除锈等级和表面粗糙度对照表
防腐是除锈的等级代号

① 表面粗糙度影响零件的耐磨性。表面越粗糙,配合表面间的有效接触面积越小,压强越大,磨损就越快。
② 表面粗糙度影响配合性质的稳定性。对间隙配合来说,表面越粗糙,就越易磨损,使工作过程中间隙逐渐增大;对过盈配合来说,由于装配时将微观凸峰挤平,减小了实际有效过盈,降低了联结强度。
③ 表面粗糙度影响零件的疲劳强度。粗糙零件的表面存在较大的波谷,它们像尖角缺口和裂纹一样,对应力集中很敏感,从而影响零件的疲劳强度。
Ra为除锈后的表面粗糙度。旧标准中叫光洁度,现在新标准定义为粗糙度,表示方法不同,光洁度用代号表示级别,粗糙度有数值Ra来表示,更科学.
光洁度和表面粗糙度是一个东西两样说法
几何形状误差分为宏观几何形状误差(形状公差)、表面波纹度(波度)和微观几何形状误差(表面粗糙度)三类,目前通常是按波距来划分,波距小于1mm的属于表面粗糙度,波距在1~10mm内的属于表面波度,大于10mm的属于形状误差。
④ 表面粗糙度影响零件的抗腐蚀性。粗糙的表面,易使腐蚀性气体或液体通过表面的微观凹谷渗入到金属内层,造成表面腐蚀。
⑤ 表面粗糙度影响零件的密封性。粗糙的表面之间无法严密地贴合,气体或液体通过接触面间的缝隙渗漏。
此外,表面粗糙度对零件的外观、测量精度也有影响。
表面粗糙度比较样块/光洁度样块特价销售2007-08-28 17:58加工方法 规格 Ra值um 块数 符合国标
D氧化皮已经因锈蚀而全面剥离,并且已普遍发生点蚀的钢材表面。
除锈等级,也有时候成为表面清洁度
钢材表面的除锈等级以采用的除锈方法用字母Sa、St或FI表示。如果字母后面有阿拉伯数字,则表示其清除氧化皮、铁锈和尤其涂层等附着物的程度等级。
喷射或抛射除锈用字母sa表示。其有4个等级。Sa1,轻度的喷射或抛射除锈;Sa2,侧底的喷射或抛射除锈;Sa2.5,非常侧底的喷射或抛射除锈;Sa3,使钢材表面洁净的喷射或抛射除锈。
钢铁表面处理标准说明及各标准比较

钢铁表面主要表面处理标准GB8923-88 中国国家标准ISO8501-1:1988 国际标准化组织标准SIS055900-1967 瑞典标准SSPC-SP2,3,5,6,7和10 美国钢结构涂装协会表面处理标准 BS4232 英国标准DIN55928 德国标准JSRA SPSS 日本造船研究协会标准国标GB8923-88 对除锈等级描述:喷射或抛射除锈以字母“Sa”表示。
本标准订有四个除锈等级:Sa1 轻度的喷射或抛射除锈钢材表面应无可见的油脂和污垢,并且没有附着不牢的氧化皮,铁锈和油漆涂层等附着物。
Sa2 彻底的喷射或抛射除锈钢材表面应无可见的油脂和污垢,并且氧化皮,铁锈和油漆涂层等附着物已基本清除,其残留物应该是附着牢固的。
Sa2.5 非常彻底的喷射或抛射除锈钢材表面应无可见的油脂,污垢,氧化皮,铁锈和油漆涂层等附着物,任何残留的痕迹应仅是点状或条纹状的轻微色斑。
Sa3 钢材表面外观洁净的喷射或抛射除锈钢材表面应无可见的油脂,污垢,氧化皮,铁锈和油漆涂层等附着物,该表面应显示均匀的金属色泽。
手工和动力工具除锈以字母“St”表示。
本标准订有二个除锈等级:St2 彻底的手工和动力工具除锈钢材表面应无可见的油脂和污垢,并且没有附着不牢的氧化皮、铁锈和油漆涂层等附着物。
St3 非常彻底的手工和动力工具除锈钢材表面应无可见的油脂和污垢,并且没有附着不牢的氧化皮、铁锈和油漆涂层等附着物。
除锈应比St2更为彻底,底材显露部分的表面应具有金属光泽。
我国的除锈标准与相当的国外除锈标准对照表:注:SSPC中的Sp6比Sa2.5 略为严格,Sp2为人工钢丝刷除锈,Sp3为动力除锈。
表面粗糙度及其评定喷砂、抛丸、手工和动力除锈,其目的除达到前述一定的表面清洁度外,还会对钢铁表面造成一定的微观不平整度,即表面粗糙度。
对于涂漆前钢铁表面的粗糙度通常以一些主要的波峰和波谷间的高度值来表示。
钢铁表面粗糙度对漆膜的附着力,防腐蚀性能和保护寿命有很大影响。
表面处理的国标
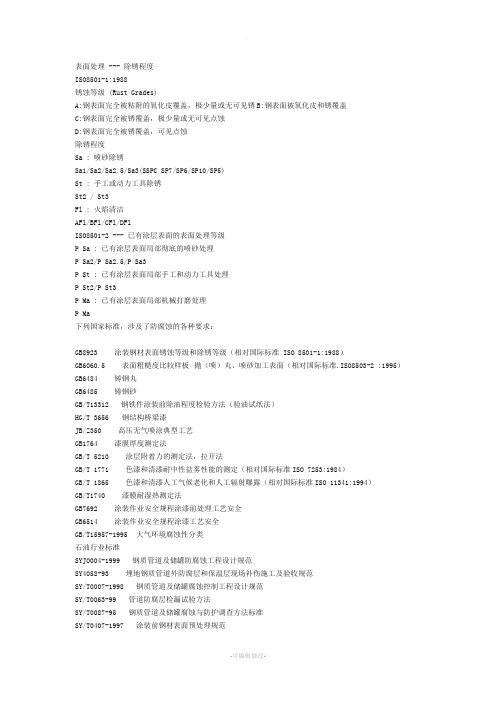
表面处理 --- 除锈程度ISO8501-1:1988锈蚀等级 (Rust Grades)A:钢表面完全被粘附的氧化皮覆盖,极少量或无可见锈B:钢表面被氧化皮和锈覆盖C:钢表面完全被锈覆盖,极少量或无可见点蚀D:钢表面完全被锈覆盖,可见点蚀除锈程度Sa : 喷砂除锈Sa1/Sa2/Sa2.5/Sa3(SSPC SP7/SP6/SP10/SP5)St : 手工或动力工具除锈St2 / St3Fl : 火焰清洁AFl/BFl/CFl/DFlISO8501-2 --- 已有涂层表面的表面处理等级P Sa : 已有涂层表面局部彻底的喷砂处理P Sa2/P Sa2.5/P Sa3P St : 已有涂层表面局部手工和动力工具处理P St2/P St3P Ma : 已有涂层表面局部机械打磨处理P Ma下列国家标准,涉及了防腐蚀的各种要求:GB8923涂装钢材表面锈蚀等级和除锈等级(相对国际标准 ISO 