机械工程可靠性优化设计
机械工程师如何进行机械系统的可靠性设计与维修

机械工程师如何进行机械系统的可靠性设计与维修机械系统作为现代工业生产中不可或缺的一部分,其可靠性设计与维修对于保障工业生产的连续性和效率至关重要。
作为一名机械工程师,我们需要掌握一定的技能和方法,以确保机械系统的可靠性。
本文将从设计和维修两个方面进行论述。
首先,机械系统的可靠性设计是机械工程师的首要任务。
在设计阶段,我们需要全面考虑机械系统的结构合理性、材料选择、工艺流程等因素。
首先,结构合理性是确保机械系统能够稳定运行的关键。
设计师应考虑各个部件的功能和相互作用,合理分配受力点,确保系统的稳定性和可靠性。
其次,材料选择是机械系统设计不可忽视的一环。
合适的材料能够提高机械系统的耐磨性、耐腐蚀性和抗疲劳性,从根本上延长系统的寿命。
此外,工艺流程的合理性也是机械系统设计中的重要环节。
设计师需要充分考虑生产工艺的可行性和成本效益,确保设计方案的实施可行,以降低系统故障和维修的频率。
其次,机械系统的可靠性维修同样重要。
机械系统在运行过程中难免会出现故障和磨损,机械工程师需要及时检修和维修,以确保机械系统的连续运行。
首先,我们需要建立完善的维修计划和检修记录,将维修工作纳入日常管理的重要环节。
此外,在维修过程中,我们需要采用合适的工具和设备,确保维修操作的准确性和安全性。
对于常见的故障和磨损问题,机械工程师需要了解相关的修复方法和技巧,能够迅速定位问题并进行修复。
在维修结束后,我们还需进行全面的测试和性能调试,确保机械系统恢复正常运行。
除了设计和维修,机械工程师还需要关注机械系统的维护和保养。
维护和保养是预防机械故障和磨损的重要手段。
在日常运行中,我们应建立定期检查和维护的计划,包括清洁、润滑、紧固螺栓等工作。
此外,对于重要部件和设备,我们还可以采用在线监测和预警系统,及时发现并解决潜在的问题,降低维修成本和生产停工时间。
综上所述,机械工程师在进行机械系统的可靠性设计与维修时,需要全面考虑结构合理性、材料选择和工艺流程等因素。
机械工程的可靠性优化设计分析
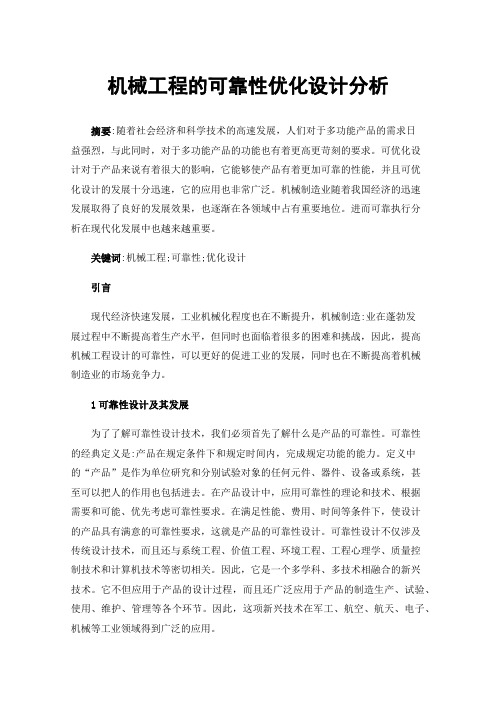
机械工程的可靠性优化设计分析摘要:随着社会经济和科学技术的高速发展,人们对于多功能产品的需求日益强烈,与此同时,对于多功能产品的功能也有着更高更苛刻的要求。
可优化设计对于产品来说有着很大的影响,它能够使产品有着更加可靠的性能,并且可优化设计的发展十分迅速,它的应用也非常广泛。
机械制造业随着我国经济的迅速发展取得了良好的发展效果,也逐渐在各领域中占有重要地位。
进而可靠执行分析在现代化发展中也越来越重要。
关键词:机械工程;可靠性;优化设计引言现代经济快速发展,工业机械化程度也在不断提升,机械制造:业在蓬勃发展过程中不断提高着生产水平,但同时也面临着很多的困难和挑战,因此,提高机械工程设计的可靠性,可以更好的促进工业的发展,同时也在不断提高着机械制造业的市场竞争力。
1可靠性设计及其发展为了了解可靠性设计技术,我们必须首先了解什么是产品的可靠性。
可靠性的经典定义是:产品在规定条件下和规定时间内,完成规定功能的能力。
定义中的“产品”是作为单位研究和分别试验对象的任何元件、器件、设备或系统,甚至可以把人的作用也包括进去。
在产品设计中,应用可靠性的理论和技术、根据需要和可能、优先考虑可靠性要求。
在满足性能、费用、时间等条件下,使设计的产品具有满意的可靠性要求,这就是产品的可靠性设计。
可靠性设计不仅涉及传统设计技术,而且还与系统工程、价值工程、环境工程、工程心理学、质量控制技术和计算机技术等密切相关。
因此,它是一个多学科、多技术相融合的新兴技术。
它不但应用于产品的设计过程,而且还广泛应用于产品的制造生产、试验、使用、维护、管理等各个环节。
因此,这项新兴技术在军工、航空、航天、电子、机械等工业领域得到广泛的应用。
2机械制造工艺可靠性的分析方法2.1管理工艺环节一个行业能否有效运行,关键点是不能离开其合理性与高效性,从机械制造行业的角度探寻问题,我们能够了解正常的运行也要讲求科学与合理,通过合理化的经营管理,能提升整个工艺流程。
机械设计可靠性研究

机械设计可靠性研究1机械工程产品的可靠性优化设计现状分析1.1可靠性优化设计的基本理论20世纪60年代,机械优化设计获得了最广阔的发展。
在这一时期,计算机技术和数学规划有机地结合起来,推动了机械优化设计向更高的层次发展。
优化设计的方法被广泛应用于工程设计领域,并伴随着计算机技术的飞速发展和数学规划理念的不断成熟,发挥着越来越重要的作用,取得了令人瞩目的成果。
具体来讲,所谓可靠性优化设计主要包含三个方面,即产品的质量、成本和可靠度。
可靠性优化设计从系统的、整体的角度对产品的可靠度进行分析,并对其性能进行约束与优化,在确保产品性能和质量的前提下,将产品的合理性和安全性有机结合,从而使得产品的可靠度实现最大化。
通过可靠性优化设计,在满足产品可靠性的同时,还使得能源以及资源获得充分的利用,避免了能源和资源的不合理使用及浪费现象。
采用可靠性优化设计所生产出来的产品,具有体积小、质量轻的特点,并使用节能材料,顺应当前可持续发展和保护环境的趋势。
对机械产品进行优化设计的根本宗旨,即为了满足安全的需要或者为了实现特定的预期点,通过最优化的方式,对产品进行处理。
在进行优化设计时,需要考虑多种因素给产品性能带来的影响,其中需要注意的两点即结构参数以及各种载荷的随机性。
1.2近年来可靠性优化设计发展近年来,高新科技不断融入机械设计领域,许多现代化的设计方法和设计理念应运而生,可靠性设计和优化设计也获得了飞速的发展。
