和缺陷。
4.6 渗透检验:利用渗透液对焊接接头进行涂抹,以检测表面裂纹和不彻底融合等问题。
5. 检验结果与评定5.1 各项检验结果的记录和整理。
5.2 根据焊接规范对检验结果进行评定,确定焊接接头的质量等级。
5.3 如检验结果不合格,需采取相应的修复措施或者重新焊接。
6. 检验报告6.1 根据检验结果编制焊接质量检验报告。
6.2 报告内容包括焊接接头的基本信息、各项检验结果、评定等级和建议措施等。
7. 扩展内容1、本文档所涉及附件如下:- 附件1:焊接质量检验报告模板- 附件2:焊接设备维护记录表- 附件3:焊接操作人员资质证书复印件2、本文档所涉及的法律名词及注释:- 法律名词1:根据《焊接质量标准》规定,焊缝的最大允许缺陷长度为...- 法律名词2:根据《焊接人员资质管理办法》要求,焊接操作人员应具有相应的职业资格证书。
焊接质量控制与检验
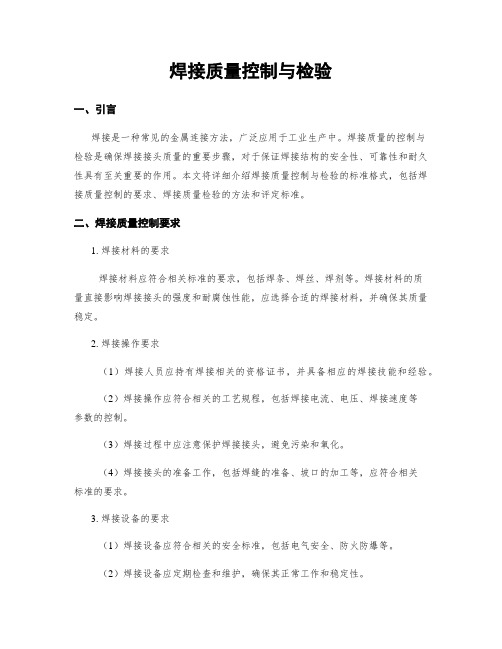
焊接质量控制与检验一、引言焊接是一种常见的金属连接方法,广泛应用于工业生产中。
焊接质量的控制与检验是确保焊接接头质量的重要步骤,对于保证焊接结构的安全性、可靠性和耐久性具有至关重要的作用。
本文将详细介绍焊接质量控制与检验的标准格式,包括焊接质量控制的要求、焊接质量检验的方法和评定标准。
二、焊接质量控制要求1. 焊接材料的要求焊接材料应符合相关标准的要求,包括焊条、焊丝、焊剂等。
焊接材料的质量直接影响焊接接头的强度和耐腐蚀性能,应选择合适的焊接材料,并确保其质量稳定。
2. 焊接操作要求(1)焊接人员应持有焊接相关的资格证书,并具备相应的焊接技能和经验。
(2)焊接操作应符合相关的工艺规程,包括焊接电流、电压、焊接速度等参数的控制。
(3)焊接过程中应注意保护焊接接头,避免污染和氧化。
(4)焊接接头的准备工作,包括焊缝的准备、坡口的加工等,应符合相关标准的要求。
3. 焊接设备的要求(1)焊接设备应符合相关的安全标准,包括电气安全、防火防爆等。
(2)焊接设备应定期检查和维护,确保其正常工作和稳定性。
(3)焊接设备的参数应符合焊接工艺规程的要求,并进行校准和记录。
三、焊接质量检验方法1. 目测检验目测检验是最常用的焊接质量检验方法之一,通过肉眼观察焊接接头的外观来评估其质量。
目测检验主要包括焊缝形状、焊接缺陷、焊接尺寸等方面的评估。
2. 放射性检测放射性检测是一种非破坏性检测方法,通过使用射线或放射性同位素来检测焊接接头内部的缺陷。
常用的放射性检测方法包括射线透视、射线摄影和射线探伤等。
3. 超声波检测超声波检测是一种非破坏性检测方法,通过使用超声波探头对焊接接头进行扫描,检测焊接接头内部的缺陷。
超声波检测可以检测到焊接接头的内部缺陷,如气孔、夹渣等。
4. 磁粉检测磁粉检测是一种非破坏性检测方法,通过在焊接接头表面涂覆磁粉,并施加磁场,通过观察磁粉的分布情况来检测焊接接头的表面和近表面缺陷。
5. 渗透检测渗透检测是一种非破坏性检测方法,通过在焊接接头表面涂覆渗透剂,并进行渗透、显像和清洗等步骤,来检测焊接接头的表面缺陷。
焊接质量、试验与检验标准(doc13页)完美版

