钢中气体
钢瓶中的气体为何要留余气?
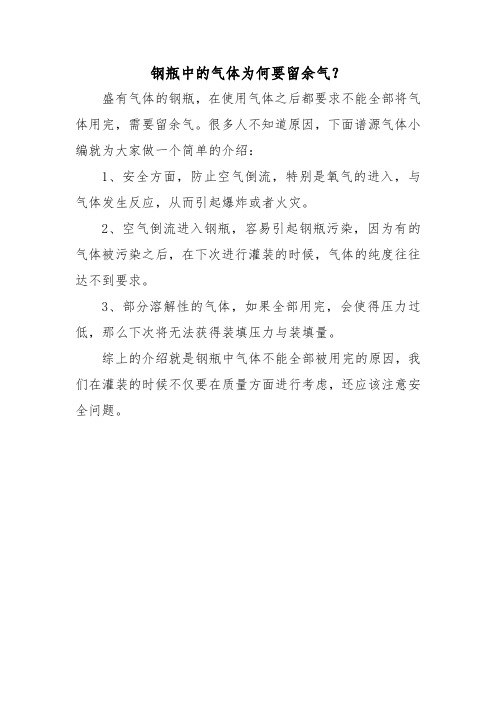
钢瓶中的气体为何要留余气?
盛有气体的钢瓶,在使用气体之后都要求不能全部将气体用完,需要留余气。
很多人不知道原因,下面谱源气体小编就为大家做一个简单的介绍:
1、安全方面,防止空气倒流,特别是氧气的进入,与气体发生反应,从而引起爆炸或者火灾。
2、空气倒流进入钢瓶,容易引起钢瓶污染,因为有的气体被污染之后,在下次进行灌装的时候,气体的纯度往往达不到要求。
3、部分溶解性的气体,如果全部用完,会使得压力过低,那么下次将无法获得装填压力与装填量。
综上的介绍就是钢瓶中气体不能全部被用完的原因,我们在灌装的时候不仅要在质量方面进行考虑,还应该注意安全问题。
底吹转炉钢中氢气的吹入与去除方案

底吹转炉钢中氢气的吹入与去除方案钢铁生产过程中,底吹转炉是一种常见的冶炼设备,通过底部吹气的方式,在高温下进行冶炼反应,生产出优质的钢材。
然而,底吹转炉钢中可能存在氢气,这对钢的质量和性能产生不利影响。
因此,合理的氢气吹入与去除方案对于提高钢材的质量至关重要。
首先,我们来探讨氢气的吹入方案。
氢气在底吹转炉炼钢过程中的吹入可以通过以下几个方面进行优化。
首先,控制底吹氧气量。
底吹转炉吹氧气是主要的冶炼手段,而氧气和氢气之间存在竞争反应。
过大的底吹氧气量会加速氢气的氧化速度,导致氢气转化为水蒸气而逸出炉外。
因此,合理调整底吹氧气量,控制氧气的浓度,有利于减少氢气的损失。
其次,增加吹氩量。
氢气在钢中溶解度较低,通过增加吹氩量,可以有效促进氢气在钢中的溶解。
同时,氩气还具有稀释效应,可以将局部高浓度的氢气稀释,降低其对钢的影响。
通过合理调整吹氩量,可以达到有效控制氢气含量的目的。
此外,调整底吹角度也是一个关键的因素。
底吹角度的改变会导致气液两相的流动方式发生变化,从而影响氢气的吹入和分布。
选择合适的底吹角度,可以将氢气均匀地吹入钢中,充分利用氢气的溶解和反应作用。
然而,在进行氢气吹入的同时,也需要与去除方案相结合,以尽量降低钢中氢气的含量。
首先,采用适当的冶炼工艺。
冶炼工艺是影响钢中氢气含量的重要因素之一。
在冶炼过程中,可以通过合理调整温度、浸渍时间和吹气速度等参数,降低氢气的溶解度和扩散速率。
此外,在进料和排渣过程中也应注意控制氢气的损失。
其次,采用适当的除气方法。
除气是去除钢中气体的常用手段。
传统的除气方式包括真空除气和气体吹扫等。
对于底吹转炉钢中的氢气去除,真空除气是一种有效的方法。
通过在冶炼过程中建立真空环境,可以有效地去除大部分的氢气。
此外,还可以采用高温脱气等技术对钢中残留的氢气进行进一步去除。
此外,合理的联合布局也可以提高氢气的去除效果。
通过将多个转炉进行串联,可将氢气的去除效果提升到更高的水平。
气体可压缩存在钢瓶中的原因

气体可压缩存在钢瓶中的原因
气体是人们常见的一种物质,它能够被压缩,而被压缩存在钢瓶中也是十分常见的现象。
那么为什么气体可以被压缩存在钢瓶中呢?
其实,气体可以被压缩存在钢瓶中的原因是其本身的物理性质与钢瓶的结构特性有关的。
首先,气体本身的物理性质决定了它可以在一定程度上被压缩。
它是由一个个微小的分子组成的,而这些分子之间又有一定的介质距离,所以在压缩的过程中它们会挤压,使得气体的体积减少。
其次,钢瓶可以把压缩后的气体存储起来。
钢瓶是由非常厚实的钢材组成的,而且它有十分严峻的断面结构。
因此,当气体被压缩后,即使外界压力减小,气体也可以在钢瓶中受到一定的外界支撑,从而防止气体的体积过大,从而使气体能够稳定地存储在钢瓶中。
此外,钢瓶的密封性也是极为重要的因素。
钢瓶所使用的密封材料一般是橡胶或者塑料,这种材料具有良好的密封性能,能够有效地防止气体泄漏,从而使其能够长期存在钢瓶中。
最后,它们也具有较强的承压能力。
由于钢瓶内部外壁厚度较高,所以它们具有较高的抗压性,有助于抵御外界的压力,使得气体能够压缩存在钢瓶中。
综上所述,气体之所以可以被压缩存在钢瓶中,主要是由于它本身的物理性质及钢瓶的结构特性所决定的。
气体可以被压缩,而耐压且密封性好的钢瓶,又能够有效地保护它,从而使得它可以安全地长期被压缩存在钢瓶中。
氢进入钢中的环节

氢进入钢中的环节
1. 吸附:氢气首先要通过吸附作用进入钢材中。
吸附是指气体分子与固体表面之间的相互作用,使气体分子附着在固体表面上。
钢材表面通常具有一定的吸附能力,能够吸附一部分氢气分子。
这种吸附作用主要是物理吸附,即氢气分子通过范德华力与钢材表面相互作用。
吸附过程中,氢气分子会与钢材表面形成一层单分子厚度的吸附层,这有助于后续的扩散过程。
2. 扩散:吸附在钢材表面的氢气分子会进一步通过扩散作用进入钢材内部。
扩散是指气体分子在固体内部的自由移动,使气体分子从高浓度区域向低浓度区域传播。
在钢材中,氢气分子会沿着浓度梯度从钢材表面向内部扩散。
扩散过程受到多种因素的影响,如温度、氢气浓度、钢材组织结构等。
一般来说,高温、高浓度和细小的钢材晶粒会加速氢气的扩散速度。
3. 溶解:在扩散的过程中,一部分氢气分子会溶解到钢材的晶格中。
溶解是指气体分子与固体晶格之间的相互作用,使气体分子与固体形成溶液。
在钢材中,氢气分子与钢材晶格发生相互作用,一部分氢气会进入钢材晶格中,形成固溶体。
溶解过程中,钢材的化学成分、温度和压力等因素都会对氢气的溶解量产生影响。
溶解的氢气在钢材中可以以原子形式存在,也可以以氢离子的形式存在。
氢气进入钢材中主要经过吸附、扩散和溶解这三个环节。
这些环节
相互作用,共同影响着氢气在钢材中的分布和浓度。
了解氢气进入钢材的过程对于研究氢脆性和氢腐蚀等问题具有重要意义,也有助于制定相应的防护措施,保障钢材的使用安全。
气体元素在钢中的存在形式以及对钢材性能的影响及金属中气体分析解读
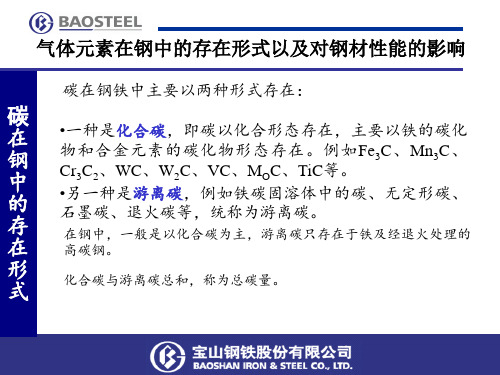
红外池的基本结构
一个典型的红外检测单元由红外光源、斩波马达、精密波长滤光片、聚 光锥、带有前置放大器的红外检测器和一个池体组成。
红外池的基本结构
斩波马达带动叶片转动“切割”光束,将光源调制为85Hz交变光,使到 达检测器中能量信号转变为交流信号,这样有利于抗拒干扰,增加检测 信号的信噪比,提高检测的精度。
如何使分析成功
助 熔 剂
1勺 LECOCEL II HP的空白值
如何使分析成功
