SF1603PT中文资料
士徒特型号PG01_2 电路保护屏熔片,6.3x32mm,400-500VAC,400VDC,1-3

1Cartridge Fuse, 6.3x32 mm, 400-500 VAC, 400 VDC, 1-32 A, High Breaking Capacity up to 3500 ASee below:Approvals and Compliances UL 248-14 · 400 - 500 VAC · Time-Lag TDescription- 6.3 x 32 mm fuses for primary protection - 16 rated currents from 0.5 A to 32 A - 400 VDC pending for 5, 6.3, 8 AUnique Selling Proposition- High rated voltages up to 500 VAC / 400 VDC - High breaking capacity up to 3500 A- Suitable for pulse-shaped continuous currents- Useable for commercial cooking appliances according UL 197Applications- 3-phase applications - DC applications - Photovoltaic- Frequency converter - Power electronics- Commercial cooking appliancesReferences Packaging DetailsPigtail Type SHT 6.3x32 PigtailWeblinkspdf data sheet , html data sheet , General Product Information , Packaging details , Distributor-Stock-Check , Detailed request for product , MicrositeApplication Note Primary Protection in Equipment with further information on increased Pulse Strength and their test conditions according to inter-national standards see Impulse Withstand VoltageT echnical DataRated Voltage 400 - 500 VAC, 63 - 400 VDC Rated current 0.5 - 32 ABreaking Capacity 3500 A - 20 kA Characteristic Time-Lag TMountingFuseholder / Clip Admissible Ambient Air Temp.-40 °C to 85 °CClimatic Category 40/085/21 acc. to IEC 60068-1Material: Tube CeramicMaterial: Endcaps Nickel-Plated Copper Alloy Material: Axial Leads Tin-Plated Copper Unit Weight2.84 gStorage Conditions 0 °C to 60 °C, max. 70% r.h.Product Marking, Type, Rated current, Rated Voltage, Characteristic, Breaking capacity, Ap-provalsApprovals and CompliancesDetailed information on product approvals, code requirements, usage instructions and detailed test conditions can be looked up in Details about ApprovalsSCHURTER products are designed for use in industrial environments. They have approvals from independent testing bodies according to national and international standards. Products with specific characteristics and requirements such as required in the automotive sector according to IATF 16949, medical technology according to ISO 13485 or in the aerospace industry can be offered exclusively with customer-specific, individual agree-ments by SCHURTER.ApprovalsThe approval mark is used by the testing authorities to certify compliance with the safety requirements placed on electronic products. Approval Reference T ype: SHT 6.3x32Approval LogoCertificates Certification Body DescriptionUL ApprovalsULUL File Number: E41599Product standardsProduct standards that are referencedOrganization Design Standard DescriptionDesigned according to UL 248-14Low voltage fuses - Part 14: Additional fusesDesigned according to CSA22.2 No. 248.14Low-Voltage Fuses - Part 14: Supplemental Fuses Application standardsApplication standards where the product can be usedOrganization Design StandardDescriptionDesigned for applications acc.IEC/UL 60950IEC 60950-1 includes the basic requirements for the safety of informationtechnology equipment.CompliancesThe product complies with following Guide LinesIdentification Details Initiator DescriptionCE declaration of conformity SCHURTER AG The CE marking declares that the product complies with the applicablerequirements laid down in the harmonisation of Community legislation onits affixing in accordance with EU Regulation 765/2008.RoHS SCHURTER AG EU Directive RoHS 2011/65/EUChina RoHS SCHURTER AG The law SJ / T 11363-2006 (China RoHS) has been in force since 1 March2007. It is similar to the EU directive RoHS.REACH SCHURTER AG On 1 June 2007, Regulation (EC) No 1907/2006 on the Registration,Evaluation, Authorization and Restriction of Chemicals 1 (abbreviated as"REACH") entered into force.Dimension [mm] 6.3 mm23Time-Current-CurvesT i m e i n S e c o n d sMultiple of Rated Current InAll VariantsPackaging Unit xxxx.xxxx Small Box Pack (10 pcs.)xxxx.xxxx.G Bulk (1000 pcs.)The specifications, descriptions and illustrations indicated in this document are based on current information. All content is subject to modifications and amendments. Information furnished is believed 0 5 . 0 2 . 2 0 1 94。
立鼎光电探测器产品手册(第二版)说明书
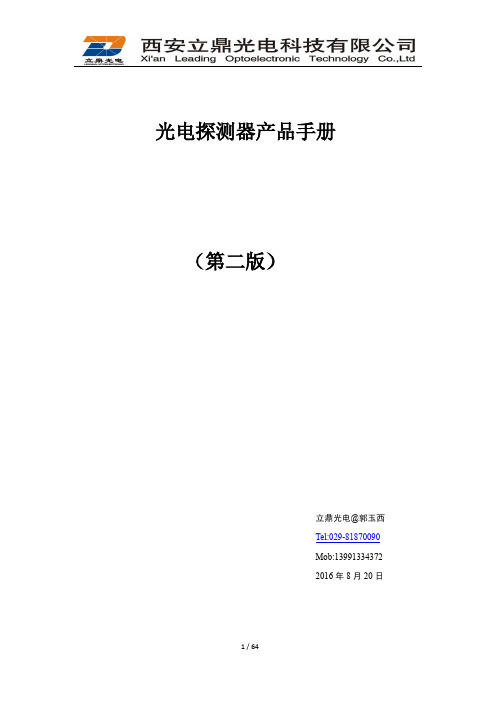
光电探测器产品手册(第二版)立鼎光电@郭玉西Tel*************Mob:139****43722016年8月20日立鼎光电探测器事业部简介西安立鼎光电科技有限公司是一家专业从事各种光电类产品及其部件、组件、元件的研发生产、系统集成、专业代理销售推广为一体的高新技术企业。
公司专注于为客户提供从元件、组件、部件到全套光电系统产品的完整解决方案。
总部位于中国古都西安的电子城街区和高新技术开发区之间,周围有众多知名高校、科研院所及高新技术企业,科研创新氛围浓厚,是公司人才引进和技术创新的强大源泉。
为了高效便捷地服务于国内广大客户,公司在北京、深圳、上海、武汉、香港等地设有分公司或办事处。
公司自成立以来,秉承“资源整合,自主创新”之思想研发产品的同时,也致力于将国外的先进产品和技术引进到国内。
立鼎光电探测器事业部以市场为导向,有效整合探测器资源,多年来与世界多家知名的探测器厂商建立了紧密的合作关系,一直专注于探测器产品在国内的售前、售中及售后的优质服务。
客户范围覆盖了航空、航天、兵器、船舶、电子、核工业等十大军工集团以及中科院所、知名高校和工农业领域。
我们始终秉承“领先技术、诚实服务、合作共赢”的发展理念,真诚与国内外广大用户、合作伙伴及同行携手合作,共创光电事业美好明天!产品目录光电探测器中华立鼎(CLPT)短波点元/焦平面探测器--------------------------------------------4 波兰VIGO公司MCT探测器及组件-----------------------------------------------------10 美国InfraRed 中/长波及双色探测器-----------------------------------------------------13 德国IFW 紫外探测器-----------------------------------------------------------------------18 美国EOS全波段光电探测器---------------------------------------------------------------22 美国GPD近红外探测器--------------------------------------------------------------------25 西班牙NIT硒化铅中波探测器------------------------------------------------------------29 德国ALPHALAS可见光/近红外高速探测器-------------------------------------------36 美国AGI短波/中波探测器-----------------------------------------------------------------40美国Teledyne Judson全波段探测器------------------------------------------------------43 俄罗斯Ekran像增强器及光电倍增管----------------------------------------------------45一、中华立鼎(CLPT )公司短波探测器前瞻技术研究室中华立鼎光电是一家研发、生产高品质InGaAs 短波探测器的公司,其产品从点元探测器到面阵探测器一应俱全,质量可靠,价格合理,得到世界客户的广泛认可和应用。
西安神电避雷器

Y5WR-51/134
YH5WR-51/134
Y5WR-84/221
YH5WR-84/221
Y5WR-90/236
YH5WR-90/236
系 统 避雷器 避雷器 直 流 2mS 雷电冲 操作冲 伞径 高度 图
标 称 额 定 持续运 1mA 参 方波通 击电流 击电流
电 压 电 压 行电压 考电压 流容量 下残压 下残压 Φ
95 255 1
10
17 13.6 24.0 150 45.0 51.8 38.3
92 270 2
-4-
续表 2
特性
产品
参数
型号
Y5WZ-51/134
YH5WZ-51/134
系 统 避雷器 避雷器 直 流 2mS 雷电冲 陡波冲 操作冲 伞径 高度 图 标 称 额 定 持续运 1mA 参 方波通 击电流 击电流 击电流 电 压 电 压 行电压 考电压 流容量 下残压 下残压 下残压 Φ H
95 255 1
10
12
9.6 17.4 150 32.4 37.2 27.6
YH5WZ-12/32.4
92 270 2
Y5WZ-15/40.5 10
YH5WZ-15/40.5
95 255 1 15 12.0 21.8 150 40.5 46.5 34.5
92 270 2
Y5WZ-17/45 YH5WZ-17/45
178 1150 9
Y5WZ-90/235
252 1210 8
66
90 72.5 130 600 235 270 201
YH5WZ-90/235
178 1150 9
Y10WZ-90/235 66
YH10WZ-90/235
SF2004PT中文资料

CAPACITANCE.(pF)
200 100 50
Tj=25 C f=1MHz Vsig=50mVp-p
0
1
SF2007PT-SF2008PT
20 10 0.1
0.2 0.1
Pulse Width=300 s 2% Duty Cycle
0 0.2 0.4 0.6 0.8 1.0 1.2 1.4 1.6 1.8
VRRM VRMS VDC I(AV) IFSM VF IR
10 uA 400 Trr 35 nS Typical Junction Capacitance (Note 1) Cj 175 pF ℃/W Typical Thermal Resistance (Note 3) 2.5 RθJC ℃ Operating Junction Temperature Range TJ -55 to +150 ℃ Storage Temperature Range TSTG -55 to +150 Notes: 1. Measured at 1 MHz and Applied Reverse Voltage of 4.0V D.C. 2. Reverse Recovery Test Conditions: IF=0.5A, IR=1.0A, Recover to 0.25A. 3. Thermal Resistance from Junction to Case Mounted on Heatsink size 3”x5”x0.25” Al-Plate.
1
TJ=25 0C
0.1 200 150 100 50
8.3ms Single Half Sine Wave JEDEC Method TJ = TJ max.
。册手户用机片单列系考参请标指数参细详

Texax Instruments 应用报告 SLAA409A-2009 06基于MSP430F471XX 系列系列单片机的三相电能单片机的三相电能单片机的三相电能表表实现作者:Stephen Underwood, Vincent Chan and Kripasagar Venkat MSP430应用摘要本应用报告描述了运用TI 公司生产的片上系统微处理器MSP430F471XX ,如何来实现三相电能表。
本应用报告运用片上系统计量解决方案包含如下重要信息:测量软件、硬件和校准步骤。
此三相电能表利用电流互感器作为传感器实现,最终仪表性能指标详见报告尾页。
1 简介这款MSP430F471XX 单片机属于MSP430F4XX 系列。
此类单片机因具有独特的内部架构,主要应用于电能测试计量场合。
具有MSP430CPUX 内部架构的MSP430F471xx 系列单片机拥有强大的16MHz 主频的CPU 。
具有二阶∑-∆结构支持差分输入的七路模数转换器(ADC )。
∑-∆ 的ADCs (SD16)具有16位精度,能够配置成群组模式,在同一信号触发下同时对电流和电压采样。
每一个SD16模块都支持电压到-1V 的普通模式,并且所有传感器均可以地为基准源。
另外,它具有可编程增益放大器,对低信号输出的传感器最大可放大32倍。
片上32位X 32位的硬件乘法器在计算电能时可以更加快速进行数学运算。
软件对三相电和单相电支持多种参数计算,在电能测量时,关键的计算测量参数有:电流和电压真有效值、无功功率、有功功率、功率因数、和频率。
以上所有运算占用CPU 处理能力的1/3,并消耗1/10的单片机资源。
此应用以“ZIP”格式文件提供测量源代码。
2 程序程序框图框图图1描述了三相电能表应用的高级接口程序框图。
三相电四线制星形接法如下图所示。
电流互感器连接到每一单相电的电流,采样分压电阻成比例采样电压。
每一路电流互感器都串联一个负载电阻以保护测量设备。
MCP1603资料
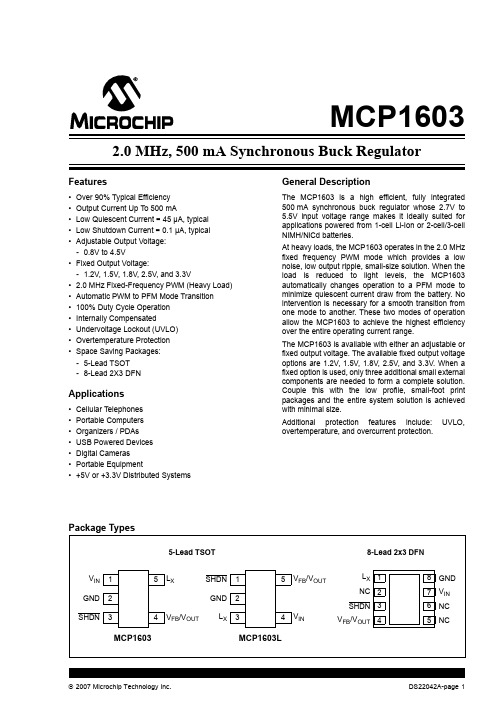
© 2007 Microchip Technology Inc.DS22042A-page 1MCP1603Features•Over 90% Typical Efficiency •Output Current Up To 500mA•Low Quiescent Current = 45µA, typical •Low Shutdown Current = 0.1µA, typical •Adjustable Output Voltage: -0.8V to 4.5V•Fixed Output Voltage:- 1.2V, 1.5V, 1.8V, 2.5V, and 3.3V• 2.0MHz Fixed-Frequency PWM (Heavy Load)•Automatic PWM to PFM Mode Transition •100% Duty Cycle Operation •Internally Compensated•Undervoltage Lockout (UVLO)•Overtemperature Protection •Space Saving Packages:-5-Lead TSOT -8-Lead 2X3 DFNApplications•Cellular Telephones •Portable Computers •Organizers / PDAs •USB Powered Devices •Digital Cameras •Portable Equipment•+5V or +3.3V Distributed SystemsGeneral DescriptionThe MCP1603 is a high efficient, fully integrated 500mA synchronous buck regulator whose 2.7V to 5.5V input voltage range makes it ideally suited for applications powered from 1-cell Li-Ion or 2-cell/3-cell NiMH/NiCd batteries.At heavy loads, the MCP1603 operates in the 2.0MHz fixed frequency PWM mode which provides a low noise, low output ripple, small-size solution. When the load is reduced to light levels, the MCP1603automatically changes operation to a PFM mode to minimize quiescent current draw from the battery. No intervention is necessary for a smooth transition from one mode to another. These two modes of operation allow the MCP1603 to achieve the highest efficiency over the entire operating current range.The MCP1603 is available with either an adjustable or fixed output voltage. The available fixed output voltage options are 1.2V, 1.5V, 1.8V, 2.5V, and 3.3V. When a fixed option is used, only three additional small external components are needed to form a complete solution.Couple this with the low profile, small-foot print packages and the entire system solution is achieved with minimal size.Additional protection features include: UVLO,overtemperature, and overcurrent protection.Package Types12345L XV FB /V OUT SHDNGND V IN 5-Lead TSOTMCP160312345L XV FB /V OUTSHDN GND V IN MCP1603L12348765L X V FB /V OUT SHDN GND V IN NC NC NC8-Lead 2x3 DFN 2.0MHz, 500mA Synchronous Buck RegulatorMCP1603DS22042A-page 2© 2007 Microchip Technology Inc.© 2007 Microchip Technology Inc.DS22042A-page 3MCP1603Functional Block DiagramILIM PWMILIM PFMIPEAK PWM IPEAK PFMV INSHDNV FB /V OUTGNDL XBand GapUVLOSwitch Drive UVLOV REFLogic and timing S RQQ Soft StartV REFPWM/PFM LogicV REFSlope CompOSC-I PK LimitUVLO Thermal ShutdownTSDEAPOFF NOFFPWM/PFMTSDPFM Error AmpPWM Error AmpOV ThresholdUV ThresholdI PK Limit-ILPKIPEAK PWMIPEAK PFMDisable Switcher-ILPKMCP1603DS22042A-page 4© 2007 Microchip Technology Inc.1.0ELECTRICALCHARACTERISTICSAbsolute Maximum Ratings †V IN - GND.......................................................................+6.0V All Other I/O ...............................(GND - 0.3V) to (V IN + 0.3V)L X to GND..............................................-0.3V to (V IN + 0.3V)Output Short Circuit Current..................................Continuous Power Dissipation (Note 5)..........................Internally Limited Storage Temperature.....................................-65°C to +150°C Ambient Temp. with Power Applied.................-40°C to +85°C Operating Junction Temperature...................