镍铬奥氏体不锈钢铁素体含量测定方法 铁素体钢的无塑性转变温度 落锤试验方法 碳素钢和低合金钢断口试验方法 焊接性试验 斜丫型坡口焊接裂纹试验方法 焊接性试验 搭接接头( CTS )焊接裂纹试 焊接性试验 T 型接头焊接裂纹试验方法 焊接性试验 压板对接( FISCO ) 焊接裂纹试 焊接热影响区最高硬度试验方法 焊接接头疲劳裂纹扩展速率试验方法 裂纹张开位移(COD 试验方法 T 型角焊接头弯曲试验方法 焊接用插销冷裂纹试验方法 裸电线试验方法 镀层可焊性试验焊球法 电工电子产品基本环境试验规程 锡焊导则 漆包线试验方法 焊锡试验 钢板可焊性试验方法 印制板可焊性测试方法 焊接接头力学性能试验取样方法 焊接接头冲击试验方法 焊接接头拉伸试验方法 焊缝及熔敷金属拉伸试验方法焊接质量1.钢材试验★ GB1954-1980★ GB6803-1986★ GB2791-19822.焊接性试验★ GB4675.1-1984★ GB4675.2-1984验方法★ GB4675.3-1984★ GB4675.4-1984验方法★ GB4675.5-1984★ GB9447-1988★ GB2358-1980★ GB7032-1986★ GB9446-1988★ GB4909.12-1985★ GB2424.17-1982★ GB4074.26-1983★ JB/ZQ3690★ SJ1798-19813.力学性能试验方法★ GB2649-1989★ GB2650-1989 试验及检验标准焊接接头弯曲及压扁试验方法 焊接接头及堆焊金属硬度试验方法 焊接接头应变时效敏感性试验方法 焊接接头和焊缝金属的疲劳试验方法 釺焊接头强度试验方法釺缝强度试验方法涂料焊条效率、金属回收率和熔敷系数的测定 电焊条熔敷金属中扩散氢测定方法 焊条用还原钛铁矿粉中亚铁量的测定 熔炼焊剂化学分析方法 熔炼焊剂化学分析方法 熔炼焊剂化学分析方法 熔炼焊剂化学分析方法 熔炼焊剂化学分析方法 熔炼焊剂化学分析方法 熔炼焊剂及化学分析法 熔炼焊剂及化学分析法 ★ GB2653-1989★ GB2654-1989★ GB2655-1989★ GB2656-1981 ★ GB11363-1989 ★ GB8619-19894. 焊机材料试验★ GB3731-1983★ GB3965-1983★ GB8454-1987★ GB5292.1-1985 化硅量★ GB5292.2-1985 氧化锰量★ GB292.3-1985法测定氧化锰量★ GB5292.4-1985 氧化铝量★ GB5292.5-1985 法测定氧化铁量★ GB5292.6-1985 钙量★ GB5292.7-1985 量法测定氟化钙量★ GB5292.8-1985 磷量 重量法测定二氧 电位滴定法测定 高锰酸盐光度 EDTA 容量法测定 磺基水杨酸光度 热解法测定氧化 氟氯化铅-EDTA 容 钼蓝光度法测定 熔炼焊剂及化学分析方法 火焰光度法测定氧化钠、★ GB5292.10-1985 熔炼焊剂及化学分析法燃烧- 库伦法测定碳量- 碘量法测定流★ GB5292.11-1985 熔炼焊剂及化学分析法燃烧量★ GB5292.12-1985 熔炼焊剂及化学分析法EDTA容量法测定氧化钙、氧化镁量★ GB11364-1989 钎焊材料铺展性及填缝性试验方法电子器件用金、银及其合金釺焊料试验方法清洁性★ GB4907.1-1985 检验方法电子器件用金、银及其合金釺焊料试验方法溅散性★ GB4907.2-1985 试验方法★ JB3169-1982 喷焊合金粉末硬度力度检测喷焊合金粉末化学成分分析方法★ JB3170-19825. 