硫化温度和硫化时间
【考研化学】第十章 硫化

★混气硫化:在硫化的第一阶段以热空气为介 质.在第二阶段再通入蒸汽作介质。胶鞋硫化 采用该方法。
(3)过热水
优点:既能保持较高的温度,又能赋予较 大的压力,因此常用于高压硫化场合。
缺点:热含量小,导热效率低,且温度不 易掌握均匀。 典型的用途是轮胎硫化时,将过热水充注 于水胎中,以保持内温。
(4)热水
二、欠硫阶段(预硫)
含义:焦烧期以后橡胶开始交联的阶段。 交联程度逐渐增加,橡胶的物理机械性能逐 渐上升。制品轻微欠硫时,强度、弹性、伸长率 未达到预期的水平,但抗撕裂性、耐磨性等却优 于正硫化胶料。
欠料的配方。
三、正硫阶段
含义:橡胶的交联反应达到一定的程度,此 时的各项物理机械性能均达到或接近最佳值,其 综合性能最佳。 正硫化温度
正硫化时间取决于制品性能要求和断面厚薄, 需考虑到“后硫化”。
抗张强度最高值略前的时间
正硫化时间=
强伸积(抗张强度×伸长率) 最高值的时间
四、过硫阶段
含义:正硫化以后继续硫化便进入过硫阶段。 氧化及热断链反应占主导地位,胶料性能下降。 硫化返原;断链多于交联
非返原性:交联继续占优势
过硫阶段胶料的性能变化情况反映了硫化平 坦期的长短。超促进剂,交联键能低,硫化温度 高,则平坦期短。
(1)饱和蒸汽
优点:热含量大、导热效率高、成本低、 压力和温度易调节。 缺点:加热温度要受到压力的牵制;对硫 化容器内壁有较大腐蚀作用。
(2)热空气
优点: 加热温度不受压力影响,比较干燥, 不含水分,产品表面光滑,外观漂亮,而且不 受罐壁腐蚀的影响。 缺点: 含热量低,导热效率很低,硫化时 间长,同时含有大量氧气,在高温高压下易使 制品氧化。
1.中间化合物的生成
硫化时间
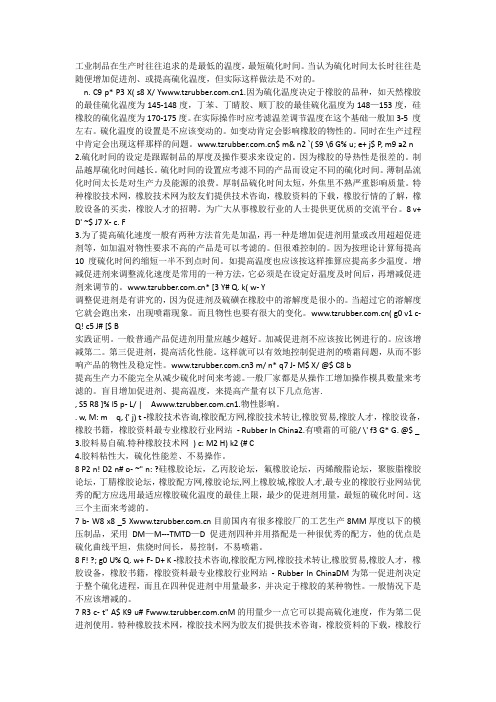
工业制品在生产时往往追求的是最低的温度,最短硫化时间。
当认为硫化时间太长时往往是随便增加促进剂、或提高硫化温度,但实际这样做法是不对的。
n. C9 p* P3 X( s8 X/ 1.因为硫化温度决定于橡胶的品种,如天然橡胶的最佳硫化温度为145-148度,丁苯、丁睛胶、顺丁胶的最佳硫化温度为148—153度,硅橡胶的硫化温度为170-175度。
在实际操作时应考滤温差调节温度在这个基础一般加3-5 度左右。
硫化温度的设置是不应该变动的。
如变动肯定会影响橡胶的物性的。
同时在生产过程中肯定会出现这样那样的问题。
$ m& n2 `( S9 \6 G% u; e+ j$ P, m9 a2 n 2.硫化时间的设定是跟踞制品的厚度及操作要求来设定的。
因为橡胶的导热性是很差的。
制品越厚硫化时间越长。
硫化时间的设置应考滤不同的产品而设定不同的硫化时间。
薄制品流化时间太长是对生产力及能源的浪费。
厚制品硫化时间太短,外焦里不熟严重影响质量。
特种橡胶技术网,橡胶技术网为胶友们提供技术咨询,橡胶资料的下载,橡胶行情的了解,橡胶设备的买卖,橡胶人才的招聘。
为广大从事橡胶行业的人士提供更优质的交流平台。
8 v+ D' ~$ J7 X- c. F3.为了提高硫化速度一般有两种方法首先是加温,再一种是增加促进剂用量或改用超超促进剂等,如加温对物性要求不高的产品是可以考滤的。
但很难控制的。
因为按理论计算每提高10度硫化时间约缩短一半不到点时间。
