《FMEA--过程潜在失效模式及后果分析作业指导书》
FMEA作业指导书
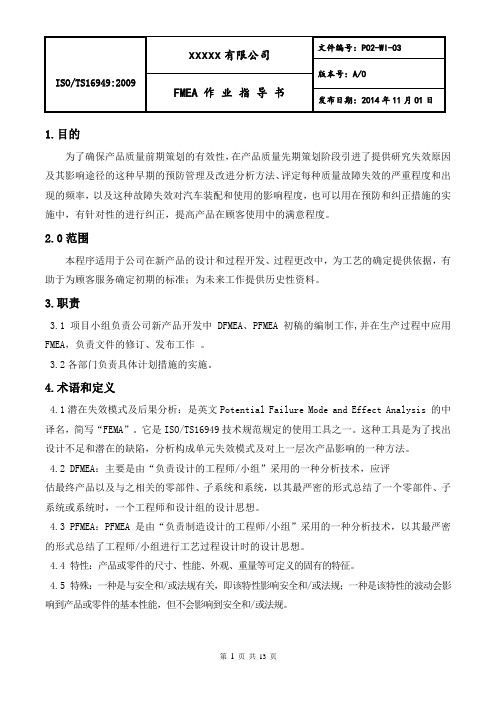
1.目的为了确保产品质量前期策划的有效性,在产品质量先期策划阶段引进了提供研究失效原因及其影响途径的这种早期的预防管理及改进分析方法、评定每种质量故障失效的严重程度和出现的频率,以及这种故障失效对汽车装配和使用的影响程度,也可以用在预防和纠正措施的实施中,有针对性的进行纠正,提高产品在顾客使用中的满意程度。
2.0范围本程序适用于公司在新产品的设计和过程开发、过程更改中,为工艺的确定提供依据,有助于为顾客服务确定初期的标准;为未来工作提供历史性资料。
3.职责3.1 项目小组负责公司新产品开发中DFMEA、PFMEA初稿的编制工作,并在生产过程中应用FMEA,负责文件的修订、发布工作。
3.2各部门负责具体计划措施的实施。
4.术语和定义4.1潜在失效模式及后果分析:是英文Potential Failure Mode and Effect Analysis 的中译名,简写“FEMA”。
它是ISO/TS16949技术规范规定的使用工具之一。
这种工具是为了找出设计不足和潜在的缺陷,分析构成单元失效模式及对上一层次产品影响的一种方法。
4.2 DFMEA:主要是由“负责设计的工程师/小组”采用的一种分析技术,应评估最终产品以及与之相关的零部件、子系统和系统,以其最严密的形式总结了一个零部件、子系统或系统时,一个工程师和设计组的设计思想。
4.3 PFMEA:PFMEA是由“负责制造设计的工程师/小组”采用的一种分析技术,以其最严密的形式总结了工程师/小组进行工艺过程设计时的设计思想。
4.4 特性:产品或零件的尺寸、性能、外观、重量等可定义的固有的特征。
4.5 特殊:一种是与安全和/或法规有关,即该特性影响安全和/或法规;一种是该特性的波动会影响到产品或零件的基本性能,但不会影响到安全和/或法规。
5.内容5.1 FMEA应用的要求5.1.1 新设计、新技术或新过程。
FEMA的范围是全部设计、技术或过程5.1.2对现有设计或过程的修改(假设对现有设计或过程已有FMEA)。
潜在的失效模式与后果分析(FMEA)精选全文
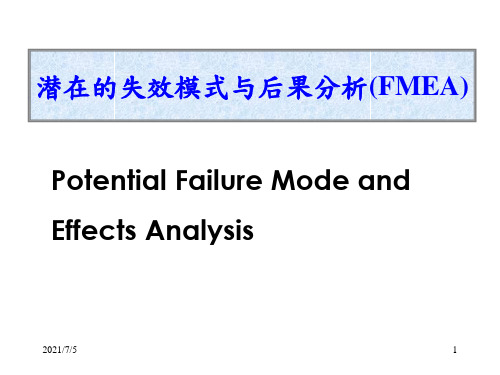
太短功能 :支撑架总成生产方法 (焊接)潜在失效模式 :
设计目标骑乘至少3000小时
不需保养, 及10000
小时的骑乘寿命适应99.5%男性成人
舒适的骑乘其它功能 :容易骑用潜在失效模式驾驶困难踩踏困难功能 :提供可靠的交通潜在失效模式链条经常损坏轮胎经常需要保养功能:提供舒适的交通潜在失效模式座椅位置令骑乘者
2021/7/5
19
FMEA的实施
FMA(失效模式分析)
FMEA(潜在失效模式及后果分析)
失效已经产生
失效还未产生,可能发生,但不是一定要发生
核心:纠正
核心:预防
诊断已知的失效
评估风险和潜在失效模式的影响开始于产品设计和工艺开发活动之前
指引开发和生产
指引贯穿整个产品周期
FMA:Failure Mode Analysis
2021/7/5
18
FMEA的实施
●及时性●它是一个事前的行为,而不是一个事后的行为。●事先花时间很好地进行综合的FMEA分析,能够容易、低成本地对产品或过程进行修改,从而减轻事后修改的危机。●FMEA能够减少或消除因修改而带来更大的机会。适当地应用FMEA是一个相互作用的过程,永无止境。● FMEA是一个动态的文件。● FMA是一种事后行为,是对产品/过程已经发生的失效 模式分析其产生的原因,评估其后果采取纠正措施的一种活动。●类似项目的FMA是FMEA的重要的输入参考资料。
2021/7/5
22
良好FMEA之具备事项
FMEA是早期预防失效及错误发生的最重要且最有效的方法之一。一个良好的FMEA必须具备: 1. 确认已知及潜在失效模式 2. 确认每一失效模式的后果和原因 3. 依据风险顺序(严重度、频度及探测度)采取措施 4. 提供问题改正行动及跟催
过程FMEA作业指导书
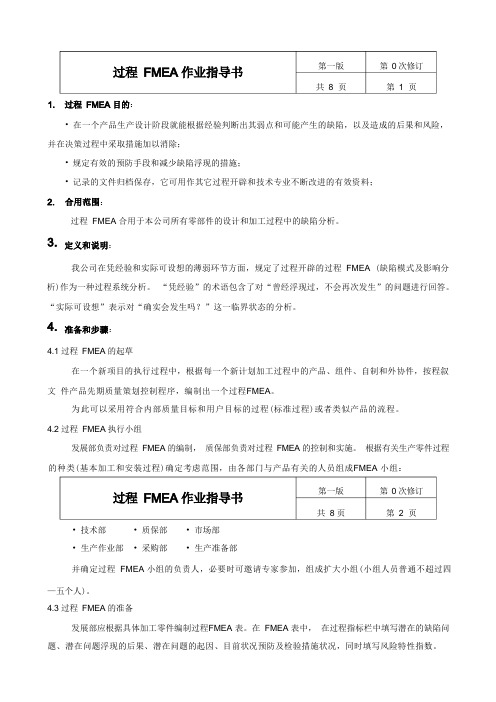
共 8 页:• 在一个产品生产设计阶段就能根据经验判断出其弱点和可能产生的缺陷,以及造成的后果和风险, 并在决策过程中采取措施加以消除;• 规定有效的预防手段和减少缺陷浮现的措施;• 记录的文件归档保存,它可用作其它过程开辟和技术专业不断改进的有效资料;:过程 FMEA 合用于本公司所有零部件的设计和加工过程中的缺陷分析。
:我公司在凭经验和实际可设想的薄弱环节方面,规定了过程开辟的过程 FMEA (缺陷模式及影响分析)作为一种过程系统分析。
“凭经验”的术语包含了对“曾经浮现过,不会再次发生”的问题进行回答。
“实际可设想”表示对“确实会发生吗?”这一临界状态的分析。
:4.1 过程 FMEA 的起草在一个新项目的执行过程中,根据每一个新计划加工过程中的产品、组件、自制和外协件,按程叙文 件产品先期质量策划控制程序,编制出一个过程FMEA 。
为此可以采用符合内部质量目标和用户目标的过程(标准过程)或者类似产品的流程。
4.2 过程 FMEA 执行小组发展部负责对过程 FMEA 的编制, 质保部负责对过程 FMEA 的控制和实施。
根据有关生产零件过程的种类(基本加工和安装过程)确定考虑范围,由各部门与产品有关的人员组成FMEA 小组:• 技术部• 生产作业部 • 质保部• 采购部 • 市场部• 生产准备部并确定过程 FMEA 小组的负责人,必要时可邀请专家参加,组成扩大小组(小组人员普通不超过四—五个人)。
4.3 过程 FMEA 的准备发展部应根据具体加工零件编制过程FMEA 表。