8501-1:1988)GB6060.5表面粗糙度比较样板抛(喷)丸、喷砂加工表面(相对国际标准.ISO8503-2 :1995)GB6484铸钢丸GB6485铸钢砂GB/T13312钢铁件涂装前除油程度检验方法(验油试纸法)HG/T 3656钢结构桥梁漆JB/Z350高压无气喷涂典型工艺GB1764漆膜厚度测定法GB/T 5210涂层附着力的测定法,拉开法GB/T 1771色漆和清漆耐中性盐雾性能的测定(相对国际标准ISO 7253:1984)GB/T 1865色漆和清漆人工气候老化和人工辐射曝露(相对国际标准ISO 11341:1994)GB/T1740漆膜耐湿热测定法GB7692涂装作业安全规程涂漆前处理工艺安全GB6514涂装作业安全规程涂漆工艺安全GB/T15957-1995大气环境腐蚀性分类石油行业标准SYJ0004-1999钢质管道及储罐防腐蚀工程设计规范SY4058-93埋地钢质管道外防腐层和保温层现场补伤施工及验收规范SY/T0007-1998钢质管道及储罐腐蚀控制工程设计规范SY/T0063-99管道防腐层检漏试验方法SY/T0087-95钢质管道及储罐腐蚀与防护调查方法标准SY/T0407-1997涂装前钢材表面预处理规范SY/T0447-96埋地钢质管道环氧煤沥青防腐层技术标准SY/T4091-1995滩海石油工程防腐蚀技术规范SYJ30-87埋地钢质管道及储罐防腐蚀工程基本术语Q/CNPC37-2002非腐蚀性天然气输送管内壁覆盖层推荐做法一、涂装标准的类别涂装标准从类别上划分可分为:1、公司标准如:国际油漆公司高压水喷射表面处理标准、海洋石油工程公司涂装施工程序等2、行业标准如:石油天然气工业标准3、国家标准如:GB, BS, DIN, ASTM, Norsok Standard, SSPC4、地区标准如:欧洲标准 ( CEN)5、国际标准如:ISO二、涉及了防腐蚀的各种要求:GB8923涂装钢材表面锈蚀等级和除锈等级(相对国际标准 ISO 8501-1:1988)GB6060.5表面粗糙度比较样板抛(喷)丸、喷砂加工表面(相对国际标准.ISO8503-2 :1995)GB6484铸钢丸GB6485铸钢砂GB/T13312钢铁件涂装前除油程度检验方法(验油试纸法)HG/T 3656钢结构桥梁漆JB/Z350高压无气喷涂典型工艺GB1764漆膜厚度测定法GB/T 5210涂层附着力的测定法,拉开法GB/T 1771色漆和清漆耐中性盐雾性能的测定(相对国际标准ISO 7253:1984)GB/T 1865色漆和清漆人工气候老化和人工辐射曝露(相对国际标准ISO 11341:1994)GB/T1740漆膜耐湿热测定法GB7692涂装作业安全规程涂漆前处理工艺安全GB6514涂装作业安全规程涂漆工艺安全GB/T15957-1995大气环境腐蚀性分类三、附着力测试标准ISO 2409:1972色漆和清漆-划格法测试ISO 4624:1978色漆和清漆-附着力拉开法测试ASTM D 3359-87胶带纸附着力标准测试法ASTM D 5162-01标准操作规程-金属底材上不传导型保护用涂料的不连续性(漏涂)测试NACE RP 0188-99标准测试规程-保护用涂料的不连续性(漏涂)测试法无机富锌漆的MEK测试ASTM D 4752-87无机硅酸富锌漆的耐MEK溶剂擦拭标准测试法四、国际上常用的相关标准有:1、新钢材表面锈蚀等级 --- ISO 8501-1:1988 / SSPC Vis2、已有涂层表面的锈蚀等级 --- ISO4628 / ASTM D6103、底材表面可溶性盐的检测 --- ISO8502-64、表面处理等级 --- ISO8501:1988 / SSPC SP / DIN 559285、表面粗糙度 --- ISO8503 / ASTM D 4417 / RUGOTEST No.36、喷砂磨料标准 --- ISO11124/ 11125/ 11126/ 111277、底材表面灰尘 --- ISO8502-38、干膜厚度的测量 --- SSPC PA2 / DIN 55929 / ISO28089、附着力 --- ISO4624 / SIS184171 / ASTM D3359 / ISO240910、无机富锌底漆固化程度 --- ASTM D475211、针孔检测 --- DIN 5567012、已有涂层的评估 --- ISO4628 / ASTM D714表面处理相关标准除锈程度ISO8501-1/ISO8501-2/SSPC SP底材表面清洁程度ISO8502-1~9表面粗糙度ISO8503/ASTM D4417/RUGOTEST No.3喷砂磨料标准ISO11124/ISO11125/ISO11126/ISO11127THANKS致力为企业和个人提供合同协议,策划案计划书,学习课件等等打造全网一站式需求欢迎您的下载,资料仅供参考。
钢铁表面处理﹑粗糙度及判别标准

