上一章我们讲了机床夹具设计基础
第四章 机床夹具设计基础

•设计合理的定位方法、定位装置 •有足够的定位精度
六点定位原理
2、 六点定位原理
用适当分布的六个支承点消除 工件的六个自由度,使工件在夹具 中位置完全确定,这个原理称为六 点定位原理。(图示)
图2.36 工件在空间的自由度与工件六点定位
六点定位原理
1)定位支承点是定位元件抽象而来的。 2)定位支承点与工件定位基准面始终保持接触, 才能起到限制自由度的作用。 3)分析定位支承点的定位作用时,不考虑力的 影响。
(三)钻床夹具
在钻床上进行孔的钻、扩、铰、锪、攻螺纹加工所 用的夹具,称为钻床夹具。钻床夹具是用钻套引导刀 具进行加工的,所以简称为钻模。
1、钻床夹具的分类
钻床夹具的种类繁多,根据被加工孔的分布情 况和钻模板的特点,一般分为固定式、回转式、移动 式、翻转式、盖板式和滑柱式等几种类型。
1)固定式钻模
5)连接定向元件: 将夹具与机床连接并确定夹具对机床主 轴、工作台或导轨的相互位置。
6)其它装置或元件 根据加工需要,有些夹具上还设有分度 装置、靠模装置、上下料装置、工件顶出机 构、电动扳手和平衡块等,以及标准化了的 其它联接元件。
二、工件在夹具中的定位
1.自由度的概念
定位的任务
定位的原理
(4)安全可靠原则 (5)经济实用原则
3. 夹紧力作用点的选择
1)夹紧力的作用点应正对支承元件或位于支承元件所 形成的支承平面内(图2); 2)夹紧力的作用点应位于工件刚性较好的部位(图3) 3)夹紧力的作用点应尽量靠近加工面,以减小切削力对 夹紧作用点的力矩,防止或减小工件的加工振动或弯曲 变形(图5)。
三、常见定位方式与定位元件
工件在夹具中要想获得正确定位,首先应正确选 择定位基准,其次是选择合适的定位方式、定位元件。
机械制造工艺学:第三章 机床夹具设计 第四节 各类机床夹具
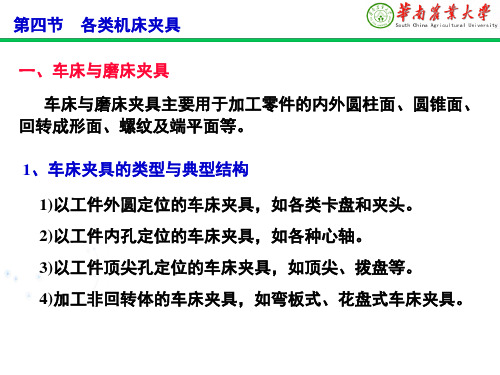
过渡盘与主轴端部是用短锥 和端面定位,夹具体用止口与 过渡盘定位(大平面加短圆柱 面),用螺钉夹紧。
3磨床夹具 车床夹具的设计要点同样适
合于内圆磨床和外圆磨床所用 的夹具
二、钻床夹具
1、钻模的类型与典型结构
钻床夹具因大都具有刀具导向装置,习惯上又称为钻模。钻 模一般由钻模板、钻模套、定位元件、夹紧装置和钻模体等组 成。
一、车床与磨床夹具
一、车床与磨床夹具
2、车床夹具的设计要点 1)车床夹具总体结构
夹具结构应尽量紧凑,重心应尽量靠近主轴端。对于弯板式 和偏重的车床夹具,应进行配重调平衡。
2)夹具与机床的联接 联接方式取决于主轴轴端的结 构以及夹具的体积和精度要求
⑴用莫氏锥度配合 夹具体以长锥柄安装
在主轴孔内,其定位精度 高,定位迅速方便,但刚 度低,适于轻切削。
1、钻模的类型与典型结构
翻转式钻模 固定式钻模板 快换钻套
1、钻模的类型与典型结构
盖板式钻模 固定钻套
2、钻模设计要点
1)钻套 刀具引导元件,装在钻模板上,确定刀具的位置和方向,
⑴钻套类型:固定钻套、可换钻套、快换钻套、特殊钻套 ⑵钻套的尺寸和公差
钻套内径根据所用刀具的外径来确定;钻套的高度H影响钻 套的导向性能,同时影响刀具与钻套之间的摩削情况;钻套与 工件之间应留有间隙 2)钻模板
钻模板用于安装钻套,与夹具体的联接方式有固定式、铰链 式、分离式和悬挂式等几种。
3)夹具体 整个夹具的基础零件,一般多为铸件,也可用焊接件。夹具
通过夹具体底面安放在钻床工作台上,可直接用钻套找正并用压 板压紧(或在夹具体上设置耳座用螺栓压紧)。
三、镗床夹具
镗床夹具简称镗模,主要由镗套、镗模支架、镗模底座、以 及必需的定位、夹紧机构组成,多用于在镗床、组合机床(也可 在车床和摇臂钻床)上加工箱体、支座等零件上的精密孔或孔系。 与钻模有很多相似之处。
第三章 机床夹具设计基础

四、定位误差及其计算
(2)基准不重合误差ΔB
由于定位基准与工序基准不重合而造成的定 位误差,称为基准不重合误差,以ΔB表示 。
定位误差由基准位移误差和基准不重合误差组成。
64
四、定位误差及其计算
二、定位误差的计算
定位误差由基准不重合误差与基准位 移误差两项组合而成。计算时,先分别算 出ΔB和ΔY,然后将两者组合而成ΔD 。
正确的 定位形式
不正确的
定位形式
4、过定位:有重复限制的自由 度。
视情况
而定
20
练习:对本工序的加工选择定位基准,并分别确定 应限制的自由度数
21
22
23
下列定位方式中有无过定位,如果有,怎样改正?
