无头铆钉双面鼓形镦头成形工艺与性能分析
铆接技术原理与工艺特点

铆接技术原理与工艺特点关于铆接技术一、铆接技术原理与工艺特点常见的铆接技术分为冷铆接和热铆接,冷铆接是用铆杆对铆钉局部加压,并绕中心连续摆动或者铆钉受力膨胀,直到铆钉成形的铆接方法。
冷铆常见的有摆碾铆接法及径向铆接法。
摆碾铆接法较易理解,该铆头仅沿着圆周方向摆动碾压。
而径向铆接原理较为复杂,它的铆头运动轨迹是梅花状或者说是以圆为中心向外扩展的,铆头每次都通过铆钉中心点。
冷铆接最常见的铆接工具有铆接机,压铆机,铆钉枪和铆螺母枪,铆钉枪和铆螺母枪是最常见单面冷铆接所用的工具。
这是冷铆接工艺中最具代表性的冷铆接方法,因为使用方便,也只需在工件的一侧进行铆接,相对双面铆接的铆钉锤来说更方便。
就两种铆接法比较而言,径向铆接面所铆零件的质量较好,效率略高,并且铆接更为稳定,铆件无须夹持,即使铆钉中心相对主轴中心略有偏移也能顺利完成铆接工作。
而摆碾铆接机必须将工件准确定位,最好夹持铆件。
然而径向铆接机因结构复杂,造价高,维修不方便,非特殊场合一般不采用。
相反地,摆碾铆接机结构简单,成本低,维修方便,可靠性好,能够满足90%以上零件的铆接要求,因而受到从多人士的亲睐。
此外,利用摆碾铆接的原理,还可以制造适宜于多点铆接的多头铆接机,在现代工业生产中有其独特的优势。
热铆接是将铆钉加热到一定温度后进行的铆接。
由于加热后铆钉的塑性提高、硬度降低,钉头成型容易,所以热铆时所需的外力比冷铆要小的多;另外,在铆钉冷却过程中,钉杆长度方向的收缩会增加板料间的正压力,当板料受力后可产生更大的摩擦阻力,提高了铆接强度。
热铆常用在铆钉材质塑性较差、铆钉直径较大或铆力不足的情况下。
冷铆接法是以连续的局部变形便铆钉成形,其所施压力离铆钉中心越远越大,这恰恰符合材料变形的自然规律。
因此,采用冷铆接技术所需设备小,节省费用。
能提高铆钉的承载能力,强度高于传统铆接的80%。
铆钉材料具有特别好的形变性能,铆杆不会出现质量问题,寿命较高,同时,只要改变铆头(不同的接杆和不同的铆接配件铆螺母铆钉等)的形状,就可以铆接多种形状。
冷铆技术介绍终稿
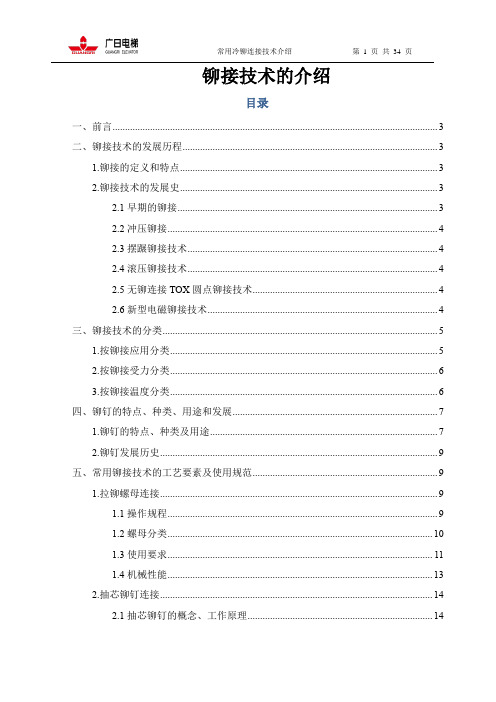
铆接技术的介绍目录一、前言 (3)二、铆接技术的发展历程 (3)1.铆接的定义和特点 (3)2.铆接技术的发展史 (3)2.1早期的铆接 (3)2.2冲压铆接 (4)2.3摆蹍铆接技术 (4)2.4滚压铆接技术 (4)2.5无铆连接TOX圆点铆接技术 (4)2.6新型电磁铆接技术 (4)三、铆接技术的分类 (5)1.按铆接应用分类 (5)2.按铆接受力分类 (6)3.按铆接温度分类 (6)四、铆钉的特点、种类、用途和发展 (7)1.铆钉的特点、种类及用途 (7)2.铆钉发展历史 (9)五、常用铆接技术的工艺要素及使用规范 (9)1.拉铆螺母连接 (9)1.1操作规程 (9)1.2螺母分类 (10)1.3使用要求 (11)1.4机械性能 (13)2.抽芯铆钉连接 (14)2.1抽芯铆钉的概念、工作原理 (14)2.2铆钉的国标、规格、性能等级 (15)2.3抽芯铆钉的种类、适用范围 (16)2.4抽芯铆钉的选用规则 (18)2.5抽芯铆钉在使用时容易出现的问题与解决方法 (20)2.6铆钉与铆枪的气压关系 (21)3.无铆连接 (21)3.1定义、形式 (21)3.2无铆连接接的工艺过程 (23)3.3无铆连接铆点的主要参数 (25)3.4影响连接性能的因素 (27)3.5无铆连接应用及使用规范 (28)4.锁铆连接 (29)4.1工作原理和工艺过程 (29)4.2锁铆链接点质量的影响因素 (30)4.3锁铆链接的技术优势 (30)4.4锁铆连接设备 (30)4.5锁铆连接的应用 (31)六、铆接结构的工艺知识与结构应用 (31)1.铆接结构的工艺知识 (31)2.铆接结构的应用 (33)一、前言铆接技术是当今世界机械连接的先进技术之一,在电梯行业中也得到广泛的运用。
拉铆螺母连接、抽芯铆钉连接、锁铆连接、无铆连接为我司常用的铆接技术。
本文通过介绍以上铆接技术的分类、工艺要素以及使用规范等各方面的要求,为产品设计、产品制造、产品结构优化提供技术指导或使用规范参考,从而提升我司产品的质量和效率。
飞机装配工艺学224

第三章 铆接和铆接结构装配普通铆接概述一、普通铆接的概念和过程普通铆接是指常用的凸头或埋头铆钉铆接,铆接过程为:制铆钉孔-制埋头窝-放铆钉 -铆接。
见课本图。
二、普通铆接的缺点增加了结构重量;降低了强度,容易引起变形;疲劳强度低;密封性能差。
导致其它连接方法迅速发展,如胶接,点焊和胶接点焊等三、铆接的优点连接强度比较稳定;容易检查和排除故障(与胶接焊接比较);使用工具比较简单,价廉; 适用于比较复杂的结构的连接。
四、铆接的发展1.无头铆钉干涉配合铆接技术可以提高接头的疲劳寿命,满足现代飞机的疲劳性能和密封 性要求。
2.各种形式的自动钻孔设备和铆接设备为不断提高铆接的机械化和自动化程度,提高铆接 质量提供了条件。
第一节 普通铆接工艺过程一、钻孔和锪窝1.对铆钉孔的要求1.1 铆钉孔的质量要求孔径公差 1.2 孔的椭圆度 1.3孔的垂直度 1.4孔边毛刺 1.5 孔的粗糙度1.2 不同直径的铆钉孔的加工方法d<5mm 钻孔、扩孔; d>6mm 或夹层厚度>15mm 钻孔、扩孔、铰孔。
2.影响钻孔质量的主要因素教案1.1 工件材料 1.2 钻头转速、 1.3 进刀量 1.4刀具的锋利程度2.确定铆钉孔的位置2.1 铆钉孔位置包含内容边距、排距(行距)、 孔距2.2 铆钉孔钻孔的方法1)按划线钻孔( 钻孔的方向)2)按导孔钻孔——导孔通常是制在孔的边距较小、材料较硬或较厚的零件上,在零件制造 阶段就制出,装配定位后,钉孔按导孔钻出 。