-40°C to +125°C ESD Protection On All Pins:HBM..............................................................................4kV MM. (300V)† Notice: Stresses above those listed under "Maximum Ratings" may cause permanent damage to the device. This is a stress rating only and functional operation of the device at those or any other conditions above those indicated in the operational sections of this specification is not intended.Exposure to maximum rating conditions for extended periods may affect device reliability.DC CHARACTERISTICSElectrical Characteristics: Unless otherwise indicated, V IN = SHDN = 3.6V, C OUT = C IN = 4.7µF, L = 4.7µH, V OUT (ADJ)=1.8V, I OUT =100mA, T A = +25°C. Boldface specifications apply over the T A range of -40°C to +85°C.ParametersSym Min Typ Max Units ConditionsInput Characteristics Input VoltageV IN 2.7— 5.5V Note 1Maximum Output Current I OUT 500——mA Note 1Shutdown Current I IN_SHDN—0.11µA SHDN = GNDQuiescent CurrentI Q —4560µASHDN = V IN , I OUT = 0mAShutdown/UVLO/Thermal Shutdown CharacteristicsSHDN, Logic Input Voltage Low V IL ——15%V IN V IN = 2.7V to 5.5V SHDN, Logic Input Voltage High V IH 45——%V IN V IN = 2.7V to 5.5V SHDN, Input Leakage Current I L_SHDN -1.0±0.1 1.0µA V IN = 2.7V to 5.5V Undervoltage LockoutUVLO2.12 2.28 2.43V V IN FallingUndervoltage Lockout Hysteresis UVLO HYS —140—mV Thermal Shutdown T SHD —150—°C Note 4, Note 5Thermal Shutdown Hysteresis T SHD-HYS—10—°CNote 4, Note 5Note 1:The minimum V IN has to meet two conditions: V IN ≥ 2.7V and V IN ≥ V OUT + 0.5V.2:Reference Feedback Voltage Tolerance applies to adjustable output voltage setting.3:V R is the output voltage setting.4:The maximum allowable power dissipation is a function of ambient temperature, the maximum allowable temperature and the thermal resistance from junction to air (i.e. T A , T J , θJA ). Exceeding the maximum allowable power dissipation causes the device to initiate thermal shutdown.5:The internal MOSFET switches have an integral diode from the L X pin to the V IN pin, and from the L X pin to the GND pin. In cases where these diodes are forward-biased, the package power dissipation limits must be adhered to. Thermal protection is not able to limit the junction temperature for these cases.6:The current limit threshold is a cycle-by-cycle peak current limit.© 2007 Microchip Technology Inc.DS22042A-page 5MCP1603Output Characteristics Adjustable Output Voltage Range V OUT 0.8— 4.5V Note 2Reference Feedback Voltage V FB—0.8—V Reference Feedback Voltage Tolerance-3.0—+3.0%T A = -40°C to +25°C -2.5—+2.5%T A = +25°C to +85°C Feedback Input Bias Current I VFB —0.1—nA Output Voltage Tolerance Fixed V OUT -3.0%V R +3.0%%T A = -40°C to +25°C, Note 3V OUT -2.5V R +2.5%T A = +25°C to +85°C, Note 3Line Regulation V LINE-REG—0.3—%/V V IN = V R + 1V to 5.5V, I OUT =100mALoad RegulationV LOAD-REG—0.35—%V IN =V R +1.5V,I LOAD =100mA to 500mA Internal Oscillator Frequency F OSC 1.5 2.0 2.8MHz Start Up Time T SS —0.6—ms T R =10%to 90%R DSon P-Channel R DSon-P —500—m ΩI P =100mA R DSon N-Channel R DSon-N —500—m ΩI N =100mAL X Pin Leakage Current I LX -1.0±0.1 1.0µA SHDN =0V, V IN =5.5V, L X =0V, L X =5.5V Positive Current Limit Threshold +I LX(MAX)—860—mANote 6DC CHARACTERISTICS (CONTINUED)Electrical Characteristics: Unless otherwise indicated, V IN = SHDN = 3.6V, C OUT = C IN = 4.7µF, L = 4.7µH, V OUT (ADJ)=1.8V, I OUT =100mA, T A = +25°C. Boldface specifications apply over the T A range of -40°C to +85°C.ParametersSym Min Typ Max Units ConditionsNote 1:The minimum V IN has to meet two conditions: V IN ≥ 2.7V and V IN ≥ V OUT + 0.5V.2:Reference Feedback Voltage Tolerance applies to adjustable output voltage setting.3:V R is the output voltage setting.4:The maximum allowable power dissipation is a function of ambient temperature, the maximum allowable temperature and the thermal resistance from junction to air (i.e. T A , T J , θJA ). Exceeding the maximum allowable power dissipation causes the device to initiate thermal shutdown.5:The internal MOSFET switches have an integral diode from the L X pin to the V IN pin, and from the L X pin to the GND pin. In cases where these diodes are forward-biased, the package power dissipation limits must be adhered to. Thermal protection is not able to limit the junction temperature for these cases.6:The current limit threshold is a cycle-by-cycle peak current limit.MCP1603DS22042A-page 6© 2007 Microchip Technology Inc.TEMPERATURE SPECIFICATIONSElectrical Specifications: Unless otherwise indicated, all limits are specified for: V IN +2.7V to 5.5VParametersSymMinTypMaxUnitsConditionsTemperature RangesOperating Junction Temperature RangeT J -40—+125°C Steady StateStorage Temperature Range T A -65—+150°C Maximum Junction Temperature T J——+150°CTransient Package Thermal Resistances Thermal Resistance, 5L-TSOT θJA —256—°C/W Typical 4-layer Board with Internal Ground Plane Thermal Resistance, 8L-2x3 DFNθJA—84.5—°C/WTypical 4-layer Board with Internal Ground Plane and 2-Vias in Thermal PadMCP1603 2.0TYPICAL PERFORMANCE CURVESNote: Unless otherwise indicated, V IN=SHDN=3.6V, C OUT=C IN= 4.7µF, L = 4.7µH, V OUT(ADJ)= 1.8V, I LOAD=100mA, T A=+25°C. Adjustable or fixed output voltage options can be used to generate the Typical Performance Characteristics.FIGURE 2-1:I Q vs. Ambient Temperature. FIGURE 2-2:Efficiency vs. Input Voltage (V OUT = 1.2V).FIGURE 2-3:Efficiency vs. Input Voltage (V OUT = 1.8V).FIGURE 2-4:I Q vs. Input Voltage. FIGURE 2-5:Efficiency vs. Output Load (V OUT = 1.2V).FIGURE 2-6:Efficiency vs. Output Load (V OUT = 1.8V).Note:The graphs and tables provided following this note are a statistical summary based on a limited number of samples and are provided for informational purposes only. The performance characteristics listed herein are not tested or guaranteed. In some graphs or tables, the data presented may be outside the specifiedoperating range (e.g., outside specified power supply range) and therefore outside the warranted range.© 2007 Microchip Technology Inc.DS22042A-page 7MCP1603DS22042A-page 8© 2007 Microchip Technology Inc.Typical Performance Curves (Continued)Note: Unless otherwise indicated, V IN =SHDN =3.6V, C OUT =C IN = 4.7µF, L = 4.7µH, V OUT (ADJ)= 1.8V, I LOAD =100mA,T A =+25°C. Adjustable or fixed output voltage options can be used to generate the Typical Performance Characteristics.FIGURE 2-7:Efficiency vs. Input Voltage(V OUT = 2.4V).FIGURE 2-8:Efficiency vs. Input Voltage(V OUT = 3.3V).FIGURE 2-9:Line Regulation vs. Ambient Temperature (V OUT = 1.8V).FIGURE 2-10:Efficiency vs. Output Load(V OUT = 2.4V).FIGURE 2-11:Efficiency vs. Output Load(V OUT = 3.3V).FIGURE 2-12:Output Voltage vs. Load Current (V OUT = 1.8V).MCP1603Typical Performance Curves (Continued)Note: Unless otherwise indicated, V IN=SHDN=3.6V, C OUT=C IN= 4.7µF, L = 4.7µH, V OUT(ADJ)= 1.8V, I LOAD=100mA, T A=+25°C. Adjustable or fixed output voltage options can be used to generate the Typical Performance Characteristics.FIGURE 2-13:Switching Frequency vs. Ambient Temperature.FIGURE 2-14:Switch Resistance vs. Input Voltage.FIGURE 2-15:Output Voltage Startup Waveform.FIGURE 2-16:Switching Frequency vs. Input Voltage.FIGURE 2-17:Switch Resistance vs. Ambient Temperature.FIGURE 2-18:Heavy Load Switching Waveform.© 2007 Microchip Technology Inc.DS22042A-page 9MCP1603DS22042A-page 10© 2007 Microchip Technology Inc.Typical Performance Curves (Continued)Note: Unless otherwise indicated, V IN =SHDN =3.6V, C OUT =C IN = 4.7µF, L = 4.7µH, V OUT (ADJ)= 1.8V, I LOAD =100mA,T A =+25°C. Adjustable or fixed output voltage options can be used to generate the Typical Performance Characteristics.FIGURE 2-19:Light Load SwitchingWaveform.FIGURE 2-20:Output Voltage Load Step Response vs. Time.FIGURE 2-21:Output Voltage Line StepResponse vs. Time.3.0PIN DESCRIPTIONSThe descriptions of the pins are listed in Table3-1. TABLE 3-1:PIN FUNCTION TABLE3.1Power Supply Input Voltage Pin(V IN)Connect the input voltage source to V IN. The input source must be decoupled to GND with a 4.7µF capacitor.3.2Ground Pin (GND)Ground pin for the device. The loop area of the ground traces should be kept as minimal as possible.3.3Shutdown Control Input Pin(SHDN)The SHDN pin is a logic-level input used to enable or disable the device. A logic high (> 45% of V IN) will enable the regulator output. A logic-low (< 15% of V IN) will ensure that the regulator is disabled.3.4Feedback / Output Voltage Pin(V FB/V OUT)For adjustable output options, connect the center of the output voltage divider to the V FB/V OUT pin. For fixed-output voltage options, connect the output directly to the V FB/V OUT pin.3.5Switch Node, Buck InductorConnection Pin (L X)Connect the L X pin directly to the buck inductor. This pin carries large signal-level current; all connections should be made as short as possible.3.6Exposed Metal Pad (EP)For the DFN package, connect the Exposed Pad to GND, with vias into the GND plane. This connection to the GND plane will aid in heat removal from the package.Pin No.Symbol DescriptionMCP1603 TSOT23MCP1603LTSOT232x3 DFN147V IN Power Supply Input Voltage Pin228GND Ground Pin313SHDN Shutdown Control Input Pin454V FB/V OUT Feedback / Output Voltage Pin531L X Switch Node, Buck Inductor Connection Pin ——2, 5, 6NC No Connect——ExposedPad EP For the DFN package, the center exposed pad is a thermal path to remove heat from the device. Electrically this pad is atground potential and should be connected to GND4.0DETAILED DESCRIPTION4.1Device OverviewThe MCP1603 is a synchronous buck regulator that operates in a Pulse Frequency Modulation (PFM) mode or a Pulse Width Modulation (PWM) mode to maximize system efficiency over the entire operating current range. Capable of operating from a 2.7V to 5.5V input voltage source, the MCP1603 can deliver 500mA of continuous output current.When using the MCP1603, the PCB area required for a complete step-down converter is minimized since both the main P-Channel MOSFET and the synchro-nous N-Channel MOSFET are integrated. Also while in PWM mode, the device switches at a constant frequency of 2.0MHz (typ) which allow for small filter-ing components. Both fixed and adjustable output voltage options are available. The fixed voltage options (1.2V, 1.5V 1.8V, 2.5V, 3.3V) do not require an external voltage divider which further reduces the required circuit board footprint. The adjustable output voltage options allow for more flexibility in the design, but require an external voltage divider.Additionally the device features undervoltage lockout (UVLO), overtemperature shutdown, overcurrent protection, and enable/disable control.4.2Synchronous Buck RegulatorThe MCP1603 has two distinct modes of operation that allow the device to maintain a high level of efficiency throughout the entire operating current and voltage range. The device automatically switched between PWM mode and PFM mode depending upon the output load requirements.4.2.1FIXED FREQUENCY, PWM MODE During heavy load conditions, the MCP1603 operates at a high, fixed switching frequency of 2.0MHz (typical) using current mode control. This minimizes output rip-ple (10 - 15mV typically) and noise while maintaining high efficiency (88% typical with V IN=3.6V, V OUT=1.8V, I OUT = 300mA).During normal PWM operation, the beginning of a switching cycle occurs when the internal P-Channel MOSFET is turned on. The ramping inductor current is sensed and tied to one input of the internal high-speed comparator. The other input to the high-speed compar-ator is the error amplifier output. This is the difference between the internal 0.8V reference and the divided-down output voltage. When the sensed current becomes equal to the amplified error signal, the high-speed comparator switches states and the P-Channel MOSFET is turned off. The N-Channel MOSFET is turned on until the internal oscillator sets an internal RS latch initiating the beginning of another switching cycle. PFM-to-PWM mode transition is initiated for any of the following conditions:•Continuous device switching•Output voltage has dropped out of regulation4.2.2LIGHT LOAD, PFM MODEDuring light load conditions, the MCP1603 operates in a PFM mode. When the MCP1603 enters this mode, it begins to skip pulses to minimize unnecessary quies-cent current draw by reducing the number of switching cycles per second. The typical quiescent current draw for this device is 45µA.PWM-to-PFM mode transition is initiated for any of the following conditions:•Discontinuous inductor current is sensed for a set duration•Inductor peak current falls below the transition threshold limit4.3Soft StartThe output of the MCP1603 is controlled during start-up. This control allows for a very minimal