钢铁表面处理﹑粗糙度及判别标准钢铁表面处理)粗糙度及判别标准钢铁表面主要表面处理标准: GB8923-88 中国国家标准ISO8501-1:1988 国际标准化组织标准SIS055900-1967 瑞典标准SSPC-SP2,3,5,6,7和10 美国钢结构涂装协会表面处理标准BS4232 英国标准DIN55928 德国标准JSRA SPSS 日本造船研究协会标准国标GB8923-88 对除锈等级描述:喷射或抛射除锈以字母“Sa”表示。
本标准订有四个除锈等级: Sa1 轻度的喷射或抛射除锈钢材表面应无可见的油脂和污垢,并且没有附着不牢的氧化皮,铁锈和油漆涂层等附着物。
Sa2 彻底的喷射或抛射除锈钢材表面应无可见的油脂和污垢,并且氧化皮,铁锈和油漆涂层等附着物已基本清除,其残留物应该是附着牢固的。
Sa2.5 非常彻底的喷射或抛射除锈钢材表面应无可见的油脂,污垢,氧化皮,铁锈和油漆涂层等附着物,任何残留的痕迹应仅是点状或条纹状的轻微色斑。
Sa3 钢材表面外观洁净的喷射或抛射除锈钢材表面应无可见的油脂,污垢,氧化皮,铁锈和油漆涂层等附着物,该表面应显示均匀的金属色泽。
手工和动力工具除锈以字母“St”表示。
本标准订有二个除锈等级:St2 彻底的手工和动力工具除锈钢材表面应无可见的油脂和污垢,并且没有附着不牢的氧化皮、铁锈和油漆涂层等附着物。
St3 非常彻底的手工和动力工具除锈钢材表面应无可见的油脂和污垢,并且没有附着不牢的氧化皮、铁锈和油漆涂层等附着物。
除锈应比St2更为彻底,底材显露部分的表面应具有金属光泽。
我国的除锈标准与相当的国外除锈标准对照表:日本中国国际标准瑞典德国美国英国JSRA GB8923 ISO8501-1 SIS055900 DIN55928 SSPC BS4232SPSS Sa1 Sa1 Sa1 Sa1 Sp7 ---- ----Sd1 Sa2 Sa2 Sa2 Sa2 Sp6 3级Sh1Sd2 Sa2.5 Sa2.5 Sa2.5 Sa2.5 Sp10 2级Sh2Sd3 Sa3 Sa3 Sa3 Sa3 Sp5 1级Sh3 St2 St2 St2 St2 Sp2 ---- Pt2 St3 St3 St3 St3 SP3 ---- Pt3注:SSPC中的Sp6比Sa2.5 略为严格,Sp2为人工钢丝刷除锈,Sp3为动力除锈。
表面处理等级

粗糙度等级区分钢材在防腐前需要除锈,达到一定的除锈等级和表面粗糙度才能进行防腐。
除锈等级和表面粗糙度等级是两个不同的概念。
钢材表面的锈蚀按GB8923分为四个等级:A 全面地覆盖着氧化皮而几乎没有铁锈的钢材表面;B已发生锈蚀,并且部分氧化皮已经脱落的钢材表面;C氧化皮已经因锈蚀而剥落,或者可以刮厨,并且与少量点蚀的钢材表面;D氧化皮已经因锈蚀而全面剥离,并且已普遍发生点蚀的钢材表面。
除锈等级,也有时候成为表面清洁度钢材表面的除锈等级以采用的除锈方法用字母Sa、St或FI表示。
如果字母后面有阿拉伯数字,则表示其清除氧化皮、铁锈和尤其涂层等附着物的程度等级。
喷射或抛射除锈用字母sa表示。
其有4个等级。
Sa1,轻度的喷射或抛射除锈;Sa2,侧底的喷射或抛射除锈;Sa2.5,非常侧底的喷射或抛射除锈;Sa3,使钢材表面洁净的喷射或抛射除锈。
手动工具除锈用St表示,有两个等级。
St2为彻底的手工或动力工具除锈;St3为非常彻底的手工或动力工具除锈。
火焰除锈以FI表示。
Sa1级——相当于美国SSPC—SP7级。
采用一般简单的手工刷除、砂布打磨方法,这是四种清洁度中度最低的一级,对涂层的保护仅仅略好于未采用处理的工件。
Sa1级处理的技术标准:工件表面应不可见油污、油脂、残留氧化皮、锈斑、和残留油漆等污物。
Sa1级也叫做手工刷除清理级。
(或清扫级)Sa2级——相当于美国SSPC—SP6级。
采用喷砂清理方法,这是喷砂处理中最低的一级,即一般的要求,但对于涂层的保护要比手工刷除清理要提高许多。
Sa2级处理的技术标准:工件表面应不可见油腻、污垢、氧化皮、锈皮、油漆、氧化物、腐蚀物、和其它外来物质(疵点除外),但疵点限定为不超过每平方米表面的33%,可包括轻微阴影;少量因疵点、锈蚀引起的轻微脱色;氧化皮及油漆疵点。
如果工件原表面有凹痕,则轻微的锈蚀和油漆还会残留在凹痕底部。
Sa2级也叫商品清理级(或工业级)。
Sa2.5级——是工业上普遍使用的并可以作为验收技术要求及标准的级别。
表面处理的国标
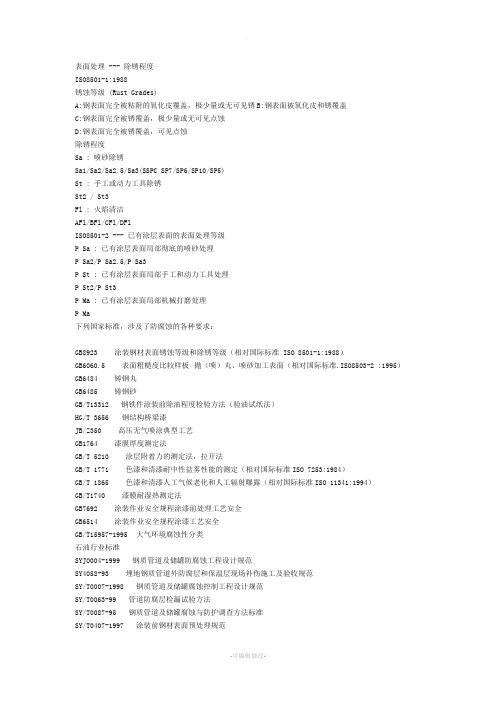
表面处理 --- 除锈程度ISO8501-1:1988锈蚀等级 (Rust Grades)A:钢表面完全被粘附的氧化皮覆盖,极少量或无可见锈B:钢表面被氧化皮和锈覆盖C:钢表面完全被锈覆盖,极少量或无可见点蚀D:钢表面完全被锈覆盖,可见点蚀除锈程度Sa : 喷砂除锈Sa1/Sa2/Sa2.5/Sa3(SSPC SP7/SP6/SP10/SP5)St : 手工或动力工具除锈St2 / St3Fl : 火焰清洁AFl/BFl/CFl/DFlISO8501-2 --- 已有涂层表面的表面处理等级P Sa : 已有涂层表面局部彻底的喷砂处理P Sa2/P Sa2.5/P Sa3P St : 已有涂层表面局部手工和动力工具处理P St2/P St3P Ma : 已有涂层表面局部机械打磨处理P