后防撞梁设计总结
后防撞梁校核内容

后防撞梁校核内容一、引言后防撞梁是指安装在汽车后部的一种保护装置,用于在车辆发生碰撞时吸收冲击力,减轻乘员受伤程度。
而后防撞梁校核则是对该装置进行检验和计算,以确保其符合安全标准和法规要求。
本文将对后防撞梁校核内容进行详细介绍。
二、后防撞梁校核的目的1. 确定后防撞梁的材料、形状和尺寸等参数;2. 检验后防撞梁是否符合安全标准和法规要求;3. 评估后防撞梁在碰撞事故中的性能。
三、后防撞梁校核的内容1. 材料选择:根据汽车型号和设计要求,选择合适的材料来制造后防撞梁。
常用材料包括钢铝复合板、高强度钢板、铝镁合金等。
2. 形状设计:设计后防撞梁的形状,通常为矩形或圆形截面。
需要考虑到空间限制、外观美观以及碰撞时对乘员的保护程度等因素。
3. 尺寸计算:根据汽车型号和设计要求,计算后防撞梁的长度、宽度、厚度以及截面积等参数。
需要保证后防撞梁具有足够的刚度和强度,能够吸收碰撞时产生的冲击力。
4. 碰撞模拟:使用计算机模拟软件对后防撞梁在碰撞事故中的性能进行评估。
需要考虑到不同碰撞角度、速度和质量等因素,以确保后防撞梁能够有效地吸收冲击力,并保护乘员免受伤害。
四、后防撞梁校核的标准1. 汽车制造商自行制定的标准;2. 国家法规和标准,如中国GB/T 32656-2016《汽车安全技术要求》;3. 国际标准,如美国联邦汽车安全标准FMVSS 301。
五、后防撞梁校核的方法1. 数值模拟法:使用计算机软件对后防撞梁进行碰撞模拟,评估其性能;2. 实验测试法:通过实验测试来检验后防撞梁的性能。
常用的测试方法包括静态弯曲试验、动态碰撞试验和疲劳试验等。
六、后防撞梁校核的注意事项1. 合理选择材料,确保后防撞梁具有足够的强度和刚度;2. 考虑到不同碰撞角度、速度和质量等因素,对后防撞梁进行全面的碰撞模拟和实验测试;3. 根据国家法规和标准以及汽车制造商自行制定的标准进行校核;4. 严格按照设计要求制造后防撞梁,确保其符合安全标准和法规要求。
汽车防撞横梁冲压工艺研究及模具设计探讨
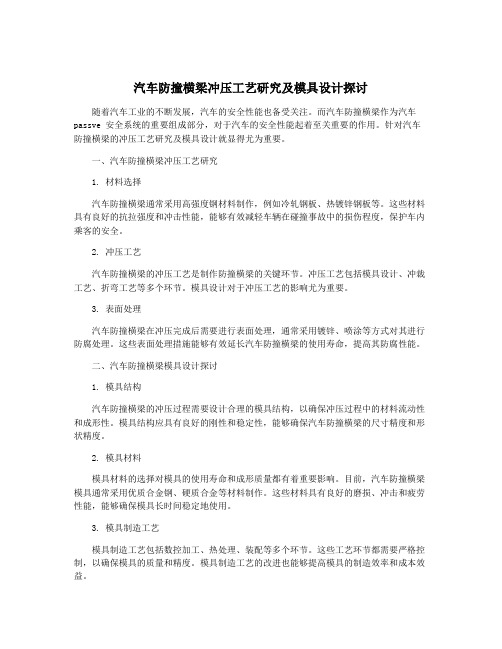
汽车防撞横梁冲压工艺研究及模具设计探讨随着汽车工业的不断发展,汽车的安全性能也备受关注。
而汽车防撞横梁作为汽车passve 安全系统的重要组成部分,对于汽车的安全性能起着至关重要的作用。
针对汽车防撞横梁的冲压工艺研究及模具设计就显得尤为重要。
一、汽车防撞横梁冲压工艺研究1. 材料选择汽车防撞横梁通常采用高强度钢材料制作,例如冷轧钢板、热镀锌钢板等。
这些材料具有良好的抗拉强度和冲击性能,能够有效减轻车辆在碰撞事故中的损伤程度,保护车内乘客的安全。
2. 冲压工艺汽车防撞横梁的冲压工艺是制作防撞横梁的关键环节。
冲压工艺包括模具设计、冲裁工艺、折弯工艺等多个环节。
模具设计对于冲压工艺的影响尤为重要。
3. 表面处理汽车防撞横梁在冲压完成后需要进行表面处理,通常采用镀锌、喷涂等方式对其进行防腐处理。
这些表面处理措施能够有效延长汽车防撞横梁的使用寿命,提高其防腐性能。
二、汽车防撞横梁模具设计探讨1. 模具结构汽车防撞横梁的冲压过程需要设计合理的模具结构,以确保冲压过程中的材料流动性和成形性。
模具结构应具有良好的刚性和稳定性,能够确保汽车防撞横梁的尺寸精度和形状精度。
2. 模具材料模具材料的选择对模具的使用寿命和成形质量都有着重要影响。
目前,汽车防撞横梁模具通常采用优质合金钢、硬质合金等材料制作。
这些材料具有良好的磨损、冲击和疲劳性能,能够确保模具长时间稳定地使用。
3. 模具制造工艺模具制造工艺包括数控加工、热处理、装配等多个环节。
这些工艺环节都需要严格控制,以确保模具的质量和精度。
模具制造工艺的改进也能够提高模具的制造效率和成本效益。
汽车防撞横梁冲压工艺研究及模具设计对于汽车 passve 安全系统的提升具有重要意义。
通过对汽车防撞横梁材料、冲压工艺和模具设计的深入研究,可以为汽车行业提供更加安全可靠的汽车 passve 安全系统产品,推动汽车工业的持续健康发展。
后防撞梁晃动的原理
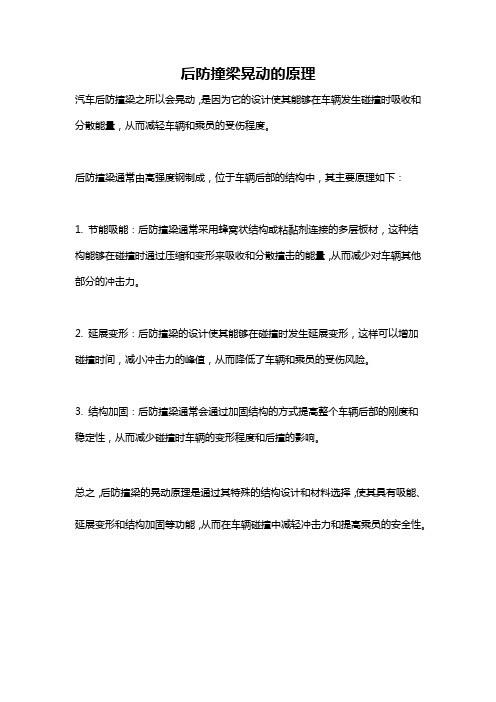
后防撞梁晃动的原理
汽车后防撞梁之所以会晃动,是因为它的设计使其能够在车辆发生碰撞时吸收和分散能量,从而减轻车辆和乘员的受伤程度。
后防撞梁通常由高强度钢制成,位于车辆后部的结构中,其主要原理如下:
1. 节能吸能:后防撞梁通常采用蜂窝状结构或粘黏剂连接的多层板材,这种结构能够在碰撞时通过压缩和变形来吸收和分散撞击的能量,从而减少对车辆其他部分的冲击力。
2. 延展变形:后防撞梁的设计使其能够在碰撞时发生延展变形,这样可以增加碰撞时间,减小冲击力的峰值,从而降低了车辆和乘员的受伤风险。
3. 结构加固:后防撞梁通常会通过加固结构的方式提高整个车辆后部的刚度和稳定性,从而减少碰撞时车辆的变形程度和后撞的影响。