然而从设计的角度来看,可靠性设计和优化设计是设计的两个不同方面,而对于机械产品的设计来说,如果单纯地考虑其中的一方面是无法达到设计要求的。
这就需要在实际的设计工作中,将两者相结合,从而发挥其潜在的巨大作用。
可靠性设计不同于优化设计,可靠性设计是以产品的可靠性为设计宗旨的,因此设计的结果并非其工作性能或参数的最佳点。
此外,优化设计有别于可靠性设计,优化设计并不考虑产品的可靠性,因此有可能导致事故,造成经济损失。
机械结构可靠性分析与优化设计
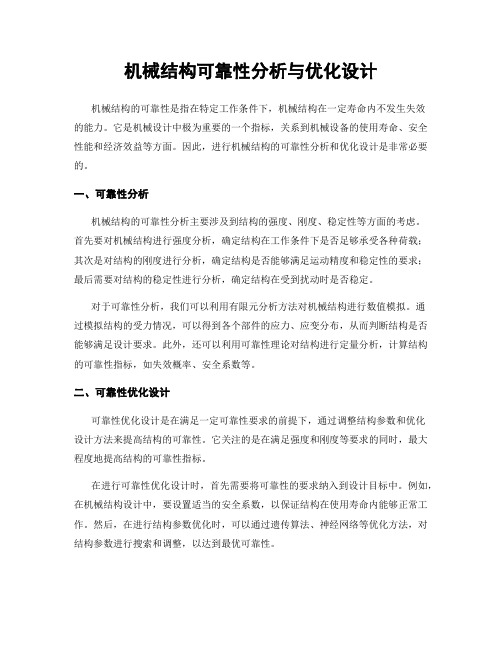
机械结构可靠性分析与优化设计机械结构的可靠性是指在特定工作条件下,机械结构在一定寿命内不发生失效的能力。
它是机械设计中极为重要的一个指标,关系到机械设备的使用寿命、安全性能和经济效益等方面。
因此,进行机械结构的可靠性分析和优化设计是非常必要的。
一、可靠性分析机械结构的可靠性分析主要涉及到结构的强度、刚度、稳定性等方面的考虑。
首先要对机械结构进行强度分析,确定结构在工作条件下是否足够承受各种荷载;其次是对结构的刚度进行分析,确定结构是否能够满足运动精度和稳定性的要求;最后需要对结构的稳定性进行分析,确定结构在受到扰动时是否稳定。
对于可靠性分析,我们可以利用有限元分析方法对机械结构进行数值模拟。
通过模拟结构的受力情况,可以得到各个部件的应力、应变分布,从而判断结构是否能够满足设计要求。
此外,还可以利用可靠性理论对结构进行定量分析,计算结构的可靠性指标,如失效概率、安全系数等。
二、可靠性优化设计可靠性优化设计是在满足一定可靠性要求的前提下,通过调整结构参数和优化设计方法来提高结构的可靠性。
它关注的是在满足强度和刚度等要求的同时,最大程度地提高结构的可靠性指标。
在进行可靠性优化设计时,首先需要将可靠性的要求纳入到设计目标中。
例如,在机械结构设计中,要设置适当的安全系数,以保证结构在使用寿命内能够正常工作。
然后,在进行结构参数优化时,可以通过遗传算法、神经网络等优化方法,对结构参数进行搜索和调整,以达到最优可靠性。
此外,还可以应用可靠性设计理论进行概率设计。
概率设计是通过考虑不确定性因素,确定合理的设计参数范围,使得结构在任何设计参数取值下都能够满足一定的可靠性要求。
例如,通过概率设计可以确定零部件的公差范围,确保结构在制造过程中的变化仍能满足可靠性要求。
结构的可靠性分析和优化设计是机械工程领域的重要内容,它直接关系到机械设备的使用寿命和安全性能。
通过可靠性分析,可以了解结构的强度、刚度、稳定性等方面的情况,并根据这些情况进行相应的改进。
机械工程中的可靠性与可行性分析
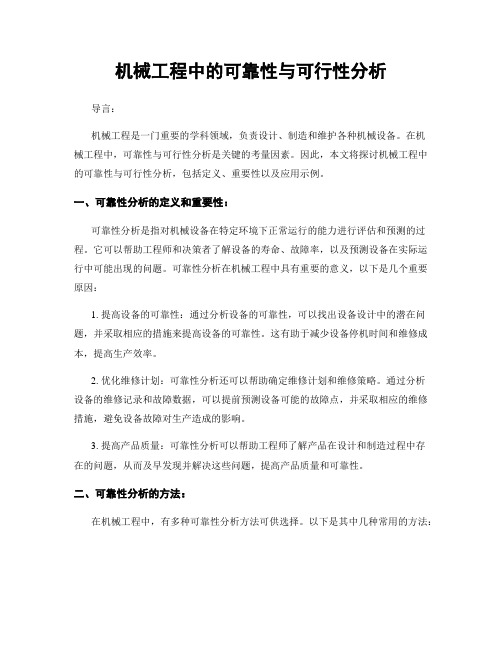
机械工程中的可靠性与可行性分析导言:机械工程是一门重要的学科领域,负责设计、制造和维护各种机械设备。
在机械工程中,可靠性与可行性分析是关键的考量因素。
因此,本文将探讨机械工程中的可靠性与可行性分析,包括定义、重要性以及应用示例。
一、可靠性分析的定义和重要性:可靠性分析是指对机械设备在特定环境下正常运行的能力进行评估和预测的过程。
它可以帮助工程师和决策者了解设备的寿命、故障率,以及预测设备在实际运行中可能出现的问题。
可靠性分析在机械工程中具有重要的意义,以下是几个重要原因:1. 提高设备的可靠性:通过分析设备的可靠性,可以找出设备设计中的潜在问题,并采取相应的措施来提高设备的可靠性。
这有助于减少设备停机时间和维修成本,提高生产效率。
2. 优化维修计划:可靠性分析还可以帮助确定维修计划和维修策略。
通过分析设备的维修记录和故障数据,可以提前预测设备可能的故障点,并采取相应的维修措施,避免设备故障对生产造成的影响。
3. 提高产品质量:可靠性分析可以帮助工程师了解产品在设计和制造过程中存在的问题,从而及早发现并解决这些问题,提高产品质量和可靠性。
二、可靠性分析的方法:在机械工程中,有多种可靠性分析方法可供选择。
以下是其中几种常用的方法:1. 故障模式与影响分析(FMEA):FMEA是一种常用的可靠性分析方法,旨在识别设备可能出现的故障模式以及这些故障对设备正常运行和工作环境的影响。
通过对故障模式进行评估,可以优化设备的设计和维护计划,提高设备的可靠性。
2. 可靠性块图(RBD):可靠性块图是一种图形化的分析方法,用于表示系统中各个组件的可靠性和相互之间的关系。
通过绘制可靠性块图,可以清晰地了解系统的功能和结构,识别潜在的故障点,并对系统进行可靠性分析。
3. 故障树分析(FTA):故障树分析是一种基于逻辑关系的可靠性分析方法,用于识别导致系统故障的关键事件和因素。
通过构建故障树,可以分析设备故障的概率和可能的原因,并采取相应的措施来提高系统的可靠性。
机械工程中的可靠性分析与维修策略优化

机械工程中的可靠性分析与维修策略优化随着科技的不断发展和进步,机械工程在现代社会中起到了至关重要的作用。
然而,由于机械设备的使用频率和复杂性的增加,设备的可靠性和维修策略的优化变得尤为重要。
本文将探讨机械工程中的可靠性分析与维修策略优化,并提供一些有效的方法和技巧。
一、可靠性分析可靠性分析是指对机械设备或系统进行评估,以确定其在给定时间内能够正常运行的概率。
通过可靠性分析,我们可以了解设备的故障模式、故障率以及故障的原因。
在机械工程中,常用的可靠性分析方法包括故障模式与影响分析(FMEA)、可靠性块图(RBD)和故障树分析(FTA)等。
FMEA是一种系统性的方法,用于识别和评估机械设备中的潜在故障模式,并确定其对系统性能的影响。
该方法可以帮助工程师在设计阶段就发现和解决潜在的问题,提高设备的可靠性。