Ma下列国家标准,涉及了防腐蚀的各种要求:GB8923涂装钢材表面锈蚀等级和除锈等级(相对国际标准 ISO 8501-1:1988)GB6060.5表面粗糙度比较样板抛(喷)丸、喷砂加工表面(相对国际标准.ISO8503-2 :1995)GB6484铸钢丸GB6485铸钢砂GB/T13312钢铁件涂装前除油程度检验方法(验油试纸法)HG/T 3656钢结构桥梁漆JB/Z350高压无气喷涂典型工艺GB1764漆膜厚度测定法GB/T 5210涂层附着力的测定法,拉开法GB/T 1771色漆和清漆耐中性盐雾性能的测定(相对国际标准ISO 7253:1984)GB/T 1865色漆和清漆人工气候老化和人工辐射曝露(相对国际标准ISO 11341:1994)GB/T1740漆膜耐湿热测定法GB7692涂装作业安全规程涂漆前处理工艺安全GB6514涂装作业安全规程涂漆工艺安全GB/T15957-1995大气环境腐蚀性分类石油行业标准SYJ0004-1999钢质管道及储罐防腐蚀工程设计规范SY4058-93埋地钢质管道外防腐层和保温层现场补伤施工及验收规范SY/T0007-1998钢质管道及储罐腐蚀控制工程设计规范SY/T0063-99管道防腐层检漏试验方法SY/T0087-95钢质管道及储罐腐蚀与防护调查方法标准SY/T0407-1997涂装前钢材表面预处理规范SY/T0447-96埋地钢质管道环氧煤沥青防腐层技术标准SY/T4091-1995滩海石油工程防腐蚀技术规范SYJ30-87埋地钢质管道及储罐防腐蚀工程基本术语Q/CNPC37-2002非腐蚀性天然气输送管内壁覆盖层推荐做法一、涂装标准的类别涂装标准从类别上划分可分为:1、公司标准如:国际油漆公司高压水喷射表面处理标准、海洋石油工程公司涂装施工程序等2、行业标准如:石油天然气工业标准3、国家标准如:GB, BS, DIN, ASTM, Norsok Standard, SSPC4、地区标准如:欧洲标准 ( CEN)5、国际标准如:ISO二、涉及了防腐蚀的各种要求:GB8923涂装钢材表面锈蚀等级和除锈等级(相对国际标准 ISO 8501-1:1988)GB6060.5表面粗糙度比较样板抛(喷)丸、喷砂加工表面(相对国际标准.ISO8503-2 :1995)GB6484铸钢丸GB6485铸钢砂GB/T13312钢铁件涂装前除油程度检验方法(验油试纸法)HG/T 3656钢结构桥梁漆JB/Z350高压无气喷涂典型工艺GB1764漆膜厚度测定法GB/T 5210涂层附着力的测定法,拉开法GB/T 1771色漆和清漆耐中性盐雾性能的测定(相对国际标准ISO 7253:1984)GB/T 1865色漆和清漆人工气候老化和人工辐射曝露(相对国际标准ISO 11341:1994)GB/T1740漆膜耐湿热测定法GB7692涂装作业安全规程涂漆前处理工艺安全GB6514涂装作业安全规程涂漆工艺安全GB/T15957-1995大气环境腐蚀性分类三、附着力测试标准ISO 2409:1972色漆和清漆-划格法测试ISO 4624:1978色漆和清漆-附着力拉开法测试ASTM D 3359-87胶带纸附着力标准测试法ASTM D 5162-01标准操作规程-金属底材上不传导型保护用涂料的不连续性(漏涂)测试NACE RP 0188-99标准测试规程-保护用涂料的不连续性(漏涂)测试法无机富锌漆的MEK测试ASTM D 4752-87无机硅酸富锌漆的耐MEK溶剂擦拭标准测试法四、国际上常用的相关标准有:1、新钢材表面锈蚀等级 --- ISO 8501-1:1988 / SSPC Vis2、已有涂层表面的锈蚀等级 --- ISO4628 / ASTM D6103、底材表面可溶性盐的检测 --- ISO8502-64、表面处理等级 --- ISO8501:1988 / SSPC SP / DIN 559285、表面粗糙度 --- ISO8503 / ASTM D 4417 / RUGOTEST No.36、喷砂磨料标准 --- ISO11124/ 11125/ 11126/ 111277、底材表面灰尘 --- ISO8502-38、干膜厚度的测量 --- SSPC PA2 / DIN 55929 / ISO28089、附着力 --- ISO4624 / SIS184171 / ASTM D3359 / ISO240910、无机富锌底漆固化程度 --- ASTM D475211、针孔检测 --- DIN 5567012、已有涂层的评估 --- ISO4628 / ASTM D714表面处理相关标准除锈程度ISO8501-1/ISO8501-2/SSPC SP底材表面清洁程度ISO8502-1~9表面粗糙度ISO8503/ASTM D4417/RUGOTEST No.3喷砂磨料标准ISO11124/ISO11125/ISO11126/ISO11127THANKS致力为企业和个人提供合同协议,策划案计划书,学习课件等等打造全网一站式需求欢迎您的下载,资料仅供参考。
除锈等级和表面粗糙度

钢材在防腐前需要除锈,达到一定的除锈等级和表面粗糙度才能进行防腐。
除锈等级和表面粗糙度等级是两个不同的概念。