总之,后防撞梁的晃动原理是通过其特殊的结构设计和材料选择,使其具有吸能、延展变形和结构加固等功能,从而在车辆碰撞中减轻冲击力和提高乘员的安全性。
前后防撞梁和
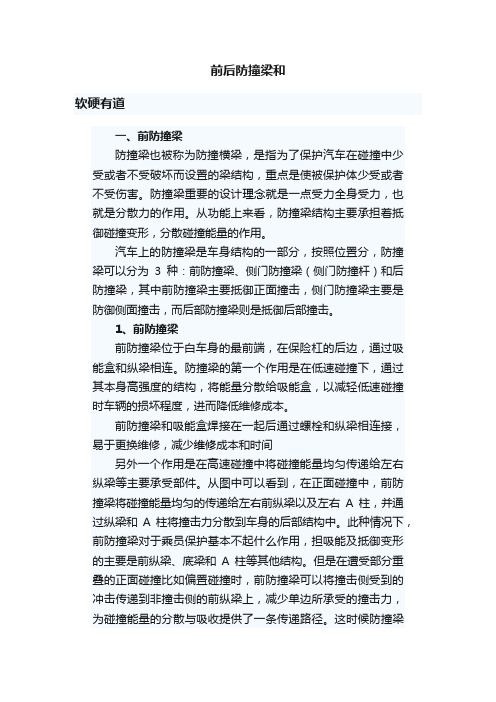
前后防撞梁和软硬有道一、前防撞梁防撞梁也被称为防撞横梁,是指为了保护汽车在碰撞中少受或者不受破坏而设置的梁结构,重点是使被保护体少受或者不受伤害。
防撞梁重要的设计理念就是一点受力全身受力,也就是分散力的作用。
从功能上来看,防撞梁结构主要承担着抵御碰撞变形,分散碰撞能量的作用。
汽车上的防撞梁是车身结构的一部分,按照位置分,防撞梁可以分为3种:前防撞梁、侧门防撞梁(侧门防撞杆)和后防撞梁,其中前防撞梁主要抵御正面撞击,侧门防撞梁主要是防御侧面撞击,而后部防撞梁则是抵御后部撞击。
1、前防撞梁前防撞梁位于白车身的最前端,在保险杠的后边,通过吸能盒和纵梁相连。
防撞梁的第一个作用是在低速碰撞下,通过其本身高强度的结构,将能量分散给吸能盒,以减轻低速碰撞时车辆的损坏程度,进而降低维修成本。
前防撞梁和吸能盒焊接在一起后通过螺栓和纵梁相连接,易于更换维修,减少维修成本和时间另外一个作用是在高速碰撞中将碰撞能量均匀传递给左右纵梁等主要承受部件。
从图中可以看到,在正面碰撞中,前防撞梁将碰撞能量均匀的传递给左右前纵梁以及左右A柱,并通过纵梁和A柱将撞击力分散到车身的后部结构中。
此种情况下,前防撞梁对于乘员保护基本不起什么作用,担吸能及抵御变形的主要是前纵梁、底梁和A柱等其他结构。
但是在遭受部分重叠的正面碰撞比如偏置碰撞时,前防撞梁可以将撞击侧受到的冲击传递到非撞击侧的前纵梁上,减少单边所承受的撞击力,为碰撞能量的分散与吸收提供了一条传递路径。
这时候防撞梁才能起到真正的作用。
碰撞时撞击力经过防撞梁的分解作用后的传递路线前防撞梁强度太弱,导致防撞梁内凹,发动机严重受损,而和防撞梁想连接的吸能盒则却安然无恙,防撞梁失去应有作用从以上可以知道,在碰撞过程中前防撞梁不能发生断裂失效,否则就不能在关键时刻起到传递和分解力的作用,所以防撞梁本身应该具有极高的强度。
而影响其强度的有材料、结构和尺寸三个方面。
对于汽车防撞梁而言,现在主要有三种材料:高强度钢材、玻璃纤维和铝合金等轻金属合金。
汽车前后防撞梁设计规范标准
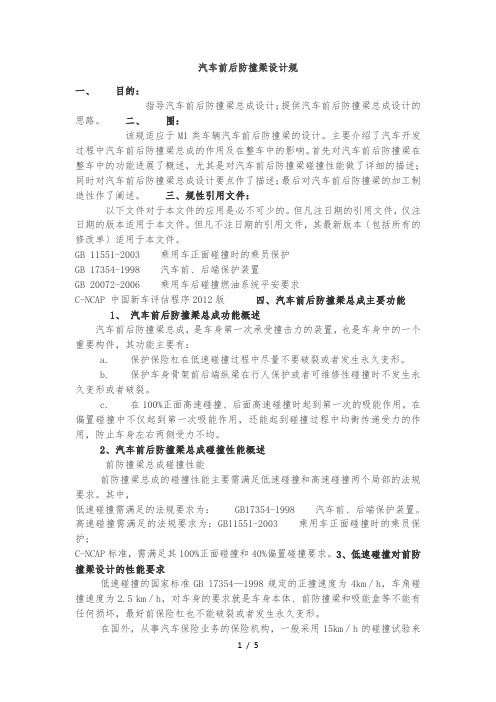
汽车前后防撞梁设计规一、目的:指导汽车前后防撞梁总成设计;提供汽车前后防撞梁总成设计的思路。
二、围:该规适应于M1类车辆汽车前后防撞梁的设计。
主要介绍了汽车开发过程中汽车前后防撞梁总成的作用及在整车中的影响。
首先对汽车前后防撞梁在整车中的功能进展了概述,尤其是对汽车前后防撞梁碰撞性能做了详细的描述;同时对汽车前后防撞梁总成设计要点作了描述;最后对汽车前后防撞梁的加工制造性作了阐述。
三、规性引用文件:以下文件对于本文件的应用是必不可少的。
但凡注日期的引用文件,仅注日期的版本适用于本文件。
但凡不注日期的引用文件,其最新版本〔包括所有的修改单〕适用于本文件。
GB 11551-2003 乘用车正面碰撞时的乘员保护GB 17354-1998 汽车前、后端保护装置GB 20072-2006 乘用车后碰撞燃油系统平安要求C-NCAP 中国新车评估程序2012版四、汽车前后防撞梁总成主要功能1、汽车前后防撞梁总成功能概述汽车前后防撞梁总成,是车身第一次承受撞击力的装置,也是车身中的一个重要构件,其功能主要有:a. 保护保险杠在低速碰撞过程中尽量不要破裂或者发生永久变形。
b. 保护车身骨架前后端纵梁在行人保护或者可维修性碰撞时不发生永久变形或者破裂。
c. 在100%正面高速碰撞、后面高速碰撞时起到第一次的吸能作用,在偏置碰撞中不仅起到第一次吸能作用,还能起到碰撞过程中均衡传递受力的作用,防止车身左右两侧受力不均。
2、汽车前后防撞梁总成碰撞性能概述前防撞梁总成碰撞性能前防撞梁总成的碰撞性能主要需满足低速碰撞和高速碰撞两个局部的法规要求。
其中,低速碰撞需满足的法规要求为:GB17354-1998 汽车前、后端保护装置。
高速碰撞需满足的法规要求为:GB11551-2003 乘用车正面碰撞时的乘员保护;C-NCAP标准,需满足其100%正面碰撞和40%偏置碰撞要求。
3、低速碰撞对前防撞梁设计的性能要求低速碰撞的国家标准GB l7354—1998规定的正撞速度为4km/h,车角碰撞速度为2.5 km/h,对车身的要求就是车身本体、前防撞梁和吸能盒等不能有任何损坏,最好前保险杠也不能破裂或者发生永久变形。
汽车前后防撞梁设计地的要求的要求规范
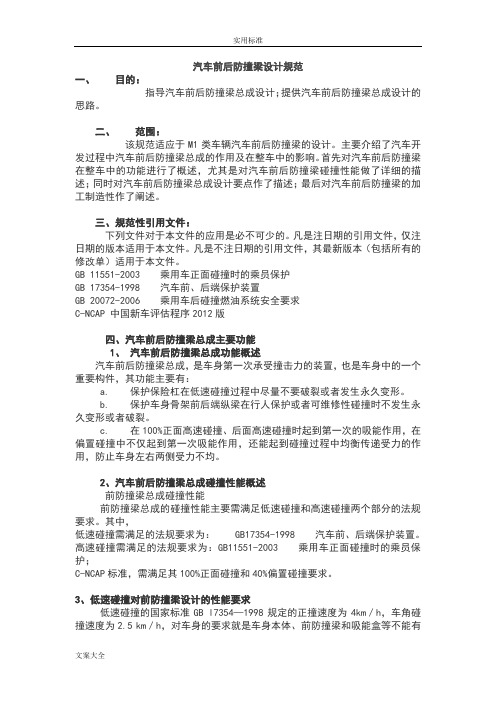
汽车前后防撞梁设计规范一、目的:指导汽车前后防撞梁总成设计;提供汽车前后防撞梁总成设计的思路。
二、范围:该规范适应于M1类车辆汽车前后防撞梁的设计。
主要介绍了汽车开发过程中汽车前后防撞梁总成的作用及在整车中的影响。
