Amantys针对高功率模块的4500V Amantys Power DriveTM 驱动器进入中国市场
艾尔森 iLS1500 系列智能实验室电源 1500W 机架式可编程电源说明书

ARTESYNiLS1500 SERIESIntelligent Laboratory Power1500W Rack Programable Power SuppliesTotal Power:1500 WattsInput Voltage:100 - 240 Vac# of Outputs:SingleAT A GLANCEAdvanced Energy’s Artesyn iLS1500 series is a programmable DC power supply with a single 1500 Watt output. With 12-bit D/A & A/D converters embedded, the power supplies come with the capability of reporting voltage and current veryaccurately. The iLS1500 series provides convenient dynamic rotary controls for voltage and current adjustment. The power supplies also come with rear ports that allow remote control via USB, Ethernet, and analog control inputs and they are designed to offer either bench use or rack mounting. The iLS1500 series is LXI certified, details for using this interface can be found in our Programming Manual.SPECIAL FEATURES⏹ 1500W with extended range ⏹ LXI certified⏹ 5 models: up to 400V and 70A ⏹ Small, high-density 1U package ⏹ Wireless digital remote sense ⏹ Built-in voltage and currentmeasurement⏹ Full OCP and OVP protection ⏹ Series and parallel operationSTANDARD USER INTERFACE INCLUDES:⏹ Ethernet, USB 2.0 and analog ⏹ LXI interface⏹ Command capability for keysight603X, sorenson DLM and xantrex XFRSAFETY⏹ Conforms to UL 60950-1 andUL 62368-1⏹ Certified to CAN/CSA C22.2No. 60950-1 & 62368-1APPLICATIONS⏹ Test and Measurement ⏹ ATE ⏹ Laboratory⏹Research and DevelopmentRESOURCE LINKSClick Here for the Programming Manual Click Here for the Scripting Manual Click Here for the User Manual Click Here for DriversiLS1500 SERIESiLS1500 SERIES Notes1. R ating is percent of full scale. Rating is for operation between 10% of minimum voltage or current rating to 100% of voltage rating and the current rating at that voltage. Minimum voltage is guaranteed at greater than 1% of the rated output voltage. Minimum current is guaranteed at greater than 1% of the rated output current.2. Measured with 20 MHz bandwidth and excluding line frequency ripple (see application note AN024 for measurement details).3. T ime for output voltage to recover within 0.5% of its rated output for a load change from 10 to 90% of its rated output current.Voltage set point from 10% to 100% of rated output.4. Add this to the output reopens time to obtain the total programming time.5. Time to provide data back to the controller using LAN interface (does not include A/D conversion time).6. 1500 Watt Output is only available with an AC input of 110 VAC or grater. With a lower AC line, output will be limited to 1100 Watts.* S upplemental characteristics are not warranted but are descriptions of typical performance determined either by design or type testing.Specifications subject to change without notice. Contact Versatile Power for full specifications and additional information.For international contact information,visit .******************(SalesSupport)*************************(TechnicalSupport) +1 888 412 7832ABOUT ADVANCED ENERGYAdvanced Energy (AE) has devoted more than three decades to perfecting power for its global customers. AE designs and manufactures highly engineered, precision power conversion, measurement and control solutions for mission-critical applications and processes.Our products enable customer innovation in complex applications for a wide range of industries including semiconductor equipment, industrial, manufacturing, telecommunications, data center computing, and medical. With deep applications know-how and responsive service and support across the globe, we build collaborative partnerships to meet rapid technological developments, propel growth for our customers, and innovate the future of power.Specifications are subject to change without notice. Not responsiblefor errors or omissions. ©2021 Advanced Energy Industries, Inc. All rights reserved. Advanced Energy®, AE® and Artesyn™ are U.S. trademarksof Advanced Energy Industries, Inc.。
Magtrol HD系列磁滞动力计说明书
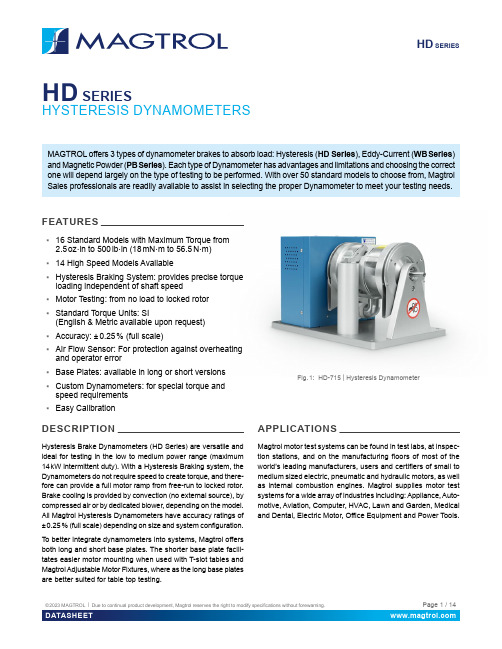
HD SERIES HD SERIESHYSTERESIS DYNAMOMETERSMAGTROL offers 3 types of dynamometer brakes to absorb load: Hysteresis (HD Series), Eddy-Current (WB Series) and Magnetic Powder (PB Series). Each type of Dynamometer has advantages and limitations and choosing the correct one will depend largely on the type of testing to be performed. With over 50 standard models to choose from, Magtrol Sales professionals are readily available to assist in selecting the proper Dynamometer to meet your testing needs.FEATURES▪16 Standard Models with Maximum Torque from2.5 oz·in to 500 lb·in (18 mN·m to 56.5 N·m)▪14 High Speed Models Available▪Hysteresis Braking System: provides precise torqueloading independent of shaft speed▪Motor Testing: from no load to locked rotor▪Standard Torque Units: SI(English & Metric available upon request)▪Accuracy: ± 0.25 % (full scale)▪Air Flow Sensor: For protection against overheatingand operator error▪Base Plates: available in long or short versions▪Custom Dynamometers: for special torque andspeed requirements▪Easy CalibrationDESCRIPTIONHysteresis Brake Dynamometers (HD Series) are versatile and ideal for testing in the low to medium power range (maximum 14 kW intermittent duty). With a Hysteresis Braking system, the Dynamometers do not require speed to create torque, and there-fore can provide a full motor ramp from free-run to locked rotor. Brake cooling is provided by convection (no external source), by compressed air or by dedicated blower, depending on the model. All Magtrol Hysteresis Dynamometers have accuracy ratings of ± 0.25 % (full scale) depending on size and system configuration. To better integrate dynamometers into systems, Magtrol offers both long and short base plates. The shorter base plate facili-tates easier motor mounting when used with T-slot tables and Magtrol Adjustable Motor Fixtures, where as the long base plates are better suited for table top testing.APPLICATIONSMagtrol motor test systems can be found in test labs, at inspec-tion stations, and on the manufacturing floors of most of the world’s leading manufacturers, users and certifiers of small to medium sized electric, pneumatic and hydraulic motors, as well as internal combustion engines. Magtrol supplies motor test systems for a wide array of industries including: Appliance, Auto-motive, Aviation, Computer, HVAC, Lawn and Garden, Medical and Dental, Electric Motor, Office Equipment and Power Tools.Fig. 1: HD-715 | Hysteresis DynamometerMagtrol’s Hysteresis Dynamometers cover a wide range of Torque, Speed and Mechanical Power ratings. To select the appropriate size Dynamometer for your motor testing needs, you will need to determine the Maximum Torque, Speed and Power applied to the Dynamometer.MAXIMUM TORQUEThe Magtrol Hysteresis Absorption Dynamometer will develop braking torque at any speed point, including low speed and stall conditions ("0" rpm). It is important to consider all torque points that are to be tested, not only rated torque, but also locked rotor and breakdown torque. Dynamometer selection should initially be based on the maximum torque requirement, subject to determining the maximum power requirements. MAXIMUM SPEEDThis rating is to be considered independent of torque and power requirements, and is the maximum speed at which the Dynamometer can be safely run under free-run or lightly loaded conditions. It is not to be considered as the maximum speed at which full braking torque can be applied.MAXIMUM POWER RATINGSThese ratings represent the maximum capability of the Dyna-mometer Braking System to absorb and dissipate heat gener-ated when applying a braking load to the motor under test. The power absorbed and the heat generated by the Dynamometer is a function of the Torque (T) applied to the motor under test, and the resulting Speed (n) of the motor. This is expressed in these Power (P) formulas:The Dynamometer’s ability to dissipate heat is a function of how long a load will be applied. For this reason, the maximum power ratings given are based on continuous operation under load, as well as a maximum of 5 minutes under load.To safely dissipate heat and avoid Dynamometer failure, the maximum power rating is the most important consideration in selecting a Dynamometer.Magtrol Hysteresis Dynamometers absorb power with a unique Hysteresis Braking Systemwhich provides frictionless torque loading independent of shaft speed. The HysteresisBrake provides torque by the use of two basic components - a reticulated pole structureand a specialty steel rotor/shaft assembly - fitted together but not in physical contact.Until the pole structure is energized, the drag cup can spin freely on its shaft bear-ings. When a magnetizing force from the field coil is applied to the pole structure,the air gap becomes a flux field and the rotor is magnetically restrained, providinga braking action between the pole structure and rotor.Magtrol’s M-TEST Software isa state-of-the-art motor testingprogram for Windows®-baseddata acquisition. Used with aMagtrol DSP 7010 Dynamom-eter Controller, Magtrol M-TESTSoftware provides the control ofany Magtrol Dynamometer and runs test sequences in a manner best suited to the overall accuracy and efficiency of the Magtrol Motor T est System. The data that is generated by Magtrol’s Motor T esting Software can be stored, dis-played and printed in tabular or graphic formats, and can be easily imported into a spreadsheet.Written in LabVIEW™, M-TEST has the flexibility to test a majority of motor types in a variety of ways. Because of LabVIEW’s versatility, obtaining data from other sources (e.g. thermocouples), controlling motor power and providing audio/visual indicators is relatively easy. Magtrol’s M-TEST Software is ideal for simulating loads, cycling the unit under test and motor ramping. Because it is easy to gather data and duplicate tests, the software is ideal for use in engineering labs. T ests can be programmed to run on their own and saved for future use allowing for valuable time savings in production testing and incoming/outgoing inspection.SI: P[W] = T[N·m] × n[min-1]× (1.047 x 10-1) English: P[W] = T[lb·in] × n[rpm]× (1.183 x 10-2) Metric: P[W] = T[kg·cm] × n[rpm]× (1.027 x 10-2) All of Magtrol’s controllers, readouts and software calculate horsepower as defined by 1 [hp] = 550 [lb·ft /s].Using this definition:P[hp] = P[W] / 745.7Pole StructureBearingAir GapOPEN LOOP SYSTEMSMagtrol offers both open loop manual test systems and PC-based closed loop test systems. A typical open loop system will consist of a Dynamometer and a Magtrol DSP 7010 Dynamom-eter Controller in Open-Loop configuration. A Magtrol Single or Three-Phase Power Analyzer, which allows for the capturing of volts, amps, watts and power factor, can be included as an option. An open loop system is often used for quick pass / fail testing on the production line or at incoming inspection. Magtrol’s DSP 7010 Dynamometer Controller provides pass / fail testing as a standard feature.CLOSED LOOP SYSTEMSIn a closed loop motor test system, data is collected on a PC using Magtrol’s M-TEST Software, DSP 7010 Dynamometer Controller, and requisite interface cards and cables. Magtrol’s DSP 7010 Dynamometer Controllers compute and display mechanical power (in horsepower or watts) in addition to torque and speed. A Single or Three Phase Power Analyzer, a required component in a test system measuring motor efficiency, can be integrated into this system as well as Magtrol’s Temperature Testing Hardware.MODEL 7500Computer witha) All -5C dynamometers are 5 Volt Output.Please, contact our sales representative for 6C (English units), 7C (Metric units) or 8C (SI units) specifications.b) Operating at the continuous power rating for periods of up to 4 hours isacceptable. However, operating for extended periods at high temperatures will result in premature component and bearing failure. Limiting the length of the cycle and the component temperatures will guard against premature failure. Where continuous duty is desired for longer time intervals, compo-nent temperatures should be maintained less than 100°C; monitoring the outside brake surface temperature is a sufficient reference.c) Requires air cooling provided by user. Regulator and filter package isprovided as standard d) Blower is includede) The maximum speed will depend on what type of keyway (if any) is usedon the shaft. Unless specified, the dynamometer shaft will be made withouta keyway.ELECTRICAL POWERHD-100 / 400 / 500 SERIES WITH LONG BASE PLATEb) Shaft Flats are not available on high speed models.a) These dimensions represent the distance between mounting holes. Thereare four (4) mounting holes on each base plate.HD-100 / 400 / 500 SERIES WITH SHORT BASE PLATEb) Shaft Flats are not available on high speed models.a) These dimensions represent the distance between mounting holes. Thereare four (4) mounting holes on each base plate.a) These dimensions represent the distance between mounting holes. Thereare four (4) mounting holes on each base plate.b) Shaft Flats are not available on high speed models.are four (4) mounting holes on each base plate.a) These dimensions represent the distance between mounting holes. There are four (4) mounting holes on each base plate.BLOWER POWER▪Models HD-710, HD-715 & HD-810 include the BL-001 blower.▪Models HD-815 include the BL-002 blower. ▪Model HD-825 uses two BL-002 blowers for cooling its two brake sets.On / Off Switch120/240 V AC / 50/60 HzAllow approximately 6 in to 8 in (152 mm to 203 mm) between rear of dynamom-eter base plate and blower for connection hardware. Required hardware is sup-plied with the dynamometer.BL-002 Blower has two filter elements.HD 106 & HD 106 HSHD-100 & HD 100 HSHD 400 & HD 400 HSHD 500 & HD 500 HS30 00040 00050 00060 000Maximum Rated Speed for standard versionMaximum Rated Speed for High Speed version m )0.0000.0020.0040.0060.0100.0120.0140.0160.018010 00020 00030 00040 00050 00060 000S P E E D (r p m )TORQUE (N·m )0.000.010.020.030.040.050.060.070.085 00010 00020 00025 00030 00035 00040 00045 00015 000S P E E D (r p m )TORQUE (N·m )HD 510 & HD 510 HSHD 505 & HD 505 HSHD 515 & HD 515 HSHD 700 & HD 700 HSHD 710 & HD 710 HSHD 705 & HD 705 HS5 00010 00020 00025 00030 00015 00035 00040 00045 0000.10.00.20.30.40.50.60.70.8S P E E D (r p m )TORQUE (N·m )0.000.250.500.751.001.251.505 00010 00020 00025 00030 00015 00035 00040 00045 000S P E E D (r p m )TORQUE (N·m )0.000.250.500.751.001.251.505 00010 00020 00025 00030 00015 00035 00040 00045 000S P E E D (r p m )TORQUE (N·m )0.00.5 1.0 1.5 2.0 2.5 3.05 00010 00020 00025 00030 00015 00035 00040 000S P E E D (r p m )TORQUE (N·m )0.00.51.01.52.02.53.0 05 00010 00020 00025 00030 00035 00040 00015 000S P E E D (r p m )0.01.02.03.04.05.06.05 00010 00020 00025 00030 00015 00035 00040 000S P E E D (r p m )HD 715 & HD 715 HSHD 800HD 805HD 810 & HD 810 HSHD 815 & HD 815 HSHD 825 & HD 825 HS0.01.02.03.04.05.06.0 05 00010 00020 00025 00030 00040 00035 00015 000S P E E D (r p m )TORQUE (N·m)0.02.0 4.0 6.08.012.010.014.04 000 2 0006 00010 00012 00014 0008 000S P E E D (r p m )TORQUE (N·m)0.05.010.015.020.025.02 0004 0006 0008 00010 00012 00014 000S P E E D (r p m )TORQUE (N·m )0.02.0 4.08.06.010.012.014.04 000 2 0006 00010 00012 00014 00016 0008 000S P E E D (r p m )TORQUE (N·m )0.05.010.015.020.025.04 000 2 0006 00010 00012 00014 00016 0008 000S P E E D (r p m )TORQUE (N·m )0.010.020.030.040.050.02 0004 0006 0008 00012 00010 000S P E E D (r p m )TORQUE (N·m )The power absorption curves represent the maximum power (heat) that the dynamometer can dissipate over time.HD SERIESHD Series Hysteresis Dynamometers can be incorporated into a Customized Motor Test System (CMTS )These PC based, turn-key systems arecustom designed and built to meet specific user requirements.Various devices such as dynamometer con-trollers, power analyzers or other customized devices can be easily integrated into a 19" rack system (in an external cabinet or directly in the table).These systems integrate specific software (such as M-TEST) to facilitate the measure-ment process.ENCODER OPTIONS FOR LOW SPEED TESTINGFor low speed motors, such as gear motors with maximum speeds of less than 200 rpm, Magtrol offers additional encoder options that allow for increased resolution of the speed signal.T-SLOT BASE PLATETo accommodate Magtrol AMF-3 Adjustable Motor Fixtures, a grooved base plate with three M12 T-slots, one centered and two 250 mm apart, is available on all HD-8XX series dynamometers.MECHANICAL CUSTOMISATIONSMagtrol is highly experienced and qualified in the customization of its products. We can provide custom-ized base plates, riser blocks and shaft modifications.Our specialized salesmen and technicians are at your service to help you find the best configuration for your project.a) In case of special design the 4 last digits will be specific; please contactour sales representative b) Please contact our sales representative regarding long base plate c) PPR means Pulse Per RevolutionExample: HD Series Dynamometer, model 106, supply in 240 V A C, shortbase plate, 60-PPR encoder and standard version would be ordered as follows: HD-106-5C2-0100HD Series Dynamometer, model 805, supply in 120 V A C, long base plate with T-slot, 6000-PPR encoder and high speed version would be ordered as follows: HD-805-5C1-024HCABLE ASSEMBLYa) Other lenght available on requestDynamometer TableBlowerAdjustable Motor FixtureMotor Under TestHeavy-duty Equipment RackFully customizable (19" rack standards)Control screen(optional touchscreen)Command Panel(allows easy access to the main functions)Connection Panel To connect external devices or options spe-cific to the test bench (temperature probe,...)DSP 7010 Series Dynamometer Controller MODEL 7500 SeriesPower AnalyzerFull Computer (inlcuding rack mounted keyboard,...)Free rack mounted spacefor third-party equipment (e.g. power supply, measuringinstrument, etc...)