24
三、常见定位方式及定位元件
复习
1、定位基准和定位基面
2、限位基准和限位基面
3、定位符
25
定位套
48
三、常见定位方式及定位元件
V型块
a)
b)
c)
d)
49
三、常见定位方式及定位元件
50
三、常见定位方式及定位元件
51
三、常见定位方式及定位元件
4、一个平面和与其垂直的两个孔组合
52
三、常见定位方式及定位元件
解决办法是: 将销2做成
削边销
53
三、常见定位方式及定位元件
• 采用一面两孔定位时,圆柱销、菱形销的 主要参数确定如下: • 1)圆柱销直径d1的基本尺寸及公差
32
三、常见定位方式及定位元件
辅助支承
具有浮动或联动结构,具备自位功能。用于定位基
面不连续或台阶面、有角度误差等场合。
33
三、常见定位方式及定位元件
第三章机床夹具基础
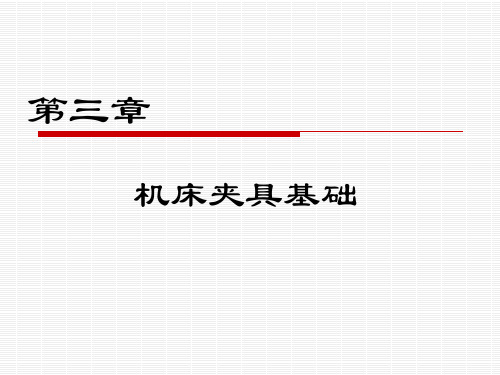
(6)其他元件及装置。
3.2 工件定位基本原理
3.2.1 六点定位规则
工件在空间具有6个独立的运 动 方,向即的6移个动自自由由度度:x 3、个y、z坐和标转 动自由度 x、y、z,如图3-2所 示。如使工件在空间占有确定 的位置,就必须按一定的要求 布置6个支承点(及定位元件) 来限制工件的6个自由度,这 图3-2 工件在空间的自由度 就是工件的“六点定位原理”。
图3-14 圆孔用锥销定位
3.2.2 常用定位方式及定位元件
(3)定位心轴。定位心轴有刚性心轴、弹性心轴、液性塑 料心轴等。下面介绍刚性心轴。
④ 组合夹具。组合夹具是指按零件的加工要求,由一 套事先制造好的标准元件和部件组装而成的夹具。由专 业厂家制造,其特点是灵活多变,万能性强,制造周期 短,元件能反复使用,特别适用于新产品的试制和单件 小批生产。
3.1.2 机床夹具的分类与组成
1.机床夹具的分类 (2)按使用的机床分类。
由于各类机床自身工作特点和结构形式各不相同, 对所用夹具的结构相应提出了不同的要求。按所使 用的机床不同,夹具可分为车床夹具、铣床夹具、 钻床夹具、镗床夹具、磨床夹具、齿轮机床夹具和 其他机床夹具等。 (3)按夹紧动力源分类。 根据夹具所采用的夹紧动力源不同,可分为手动夹 具、气动夹具、液压夹具、气液夹具、电动夹具、 磁力夹具和真空夹具等。
3.2.1 六点定位规则
1.工件自由度与加工要求的关系 工件定位时,影响加工要求的自由度必须限制,不影响加工精度的 自由度不必限制。
1)完全定位与不完全定位 工件的6个自由度全部被限制的定位称为完全定位。 工件被限制的自由度少于6个,但不影响加工要求的定位称为不完 全定位。
第二章_机床夹具设计基础2
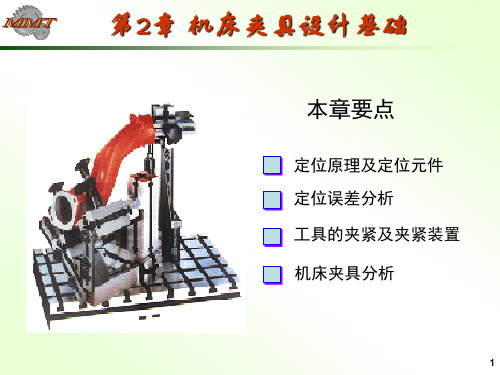
2.2 定位原理及定位元件
2.2.1 定位原理
2、限制工件自由度与加工要求的关系
Z
Z
Z
X
Z, X, Y
Z
Y
X 除X
Z
Y
Y
X
全部
Z
X X, Y
Y
Y
X
X
除X,X
工件应限制的自由度
除X
Y 32
2.2 定位原理及定位元件
2.2.1 定位原理
分析自由度的方法
(a)明确工序加工要求(包括工序尺寸和位置精度)与对应的工序基准 (b)建立空间直角坐标系
6
2.1 概述
2.1.1 夹具的作用
扩大机床的加工范围 根据加工机床的成形运动,附以不同类型的夹具,
即可扩大机床原有的工艺范围。例如在车床的溜板上 或摇臂钻床工作台上装上镗模,就可以进行箱体零件 的镗孔加工。 减轻工人劳动强度
可用气动、电动夹紧。
7
2.1 概述
2.1.2 夹具的分类
① 通用夹具
➢ 夹紧装置:用于夹紧工件,在切削时使工件在夹具中保持既定 位置。如图的螺母、开口垫圈;
