cnc攻丝
CNC加工工艺流程

06 CNC加工工艺的发展趋势 和未来展望
CNC加工工艺的发展趋势
智能化
随着人工智能和机器学习技术的不断发展,CNC 加工工艺正朝着智能化方向发展。智能化技术能 够提高加工过程的自动化程度,减少人工干预, 提高加工精度和效率。
绿色环保
随着环保意识的不断提高,CNC加工工艺正朝着 绿色环保方向发展。绿色环保的CNC加工工艺能 够减少能源消耗和废弃物排放,降低对环境的负 面影响。
确定加工余量
根据各工序的加工精度和表面质量要求,确定合 理的加工余量。
04 CNC加工过程
工件的装夹与校正
• 总结词:工件装夹是CNC加工过程中的重要环节,需要确保工件定位准确、 夹紧可靠,以减少加工误差和提高加工效率。
• 详细描述:工件装夹前,需要对工件进行仔细检查,确保其表面质量、尺寸精 度和形位公差符合要求。根据工件的特点和加工要求,选择合适的装夹方式, 如三爪卡盘、四爪卡盘、顶尖、心轴等。在装夹过程中,要确保工件定位准确 ,夹紧力适中,防止工件变形或损坏。
零件的清洗与涂装
清洗
使用清洗剂清除零件表面的油污 、切屑等杂质,确保表面清洁。
涂装
根据需要,对零件进行涂装处理 ,如喷漆、电镀等,以提高其耐 腐蚀性和美观度。
零件的包装与储存
包装
根据零件的特性和运输要求,选择适 当的包装材料和方式,确保零件在运 输过程中不受损坏。
储存
将包装好的零件存放在干燥、通风良 好的仓库中,避免阳光直射和潮湿环 境,以确保零件的质量和性能。
03 CNC加工前的准备
零件的工艺性分析
01
02
03
零件的结构分析
检查零件的结构是否适合 CNC加工,如表面形状、 尺寸精度等。
CNC机床钻孔、攻丝切削参数
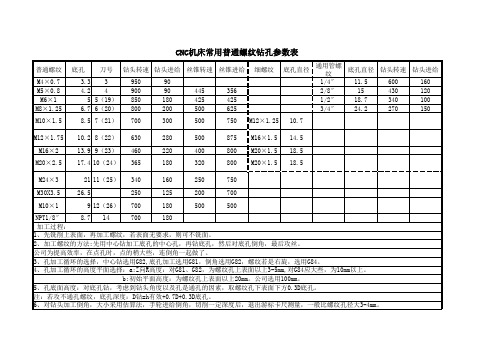
CNC机床常用普通螺纹钻孔参数表
普通螺纹 底孔 刀号 钻头转速 钻头进给 丝锥转速 丝锥进给 细螺纹 底孔直径 通用管螺 底孔直径 钻头转速 钻头进给 纹 1/4″ 11.5 600 160 2/8″ 15 430 120 1/2″ 18.7 340 100 3/4″ 24.2 270 150
M4×0.7 3.3 3 950 90 M5×0.8 4.2 4 900 90 445 356 M6×1 5 5(19) 850 180 425 425 M8×1.25 6.7 6(20) 800 200 500 625 M10×1.5 8.5 7(21) 700 300 500 750 M12×1.25 10.7 M12×1.75 10.2 8(22) 630 280 500 875 M16×1.5 14.5 M16×2 13.9 9(23) 460 220 400 800 M20×1.5 18.5 M20×2.5 17.4 10(24) 365 180 320 800 M20×1.5 18.5 M24×3 21 11(25) 340 160 250 750 M30X3.5 26.5 250 125 200 700 M10×1 9 12(26) 700 180 500 500 NPT1/8″ 8.7 700 180 14 加工过。 2、加工螺纹的方法:先用中心钻加工底孔的中心孔,再钻底孔,然后对底孔倒角,最后攻丝。 公司为提高效率,在点孔时,点的稍大些,连倒角一起做了。 3、孔加工循环的选择,中心钻选用G82,底孔加工选用G81,倒角选用G82,螺纹若是右旋,选用G84。 4、孔加工循环的高度平面选择:a:Z向R高度:对G81、G82,为螺纹孔上表面以上3-5mm,对G84应大些,为10mm以上。 b:初始平面高度:为螺纹孔上表面以上20mm。公司选用100mm。 5、孔底面高度:对底孔钻,考虑到钻头角度以及孔是通孔的因素,取螺纹孔下表面下方0.3D底孔。 注:若攻不通孔螺纹,底孔深度:D钻=h有效+0.7D+0.3D底孔。 6、对钻头加工倒角,大小采用估算法,手轮进给倒角,切削一定深度后,退出游标卡尺测量,一般比螺纹孔径大3-4mm。 7、对丝锥:因为孔加工刀具对刀时是以钻尖或丝锥端中心为刀位点,攻螺纹时,由于丝锥切削部分有锥角,端部不能切出完整的牙型, 丝锥钻入深度应大于螺纹有效深度。一般可取:H丝=h有效+0.7D。D为螺纹大径。 8、中心钻应短,有良好的刚度。
CNC操作必知代码
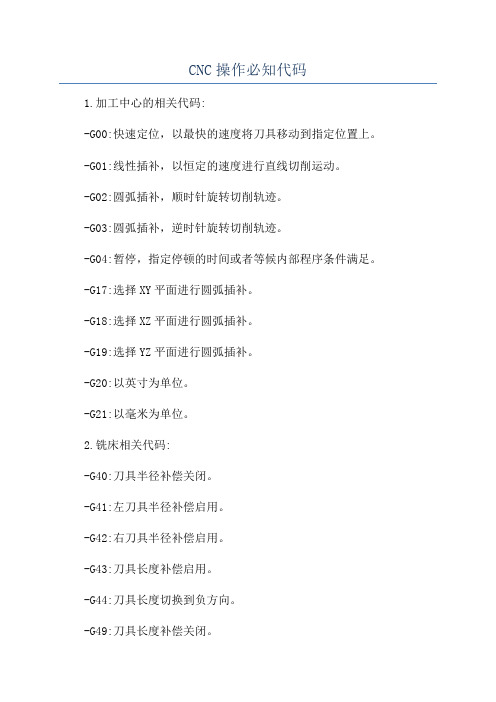
CNC操作必知代码1.加工中心的相关代码:-G00:快速定位,以最快的速度将刀具移动到指定位置上。
-G01:线性插补,以恒定的速度进行直线切削运动。
-G02:圆弧插补,顺时针旋转切削轨迹。
-G03:圆弧插补,逆时针旋转切削轨迹。
-G04:暂停,指定停顿的时间或者等候内部程序条件满足。
-G17:选择XY平面进行圆弧插补。
-G18:选择XZ平面进行圆弧插补。
-G19:选择YZ平面进行圆弧插补。
-G20:以英寸为单位。
-G21:以毫米为单位。
2.铣床相关代码:-G40:刀具半径补偿关闭。
-G41:左刀具半径补偿启用。
-G42:右刀具半径补偿启用。
-G43:刀具长度补偿启用。
-G44:刀具长度切换到负方向。
-G49:刀具长度补偿关闭。
-M04:主轴反转,以指定的转速开始反转。
-M05:主轴停止。
3.钻床相关代码:-G74:顺时针旋转,加工极坐标。
-G74.1:逆时针旋转,加工极坐标。
-G80:取消钻孔循环命令。
-G81:钻孔循环命令,指定孔深和钻孔进给速度。
-G82:钻孔循环命令,指定孔深、钻孔进给速度和进给暂停。
-G83:钻孔循环命令,指定孔深、钻孔进给速度和重复进给。
-G84:顺时针旋转,固定循环攻丝。
4.车床相关代码:-G00:快速定位,以最快的速度将车刀移动到指定位置上。
-G01:线性插补,以恒定的速度进行直线切削运动。
-G02:顺时针圆弧插补,使车刀沿指定轴旋转切削。
-G03:逆时针圆弧插补,使车刀沿指定轴旋转切削。
-G20:以英寸为单位。
-G21:以毫米为单位。
-M03:主轴正转,以指定的转速开始旋转。
-M05:主轴停止。
5.通用代码:-M00:程序停止,等待操作员干预。
-M08:启动冷却液。
-M09:关闭冷却液。
-M30:程序结束,重复循环开始。
-M98:调用子程序。
-M99:返回到主程序。
以上是一些常见的CNC操作必知代码,不同机床和控制系统可能会有所不同,需要根据具体机床的操作手册进行学习和了解。
CNC机床加工中的螺纹刀具的选择与应用

CNC机床加工中的螺纹刀具的选择与应用在CNC(计算机数控)机床加工过程中,螺纹刀具的选择和应用起到至关重要的作用。
螺纹刀具是专门用于加工螺纹的刀具,其选择和使用对于螺纹加工质量和效率有着直接影响。
本文将从螺纹刀具的类型、选择指南以及使用技巧等方面进行探讨,帮助读者更好地了解和应用螺纹刀具。
一、螺纹刀具的类型螺纹刀具根据其结构和用途可分为外螺纹刀具和内螺纹刀具。
1. 外螺纹刀具:外螺纹刀具主要用于加工螺纹外径,常见的有螺纹刀、丝锥和螺纹铣刀等。
螺纹刀主要用于车削外螺纹,适用于加工钢材、铸铁等常见材料。
丝锥则用于手工螺纹加工,适用于加工薄壁管材等;螺纹铣刀适用于铣削螺纹外径,精度较高。
2. 内螺纹刀具:内螺纹刀具主要用于加工螺纹内径,常见的有攻丝刀和挤丝刀等。
攻丝刀适用于精确的内螺纹加工,常用于机械加工中。
挤丝刀也用于内螺纹加工,适用于低硬度材料的加工。
二、螺纹刀具的选择指南在选择螺纹刀具时,需要根据加工要求、材料类型和刀具性能等因素进行综合考虑。
下面是一些选择螺纹刀具的指南:1. 加工要求:根据加工要求确定选择的螺纹刀具类型,如外螺纹刀具还是内螺纹刀具。
2. 材料类型:根据加工材料的硬度、脆性等特性选择合适的刀具材料。
对于硬度较高的材料,可以选择刚性较好的螺纹刀具。
3. 切削参数:确定切削参数,包括进给速度、转速等,以便选择适合的螺纹刀具。
4. 刀具性能:选择具有良好刀具质量、硬度、耐磨性和刀具寿命较长的螺纹刀具。
5. 成本控制:根据实际经济状况选择适合的螺纹刀具,综合考虑性价比和效益。
三、螺纹刀具的使用技巧正确使用螺纹刀具可提高切割效率和加工质量,下面是一些使用螺纹刀具的技巧:1. 加工前准备:检查刀具的整体情况,确保刀具无损坏和锈蚀。
调整好刀具的夹持装置,保证稳定和准确。
2. 切削参数设置:根据加工要求和材料特性,设定合适的切削参数,如进给速度、切割深度和转速等。
3. 冷却润滑:加工过程中应加足冷却润滑剂,保持刀具和工件的冷却状态,以提高切削效率和刀具寿命。
数控铣床加工中心编程及加工教学教案—攻丝加工