RBD方法通过绘制可靠性块图,将整个机械系统划分为多个子系统或元件,并分析每个子系统的可靠性。
通过计算每个子系统的可靠性指标,可以得出整个系统的可靠性,并找出影响系统可靠性的关键元件。
FTA是一种定性和定量分析方法,用于识别和评估造成机械设备故障的根本原因。
在FTA分析中,通过构建故障树、识别出事故的直接和间接原因,从而帮助工程师制定维修策略和措施。
二、维修策略优化维修策略的优化是指通过合理的维修方式和时机,最大程度地提高设备的运行时间和可靠性。
传统的维修方式通常采用固定周期的维护和修理,这种方式存在效率低下和资源浪费的问题。
因此,我们需要通过优化维修策略来解决这些问题。
一种常用的维修策略是预防性维护。
预防性维护是指在设备出现故障之前,根据设备的使用情况和性能指标进行定期维护和检修。
这种方式可以及时发现潜在故障,并采取相应措施,防止设备故障的发生。
另一种优化维修策略的方法是故障诊断与预测。
现代技术已经使得故障诊断和预测成为可能。
通过使用传感器和监测设备,工程师可以实时获取机械设备的运行状态和性能数据。
机械设计中的可靠性工程要点

机械设计中的可靠性工程要点机械设计中的可靠性工程是保证机械产品在使用过程中达到预期功能的关键。
在设计过程中考虑到可靠性,可以大大提高产品的使用寿命、降低维修成本,并保证用户的安全。
本文将从设计、材料选择和制造过程等方面介绍机械设计中的可靠性工程要点。
一、设计要点1. 完善的需求分析:在机械设计过程中,充分了解用户需求和产品的使用环境是至关重要的。
通过与用户的沟通和分析,准确把握用户对机械产品功能和性能的要求,并充分考虑使用环境的特点,从而为后续设计工作提供明确的方向和目标。
2. 合理的工作过程:在机械设计中,需要明确机械产品在不同工作阶段的工作过程,并根据不同工作过程对机械部件的需求进行合理设计。
合理的工作过程可以降低机械部件的磨损和疲劳程度,延长机械产品的使用寿命。
3. 结构简化和优化:结构简化是提高机械产品可靠性的有效手段之一。
简化结构可以降低零部件的数量和复杂度,减少故障部件的数量,降低故障的概率。
此外,结构优化也是提高机械产品可靠性的关键,通过结构优化可以提高零部件的强度和刚度,并提高机械产品的工作效率和稳定性。
4. 充分考虑故障模式:在设计过程中,需要充分考虑可能出现的故障模式,并采取相应的措施来避免或减轻故障的发生和影响。
例如,对于容易出现断裂故障的部件,可以采用更可靠的材料或增加冗余设计来提高其抗断裂能力。
二、材料选择要点1. 合适的材料强度:机械设计中的可靠性工程涉及到适当选择材料的强度。
根据机械产品所处环境和工作条件的要求,选择合适的材料强度能够保证机械产品在使用过程中不会发生过早损坏和破坏。
2. 耐磨性和耐腐蚀性:在一些特殊的工作环境下,机械产品可能会受到磨损或腐蚀的影响。
因此,在材料选择时,需要考虑到机械产品所处环境的磨损和腐蚀性,选择具有较好耐磨性和耐腐蚀性的材料,提高机械产品的寿命和可靠性。
3. 适当的材料可加工性:在机械设计中,材料的可加工性也是一个重要考虑因素。
选择材料时,需要考虑其可加工性是否良好,以便保证机械产品生产过程中的可靠性和高效性。
机械工程师机械设计与可靠性分析

机械工程师机械设计与可靠性分析机械工程师是负责设计、开发和制造机械设备及系统的专业人员。
机械设计是机械工程师工作的核心内容之一,而可靠性分析则是确保设计的机械系统在使用过程中能够稳定可靠运行的重要环节。
本文将从机械设计和可靠性分析两个方面进行探讨。
一、机械设计机械设计是指根据使用需求和技术要求,将机械原理、材料科学、运动学等知识应用于机械设备及系统的构思、计划、设计和制造的过程。
良好的机械设计能够确保产品在性能、质量、经济和可制造性等方面达到最佳状态。
1.1 设计概念与需求分析在机械设计的初期阶段,机械工程师需要与客户或需求方充分沟通,了解产品的使用需求和技术要求,明确设计目标和约束条件。
根据这些信息,进行设计概念的产生和需求分析,确定设计的基本框架。
1.2 机械设计过程机械设计过程涉及到理论分析、计算机辅助设计、实验验证等多个环节。
机械工程师需要运用机械学、热力学、流体力学等理论知识进行系统设计,利用CAD、CAE等软件工具进行详细设计,通过实验验证和优化,得出最佳产品方案。
1.3 性能与质量控制在机械设计中,性能和质量是衡量产品优劣的重要标准。
机械工程师需要通过合理的设计和制造工艺,确保产品具备所需的性能指标,并进行相关测试和验证,以保证产品质量符合要求。
二、可靠性分析可靠性分析是指对机械系统进行可靠性评估和预测,找出可能导致系统失效的关键部件与故障机理,并提出相应的改进措施,从而提高机械系统的可靠性和稳定性。
2.1 可靠性评估方法常用的可靠性评估方法包括故障模式与影响分析(FMEA)、故障树分析(FTA)、可靠性增长分析(RGA)等。
机械工程师可以根据具体情况选择合适的方法,对机械系统进行潜在故障分析和风险评估,以确定改进和优化的重点。
2.2 MTBF与RAM分析平均无故障时间(MTBF)是对系统可靠性的一种常用指标,它表示系统在正常使用条件下连续运行的平均时间。
可靠性、可用性和维修率(RAM)分析是评估系统整体性能和可维护性的重要手段。
机械工程产品可靠性优化设计要点分析

中需要对机械工程产品设计的可靠性进行大量 、反复的验证和修 我国的机械工程设计制造与国外具有一定的差距 ,尤其是在 改 以确保机械工程产品可靠性满足相应 的 设计标准 。 机械工程产品可靠性优化设计方面 ,我国由于缺乏相应的技术积 2 . 2 做好机械工程产 品制造过程中的可靠性优化设计