例如蒙皮和长桁的铆钉孔,是按长桁的导孔 钻出。
3)按钻模钻孔3.锪窝3.1 埋头窝的深度要求埋头窝的深度为负差,铆后铆钉头只允许铆钉头高出蒙皮表面。
3.2 埋头窝的制作方法一般使用锪窝方法,锪窝有专用的锪窝钻。
为保证埋头窝深度公差,应采用能限制窝深的锪 窝钻套。
当蒙皮厚度<0.8mm 时采用冲窝方法。
二、制孔工具设备1.风钻以压缩空气为动力,将高压空气经导管进入机身汽缸,推动活塞做高速往复运动,打击并 回转钻杆。
无头铆钉自动钻铆工艺试验研究
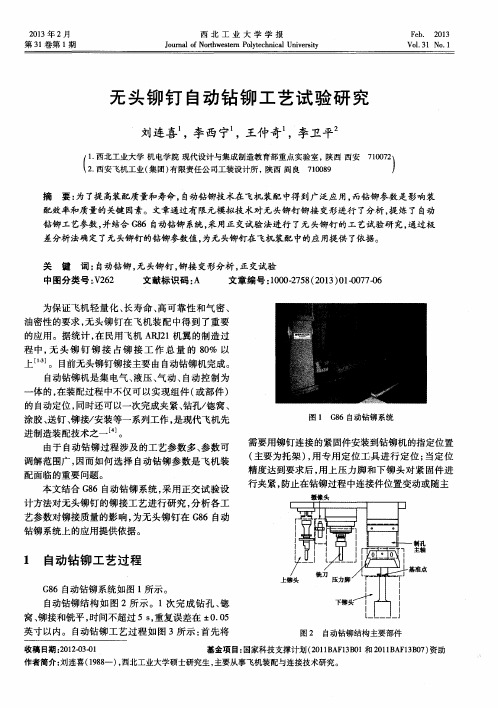
体的, 在装配过程 中不仅可 以实现组件 ( 或部件 )
图1 G 8 6自动钻铆 系统
的 自动 定位 , 同时还 可 以一次 完成 夹 பைடு நூலகம் 、 钻孔 / 锪窝 、
涂胶、 送钉 、 铆接/ 安装等一系列工作 , 是现代 飞机先 进 制造 装 配技术 之一 - 4 J 。 由于 自动钻铆过程涉及 的工艺参数多 、 参数可 调解范 围广 , 因而如何选择 自动钻铆参数是 飞机装
置, 并 在达 到该 位置 时铣 刀 自动终 止 。 3 . 2 铆钉 和试 片
表中: A ——压 铆力 、 B ——压 力 脚 回缩 压 力 、 c ——夹紧解除力 、 D ——双 向挤压夹紧力、 E ——镦
铆 过程 时 间 、 F —— 镦 铆 停 留 时 间 、 G — —上 铆 头 空
配 面临 的重 要 问题 。
需要用铆钉连接的紧固件安装到钻铆机的指定位置 ( 主要为托架) , 用专用定位工具进行 定位 ; 当定位 精度达到要求后 , 用上压力脚 和下铆头对紧固件进 行夹紧 , 防止在钻铆过程中连接件位置变动或随主
本文结合 G 8 6自动钻铆系统 , 采用正交试验设 计方法对无头铆钉 的铆接工艺进行研究 , 分析各工
摘
要: 为了提高装配质量和寿命 , 自 动钻铆技 术在飞机装配 中得到广泛应用, 而钻铆参数是影响装
配效率和质量的关键 因素。文章通过有限元模拟技 术对无头铆钉铆接变形进行 了分析, 提炼 了自 动
钻铆工艺参数, 并结合 G 8 6自 动钻铆 系统, 采用正交试验法进行 了无头铆钉的工艺试验研究, 通过极 差分析法确定 了 无头铆钉的钻铆参数值 , 为无头铆钉在飞机装配中的应用提供 了 依据。
304不锈钢扁平头半空心厚壁铆钉翻铆成形机理研究
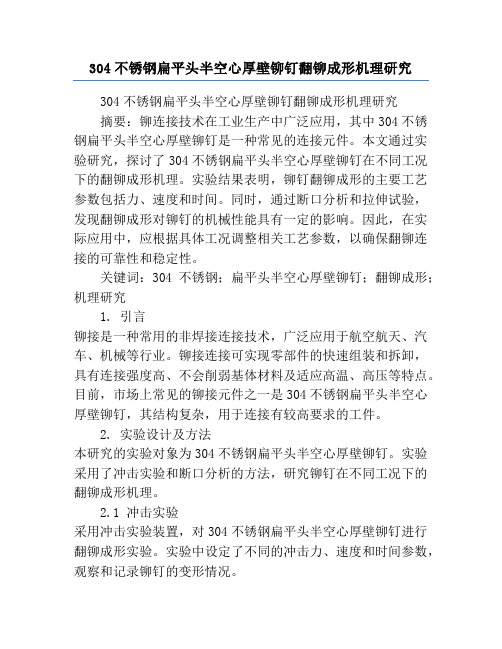
304不锈钢扁平头半空心厚壁铆钉翻铆成形机理研究304不锈钢扁平头半空心厚壁铆钉翻铆成形机理研究摘要:铆连接技术在工业生产中广泛应用,其中304不锈钢扁平头半空心厚壁铆钉是一种常见的连接元件。
本文通过实验研究,探讨了304不锈钢扁平头半空心厚壁铆钉在不同工况下的翻铆成形机理。
实验结果表明,铆钉翻铆成形的主要工艺参数包括力、速度和时间。
同时,通过断口分析和拉伸试验,发现翻铆成形对铆钉的机械性能具有一定的影响。
因此,在实际应用中,应根据具体工况调整相关工艺参数,以确保翻铆连接的可靠性和稳定性。
关键词:304不锈钢;扁平头半空心厚壁铆钉;翻铆成形;机理研究1. 引言铆接是一种常用的非焊接连接技术,广泛应用于航空航天、汽车、机械等行业。
铆接连接可实现零部件的快速组装和拆卸,具有连接强度高、不会削弱基体材料及适应高温、高压等特点。
目前,市场上常见的铆接元件之一是304不锈钢扁平头半空心厚壁铆钉,其结构复杂,用于连接有较高要求的工件。
2. 实验设计及方法本研究的实验对象为304不锈钢扁平头半空心厚壁铆钉。
实验采用了冲击实验和断口分析的方法,研究铆钉在不同工况下的翻铆成形机理。
2.1 冲击实验采用冲击实验装置,对304不锈钢扁平头半空心厚壁铆钉进行翻铆成形实验。
实验中设定了不同的冲击力、速度和时间参数,观察和记录铆钉的变形情况。
2.2 断口分析实验后,通过对翻铆后的铆钉进行断口分析,观察铆钉的微观形貌和断口特征。
采用光学显微镜和扫描电子显微镜等仪器对断口进行观察和分析,以获得铆钉翻铆成形的机理。
3. 结果与讨论3.1 冲击实验结果实验结果显示,在相同的冲击力和时间参数下,较大的冲击速度可以促进铆钉的快速翻铆成形。
而在相同的冲击速度和时间参数下,增加冲击力有利于增加铆钉的成形力度。
3.2 断口分析结果通过断口分析,观察到翻铆后的铆钉断口呈现出典型的韧性断裂特征。
铆钉的断裂面呈现出明显的裂纹和变形区,证明铆钉在翻铆成形过程中受到了较大的力和应变。
飞机的机械紧固件

飞机的机械紧固件第一节概述一. 飞机结构连接分类1. 可拆卸型连接–螺栓和螺钉2. 不可拆卸型连接–铆钉、环槽钉和高锁螺栓等。
这是在拆卸时,是否需要破坏紧固件本身来分类的。
(焊接、胶接也属于不可拆卸连接–但不属于机械紧固件)。
二. 紧固件材料 (主要指镀层) 与其连接的结构材料间的相容性。
如果两者材料不相容,对紧固件或结构零件均会产生电位腐蚀。
(因为孔的表面是不经过表面处理的)。
相容性列于表1中。
在紧固件材料栏中分为“优先”、“允许”、“禁止”提示选用者对已定的结构材料的选择,只有在“优先”栏中紧固件短缺时可考虑使用“允许”栏中的材料,对“禁止”列中的材料不能使用。
表 1 典型的紧固件和材料的相容性注:所有用在不同金属连接的紧固件或不同金属紧固件必须按 DPS2.512湿装配。
(1) 相容–在民用飞机上无处理要求。