任务三 攻丝加工[教学目标]1.了解数控铣床螺纹加工的加工过程。
2.掌握数控铣床攻螺纹编程基础知识。
[教学重点]攻丝的编程指令及方法[教学难点]攻丝的编程指令及方法[教学过程]新课教学一、攻丝概述用丝锥在工件孔中切削出内螺纹的加工方法称为攻螺纹,也称攻丝。
攻丝加工的螺纹多为三角螺纹,为零件间连接结构,常用的攻丝加工的螺纹有:牙型角为60°的公制螺纹,也称为普通螺纹;牙型角为55°的英制螺纹;用于管道连接的英制管螺纹和圆锥管螺纹。
本项目主要涉及的攻丝加工的是公制内螺纹,熟悉有关螺纹结构尺寸、技术要求的常识,是学习攻丝工艺的重要基础。
普通螺纹的基本尺寸如下:(1)螺纹大径:d =D (螺纹大径的基本尺寸与公称直径相同)(2)中径: d2=D2=d -0.6495P(3)牙型高度:H =O.5413P(4)螺纹小径:d1=D1=d -1.0825P图5-13中M10—7H 的螺纹,为普通右旋内螺纹。
查表5-15得螺距P =1.5,其基本尺寸如下:螺纹大径:D =10;螺纹中径: D2=D -0.6495P =9.02;螺纹小径:D1=D -1.0825P =8.36;中径公差带代号7H )(0.0.2240+; 小径公差带代号7H )(0.3750+;牙型高度:H =O.5413P =0.82;螺纹有效长度:L =20.0;螺纹孔口倒角:C1.5。
二、丝锥的结构及分类1.丝锥的基本结构丝锥是加工内螺纹的一种常用刀具,其基本结构是一个轴向开槽的外螺纹,如图5-14所示。
螺纹部分可分为切削锥部分和校准部分。
切削锥磨出锥角,以便逐渐切去全部余量;校准部分有完整齿形,起修光、校准和导向作用。
工具尾部通过夹头和标准锥柄与机床主轴锥孔联接。
图5-14丝锥基本结构攻丝加工的实质是用丝锥进行成型加工, 丝锥的牙型、螺距、螺旋槽形状、倒角类型、丝锥的材料、切削的材料和刀套等因素,均会影响内螺纹孔的加工质量。
cnc攻丝

攻丝cnc攻牙转速进给比例--一格式如下;G84 Z- R- F-Z和R就不需要说了吧~`而进给F就有所不同了;有的是给一个螺距~~比如说M6的是1 ;M8的是1.25; M10的是1.5; M12的是1.75.我想我应该没有记错吧~好长时间没用了` 而有的是F=S之前给定了*螺距这两者是根据G94和G95的模态不一样而决定的~~至于切削丝锥和挤压丝锥;顾名思义;两者的加工形式不一样;一个是切削出来的;一个挤压出来的`~选择时候根据加工材料而定~~例:M3内螺纹的底孔:首先应知道M3的螺距是0.5计算方法: 3-0.5×1.0 8=2.46 ; 直径2.46不好找可以钻成直径2.5..简言之做M3的牙;用2.5的钻头钻孔;用M3的丝攻攻牙..每分钟进给G94、每转进给G95如果每分钟进给模式进给f=转速*牙距;每转进给;进给速度=牙距法拉克系统要指定刚性攻丝M29G284同步攻丝;转速X螺距=进给用加工中心对孔进行攻牙加工时;攻牙的进给速度不知道怎样设定如果有谁知道的将公式发上来谢谢例M6丝攻即牙距1.0 .....S50; .....; M29; G98 G84 Z-10. R2. F50 ; G80; ....主轴转速×螺距=进给量如楼上所说的;螺距是1时是S50 F50;如果螺距是1.5就是S50 F75..但通常还有个问题:最佳转速需通过试验得出;在试验时每改一次转速就得随着改一次进给量..不仅繁琐而且易出错..解决办法是让数控系统根据S值自动计算F值..即:S50 …… F#4119*1.5 假定螺距是1.5..程序中#4119是当前S值..这样只需要修改S值就行了..还有不能攻丝的加工中心那这加工中心真是浪费了..G00G90G54B0X125.-484.5+150.Y-40.+290.S1004M03G00G43Z200.H43M07M08M29G99G84X125.-484.5+150.Y-40.+290.Z-30.-27.R10.F2008.B4302X125.-484.5-150.Y-40.+290.B4301G80G00Z50.看看你们的参数对不对进给/转速是不是你所用丝锥的螺距...攻牙的参数: F进给速度等于S转速乘以P导程P等于螺距乘以螺旋线比如:做M6的单线螺孔;那首先要5的钻头先钻个底孔底孔就是螺孔的中径;F给600. 转速必须是600. 不然做出来的孔会乱牙M6的螺孔P就是1x1=1;我S给600.;F就必须是600.用上面的公式要使攻出的牙不乱参数必须要同步;只要用上面的那个公式就可以拉;至于上面的公式是这样来的;以后有机会在说.螺距不代表牙高啊;牙高有分为牙顶高;中径.和牙底高啊.而螺距只能代表螺纹的公称直径减去螺纹中径. 如M6;公称直径为6;螺距为1;中径就是5.至于用多大的钻头钻底孔;那要看是什么材料;一般比较硬的材料可以大0.1-0.2左右;不然容易断钻头.像铸铁类的可以大0.1;而那些铝件和胶版材料的话直接可以按照你上面列出的螺距来算.注:我干CNC四年了;基本上什么材料的东西都做过;有什么经验的问题可以问我;我很乐意交朋友*********************G03 X132. Y25.I2.J0.Z-2.F500.上面Z-2.为螺距如孔内功牙的话如: 孔深10mm 螺距 2mm 坐标为 0;0G91 X-5. 刀尖碰到工件G03 I5.J0.Z-2.F500. 螺旋下刀G01 X5. 回到0.Z-10G91 X-5.G03 I5.J0.Z-2.F500.G01 X5.以上必须用螺纹刀粒;长度大于8mm; 下刀深度必须与螺距成倍数;否则会乱牙用镗刀功外圆就是用G02 X- Y- I- Z- F-就可以拉数控机床程序编制的一般步骤和手工编程数控机床程序编制的一般步骤和手工编程数控机床程序编制又称数控编程是指编程者程序员或数控机床操作者根据零件图样和工艺文件的要求;编制出可在数控机床上运行以完成规定加工任务的一系列指令的过程..具体来说;数控编程是由分析零件图样和工艺要求开始到程序检验合格为止的全部过程..一般数控编程步骤如下1.分析零件图样和工艺要求分析零件图样和工艺要求的目的;是为了确定加工方法、制定加工计划;以及确认与生产组织有关的问题;此步骤的内容包括:1确定该零件应安排在哪类或哪台机床上进行加工..2采用何种装夹具或何种装卡位方法..3确定采用何种刀具或采用多少把刀进行加工..4确定加工路线;即选择对刀点、程序起点又称加工起点;加工起点常与对刀点重合、走刀路线、程序终点程序终点常与程序起点重合..5确定切削深度和宽度、进给速度、主轴转速等切削参数..6确定加工过程中是否需要提供冷却液、是否需要换刀、何时换刀等..2.数值计算根据零件图样几何尺寸;计算零件轮廓数据;或根据零件图样和走刀路线;计算刀具中心或刀尖运行轨迹数据..数值计算的最终目的是为了获得编程所需要的所有相关位置坐标数据..3.编写加工程序单在完成上述两个步骤之后;即可根据已确定的加工方案或计划及数值计算获得的数据;按照数控系统要求的程序格式和代码格式编写加工程序等..编程者除应了解所用数控机床及系统的功能、熟悉程序指令外;还应具备与机械加工有关的工艺知识;才能编制出正确、实用的加工程序..4.制作控制介质;输入程序信息程序单完成后;编程者或机床操作者可以通过CNC机床的操作面板;在EDIT方式下直接将程序信息键入CNC系统程序存储器中;也可以根据CNC系统输入、输出装置的不同;先将程序单的程序制作成或转移至某种控制介质上..控制介质大多采用穿孔带;也可以是磁带、磁盘等信息载体;利用穿孔带阅读机或磁带机、磁盘驱动器等输入输出装置;可将控制介质上的程序信息输入到CNC系统程序存储器中..5.程序检验编制好的程序;在正式用于生产加工前;必须进行程序运行检查..在某些情况下;还需做零件试加工检查..根据检查结果;对程序进行修改和调整;检查-修改-再检查-再修改……这往往要经过多次反复;直到获得完全满足加工要求的程序为止..上述编程步骤中的各项工作;主要由人工完成;这样的编程方式称为“手式编程”..在各机械制造行业中;均有大量仅由直线、圆弧等几何元素构成的形状并不复杂的零件需要加工..这些零件的数值计算较为简单;程序段数不多;程序检验也容易实现;因而可采用手工编程方式完成编程工作..由于手工编程不需要特别配置专门的编程设备;不同文化程度的人均可掌握和运用;因此在国内外;手工编程仍然是一种运用十分普遍的编程方法..在车床上加工螺纹螺纹车削刀具已经从全面改善车刀性能的涂层及材料等级方面所取得的共同进步中获益..此外;在螺纹车削刀片方面;人们进行了更好的结构设计;实现了更佳的切屑控制..