钢材表面的锈蚀按GB8923分为四个等级:A 全面地覆盖着氧化皮而几乎没有铁锈的钢材表面;B已发生锈蚀,并且部分氧化皮已经脱落的钢材表面;C氧化皮已经因锈蚀而剥落,或者可以刮厨,并且与少量点蚀的钢材表面;D氧化皮已经因锈蚀而全面剥离,并且已普遍发生点蚀的钢材表面。
除锈等级,也有时候成为表面清洁度钢材表面的除锈等级以采用的除锈方法用字母Sa、St或FI表示。
如果字母后面有阿拉伯数字,则表示其清除氧化皮、铁锈和尤其涂层等附着物的程度等级。
喷射或抛射除锈用字母sa表示。
其有4个等级。
Sa1,轻度的喷射或抛射除锈;Sa2,侧底的喷射或抛射除锈;Sa2.5,非常侧底的喷射或抛射除锈;Sa3,使钢材表面洁净的喷射或抛射除锈。
手动工具除锈用St表示,有两个等级。
St2为彻底的手工或动力工具除锈;St3为非常彻底的手工或动力工具除锈。
火焰除锈以FI表示。
Sa1级——相当于美国SSPC—SP7级。
采用一般简单的手工刷除、砂布打磨方法,这是四种清洁度中度最低的一级,对涂层的保护仅仅略好于未采用处理的工件。
Sa1级处理的技术标准:工件表面应不可见油污、油脂、残留氧化皮、锈斑、和残留油漆等污物。
Sa1级也叫做手工刷除清理级。
(或清扫级)Sa2级——相当于美国SSPC—SP6级。
采用喷砂清理方法,这是喷砂处理中最低的一级,即一般的要求,但对于涂层的保护要比手工刷除清理要提高许多。
Sa2级处理的技术标准:工件表面应不可见油腻、污垢、氧化皮、锈皮、油漆、氧化物、腐蚀物、和其它外来物质(疵点除外),但疵点限定为不超过每平方米表面的33%,可包括轻微阴影;少量因疵点、锈蚀引起的轻微脱色;氧化皮及油漆疵点。
如果工件原表面有凹痕,则轻微的锈蚀和油漆还会残留在凹痕底部。
Sa2级也叫商品清理级(或工业级)。
Sa2.5级——是工业上普遍使用的并可以作为验收技术要求及标准的级别。
管道抛丸除锈粗糙度标准

管道抛丸除锈粗糙度标准管道抛丸除锈粗糙度标准是指对于管道进行抛丸除锈处理后,其表面的粗糙度应符合一定的标准要求。
管道抛丸除锈是一种常用的除锈方法,通过高速旋转的抛丸轮将钢丸或钢砂等抛射到管道表面,以达到去除污垢、氧化层和锈蚀的目的。
而管道表面的粗糙度则是对于抛丸除锈效果的评估指标之一。
管道抛丸除锈粗糙度标准主要有以下几个方面:1. 表面粗糙度等级:根据不同的使用要求和工艺要求,管道抛丸除锈后的表面粗糙度可以分为不同的等级。
常见的等级有Sa2.5、Sa2.0、Sa1.5、Sa1.0等,其中Sa2.5表示表面粗糙度为2.5微米。
2. 表面清洁度等级:除了粗糙度要求外,管道表面还需要达到一定的清洁度要求。
根据ISO8501-1标准,常见的清洁度等级有St2、St3等,其中St2表示表面可容许有少量残留污垢。
3. 表面处理方法:除了抛丸除锈外,还可以采用化学除锈、机械除锈等方法进行管道表面处理。
不同的处理方法对于管道表面粗糙度的要求也有所不同。
4. 抛丸设备和工艺参数:管道抛丸除锈的效果还与抛丸设备和工艺参数有关。
例如,抛丸轮的转速、抛丸轮与管道表面的距离、抛丸材料的种类和大小等都会对管道表面粗糙度产生影响。
在实际应用中,根据具体的工程要求和使用环境,可以选择适当的管道抛丸除锈粗糙度标准。
通常情况下,对于一些要求较高的工程项目,如石油、化工、航空航天等领域,需要达到较高的粗糙度标准,以确保管道表面的清洁度和耐腐蚀性能。
而对于一些一般工程项目,则可以选择较低的粗糙度标准。
总之,管道抛丸除锈粗糙度标准是对于管道表面粗糙度要求的规定,它是确保管道表面清洁度和耐腐蚀性能的重要指标之一。
在实际应用中,应根据具体的工程要求和使用环境选择适当的标准,并合理控制抛丸设备和工艺参数,以确保管道抛丸除锈效果符合要求。
表面处理标准对照表
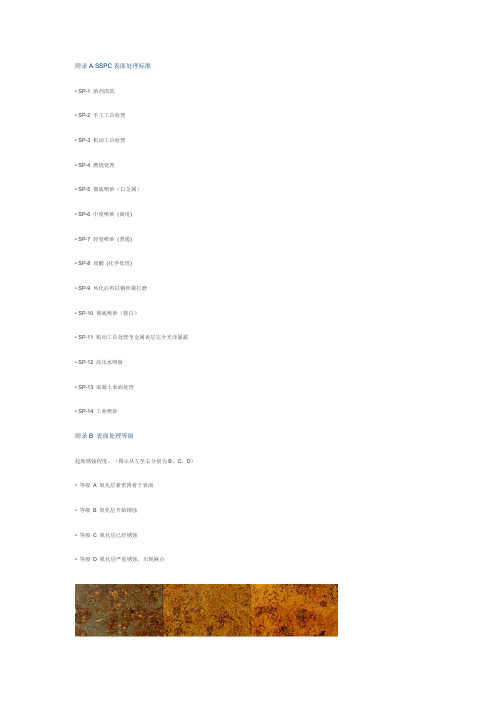
附录A SSPC表面处理标准• SP-1 溶剂清洗• SP-2 手工工具处理• SP-3 机动工具处理• SP-4 燃烧处理• SP-5 彻底喷砂(白金属)• SP-6 中度喷砂(商用)• SP-7 轻度喷砂(普通)• SP-8 浸酸(化学处理)• SP-9 风化后再以钢丝刷打磨• SP-10 彻底喷砂(接白)• SP-11 机动工具处理至金属表层完全光泽暴露• SP-12 高压水喷射• SP-13 混凝土表面处理• SP-14 工业喷砂附录B 表面处理等级起始锈蚀程度:(图示从左至右分别为B、C、D)• 等级A 氧化层紧密附着于表面• 等级B 氧化层开始锈蚀• 等级C 氧化层已经锈蚀• 等级D 氧化层严重锈蚀,出现麻点轻度喷砂:商用喷砂:近白喷砂:白金属喷砂:附录C 国际通用表面处理标准对比钢结构油漆委员会Steel Structure Painting Council (SSPC)国家防腐工程师协会National Association of Corrosion Engineers (NACE) 英国标准ISO 8501-1 / BSI BS 7079瑞典标准Swedish Standard国标GB-3092 / GB-8923-88关于表面处理等级1994年10月,NACE和SSPC发布了用于磨料清理的联合表面处理标准(这些标准大约相当于由最初的瑞典标准发展而来的ISO标准ISO8501-1SO-公布于1988年:NACE NO.I/SSPC-SP5“金属出白级喷砂” 相当于—Sa3“喷砂至可见清洁金属”NACE NO.2/SSPC-SP10“金属近于出白级喷砂” 相当于—Sa21/2“非常彻底的喷砂清理”NACE NO.3/SSPC-SP6“工业级喷砂” 相当于—Sa2“彻底的喷砂清理”NACE NO.4/SSPC-SP7“刷除锈级喷砂” 相当于—Sa1“轻喷砂清理”SSPC-SP1“溶剂清理” SSPC-SP2“手动工具清理” SSPC-SP11 “动力工具清理至裸钢”SSPC-SP8“酸洗” SSPC-SP3“动力工具清理” SSPC-SP11R “动力工具清理维修保养”一、金属(1) 新表面A.钢铁1.喷砂处理实践证明,无论是在施工现场还是在装配车间,喷砂处理都是除去锻痕的最有效方法。
除锈等级和表面粗糙度对照表

BSt2 BSt3
B BSt2 CSt3 CSa1 CSa2 CSa2.5 CSa3 DSt2 DSt3
D DSa1 DSa2
DSa2.5 DSa3 粗糙度样板
除锈等级及表面粗糙度比较图锈蚀状态图除锈等级图aasa2
除锈等级和表面粗糙度对照表
附件一 钢材表面除锈等级和表面粗糙度比较图 一、锈蚀等级 A 级:钢材表面完全覆盖粘附的氧化皮,几乎无铁锈; B 级:钢材表面已开始锈蚀,氧化皮开始成片状脱落; C 级:钢材表面上的氧化皮已锈蚀,或可刮除,但裸眼可看到轻微锈点; D 级:钢材表面上的氧化皮已锈蚀剥落,裸眼可看到大量锈点。 二、除锈等级及表面粗糙度比较图 锈蚀状态图除锈等级图
防腐除锈等级划分标准
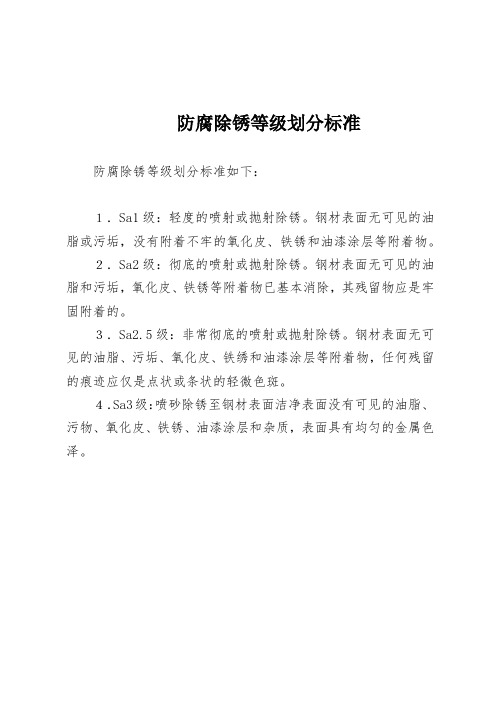
防腐除锈等级划分标准
防腐除锈等级划分标准如下:
1.Sa1级:轻度的喷射或抛射除锈。
钢材表面无可见的油脂或污垢,没有附着不牢的氧化皮、铁锈和油漆涂层等附着物。
2.Sa2级:彻底的喷射或抛射除锈。
钢材表面无可见的油脂和污垢,氧化皮、铁锈等附着物已基本消除,其残留物应是牢固附着的。
3.Sa2.5级:非常彻底的喷射或抛射除锈。
钢材表面无可见的油脂、污垢、氧化皮、铁绣和油漆涂层等附着物,任何残留的痕迹应仅是点状或条状的轻微色斑。
4.Sa3级:喷砂除锈至钢材表面洁净表面没有可见的油脂、污物、氧化皮、铁锈、油漆涂层和杂质,表面具有均匀的金属色泽。
除锈等级和表面粗糙度

钢材在防腐前需要除锈,达到一定的除锈等级和表面粗糙度才能进行防腐。
除锈等级和表面粗糙度等级是两个不同的概念。
钢材表面的锈蚀按GB8923分为四个等级:A 全面地覆盖着氧化皮而几乎没有铁锈的钢材表面;B已发生锈蚀,并且部分氧化皮已经脱落的钢材表面;C氧化皮已经因锈蚀而剥落,或者可以刮厨,并且与少量点蚀的钢材表面;D氧化皮已经因锈蚀而全面剥离,并且已普遍发生点蚀的钢材表面。
除锈等级,也有时候成为表面清洁度钢材表面的除锈等级以采用的除锈方法用字母Sa、St或FI表示。
如果字母后面有阿拉伯数字,则表示其清除氧化皮、铁锈和尤其涂层等附着物的程度等级。
喷射或抛射除锈用字母sa表示。
其有4个等级。
Sa1,轻度的喷射或抛射除锈;Sa2,侧底的喷射或抛射除锈;Sa2.5,非常侧底的喷射或抛射除锈;Sa3,使钢材表面洁净的喷射或抛射除锈。
手动工具除锈用St表示,有两个等级。
St2为彻底的手工或动力工具除锈;St3为非常彻底的手工或动力工具除锈。
火焰除锈以FI表示。
Sa1级——相当于美国SSPC—SP7级。
采用一般简单的手工刷除、砂布打磨方法,这是四种清洁度中度最低的一级,对涂层的保护仅仅略好于未采用处理的工件。
Sa1级处理的技术标准:工件表面应不可见油污、油脂、残留氧化皮、锈斑、和残留油漆等污物。
Sa1级也叫做手工刷除清理级。
(或清扫级)Sa2级——相当于美国SSPC—SP6级。
采用喷砂清理方法,这是喷砂处理中最低的一级,即一般的要求,但对于涂层的保护要比手工刷除清理要提高许多。
Sa2级处理的技术标准:工件表面应不可见油腻、污垢、氧化皮、锈皮、油漆、氧化物、腐蚀物、和其它外来物质(疵点除外),但疵点限定为不超过每平方米表面的33%,可包括轻微阴影;少量因疵点、锈蚀引起的轻微脱色;氧化皮及油漆疵点。
如果工件原表面有凹痕,则轻微的锈蚀和油漆还会残留在凹痕底部。
Sa2级也叫商品清理级(或工业级)。
Sa2.5级——是工业上普遍使用的并可以作为验收技术要求及标准的级别。
钢铁表面处理标准说明及各标准比较

钢铁表面主要表面处理标准GB8923-88 中国国家标准ISO8501-1:1988 国际标准化组织标准SIS055900-1967 瑞典标准SSPC-SP2,3,5,6,7和10 美国钢结构涂装协会表面处理标准 BS4232 英国标准DIN55928 德国标准JSRA SPSS 日本造船研究协会标准国标GB8923-88 对除锈等级描述:喷射或抛射除锈以字母“Sa”表示。