(2) 这些合金在铝合金上能引起严重的电化效应。
(3) 钛和 A286 紧固件必须按 DPS4.025 湿装配在铝或铝/钛结构上。
(4) 少量的铝紧固件与大量的钛合金结构连接时在很短时间内将产生电化腐蚀。
(5) 这些紧固件必须湿装配按 DPS2.512。
(6) 这些紧固件必须湿装配按 DPS4.025。
(7) 镉和银镀层在与钛接触时的限制如下:已经发现采用此类材料和工艺过程会使钛零件在使用中的脆化,为避免这类情况出现,应采取下列限制:(a) 钛零件或标准件不得镀镉或镀银。
(b) 镀镉或镀银的垫圈、干涉配合衬套或干涉配合紧固件均不可与钛零件一起使用。
(c) 除 (b) 外,钛零件在下列条件下可与镀镉或镀银零件使用。
(i) 温度不超过 200°F (79.1°C)。
(ii) 对于装在钛紧固件上的有干膜润滑剂的镀镉螺母,以及特别批准的零件,温度不超过 300°F (134.7°C)。
(iii) 与镀镉零件,温度不超过 400°F(190.2°C)。
铆钉铆接工艺的优化
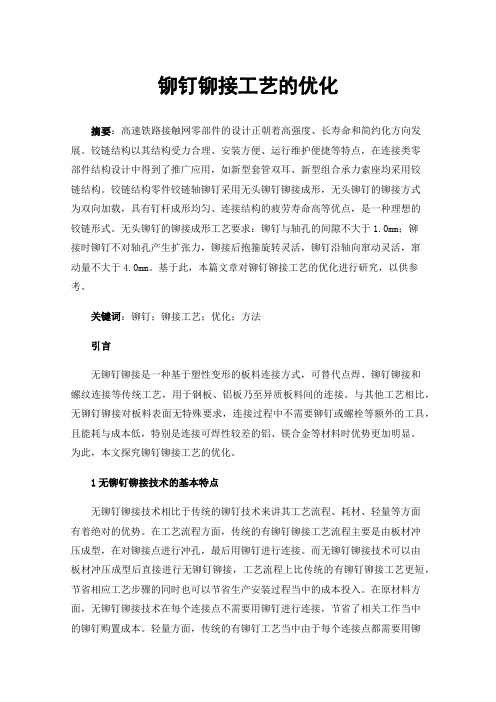
铆钉铆接工艺的优化摘要:高速铁路接触网零部件的设计正朝着高强度、长寿命和简约化方向发展。
铰链结构以其结构受力合理、安装方便、运行维护便捷等特点,在连接类零部件结构设计中得到了推广应用,如新型套管双耳、新型组合承力索座均采用铰链结构。
铰链结构零件铰链轴铆钉采用无头铆钉铆接成形,无头铆钉的铆接方式为双向加载,具有钉杆成形均匀、连接结构的疲劳寿命高等优点,是一种理想的铰链形式。
无头铆钉的铆接成形工艺要求:铆钉与轴孔的间隙不大于1.0mm;铆接时铆钉不对轴孔产生扩张力,铆接后抱箍旋转灵活,铆钉沿轴向窜动灵活,窜动量不大于4.0mm。
基于此,本篇文章对铆钉铆接工艺的优化进行研究,以供参考。
关键词:铆钉;铆接工艺;优化;方法引言无铆钉铆接是一种基于塑性变形的板料连接方式,可替代点焊、铆钉铆接和螺纹连接等传统工艺,用于钢板、铝板乃至异质板料间的连接。
与其他工艺相比,无铆钉铆接对板料表面无特殊要求,连接过程中不需要铆钉或螺栓等额外的工具,且能耗与成本低,特别是连接可焊性较差的铝、镁合金等材料时优势更加明显。
为此,本文探究铆钉铆接工艺的优化。
1无铆钉铆接技术的基本特点无铆钉铆接技术相比于传统的铆钉技术来讲其工艺流程、耗材、轻量等方面有着绝对的优势。
在工艺流程方面,传统的有铆钉铆接工艺流程主要是由板材冲压成型,在对铆接点进行冲孔,最后用铆钉进行连接。
而无铆钉铆接技术可以由板材冲压成型后直接进行无铆钉铆接,工艺流程上比传统的有铆钉铆接工艺更短,节省相应工艺步骤的同时也可以节省生产安装过程当中的成本投入。
在原材料方面,无铆钉铆接技术在每个连接点不需要用铆钉进行连接,节省了相关工作当中的铆钉购置成本。
轻量方面,传统的有铆钉工艺当中由于每个连接点都需要用铆钉进行连接,相应的工作当中车身整体质量较大,而无铆钉铆接技术则很大程度上减少了车身的重量,其本身不需要铆钉进行连接,车身的整体质量得到有效的控制。
疲劳强度方面,这种无铆钉铆接技术主要是通过对材料进行挤压,让金属流动形成需要的形体。
无头铆钉压铆力数学建模与仿真分析

面 。铆钉 镦 头 ( 头 ) 连 接 件 板 面之 间接 触 区域 钉 与
建立二维 、 三维或轴对称模型对压铆过程进行仿真 模拟, 从而求出压铆力 。这种方法缺乏理论深度 , 求
的摩擦力将阻碍铆钉镦头 ( 钉头) 的形成 , 使得金属 流动发生改变。同时连 接件因为受到镦头 ( 钉头 ) 的压力开始发 生变形 , 沿轴 向方 向压缩。冲头位移 继续增加 , 当铆钉压铆尺寸达到 目 标要求时 , 压铆力 最大 , 冲头停止移动。在此过程中 , 连接件不仅在孔 周 围受 到铆钉 膨 胀 带 来 的压 力 , 且 也 受 到铆 钉镦 而 头( 钉头) 压力 和其 延展带来 的摩擦力 作用 。接触 面包括铆钉镦头( 钉头 ) 和连接板 的接触 、 铆钉和孔 之间的接触、 上下连接件 之间的接触 。此过程定义 为阶段 1 ; 1 铆钉 尺寸达 到 目标要求 后 , I 冲头位移减 小, 载荷降低 , 但铆钉镦 头仍然与冲头相接触 , 铆钉
关 键 词: 压铆力 , 真实应变, 幂指数硬化理论 , 有限元仿真
中图分类号 :H 3. T 1 11 文献标 识码 : A 文章编 号 :0025 (0 0 0 -72 6 10 -78 2 1)504 - 0 或实验 方 法 来 设 置 压 铆 机 的最 大 铆 接 力 H 。使 用 】
同时, 铆接力过大, 会使蒙皮局部下 陷, 径向伸长。 蒙皮的下陷不仅使蒙皮结构变得具有脆性而且使得 蒙皮表层 曲面的连续性 、 光滑性受到影响 , 减低飞机 的空气动力学性能 。然而 , J 关于压铆力的选取并 没有一个理论依据 , 装配过程 中往往根据经验公式
收稿 日期 :09 1・3 20 - 1 0
经验公式所计算 出的压铆力误差较大, 而且对铆接 后铆钉的尺寸不能提前预判 ; 实验方法成本昂贵, 并 且耗费大量时间。 近年来 , 国内外学者对压铆过程做了大量研究 , 归纳起来主要 有以下几种方 法: 主应力法口 : ① J其 主要思想是将平衡微分方程与屈服方程联立求解 ,
国内外自动钻铆技术的发展现状及应用

国内外自动钻铆技术的发展现状及应用西飞国际设备维修中心 楼阿莉当代飞机制造技术的发展,对疲劳寿命、密封、防腐的要求越来越高,为了满足飞机对各种性能的要求,航空制造领域发展了各种先进技术,其中机械连接技术的干涉配合无头铆钉自动钻铆技术就是其中之一。