焊接检验★ GB/T12604.1-2005 无损检测术语超声检测★ GB/T12604.2-2005 无损检测术语射线检测★ GB/T12604.3-2005 无损检测术语渗透检测★ GB/T12604.4-2005 无损检测术语声发射检测★ GB/T12604.5-2005 无损检测术语磁粉检测★ GB/T12604.6-2005 无损检测术语涡流检测★ GB5618-1985 线性象质计★ GB3323-1987 钢熔化对接接头射线照相和质量分级钢管环缝熔化焊对接接头射线透照工艺和质量★ GB/T12605-1990分级★ GB11343-1989 接触式超声斜射探伤方法★ GB11344-1989 接触式超声波脉冲回波法测厚钢焊缝手工超声波探伤方法和探伤结果的分★ GB11345-1989级★ GB2970-1982 中厚钢板超声波探伤方法锅炉和钢制压力容器对接焊缝超声波探伤 船体焊缝超声波探伤 锅炉受压元件焊接接头金相和断口检验方法 核燃料棒焊缝金相检验 渗透探伤方法 控制渗透探伤材料质量的方法钢制压力容器磁粉探伤磁粉探伤标准 着色探伤标准 焊接熔透量的钻孔检验方法 钢焊缝内部缺陷的破断试验方法 热喷涂涂层厚度的无损检测方法 焊缝真空盒检漏操作规程 锅炉水压试验技术条件 气瓶水压试验方法 气瓶疲劳试验方法 气瓶定期检查站技术条件 气瓶密封性试验方法 溶解乙炔气瓶 多孔填料技术指标测定方 氢气检验方法 氩气检验方法 氮气检验方法 ★ JB1152-1981★ CB827-1980 ★ GB10866-1989 ★ GB11809-1989 ★ ZBJ04005-1987★ ZBJ04003-1987★ JB3965-1985★ EJ187-1980★ EJ186-1980★ JB/ZQ3692★ JB/ZQ3693★ GB11373-1989★ EJ188-1980★ JB1612-1982★ GB9251-1988★ GB9252-1988★ GB12135-1989★ GB12137-1989★ GB11639-1989法★ GB7446-1987★ GB4843-1984★ GB4845-19846.焊接质量★ GB6416-1986★ GB6417-1986★ TJ12.1-1981★ JB/ZQ3679 影响钢熔化焊接头质量的技术因素 金属熔化焊焊缝缺陷分类及说明 建筑机械焊接质量规定 焊接部位的质量 焊缝外观质量★ JB/TQ330-1983 通风机焊接质量检验★ CB999-1982 船体焊缝表面质量检验方法焊条质量管理规程★ JB3223-19837.其他★ GB8923-1983 涂装前钢材表面锈蚀等级和除锈等级★ GB1223-1975 不锈耐酸钢晶间腐蚀倾向试验方法★ GB4334.1-1984 不锈钢10%草酸浸蚀试验方法★ GB4334.2-1984 不锈钢硫酸-硫酸铁腐蚀试验方法★ GB4334.3-1984 不锈钢65%硝酸腐蚀试验方法★ GB4334.4-1984 不锈钢硝酸-氢氟酸腐蚀试验方法★ GB4334.5-1984 不锈钢硫酸-硫酸铜腐蚀试验方法★ GB4334.6-1984 不锈钢5%硫酸腐蚀试验方法★ GB4334.7-1984 不锈钢三氯化铁腐蚀方法★ GB4334.8-1984 不锈钢42%氯化镁腐蚀试验方法★ GB4334.9-1984 不锈钢点蚀电位测定法焊接技术条件、质量检验、工艺评定标准集本篇是《焊接材料资料汇编》第五篇。
焊接、切割后的安全检查(2篇)

焊接、切割后的安全检查焊、割作业中的火灾爆炸事故,有些往往是工程的结尾阶段,或在焊、割作业结束后。
原因在于结尾阶段容易放松警惕,制定的各项安全措施没能自始至终地执行;还因焊、割结束后、留下的火种没有熄灭造成。
因此,认真抓好焊、割作业后的安全检查,是焊、割防火防爆全过程中不可缺少的一个重要组成部分。
一般情况下,应做好以下几项工作:1、坚持工程后期阶段的防火防爆措施。