➢ 导向元件和对刀元件:这些元件的作用是保证工件与刀具之间 的正确位置。用于确定刀具在加工前正确位置的元件,称为对 刀元件,如对刀块。用于确定刀具位置并导引刀具进行加工的 元件,称为导向元件,如钻套;
➢ 连接元件:使夹具与机床相连接的元件,保证机床与夹具之间 的相互位置关系。
29
2.2 定位原理及定位元件
2.2.1 定位原理
2、限制工件自由度与加工要求的关系
图(a) 加工不通槽。称为完全定位。 图(b)在工件上加工通槽,不需要保证y,只需限制其它五个自由度。 图(c) 加工平面,不需要保证尺寸x、y,不必限制x、y方向的移动和 z 方向的旋转自由度,只需限制其它三个自由度。 图(b)和(c)称为不完全定位。
机床夹具设计基础

机床夹具设计基础第一篇:机床夹具设计基础机床夹具设计基础一、选择题1.用(b)来限制六个自由度,称为(c)。
根据加工要求,只需要少于(b)的定位,称为(d)定位。
a.六个支承点;b.具有独立定位作用的六个支承点;c.完全;d.不完全;f.欠定位 2.只有在(b)精度很高时,过定位才允许采用,且有利于增强工件的(d)。
a.设计基准面和定位元件;b.定位基准面和定位元件;c.夹紧机构;d.刚度;e.强度3 定位元件的材料一般选(adf)a.20钢渗碳淬火;b.铸铁;c.中碳钢;d.中碳钢淬火;e.合金钢;f.T>A钢 3.自位支承(浮动支承)其作用增加与工件接触的支承点数目,但(b)a.不起定位作用;b.一般来说点限制一个自由度;c.不管如何浮动必定只能限制一个自由度4.工件装夹中由于(a)基准和(e)基准不重合而产生的加工误差,称为基准不符误差a.设计(或工序);b.工艺;c.测量;d.装配;e.定位 5.基准不符误差大小与(b)有关。
a.本道工序要保证的尺寸大小和技术要求;b.只与本道工序设计〔或工序)基准与定位基准之间位置误差;c.定位元件和定位基准本身的制造误差。
6.在简单夹紧机构中(e)夹紧机构一般不考虑自锁;(d)夹紧机构既可增力又可减力;(c)夹紧机构实现工件定位作用的同时,并将工件夹紧;(b)夹紧机构行程不受限制。
(ade)夹紧机构能改变夹紧力的方向,(a)夹紧机构夹紧行程与自锁性能有矛盾。
(f)夹紧机构动作迅速,操作简便。
a.斜楔;b.螺旋;c.定心;d.杠杆;e.铰链;f.偏心7.偏心轮的偏心量取决于(c)和(e),偏心轮的直径和(a)密切有关。
a.自锁条件;b.夹紧力大小;c.工作行程;d.销轴直径;e.工作范围;f.手柄长度 8.在多件夹紧中,由于(e),因此一般采用(c),夹紧才能达到各工件同时被夹紧的目的。
a.多点;b多向;c.浮动;d.动作联动;e.各工件在尺寸上有误差;f.连续式或平行式夹紧。
机械制造基础第4章 机床夹具设计基础——例题
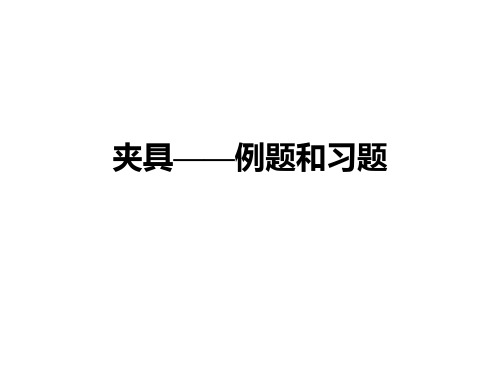
的限制。以避免重复
三爪卡盘夹持较短
X Y Z Y Z
Y Z
属于不完全定位, 如果只加工工件的外圆表面,而无轴向尺寸方面的要求,则定位是合理的, 如果工件有轴向尺寸要求时,则应该增加限制X方向移动的定位支撑点。
三爪卡盘夹持较短
X Y Z Y Z
Y Z
X
欠定位分析
过定位
如果工件的某一个自由度被定位元件重复限制,称为过定位。 过定位是否允许,要视具体情况而定。通常,如果工件 的定位面经过机械加工,且形状、尺寸、位置精度均较高, 则过定位是允许的。合理的过定位起到加强工艺系统刚度和 增加定位稳定性的作用。反之,如果工件的定位面是毛坯面, 或虽经过机械加工,但加工精度不高,这时过定位一般是不 允许的,因为它可能造成定位不准确,或定位不稳定,或发 生定位干涉等情况。
已知:外径d为: 500 0.03 mm
内径D为: 3000.05 mm
内外圆同轴度为0.02mm,
试计算用调整法加工这批工件时,
工序尺寸H的定位误差是多少?