尽管发生了这些变化;制造工程师们倾向花很少的时间来优化螺纹加工操作;将螺纹加工过程看成是一种无法不断取得进步的“黑匣子”..事实上;通过工程设计方式可以提高螺纹加工过程的效率..第一步应该是理解螺纹加工中一些基本的主题..为什么螺纹车削要求如此之高螺纹车削的要求要高于普通车削操作..切削力一般较高;螺纹刀片的切削端部半径较小;比较薄弱..在螺纹加工中;进给速度必须与螺纹的节距精确对应..对于节距为8螺纹/英寸tpi的情况;刀具必须以8转/英寸或者0.125英寸/转的进给速度前进..与普通车削应用其中典型的进给速度大约为0.012ipr相比;螺纹车削的进给速度要高出10倍..螺纹加工刀片刀尖处的作用力可能要高100~1;000倍..承受这种作用力的端部半径一般为0.015英寸;而常规车削刀片的半径为0.032英寸..对于螺纹加工刀片;该半径受许可的螺纹形状根部半径其大小由相关螺纹标准规定的严格限制..它还受所需要的切削动作限制;因为材料无法经受普通车削中的剪切过程;否则会发生螺纹变形..切削力较高和作用力聚集范围较窄导致的结果是:螺纹加工刀片要承受比一般车刀高得多的应力..部分与全轮廓刀片的比较部分轮廓刀片;有时候被称作“非加顶式”刀片;它在不给螺纹加顶或装牙顶的情况下切削螺纹沟槽..参见图1一把刀片可以产生一系列螺纹;直至最粗的节距-即每英寸螺纹数最少处为止-这是刀片端部半径强度许可的..这种端部半径设计得足够小;刀片可以加工各种节距..对于小节距;端部半径会显得尺寸过小..这意味着刀片必须穿透得深一些..例如;用一把部分轮廓刀片加工一个8tpi的螺纹需要螺纹深度为0.108英寸;而用完全轮廓刀片产生的相同螺纹则只需要0.81英寸的指定深度..因此;全轮廓刀片可以产生强度更高的螺纹..此外;全轮廓刀片加工出螺纹的操作可以少4道..多齿刀片多齿刀片连续地带有系列齿;任何齿在螺纹沟槽中切削的深度都要比它前面的一个齿更深..参见图2借助这些刀片;加工一个螺纹所需要的操作道数可以减少80%..刀具寿命要远远长于单顶尖刀片;因为最终的齿只加工某个给定螺纹一半或三分之一的金属..但是;由于它们存在较高的切削力;因此不提倡将这些刀片用于薄壁零件的加工-因为可能会产生颤振..此外;用这些刀片加工工件的结构必须具有足够的螺纹间隙;以便所有齿退出切削..每道进给每道的切削深度;或者说每道进给;在螺纹加工中是非常关键的..每个相连的操作道都要啮合刀片切削刃较大部分..如果每道进给是恒定的不推荐采用这种方式;则切削力和金属去除率从上一道到下一道会剧烈增加..例如;在采用恒定的0.010英寸进给/道的速度加工一个60度螺纹形状时;第二道去除的材料为第一道的3倍..与随后每道操作一样;去除的金属量连续成指数上升..为了避免这种切除量增加并维持比较现实的切削力;切深应该随着各道操作而减少..横切进给法至少有四种横切进给法..参见图3很少有人发现这些方法中某种方法对螺纹加工操作有效性的冲击到底有多大..径向横切进给尽管这可能是加工螺纹最常用的方法;但确是最不提倡采用的一种方法..由于刀具是径向进给的与工件中心线垂直;因此金属从螺纹齿腹两侧去除;从而产生V形切屑..这种切屑很难断裂;因此切屑流动是一个问题..此外;由于刀片端部两侧要承受较高的热和压力;因此刀具寿命通常比其他横切进给法中要短..齿腹横切进给在这种方法中;横切方向与螺纹齿腹之一平行;这一般意味着刀具沿30度直线进给..切屑与普通车削中产生的类似..参见图4..与径向横切相比;这种方法中产生的切屑比较容易成形;并且易于从切削刃中排出;热扩散性更好..但是;在这种横切进给法中;刀片后缘会摩擦齿腹而不会进行切削..这样会烧伤螺纹;导致表面粗糙度很差;甚至发生颤振现象..修改的齿腹横切进给推荐采用这种方法与齿腹横切进给法类似;不同的是横切角度小于螺纹角度-即小于30度..这种方法保留了齿腹横切法的优点;同时又避免了刀片后缘带来的问题..291/2度的横切角一般会产生最佳结果;但在现实操作中;25~291/2度范围内的横切角都是可以接受的..交替式齿腹横切进给这种方法沿两个螺纹齿腹交替进给;因此它采用刀片的两个齿腹来形成螺纹..这种方法可以保证较长的刀具寿命;因为使用的是刀片端部两侧..但也可能导致切屑流问题-这种问题可能影响表面粗糙度和刀具寿命..这种方法通常只用于大节距和英制梯形及斜四边形螺纹等..间隙角补偿某些螺纹加工刀片和刀夹系统具有这样的能力;即通过改变螺旋角而按切削的方向精确地倾斜刀片..这种特征可以加工出较高质量的螺纹;因为它可以防止刀片摩擦螺纹的齿腹..它还可以提供较长的刀具寿命;因为切削力均匀分布在切削刃的整个长度上..没有按这种方式倾斜的刀片-让切削刃与工件中心线平行的方式-会在刀片的前刃和后刃下形成不相等的间隙角..参见图5特别是对比较粗的节距;这种不等性可能会引起齿腹发生摩擦..可调式系统允许通过刀夹头定位一般采用填隙片而倾斜刀片的角度..精确调节会获得类似的前刃和后刃角;确保刃的磨损进展均匀..微型化和专用化现在市面上已经推出对直径大约为0.3英寸的孔进行内螺纹车削加工的转位刀片式刀具..通过车削方式将这样的小孔加工出螺纹具有很多优点..所加工的螺纹质量通常比较高;刀片结构允许切屑流出孔而很少损伤螺纹;且可以对刀片进行分度;因此刀具成本较低..用于这些应用场合的硬质合金的等级一般是允许以较低的表面速度进行加工的那种..对于在小孔中进行内螺纹加工;机床方面所存在的限制一般是低表面速度以外的其他问题..人们取得的技术进步已经扩大了螺纹车刀的应用范围;而进入到小孔内螺纹车削加工就是其中一个实例..但是;尽管扩大了标准刀具的应用范围;制造厂家仍然要遇到特定的问题;这就为定制刀具的存在创造了空间..参见图6与刀具供应商合作开发的特殊刀具是在针对特定作业而搜索正确螺纹加工刀具时不可忽略的一种选项..谈谈操作数控机床的经验数控车床基本坐标关系及几种对刀方法比较在数控车床的操作与编程过程中;弄清楚基本坐标关系和对刀原理是两个非常重要的环节..这对我们更好地理解机床的加工原理;以及在处理加工过程中修改尺寸偏差有很大的帮助..一、基本坐标关系一般来讲;通常使用的有两个坐标系:一个是机械坐标系;另外一个是工件坐标系;也叫做程序坐标系..两者之间的关系可用图1来表示..图1 机械坐标系与工件坐标系的关系在机床的机械坐标系中设有一个固定的参考点假设为X;Z..这个参考点的作用主要是用来给机床本身一个定位..因为每次开机后无论刀架停留在哪个位置;系统都把当前位置设定为0;0;这样势必造成基准的不统一;所以每次开机的第一步操作为参考点回归有的称为回零点;也就是通过确定X;Z来确定原点0;0..为了计算和编程方便;我们通常将程序原点设定在工件右端面的回转中心上;尽量使编程基准与设计、装配基准重合..机械坐标系是机床唯一的基准;所以必须要弄清楚程序原点在机械坐标系中的位置..这通常在接下来的对刀过程中完成..二、对刀方法1. 试切法对刀试切法对刀是实际中应用的最多的一种对刀方法..下面以采用MITSUBISHI 50L数控系统的RFCZ12车床为例;来介绍具体操作方法..工件和刀具装夹完毕;驱动主轴旋转;移动刀架至工件试切一段外圆..然后保持X坐标不变移动刀具远离工件;测量出该段外圆的直径..将其输入到相应的刀具参数中的刀长中;系统会自动用刀具当前X坐标减去试切出的那段外圆直径;即得到工件坐标系X原点的位置..再移动刀具试切工件一端端面;在相应刀具参数中的刀宽中输入Z0;系统会自动将此时刀具的Z坐标减去刚才输入的数值;即得工件坐标系Z原点的位置;参见图2..例如;2#刀刀架在X为150.0车出的外圆直径为25.0;那么使用该把刀具切削时的程序原点X值为150.0-25.0=125.0;刀架在Z为180.0时切的端面为0;那么使用该把刀具切削时的程序原点Z值为180.0-0=180.0..分别将125.0;180.0存入到2#刀具参数刀长中的X与Z中;在程序中使用T0202就可以成功建立出工件坐标系..事实上;找工件原点在机械坐标系中的位置并不是求该点的实际位置;而是找刀尖点到达0;0时刀架的位置..采用这种方法对刀一般不使用标准刀;在加工之前需要将所要用刀的刀具全部都对好..图2试切法对刀2. 对刀仪自动对刀现在很多车床上都装备了对刀仪;使用对刀仪对刀可免去测量时产生的误差;大大提高对刀精度..由于使用对刀仪可以自动计算各把刀的刀长与刀宽的差值;并将其存入系统中;在加工另外的零件的时候就只需要对标准刀;这样就大大节约了时间..需要注意的是使用对刀仪对刀一般都设有标准刀具;在对刀的时候先对标准刀..下面以采用FANUC 0T系统的倭国WASINO LJ-10MC车削中心为例介绍对刀仪工作原理及使用方法..