虽然目前的气体分析仪都具备重量自动换算计算的功能, 但应该指出,称样量不一致,会引起:
称 样 量
1)影响到的空白值的波动。 2)引起高频感应电流的不一致,即燃烧温度的波动。 3)引起试样中气体释放的快与慢。
如何使分析成功
金属和矿石 + O2 =氧化物微粒
如何使分析成功
•坩埚
•助熔剂
•称样量 •炉温 •积分时间 •试样处理
如何使分析成功
C, S分析所用的坩埚为 25×25Φ的陶瓷坩埚,虽然坩埚在出厂时已经 用高温焙烧处理,但由于保存时间,包装,运输等原因,不可避免地 会接触其它物质和空气,所以在使用前,坩埚必须经过1000℃ 4小时以 上的预处理(或于1200℃,20~30分钟高温处理),干燥箱冷却至室 温后才能使用。
•振荡器电路产生18MHz高 频电源,输出功率为2.2KW •高频电源在感应线圈中, 形成高频交变电磁场 •试样感应产生涡流使试样 发热熔融 •试样的导磁导电性能 、重 量、助熔剂 •坩埚位于感应线圈的几何 中心位置
坩埚
试样 感应线圈
高频感应炉
•振荡器电路
18MHz高频电源,输出功率为2.2KW
炉 子 单 元
红外检测的定量依据
高级炼钢工鉴定复习题带答案
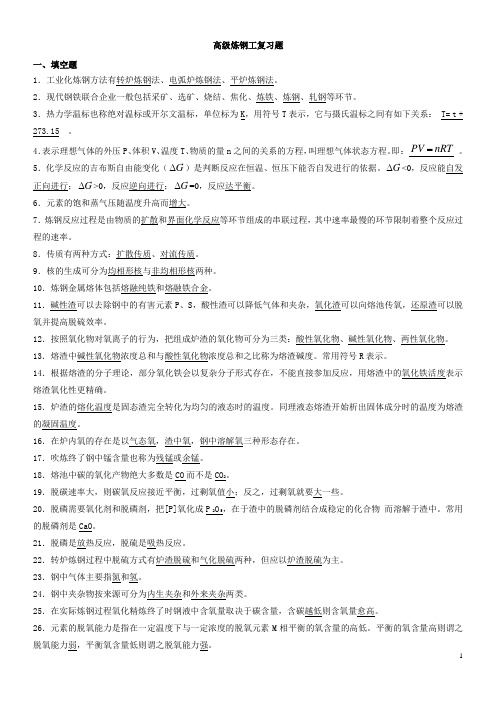
高级炼钢工复习题一、填空题1.工业化炼钢方法有转炉炼钢法、电弧炉炼钢法、平炉炼钢法。
2.现代钢铁联合企业一般包括采矿、选矿、烧结、焦化、炼铁、炼钢、轧钢等环节。
3.热力学温标也称绝对温标或开尔文温标,单位标为K,用符号T表示,它与摄氏温标之间有如下关系: T= t + 273.15 。
4.表示理想气体的外压P、体积V、温度T、物质的量n之间的关系的方程,叫理想气体状态方程。
即:nRTPV=。
5.化学反应的吉布斯自由能变化(G∆)是判断反应在恒温、恒压下能否自发进行的依据。
G∆<0,反应能自发正向进行;G∆>0,反应逆向进行;G∆=0,反应达平衡。
6.元素的饱和蒸气压随温度升高而增大。
7.炼钢反应过程是由物质的扩散和界面化学反应等环节组成的串联过程,其中速率最慢的环节限制着整个反应过程的速率。
8.传质有两种方式:扩散传质、对流传质。
9.核的生成可分为均相形核与非均相形核两种。
10.炼钢金属熔体包括熔融纯铁和熔融铁合金。
11.碱性渣可以去除钢中的有害元素P、S,酸性渣可以降低气体和夹杂,氧化渣可以向熔池传氧,还原渣可以脱氧并提高脱硫效率。
12.按照氧化物对氧离子的行为,把组成炉渣的氧化物可分为三类:酸性氧化物、碱性氧化物、两性氧化物。
13.熔渣中碱性氧化物浓度总和与酸性氧化物浓度总和之比称为熔渣碱度。
常用符号R表示。
14.根据熔渣的分子理论,部分氧化铁会以复杂分子形式存在,不能直接参加反应,用熔渣中的氧化铁活度表示熔渣氧化性更精确。
15.炉渣的熔化温度是固态渣完全转化为均匀的液态时的温度。
同理液态熔渣开始析出固体成分时的温度为熔渣的凝固温度。
16.在炉内氧的存在是以气态氧,渣中氧,钢中溶解氧三种形态存在。
17.吹炼终了钢中锰含量也称为残锰或余锰。
18.熔池中碳的氧化产物绝大多数是CO而不是CO2。
19.脱碳速率大,则碳氧反应接近平衡,过剩氧值小;反之,过剩氧就要大一些。
20.脱磷需要氧化剂和脱磷剂,把[P]氧化成P2O5,在于渣中的脱磷剂结合成稳定的化合物而溶解于渣中。
连铸钢皮下气泡的产生原因及控制
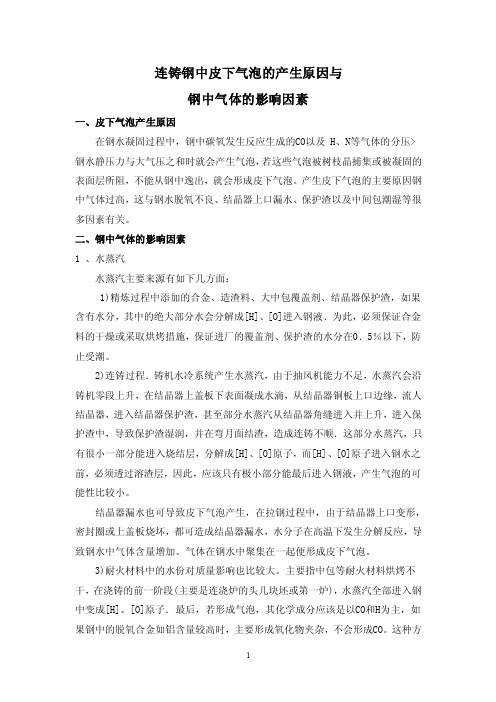
连铸钢中皮下气泡的产生原因与钢中气体的影响因素一、皮下气泡产生原因在钢水凝固过程中,钢中碳氧发生反应生成的CO以及 H、N等气体的分压>钢水静压力与大气压之和时就会产生气泡,若这些气泡被树枝晶捕集或被凝固的表面层所阻,不能从钢中逸出,就会形成皮下气泡。
产生皮下气泡的主要原因钢中气体过高,这与钢水脱氧不良、结晶器上口漏水、保护渣以及中间包潮湿等很多因素有关。
二、钢中气体的影响因素1 、水蒸汽水蒸汽主要来源有如下几方面:1)精炼过程中添加的合金、造渣料、大中包覆盖剂、结晶器保护渣,如果含有水分,其中的绝大部分水会分解成[H]、[O]进入钢液.为此,必须保证合金料的干燥或采取烘烤措施,保证进厂的覆盖剂、保护渣的水分在0.5%以下,防止受潮。
2)连铸过程.铸机水冷系统产生水蒸汽,由于抽风机能力不足,水蒸汽会沿铸机零段上升,在结晶器上盖板下表面凝成水滴,从结晶器铜板上口边缘,流人结晶器,进入结晶器保护渣,甚至部分水蒸汽从结晶器角缝进入并上升,进入保护渣中,导致保护渣湿润,并在弯月面结渣,造成连铸不顺.这部分水蒸汽,只有很小一部分能进入烧结层,分解成[H]、[O]原子,而[H]、[O]原子进入钢水之前,必须透过溶渣层,因此,应该只有极小部分能最后进入钢液,产生气泡的可能性比较小。
结晶器漏水也可导致皮下气泡产生,在拉钢过程中,由于结晶器上口变形,密封圈或上盖板烧坏,都可造成结晶器漏水,水分子在高温下发生分解反应,导致钢水中气体含量增加。
气体在钢水中聚集在一起便形成皮下气泡。
3)耐火材料中的水份对质量影响也比较大。
主要指中包等耐火材料烘烤不干,在浇铸的前一阶段(主要是连浇炉的头几块坯或第一炉),水蒸汽全部进入钢中变成[H]、[O]原子.最后,若形成气泡,其化学成分应该是以CO和H为主,如果钢中的脱氧合金如铝含量较高时,主要形成氧化物夹杂,不会形成CO。
这种方式造成皮下气泡的特点是:只有浇次的头一炉的头几支坯出现气泡,越到后面,气泡越少。
b2220-202标准
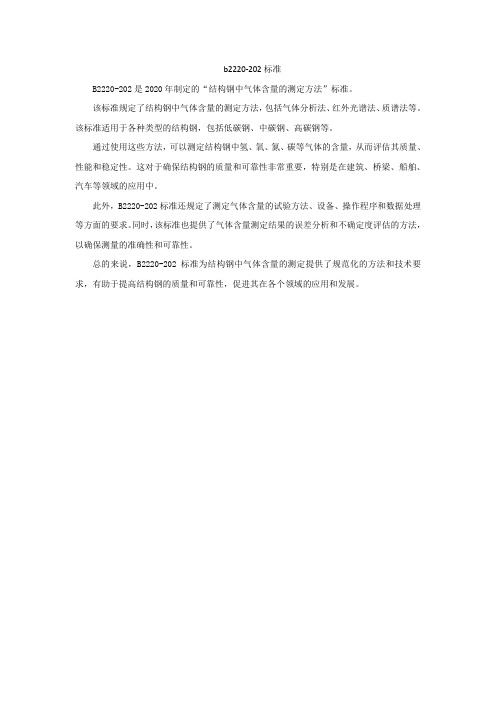
b2220-202标准
B2220-202是2020年制定的“结构钢中气体含量的测定方法”标准。
该标准规定了结构钢中气体含量的测定方法,包括气体分析法、红外光谱法、质谱法等。
该标准适用于各种类型的结构钢,包括低碳钢、中碳钢、高碳钢等。
通过使用这些方法,可以测定结构钢中氢、氧、氮、碳等气体的含量,从而评估其质量、性能和稳定性。
这对于确保结构钢的质量和可靠性非常重要,特别是在建筑、桥梁、船舶、汽车等领域的应用中。
此外,B2220-202标准还规定了测定气体含量的试验方法、设备、操作程序和数据处理等方面的要求。
同时,该标准也提供了气体含量测定结果的误差分析和不确定度评估的方法,以确保测量的准确性和可靠性。
总的来说,B2220-202标准为结构钢中气体含量的测定提供了规范化的方法和技术要求,有助于提高结构钢的质量和可靠性,促进其在各个领域的应用和发展。