amount of V OUT overshoot during start-up from V IN rising above the UVLO voltage or SHDN being enabled.4.4Overtemperature Protection Overtemperature protection circuitry is integrated in the MCP1603. This circuitry monitors the device junction temperature and shuts the device off, if the junction temperature exceeds the typical 150°C threshold. If this threshold is exceeded, the device will automatically restart once the junction temperature drops by approximately 10°C. The soft start is reset during an overtemperture condition.4.5Overcurrent ProtectionCycle-by-cycle current limiting is used to protect the MCP1603 from being damaged when an external short circuit is applied. The typical peak current limit is 860mA. If the sensed current reaches the 860mA limit, the P-Channel MOSFET is turned off, even if the output voltage is not in regulation. The device will attempt to start a new switching cycle when the internal oscillator sets the internal RS latch.4.6Enable/Disable ControlThe SHDN pin is used to enable or disable the MCP1603. When the SHDN pin is pulled low, the device is disabled. When pulled high the device is enabled and begins operation provided the input voltage is not below the UVLO threshold or a fault condition exists.4.7Undervoltage Lockout (UVLO)The UVLO feature uses a comparator to sense the input voltage (V IN) level. If the input voltage is lower than the voltage necessary to properly operate the MCP1603, the UVLO feature will hold the converter off. When V IN rises above the necessary input voltage, the UVLO is released and soft start begins. Hysteresis is built into the UVLO circuit to compensate for input impedance. For example, if there is any resistance between the input voltage source and the device when it is operating, there will be a voltage drop at the input to the device equal to I IN x R IN. The typical hysteresis is 140mV.5.0APPLICATION INFORMATION 5.1Typical ApplicationsThe MCP1603 500mA synchronous buck regulator operates over a wide input voltage range (2.7V to5.5V) and is ideal for single-cell Li-Ion battery powered applications, USB powered applications, three cell NiMH or NiCd applications and 3V or 5V regulated input applications. The 5-lead TSOT and 8-lead 2x3 DFN packages provide a small footprint with minimal external components.5.2Fixed Output Voltage Applications Typical Application Circuit shows a fixed MCP1603 in an application used to convert three NiMH batteries into a well regulated 1.8V@500mA output. A 4.7µF input capacitor, 4.7µF output capacitor, and a 4.7µH inductor make up the entire external component solu-tion for this application. No external voltage divider or compensation is necessary. In addition to the fixed 1.8V option, the MCP1603 is also available in 1.2V, 1.5V, 2.5V, or 3.3V fixed voltage options.5.3Adjustable Output VoltageApplicationsWhen the desired output for a particular application is not covered by the fixed voltage options, an adjustable MCP1603 can be used. The circuit listed in Figure6-2 shows an adjustable MCP1603 being used to convert a 5V rail to 1.0V@500mA. The output voltage is adjust-able by using two external resistors as a voltage divider. For adjustable-output voltages, it is recommended that the top resistor divider value be 200kΩ. The bottom resistor value can be calculated using the following equation:EQUATION 5-1:For adjustable output applications, an additional R-C compensation network is necessary for control loop stability. Recommended values for any output voltage are:Refer to Figure6-2 for proper placement of R COMP andC COMP.5.4Input Capacitor SelectionThe input current to a buck converter, when operating in continuous conduction mode, is a squarewave with a duty cycle defined by the output voltage (V OUT) to input voltage (V IN) relationship of V OUT/V IN. To prevent undesirable input voltage transients, the input capacitor should be a low ESR type with an RMS current rating given by Equation5.5. Because of their small size and low ESR, ceramic capacitors are often used. Ceramic material X5R or X7R are well suited since they have a low temperature coefficient and acceptable ESR. EQUATION 5-2:Table5-1 contains the recommend range for the input capacitor value.5.5Output Capacitor SelectionThe output capacitor helps provide a stable output voltage during sudden load transients, smooths the current that flows from the inductor to the load, and reduces the output voltage ripple. Therefore, low ESR capacitors are a desirable choice for the output capac-itor. As with the input capacitor, X5R and X7R ceramic capacitors are well suited for this application.The output ripple voltage is often a design specifica-tion. A buck converters’ output ripple voltage is a function of the charging and discharging of the output capacitor and the ESR of the capacitor. This ripple voltage can be calculated by Equation5-3. EQUATION 5-3:R BOT R TOPV FBV OUT V FB–----------------------------⎝⎠⎛⎞×=Example:R TOP=200kΩV OUT= 1.0VV FB=0.8VR BOT=200kΩ x (0.8V/(1.0V-0.8V)) R BOT=800kΩ(Standard Value = 787kΩ)R COMP= 4.99kΩC COMP=33pFI CIN RMS,I OUT MAX,V OUT V IN V OUT–()×V IN-----------------------------------------------------⎝⎠⎜⎟⎛⎞×=ΔV OUTΔI L ESR×ΔI L8f C××--------------------+=Table5-1 contains the recommend range for the output capacitor value.5.6Inductor SelectionWhen using the MCP1603, the inductance value can range from 3.3µH to 10µH. An inductance value of 4.7µH is recommended to achieve a good balance between converter load transient response and mini-mized noise.The value of inductance is selected to achieve a desired amount of ripple current. It is reasonable to assume a ripple current that is 20% of the maximum load current. The larger the amount of ripple current allowed, the larger the output capacitor value becomes to meet ripple voltage specifications. The inductor ripple current can be calculated according to the follow-ing equation.EQUATION 5-4:When considering inductor ratings, the maximum DC current rating of the inductor should be at least equal to the maximum load current, plus one half the peak-to-peak inductor ripple current (1/2 * ΔI L). The inductor DC resistance adds to the total converter power loss. An inductor with a low DC resistance allows for higher converter efficiency.5.7Thermal CalculationsThe MCP1603 is available in two different packages (TSOT-23 and 2x3 DFN). By calculating the power dissipation and applying the package thermal resistance,(θJA), the junction temperature is estimated. The maximum continuous junction temperature rating for the MCP1603 is +125°C.To quickly estimate the internal power dissipation for the switching buck regulator, an empirical calculation using measured efficiency can be used. Given the measured efficiency, the internal power dissipation is estimated by:EQUATION 5-5:The difference between the first term, input power dissipation, and the second term, power delivered, is the internal power dissipation. This is an estimate assuming that most of the power lost is internal to the MCP1603. There is some percentage of power lost in the buck inductor, with very little loss in the input and output capacitors.TABLE 5-1:CAPACITOR VALUE RANGEC IN C OUTMinimum 4.7µF 4.7µFMaximum—22µFΔI LV OUTF SW L×-------------------1V OUTV IN------------–⎝⎠⎛⎞×=Where:F SW = Switching Frequency TABLE 5-2:MCP1603 RECOMMENDEDINDUCTORSPartNumberValue(µH)DCRΩ(max)I SAT(A)SizeWxLxH (mm) Coiltronics®SD3110 3.30.1950.81 3.1x3.1x1.0 SD3110 4.70.2850.68 3.1x3.1x1.0 SD3110 6.80.3460.58 3.1x3.1x1.0 SD3812 3.30.159 1.40 3.8x3.8x1.2 SD3812 4.70.256 1.13 3.8x3.8x1.2 SD3812 6.80.2990.95 3.8x3.8x1.2 Würth Elektronik®WE-TPCType XS3.30.2250.72 3.3x3.5x0.95WE-TPCType XS4.70.2900.50 3.3x3.5x0.95WE-TPCType S4.70.1050.90 3.8x3.8x1.65WE-TPCType S6.80.1560.75 3.8x3.8x1.65 Sumida®CMD4D06 3.30.1740.77 3.5x4.3x0.8 CMD4D06 4.70.2160.75 3.5x4.3x0.8 CMD4D06 6.80.2960.62 3.5x4.3x0.8V OUT I OUT×Efficiency------------------------------⎝⎠⎛⎞VOUTI OUT×()–P Diss=5.8PCB Layout InformationGood printed circuit board layout techniques are important to any switching circuitry and switching power supplies are no different. When wiring the high current paths, short and wide traces should be used. This high current path is shown with red connections in Figure5-1. The current in this path is switching.Therefore, it is important that the components along the high current path should be placed as close as possible to the MCP1603 to minimize the loop area.The feedback resistors and feedback signal should be routed away from the switching node and this switching current loop. When possible ground planes and traces should be used to help shield the feedback signal and minimize noise and magnetic interference.FIGURE 5-1:PCB High Current Path.V INSHDNGNDV FBL XV IN2.7V To4.5VV OUT1.8V@500mAC OUT4.7µFC IN4.7µFL1 4.7µH6.0TYPICAL APPLICATION CIRCUITSFIGURE 6-1:Single Li-Ion to 1.5V @ 500mA Application.FIGURE 6-2:5V to 1.0V @ 500mA Application.FIGURE 6-3: 3 NiMH Batteries to 1.2V @ 500mA Application.9V INSHDN GNDV FBL XV IN3.0V To4.2VV OUT1.5V @500mA C OUT 4.7µFC IN 4.7µFL 14.7µHR TOP 200k ΩR BOT 787k ΩV INSHDNGNDV FBL XV IN 5.0VV OUT1.0V @500mAC OUT 4.7µFC IN 4.7µFL 14.7µHR COMP 4.99k ΩC COMP 33pFV INSHDN GNDV FBL XV IN2.7V To 4.5VV OUT1.2V @500mAC OUT 4.7µFC IN 4.7µFL 14.7µH7.0PACKAGING INFORMATION7.1Package Marking Information (Not to Scale)8-Lead 2x3 DFNExample :5-Lead TSOTXXNN ExampleET25Part NumberMarking Code MCP1603-120I/MC AFM MCP1603-150I/MC AFK MCP1603-180I/MC AFJ MCP1603-250I/MC AFG MCP1603-330I/MC AFA MCP1603-ADJI/MCAFQPart Number Marking Code MCP1603T-120I/OS ETNN MCP1603T-150I/OS EUNN MCP1603T-180I/OS EVNN MCP1603T-250I/OS EWNN MCP1603T-330I/OS EXNN MCP1603T-ADJI/OSEYNN Part Number Marking Code MCP1603LT-120I/OS FMNN MCP1603LT-150I/OS FKNN MCP1603LT-180I/OS EJNN MCP1603LT-250I/OS FGNN MCP1603LT-330I/OS FANN MCP1603LT-ADJI/OSFQNN。
SF1530规格书
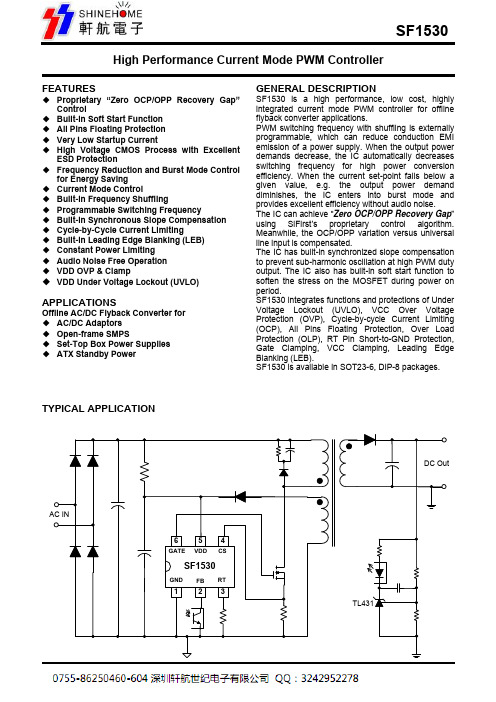
Value
35 10 20 -0.3 to 7 250 90 150 150 -40 to 85
Unit
V mA V V o C/W o C/W o C/W o C o C
SF1530
Storage Temperature Range Lead Temperature (Soldering, 10sec.) ESD Capability, HBM (Human Body Model) ESD Capability, MM (Machine Model) -65 to 150 260 3 250 C C kV V
Absolute Maximum Ratings (Note 1)
Parameter
VDD DC Supply Voltage VCC DC Clamp Current GATE pin FB, RT, CS voltage range Package Thermal Resistance (SOT-26) Package Thermal Resistance (DIP-8) Package Thermal Resistance (SOP-8) Maximum Junction Temperature Operating Temperature Range
Test Conditions
Min
13.5 8
Typ
14.5 9 5 2.5 28.5 35 3 5.5
Ordering Information
P30DP
Top Mark
.30YWW SF1530DP SOT26 DIP8
Package
Green RoHS
Tape & Reel
Yes
Marking Information
ELX1046 PTS0603 SMD PTC 重置电流保护器说明说明书