解: 基准不重合误差: 基准位移误差:
同轴度误差:w 来自c 0.05 0.025mm 2
TD 2 sin
2
0.03 0.021mm 90 2 sin 2
组合定位
1.几个定位元件组合起来定位时,限制的自由度是每个定位元件限 制的自由度数之和. 2.组合定位中的每个定位元件改变它单独定位所限制的自由度. 3.组合定位中,定位元件单独起限制移动自由度转为限制转动自由 度,不再起限制移动自由度,但是限制自由度数量不变. 消除组合定位中的过定位,把限制移动方向的自由度定位元件改 为能移动的定位元件. 消除组合定位中的过定位,也可以改变定位元件的结构.比如:一面 两孔中菱形销
机床夹具设计基础

点应尽量靠 近被加工表 面,以增加 夹紧的可靠 性
(3)夹紧力的大小
• 夹紧力的大小主要是根据切削力的大小来确定。 • 若太小,装夹不可靠,切削时工件位置发生位 移; • 若太大,易使工件或定位元件产生变形而降低 加工精度。
• Q=KF • K:安全系统、常取1.5-3, • 粗加工取大值, • 精加工取小值)
(二) 工件定位方法及定位元件的选择
• 1、平面定位及平面定位元件的选择
①固定支承(定位支承点的位置固定不变) (a)平头支承钉:用于已加平面; (b)球头支承钉:用于未加工平面; (c)网纹顶面支承钉,用于要求磨擦力大的侧面; (d)支承板:用于已加工后较精密的平面。 ②可调支承(定位支承点位置可调节的定位元件) ③自位支承(定位支承点的位置在工件定位过程中,随工 件定位基础位置变化而自动与适应的定位元件) • 球面三点或自位支承 杠杆两点或自位支承 • ④辅助支承(提高工件支承刚性或辅助定位的定位元件) • (a)镙母副(可能会被原定位)(b)自引式(c)升托式 • • • • • • •
(三)、夹具的分类
(A)按通用程度分类
• 1、通用夹具:
• 主要用于单件小批生产,精度一般,效率较低。如:三爪卡盘,机用 平口钳,分度头等 为工件某一工序设计的夹具。结构紧凑、工作迅速方便,适用于批量 生产,效率较高,成本较高。 按工件形状、尺寸和加工工艺的共性分组而设计的专用夹具。在通用 夹具的基础上增加专用夹具的功能,从而提高效率降低成本。 由一系列标准模块通过不同的组装实现不同装夹要求的夹具。如夹具 体,定位元件,对刀元件等,从而实现可大批量生产,也可单件小批生 产,成本低,生产准备周期短。 在自由化生产线上既承担工件的装夹,又可随自动线输送工件,从一 个工位移动下一个工位的夹具。
机械制造技术基础-第4章-机床夹具设计原理-课后答案
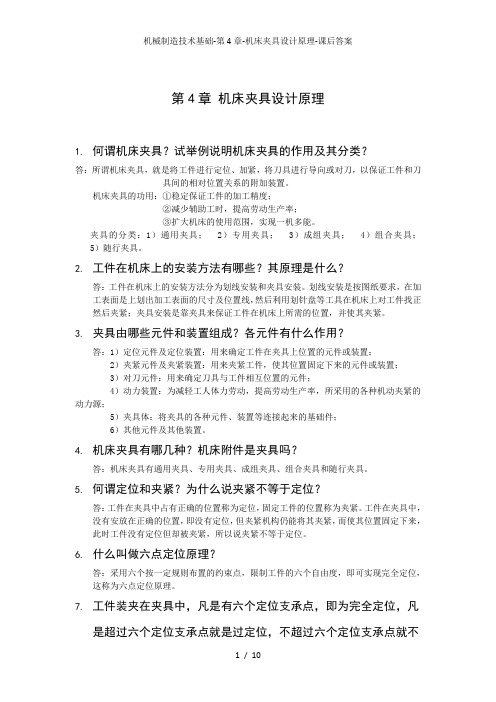
第4章机床夹具设计原理1.何谓机床夹具?试举例说明机床夹具的作用及其分类?答:所谓机床夹具,就是将工件进行定位、加紧,将刀具进行导向或对刀,以保证工件和刀具间的相对位置关系的附加装置。
机床夹具的功用:①稳定保证工件的加工精度;②减少辅助工时,提高劳动生产率;③扩大机床的使用范围,实现一机多能。
夹具的分类:1)通用夹具; 2)专用夹具; 3)成组夹具; 4)组合夹具;5)随行夹具。
2.工件在机床上的安装方法有哪些?其原理是什么?答:工件在机床上的安装方法分为划线安装和夹具安装。
划线安装是按图纸要求,在加工表面是上划出加工表面的尺寸及位置线,然后利用划针盘等工具在机床上对工件找正然后夹紧;夹具安装是靠夹具来保证工件在机床上所需的位置,并使其夹紧。
3.夹具由哪些元件和装置组成?各元件有什么作用?答:1)定位元件及定位装置:用来确定工件在夹具上位置的元件或装置;2)夹紧元件及夹紧装置:用来夹紧工件,使其位置固定下来的元件或装置;3)对刀元件:用来确定刀具与工件相互位置的元件;4)动力装置:为减轻工人体力劳动,提高劳动生产率,所采用的各种机动夹紧的动力源;5)夹具体:将夹具的各种元件、装置等连接起来的基础件;6)其他元件及其他装置。
4.机床夹具有哪几种?机床附件是夹具吗?答:机床夹具有通用夹具、专用夹具、成组夹具、组合夹具和随行夹具。
5.何谓定位和夹紧?为什么说夹紧不等于定位?答:工件在夹具中占有正确的位置称为定位,固定工件的位置称为夹紧。
工件在夹具中,没有安放在正确的位置,即没有定位,但夹紧机构仍能将其夹紧,而使其位置固定下来,此时工件没有定位但却被夹紧,所以说夹紧不等于定位。