对刀仪工作原理如图3所示..刀尖随刀架向已设定好位置的对刀仪位置检测点移动并与之接触;直到内部电路接通发出电信号通常我们可以听到嘀嘀声并且有指示灯显示..在2#刀尖接触到a点时将刀具所在点的X坐标存入到图2所示G02的X中;将刀尖接触到b点时刀具所在点的Z坐标存入到G02的Z中..其他刀具的对刀按照相同的方法操作..图3 对刀仪工作原理事实上;在上一步的操作中只对好了X的零点以及该刀具相对于标准刀在X方向与Z方向的差值;在更换工件加工时再对Z零点即可..由于对刀仪在机械坐标系中的位置总是一定的;所以在更换工件后;只需要用标准刀对Z坐标原点就可以了..操作时提起Z轴功能测量按钮“Z-axis shift measure”;CRT出现如图4所示的界面..图4 对刀数值界面手动移动刀架的X、Z轴;使标准刀具接近工件Z向的右端面;试切工件端面;按下“POSITION RECORDER”按钮;系统会自动记录刀具切削点在工件坐标系中Z向的位置;并将其他刀具与标准刀在Z方向的差值与这个值相加从而得到相应刀具的Z原点;其数值显示在WORK SHIFT工作画面上;如图5所示..图5 WORK SHIFT工作界面三、小结以上根据笔者在多年的数控机床编程与操作中积累的一些经验与体会;介绍了在数控车床操作中容易犯错的几个地方;所述内容皆经过笔者的实际操作验证..Fanuc系统数控车床对刀及编程指令介绍Fanuc系统数控车床设置工件零点常用方法1. 直接用刀具试切对刀1.用外园车刀先试车一外园;记住当前X坐标;测量外园直径后;用X坐标减外园直径;所的值输入offset界面的几何形状X值里..2.用外园车刀先试车一外园端面;记住当前Z坐标;输入offset界面的几何形状Z值里..2. 用G50设置工件零点1.用外园车刀先试车一外园;测量外园直径后;把刀沿Z轴正方向退点;切端面到中心..2.选择MDI方式;输入G50 X0 Z0;启动START键;把当前点设为零点..3.选择MDI方式;输入G0 X150 Z150 ;使刀具离开工件进刀加工..4.这时程序开头:G50 X150 Z150 ……...5.注意:用G50 X150 Z150;你起点和终点必须一致即X150 Z150;这样才能保证重复加工不乱刀..6.如用第二参考点G30;即能保证重复加工不乱刀;这时程序开头 G30 U0 W0 G50 X150 Z1507.在FANUC系统里;第二参考点的位置在参数里设置;在Yhcnc软件里;按鼠标右键出现对话框;按鼠标左键确认即可..3. 用工件移设置工件零点1.在FANUC0-TD系统的Offset里;有一工件移界面;可输入零点偏移值..2.用外园车刀先试切工件端面;这时Z坐标的位置如:Z200;直接输入到偏移值里..3.选择“Ref”回参考点方式;按X、Z轴回参考点;这时工件零点坐标系即建立..4.注意:这个零点一直保持;只有从新设置偏移值Z0;才清除..4. 用G54-G59设置工件零点1.用外园车刀先试车一外园;测量外园直径后;把刀沿Z轴正方向退点;切端面到中心..2.把当前的X和Z轴坐标直接输入到G54----G59里;程序直接调用如:G54X50Z50……..3.注意:可用G53指令清除G54-----G59工件坐标系..Fanuc系统数控车床常用固定循环G70-G80祥解1. 外园粗车固定循环G71如果在下图用程序决定A至A’至B的精加工形状;用△d切削深度车掉指定的区域;留精加工预留量△u/2及△w..G71U△dReG71PnsQnfU△uW△wFfSsTtNns…………….F__从序号ns至nf的程序段;指定A及B间的移动指令...S__.T__Nnf……△d:切削深度半径指定不指定正负符号..切削方向依照AA’的方向决定;在另一个值指定前不会改变..FANUC系统参数NO.0717指定..e:退刀行程本指定是状态指定;在另一个值指定前不会改变..FANUC系统参数NO.0718指定..ns:精加工形状程序的第一个段号..nf:精加工形状程序的最后一个段号..△u:X方向精加工预留量的距离及方向..直径/半径△w: Z方向精加工预留量的距离及方向..2. 端面车削固定循环G72如下图所示;除了是平行于X轴外;本循环与G71相同..G72W△dReG72PnsQnfU△uW△wFfSsTt△t;e;ns;nf; △u; △w;f;s及t的含义与G71相同..3. 成型加工复式循环G73本功能用于重复切削一个逐渐变换的固定形式;用本循环;可有效的切削一个用粗加工段造或铸造等方式已经加工成型的工件.程序指令的形式如下:A A’ BG73U△iW△kRdG73PnsQnfU△uW△wFfSsTtNns…………………沿A A’ B的程序段号Nnf………△i:X轴方向退刀距离半径指定; FANUC系统参数NO.0719指定..△k: Z轴方向退刀距离半径指定; FANUC系统参数NO.0720指定..d:分割次数这个值与粗加工重复次数相同;FANUC系统参数NO.0719指定..ns: 精加工形状程序的第一个段号..nf:精加工形状程序的最后一个段号..△u:X方向精加工预留量的距离及方向..直径/半径△w: Z方向精加工预留量的距离及方向..4. 精加工循环G70用G71、G72或G73粗车削后;G70精车削..G70 PnsQnfns:精加工形状程序的第一个段号..nf:精加工形状程序的最后一个段号..5. 端面啄式钻孔循环G74如下图所示在本循环可处理断削;如果省略XU及P;结果只在Z轴操作;用于钻孔..G74 Re;G74 Xu Zw P△i Q△k R△d Ffe:后退量本指定是状态指定;在另一个值指定前不会改变..FANUC系统参数NO.0722指定..x:B点的X坐标u:从a至b增量z:c点的Z坐标w:从A至C增量△i:X方向的移动量△k:Z方向的移动量△d:在切削底部的刀具退刀量..△d的符号一定是+..但是;如果XU及△I省略;可用所要的正负符号指定刀具退刀量..f:进给率:6. 外经/内径啄式钻孔循环G75以下指令操作如下图所示;除X用Z代替外与G74相同;在本循环可处理断削;可在X轴割槽及X轴啄式钻孔..G75 Re;G75 Xu Zw P△i Q△k R△d Ff7. 螺纹切削循环G76G76 Pmra Q△dmin RdG76 Xu Zw Ri Pk Q△d Ffm:精加工重复次数1至99本指定是状态指定;在另一个值指定前不会改变..FANUC系统参数NO.0723指定..r:到角量本指定是状态指定;在另一个值指定前不会改变..FANUC系统参数NO.0109指定..a:刀尖角度:可选择80度、60度、55度、30度、29度、0度;用2位数指定..本指定是状态指定;在另一个值指定前不会改变..FANUC系统参数NO.0724指定..如:P02/m、12/r、60/a △dmin:最小切削深度本指定是状态指定;在另一个值指定前不会改变..FANUC系统参数NO.0726指定..i:螺纹部分的半径差如果i=0;可作一般直线螺纹切削..k:螺纹高度这个值在X轴方向用半径值指定..△d:第一次的切削深度半径值l:螺纹导程与G32Fanuc系统数控铣床常用固定循环祥解1. 高速啄式深孔钻循环G73指令格式:G73 X---Y---Z---R---Q---P---F---K--- 加工方式:进给孔底快速退刀2. 攻左牙循环G74指令格式:G74 X---Y---Z---R---Q---P---F---K--- 加工方式:进给孔底主轴暂停正转快速退刀3. 精镗孔循环G76指令格式:G76 X---Y---Z---R---Q---P---F---K--- 加工方式:进给孔底主轴定位停止快速退刀4. 钻空循环;点钻空循环G81指令格式:G81 X---Y---Z---R---F---K---加工方式:进给孔底快速退刀5. 钻孔循环;反镗孔循环G82指令格式:G82 X---Y---Z---R---F---K---加工方式:进给孔底快速退刀6. 啄式钻空循环G83指令格式:G83 X---Y---Z---Q---R---F---加工方式:中间进给孔底快速退刀7. 攻牙循环G84指令格式:G84 X---Y---Z---R---P---F---K---加工方式:进给孔底主轴反转快速退刀8. 镗孔循环G85指令格式:G85 X---Y---Z---R---F---K---加工方式:中间进给孔底快速退刀9. 镗孔循环G86指令格式:G86 X---Y---Z---R---F---K---加工方式:进给孔底主轴停止快速退刀10. 反镗孔循环G87指令格式:G87 X---Y---Z---R---F---K---加工方式:进给孔底主轴正转快速退刀11. 镗孔循环G88指令格式:G88 X---Y---Z---R---F---K---加工方式:进给孔底暂停; 主轴停止快速退刀12. 镗孔循环G89指令格式:G89 X---Y---Z---R---F---K---加工方式:进给孔底暂停快速退刀13. 取消固定循环G80指令格式:G80。