在 FMEA 表中, 在过程指标栏中填写潜在的缺陷问 题、潜在问题浮现的后果、潜在问题的起因、目前状况预防及检验措施状况,同时填写风险特性指数。
第 0 次修订第 2 页第一版共 8 页第 0 次修订第 1 页第一版质保部应组织 FMEA 小组讨论改进措施和方案,并根据所记录的数据以及每位组员的经验,评定缺 陷可能浮现的概率和缺陷对用户的影响,必要时补充其它缺陷、后果或者原因。
潜在失效模式及后果分析(FMEA)—培训教材.

決定失效模式
確認效應 確認原因 確認目前控制 評價嚴重度 評價發生度 評價偵測度 三種 評價 完成 ? 否 是 收集數據 進行變更 確認改變 執行改變 收集數據 原因順序 影響要因 確認改變 是 知道如何 影響 遴選最重要 失效模式
嚴重度? 發生度? 偵測度? 否
更新文件 重訂優先順序
CAUSE
MODE
EFFECT
FMEA
潜在失效模式及后果分析
何謂过程 FMEA?
过程的潛在 FMEA 是一種分析技術,係由負責过程的工程師或小組使用,在 儘可能的範圍內用來確保所有潛在的失效模式及其原因/機制均已納入考量並 予以處理。过程潛在 FMEA旨在: • 鑑別过程的機能和要求 • 鑑別潛在的產品和过程有關的失效模式 • 評估失效對顧客的潛在影響 • 鑑別潛在的製造或組裝過程原因和鑑別过程變數 ( Variables ),並 且據以控制降低發生率或失效情況的偵測度。 • 鑑別过程變數,以著眼於过程控制 • 列出潛在失效模式之排序,並據以建立考慮採取預防/矯正措施 的優先順序 • 將製造或組裝過程的結果予以文件化。
偵 測 度
R P N
建議措施
責任與 目標 完成日期
措施結果
嚴 難 偵 R
採行措施 重 檢 測 P
度 度 度 N
效應為何?
有多不好?
功能, 特徵 或要求為何?
原因為何?
其發生 頻率為何?
改善風險程度 能夠做什麼? -- 設計變更 -- 过程變更 -- 特別控制 -- 標準, 程序書 或指引變更 -- 導入防呆措施 -- 加強設備保養 -- 加強參數控制 -- 加強工作技能
FMEA
潜在失效模式及后果分析
FMEA 作業說明(FMEA 團隊遴選及流程)
FMEA作业指导书

1.目的通过产品设计或过程中可能产生的潜在失效及后果,寻找能避免或减少潜在失效发生的对策措施,从而及时消除实际的或潜在的不合格,最大限度地保证产品质量、降低成本,以满足顾客的要求。
2.适用范围适用于公司新产品、新工艺及其更改,以及由普通变差引起的质量问题对产品设计或工序过程可能造成失效后果的分析和预防。
3.权责3.1.技术部:负责组织设计、过程FMEA,制订相应对策措施。
3.2.模具设计课、生产部、采购课、品质部及相关部门:参与FMEA分析,并承担对策措施中的相应责任。
3.3.各生产部门:负责对策措施的实施。
3.4.项目副总:负责DFMEA、PFMEA对策的核准。
4.定义:4.1.FMEA:Potential Failure Mode and Effects Analysis(潜在失效模式及后果分析).4.2.DFMEA:设计FMEA4.3.PFMEA: 过程FMEA.4.4.RPN: 风险顺序数,RPN=严重度(S)*频度(O)*探测度(D)4.5.CFT:多功能小组4.6.CP: 控制计划5.作业内容5.1.FMEA流程图:无5.2.FMEA准备工作.5.2.1.DFMEA的准备工作.5.2.1.1.新项目评估时,根据客户要求制定,新项目可行性评估报告PPT档或DFMEA,由技术部负责组织,包含模具设计、品质部、生产部门及相关部门的技朮人员成立CFT小组,并指定一人为CFT小组组长,负责主导FMEA并跟进预防措施的施实.5.2.1.2.制定DFMEA 必须从所要分析的系统、子系统及/或零组件的方块图着手,故在制定DFMEA之前由项目工程师制定方块图,以做DFMEA分析时使用,此方块图应说明所要分析的各项目之间的主要关系,并建立一套合符逻辑的分析顺序,制定FMEA时,使用的方块图应附在FMEA中;5.2.2.PFMEA的准备工作5.2.2.1.由技术部负责组织,包含各生产部门,品质部及相关部门人员成立CFT小组,并指定一人为CFT小组组长, 负责主导FMEA并跟进预防措施的施实.5.2.2.2.初始过程流程图已确定,具体参考《产品先期策划与开发控制程序》执行,使用的流程图应附在FMEA中.5.2.2.3.特性矩阵图已确定,具体参考《产品先期策划与开发控制程序》执行.5.2.3.FMEA编号:按照《工程图纸技术文件管理作业指导书》执行。
PFMEA潜在失效模式及后果分析
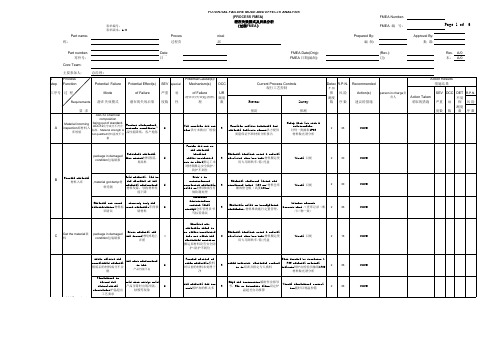
零件名称:过程责技术部编制:批准:Part number:KeyDate FMEA Date(Orig):FMEA Date(Rev.):Rev.A/0零件号:关键日FMEA 日期(编制):FMEA 日期(修订):版本:A/0Core Team:preservation溶解,保温零件名称:过程责技术部编制:批准:Part number:KeyDate FMEA Date(Orig):FMEA Date(Rev.):Rev.A/0零件号:关键日FMEA 日期(编制):FMEA 日期(修订):版本:A/0Core Team:零件名称:过程责技术部编制:批准:Part number:KeyDate FMEA Date(Orig):FMEA Date(Rev.):Rev.A/0零件号:关键日FMEA 日期(编制):FMEA 日期(修订):版本:A/0Core Team:零件名称:过程责技术部编制:批准:Part number:KeyDate FMEA Date(Orig):FMEA Date(Rev.):Rev.A/0零件号:关键日FMEA 日期(编制):FMEA 日期(修订):版本:A/0Core Team:零件名称:过程责技术部编制:批准:Part number:KeyDate FMEA Date(Orig):FMEA Date(Rev.):Rev.A/0零件号:关键日FMEA 日期(编制):FMEA 日期(修订):版本:A/0Core Team:零件名称:过程责技术部编制:批准:Part number:KeyDate FMEA Date(Orig):FMEA Date(Rev.):Rev.A/0零件号:关键日FMEA 日期(编制):FMEA 日期(修订):版本:A/0Core Team:。