钢中的气体元素

•■测试与分析〜钢中的气体元素宋红艳(中车株洲电力机车有限公司,湖南株洲412001)摘要:介绍了钢中氮、氢、氧等气体的来源、存在形式和对钢材性能特别是力学性能的影响。
举例说明了氮、氢和氧元素在碳结构钢和不锈钢中的应用。
关键词:气体元素;钢;应用中图分类号:T G 115.3+3文献标志码文章编号:1008-1690(2021)01-0058-03Gaseous Elements in SteelsSONG Hongyan(Zliuzhou C R R C Power Loco Co ., Ltd ., Zhuzhou 412001, Hunan China )Abstract : Source , existence form of gaseous elements such as nitrogen , hydrogen and oxygen i n s teels and their e ffect on performances of s t e e l product , especially mechanical properties , were introduced . The applications of nitrogen,hydrogen and oxygen i n carbon structural steel and stainless s t e e l were explained with examples .Key words : gaseous element ; steel ; application1钢铁中气体的存在形式钢中气体仅包括氮、氢、氧三种,在钢铁中并非呈气体状态存在,主要是形成化合物或固溶于钢铁 组织中,仅少量以游离形式存在钢铁的缺陷中。
钢铁中的氮主要源于空气,在冶炼和浇注过程 中,空气与金属熔池或炉渣接触时,溶解于到钢液,与金属形成氮化物,也有以氮化锰和氮化铬等铁合 金作原材料加人的钢中氮主要形成氮化物,如 Fe 4N 、Fe 2N 、CriV 、V N 、TiN 、A l N 、Si 3N 4 等,还有部分 形成固溶体,只有极微量的氮以分子形式吸附于金 属表面或存在于金属空隙中,而且在钢中的溶解度 随着某些合金元素浓度的增加而增加,例如含铬合 金的含氮量较高。
炼钢用的气体
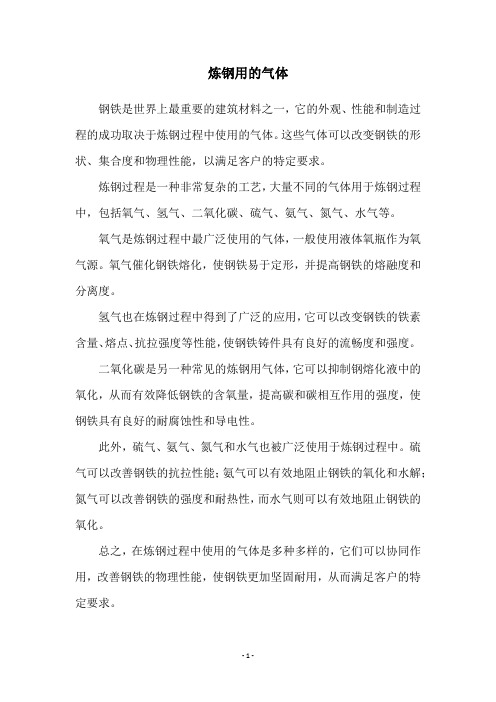
炼钢用的气体
钢铁是世界上最重要的建筑材料之一,它的外观、性能和制造过程的成功取决于炼钢过程中使用的气体。
这些气体可以改变钢铁的形状、集合度和物理性能,以满足客户的特定要求。
炼钢过程是一种非常复杂的工艺,大量不同的气体用于炼钢过程中,包括氧气、氢气、二氧化碳、硫气、氨气、氮气、水气等。
氧气是炼钢过程中最广泛使用的气体,一般使用液体氧瓶作为氧气源。
氧气催化钢铁熔化,使钢铁易于定形,并提高钢铁的熔融度和分离度。
氢气也在炼钢过程中得到了广泛的应用,它可以改变钢铁的铁素含量、熔点、抗拉强度等性能,使钢铁铸件具有良好的流畅度和强度。
二氧化碳是另一种常见的炼钢用气体,它可以抑制钢熔化液中的氧化,从而有效降低钢铁的含氧量,提高碳和碳相互作用的强度,使钢铁具有良好的耐腐蚀性和导电性。
此外,硫气、氨气、氮气和水气也被广泛使用于炼钢过程中。
硫气可以改善钢铁的抗拉性能;氨气可以有效地阻止钢铁的氧化和水解;氮气可以改善钢铁的强度和耐热性,而水气则可以有效地阻止钢铁的氧化。
总之,在炼钢过程中使用的气体是多种多样的,它们可以协同作用,改善钢铁的物理性能,使钢铁更加坚固耐用,从而满足客户的特定要求。
- 1 -。
钢中氢气体知识问答(3)
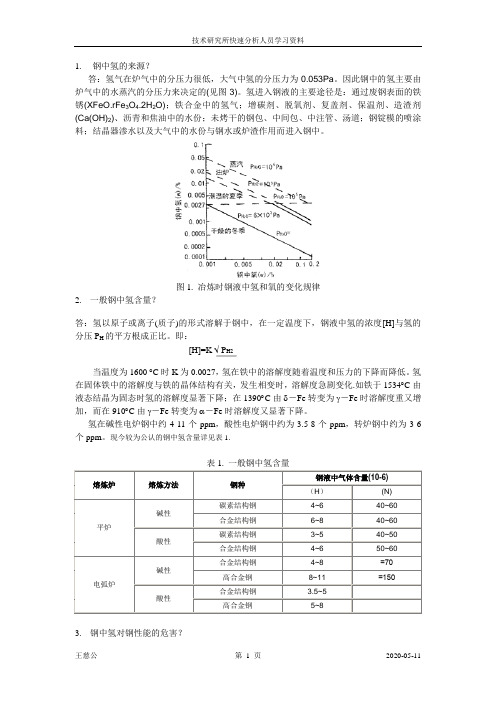
1.钢中氢的来源?答:氢气在炉气中的分压力很低,大气中氢的分压力为0.053Pa。
因此钢中的氢主要由炉气中的水蒸汽的分压力来决定的(见图3)。
氢进入钢液的主要途径是:通过废钢表面的铁锈(XFeO.rFe3O4.2H2O);铁合金中的氢气;增碳剂、脱氧剂、复盖剂、保温剂、造渣剂(Ca(OH)2)、沥青和焦油中的水份;未烤干的钢包、中间包、中注管、汤道;钢锭模的喷涂料;结晶器渗水以及大气中的水份与钢水或炉渣作用而进入钢中。
图1. 冶炼时钢液中氢和氧的变化规律2.一般钢中氢含量?答:氢以原子或离子(质子)的形式溶解于钢中,在一定温度下,钢液中氢的浓度[H]与氢的分压P H的平方根成正比。
即:[H]=K √ P H2当温度为1600 ︒C时K为0.0027,氢在铁中的溶解度随着温度和压力的下降而降低。
氢在固体铁中的溶解度与铁的晶体结构有关,发生相变时,溶解度急剧变化.如铁于1534︒C由液态结晶为固态时氢的溶解度显著下降;在1390︒C由δ-Fe转变为γ-Fe时溶解度重又增加,而在910︒C由γ-Fe转变为α-Fe时溶解度又显著下降。
氢在碱性电炉钢中约4-11个ppm,酸性电炉钢中约为3.5-8个ppm,转炉钢中约为3-6个ppm。
现今较为公认的钢中氢含量详见表1.表1. 一般钢中氢含量3.钢中氢对钢性能的危害?答:氢溶入钢中会降低钢的塑性和韧性。
研究表明,氢含量高不仅会导致钢的伸长率和面缩率急剧降低,还易产生氢致裂纹缺陷。
钢在冷却放置过程中,氢呈过饱和固溶体状态,由于其具有极强的扩散能力,很可能聚集在某些部位,使钢产品的局部压力增高,产生白点,形成内裂,进一步诱发高碳钢的疲劳损伤,严重影响其使用性能。
另一方面,冷却放置时,氢也能扩散到大气中,从而降低钢中的氢含量,减弱其危害。
4. 如何降低钢中氢?答:溶解在钢中的氢和氮以原子状态存在,其溶解反应为:{}[]H H =2%21在一定温度下达到平衡时: []212%H H P H K =[]2%H H P K H ⋅=上式说明氢在钢中的溶解度与作用在钢液面上的氢的分压的平方根成正比,即称西华特定律。
钢中气体的不良影响
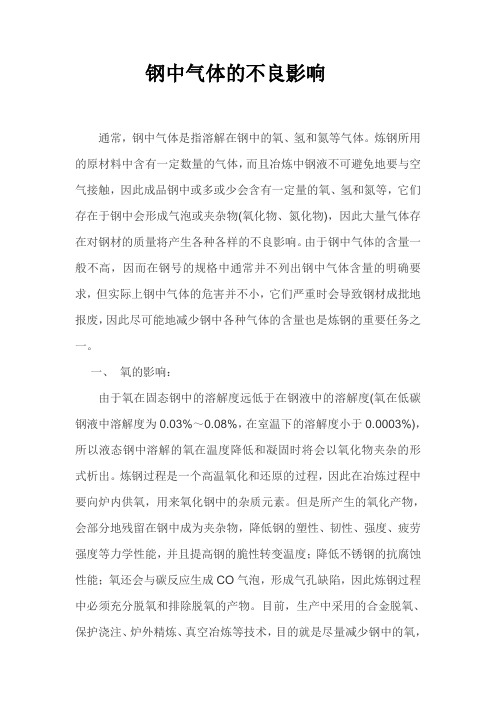
钢中气体的不良影响通常,钢中气体是指溶解在钢中的氧、氢和氮等气体。
炼钢所用的原材料中含有一定数量的气体,而且冶炼中钢液不可避免地要与空气接触,因此成品钢中或多或少会含有一定量的氧、氢和氮等,它们存在于钢中会形成气泡或夹杂物(氧化物、氮化物),因此大量气体存在对钢材的质量将产生各种各样的不良影响。