国外铆接装配技术几十年的应用证明,采用自动钻铆机后装配效率至少比手工铆接装配提高10倍,并能节约安装成本,改善劳动条件,更主要的是能够确保安装质量,大大减少人为因素造成的缺陷。
现在采用自动钻铆机已成为改善飞机性能的主要工艺措施之一。
美国是最早发展自动钻铆技术的国家,早在 50 年代初就已在飞机铆接装配生产线上应用了自动钻铆机,经过 50 多年的发展,现在世界各航空工业发达国家都已广泛采用这项技术。
自动钻铆技术主要包含以下内容:(1) 设备的研制、开发。
以不同飞机的结构为对象,发展多种型号的数控自动钻铆系统,不仅能铆接壁板,而且还可铆接各种组件,如肋、框、梁、翼面、前缘等,从而使自动钻铆系统的工作覆盖面大幅度增加,使整个飞机的铆接工作有较大的改观。
(2) 对各种干涉配合新型紧固件进行自动安装。
通过增加附件,可以对两件型紧固件进行自动安装,如环槽钉、高锁螺栓、锥形螺栓等,也可对无头铆钉进行干涉配合铆接,从而提高铆接结构疲劳寿命5~6倍,对提高飞机整体油箱的密封铆接质量有重大意义。
(3) 自动钻铆工艺。
结构铆接的整个过程通过预先编程全部由CNC程序控制,自动钻铆工艺是在一台设备上一次性地连续完成夹紧、钻孔、锪窝、注胶、放铆、铣平等工序。
由于机床带有高速、高精度的转削主轴头,一次进给即能钻出0.005mm以内高精度的孔,同时埋头窝的深度也可精确控制在±0.01mm以内,再加上机床由数控系统控制各轴运动,并采用精密自动化工装夹具,使得铆钉镦头高度保持一致,不受人为因素的影响。
所有这些因素均使钉杆在孔中充填质量大为改善,从而有利于提高细节疲劳强度许用值。
此外,由于钻孔时铆接件处在高的夹紧力下,层间不会产生毛刺和进入切削,可以减小疲劳载荷下发生磨蚀损伤的程度,这些均有利于提高接头的疲劳强度。
铆钉铆接工艺的优化

铆钉铆接工艺的优化 张晓芳,王兴全,赵 毅等 技术交流与创新DOI :10.19587/ki.1007-936x.2019.06.024铆钉铆接工艺的优化张晓芳,王兴全,赵 毅,雷尚军,唐 鹏摘 要:无头铆钉具有钉杆成形均匀、连接结构疲劳寿命高等优点,在高速铁路接触网零部件中得到了推广应用。
本文针对无头铆钉铆接成形过程中的质量控制问题,通过Deform-3D 数值模拟研究铆接压下量对翻边直径、窜动量的影响规律,分析其切向应力分布情况,并结合冲铆、残余应力试验对铆接压下量进行了优化,确保铆钉的铆接质量。
关键词:无头铆钉;窜动量;工艺优化Abstract: The headless rivets, featuring of advantages of uniformly forming of rivet shanks, higher structural fatigueservice life, are commonly served as the fittings of OCS for high speed railways. The paper presents the issues for quality control of riveting process for headless rivet, studies the regularities influencing of flanging diameter and amount of play caused by the riveting rolling reduction by means of Deform-3D simulation, analyzes the distribution of its tangential stress; the optimization has been made for rolling reduction of riveting with connection of tests of punching, riveting and residual stress so as to guarantee the riveting quality of rivets.Key words: Headless rivet; amount of play; optimization of process中图分类号:TG306 文献标识码:B 文章编号:1007-936X (2019)06-0097-030 引言高速铁路接触网零部件的设计正朝着高强度、长寿命和简约化方向发展。
锥鼓形冷镦成形球头的工艺参数优化

锥鼓形冷镦成形球头的工艺参数优化1. 绪论a. 研究背景和目的b. 冷镦成形球头的应用及现状c. 工艺参数优化的重要性2. 球头成形相关理论a. 金属塑性变形理论b. 冷镦成形理论c. 球头成形理论3. 球头成形工艺参数影响分析a. 材料b. 冷镦成形设备c. 冷镦成形工艺参数4. 工艺参数优化实验设计a. 实验材料和设备b. 实验方案设计c. 实验结果分析5. 结论与展望a. 根据实验结果作出结论和评价b. 展望球头成形工艺参数优化的未来研究方向和应用前景注:以上提纲仅供参考,可以根据具体情况进行调整和完善。
第一章:绪论1.1 研究背景和目的在现代工业生产中,球头已经成为许多机械零部件中常用的零件之一。
其广泛应用于汽车、家电、机械设备等领域。
冷镦成形是一种常用的球头形成方法,其有着成本低、生产效率高等优点,因而在工业生产中得到了广泛应用。
然而,在实际应用中,由于制造过程中的工艺参数设置存在着一定的偏差,冷镦成形球头的形状和尺寸精度往往无法满足设计要求,从而影响到产品品质和性能。