FMEA作业指导书
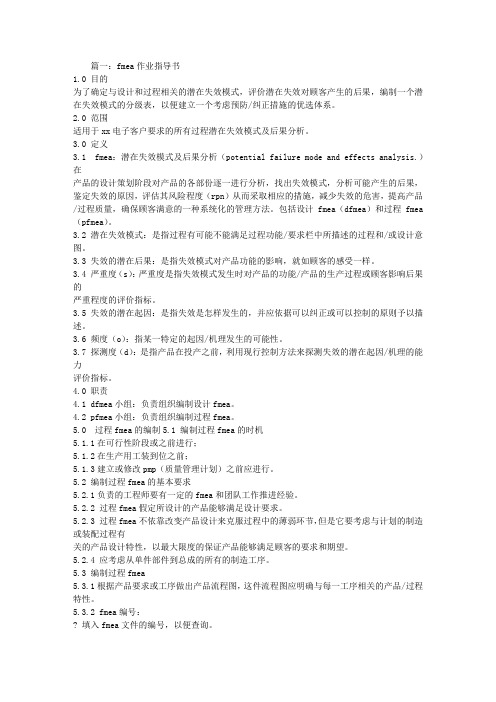
篇一:fmea作业指导书1.0 目的为了确定与设计和过程相关的潜在失效模式,评价潜在失效对顾客产生的后果,编制一个潜在失效模式的分级表,以便建立一个考虑预防/纠正措施的优选体系。
2.0 范围适用于xx电子客户要求的所有过程潜在失效模式及后果分析。
3.0 定义3.1 fmea:潜在失效模式及后果分析(potential failure mode and effects analysis.)在产品的设计策划阶段对产品的各部份逐一进行分析,找出失效模式,分析可能产生的后果,鉴定失效的原因,评估其风险程度(rpn)从而采取相应的措施,减少失效的危害,提高产品/过程质量,确保顾客满意的一种系统化的管理方法。
包括设计fmea(dfmea)和过程fmea (pfmea)。
3.2 潜在失效模式:是指过程有可能不能满足过程功能/要求栏中所描述的过程和/或设计意图。
3.3 失效的潜在后果:是指失效模式对产品功能的影响,就如顾客的感受一样。
3.4 严重度(s):严重度是指失效模式发生时对产品的功能/产品的生产过程或顾客影响后果的严重程度的评价指标。
3.5 失效的潜在起因:是指失效是怎样发生的,并应依据可以纠正或可以控制的原则予以描述。
3.6 频度(o):指某一特定的起因/机理发生的可能性。
3.7 探测度(d):是指产品在投产之前,利用现行控制方法来探测失效的潜在起因/机理的能力评价指标。
4.0 职责4.1 dfmea小组:负责组织编制设计fmea。
4.2 pfmea小组:负责组织编制过程fmea。
5.0 过程fmea的编制5.1 编制过程fmea的时机5.1.1在可行性阶段或之前进行;5.1.2在生产用工装到位之前;5.1.3建立或修改pmp(质量管理计划)之前应进行。
5.2 编制过程fmea的基本要求5.2.1负责的工程师要有一定的fmea和团队工作推进经验。
5.2.2 过程fmea假定所设计的产品能够满足设计要求。
FMEA潜在失效模式及后果分析
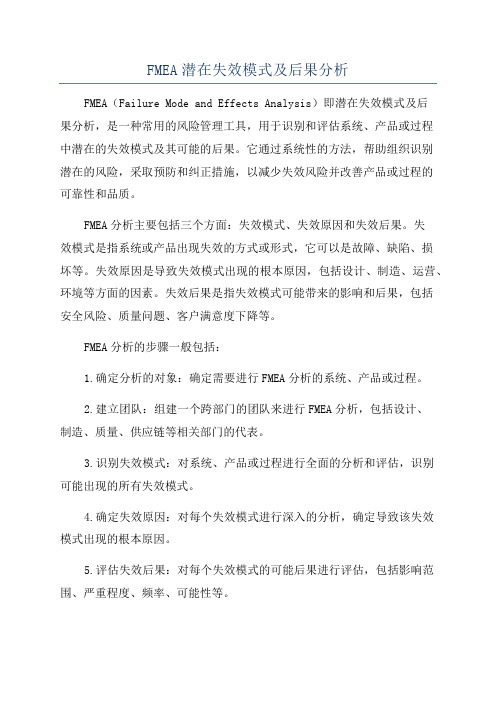
FMEA潜在失效模式及后果分析FMEA(Failure Mode and Effects Analysis)即潜在失效模式及后果分析,是一种常用的风险管理工具,用于识别和评估系统、产品或过程中潜在的失效模式及其可能的后果。
它通过系统性的方法,帮助组织识别潜在的风险,采取预防和纠正措施,以减少失效风险并改善产品或过程的可靠性和品质。
FMEA分析主要包括三个方面:失效模式、失效原因和失效后果。
失效模式是指系统或产品出现失效的方式或形式,它可以是故障、缺陷、损坏等。
失效原因是导致失效模式出现的根本原因,包括设计、制造、运营、环境等方面的因素。
失效后果是指失效模式可能带来的影响和后果,包括安全风险、质量问题、客户满意度下降等。
FMEA分析的步骤一般包括:1.确定分析的对象:确定需要进行FMEA分析的系统、产品或过程。
2.建立团队:组建一个跨部门的团队来进行FMEA分析,包括设计、制造、质量、供应链等相关部门的代表。
3.识别失效模式:对系统、产品或过程进行全面的分析和评估,识别可能出现的所有失效模式。
4.确定失效原因:对每个失效模式进行深入的分析,确定导致该失效模式出现的根本原因。
5.评估失效后果:对每个失效模式的可能后果进行评估,包括影响范围、严重程度、频率、可能性等。
6.确定风险优先级:根据失效后果的评估结果,为每个失效模式确定一个相应的风险优先级。
7.提出改进措施:根据风险优先级,制定相应的改进措施,包括预防措施、检测措施和纠正措施。
8.实施改进措施:将制定的改进措施付诸实施,并监控其有效性。
9.评估改进效果:评估实施改进措施后的效果,以判断改进措施是否有效,是否需要进一步优化。
FMEA分析具有许多优点,包括:1.早期预防:FMEA可以在产品设计和开发阶段开始进行,发现和解决潜在的风险和问题,避免在后期造成更大的损失和成本。
2.风险管理:FMEA可以帮助组织识别已知和未知的风险,评估其严重程度和可能性,制定相应的控制措施,以降低风险。
FMEA失效模式及后果分析手册精选全文