特别要注意焊、割作业已经结束,安全设施已经撤离,结果发现某一部位还需要进行一些很细小工作量的焊、割时,绝不能麻痹大意,要坚持焊、割工作大小一个样,安全措施不落实,绝不动火焊、割。
2、各种设备、容器进行焊接后,要及时检查焊接质量是否达到要求,对漏焊、假焊等毛病应立即修补好;不要待使用时再发现上述质量问题,那时就麻烦了。
焊接过的受压设备、容器管道要经过水压或气压试验合格后,才能使用。
凡是经过焊、割或加热后的容器,要待完全冷却后才能进料。
3、焊、割作业结束后,必须及时彻底清理现场,清除遗留下来的火种。
关闭电源、气源,把焊、割炬安放在安全的地方,拿出乙炔发生器内未使用完的电石,存放进电石铁桶内,排除电石污染,并把乙炔发生器冲洗干净,加好清水,待第二天使用。
4、焊、割作业场所,往往留下不容易发现的火种,因此除了作业后要进行认真检查外,下班时要主动向警卫人员或下一班人员交代,以便加强巡逻检查。
5、焊工所穿的衣服上班后也要彻底检查一下,看是否有阴燃的情况;有一些火灾往往是由一焊工穿的衣服挂在更衣室内,经几小时阴燃后而起火的。
警卫人员要加强检查,发现有焦味等异常现象,须及时采取措施。
焊接、切割后的安全检查(2)焊接和切割是一种常见的金属加工过程,用于制造和修复各种金属制品。
然而,这些过程涉及高温和火焰,因此在进行焊接和切割之前,必须进行安全检查以确保操作员的安全。
在本文中,我们将探讨焊接和切割后的安全检查措施。
焊接和切割过程涉及高温和火焰,这可能导致火灾和爆炸。
焊接质量、试验与检验标准(doc 13页)
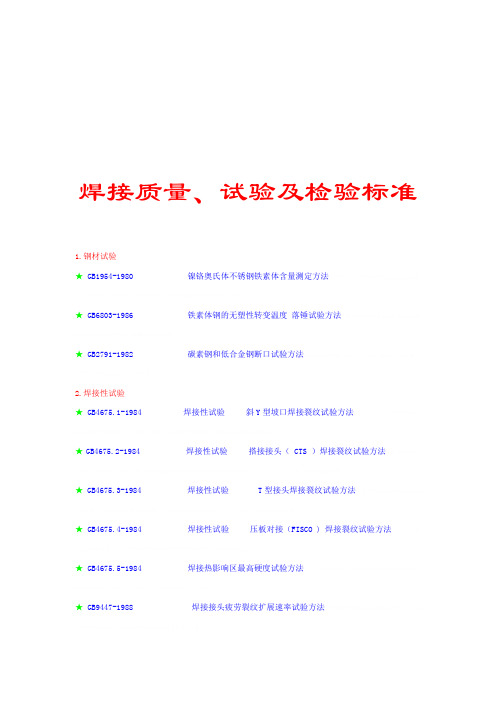
焊接质量、试验及检验标准1.钢材试验★ GB1954-1980 镍铬奥氏体不锈钢铁素体含量测定方法★ GB6803-1986 铁素体钢的无塑性转变温度落锤试验方法★ GB2791-1982 碳素钢和低合金钢断口试验方法2.焊接性试验★ GB4675.1-1984 焊接性试验斜Y型坡口焊接裂纹试验方法★GB4675.2-1984 焊接性试验搭接接头( CTS )焊接裂纹试验方法★ GB4675.3-1984 焊接性试验 T型接头焊接裂纹试验方法★ GB4675.4-1984 焊接性试验压板对接(FISCO ) 焊接裂纹试验方法★ GB4675.5-1984 焊接热影响区最高硬度试验方法★ GB9447-1988 焊接接头疲劳裂纹扩展速率试验方法★ GB2358-1980 裂纹张开位移(COD)试验方法★ GB7032-1986 T 型角焊接头弯曲试验方法★ GB9446-1988 焊接用插销冷裂纹试验方法★ GB4909.12-1985 裸电线试验方法镀层可焊性试验焊球法★ GB2424.17-1982 电工电子产品基本环境试验规程锡焊导则★ GB4074.26-1983 漆包线试验方法焊锡试验★ JB/ZQ3690 钢板可焊性试验方法★ SJ1798-1981 印制板可焊性测试方法3.力学性能试验方法★ GB2649-1989 焊接接头力学性能试验取样方法★GB2650-1989 焊接接头冲击试验方法★ GB2651-1989 焊接接头拉伸试验方法★ GB2652-1989 焊缝及熔敷金属拉伸试验方法★ GB2653-1989 焊接接头弯曲及压扁试验方法★GB2654-1989 焊接接头及堆焊金属硬度试验方法★GB2655-1989 焊接接头应变时效敏感性试验方法★ GB2656-1981 焊接接头和焊缝金属的疲劳试验方法★ GB11363-1989 釺焊接头强度试验方法★ GB8619-1989 釺缝强度试验方法4. 