行功能化扩展是现今乃至未来一段时问机械工程产业发展的重要 以及综合评分的机械工程产品可靠性设计方式。在对机械工程产
趋 势 。在 机 械工 程设 计 的过 程 中对 于机 械 工程 产 品的 可靠 性应 当 品中单个零件进行设计的过程 中要确保其能够与国家所规定的常 在 不 断 引入新 技 术 的 同时做 好对 于机械 工程 产 品结 构 和理 论 的优 规零件相匹配 。此外在机械工程产品可靠性优化设计过程中应当
2 . I 加强对于机械工程产品设计 环节 的可靠性优化设计 在机械工程产品设计 的过程 中所涉及的机械工程产 品整体 装配 和零件组装会对机械工程产品的可靠性提出较高 的要求 。 在对设计 环节进行机械工程产 品可靠性优化设计 的过程 中,将 都需要进行综合 性的分析 ,而且要采用合理的方法来对机械工程 产品可靠性及其优化指标进行综合性的分析 。
完成机械工程产品设计环节的可靠性设计后,机械工程产品 些不足。新时期,我国加大了对于机械工程产 品可靠性优化设 的加工制造是影响机械工程产品可靠性的一个极为重要的环节。 计的理论研究和应用 ,但是在机械工程产品的生产实践 中对于机 在这一环节 中,做好机械工程产品可靠性的控制关键是要做好各
解 ,而后对机械工程产品 中的各组成的零部件的可靠性进行相应 的分析 ,并 由各零部件 的可靠性来对机械工程产品整体的可靠性
进行推断。在这一设计方法中,对于机械工程产品整体的可靠性 主要是通过对机械工程产品整体可靠性进行预测的分析以判定机 械工程产品的设计指标是否满足预测的结果。 ( 2 )第二种方式是进行指标分配 ,在机械工程产品设计过
机械工程师如何进行机械设计优化
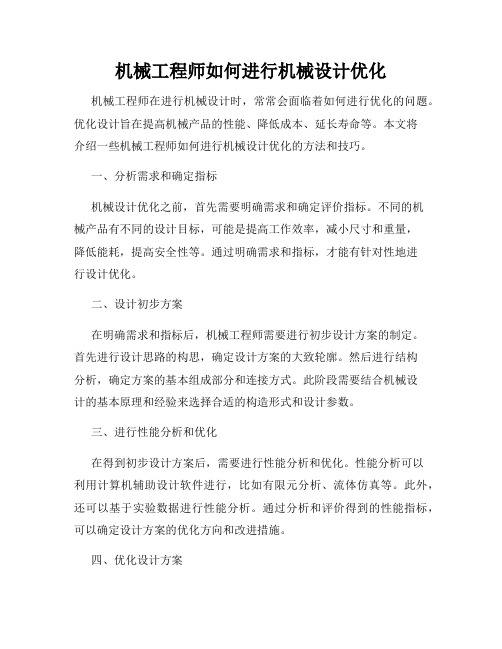
机械工程师如何进行机械设计优化机械工程师在进行机械设计时,常常会面临着如何进行优化的问题。
优化设计旨在提高机械产品的性能、降低成本、延长寿命等。
本文将介绍一些机械工程师如何进行机械设计优化的方法和技巧。
一、分析需求和确定指标机械设计优化之前,首先需要明确需求和确定评价指标。
不同的机械产品有不同的设计目标,可能是提高工作效率,减小尺寸和重量,降低能耗,提高安全性等。
通过明确需求和指标,才能有针对性地进行设计优化。
二、设计初步方案在明确需求和指标后,机械工程师需要进行初步设计方案的制定。
首先进行设计思路的构思,确定设计方案的大致轮廓。
然后进行结构分析,确定方案的基本组成部分和连接方式。
此阶段需要结合机械设计的基本原理和经验来选择合适的构造形式和设计参数。
三、进行性能分析和优化在得到初步设计方案后,需要进行性能分析和优化。
性能分析可以利用计算机辅助设计软件进行,比如有限元分析、流体仿真等。
此外,还可以基于实验数据进行性能分析。
通过分析和评价得到的性能指标,可以确定设计方案的优化方向和改进措施。
四、优化设计方案根据性能分析和优化结果,机械工程师需要对设计方案进行优化。
优化的方式有很多种,可以调整参数,改变结构,采用新材料等。
在优化设计的过程中,需要充分考虑各种因素的相互制约关系。
设计优化并非仅仅为了追求某个指标的最大化或最小化,而是要在各种约束条件下寻找到最佳的平衡点。
五、验证和测试优化设计方案之后,需要进行验证和测试。
验证的方式可以是通过实验、模型测试等。
通过验证和测试,可以评价设计方案的可行性和可靠性。
如果设计方案经过验证和测试后表现良好,机械工程师可以进一步进行细化和完善,使设计方案达到最佳效果。
六、迭代改进优化设计并非一次性完成,而是需要不断迭代和改进的过程。
迭代改进的目的是为了进一步提高设计方案的效果和性能。
在实际应用中,机械工程师需要根据实际情况进行设计方案的调整和修正,不断优化和改进,以使机械产品达到最佳状态。
机械工程的可靠性优化设计 迟明

机械工程的可靠性优化设计迟明摘要:随着社会经济的快速发展和科学技术的快速进步,人们的要求越来越高。
使用的设备需要多种功能。
产品不仅要有质量保证,还要有可靠性。
可靠产品的生产和设计逐渐引起人们的注意,并在各个行业得到了广泛的应用和发展。
关键词:机械工程;可靠性设计;应用现代化社会发展突飞猛进,各类产品的更换速度也越来越快,产品种类多样化发展趋势比较明显。
在这样的环境下,人们有了更多的选择性,对此在产品质量方面的要求也越来越高。
各行业在产品制造过程也逐渐复杂化是由于在各种各新型的科技的引领下技术运用比较多而杂。
因此,产品在设计过程智能应该要考虑到技术应用的实际性和高效性,整个产品生产过程中要不断的深入和完善。
并且大多数产品在生产过程中都会经过初要严格试阶段之后,试验结果正常的情况下挨次能向市场投入,所以在产品生产过程要严格把关。
在进行可靠性产品技术研究的前提下,首先要对产品的可靠性要有充分的认识,其中包括产品功能、生产过程中系统、设备以及其他器件等的组成进行详细的分析和探讨。
1机械工程可靠性设计中存在的不足1.1企业不够重视当前,国内大大多数企业对这一行业的重视并不够,企业感觉这种可靠性研究并且浪费金钱,而且对整体的发展影响并不大,对老板而言盈利才是重中之重,对于发达国家和国际而言可靠性研究才是主要之重,才是重要的组成部分,如果我们对可靠性研究不能产生足够的重视,将在现在就跟对手在起点上产生差距,在未来的竞争压力下将输给对手,将其残余的竞争能力也失去。
可靠性研究是一个整体的系统的工程,涉及的方面全面广泛,复杂,认为这不可能让所生产出来的产品得到保证。
所以,国内应该有专门的独立的一个部门,来测试产品的可靠性,确保所生产出来的产品在各個方面得以保证、可靠,从而将产品提升到更高的可靠水平,让中国制造面向全世界,这才能在未来的竞争中有足够的优势占据主导。