可编辑修改精选全文完整版FM E A 失效模式及后果分析手册FMEA (Failue Mode &Effect Analgsis ) Failue :失效、失败、不良 Mode :模式Effect :后果、效应、影响 Analgsis :分析一、FMEA 思维逻辑方法:D ’FMEA —→分析着重点BOM 表的零件及组装件P ’FMEA —→分析着重点OPC/AC 的零件加工及组装的工艺流程PRN 高风险优先系数 重点管理原则控制重点少数,不重要大多数列为次要管理 轻重缓急,事半功倍类比量产品(模块化) 工艺流程 过程参数/工艺条件 质量特性类比量产品 质量不良履历失败经验产品病历卡预设未来新产品投产后可能/潜在的会出现类似的不良事前 分析原因 整改措施(鱼刺图)先期产品质量策划结果控制计划(欧美) QC 工程表(台/日)新产品投产施工的要求监视和测量(首中末件检查)开发新产品例:有20项不良,前3项不良占70%,对策能解决50%的不良,70%*50%=35%后17项不良占30%,对策能解决100%的不良,30%*100%=30%①质量管理AC 柏拉图分析②物料管理MC 物料ABC法避免待料停工目的降低库存量的成本二、在何种情况下应进行FMEA分析:新产品开发阶段1、RP N≥1002、严重度/发生度/难检度(任一项)≥7;3、严重度≥7,发生度≥3;4、发生度≥5,难检度≥4量产阶段秉持持续改善的精神三、FMEA建立与更新时机1、新产品开发时;2、设计变更时(材质变更,BOM变更);3、工程变更;4、检验方法变更(检验设备/项目/频度)5、定期审查更新(建议每季度修订,至少也要每半年)四、FMEA分析表作成说明35%>30%重效果大,轻效果小活性化文件随时更新有效版本的识别(以修订日期)1、增加零件编号与名称:与BOM 表一致(D ’FMEA 分析,着眼在构成零件及组装件);2、增加工序编号与名称:与OPC/AC 表一致(P ’FMEA 分析,着眼在加工与组装工艺流程,D ’FMEA 可省略)3、功能与要求:已含外观、颜色、尺寸及ES TEST 功能质量要求;4、潜在失效模式:类比量产品质量不良履历(历史档)→产量履历→失效分析累积5、潜在失效效应(后果):万一不良时会造成的后果,如影响安全性/功能性/一般性,必须站在广义的客户中思考,包含: ● 下工程● 直接客户:下购销合同者/客户:如代理商 ● 最终客户:user/消费者6、严重度:参照对照表予以评估,复合型≥7;功能性4~6;一般性<4;7、分类(等级)class :与CC/SC 管制特性计划清单一致,包含符号识别,如FORD ▽,通用,依客户指定或本司对等的符合标注。
潜在失效模式及后果分析(FMEA)工作指引

6.0附录:FMEA填写
6.1 FMEA编号:填入FMEA文件的编号,以便查询。FMEA的编号原则如下:
P(或D)FMEA-X-001
①② ③
其中:
①PFMEA为“产品过程潜在失效模式及后果分析”的简称;DFMEA为“设计潜在失效模式及后果分析”的简称;
②“M”表示为话筒;“S”表示为喇叭;
一般与以前时有失效发生,但不占主要比例的过程相类似的工序有关
≥1.00
≤1.32
3
低
很少几次与相似过程有关的失效
≥1.33
≤1.66
2
非常低
5.2.1上述资料若不易收集,也可利用同类或相近产品的资料作某些假设,在以后的试验或使用过程中逐步完善、修改即可。
决定分析层次
5.3 FMEA小组确定任务和实施对象后,从产品的工艺和工序分层次进行分析;
5.3.1各层次之间的工艺和工序可以用检验或试验进行质量/环境判定。
绘制功能方块图
5.4(必要时采用)功能小组决定分析层次后,应描述各工序之间的工艺联系,其作用在使分析者了解该工序时,其输出与输入的逻辑关系。
3
非常低
外观或尺寸等项目不符合要求,但很少有顾客发现有缺陷且不影响使用
2
非常轻微
无影响(外观项目不符合要求,但很少有顾客发现有缺陷)
1
附表二:发生度分级参考
发生度
失效发生可能性
CP(参考)
发生度
非常高
失效几乎是不可避免的
<0.67
5
高
一般与以前经常发生失效的过程相似的工序有关
≥0.67
≤0.99
4
普通
6.7潜在失效起因/机理:潜在的失效起因是指失效是怎样发生的,并应依据可以纠正或可以控制的原则予以描述。针对每一个潜在的失效模式,在尽可能的范围内,应尽可能地列出每个可以可归结到每一失效模式的每一个潜在起因。如果起因对失效模式来说是唯一的(即:如果纠正该起因对该失效模式有直接的影响),那么这部分FMEA考虑的过程就完成了。但是,失效的许多起因往往并不是相互独立的,要纠正或控制一个起因,需要考虑诸如试验设计之类的方法,来明确哪些起因起主要作用,哪些起因最容易得到控制。起因列出的方式应有利于有的放矢地针对起因采取补救的努力。
过程潜在失效模式及后果分析(P-FMEA)
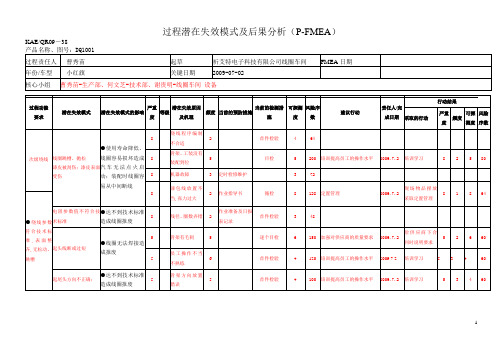
等级
潜在失效原因及机理
频度
当前的预防措施
当前的检测措施
可探测度
风险序数
建议行动
责任人/完成日期
行动结果
采取的行动
严重度
频度
可探测度
风险序数
高压插针烫锡
虚焊
●达不到技术标准造成线圈报废或返工;
5
温度过高、烫锡时间过长
3
巡检
高温预热后检测
4
60
●以便与外壳安装
无电阻
5
断线
7
逐个检测
2
70
高低压ቤተ መጻሕፍቲ ባይዱ装
5
人工剪的线头不够长
7
首件检验
4
140
培训提高员工的操作水平
2009.7.2
培训学习
5
4
4
80
绕线松弛、不整齐
●使用寿命降低、线圈电流大容易损坏造成汽车无法点火启动;
5
员工操作不当不熟练
3
首件检验
4
60
漆皮表面脱落
8
放置不当,挤压
3
作业指导书
目厕
5
120
定置管理
2009.7.2
物品摆放采取定置管理
8
电阻参数值不符合技术标准
●达不到技术标准造成线圈报废
8
线径、圈数弄错
2
作业准备及日报表记录
首件检验
3
48
起头线断或过短
●线圈无法焊接造成报废
5
骨架有毛刺
5
逐个目检
6
150
加强对供应商的质量要求
2009.7.2
给供应商下合同时说明要求
5
潜在的失效模式及后果分析(FMEA)(DOC 8页)