© 2023 MAGTROL | Due to continual product development, Magtrol reserves the right to modify specifications without forewarning.Page 14 / 14DATASHEETI E S - U S 06 / 2023HD SERIESSYSTEM OPTIONS AND ACCESSORIESDSP 7010 - DYNAMOMETER CONTROLLERSMagtrol’s MODEL DSP 7010 Series Dynamometer Controller employs state-of-the-art Digital Signal Processing Technol-ogy to provide superior motor testing capabilities. Designed for use with any Magtrol Hysteresis, Eddy-Current or Powder Dynamometer, Magtrol In-Line Torque Transducer or auxiliary instrumentation, the DSP 7010 can provide complete PC control via the USB or IEEE-488 interface. With up to 500 readings per second, the DSP 7010 is ideally suited for both the test lab and the production line.WB & PB SERIES - DYNAMOMETERThe WB Series (eddy current) and PB Series (magnetic powder) dyna-mometers are particularly suitable for demanding applications requiring low (PB) to high (WB up to 65 000 rpm) speeds. The PB brakes will develop their nominal torque atstandstill, while the WBbrakes develop a braking torque proportional to the speed and their maximum torque is reached at nominal speed. The brake is cooled by water circulating in the stator. As a result, these dynamometers are able to dissipate high continuous loads (up to 140 kW). The WB and PB dynamometers incorporate a torque measuring system which has an accuracy of ± 0.3 % to ± 0.5 % at full scale.MODEL 7500 - POWER ANALYZERSThe Magtrol MODEL 7500 Power Analyzer is an easy-to-use instrument ideal for numerous power measurement applications. From DC to 80 kHz, the MODEL 7500 measures volts, amps, watts, volt-amps, frequency, crest factor, Vpeak, Apeak and power factor in one convenient display. They may be used either as stand-alone instruments or in conjunction with any Magtrol Hysteresis, Eddy-Current or Powder Brake Dynamometer; any Magtrol Dynamometer Controller and M-TEST Software for more demanding motor test applications.AMF SERIES - MOTOR FIXTURESPositioning and alignment have a great influence on the measured parameters (friction torque). MAG-TROL strongly recommends a sup-port specifically dedicated to the products to be tested to ensure the best positioning tolerances in X-Y , and its repeatability.Alternatively, Magtrol AMF Series (Adjustable Motor Fixtures) can be used. These extremely versatile fixtures can accommodate motors up to 101 m m (4") in diameter. It enables easy motor centering during testing, but does not have centering references.TAB SERIES - DYNAMOMETER TABLESTest from a stationary position or move a dynamometer to alternate testing stations with ease with Magtrol’s Dynamometer Table. The stand is designed from lightweight aluminum with casters for smooth mobility, and is sturdy enough to support even the heaviest of Magtrol dynamometers. The design can be retrofitted to any Magtrol dynamometer and is easily reconfigured for added versatility.Fig. 7: DSP 7011 | Programmable Dynamometer ControllersFig. 8: 1 PB 115 | Powder DynamometerFig. 9: MODEL 7510 | Power AnalyzersFig. 10: T AB Series | Dynamometer Tables。
AM18X5系列系统电源管理应用说明书

1.IntroductionIn addition to fundamentally low power RTC operation, the Ambiq AM18X5 includes the capability to effectively manage the power of other devices in a system. This allows the creation of extremely power efficient systems with minimal additional components. This Application Note describes how the AM18X5 may be used in various applications.2.System Power Control ApplicationsThe AM18X5 enables a variety of system implementations in which the AM18X5 can control the power used by other elements in the system. This configuration is typically used when the entire system is powered from a battery and minimizing total power usage is critical.2.1VSS Power SwitchedFigure 1 shows the recommended implementation, in which the internal power switch of the AM18X5 is used to completely turn off the MCU and/or other system elements. In this case the PSW/nIRQ2 output is configured to generate the SLEEP function, and the PWR2 bit is asserted. Under normal circumstances, the PSW/nIRQ2 pin is pulled to VSS with ~1 ohm of resistance, so that the MCU receives full power. The MCU initiates a SLP operation, and when the AM18X5 enters the SLEEP state the PSW/nIRQ2 pin is opened and power is completely removed from the MCU. This results in significant additional power savings relative to the other alternatives because even very low power MCUs require more current in their lowest power state than the AM18X5.The AM18X5 normally powers up selecting the OUTB register bit to drive the PSW/nIRQ2 pin, and the default value of the OUTB bit is zero. This ensures that the power switch is enabled at power up. If the power switch function is used, software should only change the PSW/nIRQ2 selection between OUTB (0b111) and SLEEP(0b110) to ensure no glitches occur in the power switching function.Figure 1 – Switched VSS Power Control2.2 VCC Power SwitchedFigure 2 shows the application in which an external transistor switch T is used to turn off power to the MCU. The SLP function operates identically to the VSS switched case above, but this implementation allows switchinghigher current and maintains a common ground. R can be on the order of megohms, so that negligible current is drawn when the circuit is active and PSW/nIRQ2 is low.Figure 2 – Switched VCC Power Control2.3 Reset DrivenFigure 3 shows the application in which the AM18X5 communicates with the system MCU using the reset function. In this case the MCU initiates a SLP operation, and sets the SLRES bit so that when the AM18X5enters the SLEEP state, it brings nRST low to reset the MCU. When the trigger occurs, the AM18X5 releases the MCU from reset, and may also generate an interrupt which the MCU can query to determine how reset wasexited. Since many MCUs use much less power when reset, this implementation can save some system power.Figure 3 – Reset Driven Power ControlOne potential issue with this approach is that many MCUs include internal pullup resistors on their reset inputs, and the current drawn through that resistor when the reset input is held low is generally much higher than theMCU would draw in its inactive state. Any pullup resistor should be disabled and the nRST output of the AM18X5 should be configured as a push-pull output.2.4Interrupt DrivenFigure 4 shows the simplest application, in which the AM18X5 communicates with the system MCU using an interrupt. The MCU can go into standby mode, reducing power somewhat, until the AM18X5 generates an interrupt based on an alarm or a timer function. This produces smaller power savings than other alternatives, but allows the MCU to wake in the shortest time.Figure 4 – Interrupt Driven Power Control3.Sleep RegisterThe register which controls the Sleep function of the Power Management system in the AM18X5 is the Sleep Register, accessed at register offset 0x17. The bits of the Sleep Register are defined below.SLP [7] - when 1, the Power Control State Machine (SM) described in Section 4will transition to theSWAIT state. This bit will be cleared when the SM returns to the RUN state. If either STOP is 1 or no interrupt is enabled, SLP will remain at 0 even after an attempt to set it to 1.SLRES [6] - when 1, assert nRST low when the Power Control SM is in the SLEEP state.EX2P [5] - when 1, the external interrupt XT2 will trigger on a rising edge of the WDI pin. When 0, the external interrupt XT2 will trigger on a falling edge of the WDI pin.EX1P [4] - when 1, the external interrupt XT1 will trigger on a rising edge of the EXTI pin. When 0, the external interrupt XT1 will trigger on a falling edge of the EXTI pin.SLST [3] - set when the AM18X5 enters Sleep Mode. This allows software to determine if a SLEEP has occurred since the last time this bit was read.SLTO [2:0] - the number of 7.8 ms periods after SLP is set until the Power Control SM goes into theSLEEP state. If SLTO is not 0, the actual delay is guaranteed to be between SLTO and (SLTO - 1)periods. If SLTO is 0, the transition will occur with no delay.4.Sleep Control State MachineThe AM18X5 includes a sophisticated Sleep Control system that allows the AM18X5 to manage power for other chips in a system. The Sleep Control system provides two outputs which may be used for system power control:1) A reset (nRST) using the nRST output pin may be generated to put any host controller into a minimumpower mode and to control sequencing during power up and power down operations.2) A power switch signal may be generated (PWR), which allows the AM18X5 to completely power downother chips in a system by allowing the PSW/nIRQ2 pin to float. The OUT2S field must be set to a value of 6 to select the SLEEP output. When using the PWR output, PSW/nIRQ2 is configured as an opendrain pin with 1 ohm resistance. This allows the AM18X5 to directly switch up to 50 mA of current with no external components or to control a single external transistor for higher current switching. The lowresistance power switch is enabled by setting the PWR2 bit. If the I2C or SPI master (i.e., the hostcontroller) is powered down by the power switch, the PWGT bit should be set to ensure that a floating bus does not corrupt the AM18X5.3) If OUT2S is 6, but the PWR2 bit is not set, PSW/nIRQ2 will be configured as a high true Sleep outputwhich may be used as an interrupt.The Sleep state machine in Figure 5 receives several inputs which it uses to determine the current Sleep State:1) POR – the indicator that power is valid, i.e. either VCC or VBAT is above the minimum voltage.2) SLP - the Sleep Request signal which is generated by a software access to the Sleep Register.3) TRIG - the OR of the enabled interrupt request from the Alarm comparison in the RTC, the interrupt signalfrom the Countdown Timer in the RTC, the interrupt signal from the Watchdog Timer in the RTC, theExternal Interrupt 1 or 2 pins, the Battery Low detection interrupt, the Autocalibration Fail interrupt, or the Oscillator Fail interrupt.4) TO - the timeout signal from the SL Timeout counter.4.1RUNRUN is the normal operating state of the AM18X5. PWR and nRST are not asserted, SLP is 0, and SLST holds the state of the previous Sleep. SLST should be cleared by software before entering the SWAIT state.4.2SWAITSoftware can put the chip to sleep by setting the SLP bit in the Sleep Register, as long as a valid interrupt is enabled (see Section 4.4) indicated by VAL being asserted. The SM moves to the SWAIT state and waits for a programmable number of seconds (0 to 7) selected by the SLTO field in the Sleep Register. This allows software to perform additional cleanup functions after setting SLP before the MCU is shut down. Operation is the same in SWAIT as it is in RUN, and if an enabled interrupt occurs (TRIG) the SM returns to the RUN state and clears the SLP bit. PWR and nRST are not asserted, SLP is 1, and SLST is 0.4.3SLEEPOnce the programmed number of seconds has elapsed in the SWAIT state, the TO signal is asserted and the machine moves to the SLEEP state, putting the AM18X5 into Sleep Mode. In this case the PWR signal is removed, and nRST is asserted if SLRES is set. Once an enabled operational interrupt occurs (TRIG), the SM returns to the RUN state, reactivates power and removes reset as appropriate. The SLST register bit in the Sleep Register is set when the SLEEP state is entered, allowing software to determine if a SLEEP has occurred.!POR!TO * !TRIG!SLP + !VAL!TRIGFigure 5 – Sleep State Machine4.4 SLP ProtectionSince going into Sleep Mode may prevent an MCU from accessing the AM18X5, it is critical to ensure that the AM18X5 will receive a TRIG signal. To guarantee this, the SLP signal cannot be set unless the STOP bit is 0 and at least one of the following conditions exists:1) The AIE bit is 1, enabling an Alarm interrupt.2) The TIE and the TE bits are 1, enabling a Countdown Timer interrupt. 3) Either the EX1E or EX2E bit is a 1, enabling an External interrupt.4) The BMB field is not zero and the WDS bit is zero, enabling a Watchdog InterruptIn addition, SLP cannot be set if there is an interrupt pending. Software should read the SLP bit after attempting to set it. If SLP is not asserted, the attempt to set SLP was unsuccessful either because a correct trigger was not enabled or because an interrupt was already pending. Software must correct the situation before attempting to enter Sleep Mode again.5.Typical System ImplementationFigure 6 is a more detailed view of a typical system using the VSS Power Switched approach. The VSS pin of the MCU, and potentially other system components, is switched using the PSW pin of the AM18X5. The nIRQ pin of the AM18X5 is connected to an interrupt input of the MCU, allowing the MCU to utilize the RTC interrupt functions of the AM18X5 when it is awake. The nRST output of the AM18X5 is connected to the reset input of the MCU, enabling the AM18X5 to control power on reset and integrate an external MCU reset button RESET. The MCU controls the AM18X5 over a SPI or I2C I/O channel.Figure 6 – System ExampleThe key value of the AM18X5 in this type of system is the ability to put the MCU into an off state, and providing a very rich variety of triggers which can cause the AM18X5 to wake the MCU from the off state. There are a number of different triggers which may be useful.5.1AlarmsThe system may require the MCU to wake up at particular times, which is accomplished by configuring the Alarm Interrupt function of the AM18X5.5.2Countdown TimerThe system may require the MCU to wake up at periodic intervals which do not necessarily correspond to specific calendar times. The Countdown Timer of the AM18X5 provides highly flexible time interval configuration to support this function.5.3WAKE Button/SwitchA very common requirement is the capability to wake the system with a manual input such as a pushbutton or switch, typified by the WAKE button in Figure 6. One of the external interrupt inputs such as EXTI may be simply connected to the button. All AM18X5 inputs include Schmitt trigger circuitry to enable clean interrupts. If additional debouncing of the input is required, the AM18X5 provides direct access to the interrupt input pins to facilitate software implementations.5.4External Device InputsIn some systems an external device such as a wakeup radio may provide a signal which must wake the MCU. An AM18X5 external interrupt such as the WDI pin provides this capability.5.5Analog InputsSome systems include analog signals, such as light sensors or detectors on radio antennas, which must wake the MCU. The Analog Comparator function, which allows the voltage on the VBAT input of the AM18X5 to be compared with a configurable voltage threshold and generate an interrupt, can easily be used in this application, and it allows flexible configuration, both in voltage levels and in transition direction to support different environments. The Analog Comparator may also be used to provide a third external digital interrupt if necessary by selecting the proper digital threshold.5.6Battery Low DetectionThe Analog Comparator can provide a battery low detection function. In this case, the VCC pin would be tied to the VBAT pin, and the thresholds would be adjusted to ensure that the Battery Low interrupt occurs prior to any Brownout Detection on the VCC input. This allows software to prepare for a potential battery failure in advance without having to poll the battery level.5.7ErrorsAny failure interrupt in the AM18X5 may also be configured to wake the MCU. This can be particularly valuable for Oscillator Failure detection, when software may need to respond to the error in order to report the problem quickly.6.Saving ParametersIf the MCU is powered down in Sleep Mode, there is often some data which must be preserved until the next power up. The internal RAM of the AM18X5 is always available, so software can easily save any necessary parameters prior to entering Sleep Mode and retrieve them when the MCU wakes up.7.Power Switch Electrical CharacteristicsThe power switch on the AM18X5 PSW pin has a typical on resistance of 1 ohm over the full temperature range so that currents up to 50 mA may be handled without appreciable voltage drop. This allows the AM18X5 to switch power to multiple devices in most systems, which can