1.2稳健提升产品的可靠才是有效途径产品的提升需要稳,要一步一步,产品的质量因时间和环境的不同存在一定的波动有不敏感性,不敏感要求的越强,产品的可靠性才能越高。
机械工程中的可靠性分析与优化设计

机械工程中的可靠性分析与优化设计在机械工程中,可靠性是一个至关重要的概念。
机械设备的可靠性决定了它们是否能够在设计寿命内正常运行,而可靠性分析与优化设计则是确保机械设备具有高度可靠性的关键。
可靠性分析是通过对机械设备的各种故障形式和失效原因进行分析,以确定可能导致失效的主要因素。
这些因素可以包括材料质量、制造工艺、工作环境等等。
通过对这些因素的分析,可以找出引起故障的根本原因,并采取相应的措施来提高机械设备的可靠性。
一种常用的可靠性分析方法是故障模式和效应分析(Failure Mode and Effects Analysis,简称FMEA)。
FMEA的基本原理是通过分析潜在的失效模式和它们对系统性能的影响,来确定机械设备中的关键零部件和失效途径。
通过对失效途径的分析,可以找出引起故障的原因,并采取相应的措施来预防故障的发生。
而在可靠性优化设计方面,一种常用的方法是可靠性设计优化(Reliability-based Design Optimization,简称RBDO)。
RBDO是一种结合了可靠性分析和优化技术的方法,旨在通过将可靠性约束嵌入到设计优化过程中,以实现对机械设备的可靠性进行优化。
在RBDO中,首先需要对机械设备的可靠性进行分析,确定失效概率和可靠度等指标。
然后,在设计优化过程中,将这些可靠性指标作为约束条件,以保证设计方案具有足够的可靠性。
通过不断优化设计方案,可以得到一个在可靠性和性能方面都达到最优的机械设备。
除了这些传统的可靠性分析与优化方法外,近年来一些新兴的技术也被应用到机械工程中的可靠性分析与优化设计中。
例如,基于故障树分析(Fault Tree Analysis,简称FTA)的可靠性分析方法可以更加直观地描述故障的发生途径;而基于人工智能技术的优化算法如遗传算法、神经网络等能够更高效地搜索最优解。
需要注意的是,机械工程中的可靠性分析与优化设计应该考虑的因素众多。
除了上述提到的材料质量、制造工艺、工作环境等外,还包括设计参数的选择、零部件的可靠性要求、运输和安装过程中的影响等。
解析机械工程的可靠性优化设计

解析机械工程的可靠性优化设计摘要:随着机械制造业的迅猛发展,机械工程在经济建设各领域中占有非常重要的地位。
文章从可靠性的角度阐述了进行产品开发设计时所要注意的问题,将可靠性优化设计方案应用在机械工程的设计中。
关键词:新技术;可靠性;优化设计;机械工程中图分类号:n945.17在当今科学技术快速发展的当今社会,产品的更新换代速度也越来越快,人们也对产品的可靠性和质量给予了更多的关注,因此,有关产品可靠性的设计也普遍得到广泛应用和发展。
设计产品是一个需要不断深化认识、逐步完善和改进的过程。
所有产品都是必须要经过初试后才能投入市场,因为产品在初期完成时,其自身会存在许多工艺和设计方面的缺陷,也就相应地存在一些不可靠性。
所以,生产商在生产产品的初期必须有计划地改进产品设计和工艺规程,才能从而提高产品的可靠性水平,把问题的故障消灭在萌芽状态。
这样一来,可靠性设计研究就产生了,它有助于预期目标的达成。
在对可靠性设计技术进行研究之前,必须对产品可靠性的概念有所了解。
在可靠性设计中,必须要满足时间、花费、功能等条件,使得设计产品的可靠性达到要求。
可靠性设计涉及的范围极其广泛,它不仅仅包含了传统的设计技术,还关联着计算机技术、质量控制技术、环境工程、系统工程等。
它不但运用在在产品的设计过程中,还涉及到初产品到成品的各个工艺生产环节。
它是一个集多方面科学技术于一身的现代化新兴技术。
所以,在机械、电子、航天、军事等一些重要的领域,都需要应用可靠性设计技术。
它的作用极为重要,应用也极其广泛。
1、可靠性发展可靠性发展的阶段分为早期研究阶段、过程发展阶段和国际化阶段。
早期研究阶段体现在二战中的英美军舰和战斗机等的军事方面,当重要的装备频频出现机械故障导致战争被动,为了减少战争中频发的机械故障,于是人们就开始重视机械设备的可靠性问题,也就开始进行对机械可靠性的研究和筹划。
最早是英美德等国家在军事装备方面提出了相应的可靠性指标。
机械工程的可靠性优化设计分析
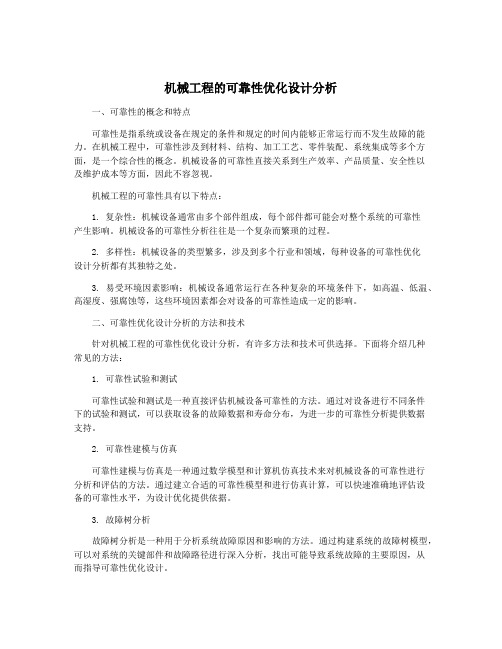
机械工程的可靠性优化设计分析一、可靠性的概念和特点可靠性是指系统或设备在规定的条件和规定的时间内能够正常运行而不发生故障的能力。
在机械工程中,可靠性涉及到材料、结构、加工工艺、零件装配、系统集成等多个方面,是一个综合性的概念。
机械设备的可靠性直接关系到生产效率、产品质量、安全性以及维护成本等方面,因此不容忽视。
机械工程的可靠性具有以下特点:1. 复杂性:机械设备通常由多个部件组成,每个部件都可能会对整个系统的可靠性产生影响。
机械设备的可靠性分析往往是一个复杂而繁琐的过程。
2. 多样性:机械设备的类型繁多,涉及到多个行业和领域,每种设备的可靠性优化设计分析都有其独特之处。
3. 易受环境因素影响:机械设备通常运行在各种复杂的环境条件下,如高温、低温、高湿度、强腐蚀等,这些环境因素都会对设备的可靠性造成一定的影响。
二、可靠性优化设计分析的方法和技术针对机械工程的可靠性优化设计分析,有许多方法和技术可供选择。
下面将介绍几种常见的方法:1. 可靠性试验和测试可靠性试验和测试是一种直接评估机械设备可靠性的方法。