潜在的失效模式及后果分析(FMEA)(DOC 8页)潜在的失效模式及后果分析(FMEA)一.前言(一)目的:1. 发现、评价设计/过程中潜在的失效模式及后果;2. 找到能够避免或减少这些潜在失效发生的措施;3. 书面总结上述过程。
对设计/过程完善,确保顾客满意。
事前花时间进行综合的FMEA分析,能够容易\低成本地对产品或过程进行修改.减轻事后的危机。
减少或消除因修改带来的损失。
(二)发展历史:首次正式应用FMEA技术是60年代中期航天工业的一项革新。
(三)形式:1. 设计的潜在的失效模式及后果分析(DFMEA);2. 过程的潜在的失效模式及后果分析(PFMEA).事前花时间很好的进行FMEA分析,能够容易地、低成本的对设计/过程进行修改。
从而减轻事后修改的危机。
二.设计FMEA一.设计FMEA作用:用以下方法降低产品的失效风险:1.有助于对设计要求的评估及对设计方案的相互权衡2.有助于对制造和装配要求的最初设计3.提高对系统和车辆运行影响的可能4.对设计试验计划和开发项目提供更多的信息5.有助于建立一套改进设计和开发试验的优先控制系统6.为推荐降低风险的措施提供一个公开的讨论形式7.为将来的分析研究现场情况,评价设计的更改及开发更先进的设计,提供参考。
二.概念:1.严重度(S)——FMEA分析中,对零件、系统或顾客影响后果的严重程度。
(推荐后果评定准则;后果的严重程度严重度(S)无警告的严重危害无预兆;影响安全或违反政府规章10 有警告的严重危害有预兆;影响安全或违反政府规章9 很高车辆(系统)不能运行,丧失基本功能8高车辆(系统)能运行,性能下降,顾客7中等车辆(系统)能运行,舒适性下降,顾客不舒服 6低车辆(系统)能运行,舒适性下降,顾客轻微不舒服 5很低配合、外观或尖响、卡喀响等项目不符合要求,大多数顾客能发现的缺陷4轻微配合、外观或尖响、卡喀响等项目不符合要求,有一半顾客能发现的缺陷3很轻微配合、外观或尖响、卡喀响等项目不符合要求,有很少顾客能发现的缺陷2无无影响 1后果评定准则;后果的严重程度严重度(S)1.2.年型/车型:3.关键日期:DFMEA——在制造样件以前完成。
FMEA潜在失效模式及后果分析

2.改变弹簧几何尺寸
8
HIC
1.回火温度超差
2.回火时间超差
3
见上
质保部打硬度2只/班
4
96
8
HIC
1.回火炉设备故障
2.温度计失效
2
-设备预防性维修
-温度计采用PLC控制、温控报警装置
-定期对温度计标定、报警装置标定
-温度计寿命管理
-记录纸100%数据记录
-操作工检查1次/2h
-每周重新配置
检查PH值2次/班
5
90
加作业指导书关于表调液的调整方法
生产科
6
3
5
90
9-4磷化
精密度、厚度未符合要求
弹簧涂层易剥落防锈防腐性能降低
6
温度、时间、喷头压力、总酸度、游离酸度、促进剂比例失调
4
-检测中心对磷化液进行来料检查
-.操作者点检1次/2h
-检查磷化膜外观1次/2h
-检测SEA/重量2次/月
1.操作工定期抽检一班1次/2h
2.质保定期抽检1次/4h
3
72
专用量具
6
4
2
40
2
冷卷成形
-达到指定几何尺寸:
表面平滑
2-3.旋向错误
影响弹簧影响弹簧装配
6
方向绕反
2
同上
最后线菏载测试误差验证
1
12
总圈数
2-4.自由长度
力超差
影响整车舒适性
7
HIC
1.顶杆节距推出误差
2.设备精度误差
3
-首件样品确认程序
-设备PM计划
-.操作者1次/2h
-.QC 2次/4h
潜在失效模式及后果分析(FMEA)作业指导书

广州市XXX股份有限公司FMEA作业指导书文件编号:版本:编制:审核:批准:修订记录日期修订版本修订内容的描述修订人2010.05.27 B.1 1、根据FMEA第四版的要求,更新严重度,发生率、探测率评价准则表内容。
2、修订“FMEA开发时机、更新维护、与其它文件的关联”内容,具体见正文第5节。
3、修订D/PFMEA表格。
2015-4-13 C.1 1、增加制作FMEA的流程简图。
2、增加对失效模式采取措施项的规则。
3、修订特殊特性标识的定义。
2018-7-4 D.1 1、增加IATF16949:2016标准10.2.4 防错的要求;2、增加安全特性“SC”的标识;3、增加FMEA上传OA后的邮件提醒。
FMEA作业指导书1目的1.1了解本公司产品在故障、寿命、安全、效率、可靠性等方面的潜在的失效模式,评估其风险序数,寻找预防失效发生的方法, 并采取改善措施减少高风险的失效模式产生, 以及透过FMEA的实施持续改进产品设计从而降低成本。
1.2在制造过程策划阶段对产品的工艺流程或更改的工艺流程进行早期的评审和分析,以便预测、解决或监控潜在的过程问题,从而提高产品质量。
2范围2.1DFMEA适用于新设计、新技术以及对现有设计的修改;2.2PFMEA适用于新工艺流程以及对现有工艺流程的修改。
3职责和权限3.1机械/电气设计工程师负责主导设计FMEA的策划、制作、维护(DFMEA);3.2工艺工程师负责主导过程FMEA的策划、制作、维护(PFMEA);3.3项目小组成员(包括:机械/电气设计工程师、QC工程师、工艺工程师,测试工程师、技术服务工程师、生产主管)共同参与FMEA策划、制作、维护。
4定义4.1FMEA指潜在失效模式及后果分析,是发现和评价产品/过程中的潜在失效模式和失效后果,通过引起失效要因的分析,以找到能够避免或减少这些潜在失效模式发生的措施的一组系统性、文件化的活动。
4.2特殊特性产品特性或制造过程特性,可能影响产品的安全性或法规的符合性、配合、功能、性能或其后续过程的产品特性或制造过程参数。
FMEA失效模式及后果分析手册
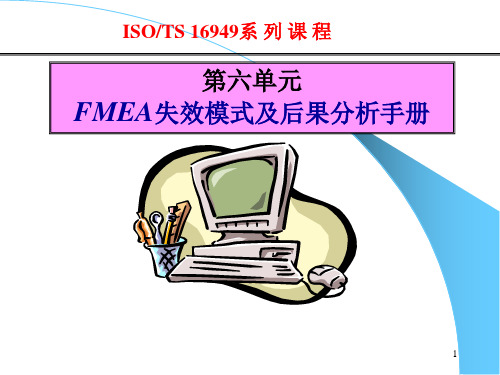