be particularly important for components without internal Sleep functions. If the PSW pin is not used as a power switch, the maximum leakage current of the ~1 Ω switch is less than 250 pA at 25 °C.8.Avoiding Unexpected Leakage PathsOne potential problem which can occur when the AM18X5 powers other devices down is that unexpected leakage paths can be created between the powered AM18X5 and the unpowered device. The AM18X5 can be configured to disable inputs and outputs in Sleep Mode to prevent leakage. In general, any input or output pin connected to a device which is powered down should be disabled. Any pins which remain powered in Sleep Mode, such as pushbutton inputs used to wake the system, must not be disabled.1) nRST is disabled in Sleep Mode by clearing the RSEN bit in the Output Control Register.2) FOUT/nIRQ is disabled in Sleep Mode by clearing the O1EN bit in the Output Control Register.3) CLKOUT/nIRQ3 is disabled in Sleep Mode by clearing the O4EN bit in the Output Control Register.4) nTIRQ (I2C devices only) is disabled in Sleep Mode by clearing the O3EN bit in the Output ControlRegister.5) EXTI is disabled in Sleep Mode by setting the EXDS bit in the Output Control Register.6) WDI is disabled in Sleep Mode by setting the WDDS bit in the Output Control Register.7) The I2C or SPI interface pins are disabled in Sleep Mode by setting the PWGT bit in the Oscillator ControlRegister. This is a particularly important function because there are multiple leakage paths in the I/Ointerfaces.9.System Power AnalysisThe AM18X5 can significantly improve the power characteristics of many different types of systems. A specific example will be presented, and several other generalizations can be made from this. The fundamental advantage provided by the AM18X5 is that it allows the system designer to essentially ignore the sleep current of other system components, which allows the utilization of components which have be optimized for other parameters, such as active power, cost or functionality.9.1Using an External RTC with Power ManagementThe key element in any system power analysis is the usage profile, and for this example we assume the system is active for T act and inactive for T inact. I act is the current drawn when the system is active, and I inact is the current drawn when the system is inactive. The average current I avg is therefore:I avg = (T act * I act + T inact * I inact )/(T act + T inact)An example will use a PIC16LF1947 MCU, which is highly optimized for low power operation. This MCU draws 80 nA in Sleep Mode, 1.8 uA in Sleep Mode with the internal oscillator and RTC active, and 120 uA in 500 KHz active mode. Assume a usage profile where the system in active for 1 second every 30 minutes, so that T act is 1 and T inact is 1799. If this MCU is used alone and supplies the RTC functions, the average current for theusage profile is:I avg = (1 * 120 uA + 1799* 1.8 uA)/1800 = 1.865 uAIf the AM18X5 is used to provide the RTC functionality in Autocalibrated RC Mode (<20 nA continuous current) and the PIC is placed into Sleep Mode, the average current for the usage profile is dramatically lower:I avg = (1 * 120 uA + 1799* 80 nA)/1800 + 20 nA = 166 nAThis is a significant improvement, but the current can be further reduced by having the AM18X5 switch power to the MCU. The resulting average current is ~50% lower:I avg = (1 * 120 uA + 1799* 0 nA)/1800 + 20 nA = 86 nA9.2Managing MCU Active PowerIn many cases, the duration of the active time is a function of how much processing must be accomplished, and can therefore be assumed to be a linear function of the MCU clock frequency in active mode. The examples in the previous section assumed that the MCU ran for 1 second at 500 KHz, so 500,000 cycles of an 8-bit processor were required. Like most MCUs, the PIC has a relatively constant active current as a function of clock frequency, so using a higher internal frequency in the same MCU would have little effect on the overall power. However, there may be other MCUs (such as those with 32-bit processors) which have better active power efficiency but poor sleep power, and power switching with the AM18X5 eliminates any sleep power considerations.9.3Lower Cost MCUsLower cost MCUs often have poor sleep power characteristics relative to sleep optimized parts. Since theAM18X5 eliminates sleep power considerations, these lower cost processors may provide equivalent overall average power at significant cost savings.9.4High Performance ProcessorsIn some applications very high performance processors such as DSPs must be used due to real time processing requirements. These processors are generally not optimized for sleep performance, but they may be used in applications with low duty cycles. One example of this is fingerprint recognition, which is rarely accessed but must provide very fast response with complex processing. The AM18X5 power management functions enable a system design where the processor is powered down the vast majority of the time, providing low average power combined with very high instantaneous performance.Document Revision HistoryRev # Description0.01 Initial version0.02 Add leakage management0.03 Corrected calculations in section 9.10.04 Updated doc to only reflect the AM18X5 part numbersAddress:Ambiq Micro, Inc.11305 Four Points Drive, Building 2, Suite 250Austin, TX 78726+1-512-879-2850Website:General Information:*******************Sales:********************Technical Support:**********************。
Table Top Type Robot TT 第一步指南 第二版说明书
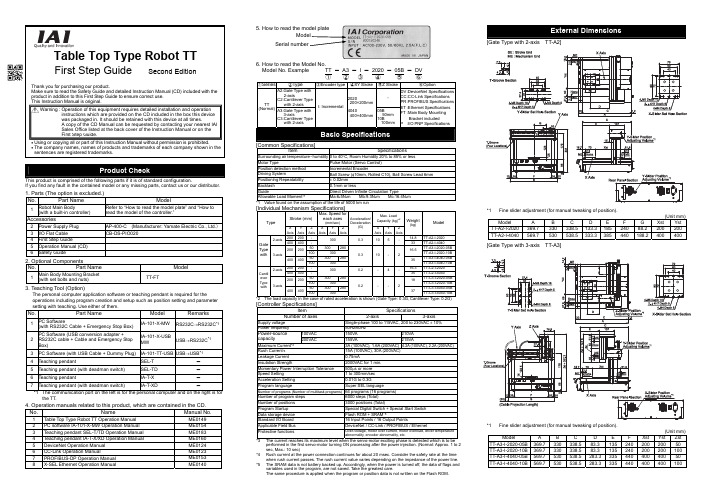
Table Top Type Robot TTFirst Step Guide Second EditionThank you for purchasing our product.Make sure to read the Safety Guide and detailed Instruction Manual (CD) included with theproduct in addition to this First Step Guide to ensure correct use.This Instruction Manual is original.• Using or copying all or part of this Instruction Manual without permission is prohibited.• The company names, names of products and trademarks of each company shown in thesentences are registered trademarks.This product is comprised of the following parts if it is of standard configuration.If you find any fault in the contained model or any missing parts, contact us or our distributor.1. Parts (The option is excluded.)No.Part Name Model1Robot Main Body(with a built-in controller)Refer to “How to read the model plate” and “How toread the model of the controller.”Accessories2 Power Supply Plug AP-400-C (Manufacturer: Yamate Electric Co., Ltd.)3 I/O Flat Cable CB-DS-PIO0204 First Step Guide5 Operation Manual (CD)6 Safety Guide2. Optional ComponentsNo.Part Name Model1Main Body Mounting Bracket(with set bolts and nuts)TT-FT3. Teaching Tool (Option)The personal computer application software or teaching pendant is required for theoperations including program creation and setup such as position setting and parametersetting with teaching. Use either of them.No.Part Name Model Remarks1PC Software(with RS232C Cable + Emergency Stop Box)IA-101-X-MW RS232C→RS232C*12PC Software (USB conversion adapter +RS232C cable + Cable and Emergency StopBox)IA-101-X-USBMW USB→RS232C*13 PC Software (with USB Cable + Dummy Plug) IA-101-TT-USB USB→USB*14 Teaching pendant SEL-T -5 Teaching pendant (with deadman switch) SEL-TD -6 Teaching pendant IA-T-X -7 Teaching pendant (with deadman switch) IA-T-XD -*1 The communication port on the left is for the personal computer and on the right is forthe TT.4. Operation manuals related to this product, which are contained in the CD. Manual No.1 Table Top Type Robot TT Operation Manual ME01492 PC software IA-101-X-MW Operation Manual ME01543 Teaching pendant SEL-T/TD Operation Manual ME01834 Teaching pendant IA-T-X/XD Operation Manual ME01605 DeviceNet Operation Manual ME01246 CC-Link Operation Manual ME01237 PROFIBUS-DPOperationManual ME01538 X-SEL Ethernet Operation Manual ME01406. How to read the Model No.Model No. Example TT - A3 -I - 2020 - 05B - DV①②③④⑤⑥①Series②Type③Encoder type④XY Stroke⑤Z Stroke⑥OptionA2:Gate Type with2-axisC2:Cantilever Typewith 2-axis-TT(Normal) A3:Gate Type with3-axisC3:Cantilever Typewith 2-axisI: Incremental2020200×200mm4040400×400mm05B50mm10B100mmDV :DeviceNet SpecificationsCC :CC-Link SpecificationsPR :PROFIBUS SpecificationsET :Ethernet SpecificationsFT :Main Body MountingBracket includedP :I/O PNP SpecificationsBasic Specifications[Common Specifications]Item SpecificationsSurrounding air temperature・humidity0 to 40°C, Room Humidity 20% to 85% or lessMotor Type Pulse Motor (Servo Control)Position detection method Incremental EncoderDriving System Ball Screw (φ10mm, Rolled C10), Ball Screw Lead 6mmPositioning Repeatability± 0.02mmBacklash 0.1mm or lessGuide Direct Driven Infinite Circulation TypeAllowable Load Moment*1Ma:6•5N•m Mb:9.3N•m Mc:16.4N•m*1 Value found on the assumption of the life of 5000 km run[Individual Mechanism Specifications]Stroke (mm)Max. Speed foreach axes(mm/sec)Max. LoadCapacity(kg)*2TypeXAxisYAxisZAxisXAxisYAxisZAxisAcceleration/Deceleration(G) XAxisYAxisZAxisWeight(kg)Model200 200- 14.8 TT-A2-I-20202-axis400 400-300 0.310 5-33 TT-A2-I-404050300 280TT-A3-I-2020-05B200 20010030016.5TT-A3-I-2020-10B50300 280TT-A3-I-4040-05BGateTypewith 3-axis400 4001003000.3 10- 235TT-A3-I-4040-10B200 200- 16.3 TT-C2-I-20202-axis400 400-300 0.2-4-35 TT-C2-I-404050300 280TT-C3-I-2020-05B200 20010030018TT-C3-I-2020-10B50300 280TT-C3-I-4040-05BCantileverTypewith 3-axis400 4001003000.2 --237TT-C3-I-4040-10B*2 The load capacity in the case of rated acceleration is shown (Gate Type: 0.3G, Cantilever Type: 0.2G)[Controller Specifications]Item SpecificationsNumber of axes 2-axis 3-axisSupply voltage Single-phase 100 to 115VAC, 200 to 230VAC ± 10%Power frequency50Hz/60Hz100VAC 150VA 210VAPower-sourcecapacity 200VAC 155VA 215VAMaximum Current*33A (100VAC), 1.6A (200VAC) 4.2A (100VAC), 2.2A (200VAC)Rush Current*415A (100VAC), 30A (200VAC)Leakage Current0.75mAInsulation Strength 2000VAC for 1 min.Momentary Power Interruption Tolerance500μs or moreSpeed Setting 1 to 300mm/secAcceleration Setting0.01G to 0.3GProgram language Super SEL languageNumber of programs (Number of multitask programs)64 programs (16 programs)Number of program steps 6000 steps (Total)Number of positions 3000 positions (Total)Program Startup Special Digital Switch + Special Start SwitchData storage device Flash ROM + SRAM*5Standard I/O Board 16 Input Points / 16 Output PointsApplicable Field Bus DeviceNet / CC-Link / PROFIBUS / EthernetProtective functions Over-voltage, motor over current, motor overload, driver temperatureabnormality, encoder abnormality, etc.*3 The current reaches its maximum level when the servo-motor exciting phase is detected which is to beperformed in the first servo-motor turning ON processing after the power injection. (Normal: Approx. 1 to 2sec, Max.: 10 sec)*4 Rush current at the power connection continues for about 20 msec. Consider the safety rate at the timewhen rush current passes. The rush current value varies depending on the impedance of the power line.*5 The SRAM data is not battery backed up. Accordingly, when the power is turned off, the data of flags andvariables used in the program, are not saved. Take the greatest care.The same procedure is applied when the program or position data is not written on the Flash ROM.External Dimensions[Gate Type with 2-axis TT-A2]*1 Fine slider adjustment (for manual tweaking of position).(Unit mm)Model A B C DEFGXstYstTT-A2-I-2020 369.7 330 338.5 133.318524088.2200200TT-A2-I-4040 569.7 530 538.5 333.3385440188.2400400[Gate Type with 3-axis TT-A3]*1 Fine slider adjustment (for manual tweaking of position).(Unit mm)Model ABCDEFXst Yst ZstTT-A3-I-2020-05B 369.7 330 338.5 83.313524020020050TT-A3-I-2020-10B 369.7 330 338.5 83.3135240200200100TT-A3-I-4040-05B 569.7 530 538.5 283.333544040040050TT-A3-I-4040-10B 569.7 530 538.5 283.3335440400400100 Warning : Operation of this equipment requires detailed installation and operationinstructions which are provided on the CD included in the box this devicewas packaged in. It should be retained with this device at all times.A copy of the CD Manual can be requested by contacting your nearest IAISales Office listed at the back cover of the Instruction Manual or on theFirst Step Guide.[Cantilever Type with 2-axis TT-C2]*1Fine slider adjustment (for manual tweaking of position).(Unit mm)Model A B C D E F XstYst TT-C2-I-2020 405 320 135 120 310 42 200 200 TT-C2-I-4040 605 520 335 213.6 510 142 400 400[Cantilever Type with 3-axis TT-C3]*1 Fine slider adjustment (for manual tweaking of position).(Unit mm)Model A B C D E F Xst Yst Zst TT-C3-I-2020-05B 405 330.6 135 120 310 71 200 200 50 TT-C3-I-2020-10B 405 330.6 135 120 310 71 200 200 100 TT-C3-I-4040-05B 605 530.6 335 213.6 510 171 400 400 50 TT-C3-I-4040-10B 605 530.6 335 213.6 510 171 400 400 100Do not use this product in the following environment:• Location where the surrounding air temperature exceeds the range of 0 to 40°C • Location where condensation occurs due to abrupt temperature changes • Relative humidity less than 20%RM or greater than 85%RM • Location exposed to corrosive gases or combustible gases• Location exposed to significant amount of dust, salt or iron powder • Location subject to direct vibration or impact • Location exposed to direct sunlight• Location where the product may come in contact with water, oil or chemical dropletsWhen using the product in any of the locations specified below, provide a sufficient shield.• Location subject to electrostatic noise• Location where high electrical or magnetic field is present • Location with the mains or power lines passing nearbyInstallation and Noise Elimination1. There is a cooling vent hole on the main body’s rear panel section. Do not close the vent hole when the main body is installed.2. When it required to fix the main body, fix it as follows using the optional mounting brackets3. Protective Ground4. Noise Elimination Grounding (Frame Ground)Connect it using a soft copper wire with the diameter of 1.6 mm or more to the frame ground on the main body (Refer to the above figure).Do not share the ground wire with or connect to other equipment. Ground each controller. The same procedure is applied for the protective ground.5. Precautions Regarding wiring Method6. Noise Sources and EliminationCarry out noise elimination measures for power devices on the same power path and in the same equipment. The following are examples of measures to eliminate noise sources:①AC solenoid valves, magnet switches and relays [Measure] Install a Noise killer parallel with thecoil.②DC solenoid valves, magnet switches and relays [Measure] Install a diode parallel with the coil.Use a DC relay with a built-in diode.Table Top TTTable Top TTOther equipmentOther equipment Other equipment+24V 0V4-M4 Depth 82- φ 4H7 Depth 5(Cable Projection Length)7.34.34.31.837.430304250Z-Slider Set Hole Section4-M5 Depth 10T-Groove SectionRear Panel Section*1 For the selection of the circuit breaker, perform it according to the following items.Breaker Teaching pendant Value > Power Capacity ÷ AC Input Voltage(Refer to the item for the controller specifications for the power capacity).•The current reaches the maximum level when the servo-motor is turned on and theservo-motor exciting phase is detected. Select the circuit breaker rated current thatdoes not trip the maximum current.• Select the circuit breaker that does no trip with the rush current described in thecontroller specifications.(Refer to the operating characteristic curve described in the manufacturer’s catalog.)• For the rated breaking current for the circuit breaker, select the breaking current valuewith which the current can be securely broken down even when short-circuit currentpasses.Rated Breaking Current > Short-circuit Current = Primary Power SupplyCapacity/Power Voltage.• Select the breaking current value for the circuit breaker leaving some margin.*2When the leakage breaker is to be installed, it is required to select it with the purposeclarified such as protection from fire or human body protection.Measure the leakage current at the location where the leakage breaker has beeninstalled.Use the “applicable to higher harmonics type” leakage breaker.Input*1Set the input functions using the I/O parameter Nos. 30 to 45 (Input Function Selection 000 to 015) and set the port Nos.that assign the each of the set functions, using the I/O parameter Nos. 282 to 298.*2If the input function selection 000 (program start) is assigned to any port except for the Port No. 000, the start switch onthe front panel is disabled.*3When the input function selection 007 to 013 (program No. designating digital switch) are assigned to any port except forthe port Nos. 007 to 013, the program change digital switch on the front panel is disabled.Output*4Set the output functions using the I/O parameter Nos. 46 to 61 (Output Function Selection 300 to 315) and set the portNos. that assign the each of the set functions, using the I/O parameter Nos. 299 to 314. Also, setting the output functionsusing the I/O parameter Nos. 331 to 346 (Output Function Selection 300 Area 2 to 315 Area 2) and setting the Port Nos.that assign the each of the set functions, using the I/O parameter Nos. 315 to 330, are available.When the system output signal is output to the I/Os on the above table, use the Output Function Selection Area 2.