通过对设备进行不同条件下的试验和测试,可以获取设备的故障数据和寿命分布,为进一步的可靠性分析提供数据支持。
2. 可靠性建模与仿真可靠性建模与仿真是一种通过数学模型和计算机仿真技术来对机械设备的可靠性进行分析和评估的方法。
通过建立合适的可靠性模型和进行仿真计算,可以快速准确地评估设备的可靠性水平,为设计优化提供依据。
3. 故障树分析故障树分析是一种用于分析系统故障原因和影响的方法。
通过构建系统的故障树模型,可以对系统的关键部件和故障路径进行深入分析,找出可能导致系统故障的主要原因,从而指导可靠性优化设计。
4. FMEA分析5. 可靠性工程设计可靠性工程设计是一种将可靠性考虑融入到产品设计过程中的方法。
通过在设计阶段就充分考虑设备的可靠性需求,采用先进的设计原则、材料和工艺,可以有效提高设备的可靠性水平。
机械工程中的可靠性与维修性设计

机械工程中的可靠性与维修性设计机械工程是应用物理学和材料科学原理来设计和制造机械设备和工具的学科。
在机械工程中,设计师们要考虑许多因素,其中包括可靠性和维修性。
可靠性指的是机械系统在特定条件下运行的能力,而维修性则是指维护和修理机械系统的难易程度。
本文将探讨机械工程中的可靠性与维修性设计的重要性以及应考虑的因素。
一、可靠性设计在机械工程中,可靠性设计是至关重要的。
可靠性设计的目标是确保机械系统在规定的运行条件下能够按照预期的方式工作。
为了实现可靠性设计,设计师需要考虑以下几个关键因素。
1. 材料选择:在机械工程中,选择合适的材料对于系统的可靠性至关重要。
材料应具备足够的强度和耐久性,以承受工作过程中的应力和磨损。
2. 零件设计:机械系统中的每个零件都应经过精心设计和验证,以确保其可靠性。
设计师应考虑零件的形状、尺寸、材料和制造工艺等因素。
3. 组装技术:机械系统的可靠性还与组装技术密切相关。
正确的组装过程和技术能够保证零件的准确配合和紧固,提高系统的可靠性。
4. 适应性设计:机械工程师还应考虑机械系统在不同工作条件下的可靠性。
机械系统应具备一定的适应性,以适应不同温度、湿度和环境的变化。
二、维修性设计除了可靠性外,维修性设计也是机械工程中应重视的方面。
良好的维修性设计可以降低维修和保养的难度,减少停机时间和维修成本,提高系统的可用性。
1. 维修空间:机械系统中应提供足够的维修空间,以方便技术人员进行维修和更换零件。
维修空间的设计应充分考虑到维修人员的工作需求,使其能够方便地操作和维修机械系统。
2. 零件易损性设计:在机械系统设计中,应尽量避免使用易损零件或易损部件。
如果不可避免地需要使用易损零件,应考虑其易于更换并提供相应的备件。
3. 维修手册和培训:设计师应编写详细的维修手册,为维修人员提供清晰的维修流程和指导。
此外,培训维修人员并提供定期培训也是提高维修性的重要举措。
4. 预防性维护:维修性设计还包括预防性维护的考虑。
机械工程中的可靠性与维修性分析研究

机械工程中的可靠性与维修性分析研究引言机械工程作为一门重要的学科领域,旨在研究机械设备的设计、制造和运行等方面。
机械工程的可靠性与维修性是两个关键的概念,对于提高机械设备的性能和延长使用寿命至关重要。
本文将对机械工程中的可靠性与维修性进行深入的研究与分析。
一、定义与概念1. 可靠性可靠性是评估机械设备工作正常的能力。
维修性是评估设备出现故障后维修的便捷程度和速度。
在机械工程中,可靠性是指一个设备在规定条件下,经过规定时间的工作后,不出现故障的能力。
它是一个综合性指标,与设计、制造、运行环境等多个因素相关。
2. 维修性维修性是指在设备故障发生时,对其进行修复和恢复正常工作的便捷程度和速度。
好的维修性能可以减少停机时间和成本,提高生产效率。
二、主要研究内容1. 可靠性分析方法(1)故障树分析法故障树分析法是一种定性与定量相结合的分析方法,通过对系统各个元件的故障进行分类和分析,确定系统故障的原因和发生概率。
(2)失效模式与效果分析法失效模式与效果分析法旨在通过对设备的失效模式进行分析,推测失效原因,并评估对系统产生的影响,以确定设备的可靠性。
2. 维修性分析方法(1)故障树分析法故障树分析法不仅可以用于可靠性分析,也可以用于维修性分析。
通过梳理设备故障树,确定故障发生的原因和对策,以提高维修效率。
(2)维修时间分析法维修时间分析法旨在通过对维修过程中各个环节的时间进行统计和分析,找出影响维修速度的关键因素,从而优化维修流程。
三、应用案例分析1. 常见机械设备的可靠性与维修性研究(1)风力发电机组风力发电机组是一种常见的可再生能源设备,其可靠性与维修性直接影响到发电效率。
研究表明,定期维护和故障预测技术可以显著提高机组的可靠性,并降低维修成本。
(2)汽车发动机汽车发动机是一种需要高度可靠性和快速维修的设备。
研究发现,通过使用先进的故障监测系统和提前维修策略,可以减少故障率和维修时间。
2. 可靠性与维修性参数的优化设计在机械设备的设计过程中,可靠性与维修性参数的选择和优化设计对于设备的性能和寿命有着重要影响。
机械工程中的可靠性和维修性设计

可靠性是维修性的基础,只有设备具有较高的可靠性,才能减少维修次数, 降低维修成本。
维修性是提高可靠性的重要手段,通过改进设备的维修性,可以及时发现和 修复故障,提高设备的可靠性。
在机械工程中,可靠性与维修性是相互影响、相互促进的。通过协同设计, 可以优化设备的可靠性和维修性,提高设备的整体性能。
设计方法:采用冗余设计、故障 安全设计、环境适应性设计等方 法提高产品的可靠性
设计评价:通过可靠性测试、仿 真分析等手段评估产品的可靠性 性能,并进行优化改进
汽车发动机:通过优化设 计提高发动机的可靠性,