机床CNC 基础知识(FANUC)

机床 CNC 基础知识北京发那科机电有限公司 王玉琪20061此文是本人对 GM(中国厂)培训时的讲义。
目的是对初学者对 CNC 有基本的综合概念。
以便于更深入地学习诸如:加工编程, PMC 和系统维修等课程。
2机床 CNC 基础知识一. CNC 机床与 CNC 系统 CNC 的含义是计算机数值控制。
1. CNC 机床 ⑴.金属切削用 孔加工、攻丝、镗削、铣削、车削、切螺纹、切平面、轮廓加工、平面磨削、外圆磨 削、内圆磨削等。
⑵.线电极切割机。
⑶.冲床、步冲、冲压、金属成型、弯管等机床。
⑷.产业机器人。
⑸.注塑机。
⑹.检测、测量机。
⑺.木工机械。
⑻.特殊材料加工机械:如加工石材、玻璃、发射性矿料等。
⑼.特种加工机械 激光加工机、气体切割机、焊接机、制图机、印刷机等。
随着电子技术和计算机技术以及 IT 技术的发展,目前,这些机床与加工设备都可用数值计算 机用数值数据进行控制,称为 CNC 控制。
下图是一台金属加工机床------立式加工中心的一般结构。
32. CNC 系统 CNC 系统的含义是计算机数值控制系统。
下图是一台 CNC 系统的基本配置图。
FANUC LTDSeries 0i-C以太网 10 base T/100 base TX系统配置Internet 7.2 “ LCD/MDI(单色) 8.4 “ LCD /MDI(彩色) 系统在LCD后面 PC αi 伺服放大器FSSBαi 主轴电机FANUC I/O Link DI/DO 1024/1024αis 伺服电机操作面板I/O 模块I/O 单元βis 伺服电机 I/O Link βi 伺服放大器FS0 i - 6CNC 系统的基本配置 机床的 CNC 控制是集成多学科的综合控制技术。
上图是一台典型的 CNC 控制系统。
从图中可见,一台 CNC 系统包括:⑴.CNC 控制单元(数 值控制器部分) 。
⑵.伺服驱动单元和进给伺服电动机。
常用CNC机床钻孔攻丝切削参数

常用CNC机床钻孔攻丝切削参数1. 切削速度(Cutting Speed)切削速度指的是工件表面上一点在单位时间内被切除的长度。
对于钻孔操作来说,切削速度可以用来控制钻头进给速度,通常以每分钟一些距离(mm/min)或每转一些距离(mm/rev)表示。
切削速度的选择应根据工件材料和刀具的硬度来确定。
2. 进给量(Feed Rate)进给量指的是工件和刀具之间相对运动过程中,刀具在单位时间内沿工件轴向移动的距离。
对于钻孔操作来说,进给量决定了钻孔的深度和速度,通常以每分钟一些距离(mm/min)表示。
进给量的选择应根据工件材料、刀具类型和加工要求来确定。
3. 主轴转速(Spindle Speed)主轴转速指的是主轴每分钟旋转的圈数,通常以转/分钟(rpm)表示。
主轴转速的选择应根据刀具直径、材料硬度和加工要求等因素来确定。
较小的刀具直径可选择较高的主轴转速,而大直径刀具则需要较低的转速。
4. 切削深度(Depth of Cut)切削深度指的是刀具进入工件的深度。
对于钻孔操作来说,切削深度由工件材料和创allenge参数所限制。
在进行钻孔操作时,应确保切削深度不超过钻头长度的80%,以避免过度切削,造成负载过大和刀具损坏。
5. 降刀速度(Plunge Rate)降刀速度指的是刀具从工件表面向下进入工件的速度。
对于钻孔操作来说,降刀速度通常选择较低的数值,以避免切削过快而导致刀具容易折断。
6. 切削液(Cutting Fluid)切削液是进行钻孔、攻丝和切削等操作时必不可少的润滑剂。
切削液的使用可以减少摩擦、冷却刀具、切削表面以及清洁切屑等功能,从而提高加工质量和刀具寿命。
除了上述参数,还有一些与具体机床和刀具相关的参数也需要考虑,例如进给速度、切削角度、切削力等。
在选择这些参数时,需要根据具体的工件和加工要求来进行调整,以保证加工质量和生产效率。
总结起来,CNC机床钻孔、攻丝和切削参数的选择应考虑工件材料、刀具类型、加工要求等因素,并结合实际应用进行合理调整。
g84攻丝循环编程实例

g84攻丝循环编程实例本文将介绍G84攻丝循环编程的实例。
G84攻丝循环编程是一种常用的CNC加工程序,适用于攻丝、螺纹加工等领域。
它可以循环执行攻丝操作,从而提高加工效率和加工精度。
先来了解一下G84攻丝循环编程的语法格式。
G84攻丝循环编程需要在G代码中加入以下指令:G84 Xx Yy Zz Rr Pp Ff其中,X、Y、Z分别代表攻丝的起点坐标;R代表刀具半径;P 代表攻丝深度;F代表进给速度。
下面是一个G84攻丝循环编程的实例:O0001 (攻丝程序)G21 (设置为公制系统)G90 (设置为绝对编程)G54 (选择工件坐标系)G00 X20 Y20 Z10 (刀具移动到攻丝起点)M03 S500 (主轴正转,转速为500转/分)G84 X30 Y30 Z-10 R5 P15 F50 (攻丝循环开始)X50 Y50 Z-10 (攻丝结束,返回起点)G80 (攻丝循环结束)M05 (主轴停止)M30 (程序结束)在这个实例中,我们定义了攻丝的起点坐标为X20 Y20 Z10,结束坐标为X50 Y50 Z-10,刀具半径为5,攻丝深度为15,进给速度为50。
程序执行完毕后,刀具移动回攻丝起点,攻丝循环结束。
需要注意的是,G84攻丝循环编程需要根据实际情况进行调整,包括攻丝深度、进给速度、刀具半径等,以确保加工精度和效率。
同时,也需要注意安全措施,避免刀具碰撞或其他意外情况发生。
总的来说,G84攻丝循环编程是一种常用的CNC加工程序,可以提高加工效率和加工精度。
如果您需要进行攻丝、螺纹加工等领域的加工,可以尝试使用G84攻丝循环编程。
CNC数控常用基本指令

CNC基本指令●G00---定位﹕在绝对命令下将刀具快速移动到工件坐标系指定的位置﹔在增量命令下将刀具快速移动到仅偏离当前位置指定的值的位置。
●格式﹕G00 IP—●G01---线性插补﹕使刀具沿直线或斜线移动。
●格式﹕G01 IP—F--●G02.G03---顺时针(CW),逆时针(CCW)圆弧插补﹕可以在已指定的平面上使刀具沿一圆弧移动。
●格式﹕G02.G03 X-Y-R-(I-J-)F-●G04---暂停﹐准确停止﹕加工的过程中进给暂时停止﹐主轴继续运转。
●格式﹕G04X-(Y-或Z-)●G05---高速遥控缓冲器●格式﹕G05.1 Q1:AI先行控制方式接通◆G05.1 Q1:AI先行控制方式断开●G07.1---圆柱插补﹕●格式﹕G07.1 IP r: 开始圆弧插补方式◆G07.1 IP 0 取消圆弧插补方式●G08---先行控制﹕●格式﹕G08 P1 ﹕先行控制方式接通◆G08 P0 ﹕先行控制方式断开●G09---准确停止﹕刀具在程序块的终点减速﹐在进行到位检查后执行下一程序块。
(只有指定的程序块有效)●格式﹕G09 G01(G02或G03) IP_●G10---用程序改变偏置值﹕通过改变一个外部原点偏置值来改变在G54~●G59中指定的6个坐标系。
●格式﹕G10 L2 Pp IP-﹔参数输入方式设定◆G11﹔参数输入方式取消●P=0﹕指定外部工件原点偏置值●P=1~6﹕指定相对于工件坐标系1~6的工件原点偏置值●IP-:对一个绝对命令(G90)﹐每个轴的工件原点偏置值。
对一个增量命令(G91)﹐该值要加到每个轴原设置的工件原点偏置值上。
●G15﹐G16---极坐标输入﹕可以在极坐标(半径和角度)上输入终点坐标值。
●格式﹕G11 G22 G16﹔开始极坐标命令◆G00 IP-; 极坐标命令◆G15﹔取消极坐标命令◆G11﹕选择极坐标命令的平面(G17,G18,G19)◆G22﹕选择极坐标命令的中心(G90,G91)⏹G90时工件坐标系的原点为极坐标的中心⏹G91时当前位置为极坐标的中心◆IP-: 构成极坐标命令的平面的轴地址和命令值⏹平面的第一轴﹕指定极坐标的半径⏹平面的第二轴﹕指定极坐标的角度●G17,G18,G19---平面选择﹕通过G码来选择进行圆弧插补﹐刀具半径补偿﹐坐标旋转的平面以及进行开孔的平面。
cnc加工中心常用刀具的叫法,你知道多少?你都是怎么个叫法?