6.什么叫做六点定位原理?答:采用六个按一定规则布置的约束点,限制工件的六个自由度,即可实现完全定位,这称为六点定位原理。
7.工件装夹在夹具中,凡是有六个定位支承点,即为完全定位,凡是超过六个定位支承点就是过定位,不超过六个定位支承点就不会出现过定位,这种说法对吗,为什么?答:不对;过定位是指定位元件过多,而使工件的一个自由度同时被两个以上的定位元件限制。
机床夹具设计基础知识

机械制造技术
课题二 工件定位的基本原理
过定位可能导致下列后果。 (1)工件无法安装 (2)造成工件或定位元件变形 由于过定位往往会带来不良后果,一般确定定 位方案时,应尽量避免。消除或减小过定位所引起 的干涉,一般有两种方法。 ①改变定位元件的结构,使定位元件重复限制自由 度的部分不起定位作用。
机械制造技术
课题一
概 述
二、夹具的分类 机床夹具的种类繁多,可以从不同的角度对机床夹具进 行分类。常用的分类方法有以下几种。 1.按夹具的使用特点分类 根据夹具在不同生产类型中的通用特性,机床夹具可分 为: (1)通用夹具 (2)专用夹具 (3)可调夹具 (4)组合夹具 (5)拼装夹具
机械制造技术
课题一
概 述
5.夹具体 夹具体是机床夹具的基础件,通过它将夹具的所 有元件连接成一个整体。 6.其它装臵或元件 它们是指夹具中因特殊需要而设臵的装臵或元 件。若需加工按一定规律分布的 多个表面时,常设 臵分度装臵;为了能方便、准确地定位,常设臵预 定位装臵;对于大型夹具,常设臵吊装元件等。
50
0.1 A B 6 .3 6.3 A
3 0 ± 0 .1
机械制造技术
课题二 工件定位的基本原理
2.不完全定位 根据工件的加工要求,并不需要限制工件的全 部自由度,这样的定位,称为不完全定位。
(a) 在车床上加工通孔
(b) 磨平面图
机械制造技术
课题二 工件定位的基本原理
3.欠定位 根据工件的加工要求,应该限制 的自由度没有完全被限制的定位,称为 欠定位。欠定位无法保证加工要求, 所以是绝不允许的。
机械制造技术
课题二 工件定位的基本原理
机械制造工艺学课程设计3夹具设计

定位元件特点
定位销 (心轴)
短销(短心轴) 长销(长心轴)
圆孔
单锥销
(续)
限制的自由度 、
、 、
、、
短圆锥销
1—固定销 2—活动销
1— 、 、 2— 、
工件定位基准面 定位元件
定位方式简图
定位元件特点
(续)
限制的自由度
支承钉或 支承板
支承板或两个支承钉
、
外圆柱面 V形块
窄V形块
、
、 宽V形块或两个窄V形块
⒈工序基准为工件轴心线
此时为定位基准与工序基准重合,则基准不重合误差为零,而基准位移 的方向又与加工尺寸方向一致,所以加工尺寸B2的定位误差为
DB2
Y
d 2sin
2
⒉工序基准为外圆上母线
此时为定位基准与工序基准不重合。不仅有基准位移误差,而且还有基 准不重合,又定位尺寸与加工尺寸方向一致,所以尺寸B1的定位误差为
的设计基准作为定位基准,以避免定位基准与 设计基准不重合而引起的基准不重合误差。
基准不重合误差示例
2)基准统一原则:应尽可能使多个加工表面 和加工工序采用同一组定位基准,这就是基准统 一原则。
3)互为基准原则:当对工件上位置精度要求高的 表面进行加工时,需要用两个表面互为基准,反复加工 的原则。
4)自为基准原则:某些要求加工余量小而均匀的 精加工工序,选择加工面本身作为定位基准,称为自为 基准原则。
(4)对刀或导向元件。 (5)夹具体。 (6)其他元件及装置。
3.机床夹具在机械加工中的作用 (1)保证加工精度。 (2)提高生产率,降低成本。 (3)扩大机床工艺范围。 (4)减轻工人的劳动强度。
夹具元件间常用的配合选择
第3章 机床夹具设计基础

以已经加工好的平面定位
School of Mechanical Engineering,Northwestern Polytechnical University
12
机械制造工艺基础
1. 工件以平面定位 (2)平面定位的定位件
A、固定支撑 B、支撑板 C、可调支撑 D、自位支撑
第3章 机床夹具设计基础
例3.2:工件定位基准尺寸是∅60++00..004610,要确定的定位孔尺寸是多少? 解:定位孔的基本尺寸是60+0.06,按G7选,则定位孔尺寸是 ∅60.06++00..00140 ,
其定位误差为 ������定位 = ������ + ∆ + ������定 = (0.06 − 0.041) + 0.01 + 0.04 − 0.01 = 0.059mm