核心小组: A.-Tade -- 车身工程师 J.Smith –-作业控制 R. James – 制造部 J. J ones—维修部
(8)
过程功 能
潜 潜严 在 在重 失 失度
分 类
潜在失 效起因/
发 生
效 效 (S) (1 机理(14) 率
现行预防 控制(16)
要 求
模 式
效 (1 应 2)
3)
(O)
效应
无警告的 严重危害 有警告的 严重危害
很高 高
中等
低 很低 轻微 很轻微 无
判定准则:效应的严重度这级别导致当一个潜在失
交效模式造成了在最终顾客和/或制造/组装工厂的
缺陷。应该随时首先考虑到最终顾客。如果在两者
都发生缺陷,则采用较高两级的严重度
(顾
客效应)
判定准则:效应的严重度这级别导致当一个潜在失交
把相似过程的比较和顾客(最终用户和后续作业)对类似零组件的投诉情况的研究
作为出发点。此外,对设计目的的了解也很必要。典型的失效模式可能是,但不局限
于下列情况:
弯曲
毛刺
毛位错误
断裂
孔太浅 孔未加工
搬运损坏
脏污
孔太深
表面太粗造 变形
表面太平滑
开路
短路
未贴标签
注:应该用物理的、专业性的术语来描述潜在失效模式,而不同于顾客所见的现象。
效模式造成了在最终顾客和/或制造/组装工厂的缺陷。
应该随时首先考虑到最终顾客。如果在两者都发生缺 陷,则采用较高两级的严重度 (制造/组装效应)
级 别
严重级别很高。潜在失效模式影响车辆安全运行和/ 或,可能危及作业员(机器或组装)而无警告。
10
潜在失效模式及后果分析(过程FMEA)

潜在失效模式及后果分析(过程FMEA)FMEA过程FMEA标准表编制说明1FMEA编号填入FMEA文件编号,以便查询。
2项目注明正在进行过程分析的系统、子系统或部件的名称及编号。
3过程责任填入整车、部门和小组。
如已知,还应包括供方的名称。
4编制人填入负责编制FMEA的工程师的姓名、电话和所在公司的名称。
5车型年/车辆类型填入所分析的设计/过程将要应用和/或影响的车型年/车辆类型(如已知的话)。
6关键日期填入初次FMEA应完成的时间,该日期不应超过计划的投入生产日期。
7FMEA日期(编制)填入编制FMEA原始稿的日期及最新修订的日期。
8核心小组列出有权确定和/或执行任务的部门的名称和个人的姓名。
9过程功能/要求填入被分析过程或工序的简要说明(如车削、钻孔、功丝、焊接、装配等)。
——过程功能:列出与所分析的每一个过程步骤相或操作相对应的过程功能。
——要求:列出所分析的过程步骤/操作的每一个过程功能的要求。
10潜在失效模式所谓潜在失效模式是指过程有可能不能满足过程功能/要求栏中所描述的过程要求和/或设计意图。
11潜在失效后果失效的潜在后果是指失效模式对顾客产生的影响。
12严重度(S)严重度是一给定失效模式最严重的影响后果的级别。
严重度数值的降低只有通过设计更改才能够实现。
13级别本栏目可用于对那些可能需要附加的过程控制的部件、子系统或系统的特殊产品或过程特性的分级(如关键、主要、重要、重点)。
14潜在失效起因/机理所谓失效的潜在要因是指失效是怎样发生的,并应依据可以纠正或可以控制的原则予以描述。
15频度(O)频度是指某一特定的要因发生的可能性。
16现行过程控制现有的过程控制是对已经采用的防止失效模式或其要因发生的控制措施的现状说明。
有两类过程控制可以考虑:——预防:防止失效的要因或失效模式出现,或者降低其出现的几率;——探测:探测出失效的要因或者失效模式,导致采取纠正措施。
17探测度(D)探测度是与过程控制栏中所列的最佳探测控制相关联的定级数。
FMEA作业指导书
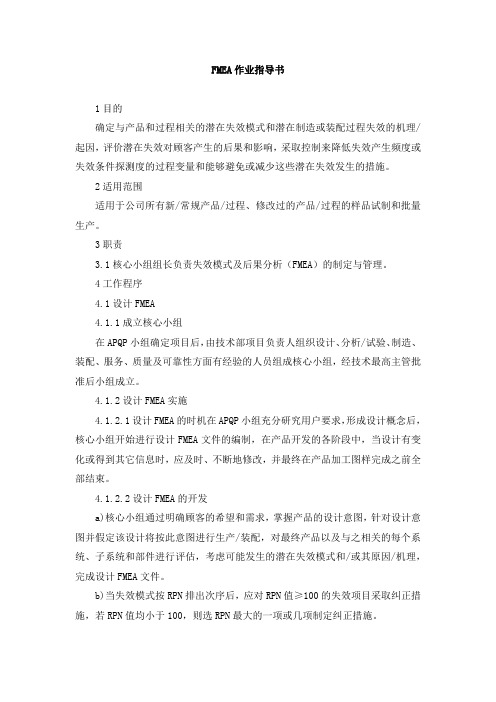
FMEA作业指导书1目的确定与产品和过程相关的潜在失效模式和潜在制造或装配过程失效的机理/起因,评价潜在失效对顾客产生的后果和影响,采取控制来降低失效产生频度或失效条件探测度的过程变量和能够避免或减少这些潜在失效发生的措施。
2适用范围适用于公司所有新/常规产品/过程、修改过的产品/过程的样品试制和批量生产。
3职责3.1核心小组组长负责失效模式及后果分析(FMEA)的制定与管理。
4工作程序4.1设计FMEA4.1.1成立核心小组在APQP小组确定项目后,由技术部项目负责人组织设计、分析/试验、制造、装配、服务、质量及可靠性方面有经验的人员组成核心小组,经技术最高主管批准后小组成立。
4.1.2设计FMEA实施4.1.2.1设计FMEA的时机在APQP小组充分研究用户要求,形成设计概念后,核心小组开始进行设计FMEA文件的编制,在产品开发的各阶段中,当设计有变化或得到其它信息时,应及时、不断地修改,并最终在产品加工图样完成之前全部结束。
4.1.2.2设计FMEA的开发a)核心小组通过明确顾客的希望和需求,掌握产品的设计意图,针对设计意图并假定该设计将按此意图进行生产/装配,对最终产品以及与之相关的每个系统、子系统和部件进行评估,考虑可能发生的潜在失效模式和/或其原因/机理,完成设计FMEA文件。
b)当失效模式按RPN排出次序后,应对RPN值≥100的失效项目采取纠正措施,若RPN值均小于100,则选RPN最大的一项或几项制定纠正措施。
c)执行纠正措施后,计算并记录RPN的结果。
如措施后的RPN级数仍≥100,应考虑采取进一步的措施,并对措施后的RPN再次评审。
4.1.3跟踪负责设计的工程师应负责保证所有的建议措施已被实施或已妥善地落实。
负责设计的工程师可采用以下几种方式来保证所关注的问题得到明确,所建议的测试得到实施:●保证设计要求达到得到实现;●评审工程图样和规范;●确认这些已反映在装配/生产文件之中;●评审过程FMEA和控制计划。
- 1、下载文档前请自行甄别文档内容的完整性,平台不提供额外的编辑、内容补充、找答案等附加服务。