焊机材料试验★ GB3731-1983 涂料焊条效率、金属回收率和熔敷系数的测定★GB3965-1983 电焊条熔敷金属中扩散氢测定方法★ GB8454-1987 焊条用还原钛铁矿粉中亚铁量的测定★ GB5292.1-1985 熔炼焊剂化学分析方法重量法测定二氧化硅量★ GB5292.2-1985 熔炼焊剂化学分析方法电位滴定法测定氧化锰量★ GB292.3-1985 熔炼焊剂化学分析方法高锰酸盐光度法测定氧化锰量★ GB5292.4-1985 熔炼焊剂化学分析方法 EDTA容量法测定氧化铝量★ GB5292.5-1985 熔炼焊剂化学分析方法磺基水杨酸光度法测定氧化铁量★ GB5292.6-1985 熔炼焊剂化学分析方法热解法测定氧化钙量★GB5292.7-1985 熔炼焊剂及化学分析法氟氯化铅-EDTA容量法测定氟化钙量★ GB5292.8-1985 熔炼焊剂及化学分析法钼蓝光度法测定磷量★ GB5292.9-1985 熔炼焊剂及化学分析方法火焰光度法测定氧化钠、氧化钾量★ GB5292.10-1985 熔炼焊剂及化学分析法燃烧-库伦法测定碳量★ GB5292.11-1985 熔炼焊剂及化学分析法燃烧-碘量法测定流量★GB5292.12-1985 熔炼焊剂及化学分析法 EDTA容量法测定氧化钙、氧化镁量★ GB11364-1989 钎焊材料铺展性及填缝性试验方法★ GB4907.1-1985 电子器件用金、银及其合金釺焊料试验方法清洁性检验方法★ GB4907.2-1985 电子器件用金、银及其合金釺焊料试验方法溅散性试验方法★ JB3169-1982 喷焊合金粉末硬度力度检测★ JB3170-1982 喷焊合金粉末化学成分分析方法5.焊接检验★ GB/T12604.1-2005 无损检测术语超声检测★ GB/T12604.2-2005 无损检测术语射线检测★ GB/T12604.3-2005 无损检测术语渗透检测★ GB/T12604.4-2005 无损检测术语声发射检测★GB/T12604.5-2005 无损检测术语磁粉检测★ GB/T12604.6-2005 无损检测术语涡流检测★ GB5618-1985 线性象质计★ GB3323-1987 钢熔化对接接头射线照相和质量分级★ GB/T12605-1990 钢管环缝熔化焊对接接头射线透照工艺和质量分级★ GB11343-1989 接触式超声斜射探伤方法★ GB11344-1989 接触式超声波脉冲回波法测厚★ GB11345-1989 钢焊缝手工超声波探伤方法和探伤结果的分级★ GB2970-1982 中厚钢板超声波探伤方法★ JB1152-1981 锅炉和钢制压力容器对接焊缝超声波探伤★CB827-1980 船体焊缝超声波探伤★ GB10866-1989 锅炉受压元件焊接接头金相和断口检验方法★ GB11809-1989 核燃料棒焊缝金相检验★ZBJ04005-1987 渗透探伤方法★ ZBJ04003-1987 控制渗透探伤材料质量的方法★ JB3965-1985 钢制压力容器磁粉探伤★EJ187-1980 磁粉探伤标准★EJ186-1980 着色探伤标准★ JB/ZQ3692 焊接熔透量的钻孔检验方法★ JB/ZQ3693 钢焊缝内部缺陷的破断试验方法★GB11373-1989 热喷涂涂层厚度的无损检测方法★ EJ188-1980 焊缝真空盒检漏操作规程★JB1612-1982 锅炉水压试验技术条件★ GB9251-1988 气瓶水压试验方法★ GB9252-1988 气瓶疲劳试验方法★GB12135-1989 气瓶定期检查站技术条件★ GB12137-1989 气瓶密封性试验方法★ GB11639-1989 溶解乙炔气瓶多孔填料技术指标测定方法★ GB7446-1987 氢气检验方法★ GB4843-1984 氩气检验方法★ GB4845-1984 氮气检验方法6.