cnc加工中心常用刀具的叫法,你知道多少?你都是怎么个叫法?cnc加工中心常用刀具是CNC机床上完成工件加工所必备的刀具,主要由刀片、刀杆和刀柄组成,它们之间的组合方式和性能参数会让CNC机床的加工性能有质的提升。
CNC加工中心常用刀具的叫法:1、平刀,是CNC加工中心常用的刀具,它具有切削效率高、切口平整、切削力小等特点,可以用于铝合金、铁合金、钢材等实际加工中的平面、槽、沟、圆柱面等面的加工。
2、立铣刀,是CNC加工中心常用的刀具,它具有切削效率高、切口平整、切削力小等特点,可以用于立面、斜面、圆柱面、槽、沟等实际加工中的铣削、圆弧铣削、凹口加工等工艺。
3、钻头,是CNC加工中心常用的刀具,它具有切削效率高、切削力小等特点,可以用于实际加工中的钻孔、攻丝等工艺。
4、铰刀,是CNC加工中心常用的刀具,它具有切削效率高、切削力小等特点,可以用于实际加工中的开槽、开孔、打孔、扩孔等工艺。
5、铣刀,是CNC加工中心常用的刀具,它具有切削效率高、切口平整、切削力小等特点,可以用于实际加工中的铣削、拉削、抛光等工艺。
6、刨刀,是CNC加工中心常用的刀具,它具有加工精度高、切削力小等特点,可以用于实际加工中的刨削、镗削、拉削等工艺。
7、刃具,是CNC加工中心常用的刀具,它具有切削效率高、切削力小等特点,可以用于实际加工中的切削、攻丝、削圆等工艺。
以上就是CNC加工中心常用刀具的叫法,它们在CNC加工中心中的应用非常广泛,能够提高CNC机床的加工性能,为工件加工提供最佳的加工解决方案。
CNC加工中心常用刀具的叫法不仅要了解它们的名称,还要了解它们的性能参数和结构特点,根据不同的加工要求选择合适的刀具,以满足工件加工的要求,可以达到更好的加工效果。
CNC加工中心常用刀具的正确使用,可以更好地发挥它们的功效,同时还能够延长刀具的使用寿命,为CNC机床的加工过程提供更好的加工保证。
兄弟公司的数控钻孔攻丝中心介绍
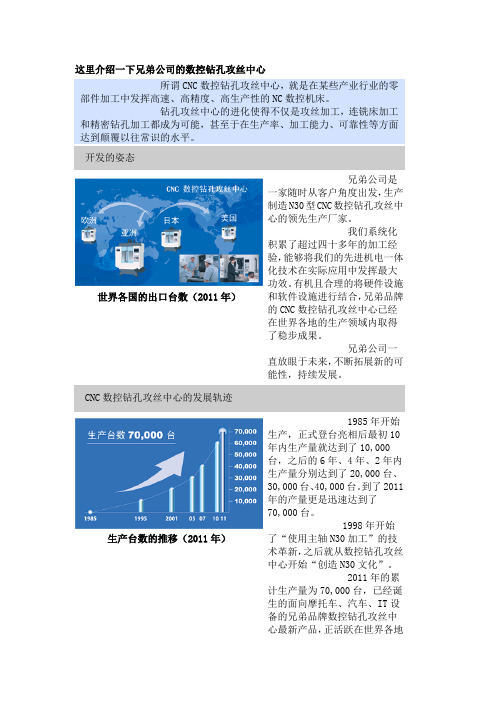
这里介绍一下兄弟公司的数控钻孔攻丝中心所谓CNC 数控钻孔攻丝中心,就是在某些产业行业的零部件加工中发挥高速、高精度、高生产性的NC 数控机床。
钻孔攻丝中心的进化使得不仅是攻丝加工,连铣床加工和精密钻孔加工都成为可能,甚至于在生产率、加工能力、可靠性等方面达到颠覆以往常识的水平。
开发的姿态世界各国的出口台数(2011年)兄弟公司是一家随时从客户角度出发,生产制造N30型CNC 数控钻孔攻丝中心的领先生产厂家。
我们系统化积累了超过四十多年的加工经验,能够将我们的先进机电一体化技术在实际应用中发挥最大功效。
有机且合理的将硬件设施和软件设施进行结合,兄弟品牌的CNC 数控钻孔攻丝中心已经在世界各地的生产领域内取得了稳步成果。
兄弟公司一直放眼于未来,不断拓展新的可能性,持续发展。
生产台数的推移(2011年)1985年开始生产,正式登台亮相后最初10年内生产量就达到了10,000台,之后的6年、4年、2年内生产量分别达到了20,000台、30,000台、40,000台。
到了2011年的产量更是迅速达到了70,000台。
1998年开始了“使用主轴N30加工”的技术革新,之后就从数控钻孔攻丝中心开始“创造N30文化”。
2011年的累计生产量为70,000台,已经诞生的面向摩托车、汽车、IT 设备的兄弟品牌数控钻孔攻丝中心最新产品,正活跃在世界各地的生产领域内。
主轴N30的优势变更为主轴N30后的优势体现事例原先只能用N30以上机床加工的中型部品,现在也能用N30机床进行加工了。
除了攻丝以外,也能对应钻孔和铣床加工。
通过从大型机床到N30机床的转变,可以减小设备的放置面积、降低耗电量、缩短加工时间,同时还有利于减少二氧化碳的排放量。
*优势体现事例的加工条件: M6P1.0 深12mm 40孔主轴转速2000min-1的情况。
配备本公司自行开发的NC兄弟品牌的数控钻孔攻丝中心配备了本公司自行开发的NC装置。
通过机电一体化的开发,进行能最大程度发挥机械性能的最优化NC控制。
cnc法兰克系统G19面攻牙指令

cnc法兰克系统G19面攻牙指令
在法兰克系统G19面的前一程序段指令M29Sxxxx;则机床进刚性攻丝模态。
NC执行到该指令时,主轴停止,然后主轴正转指示灯亮,表示进入刚性攻丝模态,其后的G74或G84循环被称为法兰克系统G19面,由于刚性攻丝循环中,主轴转速和Z轴的进给严格成比例同步,因此可以使用刚性夹持的丝锥进行螺纹孔的加工,并且还可以提高螺纹孔的加工速度,提高加工效率。
使用G80和01组G代码都可以解除法兰克系统G19面,另外复位操作也可以解除法兰克系统G19模面。
使用刚性攻丝循环需注意以下事项:
(1)G74或G84中指令的F值与M29程序段中指令的S值的比值(F/S)即为螺纹孔的螺距值。
(2)Sxxxx必须小于0617号参数指定的值,否则执行固定循环指令时出现编程报警。
(3)F值必须小于切削进给的上限值4000mm/min即参数0527的规定值,否则出现编程报警。
(4)在M29指令和固定循环的G指令之间不能有S指令或任何坐标运动指令。
(5)不能在攻丝循环模态下指令M29。
(6)不能在取消刚性攻丝模态后的第一个程序段中执行S指令。
(7)不要在试运行状态下执行刚性攻丝指令。
cnc加工中心常用的几种螺纹加工方法

螺纹加工是cnc加工中心非常重要的应用之一,螺纹的加工质量和效率将直接影响零件的加工质量及加工中心的生产效率。
随着cnc加工中心性能的提高及切削刀具的改进,螺纹加工的方法也在不断改进,螺纹加工的精度和效率也在逐渐提高。
为了使工艺人员能够在加工中合理选择螺纹加工方法,提高生产效率,避免质量事故,现将在实际中cnc加工中心常用的几种螺纹加工方法总结如下:1. 丝锥加工法1.1 丝锥加工的分类及特点采用丝锥加工螺纹孔是*常用的加工方法,它主要适用于直径较小(D<30),孔位置精度要求不高的螺纹孔。
在20世纪80年代,螺纹孔均采用柔性攻丝方法,即采用柔性攻丝夹头夹持丝锥,攻丝夹头可做轴向补偿,补偿机床轴向进给与主轴转速不同步造成的进给误差,保证正确螺距。
柔性攻丝夹头结构复杂,成本较高,容易损坏,加工效率较低。
近年来,cnc加工中心的性能逐步提高,刚性攻丝功能成为cnc加工中心的基本配置。
因此,刚性攻丝成为目前螺纹加工的主要方法。
即用刚性弹簧夹头夹持丝锥,主轴进给与主轴转速由机床控制保持一致。
弹簧夹头相对于柔性攻丝夹头来说,结构简单,价格便宜,用途广泛,除夹持丝锥外,还可夹持立铣刀、钻头等刀具,可以降低刀具成本。
同时,采用刚性攻丝,可以进行高速切削,提高加工中心使用效率,降低制造成本。
1.2 攻丝前螺纹底孔的确定螺纹底孔的加工对于丝锥的寿命、螺纹加工的质量等方面有较大影响。
通常,螺纹底孔钻头直径选择接近螺纹底孔直径公差的上限,例如,M8螺纹孔的底孔直径为Ф6.7+0.27mm,选择钻头直径为Ф6.9mm。
这样,可减少丝锥的加工余量,降低丝锥的负荷,提高丝锥的使用寿命。
1.3 丝锥的选择选择丝锥时,首先,必须按照所加工的材料选择相应的丝锥,刀具公司根据加工材料的不同生产不同型号的丝锥,选择时要特别注意。
因为丝锥相对于铣刀、镗刀来说,对被加工材料非常敏感。
例如,用加工铸铁的丝锥来加工铝件,容易造成螺纹掉牙、乱扣甚至丝锥折断,导致工件报废。
攻丝基础知识,总结很全面