*5Because the output function selections 300 to 304 are allocated to the LEDs on the panel window, when the parameters of46 to 50 are set to universal output, or the Port No. allocation is changed using the parameter 299 to 303 settings, theLEDs are disabled.I/O Flat Cable (Accessories) CB-DS-PIO020No.Color Wirings No.Color Wirings1BR118GY22RD 119WT 23OR120BK24YW121BR35GN 122RD 36BL123OR37PL124YW38GY125GN39WT126BL310BK 127PL 311BR 228GY 312RD 229WT 313OR 230BK 314YW 231BR 415GN 232RD 416BL 233OR 417PL 2Flat cable(Presswelding)34YW 4Flat cable(Presswelding)I/O Circuit DiagramsNPN Specifications PNP SpecificationsPinNo.ElectricwirecolorPortNo.Function inStandardSetting(in Delivery)1 BR1 -I/O PowerSource +24V2 RD1 016UniversalInput3 OR1 017UniversalInput4 YW1 018UniversalInput5 GN1 019UniversalInput6 BL1 020UniversalInput7 PL1 021UniversalInput8 GY1 022UniversalInput9 WT1 023UniversalInput10 BK1 024UniversalInput11 BR2 025UniversalInput12 RD2 026UniversalInput13 OR2 027UniversalInput14 YW2 028UniversalInput15 GN2 029UniversalInput16 BL2 030UniversalInput17 PL2 031UniversalInputRemarksIt is set to the universal input when it is delivered. However, the change of the inputfunction is available with the I/O parameter setting.Parameter*1No. Parameter Name Remarks30 Input function select 000*21: Program Start31 Input function select 001 0: Universal Input1: Software Reset32 Input function select 002 0: Universal Input1: Servo ON signal33 Input function select 003 0: Universal Input1: Program automatically started when the power ON is reset inAUTO mode and software is reset2: Automatic Starting Program Signal34 Input function select 004 0: Universal Input1: All servo-axes soft interlock (OFF level)35 Input function select 005 0: Universal Input1: Pause Release (ON edge)36 Input function select 006 0: Universal Input1: Pause Signal (OFF level)37 Input function select 007*30: Universal Input1: Program No. appointment (LSB)38 Input function select 008*30: Universal Input1: Program No. appointment(The second bit)39 Input function select 009*30: Universal Input1: Program No. appointment(The third bit)40 Input function select 010*30: Universal Input1: Program No. appointment(The fourth bit)41 Input function select 011*30: Universal Input1: Program No. appointment(The fifth bit)42 Input function select 012*30: Universal Input1: Program No. appointment(The sixth bit)43 Input function select 013*30: Universal Input1: Program No. appointment(MSB : The seventh bit)2: Error Reset(ON edge)44 Input function select 014 0: Universal Input1: Driving Power Interruption Cancellation Input (ON Edge)45 Input function select 015 0: Universal Input1: All Effective Axes Homing (ON Edge)2: All Increment Effective Axes Homing (ON Edge)PinNo.ElectricwirecolorPortNo.Function inStandardSetting(in Delivery)18 GY2 316UniversalOutput19 WT2 317UniversalOutput20 BK2 318UniversalOutput21 BR3 319UniversalOutput22 RD3 320UniversalOutput23 OR3 321UniversalOutput24 YW3 322UniversalOutput25 GN3 323UniversalOutput26 BL3 324UniversalOutput27 PL3 325UniversalOutput28 GY3 326UniversalOutput29 WT3 327UniversalOutput30 BK3 328UniversalOutput31 BR4 329UniversalOutput32 RD4 330UniversalOutput33 OR4 331UniversalOutput34 YW4 -I/O PowerSource 0VRemarksIt is set to the universal output when it is delivered. However, the change of the outputfunction is available with the parameter setting.Parameter*4No. Parameter Name Function46331Output function select 300*5Output function select 300(Area 2)0: Universal Output1: Error Output at the operation cancellation level or more (ON)2: Error Output at the operation cancellation level or more (OFF)3: Error Output at the operation cancellation level or more +emergency stop output (ON)4: Error Output at the operation cancellation level or more +emergency stop output (OFF)47332Output function select 301*5Output function select 301(Area 2)0: Universal Output1: READY Output (PIO Trigger Program Operation Available)2: READY Output (PIO Trigger Program Operation Available)and without occurrence of any error at the operationcancellation level or more3: READY Output (PIO Trigger Program Operation Available)and READY Output (PIO Trigger Program OperationAvailable, and without occurrence of any error at the cold startlevel or more or more level or more48333Output function select 302*5Output function select 302(Area 2)0: Universal Output1: Emergency-stop output(ON)2: Emergency-stop output(OFF)49334Output function select 303*5Output function select 303(Area 2)0: Universal Output1: AUTO Mode Output2: Output during the Automatic Operation (In addition, when theparameter No. 12 is set to “1”)50335Output function select 304*5Output function select 304(Area 2)0: Universal Output1: Output at the time of “All Effective Axes Homing (=0)”2: Output when all the effective axes homing is completed3: Output when all the effective axes home preset coordinatesare set51336Output function select 305Output function select 305(Area 2)0: Universal Output2: Output during the first axis servo ON52337Output function select 306Output function select 306(Area 2)0: Universal Output2: Output during the second axis servo ON53338Output function select 307Output function select 307(Area 2)0: Universal Output2: Output during the third axis servo ON54339Output function select 308Output function select 308(Area 2)0: Universal Output55340Output function select 309Output function select 309(Area 2)0: Universal Output56341Output function select 310Output function select 310(Area 2)0: Universal Output57342Output function select 311Output function select 311(Area 2)0: Universal Output58343Output function select 312Output function select 312(Area 2)0: Universal Output59344Output function select 313Output function select 313(Area 2)0: Universal Output60345Output function select 314Output function select 314(Area 2)0: Universal Output61346Output function select 315Output function select 315(Area 2)0: Universal OutputWhen using this product for the first time, make sure to avoid mistakes and incorrect wiring by referring to the procedure below.Set-up for operation is completed.TroubleshootingThe following alarm displays are frequently generated at the start-up operation.Head Office: 577-1 Obane Shimizu-KU Shizuoka City Shizuoka 424-0103, JapanTEL +81-54-364-5105 FAX +81-54-364-2589website: www.iai-robot.co.jp/Ober der Röth 4, D-65824 Schwalbach am Taunus, GermanyTEL 06196-88950 FAX 06196-889524SHANGHAI JIAHUA BUSINESS CENTER A8-303, 808, Hongqiao Rd. Shanghai 200030, ChinaTEL 021-6448-4753 FAX 021-6448-3992website: Technical Support available in USA, Europe and ChinaHead Office: 2690 W. 237th Street, Torrance, CA 90505TEL (310) 891-6015 FAX (310) 891-0815Chicago Office: 110 East State Parkway, Schaumburg, IL 60173TEL(847) 908-1400 FAX (847) 908-1399TEL (678) 354-9470 FAX (678) 354-9471website: Atlanta Office: 1220 Kennestone Circle, Suite 108, Marietta, GA 30066825 PhairojKijja Tower 12th Floor, Bangna-Trad RD., Bangna, Bangna, Bangkok 10260, ThailandTEL +66-2-361-4458 FAX +66-2-361-4456Manual No.: ME0205-2D。
海尔源泉5电动汽车技术参数手册说明书

Hyundai IONIQ 5.Specifications.Electric motor(s)DYNAMIQ 2WD TECHNIQ AWDMotor type - rear Permanent magnet synchronous motorMotor type - front-Permanent magnet synchronous motor Configuration Rear mounted driving rear wheels Rear + front mounted driving rear + front wheels Maximum power - rear motor / front motor160 kW / -155 kW / 70 kWMaximum torque - rear motor / front motor350 Nm / -350 Nm / 255 NmMaximum power - total160 kW225 kWMaximum torque - total350 Nm605 NmBattery DYNAMIQ 2WD TECHNIQ AWDBattery type Liquid cooled Lithium-ionCapacity72.6 kWhOutput253 kWVoltage653 VCooling system DYNAMIQ 2WD TECHNIQ AWDActive Air Flap (AAF) - front lower air intake shutters●On-board AC charger DYNAMIQ 2WD TECHNIQ AWDCharging capacity (maximum)10.5 kWStandard charging time (240 V at maximum charging capacity)Approximately 6 hours 6 minutesCharging port Type 2 (IEC 62196-2 Type 2)On-board DC fast charger DYNAMIQ 2WD TECHNIQ AWDCharging capacity350 kWSuspension DYNAMIQ 2WD TECHNIQ AWDFront MacPherson strutRear Multi-linkDamping control system High performance dampersBrakes DYNAMIQ 2WD TECHNIQ AWDSystem Dual diagonal-split circuit, power assisted with Electronic Brake-force Distribution (EBD),Electronic Stability Control (ESC) and active hydraulic booster (regenerative braking)Booster Integrated Electric Booster (IEB)Front brake type Ventilated discFront disc dimensions345 mm x 30 mmRear brake type Ventilated discRear disc dimensions345 mm x 20 mmWeight DYNAMIQ 2WD TECHNIQ AWDTare Mass1990 kg2100kgGross Vehicle Mass (GVM)2430 kg2540 kgPermissible Axle Weight (PAW) - front1280 kg1280 kgPermissible Axle Weight (PAW) - rear1370kg1370 kgRoof rack load limit80 kgFront under bonnet cargo area load limit25 kg10 kgTowing Capacity DYNAMIQ 2WD TECHNIQ AWDBraked1600 kgUn-braked750 kgMaximum tow ball weight100 kgTrailer pre-wiring package●Energy consumption*DYNAMIQ 2WD TECHNIQ AWDElectric driving efficiency; Combined:Wh/km168190 kWh/100km16.819.0All Electric Range (AER)481 km430 km* F igure based on WLTP (Worldwide Harmonised Light-Duty Vehicles Test Procedure) static laboratory combined average city and highway cycle test, which measure, energy consumption, range and emissions in passenger vehicles, designed to provide figures closer to real-world driving behaviour. Real life driving results will vary depending on a combination of driving style, type of journey, vehicle configuration, battery age and condition, use of vehicle features (such as heating and air conditioning), as well as operating, environmental and climate conditions. Performance DYNAMIQ 2WD TECHNIQ AWDMaximum speed (km/h)1850 ~ 100 km/h (seconds)7.4 5.280 ~ 120 km/h (seconds) 4.7 3.8)0.288Coefficient of drag (CdDimensions DYNAMIQ 2WD TECHNIQ AWDExteriorLength4635 mmWidth1890 mmHeight (with shark fin antenna)1605 (1647) mmWheelbase3000 mmWheel track - front / rear1638 / 1647 mm1628 / 1637 mmMinimum ground clearance160 mmInteriorHead room front / rear (with Vision Roof)1046 / 970 mm1046 / 970 mm (1034 / 953 mm)Leg room front / rear1138 / 1002 mmShoulder room front / rear1465 / 1470 mm1465 / 1465 mmHip room front / rear1368 / 1362 mmCargo area rear - VDA (minimum / maximum)527 L / 1587 LCargo area front - VDA 57 L24 LCargo area glovebox compartment - VDA 9 LTotal cargo area - VDA (minimum / maximum)593 / 1653 L560 / 1620 LWheels & tyres DYNAMIQ 2WD TECHNIQ AWDWheel type Alloy - aerodynamic designWheel dimensions19 x 7.5J + 49.520 x 8.5J +54.5Tyre type Michelin Primacy 4Michelin Pilot Sport EVTyre dimensions235/55R19 105W255/45R20 105WSpare wheel type Tyre Mobility Kit (TMK)Electric vehicle functionsDYNAMIQ 2WDTECHNIQ AWDiPedal mode - intelligent one pedal driving mode●●Smart regenerative braking mode 2.0 - traffic & navigation based ●●Regenerative braking control - via paddle shifters●●Vehicle to Load (V2L) connection (outside) - 2-way adapter to domestic 3-pin plug output●●Vehicle to Load (V2L) connection (inside) - domestic 3-pin plug output ●●Voice notification of charging status (outside) - using external VESS speaker●●Visual notification of charging status (charge port door) - Parametric pixel LED indicator●●Navigation POI - EV charging stations; with auto display when needed ●●Trailer Mode - Automatic AER adjustment●●Trailer Mode - HTRAC AWD drive torque distribution-●Next departure function - set the intended departure time for the scheduled charging●●Scheduled charging function - set the intended start and end time for charging; Off-peak tariffs prioritised/Off-peak tariffs only ●●Target temperature function - set the intended climate control temperature for next departure●●EV charge transfer function - set the minimum battery % the V2L automatically discharges down to●●Charging limit function - set the defined battery charging limit for AC/DC charging●●Charging current function - set the defined battery charging current limit for AC charging●●Utility mode function - uses the high voltage battery to power vehicle electronics●●Eco mode climate control function - increases driving range in Eco drive mode●●Driver only climate control fan function - increases driving range ●●Heat off climate control function - increases driving range ●●Driving convenience DYNAMIQ 2WDTECHNIQ AWDAuto Hold function●●Electronic Parking Brake (EPB)●●Integrated Memory System (IMS), 2 driver positions - including;-●Driver’s seat (excluding lumbar) & exterior rear view mirror position Easy Access function - driver’s seat -●One touch turn signal - 3, 5, or 7 flashes ●●Rain sensing aero wipers ●●Remote Start - via Smart Key●●Reverse parking aid function - exterior mirrors -●Smart key with push button start●●Steering wheel mounted controls - audio, favourite, phone, voice control, lane safety, smart cruise control, speed limiter, trip computer & drive mode ●●Tilt & telescopic steering column●●Personalised User Profile selection - 3 custom profiles; Driver 1, Driver 2 & Guest ●●Driving engagementDYNAMIQ 2WDTECHNIQ AWDBrake Mode - 2 settings; Normal & Sport●●Drive Mode - 4 settings; Eco, Normal, Sport, Snow ●●Shift By Wire (SBW), electronic gear shift control ●●Active safetyDYNAMIQ 2WDTECHNIQ AWDElectronic Stability Control (ESC) including;Anti-lock Braking System (ABS)●●Brake Assist System (BAS)Electronic Brakeforce Distribution (EBD)Hill-start Assist Control (HAC)Multi Collision-Avoidance Brake (MCB)Traction Control System (TCS)Vehicle Stability Management (VSM)Active safetyDYNAMIQ 2WD TECHNIQ AWDHyundai SmartSense ™ including;Blind-Spot Collision Avoidance-Assist (BCA)●●Blind-Spot View Monitor (BVM)Driver Attention Warning (DAW), including;Leading Vehicle Departure AlertForward Collision-Avoidance Assist (FCA) including:Car / Pedestrian / Cyclist Detection (FCA - CAR/PED/CYC)Junction Turning / Crossing functions (FCA - JT/JC)Lane Change Oncoming / Side functions (FCA - LO/LS)Evasive Steering Assist function (FCA - w/ ESA)High Beam Assist (HBA)Intelligent Speed Limit Assist (ISLA)Lane Following Assist (LFA)Lane Keeping Assist - Line/Road-Edge (LKA-L/R)Parking Collision-Avoidance Assist - Reverse (PCA-R)Rear Cross-Traffic Collision-Avoidance Assist (RCCA)Rear Occupant Alert (ROA) - warning type Safe Exit Assist (SEA)Smart Cruise Control (SCC), including;Stop & Go function (SCC w/ S&G)Machine Learning function (SCC w/ ML) - Based on Driving Style Surround View Monitor (SVM) including;3D Surround View functionDriving Rear-View Monitor (DRM) function - rear view image on commandParking Distance Warning function w/ dynamic guidelines & guidance display Car wash entering mode Tailgate guide-line mode Trailer connection mode Other featuresEmergency Stop Signal (ESS)●●Steering wheel with Haptic feedback - SmartSense ™ functions ●●Manual Speed Limit Assist (MSLA)●●Parking Distance Warning - Forward/Reverse (PDW-F/R) - 6 sensors front & rear with guidance display ●●Smart Parking Assist (SPA), including;●●Perpendicular & Parallel reverse parking and Parallel forward exit functionsRemote Smart Parking Assist (RSPA), via Smart Key, including;●●Perpendicular & Parallel reverse parking and Forward/Rearward parking functionsTyre Pressure Monitoring System (TPMS) - individual tyre pressure readout ●●Virtual Engine Sound System (VESS)- external sound notification for pedestrians ●●Passive safety DYNAMIQ 2WDTECHNIQ AWDAirbagsFront airbags - driver & front passenger ●●Front centre side airbag●●Side (thorax & pelvis) airbags - driver & front passenger ●●Side curtain airbags ●●DoorsImpact sensing auto door unlock●●Electronic child safety lock - rear doors & windows ●●SeatbeltsPretensioners & height adjustable upper mounts on front seat belts●●Pretensioners on rear outboard seat belts ●●Load limiters - front & rear seat belts ●●Seat belt reminder - front & rear seatbelts ●●SeatingHeight adjustable front head restraints with tilt function ●●Height adjustable rear head restraints●●ISOFIX child restraint anchors (rear outboard seats)●●Top tether child restraint anchors (rear) - 3 anchors●●Security DYNAMIQ 2WD TECHNIQ AWDSecurity systemActive lock/unlock operation (user configurable)●●Anti-theft alarm ●●Central locking ●●Engine immobiliser ●●RemotesSmart key remote - 2x ●●OtherCapacitive touch front door handles - lock / unlock function ●●Multimedia system DYNAMIQ 2WDTECHNIQ AWDAudio/media sources AM radio●●FM / Digital radio (DAB+)●●Apple CarPlay 1 & Android Auto 2 compatibility ●●Bluetooth audio streaming●●Sounds of Nature - 6 pre-set sounds ●●USB multimedia input - music/video ●●FunctionsBluetooth® Multi-Connection; 1 x phone/audio & 1 x audio●●Bluetooth® Message Access Profile (MAP) - SMS playback capability; audio & visual●●Capacitive touch screen - 12.3” HD display with blue light filter ●●Radio Data System (RDS)●●Satellite navigation●●Live traffic updates (RDS-TMC)●●Voice memo function - up to 70 minutes recording time ●●SpeakersBOSE™ Premium audio system - 8 speakers with external amplifier ●●Other featuresColour theme layout - White or Black ●●EV vehicle functions display●●Quiet Mode function - Audio volume limited to ‘25’ in 1st row and muted in rear●●Occupant comfort & convenience DYNAMIQ 2WDTECHNIQ AWDUpholstery/trim Leather 3 appointed seats●●Leather 3 appointed steering wheel●●Leather 3 appointed centre console armrest w/real stitching ●●Leather 3 appointed door armrests w/cloth inserts & real stitching ●●Front seatsDriver’s seat - power adjustable - 10-way (including 2-way lumbar support) ●-Driver’s seat - power adjustable - 12-way (including 2-way lumbar support & 2-way calf support)-●Driver’s seat - ‘Relaxion’ comfort seat function (zero gravity position)-●Driver’s seat - Seat position change alert - displayed in multimedia system screen-●Passenger’s seat - power adjustable - 10-way (including 2-way lumbar support)●-Passenger’s seat - power adjustable - 12-way (including 2-way lumbar support & 2-way calf support)-●Passenger’s seat - ‘Relaxion’ comfort seat function (zero gravity position)-●Passenger’s seat - centre side control switch, including;-●Driver/rear passenger control for 2nd row slide (individual left & right)One-touch relaxation seat controlIntegrated Memory System (IMS) - passenger seat via multimedia screen -●Adjustable centre console (2-way sliding)●●2 x USB power outlet - centre console ●●1 x 12V power outlet - front console●●Wireless charging pad 15w (Qi standard)4 with cooling function - centre console●●Grip handles - 1x (passenger)●●Occupant comfort & convenience DYNAMIQ 2WD TECHNIQ AWDRear seatsCentre fold down armrest ●●Grip handles - 2x●●2 x USB power outlet - rear of centre console ●●Manual backrest recline function - 2-way (60:40)●●Manual seat base slide function - 2-way (60:40)●-Power seat base slide function - 2-way (60:40)-●Integrated Memory System (IMS) - rear seats via multimedia screen (60:40)-●Windows/shadesAcoustic laminated glass - windshield glass ●●Acoustic laminated glass - side doors ●●Solar control glass - windshield & front doors ●●Privacy glass - rear doors & tailgate●●Power windows - one touch up & down function with anti-pinching safety feature - front windows●●Convenience opening/closing function with Smart Key remote - front windows ●●Rear door window sunshades-●Sun visors (extendable) - driver and front passenger ●●Doors/tailgateLuggage area power outlet - 1 x 12V outlet●●Power charge flap - open/close; with Smart Key control●●Power retractable door handles - with approach open & unlock function ●●Power Tailgate - open/close; with adjustable height and speed ●●Smart Tailgate function - hands-free opening ●●OtherInstrument panel display board - with magnetic attachment capability ●●Vision & sight DYNAMIQ 2WDTECHNIQ AWDInterior mirrorElectro-Chromatic Mirror (ECM) - auto-dimming ●●Exterior mirrors Heated●●Power adjustable●●Power folding with auto fold function ●●Instrument clusterSupervision cluster including;●●12.3” colour TFT-LCD full screen displayDigital instrumentation with Driving Assist, Utility (Trip Computer), Turn By Turn & Powertrain view modes3 x display themes; Eco/Snow, Normal & Sport with torque gauge Colour theme layout - White or Black Head-Up-Display●●Augmented Reality Display Mode functions:Turn-by-turn navigation display Driving convenience information Blind-spot safety information Speedometer display Normal Display Mode functions: Turn-by-turn navigation display Driving convenience information Blind-spot safety information Multimedia information display Speedometer display Ventilation & heating DYNAMIQ 2WD TECHNIQ AWDAir conditioningClimate control - dual zone including;●●Touch type control panel Auto defog function Auto dehumidify function Smart vent functionAuto internal air circulation function; windscreen washer based & navigation map data based Auto fan function - including 3 modes; Low, Medium & High Cabin air filterCooling/heating vents - rear ‘B’ pillars Cooling/heating ducts - rear floorVentilation & heating DYNAMIQ 2WD TECHNIQ AWD Front seatsHeated front seats - 3 stage●●Air ventilated front seats - 3 stage-●Rear seatsHeated rear outboard seats - 2 stage-●Other featuresAuto Comfort Control -auto activation of driver’s heated / ventilated seat& heated steering wheel-●Heated rear windshield●●Heated steering wheel-●PTC Heater - electric heater●●Exterior styling DYNAMIQ 2WD TECHNIQ AWD FrontHeadlights - black bezel with Parametric Pixel graphics●●Front upper middle trim - gloss black with Parametric Pixel graphics●●Front bumper upper trim - satin chrome●●Front bumper lower middle trim - gloss black●●Front bumper lower trim - satin chrome●●Front bumper cladding - liquid silver●●Front bumper skid plate - liquid silver●●RearTaillights - black bezel with parametric pixel graphics●●Rear bumper/tailgate upper trim - satin chrome●●Rear bumper upper middle side trims & skid plate surround- gloss black●●Rear bumper lower middle side trims - satin chrome●●Rear bumper cladding - liquid silver●●Rear bumper skid plate - liquid silver●●Roof spoiler - tailgate mounted aero type;●●Body colour with piano black wind deflectorSideDoor frame, beltline moulding & mirror base/lower cover/front surround- gloss black●●Flush type door handle●●Middle upper side trim insert - gloss black●●Middle lower side trim insert - satin chrome●●Side cladding - liquid silver●●WheelsMulti-spoke gloss black / machined finish aero wheel- with Parametric Dynamics pattern●●Other featuresRoof aerial (shark fin type) - gloss black●●Interior styling DYNAMIQ 2WD TECHNIQ AWD TreatmentsAlloy effect finish (dashboard, door handles/speakers, cabin switches,●●wiper/light/transmission controls, air vents, centre console & overheadlight console)Gloss black - hybrid-touch steering wheel buttons, drive mode button,EV start/stop button, electronic park brake button & auto hold button●●Interior styling DYNAMIQ 2WD TECHNIQ AWD MaterialsPedals - alloy●●Door scuff plates - stainless steel●●Door trim insert garnish - paperette w/ParametricPixel graphics●●Headlining - cloth knit melange look●●DesignSteering wheel - EV exclusive with flat bottom & Parametric Pixel graphics●●Lighting DYNAMIQ 2WD TECHNIQ AWD Exterior lighting - frontHeadlight functions - automatic dusk sensing with escort and welcome●●Headlight type - Dual projector beam LED - low/high beam●●Positioning lights - LED w/Parametric Pixel graphics●●Daytime Running Lights (DRL) - LED w/Parametric Pixel graphics●●Turn signal lights - LED w/Parametric Pixel graphics●●Hidden LED light guide - upper bumper trim ●●Exterior lighting - rearTaillights - Full LED w/Parametric Pixel graphics●●Positioning lights - LED●●LED light guide - full width●●Brake lights - LED●●Turn signal lights - LED●●Reverse lights - LED●●Fog lights - LED●●License plate lights - LED●●High mount stop light (HMSL) - LED●●Exterior lighting - othersSide repeaters - LED w/Parametric Pixel graphics, integrated intoside mirrors●●Front cargo area light - LED●●Manual headlight levelling function - 4 levels; 0, 1, 2, & 3●●Interior lighting - frontMap lights with touch type operation - LED ●●Mood light - LED ●●Room lights including map lights & mood light - LED ●●Glovebox compartment light - LED●●Vanity mirror lights ●●Interior lighting - rearCentre room light - LED●●Room lights and map lights - LED (outboard)-O Interior lighting - othersInterior Ambient lighting - LED: door armrests & speaker surrounds,including;●●Adjustable colours & brightness; 10 pre-set and up to 64 colour choicesRear cargo area light●●Interior light fade-out delay●●Storage solutions DYNAMIQ 2WD TECHNIQ AWD Front seatsCentre console w/main & armrest compartment storage●●Cup holders including phone holder - centre console ●●Front console storage compartment●●Glovebox compartment - sliding type●●Ticket holders - sun visors (driver and front passenger)●●Rear seatsCentre console rear storage compartment●●Coat hooks - 1x●●Cup holders including phone holder - armrest●●Front seat back pockets - net type●●Split folding backrest - 60:40●●Boot/luggage areaCargo cover - dual position, retractable●●Luggage board - foldable●●Luggage compartment - 4x tie down hooks●●Luggage net ●●Underfloor storage compartment●●BonnetFront cargo compartment●●OthersDoors - map pockets and bottle holders (front and rear)●●Options DYNAMIQ 2WD TECHNIQ AWD Vision roof - fixed glass roof panel with power sunshade-O Notes:1. Apple CarPlay requires iPhone 5 or subsequent model (lightning cable) in order to operate.2. Android Auto requires a device with Android 5.0 operating system or subsequent version in order to operate.3. Finishes specified as leather may contain elements of genuine leather, polyurethane leather (leather substitute) or man-made materials, or a combination thereof.4. Wireless charging requires a Qi-enabled smartphone or adapter in order to operate.Key:● = Feature included as standard on trim- = Feature is not available on trim。
AMAT公司真空镀膜产品线介绍
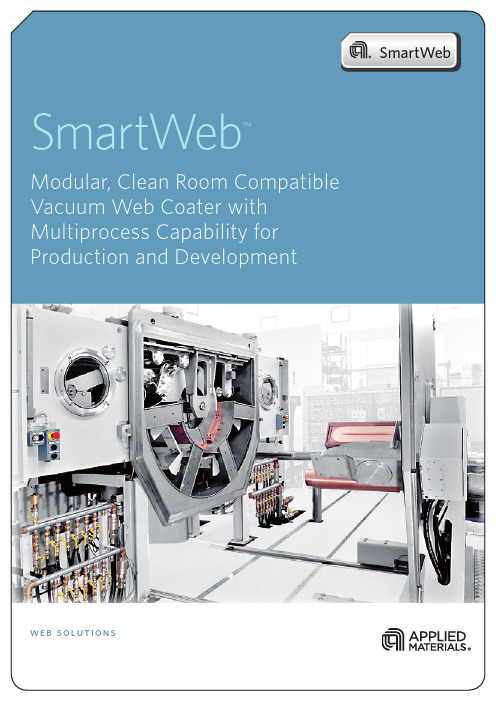
New products require clean room compatible vacuum web coaters. New products are constantly being developed in laboratories, which put increasing demands on mass production roll coaters. SMARTWEB is designed to eliminate the costly transition from development to production and to allow faster turnover to higher volumes.Applied SMARTWEBapplicationsSMARTWEB offers the highestflexibility for multiprocess web coaters. It incorporates sputter sources,evaporation sources for metals and for polymers as well as PECVD equipment. SMARTWEB’s design enables any combination of these technologies in a single coating operation and with its small footprint, it fits into standard clean rooms.New products include:Flexible Printed Circuit Boards (FPCB): Higher adhesionstrength of copper coatings is being demanded due to increasing line density and decreasing width. SMARTWEB enables the use of a range of improved pre-treatment tools for supporting adhesion promotion processes.Transparent ITO top-electrodes for displays as well as thesmall geometrical structures of FPCBs need a dust and particle free deposition environment in the process chamber. No moving parts or particle generating operations are allowed above the coating drum. The complete coater must also be small enough to fit into standard size clean rooms.Flexible displays using Organic Light Emitting Devices (OLEDs)require metal evaporator sources for the cathode layer and low temperature evaporators for the organic polymers.Super barrier layers for in-line encapsulation of moisturesensitive OLED layers are needed.Flexible solar cells have been developed with differentphotovoltaic materials, using various deposition technologies such as poly crystalline or amorphous Silicon, Copper-Indium-Gallium Selenide. All require transparent conductive top electrodes with low specific resistivity and high optical transparency.Flexible printed circuit board on ink cartridge.1 2 3FEATURESPre- and Post-Treatment ToolsMagnetically Enhanced Glow-DischargeTREATMAG ™ is the state of the art magnetron glow discharge device. It cleans the substrate surface from adherent water molecules. It is used successfully in Applied Materials’ metallizers, electron beam and sputter web coaters. TREATMAG ™ produces ion energies up to 70 eV.Linear Ion SourcesAs an alternative to TREATMAG,™ linear ion sources from different suppliers can be installed in the SMARTWEB process chamber. These provide higher ion energies above 70 eV.RF Hollow AnodeFor even higher ion energies up to 2000 eV, an RF-powered hollow anode is available. With an asymmetric RF-discharge, the substrate is biased negatively. Depending on the gases used, this results in an Argon-ion bombardment of the web (sputter cleaning) or in an ion-assisted base coating.Deposition ToolsPlanar MagnetronThe newly developed Applied Materials’ planar magnetron for the SMARTWEB uses clamped rectangular target plates. No water circuit is opened during target exchange. Optimized magnetic field arrangement achieves a target utilization of > 40%.Rotatable MagnetronFor target utilization above 80%, Applied Materials hasdeveloped a rotatable magnetron. With the cylindrical targetrotating around a stationary set of permanent magnets, a uniform erosion of the target tube results in a high utilization and thus a long lifetime of the target.Evaporator for MetalsFor evaporation of metals such as silver and magnesium, which are used as metal cathode layers in OLED displays, a linearevaporator is used with optimized lateral uniformity. Independent temperature control of crucible and nozzle plate allows foroptimum thermal conditions for different types of metals.Applied Materials’ planar magnetron with high target utilizationClamped planar target, new (right) and used (left)Planar (left) and rotatable (right) magnetrons availableSMARTWEB—The production and development tool with multiprocess capability. With its innovative modular design, SMARTWEB offers a wide variety ofpre- and post-treatment processes, deposition processes and in-line layer quality measurement methods.Machine control with PC andmonitor Layer measurement withOPTOPLEX (optional)1234SMARTWEB offers an infinite number of process configurations by using the following options:Up to six coating sources in one or two process modulesUp to 800 mm web width Web drive in both directions Handling of thick web > 70μm Handling of thin web < 70μmLoad locks, separating process modules from winding modulesIn-line degassing of the substrate with IR-heaterPre-treatment with DC-magnetron, ion-source or rf-hollow anodeCoating drum temperatures ranging from -40°C to +180°CPlanar DC-magnetrons, e.g. TORAMAG ™ Planar AC-Magnetrons, e.g. TWINMAG ™Rotatable DC-magnetronsEvaporators for low-melting polymers Evaporators for metals PECVD systemsRoll-to-roll measurement of sheet resistivityLocal measurement of sheet resistivity using eddy current deviceMeasurement of optical densityMeasurement of spectral transmission Measurement of spectral reflection••••••••••••••••••••SMARTWEB comes with the following high value features:Easy installation on flat floor Stainless steel process moduleTurbomolecular pumps plus cold traps Low particle generation through soft ventingMotor drive for cover plate of process moduleEasy roll exchange by pivoting rails and automatic release of the winders Process control and machine control by universally used PLC Siematic S7 Human Machine Interface with PC and flat panel display.••••••••SMARTWEB —Highest Flexibility, Clean Room Compatibility andMultiprocess Capability。
电力克泰国有限公司产品说明书:电力EME3500SA顶部冰箱-空调