如提高温度也应该按这样推算应提高多少温度。
增减促进剂来调整流化速度是常用的一种方法,它必须是在设定好温度及时间后,再增减促进剂来调节的。
* [3 Y# Q. k( w- Y调整促进剂是有讲究的,因为促进剂及硫磺在橡胶中的溶解度是很小的。
当超过它的溶解度它就会跑出来,出现喷霜现象。
而且物性也要有很大的变化。
( g0 v1 c- Q! c5 J# [$ B实践证明。
一般普通产品促进剂用量应越少越好。
橡胶硫化三要素(时间、温度、压力)

橡胶硫化三要素(时间、温度、压力)橡胶件硫化的三大工艺参数是:温度、时间和压力。
其中硫化温度是对制品性能影响最大的参数,硫化温度对橡胶制品的影响的研究也比比皆是。
但对硫化压力比较少进行试验。
橡胶硫化三要素之时间橡胶制品硫化时间:在一定的温度、模压下,为了使胶料从塑性变成弹性,且达到交联密度最大化,物理机械性能最佳化所用的时间叫橡胶制品硫化时间。
通常不含操作过程的辅助时间。
硫化时间是和硫化温度密切相关的,在硫化过程中,硫化胶的各项物理、力学性能达到或接近最佳点时,此种硫化程度称为正硫化或最宜硫化。
在一定温度下达到正硫化所需的硫化时间称为正硫化时间,一定的硫化温度对应有一定的正硫化时间。
当胶料配方和硫化温度一定时,硫化时间决定硫化程度,不同大小和壁厚的橡胶制品通过控制硫化时间来控制硫化程度,通常制品的尺寸越大或越厚,所需硫化的时间越长。
硫化时间的设定方法:1. 1.正硫化时间的测试,胶料正硫化时间的测试方法有:1.1物理-化学法(包括游离硫测定法和溶胀法);1.2 物理-力学性能测定法(包括定伸应力法、拉伸强度法、定伸强度法、抗张积法、压缩永久变形法、综合取值法等);1.3专用仪器法(包括门尼粘度法、硫化仪法)等。
目前最常用的是硫化仪法。
通过硫化仪测试,可以得到胶料的正硫化时间。
2.制品硫化时间的确定2.1若制品厚度为6mm或小于6mm,并且胶料的成形工艺条件可以认为是均匀受热状态,那么,制品的硫化时间与硫化曲线中所测得的正硫化时间相同(温度一致的情况下,即加硫温度使用硫化仪测试的温度);2.2若制品壁厚大于6mm,每增加1mm的厚度,则测试的正硫化时间增加1min,这是一个经验数据。
例如,一橡胶制品,其厚度为22mm,试片测试的正硫化时间为6min(温度设定150℃),那么,在150℃硫化时,该制品的硫化时间为6+(22-6)×1=22min。
这时间不包括操作过程的辅助时间。
二段加硫时间设定:1.定义为了达到合理的制造工艺和合理成本,把橡胶硫化分为一段、二段两个过程来完成的工艺方法,其第二段的工艺就是所谓的二段加硫。
硫化时间1

1/2
• h —布层相当于胶层的当量厚度,cm • h —布层实际厚度,cm
2
• α -布层的热扩散系数,cm²/s • α -胶层的热扩散系数,cm²/s • 制品的总计算厚度: • H =制品的胶层厚度+布层当量厚度 求出滞后时间与制品的硫化时间。p99
2 1 总
二 硫化时间的调整
一 硫化时间的确定方法
• 1)成品厚度在6mm或以下,硫化时间 与试片正硫化时间相同。 • 2)若成品厚度大于6mm,每增加 1mm厚度,硫化时间滞后1分钟(经验) • 3)如制品内含有布层骨架,还要另加滞 后时间。按下式将布层厚度换算成相当 胶层厚度的当量厚度:
一 硫化时间的确定方法
• h =h (α /α )