因此,针对球头成形工艺的优化研究显得尤为重要。
本研究旨在通过对球头冷镦成形中的工艺参数进行系统的优化设计,进一步提高球头成形的精度和稳定性,为其在工业生产中的应用提供技术支持。
1.2 冷镦成形球头的应用及现状冷镦成形球头是现代机械加工领域中常见的一种精密成形工艺,广泛应用于各类金属材料零件的加工。
特别是在汽车、汽车零配件、机械设备等领域,冷镦成形球头的应用更是广泛。
近年来,随着工业自动化技术的快速发展,企业对冷镦成形球头精度和质量的要求越来越高。
同时,竞争日趋激烈,工厂生产成本也在不断的攀升,在此背景下,球头成形工艺的优化研究显得尤为重要。
1.3 工艺参数优化的重要性一般来说,球头成形工艺参数的优化对提高产品的质量和产量都有着重要的意义。
冷镦成形球头的优化,其核心是要在保证成形质量的基础上,尽可能地提高球头的成形效率和稳定性,从而为企业生产的效益做出贡献。
无头铆钉双面鼓形镦头铆接试验及缺陷研究

Material Sciences 材料科学, 2020, 10(8), 668-677Published Online August 2020 in Hans. /journal/mshttps:///10.12677/ms.2020.108081Research on Riveting Testsand Defects of Headless Rivetwith Double Drum Upsetting HeadQingtao Sha, Jianwen Zhu, Xiuyan Zhang, Song Li, Zhaoyang LiuCapital Aerospace Machinery Corporation Limited, BeijingReceived: Aug. 5th, 2020; accepted: Aug. 21st, 2020; published: Aug. 28th, 2020AbstractIn order to analyze the cause of the defects of the headless rivet with double drum upsetting head, the process flow of the headless rivet is analyzed first. Then the rivet technology test with diame-ter 4 and 5 is carried out to obtain the recommended rivet lengths with different diameters and different specimen thicknesses. The causes of defects are analyzed from the process flow and process test, and the preventive measures are given.KeywordsHeadless Rivet, Technological Process, Riveting Defects, Metallographic Analysis无头铆钉双面鼓形镦头铆接试验及缺陷研究沙庆涛,朱建文,张秀艳,李松,刘昭阳首都航天机械有限公司,北京收稿日期:2020年8月5日;录用日期:2020年8月21日;发布日期:2020年8月28日摘要为分析无头铆钉双面鼓形镦头缺陷产生原因,首先分析无头铆钉铆接工艺流程,然后进行Φ4、Φ5铆钉的工艺试验,得出不同直径、不同试件厚度的铆钉建议长度。
【正式版】铆工讲义矫形成形PPT文档

下料是将材料说根据明展开:,切也割成可所需采要的用形状线。 状加热方式,即从中间凸鼓部分的两侧 图(36开-)5 鹤始嘴边锤缘加:翘主曲热要的用矫,于正消然除工后件表逐面的步小凹向坑,凸如图鼓2-15处f所示围。 拢的方式进行矫平,如图3-31b
钢材因受外力或加热等因素的影响,会产生各种变形。
所示。 (2)边缘翘曲的矫正:
钢材因受外力或加热等因素的影响,会产生各种变形。
仅适用于对小步件的骤矫正3。:矫平后再用锤子沿水平方向轻击卡子,便能松开卡 子取出板料。 (3)检查手柄是否松动,以免锤头脱出造成事故。
1、锤子:锤子是冷作钣金工中的基本工具,它的形状很多,作用也不一样。 若经过第一次加热后还有不平,可重复进行第二次加热矫正,但加热线位置应与第一次错开。 图3-31 中部凸鼓工件的火焰矫正 2、边缘波浪形工件的火焰矫正: 说明:也可采用线状加热方式,即从中间凸鼓部分的两侧开始加热,然后逐步向凸鼓处围拢的方式进行矫平,如图3-31b所示。 它是利用反向弯曲或反向扭转原理进行矫正的,通常在油压机上矫正的应用实例 冷作钣金使用的原材料均是较长、较大的钢板和型钢,如果吊装、运输和存放不当,钢材就会因自重而产生弯曲、扭曲和局部变形。
• 2.1 折弯成形 —— 折弯机将上、下模分别固定于折床的上下工作台
,利用伺服马达传输驱动工作台的相对运动,结合上下模的形状,从而实 现对板材的折弯成形。折弯的成形精度可以达到0.1mm。
• 2.2 冲压成形 —— 冲床利用电机驱动飞轮产生的动力驱动上模,结
合上、下模相对形状,使板材发生变形,实现料件的加工成形。冲压成 形的精度可以达到0.1mm以上。冲床可以分为普通冲床及高速冲床。
免滑脱伤人;
• (3)检查手柄是否松动,以免锤头脱出造 成事故。
双鼓型铆钉小知识
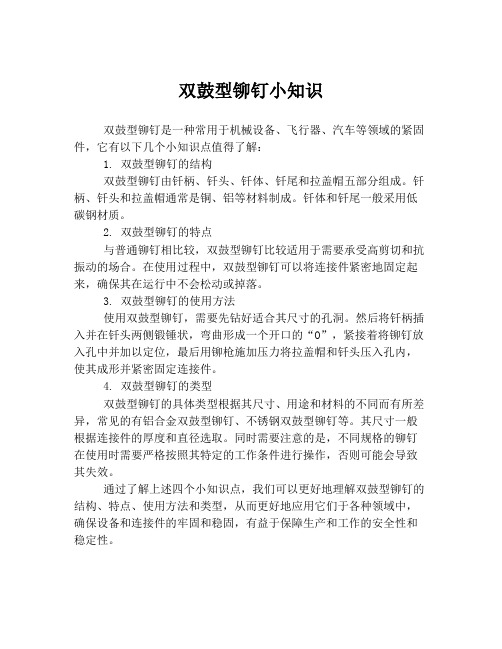
双鼓型铆钉小知识