Item PNC ELC Brand Model MarketSPARE PARTS LISTFreestanding fridge-freezers, top freezers3713A 925053050 00 Electrolux EME3500SA VNE Electrolux Thailand Co.,Ltd. 1910 Electrolux Building New Petchburi Rd. Bangkapi HuaykwangBangkok , 10310 Tel : +662 725 9000Publication-No. 130709Freestanding fridge-freezers,top freezersSAFETY WARNINGAlways turn off and unplug the machine before detaching any parts.When servicing machines, do not removeANY detachable parts while the machine is powered. The reason is internal faults may cause shorts to components that are normally at low voltage presenting a shock hazard.A 925053051 00 Electrolux EME3500SA PHH A 925053052 00 Electrolux EME3500SA SGE A 925053053 00 Electrolux EME3500SA MYH A 925053054 00 Electrolux EME3500SA THE A 925053086 00 Electrolux EME3500SA IDHModel : PNC :Ex. View DrawingEME3500SACabinet Assembly49Pos.Part No. DescriptionE M E 3500P N C 9250 E M E 3500P N C 9250E M E 3500P N C 9250E M E 3500P N C 9250 E M E 3500P N C 9250 E M E 3500P N C 92501 811924701CABINET FOAMED MD350 GRVN 1 1 811924601 CABINET FOAMED MD350 GRPH 1 811924501 CABINET FOAMED MD350 GRSG 1 811924401 CABINET FOAMED MD350 GRMY 1 811991901 CABINET FOAMED MD350 GR1 2 811999101 HINGE BOTTOM BASE RIGHT 1 1 1 1 1 1 3 811996201 FEET BASE HINGE 1 1 1 1 1 1 4 811998901 FEET LEVER2 2 2 2 2 2 5 811949503 SCREW TRUSS 4.2x13 6 6 6 6 6 6 6 811999001 FEET BASE1 1 1 1 1 1 7 811943001 SWITCH DOOR TF DOUBLE 1 1 1 1 1 1 8 811943601 SWITCH DOOR2 2 2 2 2 2 9 811981301SUPPORT HEATER MD1 1 1 1 1 811981402 SUPPORT HEATER TF R600a1 10 811981801HEATER DEFROST R134A 240V 1 1 1 1 1 811981701 HEATER DEFROST R600A 240V1 11 811981201COVER HEATER R134A 1 1 1 1 1 811981101 COVER HEATER R600a 1 12 811980401 CLAMP NTC EVAPORATOR 1 1 1 1 1 1 13 811944701 HARNESS THERMO FUSE 1 1 1 1 1 1 14 811948501 CABLE TIES 2.5x1204 4 4 4 4 4 15 811982002 EVAPORATOR 7 PASSES 6.5 1 1 1 1 1 1 16 811981501 RETAINER THERMAL FUSE 1 1 1 1 1 1 17 811974401 SHROUD FAN1 1 1 1 1 1 18 811974301 BRACKET SHROUD FAN 1 1 1 1 1 1 19 811972801 GROMMET FAN SIDE2 2 2 2 2 2 20 1446048 GROMMET , FAN MOUNTING 2 2 2 2 2 2 21 1451299 BLADE ASSY FAN1 1 1 1 1 1 22 811973301MOTOR FAN 240V/50HZ 1 1 1 1 1 811973302 MOTOR FAN 240V/60HZ 1 23 242585005 PCBA MAIN ERF2002 1 1 1 1 1 1 24 811968401 HOUSING BOX PCB 1 1 1 1 1 1 25 811968301 COVER BOX PCB1 1 1 1 1 1 26 811974701COVER EVAPORATOR FRONT TF1 1 1 1 1 1 811971901 COVER EVAPORATOR MD 1 1 1 1 1 1 28 811972601COVER MID CONNECTOR HOUSIN1 1 1 1 1 1 29 811930402 COVER DEODORIZER BLUE3 3 3 3 3 3 30 811972201 DUCT EVAPORATOR REAR MD111111Pos.Part No. DescriptionE M E 3500P N C 9250 E M E 3500P N C 9250E M E 3500P N C 9250E M E 3500P N C 9250 E M E 3500P N C 9250 E M E 3500P N C 925031 811972901 DUCT MID EPS REAR MD 1 1 1 1 1 1 32 811973101 DUCT MID EPS FRONT MD 1 1 1 1 1 1 33 811969301 BAFFLE DOUBLE MD1 1 1 1 1 1 34 811951901 TAPE ALUMINUM EVC REAR MD1 1 1 1 1 1 35 811971601 COVER SCREW5 5 5 5 5 5 36811974201COVER MULTIFLOW FRONT LUX MD S1 1 1 1 1 1 37 811973401 COVER MULTIFLOW SLIDE 1 1 1 1 1 1 38 811973201 COVER MID FRONT MD1 1 1 1 1 1 39 811944801 HARNESS MULTIFLOW TF LUXUR 1 1 1 1 1 1 40 811974001 DUCT MULTIFLOW TF SMALL 1 1 1 1 1 1 41 811930301 DEODORIZER NANO COPPER 1 1 1 1 1 1 42 811943801 PCBA LIGHTING LED HSLB3 3 3 3 3 3 43 811971501 LENS MULTIFLOW TF 1 1 1 1 1 1 44 811971201 LENS FREEZER MD 350 2 2 2 2 2 2 45 811999201 HINGE CENTRE RIGHT 2 2 2 2 2 2 46 811999401 HINGE TOP RIGHT1 1 1 1 1 1 47 811998801 HINGE TOP COVER RIGHT GR 1 1 1 1 1 1 48 811949401 SCREW TRILOB M5x16 8 8 8 8 8 8 49 811942601 HARNESS SENSOR111111Model : PNC :Ex. View DrawingEME3500SACabinet InteriorParts Assembly25Pos.Part No. DescriptionE M E 3500S A P N C 925053050 E M E 3500S A P N C 925053051E M E 3500S A P N C 925053052E M E 3500S A P N C 925053053 E M E 3500S A P N C 925053054 E M E 3500S A P N C 9250530861 811956701 T&S ASSY WHITE 1 1 1 1 1 12 811956801 FRAME ICE T&S 1 1 1 1 1 13 243262600 T&S ICE CUBE TRAY 2 2 2 2 2 24 811957001 SUPPORT ICE T&S 1 1 1 1 1 15 243262903 KNOB ICE T&S WHITE 2 2 2 2 2 26 811956601 BIN ICE1 1 1 1 1 1 7 1451543 SPRING TWIST&SERVE2 2 2 2 2 2 8 811957201 LID FREEZER SHELF 60W LUX 1 1 1 1 1 1 9 811957701 SHELF FZR FOLDABLE FRONT 60W1 1 1 1 1 1 10 811957501 SHELF FZR FOLDABLE REAR60W1 1 1 1 1 1 11 811957901 SHELF FZR ASSY 60W1 1 1 1 1 1 12 811956201 DRAWER MIDDLE BODY MD350 1 1 1 1 1 1 13 811958101 TRAY CHILL ROOM 60W L 1 1 1 1 1 1 14 811955401 SHELF SPLIT ASSY 60W LUX 1 1 1 1 1 1 15 811958701 SHELF FC ASSY 60W1 1 1 1 1 1 16 811959001 COVER CRISPER ASSY 60W 1 1 1 1 1 1 17 807323001 CRISPER BODY 60W LUX 1 1 1 1 1 1 18 811960201 CRISPER FRONT TF 60W 1 1 1 1 1 1 19 811959801 CRISPER HANDLE TF 60W 1 1 1 1 1 1 20 811959601 DIVIDER CRISPER TF 60W 1 1 1 1 1 1 21 811967901 HOUSING PCBA VLIGHT1 1 1 1 1 1 22 807238301 LIGHT GUIDE N-LIGHT 4LED 1 1 1 1 1 1 23 807114501 LENS N LIGHT 4LED 1 1 1 1 1 1 24 807114301 PCB N LIGHT 60W 4LED 1 1 1 1 1 1 25 811956401 SHELF MID ASSY MD350 1 1 1 1 1 1 26 811967801 COVER PCBA VLIGHT 1 1 1 1 1 1 27 811949501 SCREW TRUSS 4.2x35 1 1 1 1 1 1 28 811958501 LID CHILL ROOM 60W1 1 1 1 1 1 29 811956001 DRAWER MIDDLE FRONT MD350 1 1 1 1 1 1 30 811960801 DRAWER HANDLE MID MD350 1 1 1 1 1 1 31 811959201 KNOB HUMIDIFIER111111Model : PNC :Ex. View DrawingEME3500SASystemcompartment Assembly2.1Pos.Part No. DescriptionE M E 3500S A P N C 925053050 E M E 3500S A P N C 925053051E M E 3500S A P N C 925053052E M E 3500S A P N C 925053053 E M E 3500S A P N C 925053054 E M E 3500S A P N C 9250530861 811998401 BASE COMPRESSOR 60W1 1 1 1 1 12 811979402 COMPRESSOR ACC GVY57AG1 811979301 COMPRESSOR ACC HXK95AA 1 811979003 COMPRESSOR WANBAO ASF 1 1 1 1 2.1 807305701 TERMINAL BLOCK ACC1 1 807306201 TERMINAL BLOCK HXK 1 807280401 BLOCK TERMINAL WANBAO 1 1 1 1 3 811978901 GROMMET COMPRESSOR 4 4 4 4 4 4 4 811998601 CLAMP COMPRESSOR2 2 2 2 2 2 5 811978201 CLAMP DRYER 1 1 1 1 1 1 6 811945601 CAPACITOR 4UF1 1 1 1 811945602 CAPACITOR 4UF 4.8mm1 1 7 811943301 POWERCORD REFRIGERATOR VN1 811943401 POWERCORD REFRIGERATOR PH 1 1 811943201 POWERCORD REFRIGERATOR SG 1 1 811943101 POWERCORD REFRIGERATOR TH 1 8 811942901 HARNESS EARTH1 1 1 1 1 1 9 811949301 SCREW TRILOB M3x102 2 2 2 2 2 10 1441189 DRYER1 1 1 1 1 1 11 1401884 TUBE PROCESS2 2 2 2 2 2 12 811983601 TUBE DISCHARG EXTENSION ACC11 1 1 811983501 TUBE DISCHARG EXTENSION ACC2 1 811983301 TUBE DISCHARG EXTENSION WANB 1 1 13 811982501 TUBE SUCTION EXTENSION ACC11 1 1 811982401 TUBE SUCTION EXTENSION ACC2 1 811982201 TUBE SUCTION EXTENSION WANBA 1 1 14 811978101 PAN DRAIN WATER ACC1 1 1 811977901 PAN DRAIN WATER HXK 1 896113194 PAN DRAIN WATER WANBAO 1 1 15 811949401 SCREW TRILOB M5x162 2 22 2 2Model : PNC : Ex. View DrawingEME3500SA Door Assembly5.15.25.36.16.3 6.2Pos.Part No. DescriptionE M E 3500S A P N C 925053050 E M E 3500S A P N C 925053051E M E 3500S A P N C 925053052E M E 3500S A P N C 925053053 E M E 3500S A P N C 925053054 E M E 3500S A P N C 9250530861 811933901 DOOR FOAMED FC MD350 SS 1 1 1 1 1 12 811933701 DOOR FOAMED MID MD350 SS 1 1 1 1 1 13 811934801 DOOR FOAMED FZR MD350 SS 1 1 1 1 1 14 811986804 RAIL DOOR SUPPORT 60W SILV 1 1 1 1 1 1 5.1 811988515 GASKET FC MD350 1 1 1 1 1 1 5.2 811988514 GASKET MID MD350L 1 1 1 1 1 1 5.3 811988502 GASKET FZR TF60W1 1 1 1 1 1 6.1 807439106 HANDLE FC MD ASSEMBLY 1 1 1 1 1 1 6.2 807439105 HANDLE FC MID ASSEMBLY 1 1 1 1 1 1 6.3 807439104 HANDLE FC FZR ASSEMBLY 1 1 1 1 1 1 7 811962002 BIN DOOR BOTTLE ASSY 60W 1 1 1 1 1 1 8 811961501 BIN DOOR FLEX 1/2 ASSY 1 1 1 1 1 1 811961401 BIN DOOR FLEX 2/3 ASSY 2 2 2 2 2 2 9 807489801 TRAY EGG 10 1 1 1 1 1 1 10 811960701 BIN DAIRY ASSY 1 1 1 1 1 1 12 811960601 CLIP BAG DOOR2 2 2 2 2 2 13 811962102 BIN DOOR SHALLOW ASSY 60W 1 1 1 1 1 1 14 811967401 DOOR COMPLETE UI ASSY TF 1 1 1 1 1 1 15 811969601 PCBA UI1 1 1 1 1 1 16 811988701 BEARING AUTO CLOSER R 3 3 3 3 3 3 17 811948801 SCREW COUNTERSUNK M4.8x19 3 3 33 3 3Model : PNC : - 11 -EME3500SA SAFETY WARNINGAlways turn off and unplug the machine before detaching any parts. When servicing machines, do not remove ANY detachable parts while the machine is powered. The reason is internal faults may cause shorts to components that are normally at low voltage presenting a shock hazard.。
爱文海默北美公司电源预算说明书

How Many Batteห้องสมุดไป่ตู้ies Do I Need?
For the EcoTrek Power Modules, for most household functions like watching TV or turning on the lights you only need to have one module turned on. Remember, each EcoTrek BMS uses 60 watts so the fewer you have on, the lower your standby current draw. If you plan to use your air conditioner, microwave or induction stove, you should turn on at least two, if not four, EcoTrek Power Modules.
Run times and energy consumption depend on many factors. For example, your Air Conditioning (A/C) will work much harder in a hot parking lot in 104°F weather in 99% humidity with a filter full of cat hair than it would under a shade tree in 85°F weather with 50% humidity with a new filter.
What Affects Battery Life
There are many factors that affect battery life. Temperature extremes, both hot and cold, the age and condition of the battery, the state of charge and even humidity all affect the life of the battery.
PHOENIX CONTACT VAL-MS 230 ST 高容量变压器保护连接器说明书

Extract from the onlinecatalogVAL-MS 230 STOrder No.: 2798844http://eshop.phoenixcontact.de/phoenix/treeViewClick.do?UID=2798844Surge protection connector type 2 with high-capacity varistor for VAL-MS base element, thermal monitoring, visual fault warning. Design: 230 V AChttp://Please note that the data givenhere has been taken from theonline catalog. For comprehensiveinformation and data, please referto the user documentation. TheGeneral Terms and Conditions ofUse apply to Internet downloads. Technical dataStandardsHousing material PAInflammability class acc. to UL 94V0Color blackStandards for air and creepage distances DIN VDE 0110-1IEC 60664-1: 1992-10VDE 0675-6Degree of protection IP20Mounting type On base elementDesign DIN rail module, two-section, divisible Number of positions1Ambient temperature (operation)-40 °C ... 80 °CFrom SW rev. 1.10Arrester can be tested with CHECKMASTER fromsoftware version:Message: Surge protection fault OpticalDirection of action1L-N/PEWidth17.70 mmHeight54.50 mmLength52.40 mmPitch unit 1 Div.Protective circuitIEC category IIT2EN type T2Nominal voltage U N230 V ACArrester rated voltage U C275 V AC350 V DCNominal frequency f N50 Hz (60 Hz)Ground conductor current I PE≤ 0.3 mAStandby power consumption P C≤ 125 mVAMax. discharge surge current Imax (8/20) µs40 kANominal discharge surge current I n (8/20) µs20 kALightning test current (10/350) µs, peak value l imp 3 kAMax. energy absorption (2 ms)550 JProtection level U p≤ 1.35 kVResidual voltage≤ 1 kV (at 5 kA)≤ 1.15 kV (at 10 kA)≤ 1.35 kV (at In)≤ 950 V (at 3 kA)Response time≤ 25 nsMax. required backup fuse with branch wiring125 A (gL)25 kAShort-circuit resistance I P with max. backup fuse(effective)Capacity 3 nFConnection, protective circuitConnection method FLASHTRAB/VALVETRAB plug-in system connector StandardsStandards/regulations IEC 61643-1 2005EN 61643-11/A11 2007UL 1449 ed. 2Certificates / ApprovalsCertification CB, CCA, CSA, CUL, GOST, KEMA, OEVE, ULAccessoriesItem Designation DescriptionMarking1051993B-STIFT Marker pen, for manual labeling of unprinted Zack strips, smear-proof and waterproof, line thickness 0.5 mm2749589ZBN 18,LGS:ERDE Marking labels, printed horizontally, strips with 5 labels, GND(grounding symbol), color: White2749576ZBN 18,LGS:L1-N,ERDE Marker labels, printed horizontally, strips with 5 labels, L1, L2, L3,N, GND, color: white0800763ZBN 18:SO/CMS Marker labels, 5-section, special printing, labeled according tocustomer requirements (Please specify the required marking withorder), for terminal width: 17.5 mm, color: White2809128ZBN 18:UNBEDRUCKT Unprinted marker labels, strips with 5 labels for individual labelingwith M-PEN or CMS system, for terminal block width: 17.5 mm,color: WhiteAdditional productsItem Designation DescriptionGeneral2817741VAL-MS BE Base element for type 2 arresters of the VALVETRAB MS seriesof products. Design: 1-channel2817738VAL-MS BE/FM Base element for type 2 arresters of the VALVETRAB MS seriesof products, with remote indication contact. Design: 1-channel Diagrams/DrawingsDimensioned drawingCircuit diagramAddressPHOENIX CONTACT Inc., USA586 Fulling Mill Road Middletown, PA 17057,USA Phone (800) 888-7388Fax (717) 944-1625© 2011 Phoenix Contact Technical modifications reserved;。
赛米控丹佛斯 功率组件SKS B2 140 GD 69 12 U-MA PB数据表

Absolute maximum ratings 1)Symbol Conditions Unit I OUT MAX Maximum permanent output current A RMS I IN MAX Maximum permanent input current A DC V OUT MAX Maximum output voltage V AC V BUS MAX Maximum DC Bus voltage V DC F OUT MAX Maximum inverter output frequency HzFSW MAXMaximum switching frequency kHzElectrical characteristics: application example T AMBIENT=40°C unless otherwise specifiedSymbol Conditions min typ max UnitAC phaseV BUS DC bus rated voltage 1 250V DCI OUT RATED Rated output current 1 400A RMSI OUT OVL Overload output current 1 540A RMSt OVL Overload duration60sT OVL Time between 2 overloads10minV OUT Output voltage620690760V ACP OUT Rated output power 1 670kW SEMISTACK® Renewable Energy - Size W2F SW Inverter switching frequency2kHz Two Quadrant 3-phase IGBT inverter F OUT Output frequency50HzPF Power factor-11-P LOSS INV 2)18 200Wη 2)99% Ordering No.08800564Description SKS B2 140 GD 69/12 U - MA PB DC BusV BUS Rated DC voltage applied to the capacitor bank 1 250V DC Features V BUS MAX Max DC voltage applied to the caps bank (max 30% of LTE) 1 300V DCτd5%Discharge time of the capacitors (V DC < 60 V)6min Designed in regard to EN50178 C DC Capacitor bank capacity8,1mF and UL508C recommendations LTE Calculated LTE of the caps with forced air cooling100kh Designed for a 600 x 600 x 2000 mm cabinetEmbedded SKiiP® Technology 4Stack InsulationSKiiP 2414GB17E4-4DUW, Trench 4 1700V IGBT,Crd Minimum creepage distance11mm CAL4 diode Cld Minimum clearance distance9.4mm Integrated current, temperature and voltage sensors Visol Chassis / power stage AC/DC (insulation test voltage DC, 5s)-4 200 4 200V DC Water cooling dv/dt SKiiP driver only, secondary to primary side75kV/µs Typical ApplicationsWind generators (SG and DFIG)Solar InvertersFootnotes1) Absolute maximum ratings are values not to beexceeded in any case and do not imply that the stackcan operate in all these conditions taken together.2) fan consumption and losses in air includedREMARKSB6CISKiiP stackThis technical information specifies semiconductor devices butpromises no characteristics. No warranty or guarantee,expressed or implied is made regarding delivery, performanceor suitability.Values1 4001 300Losses at rated currentEfficiency at rated currentT INLET=45°C, 50% glycol,Flowrate = 16 L/minT J<150°C,ambient air temperature = 40°C,air extraction according to thermaldata page 21 8007601005Environmental conditions T AMBIENT =40°C unless otherwise specifiedCharacteristics Conditions min typ max UnitAmbient temperature3)Humidity Installation altitude without derating1 000m Max installation altitudewith derating4 000m Ingress protection IEC 60529IP00-IEC 60721-3-2, Storage & transportation 2M1-IEC 60721-3-3, in operation 3M3-Pollution degree EN 501782-Thermal data SEMISTACK® Renewable Energy - Size W2∆V /∆t WATER Water flow of the 3-phase inverter81635L/min Two Quadrant 3-phase IGBT inverterWater pressureRated water pressure per inverter 3bar Coolant type Recommended coolant50% glycol / 50% water -Ordering No.08800564T INLETCooling water inlet temperature-204560°C Description SKS B2 140 GD 69/12 U - MA PBRequired cooling airflow Airflow direction bottom to top on snubbers 3)1m.s -1V SUPPLY Fan DC voltage supply162430V DC FeaturesP FAN Fan power consumption at typical voltage supply 90W LTE Capacitor DC fan lifetime expectancy (L10 method)57khDesigned in regard to EN50178and UL508C recommendationsGate Driver Characteristics T AMBIENT =25°C unless otherwise specifiedDesigned for a 600 x 600 x 2000 mm cabinet Symbol Conditions min typ max Unit Embedded SKiiP ® Technology 4Gate Driver / controler data SKiiP 2414GB17E4-4DUW, Trench 4 1700V IGBT,V S supply voltage non stabilized 19.22428.8V CAL4 diodeI S V S2 = 24 V, F SW in kHz, I RMS in A mA Integrated current, temperature and voltage sensors V iT+input threshold voltage HIGH 0.7 V SV Water coolingV iT-input threshold voltage LOW0.3 V SV R IN Input resistance 13k ΩTypical ApplicationsC IN Input capacitance1nFWind generators (SG and DFIG)Measurement & protection Solar InvertersHB_I Analogue current signal HB_I353360367 A.V -1I TRIP SC Over current trip level(I analogue OUT=10V) 3 5253 6003 675A PEAKFootnotesAnalogue temperature signalMin.30 + 11.3xCMN_TEMP °CTyp30 + 12xCMN_TEMP °C 3)the user shall ensure that the ambient air is sufficientlyMax 30 + 12.7xCMN_TEMP °C ventilated to avoid hot spots.T TRIPOver temperature protection 128135142°C CMN_DCL DC-link voltage analog signal 130134138V.V -1V DCtripOvervoltage trip level130013401380VREMARKS85%3-phase inverter, with cable plate terminal and no DC bus connectionCMN_TEMP 340mbar kg106360 + 47×F sw + 0.258×I RMS ClimaticMechanical This technical information specifies semiconductor devices butpromises no characteristics. No warranty or guarantee,expressed or implied is made regarding delivery, performance or suitability.Storage: IEC 60721-3-1, class 1K2Transportation: IEC 60721-3-2, class 2K2Operation: IEC 60721-3-3, class 3K3 extended-2560°C -2055°C IEC 60721-3-3, class 3K3no condensation no icing 5Vibrations & ShocksSKiiP stackB6CI∆P WATERWater pressure drop of the inverter, with male and female connectors, 50% glycol, 16 L/min MassPinSignalRemark 12PWR_V S Power Supply31415PWR_GND Ground for PWR_V S164CMN_DIAG Reserved17CMN_GND Ground for CMN_DIAG, CMN_HALT, CMN_GPIO 5CMN_HALT Digital input/output, bidirectional status signal 18CMN_GPIO Digital input/output, general purpose IO 6CMN_TEMPTemperature signal out19CMN_TEMP_GND Ground for CMN_TEMP 7CMN_DCL DC-link voltage out20CMN_DCL_GND Ground for CMN_DCL 8HB_TOPSwitching signal input for HB high side IGBT 21HB_BOT Switching signal input for HB low side IGBT9HB_RSRVD Reserved22HB_GNDGround for HB_TOP, HB_BOT, HB_RSRVD 10HB_ICurrent sensor out 23HB_I_GND Ground for HB_I11AUX_0A CAN interface INPUT/OUTPUT HIGH 24AUX_0B CAN interface INPUT/OUTPUT LOW 12AUX_1A Reserved 25AUX_1B Reserved 13SHLD_GNDGNDX1U, X1V, X1W Sub-D 25 pin male connectorDC-X1UX1VX1WDC BUS connectionDriver connectorsPhase UPhase VPhase W14DC fan speed controlThis technical information specifies semiconductor devices but promises no characteristics. No warranty or guarantee050010001500200025003000350040000200400600800100012001400M a x c u r r e n t s w i t c h e d (A )DC bus voltage (V)02004006008001000120014001600303540455055O u t p u t c u r r e n t (A R M S )Ambient air temperature (°C)Cooling liquid 45°C Cooling liquid 60°CVdc = 1250 V DC Vac =690 V RMS F OUT = 50 Hz f SW = 2 kHz cos ϕ= 1Flowrate = 16 L/minGlycol/water ratio = 50%Altitude <1000 m02004006008001000120014001600051015A C O u t p u t C u r r e n t (A R M S )AC Fundamental Frequency (Hz)Vdc = 1250 V DC Vac =690 V RMS f SW = 2 kHz cos ϕ= 1Flowrate = 16 L/min Glycol/water ratio = 50%Water temperature = 45°C Air temperature = 40°C T J = 150°C00,0020,0040,0060,0080,010,0120,0140,0160,01805101520253035R t h (°C /W )Flowrate (L/min)Stack Rth 50% glycol (°C/W)Stack Rth 10% glycol (°C/W)020040060080010001200140016001800510152025303540P r e s s u r e d r o p (m b a r )Flowrate (L/min)Pressure drop with 50% glycol (mbar)Pressure drop without glycol (mbar)0200400600800100012001400160005001000150020002500300035004000O u t p u t c u r r e n t (A R M S )Altitude (m)Cooling liquid 45°C, ambient 40°CCooling liquid 60°C, ambient 55°CVdc = 1250 V DC Vac =690 V RMS F OUT = 50 Hz f SW = 2 kHz cos ϕ= 1Flowrate = 16 L/minGlycol/water ratio = 50%。