Product features• Positive temperature coefficient (PTC)• Surface mount resettable fuse • Low resistance• Compact 0603 (1608 metric) footprint • Voltage rating 6 V to 15 V• Current rating from 0.04 A to 0.35 A • Fast time-to-tripApplications• Data ports• Micromotors and fans• Low voltage test and measurement • Low voltage hand held equipment • PC-based medical equipment • USB protection• Secondary Li-ion battery protection • Game consoles, set top boxes• Battery charging & charging connectionsPTS0603SMD PTC fusesAgency information• cURus Recognized file no. E343021• TUV: File R 50506608Part number system/ordering: PTS060315V004• PT= PTC resettable fuse • S= Surface mount • 0603= Dimension code • 15V= Maximum voltage• 004= Ihold current rating (004= 0.04 A)Environmental compliancePb HALOGENHFFREE2Technical Data ELX1046Effective June 2021PTS0603SMD PTC fuses/electronicsProduct specificationsVmax 1lmax 2lhold 3ltrip 4Pd 5Time-to-trip (maximum)Resistance 6Safety approvalsPart number(V dc )(A)(A)(A)typical (W)(A)(seconds)Initial (R i )minimum (Ω)Post trip (R 1)maximum (Ω)cU us TUVPTS060315V0041510.040.120.50.2 1.0 1.540√√PTS060315V0051510.050.150.50.25 1.0 1.040√√PTS060315V0101530.100.250.50.5 1.00.56√√PTS06039V016940.160.400.5 1.0 1.00.45√√PTS06039V020940.200.500.5 1.00.60.34√√PTS06036V035680.350.750.58.00.10.091.5√√Dimensions–mm 1.Vmax: Maximum continuous voltage the device can withstand without damage at rated current 2. Imax: Maximum fault current the device can withstand without damage at rated voltage 3. Ihold: Maximum current the device will pass without interruption at +23 °C still air4.Itrip: Minimum current that will transition the device from low resistance to high resistance at +23 °C still air5. Pd: Power dissipated from the device when in tripped state at +23 °C still air6. R i : Minimum resistance of the device at +23 °CR 1: Maximum resistance of the device one hour after tripping at +23 °CPart number A typ A max B typ B max C typ C max D min F G HPTS060315V004 1.65 1.800.80 1.000.560.800.150.80.60.8PTS060315V005 1.65 1.800.80 1.000.560.800.150.80.60.8PTS060315V010 1.65 1.800.80 1.000.530.800.150.80.60.8PTS06039V016 1.65 1.800.80 1.000.500.800.150.80.60.8PTS06039V020 1.65 1.800.90 1.000.450.800.150.80.60.8PTS06036V035 1.65 1.800.90 1.000.700.800.150.80.60.8RRecommended pad layoutNo marking3Technical Data ELX1046Effective June 2021PTS0603SMD PTC fuses /electronics General specificationsOperating temperature: -40 °C to + 85 °C (with derating)Storage temperature: -10 °C to + 40 °C Storage relative humidity: ≤70%Storage conditon: Keep away form corrosive atmosphere and sunlight Passive aging: IEC60738-1, +85 °C, 1000 hours, ≤20% Humidity aging: +85 °C, 85% RH, 100 hours, ≤20%Thermal shock: IEC60738-1, +85 °C/ -40 °C, 20 cycles, ≤50%Trip cycle life: UL1434, Vmax, Imax, 100 cycles, no arcing or burning Trip endurance: UL1434, Vmax, Itrip ≤ I ≤ Imax, 2 hours, no arcing or burning MSL test: J-STD-020, MSL=1, pass and no visible damageThermal derating curvePTS0603T emperature (°C)P e r c e n t a g e o f r a t e d c u r r e n t4Technical Data ELX1046Effective June 2021PTS0603SMD PTC fuses/electronicsWFE1E2P0P1P2D0D1A0B0K0T8.00 ± 0.30 3.50 ± 0.10 1.75 ± 0.10- 4.00 ± 0.10 4.00 ± 0.10 2.00 ± 0.05 1.50 + 0.10/-0- 1.10 ± 0.10 1.85 ± 0.100.60 ± 0.10 0.20 ± 0.05Packaging informationPTS0603xxV004-xxV020Supplied in tape and reel packaging, 5000 parts per 7.0” (178 mm) diameter reel (EIA-481 compliant)PTS06036V035Supplied in tape and reel packaging, 5000 parts per 7.0” (178 mm) diameter reel (EIA-481 compliant)PTS0603xxV004-xxV020WFE1E2P0P1P2D0D1A0B0K0T8.00 ± 0.30 3.50 ± 0.10 1.75 ± 0.10- 4.00 ± 0.10 4.00 ± 0.10 2.00 ± 0.05 1.50 + 0.10/-0- 1.10 ± 0.10 1.85 ± 0.100.85 ± 0.10 0.20 ± 0.05PTS06036V0355Technical Data ELX1046Effective June 2021PTS0603SMD PTC fuses /electronics Wave solder profileReference EN 61760-1:2006Profile featureStandard SnPb solderLead (Pb) free solderPreheat • Temperature min. (T smin )100 °C 100 °C • Temperature typ. (T styp )120 °C 120 °C • Temperature max. (T smax )130 °C 130 °C • Time (T smin to T smax ) (t s )70 seconds 70 seconds ∆ preheat to max Temperature 150 °C max.150 °C max.Peak temperature (T P )*235 °C – 260 °C 250 °C – 260 °C Time at peak temperature (t p )10 seconds max5 seconds max each wave 10 seconds max5 seconds max each wave Ramp-down rate~ 2 K/s min ~3.5 K/s typ ~5 K/s max ~ 2 K/s min ~3.5 K/s typ ~5 K/s max Time 25°C to 25°C4 minutes4 minutesManual solder+350 °C (4-5 seconds by soldering iron), generally manual/hand soldering is not recommendedT e m p e r a t u r eTimeT T T TEatonElectronics Division 1000 Eaton Boulevard Cleveland, OH 44122United States/electronics© 2021 EatonAll Rights Reserved Printed in USAPublication No. ELX1046 BU-ELX21046June 2021PTS0603SMD PTC fusesTechnical Data ELX1046Effective June 2021Life Support Policy: Eaton does not authorize the use of any of its products for use in life support devices or systems without the express writtenapproval of an officer of the Company. Life support systems are devices which support or sustain life, and whose failure to perform, when properly used in accordance with instructions for use provided in the labeling, can be reasonably expected to result in significant injury to the user.Eaton reserves the right, without notice, to change design or construction of any products and to discontinue or limit distribution of any products. Eaton also reserves the right to change or update, without notice, any technical information contained in this bulletin.Solder reflow profileTable 1 - Standard SnPb solder (T c )Package thicknessVolume mm3 <350Volume mm3 ≥350<2.5 mm)235 °C 220 °C ≥2.5 mm220 °C220 °CTable 2 - Lead (Pb) Free Solder (T c )Package thicknessVolume mm 3 <350Volume mm 3350 - 2000Volume mm 3 >2000<1.6 mm 260 °C 260 °C 260 °C 1.6 – 2.5 mm 260 °C 250 °C 245 °C >2.5 mm250 °C245 °C245 °CEaton is a registered trademark.All other trademarks are property of their respective owners.Follow us on social media to get thelatest product and support information.Reference J-STD-020Profile featureStandard SnPb solderLead (Pb) free solderPreheat and soak • Temperature min. (T smin )100 °C 150 °C • Temperature max. (T smax )150 °C 200 °C • Time (T smin to T smax ) (t s )60-120 seconds 60-120 seconds Ramp up rate T L to T p 3 °C/ second max. 3 °C/ second max.Liquidous temperature (T l ) Time (t L ) maintained above T L183 °C60-150 seconds 217 °C60-150 seconds Peak package body temperature (T P )*Table 1Table 2Time (t p )* within 5 °C of the specified classification temperature (T c )20 seconds*30 seconds*Ramp-down rate (T p to T L ) 6 °C/ second max. 6 °C/ second max.Time 25 °C to peak temperature6 minutes max.8 minutes max.* Tolerance for peak profile temperature (T p ) is defined as a supplier minimum and a user maximum.。
常用钢号对照表
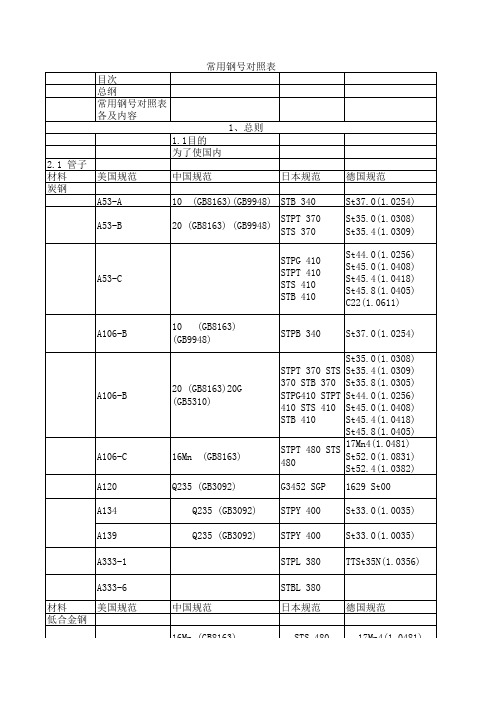
SUS304TP
X5CrNi189(1.4301)
A312_TP304H
1Cr18Ni9 (GB13296)1Cr19Ni9 (GB5310) (GB9948)
SUS304HTP
X5CrNi189(1.4301) X12CrNi188(1.4300 )
A312-TP304L
00Cr19Ni10 (GB13296)(GB/T14976)0 0Cr19Ni11(GB12771)
ASt45 ASt52
A662-C
16Mng 16MnR
(GB713) (GB 6654)
SPV355
19Mn6(1.0473)
A662-C A204-A A205-B A387-2 A387-12 A387-11 A387-22 A387-21 A387-5 不锈钢
16MnDR (GB3531)
SLA325 SLA360 SB 450M SB 480M SCMV1 SCMV2 SCMV3 SCMV4 SCMV5 SCMV6 15Mo3(1.5415) 16Mo5
X10Cr13(1.4006)
A312-TP410 2.2 板材 材料 碳钢
0Cr13 (GB/T14976)
SUS410TP
X10Cr13(1.4006)
美国规范 A283-C A283-D A283-D A515Gr.55
中国规范
日本规范 SS400
德国规范 St37.2(1.0037) St42.2(1.0044)
10 (GB8163)(GB9948) STB 340 20 (GB8163) (GB9948) STPT 370 STS 370
A53-C
STPG 410 STPT 410 STS 410 STB 410
DS1603;中文规格书,Datasheet资料
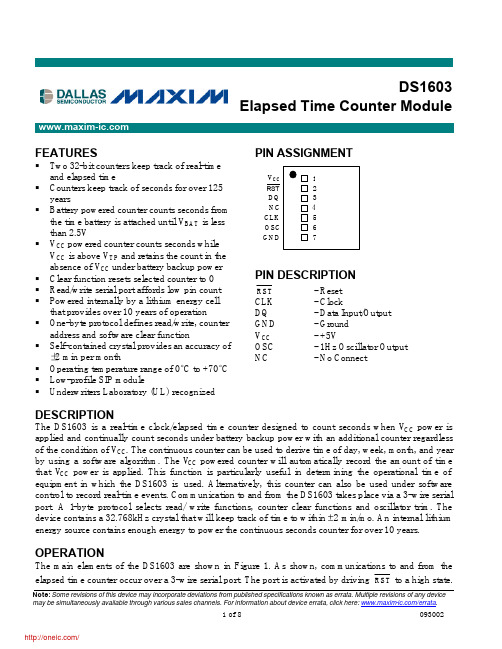
Note: Some revisions of this device may incorporate deviations from published specifications known as errata. Multiple revisions of any device may be simultaneously available through various sales channels. For information about device errata, click here: /errata .FEATURES§ Two 32-bit counters keep track of real -time and elapsed time§ Counters keep track of seconds for over 125 years§ Battery powered counter counts seconds from the time battery is attached until V BAT is less than 2.5V§ V CC powered counter counts seconds while V CC is above V TP and retains the count in the absence of V CC under battery backup power § Clear function resets selected counter to 0 § Read/write serial port affords low pin count § Powered internally by a lithium energy cell that provides over 10 years of operation§ One-byte protocol defines read/write, counter address and software clear function§ Self-contained crystal provides an accuracy of ±2 min per month§ Operating temperature range of 0°C to +70°C § Low-profile SIP module§ Underwriters Laboratory (UL) recognized PIN ASSIGNMENTPIN DESCRIPTIONRST- Reset CLK - ClockDQ - Data Input/Output GND - Ground V CC - +5VOSC - 1Hz Oscillator Output NC- No ConnectDESCRIPTIONThe DS1603 is a real -time clock/elapsed time counter designed to count seconds when V CC power is applied and continually count seconds under battery backup power with an additional counter regardless of the condition of V CC . The continuous counter can be used to derive time of day, week, month, and year by using a software algorithm. The V CC powered counter will automatically record the amount of time that V CC power is applied. This function is particularly useful in determining the operational time of equipment in which the DS1603 is used. Alternatively, this counter can also be used under software control to record real -time events. Communication to and from the DS1603 takes place via a 3-wire serial port. A 1-byte protocol selects read/ write functions, counter clear functions and oscillator trim. The device contains a 32.768kHz crystal that will keep track of time to within ±2 min/mo. An internal lithium energy source contains enough energy to power the continuous seconds counter for over 10 years.OPERATIONThe main elements of the DS1603 are shown in Figure 1. As shown, communications to and from the elapsed time counter occur over a 3-wire serial port. The port is activated by driving RST to a high state.V CC RST DQ NC CLK OSC GND DS1603Elapsed Time Counter Moduleselect, register clear, and oscillator trim information. Each bit is serially input on the rising edge of the clock input. After the first eight clock cycles have loaded the protocol register with a valid protocol additional clocks will output data for a read or input data for a w rite. V CC must be present to access the DS1603. If V CC < V TP, the DS1603 will switch to internal power and disable the serial port to conserve energy. When running off of the internal power supply, only the continuous counter will continue to count and the counter powered by V CC will stop, but retain the count, which had accumulated when V CC power was lost. The 32-bit V CC counter is gated by V CC and the internal 1Hz signal.PROTOCOL REGISTERThe protocol bit definition is shown in Figure 2. Valid protocols and the resulting actions are shown in Table 1. Each data transfer to the protocol register designates what action is to occur. As defined, the MSB (bit 7 which is designated ACC) selects the 32-bit continuous counter for access. If ACC is a logical 1 the continuous counter is selected and the 32 clock cycles that follow the protocol will either read or write this counter. If the counter is being read, the contents will be latched into a different register at the end of protocol and the latched contents will be read out on the next 32 clock cycles. This avoids reading garbled data if the counter is clocked by the oscillator during a read. Similarly, if the counter is to be written, the data is buffered in a register and all 32 bits are jammed into the counter simultaneously on the rising edge of the 32nd clock. The next bit (bit 6 which is designated AVC) selects the 32–bit V CC active counter for access. If AVC is a logical 1 this counter is selected and the 32 clock cycles that follow will either read or write this counter. If both bit 7 and bit 6 are written to a logic high, all clock cycles beyond the protocol are ignored and bit 5, 4, and 3 are loaded into the oscillator trim register. A value of binary 3 (011) will give a clock accuracy of ±120 seconds per month at +25°C. Increasing the binary number towards 7 will cause the real-time clock to run faster. Conversely, lowering the binary number towards 0 will cause the clock to run slower. Binary 000 will stop the oscillator completely. This feature can be used to conserve battery life during storage. In this mode the internal power supply current is reduced to 100 nA maximum. In applications where oscillator trimming is not practical or not needed, a default setting of 011 is recommended. Bit 2 of protocol (designated CCC) is used to clear the continuous counter. When set to logic 1, the continuous counter will reset to 0 when RST is taken low. Bit 1 of protocol (designated CVC) is used to clear the V CC active counter. When set to logical 1, the V CC active counter will reset to 0 when RST is taken low. Both counters can be reset simultaneously by setting CCC and CVC both to a logical 1. Bit 0 of the protocol (designated RD) determines whether the 32 clocks to follow w ill write a counter or read a counter. When RD is set to a logical 0 a write action will follow when RD is set to a