• 由于胶料达到正硫化后都有一个硫化平 坦范围,因此在改变硫化条件时,只要 把改变后的硫化效应控制在原来硫化条 件的最小硫化效应和最大硫化效应之内, 制品的物理机械性能就可与原硫化条件 相近。即E <E<E
min max
三 硫化效应与厚制品等效硫化 时间的确定
• 原制品等效硫化时间的确定 由于橡胶是一种热的不 良导体,因而厚制品在硫化时各部位或各部件的温度 是不相同的(即使是同一部位或同一部件在不同的硫 化时间内温度也是不同的),在相同的硫化时间内所 取得的硫化效应也是不同的。并且,随着制品厚度的 增加这种现象越为明显。为了正确确定厚制品的硫化 工艺时间和各层胶件的胶料配方,往往需要首先拟定 一个硫化工艺条件,然后将厚制品与该硫化工艺条件 下进行硫化。同时,测出各胶层温度随硫化时间的变 化情况,计算出各胶层的硫化效应,再将其分别与各 胶层胶料试片在硫化仪上测出的达到正硫化的允许硫 化效应相比较,如果各胶层的实际硫化效应都在允许 的范围之内,即可认为拟定的硫化工艺条件是适宜的。 否则,要对硫化工艺条件或各胶层胶料配方作调整。
硫化的工艺参数

硫化历程
橡膠不同厚度的溫升图
• 橡胶为不良导热 体,表层与内层 的温差随着厚度 的增加而增大。 • 正硫化時间只适 用于厚度6mm以內 之制品。 • 厚度每增加1mm, 硫化时间需增加 约47sec.。
硫化温度与时间
• 温度每差10℃,时间差一倍。 • 硫化温度系数 1.8 ~ 2.5 随胶料配方而有差异。
14.886 15.204 15.528 15.857
气胎硫化
• • • • 1、模温:160℃左右。 2、内硫化介质:空气。 3、压力:一般17±1kgf/cm² 缺点:气胎整形劳动强度大;硫化时间长;气胎 内部容易氧化发粘、发烂。) • 优点:可多层模硫化。
胶囊隔膜硫化
• 1、模温: 160℃左右。 • 2、内硫化介质: ※过热水,一般采用20kgf/cm² 左右的压力,热水温度 一般在160~170 ℃,对轮胎硫化质量来讲是较好的硫 化工艺。 ※氮气,有二种,液氮(成本较高,但纯度高);制氮 装置直接从空气中分离制取氮气(纯度不稳定),一 般采用20kgf/cm² 左右的压力。氮气硫化工艺在理论 上是较为理想的一种工艺,但由于氮气制取纯度不稳 定、对设备和管道密封性要求很高等因素,目前在国 内还未被大部分轮胎企业采用。
胶囊隔膜硫化
4.50-12 双向导热硫化测温 2012.12.28
内压蒸汽约11kgf/cm²
胶囊隔膜硫化
※空气,胶囊隔膜硫化内压使用空气,业内基本没 有厂家使用。此工艺就轮胎质量而言,是可行的, 业内不采用的原因是:内压采用空气时,空气中 含有的大量氧分子会加快胶囊的老化,胶囊的使 用寿命会很短(只有正常的1/4~1/3),也会增加 废胶囊导致的废胎,对生产成本增加明显;更大 的问题是,由于胶囊很容易氧化,发粘、发烂会 损坏硫化机的中心机构,到一定程度时甚至有使 整个硫化管道堵塞瘫痪的风险。
硫化作业指导书
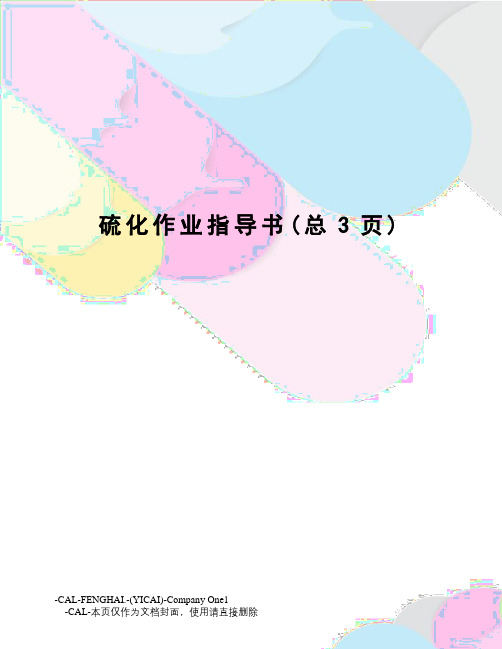
序号
检 验 项 目 和 要 求
样本
检 验 仪 器/方法
控制方法
容量
频率
1
首件按图纸检验
连续3模
每次生产
游标卡尺
首件检验记录
2
外观:表面光滑、清洁,无裂纹、杂质、缺胶等.