- 2、"仅部分预览"的文档,不可在线预览部分如存在完整性等问题,可反馈申请退款(可完整预览的文档不适用该条件!)。
- 3、如文档侵犯您的权益,请联系客服反馈,我们会尽快为您处理(人工客服工作时间:9:00-18:30)。
1目的过程潜在失效模式及后果分析,简称PFMEA。
是一种信赖度分析的工具,可以描述为一组系统化的活动,是对确定产品/过程必须做哪些事情才能使顾客满意这一过程的补充。
其目的是:(a)并评价产品/过程中的潜在失效以及该失效的后果;(b)确定能够消除或减少潜在失效发生机会的措施;(c)将全部过程形成文件。
2 范围:适用于公司用于汽车零组件的所有新产品/过程的样品试制和批量生产。
适用于过程设计的风险性及后果的分析;适用于过程重复,周期性永不间断的改进分析。
3 术语和定义:1)PFMEA:指Process Failure Mode and Effects Analysis(过程失效模式及后果分析)的英文简称。
由负责制造/装配的工程师/小组主要采用的一种分析技术,用以最大限度地保证各种潜在的失效模式及其相关的起因/机理已得到充分的考虑和论述。
2)失效:在规定条件下(环境、操作、时间),不能完成既定功能或产品参数值和不能维持在规定的上下限之间,以及在工作范围内导致零组件的破裂卡死等损坏现象。
3)严重度(S):指一给定失效模式最严重的影响后果的级别,是单一的PFMEA范围内的相对定级结果。
严重度数值的降低只有通过设计更改或重新设计才能够实现。
4)频度(O):指某一特定的起因/机理发生的可能发生,描述出现的可能性的级别数具有相对意义,但不是绝对的。
5)探测度(D):指在零部件离开制造工序或装配之前,利用第二种现行过程控制方法找出失效起因/机理过程缺陷或后序发生的失效模式的可能性的评价指标;或者用第三种过程控制方法找出后序发生的失效模式的可能性的评价指标。
6)风险优先数(RPN):指严重度数(S)和频度数(O)及不易探测度数(D)三项数字之乘积。
7)顾客:一般指“最终使用者”,但也可以是随后或下游的制造或装配工序,维修工序或政府法规。
4职责技术装备部负责过程潜在失效模式及后果分析,并填写相应分析表格。
各部门按APQP要求参与过程FMEA活动。
5工作流程和内容:过程PFMEA实施与启动的顺序。
见图1当顾客或公司有需求和要求时,项目组依APQP要求,在生产用工装准备之前,在可行性阶段或之前进行过程失效模式及后果分析(以下简称过程PFMEA),经项目组长核准。
如顾客有要求时,过程PFMEA必须提交顾客评审和批准。
1)针对新产品,项目组将建立和制订其单独的过程PFMEA;针对常规产品(即:老产品),项目组根据其系列分类、相同的工艺流程/过程和相同的产品/过程特性(特别是其相同的产品/过程特殊特性)建立和制定其通用的过程PFMEA。
2)项目组应列出产品生产过程流程图清单,过程PFMEA从产品整个过程的流程图开始,该产品的流程图应确定与每一工序相关的产品/过程特性。
项目组应将用于该产品过程PFMEA准备工作的流程图纸的复印件,附在该产品过程PFMEA分析表之后,作为进行该产品过程PFMEA分析的依据。
3)项目组在进行过程PFMEA前,应根据该产品的过程流程图,先完成过程PFMEA过程流程图风险评定表的风险分析和评估:★该风险分析和评估必须考虑到所有制造工序,过程PFMEA 应包括从进料检验到出货的所有过程的特殊特性。
★分析产品在制造过程中的每一个工序步骤操作评定过程的风险(如:高、中、低风险)。
★对评定为高风险(即:RPN≧100和/或严重度≧8)的工序/项目和特殊特性应优先采取纠正与预防措施。
★当顾客有要求或公司认为需要的中等风险,也应对其纠正与预防措施。
★在确定了潜在的失效模式之后,应采取纠正/预防措施来消除潜在失效模式或不断减少它们发生的可能性。
4)在进行过程PFMEA时,应假定所设计的产品能够满足设计要求,因为设计缺陷和薄弱环节所产生的潜在失效模式可包括在过程图1. PFMEA过程顺序PFMEA过程潜在失效模式及后果分析顺序4PFMEA中,但它们的影响/后果及避免措施由设计DFMEA来解决。
5)过程PFMEA并不是依靠改变产品设计来克服过程中的缺陷和薄弱环节的,但它要考虑与计划的制造或装配过程有关的产品设计特性,以最大限度的保证产品能满足顾客的要求和期望。
6)公司必须对每一个过程中所涉及到的产品和/或过程的特殊特性进行过程(PFMEA),并寻找最佳改善方法努力改进过程,以防止发生缺陷和预防潜在失效发生,而不是依靠检测找出缺陷和失效。
在过程PFMEA分析过程中1)被评价列为高RPN(RPN≧100)的项目/工序和/或严重度≧8的项目/工序,公司必须将其列为特殊特性。
2)对所有被评价为高RPN的项目/工序和/或严重度≧8的项目/工序必须制定纠正/预防措施。
3)对不可降低的高RPN项目/工序和/或严重度≧8的项目/工序必须附有明确的探测方法。
所有的特殊特性均需在过程PFMEA中加以说明,并将特殊特性的符号或记号在过程PFMEA中进行明确标识;进行过程PFMEA可采用参考手册《FMEA潜在的失效模式及后果分析》第三版中规定的格式---“潜在的失效模式及后果分析表(过程FMEA)”进行,见附表1。
(如顾客有特殊要求时则依顾客规定的表单进行)。
填写过程(PFMEA)的栏目说明:PFMEA编号:填入PFMEA文件的编号,以便查询。
PFMEA的编号原则:PFMEA 零(组)件图号。
例如: PFMEA LJZ/J-001项目名称:填入正在进行过程分析的系统、子系统或部件的过程名称和编号。
过程责任:填整车厂(OEM)、部门和小组。