logical 1 a read action will follow. When sending the protocol, 8 bits should always be sent. Sending less than 8 bits can produce erroneous results. If clearing the counters or trimming the oscillator, the data transfer can be terminated after the 8-bit protocol is sent. However, when reading or writing the counters, 32 clock cycles should always follow the protocol.RESET AND CLOCK CONTROLAll data transfers are initiated by driving the RST input high. The RST input has two functions. First, RST turns on the serial port logic, which allows access to the protocol register for the protocol data entry. Second, the RST signal provides a method of terminating the protocol transfer or the 32-bit counter transfer. A clock cycle is a sequence of a rising edge followed by a falling edge. For write inputs, data must be valid during the rising edge of the clock. Data bits are output on the falling edge of the clock when data is being read. All data transfers terminate if the RST input is transitioned low and the DQ pin goes to a high-impedance state. RST should only be transitioned low while the clock is high to avoid disturbing the last bit of data. All data transfers must consist of 8 bits when transferring protocol only or 8 + 32 bits when reading or writing either counter. Data tran sfer is illustrated in Figure 3.DATA INPUTFollowing the 8-bit protocol that inputs write mode, 32 bits of data are written to the selected counter on the rising edge of the next 32 CLK cycles. After 32 bits have been entered any additional CLK cycles will be ignored until RST is transitioned low to end data transfer and then high again to begin new data transfer.DATA OUTPUTFollowing the eight CLK cycles that input read mode protocol, 32 bits of data will be output from the selected counter on the next 32 CLK cycles. The first data bit to be transmitted from the selected 32-bit counter occurs on the falling edge after the last bit of protocol is written. When transmitting data from the selected 32-bit counter, RST must remain at high level as a transition to low level will terminate data transfer. Data is driven out the DQ pin as long as CLK is low. When CLK is high the DQ pin is tristated. OSCILLATOR OUTPUTPin 6 of the DS1603 module is a 1Hz output signal. This signal is present only when V CC is applied and greater than the internal power supply. However, the output is guaranteed to meet TTL requirement only while V CC is within normal limits. This output can be used as a 1-second interrupt or time tick needed in some applications.INTERNAL POWERThe internal battery of the DS1603 module provides 35mAh and will run the elapsed time counter for over 10 years in the absence of power.PIN DESCRIPTIONSV CC, GND – DC power is provided to the device on these pins. V CC is the +5V input. When 5V is applied within normal limits, the device is fully accessible and data can be written and read. When a 3V battery is connected to the device and V CC is below 1.25 x V BAT, reads and writes are inhibited. As V CC falls below V BAT the continuous counter is switched over to the internal battery.CLK (Serial Clock Input) – CLK is used to synchronize data movement on the serial interface.DQ (Data Input/Output) – The DQ pin is the bi-directional data pin for the 3-wire interface.RST (Reset) – The reset signal must be asserted high during a read or a write.OSC (One Hertz Output Signal) – This signal is only present when Vcc is at a valid level and the oscillator is enabled.Figure 1. ELAPSED TIME COUNTER BLOCK DIAGRAMFigure 2. PROTOCOL BIT MAP7 6 5 4 3 2 1 0ACC AVC OSC2 OSC1 OSC0 CCC CVC RDTable 1. VALID PROTOCOLSPROTOCOLACTIONACC AVC OSC2 OSC1 OSC0 CCC CVC RDFUNCTION ReadContinuous Counter 1 0 X X X X X 1Output continuouscounter on the 32 clocksfollowing protocol.Oscillator trim registeris not updated. Countersare not reset.WriteContinuous Counter 1 0 X X X X X 0Input data to continuouscounter on the 32 clocksfollowing protocol.Oscillator trim registeris not updated. Countersare not reset.Read V CCActive Counter 0 1 X X X X X 1Output V CC activecounter on the 32 clocksfollowing protocol,oscillator trim registeris not updated. Countersare not reset.Write V CCActive Counter 0 1 X X X X X 0Input data to continuouscounter on the 32 clocksfollowing protocol.Oscillator trim registeris not updated. Countersare not reset.ClearContinuous Counter 0 0 X X X 1 X XResets the continuouscounter to all zeros atthe end of protocol.Oscillator trim registeris not updated.Clear V CCActive Counter 0 0 X X X X 1 XResets the V CC activecounter to all zeros atthe end of protocol.Oscillator trim registeris not updated.Set Oscillator Trim Bits 1 1 A B C X X 0Sets the oscillator trimregister to a value ofABC. Counters areunaffected.X = Don’t CareFigure 3. DATA TRANSFERTIMING DIAGRAM: READ/WRITE DATA TRANSFERNote: t CL, t CH, t R, and t F apply to both read and write data transfer.ABSOLUTE MAXIMUM RATINGSVoltage Range on Any Pin Relative to Ground -0.3V to +7.0VOperating Temperature Range 0°C to +70°CStorage Temperature Range -40°C to +70°CSoldering Temperature Range See IPC/JEDEC J-STD-020A (See Note 11)This is a stress rating only and functional operation of the device at these or any other conditions beyond t h ose indicated in the operation sections of this specification is not implied. Exposure to absolute maximum rating conditions for extended periods of time can affect reliability.RECOMMENDED DC OPERATING CONDITIONS (0°C to +70°C) PARAMETER SYMBOL MIN TYP MAX UNITS NOTES Supply Voltage V CC 4.5 5.0 5.5 V 1 Logic 1 Input V IH 2.0 V CC + 0.3 V 1 Logic 0 Input V IL-0.3 0.8 V 1DC ELECTRICAL CHARACTERISTICS (0°C to +70°C; V CC = 5V ±10%) PARAMETER SYMBOL MIN TYP MAX UNITS NOTES Input Leakage I LI-1 +1 µAI/O Leakage I LO-1 +1 µALogic 1 Output V OH 2.4 V 2 Logic 0 Output V OL0.4 V 3 Active Supply Current I CC 1 mA 4 Timekeeping Current I CC150 µA 5 Battery Trip Point V TP 3.0 4.5 V 9 CAPACITANCE (T A = +25°C) PARAMETER SYMBOL MIN TYP MAX UNITS NOTES Input Capacitance C I 5 pFI/O Capacitance C I/O10 pF(T A = +25°C) PARAMETER SYMBOL MIN TYP MAX UNITS NOTES Expected Datat DR10 years 10 Retention TimeNOTES:1) All voltages are referenced to ground.2) Logic 1 voltages are specified at a source current of 1mA.3) Logic 0 voltages are specified at a sink current of 4mA.4) I CC is specified with the DQ pin open.5) I CC1 is specified with V CC at 5.0V and RST = GND.6) Measured at V IH= 2.0V or V IL = 0.8V.7) Measured at V OH = 2.4V or V OL - 0.4V.8) Load capacitance = 50pF.9) Battery trip point is the point at which the V CC powered counter and the serial port stops operation.The battery trip point drops below the minimum once the internal lithium energy cell is exhausted. 10) The expected t D R is defined as accumulative time in the absence of V CC with the clock oscillatorrunning.11) Real-time clock modules can be successfully processed through conventional wave-solderingtechniques as long as temperature exposure to the lithium energy source contained within does not exceed +85°C. Post-solder cleaning with water-washing techniques is acceptable, provided that ultrasonic vibration is not used.DS1603DS1603 7-PIN MODULEPKG7-PIN DIM MIN MAX A IN. MM 0.830 21.08 0.850 21.59 B IN. MM 0.650 16.51 0.670 17.02 C IN. MM 0.310 7.87 0.330 8.38 D IN. MM 0.015 0.38 0.030 0.76 E IN. MM 0.110 2.79 0.140 3.56 F IN. MM 0.015 0.38 0.021 0.53 G IN. MM 0.090 2.29 0.110 2.79 H IN. MM 0.105 2.67 0.135 3.43 J IN. MM 0.360 9.14 0.390 9.91分销商库存信息: MAXIMDS1603。
SF16JZ51中文资料

TOSHIBA THYRISTOR SILICON PLANAR TYPESF16GZ51,SF16JZ51MEDIUM POWER CONTROL APPLICATIONSl Repetitive Peak Off −State Voltage : V DRM = 400,600VRepetitive Peak Reverse Voltage : V RRM = 400,600V l Average On −State Current : I T (AV) = 16A l Isolation Voltage : V Isol = 1500V ACMAXIMUM RATINGSCHARACTERISTIC SYMBOL RATING UNITSF16GZ51 400Repetitive PeakOff −State Voltage and Repetitive Peak Reverse Voltage SF16JZ51V DRMV RRM600 VSF16GZ51 500Non −Repetitive Peak Reverse Voltage(Non −Repetitive <5ms, T j = 0~125°C)SF16JZ51V RSM720 V Average On −State Current(Half Sine Waveform) I T(AV) 16 A R.M.S On −State Current I T(RMS) 25 A 250 (50Hz) Peak One Cycle Surge On −State Current (Non-Repetitive) I TSM275 (60Hz)AI 2t Limit ValueI 2t 312 A 2sCritical Rate of Rise of On −StateCurret (Note) di / dt 100A / µsPeak Gate Power Dissipation P GM 5 W Average Gate Power Dissipation P G (AV) 0.5 W Peak Forward Gate Voltage V FGM 10 V Peak Reverse Gate Voltage V RGM−5 VPeak Forward Gate Current I GM 2 A Junction Temperature T j −40~125 °C Storage Temperature Range T stg−40~125 °CIsolation Voltage (AC, t = 1min.)V Isol 1500 VNote : di / dt Test Condition, i G = 30mA, t gw = 10µs, t gr ≤ 250nsJEDEC ―JEITA ― TOSHIBA 13−16A1BWeight: 5.9gUnit:mmELECTRICAL CHARACTERISTICS (Ta = 25°C)CHARACTERISTIC SYMBOLTESTCONDITIONMINTYP.MAX UNITRepetitive Peak Off−State Current and Repetitive Peak Reverse Current I DRMI RRMV DRM = V RRM = Rated ―― 20µA Peak On−State Voltage V TM I TM = 50A ―― 1.5 V Gate Trigger Voltage V GT―― 1.5 V Gate Trigger Current I GTV D = 6V, R L = 10Ω―― 15 mA Holding Current I H V D = 6V, I TM = 500mA ―― 50 mACritical Rate of Rise of Off−State Voltage dv / dtV DRM = Rated, Tc = 125°CExponential Rise― 50 ― V/µs Thermal Resistance R th (j−c) JunctiontoCase ―― 1.5 °C/W MARKINGNUMBER SYMBOL MARKSF16GZ51 F16GZ51*1 TYPESF16JZ51 F16JZ51*2Example8A: January 19988B: February 19988L: December 1998· TOSHIBA is continually working to improve the quality and reliability of its products. Nevertheless, semiconductor devices in general can malfunction or fail due to their inherent electrical sensitivity and vulnerability to physical stress. It is the responsibility of the buyer, when utilizing TOSHIBA products, to comply with the standards of safety in making a safe design for the entire system, and to avoid situations in which a malfunction or failure of such TOSHIBA products could cause loss of human life, bodily injury or damage to property.In developing your designs, please ensure that TOSHIBA products are used within specified operating ranges as set forth in the most recent TOSHIBA products specifications. Also, please keep in mind the precautions and conditions set forth in the “Handling Guide for Semiconductor Devices,” or “TOSHIBA Semiconductor Reliability Handbook” etc.. · The TOSHIBA products listed in this document are intended for usage in general electronics applications (computer, personal equipment, office equipment, measuring equipment, industrial robotics, domestic appliances, etc.). These TOSHIBA products are neither intended nor warranted for usage in equipment that requires extraordinarily high quality and/or reliability or a malfunction or failure of which may cause loss of human life or bodily injury (“Unintended Usage”). Unintended Usage include atomic energy control instruments, airplane or spaceship instruments, transportation instruments, traffic signal instruments, combustion control instruments, medical instruments, all types of safety devices, etc.. Unintended Usage of TOSHIBA products listed in this document shall be made at the customer’s own risk. · The information contained herein is presented only as a guide for the applications of our products. No responsibility is assumed by TOSHIBA CORPORATION for any infringements of intellectual property or other rights of the third parties which may result from its use. No license is granted by implication or otherwise under any intellectual property or other rights of TOSHIBA CORPORATION or others. · The information contained herein is subject to change without notice.000707EAARESTRICTIONS ON PRODUCT USE。
常用开关电源芯片大全之欧阳育创编