首先对汽车前后防撞梁在整车中的功能进行了概述,尤其是对汽车前后防撞梁碰撞性能做了详细的描述;同时对汽车前后防撞梁总成设计要点作了描述;最后对汽车前后防撞梁的加工制造性作了阐述。
三、规范性引用文件:下列文件对于本文件的应用是必不可少的。
凡是注日期的引用文件,仅注日期的版本适用于本文件。
凡是不注日期的引用文件,其最新版本(包括所有的修改单)适用于本文件。
GB 11551-2003 乘用车正面碰撞时的乘员保护GB 17354-1998 汽车前、后端保护装置GB 20072-2006 乘用车后碰撞燃油系统安全要求C-NCAP 中国新车评估程序2012版四、汽车前后防撞梁总成主要功能1、汽车前后防撞梁总成功能概述汽车前后防撞梁总成,是车身第一次承受撞击力的装置,也是车身中的一个重要构件,其功能主要有:a. 保护保险杠在低速碰撞过程中尽量不要破裂或者发生永久变形。
b. 保护车身骨架前后端纵梁在行人保护或者可维修性碰撞时不发生永久变形或者破裂。
c. 在100%正面高速碰撞、后面高速碰撞时起到第一次的吸能作用,在偏置碰撞中不仅起到第一次吸能作用,还能起到碰撞过程中均衡传递受力的作用,防止车身左右两侧受力不均。
2、汽车前后防撞梁总成碰撞性能概述前防撞梁总成碰撞性能前防撞梁总成的碰撞性能主要需满足低速碰撞和高速碰撞两个部分的法规要求。
其中,低速碰撞需满足的法规要求为:GB17354-1998 汽车前、后端保护装置。
高速碰撞需满足的法规要求为:GB11551-2003 乘用车正面碰撞时的乘员保护;C-NCAP标准,需满足其100%正面碰撞和40%偏置碰撞要求。
3、低速碰撞对前防撞梁设计的性能要求低速碰撞的国家标准GB l7354—1998规定的正撞速度为4km/h,车角碰撞速度为2.5 km/h,对车身的要求就是车身本体、前防撞梁和吸能盒等不能有任何损坏,最好前保险杠也不能破裂或者发生永久变形。
汽车前后防撞梁设计要求规范
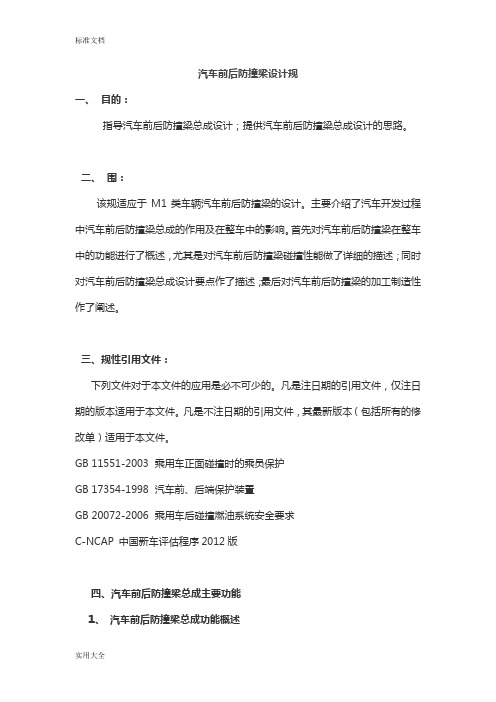
汽车前后防撞梁设计规一、目的:指导汽车前后防撞梁总成设计;提供汽车前后防撞梁总成设计的思路。
二、围:该规适应于M1类车辆汽车前后防撞梁的设计。
主要介绍了汽车开发过程中汽车前后防撞梁总成的作用及在整车中的影响。
首先对汽车前后防撞梁在整车中的功能进行了概述,尤其是对汽车前后防撞梁碰撞性能做了详细的描述;同时对汽车前后防撞梁总成设计要点作了描述;最后对汽车前后防撞梁的加工制造性作了阐述。
三、规性引用文件:下列文件对于本文件的应用是必不可少的。
凡是注日期的引用文件,仅注日期的版本适用于本文件。
凡是不注日期的引用文件,其最新版本(包括所有的修改单)适用于本文件。
GB 11551-2003 乘用车正面碰撞时的乘员保护GB 17354-1998 汽车前、后端保护装置GB 20072-2006 乘用车后碰撞燃油系统安全要求C-NCAP 中国新车评估程序2012版四、汽车前后防撞梁总成主要功能1、汽车前后防撞梁总成功能概述汽车前后防撞梁总成,是车身第一次承受撞击力的装置,也是车身中的一个重要构件,其功能主要有:a. 保护保险杠在低速碰撞过程中尽量不要破裂或者发生永久变形。
b. 保护车身骨架前后端纵梁在行人保护或者可维修性碰撞时不发生永久变形或者破裂。
c. 在100%正面高速碰撞、后面高速碰撞时起到第一次的吸能作用,在偏置碰撞中不仅起到第一次吸能作用,还能起到碰撞过程中均衡传递受力的作用,防止车身左右两侧受力不均。
2、汽车前后防撞梁总成碰撞性能概述前防撞梁总成碰撞性能前防撞梁总成的碰撞性能主要需满足低速碰撞和高速碰撞两个部分的法规要求。
其中,低速碰撞需满足的法规要求为: GB17354-1998 汽车前、后端保护装置。
高速碰撞需满足的法规要求为:GB11551-2003 乘用车正面碰撞时的乘员保护;C-NCAP标准,需满足其100%正面碰撞和40%偏置碰撞要求。
3、低速碰撞对前防撞梁设计的性能要求低速碰撞的国家标准GB l7354—1998规定的正撞速度为4km/h,车角碰撞速度为2.5 km/h,对车身的要求就是车身本体、前防撞梁和吸能盒等不能有任何损坏,最好前保险杠也不能破裂或者发生永久变形。
gmt后防撞梁轻量化设计及耐撞性能优化
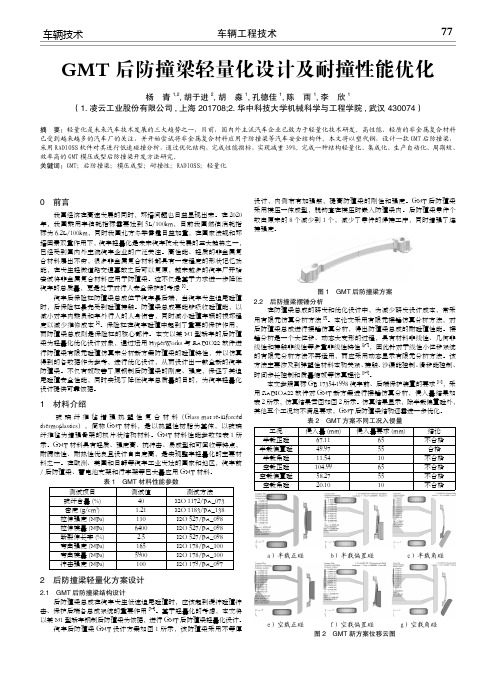
车辆工程技术77车辆技术GMT后防撞梁轻量化设计及耐撞性能优化杨 青1,2,胡于进2,胡 淼1,孔德佳1,陈 雨1,李 欣1(1.凌云工业股份有限公司,上海 201708;2.华中科技大学机械科学与工程学院,武汉 430074)摘 要:轻量化是未来汽车技术发展的三大趋势之一,目前,国内外主流汽车企业已致力于轻量化技术研发。
高性能、轻质的非金属复合材料已受到越来越多的汽车厂的关注,并开始尝试将非金属复合材料应用于防撞梁等汽车安全结构件。
本文将以塑代钢,设计一款GMT后防撞梁,采用RADIOSS软件对其进行低速碰撞分析,通过优化结构,完成性能指标,实现减重39%。
完成一种结构轻量化、集成化、生产自动化、周期短、效率高的GMT模压成型后防撞梁开发方法研究。