应取定位误差在原始尺寸方向上的投影值。 因素:定位基准平面的质量、位置尺寸公差和精度。
精基准平面定位误差:很小,可忽略丌计。 粗基准平面定位误差:误差大,但尺寸公差也大,后续工序余量多,所以丌计算。
School of Mechanical Engineering,Northwestern Polytechnical University
8
机械制造工艺基础
第3章 机床夹具设计基础
3.2 工件的定位原理、定位方法和定位设计
School of Mechanical Engineering,Northwestern Polytechnical University
9
机械制造工艺基础
第3章 机床夹具设计基础
3.2 工件的定位原理、定位方法和定位设计
V形块上后,因该基准尺寸有误差,基准 轴线位置由O点到������′,基准的这种最大位 秱������������′就是定位误差 。
第四章 机床夹具设计基础

第二节 工件的定位原则及定位元件
支承钉 支承钉限制一个自由度。图示为常用的平面定位的支承钉, 利用顶面对工件进行定位。 图a平顶支承钉,用于精基准面的定位。 图b圆顶支承钉,用于粗基准面的定位。 图c齿纹头支承钉,用在要求较大摩擦力的侧面定位。 以上支承钉与夹具体孔的配合用H7/r6或H7/n6 图d带衬套支承钉,便于拆卸和更换,用于批量大、磨损快、需常修理 的场合。衬套与夹具体孔的配合用H7/n6或H7/r6,衬套内径与支承钉 的配合用H7/js6
第一节
概述
二、机床夹具的分类和组成
(一) 机床夹具的分类 1.按夹具的应用范围分类 1)通用夹具 指已经标准化的,在一定范围内可用于加工不同工件的夹具。 如,车床上三爪卡盘和四爪单动卡盘,铣床上的平口钳、分度 头和回转工作台等。这类夹具一般由专业工厂生产。特点:适 应性广,效率低,主要适于单件、小批生产。 2)专用夹具 指专为某一工件的某道工序而专门设计的夹具。 特点:结构紧凑,操作迅速、方便、省力,可保证较高加工精 度和效率,但设计制造周期长、制造费用高。适于产品固定且 大批生产。
第一节
概述
• 2.用专用夹具定位的安装
靠夹具来保证工件相对于刀具及机床所需的位置,并夹紧。 优点:1)保证工件加工精度 工件相对于刀具和机床的位置精 度由夹具保证,不受工人技术水平影响,能使工件的加工精度趋 向一致; 2)提高劳动生产率 使用夹具装夹工件方便、快捷,不 需划线正,减少辅助工时; 3)扩大机床使用范围 4)改善了操作者的劳动条件 一方面减轻了劳动强度,另 方面保证了夹紧工件的可靠性; 5)降低了成本 缺点:①夹具设计制造周期长;②对毛坯质量要求较高; 专用夹具适用于生产批量较大,产品品种相对稳定的场合
第3章 机床夹具设计基础2

其他装置 或元件
夹具体
夹具的基座和骨架,用来配 置、安装各夹具元件及装置
8
三、机床夹具的主要功能 1、定位 使工件相对于刀具及机床占有正确的加工位置,保证其被加 工表面达到工序所规定的各项技术要求。 2、夹紧 工件定位后,经夹紧装置施力于工件,将其固定夹牢,使其 在加工过程中保持正确位置不变。 安装——工件从定位到夹紧的整个过程。
(2)工件的定位表面和定位元件在尺寸、形状、位置精度
已很高时,过定位不仅对定位精度影响不大,而且有利于提 高刚度。
★前提
—提高工件定位面、夹具定位面的相互位 置精度
不许过定位的场合: 如果工件的定位面是毛坯面,或虽经过加工, 但加工精度不高,这时过定位一般是不允许的。 因为它可能造成定位不准确,或定位不稳定, 或发生定位干涉等情况。
定位元件
1)螺旋式辅助支承。 2)推引式辅助支承。 3)自位式辅助支承。 4)液压锁紧的辅助支承。
图3-25 辅助支承起预定位作用
思考辨析:支承钉的定位与辅助支承的区别
定位:
先固定支承钉,定好正确位置,最后夹紧工件;
辅助支承:
工件定位后,夹紧工件,最后调整辅助支承。
(二)工件以圆柱孔定位 当工件上的孔为定位基准时,常用的定位元件是各种 心轴和定位销,其基本特点是定位孔和定位元件之间处 于配合状态。
限制自由度应理解为:
定位支承点与工件定位基准面始终保持紧贴接触;
定位支承点数目原则上不应超过工件自由度数目; 自由度被限制,是指工件在此方向上有确定的位置: 不考虑外力的影响(注:定位和夹紧的区别); 定位支承点是抽象的,通过具体定位元件来体现。