攻丝基础知识,总结很全⾯来源:⼑具界丝锥是加⼯各种中、⼩尺⼨内螺纹的⼑具,它结构简单,使⽤⽅便,既可⼿⼯操作,也可以在机床上⼯作,在⽣产中应⽤得⾮常⼴泛。
攻丝的相关知识有哪些呢?本⽂总结很全⾯。
01什么是攻丝攻丝是⽤丝锥在⼯件的孔内部切削出内螺纹。
(1)决定丝锥性能的因素包括:⼯件材料切削速度切削刃材料⼑柄丝锥形式孔的尺⼨攻丝⼑柄切削液孔深(2)螺距:螺纹上相邻两⽛在中径线上对应两点间的轴向距离。
(3)导程:同⼀螺旋线上相邻两⽛对应点的轴向距离。
⽤代号S表⽰。
(4)螺纹的公称直径:除管螺纹以通管的内径(英⼨单位)为公称直径外,其他螺纹的公称直径,均以螺纹的⼤径为公称直径(公制单位)。
(5)螺纹中径:中径最为重要,因为它控制所有螺纹组装的配合与强度。
中径在节线上,这⼀位置的齿宽与相邻齿槽宽度⼀致。
02螺纹的命名英制螺纹:英制螺纹是螺纹尺⼨⽤英制标注,是美国、英国与加拿⼤根据统⼀的体系开发的。
点击免费领取☞数控车(铣),ug编程,cad绘图,数控仿真,数控机械类书籍等上10G教程公制螺纹:根据ISO(国际标准化组织)系统开发的,是全球公制螺纹的标准。
03设计⾼性能攻丝加⼯(1)完美应⽤攻丝过程需要考虑的因素有:⼯件设计、丝锥设计、应⽤。
其⽬标是降低切削⼒,同时丝锥强度达到最⼤。
(2)平衡各种选项:必须兼顾应⽤的⽅⽅⾯⾯(3)丝锥设计要点1)对于形成长屑的较软的粘性材料丝锥结构简单前⾓和钩形⾓度较⼤后⾓和避空较⼤⾃由切削易于崩刃丝锥整体较脆弱容屑空间⼤2)对于硬性材料丝锥具有重载结构前⾓和钩形⾓度⼩铲背和后⾓⼩切削压⼒较⾼刃⼝设计粗壮,减少崩刃横截⾯⼤容屑空间有限(4)丝锥设计需考虑的因素:丝锥槽型、⼑具材料、表⾯强化处理。
这些设计特点必须保持平衡,才能提供适当的切削,切屑控制,润滑和扭转强度。
*注:攻丝中丝锥必须做什么动作,⽽其它⼑具不需要?必须在切削中途停⽌并反转出孔,⽽切削依然留在沟槽中。
这就给⾦属加⼯中的攻丝和丝锥的设计带来⼀个最⼤的挑战。
CNC钻孔与攻牙参数

CNC钻孔与攻牙参数CNC钻孔与攻牙是数控加工中常见的两个操作,它们都是针对金属材料进行的加工过程。
在实际操作中,不同的材料和要求会有不同的参数设置。
本文将从两个方面进行详细介绍,以帮助读者更好地了解CNC钻孔与攻牙参数设置。
1.选择合适的切削液:切削液的选择对CNC钻孔过程中的切削效果和工具寿命有着重要的影响。
切削液可用于冷却和润滑切削区域,减少切削温度,防止刀具磨损和工件变形。
一般而言,切削液的选择应根据材料的种类、切削深度和加工速度等因素进行。
2.选择合适的切削刃数:切削刃数是决定CNC钻孔过程中切削速度和效果的一个重要参数。
刀具的切削能力与切削刃数有关,刃数越多,切削效率越高,但单刃刀和多刃刀的切削速度并不相同。
一般情况下,单刃刀的切削速度较快,多刃刀的切削速度较慢,因此在实际应用中要根据具体情况选用。
3.设置合适的切削速度:切削速度是在CNC钻孔过程中控制刀具切削进给速度的参数,直接影响到钻孔加工的质量和效率。
切削速度过快,会导致刀具磨损加剧,切削效果变差;切削速度过慢,则会浪费时间、降低生产效率。
因此,要根据刀具和材料的特性,合理设置切削速度。
4.确定合适的切削深度:切削深度是指刀具在CNC钻孔过程中进给的距离,它与切削速度和切削宽度等参数密切相关。
切削深度过大,会增加刀具的负荷,容易导致刀具磨损;切削深度过小,则会延长加工时间。
因此,要选择适中的切削深度,一般根据刀具和材料的情况来进行调整。
CNC攻牙参数设置:1.选用合适的攻牙刀具:攻牙刀具的种类和材质对攻牙质量和效率有着重要影响。
一般而言,对于不同类型的材料和攻牙要求,需要选用相应的刀具。
常见的攻牙刀具主要有刀条、刀头、攻丝式、攻丝锥等,大部分采用高速钢或硬质合金制作。
2.设置合适的进给速度:进给速度是指攻牙刀具在CNC攻牙过程中的进给速度,直接影响到攻牙的质量和效率。
进给速度过快,会导致刷牙效果差;进给速度过慢,则会浪费时间。
- 1、下载文档前请自行甄别文档内容的完整性,平台不提供额外的编辑、内容补充、找答案等附加服务。
- 2、"仅部分预览"的文档,不可在线预览部分如存在完整性等问题,可反馈申请退款(可完整预览的文档不适用该条件!)。
- 3、如文档侵犯您的权益,请联系客服反馈,我们会尽快为您处理(人工客服工作时间:9:00-18:30)。
攻丝cnc攻牙转速进给比例--一格式如下,G84 Z- R- F-Z和R就不需要说了吧~`而进给F就有所不同了,有的是给一个螺距~~比如说M6的是1 ,M8的是1.25, M10的是1.5, M12的是1.75.我想我应该没有记错吧~好长时间没用了`而有的是F=S(之前给定了)*螺距这两者是根据G94和G95的模态不一样而决定的~~至于切削丝锥和挤压丝锥,顾名思义,两者的加工形式不一样,一个是切削出来的,一个挤压出来的`~选择时候根据加工材料而定~~例:M3内螺纹的底孔:首先应知道M3的螺距是0.5计算方法: 3-0.5×1.0 8=2.46 ,直径2.46不好找可以钻成直径2.5。
简言之做M3的牙,用2.5的钻头钻孔,用M3的丝攻攻牙。
每分钟进给G94、每转进给G95如果每分钟进给模式进给(f)=转速*牙距,每转进给,进给速度=牙距法拉克系统要指定刚性攻丝M29 G284同步攻丝,转速X螺距=进给用加工中心对孔进行攻牙加工时,攻牙的进给速度不知道怎样设定?如果有谁知道的将公式发上来谢谢!!例M6丝攻(即牙距1.0) .....S50; .....; M29; G98 G84 Z-10. R2. F50 ; G80; ....主轴转速×螺距=进给量如楼上所说的,螺距是1时是S50 F50,如果螺距是1.5就是S50 F75。
但通常还有个问题:最佳转速需通过试验得出,在试验时每改一次转速就得随着改一次进给量。
不仅繁琐而且易出错。
解决办法是让数控系统根据S值自动计算F值。
即:S50 …… F[#4119*1.5] (假定螺距是1.5)。
程序中#4119是当前S值。
这样只需要修改S值就行了。
还有不能攻丝的加工中心?那这加工中心真是浪费了。
G00G90G54B0X[125.-484.5+150.]Y[-40.+290.]S1004M03G00G43Z200.H43M07M08M29G99G84X[125.-484.5+150.]Y[-40.+290.]Z[-30.-27.]R10.F2008.(B4302)X[125.-484.5-150.]Y[-40.+290.](B4301)G80G00Z50.看看你们的参数对不对?进给/转速是不是你所用丝锥的螺距。
.攻牙的参数: F(进给速度)等于S(转速)乘以P(导程)P等于螺距乘以螺旋线比如:做M6的单线螺孔,那首先要5的钻头先钻个底孔(底孔就是螺孔的中径),F给600. 转速必须是600. 不然做出来的孔会乱牙M6的螺孔P就是1x1=1,我S给600.,F就必须是600.用上面的公式要使攻出的牙不乱参数必须要同步,只要用上面的那个公式就可以拉,至于上面的公式是这样来的,以后有机会在说.螺距不代表牙高啊,牙高有分为牙顶高,中径.和牙底高啊.而螺距只能代表螺纹的公称直径减去螺纹中径. 如M6,公称直径为6,螺距为1,中径就是5.至于用多大的钻头钻底孔,那要看是什么材料,一般比较硬的材料可以大0.1-0.2左右,不然容易断钻头.像铸铁类的可以大0.1,而那些铝件和胶版材料的话直接可以按照你上面列出的螺距来算.注:我干CNC四年了,基本上什么材料的东西都做过,有什么经验的问题可以问我,我很乐意交朋友.huangqing088@G03 X132. Y25.I2.J0.Z-2.F500.上面Z-2.为螺距如孔内功牙的话如: 孔深10mm 螺距 2mm 坐标为 (0,0)G91 X-5. 刀尖碰到工件G03 I5.J0.Z-2.F500. 螺旋下刀G01 X5. 回到0.Z-10G91 X-5.G03 I5.J0.Z-2.F500.G01 X5.以上必须用螺纹刀粒,长度大于8mm, 下刀深度必须与螺距成倍数,否则会乱牙用镗刀功外圆就是用G02 X- Y- I- Z- F-就可以拉数控机床程序编制的一般步骤和手工编程数控机床程序编制的一般步骤和手工编程数控机床程序编制(又称数控编程)是指编程者(程序员或数控机床操作者)根据零件图样和工艺文件的要求,编制出可在数控机床上运行以完成规定加工任务的一系列指令的过程。