4500B电源计量器和内置精度校准仪器应用说明书

4500B Power Meter and the Built-In Precision CalibratorApplication NoteMazumder AlamProduct Marketing Manager, Boonton ElectronicsThe internal step calibrator of Boonton 4500B is traceable to NIST (National Institute for Standards and Technology) and it enhances the measurement accuracy. The output of the built-in program-mable calibrator is available from a Type-N connector located on the front of the instrument. This calibrator is used to automatically calibrate sensor offset and linearity, and can also be used as an internal signal source. In order to maintain measurement accuracy, it is always recommended to calibrate the 4500B instrument once in a year.Built-In CalibratorBelow is a brief specification of the internal calibrator of the Boonton 4500B power meter.Operating Modes CW, internal or external pulse Frequency 1.024 GHz ± 0.01%Level Range -50 to +20 dBm Resolution 0.1 dB Output VSWR 1.20 maximumAbsolute Accuracy ±0.065 dB (±1.5%) at 0 dBm Accuracy vs Level add ±0.03 dB per 5 dB increment from 0 dBm Preset Internal Pulse Period 0.1 or 1 or 10 msecPreset Internal Pulse Duty Cycle 10% to 90% in 10% increments Variable Pulse On Time 7 usec to 65.535 msec in 1 usec stepsVariable Pulse Period28 usec to 131.072 msec in 2 usec steps Off-time limits - within 7 usec to 65.535 msecPulse Polarity + or –RF Connector Precision type NExternal Pulse Input Rear panel BNC, TTL level compatibleAuto-CalibrationThe calibrator is used to automatically generate linearity calibration data for peak power sensors.The built-in 1 GHz internal calibrator provides a convenient means for calibrating the sensor. The internal calibrator is used to auto-matically generate linearity calibration data for peak power sen-sors. Before starting any measurement by using the 4500B power meter, the sensor must be connected to the built-in calibrator and need to be calibrated. The internal calibrator has a dynamic range from -50 dBm to +20 dBm. The user-selectable automatic calibra-tion routine has a group of commands which is used to control automatic zero offset and linearity adjustment to the RF power sensor in steps over its full dynamic range.Auto-CalibrationFig. 1: Screenshot of the automatic calibration menu selection for channel 1 on Boonton 4500BThere is a report information available about the installed calibra-tor in the Boonton 4500B power meter. The calibrator information can be retrieved by pressing “Calibrator” > “Extensions” > “Calibra-tor” menu keys. The report includes: Status, Serial Number, Soft-ware Version, Calibration Date and Internal Temperature.Calibrator Report InformationThe internal calibrator of Boonton 4500B power meter has two selectable output modes – CW and Pulse. The calibrator output mode can be set as CW by selecting buttons “Spcl” > “Calibrator” > “Cal Mode” > “CW”. For Pulse mode, the button selection should be as “Spcl” > “Calibrator” > “Cal Mode” > “Pulse”. For each out-put mode, the calibrator output need to be enabled by selecting “Calibrator” > “Cal” > “Output” > “ON”.Calibrator Output ModesSpecifications of the Internal Calibration SourceThe internal calibrator of Boonton 4500B peak power analyzer can be configured as a programmable pulse signal generator in pulse mode, with the options for modulation rate and duty cycle. The preset internal pulse period can be adjusted as 0.1, 1 or 10 msec and the internal pulse duty cycle can be adjusted from 10% to 90% in 10% increments. The pulse measurement can be started by pressing “Esc” button, and then selecting “Measurement” > “Run”, “Measurement Mode” > “Pulse” and finally “Auto-Setup” > “START”. The highlighted automatic measurement parameters in pulse mode are: Pulse width, Risetime, Falltime Period, Duty cycle, Pulse Period, Overshoot. The screenshot of pulse measurements by using the internal calibrator as a internal signal source is shown in Fig. 2Calibrator as an Internal Pulse GeneratorThe 1 GHz internal calibrator can also be driven by an external modulation source. An external pulse generator with TTL compat-ible output must be connected to the rear mounted BNC connector of the 4500B power meter labeled as “EXT PULSE”. The source for the calibrator output pulse modulation can be selected by pressing the “Calibrator” > “Pulse” > “Source” > “Ext” menu key to specify the calibrator output pulse is to be externally generated. Now if the internal calibrator is selected as a “Pulse” mode, the output will be pulse modulated by the external source. Here is the example screenshot of the pulse measurement by using an external TTL compatible pulse signal generator (Fig. 3).Calibrator Driven by anExternal Pulse GeneratorFig 2: Example of pulse signals by using the internal 1 GHz calibrator source as a signal generatorFig 3: Example of a pulse train by using an external TTL compatible signal generator and modulated by the internal calibratorReferences:[1] Boonton 4500B Peak Power Analyzer (/products/power-meters/4500b-peak-power-meter)[2] Boonton 4500B Data Sheet (/~/media/Boonton/Datasheets/4500B_Datasheet_WEB.ashx )[3] Boonton 4500B Instruction Manual (/~/media/Boonton/Manuals%20and%20Software/4500B_Instruction_Manual.ashx)Wireless Telecom Group Inc.25 Eastmans Rd Parsippany, NJUnited StatesTel: +1 973 386 9696 Fax: +1 973 386 9191 © Copyright 2011All rights reserved.Note: Specifications, terms and conditions are subject to change without prior notice.。
Voltech PM6000电源分析仪说明书

V oltech PM6000Power AnalyzerA New Standard in Power AnalysisThe Voltech PM6000 Power Analyzer• Up to 6 wattmeter channels• 0.02% basic accuracy for definitive power loss and efficiency measurements • Sampling at 40MHz (5MHz minimum) for error-free results• Outstanding rejection of common-mode signals for accuracy in all applications • A bright color display and intuitive menu system for ease of use • Connectivity: RS232, Printer, Ethernet, USB* (*Future Release)New generation power analyzer PM6000 has the power to provide:Versatile, accurate, fully-featuredand yet easy-to-useThe PM6000 provides definitive measurements of all electrical power quantities on all products that consume, convert or generate electrical power. The Voltech PM6000 combines years of power measurement know-how with the latest digital signal processing technology to provide a unique combination of measurement and reporting features that will solve power measurement problems.Why the PM6000? There is a constant consumer and legislative pressure to design electrical products that are more efficient, power electronics designers use more and more sophisticated control methods and increases in switching frequency to achieve this. Therefore more sophisticated, more accurate and higher bandwidth power measurements are required to validate and test power electronic designs.The PM6000 has been designed especially to meet the needs of today’s design and test engineers by providing greater flexibility and bandwidth at high accuracy.The PM6000 is an advanced digital sampling power analyzer. From 1 to 6 measurement channels may be fitted to a PM6000. Each measuring channel is a separate wattmeter with fully floating inputs for connection to the voltage and current of the power circuit to be measured.Voltages up to 2000 Vpk may be connected directly to the measurements channels and a wide variety of current transducers may be used, including wide-bandwidth resistive current shunts from Voltech. The Voltech shunts plug directly into the measurement channel for convenience, and have the advantage that the shunt’s calibration data is automatically transferred to the PM6000, providing optimum accuracy for the complete measurement path. For other external current transducers, each channel can supply ±12V DC power. Unique and proprietary algorithms are then used to process the samples and provide stable and accurate measurements in all applications.MeasurementsFront PanelThe intuitive menu system will guide you through the set-up and control of the analyzer. Working through the options step-by-step allows you to configure channels into groups for a variety of multi-phase connections, to set scaling for external voltage and current transducers, and to choose the required measurements.Rear PanelAt the rear, comprehensive control is provided via RS232. Standard printers may be connected directly for local print-out of numeric results.The ethernet port allows for powerful control and datalogging to a network drive.Set-Up and Controlcontrolfunction keysAdvantages• U p to six channels configurable as required, for example AC input plus 5 DC outputs or three-phase input and output.• Excellent 0.02% basic accuracy - useful for high efficiency measurements.• Accurate on all waveforms.• Samples continuously, without gaps at 5 MSPS so there is no missing dataduring integration or low-power standby measurements.Power transformers are characterized under open-circuit and short-circuit conditions. Open-circuit, the power factor of the transformer is closeto zero (<0.01), which demands very low phase error, from the power analyzer.The analog design of the PM6000 ensures that its voltage and current channels are carefully matched, providing optimum performance at low power factors.Applications - Power TransformersAdvantages• Up to six channels for simultaneous three-phase input and output – Star (Wye) or Delta connection.• Accurate at low power factors. (<0.01)• Simultaneous measurement of rms and mean voltage as required by IEC76 and IEEEC57.• Measure turns ratio directly using the math function.MeasurementsWatts, Vrms, Vrmn, Arms, VA, VAr, Apk, Harmonics, THD, Inrush.K-factor and corrected power to IEEE and IEC standards.Applications – Variable Frequency Drivesand MachinesThe versatile PM6000 will make simultaneous measurements at the input and output of a drive, allowing accurate efficiency measurements under all load and speed conditions.Advantages• Up to six channels configurable as required, for example 3 wattmeter, three- phase input, DC bus and two-wattmeter drive output and torque and speed measured simultaneously.• Excellent 0.02% basic accuracy - useful for high efficiency measurements.• 10MHz bandwidth captures all motor frequency and high-frequency data for the most accurate overall power measurement.• High rejection of common-mode signals found on the drive output. 140dB @ 60Hz, 95dB@1MhzMeasurementsApplications - Power Integration / StandbyThe power consumption of everyday home and office electrical appliances is of importance to consumers and generators of electricity alike.When the power consumption varies over time, then integration of the power ( W-h integration) is required. The PM6000 provides comprehensive integration features suitable for Energy Star measurements and for low-power measurements in accordance with international directives, eg. IEC 62301 which also requires crest factor measurements up to 8 and 50 harmonics.Advantages• Excellent 0.02% basic accuracy - useful for high efficiency measurements.• Accurate on all waveforms.• Samples continuously, without gaps at 5 MSPS so there is no missingdata during integration or low-power standby measurements.• Versatile current channel input for low – current measurements. 1A Voltech plug-in shunt available.MeasurementsIEC 62301Voltech continues to be a leader in producing power analyzers that meet the ever changing needs of today’s world. A mandatory measurement for products in Europe and many other countries, the IEC standards definespecific methods for testing current harmonics and flickerApplications - IEC Harmonics and FlickerAdvantages.• F ull compliance testing for EMC laboratories when used with an AC Source and Impedance Network.• S uperb pre-compliance measurements when used stand-alone.• P C software plays back previous tests and generates reports suitable for technical construction files.• D iscrete Fourier Transform (DFT) ‘reference instrument’ implementation avoids the problems of Fast Fourier Transform (FFT) analyzers.• S olutions for harmonics and flicker to 75A.(voltage changes). The PM6000 and its easy-to-use software provide design engineers and EMC test laboratories with a comprehensive suite of measurements and reports that fully comply with the latest standards.To measure the efficiency of a high-frequency ballast, its essential tohave an accurate measurement of both the input and output power of the ballast. With unbeatable accuracy at both low and high frequencies, and superior common-mode rejection, the PM6000 will make the most accurate efficiency measurements possible.Applications - Lighting BallastsPurposely designed for lighting applications, this device overcomes problems that are usually found when using conventional or Hall effect CTs.• Convenient: No need to feed cables through a CT core. • Better than 1% accuracy: Trifilar wound toroidal core.• 5kHz to 1MHz bandwidth . • 5mA to 1A measurement rangeAccessoriesPM6000 Back Panel with 6 channels and 3 Voltech 30A shunts fitted.• Accuracy better than 1%• Connect to the PM6000 via safety leads and 1A shunt • CL100 100A:1A • CL1000 1000A:1A• Accuracy (23°C ± 5°C): ± 0.2% of specified ratio • Frequency range: 45Hz to 1kHz• Current range: 100:1 ratio: 10A to 120A rms 1000:1 ratio: 100A to 1200A rms• Maximum input current: 1000A continuous 2000A for 1 hour • Phase error (23°C ± 5°C): Better than ± 0.1° at 50HzSolid-state switch for energizing loads (up to 200Apk) at either the peak or the zero crossing of AC voltage. Ideal for inrush current testing.Clamp-on Current TransformersCT1000 –Dual Ratio Precision Current TransformerPS1000 - Inrush SwitchBallast CTPM6000 ChassisWith color VGA display and 3½” floppy drive. Connectivity: RS232, Printer, Ethernet, USB*(*Future Release)Hard Disk Drive (Optional)PM6000 Measurement ChannelHigh performance wattmeter channel. Voltage 1500V , Current 2.5V for shunt or current transducer. ±12V DC supply for external current transducer.OrderingVoltageCurrentPower1. At 23ºC ± 5ºC, valid 1 year from calibration.2. %rdg = percentage of reading, % rng = percentage of range, F = frequency in kHz.3. Vrng = Voltage range: 5, 10, 20, 50, 100, 200, 500, 1000, 2000Vpk.4. Irng = Current range.30A shunt: 0.5, 1, 2.5, 5, 10, 20, 50, 100, 250Apk.1A shunt: 0.01, 0.02, 0.05, 0.1, 0.2, 0.5, 1.0, 2.0, 5.0Apk.Voltage input: 0.005, 0.010, 0.025, 0.05, 0.10, 0.25, 0.50, 1.0, 2.5Vpk.1A Shunt1A rms, 5Apk precision measuring shunt withcalibration stored in EEPROM. (Bandwidth 10MHz)30A shunt30A rms, 200Apk precision measuring shunt with calibration stored in EEPROM. (Bandwidth 1MHz)Lead set2 pairs (yellow and black) 1.5m, 2000V , 30A leads with safety connectors and alligator clips.Magnitude(V)=0.02%rdg +0.05%rng +(0.001%x F )rdg +20mVPhase (º)=0.005+ 0.0003x + +(0.001xF)][V rng V 0.05VMagnitude(A)=0.02%rdg +0.05%rng +(0.001%x F )rdg +20uVZ EXTPhase (º)=0.0025+ 0.0005x + +(0.0006x F)][I rng I0.00004IxZ EXT Specifications5. Ø = angle between voltage and current.6. Zext = 0.01 (30A shunt), 0.5 (1A shunt), 0.0125 (default voltage input) ohms.Voltech Instruments Inc.11637 Kelly Road, Suite 306Fort Myers, FL 33908USATel: (239) 437 0494Fax: (239) 437 3841**********************Voltech has an intensive program of design and development andreserves the right to alter product specification without notice. Although every care has been taken in compiling this information Voltech does not accept any liability for errors or omissions. ©2006 Voltech.Voltech Instruments Ltd.148 Harwell Int’l Business Centre Didcot, Oxon. OX11 0RA UKTel: +44 (0) 1235 834555Fax: +44 (0) 1235 835016Email:****************.ukV oltechDistributorVPN: 86-506/9Error(Watts)= + + (tan 0x(Vh1Ph error+Ah1Ph error ) x ) x W [V RMS V RMS error A RMSA RMS error]180 π。
赛米控丹佛斯电子 Board_93_GB_SKYPER_42_R 数据表