关键词:GMT;后防撞梁;模压成型;耐撞性;RADIOSS;轻量化0 前言 我国经济在高速发展的同时,环境问题也日益显现出来。
在2020年,我国乘用车油耗指标需要达到5L/100km,目前我国燃油消耗指标为6.2L/100km,同时我国北方冬季雾霾日益加重,在国家法规和环境因素双重作用下,汽车轻量化是未来汽车技术发展的三大趋势之一,已经受到国内外主流汽车企业的广泛关注。
高性能、轻质的非金属复合材料层出不穷,很多非金属复合材料都具有一定程度的形状记忆功能,在发生轻微道路交通事故之后可以复原,越来越多的汽车厂开始尝试将非金属复合材料应用于防撞梁。
这不仅是基于力求进一步降低汽车的总质量,更是处于对行人安全保护的考虑[1]。
汽车后保险杠防撞梁总成位于汽车最后端,当汽车发生追尾碰撞时,后保险杠最先受到碰撞接触。
防撞梁总成要能够吸收碰撞能,以减小对车内乘员和车外行人的人身伤害,同时减小碰撞车辆的损坏程度以减少维修成本[2]。
保险杠在汽车碰撞中起到了重要的保护作用,而防撞梁总成则是保险杠的核心部件。
本文以某M1型轿车的后防撞梁为轻量化优化设计对象,通过运用HyperWorks与RADIOSS软件进行防撞梁有限元碰撞仿真来分析新方案防撞梁的碰撞特性,并以仿真得到的各数据作为参考,进行优化设计,从而设计出一款全新的汽车防撞梁。
防撞梁结构优化方法
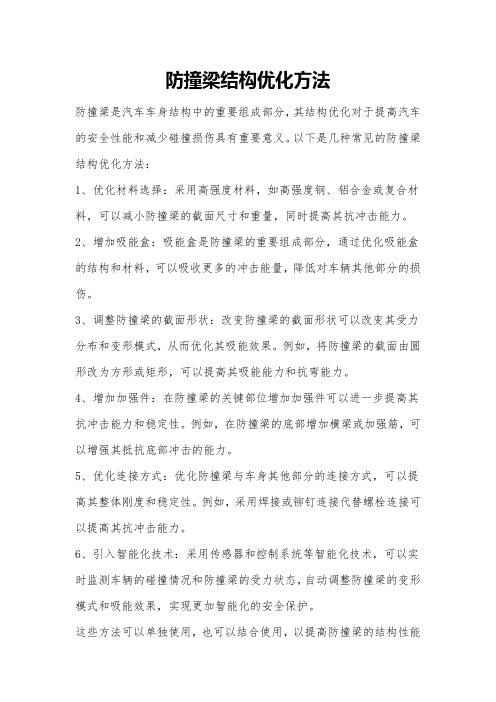
防撞梁结构优化方法
防撞梁是汽车车身结构中的重要组成部分,其结构优化对于提高汽车的安全性能和减少碰撞损伤具有重要意义。
以下是几种常见的防撞梁结构优化方法:
1、优化材料选择:采用高强度材料,如高强度钢、铝合金或复合材料,可以减小防撞梁的截面尺寸和重量,同时提高其抗冲击能力。
2、增加吸能盒:吸能盒是防撞梁的重要组成部分,通过优化吸能盒的结构和材料,可以吸收更多的冲击能量,降低对车辆其他部分的损伤。
3、调整防撞梁的截面形状:改变防撞梁的截面形状可以改变其受力分布和变形模式,从而优化其吸能效果。
例如,将防撞梁的截面由圆形改为方形或矩形,可以提高其吸能能力和抗弯能力。
4、增加加强件:在防撞梁的关键部位增加加强件可以进一步提高其抗冲击能力和稳定性。
例如,在防撞梁的底部增加横梁或加强筋,可以增强其抵抗底部冲击的能力。
5、优化连接方式:优化防撞梁与车身其他部分的连接方式,可以提高其整体刚度和稳定性。
例如,采用焊接或铆钉连接代替螺栓连接可以提高其抗冲击能力。
6、引入智能化技术:采用传感器和控制系统等智能化技术,可以实时监测车辆的碰撞情况和防撞梁的受力状态,自动调整防撞梁的变形模式和吸能效果,实现更加智能化的安全保护。
这些方法可以单独使用,也可以结合使用,以提高防撞梁的结构性能
和安全性。
在优化过程中需要考虑车辆的整体性能、制造成本和工艺要求等因素。
汽车防撞梁总成结构设计
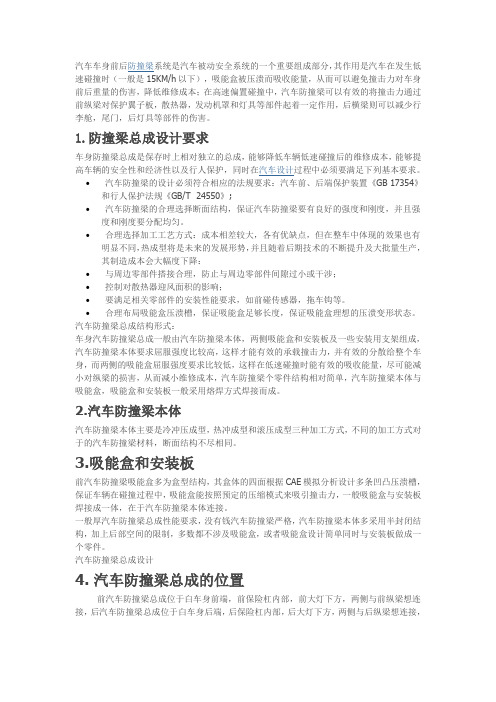
汽车车身前后防撞梁系统是汽车被动安全系统的一个重要组成部分,其作用是汽车在发生低速碰撞时(一般是15KM/h以下),吸能盒被压溃而吸收能量,从而可以避免撞击力对车身前后重量的伤害,降低维修成本;在高速偏置碰撞中,汽车防撞梁可以有效的将撞击力通过前纵梁对保护翼子板,散热器,发动机罩和灯具等部件起着一定作用,后横梁则可以减少行李舱,尾门,后灯具等部件的伤害。
1.防撞梁总成设计要求车身防撞梁总成是保存时上相对独立的总成,能够降低车辆低速碰撞后的维修成本,能够提高车辆的安全性和经济性以及行人保护,同时在汽车设计过程中必须要满足下列基本要求。
∙汽车防撞梁的设计必须符合相应的法规要求:汽车前、后端保护装置《GB 17354》和行人保护法规《GB/T 24550》;∙汽车防撞梁的合理选择断面结构,保证汽车防撞梁要有良好的强度和刚度,并且强度和刚度要分配均匀。
∙合理选择加工工艺方式:成本相差较大,各有优缺点,但在整车中体现的效果也有明显不同,热成型将是未来的发展形势,并且随着后期技术的不断提升及大批量生产,其制造成本会大幅度下降:∙与周边零部件搭接合理,防止与周边零部件间隙过小或干涉;∙控制对散热器迎风面积的影响;∙要满足相关零部件的安装性能要求,如前碰传感器,拖车钩等。
∙合理布局吸能盒压溃槽,保证吸能盒足够长度,保证吸能盒理想的压溃变形状态。
汽车防撞梁总成结构形式:车身汽车防撞梁总成一般由汽车防撞梁本体,两侧吸能盒和安装板及一些安装用支架组成,汽车防撞梁本体要求屈服强度比较高,这样才能有效的承载撞击力,并有效的分散给整个车身,而两侧的吸能盒屈服强度要求比较低,这样在低速碰撞时能有效的吸收能量,尽可能减小对纵梁的损害,从而减小维修成本,汽车防撞梁个零件结构相对简单,汽车防撞梁本体与吸能盒,吸能盒和安装板一般采用熔焊方式焊接而成。
2.汽车防撞梁本体汽车防撞梁本体主要是冷冲压成型,热冲成型和滚压成型三种加工方式,不同的加工方式对于的汽车防撞梁材料,断面结构不尽相同。