焊接质量★ GB6416-1986 影响钢熔化焊接头质量的技术因素★ GB6417-1986 金属熔化焊焊缝缺陷分类及说明★ TJ12.1-1981 建筑机械焊接质量规定★ JB/ZQ3679 焊接部位的质量★ JB/ZQ3680 焊缝外观质量★ JB/TQ330-1983 通风机焊接质量检验★ CB999-1982 船体焊缝表面质量检验方法★JB3223-1983 焊条质量管理规程7.其他★ GB8923-1983 涂装前钢材表面锈蚀等级和除锈等级★ GB1223-1975 不锈耐酸钢晶间腐蚀倾向试验方法★GB4334.1-1984 不锈钢10%草酸浸蚀试验方法★ GB4334.2-1984 不锈钢硫酸-硫酸铁腐蚀试验方法★ GB4334.3-1984 不锈钢65%硝酸腐蚀试验方法★GB4334.4-1984 不锈钢硝酸-氢氟酸腐蚀试验方法★GB4334.5-1984 不锈钢硫酸-硫酸铜腐蚀试验方法★ GB4334.6-1984 不锈钢5%硫酸腐蚀试验方法★ GB4334.7-1984 不锈钢三氯化铁腐蚀方法★GB4334.8-1984 不锈钢42%氯化镁腐蚀试验方法★ GB4334.9-1984 不锈钢点蚀电位测定法焊接技术条件、质量检验、工艺评定标准集本篇是《焊接材料资料汇编》第五篇。
焊接、切割后的安全检查
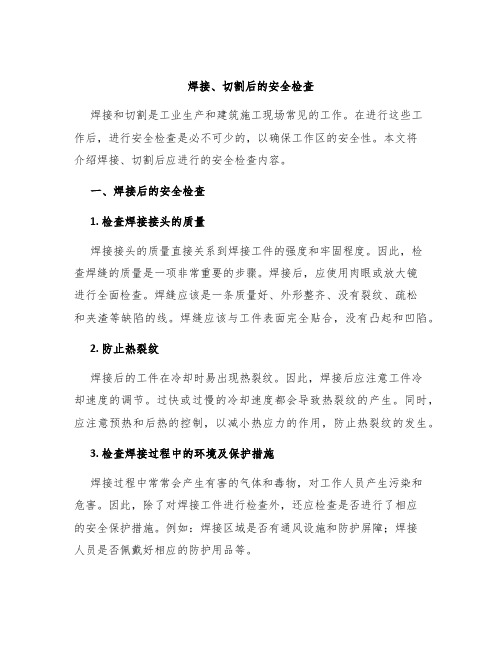
焊接、切割后的安全检查焊接和切割是工业生产和建筑施工现场常见的工作。
在进行这些工作后,进行安全检查是必不可少的,以确保工作区的安全性。
本文将介绍焊接、切割后应进行的安全检查内容。
一、焊接后的安全检查1. 检查焊接接头的质量焊接接头的质量直接关系到焊接工件的强度和牢固程度。
因此,检查焊缝的质量是一项非常重要的步骤。
焊接后,应使用肉眼或放大镜进行全面检查。
焊缝应该是一条质量好、外形整齐、没有裂纹、疏松和夹渣等缺陷的线。
焊缝应该与工件表面完全贴合,没有凸起和凹陷。
2. 防止热裂纹焊接后的工件在冷却时易出现热裂纹。
因此,焊接后应注意工件冷却速度的调节。
过快或过慢的冷却速度都会导致热裂纹的产生。
同时,应注意预热和后热的控制,以减小热应力的作用,防止热裂纹的发生。
3. 检查焊接过程中的环境及保护措施焊接过程中常常会产生有害的气体和毒物,对工作人员产生污染和危害。
因此,除了对焊接工件进行检查外,还应检查是否进行了相应的安全保护措施。
例如:焊接区域是否有通风设施和防护屏障;焊接人员是否佩戴好相应的防护用品等。
4. 确保设备使用安全焊接设备是安全使用的关键。
在检查焊接后,应及时对焊接设备的状态进行检查,是否设备损坏、漏电等等。
同时,应该检查对焊接设备进行的相应维护和保养措施是否到位,确保设备的安全使用。
二、切割后的安全检查1. 检查切割面切割后的工件的表面应平整、光滑,没有毛刺和裂纹。
切割面的表面质量直接影响工件的强度和使用寿命,因此,切割后的工件应进行全面检查,特别是在高强度、高负荷下工作的部位,应该检查是否存在切割表面的裂纹和裂纹扩展等问题。
2. 清理切割后的残留物在切割过程中,常常会产生切割残留物。
这些残留物可能会对工作造成损害。
因此,在进行安全检查时,要特别检查切割区域的残留物是否清理干净。
如果有残留物堵塞了设备的通道,将会对设备的正常使用造成危害。
清理残留物还可以减少潜在的火灾、爆炸等风险。