双鼓型铆钉是一种常用于机械设备、飞行器、汽车等领域的紧固件,它有以下几个小知识点值得了解:
1. 双鼓型铆钉的结构
双鼓型铆钉由钎柄、钎头、钎体、钎尾和拉盖帽五部分组成。
钎柄、钎头和拉盖帽通常是铜、铝等材料制成。
钎体和钎尾一般采用低碳钢材质。
2. 双鼓型铆钉的特点
与普通铆钉相比较,双鼓型铆钉比较适用于需要承受高剪切和抗振动的场合。
在使用过程中,双鼓型铆钉可以将连接件紧密地固定起来,确保其在运行中不会松动或掉落。
3. 双鼓型铆钉的使用方法
使用双鼓型铆钉,需要先钻好适合其尺寸的孔洞。
然后将钎柄插入并在钎头两侧锻锤状,弯曲形成一个开口的“O”,紧接着将铆钉放入孔中并加以定位,最后用铆枪施加压力将拉盖帽和钎头压入孔内,使其成形并紧密固定连接件。
4. 双鼓型铆钉的类型
双鼓型铆钉的具体类型根据其尺寸、用途和材料的不同而有所差异,常见的有铝合金双鼓型铆钉、不锈钢双鼓型铆钉等。
其尺寸一般根据连接件的厚度和直径选取。
同时需要注意的是,不同规格的铆钉在使用时需要严格按照其特定的工作条件进行操作,否则可能会导致其失效。
通过了解上述四个小知识点,我们可以更好地理解双鼓型铆钉的结构、特点、使用方法和类型,从而更好地应用它们于各种领域中,确保设备和连接件的牢固和稳固,有益于保障生产和工作的安全性和稳定性。
重卡车架铆钉受力分析与变形工艺验证
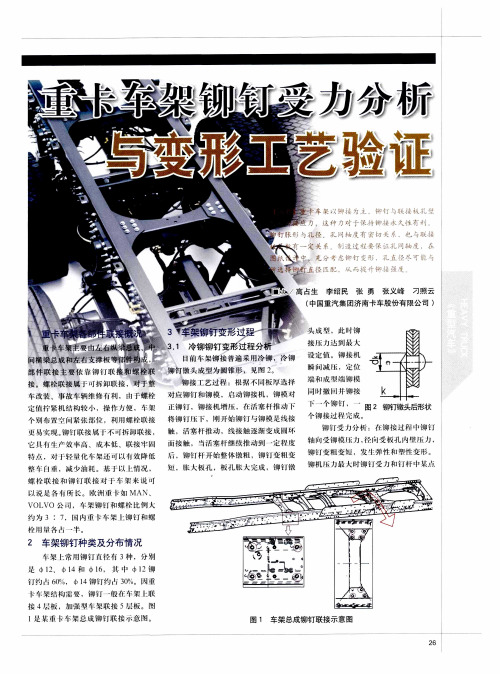
切割机。 方案 1 : 选 用 l 4铆 钉 , 对 应 板
孔径分别为 中1 4 . 5 ; 1 5 . 5 ( 为 r便 于
穿装铆 钉,有些 车型设计 为大孔 ) ,铆
点 应 力 变分 析 见 l 冬 l 4 。
钉 长度 为 标 准 值 。 从 剖 面 图 分 析 铆 钉 胀
铆 钉受力分忻 : 铆 接 过程 I l 铆 钉
它 具 仃 生 产 效 率 高 、成 本 低 、联 接 心
特 点 ,对 1 : 轻 量 化 乍 架还 可 以有 效 降 低 1 | I ' 1 重 ,减 少 油 耗 。 基 于 以 I : 情况 ,
径 向受 板 扎 内罐 压 力 , 面接 触 , 当活 塞 杆继 续 推 动 到 一 定 程 度 轴 向受 铆 模 力 , 铆 钉 变 粗 变 ,发 , 1 j 弹性 午 ¨ 性 变肜。 后 ,铆 钉 杆 开 始 整 体 镦 芈 H,铆 钉 变 变 力最 人时 铆 钉 受 和 钉 杆 巾 某 点 短 ,J } l 乏 人 板孔 ,板 孔 胀 人 完 成 ,铆 钉 镦 铆 机 J
铆 钉 : 由I 4 , 孔 径 (自上 而 下 ) :
图5 - 2 3层铆接后剖视 图
铆钉 : 1 4 孔径 : 1 4 . 5 ,成 型
1 6. 5
ቤተ መጻሕፍቲ ባይዱ、
1 6 . 5和 1 4 . 5 ,成型端:
上端 ,铆 接 质 量 :铆 钉 胀 形 充 分 ,孔 全
况,见图 6 。
和钉杆 中某点应力应变分析
端 :上 端 ,铆 接 质量 :铆 钉 胀 形 充 分
/ n — I /
-
新型铆钉原理
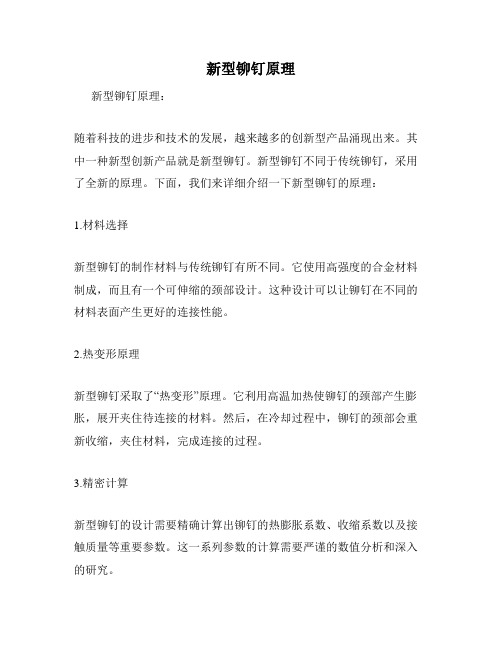
新型铆钉原理
新型铆钉原理:
随着科技的进步和技术的发展,越来越多的创新型产品涌现出来。
其中一种新型创新产品就是新型铆钉。
新型铆钉不同于传统铆钉,采用了全新的原理。
下面,我们来详细介绍一下新型铆钉的原理:
1.材料选择
新型铆钉的制作材料与传统铆钉有所不同。
它使用高强度的合金材料制成,而且有一个可伸缩的颈部设计。
这种设计可以让铆钉在不同的材料表面产生更好的连接性能。
2.热变形原理
新型铆钉采取了“热变形”原理。
它利用高温加热使铆钉的颈部产生膨胀,展开夹住待连接的材料。
然后,在冷却过程中,铆钉的颈部会重新收缩,夹住材料,完成连接的过程。
3.精密计算
新型铆钉的设计需要精确计算出铆钉的热膨胀系数、收缩系数以及接触质量等重要参数。
这一系列参数的计算需要严谨的数值分析和深入的研究。
4.适用范围
新型铆钉可以应用于各种材料的连接,如金属材料、非金属材料以及
复合材料等。
并且,在实际工作中,新型铆钉的连接效果要比传统铆
钉更加可靠和牢固,受到了各行业的广泛认可。
5.市场前景
随着科技的不断发展,新型铆钉的应用范围越来越广泛。
它具有连接
效率高、连接牢固、安装方便等优点,成为未来连接行业的一个发展
趋势。
因此,新型铆钉的市场前景非常广阔,具有巨大的经济潜力。
通过以上分析,我们可以看出,新型铆钉采用了一种全新的工艺原理,不仅连接效果优越,而且易于安装,适用于各种材料。
它将会是未来
连接行业的一大发展趋势,为社会、经济的进步做出更大的贡献。
- 1、下载文档前请自行甄别文档内容的完整性,平台不提供额外的编辑、内容补充、找答案等附加服务。
- 2、"仅部分预览"的文档,不可在线预览部分如存在完整性等问题,可反馈申请退款(可完整预览的文档不适用该条件!)。
- 3、如文档侵犯您的权益,请联系客服反馈,我们会尽快为您处理(人工客服工作时间:9:00-18:30)。
2.1. 无头铆钉的选型
无头铆钉主要有三种:1) 国军标 GJB131.1 [6]内的两头实心无头铆钉;2) 国标 GB1016-86 内的两头 空心无头铆钉;3) 国外铆钉,美国航空航天工业协会的 NAS1321 内的无头铆钉。
本文采用国军标 GJB131.1 的无头铆钉,规格如表 1 所示,仅有直径 4 mm,5 mm,6 mm 的铆钉,
Keywords
Headless Rivet, Pressing Rivet, Double Drum Upsetting Head, Shearing Test, Microstructure Analysis