常用开关电源芯片大全第1章DC-DC电源转换器/基准电压源1.1 DC-DC电源转换器1.低噪声电荷泵DC-DC电源转换器AAT3113/AAT31142.低功耗开关型DC-DC电源转换器ADP30003.高效3A开关稳压器AP15014.高效率无电感DC-DC电源转换器FAN56605.小功率极性反转电源转换器ICL76606.高效率DC-DC电源转换控制器IRU30377.高性能降压式DC-DC电源转换器ISL64208.单片降压式开关稳压器L49609.大功率开关稳压器L4970A10.1.5A降压式开关稳压器L497111.2A高效率单片开关稳压器L497812.1A高效率升压/降压式DC-DC电源转换器L597013.1.5A降压式DC-DC电源转换器LM157214.高效率1A降压单片开关稳压器LM1575/LM2575/LM2575HV15.3A降压单片开关稳压器LM2576/LM2576HV16.可调升压开关稳压器LM257717.3A降压开关稳压器LM259618.高效率5A开关稳压器LM267819.升压式DC-DC电源转换器LM2703/LM270420.电流模式升压式电源转换器LM273321.低噪声升压式电源转换器LM275022.小型75V降压式稳压器LM500723.低功耗升/降压式DC-DC电源转换器LT107324.升压式DC-DC电源转换器LT161525.隔离式开关稳压器LT172526.低功耗升压电荷泵LT175127.大电流高频降压式DC-DC电源转换器LT176528.大电流升压转换器LT193529.高效升压式电荷泵LT193730.高压输入降压式电源转换器LT195631.1.5A升压式电源转换器LT196132.高压升/降压式电源转换器LT343333.单片3A升压式DC-DC电源转换器LT343634.通用升压式DC-DC电源转换器LT346035.高效率低功耗升压式电源转换器LT346436.1.1A升压式DC-DC电源转换器LT346737.大电流高效率升压式DC-DC电源转换器LT378238.微型低功耗电源转换器LTC175439.1.5A单片同步降压式稳压器LTC187540.低噪声高效率降压式电荷泵LTC191141.低噪声电荷泵LTC3200/LTC3200-542.无电感的降压式DC-DC电源转换器LTC325143.双输出/低噪声/降压式电荷泵LTC325244.同步整流/升压式DC-DC电源转换器LTC340145.低功耗同步整流升压式DC-DC电源转换器LTC340246.同步整流降压式DC-DC电源转换器LTC340547.双路同步降压式DC-DC电源转换器LTC340748.高效率同步降压式DC-DC电源转换器LTC341649.微型2A升压式DC-DC电源转换器LTC342650.2A两相电流升压式DC-DC电源转换器LTC342851.单电感升/降压式DC-DC电源转换器LTC344052.大电流升/降压式DC-DC电源转换器LTC344253.1.4A同步升压式DC-DC电源转换器LTC345854.直流同步降压式DC-DC电源转换器LTC370355.双输出降压式同步DC-DC电源转换控制器LTC373656.降压式同步DC-DC电源转换控制器LTC377057.双2相DC-DC电源同步控制器LTC380258.高性能升压式DC-DC电源转换器MAX1513/MAX151459.精简型升压式DC-DC电源转换器MAX1522/MAX1523/MAX152460.高效率40V升压式DC-DC电源转换器MAX1553/MAX155461.高效率升压式LED电压调节器MAX1561/MAX159962.高效率5路输出DC-DC电源转换器MAX156563.双输出升压式DC-DC电源转换器MAX1582/MAX1582Y64.驱动白光LED的升压式DC-DC电源转换器MAX158365.高效率升压式DC-DC电源转换器MAX1642/MAX164366.2A降压式开关稳压器MAX164467.高效率升压式DC-DC电源转换器MAX1674/MAX1675/MAX167668.高效率双输出DC-DC电源转换器MAX167769.低噪声1A降压式DC-DC电源转换器MAX1684/MAX168570.高效率升压式DC-DC电源转换器MAX169871.高效率双输出降压式DC-DC电源转换器MAX171572.小体积升压式DC-DC电源转换器MAX1722/MAX1723/MAX172473.输出电流为50mA的降压式电荷泵MAX173074.升/降压式电荷泵MAX175975.高效率多路输出DC-DC电源转换器MAX180076.3A同步整流降压式稳压型MAX1830/MAX183177.双输出开关式LCD电源控制器MAX187878.电流模式升压式DC-DC电源转换器MAX189679.具有复位功能的升压式DC-DC电源转换器MAX194780.高效率PWM降压式稳压器MAX1992/MAX199381.大电流输出升压式DC-DC电源转换器MAX61882.低功耗升压或降压式DC-DC电源转换器MAX62983.PWM升压式DC-DC电源转换器MAX668/MAX66984.大电流PWM降压式开关稳压器MAX724/MAX72685.高效率升压式DC-DC电源转换器MAX756/MAX75786.高效率大电流DC-DC电源转换器MAX761/MAX76287.隔离式DC-DC电源转换器MAX8515/MAX8515A88.高性能24V升压式DC-DC电源转换器MAX872789.升/降压式DC-DC电源转换器MC33063A/MC34063A90.5A升压/降压/反向DC-DC电源转换器MC33167/MC3416791.低噪声无电感电荷泵MCP1252/MCP125392.高频脉宽调制降压稳压器MIC220393.大功率DC-DC升压电源转换器MIC229594.单片微型高压开关稳压器NCP1030/NCP103195.低功耗升压式DC-DC电源转换器NCP1400A96.高压DC-DC电源转换器NCP140397.单片微功率高频升压式DC-DC电源转换器NCP141098.同步整流PFM步进式DC-DC电源转换器NCP142199.高效率大电流开关电压调整器NCP1442/NCP1443/NCP1444/NCP1445100.新型双模式开关稳压器NCP1501101.高效率大电流输出DC-DC电源转换器NCP1550102.同步降压式DC-DC电源转换器NCP1570103.高效率升压式DC-DC电源转换器NCP5008/NCP5009 104.大电流高速稳压器RT9173/RT9173A105.高效率升压式DC-DC电源转换器RT9262/RT9262A106.升压式DC-DC电源转换器SP6644/SP6645107.低功耗升压式DC-DC电源转换器SP6691108.新型高效率DC-DC电源转换器TPS54350109.无电感降压式电荷泵TPS6050x110.高效率升压式电源转换器TPS6101x111.28V恒流白色LED驱动器TPS61042112.具有LDO输出的升压式DC-DC电源转换器TPS6112x 113.低噪声同步降压式DC-DC电源转换器TPS6200x114.三路高效率大功率DC-DC电源转换器TPS75003115.高效率DC-DC电源转换器UCC39421/UCC39422116.PWM控制升压式DC-DC电源转换器XC6371117.白光LED驱动专用DC-DC电源转换器XC9116118.500mA同步整流降压式DC-DC电源转换器XC9215/XC9216/XC9217119.稳压输出电荷泵XC9801/XC9802120.高效率升压式电源转换器ZXLB16001.2 线性/低压差稳压器121.具有可关断功能的多端稳压器BAXXX122.高压线性稳压器HIP5600123.多路输出稳压器KA7630/KA7631124.三端低压差稳压器LM2937125.可调输出低压差稳压器LM2991126.三端可调稳压器LM117/LM317127.低压降CMOS500mA线性稳压器LP38691/LP38693128.输入电压从12V到450V的可调线性稳压器LR8129.300mA非常低压降稳压器(VLDO)LTC3025130.大电流低压差线性稳压器LX8610131.200mA负输出低压差线性稳压器MAX1735132.150mA低压差线性稳压器MAX8875133.带开关控制的低压差稳压器MC33375134.带有线性调节器的稳压器MC33998135.1.0A低压差固定及可调正稳压器NCP1117136.低静态电流低压差稳压器NCP562/NCP563137.具有使能控制功能的多端稳压器PQxx138.五端可调稳压器SI-3025B/SI-3157B139.400mA低压差线性稳压器SPX2975140.五端线性稳压器STR20xx141.五端线性稳压器STR90xx142.具有复位信号输出的双路输出稳压器TDA8133143.具有复位信号输出的双路输出稳压器TDA8138/TDA8138A144.带线性稳压器的升压式电源转换器TPS6110x145.低功耗50mA低压降线性稳压器TPS760xx146.高输入电压低压差线性稳压器XC6202147.高速低压差线性稳压器XC6204148.高速低压差线性稳压器XC6209F149.双路高速低压差线性稳压器XC64011.3 基准电压源150.新型XFET基准电压源ADR290/ADR291/ADR292/ADR293151.低功耗低压差大输出电流基准电压源MAX610x152.低功耗1.2V基准电压源MAX6120153.2.5V精密基准电压源MC1403154.2.5V/4.096V基准电压源MCP1525/MCP1541155.低功耗精密低压降基准电压源REF30xx/REF31xx156.精密基准电压源TL431/KA431/TLV431A第2章AC-DC转换器及控制器1.厚膜开关电源控制器DP104C2.厚膜开关电源控制器DP308P3.DPA-Switch系列高电压功率转换控制器DPA423/DPA424/DPA425/DPA4264.电流型开关电源控制器FA13842/FA13843/FA13844/FA138455.开关电源控制器FA5310/FA53116.PWM开关电源控制器FAN75567.绿色环保的PWM开关电源控制器FAN76018.FPS型开关电源控制器FS6M07652R9.开关电源功率转换器FS6Sxx10.降压型单片AC-DC转换器HV-2405E11.新型反激准谐振变换控制器ICE1QS0112.PWM电源功率转换器KA1M088013.开关电源功率转换器KA2S0680/KA2S088014.电流型开关电源控制器KA38xx15.FPS型开关电源功率转换器KA5H0165R16.FPS型开关电源功率转换器KA5Qxx17.FPS型开关电源功率转换器KA5Sxx18.电流型高速PWM控制器L499019.具有待机功能的PWM初级控制器L599120.低功耗离线式开关电源控制器L659021.LINK SWITCH TN系列电源功率转换器LNK304/LNK305/LNK30622.LINK SWITCH系列电源功率转换器LNK500/LNK501/LNK52023.离线式开关电源控制器M51995A24.PWM电源控制器M62281P/M62281FP25.高频率电流模式PWM控制器MAX5021/MAX502226.新型PWM开关电源控制器MC4460427.电流模式开关电源控制器MC4460528.低功耗开关电源控制器MC4460829.具有PFC功能的PWM电源控制器ML482430.液晶显示器背光灯电源控制器ML487631.离线式电流模式控制器NCP120032.电流模式脉宽调制控制器NCP120533.准谐振式PWM控制器NCP120734.低成本离线式开关电源控制电路NCP121535.低待机能耗开关电源PWM控制器NCP123036.STR系列自动电压切换控制开关STR8xxxx37.大功率厚膜开关电源功率转换器STR-F665438.大功率厚膜开关电源功率转换器STR-G865639.开关电源功率转换器STR-M6511/STR-M652940.离线式开关电源功率转换器STR-S5703/STR-S5707/STR-S570841.离线式开关电源功率转换器STR-S6401/STR-S6401F/STR-S6411/STR-S6411F 442.开关电源功率转换器STR-S651343.离线式开关电源功率转换器TC33369~TC3337444.高性能PFC与PWM组合控制集成电路TDA16846/TDA1684745.新型开关电源控制器TDA1685046.“绿色”电源控制器TEA150447.第二代“绿色”电源控制器TEA150748.新型低功耗“绿色”电源控制器TEA153349.开关电源控制器TL494/KA7500/MB375950.Tiny SwitchⅠ系列功率转换器TNY253、TNY254、TNY25551.Tiny SwitchⅡ系列功率转换器TNY264P~TNY268G52.TOP Switch(Ⅱ)系列离线式功率转换器TOP209~TOP22753.TOP Switch-FX系列功率转换器TOP232/TOP233/TOP23454.TOP Switch-GX系列功率转换器TOP242~TOP25055.开关电源控制器UCX84X56.离线式开关电源功率转换器VIPer12AS/VIPer12ADIP57.新一代高度集成离线式开关电源功率转换器VIPer53第3章功率因数校正控制/节能灯电源控制器1.电子镇流器专用驱动电路BL83012.零电压开关功率因数控制器FAN48223.功率因数校正控制器FAN75274.高电压型EL背光驱动器HV8265.EL场致发光背光驱动器IMP525/IMP5606.高电压型EL背光驱动器/反相器IMP8037.电子镇流器自振荡半桥驱动器IR21568.单片荧光灯镇流器IR21579.调光电子镇流器自振荡半桥驱动器IR215910.卤素灯电子变压器智能控制电路IR216111.具有功率因数校正电路的镇流器电路IR216612.单片荧光灯镇流器IR216713.自适应电子镇流器控制器IR252014.电子镇流器专用控制器KA754115.功率因数校正控制器L656116.过渡模式功率因数校正控制器L656217.集成背景光控制器MAX8709/MAX8709A18.功率因数校正控制器MC33262/MC3426219.固定频率电流模式功率因数校正控制器NCP165320.EL场致发光灯高压驱动器SP440321.功率因数校正控制器TDA4862/TDA486322.有源功率因数校正控制器UC385423.高频自振荡节能灯驱动器电路VK05CFL24.大功率高频自振荡节能灯驱动器电路VK06TL第4章充电控制器1.多功能锂电池线性充电控制器AAT36802.可编程快速电池充电控制器BQ20003.可进行充电速率补偿的锂电池充电管理器BQ20574.锂电池充电管理电路BQ2400x5.单片锂电池线性充电控制器BQ2401xB接口单节锂电池充电控制器BQ2402x7.2A同步开关模式锂电池充电控制器BQ241008.集成PWM开关控制器的快速充电管理器BQ29549.具有电池电量计量功能的充电控制器DS277010.锂电池充电控制器FAN7563/FAN756411.2A线性锂/锂聚合物电池充电控制器ISL629212.锂电池充电控制器LA5621M/LA5621V13.1.5A通用充电控制器LT157114.2A恒流/恒压电池充电控制器LT176915.线性锂电池充电控制器LTC173216.带热调节功能的1A线性锂电池充电控制器LTC173317.线性锂电池充电控制器LTC173418.新型开关电源充电控制器LTC198019.开关模式锂电池充电控制器LTC400220.4A锂电池充电器LTC400621.多用途恒压/恒流充电控制器LTC400822.4.2V锂离子/锂聚合物电池充电控制器LTC405223.可由USB端口供电的锂电池充电控制器LTC405324.小型150mA锂电池充电控制器LTC405425.线性锂电池充电控制器LTC405826.单节锂电池线性充电控制器LTC405927.独立线性锂电池充电控制器LTC406128.镍镉/镍氢电池充电控制器M62256FP29.大电流锂/镍镉/镍氢电池充电控制器MAX150130.锂电池线性充电控制器MAX150731.双输入单节锂电池充电控制器MAX1551/MAX155532.单节锂电池充电控制器MAX167933.小体积锂电池充电控制器MAX1736B接口单节锂电池充电控制器MAX181135.多节锂电池充电控制器MAX187336.双路输入锂电池充电控制器MAX187437.单节锂电池线性充电控制器MAX189838.低成本/多种电池充电控制器MAX190839.开关模式单节锂电池充电控制器MAX1925/MAX192640.快速镍镉/镍氢充电控制器MAX2003A/MAX200341.可编程快速充电控制器MAX712/MAX71342.开关式锂电池充电控制器MAX74543.多功能低成本充电控制器MAX846A44.具有温度调节功能的单节锂电池充电控制器MAX8600/MAX860145.锂电池充电控制器MCP73826/MCP73827/MCP7382846.高精度恒压/恒流充电器控制器MCP73841/MCP73842/MCP73843/MCP73844 647.锂电池充电控制器MCP73861/MCP7386248.单节锂电池充电控制器MIC7905049.单节锂电池充电控制器NCP180050.高精度线性锂电池充电控制器VM7205。
西安威克产品介绍

先进的安全技术,防爆,防火,防漏。
内置电容器芯体故障保护使故障安全隔离 特殊的工艺工程及优质环保灌注材料。
多重保护
无油,无蜡,全干式结构。 壳体采用钢板喷塑结构。
油或蜡,容易漏出。
马口铁外壳结构,容易生锈。 内置一般放电电阻。
内置放电 内置超低损耗放电电阻。
随变张力卷制
提高电容器元件端面的平整 度 。确保每只产品,都能通 过严格的过电流试验,确保 质量的稳定性.
优越的产品工艺
德威克电容器
边缘加厚 金属化薄膜镀层边缘加厚提高电容器 元件过电流的能力 。 大大增加喷金面的有效面积。 随变张力 渐进方阻 过电流试验 每只产品,都要通过严格的过电流试验, 确保质量的稳定性. 真空灌注 采用在高真空抽取元件内的水份,并注 入性能良好环保树脂。 有效提高自愈合的能力和综合电气性 能。
自愈合能力
金属化薄膜的电极采用锌铝复合 技术 击穿点使电极介质层气化分开, 产生绝缘区,电容器恢复正常工 作能力。
DWKCL滤波电抗器
概述: 德威克滤波电抗器用于电力系统低压无功补偿,与电容器串联,能有效抑制 电网谐波,改善系统的电压波形,提高系统的功率因数。 电抗器结构: 电抗器为铁芯干式结构,产品分为单相和三相。 产品型号: DWKCLS□-○/△
只有每年2000次的投切次数。 介质损耗大于0.25/Kvar。。 60000小时的寿命设计甚至更低。
极低的介质损耗,只有0.25/Kvar。。
低温升
100000小时的寿命设计。
先进的安全保护性能
德威克电容器
自愈合 三防结构 自愈合能力,自我修复,容降低
其它厂家电容器
联动保护装置
有自愈合能力,但容降大。 安全技术不过关,有可能爆裂, 起火。 油或蜡的灌注材料,容易起火。
LTC1603CG#PBF;LTC1603CG;LTC1603CG#TRPBF;LTC1603CG#TR;LTC1603IG;中文规格书,Datasheet资料

U APPLICATIO S
s s s s s s
Telecommunications Digital Signal Processing Multiplexed Data Acquisition Systems High Speed Data Acquisition Spectrum Analysis Imaging Systems
The q denotes the specifications which apply over the full operating temperature range, otherwise specifications are at TA = 25°C. With Internal Reference (Notes 5, 6)
, LTC and LT are registered trademarks of Linear Technology Corporation.
s s s s s
A Complete, 250ksps 16-Bit ADC 90dB S/(N+D) and –100dB THD (Typ) Power Dissipation: 220mW (Typ) Nap (7mW) and Sleep (10µW) Shutdown Modes No Pipeline Delay No Missing Codes over Temperature Operates with Internal 15ppm/°C Reference or External Reference True Differential Inputs Reject Common Mode Noise 5MHz Full Power Bandwidth ± 2.5V Bipolar Input Range Pin Compatible with LTC1604 and LTC1608 36-Pin SSOP Package
SF3003PT中文资料

SF3001PT – SF3006PT30A SUPER-FAST GLASS PASSIVATED RECTIFIERSingle Phase, half wave, 60Hz, resistive or inductive load.For capacitive load, derate current by 20%.CharacteristicSymbol SF 3001PT SF 3002PT SF 3003PT SF 3004PT SF 3005PT SF 3006PT UnitPeak Repetitive Reverse Voltage Working Peak Reverse Voltage DC Blocking Voltage V RRMV RWM V R 50100150200300400V RMS Reverse VoltageV R(RMS)3570105140210280V Average Rectified Output Current @T C = 100°C I O30ANon-Repetitive Peak Forward Surge Current 8.3ms Single half sine-wave superimposed on rated load (JEDEC Method)I FSM 300A Forward Voltage @I F = 15A V FM 0.951.3V Peak Reverse Current @T A = 25°C At Rated DC Blocking Voltage @T A = 100°C I RM 10500µA Reverse Recovery Time (Note 1)t rr 35nS Typical Junction Capacitance (Note 2)C j 175pF Operating and Storage Temperature RangeT j , T STG-55 to +150°CNote: 1. Measured with IF = 0.5A, IR = 1.0A, IRR = 0.25A.2. Measured at 1.0 MHz and applied reverse voltage of 4.0V D.C.W T EWER SEMICONDUCTORS601201800240300360110100I ,P E A K F O R W A R D S U R G E C U R R E N T (A )F S M NUMBER OF CYCLES AT 60HzFig.3Max Non-Repetitive10100400V ,REVERSE VOLTAGE (V)Junction CapacitanceR C ,C A P A C I T A N C E (p F )j 0.010.11.0101004080120I ,I N S T A N T A N E O U S R E V E R S E C U R R E N T (m A )R PERCENT OF RATED PEAK REVERSE VOLTAGE (%)Fig.5Typical Reverse Characteristics0612182430050100150I ,A V E R A G E F O R W A R D C U R R E N T (A )(A V )T ,CASE TEMPERATURE (C)Fig.1Forward Current Derating CurveC °0.11.0101000.20.61.01.4I ,I N S T A N T A N E O U S F O R W A R D C U R R E N T (A )F V ,INSTANTANEOUS FORWARD VOLTAGE (V)Fig.2Typical Forward CharacteristicsFORDERING INFORMATIONProduct No.Package TypeShipping QuantitySF3001PT TO-3P 30 Units/Tube SF3002PT TO-3P 30 Units/Tube SF3003PT TO-3P 30 Units/Tube SF3004PT TO-3P 30 Units/Tube SF3005PT TO-3P 30 Units/Tube SF3006PTTO-3P30 Units/TubeShipping quantity given is for minimum packing quantity only. For minimum orderquantity, please consult the Sales Department.Won-Top Electronics Co., Ltd (WTE) has checked all information carefully and believes it to be correct and accurate. However, WTE cannot assume any responsibility for inaccuracies. Furthermore, this information does not give the purchaser of semiconductor devices any license under patent rights to manufacturer. WTE reserves the right to change any or all information herein without further notice.WARNING : DO NOT USE IN LIFE SUPPORT EQUIPMENT. WTE power semiconductor products are not authorized for use as critical components in life support devices or systems without the express written approval.We power your everyday.Won-Top Electronics Co., Ltd.No. 44 Yu Kang North 3rd Road, Chine Chen Dist., Kaohsiung, Taiwan Phone: 886-7-822-5408 or 886-7-822-5410Fax: 886-7-822-5417Email: sales@Internet: 。
ER1603FCT中文资料(Won-Top Electronics)中文数据手册「EasyDatasheet - 矽搜」

标识信息
WTE
ER160xFCT WTE =制造商标志 ER160xFCT =设备号 x = 0,1,1A,2,3,4或6个 极性 =对人体标示
封装信息
BULK
管尺寸 长×宽×高(mm) 数量 内箱尺寸 长×宽×高(mm) 数量 外箱尺寸 长×宽×高(mm) 数量 约.总重量
(PCS) 50
(PCS) 2,000
6-32六角头螺丝
平焊盘圈
锥形焊盘圈应该用于正确力施加到所述设 备.螺钉不应收紧与任何类型空气被迫扭 矩或器材可能导致裂纹器件封装.