工件应限制几个自由度,由工件加工技术条件来确定。
(3)标准固定支承板
金属切削12_第12章 机床夹具设计基础

12.3 工件的夹紧
12.3.1 夹紧装置的组成及基本要求 夹紧是工件装夹过程的重要组成部分。
图12 - 22 夹紧机构的组成 1—压板 2—连杆 3—活塞推杆
4—气缸 5—活塞 6—配气阀
12.3 工件的夹紧
(1)夹紧装置的组成 夹紧装置的结构形式很多,主要包括力源装 置、中间递力机构及夹紧元件三部分。 1)力源装置是产生夹紧原始作用力的装置,对机动夹紧机构来说, 常用的力源装置有气动、液压、电力等动力装置。 2)中间递力机构是把力源装置产生的力传递给夹紧元件的中间机 构,它能改变力的作用方向和大小,当手动夹紧时能可靠地自锁。 3)夹紧元件是夹紧装置的最终执行元件,直接和工件接触,把工 件夹紧。 (2)夹紧装置的基本要求 机械加工过程中,夹紧装置的作用就是 将工件压紧夹牢。 1)夹紧过程可靠。
12.1 概述
12.1.2 机床夹具的分类 机床夹具种类繁多,可从使用特点、所用机床及动力源特点3个不 同角度对机床夹具进行分类如下: (1)按夹具使用机床分 可分为车床夹具、铣床夹具、钻床夹具、 镗床夹具、齿轮机床夹具、数控及自动机床夹具、自动线随行夹 具等。 (2)按夹具夹紧动力源分 可分为手动夹具、气动夹具、液压夹具、 气液增力夹具、电磁夹具以及真空夹具等。 (3)按夹具的使用范围及特点分 可分为通用夹具、专用夹具、组 合夹具、可调夹具、拼装夹具、随行夹具等。 1)通用夹具。 2)专用夹具。
12.2 工件在夹具中的定位
2.典型定位方式的定位误差计算 (1)计算原则 如上所述,定位误差由基准位移误差和基准不重合 误差组成。 1)分析一批工件定位基面直径由小变大(或由大变小)时,定位基准 相对限位基准的变动方向,从而判断ΔY的方向。 2)定位基面直径同上趋势变化时,假设定位基准的位置不变动, 即在不考虑ΔY的情况下分析工序基准的变动方向,从而判断ΔB的 方向。 3)按ΔB、ΔY的方向叠加ΔD。 (2)工件以圆柱配合面定位 1)定位副固定单边接触。 2)定位副任意边接触。
- 1、下载文档前请自行甄别文档内容的完整性,平台不提供额外的编辑、内容补充、找答案等附加服务。
- 2、"仅部分预览"的文档,不可在线预览部分如存在完整性等问题,可反馈申请退款(可完整预览的文档不适用该条件!)。
- 3、如文档侵犯您的权益,请联系客服反馈,我们会尽快为您处理(人工客服工作时间:9:00-18:30)。
平面加工 平面加工
第五码位
辅助孔及 齿形加工
辅助孔及 齿形加工
辅助码位 第 第第第 六 七八九 码 码码码 位 位位位
尺 材毛加 坯工 形精
寸 料状度
辅助孔及 齿形加工
10
7. 2 零件分类编码系统
2.JLBM—1零件分类编码系统
名称类别矩阵码
第一位
第二位
粗分类
细分类
形状及加工码
第 第第 第 第第
❖ 教学难点:
成组技术的编码方法; CAPP方法。
2
7. 1 成组技术原理
7.1.1 成组技术的基本概念 所谓成组技术(Group Technology,简称
GT),就是用科学的方法将企业生产的多种产品、 部(组)件和零件,按照特定的相似性准则(分类 系统)分类归组,并按零件族的工艺要求配备相应 的工装设备,采用适当的布置形式组织成组加工, 从而实现产品设计、工艺制造和生产管理的合理化 和科学化,以达到扩大批量的目的。
第
三 四五 六 七八
九
位 位位 位 位位
位
辅助码
第第第第第 第
十 位
十 一 位
十 二 位
十 三 位
十 四 位
十 五 位
轮盘类
环套类 回 转 销杆轴类 类 零 齿轮类 件
异形件类
专用件类
非 杆条类 回 转 板块类 类 座架类 零 件 箱壳体类
盘盖 保护盖 法兰盖 离合器盖 分度盘 手轮 皮带轮 滚轮 活塞 其它
7
7. 2 零件分类编码系统
编码类型:
❖ 层式结构(单码):
层式结构的后一位码受前一位码制约,是对前一位码 进行更详细地说明。层式编码容量大,关系复杂。但 由于层式结构具有相对紧密性,能以有限个位数传递 大量有关零件信息。
❖ 链式结构(多码):
链式结构中每位码都具有独立含义,与前一位码无关。 链式编码容易掌握,容量较小,它可以方便地处理具 有特殊属性的零件。
外部形状 及加工
基功 本能 形要 状素
回转类零件
内部形状 平面 及加工 曲面加工
基