由于钢中气体的含量一般不高,因而在钢号的规格中通常并不列出钢中气体含量的明确要求,但实际上钢中气体的危害并不小,它们严重时会导致钢材成批地报废,因此尽可能地减少钢中各种气体的含量也是炼钢的重要任务之一。
一、氧的影响:由于氧在固态钢中的溶解度远低于在钢液中的溶解度(氧在低碳钢液中溶解度为0.03%~0.08%,在室温下的溶解度小于0.0003%),所以液态钢中溶解的氧在温度降低和凝固时将会以氧化物夹杂的形式析出。
炼钢过程是一个高温氧化和还原的过程,因此在冶炼过程中要向炉内供氧,用来氧化钢中的杂质元素。
但是所产生的氧化产物,会部分地残留在钢中成为夹杂物,降低钢的塑性、韧性、强度、疲劳强度等力学性能,并且提高钢的脆性转变温度;降低不锈钢的抗腐蚀性能;氧还会与碳反应生成CO气泡,形成气孔缺陷,因此炼钢过程中必须充分脱氧和排除脱氧的产物。
目前,生产中采用的合金脱氧、保护浇注、炉外精炼、真空冶炼等技术,目的就是尽量减少钢中的氧,这就是氧在炼钢过程中所具有的二重性。
二、氮的影响:钢中的氮主要来自炉料和炉气,碳素钢中的氮含量一般在0.00 1%~0.02%之间。
氮能溶于铁中,591℃时在α-Fe中的溶解度为0. 1%,而在室温时只有0.001%。
因此,氮能固溶于钢中,也能以氮化物和气体形式存在于钢中。
钢材在室温长时间放置时,溶于钢中过饱和的氮会以Fe4N形式析出,从而使钢的强度、硬度升高,而塑性、韧性下降,这种现象叫时效。
钢中含氮量越高,这种时效倾向就越大。
如果在浇注前向钢液中加入少量的铝(每1t钢加0.5~1.0kgAl),可以形成AlN而大大降低固溶于铁素体中的氮化物,从而降低氮的时效作用。
冶金质量分析第二章炼钢过程中气体和夹杂物的冶金控制
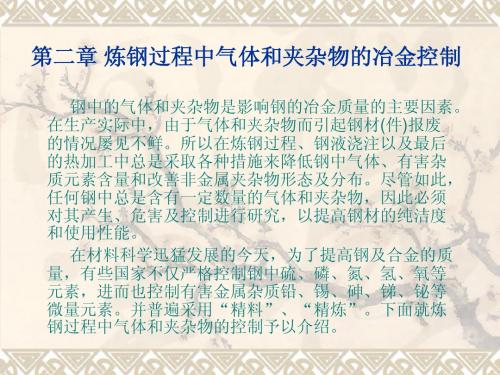
上式表明,给定的温度下,钢液中溶解的氢、 氮的浓度与钢液上氢、氮的分压的平方根成正 比。氢、氮在钢液中的溶解反应为吸热过程, 随着温度升高,溶解度也增大,由此可见,出 钢温度过高会增加氢、氮在钢中的溶解量,从 而降低钢的质量和性能。 钢液中其他溶质元素对气体的溶解度也有影 响,凡与气体有较强亲和力的元素(如V、Mn, Ti, Nb等),将增加气体在钢液中的溶解度,而 与铁的亲和力大于气体与铁的亲和力的元素(如 C , Si等),会降低气体在钢液中的溶解度。
(二)氢对钢质量的影响 氢的原子半径小(0.053nm),进入钢中后, 相当容易移动。由于氢在铁中移动的激活能 只为碳在铁中移动激活能的1/10,以致钢中的 氢容易在应力(主要指外加应力、残余应力、原 子之间相互作用力等)作用下,向钢中一些危险 区域扩散,以不同形式危害钢的性能。 钢中氢的危害主要表现在以下几个方面:
一般来讲,钢的氢脆随钢的强度增高而加剧, 高强度钢和超高强度钢含氢时脆性将明显 增加。研究认为,高强度钢平均含氢量不到 10-4%就可能产生氢脆。 图4--2中表明,在低于屈服强度的恒定静载 荷持续作用下,经过一定时间的孕育期后,、 在试样表面缺陷处或缺口根部产生裂纹源,随 着时间的延长,裂纹不断扩展长大,到一定程 度后导致试样突然断裂。由于图4-2中的断裂 曲线与疲劳曲线相似,因此这种氢脆也称为静 疲劳。图4-2中有一个下临界应力值(门槛值), 试样在低于此值的应力作用下,加载时间再长 也不会产生脆性断裂。下临界应力的大小与试 样表面缺口形状有关,缺口愈尖锐,下临界应 力也愈低。
Triano在1955年提出的应变时效型氢脆的 解释,目前已为较多的人所接受,其概念如 下:含氢试样受载后,在其缺口尖端处产生应力 集中。氢原子在应力作用下向这里扩散聚集, 使缺口尖端处的位错周围形成柯氏气团,对位 错产生钉扎作用,导致位错难以运动,表现为 缺口尖端处被局部硬化。在外加应力作用下, 如果试样缺口尖端处的基体不能通过位错运动 产生局部塑性变形而使应力集中松弛的话,此 处就会萌生裂纹并由此扩展长大。
气体可压缩存在钢瓶中的原因

气体可压缩存在钢瓶中的原因
气体的可压缩性是一种物理性质,在自然界中存在着大量的气体,它们可以被存储在钢瓶或容器中再发挥其作用。
为什么气体能被储存到钢取呢?原因是气体可以压缩在钢瓶中,这是一种重要的物理性质。
首先,气体可压缩性是由它们的体积可变性决定的。
气体分子之间的距离反映出体积的大小,当分子在某一特定物理环境下离得越远,气体的体积就会越大。
当该气体被压缩时,分子之间的距离会更近,气体的体积会变小,从而使得该气体变得更加紧凑。
由于气体的体积可变性,使得气体可以存放在紧凑的容器中,而且不会被压缩变形或受损。
其次,气体可压缩性是由它们的密度可变性决定的。
密度可变性是指气体的比重可以随着压力变化而变化,从而改变气体体积。
当气体受压力时,它的分子会被和合在一起,从而使得其体积减小;当压力衰减时,气体的分子会分散开来,使得其体积增大。
这一物理现象使得气体在受压后可以存放在钢瓶中而不会有破坏。
最后,气体可压缩性是基于其独特的分子构造。
气体的分子具有相对较大的空间,当它们接近时,分子之间的空间会被填补,而不会有任何变形现象发生,且可以在压力变化的情况下保持相对稳定的状态,从而能被压缩在钢瓶中存储起来。
综上所述,气体可压缩性是由它们的体积可变性、密度可变性以及分子独特构造决定的,这使得气体可以存放在钢瓶中,而不会因压缩而变形或受损。
因此,气体可压缩存在钢瓶中是非常有效的储存方
式,使得气体能够及时发挥其作用,为人类社会的可持续发展发挥着重要作用。
降低钢中氢、氧、氮气体含量的措施
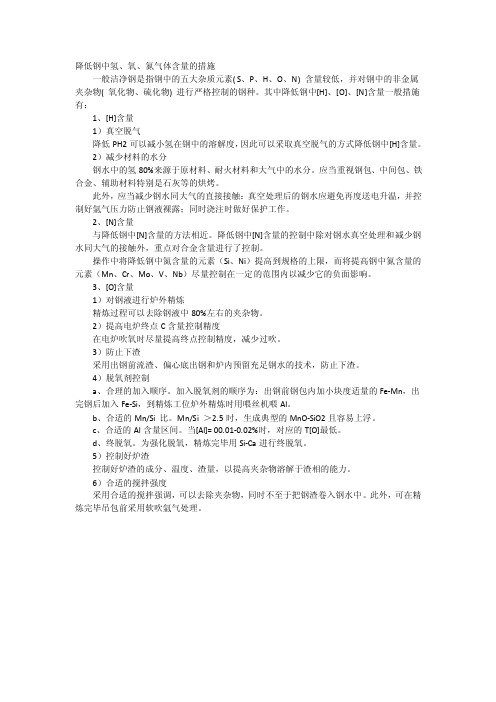
降低钢中氢、氧、氮气体含量的措施一般洁净钢是指钢中的五大杂质元素( S、P、H、O、N) 含量较低,并对钢中的非金属夹杂物( 氧化物、硫化物) 进行严格控制的钢种。
其中降低钢中[H]、[O]、[N]含量一般措施有:1、[H]含量1)真空脱气降低PH2可以减小氢在钢中的溶解度,因此可以采取真空脱气的方式降低钢中[H]含量。
2)减少材料的水分钢水中的氢80%来源于原材料、耐火材料和大气中的水分。
应当重视钢包、中间包、铁合金、辅助材料特别是石灰等的烘烤。
此外,应当减少钢水同大气的直接接触:真空处理后的钢水应避免再度送电升温,并控制好氩气压力防止钢液裸露;同时浇注时做好保护工作。
2、[N]含量与降低钢中[N]含量的方法相近。