防撞梁设计

盾构施工防撞梁改进摘要:利用缓冲梁来减小撞击力,使电瓶车减速,减小对盾构机主体及后配套台车的安全隐患,保证盾构施工安全。
关键词:缓冲摩擦力滑行盾构施工中的工矿电瓶车的行驶安全是很重要的环节,而我们现有的盾构设备上面对电瓶车在发生溜车时的防护措施都比较简单,只有一根固定横梁,连接于台车之间,用螺栓横向固定。
当电瓶车发生溜车事故后,对横梁产生撞击。
这个时候由于撞击力比较大,使横梁产生变形,当连接螺栓强度足够,会将盾构机后配套台车拉的偏离行走轨道,严重时会引起侧翻危险。
当连接螺栓强度不够时,撞击会使螺栓断裂,无法起到阻挡作用,使电机车撞向盾构机,造成不必要的损失。
为了保证盾构施工中电瓶车的使用安全,也为了减少溜车事故给公司带来的损失,特对防撞梁进行了如下改进。
一.将防撞梁由单一的横梁改为U型梁,目的是:1.改变防撞梁与盾构机台车之间连接螺栓的安装方向。
改变当防撞梁受力时对螺栓作用力的方向,增强螺栓的强度。
保证螺栓在电瓶车撞击防撞梁时不易断裂。
2.增加滑行导轨,给新加入的缓存梁有一定的安装位置。
二.增加缓存梁,目的是:1.保证电瓶车在发生溜车时,作用力不会直接作用在防撞梁上,减少撞击力对防撞梁的损害,并通过缓存梁在滑行导轨上的滑行产生的摩擦力来减小撞击产生的作用力。
并在缓存梁上安装上缓存垫,进一步的减小撞击的作用力,保证电瓶车撞击产生作用力的进一步的分散。
三.在防撞梁里面加入筋板,目的是:1.增强防撞梁的强度,保证在防撞梁受力时不易发生弯曲变形,保证盾构机后配套台车在撞击发生时不会发生偏离轨道甚至侧翻危险。
材料说明:防撞梁焊接用钢板均为20mm厚的钢板,防撞梁与盾构机台车连接使用的螺栓为直径22mm,强度12.9级的高强螺栓。
为了节约成本缓冲梁与滑行轨道直接压紧螺栓使用直径22mm,强度8.8级普通螺栓。
合肥地铁项目经理部朱东海毛卓。
后防撞横梁总成设计指南—20090610
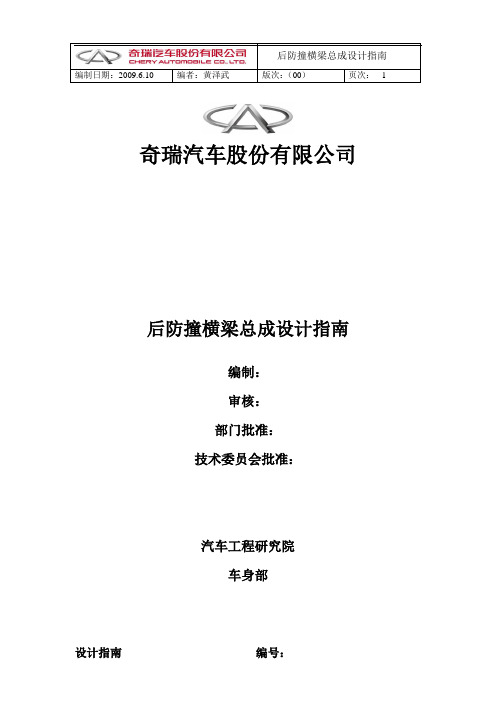
奇瑞汽车股份有限公司后防撞横梁总成设计指南编制:审核:部门批准:技术委员会批准:汽车工程研究院车身部目录第一章概述 (1)1.1该指南的主要目的 (1)1.2该指南的主要内容 (1)第二章法规对比分析 (1)2.1低速碰撞法规要求 (1)2.1.1 政府法规试验规范简介 (1)2.1.2保险协会试验规范简介 (4)2.2高速碰撞法规要求 (5)第三章后防撞横梁的布置设计 (5)3.1后防撞横梁离地高度布置要求 (6)3.2后防撞横梁距后保蒙皮、后备箱边缘等部件的距离 (9)3.3后防撞横梁长度要求 (10)第四章后防撞横梁结构设计 (11)4.1后防撞横梁的安装方式 (11)4.2后防撞横梁的工艺分类 (11)4.3后防撞横梁的截面型式 (13)4.4后防撞横梁的轨迹曲线 (17)4.5吸能盒结构设计 (18)4.5.1常见吸能盒结构 (19)4.6拖车钩结构设计 (20)第五章后防撞横梁的材料定义及减重 (21)5.1后防撞横梁材料选用 (21)5.2后防撞横梁减重设计 (23)第六章后防撞横梁的CAE模拟分析 (23)6.1典型截面的CAE对比分析 (23)6.2后防撞横梁总成碰撞CAE模拟分析 (24)第七章后防撞横梁的设计趋势 (26)7.1高强度材料运用 (26)7.2保护系统装配集成 (27)第一章概述保险杠系统由保险杠蒙皮、吸能块和防撞横梁总成所组成。
防撞横梁总成是保险杠系统的重要组成部分,也是车身结构的重要组成部分,它在汽车低速碰撞中起着决定性作用,同时在高速碰撞中也起着吸能和力量传导的重要作用。
1.1 该指南的主要目的使大家对防撞横梁总成的设计有一个初步的思路,对需要满足的各种条件有一个比较全面的基本认识。
该指南的撰写主要解决以下两个方面的问题:1)防撞横梁的设计需要满足哪些法规方面的要求;2)防撞横梁结构设计需要考虑到的因素,包括材料选用、横梁截面设计、成型工艺选择、拖车钩结构设计、吸能盒结构设计等。
汽车前后防撞梁设计规范
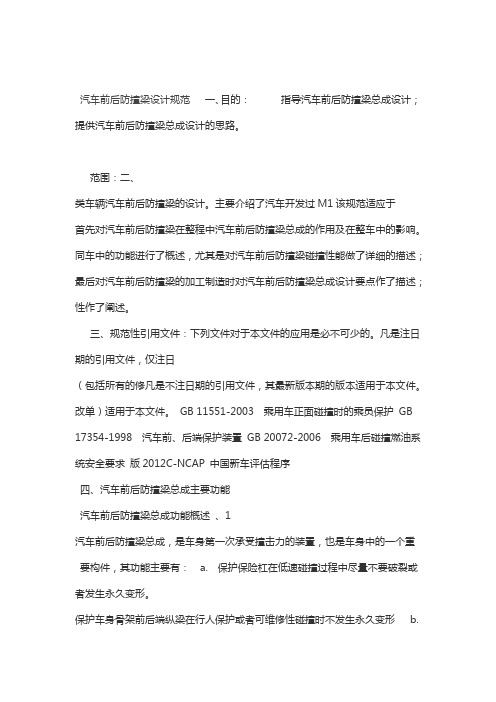
汽车前后防撞梁设计规范一、目的:指导汽车前后防撞梁总成设计;提供汽车前后防撞梁总成设计的思路。
范围:二、类车辆汽车前后防撞梁的设计。
主要介绍了汽车开发过M1该规范适应于首先对汽车前后防撞梁在整程中汽车前后防撞梁总成的作用及在整车中的影响。
同车中的功能进行了概述,尤其是对汽车前后防撞梁碰撞性能做了详细的描述;最后对汽车前后防撞梁的加工制造时对汽车前后防撞梁总成设计要点作了描述;性作了阐述。
三、规范性引用文件:下列文件对于本文件的应用是必不可少的。
凡是注日期的引用文件,仅注日(包括所有的修凡是不注日期的引用文件,其最新版本期的版本适用于本文件。
改单)适用于本文件。