整流器 散热器 锥形焊盘圈
导热硅脂或接口散热焊盘一层将是散热相当 有帮助.
6-32六角螺母
ER1600FCT – ER1606FCT
3 of 4
芯片中文手册,看全文,戳
芯片中文手册,看全文,戳
ER1600FCT – ER1606FCT
16A玻璃钝化双超快速整流器 特征
玻璃钝化模具结构 超快速切换 低正向压降 低反向漏电流 高浪涌电流能力 塑料材料具有UL可燃性 分类94V-O
Pb
B C G
PIN1 2 3
A
D
机械数据
案例:ITO-220,全模制塑料 终端:每焊镀信息 MIL-STD-202,方法208 极性:见图 重量:2.24克(约) 安装位置:任意 安装扭矩:11.5厘米千克(10磅)最大. 无铅:对于符合 RoHS /无铅版本 , 新增 "-LF"后缀型号 ,见第 4页
循环次数在60Hz 图. 3最大不重复浪涌电流
10 10 100 0.1 1.0 VR,反向电压(V) 图. 4典型结电容
t +0.5A
10
100
SMB系列600瓦尖峰功率抗冲击电阻抑制器说明书

P6SMB91AT3G P6SMB75AT3G P6SMB13AT3G P6SMB200AT3G.P6SMB160AT3G P6SMB27AT3G.P6SMB33AT3G.P6SMB51AT3G P6SMB16AT3GP6SMB6.8AT3 Series600 Watt Peak Power Zener Transient Voltage SuppressorsUnidirectional*The SMB series is designed to protect voltage sensitivecomponents from high voltage, high energy transients. They have excellent clamping capability, high surge capability, low zener impedance and fast response time. The SMB series is supplied in ON Semiconductor’s exclusive, cost-effective, highly reliable Surmetic™ package and is ideally suited for use in communication systems, automotive, numerical controls, process controls, medical equipment, business machines, power supplies and many other industrial/consumer applications.Specification Features:•Working Peak Reverse V oltage Range − 5.8 to 171 V •Standard Zener Breakdown V oltage Range − 6.8 to 200 V •Peak Power − 600 W @ 1 ms•ESD Rating of Class 3 (>16 KV) per Human Body Model •Maximum Clamp V oltage @ Peak Pulse Current•Low Leakage < 5 m A Above 10 V•UL 497B for Isolated Loop Circuit Protection •Response Time is Typically < 1 ns•Pb−Free Packages are AvailableMechanical Characteristics:CASE:V oid-free, transfer-molded, thermosetting plasticFINISH:All external surfaces are corrosion resistant and leads are readily solderableMAXIMUM CASE TEMPERATURE FOR SOLDERING PURPOSES: 260°C for 10 SecondsLEADS:Modified L−Bend providing more contact area to bond pads POLARITY:Cathode indicated by polarity bandMOUNTING POSITION:AnyMAXIMUM RATINGSPlease See the Table on the Following Page*Please see P6SMB11CAT3 to P6SMB91CAT3 for Bidirectional devices.Device Package Shipping†ORDERING INFORMATIONP6SMBxxxAT3SMB2500/Tape & ReelSMBCASE 403APLASTICP6SMBxxxAT3G SMB(Pb−Free)2500/Tape & Reel†For information on tape and reel specifications, including part orientation and tape sizes, please refer to our T ape and Reel Packaging Specifications Brochure, BRD8011/D.A= Assembly LocationY= YearWW= Work Weekxx= Device Code (Refer to page 3)G= Pb−Free PackageMARKING DIAGRAMAYWWxx GG(Note: Microdot may be in either location)MAXIMUM RATINGSRating Symbol Value Unit Peak Power Dissipation (Note 1) @ T L = 25°C, Pulse Width = 1 ms P PK600WDC Power Dissipation @ T L = 75°C Measured Zero Lead Length (Note 2) Derate Above 75°CThermal Resistance from Junction−to−LeadP DR q JL3.04025WmW/°C°C/WDC Power Dissipation (Note 3) @ T A = 25°C Derate Above 25°CThermal Resistance from Junction−to−AmbientP DR q JA0.554.4226WmW/°C°C/WForward Surge Current (Note 4) @ T A = 25°C I FSM100A Operating and Storage Temperature Range T J, T stg−65 to +150°C Stresses exceeding Maximum Ratings may damage the device. Maximum Ratings are stress ratings only. Functional operation above the Recommended Operating Conditions is not implied. Extended exposure to stresses above the Recommended Operating Conditions may affect device reliability.1.10 X 1000 m s, non−repetitive2.1″ square copper pad, FR−4 board3.FR−4 board, using ON Semiconductor minimum recommended footprint, as shown in 403A case outline dimensions spec.4.1/2 sine wave (or equivalent square wave), PW = 8.3 ms, duty cycle = 4 pulses per minute maximum.ELECTRICAL CHARACTERISTICS(T A = 25°C unless otherwise noted, V F = 3.5 V Max. @I F (Note 4) = 30 A) (Note 5)Symbol ParameterI PP Maximum Reverse Peak Pulse CurrentV C Clamping Voltage @ I PPV RWM Working Peak Reverse VoltageI R Maximum Reverse Leakage Current @ V RWMV BR Breakdown Voltage @ I TI T Test CurrentQ V BR Maximum Temperature Coefficient of V BRI F Forward CurrentV F Forward Voltage @ I F5.1/2 sine wave or equivalent, PW = 8.3 ms, non−repetitiveduty cycleELECTRICAL CHARACTERISTICS (Devices listed in bold, italic are ON Semiconductor Preferred devices.)DeviceDeviceMarkingV RWM(Note 6)I R@V RWMBreakdown Voltage V C @ I PP(Note 8)Q V BRC typ(Note 9)V BR V (Note 7)@ I T V C I PPV m A Min Nom Max mA V A%/°C pFP6SMB6.8AT3, G P6SMB7.5AT3, G P6SMB8.2AT3, G P6SMB9.1AT3, G 6V8A7V5A8V2A9V1A5.86.47.027.781000500200506.457.137.798.656.87.518.29.17.147.888.619.55101010110.511.312.113.4575350450.0570.0610.0650.0682380218020151835P6SMB10AT3, G P6SMB11AT3, G P6SMB12AT3, G P6SMB13AT3, G 10A11A12A13A8.559.410.211.1105559.510.511.412.41011.051213.0510.511.612.613.7111114.515.616.718.2413836330.0730.0750.0780.0811690155014351335P6SMB15AT3, G P6SMB16AT3, G P6SMB18AT3, G P6SMB20AT3, G 15A16A18A20A12.813.615.317.1555514.315.217.11915.0516182015.816.818.921111121.222.525.227.7282724220.0840.0860.0880.09117511101000910P6SMB22AT3,G P6SMB24AT3, G P6SMB27AT3, G P6SMB30AT3, G 22A24A27A30A18.820.523.125.6555520.922.825.728.5222427.053023.125.228.431.5111130.633.237.541.420181614.40.0920.0940.0960.097835775700635P6SMB33AT3, G P6SMB36AT3, G P6SMB39AT3, G P6SMB43AT3, G 33A36A39A43A28.230.833.336.8555531.434.237.140.933.053639.0543.0534.737.84145.2111145.749.953.959.313.21211.210.10.0980.0990.10.101585540500460P6SMB47AT3, G P6SMB51AT3, G P6SMB56AT3, G P6SMB62AT3, G 47A51A56A62A40.243.647.853555544.748.553.258.947.0551.05566249.453.658.865.1111164.870.177859.38.67.87.10.1010.1020.1030.104425395365335P6SMB68AT3, G P6SMB75AT3, G P6SMB82AT3, G P6SMB91AT3, G 68A75A82A91A58.164.170.177.8555564.671.377.986.56875.05829171.478.886.195.51111921031131256.55.85.34.80.1040.1050.1050.106305280260235P6SMB100AT3, G P6SMB110AT3, G P6SMB120AT3, G P6SMB130AT3, G 100A110A120A130A85.594102111555595105114124100110.5120130.510511612613711111371521651794.44.03.63.30.1060.1070.1070.107215200185170P6SMB150AT3, G P6SMB160AT3, G P6SMB170AT3, G P6SMB180AT3, G 150A160A170A180A1281361451545555143152162171150.516017018015816817918911112072192342462.92.72.62.40.1080.1080.1080.108150140135130P6SMB200AT3, G200A17151902002101274 2.20.1081156. A transient suppressor is normally selected according to the working peak reverse voltage (V RWM), which should be equal to or greater thanthe DC or continuous peak operating voltage level.7.V BR measured at pulse test current I T at an ambient temperature of 25°C.8.Surge current waveform per Figure 2 and derate per Figure 3.9.Bias Voltage = 0 V, F = 1 MHz, T J = 25°C*The “G” suffix indicates Pb−Free package available.P , P E A K P O W E R (k W )P 1101000.1t, TIME (ms)Figure 2. Pulse WaveformTYPICAL PROTECTION CIRCUITFigure 3. Pulse Derating CurveP E A K P U L S E D E R A T I N G I N % O F P E A K P O W E R O R C U R R E N T @ T A = 25C°T A , AMBIENT TEMPERATURE (°C)Figure 4. Typical Junction Capacitance vs.Bias VoltageBIAS VOLTAGE (VOLTS)1101001000C , C A P A C I T A N C E (p F )APPLICATION NOTESRESPONSE TIMEIn most applications, the transient suppressor device is placed in parallel with the equipment or component to be protected. In this situation, there is a time delay associated with the capacitance of the device and an overshoot condition associated with the inductance of the device and the inductance of the connection method. The capacitive effect is of minor importance in the parallel protection scheme because it only produces a time delay in the transition from the operating voltage to the clamp voltage as shown in Figure 5.The inductive effects in the device are due to actual turn-on time (time required for the device to go from zero current to full current) and lead inductance. This inductive effect produces an overshoot in the voltage across the equipment or component being protected as shown in Figure 6. Minimizing this overshoot is very important in the application, since the main purpose for adding a transient suppressor is to clamp voltage spikes. The SMB series have a very good response time, typically < 1 ns and negligible inductance. However, external inductive effects could produce unacceptable overshoot. Proper circuit layout,minimum lead lengths and placing the suppressor device as close as possible to the equipment or components to be protected will minimize this overshoot.Some input impedance represented by Z in is essential to prevent overstress of the protection device. This impedance should be as high as possible, without restricting the circuit operation.DUTY CYCLE DERATINGThe data of Figure 1 applies for non-repetitive conditions and at a lead temperature of 25°C. If the duty cycle increases, the peak power must be reduced as indicated by the curves of Figure 7. Average power must be derated as the lead or ambient temperature rises above 25°C. The average power derating curve normally given on data sheets may be normalized and used for this purpose.At first glance the derating curves of Figure 7 appear to be in error as the 10 ms pulse has a higher derating factor than the 10 m s pulse. However, when the derating factor for a given pulse of Figure 7 is multiplied by the peak power value of Figure 1 for the same pulse, the results follow the expected trend.VFigure 5. Figure 6.Figure 7. Typical Derating Factor for Duty CycleD E R A T I N GF A C T O R10.70.50.30.050.10.20.010.020.030.07D, DUTY CYCLE (%)UL RECOGNITIONThe entire series has Underwriters Laboratory Recognition for the classification of protectors (QVGV2)under the UL standard for safety 497B and File #E210057.Many competitors only have one or two devices recognized or have recognition in a non-protective category. Some competitors have no recognition at all. With the UL497B recognition, our parts successfully passed several testsincluding Strike V oltage Breakdown test, Endurance Conditioning, Temperature test, Dielectric V oltage-Withstand test, Discharge test and several more.Whereas, some competitors have only passed a flammability test for the package material, we have been recognized for much more to be included in their Protector category.PACKAGE DIMENSIONSSMBCASE 403A−03ISSUE F*For additional information on our Pb−Free strategy and solderingdetails, please download the ON Semiconductor Soldering and Mounting Techniques Reference Manual, SOLDERRM/D.SOLDERING FOOTPRINT*ǒmm inchesǓSCALE 8:1NOTES:1.DIMENSIONING AND TOLERANCING PER ANSI Y14.5M, 1982.2.CONTROLLING DIMENSION: INCH.3.D DIMENSION SHALL BE MEASURED WITHIN DIMENSION P.DIM A MIN NOM MAX MIN MILLIMETERS1.902.13 2.450.075INCHES A10.050.100.200.002b 1.96 2.03 2.200.077c 0.150.230.310.0063.30 3.56 3.950.130E4.06 4.32 4.600.160L 0.761.02 1.600.0300.0840.0960.0040.0080.0800.0870.0090.0120.1400.1560.1700.1810.0400.063NOM MAX 5.21 5.44 5.600.2050.2140.220H E 0.51 REF0.020 REFD L1ON Semiconductor and are registered trademarks of Semiconductor Components Industries, LLC (SCILLC). SCILLC reserves the right to make changes without further notice to any products herein. SCILLC makes no warranty, representation or guarantee regarding the suitability of its products for any particular purpose, nor does SCILLC assume any liability arising out of the application or use of any product or circuit, and specifically disclaims any and all liability, including without limitation special, consequential or incidental damages.“Typical” parameters which may be provided in SCILLC data sheets and/or specifications can and do vary in different applications and actual performance may vary over time. All operating parameters, including “Typicals” must be validated for each customer application by customer’s technical experts. SCILLC does not convey any license under its patent rights nor the rights of others. SCILLC products are not designed, intended, or authorized for use as components in systems intended for surgical implant into the body, or other applications intended to support or sustain life, or for any other application in which the failure of the SCILLC product could create a situation where personal injury or death may occur. Should Buyer purchase or use SCILLC products for any such unintended or unauthorized application, Buyer shall indemnify and hold SCILLC and its officers, employees, subsidiaries, affiliates,and distributors harmless against all claims, costs, damages, and expenses, and reasonable attorney fees arising out of, directly or indirectly, any claim of personal injury or death associated with such unintended or unauthorized use, even if such claim alleges that SCILLC was negligent regarding the design or manufacture of the part. SCILLC is an Equal Opportunity/Affirmative Action Employer. This literature is subject to all applicable copyright laws and is not for resale in any manner.PUBLICATION ORDERING INFORMATIONSURMETIC is a trademark of Semiconductor Components Industries, LLC.P6SMB91AT3G P6SMB75AT3G P6SMB13AT3G P6SMB200AT3G.P6SMB160AT3G P6SMB27AT3G.P6SMB33AT3G.P6SMB51AT3G P6SMB16AT3G。
维莎Sfernice MEPIC巨大电子火工品激活电阻器说明书