100%
连续
目测
流程卡
3
尺寸符合图纸的要求
2次
每班
游标卡尺
半成品检验记录
应急计划:
持续出现不合格情况应停机报告班长或主管,记录现象并对缺陷产品进行隔离、标识,同时调整工艺参数。必要时,维修模具。
注意事项:1、密切关注硫化机的温度、时间、压力是否符合规定的要求。
2、产品在开始生产前是否进行了首件检验。
3、产品是否存在割边线厚等现象。
编制: 审核: 批准: 日期:
注意事项:1、密切关注硫化机的温度、时间、压力是否符合规定的要求。
2、产品在开始生产前是否进行了首件检验。
3、产品出模等现象。
编制: 审核: 批准: 日期:
作业指导书
产 品 名 称
图号/零件号
等 级
O形圈
详见
编号:02
本页状态: 0
版本 A
工序名称
硫化
★
设备及工装
硫化作业指导书(总3页)
作业指导书
产品名称
图号/零件号
等级
骨架油封
详见检验规程
编号:01
本页状态: 0
版本 A
工序名称
硫化
★
设备及工装
全自动平板硫化机油封模具
丁腈橡胶硫化温度和时间

丁腈橡胶硫化温度和时间引言丁腈橡胶是一种合成橡胶,具有优异的耐油、耐磨、耐老化等特性,广泛应用于汽车、航空航天、化工等领域。
硫化是丁腈橡胶加工过程中的关键步骤,通过硫化可以使橡胶材料具有更好的强度、弹性和耐用性。
本文将详细介绍丁腈橡胶硫化温度和时间的相关知识。
丁腈橡胶硫化的原理丁腈橡胶硫化是指在一定的温度和时间条件下,将丁腈橡胶与硫化剂反应,使其分子间发生交联,形成三维网络结构。
硫化剂一般使用硫或者含硫化合物,如硫化氢、二硫化碳等。
在硫化过程中,硫化剂与丁腈橡胶中的双键反应,使丁腈橡胶分子链之间形成硫醚键,从而增强橡胶的强度和耐用性。
硫化温度对丁腈橡胶的影响硫化温度是丁腈橡胶硫化过程中的重要参数,它对丁腈橡胶的性能有着重要影响。
一般来说,硫化温度越高,硫化反应的速度越快,但过高的温度可能会导致橡胶热分解,降低橡胶的性能。
同时,硫化温度也会影响丁腈橡胶的硫化程度,即交联程度。
在较低的硫化温度下,橡胶的交联程度较低,弹性较好,但强度较低;而在较高的硫化温度下,橡胶的交联程度较高,强度较高,但弹性较差。
因此,选择合适的硫化温度对于获得理想的丁腈橡胶性能至关重要。
硫化时间对丁腈橡胶的影响硫化时间是指丁腈橡胶在硫化温度下所需的反应时间。
硫化时间的长短直接影响着丁腈橡胶的硫化程度和性能。
一般来说,硫化时间越长,丁腈橡胶的硫化程度越高,强度越大,但弹性越差。
过长的硫化时间可能导致橡胶过硫化,使其变得脆化。
相反,硫化时间过短则会导致橡胶交联不完全,强度不够。
因此,选择合适的硫化时间是确保丁腈橡胶性能的关键。
硫化温度和时间的选择在实际生产中,选择合适的硫化温度和时间是根据具体的丁腈橡胶配方和产品要求来确定的。
一般来说,硫化温度和时间需要综合考虑以下几个因素:1.丁腈橡胶的类型和配方:不同类型的丁腈橡胶在硫化时具有不同的温度和时间要求。
不同的配方中可能还包含其他添加剂,如加硫促进剂、抗老化剂等,这些也会对硫化温度和时间产生影响。
橡胶硫化压力、温度、(厚制品)时间计算(公式全,收藏)
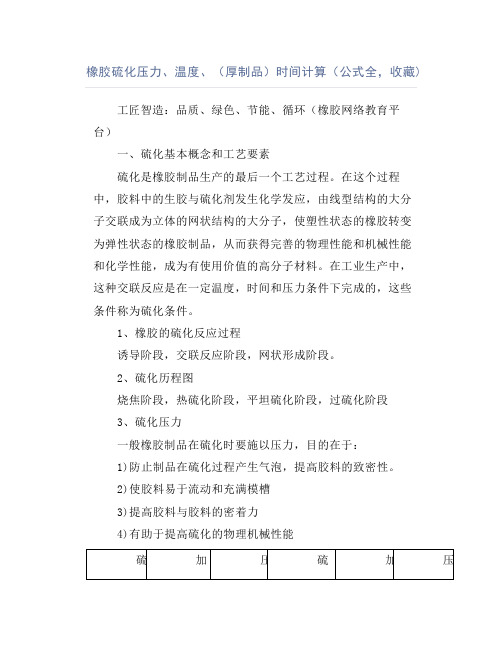
橡胶硫化压力、温度、(厚制品)时间计算(公式全,收藏)工匠智造:品质、绿色、节能、循环(橡胶网络教育平台)一、硫化基本概念和工艺要素硫化是橡胶制品生产的最后一个工艺过程。
在这个过程中,胶料中的生胶与硫化剂发生化学发应,由线型结构的大分子交联成为立体的网状结构的大分子,使塑性状态的橡胶转变为弹性状态的橡胶制品,从而获得完善的物理性能和机械性能和化学性能,成为有使用价值的高分子材料。
在工业生产中,这种交联反应是在一定温度,时间和压力条件下完成的,这些条件称为硫化条件。