降低钢中[N]含量的控制中除对钢水真空处理和减少钢水同大气的接触外,重点对合金含量进行了控制。
操作中将降低钢中氮含量的元素(Si、Ni)提高到规格的上限,而将提高钢中氮含量的元素(Mn、Cr、Mo、V、Nb)尽量控制在一定的范围内以减少它的负面影响。
3、[O]含量1)对钢液进行炉外精炼精炼过程可以去除钢液中80%左右的夹杂物。
2)提高电炉终点C含量控制精度在电炉吹氧时尽量提高终点控制精度,减少过吹。
3)防止下渣采用出钢前流渣、偏心底出钢和炉内预留充足钢水的技术,防止下渣。
4)脱氧剂控制a、合理的加入顺序。
加入脱氧剂的顺序为:出钢前钢包内加小块度适量的Fe-Mn,出完钢后加入Fe-Si,到精炼工位炉外精炼时用喂丝机喂Al。
b、合适的Mn/Si 比。
Mn/Si >2.5时,生成典型的MnO-SiO2且容易上浮。
c、合适的Al含量区间。
当[Al]= 00.01-0.02%时,对应的T[O]最低。
d、终脱氧。
为强化脱氧,精炼完毕用Si-Ca进行终脱氧。
5)控制好炉渣控制好炉渣的成分、温度、渣量,以提高夹杂物溶解于渣相的能力。
6)合适的搅拌强度采用合适的搅拌强调,可以去除夹杂物,同时不至于把钢渣卷入钢水中。
钢气体含量标准
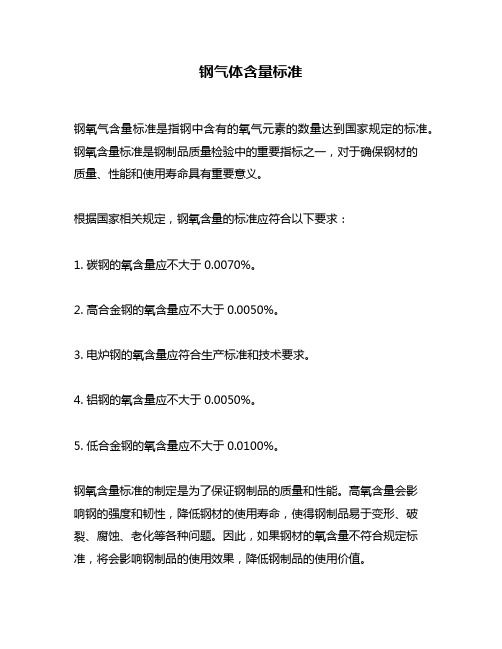
钢气体含量标准
钢氧气含量标准是指钢中含有的氧气元素的数量达到国家规定的标准。
钢氧含量标准是钢制品质量检验中的重要指标之一,对于确保钢材的
质量、性能和使用寿命具有重要意义。
根据国家相关规定,钢氧含量的标准应符合以下要求:
1. 碳钢的氧含量应不大于0.0070%。
2. 高合金钢的氧含量应不大于0.0050%。
3. 电炉钢的氧含量应符合生产标准和技术要求。
4. 铝钢的氧含量应不大于0.0050%。
5. 低合金钢的氧含量应不大于0.0100%。
钢氧含量标准的制定是为了保证钢制品的质量和性能。
高氧含量会影
响钢的强度和韧性,降低钢材的使用寿命,使得钢制品易于变形、破裂、腐蚀、老化等各种问题。
因此,如果钢材的氧含量不符合规定标准,将会影响钢制品的使用效果,降低钢制品的使用价值。
同时,通过加强对钢氧含量的检测,可以提高钢材生产的科学性和精细化程度,为国际市场上的竞争提供有力的保障。
因此,钢氧含量标准的制定不仅关乎企业的生产质量和效益,也关乎国家科技实力和经济竞争力的发展。
在实际生产中,钢厂需要加强对钢材氧含量的监测和测量。
通过采用现代化的液相法、电解法、火焰法或红外法等检测技术,可以更准确地确定钢材的氧含量,并且可以对不同种类的钢材进行针对性的检测和分析,保证钢材氧含量的符合要求。
总之,钢氧含量标准是保证钢制品质量和性能的重要指标之一,只有通过加强钢氧含量的检测和监管,才能保证钢制品质量和稳定性,并为钢材行业的发展打下坚实的基础。
钢铁冶炼过程中气体的实时分析技术

钢铁冶炼过程中气体的实时分析技术随着我国钢铁行业的快速发展,钢铁冶炼过程中气体的实时分析技术也得到了广泛应用。
由于钢铁生产过程中产生的气体种类繁多,其中含有的有害气体成分较高,如果不及时分析和处理,不仅会对环境造成严重的污染,还会对工人的身体健康产生极大的影响。
因此,在钢铁冶炼过程中对气体进行实时分析已经成为一项十分重要的技术。
对于钢铁生产工厂来说,气体实时分析技术在生产过程中扮演了重要的角色。
它可以帮助企业监测钢铁炉的运行情况,有效地诊断出故障点,提高生产效率。
同时,钢铁公司把实时气体监测作为环保投入的一部分,以期达到国家环保要求。
因此,对于钢铁企业来说,气体实时分析技术是十分重要的。
气体实时分析技术采用不同种类的传感器和分析仪器嵌入在钢铁生产的不同环节中。
这些仪器通过收集钢铁生产时产生的各种气体,进行实时分析,并反馈给自动控制系统。
这样,系统就可以根据实时气体分析结果,自动进行调整,保证钢铁冶炼过程的持续稳定。
与以往使用的手动气体分析仪器不同,随着传感技术的日益成熟,现在的气体实时分析仪器已经具备了更加先进和精准的特点。
例如,红外线气体分析仪、拉曼光谱气体分析仪以及激光光谱气体分析仪等。
这些先进的气体分析仪器能够快速准确的实时监测钢铁生产过程中的气体组成及变化,大大提高生产效率。
而且,在钢铁冶炼过程中,随着气体温度、压力的变化,气体实时分析系统也能够快速的对这些不同环节的变化进行响应和反馈,及时进行调整,保持更加稳定和高效的生产过程。
综上所述,气体实时分析技术在钢铁冶炼过程中具有十分重要的作用。
它不仅能够有效的监测生产过程中产生的气体,确保生产过程的稳定进行,而且可以实现对钢铁公司的环保监测,保护环境,提高钢铁公司在可持续发展方面的形象和效益。
浅谈铸钢中气体含量分析现状及发展
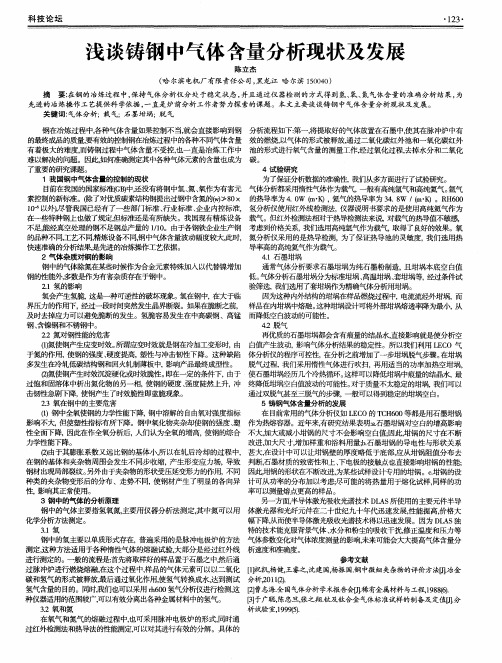
・ 1 2 3 ・
浅谈铸钢 中气体 含量分析 尔滨电机厂有 限责任公 司, 黑龙 江 哈 尔滨 1 5 0 0 4 0 ) 摘 要: 在钢 的冶炼过程 中, 保持 气体分析仪 分处于稳 定状态 , 并且通过仪 器检 测的方式得到氢、 氧、 氮气体含量 的准确 分析 结果 , 为 先进的 台 炼操作工 艺提供科 学依 据 , 一直是 炉前分析 工作者努力探 索的课题 。本文主要谈谈铸钢 中气体含量分析现状及发展 。 关键词: 气体 分析 ; 载 气:石墨坩埚; 脱 气 钢在冶炼过程中, 各种气体含量如果控制不 当, 就会直接影响到钢 分析流程如下: 第一, 将提取好的气体放置在石 墨中, 使其在脉 冲炉中有 的最终成品的质量要 有效的控制钢在冶炼过程中的各种不同气体含量 效 的燃烧, 以气体 的形式被释放, 通过二氧化碳红外池和一氧化碳红外 有着极大的难度, 而铸钢过程中气体含量不受控, 也一直是冶炼工作中 池 的形式进行氧气含量的测量工作, 经过氧化过程, 去掉水分和二氧化 难以解决的问题。因此, 如何准确测定其中各种气体元素的含量也成为 碳 。 了重要的研究课题 。 4试 验研 究 1我国钢 中气体含量的控制的现状 为了保证分析数据的准确性, 我们从多方面进行了试验研究。 目前在我国的国家标准( G B ) 中, 还没有将钢中氢 、 氮、 氧作为有害元 气体分析都采用情 陆气体作为载气, 一般有高纯氩气和高纯氦气。 氩气 素控制的新标准。滁 了对优质碳素结构钢提出过钢中含氮的( w ) >8 0 × 的热导率为 4 . 