编制者:填入负责准备PFMEA工作的工程师的姓名、电话及所在公司名称。
车年型/项目(或产品型号):填入所分析的设计/过程将要应用和/或影响的车年型/项目(如果已知的话),如果未知道的话则填入进行PFMEA分析的产品规格/型号。
关键日期:填入初次PFMEA应完成的日期,该日期不应超过计划的投入生产的日期。
对本公司初始的PFMEA日期不应超过顾客要求的生产件批准(PPAP)的提交日期。
PFMEA 日期:填入编制PFMEA原始稿的日期及最新修订的日期。
核心小组(主要参加人):列出有权确定和/或执行任务的责任部门的名称和个人姓名。
过程功能/要求:★填入被分析的过程或工序的简要说明(如:车削、钻孔、攻丝、焊接、装配等),并记录所分析的步骤的相关过程/工序编号。
★核心小组应评审适用的性能、材料、过程、环境和安全标准,并以尽可能简洁的方式指明所分析的过程或工序的目的,包括有关系统、子系统或部件的设计(度量/变量)的信息。
★如果过程包括许多具有不同潜在失效模式的工序(如装配),则可以把这些工序作为独立过程列出。
潜在失效模式:指过程有可能发生不能满足过程功能要求栏中所描述的过程要求和/或设计意图,是对该特定工序上的不符合要求的描述。
它可能是下一工序的某个潜在失效模式的一个相关起因或者是前一工序的某个潜在失效模式的一个相关后果。
但是,在PFMEA准备中,应假定提供的零件/材料是正确和合格的。
1)按照部件、子系统、系统或过程特性,列出特定工序的每一个潜在失效模式,前提是这是这种失效可能发生,但不一定发生。
过程工程师对以下问题应能提出并能回答,并以对类似过程的比较和对顾客(最终使用者和后续工序)对类似部件的索赔研究为起点。
★过程/零件怎样不满足要求★无论工程规范如何,顾客(最终使用者,后续工序或服务)认为的可拒收的条件是什么2)一般的失效模式可能是但不仅仅局限于下列情况:弯曲、孔错位、粘合、毛刺、开孔太浅、开孔太深、漏开孔、表面太粗糙、表面太平滑、贴错标签、转运损坏、断裂、变形、脏污、安装调试不当、接地、短路、工具磨损等。
潜在的失效后果:指失效模式对顾客产生的影响。
根据顾客可能发现或经历的情况来描述失效的后果,顾客可能是内部的顾客也可能是最终用户;如果失效模式可能影响安全性或对法规的符合性,则PFMEA分析人员要对其清楚地予以说明。
顾客可以是下一道工序、后续工序或工位、经销商和/或车主。
当评价潜在失效后果时,这些因素都必须予以考虑。
1) 对最终使用者来说,失效的后果应一律用产品或系统的性能来描述,如:噪声、工作不正常、不能工作、泄漏、返工/返修、报废、不起作用、不稳定、牵引阻力、外观不良、粗糙、费力、异味、工作减弱、漏油、侵蚀、间歇性工作、车辆控制减弱、顾客不满意等。
2) 如果顾客是下一道工序或后续工序或工位,失效的后果应用过程/工序性能来描述,如:无法紧固、无法钻孔/攻丝、无法安装、无法加工表面、危害操作者、不能配合、不能连接、不匹配、损坏设备、引起工装过度磨损等。
严重度(S):指一给定失效模式最严重的影响后果的级别,是单一的PFMEA范围内的相对定级结果。
严重度数值的降低只有通过设计更改或重新设计才能够实现。
严重度仅适用于失效的后果,严重度的评估分为1—10级(见表1)。
级别(分级):用来对那些可能需要附加的过程控制的部件、子系统或系统的特殊产品或过程特性的分级(如:关键、重要、等)。
如果过程PFMEA中确定了分级,应通知负责设计的工程师,因为这可能影响涉及及控制项目标识的工程文件。
产品和/或过程的特殊特性符号应在此栏目中予以明确标识/注明。
潜在失效起因/机理:潜在的失效起因是指失效是怎样发生的,并应依据可以纠正或可以控制的原则予以描述。
针对每一个潜在的失效模式,在尽可能的范围内,应尽可能地列出每个可以可归结到每一失效模式的每一个潜在起因。
如果起因对失效模式来说是唯一的(即:如果纠正该起因对该失效模式有直接的影响),那么这部分PFMEA考虑的过程就完成了。
但是,失效的许多起因往往并不是相互独立的,要纠正或控制一个起因,需要考虑诸如试验设计之类的方法,来明确哪些起因起主要作用,哪些起因最容易得到控制。
起因列出的方式应有利于有的放矢地针对起因采取补救的努力。
1)一般的失效起因可包括但不限于:扭矩不当——过大或过小;焊接不当——电流、时间、压力不正确;测量不精确;热处理不当——时间、温度有误;浇口/通风不足;润滑不足或无润滑;零件漏装或错装;磨损的定位器;磨损的工装;定位器上有碎屑;损坏的工装;不正确的机器设置;不正确的程序编制等。
2)列表分析时应列出具体的错误或故障情况(如:操作者未装密封件),而不应用一些含糊不清的词语(如:操作者错误、设备不正常)。
频度(O):指某一特定起因/机理发生的可能性。
描述出现的可能性的级别数具有相对意义,但不是绝对的。
通过设计更改或过程更改来预防或控制失效模式的起因/机理是可能导致发生评度数降低的唯一的途径。
频度评估的大小分为1—10级(见表2)计算范例由可能的失效率为5/1000件来确定PpK 值的计算过程演示如下:缺陷率=10005=.将除以2得出高于或低于规范以外的部分。
205.0=使用“Z”表查到尾值为所对应的“Z”值为。
(见《控制图的应用指 导书》Z 表的使用) ① 引入公式: Z USL =2/d X USL R δ- Z LSL =2/d LSLX R δ-X =均值,SL =规范② 确定Z 最小值: Zmin= Z USL 或Z LSL 的最小值③ 计算Ppk ,使用以下公式:Ppk=3min Z =Ppu (即2/3d R δ)或CPL (即2/3d R δ)的最小值式中:USL 和LSL 为工程规范的上、下限,X 为过程均值,δ为过程标准偏差,由R /d 2计算得到。