1、橡胶的硫化反应过程诱导阶段,交联反应阶段,网状形成阶段。
2、硫化历程图烧焦阶段,热硫化阶段,平坦硫化阶段,过硫化阶段3、硫化压力一般橡胶制品在硫化时要施以压力,目的在于:1)防止制品在硫化过程产生气泡,提高胶料的致密性。
2)使胶料易于流动和充满模槽3)提高胶料与胶料的密着力4)有助于提高硫化的物理机械性能硫化机把压力传递给模型,再由模型传递给胶料;二是硫化介质直接加压(如蒸汽加压);三是以压缩空气加压;四是由注压机注压等。
4、硫化温度和硫化时间硫化温度是橡胶发生硫化反应的基本条件,它直接影响硫化速度和产品质量。
硫化温度高,硫化速度快,生产效率高。
反之,硫化速度慢,生产效率低。
硫化温度高低应取决于胶料配方,其中最重要的是取决于橡胶种类和硫化体系。
但应注意的是,高温橡胶分子链裂解,至发生硫化返原现象,结果导致强伸性能下降,困此硫化温度不宜太高。
温度是硫化三大要素之一,与所有化学反应一样,硫化反应随温度升高而加快,并且大体适用范特霍夫定律,即温度每上升8~10。
C(约相当于一个表压的蒸汽压力),其反应速度约增加一倍;或者说,反应时间约减少一半。
随着室温硫化胶料的增加和高温硫化出现,硫化温度趋向两个极端。
从提高硫化效率来说,应当认为硫化温度越高越好,但实际上不能无限提高硫化温度。
首先受到橡胶导热性极小阻碍,对于厚制品来说,采用高温硫化很难使内外层胶料同时达到平坦范围;其次,各种橡胶的耐高温性能不一,有的橡胶经受不了高温的作用,如高温硫化天然橡胶时,溶于橡胶中的氧随温度提高而活性加大,引起强烈的氧化作用,破坏了橡胶的组织,降低了硫化胶的物理机械性能,第三,高温对橡胶制品中的纺织物有害为棉纤维布料超过期作废140℃时,强力下降,在240℃下加热四小时则完全破坏。
硫化温度和硫化时间

硫化温度和硫化时间
硫化温度是硫化反应的最基本条件。
硫化温度的高低,可直接影响硫化速度、产品质量和企业的经济效益
硫化温度高,硫化速度快,生产效率高;反之生产效率低
提高硫化温度会导致以下问题;
(1) 引起橡胶分子链裂解和硫化返原,导致胶料力学性能下降
(2) 使橡胶制品中的纺织物强度降低
(3) 导致胶料焦烧时间缩短,减少了充模时间,造成制品局部缺胶
(4) 由于厚制品会增加制品的内外温差,导致硫化不均
硫化温度的选取应综合考虑橡胶的种类、硫化体系及制品结构等因素各种橡胶的最宜硫化温度一般是:
NR<143℃;SBR<180℃;IR、BR、CR<151℃;IIR<170℃;NBR<180℃
1.等效硫化时间的计算
1.通过范特霍夫方程计算等效硫化时间
根据范特霍夫方程,硫化温度和硫化时间的系可用下式表示:τ1/τ2=k 式中τ1—温度为t1的正硫化时间,min
τ2—温度为t2的正硫化时间,min
K—硫化温度系数
例:已知某一胶料在140℃时的正硫化时间是20m in,利用范特霍夫方程可计算出130℃和150℃时的等效硫化时间
130℃的等效硫化时间为40m in;150℃的等效硫化时间为10m in。
不同颜色橡胶硫化时间

不同颜色橡胶硫化时间
橡胶硫化时间是指在一定的温度和压力下,橡胶从塑性状态转变为弹性状态,并且达到最佳物理机械性能的时间。
不同颜色的橡胶由于其成分和配方可能会有不同的硫化时间。
以下是一些常见颜色橡胶的硫化时间参考。
1.天然橡胶(NR):通常在140-150°C下硫化,硫化时间约为15-30分钟。
2.丁苯橡胶(SBR):在150-160°C下硫化,硫化时间约为20-40分钟。
3.顺丁橡胶(BR):在150-160°C下硫化,硫化时间约为20-40分钟。
4.氯丁橡胶(CR):在160-170°C下硫化,硫化时间约为30-60分钟。
5.丁腈橡胶(NBR):在150-190°C下硫化,硫化时间约为20-80分钟。