GB 11551-2003 乘用车正面碰撞时的乘员保护GB 17354-1998 汽车前、后端保护装置GB 20072-2006 乘用车后碰撞燃油系统安全要求版2012C-NCAP 中国新车评估程序四、汽车前后防撞梁总成主要功能汽车前后防撞梁总成功能概述、1汽车前后防撞梁总成,是车身第一次承受撞击力的装置,也是车身中的一个重要构件,其功能主要有: a. 保护保险杠在低速碰撞过程中尽量不要破裂或者发生永久变形。
保护车身骨架前后端纵梁在行人保护或者可维修性碰撞时不发生永久变形 b.或者破裂。
正面高速碰撞、后面高速碰撞时起到第一次的吸能作用,在偏置 c. 在100%防碰撞中不仅起到第一次吸能作用,还能起到碰撞过程中均衡传递受力的作用,止车身左右两侧受力不均。
2、汽车前后防撞梁总成碰撞性能概述前防撞梁总成碰撞性能前防撞梁总成的碰撞性能主要需满足低速碰撞和高速碰撞两个部分的法规要求。
其中,汽车前、后端保护装置。
低速碰撞需满足的法规要求为:GB17354-1998乘用车正面碰撞时的乘员保GB11551-2003 高速碰撞需满足的法规要求为:护;100%偏置碰撞要求。
正面碰撞和40%C-NCAP标准,需满足其3、低速碰撞对前防撞梁设计的性能要求,车角碰h1998—规定的正撞速度为4km/l7354低速碰撞的国家标准GB前防撞梁和吸能盒等不能有对车身的要求就是车身本体、h2.5 km撞速度为/,任何损坏,最好前保险杠也不能破裂或者发生永久变形。
汽车前后防撞梁设计规范总结实施方案
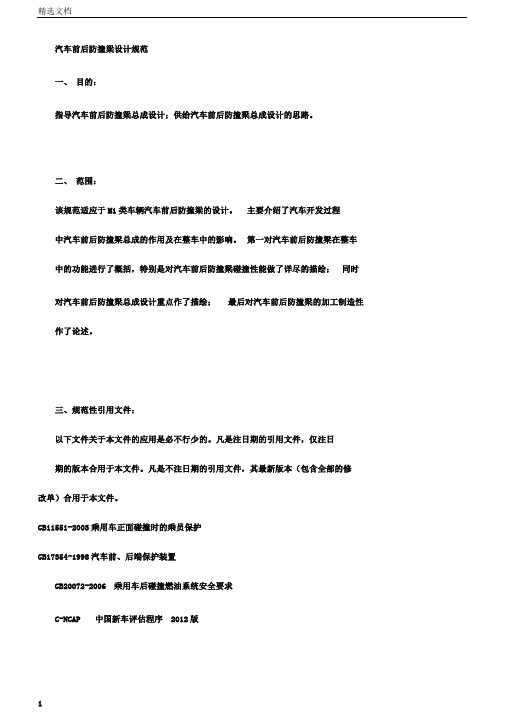
汽车前后防撞梁设计规范一、目的:指导汽车前后防撞梁总成设计;供给汽车前后防撞梁总成设计的思路。
二、范围:该规范适应于M1类车辆汽车前后防撞梁的设计。
主要介绍了汽车开发过程中汽车前后防撞梁总成的作用及在整车中的影响。
第一对汽车前后防撞梁在整车中的功能进行了概括,特别是对汽车前后防撞梁碰撞性能做了详尽的描绘;同时对汽车前后防撞梁总成设计重点作了描绘;最后对汽车前后防撞梁的加工制造性作了论述。
三、规范性引用文件:以下文件关于本文件的应用是必不行少的。
凡是注日期的引用文件,仅注日期的版本合用于本文件。
凡是不注日期的引用文件,其最新版本(包含全部的修改单)合用于本文件。
GB11551-2003乘用车正面碰撞时的乘员保护GB17354-1998汽车前、后端保护装置GB20072-2006 乘用车后碰撞燃油系统安全要求C-NCAP 中国新车评估程序2012版四、汽车前后防撞梁总成主要功能1、汽车前后防撞梁总成功能概括汽车前后防撞梁总成,是车身第一次蒙受撞击力的装置,也是车身中的一个重要构件,其功能主要有:保护保险杠在低速碰撞过程中尽量不要破碎或许发生永远变形。
保护车身骨架前后端纵梁内行人保护或允许维修性碰撞时不发生永远变形或许破碎。
在100%正面高速碰撞、后边高速碰撞时起到第一次的吸能作用,在偏置碰撞中不单起到第一次吸能作用,还可以起到碰撞过程中平衡传达受力的作用,防备车身左右双侧受力不均。
2、汽车前后防撞梁总成碰撞性能概括前防撞梁总成碰撞性能前防撞梁总成的碰撞性能主要需知足低速碰撞和高速碰撞两个部分的法例要求。
此中,低速碰撞需知足的法例要求为:GB17354-1998汽车前、后端保护装置。
高速碰撞需知足的法例要求为:GB11551-2003乘用车正面碰撞时的乘员保护;C-NCAP标准,需知足其100%正面碰撞和40%偏置碰撞要求。
3、低速碰撞对前防撞梁设计的性能要求低速碰撞的国家标准GBl7354—1998规定的正撞速度为4km/h,车角碰撞速度为km/h,对车身的要求就是车身本体、前防撞梁和吸能盒等不可以有任何破坏,最好前保险杠也不可以破碎或许发生永远变形。
23款unit运动版防撞梁
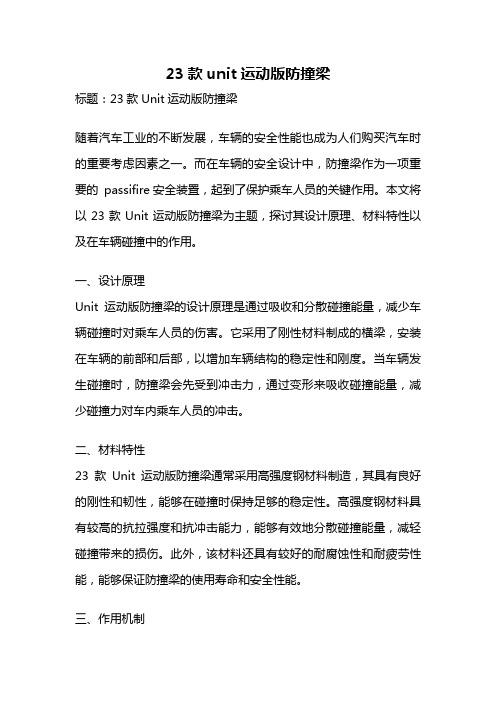
23款unit运动版防撞梁标题:23款Unit运动版防撞梁随着汽车工业的不断发展,车辆的安全性能也成为人们购买汽车时的重要考虑因素之一。
而在车辆的安全设计中,防撞梁作为一项重要的passifire安全装置,起到了保护乘车人员的关键作用。
本文将以23款Unit运动版防撞梁为主题,探讨其设计原理、材料特性以及在车辆碰撞中的作用。
一、设计原理Unit运动版防撞梁的设计原理是通过吸收和分散碰撞能量,减少车辆碰撞时对乘车人员的伤害。
它采用了刚性材料制成的横梁,安装在车辆的前部和后部,以增加车辆结构的稳定性和刚度。
当车辆发生碰撞时,防撞梁会先受到冲击力,通过变形来吸收碰撞能量,减少碰撞力对车内乘车人员的冲击。
二、材料特性23款Unit运动版防撞梁通常采用高强度钢材料制造,其具有良好的刚性和韧性,能够在碰撞时保持足够的稳定性。
高强度钢材料具有较高的抗拉强度和抗冲击能力,能够有效地分散碰撞能量,减轻碰撞带来的损伤。
此外,该材料还具有较好的耐腐蚀性和耐疲劳性能,能够保证防撞梁的使用寿命和安全性能。
三、作用机制23款Unit运动版防撞梁在车辆碰撞中起到了重要的作用。
首先,它可以吸收和分散碰撞能量,减少碰撞力对车辆结构的破坏,从而保护车内乘车人员的安全。