Massive Electro-Pyrotechnic Initiator Chip ResistorLINKS TO ADDITIONAL RESOURCESThe Massive Electro-Pyrotechnic Initiator Chips (MEPIC) are resistors dedicated to pyrotechnic applications. The MEPIC resistors are the Surface Mount Device (SMD) variants from the established NiCr on FR type substrate technology from Vishay Sfernice. The standard case geometry (SMD) enables the implementation of assembly process commonly used in the electronic component industry (pick and place, reflow soldering on flat PCB used as header) providing high productivity. The principle of MEPIC is to convert electrical energy into heat in a precise electro-thermal profile for the purpose of initiating a series of pyrotechnic events in a controlled energetic reaction. I n the mining industry this effect is commonly used for the ignition of electronic detonators (digital blasting). Other industries such as firework (e-match manufacturing) and demolition (various electric detonators) are also focused applications.The MEPIC design has been developed specifically to offer an alternative to the Bridge Wire (BW) technology, insuring at least the same level of performances, while providing cost efficient assembly process and initiator design alternatives.FEATURES•Surface mount design for standard assembly process•SMD version only•Active area designed upon performances •Case size 0805•Firing energy down to 1.0 mJ (1)•Firing time down to 250 μs•Ohmic value: 2 Ω to 8 Ω ± 10 % (typical) (2)•Joule effect ignition•Easy set up by design of firing levels•Very predictable, reproducible and reliable behavior •Compatibility with pyrotechnic element has to be tested in real environment•Material categorization: for definitions of compliance please see /doc?99912Notes*This datasheet provides information about parts that are RoHS-compliant and / or parts that are non-RoHS-compliant. For example, parts with lead (Pb) terminations are not RoHS-compliant. Please see the information / tables in this datasheet for details(1)gnitor performances are dependent on both pyrotechnic primer chemistry and active areas geometry(2)For ohmic value < 3 Ω the tolerance will be discussed with Vishay SferniceTECHNOLOGYThe MEPIC active area (heating zone) will be impregnated by the user with a primary pyrotechnic material (usually wet primer followed by drying) in such way to ensure an intimate contact for an optimum heat transfer of thermal energy. The geometry of the active area of the MEP C, and both the primer chemistry and its impregnation method, will determine the global performances. Note that the active area of MEPIC shall not be put in direct contact with explosive powder as grain size will not ensure intimate contact and will induce non reproducible and non reliable performances.The two main characteristics of a MEPIC resistor are their “All Fire” (AF) and “No Fire” (NF) performances:-“All Fire” (AF) represents the command pulse where the major amount of the dissipated energy will be transferred to the primer to generate the ignition. Customer will have to provide Vishay Sfernice with “All Fire” conditions, usually with capacitance discharge parameters or with Minimum Current or Voltage and corresponding short pulse duration.-“No Fire” (NF) represents the immunity of the resistor with primer to the environmental electro-magnetic pollution and electric continuity test, where the major amount of the dissipated energy will be transferred to the substrate to ensure no ignition. Customer will have to provide Vishay Sfernice with “No Fire” conditions, usually maximum current or voltage and corresponding longest duration. In case of applicable capacitance discharge test the parameters shall also be provided.ASSEMBLY PRECAUTIONSIn order to obtain reproducible ignition performances it is important that the assembly process fulfills the following criteria:-Do not use iron soldering method to mount the MEPIC on its header because uncontrolled amount of solder could impact the heat transfer (potential misfire or ignition delay) and local over heating may damage the MEPIC (deformation that may cause active area cracks).-Take specific precautions, such as no air bubble during preparation and application of primer, in order to ensure the intimate contact of pyrotechnic primer and MEPIC active area (potential misfire).-Take specific handling precaution in order not to damage MEPIC active area (ex: pickup head design for pick and place or specific fixing tools in the entire assembly process.-All along the assembly process, take specific care to extreme thermo-mechanic stress that could be applied to the MEPIC (such as stress induced during over molding) because the active area of MEPIC is subjected to crack (and generate unstable resistance value).-The MEPIC reliability is only guaranteed for one single reflow profile.-In case of necessity to dismantle a MEPIC, another MEPIC must be used (no rework is allowed).-Pay specific attention to the cleaning process after reflow soldering in order not to damage the active area and to keep it cleanfrom various pollutions.3D 3D3D ModelsAvailable AvailableNote(1)Detailed dimensions are specified in Dimensions and Tolerances tableNote•Ignition performances are dependent on both pyrotechnic primer chemistry and active area geometryCONSTRUCTION•Substrate: epoxy based (FRx type)•Resistive element: NiCr •Terminations: SMD wraparound •Tin plated copper or silver plated copperHOW TO GET THE RIGHT MEPICEach MEPIC will have to be adapted to customer pyrotechnic primer chemistry (energetic material). To reach the right MEPIC design it is necessary to work by “iterations”. Upon receipt of the MEPIC Design Guide duly filled, an initial sampling lot is given to customer (along with a MEPIC reference) so he can provide “No Firing” / “All Firing” performances obtained after first testing. After the analysis of these first test results a new set of samples will be proposed (eventually tooling charges will be necessary) in order to get closer to the customer requirements. It may be several iterations until the right design is found. It may also happen that all requirements cannot be fulfilled simultaneously and then a compromise will be necessary between MEPIC design and customer pyrotechnic primer chemistry or ignition parameters.When the iterations are finished, which means that the design is validated with total or partial requirements fulfilled, Vishay Sfernice will design a final set of photomasks for serial production.STANDARD ELECTRICAL SPECIFICATIONSMODEL SIZE / CASE DESIGNATION (1)RESISTANCE RANGEΩRESISTANCE TOLERANCE%MEPIC (SMD)08052 to 810 to 30RANGE OF IGNITION PERFORMANCESMODEL “NO FIRE”CURRENTA “NO FIRE” DURATIONs “ALL FIRE”CURRENTAIGNITION TIME ms “ALL FIRE”ENERGYμJ MEPIC (SMD)0.5 to 1.22 to 10Down to 1Down to 0.25Down to 1000DIMENSIONS AND TOLERANCES in millimeters (inches)MODELSIZE / CASE DESIGNATION WIDTH W LENGTHL THICKNESST INSULATION DISTANCEIBACK SIDE PADS P ACTIVE AREAWIDTH TOLERANCEA MEPIC (SMD)08052.00 ± 0.15(0.080 ± 0.006)1.25 ± 0.10(0.050 ± 0.004)0.6 ± 0.1(0.024 ± 0.004)-0.45 ± 0.15(0.018 ± 0.006)± 0.01(± 0.0004)Notes •MEP I C being a semi-custom product, please fill EP I C / MEP I C Design Guide (/doc?53045) and send to *********************** to get appropriate part number(1)Silver termination finish valid for both reflow soldering and conductive gluing. Tin termination finish only valid for reflow soldering (2)Customer assembly process requirement: - Waffle pack for manual placing on PCB - Tape and reel for automatic pick and place - Bag for bowl feedingORDERING PROCEDUREGlobal Part Numbering: MEPICxxxxWTTMODEL xxxxTERMINATIONTYPE TERMINATION MATERIAL (1)PACKAGING (2)MEPICDetermined at design stepW : wraparoundT = tin S = silver,please consultT = tape and reel (plastic tape)W = waffle packB = bagPI C x x x x W T E MTLegal Disclaimer Notice VishayDisclaimerALL PRODU CT, PRODU CT SPECIFICATIONS AND DATA ARE SU BJECT TO CHANGE WITHOU T NOTICE TO IMPROVE RELIABILITY, FUNCTION OR DESIGN OR OTHERWISE.Vishay Intertechnology, Inc., its affiliates, agents, and employees, and all persons acting on its or their behalf (collectively,“Vishay”), disclaim any and all liability for any errors, inaccuracies or incompleteness contained in any datasheet or in any other disclosure relating to any product.Vishay makes no warranty, representation or guarantee regarding the suitability of the products for any particular purpose or the continuing production of any product. To the maximum extent permitted by applicable law, Vishay disclaims (i) any and all liability arising out of the application or use of any product, (ii) any and all liability, including without limitation special, consequential or incidental damages, and (iii) any and all implied warranties, including warranties of fitness for particular purpose, non-infringement and merchantability.Statements regarding the suitability of products for certain types of applications are based on Vishay's knowledge of typical requirements that are often placed on Vishay products in generic applications. Such statements are not binding statements about the suitability of products for a particular application. It is the customer's responsibility to validate that a particular product with the properties described in the product specification is suitable for use in a particular application. Parameters provided in datasheets and / or specifications may vary in different applications and performance may vary over time. All operating parameters, including typical parameters, must be validated for each customer application by the customer's technical experts. Product specifications do not expand or otherwise modify Vishay's terms and conditions of purchase, including but not limited to the warranty expressed therein.Hyperlinks included in this datasheet may direct users to third-party websites. These links are provided as a convenience and for informational purposes only. Inclusion of these hyperlinks does not constitute an endorsement or an approval by Vishay of any of the products, services or opinions of the corporation, organization or individual associated with the third-party website. Vishay disclaims any and all liability and bears no responsibility for the accuracy, legality or content of the third-party website or for that of subsequent links.Except as expressly indicated in writing, Vishay products are not designed for use in medical, life-saving, or life-sustaining applications or for any other application in which the failure of the Vishay product could result in personal injury or death. Customers using or selling Vishay products not expressly indicated for use in such applications do so at their own risk. Please contact authorized Vishay personnel to obtain written terms and conditions regarding products designed for such applications. No license, express or implied, by estoppel or otherwise, to any intellectual property rights is granted by this document or by any conduct of Vishay. Product names and markings noted herein may be trademarks of their respective owners.© 2023 VISHAY INTERTECHNOLOGY, INC. ALL RIGHTS RESERVED。
- 1、下载文档前请自行甄别文档内容的完整性,平台不提供额外的编辑、内容补充、找答案等附加服务。
- 2、"仅部分预览"的文档,不可在线预览部分如存在完整性等问题,可反馈申请退款(可完整预览的文档不适用该条件!)。
- 3、如文档侵犯您的权益,请联系客服反馈,我们会尽快为您处理(人工客服工作时间:9:00-18:30)。
SF
10.0
16
01
20
PT -04
PT
40
SF1605PT-06PT
4.0 2.0 1.0
125 0C 25 0C
0
50 CASE TEMPERATURE. ( C)
o
100
150
PEAK FORWARD SURGE CURRENT. (A)
FIG.3- MAXIMUM NON-REPETITIVE FORWARD SURGE CURRENT PER LEG
NOTES: 1. Rise Time=7ns max. Input Impedance= 1 megohm 22pf 2. Rise Time=10ns max. Sourse Impedance= 50 ohms
-1.0A 1cm SET TIME BASE FOR 5/ 10ns/ cm
AVERAGE FORWARD CURRENT. (A)
Maximum Instantaneous Forward Voltage @8.0A Maximum D.C. Reverse Current at Rated DC Blocking Voltage @ Tc=25℃ @ Tc=100℃
Symbol VRRM VRMS VDC I(AV) IFSM VF IR
SF1601PT THRU SF1606PT
16.0 AMPS. Glass Passivated Super Fast Rectifiers
Voltage Range 50 to 400 Volts Current 16.0 Amperes TO-3P/TO-247AD
Features
Dual rectifier construction, positive center-tap Plastic package has Underwriters Laboratory Flammability Classifications 94V-0 Glass passivated chip junctions Superfast recovery time, high voltage Low forward voltage, high current capability Low thermal resistance Low power loss, high efficiency High temperature soldering guaranteed: 260oC / 10 seconds, 0.16”(4.06mm) lead lengths at 5 lbs., (2.3kg) tesion
Mechanical Data
Cases: JEDEC TO-3P/TO-247AD molded plastic Terminals: Leads solderable per MIL-STD-750, Method 2026 Polarity: As marked Mounting position: Any Weight: 0.2 ounce, 5.6 grams Rating at 25℃ambient temperature unless otherwise specified. Single phase, half wave, 60 Hz, resistive or inductive load. For capacitive load, derate current by 20%
1000 500
10
CAPACITANCE.(pF)
200 100 50 20 10 .1
Tj=25oC f=1MHz Vsig=50mVp-p
TC=25 0C
1.0
0.1 1.0 5.0 10.0 50 100
0
20
40
60
80
100
120
140
.5
PERCENT OF RATED PEAK REVERSE VOLTAGE. (%)
- 236 -
RATINGS AND CHARACTERISTIC CURVES (SF1601PT THRU SF1606PT)
FIG.1- REVERSE RECOVERY TIME CHARACTERISTIC AND TEST CIRCUIT DIAGRAM
50W NONINDUCTIVE 10W NONINDUCTIVE +0.5A (-) DUT (+) 50Vdc (approx) (-) PULSE GENERATOR (NOTE 2) 1W NON INDUCTIVE OSCILLOSCOPE (NOTE 1) (+) 0 -0.25A trr
Trr Cj
RθJC TJ
V uA uA nS pF
2
℃/W
℃ ℃
-55 to +150 Storage Temperature Range TSTG -55 to +150 Notes: 1. Measured at 1 MHz and Applied Reverse Voltage of 4.0V D.C. 2. Reverse Recovery Test Conditions: IF=0.5A, IR=1.0A, Recover to 0.25A. 3. Mounted on Heatsink. Size of 3" x 5" x 0.25" Al-Plate.
REVERSE VOLTAGE. (V)
- 237 -
SF SF SF SF SF SF 1601PT 1602PT 1603PT 1604PT 1605PT 1606PT
Units
V V V A A
50 35 50
100 70 100
150 105 150 16 200
200 140 200
300 210 300
400 280 400
0.95 10.0 500 35 85.0
1.3
Maximum Reverse Recovery Time(Note 2) TJ=25℃
Typical Junction Capacitance (Note 1) Typical Thermal Resistance (Note 3) Operating Junction Temperature Range
FIG.2- MAXIMUM FORWARD CURRENT DERATING CURVE
20.0 16.0 12.0 8.0 4.0 0
FIG.5- TYPICAL INSTANTANEOUS FORWARD CHARACTERISTICS PER LEG
100
INSTANTANEOUS FORWARD CURRENT. ( A)
FIG.6- TYPICAL REVERSE CHARACTERISTICS
100 75 50 1.0 1000
INSTANTANEOUS REVERSE CURRENT. ( A)
2.0
5
10
20
50
100
TC=100 0C
NUMBER OF CYCLES AT 60Hz
100
FIG.4- TYPICAL JUNCTION CAPACITANCE PER LEG
PIN 1 PIN 3 Positive CT PIN 2
Dimensions in inches and (millimeters)
Maximum Ratings and Electrical Characteristics
Type Number
Maximum Recurrent Peak Reverse Voltage Maximum RMS Voltage Maximum DC Blocking Voltage Maximum Average Forward Rectified Current at Tc=100℃ Peak Forward Surge Current, 8.3 ms Single Half Sine-wave Superimposed on Rated Load (JEDEC method )
200 175 150 125
8.3ms Single Half Sine Wave JEDEC Method Tj=Tj max.
0.4 0.2 0.1 .2
Pulse Width=300 s 2% Duty Cycle
.4
.6
ห้องสมุดไป่ตู้
.8
1.0
1.2
1.4
1.6
1.8
2.0
FORWARD VOLTAGE. (V)