3. 安全保护措施切割过程中会产生大量的火花和火焰,对工作人员的安全产生威胁。
- 1、下载文档前请自行甄别文档内容的完整性,平台不提供额外的编辑、内容补充、找答案等附加服务。
- 2、"仅部分预览"的文档,不可在线预览部分如存在完整性等问题,可反馈申请退款(可完整预览的文档不适用该条件!)。
- 3、如文档侵犯您的权益,请联系客服反馈,我们会尽快为您处理(人工客服工作时间:9:00-18:30)。
最新整理焊接安全与检验
前言:焊接焊接是被焊工件的材质(同种或异种),通过加热或加压或两者并用,并且用或不用填充材料,使工件的材质达到原子间的建和而形成永久性连接的工艺过程。
焊接过程中,工件和焊料熔化形成熔融区域,熔池冷却凝固后便形成材料之间的连接。
这一过程中,通常还需要施加压力。
焊接的能量来源有很多种,包括气体焰、电弧、激光、电子束、摩擦和超声波等。
19世纪末之前,唯一的焊接工艺是铁匠沿用了数百年的金属锻焊。
最早的现代焊接技术出现在19世纪末,先是弧焊和氧燃气焊,稍后出现了电阻焊。
20世纪早期,随着第一次和第二次世界大战开战,对军用器材廉价可靠的连接方法需求极大,故促进了焊接技术的发展。
今天,随着焊接机器人在工业应用中的广泛应用,研究人员仍在深入研究焊接的本质,继续开发新的焊接方法,以进一步提高焊接质量。
焊接是现代工业中不可少技术之一。
它可以减少节省材料,来降低成本及减轻构件的自重等;焊接件是永久的结合在一起,与其他连接方式相比更加的牢固,耐用。
在众多连接方式中,焊接有许多突出的优点,但是在焊接过程中总是要加热、加压、用电、用可燃气体等,所以在此过程中无可厚非的会带来一些安全隐患。
纵观历史长河,有许许多多的焊接事故发生在我们的身旁。
我们该如何来预防和避免这些事故的发生呢? 1.焊接存在的危害在焊接过程中总会存在着对焊工的一些危害,下表是焊接事故中各种原因的统计表,如表一:表一焊接事故原因的统计表
事故类型触电事故火灾及爆炸事故灼伤高空坠落电光眼有害气体及烟尘其他事故所占比例32%27%14%11%6%6%4% 1.1.对焊工的危害焊工的主要职业危害是粉尘、有毒气体、高温、电弧光、高频磁场等。
电焊工接触到的有害因素示意如下图1:
图1电焊工有害因素示意图在焊接的过程中各种化学反应会产生大量的气体,其中一部分是对人体有害的,比如一氧化碳、氮氧化合物、臭氧。
1.1.1电焊工
尘肺电焊烟尘可通过呼吸道进入人体,主要损害呼吸系统。
早期多无临床症状和体征,发病工龄一般在10年以上。
1.1.2急性一氧化碳中毒一氧化碳可经呼吸道进入人体。
主要损害神经系统.表现为剧烈头痛、头晕、心悸、恶心、呕吐、无力、脉快、烦躁、步态不稳、意识不清、重者昏迷、抽搐、大小便失禁、休克。
严重者会立即死亡。
1.1.3慢性锰中毒锰尘可经呼吸道进入人体。
慢性锰中毒一般发病缓慢,早期主要表现为类神经症和自主神经功能障碍,病情继续发展后,可出现锥体外系神经障碍的症状和体征。
1.1.4急性氮氧化物中毒氮氧化物可经呼吸道进入人体。
主要损害呼吸系统。
表现为咽痛、胸闷、咳嗽、咳痰;可有轻度头晕、头痛、无力、心悸、恶心等。
进而出现呼吸困难,胸部紧迫感,咳白色或粉红色泡沫状痰、口唇青紫、甚至昏迷或窒息。
1.1.5急性臭氧中毒臭氧可经呼吸道进入人体。
主要损害呼吸系统。
短期低浓度吸入表现为口腔,咽喉干燥、胸骨下紧束感、胸闷、咳嗽、咳痰等症状,以及嗜睡、头痛、分析能力减退、味觉异常等。
吸入高浓度时可引起黏膜刺激症状,并可逐渐发生肺水肿表现。