6.硅橡胶(VMQ):在140-160°C下硫化,硫化时间约为2-4小时。
7.氟橡胶(FVMQ):在150-200°C下硫化,硫化时间约为2-4小时。
请注意,这些硫化时间仅供参考,实际硫化时间可能会因橡胶配方、硫化体系、模具设计、温度控制等因素而有所不同。
在生产过程中,通常会通过实验和测试来确定最佳的
硫化时间。
硫化工艺

硫化工艺硫化工艺对粘接强度起至关重要的作用。
硫化过程中必需具备的条件是指:温度、时间和压力,一般统称皮带硫化胶接的“三要素”。
1、硫化温度:一般控制在145°c+-5°c,也有皮带产家根据芯层耐热度和胶带厚度来规定该胶带的硫化温度。
2、硫化时间:是指硫化过程中保温时间是25~35分钟。
然后开始断电降温。
3、硫化压力:硫化机开启电源前,需用打压泵对接头施以一定的压力。
通常情况下取0.8~1Mpa即可。
之后,开启电源进行升温。
当温度达到100度时,将水压加至2Mpa。
当温度达到145~150°c时进行保温。
4、硫化过程应严格按照操作规程进行,切不可操之过急。
防止因温度过高导致过硫及温度过低不能硫化,而影响粘接质量。
5、硫化结束后把电源关了,让皮带接头进行保养一段时间。
等待硫化机温度降至70°c以下,方可拆除硫化机。
但皮带不可马上工作运料,待3~5小时后才开始工作。
输送带硫化质量问题一、1、硫化面有气泡和局部粘接不好的原因:○1硫化面有气泡和局部粘接不好的现象是硫化接头的大敌。
有气泡其是一种内部粘接不好的外在表现。
这种气泡主要是产生在两心胶,最后在硫化过程中透过在盖胶的硫化面形成内部气泡。
○2空气、温度相对较大,水分不易清除在硫化时内部形成气泡。
○3局部粘接不好,多为结合面不干净以及胶糊的成份和原输送带的成份不附所造成。
2、人为因素的影响:○1胶糊浆未充分干燥便开始硫化,从而导致内部在高温时产生气泡。
○2硫化时压力、温度不均。
3、跑胶的原因:○1跑胶的原因主要是胶接用料不准确,且硫化时硫化两侧板档胶固定不实,厚度与原皮带相差远。
硫化过程中,上下箱体加压时,胶浆溶化便从两侧流出,形成跑胶。
结果会导致因硫化压力不足所形成的低强度接头。
陆振国2009年7月5日。
橡胶制品硫化温度时间控制规定

橡胶制品硫化温度、时间控制规定
(一)、硫化温度控制规定
1、规定硫化温度控制范围140±3℃
2、为达到用户(硫化机)温度控制要求,规定锅炉房输出
油温应控制在150±5℃,回油温度应控制在136±5℃。
3、要求锅炉工应对输油温度,回油温度每整点记录一次,记录当时的即时温度。
4、硫化工应在工艺卡上记录热板温度,记录合模后半小时
的即时温度; 总硫化时间不够半小时记录合模后三分钟的即时温度。
(二)、成品硫化时间控制规定规定硫化时间计算方法为成品毫米厚度乘以系数1.3~1.8,即为硫化产品使用分钟数。
具体:支座厚度≤50mm 乘以1.3
50mm<厚度≤90 mm 乘以1.5
厚度>90 mm 乘以1.8
当硫化总时间≤10分钟时,允许t+2分钟范围内;总硫化时间>10分钟时,允许t±3分钟范围内。
硫化温度和硫化时间的关系

硫化温度和硫化时间的关系嘿,你知道不?前段时间我去了一家橡胶制品厂参观,那可真是让我大开眼界啊!一进工厂,就闻到一股怪怪的味道。
我跟着导游一路走,来到了硫化车间。
哇,那里面可热闹了,机器轰鸣,热气腾腾。
导游跟我们介绍说,硫化是橡胶制品生产中非常重要的一个环节,而硫化温度和硫化时间的关系就像是一对欢喜冤家。
我看到工人们把一个个还没硫化的橡胶制品放进一个大锅里,那个锅下面烧着火,温度可高了。
导游说,这就是在进行硫化呢。
温度越高,硫化的速度就越快。
但是呢,如果温度太高了,橡胶制品就可能会被烧坏。
就好像你做饭的时候,如果火开得太大,菜就容易烧焦。
我还看到一个工人拿着一个温度计,时不时地去测量锅里的温度。