®Adaptor boardIGBT Driver CoreBoard 93 GB SKYPER 42 R Preliminary Data Features•Two output channels •Gold nickel finish •Failure managementTypical Applications*•Adaptor board for SKYPER 42 IGBT drivers in bridge circuits for industrial applications •PCB with gold plating •DC bus up to 1200VFootnotesIsolation test voltage with external high voltage diodeThe isolation test is not performed as a series test at SEMIKRONThe driver power can be expanded to 50µC with external boost capacitorsIsolation coordination in compliance with EN50178 PD2Operating temperature is real ambient temperature around the driver core Degree of protection: IP00This is an electrostatic discharge sensitive device (ESDS), international standard IEC 60747-1, Chapter IX* The specifications of our components may not be considered as an assurance of component characteristics. Components have to be tested for the respective application. Adjustments may be necessary. The use of SEMIKRON products in life support appliances and systems is subject to prior specification and written approval by SEMIKRON. We therefore strongly recommend prior consultation of our staff.Absolute Maximum Ratings SymbolConditionsValuesUnitV s Supply voltage primary 16V Iout PEAK Output peak current 30A Iout AVmax Output average current 150mA f max Max. switching frequency100kHz V CECollector emitter voltage sense across the IGBT1700V V isol IO Isolation test voltage input - output (AC, rms, 2s)4000V V isolPD Partial discharge extinction voltage, rms, Q PD ≤ 10pC1500V V isol12Isolation test voltage output 1 - output 2 (AC, rms, 2s)1500V R Gon min Minimum rating for external R Gon 0.8ΩR Goff min Minimum rating for external R Goff 0.8ΩT op Operating temperature -40...85°C T stgStorage temperature-40 (85)°CCharacteristics SymbolConditionsmin.typ.max.UnitV s Supply voltage primary side 14.41515.6V V i Input signal voltage on / off 15 / 0V V IT+Input treshold voltage HIGH 12.3V V IT-Input threshold voltage (LOW) 4.6V V G(on)Turn on output voltage 15V V G(off)Turn off output voltage-8V t d(on)IO Input-output turn-on propagation time 1.1µs t d(off)IOInput-output turn-on propagation time1.1µsAdaptor Board 93 SKYPER® 42 RTechnical ExplanationsRevision 04------------------------------------------------------------------------------------------------------------------------------------------------------------------------------------------ This Technical Explanation is valid for the following parts:Related documents:Prepared by: Johannes Krapp------------------------------------------------------------------------------------------------------------------------------------------------------------------------------------------ ContentApplication and Handling Instructions (2)Further application support (2)General Description (2)Dimensions (3)PIN Array (3)Setting Dynamic Short Circuit Protection (4)Collector Series Resistance (4)Adaptation Gate Resistors (5)Boost Capacitors (6)Environmental conditions (6)Mounting Notes (6)Please note:All values in this technical explanation are typical values. Typical values are the average values expected in large quantities and are provided for information purposes only. These values can and do vary in different applications. All operating parameters should be validated by user’s technical experts for each application.Application and Handling Instructions▪Please provide for static discharge protection during handling. As long as the hybrid driver is not completely assembled, the input terminals have to be short-circuited. Persons working with devices have to wear a grounded bracelet. Any synthetic floor coverings must not be statically chargeable. Even during transportation the input terminals have to be short-circuited using, for example, conductive rubber. Worktables have to be grounded. The same safety requirements apply to MOSFET- and IGBT-modules.▪Any parasitic inductances within the DC-link have to be minimised. Over-voltages may be absorbed by C- or RCD-snubber networks between main terminals for PLUS and MINUS of the power module.▪When first operating a newly developed circuit, SEMIKRON recommends to apply low collector voltage and load current in the beginning and to increase these values gradually, observing the turn-off behaviour of the free-wheeling diode and the turn-off voltage spikes generated across the IGBT. An oscillographic control will be necessary. Additionally, the case temperature of the module has to be monitored. When the circuit works correctly under rated operation conditions, short-circuit testing may be done, starting again with low collector voltage.▪It is important to feed any errors back to the control circuit and to switch off the device immediately in failure events.Repeated turn-on of the IGBT into a short circuit with a high frequency may destroy the device.▪The inputs of the hybrid driver are sensitive to over-voltage. Voltages higher than V S +0,3V or below -0,3V may destroy these inputs. Therefore, control signal over-voltages exceeding the above values have to be avoided.▪The connecting leads between hybrid driver and the power module should be as short as possible (max. 20cm), the driver leads should be twisted.Further application supportLatest information is available at . For design support please read the SEMIKRON Application Manual Power Modules available at .General DescriptionThe Board 93 GB SKYPER® 42 is an adaptor board for the IGBT module SKiM® 93 (spring contact). The board is paralleling three channels so the SKiM module can be used in half bridge configuration. The board can be customized allowing adaptation and optimization to the used IGBT module.The switching characteristic of the IGBT can be influenced through user settings, e.g. changing turn-on and turn-off speed by variation of R Gon and R Goff. Furthermore, it is possible to adjust the monitoring level and blanking time for the DSCP (see Technical Explanations SKYPER® 42 R).Please note:This technical explanation is based on the Technical Explanations for SKYPER®42 R. Please read the Technical Explanations SKYPER® 42 R before using the Adaptor Board.Dimensions116 PIN ArraySetting Dynamic Short Circuit ProtectionThe Vce formula for the Vce monitoring is described in the technical explanation of SKYPER 42 R. Collector Series ResistanceDesignation Shape SettingR105 MiniMELF (SMD) R VCE*Factory setting: not equippedTOPR205 MiniMELF (SMD) R VCE *Factory setting: not equippedBOTAdaptation Gate ResistorsBoost CapacitorsEnvironmental conditionsPlease refer to the technical explanation of SKYPER 42 R for the environmental conditions.Mounting NotesDISCLAIMERSEMIKRON reserves the right to make changes withoutfurnished in this document is believed to be accurate and reliable. However, no representation or warranty is given and no liability is assumed with respect to the accuracy or use of such information. SEMIKRON does not assume any liability arising out of the application or use of any product or circuit described herein. Furthermore,。
贝利尼瓦斯3500 53电子超速检测系统说明书
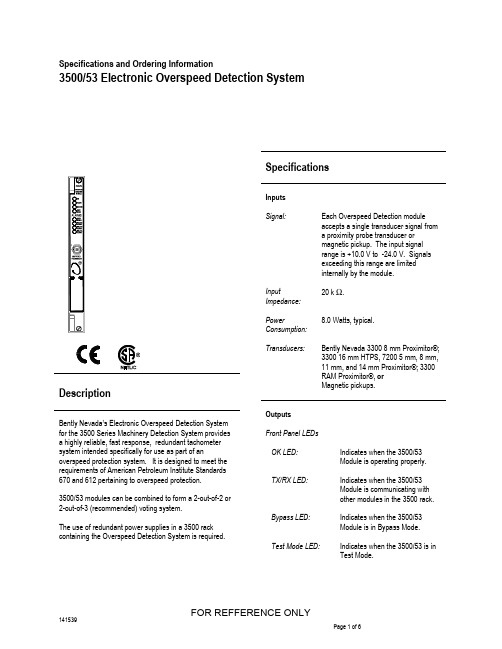
Specifications and Ordering Information3500/53 Electronic Overspeed Detection SystemDescriptionBently Nevada’s Electronic Overspeed Detection System for the 3500 Series Machinery Detection System provides a highly reliable, fast response, redundant tachometer system intended specifically for use as part of anoverspeed protection system. It is designed to meet the requirements of American Petroleum Institute Standards 670 and 612 pertaining to overspeed protection.3500/53 modules can be combined to form a 2-out-of-2 or 2-out-of-3 (recommended) voting system.The use of redundant power supplies in a 3500 rack containing the Overspeed Detection System is required.RAM Proximitor®, or Magnetic pickups.OutputsFront Panel LEDs OK LED:Indicates when the 3500/53Module is operating properly.TX/RX LED:Indicates when the 3500/53Module is communicating with other modules in the 3500 rack.Bypass LED:Indicates when the 3500/53Module is in Bypass Mode.Test Mode LED:Indicates when the 3500/53 is in Test Mode.Alarm LEDs:Indicates that an alarm conditionhas occurred with the associatedrelay.Buffered Transducer Outputs:The front of each module has one coaxial connector for buffered output. Each connector is short circuit and ESD protected.Output Impedance:550 Ω.Transducer PowerSupply:-24 Vdc, 40 mA maximum.Recorder:+4 to +20 mA. Values areproportional to module full-scalerange (rpm). Module operation isunaffected by short circuits onrecorder output.Voltage Compliance (current output):0 to +12 Vdc range across load. Load resistance is 0 to 600 Ω.Resolution:0.3662 µA per bit ±0.25% error atroom temperature ±0.7% errorover temperature range. Updaterate approximately 100 ms. RelaysType:Single-pole, double-throw (SPDT)relays.EnvironmentalSealing:Epoxy sealed.Arc Suppressers:250 Vrms, installed as standard. Contact RatingsMax switched power:dc: 120 W ac: 600 VA.Resistive LoadMax switchedcurrent:5AMin switchedcurrent:100 mA @ 5 VdcMax switched voltage:dc: 30 Vdcac: 250 Vac.Contact Life:100,000 @ 5 A, 24 Vdc or 120Vac.Operation:Each relay is switch selectable forNormally De-energized orNormally Energized.Signal Conditioning Specified at +25°C (+77° F).Frequency ResponseSpeed Input:The 3500 Overspeed ProtectionModule will support from 1 to 255events per revolution with amaximum full-scale range of99,999 rpm and a maximum inputfrequency of 20 kHz. Minimuminput frequency for proximitytransducers is 0.0167 Hz (1 rpmfor 1 event/revolution) and forpassive magnetic pickups is 3.3Hz.RPM Accuracy:Less than 100 rpm = ± 0.1 rpm,100 to 10,000 rpm = ±1 rpm,10,000 to 99,999 rpm = ± 0.01%.Transducer ConditioningAuto Threshold:Use for any input above 0.0167Hz (1 rpm for 1 event/revolution).Minimum signal amplitude fortriggering is 1 volt peak-to-peak.Manual Threshold:User selectable from +9.9 Vdc to-23.9 Vdc. Minimum signalamplitude for triggering is 500millivolts peak-to-peak.Hysteresis:User selectable from 0.2 to 2.5volts.AlarmsAlarm Setpoints:Under and Over Alert levels(setpoints) can be set for speed.In addition, a Danger (Overspeed)setpoint can be set for speed. Allalarm setpoints are set usingsoftware configuration. Alarmsare adjustable and can normallybe set from 0 to 100% of full-scaleof speed full-scale range.Alarm Time Delays:Less than 30 ms above 300 Hz. Proportional Values Proportional values are speedmeasurements used to monitor amachine. The OverspeedDetection Module returns thefollowing proportional values: OverspeedSpeed:The primary value for thechannel. This value can beincluded in contiguous registers inthe Communications GatewayModule.Peak Speed:Peak Speed proportional valuesare for display purposes only. Noalarming is provided for PeakSpeed.Environmental LimitsOperating Temperature:-30°C to +65°C (-22°F to +149°F)Storage Temperature:-40°C to +85°C (-40°F to +185°F)Humidity:95%, non-condensing. CE Mark DirectivesEMC Directives:EN50081-2:Radiated EmissionsEN 55011, Class AConducted EmissionsEN 55011, Class AEN50082-2:Electrostatic DischargeEN 61000-4-2, Criteria BRadiated SusceptibilityENV 50140, Criteria AConducted SusceptibilityENV 50141, Criteria AElectrical Fast TransientEN 61000-4-4, Criteria BSurge CapabilityEN 61000-4-5, Criteria BMagnetic FieldEN 61000-4-8, Criteria APower Supply DipEN 61000-4-11, Criteria BRadio TelephoneENV 50204, Criteria BLow Voltage Directives:EN 61010-1Safety RequirementsHazardous Area ApprovalsCSA/NRTL/C:Class I, Division 2, Groups Athrough D.PhysicalMonitor ModuleDimensions (Heightx Width x Depth):241.3 mm x 24.4 mm x 241.8 mm(9.50 in x 0.96 in x 9.52 in). Weight:0.82 kg (1.8 lbs.).I/O ModulesDimensions (Heightx Width x Depth):241.3 mm x 24.4 mm x 99.1 mm(9.50 in x 0.96 in x 3.90 in). Weight:0.45 kg (1.0 lb.).Rack Space RequirementsMonitor Module: 1 full-height front slot/per channel. I/O Modules: 1 full-height rear slot/per channel.Ordering ConsiderationsGeneralIf the 3500/53 is added to an existing 3500 Systemthe following firmware and software versions (orlater) are required:3500/20 Module Firmware – Revision G3500/01 Software – Version 2.003500/02 Software – Version 2.033500/03 Software – Version 1.13The use of redundant power supplies in a 3500rack containing the Overspeed Detection System isrequired.Ordering InformationElectronic Overspeed Detection System3500/53-AXX-BXXOption DescriptionsA: Channel Option0 2 Two Channel System0 3 Three Channel SystemB: Agency Approval Option 0 0 None0 1 CSA/NRTL/CSpares133388-013500/53 Overspeed DetectionModule133396-01Overspeed Detection I/O Module04425545Grounding Wrist Strap (single use)04400037IC Removal Tool134129-01Firmware IC00580438Connector Header, InternalTermination, 4-position, Green00580436Connector Header, InternalTermination, 6-position, Green00580432Connector Header, InternalTermination, 10-position, Green134939-013500/53 Overspeed DetectionManualFigures and Tables3) Buffered transducer output. Provides an unfiltered output for the transducer.The output is short-circuit protected.4) I/O Module, rear view.Front and rear view of the Electronic Overspeed Detection ModuleMaximum Switching CapacityMaximum Switching Capacity2)Current (AdcAll data is subject to change without notice1999 Bently Nevada Corporationused in this document are registered marks of Bently Nevada Corporation。
PowerVerter Ultra-Compact 12V DC输入和120V AC输出端口的可移植

PowerVerter Ultra-Compact InverterPortable Power for All ApplicationsModel #: PV37512V DC input; 120V AC output; 2 outlets375 watts continuous output600 watts peak outputConvenient cigarette lighter plugDESCRIPTIONHarness your vehicle's battery to efficiently power office equipment on the road. Continuously supplies up to 375 watts of 120V AC power to 2 AC outlets from any 12V battery or automotive DC source. Convenient cigarette lighter DC input jack with 3-ft. cable provides 1-step installation. Portable and compact, the inverter's design is among the most rugged available thanks to its lightweight metal casing.KEY BUYING POINTSAllows users to run AC appliances from any 12V cigarette lighter socketConverts 12V DC battery power to 120V AC power375 watts continuous output power; 600 watts peak output power2 outlets3-ft. cord with cigarette lighter plugUltra compact, lightweight design with all-metal housingLow battery alarm with auto-shutoff preserves vehicle batteryOverload alarm with auto-shutoff prevents wattage overloadReplaceable fuse protects inverter from overloadLighted power switch1 year manufacturer's product warrantyTYPICAL APPLICATIONSIdeal for laptop computers, portable electronics, battery chargers for cell phones, pagers, notepads, game systems, personal printers and battery rechargers for small battery-operated power tools, portable TV-VCR-stereo systems, camcorders, lighting and other low-power applications under 375 watts.PACKAGE INCLUDESPV375 InverterWarranty informationInstruction manualCOMPLETE SPECIFICATIONSSystem overview:Compact 12 volt DC to 120 volt AC power inverter. 375 watts continuous / 600 watts peak.Cigarette lighter input jack, 2 AC outlets.Voltage compatibility:Compatible with 12V DC automotive systemsFrequency compatibility:60 HzOutput watt capacity (watts):375 watts continuous, supports peak output up to 600 watts for up to 500 milliseconds Output nominal voltage:120V nominalOutput voltage regulation:Maintains PWM sine wave output voltage of 115 V AC (+/- 8 V AC)Output frequency regulation:60 Hz (+/- 3 Hz)Outlet quantity / type:Includes 2 NEMA 5-15R output receptaclesOverload protection:Via 40A automotive input fuseMaximum input amps / watts:Full continuous load - 40A at 12V DC, No load - 0.65A at 12V DCInput connection type:12V DC cigarette lighter input plug connectionInput cord length: 3 ft. hardwire input cable, 16 gauge, 2 wireDC system voltage:DC input operating range 10-15V DC. Alarm sounds as voltage drops to 10.5V. Auto-shutdown occurs at 10V.Alarms:Dual function alarm indicates overload conditions or low DC input voltage of 10.5V or less. Switches:Lighted on/off power switchShipping weight (lbs): 2.3Shipping weight (kg): 1.04Unit weight (lbs): 2.2Unit weight (kg):0.99Unit Dimensions (HWD/in): 2 x 4.25 x 7Unit Dimensions (HWD/cm): 5 x 10.8 x 17.8Shipping Dimensions (HWD/in):11.5 x 7.3 x 2.2Shipping Dimensions (HWD/cm):29.2 x 18.54 x 5.59Material of construction:Aluminum / sheet metalCooling method:FanOperating Temperature:32-104 Fahrenheit / 0-40 CelciusRelative Humidity:0-95% non-condensingProduct warranty: 1 year (Outside the U.S. and Canada, call for warranty information)Appearance:Attractive, rugged, metallic blue color inverter systemThe policy of Tripp Lite is one of continuous improvement.Specifications are subject to change without notice. Therefore, your product may vary slightly from what is currently listed.Tripp Lite World Headquarters1111 W. 35th StreetChicago, IL 60609 USACustomer Support(773) 869-1234© 2003 Tripp Lite. All Rights Reserved.。
Amantys加快在中国的发展

P o we r D r i v e 系列I GB T 驱动 器 住 中 国的 销 售 ,各
Ama n t y s 市场 营销副总 裁S t e v e E v a n s 表
分 销 商将 提 供 采 用 多种 封 装 类 型 和 _ ¨ I : 作 电 压 覆 示 : “ 自我 们 的 上 海 办 事 处 开 业 以 来 ,为 了 曼
C删
I 技ቤተ መጻሕፍቲ ባይዱ前沿 l F r o n t i e r T e c h n o l o g y
其 它 处理 器 , I | I 让 系统 节 能 的 范 围更 宽 广 。
・
中接口。
闲置模式
DSP 和 实 时 处 理 器 可 提 供 高 效 的 多模 式 支
在这 种 场 景 中 ,UE 没 有 任 何 主 动 的 数 据 会 话 持 ,并 在 同 一内 核 支 持 2 G 、3 G、 L TE 与L TE — ( A c t i v e D a t a S e s s i o n ) ,但 是数据 会话 保 留在 网 络上 执 Ad v a n c e d 的通 用 架 构 ,为 促 进 多模 式 运 作 ,覆 盖
将 伴 随L T E 继 续 存 在 许 多年 。
支 持 实 时 追 踪 等 功 能 。 利 用 多 内 核 除 错 器 ,DS P
与 实时 处 理 器支 持 全 面 的 共 除 错 ( C o — d e b u g g i n g ) 功
随 着L TE 标 准 继 续 演 进 ,I H的 3 G网络 还会 支 能 ,以 简化 S o C设 计 。
行 定 期 同步/ 化 置 更新 操作 , 由于L T E 标 准 是 包括 节 各 自 的 基 频 ,调 制 解 调 器 需 要 更 大 的 数 据 和 可 编
- 1、下载文档前请自行甄别文档内容的完整性,平台不提供额外的编辑、内容补充、找答案等附加服务。
- 2、"仅部分预览"的文档,不可在线预览部分如存在完整性等问题,可反馈申请退款(可完整预览的文档不适用该条件!)。
- 3、如文档侵犯您的权益,请联系客服反馈,我们会尽快为您处理(人工客服工作时间:9:00-18:30)。
Amantys 针对高功率模块的4500V Amantys Power DriveTM 驱动器进入中国市场
4.5kV 栅极驱动器可满足电力机车、风力发电机组、高压直流和工业
驱动应用不断增长的高压IGBT 市场需求
中国上海和英国剑桥2013 年10 月22 日– Amantys 今日宣布推出一款针对高功率模块的全新绝缘栅双极晶体管(IGBT)栅极驱动器,其
工作电压为4500V,额定电流从400A 至1200A,它专为支持包括ABB、Dynex、日立、英飞凌和三菱等制造商的模块产品而设计。
这一全新的Amantys IGBT 栅极驱动器集成了Amantys Power InsightTM 状态监测硬件和软件子系统,用以观察和报告关键性的电源开关特性。
基于通过设计简化电源的理念,Amantys 电源驱动器实现了完全集成,。