0 W( m・ , 氦气的热导率为 3 4 . 8 W/ f m・ 。R H 6 0 0 1 0 以外 尽管我国已经有了一些部 门标准、 行业标准 、 企业 内控标准, 氢分析仪使用红外线检测法, 仪器说明书要求的是使用高纯氦气作为 在—些特种钢上也做了规定胆标准还是有所缺失。我国现有精炼设备 载气 。但红外检测法相对于热导检测法来说 对载气的热导值不敏感, 不足. 台 色 经真空处理的钢不足钢总产量的 1 / 1 0 。由于各钢铁企业生产钢 考虑到价格关系, 我们选用高纯氩气作为载气, 取得了良好的效果 。氧 的品 种不同, 工艺不同捕 炼设备不同期 中气体含量波动幅度较大, 此时, 氮分析仪采用的是热导检测,为了保证热导池的灵敏度, 我们选用热 快速准确的分析结果, 是先进的冶炼操作工艺依据。 导率高的高纯氦气作为载气。 2气体杂质对钢的影响 4 . 1石 墨坩 埚 钢 中的气体除氮在某些时候作为合金元素特殊加入 以代替镍增加 通常气体分析要求石墨坩埚为纯石墨粉制造, 且坩埚本底空 白 值 钢的性能外, 多数是作为有害杂质存在于钢中。 低。 气体分析石墨坩埚分为标准坩埚、 高温坩埚、 套坩埚等, 经过条件试 2 . 1氢的影响 验筛选, 我们选用了套坩埚作为精确气体分析用坩埚。 氢会产生氢脆 这是一种可逆性的破坏现象。氢在钢中, 在大于临 因为这种内外结构 的坩埚在粥 品燃烧过程 中, 电流流经外坩埚,而 界压力的作用下, 经过一段时间突然发生晶界断裂。如果在脆断之前, 样品在 内坩埚中熔融。 这种坩埚设计可将外部坩埚熔透率降为最小, 从 及时去掉应力可以避免脆断 的发生。氢脆容易发生在中高碳钢 、高锰 而降低空白波动的可能性。 钢、 含镍钢和不锈钢中。 4 . 2脱气 2 . 2氮对钢性能的危害 再优质的石墨坩埚都会含有痕量的结晶水 ’ 直接影响就是使分析空 ( 1 岚 使钢产生应变时效。 所谓应变时效就是钢在冷加工变形时, 由 白值产生波动, 影 响气体分析结果 的稳定 l 生。所以我们利用 L E C O 气 于氮的作用, 使钢的强度 、 硬度提高, 塑性与冲击韧性下降。这种缺陷 体分析仪的程序可控性, 在分析之前增加了一步坩埚脱气步骤。 在坩埚 多发生在冷轧低碳结构钢和回火轧制薄板 中, 影响产品最终成型性。 脱气过程, 我们采用惰性气体进行吹扫, 再用适当的功率加热空坩埚, ( 2 】 氮使钢产生时效沉淀硬化或时效胞 。 即在一定的条件下,由于 使石墨坩埚经历几个冷热循环。 这样可以降低坩埚中痕量的结晶水, 最 过饱和固溶体中析出氮化物 的另一相, 使钢的硬度 、 强度陡然上升, 冲 终降低坩埚空 白值波动的可能性。 对于质量不太稳定的坩埚, 我们可以 击韧 陛急剧下降, 使钢产生了时效胞 陛即蓝脆现象。 通过双脱气甚至三脱气的步骤, 一般可以得到稳定的坩埚空白。 2 . 3氧在钢中的主要危害 5铸钢气体含量分析的发展 ( 1 )钢中全氧使钢的力学 陛能下降, 钢中溶解的自由氧对强度指标 在 目前常用的气体分析仪如 L E C O的 T C H6 0 0 等都是用石墨坩锅 影响不尢 但使塑性指标有所下降。钢中氧化物夹杂却使钢的强度 、 塑 作为热熔容器。近年来洧 研究结果表明 石墨坩锅对空 白的增高影响 性全面下降 因此在作全氧分析后, 人们认为全氧的增高, 使钢 的综合 不大, 加大或减小坩锅的尺寸不会影响空白值洇 此, 坩锅 的尺寸在不断 力学 I 生 能下降。 改进, 加大尺寸, 增加样重和浴料用量; h 石墨坩锅的导电性与形状关 系 ( 2 ) 由于其膨胀系数又远 比钢的基体小, 所以在轧后冷却 的过程中, 甚大, 在设计 中可以让坩锅壁的厚度略低于底部应 从坩锅阻值分布去 在钢的基体和夹杂物周 围会 发生不同步收缩, 产生形变应力场, 导致 判断, 石墨材质 的致密 『 生 和上、 下电极的接触 也直接影响坩锅的性能; 钢材出现局部裂纹。 另外由于夹杂物的形状受压延变形力的作用, 不 同 因此, 坩锅的形状在不断改进, 为某些试样设计专用 的坩锅。c . 坩锅的设 种类的夹杂物变形后 的分布、走势不同, 使钢材产生了明显的各 向异 计可从功率 的分布加以考虑; 尽可能的将热量用 于熔化试样, 同样的功 性, 影响其正常使用。 率可以测量熔点更高的样品。 3钢中的气体的分析原理 另一方面’ 半导体激光吸收光谱技术 D L A S 所使用的主要元件半导 钢 中的气体主要指氢氧氮, 主要用仪器分析法测定, 其中氮可以用 体激光器和光纤元件在二十世纪九十年代迅速发展, 性能提高, 价格大 化学分析方法测定 。 幅下降从 而使半导体激光吸收光谱技术得以迅速发展。因为 D L A S 独 3 . 1氢 特的技术能克服背景气体 、 水分 和粉尘 的吸收干扰修 正温度和压力等 钢中的氢主要以单质形式存在, 普遍采用的是脉冲电极炉的方法 气体参数变化对气体浓度测量的影响, 未来可能会大大提高气体含量分 测定, 这种方法适用于各种 隋性气体的熔融试验, 大部分是经过红外线 析速度和准确度。 进行测定的。一般的流程是: 首先将取样好的样品置于石墨之中然 后通 参考文献 过脉 冲炉进行燃烧熔融, 在这个过程中, 样品的气体元素可 以以二氧化 [ 1 凯, 杨健, 王睿之, 沈建国, 杨振 国. 钢 中微细夹杂物的评价方法叨 . 冶金 碳 和氢气的形式被释放, 最后通过氧化作用, 使氢气转换成水, 达到测试 分析2 0 1 1 ( 2 ) . 氢气含量的目的。同时戒 们也可以 采用 r h 6 0 0 氢气分析仪进行检测, 这 [ 2 ] 曹志海. 全 国气体分析学术报告会切. 稀有金属材料与工程, 1 9 8 8 ( 6 ) . 种仪器适用 的范围较广, 可以有效分离出各种金属材料中的氢气。 [ 3 ] 于广聪 , 陈忠旦 , 张之 翔 . 钛及 钛 合金 气体标 准 试样 的 制备 及 定值 明. 分 3 . 2氧和氮 析试验室, 1 9 9 9 ( 5 ) . 在氧气和氮气 的熔融过程中, 也可采用脉冲电极炉的形式, 同时通 过红外检测法和热导法的性能测定, 可以对其进行有效的分解。具体的
冶金学3炼钢的基本任务
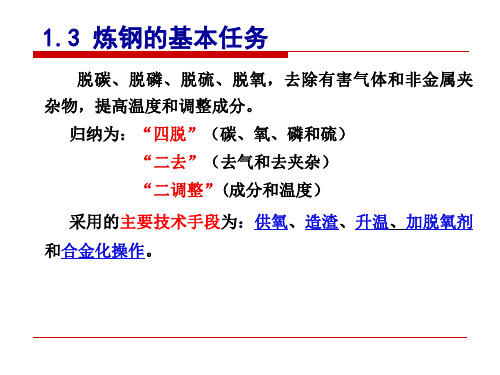
[Mn]/[S]比对低碳钢热延展性的影响