本标准订有四个除锈等级:Sa1 轻度的喷射或抛射除锈钢材表面应无可见的油脂和污垢,并且没有附着不牢的氧化皮,铁锈和油漆涂层等附着物。
Sa2 彻底的喷射或抛射除锈钢材表面应无可见的油脂和污垢,并且氧化皮,铁锈和油漆涂层等附着物已基本清除,其残留物应该是附着牢固的。
Sa2.5 非常彻底的喷射或抛射除锈钢材表面应无可见的油脂,污垢,氧化皮,铁锈和油漆涂层等附着物,任何残留的痕迹应仅是点状或条纹状的轻微色斑。
Sa3 钢材表面外观洁净的喷射或抛射除锈钢材表面应无可见的油脂,污垢,氧化皮,铁锈和油漆涂层等附着物,该表面应显示均匀的金属色泽。
手工和动力工具除锈以字母“St”表示。
本标准订有二个除锈等级:St2 彻底的手工和动力工具除锈钢材表面应无可见的油脂和污垢,并且没有附着不牢的氧化皮、铁锈和油漆涂层等附着物。
St3 非常彻底的手工和动力工具除锈钢材表面应无可见的油脂和污垢,并且没有附着不牢的氧化皮、铁锈和油漆涂层等附着物。
除锈应比St2更为彻底,底材显露部分的表面应具有金属光泽。
我国的除锈标准与相当的国外除锈标准对照表:中国GB8 923国际标准ISO8501-1瑞典SIS055900德国DIN55928美国SSPC英国BS4232日本JSRA SPSSSa1 Sa1 Sa1 Sa1 Sp7--------Sa2 Sa2 Sa2 Sa2 Sp6 3级Sd1 Sh1Sa2 .5Sa2.5Sa2.5Sa2.5Sp12级Sd2Sh2Sa3 Sa3 Sa3 Sa3 Sp5 1级Sd3 Sh3St2 St2 St2 St2 Sp2----Pt2St3 St3 St3 St3 SP3----Pt3注:SSPC中的Sp6比Sa2.5 略为严格,Sp2为人工钢丝刷除锈,Sp3为动力除锈。
除锈质量等级标准表
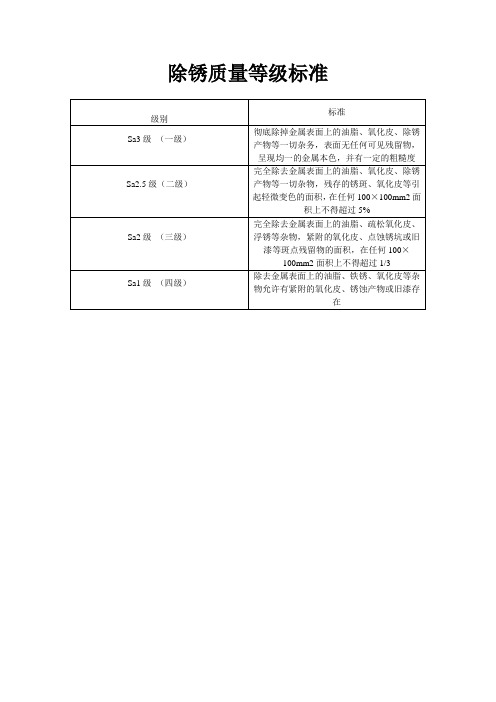
完全除去金属表面上的油脂、疏松氧化皮、浮锈等杂物,紧附的氧化皮、点蚀锈坑或旧漆等斑点残留物的面积,在任何100×100mm2面积上不得超过1/3
Sa1级(四级)除去金来自表面上的油脂、铁锈、氧化皮等杂物允许有紧附的氧化皮、锈蚀产物或旧漆存在
除锈质量等级标准
级别
标准
Sa3级(一级)
彻底除掉金属表面上的油脂、氧化皮、除锈产物等一切杂务,表面无任何可见残留物,呈现均一的金属本色,并有一定的粗糙度
Sa2.5级(二级)
完全除去金属表面上的油脂、氧化皮、除锈产物等一切杂物,残存的锈斑、氧化皮等引起轻微变色的面积,在任何100×100mm2面积上不得超过5%
除锈质量等级标准级别标准sa3一级彻底除掉金属表面上的油脂氧化皮除锈产物等一切杂务表面无任何可见残留物呈现均一的金属本色并有一定的粗糙度sa25级二级完全除去金属表面上的油脂氧化皮除锈产物等一切杂物残存的锈斑氧化皮等引起轻微变色的面积在任何100100mm2积上不得超过5sa2三级完全除去金属表面上的油脂疏松氧化皮漆等斑点残留物的面积在任何100100mm2面积上不得超过13sa1四级除去金属表面上的油脂铁锈氧化皮等杂物允许有紧附的氧化皮锈蚀产物或旧漆存精品范文精品范文
表面粗糙度等级对照表

镜面0.006微米雾状镜面0.012镜状光泽面0.025亮光泽面0.05暗光泽面0.1不可见加工痕迹的方向0.2可见加工痕迹方向0.8微见加工痕迹方向0.4看不清加工痕迹方向 1.6微见加工痕迹方向 3.2可见加工痕迹方向 6.3微见刀痕12.51级Ra值不大于\μm=100表面状况=明显可见的刀痕加工方法=粗车、镗、刨、钻应用举例=粗加工的表面,如粗车、粗刨、切断等表面,用粗镗刀和粗砂轮等加工的表面,一般很少采用2级Ra值不大于\μm=25、50表面状况=明显可见的刀痕加工方法=粗车、镗、刨、钻应用举例=粗加工后的表面,焊接前的焊缝、粗钻孔壁等3级Ra值不大于\μm=12.5表面状况=可见刀痕加工方法=粗车、刨、铣、钻应用举例=一般非结合表面,如轴的端面、倒角、齿轮及皮带轮的侧面、键槽的非工作表面,减重孔眼表面4级Ra值不大于\μm=6.3表面状况=可见加工痕迹加工方法=车、镗、刨、钻、铣、锉、磨、粗铰、铣齿应用举例=不重要零件的配合表面,如支柱、支架、外壳、衬套、轴、盖等的端面。
紧固件的自由表面,紧固件通孔的表面,内、外花键的非定心表面,不作为计量基准的齿轮顶圈圆表面等5级Ra值不大于\μm=3.2表面状况=微见加工痕迹加工方法=车、镗、刨、铣、刮1~2点/cm^2、拉、磨、锉、滚压、铣齿应用举例=和其他零件连接不形成配合的表面,如箱体、外壳、端盖等零件的端面。
要求有定心及配合特性的固定支承面如定心的轴间,键和键槽的工作表面。
不重要的紧固螺纹的表面。