降低故障率
飞机控制系பைடு நூலகம்:采用冗余 设计提高控制系统的可靠
性,确保飞行安全
航天器:通过可靠性设计 确保航天器在恶劣环境下
汇报人:XX
可靠性定义:产 品在规定条件下, 规定时间内,完 成规定功能的能 力
重要性:可靠性 直接影响产品的 性能、寿命和成 本
可靠性设计原则 :预防为主,维 修为辅
可靠性设计方法 :冗余设计、容 错设计、可靠性 分配等
设计目标:确保产品在使用过程 中能够稳定、可靠地工作
设计原则:以可靠性为中心,注 重产品的安全性、耐用性和可维 护性
重要性:维修性设计可以提高 产品的可靠性、安全性和使用 寿命,降低维修成本和停机时 间,提高生产效率和经济效益。
维修性定义:指产品在使用过 程中,能够方便地进行维修、 更换和升级的能力。
维修性设计的原则:模块化、 标准化、互换性、易拆卸、易
检测、易更换等。
维修性设计的方法:采用可 靠性设计、故障预测与预防、 维修策略优化等方法,提高
修性
方法五:人 机工程学设 计,提高可 维修性和可
靠性
机械工程中的动力学响应与优化设计

机械工程中的动力学响应与优化设计在机械工程中,动力学响应和优化设计是两个非常重要的概念。
动力学响应涉及到机械系统在外界力的作用下的运动和变形情况,而优化设计则是为了使机械系统在给定的工作条件下达到最佳性能。
1. 动力学响应的概念动力学响应是指机械系统在外界载荷或激励下产生的运动和变形情况。
在机械工程中,我们经常会遇到各种各样的载荷,例如冲击载荷、振动载荷等。
这些载荷对机械系统的影响是非常复杂的,需要通过动力学分析方法来研究。
在动力学响应的研究中,我们经常使用的一个概念是固有频率。
固有频率是指机械系统在自由振动时的固有振动频率,它是机械系统的一种固有特性。
当外界激励频率与机械系统的固有频率接近时,机械系统的动力学响应会出现共振现象,从而引发严重的振动和变形问题。
2. 动力学响应的分析方法为了研究机械系统的动力学响应,我们需要使用一些分析方法。
其中最常用的方法之一是有限元分析方法。
有限元分析是一种将连续介质离散为有限个几何单元的方法,它可以有效地求解机械系统的运动方程和变形方程。
另外一个常用的方法是模态分析方法。
模态分析是一种分析机械系统共振和固有频率的方法。
通过模态分析,我们可以确定机械系统的模态形式和对应的固有频率。
除了有限元分析和模态分析,还有一些其他方法也可以用于动力学响应的分析,例如频域分析和时域分析等。
这些方法可以根据实际情况选择使用,以获得更准确和可靠的结果。
3. 优化设计的概念机械系统的优化设计是指在满足给定工作条件和约束条件的情况下,通过调整设计变量来达到最佳性能。
优化设计是机械工程领域的一个重要研究领域,它可以提高机械系统的性能和效率。
在优化设计中,我们通常需要考虑多个目标函数和多个约束条件。
目标函数是我们希望最小化或最大化的性能指标,例如系统的重量、成本、能量损失等。
约束条件是我们在设计中必须满足的条件,例如材料的强度限制、空间限制等。
为了实现优化设计,我们可以使用一些数值优化算法,例如遗传算法、粒子群算法等。
机械工程中的零部件可靠性优化设计
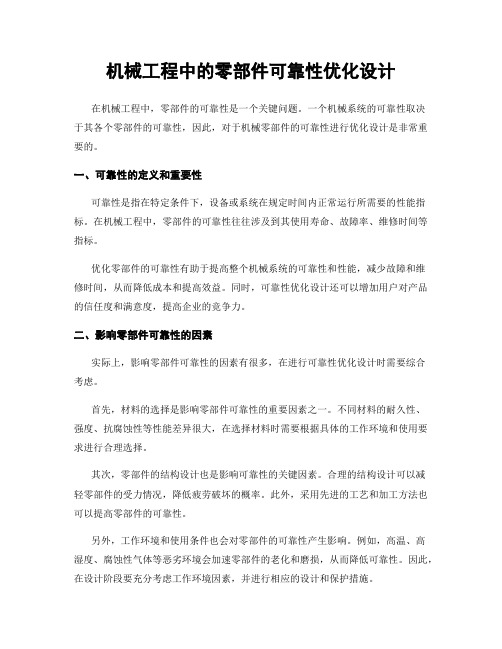
机械工程中的零部件可靠性优化设计在机械工程中,零部件的可靠性是一个关键问题。
一个机械系统的可靠性取决于其各个零部件的可靠性,因此,对于机械零部件的可靠性进行优化设计是非常重要的。
一、可靠性的定义和重要性可靠性是指在特定条件下,设备或系统在规定时间内正常运行所需要的性能指标。
在机械工程中,零部件的可靠性往往涉及到其使用寿命、故障率、维修时间等指标。
优化零部件的可靠性有助于提高整个机械系统的可靠性和性能,减少故障和维修时间,从而降低成本和提高效益。
同时,可靠性优化设计还可以增加用户对产品的信任度和满意度,提高企业的竞争力。
二、影响零部件可靠性的因素实际上,影响零部件可靠性的因素有很多,在进行可靠性优化设计时需要综合考虑。
首先,材料的选择是影响零部件可靠性的重要因素之一。
不同材料的耐久性、强度、抗腐蚀性等性能差异很大,在选择材料时需要根据具体的工作环境和使用要求进行合理选择。
其次,零部件的结构设计也是影响可靠性的关键因素。
合理的结构设计可以减轻零部件的受力情况,降低疲劳破坏的概率。
此外,采用先进的工艺和加工方法也可以提高零部件的可靠性。
另外,工作环境和使用条件也会对零部件的可靠性产生影响。
例如,高温、高湿度、腐蚀性气体等恶劣环境会加速零部件的老化和磨损,从而降低可靠性。
因此,在设计阶段要充分考虑工作环境因素,并进行相应的设计和保护措施。
三、可靠性优化设计方法针对机械工程中的零部件可靠性优化设计,现代工程学科提出了许多方法和技术。
首先,应用故障树分析(FTA)方法可以帮助工程师理解零部件故障的原因和可能性,并制定相应的措施来降低故障和提高可靠性。
FTA将零部件故障看作是一个逻辑事件,通过分析零部件的失效模式和失效率,可以识别出可能导致整个系统失效的关键因素,并采取相应措施进行优化。
其次,采用可靠性设计(RD)方法可以在设计阶段考虑到可靠性要求,从而在设计过程中解决可能导致故障的问题。
可靠性设计包括统计分析、可靠性控制、设计改进和可靠性测试等方法。
- 1、下载文档前请自行甄别文档内容的完整性,平台不提供额外的编辑、内容补充、找答案等附加服务。
- 2、"仅部分预览"的文档,不可在线预览部分如存在完整性等问题,可反馈申请退款(可完整预览的文档不适用该条件!)。
- 3、如文档侵犯您的权益,请联系客服反馈,我们会尽快为您处理(人工客服工作时间:9:00-18:30)。