无头铆钉双面鼓形镦头成形工艺与性能分析
吕九九1,张秀艳1,马兴海1,黄殿阁1,臧建新1,安立辉2
吕九九 等
摘要
针对双面鼓形镦头无头铆钉的铆接方法,设计出适用压铆设备的专用工装,通过力学性能检测和截面微力越大,同一直径的铆钉,镦头直径 一致,镦头高度越大,剪切力越小;同一直径的铆钉,镦头高度一致,镦头直径越大,剪切力越大;不 同直径的铆钉,长度相同,铆钉直径越大,剪切力越大;Φ4和Φ5铆钉均能较好填充至孔隙中,而Φ6两 试片对接处出现明显的缝隙,偏心和试片错位是造成该现象的主要原因。
目前的研究对于铆接完成后的性能试验:干涉量、剪切试验、拉脱试验、剖切后放大等均是破坏性 试验,做完试验后的铆钉或试片失去紧固件功能,不能继续使用。建立一种破坏性试验与非破坏性试验 的关系是现在铆接试验亟待解决的问题,本文将从铆钉镦头尺寸与剪切力间的关系来分析无头铆钉的长 度及铆接参数的选择,用来指导生产。
据 QJ3143 普通铆钉通用规范中附录 A.1 [7]中推荐的铆钉长度,可总结出铆钉长度需要超出工件厚度的 经验公式为:
L =S + L外 + L内
(1)
L外 + L内 =2× (1.2 ~ 1.4)× d
(2)
其中:L 为铆钉总长度;S 为工件总厚度;d 为铆钉直径;L 外和 L 内分别为工件两端,铆钉的外伸量。
1首都航天机械有限公司,北京 2中国运载火箭技术研究院,北京
收稿日期:2018年9月14日;录用日期:2018年10月10日;发布日期:2018年10月17日
文章引用: 吕九九, 张秀艳, 马兴海, 黄殿阁, 臧建新, 安立辉. 无头铆钉双面鼓形镦头成形工艺与性能分析[J]. 机械 工程与技术, 2018, 7(5): 344-355. DOI: 10.12677/met.2018.75042
众多学者对无头铆钉进行了研究,发表于西北工业大学学报的《无头铆钉干涉配合铆接工艺试验报 告(之一)》针对不同铆模进行了干涉量对比,得出无头铆钉的干涉配合铆接必须采用凹形上下铆模的结论, 以保证均匀合理的干涉量;钉孔直径、铆钉长度、外伸量、板材厚度等也影响干涉量的变化,生产时需 合理选用[1]。王晶等通过有限元分析得出应力波安装(动态加载)相比铆枪锤击打入(准静态加载)和液压压 入(静态加载),可获得较大的干涉量[2]。刘连喜采用正交试验分析各工艺参数对无头铆钉铆接质量的影 响[3]。牟伟强等提出采用幂指数硬化理论来确定压铆力关于镦头高度的数学函数[4]。刘恩洋等通过电磁 铆接试验得出镦头是否铣平对剪切强度影响不大,但镦头铣平后拉脱强度有所减小,为满足铆钉的拉脱 强度,可适当增加钉孔锪窝深度[5]。
1Capital Aerospace Engineering Machinery Co., Ltd., Beijing 2China Academy of Launch Vehicle Technology, Beijing
Received: Sep. 14th, 2018; accepted: Oct. 10th, 2018; published: Oct. 17th, 2018
4.1. 铆钉镦头成形性能
剪切试片铆接后实物如图 4 所示,分别用来研究铆钉成形后镦头高度,成形后镦头直径,铆钉原始 长度以及铆钉原始直径对铆钉镦头性能的影响:
1) 铆钉原始尺寸为 Φ4 × 15、Φ4 × 16,成形后使镦头直径保持基本一致,铆钉长度不同会使镦头高 度不同。
2) 铆钉原始尺寸为 Φ4 × 16、Φ4 × 17,成形后使镦头高度保持基本一致,铆钉长度不同会使镦头直 径不同。
4.08
5.08
6.08
+0.075
0
无头铆钉压铆定位工装需成对使用,内置压缩弹簧,使用时保证铆钉处于工装中心,压铆机向下移 动,带动上定位工装向下运动,上定位工装向下运动的同时会压缩弹簧将压力传铆接件,进而传至下定 位工装。因工装是成对使用,两弹簧的初始压缩量是一致的,弹簧刚度足够大,定位工装的重量和铆接 试片的重量对弹簧的压缩可忽略,如图 2 所示。
Mechanical Engineering and Technology 机械工程与技术, 2018, 7(5), 344-355 Published Online October 2018 in Hans. /journal/met https:///10.12677/met.2018.75042
DOI: 10.12677/met.2018.75042
345
机械工程与技术
吕九九 等
铆钉长度为整数。
2.2. 铆钉长度选择
铆钉长度是关乎铆接质量的重要参数,铆钉过长,铆钉墩头就过大,钉杆易弯曲;铆钉过短,则墩
粗量不足,钉头成型不完整,影响铆接强度和紧密性。无头铆钉长度与工件厚度的关系如图 1 所示,根
Open Access
1. 引言
铆接是一种不可拆卸的干涉配合连接,有头铆钉的制造和装配工艺技术成熟,广泛应用于飞机和运 载火箭的装配。然而,有头铆钉的钉头限制了自动化生产设备中送钉杆、内铆接杆直径的最小值。送钉 杆直径和内铆接杆直径过大会与桁条立筋干涉,制约了自动钻铆技术的发展。因此,一种将有头铆钉的 铆钉头去掉,形成一种新的铆钉——无头铆钉的铆接技术,可解决这一难题。