他可认真了,就像一个医生在给病人量体温一样。
他跟旁边的同事说:“这温度可得控制好啊,不然这批货就废了。
” 然后他们又一起讨论着硫化时间。
原来,硫化时间也不能太长或太短。
如果时间太长了,橡胶制品可能会变得过硬;如果时间太短了,又达不到理想的硫化效果。
我突然想起我小时候玩的橡皮泥。
有时候我把橡皮泥放在太阳底下晒,晒久了它就会变得硬邦邦的。
这就有点像硫化时间太长了吧。
而如果我只是晒一会儿,它就还是软软的,这就像硫化时间不够。
在工厂里转了一圈,我对硫化温度和硫化时间的关系有了更深刻的理解。
它们就像是一对默契的搭档,只有配合好了,才能生产出高质量的橡胶制品。
从工厂出来,我一直在想,其实生活中也有很多像硫化温度和硫化时间这样的关系呢。
比如我们做事情,不能太急躁,也不能太拖沓。
要找到那个合适的“温度” 和“时间”,才能把事情做好。
所以啊,硫化温度和硫化时间,这看似简单的两个因素,却有着不简单的关系呢。
下次要是再看到橡胶制品,我肯定会想起这次有趣的参观经历。
xilinx u200 硫化标准

xilinx u200 硫化标准
一、目的
本标准规定了Xilinx U200系列FPGA芯片的硫化要求、工艺流程、操作规程及注意事项,旨在确保生产过程中的硫化效果和质量。
二、适用范围
本标准适用于使用Xilinx U200系列FPGA芯片的所有生产过程,包括但不限于电路板焊接、系统集成等。
三、硫化要求
1. 温度控制:在硫化过程中,温度应保持在250℃±5℃的范围内,保持温度稳定,避免温度过高或过低。
2. 时间控制:硫化时间应不少于30分钟,以保证芯片充分硫化,提高硫化质量。
3. 湿度控制:硫化环境湿度应保持在30%~60%的范围内,以防止静电和氧化。
4. 清洁度控制:焊接前应对电路板进行清洁,去除油污、氧化层等杂质,保证焊接质量。
四、工艺流程
1. 预热:将电路板放入硫化炉中,预热至规定温度。
2. 装载:将Xilinx U200系列FPGA芯片按照规定的位置放置在电路板上。
3. 焊接:在规定温度和时间下进行焊接,保证芯片与电路板良
好连接。
4. 后处理:焊接完成后,取出电路板,进行必要的后处理工作,如冷却、清洁等。
五、操作规程
1. 在操作前应详细了解Xilinx U200系列FPGA芯片的规格书和本标准,确保正确理解和掌握硫化要求。
2. 在操作过程中应穿戴好防静电工作服和手套,防止静电对芯片造成损坏。
3. 在装载芯片时应注意轻拿轻放,避免碰撞和划伤芯片表面。
硫化机硫化过程中需注意的三大因素

硫化机硫化过程中需注意的三大因素
硫化机是工业上将熟橡胶半成品转变为工业成品这个过程的机械设备,随着硅橡胶制品的快速发展,我国已成为世界橡胶机械的生产大国,是世界橡胶机械发展最快的地区,正成为世界橡胶机械的中心。
影响硫化机硫化过程的第一因素:硫化温度
硫化温度决定着硫化均匀程度,经验及试验表明,当温度高10℃,硫化时间会缩短约一半,而橡胶是不良导热体,制品其硫化进程会因其各处温度不同而不同,要达到均匀硫化效果,厚橡胶制品的温度控制就非常关键了,应逐步升温,原则是低温长时间硫化。
影响硫化机硫化过程的第二因素:硫磺用量
硫化机加热板硫磺用量越大其硫化速度也会越快,致硫化程序也会越高,但是硫磺与橡胶中的溶解度是有一定限量的,也并不是硫磺使用量越大越好,过量的硫磺会由胶料表面析出,这种现象称为“喷硫”,要尽量减少喷硫发生,做法则是在尽量低的温度下,加适当量的硫磺,一般情况下,硫磺于软质橡胶用量不要超3%,半硬质胶则不超20%,纯硬质胶的用量较高,达40%以上。
影响硫化机硫化过程的第三因素:硫化时间
硫化时间是硫化工艺中重要的环节所在,若过短或至硫化程序不够,俗称“欠硫:,过长时则硫化程度会过高,俗称“过硫”,只有适宜的时间长度才可以达到最佳的硫化效果,俗称为正硫化。