1.1.6职业性电光性眼炎和职业性电光性皮炎长期重复的紫外线照射,可引起慢性睑缘炎和角膜炎等;皮肤受强烈的紫外线辐照可引起皮炎,表现为红斑,有时伴有水泡和水肿。
长期暴露,于结缔组织损害和弹性丧失而致皮肤皱缩、老化、更严重的是诱发皮肤癌。
1.2焊接对周围环境危害在焊接过程中,都存在加热或加压。
如果周围有易燃易爆物品的话,这会给周围带来安全隐患。
焊接飞溅物接触到易燃易爆物品就易产生火灾。
焊接过程中产生的噪音,光污染,辐射等染给周边人群带来的不便及。
2焊工自身的保护措施根据历年的焊接事故统计中得出,焊接事故在实施中操作不当和违规作业所占的比例占了绝大部分。
将事故主要原因归为五个方面,即为缺乏知识、操作不当、违章作业、设备设施有缺陷、其它。
各种事故主要原因所占的比例如下表二:表二焊接事故主要原因事故原因知识缺乏操作不当违章作业设备设施有缺陷其它所占百分百9%48%31%8%4% 焊工要有意识的保护自己,电焊作业中有害因素种类繁多,危害较大,因此,为了降低电焊工的职业危害,必须采取一系列有效的防治措施。
2.1加强防护措施加强个人防护,可以防止焊接时产生的有毒气体和粉尘的危害。
作业人员必须使用相应的防护眼镜、面罩、口罩、手套,穿白色防护服、绝缘鞋,决不能穿短袖衣或卷
起袖子,若在通风条件差的封闭容器内工作,还要佩戴使用有送风性能的防护头盔。
改进焊条材料,选择无毒或低毒的电焊条,以降低有害气体对焊工的身体侵害。
用机械代替人工,在可以用自动埋弧焊和机械手自动焊接的场合尽量选用自动焊接,以降低对焊工的直接伤害。
改善作业场所的通风状况,焊接过程中的粉尘和有害气体及时排出,减少焊工粉尘和有害气体的吸入量。
2.2常用护具用法及作用所谓的个人防护用品,即为保护工人在劳动过程中的安全和健康所需要的,必不可少的个人预防用品。
在各种焊接与切割中,一点要按规定佩戴防护用品,以防止有害气体、焊接烟弧光等对人体造成的危害。
防护用具种类及作用如下:2.2.1面罩焊接面罩是一种为防止焊接时的飞溅、弧光及其他辐射对焊工面部及颈部损伤的一种遮盖工具。
最常用的面罩有手持式面罩和头戴式面罩两种。
2.2.2焊接防护镜片焊接弧光的主要成分是紫外线、可见光和红外线。
而对眼睛伤害最大的是紫外线和红外线。
防护镜片的作用是适当地透过可见光,使操作人员既能观察熔池,又能将紫外线和红外线减弱到允许值(透过率等于0.0003%)一下。
防护镜片有滤光玻璃(用于遮蔽焊接有害光线的黑玻璃)和防护白玻璃(为保护黑玻璃不受飞溅损坏而罩在其外的一种无色透明玻璃)两部分组成。
2.2.3防护眼镜防护眼镜包括滤光玻璃(黑色玻璃)和防护白玻璃两层,焊工在气焊或气割中必须佩带,它除了与防护镜片有相同的滤光要求外。
还应满足不能因镜框受热造成镜片脱落,接触人体面部的部分不能有锐角,接触皮肤的部分不能用有毒材料制作三个要求。
2.2.4防尘口罩及防毒面具焊工在焊接、切割作业时,当采用整体或局部通风不能使烟尘浓度降低到卫生标准以下时,必须选用适当的防尘口罩或防毒面具。
2.2.5噪声防护用具国家标准规定若噪声超过85dB时,应采取隔声、消声、减振和阻尼等控制技术。
当采取措施仍不能把噪声降低到允许值以下时,操作者应采用个人噪声防护用具,如耳塞或噪声头盔等。
2.2.6安全帽在高层空交叉作业现场,为了预防高空和外界飞来物的危害,焊工应佩戴安全帽。
2.2.7防护服焊接用防护工作服,主要起隔热、反射和吸收等屏蔽作用,以保护人体免受焊接热辐射或飞溅物的伤害。
2.2.8焊工手套、工作鞋及护脚为防止焊工四肢触电、灼伤和砸伤,避免不必要的伤亡事故发生,要求焊工在任何情况下操作都必须佩戴好规定的焊工手套、胶鞋及护脚。
2.2.9安全带为。