21年 1 02 月
林 业 机 械 与 木 工 设 备
F R S R C I E Y& WO D R I G E U P N O E T Y MA H N R O WO K N Q IME T
V l 0N . o 4 o 1
J .02 a 21 n
随着科 学技术的飞速发展 ,人 们不仅需要 多功能 的产 品 ,而且 还需要产 品能够 可靠 地实现其所 具有 的 功能 。因此 , 以产品可靠性为 目的的可靠性设计应运而 生, 并得到迅 速发展 和广泛应用 。
1 可靠性设计及 其发展
制造生产 、 验 、 、 试 使用 维护 、 管理等各个环节。因此 , 这
项新兴技术在军工 、 航空 、 天 、 航 电子 、 机械等 工业领域
得到广泛的应 用。
1 可靠性 的发展 史 . 1
人类从开始研究 可靠性技术 至今 ,大 约经历 了 6 0
为 了了解可靠性设计 技术 , 我们必须首先 了解什么
余年的历史 。研究其发展过 程 , 可归纳为初期研究 、 形 成发展 和进一 步国际化三个 阶段 。
大战爆发后 , 国参 战的飞机 、 美 军舰等重要军 事装备常 因故障贻误战机 ,为 此军事 装备 的可靠性 问题逐渐引 起 了人们 的关注 ,开始着 手研究如何避免 和减少这些
间等条件下 , 使设计的产品具有满意的可靠性要求, 这 就是产 品的可靠性设计 。可靠性设 计不仅涉及传 统设
计技术 , 还与系统工程 、 而且 价值 工程 、 环境工程 、 工程
关键词 : 机械工程 ; 设计 ; 可靠性 ; 新技术
中图分类号 :H12 T 2 文献标识码 : A 文章编号 :0 5 2 5 (0 2 0 — 0 9 0 2 9 — 9 3 2 1 ) 10 4 — 2
Rei b l y Op i ia i n De i n o e h n c lEn i e rn l i t t z t sg fM c a i a gn e i g a i m o
许鹏辉 韩 。
青
(. 1江苏省 交通技 师学院机械 系, 江苏 镇 江 2 20 ;. 10 6 2红河学院工学院, 云南 蒙 自 6 10 ) 6 10
摘
要 : 可靠性优化设 计方法应用 于机械 工程的设计 中, 将 阐述 了从 可靠性 角度进 行产品开发设 计 时应注意
的几 个 问题 。
“ 意外” 事故的发生并最早提出了产品的定量可靠性问 题。接 着美 国 、 国的专家 针对 飞机 、一Ⅱ火箭诱导装 德 V
置的可靠性又 提出了相应 的指标 。14 92年美 国麻省理 工学院 的一个研究室对真空 管的可靠性进行 了相当深
心理学、质量控制技术和计算机技术等密切相关 。因 此, 它是一个多学科、 多技术相融合的新兴技术。它不
但应用 于产 品的设 计过程 ,而且 还广泛应用 于产 品 的
收稿 日期 :0 1 1— 9 2 1-0 2
入的研究。所有这些都表明可靠性研究已进入了定量 研究的初期 阶段 。
() 2形成发展 阶段(o世纪 5—0年代 )在这一时 2 06 :
期, 世界上一些工业发达 的国家 , 如美 国 、 苏联 、 前 原西
() 1初期研究 阶段 (0世纪 3 ~ O年代 )二次世界 2 04 :
是产 品的可靠性 。可靠性 的经典定义是 :产 品在规定条 “
件下和规定 时间 内, 完成规定 功能的能力 。” 义 中的 定
“ 产品” 是作为单位研究和分别试 验对象 的任何元件 、 器 件、 设备或系统 , 甚至可 以把人的作用也包括进去。 在产 品设计 中 , 应用可靠性 的理论和技术 、 据需 根 要和可能 、 优先考虑 可靠性要求 。在满 足性能 、 费用 、 时
p o lmsn e i gatnini h e eo me t n e in o r d csaesae rm ep rp cieo l it . r be e d n t to t ed v lp n dd sg f o u t y ttdfo t e s e t f ei l y e n a p h v r a i b Ke r s: c ie n i e rn ; e in r l b l y n w c n lg y wo d ma hn r e gn ei g d sg ;ei i t; e t h oo y y a i e
X eg h i HA n ̄ U P n - u , N Qig
(.e a m n cai l nier g J n s r f ehi a o ee hnin a gu2 20 , hn; 1 pr et f h n a E g ei ,i guTa i Tc nc nC l g,Z ej g i s 10 6 C i D t o Me c n n a fc i 与 木 工 设 备
第4 卷 0
德、 日本等对 可靠 性开始 了有组织 的研究 工作 , 并取得
了许 多重要 成果 ,基本上确定 了可靠 性研究 的理论基 础和研究方 向,使 可靠性研究进 入了一个新 的发展 阶
2Sho o eh o g, e ie C l g, nzY na 6 0 C ia . ol f cn l y R dRvr ol e Megi u nn6 10 , h ) c T o e 1 n
Ab ta t T eie l blyo t zt nd s nia pidi ed s f n ier gma hn r rd cs n v rl sr c : h a f ei it pi ai ei p l t ei o gn ei c ieyp o u t a ds ea d or a i mi o g s e nh n g e n e