蓝色极光七年专注硫化机节能改造,现推出的硫化机节电器第三代,技术比较成熟,性能稳定!综合省电效果达一半以上!。
epdm橡胶 硫化时间

epdm橡胶硫化时间EPDM橡胶硫化时间EPDM橡胶是一种具有优良耐候性和化学稳定性的合成橡胶,广泛应用于汽车工业、建筑材料和电气设备等领域。
硫化是EPDM橡胶加工过程中不可或缺的步骤,通过硫化可以使橡胶材料具有良好的弹性和耐用性。
本文将探讨EPDM橡胶的硫化时间及其影响因素。
EPDM橡胶的硫化时间是指在一定温度和压力下,橡胶材料达到预定硫化程度所需的时间。
硫化过程是通过加入硫化剂和促进剂,使橡胶分子间发生交联反应,形成三维网状结构,从而提高橡胶的物理性能。
硫化时间的长短直接影响到橡胶制品的质量和性能。
EPDM橡胶的硫化时间受多种因素的影响。
首先是硫化温度,一般来说,硫化温度越高,硫化时间越短。
这是因为高温可以提高反应速率,加速硫化反应的进行。
然而,过高的温度可能会导致橡胶材料的老化和降解,因此需要选择合适的硫化温度。
其次是硫化剂的种类和用量。
硫化剂是促进硫化反应进行的重要组分,常用的硫化剂包括硫和过氧化物类化合物。
不同硫化剂的活性和反应速率不同,会直接影响到硫化时间。
同时,硫化剂的用量也会对硫化时间产生影响,过高或过低的用量都可能引起硫化时间的变化。
橡胶材料的成分和配方也会对硫化时间产生影响。
EPDM橡胶通常与填料、增塑剂、防老化剂等进行混炼,这些添加剂的种类和用量都会对硫化时间产生影响。
例如,填料的种类和用量会影响到橡胶材料的热传导性能和流变性能,进而影响硫化过程的进行。
硫化时间还与硫化压力有关。
一般来说,硫化压力越高,硫化时间越短。
因为高压可以增加橡胶材料分子间的碰撞几率,促进硫化反应的进行。
然而,过高的压力可能会导致橡胶材料的变形和破坏,因此需要选择适当的硫化压力。
EPDM橡胶的硫化时间需要通过实验确定。
常用的实验方法包括恒温硫化试验和动态硫化试验。
恒温硫化试验是将橡胶样品置于恒定温度下,测定不同时间下的硫化程度,以确定硫化时间。
动态硫化试验则是在一定温度和时间下,通过测定硫化反应前后的物理性能变化,以求得硫化时间。
- 1、下载文档前请自行甄别文档内容的完整性,平台不提供额外的编辑、内容补充、找答案等附加服务。
- 2、"仅部分预览"的文档,不可在线预览部分如存在完整性等问题,可反馈申请退款(可完整预览的文档不适用该条件!)。
- 3、如文档侵犯您的权益,请联系客服反馈,我们会尽快为您处理(人工客服工作时间:9:00-18:30)。
硫化温度和硫化时间
硫化温度是硫化反应的最基本条件。
硫化温度的高低,可直接影响硫化速度、产品质量和企业的经济效益
硫化温度高,硫化速度快,生产效率高;反之生产效率低
提高硫化温度会导致以下问题;
(1) 引起橡胶分子链裂解和硫化返原,导致胶料力学性能下降
(2) 使橡胶制品中的纺织物强度降低
(3) 导致胶料焦烧时间缩短,减少了充模时间,造成制品局部缺胶
(4) 由于厚制品会增加制品的内外温差,导致硫化不均
硫化温度的选取应综合考虑橡胶的种类、硫化体系及制品结构等因素各种橡胶的最宜硫化温度一般是:
NR<143℃;SBR<180℃;IR、BR、CR<151℃;IIR<170℃;NBR<180℃
1.等效硫化时间的计算
1.通过范特霍夫方程计算等效硫化时间
根据范特霍夫方程,硫化温度和硫化时间的系可用下式表示:τ1/τ2=k 式中τ1—温度为t1的正硫化时间,min
τ2—温度为t2的正硫化时间,min
K—硫化温度系数
例:已知某一胶料在140℃时的正硫化时间是20min,利用范特霍夫方程可计算出130℃和150℃时的等效硫化时间
130℃的等效硫化时间为40min;150℃的等效硫化时间为10min。