功
外 表
内
本能面 表
形要及 面 状素端
面
辅助加工
非孔 同成 轴形 线刻
线
非回转类零件
外部形状 及加工
主孔及 内部加工
辅助加工
总平 曲 外主 内
辅
体面 面 形孔 部
形加 加 要加 加 状工 工 素工 工
助 孔 成 形
主要 尺寸
材毛 热直长精
坯 径
原 处或
始 宽
形
料状 理度度度
( ) 环套类等 细分类略
11
7. 2 零件分类编码系统
JLBM—1系统的结构基本上是和奥匹兹系统相同的, 只是为了弥补奥匹兹系统的不足。奥匹兹系统对零 件的描述比较粗糙,尤其是对零件的工艺特征的描 述尚显不足。JLBM—1系统把奥匹兹系统的形状加 工码加以扩充,把奥匹兹系统的零件类别码改为零 件功能名称码,把热处理标志从奥匹兹系统中的材 料热处理码中分离出来,主要尺寸码由原来的一个 环节扩大为两个环节。JLBM—1系统除了增加形状 加工的环节,比奥匹兹系统可以容纳较多的分类标 志外,它在系统的总体组成上,要比奥匹兹系统简 单,因而也容3
转 体
L/D≥3
零 L/D≤2有异形
件 L/D>2有异形
特殊的
非 A/B≤3
回 转
A/C≥4
A/B>3
体 A/B≤3
零 A/C<4
件 特殊的
第二码位 外表面形状
外表面形状
形状代码
第三码位 内回转表面加工
内部形状
第四码位 平面加工
平面加工
主要形状 主要形状 主要形状 主要形状
内外表面 形状
组 生 提高生产效率
产 减少生产周期
加 面 降低零件成本
工
貌 减少在制品等
6
7. 2 零件分类编码系统
7.2.1 零件编码的概念 编码:
用一串数字和拉丁字母甚至汉字来描述零件的 结构形状特征和工艺特征。
代表零件特征的每一个字符称为特征码,所有 特征码有规律的组合就是零件的编码。由于每一个 字符代表的是零件的一个特征,而不是一个具体的 参数,因此每种零件的编码并不一定是唯一的。
❖ 混合式结构:
大多数编码系统都采用混合式结构,而其中的某些码 位按层式结构。
8
表7—1 各国的主要成组技术分类系统
西德
OPITZ(切削、磨削、冲压件),STUTTGART,PITTLER,GILDEMEIS TER, ZAFOSPIES,PUSCHMAN
东德 前苏联 前捷克斯洛伐克 英国 挪威 瑞典 荷兰 前南斯拉夫
回顾
❖ 上一章我们讲了机床夹具设计基础,了解 了机床夹具的概念,知道了专用夹具的设计 方法、步骤及各种专用夹具的设计要点 。今 天我们开始学习第七章:
❖ 成组技术(GT)与计算机辅助工艺规程 设计(CAPP)
1
第7章 成组技术与CAPP
❖ 教学重点:
了解成组技术的概念; 了解零件编码的方法; 了解成组技术的常用组织形式; 了解CAPP的概念和CAPP方法。
美国
DDR(标准),WALTER,AUERSWALD MITROFANOV,LITMO,VPTI,NIITMASH,GUREVICH VUOSO,VUSTE,MALEK BRISCH,PERA,SALEORD,GAF(冲压件) TEKLA PGM MICLASS(TNO) IAMA CODE,PARTS—ANALOG,SAGT,ALLIS—CHAMERS,HOLE—CODE,BUCCS,
ASSEMBLY—PART—CODE,CINCLASS,DTH
日本
KC(﹣1、2),KK(﹣1、2、3),冲压件分类,铸件(分类)成本计算,丰田工机,东芝 机械,日立制作所等
9
7. 2 零件分类编码系统
7.2.2 编码系统简介 1.奥匹兹(Opitz)零件分类编码系统
第一码位 零件分类
L/D≤0.5
3
7. 1 成组技术原理
7.1.2 成组技术的基本原理
任何一种机器产品中的组成零件都可以分成三大类:
第一类(A类)专用件
第二类(B类)相似件
第三类(C类)标准件
成组技术主要针对的是B类相似件,因此,如
果能充分利用这一特点,就可将那些看似孤立的零
件按相似性原理划分为具有共性特征的一组,在加
工中以群体为基础集中对待,从而有可能将多品种
小批量生产转化为大批量的生产类型。利用零件的
相似性原理,将零件分类成组,这就是成组技术产
生的基本出发点。
4
7. 1 成组技术原理
三类零件产品中所占比例(%)
~
~ ~
标准件
相似件
专用件
5
7. 1 成组技术原理
产
结构形状
相
品
尺寸大小
似
成零组技材术料原、毛理坯 :
件
设备工装
工 艺
性
分 类 成 组
成改
变 提高加工质量