需要滚花或氧化处理的表面6级Ra值不大于\μm=1.6表面状况=看不清加工痕迹加工方法=车、镗、刨、铣、铰、拉、磨、滚压、刮1~2点/cm^2铣齿应用举例=安装直径超过80mm的G级轴承的外壳孔,普通精度齿轮的齿面,定位销孔,V 型带轮的表面,外径定心的内花键外径,轴承盖的定中心凸肩表面7级Ra值不大于\μm=0.8表面状况=可辨加工痕迹的方向加工方法=车、镗、拉、磨、立铣、刮3~10点/cm^2、滚压应用举例=要求保证定心及配合特性的表面,如锥销与圆柱销的表面,与G级精度滚动轴承相配合的轴径和外壳孔,中速转动的轴径,直径超过80mm的E、D级滚动轴承配合的轴径及外壳孔,内、外花键的定心内径,外花键键侧及定心外径,过盈配合IT7级的孔(H7),间隙配合IT8~IT9级的孔(H8,H9),磨削的齿轮表面等8级Ra值不大于\μm=0.4表面状况=微辨加工痕迹的方向加工方法=铰、磨、镗、拉、刮3~10点/cm^2、滚压应用举例=要求长期保持配合性质稳定的配合表面,IT7级的轴、孔配合表面,精度较高的齿轮表面,受变应力作用的重要零件,与直径小于80mm的E、D级轴承配合的轴径表面、与橡胶密封件接触的轴的表面,尺寸大于120mm的IT13~IT16级孔和轴用量规的测量表面9级Ra值不大于\μm=0.2表面状况=不可辨加工痕迹的方向加工方法=布轮磨、磨、研磨、超级加工应用举例=工作时受变应力作用的重要零件的表面。
表面粗糙度等级对照表

镜面0.006微米雾状镜面0.012镜状光泽面0.025亮光泽面0.05暗光泽面0.1不可见加工痕迹的方向0.2可见加工痕迹方向0.8微见加工痕迹方向0.4看不清加工痕迹方向 1.6微见加工痕迹方向 3.2可见加工痕迹方向 6.3微见刀痕12.51级Ra值不大于\μm=100表面状况=明显可见的刀痕加工方法=粗车、镗、刨、钻应用举例=粗加工的表面,如粗车、粗刨、切断等表面,用粗镗刀和粗砂轮等加工的表面,一般很少采用2级Ra值不大于\μm=25、50表面状况=明显可见的刀痕加工方法=粗车、镗、刨、钻应用举例=粗加工后的表面,焊接前的焊缝、粗钻孔壁等3级Ra值不大于\μm=12.5表面状况=可见刀痕加工方法=粗车、刨、铣、钻应用举例=一般非结合表面,如轴的端面、倒角、齿轮及皮带轮的侧面、键槽的非工作表面,减重孔眼表面4级Ra值不大于\μm=6.3表面状况=可见加工痕迹加工方法=车、镗、刨、钻、铣、锉、磨、粗铰、铣齿应用举例=不重要零件的配合表面,如支柱、支架、外壳、衬套、轴、盖等的端面。
紧固件的自由表面,紧固件通孔的表面,内、外花键的非定心表面,不作为计量基准的齿轮顶圈圆表面等5级Ra值不大于\μm=3.2表面状况=微见加工痕迹加工方法=车、镗、刨、铣、刮1~2点/cm^2、拉、磨、锉、滚压、铣齿应用举例=和其他零件连接不形成配合的表面,如箱体、外壳、端盖等零件的端面。
要求有定心及配合特性的固定支承面如定心的轴间,键和键槽的工作表面。
不重要的紧固螺纹的表面。
需要滚花或氧化处理的表面6级Ra值不大于\μm=1.6表面状况=看不清加工痕迹加工方法=车、镗、刨、铣、铰、拉、磨、滚压、刮1~2点/cm^2铣齿应用举例=安装直径超过80mm的G级轴承的外壳孔,普通精度齿轮的齿面,定位销孔,V 型带轮的表面,外径定心的内花键外径,轴承盖的定中心凸肩表面7级Ra值不大于\μm=0.8表面状况=可辨加工痕迹的方向加工方法=车、镗、拉、磨、立铣、刮3~10点/cm^2、滚压应用举例=要求保证定心及配合特性的表面,如锥销与圆柱销的表面,与G级精度滚动轴承相配合的轴径和外壳孔,中速转动的轴径,直径超过80mm的E、D级滚动轴承配合的轴径及外壳孔,内、外花键的定心内径,外花键键侧及定心外径,过盈配合IT7级的孔(H7),间隙配合IT8~IT9级的孔(H8,H9),磨削的齿轮表面等8级Ra值不大于\μm=0.4表面状况=微辨加工痕迹的方向加工方法=铰、磨、镗、拉、刮3~10点/cm^2、滚压应用举例=要求长期保持配合性质稳定的配合表面,IT7级的轴、孔配合表面,精度较高的齿轮表面,受变应力作用的重要零件,与直径小于80mm的E、D级轴承配合的轴径表面、与橡胶密封件接触的轴的表面,尺寸大于120mm的IT13~IT16级孔和轴用量规的测量表面9级Ra值不大于\μm=0.2表面状况=不可辨加工痕迹的方向加工方法=布轮磨、磨、研磨、超级加工应用举例=工作时受变应力作用的重要零件的表面。
表面粗糙度等级

本人从事机械行业多年,为大家提供一些简单的数据:【表面粗糙度等级】
【表面粗糙度Ra特征】
附件一
钢材表面除锈等级和表面粗糙度比较图
一、锈蚀等级
A 级:钢材表面完全覆盖粘附的氧化皮,几乎无铁锈;
B 级:钢材表面已开始锈蚀,氧化皮开始成片状脱落;
C 级:钢材表面上的氧化皮已锈蚀,或可刮除,但裸眼可看到轻微锈点;
D 级:钢材表面上的氧化皮已锈蚀剥落,裸眼可看到大量锈点。
二、除锈等级及表面粗糙度比较图
锈蚀状态图除锈等级图
A ASa2.5ASa3
BSt2 BSt3
BBSa1 BSa2
BSa2.5 BSa3 C CSt2 CSt3
CSa1 CSa2
CSa2.5 CSa3
DSt2 DSt3 D DSa1 DSa2
DSa2.5 DSa3
粗糙度样板
镜面0.006微米雾状镜面0.012
镜状光泽面0.025
亮光泽面0.05
暗光泽面0.1
不可见加工痕迹的方向0.2
可见加工痕迹方向0.8
微见加工痕迹方向0.4
看不清加工痕迹方向 1.6
微见加工痕迹方向 3.2
可见加工痕迹方向 6.3
微见刀痕12.5
可见刀痕25
明显可见刀痕50。