硫还会明显降低钢的焊接性能,引起高温龟裂,并在焊缝中产生气孔和疏松, 从而降低焊缝的强度。硫含量超过0.06%时,会显著恶化钢的耐蚀Байду номын сангаас。硫还 是连铸坯中偏析最为严重的元素。
不同钢种对硫含量有严格的规定: ●非合金钢中普通质量级钢[S]≤0.045%; ●优质级钢[S]≤0.035%; ●特殊质量级钢[S]≤0.025%; ●有的钢种要求如管线钢[S]≤0.005%。 有些钢种,如易切削钢硫则作为合金元素加入,要求 [S]=0.08%-0.20%。
钢中的氧
在吹炼过程中,向熔池供入了大量的氧气,到吹炼终点时,钢水中含有过量的 氧,即钢中实际氧含量高于平均值。如不脱氧,在出钢、浇铸中,温度降低, 氧溶解度降低,促使碳氧反应,钢液剧烈沸腾,使浇铸困难,得不到正确凝固 组织结构的连铸坯。
钢中大部分内生夹杂是在脱氧和凝固过程中产生的。 由于夹杂对钢的性能产生严重的影响,因此在炼钢、精炼和连铸过程应
最大限度地降低钢液中夹杂物的含量,控制其形状、尺寸。
根据成分不同,夹杂物可分为:
氧化物夹杂,即 FeO、MnO、SiO2、Al2O3 、Cr2O3等简单氧化物; FeO-Fe2O3 、FeO-Al2O3、MgO-Al2O3等尖晶石类和各种钙铝的复杂氧化物; 2FeO-SiO2,、2MnO-SiO2、 3MnO-Al2O3-2SiO2等硅酸盐;
131钢中的磷磷是仅次于硫在钢的连铸坯中偏析度高的元素而且在铁固熔体中扩散速率很小因而磷的偏析很难消除从而严重影响钢的性能所以脱磷是炼钢过程的重要任务之一
氩气在炼钢生产中的应用
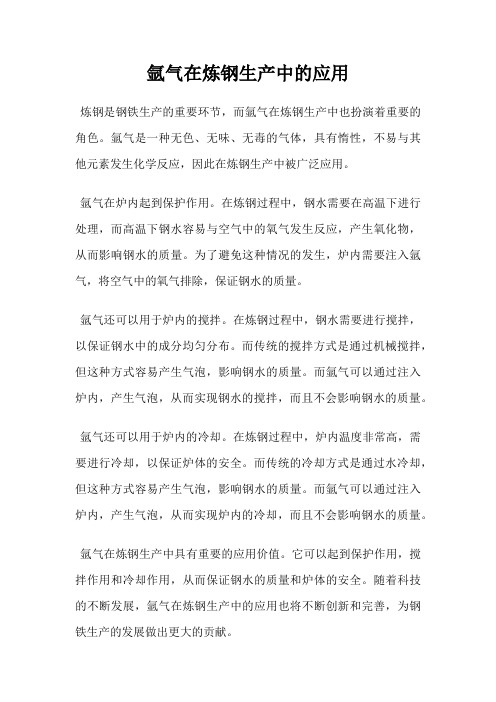
氩气在炼钢生产中的应用
炼钢是钢铁生产的重要环节,而氩气在炼钢生产中也扮演着重要的角色。
氩气是一种无色、无味、无毒的气体,具有惰性,不易与其他元素发生化学反应,因此在炼钢生产中被广泛应用。
氩气在炉内起到保护作用。
在炼钢过程中,钢水需要在高温下进行处理,而高温下钢水容易与空气中的氧气发生反应,产生氧化物,从而影响钢水的质量。
为了避免这种情况的发生,炉内需要注入氩气,将空气中的氧气排除,保证钢水的质量。
氩气还可以用于炉内的搅拌。
在炼钢过程中,钢水需要进行搅拌,以保证钢水中的成分均匀分布。
而传统的搅拌方式是通过机械搅拌,但这种方式容易产生气泡,影响钢水的质量。
而氩气可以通过注入炉内,产生气泡,从而实现钢水的搅拌,而且不会影响钢水的质量。
氩气还可以用于炉内的冷却。
在炼钢过程中,炉内温度非常高,需要进行冷却,以保证炉体的安全。
而传统的冷却方式是通过水冷却,但这种方式容易产生气泡,影响钢水的质量。
而氩气可以通过注入炉内,产生气泡,从而实现炉内的冷却,而且不会影响钢水的质量。
氩气在炼钢生产中具有重要的应用价值。
它可以起到保护作用,搅拌作用和冷却作用,从而保证钢水的质量和炉体的安全。
随着科技的不断发展,氩气在炼钢生产中的应用也将不断创新和完善,为钢铁生产的发展做出更大的贡献。
- 1、下载文档前请自行甄别文档内容的完整性,平台不提供额外的编辑、内容补充、找答案等附加服务。
- 2、"仅部分预览"的文档,不可在线预览部分如存在完整性等问题,可反馈申请退款(可完整预览的文档不适用该条件!)。
- 3、如文档侵犯您的权益,请联系客服反馈,我们会尽快为您处理(人工客服工作时间:9:00-18:30)。
钢中气体 (gases in steel)溶解于钢中的氢和氮的通称。
有的把溶解于钢中的氧也看作钢中气体,但氧在钢凝固时大多成为非金属夹杂物析出,所以对钢中氧的问题往往和非金属夹杂问题一并考虑,而不归入钢中气体范畴来研究。
钢中气体常造成钢的一些缺陷如白点、气孔、裂纹等,氮还促使低碳钢发生时效硬化和蓝脆,所以在炼钢时要尽量降低钢中气体。
只有极特殊情况下,利用氮能扩大奥氏体区这一特点,把氮作为奥氏体化合金元素来利用,例如锰氮奥氏体不锈钢。
气体在钢中的溶解度氢和氮在大气中都以双原子的气体存在,高温下则都分解成单原子溶解。
气体接触到固态或液态的表面后产生物理吸附,当气体和钢的表面分子结合力大于气体内部分子的结合力时发生化学吸附,吸附的分子可以分解成原子,由钢的表面扩散到内部。
由于氢、氮的原子半径r x (分别为0.046和0.071nm)比铁的原子半径r Fe (0.126nm)小,其比值r x / r Fe 小于0.59,它们占据固体晶体点阵的间隙位置,形成间隙固溶体,若钢中存在的合金元素(如Ti、Al等)能与氮发生反应时就产生氮化物;当钢中存在微孔隙或气孔、缩孔时,过饱和气体也能以分子状态析于这些孔隙中。
气体在液体或固体铁中的溶解度与温度和外界气体分压力有关,当温度一定时气体溶解度和分压的平方根成正比,此即西韦特(Sievert)定律(也称平方根定律),氢、氮的溶解反应可写成:式中K H,K N为平衡常数,其数值和气相分压力为1atm(101325Pa)时的溶解度数相等;[%H]、[%N]为某一气压下的溶解度值,a[H]、a[N]为氢、氮的活度,f H 、f N为氢、氮的活度系数。
图1给出了不同温度下氢、氮在α、γ、δ液体铁中的溶解度。
从图1看出,随温度上升溶解度线性增加,为吸热反应,只有氮在奥氏体(γ-Fe)温度(910~1390℃)范围内,溶解度随温度的升高而降低,为放热反应。
冶炼不同钢种时向钢液加入铁合金,由于成分的变化不仅改变钢的相变温度、组织状态,也改变了钢液中的气体溶解度。
在冶炼温度下合金元素含量对氢、氮活度系数的影响见图2、图3。
降低f H(3)、f N(3)活度系数的元素都增大钢液中气体的溶解度,增加活度系数的元素则减小钢液中气体的溶解度,用具体成分下气体的活度系数可计算出不同外界气相分压下达到平衡时的气体含量。
氮和一些元素在冶炼温度下形成氮化物,其结合能力的强弱可由平衡常数K N表示,炼钢温度下各元素的脱氮反应常数K N与温度的关系和1600℃、1550℃时的K N 。
值见表1,可近似地用强脱氮反应的平衡常数估算残存的[N]值。
凝固后钢中溶解的氮量和产生的氮化物也可由该温度下的平衡常数计算和估量。
气体对钢的危害普通的炼钢方法在高温冶炼过程吸收了较多的氢和氮,在钢凝固后溶解的氢和氮呈饱和状态。
一些钢种含有与氮结合力强的元素还会生成氮化物。
凝固时外层已凝固的钢中的气体向未凝的内部扩散(由于固相气体溶解度低),聚集在疏松的局部地区或中心的孔隙中。