其次,防撞梁的刚性设计可以增加车辆的整体刚度,提高车辆的稳定性和操控性能,减少碰撞时的车辆偏移和侧翻的风险。
再次,防撞梁还可以起到分隔车辆前后部分的作用,防止碰撞时车辆的挤压变形,保持车辆的完整性。
四、应用场景23款Unit运动版防撞梁广泛应用于各类汽车中,特别是高端运动版车型。
运动版车型在设计上追求操控性能和外观动感,而防撞梁的使用可以有效地提升车辆的安全性能,保护乘车人员的生命安全。
因此,23款Unit运动版防撞梁成为了高端运动版车型的标配装置。
五、发展趋势随着汽车工业的不断发展,防撞梁的设计和材料将会不断创新和改进。
未来的防撞梁可能采用更轻量化的材料,如碳纤维复合材料,以提高车辆整体的节能性能。
防撞梁

防撞梁防撞梁可以起到什么作用?大家都知道三角形是最稳定的一个结构,而车身骨架其实就是由许多不规则的三角形所组成,用以抵御来自四面八方的冲击,但是需要说明的是,汽车的骨架并不是所有地方的承受力都一样,因为这关系到力的传导、溃缩等等。
从图中我们可以看到,不同颜色代表着材料的屈服强度不同,红色为超高强度钢,黄色材质的屈服强度则稍弱一些,而粉色部位的屈服强度最低,它主要起到溃缩吸能的作用。
前后防撞梁的意义就是车辆第一次承受撞击力的装置,在车身被动安全方面有一个重要理念就是一点受力全身受力。
说白了就是汽车车体的某一个位置受到了撞击,如果仅仅让这一部位去承受力的话,那么达到的保护效果会很差。
如果在某一点受到力的时候,让整个骨架结构去承受力,则可以最大限度的降低一个点所受到的力的强度,特别是前后防撞钢梁在这里就起到很明显的作用。
在这个结构中我们可以看到,防撞梁两端连接的是屈服强度很低的低速吸能盒,然后通过螺栓的形式连接在车体纵梁上。
低速吸能盒可以在车辆发生低速碰撞时有效吸收碰撞能量,尽可能减小撞击力对车身纵梁的损害,这样可以降低维修成本,而螺栓连接的方式可以更方便的对防撞梁进行更换。
在高速偏置碰撞中,防撞梁可以有效的将撞击力从车身左侧(或右侧)传递到右侧(或左侧),尽可能让整个车体去吸收碰撞能量。
在发生低速碰撞时(一般为15km/h以下),防撞梁可以避免撞击力对车身前后纵梁的损害,降低维修成本。
防撞梁的样式、薄厚是否对车辆安全有影响?其实车身被动安全涉及到车身的整体结构,防撞梁的样式与薄厚以及材质会关系到它最终的强度。
而防撞梁的强度既不能太大,也不能太小,需要和整车相配,只有配合完美的车身结构才是最安全的。
所以很难单纯的从防撞梁的样式、薄厚去判断整车的安全性。
防撞梁的安装高度应是多少?防撞梁的安装位置需要根据车身高度,轮毂直径的大小来综合评定,并没有一个明确的标准,同时还要考虑到相容性原理,即两车发生正面相撞时,不合适的防撞梁高度既保护不到自身,还会对对方车辆造成巨大伤害。
汽车前后防撞梁设计规范
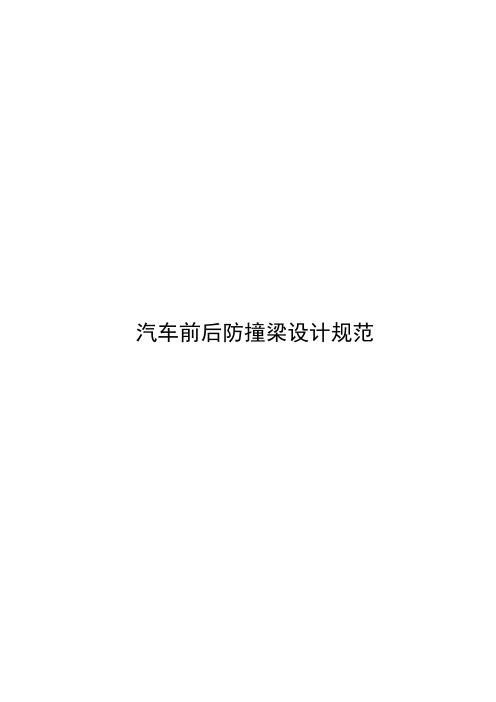
GB/T 24550-2009汽车对行人的碰撞保护
3. 前后防撞梁总成主要功能
3.1前后防撞梁总成功能概述
前后防撞梁总成,是车身第一次承受撞击力的装置,也是车身中的一个重要构件,其功能主要有:
a.保护保险杠在低速碰撞过程中尽量不要破裂或者发生永久变形。
b.保护车身骨架前后端纵梁在行人保护或者可维修性碰撞时不发生永久变形或者破裂。
图3正面碰撞3层传力路径
3.2.2后防撞梁总成碰撞性能
后防撞梁总成的碰撞性能主要需满足低速碰撞和高速碰撞两个部分的法规要求。
其中,低速碰撞需满足的法规要求为:
GB 17354-1998汽车前、后端保护装置。
高速碰撞需满足的法规要求为:
GB20072-2006乘用车后碰撞燃油系统安全要求。
3.2.2.1低速碰撞对后防撞梁设计的性能要求
a.将吸能盒设计成和纵梁在同一轴线上,避免产生弯曲变形。
b.在吸能盒上预设一些压溃筋,以便让吸能盒在轴向上发生压溃进而吸收所有能量,从而不对包括前纵梁在内的车身本体产生损害。
c.将这些容易损坏的部分骨架件,如前防撞梁和吸能盒设计成用螺栓和车身本体联结的可拆卸结构,为减少维修和保险成本。
图1可维修性碰撞前防撞梁吸能盒设计细节
2.规范性引用文件
下列文件对于本文件的应用是必不可少的。凡是注日期的引用文件,仅注日期的版版本(包括所有的修改单)适用于本文件。
GB 11551-2003乘用车正面碰撞时的乘员保护
C-NCAP中国新车评估程序2012版
GB20072-2006乘用车后碰撞燃油系统安全要求
汽车前后防撞梁设计规范
1.目的、范围
1.1目的
指导前后防撞梁总成设计;提供前后防撞梁总成设计的思路。
汽车防撞梁和吸能盒原理
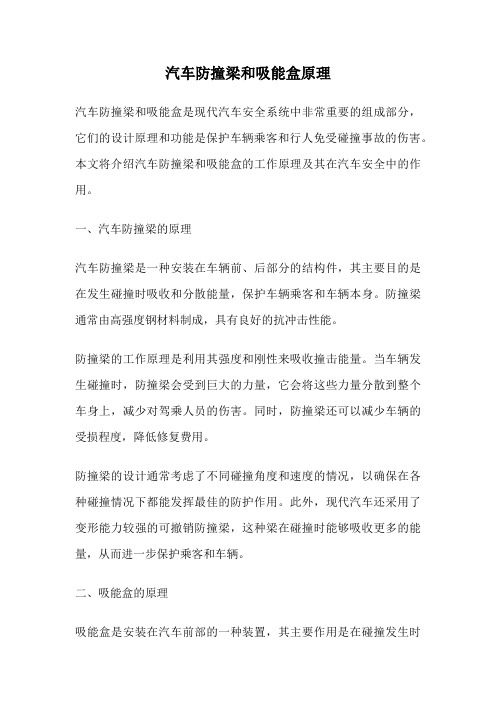
汽车防撞梁和吸能盒原理汽车防撞梁和吸能盒是现代汽车安全系统中非常重要的组成部分,它们的设计原理和功能是保护车辆乘客和行人免受碰撞事故的伤害。
本文将介绍汽车防撞梁和吸能盒的工作原理及其在汽车安全中的作用。
一、汽车防撞梁的原理汽车防撞梁是一种安装在车辆前、后部分的结构件,其主要目的是在发生碰撞时吸收和分散能量,保护车辆乘客和车辆本身。