3) 铆钉原始尺寸为 Φ4 × 17、Φ5 × 17,成形后使镦头高度保持基本一致,铆钉直径不同。 做完铆接试片后,先测量镦头尺寸再进行剪切试验,得到镦头尺寸的测量值和最大剪切力。表 3 所 示为相同铆钉直径下,不同成形后镦头尺寸与最大剪切力均值。 分析铆钉成形后镦头尺寸对最大剪切力的影响,分别作图,镦头高度对比组如图 5 所示,镦头直径 对比组如图 6 所示。可以得出,镦头直径一致,镦头高度越大,剪切力越小。这是由于铆钉长度不一致, 在镦粗过程中,镦头高度小的,铆钉镦粗越明显,铆钉剪切强度越高。铆钉镦头高度一致,镦头直径 越大,剪切力越大。这是由于铆钉长度不一致,镦粗过程中,镦头直径越大的,镦粗现象越明显,镦 头剪切强度越高。相比之下,镦头高度的降低,比镦头直径的提高,对于最大剪切力的提升,效果更 为明显。 将相同铆钉直径,不同铆钉长度铆接试样的最大剪切力进行对比,如图 7 所示,可以得到在满足条 件的铆钉长度当中,长度为 15 的铆钉最大剪切力明显高于长度为 16 和 17 的铆钉。因此,铆钉长度越短, 也即铆钉外伸量越小,最大剪切力越大。相同铆钉长度,不同铆钉直径铆钉镦头成形后及试样最大剪切 力如表 4 和图 8 所示,可以得到长度相同,直径不同的铆钉,直径越大,剪切力越大的结论。 综合以上结论,在满足镦头直径和镦头高度要求的前提下:可适当增加镦头直径来提高剪切强度。
关键词
无头铆钉,压铆铆接,双面鼓形镦头,剪切试验,微观分析
Copyright © 2018 by authors and Hans Publishers Inc. This work is licensed under the Creative Commons Attribution International License (CC BY). /licenses/by/4.0/
为适应不同长度无头铆钉外伸量的变化,压铆定位工装还配备了调整垫片,三种厚度:0.3 mm、0.5 mm、1 mm,可组合使用来调整铆钉的外伸量。
使用时应使无头铆钉中心位于工装中心,保证工装和工件表面清洁,确保压铆圆周方向受力均匀。
4. 剪切试验
剪切试验试片如图 3 所示[9],在万能试验机上进行剪切破坏试验,获得最大剪切力数据。本文使用 的铆接设备为压铆铆接设备,为节约材料,作废的试片可将铆钉拆除,直径扩大一级当正常试片使用。
Forming Technology and Performance Analysis of Headless Rivet with Double Drum Upsetting Head
Jiujiu Lv1, Xiuyan Zhang1, Xinghai Ma1, Diange Huang1, Jianxin Zang1, Lihui An2
Table 1. GJB131.1 Non-head rivet information sheet 表 1. 国军标(GJB131.1)无头铆钉信息表
R0.4±0.2
d
d
L
材料
4
12~24
5
15~30
LY10
L
6
18~36
DOI: 10.12677/met.2018.75042
Figure 1. Length dimension figure of Non-head rivets 图 1. 无头铆钉长度尺寸图
346
机械工程与技术
吕九九 等
Table 2. GJB131.2 Non-head rivet Interference fit riveting rivet hole diameter 表 2. GJB131.2 无头铆钉干涉配合铆接的铆钉孔直径
铆钉直径/mm 钉孔直径/mm
基本尺寸 偏差
4
5
6
Abstract
According to the riveting of headless rivet with double drum upsetting head, the special equipment for pressing rivet is designed. It’s concluded that the greater the shear force, the more obvious the upsetting phenomenon. It can be described as follows. The first one is: the higher the upsetting head, the lower the shear force when the riveting diameter and the upsetting head diameter are the same. The second one is: the bigger the upsetting head diameter, the larger the shear force when the riveting diameter and the upsetting head height are the same. The third one is: for the rivet of different diameters, the bigger the rivet diameter, the larger the shear force when the diameter of rivet is different. Through the incision test, it’s concluded that the rivet with the diameter of 4 and 5 can be filled well, but the diameter of 6 has obvious cracks in the joint, and the reasons for the poor filling are analyzed.