氢在铁液中的扩散系数(10-3cm2 /s)比氮的(10-4 cm2/s)大一个数量级,氮比其他合金元素Cr、Cu、Co、Ni、Mo等的扩散系数(约1×10-5 cm2/s)又大一个数量级,因此钢中气体很易偏析,氢气的偏析最大,对钢品质的影响也最严重,是形成钢中白点、发纹、气孔等缺陷的主要原因。
微孔隙中的氢在低温时产生很大的氢气分压力,致使孔隙周边钢中溶解了大量的氢,故钢的韧性显著降低,再加上低温时钢本身的相变应力,使钢产生不同方位的细微裂纹,在轧制、锻造材的纵向断口上呈现白点,这类钢不能交付使用。
冶炼和浇注常温呈铁素体组织的钢(如变压器钢,[si]≈4%)时,因固相(铁素体)和液相氢的溶解度相差很大,易产生偏析聚集,严重时钢锭(坯)易产生气泡或上涨等现象,生产奥氏体组织的钢时则很少产生气泡或上涨现象。
表1各元素的脱氮反应常数与温度的关系及1600℃和1550℃的K N值注:K N =[E][N];E为合金元素。
钢中气体来源钢中氢的来源是水汽、燃气或燃油中碳氢化合物的燃烧产物(H2O),用木耙扒渣时的燃烧产物(H2O),砌制盛钢桶、中间罐等使用的黏结剂中的水分以及补炉和打结炉衬的焦油沥青等碳氢化合物都会增加钢中的氢气。
钢铁料、合金剂、脱氧剂等的表面的含水量也是钢中氢的来源。
但冶炼中影响最大的是石灰中的水分。
石灰的吸水性能很强,能生成Ca(0H)2,在炉内烘烤到507℃才能完全解离,故冶金生产必须采用新焙烧的石灰,转炉生产常使用新焙烧的活性石灰并用管道输送。
大气中氢气的分压力(约0.053Pa)很低,故不构成钢中氢的来源。
在炉内生成的H2O气分压力与使用原材料的干燥程度、炉衬使用次数等因素有关。
高温下H2O的分解反应为H2O=H2+1/2O2 lgK=-1 3130/T+3.041650℃时H2约占H2O分解量的0.3%。
在还原气氛下由H2O反应生成的H2量更大,反应式如下:CO2+H2=CO+H2O lgK=-1430/T+1.382 在1650℃时K=4035,pCO/pCO2=10时,pH2/pH2O=2.3,由此可见在还原气氛下(如电炉还原期),H2O气分压力大,钢中溶解氢的数量显著增大。
钢液和水汽接触时按下式进行反应:H2O=2[H]+[O]达到平衡时的平衡常数K为lgK=lg[H]2[O]/pH2O=-10850/T+8.01脱氧良好的钢液有很强的吸氢能力。
应避免使用新砌的、潮湿的钢包。
钢中氮气的主要来源是大气中的氮,大气中的氮为0.79×105Pa(0.78atm),进入炉气中的氮可在裸露的钢液面上溶于钢液内。
也可溶解于炉渣再传递到钢液内。
在电弧炉冶炼时电弧温度可达4000~7000℃,使炉中气体(H2O、N2、H2)大量分解成原子或离子状态,因此加快了高温区氢、氮向渣中的溶解速率和数量,并随炉内还原性的增强而增大,一般溶解氢、氮是通过炉渣溶解的,故一般渣中气体含量高于和钢液平衡的数量,如果采用钢渣混出方式出钢,盛钢桶中的钢液能充分吸收渣中气体。
出钢浇注时钢液表面吸收空气中的N2、H2O、O2,脱氧好、含碳低的钢液吸气较多。
浇注时被卷入到钢液中的空气气泡(上注或下注等),由于气泡单位体积接触到的钢液面很大,吸气(氮、氢、氧)很快,故在浇注时常采用氩气保护浇注、长水口浇注等措施。
表2为不同方法生产的钢中气体含量。
表2不同冶炼方法和不同钢种的钢中气体含量钢液的脱气用普通方法冶炼时,常采用脱碳反应作为去气的手段,转炉、平炉、电炉操作中的脱碳对降低钢中气体含量起着非常积极的作用。
一般转炉和平炉的脱碳量很大,有较好的脱气效果,在脱碳量较少的电炉操作中要规定合适的脱碳量,因为它影响着冶炼时间、耗电量和原材料的消耗,直接和产量、成本有关。
对气体含量要求严格的钢种,还要经过真空处理、炉外精炼等工艺操作。
脱气反应有3个环节:(1)溶解的气体由液相向气一液界面传质;(2)在气一液界面上进行化学反应;(3)由气一液界面向气相传质而逸出。
第2环节化学反应进行的很迅速;第3环节由于气相中反应气体的分压力很低,传质的驱动力很大,速率也较快;故而第1环节液相传质是脱气反应的限制环节。
要提高脱气效果就必须加强搅拌提高传质系数,同时要有效增大反应的界面积。
用铁矿石、氧化铁皮等氧化钢液脱碳时,氧通过炉渣向钢液溶解,在钢液中进行脱碳反应并生成CO气泡,在CO气泡表面产生脱气反应。
因为CO气泡中氢、氮的分压力接近于零,故在气-液界面处发生[H]=1/2H2和[N]=1/2N2反应,H2和N2随CO上浮排出,而使钢中气体含量降低。
同理向钢液吹入氩气也可去除气体。
熔池的吹氧脱碳使钢液中CO气泡带有氧化性,界面处又增加了氧化脱氢反应2[H]+1/2O2=H2O。
同理向熔池吹入CO2 时,界面处也会产生氢的氧化反应,这些都有利于钢液的脱气。
钢液的脱气速率决定于脱碳速率和钢液的原始气体含量。
因为氢在钢液中的扩散系数很大,沸腾钢液又提高了氢的传质系数,可假设由钢液放出的CO和H2气之比和由钢液成分决定的平衡气相分压力之比成正比,即式中V H2、V CO为钢液中放出气体的体积;p H2 、p CO为由钢液中元素的含量决定的平衡压力,通过公式推导,代入p CO=0.15MPa、K H=0.00268(为1600℃时p H2=0.1MPa时的值),得到钢液的脱氢速率v%/min)和脱碳速率V[C](%/min)及它们与[H]2成正比的关系[H] (式:为了加速脱氢应提高脱碳速率,在氢含量降低时因为平衡的氢分压降低,脱氢速率减慢,从实际冶炼分析,电炉氧化末期钢液最低的氢含量约为0.0002%。
吹氩可以脱除钢液的氢和氮,一些要求气体较严的钢种多采用钢包底部吹氩。
一是氩气泡上浮经过的钢液距离大,再者经透气砖进入钢液的氩气气泡直径小,脱气效果好。
经数量关系计算出吹氩和脱氢量的关系:式中V Ar为吹氩量,m3;Q钢为钢液重,t;K H为氢在处理温度时的平衡常数,P Ar为吹氩时氩气在钢水中经受的平均压力(钢液高的1/2处经受的压力),[%H]1,、[%H]2为吹氩前后钢液中的氢含量。
从上式不难算出吹氩量和脱氢量的关系。
钢液在真空下有一定的脱气效果。
不同的真空处理设备脱气效果是有区别的,关键是要保持在真空下的钢液比表面积(单位重量钢液的表面积)。
真空脱气的钢液分为两类,一类是未脱氧的钢液,主要靠外界压力降低促进碳氧反应,使产生的CO气泡和钢液接触面积扩大,促进了脱氧、脱氢和脱氮;另一类是用铝或其他脱氧剂脱氧后,在真空下进行脱气反应。
实践表明真空下的脱氢效果远优于脱氮的效果。