防撞梁通常由高强度钢材料制成,具有良好的抗冲击性能。
防撞梁的工作原理是利用其强度和刚性来吸收撞击能量。
当车辆发生碰撞时,防撞梁会受到巨大的力量,它会将这些力量分散到整个车身上,减少对驾乘人员的伤害。
同时,防撞梁还可以减少车辆的受损程度,降低修复费用。
防撞梁的设计通常考虑了不同碰撞角度和速度的情况,以确保在各种碰撞情况下都能发挥最佳的防护作用。
此外,现代汽车还采用了变形能力较强的可撤销防撞梁,这种梁在碰撞时能够吸收更多的能量,从而进一步保护乘客和车辆。
二、吸能盒的原理吸能盒是安装在汽车前部的一种装置,其主要作用是在碰撞发生时吸收和分散能量,以保护车辆乘客。
吸能盒通常由塑料或金属材料制成,其设计考虑了不同碰撞情况下的能量吸收需求。
吸能盒的工作原理是通过其结构和材料的特性来吸收和分散碰撞能量。
当车辆发生碰撞时,吸能盒会在瞬间发生变形,将撞击能量转化为热能和机械能,从而减轻对乘客和车辆的伤害。
吸能盒通常由多个层次的结构组成,每个层次的材料和设计都有特定的功能。
例如,吸能盒的外层通常由刚性材料制成,用于分散撞击力和保护内部结构。
而内部层次则通常使用可变形的材料,如泡沫塑料或可压缩材料,用于吸收撞击能量。
吸能盒的设计还考虑了车辆乘客的安全性。
例如,在前部碰撞中,吸能盒可以减少乘客面部和胸部的伤害风险,同时减少颈部和脊柱的受伤风险。
此外,吸能盒还可以减少车辆的受损程度,降低修复费用。
总结:汽车防撞梁和吸能盒是现代汽车安全系统中至关重要的组成部分。
汽车防撞梁利用材料的强度和刚性,通过分散和吸收碰撞能量来保护车辆乘客和车辆本身。
- 1、下载文档前请自行甄别文档内容的完整性,平台不提供额外的编辑、内容补充、找答案等附加服务。
- 2、"仅部分预览"的文档,不可在线预览部分如存在完整性等问题,可反馈申请退款(可完整预览的文档不适用该条件!)。
- 3、如文档侵犯您的权益,请联系客服反馈,我们会尽快为您处理(人工客服工作时间:9:00-18:30)。
1规范性引用文件
下列文件中的条款通过本标准的引用而成为本标准的条款。
凡是注日期的引用文件,其随后所有的修改单(不包括勘误的内容)或修订版均不适用于本标准,然而,鼓励根据本标准达成协议的各方研究是否可使用这些文件的最新版本。
凡是不注日期的引用文件,其最新版本适用于本标准。
GB 17354-1998汽车后、后端保护装置
QC T 566-1999 轿车的外部防护
GB 20072-2006乘用车后碰撞燃油系统安全要求
2法规要求
根据GB 17354-1998 之规定:装在车辆后后端的诸元件,其设计要求为在发生接触和轻度碰撞时,不会导致车辆的严重损伤
根据GB 20072-2006乘用车后碰撞燃油系统安全要求之规定:
1.在碰撞过程中,燃油装置不应发生液体泄漏;
2.碰撞试验后,燃油装置若有液体连续泄漏,则在碰撞后前5min平均泄漏速率不应大于
30g/min;如果从燃油装置中泄漏的液体与从其他系统泄漏的液体混淆且这几种液体不容易分开和辨认,则应根据收集到的所有液体评价连续泄漏量。
3后防撞梁总成功能描述
后防撞梁总成要求能在车辆纵向及高度方向支撑汽车后端保护装置,保证汽车后端保护装置的安装牢靠。
能在车辆低速碰撞时连同汽车后端保护装置对车辆的照明和信号装置提供必要的保护;
保证后备门(行李舱盖)、车辆的侧门正常的开闭;保证车辆燃料和冷却系统无泄漏、无堵塞,其密封装置与油、水箱口盖能正常开启;车辆的传动、悬架、转向和制动等系统能保持良好的调整状态并正常工作;车辆的排气系统不应该有妨碍其正常工作的损坏或错位。
后防撞梁总成要求在车辆发生中高速碰撞时能吸收部分撞击能量,并将能量平衡传递至车身左右纵梁,保障乘员安全和燃油箱的安全。
后防撞梁总成的最后表面应该能比后围板总成和后备门总成(后行李舱盖总成)更突出,保证车辆碰撞时能适当变形,减少车辆后围板总成(后行李舱盖总成)的维修成本。
4后防撞梁总成的设计
4.1后防撞梁总成高度位置确定
根据GB 17354-1998中4.3.5规定:碰撞发生时,碰撞器与车辆首先接触的应是撞击头与车辆的保护装置,当车辆分别在整车装备质量与加载试验车质量的状态是,位于车角间的保护装置均
能被通过碰撞器基准线的水平面所截。
如图一所示:碰撞器的中心高度为距离地面445mm,无论车辆空载还是设计载荷是时保险杠和吸能泡沫应该与碰撞器的撞击头的重叠距离不小于50mm,而防撞梁应该能最大限度支撑保险杠和吸能泡沫,至少能为保险杠和吸能泡沫应该与碰撞器的撞击头的重叠提供支撑。
(图一)
4.2后防撞梁总成前后位置确定
后防撞梁总成的后后位置受到造型影响较大。
首先,后防撞梁总成的最后表面与车身外表面之间一般填充吸能泡沫,其X方向厚度一般推荐不小于30mm(厚度主要根据吸能泡沫的制造工艺决定)。
如图二所示。
其次,保证后防撞梁总成的最后表面应该能比后围板总成和后备门总成(后行李舱盖总成)更突出,以减少车辆碰撞时对车身维修成本,突出距离建议不少于20mm。
如图二所示。