具体来说,数控编程是由分析零件图样和工艺要求开始到程序检验合格为止的全部过程。
一般数控编程步骤如下1.分析零件图样和工艺要求分析零件图样和工艺要求的目的,是为了确定加工方法、制定加工计划,以及确认与生产组织有关的问题,此步骤的内容包括:1)确定该零件应安排在哪类或哪台机床上进行加工。
2)采用何种装夹具或何种装卡位方法。
3)确定采用何种刀具或采用多少把刀进行加工。
4)确定加工路线,即选择对刀点、程序起点(又称加工起点,加工起点常与对刀点重合)、走刀路线、程序终点(程序终点常与程序起点重合)。
5)确定切削深度和宽度、进给速度、主轴转速等切削参数。
6)确定加工过程中是否需要提供冷却液、是否需要换刀、何时换刀等。
2.数值计算根据零件图样几何尺寸,计算零件轮廓数据,或根据零件图样和走刀路线,计算刀具中心(或刀尖)运行轨迹数据。
数值计算的最终目的是为了获得编程所需要的所有相关位置坐标数据。
3.编写加工程序单在完成上述两个步骤之后,即可根据已确定的加工方案(或计划)及数值计算获得的数据,按照数控系统要求的程序格式和代码格式编写加工程序等。
编程者除应了解所用数控机床及系统的功能、熟悉程序指令外,还应具备与机械加工有关的工艺知识,才能编制出正确、实用的加工程序。
4.制作控制介质,输入程序信息程序单完成后,编程者或机床操作者可以通过CNC机床的操作面板,在EDIT方式下直接将程序信息键入CNC系统程序存储器中;也可以根据CNC系统输入、输出装置的不同,先将程序单的程序制作成或转移至某种控制介质上。
控制介质大多采用穿孔带,也可以是磁带、磁盘等信息载体,利用穿孔带阅读机或磁带机、磁盘驱动器等输入(输出)装置,可将控制介质上的程序信息输入到CNC系统程序存储器中。
5.程序检验编制好的程序,在正式用于生产加工前,必须进行程序运行检查。
在某些情况下,还需做零件试加工检查。
根据检查结果,对程序进行修改和调整,检查-修改-再检查-再修改……这往往要经过多次反复,直到获得完全满足加工要求的程序为止。
上述编程步骤中的各项工作,主要由人工完成,这样的编程方式称为“手式编程”。
在各机械制造行业中,均有大量仅由直线、圆弧等几何元素构成的形状并不复杂的零件需要加工。
这些零件的数值计算较为简单,程序段数不多,程序检验也容易实现,因而可采用手工编程方式完成编程工作。
由于手工编程不需要特别配置专门的编程设备,不同文化程度的人均可掌握和运用,因此在国内外,手工编程仍然是一种运用十分普遍的编程方法。
在车床上加工螺纹螺纹车削刀具已经从全面改善车刀性能的涂层及材料等级方面所取得的共同进步中获益。
此外,在螺纹车削刀片方面,人们进行了更好的结构设计,实现了更佳的切屑控制。
尽管发生了这些变化,制造工程师们倾向花很少的时间来优化螺纹加工操作,将螺纹加工过程看成是一种无法不断取得进步的“黑匣子”。
事实上,通过工程设计方式可以提高螺纹加工过程的效率。
第一步应该是理解螺纹加工中一些基本的主题。
为什么螺纹车削要求如此之高螺纹车削的要求要高于普通车削操作。
切削力一般较高,螺纹刀片的切削端部半径较小,比较薄弱。
在螺纹加工中,进给速度必须与螺纹的节距精确对应。
对于节距为8螺纹/英寸(tpi)的情况,刀具必须以8转/英寸或者0.125英寸/转的进给速度前进。
与普通车削应用(其中典型的进给速度大约为0.012ipr)相比,螺纹车削的进给速度要高出10倍。
螺纹加工刀片刀尖处的作用力可能要高100~1,000倍。
承受这种作用力的端部半径一般为0.015英寸,而常规车削刀片的半径为0.032英寸。
对于螺纹加工刀片,该半径受许可的螺纹形状根部半径(其大小由相关螺纹标准规定)的严格限制。
它还受所需要的切削动作限制,因为材料无法经受普通车削中的剪切过程,否则会发生螺纹变形。
切削力较高和作用力聚集范围较窄导致的结果是:螺纹加工刀片要承受比一般车刀高得多的应力。
部分与全轮廓刀片的比较部分轮廓刀片,有时候被称作“非加顶式”刀片,它在不给螺纹加顶或装牙顶的情况下切削螺纹沟槽。
(参见图1)一把刀片可以产生一系列螺纹,直至最粗的节距-即每英寸螺纹数最少处为止-这是刀片端部半径强度许可的。
这种端部半径设计得足够小,刀片可以加工各种节距。
对于小节距,端部半径会显得尺寸过小。
这意味着刀片必须穿透得深一些。
例如,用一把部分轮廓刀片加工一个8tpi的螺纹需要螺纹深度为0.108英寸,而用完全轮廓刀片产生的相同螺纹则只需要0.81英寸的指定深度。
因此,全轮廓刀片可以产生强度更高的螺纹。
此外,全轮廓刀片加工出螺纹的操作可以少4道。
多齿刀片多齿刀片连续地带有系列齿,任何齿在螺纹沟槽中切削的深度都要比它前面的一个齿更深。
(参见图2)借助这些刀片,加工一个螺纹所需要的操作道数可以减少80%。
刀具寿命要远远长于单顶尖刀片,因为最终的齿只加工某个给定螺纹一半或三分之一的金属。
但是,由于它们存在较高的切削力,因此不提倡将这些刀片用于薄壁零件的加工-因为可能会产生颤振。
此外,用这些刀片加工工件的结构必须具有足够的螺纹间隙,以便所有齿退出切削。
每道进给每道的切削深度,或者说每道进给,在螺纹加工中是非常关键的。
每个相连的操作道都要啮合刀片切削刃较大部分。
如果每道进给是恒定的(不推荐采用这种方式),则切削力和金属去除率从上一道到下一道会剧烈增加。
例如,在采用恒定的0.010英寸进给/道的速度加工一个60度螺纹形状时,第二道去除的材料为第一道的3倍。
与随后每道操作一样,去除的金属量连续成指数上升。
为了避免这种切除量增加并维持比较现实的切削力,切深应该随着各道操作而减少。
横切进给法至少有四种横切进给法。
(参见图3)很少有人发现这些方法中某种方法对螺纹加工操作有效性的冲击到底有多大。
?径向横切进给? 尽管这可能是加工螺纹最常用的方法,但确是最不提倡采用的一种方法。
由于刀具是径向进给的(与工件中心线垂直),因此金属从螺纹齿腹两侧去除,从而产生V形切屑。
这种切屑很难断裂,因此切屑流动是一个问题。
此外,由于刀片端部两侧要承受较高的热和压力,因此刀具寿命通常比其他横切进给法中要短。
? 齿腹横切进给在这种方法中,横切方向与螺纹齿腹之一平行,这一般意味着刀具沿30度直线进给。
切屑与普通车削中产生的类似。
(参见图4。
)与径向横切相比,这种方法中产生的切屑比较容易成形,并且易于从切削刃中排出,热扩散性更好。
但是,在这种横切进给法中,刀片后缘会摩擦齿腹而不会进行切削。
这样会烧伤螺纹,导致表面粗糙度很差,甚至发生颤振现象。
? 修改的齿腹横切进给(推荐采用)这种方法与齿腹横切进给法类似,不同的是横切角度小于螺纹角度-即小于30度。